Что нужно для изготовления полимерных изделий – Производство пластмассовых изделий: анализ, оборудование, окупаемость
Сферы применения полимерных материалов
Полимеры — это соединения макромолекулярного типа. Их основа — мономеры, из которых формируется макроцепь полимерных веществ. Применение полимеров позволяет создавать материалы, обладающие высоким уровнем прочности, износостойкости и рядом других полезных характеристик.
Классификация полимеров
Природные. Образуются естественным природным путем. Пример: янтарь, шелк, натуральный каучук.
Синтетические. Производятся в лабораторных условиях и не содержат природных компонентов. Пример: поливинилхлорид, полипропилен, полиуретан.
Искусственные. Производятся в лабораторных условиях, но в их основе лежат природные составляющие. Пример: целлулоид, нитроцеллюлоза.
Виды полимеров и их применение очень многообразны. Большая часть предметов, которые окружают человека, созданы с использованием этих материалов. В зависимости от типа, они имеют различные свойства, которые и определяют сферу их применения.
Существует ряд распространенных полимеров, с которыми мы сталкиваемся ежедневно и этого даже не замечаем:
- Полиэтилен. Используется для производства упаковки, труб, изоляций и других изделий, где требуется обеспечить влагонепроницаемость, устойчивость к агрессивным средам и диэлектрические характеристики.
- Фенолформальдегид. Является основой пластмасс, лаков и клеевых составов.
- Синтетический каучук. Обладает лучшими прочностными характеристиками и устойчивостью к истиранию, чем натуральный. Из него изготавливается резина и различные материалы на ее основе.
- Полиметилметакрилат — всем известный плексиглас. Используется в электротехнике, а также в качестве конструкционного материала в других производственных областях.
- Полиамил. Из него изготавливается ткань и нитки. Это капрон, нейлон и другие синтетические материалы.
- Политетрафторэтилен, он же — тефлон. Применяется в медицине, пищевой промышленности и различных других областях. Всем известны сковородки с тефлоновым покрытием, которые были когда-то очень популярны.
- Поливинилхлорид, он же ПВХ. Часто встречается в виде пленки, используется для изготовления изоляции кабелей, кожзаменителей, оконных профилей, натяжных потолков. Имеет очень широкую сферу использования.
- Полистирол. Применяется для производства бытовых изделий и широкого ряда строительных материалов.
- Полипропилен. Из этого полимера изготавливаются трубы, тара, нетканые материалы, бытовые изделия, строительные клеи и мастики.
Где применяются полимеры
Область применения полимерных материалов очень широка. Сейчас можно с уверенностью сказать — они используются в промышленности и производстве практически в любой сфере. Благодаря своим качествам полимеры полностью заменили природные материалы, существенно уступающие им по характеристикам. Поэтому стоит рассмотреть свойства полимеров и области их применения.
По классификации материалы можно разделить на:
- композиты;
- пластмассы;
- пленки;
- волокна;
- лаки;
- резины;
- клеящие субстанции.
Качества каждой разновидности определяет область применения полимеров.
Быт
Оглядевшись вокруг, мы можем увидеть огромное количество изделий из синтетических материалов. Это детали бытовых приборов, ткани, игрушки, кухонные принадлежности и даже бытовая химия. По сути — это огромный ряд изделий от обычной пластмассовой расчески до стирального порошка.
Такое широкое использование обусловлено низкой стоимостью производства и высокими качественными характеристиками. Изделия прочны, гигиеничны, не содержат вредных для организма человека компонентов и универсальны. Даже обычные капроновые колготки изготовлены из полимерных составляющих. Поэтому полимеры в быту применяются гораздо чаще, чем натуральные материалы. Они существенно превосходят их по качествам и обеспечивают низкую цену изделия.
Примеры:
- пластиковая посуда и упаковка;
- части различных бытовых приборов;
- синтетические ткани;
- игрушки;
- кухонные принадлежности;
- изделия для санузлов.
Любая вещь из пластика или с включением синтетических волокон изготавливается на основе полимеров, так что перечень примеров может быть бесконечным.
Строительная отрасль
Применение полимеров в строительстве тоже очень обширно. Их стали использовать сравнительно недавно, примерно 50-60 лет тому назад. Сейчас большая часть строительных материалов производится с применением полимеров.
Основные направления:
- изготовление ограждающих и строительных конструкций различного типа;
- клеящие составы и пены;
- производство инженерных коммуникаций;
- материалы для тепло- и гидроизоляции;
- наливные полы;
- различные отделочные материалы.
В сфере ограждающих и строительных конструкций — это полимербетон, композитная арматура и балки, рамы для стеклопакетов, поликарбонат, стеклопластик и различные другие материалы подобного типа. Все изделия на полимерной основе имеют высокие прочностные характеристики, длительный срок службы и устойчивость к негативным природным явлениям.
Клеи отличаются устойчивостью к влаге и отличной адгезией. Они используются для склеивания различных материалов и имеют высокую прочность соединения. Пены — идеальное решение для герметизации стыков. Они обеспечивают высокие теплосберегающие характеристики и насчитывают огромное количество разновидностей с различными качествами.
Применение полимерных материалов в сфере производства инженерных коммуникаций — одно из наиболее обширных направлений. Они используются в водоснабжении, электрообеспечении, теплосбережении, оборудовании канализационных сетей, вентиляции и отопительных систем.
Материалы для теплоизоляции имеют отличные теплосберегающие характеристики, малый вес и доступную стоимость. Гидроизоляция отличается высоким уровнем водонепроницаемости и может выпускаться в различном виде (рулонные изделия, порошок или жидкие смеси).
Полимерные полы — это специализированный материал, который позволяет создать на черновой основе идеально ровную поверхность без трудоемких работ. Такая технология используется как в бытовом, так и в промышленном строительстве.
Современная промышленность выпускает широкий ряд отделочных материалов на основе полимеров. Они могут иметь различную структуру и форму выпуска, но по характеристикам всегда превосходят натуральную отделку и имеют гораздо меньшую стоимость.
Медицина
Применение полимеров в медицине имеет широкое распространение. Самый простой пример — одноразовые шприцы. На данный момент производится около 3 тысяч изделий, используемых в медицинской сфере.
Чаще всего в данной области используются силиконы. Они незаменимы при проведении пластических операций, создания защиты на ожоговых поверхностях, а также изготовления различных изделий. В медицине полимеры использовались с 1788 года, но в ограниченном количестве. А 1895 году они получают более широкое распространение после операции, в ходе которой костный дефект был закрыт полимером на основе целлулоида.
- 1 группа — для введения в организм. Это искусственные органы, протезы, кровезаменители, клеи, лекарственные препараты.
- 2 группа — полимеры, имеющие контакт с тканями, а также веществами, предназначенными для введения в организм. Это тара для хранения крови и плазмы, стоматологические материалы, шприцы и хирургические инструменты, составляющие медицинского оборудования.
- 3 группа — материалы, не имеющие контакта с тканями и не вводящиеся в организм. Это оборудование и приборы, лабораторная посуда, инвентарь, больничные принадлежности, постельное белье, оправы для очков и линзы.
Сельское хозяйство
Наиболее активно полимеры используются в тепличном хозяйстве и мелиорации. В первом случае имеется потребность в различных пленках, агроволокне, сотовом поликарбонате, а также арматуре. Это все необходимо для сооружения теплиц.
В мелиорации используются трубы из полимерных материалов. Они имеют меньший вес, чем металлические, доступную стоимость и более длительный срок службы.
Пищевая промышленность
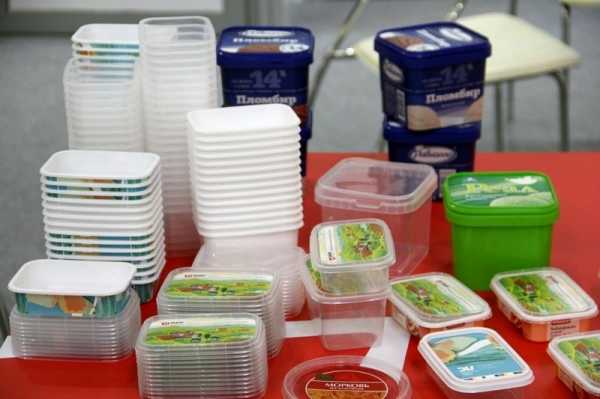
В пищевой промышленности полимерные материалы используются для изготовления тары и упаковки. Могут иметь форму твердых пластиков или пленок. Основное требование — полное соответствие санитарно-эпидемиологическим нормам. Не обойтись без полимеров и в пищевом машиностроении. Их применение позволяет создавать поверхности с минимальной адгезией, что важно при транспортировке зерна и других сыпучих продуктов. Также антиадгезионные покрытия необходимы в линиях выпечки хлеба и производства полуфабрикатов.
Полимеры применяются в различных отраслях деятельности человека, что обусловливает их высокую востребованность. Обойтись без них невозможно. Натуральные материалы не могут обеспечить ряда характеристик, необходимых для соответствия конкретным условиям использования.
plastmass-group.ru
Изделия из полимерных материалов | Строительный портал
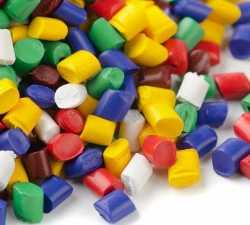
Полимеры окружают нас повсюду, большинство предметов общего употребления изготовлены именно из них. Существует несколько видов полимерных материалов. Об их особенностях, свойствах и характеристике поговорим далее.
Оглавление:
- Классификация полимерных материалов и изделий
- Технология производства полимерных материалов
- Кровельные полимерные материалы и изделия в строительной отрасли
Классификация полимерных материалов и изделий
Полимерные материалы объединяют в себе несколько групп пластика синтетического происхождения. Среди них отметим:
- полимерные вещества;
- пластмассовые составы;
- ПКМ — полимерные композитные материалы.
В каждой из перечисленных групп присутствует полимерное вещество, с помощью которого можно определить характеристику того или иного состава. Полимеры являются высокомолекулярными веществами, в которые вводят специальные добавки, то есть стабилизаторы, пластификаторы, смазки и т.д.
Пластмасса — является композиционным материалом, в основе которых лежит полимер. Кроме того, в их составе содержится наполнитель дисперсного или коротковолокнистого типа. Наполнители не склонны к образованию непрерывных фаз. Различают два вида пластмассовых веществ:
- термопластик;
- термоактивы.
Первый вариант пластмасс склонен к расплавлению и дальнейшему использованию, второй вариант пластмассы не склонен к расплавлению под воздействием высокой температуры.
В соотношении со способом полимеризации, пластмассы добывают с помощью:
- поликонцентрирования;
- полиприсоединений.
Рассматривая виды полимерных веществ, выделим:
1. Вид полиоэфинов — полимеры с одинаковой химической природой относятся к данной разновидности полимеров. В их составе присутствует два вещества:
- полиэтиленовое;
- полипропиленовое.
Каждый год, в мире производят более ста пятидесяти тонн таких полимеров. Среди преимуществ полиоэфинных веществ отметим:
- стойкость перед ультрафиолетовым излучением;
- устойчивость перед окислителями и разрывом;
- механическая стойкость;
- отсутствие усадки;
- изменение свойств при необходимости.
Если сравнивать полиоэфины с другими типами полимерных веществ, то первые отличаются наибольшей экологической безопасностью. Для их изготовления и переработки материалов необходимо минимальное количество энергии.
2. Полиэтилен широко распространен в процессе упаковки любых изделий. Среди преимуществ использования данного материала отметим широкую сферу применения и отличные эксплуатационные характеристики.
Строение полиэтилена довольно простое, поэтому он легко кристаллизуется.
Полиэтиленовые вещества с высоким давлением. Данный материал отличается наличием легкого матового блеска, пластичностью, наличием волнообразной текстуры. Данный вид пленки отличается высокой механической стойкостью, устойчивостью перед ударами и разрывом, прочностью даже при морозе. Для его размягчения потребуется наличие температуры около ста градусов.
Полиэтиленовые вещества с низким давлением. Пленки такого типа имеют жесткую, прочную основу, которая отличается меньшей волнообразностью, по сравнению с предыдущим вариантом полиэтилена. Для стерилизации данного вещества используется пар, а температура его размягчения составляет более ста двадцати одного градуса. Несмотря на наличие высокой стойкости перед сжатием, пленка отличается более низкими характеристиками стойкости перед ударом и разрывом. Однако, среди их преимуществ также отмечают стойкость перед влагой, химическими веществами, жиром, маслом.
Использование полиэтилена при комнатной температуре позволяет получить более мягкую и гибкую его текстуру. Однако, в морозных условиях, данные характеристики сохраняются. Поэтому полиэтилены используются для хранения замороженной продукции. Однако, при повышении температуры до ста градусов тепла, характеристики полиэтилена изменяются, он становится непригодным к использованию.
Полиэтилен низкого давления используется при изготовлении бутылок и для упаковки разного рода веществ. Он обладает отличными эксплуатационными характеристиками.
Полиэтилен высокого давления более широко применим как упаковочный полимер. У него присутствует низкая кристалличность, мягкость, гибкость и доступная стоимость.
3. Полипропилен — материал у которого присутствует отличная прозрачность, высокая температура расплавления, химическая стойкость и устойчивость перед влагой. Полипропилен способен пропускать пар, неустойчив перед кислородом и окислителями.
4. Поливинилхлорид — довольно хрупкий и не эластичный материал, который чаще всего используется в качестве добавки к полимерам. Отличается дешевой стоимостью, высоковязким расплавом, термической нестабильностью, а при нагреве, склонен выделять токсичные вещества.
Технология производства полимерных материалов
Изготовление полимеров — довольно сложный процесс, для выполнения которого следует учитывать многие технические моменты работы с данными материалами. Различают несколько разновидностей технологий изготовления материалов на полимерной основе. Полимерные материалы, изделия, оборудование, технологии, методы:
- вальцево-каландровый метод;
- применение трехкомпонентной технологии;
- использование экструзии термопластиковых изделий;
- метод литья полимеров крупной, средней и маленькой формы;
- формирование полистирольных веществ;
- изготовление плит из пенополистирола;
- выдувной метод;
- изготовление изделий на основе ППУ.
Самыми популярными методами производства изделий из полимерных материалов являются выдув и термоформировка. Для выполнения первого метода главными исходными материалами выступает полиэтилен и полипропиленовые составы. Среди основных характеристик полиэтилена отметим быструю усадку, стойкость к температурной нестабильности. С помощью выдува формируются изделия объемной формы.
С помощью термической формировки удается сделать пластиковую посуду. В таком случае, процедура изготовления изделий состоит из трех этапов. Вначале определяют количество пластика, далее он помещается в предварительно подготовленную форму, далее производится его расплавливание. Пластмасса устанавливается под прессом, далее она закрывается. В формирующей станции изделия доводится до нужной формы, на следующем этапе производится его охлаждение и затвердение. Далее изделие извлекают из формы и выбрасывают в специальный резервуар.
Использование современного оборудования для изготовления пластмассовых изделий, позволяет получить вещество, отличающееся прочностью, длительностью эксплуатации.
Выделяют оборудование автоматизированного типа, с его помощью также производят полимерные вещества. В таком случае, в процессе работы над полимерными изделиями человеческий фактор практически отсутствует вся работа проводится специальными роботами.
С помощью применения автоматизированного оборудования удается получить вещества, отличающиеся более высоким качеством, широким ассортиментом продукции и снижением расходов на их изготовление.
Различают огромное количество изделий из полимерных материалов. Они различаются между собой по величине, способу изготовления, составу, Для изготовления полимеров используют вещества в виде:
- натуральных полиамидов с содержанием стекловолокна;
- полипропиленов, которые делают изделия стойкими перед морозом;
- поликарбонатов;
- полиуретана;
- ПВХ и т.д.
Кровельные полимерные материалы и изделия в строительной отрасли
Любая кровля должна быть долговечной и надежной. Довольно популярными отделочными материалами для кровли являются изделия на основе полимерных материалов. Среди преимуществ их использования отметим:
- высокую степень эластичности;
- надежность;
- отличную прочность;
- стойкость перед растяжением и механическими повреждениями;
- установка практически в любом климатическом регионе;
- легкий монтаж и простая эксплуатация;
- длительность эксплуатации.
Использование мембранной кровли полимерного состава основывается на механическом креплении сначала теплоизоляционного и гидроизоляционного слоев. С помощью мембраны удается создать различные по форме и конфигурации кровли зданий.
Выделяют несколько видов полимерных мембран в зависимости от их состава и основных характеристик:
- поливинилхлоридные мембраны, в составе которых присутствуют дополнительные наполнители;
- мембраны на основе пластичных полиэфинов;
- мембраны, в составе которых присутствует этиленпропилендиенпономер.
Первый вариант мембраны отличается особой популярностью. Основным составляющим веществом мембраны является поливинилхлорид и разного рода добавки. С их помощью состав становится более устойчив перед низкой температурой. В качества армирования пленки используется сетка из полиэстера. Она делает изделие более прочным и стойким к разрыву. Именно с помощью данных характеристик удается обеспечить механическое крепление пленки.
Если рассматривать недостатки ПВХ мембран, то стоит отметить потерю их эластичности, по прошествии определенного периода эксплуатации. Так как, добавки, присутствующие в их составе со временем теряют свойства. Кроме того, данный материал ни в коем случае не используется с гидроизоляторами на битумной основе, они между собой несовместимы. Длительность эксплуатации ПВХ мембран составляет не более тридцати лет.
Мембраны на основе термопластичных полиэфинов содержат в составе каучук и особые вещества, улучшающие их пожарную безопасность. В данном материале удается удачность скомбинировать пластичность и резину. Среди их преимуществ отметим:
- совместимость с веществами на битумной основе;
- длительность эксплуатации, не нуждаются в ремонте до сорока лет;
- существует возможность ремонта поверхности, при необходимости;
- легки в монтаже;
- более длительный срок эксплуатации, по сравнению с материалами на основе ПВХ.
Среди недостатков отметим только более высокую стоимость такой кровли. Которая вполне перекрывается всеми ее достоинствами.
Мембраны на основе ЭПДМ отличаются отличной стойкостью перед климатическими изменениями, эластичностью и длительностью эксплуатации.
Среди большого количества полимерных строительных материалов и изделий, к особой группе относят наличную полимерную кровлю. Среди преимуществ ее применения, отмечают:
- отличные гидроизоляционные характеристики;
- высокий уровень прочности;
- стойкость к изменению температуры;
- высокий уровень морозостойкости;
- отсутствие стыков;
- высокая стойкость к механическим повреждениям и износу;
- стойкость перед гниением;
- разнообразие цветовых решений;
- легкость выполнения монтажных работ;
- срок эксплуатации составляет около пятнадцати лет.
Полимерная кровля наливного характера очень схожа с мембраной, однако, они различаются в технологии монтажа материала. В зависимости от технологии наливки кровли она бывает:
- полимерной;
- полимерно-резиновой.
Первый вариант более распространен из-за наличия в нем огромного количества преимуществ. Для нанесения данного типа кровли потребуется налить состав на поверхность и равномерно распределить его с помощью кисти или валиком. Главным преимуществом данной кровли является полная ее герметичность, эластичность и монолитность.
В соотношении с технологией установки наливной кровли, она бывает:
- армированной;
- неармированной;
- комбинированной.
Наливная кровля с армированием содержит в своем составе цельную битумную эмульсию и дополнительное армирование с помощью стеклоткани. Неармированное покрытие состоит из эмульсионного материала, который наносится непосредственно на кровлю, толщиной около 1 мм. Комбинированный вариант предполагает использование полимерных мастик, гидроизоляционных материалов рулонного типа, верхнего слоя, в составе которого присутствует каменная крошка, гравий и краска на влагостойкой основе. Нижний слой кровли содержит подкладку в виде недорогого рулонного материала. При этом, армирование обеспечивается верхним слоем из каменной крошки.
В составе полимерной наливной кровли присутствует:
- композиции полимерного типа;
- наполнители, повышающие эксплуатационные характеристики материала;
- грунтовка, с помощью которой выполняется подготовка основания перед нанесением кровли;
- армирующий состав — полиэфирное волокно или стеклоткань.
Довольно распространенным вариантом является использование кровли на основе полиуретана. Она отлично ложится на поверхность и легко устанавливается на сложных участках вблизи дымохода или телевизионной антены. Полиуретан делает кровлю схожей с резиной, он придает ей таких качеств как стойкость к перепаду температур, длительность эксплуатации.
Еще одним вариантом полимера на органической основе, используемого в процессе ремонта и изготовления наливной кровли, является полимочевина. Среди ее преимуществ отметим:
- очень быстрая полимеризация, для хождения по кровле достаточно подождать один час после нанесения материала;
- способность проводить работы при температуре до -16 и высокой влажности;
- отличные электроизоляционные характеристики;
- стойкость перед ультрафиолетовым излучением;
- пожарная безопасность и стойкость перед высокой температурой;
- длительность эксплуатации;
- экологическая безопасность.
Применение полимерных материалов и изделий связано с разными отраслями промышленности и общественности. Использование полимочевины особо актуально в регионах с нестабильным климатом и резкими изменениями температурного режима.
strport.ru
Производство пластмассовых изделий
В начале семидесятых годов ХХ века всемирное производство пластмассовых изделий составляло не более 7% от общего производства полимерных изделий, то сейчас эта цифра превышает 25%. Существует немалый спрос на данный вид изделий, поэтому и заработать можно не плохо в этой области.
Рентабельность выпуска изделий из пластика может доходить и до 30%. Уровень выгодности зависит продукта, какой выпускается. Также большую роль играет размер начальных капиталовложений.
Помещение, цех для производства изделий из пластмассы, пластика
Для того чтобы разместить производство изделий из пластика, необходимо помещение со стандартными коммуникациями. Каких-либо особых требований обычно не предъявляется. Исключение составляют те производства, где процесс вспенивания происходит с использованием пентана. Важно не забыть, что помещения для производства необходимо подбирать вдали от “спальных” районов больших городов, лучше всего расположиться на окраине населенного пункта или в промышленной зоне. Для размещения линии площадей потребуется всего лишь 40 — 200 кв.м. Но склад может понадобиться очень большой (так как складировать придется «воздух» — изделия весят не много, но места при этом занимают не мало).
В этом качестве можно применять практически любое помещение, которое обеспечивает защиту изделий от влаги, ветра, пыли, бомжей, воров и других неблагоприятных факторов. Необходимо хранить гранулированные полимеры в сухом и, если это возможно, отапливаемом помещении: в таком случае их поверхность будет адсорбировать меньше влаги, а качество какого-либо изделия от этого ещё больше улучшится. К инстанциям, у которых необходимо получить разрешение для организации производства изделий из пластика, относятся санэпидстанция, местные органы исполнительной власти, местные подразделения Госнадзорохрантруда, пожарная инспекция, тепловики, газовая служба и электрики. Затраты материальных средств и времени на получение разрешений будут зависеть от сноровки владельца. В благоприятных случаях хватает 2-3 месяцев.
Оборудование для производства изделий из пластмассы, пластика
Технику для производства пластмассовых изделий можно найти разнообразную. На некоторых предприятиях существует простаивающая техника, которую при надлежащей сноровке можно приобрести довольно дешево и с помощью специалистов модернизировать ее и привести в рабочее состояние. Если же есть достаточно материальных средств, лучше приобрести новую технику. В нашей стране есть большое количество машиностроительных организаций, которые выпускают технику для изготовления машин для переработки пластика. Можно приобрести и импортное оборудование.
Основное оборудование:
- вакуум-формовочное оборудование,
- станок для нарезки резьбы на пластиковых трубах,
- термопластавтомат,
- литейные машины термопластов,
- оборудование производства пластиковой упаковки
Всё будет зависеть от того, какое изделие будет производится.
Сырье для пластмассовых изделий
С сырьем для производства изделий из пластика довольно сложно. Каким бы ни было хорошим оборудование, его использование, не позволит получить продукцию одинакового качества из аналогичного пластика от разных производителей. Чтобы перейти от одного сырья к другому, необходима серьезная переналадка техники и отработка технологии с применением нового пластика. Самый лучший вариант — постоянно покупать пластик у одного производителя.
Для обслуживания линии по производству изделий из пластика понадобится до 10 человек. Рабочих, наверное, придется учить “с нуля”. Также придется за немалые деньги нанимать технолога.
Технологический процесс производства пластмассовых изделий
Технология получения пластика заключается в организации композиции, введении газовой фазы в специальную полимерную среду (обычно благодаря вспениванию), придании этой вспененной массе нужной формы с ее фиксацией. Иногда эту композицию могут заливать в форму, а потом уже вспенивают. В процессе создания композиции совмещают ингредиенты резиновой смеси или пластической массы.
Для введения газовой фазы в полимерную среду можно использовать несколько способов: введение в композицию газа под давлением, механическое вспенивание, насыщение композиций легкокипящими жидкостями, превращающимися при нагревании в пар. Способ введения газовой фазы используются в зависимости, какой пластик будет подвергаться переработке и что хотят из него получить. Перерабатывая разнообразный пластик и используяя разнообразные приемы, можно получать газонаполненные пластмассы, которые будут обладать разными свойствами.
Пластмассовые изделия обладают более высокими показателями термической устойчивости и прочности по сравнению с продукцией из полиэтилена. Газонаполненные пластмассы разделяют на поропласты (с открытыми порами) и пенопласты (с замкнутыми порами). Пенопласты являются более распространенным изделием, чем поропласты.
Производство изделий из пластмассы — видео
Производство изделий из пластмассы — формы для пластмассыВ этом видео показано изготовление и применение форм для литья изделий из пластмассы |
promplace.ru
20. Производство изделий из полимерных материалов
20.1. Способы формообразования деталей из полимеров в вязкотекучем состоянии
Полимеры и композиции на их основе разделяют на термопластичные и термореактивные.
Термопластичные полимеры (пластмассы) при нагреве приобретают пластичность, при охлаждении возвращаются в твердое состояние, повторно и неоднократно плавятся без изменения свойств. К таким полимерам относятся полиэтилен, полипропилен, винилпласт, фторопласты, полистирол, капрон и др.
Термореактивные полимеры (пластмассы) при нагревании переходят в вязкотекучее состояние, но с увеличением длительности действия повышенных температур в результате химической реакции переходят в твердое нерастворимое и неплавкое состояние. К этой группе относятся фенопласты, аминопласты, эфиропласты, эпоксипласты и др.
В зависимости от физического состояния, технологических свойств и других факторов все способы переработки пластмасс в детали наиболее целесообразно разбить на следующие основные группы:
переработка в вязкотекучем состоянии;
переработка в высокоэластичном состоянии;
получение деталей из жидких пластмасс различными способами формообразования;
переработка в твердом состоянии разделительной штамповкой;
обработка резанием;
получение неразъемных соединений сваркой, склеиванием и др.;
различные способы переработки (спекание, напыление и др.).
Основными требованиями к технологии производства изделий из пластмасс являются получение требуемой точности при оптимальной производительности и сохранение или улучшение свойств исходного материала. Это достигается как конструктивными решениями формообразующего инструмента, так и наиболее полным удалением низкомолекулярных примесей и летучих компонентов (влаги) из формуемого материала, снижением внутренних напряжений, обеспечением равномерного прогревания и наибольшей пластичности материала до заполнения им формы, а также его достаточно полным уплотнением и отвердением при формировании термореактивных материалов.
Подавляющее количество полимерных материалов перерабатывается в изделия в вязкотекучем состоянии. К этому методу обработки относятся следующие процессы:
Во всех перечисленных процессах изделия оформляются под действием тепла и давления.
Литье при атмосферном давлении. Литьем в формы получают детали различной конфигурации из термореактивных материалов на основе фенольных, акриловых, эпоксидных, полиэфирных и других смол, которые затвердевают непосредственно в формах в результате поликонденсации или полимеризации, а также остывания или затвердения растворителя.
Перед заливкой в формы фенольные и карбомидные смолы предварительно приготавливаются в реакторе, из которого они поступают в ковш. В ковше происходит перемешивание смолы с красителями и катализаторами.
Залитые формы помещаются в сушильные шкафы, где они прогреваются при температуре 80–90° С в течение длительного времени (от нескольких часов до суток и более). Этим методом из фенольных и карбомидных смол изготавливают различные плиты, блоки, фасонные детали и др.
Детали из полиметилметакрилата получают заливкой в формы метилметакрилата (мономера) с катализатором и последующим нагреванием до температуры плавления. При этом в форме протекает реакция полимеризации, и материал затвердевает. В процессе затвердевания полиметилметакрилата происходит усадка, поэтому в формах предусматриваются усадочные емкости. Если же необходимо получить изделие в виде толстых плит, то последние отливаются слоями – каждый последующий заливают после затвердения предыдущего.
Из полиакриловых смол отливают плиты, стержни, трубы, фитинги и различные прозрачные изделия для технических и бытовых нужд.
Отливки из эпоксидных и полиэфирных смол получают в формах при комнатной или слегка повышенной температуре при добавлении к исходному материалу катализаторов. Этим методом изготавливают детали сравнительно небольшой величины, часто с металлической или керамической арматурой.
Литьем получают также пленку из полихлорвинила или производных целлюлозы толщиной 0,03–0,15 мм. Для этого пластифицированный материал тонким слоем наносится на ленту транспортера или вращающийся барабан. Лента или часть барабана с нанесенной массой проходит через нагревательную камеру, в которой происходит желатинизация материала. После охлаждения пленка снимается и наматывается на барабан.
Формовое прессование. При формовом прессовании исходным материалом (смесь полимера с наполнителями, пластификаторами, стабилизаторами, красителями и т. д.) заполняется пресс-форма, а затем пуансоном производится горячее прессование.
Различают компрессионное и литьевое прессование.
При компрессионном прессовании (рис. 20.1) пресс-порошок (таблетки) 7 засыпается в матрицу 5, а затем формуется пуансоном 1. Пресс-порошок перед подачей в пресс-форму может быть предварительно нагрет.
а
б
Рис. 20.1. Схема компрессионного прессования: а – начало прессования; б – конец прессования: 1 – пуансон, 2 – сердечник, 3 – направляющие стержни, 4 – направляющие отверстия, 5 – матрица, 6 – гнездо матрицы, 7 – пресс-материал, 8 – изделие
Если изделие изготавливается из термореактивных материалов, то оно извлекается из пресс-формы вгорячую, а детали из термопластичных материалов – только после остывания. В связи с последним обстоятельством использование этого метода для переработки термопластичных материалов нецелесообразно вследствие низкой производительности.
Этим методом получают изделия средней сложности и небольших габаритов.
При литьевом прессовании (рис. 20.2) исходный материал нагревается до вязкого состояния в специальной загрузочной камере 2, откуда он под давлением пуансона 1 через отверстие в литниковой плите 3 поступает в полость матриц 5. Далее материал затвердевает и готовое изделие 4 извлекается выталкивателем.
Литьевым прессованием производят детали сложной формы, с резьбовыми отверстиями, со сложной арматурой. Но при данном способе увеличивается расход материала за счет литниковой системы и части материала, остающейся в загрузочной камере.
В зависимости от способа установки на прессах пресс-формы делятся на стационарные, съемные и сменные.
У стационарных пресс-форм матрица и пуансон закреплены соответственно на столе и ползуне пресса, у съемных – только матрица, а у сменных на столе пресса прикреплен только корпус матрицы. Формообразующая часть сменной матрицы может быть легко заменена, что позволяет быстро переналаживать пресс на изготовление различных деталей.
Рис. 20.2. Схема литьевого прессования: 1 – пуансон, 2 – загрузочная камера, 3 – литниковая плита, 4 – готовая деталь, 5 – матрица
Нагрев пресс-форм может осуществляться источником тепла, расположенным как непосредственно в пресс-форме, так и за ее пределами. Для этого используют перегретый пар с избыточным давлением 4–9 атм., горячую воду, газ, сжигаемый в камерах пресс-форм, электрический ток (сопротивление), токи высокой частоты и горячее масло. Для повышения производительности работы применяют предварительный подогрев пресс-материала электрическими, воздушными или паровыми подогревателями.
Материалами для пресс-форм служат термически упрочненные высоколегированные или инструментальные стали. Для обеспечения высокого качества поверхности формуемых изделий основные детали пресс-форм полируются и хромируются.
Для прессования используются гидравлические и механические прессы простого и двойного действия. Удельное давление прессования в зависимости от рода материала и вида изделия принимается в пределах 2000–6000 МПа.
Формование при низком давлении. Для изготовления крупногабаритных деталей из композиций на основе эпоксидных, полиэфирных и фенольных смол, способных затвердевать при невысоком нагреве и малом удельном давлении (не более 350 МПа), применяется формование при низком давлении.
В качестве пресс-материала используют обычно ткань или волокно, пропитанные смолой. При этом синтетическая смола предварительно подвергается частичной полимеризации, что при введении в нее катализаторов обусловливает сокращение процесса затвердевания до 1–2 часов.
Формы для формования изделий при низком давлении (рис. 20.3) изготавливают из гипса, бетона, дерева, полимерных материалов и легкоплавких металлов. Формующим силовым элементом является эластичный баллон из резины 1 или из полимерного материала (например, полиуретана), в который под давлением 8–12 атм. подаются воздух, вода или масло. При этом пресс-форма 3 нагревается до 80 °С. После затвердевания газ или жидкость из баллона выпускается и извлекается изделие 2.
Рис. 20.3. Прессование под низким давлением: 1 – баллон, 2 – прессуемое изделие, 3 – пресс-форма
На таком же принципе основано вакуумное формование, при котором форма с исходным материалом помещается в баллон. Затем из баллона выкачивается воздух. Под действием атмосферного давления баллон прижимает пресс-материал к форме, что способствует получению требуемой конфигурации изделия.
Плитовое прессование. Методом плитового прессования получают листы и плиты, а также детали более сложной формы (втулки подшипников скольжения, заготовки шестерен и др.) из пластиков со слоистыми или мелкокусковыми наполнителями. Слоистые пластики изготавливают с хлопчатобумажными, стекловолокнистыми, древесными, металлическими (в виде сеток) и другими армирующими наполнителями. Методом плитового прессования получают такие материалы, как текстолит (хлопчатобумажная ткань и фенолоформальдегидная смола), асботекстолит (асбестовая ткань и фенолоформадьдегидная смола), гетинакс (листовая бумага и феноло-формальдегидная смола), лигнофоль (древесно-слоистый пластик) и т. д.
Количество укладываемых листов наполнителя зависит от толщины материала и степени его уплотнения.
При изготовлении слоистых пластиков с тканевыми или бумажными наполнителями вводят до 30–55 % смолы, в древесно-слоистые пластики – от 15 до 20 %.
В зависимости от направления волокон в слоях шпона (наполнителя) различают древесно-слоистые пластики, параллельно-слоистые (волокна во всех слоях параллельны), поперечно-слоистые (волокна соседних слоев взаимно перпендикулярны), звездчатые (волокна соседних слоев расположены под углом от 15 до 45°) и упрочненные параллельно-поперечные (слои с параллельными волокнами перемежаются слоями с перпендикулярным направлением волокон).
Слоистые пластики изготавливают следующим образом. Наполнители пропитываются связующей смолой иукладываются на плиты или формы, соответствующие конфигурации требуемой детали, затем заготовки устанавливаются на пресс, нагреваются и прессуются. Температура прессования фенопластов составляет 40–200 °С, а аминопластов – 140–165 °С. Давление прессования в зависимости от вида наполнителя выбирается в пределах от 800 до 2000 МПа. Большие значения давления принимают при прессовании древесно-слоистых пластиков, меньшие – для асбестовой ткани и бумаги. Прессование материала на основе стеклоткани происходит при давлении 200—500 МПа. Время прессования составляет 4–5 часов.
Давление на прессуемый материал должно возрастать постепенно во избежание повреждения волокон и выдавливания смолы из межлистового пространства.
Прессование производится на гидравлических прессах различных конструкций. Наибольшая производительность достигается на этажных прессах, у которых на рабочих плитах одновременно устанавливается большое количество заготовок.
Литьем под давлением в основном формуются изделия из термопластичных материалов (полиэтилена, полиамидов, полистирола и его сополимеров, полихлорвинилидена и др.). Иногда его используют и для получения деталей из термореактивных материалов.
Исходный материал 2 с пластификатором загружается в бункер литьевой машины 1 (рис. 20.4), из которого он определенными дозами поступает в нагнетательный цилиндр 3. В цилиндре происходит нагрев материала нагревателями 5, расположенными по внешней его оболочке.
При помощи нагнетательного поршня 4 разогретый материал через переходник подается в пресс-форму 7. Для лучшего перемешивания и прогрева материала в нагнетательном цилиндре имеется обтекатель 6. В некоторых конструкциях литьевых машин цилиндрические обтекатели заменяют пластифицирующими втулками, которые вызывают меньше потерь давления, чем обтекатели.
Рис. 20.4. Схема термопластавтомата: 1 – бункер, 2 – исходный материал, 3 – нагнетательный цилиндр, 4 – поршень, 5 – нагреватели, 6 – обтекатель, 7 – пресс-форма, 8 – готовое изделие
Термопластичные материалы в нагнетательном цилиндре нагреваются до температуры размягчения и течения. Нагрев термореактивных материалов в нагнетательном цилиндре производится до температур, несколько меньших температур отвердения. Окончательный нагрев происходит при прохождении материала через переходник.
При конструировании пресс-форм для литья под давлением учитывается усадка материала при затвердевании. У кристаллических полимеров (полиэтилена, полиамидов и полихлорвинилидена) усадка достаточно высока, в зависимости от ориентировки кристаллов она может доходить до 2 %. Усадка аморфных материалов сравнительно невелика (0,4–0,6 %) и одинакова во всех направлениях.
Кристаллические полимеры при нагреве обладают высокой текучестью, поэтому пресс-формы должны быть плотными. Зазор по диаметру не должен превышать 0,05 мм. Высокая текучесть позволяет быстро заполнять пресс-форму.
Одним из условий качественного и высокопроизводительного литья под давлением термопластичных материалов является удаление воздуха из пресс-формы во время подачи в нее материала.
У аморфных материалов текучесть значительно ниже. Это увеличивает время заполнения пресс-формы, что позволяет более полно удалять из пресс-формы воздух, поступающий в нее с материалом.
Литьем под давлением изготавливают не только детали различной конфигурации, но и профильные заготовки, в частности, трубы. При этом применяют специальные приставные головки.
Литье под давлением осуществляется на специальных литьевых машинах с ручным, механическим, гидравлическим, пневматическим и смешанным типом привода. В работе происходят два движения: 1) ход поршня в литьевой машине, 2) открывание и закрывание пресс-формы. При смешанном типе привода открывание и закрывание пресс-формы производится вручную, а ход поршня – одним из вышеперечисленных способов.
В зависимости от способа управления литьевые машины бывают ручные, полуавтоматические и автоматические.
Экструзия. Экструзионным формованием термопластичных материалов изготавливают трубы, листы, пленки и различные профили. Этот метод основан на выдавливании полимерного материала из цилиндра (экструдера) через насадку, имеющую профильное отверстие. Насадки для производства труб имеют дорн, образующий выходное отверстие в виде кольцевой щели. Перемешивание материала в цилиндре и выдавливание его через насадку производятся шнеком или плунжером (рис. 20.5).
При работе исходный материал в виде порошка или гранул с пластификатором 2 загружается в бункер 1, из которого шнеком 3 подается к оправке 6. Шнек, вращающийся со скоростью 80–100 об/мин, перемешивает и уплотняет материал. Одновременно происходит нагрев материала от стенок цилиндра 4. Обогрев цилиндра осуществляется с помощью нагревательного элемента 5. После выхода из насадки прессованный профиль охлаждается воздухом или водой.
В зависимости от назначения и вида формуемого материала используются экструдеры с размером шнека от 9 до 400 мм с различным отношением его длины к диаметру (от 6 до 36), однозаходным и многозаходным шнеком, с постоянным и переменным шагом, с постоянной или изменяющейся глубиной нарезки.
Рис. 20.5. Схема экструзионного выдавливания: 1 – бункер, 2 – порошок, 3 – шнек, 4 – рабочий цилиндр, 5 – нагревательный элемент, 6 – оправка, 7 – готовое изделие
Имеются экструдеры, в которых не производится нагрев цилиндра. Материал в них нагревается за счет трения о стенки цилиндра, поверхности шнека, а также трения друг о друга частиц материала. Скорость вращения шнека в этом случае составляет около 1000 об/мин.
Различные профили и трубы образуются непосредственно в насадках экструдера. Для полученияпленок вводятся следующие дополнительные операции. Образовавшуюся трубу на выходе из насадки не охлаждают, а раздувают сжатым воздухом (0,2–0,3 атм.). Раздутая труба поступает в специальные валки, обжимающие цилиндрическую тонкостенную трубу в пленку требуемой толщины.
studfiles.net
7.3. Способы изготовления полимерных изделий.
КАЛАНДРИРОВАНИЕ — способ формования изделий в зазоре между двумя вращающимися валками из термопластичных композиций для получения рулонных, пленочных и листовых материалов.
ЭКСТРУЗИЯ — продавливание формовочной массы через мундштук экструдера — насадку, соответствующую профилю изделия.
Применяются шнековые экструзионные машины, в которые полимер подается в виде порошка или гранулята. В экструдере полимер нагревается до вязкотекучего состояния и выдавливается через мундштук.
Этим методом изготавливают трубы, погонажные изделия, плитки, пленки и т.д.
ЛИТЬЕ ПОД ДАВЛЕНИЕМ осуществляют при получении изделий из вязкотекучих термопластичных композиций методом инжекции. Порция расплавленной массы, полученной в литьевых машинах, под давлением впрыскивается в форму, где охлаждается и быстро затвердевает.
Этим способом получают детали для соединения труб, сифоны, облицовочные плитки.
ТЕРМОФОРМОВАНИЕ производят вакуумным и пневматическим методами.
При вакуумном термоформовании изделия получают из листовых термопластичных заготовок, которые в пластическом состоянии под влиянием вакуума принимают конфигурацию формы.
Этим методом получают крупногабаритные тонкостенные изделия сложного профиля — ванны, раковины, смывные бачки.
При пневмо формовании размягченные заготовки превращают в изделия с помощью сжатого воздуха.
ПРЕССОВАНИЕ осуществляют в обогреваемых гидравлических прессах при переработке смесей на основе термореактивных полимеров.
+ Прессованием получают древесно-волокнистые и древесно-стружечные плиты, слоистые пластики.
7.4. Основные свойства пластмасс.
7.4.1. Физические свойства.
ИСТИННАЯ ПЛОТНОСТЬ пластмасс обычно составляет 1…2 г/см, т.е. в 1,5…2 раза меньше, чем у каменных материалов.
ПОРИСТОСТЬ пластмасс регулируется в широких пределах от 0 до 95..98 %.
ВОДОПОГЛОЩЕНИЕ пластмасс обычно не более 1 %.
ВОДОСТОЙКОСТЬ пластмасс высокая.
ТЕПЛОСТОЙКОСТЬ большинства пластмасс невысокая и составляет 100…200 С, но у фторопластов и кремний-органических полимеров она достигает 300…500 С.
ТЕПЛОПРОВОДНОСТЬ пластмасс низкая ( λ = 0,23…0,7Вт/м С), у пено- и поропластов она близка к теплопроводности воздуха.
КОЭФФИЦИЕНТ ТЕПЛОВОГО РАСШИРЕНИЯ в 5…10 раз выше, чем у других материалов, поэтому при сооружении водоводов из пластмассовых труб необходимо устраивать компенсаторы в виде петель.
7.4.2. Механические свойства.
ПРОЧНОСТЬ пластмасс определяется связующим полимером и заполнителем. Например, конструкционные пластики СВАМ — стекловолокнистые анизотропные материалы на полиэфирных связующих, характеризуются высокими механическими свойствами:
Rизг = 200…500 МПа, Rсж Rраст Rизг, в то время как у каменных материалов Rраст 0,2…0,1 Rсж.
МОДУЛЬ УПРУГОСТИ пластмасс примерно в 10 раз ниже, чем у бетона и стали, поэтому им характерна высокая ползучесть и деформативность.
7.4.3. Химические и физико-химические свойства.
ХИМИЧЕСКАЯ СТОЙКОСТЬ — большинство пластмасс стойки к неорганическим кислотам и щелочам, но в органических растворителях, близких по природе полимеру, могут растворяться.
СТАРЕНИЕ — изменение структуры и состава полимера под действием света, кислорода воздуха, нагревания, при этом появляется хрупкость, исчезает эластичность, в конечном итоге наступает полное разрушение.
ВЫДЕЛЕНИЕ ТОКСИЧНЫХ ВЕЩЕСТВ происходит в результате присутствия в полимерах продуктов их деструкции, появляющихся из-за нарушения технологических режимов производства полимеров, а так же из-за вводимых в пластмассу низкомолекулярных продуктов (пластификаторы, стабилизаторы и др.) В жидком виде все полимеры токсичны.
ГОРЮЧЕСТЬ ПЛАСТМАСС связана с горючестью полимеров как органических веществ. Добавляя в пластмассы антипирены снижают их горючесть.
ОКРАШИВАЕМОСТЬ полимеров в различные цвета производится путем введения красителей в его расплав или раствор.
studfiles.net
Как производят полимеры? | Как это сделано
Для многих воронежцев не секрет, что одно из старейших предприятий города ОАО «Воронежсинтезкаучук» (ВСК) ныне является дочерним предприятием СИБУРа (крупнейший нефтехимический холдинг России). ВСК, в свою очередь, является одним из крупнейших производителей высококачественных каучуков, латексов и термоэластопластов в России. Продукция завода реализуется как на внутреннем рынке, так и за рубежом. Экспортные поставки занимают около 50% объема производимой продукции и осуществляются в Испанию, Италию, Германию, Австрию, Финляндию, Китай, Тайвань, Индонезию, США и другие страны.
В середине августа этого года на территории завода было введено в эксплуатацию новое производство современных полимерных материалов — бутадиен-стирольных термоэластопластов (ТЭПов). Это полимеры, которые используется в дорожном строительстве (добавляются в битум и способствуют увеличению срока службы дорожного полотна), при изготовлении мягких кровельных материалов, при изготовление клеев, различных пластмасс, а так же в обувной промышленности. По некоторым данным, если на вас сейчас обувь российского производства, то, скорее всего, её подошва сделана из термоэластопласта, произведенного на ВСК. Дело в том, что завод занимается производством ТЭПов с начала 90-х. Более того, ВСК является единственным производителем этой продукции в странах СНГ. До недавних пор годовой объем выпуска составлял 35 тысяч тонн в год, которых катастрофически не хватало для использования одновременно нужд РФ, стран СНГ и экспорта. После запуска нового производства общая мощность предприятия по выпуску термоэластопластов составит уже 85 тысяч тонн.
В начале сентября мне довелось погулять по новому технологическому объекту и немного пофотографировать.
Буду откровенен — химия мне в школе давалась с трудом. Хорошо помню только h3O, h3SO4 и как на практике высыпал в карман рубашки какой-то кристаллический порошок (крупинки напоминали драгоценные камни), после чего в моей рубашке «прогорела» дырка. Посему данный репортаж может содержать некоторые неточности, но желающие, надеюсь, всё же поймут основной принцип работы участка ТЭП-50. За непонятными словами типа «полимер», «катализатор», «ингибитор» и т.д., пожалуйста, обращаемся к википедии или учебнику химии.
Итак, основным исходным сырьем для производства термоэластопласта являются стирол и бутадиен. Поскольку это мономеры, чтобы получить полимер, надо химически связать между собой определенное количество мономеров. Причем не только связать, а связать в определенном количестве, соотношении и правильной пространственной ориентации. Итак, вкратце: необходимое количество мономера (стирола) помещается в специальный реактор и с помощью катализатора процесса (бутила лития) производим «сшивку» стирола.
02. На фото узел приема и приготовления катализатора – бутила лития:
Получили активный полимер стирола. В этот активный или, как говорят, «живой» полистирол добавляют необходимое количество бутадиена. Проводится вторая реакция полимеризации и образуется новый активный полимер, состоящий уже из полимерных цепей стирола и присоединенного к ним бутадиена. Это полупродукт, из которого можно будет получить термоэластопласт с нужными потребительскими свойствами. Надо только эти полимерные цепочки правильно между собой «связать». Если по длине, то получится ТЭП с линейной структурой (этот продукт необходим для улучшения качества дорог), а если их «связать» крестом, то получим ТЭП с уже разветвленной структурой. Этот продукт нужен для улучшения мастик и битумов в кровельных материалах.
03. На фото реакторы и все необходимое для процесса полимеризации оборудование:
Химический процесс полимеризации проходит с выделением большого количество тепла, а готовый продукт ТЭП физически представляет из себя твердое вещество. Одним словом, просто так синтез не проведешь. Выход из этой ситуации – провести процесс в жидкости, которая растворяет ТЭП и не мешает процессу полимеризации. Также в жидкой фазе легко отвести избыточное тепло процесса синтеза. В качестве растворителя используется смесь циклогексана и гексана.
04. Благодаря этим насосам, растворитель постоянно участвует в процессе, поступая на полимеризацию и возвращаясь обратно после водной отпарки.
05. Мой сопровождающий Роман на пути к участку подготовки мономеров и растворителей.
06. Безопасность — главное. На всякий пожарный случай по всему оборудованию установлены пожарные гидранты.
07. Заглянем на минутку в ЦПУ (Центральный пульт управления). На больших экранах выводится изображение с видеокамер, установленных, в том числе, и внутри технологических резервуаров, а сотрудницы внимательно следят за мониторами. Это распределенная система управления (РСУ). Предназначена для автоматизации контроля и управления технологическими процессами и позволяет удаленно в режиме реального времени получать информацию о технологических процессах на участках и в лабораториях производства. Непосредственно на рабочем месте оператор может визуально отслеживать изменение большинства технологических параметров, получать данные анализов, контролировать подачу требуемых компонентов для постановки синтезов, расход на колонны сушки растворителя, подачу на дегазацию и, наконец, выработку, то есть количество готовой продукции.
Но продолжаем разговор о технологическом процессе. После проведения всех стадий полимеризации получаем раствор ТЭП в растворителе. Он представляет из себя хорошо сваренный кисель: чем холоднее, тем гуще. «Кисель» собирают в больших емкостях для определения качественных показателей ТЭП.
08. В этих емкостях (4 штуки вместимостью 340 м3 каждая) после проведения полимеризации в реакторах собирается раствор ТЭП. Далее он будет проанализирован по качественным показателям и отправлен на водную отгонку растворителей из раствора.
09. Для того, что бы извлечь ТЭП в чистом виде на первом этапе применяют метод водной отгонки растворителя из раствора. На фото узел водной отгонки растворителей из раствора ТЭП.
10. Далее в аппарат с горячей водой и при активном перемешивании подают пар и раствор полимера. Растворитель испаряется и выводится из аппарата и потом повторно используется в процессе, а твердый ТЭП в виде мелких пористых хлопьев вместе с водой отправляется на установку сушки. Сначала эти хлопья задерживают на сетке как на дуршлаке. На фото как раз эта наклонная сетка типа «дуршлака»:
11. Затем мокрые хлопья отправляют в отжимные машины. Вот они на фото:
12. В них основная часть воды отжимается, а ТЭП в твердом виде и с малым содержанием воды досушивается в сушилках за счет обдува горячим воздухом. Вот так выглядят эти сушилки. Совершеннейший стимпанк, не так ли?
13. Всё. Готовый продукт получен.
14. Осталось его упаковать. Для этого применяются разные упаковочные машины – от полиэтиленовых мешков весом 15кг до больших «биг-бегов» весом в 800 кг. На фото упаковка в маленькие мешки по15 кг:
15. А это упаковка в большие биг-беги:
16. Как и любой товар, до продажи готовый ТЭП нужно где-то хранить.
17. Перемещаемся на склад. Сюда же с помощью погрузчиков перемещают и готовую продукцию.
18. Которая, кстати, уже находит своего потребителя. Первым стала компания «ТехноНИКОЛЬ». Это крупнейший производитель и поставщик кровельных, гидроизоляционных и теплоизоляционных материалов. При этом ВСК рассчитывает и на интерес к продукции со стороны дорожников. Термоэластопласты давно применяются во всем мире при производстве полимерно-битумных вяжущих (ПБВ) — одного из элементов верхнего слоя дорожного покрытия. Применение ПБВ обеспечивает увеличение межремонтных сроков службы покрытия дорог с 3–4 лет до 7–10 лет. Доля полимерно-битумных вяжущих в общем объеме потребления дорожных битумов в нашей стране за последние три года выросла с 1% до 3%, при этом она до сих пор существенно ниже, чем в других странах. Для сравнения, в Германии этот показатель превышает 30%.
19. Отгрузка потребителю.
Вот такой, вкратце, технологический процесс. Бонусом еще несколько видов производства.
20. Колонны очистки бутадиена и осушки растворителей.
Они же на титульном фото.
21. Цех выделения продукта.
22. Многие километры труб…
23. Панорама производства.
24. Вот, в целом, и всё, что касается производства ТЭП-50. Но до кучи покажу, что еще попало в поле зрения моей камеры. Административно – бытовое здание с лабораторией.
25. Наверное, самый неизвестный памятник в Воронеже — товарищу Кирову у первой проходной ВСК.
26. Сотрудница. Заметил, что на ВСК очень молодой коллектив. Особенно относительно «классических» заводов.
27. Хотя, как я уже писал выше, ВСК — одно из старейших предприятий города (основан в 1932 году под вывеской СК-2) и имеет богатейшую историю. Впрочем, об этом сегодня я писать, пожалуй, не буду. Может, в следующий раз. Тем более, что в пресс-службе мне подарили раритетную книгу о истории завода буквально с момента строительства, когда левый берег Воронежа еще представлял собой практически степь. Персональное спасибо за книгу и экскурсию руководителю отдела корпоративных коммуникаций Ксении Барыниной и инженеру-технологу производства ТЭП-50 Роману Малинову.
Источник: блог Андрея Кирнова
kak-eto-sdelano.ru
Основы производства полимерных материалов
Пластические массы
Особенности технологических процессов изготовления полимерных материалов зависят от их состава и назначения. Главными технологическими факторами являются определенные температурные и силовые, формирующие изделия, для чего применяется различное оборудование. В основном производство складывается из подготовки, дозировки и приготовления полимерных композиций, которые затем перерабатываются в изделия, и обеспечивается стабилизация их физико-механических свойств, размеров и формы.
Основные приемы переработки пластмасс: вальцевание, каландрирование, экструзия, прессование, литье, промазывание, пропитка, полив, напыление, сварка, склеивание и др.
Смешение композиций — это процесс повышения однородно
сти распределения всех ингредиентов по объему полимера иногда с дополнительным диспергированием частиц. Смешение может быть периодическим и непрерывным. Конструкция и характер работы смесителей зависят от вида смешиваемых материалов (сыпучие или пастообразные).
Рис. 14.2. Схема вальцевания: а) загрузка массы; 6) вальцевание; в) переход массы на один валок; г) срез массы |
Вальцевание — операция, при которой пластмасса формуется в зазоре между вращающимися валками (рис. 14.2). Перерабатываемая масса 2 несколько раз пропускается через зазор между валками 1 и 3, равномерно перемешивается, затем переводится на один валок и срезается ножом 4. На вальцах непрерывного действия масса не только пропускается через зазор, но и движется вдоль него, а в конце процесса срезается ножом в виде узкой непрерывной ленты.
Вальцевание позволяет доброкачественно смешивать компоненты пластмасс с целью получения однородной массы, при этом полимер, как правило, переводится в вязкотекучее состояние благодаря повышению температуры при перетирании. При многократном пропускании массы через вальцы происходит пластификация, т. е. совмещение полимера с пластификатором путем ускоренного взаимного проникновения. Вальцы позволяют перетирать и дробить компоненты пластмасс. Это обеспечивается тем, что при движении в зазоре материалы сжимаются, раздавливаются и истираются, поскольку валки могут вращаться с различной окружной скоростью.
Вальцы, на которых происходит окончательная отделка поверхности и калибровка, должны иметь гладкую полированную поверхность. По характеру работы вальцы бывают периодического и непрерывного действия, а по способу регулирования температуры — обогреваемые (паром или электричеством) и охлаждаемые (водой).
Каландрирование — процесс образования бесконечной ленты заданной толщины и ширины из размягченной полимерной смеси, однократно пропускаемой через зазор между валками.
Рис. 14.3. Схемы работы четырехвалковых каландров: а) Г-образный каландр, б) Z-образный каландр |
По числу валков каландры подразделяются на двух-, трех-, четырех — и пятивалковые. Валки могут располагаться вертикально в линию, горизонтально в линию, Г-образно, L-образно и Z-образно. Схемы работы Г-образного и Z-образного четырехвалковых каландров показаны на рис. 14.3. |
Конструкции каландров различаются в основном в зависимости от вида перерабатываемой массы — резиновых смесей или термопластов. Валки каландров изготовляют из высококачественного кокильного чугуна. Рабочую поверхность валка шлифуют и полируют до зеркального блеска. Валки обогреваются паром через внутреннюю центральную полость и периферийные каналы.
Как правило, каландрирование выполняется в комплексе с вальцеванием в одной технологической линии.
Экструзией называется операция, при которой изделиям из пластмасс придают определенный профиль путем продавливания нагретой массы через мундштук (формообразующее отверстие). Методом экструзии получают профильные (погонажные) строительные изделия, трубы, листы, пленки, линолеум, пороизол и многие другие. Размеры поперечного сечения изделий, изготовляемых методом экструзии, лежат в большом интервале: диаметр труб 05-250 мм, ширина листов и пленок 0,3-1,5 м, толщина 0,1-4 мм. Экструзионными машинами пользуются также для смешения композиций и гранулирования пластмасс. Применяются экструзионные машины двух типов: шнековые с одним или несколькими шнеками и шприц — машины. Наибольшее распространение нашли шнековые, или червячные, экструдеры (рис. 14.4). Рабочим органом машины является винт (червяк), который осуществляет перемешивание массы и продвижение ее через профилирующую головку (дорн). В машину масса подается в виде гранул, бисера или порошка. Размягчение материала происходит за счет тепла, поступающего от обогревателей, которые устанавливаются в нескольких зонах.
Обогрев J
Рис. 14.4. Схема работы экструзионной машины:
1 — загрузочный бункер; 2 — шнек; 3 — головка; 4 — калибрующая насадка; 5 — тянущее устройство; б — дорн; 7 — фильтр
SHAPE * MERGEFORMAT
Рис. 14.5. Схема штампования (пресс-формования): а) загрузка пресс-материала; 6) смыкание формы и прессование; в) выталкивание изделия; 1 — пресс-материал; 2 — обогреваемая матрица пресс — формы; 3 — обогреваемый пуансон; 4 — ползун пресса; 5 — электрообогреватель; 6 — изделие; 7 — выталкиватель
Прессованием называют способ формования изделий в обогреваемых гидравлических прессах. Различают формование в пресс — формах (рис. 14.5) — при изготовлении изделий из пресс-порошков и плоское прессование в многоэтажных прессах — при изготовлении листовых материалов, плит и панелей. Прессование применяется преимущественно при переработке термореактивных полимерных композиций (фенопласты, аминопласты и др.).
Для прессования строительных листовых материалов и панелей применяют многоэтажные гидравлические прессы усилием от 10 до 50 т, обогреваемые подогретой водой или паром. Прессование на многоэтажных прессах складывается из следующих операций: за
грузка пресса, смыкание плит, тепловая обработка под давлением, снятие давления, разгрузка. Методом плоского прессования формуют древесно-стружечные плиты, бумажные слоистые пластики, тек — столиты, древесно-слоистые пластики, трехслойные клееные панели. В пресс-формах изготовляют детали санитарно-технического и электротехнического оборудования, детали для отделки встроенного оборудования, оконные и дверные приборы, детали строительных машин и механизмов.
Вспенивание — метод изготовления пористых звукотеплоизоляционных и упругих герметизирующих пластмасс. Пористая структура пластмасс получается в результате вспенивания жидких или вязкотекучих композиций под влиянием газов, выделяющихся при реакции между компонентами или при разложении специальных добавок (порофоров) от нагревания. Вспенивание веществ — стабилизаторов пены путем нагнетания или растворения в полимере газообразных и легкоиспаряющихся веществ.
Вспенивание может происходить в замкнутом объеме под давлением и без давления, а также в открытых формах или на поверхности конструкции.
Промазыванием называется операция, при которой пластическая масса в виде раствора, дисперсии или расплава наносится на основание — бумагу, ткань, войлок, разравнивается, декоративно обрабатывается и закрепляется. Примером может служить промазной линолеум, павинол, линкруст и др. Наносимая масса разравнивается специальным ножом-раклей, регулирующим толщину слоя и степень вдавливания. Обычно основание движется, а разравнивающий нож неподвижен; регулируется лишь его наклон и зазор. Нанесенная и разровненная масса проходит обычно этап термообработки для размягчения и лучшего сцепления ее с основанием.
Пропитка состоит в окунании основы (ткани, бумаги, волокон) в пропиточный раствор с последующей сушкой. Эта операция осуществляется в пропиточных машинах вертикального и горизонтального типа. Методом пропитки получают клеящие пленки (бакелитовая), декоративные пленки (мочевино-меламиновые), а также полотнища на основе стеклянных, асбестовых и хлопчатобумажных тканей, из которых в дальнейшем получают текстолиты.
Полив — это процесс, при котором пластическая масса распределяется тонким слоем на металлической ленте или барабане и, затвердевая, снимается в виде тонкой пленки. Часто этот процесс связан с испарением растворителей. Таким путем получают, например, ацетилцеллюлозные прозрачные пленки.
Литье. Различаются два вида литья: простое в формы и под давлением. При простом литье жидкая композиция или расплав заливаются в формы и отвердевают в результате реакций полимеризации, поликонденсации или вследствие охлаждения. Примером служат отливка плиток пола из реактопластов, получение органического стекла и декоративных изделий из полиметилметакрилата. Охлаждением расплава при простом литье получают некоторые простейшие изделия из полиамидов (поликапролактама).
Литье под давлением применяется при изготовлении изделий из термопластов. Полимер нагревается до вязкотекучего состояния в нагревательном цилиндре литьевой машины (рис. 14.6) и плунжером впрыскивается в разъемную форму, охлаждаемую водой.
Давление, под которым впрыскивается расплав, может достигать 20 МПа. Таким способом изготовляют изделия из полистирола, эфиров целлюлозы, полиэтилена, полиамидов. Литье под давлением отличается быстротой цикла, при этом виде переработки операции автоматизированы.
Рис. 14.6. Схема работы машины для литья под давлением: а) плавление и пластификация массы; 1 — поршень; 2 — загрузочный бункер; 3 — обогреватели цилиндра; 4 — цилиндр; 5 — разъемная форма; б) впрыскивание массы в форму и выдержка; в) размыкание формы |
Формованием называют переработку листовых, пленочных, трубчатых пластмассовых заготовок с целью придания им более сложной формы и получения готовых изделий. Формование производят в основном при нагревании. К главным методам формования из листов относят штампование, пневмоформование и вакуум — формование (рис. 14.7).
1Ш
Рис. 14.7. Схема вакуум-формования: а) негативная форма; б) позитивная форма; в) предварительная вытяжка заготовки пуансоном; г) предварительная пневматическая вытяжка заготовки; I-1II — позиции формования; 1 — заготовка; 2 — негативная форма; 3 — стойка; 4 — зажимная рама; 5 — пуансон; 6 — позитивная форма; 7 — формовочная камера
При штамповании из листов вырезают заготовки, нагревают их, помещают в пресс-форму между матрицей и пуансоном и сжимают под давлением до 1 МПа. Таким путем изготовляют детали канализационных систем из винипласта, световые колпаки из оргстекла для покрытий промышленных зданий, профильные детали из текстоли — тов для строительных конструкций.
При пмевмо-формовании лист закрепляют по контуру матрицы и нагревают до слабого провисания. Затем нагретым воздухом, сжатым до 7-8 МПа, прижимают лист к поверхности матрицы. Разновидностью этого способа является свободное выдувание. Таким способом получают световые колпаки, емкости, кольца из полиакрилатов, детали вентиляционных систем и химически стойкой аппаратуры из поливинилхлорида.
При вакуум-формовании лист закрепляют по контуру полой формы, нагревают и создают разрежение в полости. Под влиянием атмосферного давления лист прижимается к поверхности формы. Таким путем изготовляют детали санитарно-технического оборудования из ударопрочного полистирола, полиакрилатов, виниловых полимеров.
Напыление — способ нанесения на поверхность порошкообразных полимеров, которые, расплавляясь, прилипают к ней, а при охлаждении образуют прочную пленку покрытия. Различают газопламенное, вихревое и псевдосжиженное напыление. При газопламенном напылении порошок полимера (полиэтилен, полиамид, по- ливинилбутироль), проходя через пламя, расплавляется и, падая на поверхность каплями, прилипает, образуя слой нужной толщины.
Сварка и склеивание служат для соединения заготовок из пластмасс для получения изделий заданной формы. Сварку применяют для соединения термопластических пластмасс — полиэтилена, поливинилхлорида, полиизобутилена и др. По способу нагревания с
msd.com.ua