Арболит технология изготовления – Арболит своими руками — состав и пропорции для блоков
Cостав арболита: пропорции, химдобавки, технология изготовления
Общая характеристика арболита
Арболит – строительный материал, являющийся разновидностью легкого бетона, в нашей стране еще недостаточно широко распространен. В то время как за границей он существует под названиями дюризол и велокс и служит теплоизоляционным и конструктивно — теплоизоляционным материалом.
Основу арболита составляет древесный заполнитель и цемент. Его не следует путать с опилкобетоном, потому что щепа для него изготавливается специально и имеет свою фракцию и геометрию. Эти особенности утверждены ГОСТОМ 19222-84 «Арболит и изделия из него». Изделия из этого материала производят в виде блоков, плит, панелей.
Изделия из арболита классифицируют, в зависимости от назначения:
- для теплоизоляции и конструктивной теплоизоляции;
- армирования – армированные и неармированные;
- наружного профиля – гладкие и из сложного профиля;
- отделки поверхности — фактурные и нефактурные.
Арболит разделяется в зависимости от марок: 5; 10; 15; 25; 35; 50. Марки означают прочность арболитовых блоков, в зависимости от их предназначения. Теплоизоляционный имеет плотность до 500 кг/м3, конструкционный — плотность свыше 500 до 850 кг/м3. К теплоизоляционному относится арболит М 5,М 10, М15; к конструктивному М 25, М 35, М50.
Арболит используется при возведении жилых, гражданских, производственных зданий не более двух этажей, в качестве наружных несущих конструкций и внутренних стен помещений, теплоизоляции.
Преимущества и недостатки арболита
- высокий уровень тепло и звукоизоляции;
- высокая пожароустойчивость;
- устойчив к гниению;
- экономичен и недорог в строительстве;
- достаточно прочен, при нагрузке не ломается, а только продавливается. экологически чистый материал;
- в нем надежно крепятся гвозди, шурупы без дополнительного применения деревянных основ.
Однако, арболитовые конструкции без применения пароизоляции допущены к эксплуатации только в условиях сухого и нормального влажностного режима. При относительной влажности воздуха внутри помещения более 60% стены из него должны быть защищены пароизоляционным материалом.
Арболит не применяют для строительства цокольных этажей, карнизов, стен подвалов. Арболит следует защищать от атмосферных осадков путем гидрофобной окраски.
Состав арболита
Арболит изготавливается из древесного заполнителя, минерализатора, химических добавок и воды.
Органические составляющие
В качестве древесного наполнителя используют отходы древесины (сосна, ель, пихта, береза, осина, тополь) камыш, костру конопли, льна. Наиболее используемым древесным составом является деревянная щепа или дробленка и древесная стружка в соотношении 1:1 или 1:2. Вместо опилок можно использовать конопляные стебли или костру льна. Костру льна, из-за содержания в ней сахаров, разрушающих цемент, необходимо предварительно погрузить в известковое молоко (расход 50 кг извести на 200 кг костры) и выдержать 1-2 дня в куче. Другим способом является — выдерживание костры конопли, льна на открытом воздухе в течение 3-4 месяцев, тогда арболитовые блоки будут соответствовать показателям прочности. Форма костры имеет важное значение — она должна быть игольчатой длиной от 15 до 25 мм, шириной в 2-5 мм.
Минеральные вяжущие составляющие
Минерализатором в составе арболита выступает портландцемент 400, 500 или более высоких марок. Его расход зависит от его марки заполнителя арболита.
Обычно расход цемента рассчитывают следующим образом: для приготовления 1м3 арболита марки 15, необходимо умножить его значение на на коэффициент 17, например, 15 х 17 = 255 кг.
Химические составляющие арболита
Технические и строительные свойства арболита определяются химическими добавками. Их применение обязательно вне зависимости от климатических условий, в которых будет сооружаться здание из арболита. Именно химические вещества позволят использовать любой древесный наполнитель без предварительной обработки и выдержки, благодаря их способности нейтрализовать сахара.
В производстве арболита используют следующие химические добавки: хлористый кальций, гашеная известь, сернокислый алюминий, растворимое стекло. Наиболее эффективными являются хлористый кальций и алюминий. Сернокислый алюминий в соединении с сахарами нейтрализует их, обеспечивая возрастание прочности арболита.
Общее количество химических добавок в 1 м3 арболита составляет 2-4 % от общего веса цемента (около 6-12 кг). Добавки применяют как отдельно, так и смешивая алюминий с хлористым кальцием в пропорции 1:1, либо соединяя гашеную известь и растворимое стекло (1:1). Перед соединением с арболитовой смесью эти добавки необходимо растворить в воде.
Необходимые пропорции добавок зависят от вида арболита. Для арболитовых блоков марки 30 соотношение добавок следующее: сернокислый алюминий и хлористый кальций (1:1) в пропорции 4% от веса цемента; сернокислый натрий и хлористый кальций (1:1) в объеме 4% от веса цемента; сернокислый натрий и хлористый алюминий (1:1) в пропорции 2% от веса цемента; хлористый алюминий и хлористый кальций (1:1) в пропорции 4% от веса цемента.
Для арболитовой смеси марки 35 хлористый кальций добавляют в пропорции 2% от всей массы цемента. Использование хлористого кальция повышает прочность арболита. Для этого применяется жидкое стекло — силикат натрия или кальция, растворенные в горячей воде в количестве 8—10 кг на 1 м3 арболита.
Технология изготовления арболита
Производственная схема содержит следующие стадии:
- Дробление и придание необходимой формы заполнителю.
- Предварительная обработка органического заполнителя химическими составами.
- Дозирование составляющих компонентов для арболитовой массы.
- Подготовка арболитовой смеси.
- Формирование арболитовых блоков.
Дробление и придание необходимой формы заполнителю.
Перед дроблением куски и отходы древесины складываются в кучи и выдерживаются под навесом около месяца при положительной температуре. Затем эти отходы необходимо превратить в щепу на специальных машинах.
Отходы от деревопереработки, лесопиления подаются на приемную площадку, там они складируются, потом направляются в принимающую воронку рубильного механизма (ДУ-2). Для измельчения древесины рекомендуют пользоваться барабанной рубительной машиной, имеющей широкий спектр применения. Она может обработать практически каждый тип древесных отходов — рейки, кругляки, горбыль, обрезки, отторцовку, кривоствольную древесину. Обработанная таким образом щепа направляется в бункер, а затем идет в молотковую дробильную машину (ДМ-1), после этого древесная дробленка отправляется на вибрационный грохот, в целях отсеивания отходов и слишком крупных частиц.
На выходе дробленка представляет собой фракции древесины игольчатого или пластинчатого вида длиной от 2 до 20 мм, шириной от 2 до 5 мм, толщиной не больше 5 мм.
Предварительная обработка органического заполнителя химическими составами
Измельченная щепа с необходимым гранулометрическим составом направляется через промежуточный бункер в бак с водой для вымачивания и удаления, вредных для производства сахаров и веществ. Туда же направляют хлорид кальция. Вымачивание щепы при гидромодуле 1:10 продолжается 6 часов при температурном режиме 20°С. Применение предварительной гидротермической обработки улучшает физико-механические качества арболита. В воде древесина разбухает и этот процесс происходит до насыщения влагой волокна на 30%, при этом объем древесины и отдельные ее составляющие увеличиваются.
Дозирование составляющих компонентов для арболитовой массы
Важным условием однородности состава арболитовой массы и ее высокой стабильности является точное дозирование и качественное смешивание всех компонентов. Древесную щепу дозируют с помощью объемно — весового способа, с учетом коррекции насыпной плотности материала. Дробленке перед подачей на дозирование нужно иметь положительную температуру.
Для дозирования воды и химических добавок (хлорида кальция) используют автоматические дозаторы турбинного типа, работающие в цикличном либо непрерывном режиме. Возможен вариант дозирования добавок с помощью весового дозатора воды. При расчете дозировки воды и химических наполнителей учитывается влажность органического заполнителя и, соответственно, корректируются объемы добавляемой жидкости. Расчет доз цемента производится с помощью автоматических весовых дозаторов.
Загрузка и дозирование составляющих арболитовой смеси должна идти в следующей последовательности:
1) Древесный органический заполнитель.
2) Цемент.
3) Вода или водный раствор химических компонентов, регулируемый через расходомер.
4) Химические добавки, поступающие в течение всего процесса.
Подготовка арболитовой смеси
После вымачивания, дробленные деревянные фракции направляют в циклический смесительный механизм, являющийся бетономешалкой с принудительным действием. В смеситель подают из дозаторов вяжущие компоненты, воду, химические добавки. Там происходит смешивание всех составляющих до однородного состояния. Во время смешения вводят хлорид кальция с помощью метода дождевания и дозирования из перфорированных труб-распылителей. Данный способ точно вводит хлорид кальция и равномерно распределяет его, улучшая технологические свойства арболита. Все составляющие примешиваются в течение 10 минут. После смешивания из массы можно формировать арболитовые блоки.
Формирование арболитовых блоков
Приготовленная арболитовая смесь направляется через специальные бункеры-укладчики в металлические формы или разборные деревянные формы, там смесь утрамбовывается и уплотняется, с помощью пресса, силового вибропроката и виброштампования. Чтобы арболит, произведенный на стандартном портландцементе , достиг 50% прочности от марки, его выдерживают в формах 5 суток при температуре 15° С и относительной влажностью воздуха около 60-70%.
Можно также залить арболитовую массу в формы и выдержать ее в течение 24 часов при температуре 40° С и аналогичной влажностью. В таких условиях блоки выдерживаются 2 суток с сохранением постоянной температуры не ниже 15° С.
Далее происходит распалубка смеси на блоки, панели и изделия поступают на склад.
Наряду с описанной выше технологией, существует вариант приготовления арболитовых блоков, с древесным заполнителем из одубины — щепы древесины дуба, являющейся отходом производства экстрактов дуба.
Процесс производства арболита из одубины более прост, так как данный заполнитель не нуждается в дополнительном измельчении. Также существует технология изготовления арболита из высокопрочного гипса, которая гораздо проще, чем на базе цемента. Это происходит из-за того что гипс, взаимодействуя с водой, образует нейтральную среду, а не щелочную, которая вызывает выделение сахара из дерева. Так как нет факторов, снижающих отвердение цемента, то использование минерализующих добавок в производстве не требуется. Технология упрощается еще и в связи с тем, что используя высокопрочный гипс, можно применять дробленку гораздо крупнее по фракции, прошедшую только одно измельчение в рубильном механизме.
Таким образом, производство арболита на основе гипса менее затратное, чем при использовании цемента.
Щепа для арболита своими руками Арболит: недостатки и достоинства строительного материала Достоинства и недостатки кремнегранитных блоков
superarch.ru
Производство арболита своими руками: состав, пропорции, оборудование
Арболит (он же деревобетон) все чаще используется в малоэтажном строительстве. Во многом это связано с простотой производственной технологии и доступностью исходных компонентов. Именно о технологии, оборудовании и способах производства я расскажу в этой статье.
Производственное оборудование
Оборудование для производства арболита не отличается особой сложностью и габаритами. Его можно разместить на приусадебном или дачном участке, в любом боксе, цеху или просто на улице под навесом. Главное условие – наличие электроэнергии и удобство эксплуатации. Полный перечень заводского оборудования, необходимого для промышленного производства арбоблоков выглядит следующим образом:
- Шредер – измельчитель органических наполнителей (щепы, соломы и т.д.).
- Ёмкость для приготовления и розлива химических компонентов.
- Дозатор цемента.
- Дозатор органических наполнителей.
- Дозатор заполнителей для бетонного раствора.
- Бетоносмеситель для арболита принудительного типа действия.
- Подъёмно-поворотный бункер для приёма и дальнейшего розлива готового арболитового раствора.
- Система лебёдок для погрузочно-разгрузочных работ.
- Самозапечатываемые формы для отливки блоков.
- Вибропресс для арболита.
При кустарном производстве деревобетона, для собственных нужд, могут использоваться самодельные станки.
Состав арболита
Состав арболита регламентируется ГОСТ №19-222-84. Готовая к заливке арболитовая смесь состоит из следующих компонентов:
- Цементный раствор;
- Химические добавки;
- Органические наполнители.
Цемент
В качестве связующего компонента в производстве используется раствор на цементной основе. По ГОСТу, портландцемент для приготовления арболита должен иметь марку не ниже М-400.
Таблица . Технические характеристики цемента М-400
Добавлять песок в состав арболитного раствора не рекомендуется, так как это ухудшает показатели сцепки органических наполнителей с цементным вяжущим веществом. В результате блоки становятся менее прочными и склонными к расслоению и растрескиванию.
Химические добавки
Химические добавки предназначены для улучшения эксплуатационных характеристик арболита. В состав арболита входят следующие химические компоненты:
- Сернокислый алюминий, он же сульфат алюминия – неорганическая соль, хорошо растворимая в воде. При изготовлении арболита он используется в качестве гидроизолятора, увеличивающего стойкость материала к воздействию сырости.
Из-за высокой гигроскопичности, хранение сернокислого алюминия должно производиться в помещениях с низким уровнем влажности и в герметичной упаковке.
- Хлористый кальций – химический элемент, получаемый при промышленном производстве соды. Добавляется в арболитную смесь для связывания сахаров, содержащихся в органических заполнителях, что значительно повышает прочностные характеристики получаемого цементного раствора и позволяет повысить степень его сцепления с древесными компонентами.
- Жидкое стекло – водорастворённые силикаты натрия или калия. При изготовлении смеси для деревобетона, жидкое стекло выполняет роль отвердителя, а также для придания цементному раствору кислотоупорных и гидроупорных свойств.
- Гашёная известь добавляется в раствор для нейтрализации содержащихся в органических добавках природных сахаров и улучшения связующих качеств цемента и древесины.
Органические заполнители
В качестве наполнителя при производстве арболита используются отходы деревообрабатывающего производства. Главное отличие арболита от других видов лёгких бетонов состоит в том, что в его состав входят достаточно крупные компоненты – древесная щепа, костра льна, конопляная солома и т.д. От процентного содержания органического наполнителя зависят основные показатели материала: плотность, гигроскопичность, коэффициент теплопроводности и т.д.
- Древесная щепа – наиболее часто используемый заполнитель. Согласно ГОСТу, её размер не должен превышать 4 х 1 х 0,5 см. В связи с этим, технические характеристики арболитовых конструкций отличаются от характеристик опилкобетона и фибролита (стружкобетона).
Древесная щепа – главная составляющая арболитового блока
Нужный размер органической фракции получают при помощи специального станка-щепореза (шредера). Содержание щепы в общем объёме арболита может быть разным, и составлять от 30% до 90%.
- Льняная костра добавляется в таком же виде, в каком она получается на льноперерабатывающем заводе после предварительной обработки сырья.
- Конопляную солому перед использованием следует перемолоть в шредере.
Согласно техническим нормативам, льняные и конопляные наполнители должны иметь следующие размеры:
- Длина – от 15 до 25 мм.
- Ширина – от 2 до 5 мм.
В разных регионах для производства арболитовых блоков и панелей могут применяться и другие органические заполнители: рисовая и гречневая солома, отходы обработки хлопчатника и т.п.
В таблице даны технические характеристики арболита, изготовленных с применением разных органических наполнителей:
Технология производства
Технология производства арболита имеет ряд отличительных особенностей, которые касаются подготовки сырья, рецепта приготовления, дозировки компонентов. Её соблюдение обязательно как при промышленном выпуске, так и при производстве арболита своими руками в домашних условиях.
Подготовка органических заполнителей
Для деревобетона может использоваться щепа древесины хвойных пород – ели, сосны, пихты, а также лиственных деревьев с твёрдой древесиной – дуба, ясеня, берёзы.
Не рекомендуется применять в производстве щепу лиственницы и бука из-за химического состава – их древесина содержит значительно больше сахаров, что приводит к значительному снижению качества блоков. В крайнем случае, при производстве раствора с лиственничной или буковой щепой, придётся, как минимум, вдвое увеличить количество химдобавок – извести или хлористого кальция.
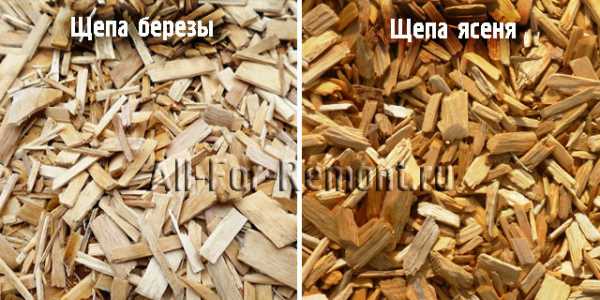
Щепа березы и ясеня – лучший наполнитель для арболитового блока
Первым шагом древесные отходы измельчаются посредством щепореза до размеров, регламентируемых ГОСТ №19-222-84 – не более 40х10х50 мм. Фактически же оптимальными размерами древесной фракции для формовки блоков являются 25х5х3 мм, так как более крупные компоненты хуже связываются цементным раствором и более склонны к расслаиванию в процессе эксплуатации.
После измельчения щепа просушивается. На крупных производственных линиях для этих целей применяют специальные сушилки барабанного типа, в которые подаётся горячий воздух.
Если арболит производится в домашних условиях, щепу складируют для просушки под навесами на срок не менее месяца, при температуре воздуха +15С.
Непосредственно перед замешиванием щепа замачивается на 6-8 ч в растворе воды с химическими добавками. Вода для этого должна соответствовать ГОСТу №23-732-79, где регламентируется её химический состав, кислотность и т.д. На деле же, при кустарном производстве деревобетона применяется любая доступная вода – из водопровода, реки или колодца. Единственное необходимое условие – она должна быть чистой и иметь температуру не ниже +15…+20С. После замачивания древесный наполнитель должен иметь влажность не более 30%.
Костра льна и солома конопли, для удаления из неё излишков сахаров, выдерживается на открытом воздухе не менее 2 – 3 месяцев при плюсовой температуре, либо замачивается в известковом молоке на 3-4 дня. Известковый раствор приготавливается в следующих пропорциях на 1 куб. м органики.
Органический заполнитель | Гашёная известь | Вода | Дополнительные условия |
1 куб. м костры льна или конопли | 2 – 2,5 кг | 150 – 200 л в зависимости от влажности наполнителя | Смесь перемешивается каждые 2 дня |
Пропорции смеси
Пропорции замеса могут незначительно изменяться, в зависимости от класса прочности деревобетона. Для получения более высокой марки арболита увеличивают долю цемента в общем объёме раствора. Ниже представлены рекомендуемые пропорции замеса раствора для деревобетона различных марок на куб готового раствора:
Марка | Портландцемент М-400 | Органический наполнитель | Химдобавки | Вода |
М-5 | 200 – 220 кг | 280 – 320 кг | 12-14 кг | 350 – 400 л |
М-15 | 250 – 280 кг | 240 – 300 кг | 12 кг | 350 – 400 л |
М-25 | 300 – 330 кг | 240 – 300 кг | 12 кг | 350 – 400 л |
М-50 | 350 – 400 кг | 220 – 240 кг | 10-12 кг | 350 – 400 л |
Химические добавки могут добавляться как по отдельности, так и комплексно. К примеру, строительные нормативы СН №54982 допускают смешивание сернокислого алюминия с известью в пропорции 8 кг и 4 кг на куб раствора.
Очерёдность загрузки
При замесе раствора важно соблюдать не только пропорции, но и очерёдность загрузки компонентов. Для изготовления качественной арболитной смеси обычные бетоносмесители, используемые для замеса бетона, не подойдут – щепа в них не сможет хорошо перемешаться с цементным раствором. Бетономешалка для арболита должна быть принудительного типа, например отечественные модели серии СБ, РН, импортные ZZBO и т.д. В них перемешивание компонентов производится не вращением барабана, а расположенным внутри него шнеком или лопастью.
Таблица 3. Технические характеристики принудительных смесителей серии СБ:
- Первым шагом в барабан смесителя насыпается подготовленная щепа в нужной пропорции.
- Затем бетоносмеситель запускается и в него заливается вода с растворёнными в ней химическими добавками. Органический заполнитель размешивается с химраствором в течение 30-60 секунд, чтобы щепки хорошо пропитались.
- После этого добавляется цемент и продолжается размешивание смеси в течение 3-5 минут, до получения однородной массы.
Формирование блоков
Формовка арбоблоков происходит с помощью специальных матриц, в которые заливается готовый раствор. Они изготавливаются из нержавеющей стали разборной конструкции для более лёгкого извлечения блоков.
Также такие формы можно изготовить самому из дерева или фанеры, обив их изнутри линолеумом или жестью. Размеры ячеек матрицы могут быть различными, в зависимости от потребностей в блоках тех или иных габаритов.
Трамбовка производится вручную, либо для этого используется вибростанок. В первом случае раствор заливается в формы слоями толщиной в 5 см, каждый из которых уплотняется металлической трамбовкой.
Во втором случае уплотнение раствора производится на вибростоле, которым обычно оборудуется промышленный станок для производства арболита.
Также при формовке для уплотнения раствора можно использовать ручной или механический пресс. Чтобы из уплотняемых блоков лучше выходил воздух, они периодически прокалывается металлическим стержнем.
Сушка
Сушка готовой продукции является завершающим этапом производственного процесса. В связи с особенностью конструкции, наилучшим вариантом является мягкий режим просушки.
Пропаривать арбоблоки по примеру железобетонных конструкций, не рекомендуется, так как материал теряет прочность из-за возрастающих внутренних напряжений. По этой же причине не следует пытаться ускорить высыхание блоков при помощи сушильных камер и других приспособлений.
Оптимальный режим просушки для арболита – температура 40-50 градусов, при влажности воздуха порядка 70-80%. В этом случае блоки набирают необходимую для распалубки прочность уже спустя 18-20 ч. что составляет около 1/3 от окончательной марочной. Дальнейшая выдержка материала производится при температуре 15-20 С в течение одной-двух недель – за это время деревобетон набирает окончательную прочность.
all-for-remont.ru
технология изготовления в домашних условиях
Арболит считается отличным строительным материалом, который годится для возведения стен любых помещений. Относится данный материал к группе легких бетонов и в простонародье его иногда называют опилкобетоном.
Технология изготовления
Раз арболит является опилкобетоном, то нетрудно догадаться, что в его состав, как и в состав любых других бетонов, входит цемент марки 400 и 500. Иногда при изготовлении арболита используется цемент с еще более высокими показателями для увеличения прочности готовых изделий. Что касается наполнителя, то в бетон добавляют мелкую древесную щепу, стружку, и, конечно же, опилки. При недостатке какого-либо из перечисленных наполнителей его заменяют остатками листвы, хвои или коры, которые не должны превышать 5% от массы заменяемого наполнителя.
Размеры используемых материалов в арболите не должны превышать в толщину — 5 мм, а в длину 25 мм. Именно поэтому вся органика сначала пропускается через дробилку, а уж потом смешивается с цементом. На заводах в органические отходы добавляют специальные химические вещества, которые нейтрализуют сахар, имеющийся в органике. Этот сахар очень негативно влияет на прочность арболита, поэтому его нейтрализация просто необходима.
В качестве химреактивов используется хлористый кальций и сернокислый алюминий. Естественно, если арболит изготавливается в домашних условиях, то таких веществ может просто не оказаться под рукой, поэтому можно будет обойтись и без них. Однако если вообще не убрать сахар, то арболит будет вспучиваться и чтобы этого избежать, нужно выдержать древесные отходы 3-4 месяца на улице под открытым небом.
Начинать изготовление арболита следует с обработки органики. Для этого дробленную древесную массу заливают водой и тщательно перемешивают. Специалисты рекомендуют выдерживать древесные отходы в известковом растворе около 3 часов, что также способствует разложению сахара. Замоченная в известковом растворе органика перемешивается с цементом до однородной массы.
Соотношение воды, опилок и цемента примерно должно выглядеть так: 4:3:3.
Перемешивается такой древесно-цементный раствор в бетоносмесителе, потому что образование комков здесь недопустимо. Полученная масса должна быть слегка рассыпчатой, но при сжатии в кулаке она должна держать форму комка. Если раствор держит форму, то значит он готов для дальнейшего применения по назначению.
Преимущества арболита
На западе арболит является одним из самых востребованных материалов и потихоньку он начинает завоевывать и наш рынок благодаря ряду весомых преимуществ:
- из арболита можно изготавливать блоки, перемычки, плиты или применять его для монолитной заливки стен;
- затвердевший арболит легко поддается любой обработке, поэтому его можно пилить, сверлить и подгонять другими способами под нужный размер;
- арболит является очень выгодным строительным материалом, потому что ингредиенты, применяемые в его изготовлении, очень доступны и сама технология производства не занимает много времени и средств;
- к затвердевшему арболиту очень хорошо подходит любая отделка, поэтому стены из него изготовленные можно штукатурить, обкладывать облицовочным кирпичом и даже обшивать гипсокартоном без установки каркаса и армирующей сетки;
- арболит может похвастать хорошей теплоизоляцией, поэтому дома построенные из арболитовых блоков требуют намного меньше отопления, чем кирпичные и плиточные аналоги;
- одно из главных преимуществ материала заключается в том, что он абсолютно пожаробезопасный так как, несмотря на наличие древесных отходов, он не загорается;
- также арболит не гниет и не подвергается грибковым поражениям;
- отличается морозостойкостью, поэтому широко применяется для строительства жилых объектов в северных регионах;
- ко всему прочему для арболита характерна хорошая звукоизоляция, что также является весомым преимуществом.
Самостоятельное производство блоков из арболита
Чаще всего из готовой арболитовой смеси изготавливают блоки, которые транспортируются легко, весят не много и подходят как для строительства разного типа. Изготовить такие блоки можно также просто, как и сам арболит, поскольку ничего особенного для этого не требуется.
Формы для арболитовых блоков можно сделать из деревянных ящиков со снимаемым дном. Некоторые опытные домашние изготовители рекомендуют с внутренней стороны оббивать ящик линолеумом, чтобы облегчить вынимание готового блока. В готовую форму арболит закладывается в два-три этапа послойно, и каждый слой обязательно тщательно утрамбовывается. Поверхность последнего слоя должна оставаться неровной, а до края бортов нужно оставить около 2-х см, чтобы это пространство можно было еще залить штукатурным раствором.
Наружную поверхность блоков можно смазать цементным раствором, что увеличит их прочность и устойчивость к атмосферному воздействию. Держать блоки в форме рекомендуется не меньше суток, чтобы смесь успела затвердеть. После этого блоки переносятся под навес, так как на солнце они могут пересохнуть и впоследствии раскрошиться.
Арболит считается чистым экологическим материалом, поэтому построенные из него здания не влияют негативно на человеческое здоровье.
personalhouse.net
Арболит — технология изготовления
Чтобы получить арболит, нужно четко следовать технологическому процессу, иначе будут допущены ошибки, способные негативно сказаться на качестве итогового продукта. Получение превосходных эксплуатационных свойств, возможно только в том случае, если производитель знает, что такое арболит технология изготовления, и соблюдает все пропорции и характеристики компонентов, участвующие в процессе изготовления.
Так как арболитовые блоки обладают сравнительно небольшой массой, из них сооружаются конструкции, которые не оказывают сильного воздействия на фундамент. Застройщики получают возможность экономить на формировании фундамента и на прочих строительных работах, которые необходимы при возведении объектов из кирпича или бетонных плит.
Свойства и состав арболита
Благодаря своей пористой структуре, арболитовый блок выгодно отличается от многих других строительных материалов, так как обладает меньшим весом при больших габаритных размерах. С помощью арболита быстро возводятся объекты различной степени сложности, и остается только провести отделочные работы. В составе арболитовых блоков находится:
- портландцемент,
- связующие элементы,
- древесные опилки,
- химические добавки,
- целлюлозное сырье,
- жидкость в необходимом объеме.
Если соблюдается арболит технология изготовления, то на выходе получаются арболитовые блоки или арболитовые плиты. По свойствам данные материалы отличий практически не имеют, но зато отличаются габаритные размеры и сфера использования данных элементов.
Строить из арболита допускается различные сооружения, но они не должны превышать двух уровней, потому что данному материалу присуща склонность к деформациям под действием чрезмерных нагрузок. Зато арболитовыми плитами утепляют множество строительных объектов, причем их монтаж производится и с наружной стороны здания, и с внутренней.
Габаритные размеры и сферы применения изделий из арболита
Арболитовые блоки обладают габаритными размерами: 25х25х50 сантиметров. При помощи этих блоков быстро возводятся объекты, и кроме того, для арболита характерны:
- долговечность,
- прочность,
- устойчивость к солнечным лучам,
- устойчивость к перепадам температуры,
- экологически чистый материал,
- практичность.
Если арболит технология изготовления используется для получения плит, то производитель должен выдерживать следующие габариты изделия:
- 100х150 см;
- 100х125 см;
- 50х100 см.
Допускаются и другие размеры, но значительно реже, если делается индивидуальный заказ.
Как изготавливается арболит?
Производство материала осуществляется, как в заводских, так и в домашних условиях, и если выдержаны количественные параметры всех элементов, участвующих в производственном процессе, то получается арболит с присущими ему свойствами. Естественно, что более высокое качество имеют арболитовые блоки и плиты, которые изготавливаются на заводе на специальном оборудовании.
В основном заводские процессы автоматизированы и постоянно осуществляется контроль за производством. В процессе изготовления применяются специальные формы, сушильная камера и вибростол.
Чтобы добиться оптимального результата, необходимо использование смазывающих веществ, так как после получения плиты или блока их нужно извлекать из форм. Если этого не делать, изделие способно потерять правильную конфигурацию, а значит, получится брак.
Но все-таки в домашних условиях тоже есть возможность получать арболитовые изделия, но для этого придется все процессы выполнять вручную, пользуясь специальными приспособлениями и инструментом. Для получения данного материала потребуется:
- Бетономешалка,
- Форма из листового металла или из пиломатериалов,
- Компоненты для замешивания.
Специалисты рекомендуют использовать формы именно из древесины, так как они отличаются практичностью и обходятся недорого. Нужно только сбить из досок необходимую форму, обшить изнутри пленкой, чтобы исключить прилипание смеси к дереву, а затем заливать раствор, выдерживая параметры.
Не следует забывать про специальную смазку, чтобы не испортить арбонитовые блоки при изъятии из деревянной формы. При загрузке компонентов в формы нужно соблюдать последовательность и не спешить загружать ингредиенты в полном объеме, так как это негативно скажется на качестве и прочности блока.
Сушить плиты придется в естественных условиях, так как обычно дома отсутствуют специальные сушильные камеры – если повезет с погодными условиями, блок сформируется и высохнет в течение нескольких часов.
Покупка и доставка арболита из другого региона
В силу того, что арболит как строительный материал в новейшей истории применяется не так часто (не берем в расчет строительство во времена СССР), не во всех регионах есть «правильные» производители, которые делают блоки по ГОСТу.
В некоторых случаях выгоднее купить арболитовые блоки в соседнем регионе и привезти их при помощи транспортной компании. Фактически любая транспортная компания из тех, что мы знаем (Рус-Экспресс Rus-Express.com, ЖелДорЭкспедиция JDE.ru, ПЭК Pecom.ru) возит стройматериалы от производителя к заказчику.
Транспортной компании выгодно везти такой груз, потому что на строительство даже небольшого арболитового дома мы заказываем как минимум панель, а иногда и две — от 6 до 20 поддонов блоков.
И нам это выгодно, потому что на объеме мы можем получить скидки у производителя арболитовых блоков, и тогда доставка выйдет нам бесплатно.
dnevnik-stroika.ru
Технология изготовления арболита
Совмещать раствор из цемента и древесные волокна в строительстве давно уже известный способ изготовления строительного материала.
Что такое арболит
Арболит изготавливают из древесных щепок, размером не больше 50 мм и раствора из цемента. Его основное свойство заключается в его низкой теплопроводности, но при этом нужно учитывать, что такой стройматериал не способен выдержать больших весовых нагрузок. По этой причине его больше применяют для стен верхних этажей. Данный материал уже давно широко известен, а появился он тогда, когда активно искали, чем заменить щебень, который использовали в качестве наполнителя. Общеизвестно, что древесина прекрасно способна сохранять тепло, и делает это намного лучше, чем камень.
Технология изготовления арболита достаточно проста — можно использовать практически все отходы, которые получаются после обработки дерева. Не подойдет для этого только кора. Эти самые древесные опилки можно купить на любой действующей лесопилке, где этого сырья всегда в избытке. Обычная технология изготовления арболита со следующими пропорциями: ведро цемента – два ведра песка – семь ведер древесных отходов.
Что такое опилкобетон
Опилкобетон по составу очень схож по составу с арболитом, но для его изготовления нужны именно опилки. Его блоки отличаются особой прочностью, но опилки должны быть размером не более 5 мм. Пропорции каждый выбирает сам, но стандарт примерно такой: одно ведро цемента – одно ведро песка – пять ведер опилок. В общем, количество опилок равно тому количеству щебня, который заменяется. Но в зависимости от стен, их прочности, высоты и прочего состав может немного изменяться.
По сути, арболит и опилкобетон это один и тот же материал, а различает их между собой только размер частиц наполнителя.
Что можно изготавливать из арболита?
С тех пор, как был создан данный материал, очень много продукции пытались из него сделать, но самые известные и широко используемые есть ЦСП и стенные блоки.
Что такое ЦСП?
Цементно – стружечная плита производится в заводских условиях. Для этого спрессовывается раствор из цемента и древесная щепка. Из данного состава выходит плита, которая имеет отличные теплоизоляционные свойства. Также, не последним фактором в пользу этого материала является его экологичность.
Производство арболитового блока происходит, так же как и плита, только на выходе имеет другую форму. Такой блок весит всего 4,5 кг, что выгодно оттеняет его на фоне восьми килограммового шлакоблока.
Стены из арболита
Из – за того, что арболит весит немного он способен сохранять жесткость конструкции, и даже в случае падении не крошится. Его можно сделать и самостоятельно имея под рукой нужный инструмент, а именно: бетономешалку, перфоратор и емкость из стали с крышкой.
Арболит своими руками
Если Вы приняли решение изготовить именно такой стройматериал, а древесные отходы не где взять, то не отчаивайтесь, так как их можно изготовить самостоятельно. Для этого нужно приобрести специальную машину для измельчения древесины, и хоть ее цена не маленькая, но эти затраты не так велики, как если бы пришлось потратить на закупку готовых блоков.
Бытует мнение, что древесина, которая входит в состав блока со временем начинает гнить, но на практике это не имеет никаких доказательств. Жилье из такого материала долгое время верой и правдой служит своим владельцам.
stroim.club
ᐓ Арболит ᐓ Технология изготовления арболита ᐓ САЙТ ПРО ДОМ
Готовят арболитовую смесь на ровной площадке в ящике с низкими бортами. В ящик высыпают органический заполнитель и поливают его водой с растворенными в ней химическими добавками. Тщательно перемешивают. Вода не должна вытекать из массы — ее поглотит заполнитель. Затем мокрый органический заполнитель посыпают цементом и всю массу перемешивают до получения однородной смеси. У хорошей смеси все древесные частицы покрыты цементом.
Мини-станок для производства арболит блоков
Арболитовая масса должна быть достаточно сыпучей, что определяется следующим образом. Возьмите в руку немного арболита, сожмите и покатайте комочек по ладони; при этом он должен сохранить форму и не рассыпаться. Воду необходимо вводить не всю сразу, а по частям, периодически проверяя массу указанным способом. Следует знать, что небольшой избыток воды и лишний расход цемента не ухудшают качество арболита, а лишь незначительно увеличивает себестоимость изделий. Для строительства одноэтажного дома из арболита достаточна марка арболита 15, для двухэтажного — марка 25 для первого этажа и марка 15 — для второго. Примерный расход материалов на 1 м3 арболита марки 15 и 25 приведен в таблице.
Потребность материалов для получения 1 м3 арболита марок 15 и 25
Марка арболита | Портландцемент марки 400, кг | Органический заполнитель (любого вида),кг | Химические добавки, кг | Вода л |
15 | 250-280 | 240-300 | 12 | 350-400 |
25 | 300-330 | 240-300 | 12 | 350-400 |
Для формования арболитовых блоков потребуются формы из дерева с обшивкой из фанеры, кровельной стали или из железа. Борта и днище формы желательно покрыть отходами линолеума, тогда не нужно будет смазывать формы известковым молоком. Арболитовую массу укладывают в форму в два-три приема послойно с трамбованием каждого слоя. По высоте форму заполняют так, чтобы до уровня бортов осталось 1,5—2,0 см. Поверхность арболита не обязательно делать гладкой. Важно хорошо ее утрамбовать, так как от этого зависит качество будущего арболитового блока. Оставшиеся 1,5—2 см заполняют обычным штукатурным раствором, который является защитой арболита от влаги. Эта поверхность уже должна быть ровной, поскольку она лицевая.
Арболитовый блок выдерживают в форме в течение нескольких суток при температуре воздуха 16—18° После приобретения некоторых навыков борта форм можно открывать уже через 2 — 3 часа или даже сразу. Арболитовые блоки оставляют на поддоне на одни, двое суток. Такая последовательность работы уменьшает расход материала на изготовление форм, поскольку одни и те же борта используют чаще.
Отформованные арболитовые блоки до монтажа следует выдержать от 7 до 14 суток где-нибудь под навесом. Нужно следить, чтобы поверхности арболитовых блоков не высыхали и не шелушились. Через 14 суток можно приступать к возведению стен.
По желанию арболитовым блокам можно придать декоративную отделку. Для этого на дно формы (это будет лицевая поверхность блока) укладывают тонким слоем гранитную крошку, посыпают ее цементом и наполняют арболитовой смесью. Можно использовать и битую керамическую плитку. Выложив ею дно, пространство между плитками заливают цементным раствором заподлицо с плитками, а затем укладывают арболитовую смесь. Для придания архитектурной выразительности фасадам зданий арболитовые блоки можно изготовлять «фигурными» — специально для углов, простенков, перегородок и т.д.
saitprodom.ru
Технология изготовления арболитовых блоков своими руками
Слово «арболит» произошло от французского «arbre», что в дословном переводе означает дерево.
Арболит представляет собой легкий бетон, изготовленный на базе цементного вяжущего, химических добавок и органических заполнителей, которых в составе смеси содержится до 90% от общего объема.
В качестве строительного материала арболит был стандартизирован в Советском Союзе еще в шестидесятые годы.
Такой материал известен еще под названием древобетон. Арболитовые блоки начали использовать еще в период 60-х годов прошлого века. Производство и дальнейшее использование арболита имеет множество преимуществ, если сравнивать его с традиционными стройматериалами.
Арболитовые блоки способны снизить массу зданий, сократить трудоемкость их возведения, снизить расход цемента и песка в 2,5 раза на 1 квадратный м. Кроме того, конструкция из этого материала способна демонстрировать значительное термическое сопротивление. Арболитовые блоки, имея крупнопористую структуру, способны обеспечить отличный воздухообмен во внутреннем пространстве помещений и превосходные теплотехнические показатели, что значительно снижает расходы на вентиляцию и отопление зданий. Применение арболита в строительстве исключает необходимость проводить дополнительные работы по наружной звуко- и теплоизоляции.
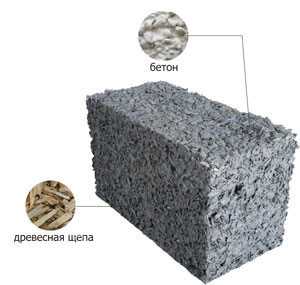
Строение блока арболита.
В современном строительстве многоэтажных домов, которое предполагает применение несущих каркасных монолитных элементов, в особенности актуальным считается использование мелкоштучных блоков из арболита, когда как оптимальная толщина самонесущей ограждающей стены равна З90 мм, что эквивалентно 1 метру кладки из кирпича. Это позволяет получить экономию материальных затрат и стройматериалов.
При индивидуальном строительстве в особенности ощутим эффект в процессе возведения несущих стен, где применяются такие блоки. В этом случае при идентичной толщине стен экономия стенового материала равна 60 процентам, что в 2,5 раза позволяет сократить расходы на обогрев или охлаждение помещений в неблагоприятные климатические периоды года.
Стены из этого материала отлично поддаются отделке традиционными и самыми современными отделочными материалами. Экономия применения этого материала заключается еще и в том, что он не нуждается в возведении сложных и тяжелых фундаментов, так как его относят к группе легких бетонов, а в простонародье такие блоки получили название опилкобетон.
Технология производства
В состав арболита входит цемент марки 400 или 500. В некоторых случаях в процессе изготовления этого материала своими руками используется цемент, который способен обеспечить еще более высокую прочность изделий. В качестве наполнителей к составу бетона добавляют мелкую древесную стружку, щепу, а также опилки. В случае недостатка какого-либо из наполнителей его можно заменить остатками хвои, листвы либо коры, однако процент такого заменителя не должен превышать 5 процентов от общего веса заменяемого наполнителя.
Схема стены из арболита.
Размеры применяемых материалов в составе арболита не должны превышать по толщине 5 мм, а вот их длина не должна быть больше 25 мм. Именно по этой причине при изготовлении арболита своими руками всю органику прежде следует пропустить через дробилку, а уже после можно переходить к смешиванию с цементом. В условиях заводов к органическим отходам добавляют химические вещества, нейтрализующие сахар, который имеется в органике. Это делают потому, что сахар способен негативно влиять на прочность материала, именно поэтому процесс нейтрализации так необходим. В качестве химреактивов применяется сернокислый алюминий и хлористый кальций. Естественно, при изготовлении арболита своими руками таких веществ можно не найти, поэтому в процессе можно обойтись и без них. Но если не позаботиться о нейтрализации сахара, то смесь станет вспучиваться. Способ этого избежать все же есть, для этого древесные отходы предстоит выдержать в течение примерно 4 месяцев под открытым небом.
Процесс изготовления арболита начинается с этапа обработки органики. Дробленая древесная масса для этого заливается водой и тщательно перемешивается. Профессионалы советуют выдержать древесные отходы около 3 часов в известковом растворе, что будет способствовать разложению сахара. Органику, которую предварительно замачивают в известковом растворе, следует перемешать до однородной массы с цементом. Соотношение воды, цемента и опилок должно быть таким, 4:3:3.
Фундамент своими руками.
Что такое каркасная конструкция?
Монолитный дом — это? Подробнее>>
Тонкости изготовления
Для перемешивания компонентов арголита, советуется использовать бетономешалку, чтобы избежать оброзование комков.
Перемешивается вышеописанный раствор из древесины и цемента в бетоносмесителе, образование комков в этом случае недопустимо. Полученная масса при соблюдении всех требований должна получиться слегка рассыпчатой, однако после сжатия в кулаке она должна удерживать форму. Если раствор способен удержать форму, значит, его уже можно использовать по назначению.
Арболит подходит не только для изготовления блоков, с его применением можно производить плиты или перемычки, подходит этот материал и для заливки монолитных стен. Затвердевший арболит отлично поддается обработке, именно поэтому его можно сверлить, пилить, а также подгонять всевозможными способами под требуемый размер.
При выдерживании опилок и стружки на открытом воздухе следует их периодически перелопачивать. В том случае когда такая возможность отсутствует, необходимо обработать смесь, используя окись кальция. Данный известковый раствор делают из расчета 200 литров 1,5-процентного раствора на объем сырья в количестве 1 кубического метра. Обработанные таким раствором стружку и опилки оставляют на 4 дня с учетом перемешивания, что необходимо делать несколько раз в течение дня.
Арболитовые блоки своими руками получатся качественными только с учетом использования бетономешалки. В качестве добавок можно применять жидкое стекло, хлористый кальций, сернокислый кальций или алюминий и гашеную известь. Эти добавки следует готовить в количестве 4 процентов от общей массы цемента. Лучшей комбинацией добавок для блоков станет смесь сернокислого алюминия и сернокислого кальция в соотношении 50/50 или смесь, в составе которой жидкое стекло и окись кальция присутствуют в том же соотношении. После того как древесина для будущих блоков была пропущена через рубильную машину, что предполагает первичную обработку, следует осуществить дробление материала, используя молотковую дробилку.
Следующим этапом станет сортировка, в процессе этого должна отсеяться земля, кора, пыль и недопустимые вещества в составе арболитовых блоков. После предстоит добавить 20% просеянных опилок. Полученный материал должен быть подвергнут химической обработке, что предполагает замачивание в воде, в которую предварительно добавлено жидкое стекло.
Материалы для работы
- цемент;
- мелкая древесная стружка;
- щепа;
- опилки;
- вода;
- хлористый кальций;
- жидкое стекло;
- сернокислый кальций;
- сернокислый алюминий.
Качество материала
Для ускорения процесса отвердевания и минерализации материала следует добавить хлористый кальций в древесную массу. В качестве дезинфекции используется гашеная известь. Готовая масса замешивается с цементом, а после подается в вертикальные и горизонтальные формы. Для придания будущим изделиям большей плотности материал следует подвергнуть обработке пневматическими или электрическими трамбовками и вибропрессом. Формы для арболитовых блоков, которые вы намерены сделать своими руками, рекомендуется изготавливать из досок. Упростит процесс выемки изделий линолеум, который необходимо набить на стенки форм.
1pobetonu.ru