Процесс выдувки пакетов – Технология производства пластиковых пакетов
Технология производства пластиковых пакетов
Технология производства пластиковых пакетов
Сегодня население планеты повсеместно использует огромное количество пластиковых пакетов. Известно, что ежегодно производится более 1 трлн. пакетов, которые можно встретить в разных местах и сферах деятельности человека, где они применяются в самых различных целях: от упаковки бытовой техники до переноски продуктов питания.
Полиэтилен
Пластиковые пакеты изготавливаются из полимерного вещества, известного как полиэтилен (PE) и образованного из длинных цепей атомов углерода и водорода. Структуры этих цепей могут отличаться в зависимости от того, какой тип полиэтилена нужно получить на выходе, но практически все они применяются в производстве различных типов пластиковых пакетов.
Например, HDPE представляет собой полиэтилен высокой плотности и является наиболее распространенным типом полиэтилена, используемого для создания сумок. Этот пластик создан из прямых цепочек молекул, которые очень мало ветвятся, оставаясь линейными от начала до конца. Эта линейная структура создает очень прочный материал, который выдерживает нагрузку значительной массы без разрыва. LDPE – это пластик, созданный с малой плотностью, то есть из разветвляющихся цепей полимерных материалов. Это очень легкий, почти пленочный пластик, который используется для изготовления сухих чистящих мешков, необходимых чаще всего для обертывания предметов одежды. Структура LLDPE, при сравнении с линейным полиэтиленом низкой плотности, тоже не разветвляется, но и не имеет прочности такого уровня, как HDPE. Это означает, что мешки, изготовленные из пластмасс LLDPE, должны быть более толстыми и более тяжелыми, чтобы обеспечить необходимую прочность. Сумки, используемые в магазинах одежды, являются распространенным примером мешков, изготовленных из этого вещества.
Полиэтилен является одним из самых универсальных и широко используемых термопластов в мире благодаря его отличным свойствам, таким как прочность, почти нулевое поглощение влаги, отличная химическая инертность, низкий коэффициент трения, простота обработки и др.
Экструзия
Изготовление пластикового пакета – технологический процесс, который состоит из двух основных производственных этапов.
Первый этап заключается в изготовлении полимерной пленки, и он называется – экструзия, при этом, чаще всего принято говорить о двух направлениях этой технологии: экструзия литой пленки и экструзия с выдуванием пленки.
Литые пленки используются для упаковки пищевых продуктов и текстиля, обертывания цветов, ламинирования других материалов и т.п. Как правило, процесс получения литой пленки включает операцию соэкструзии, которая представляет собой одновременную экструзию двух или более материалов из одной матрицы для образования многослойной пленки. Это связано с тем, что во многих случаях окончательное применение пластиковой пленки требует прочности, которая не может быть достигнута, если пленка состоит только из одного материала. Например, для применения в пищевой упаковке требуется использование пленок с возможностями кислородного барьера. Количество слоев, их положение в соэкструдате и их индивидуальная толщина являются переменными величинами, которые изменяются в зависимости от конкретного применения пленки.
В процессе экструзии литой пленки расплавленный полимер проходит через плоскую матрицу, чтобы принять форму плоской пленки. Матричная система состоит из матрицы и блока подачи (если это соэкструзия) или просто матрицы, если процесс основан на технологии монослойной экструзии. Процесс начинается с подачи гранул с помощью гравиметрической системы подачи на один или несколько экструдеров. Затем материалы расплавляют и смешивают с экструдерами, фильтруют и подают в матричную систему. Сразу же после выхода из матрицы расплавленное сырье поступает в охлаждающий блок, где его температура опускается при взаимодействии с холодной водой через охлаждающий валик.
В цикле получения литой пленки степень вытяжки и ориентации значительно ниже, чем в процессе выдувной пленки. Кроме того, механические свойства пленки в поперечном направлении ниже по сравнению с материалами, полученными в процессе выдувной пленки, из-за более высокого уровня ориентации, который испытывает пленка в процессе выдувания.
И так как в процессе производства пакетов чаще всего нет необходимости в использовании плотных пленок для первичного материала, то экструзия с выдуванием пленки стала наиболее распространенным процессом, с помощью которого в дальнейшем изготавливаются пленки именно для пакетов.
В такой производственной линии на начальном этапе тоже используется экструдер (несколько экструдеров), предназначенный для нагрева гранул полиэтиленового пластика до высокой температуры. Эта температура плавит и пластифицирует гранулы, и в это время расплавленный пластик подается в матрицу машины, где определяется толщина, которую должен иметь мешок.
Но далее процесс сопряжен уже с непрерывным выдуванием пластика до таких размеров, которые в несколько раз превышают первоначальный диаметр матрицы с образованием при этом тонкой трубчатой пленки. Пластиковый расплав экструдируют через матрицу вертикально снизу наверх, а воздух вводится в полученный пузырь через отверстие в середине формующей головки, чтобы наполнить объем пузыря, как воздушный шар.
Чтобы охладить пленку, поверх матрицы установлено воздушное кольцо, которое ударяет по горячей пленке воздушными потоками, поступающими через каналы от мощного вентилятора. Затем трубчатый пузырь пленки движется вверх (внутри него поддерживается постоянное атмосферное давление), и практически полностью остывает на открытом воздухе, пока не пройдет через систему прижимных валков. Последние элементы служат для того, чтобы сплющить трубку в полотно, то есть, образовать единую ленту.
Как правило, коэффициент расширения между матрицей и выдувной трубой пленки будет в 1,5-4 раза больше диаметра матрицы. Прогиб между толщиной стенки расплава и толщиной охлажденной пленки происходит как в радиальном, так и в продольном направлениях. Это легко регулируется путем изменения величин объема воздуха внутри пузыря и скорости вылета.
В автоматическую линию производства пакетов нередко внедряется машина для флексографической печати, с помощью которой пакет обретает соответствующее графическое оформление. Но, чтобы облегчить качественное прилипание красок на поверхность пленки, необходимо провести предварительную поверхностную обработку. Коронирование является наиболее часто используемым из существующих методов, который увеличивает поверхностную энергию пленки и, следовательно, ее поверхностное натяжение. Система включает в себя источник питания и станцию очистки. Источник питания преобразует мощность 50/60 Гц в гораздо более высокую частотную мощность в диапазоне от 10 до 30 кГц. Эта высокочастотная энергия подается на станцию обработки и наносится на поверхность пленки с помощью двух электродов с высоким потенциалом, а другой (низкий потенциал) наносится через воздушный зазор, который обычно составляет от 0,5 дюйма до 1 дюйма. Поверхностное натяжение на поверхности пленки увеличивается, когда возникает высокая разность потенциалов, которая ионизирует воздух.
Намоточные машины используются для преобразования экструдированной пленки в рулоны материала. Процесс наматывания должен быть таким, чтобы пленка сохраняла свои свойства и размеры, когда в дальнейшем эти рулоны разматываются и трансформируются в пакеты.
Компоненты линии не действуют сами по себе, они управляются компьютеризированной системой. Главный компьютер – это центр, который объединяет и управляет всеми компонентами линии в организованном порядке. Хорошая система управления должна обеспечивать операторам простой в эксплуатации графический интерфейс или систему мониторинга.
Основными задачами компьютера являются:
- Управление запуском, выключением и скоростью линии.
- Контроль над массой материала, подаваемой в экструдеры, а также контроль над скоростью работы экструдера, что необходимо для поддержания его постоянной пропускной способности.
- Управление всеми температурными зонами и температурами всех материалов.
- Контроль натяжение полотна.
- Хранение и анализ всех рецептур, хранение оперативных данных и управление системой сигнализации.
Формовка (конвертирование)
Непосредственное изготовление мешков, которое еще называют конвертированием, требует использования машин, которые сочетают в себе высокую производственную мощность, безопасность цикла, надежность элементов конструкции, оптимальное соотношение качества продукции с трудозатратами и эксплуатационными расходами. Машины также должны быть достаточно гибкими, чтобы адаптироваться к изменениям длины мешка, материала и типа мешка.
Машины для изготовления пакетов выпускаются в различных конфигурациях на основе типов мешков, производимых на этой технике. Цикл заключается в том, что рулон пленки разматывается в операционную зону станка, где подвергается ряду таких операций технологического деформирования, как термическая сварка, резка, высекание. Все операции выполняются в полностью автоматическом режиме и требуют вмешательства оператора только для пополнения рулонов сырья и удаления уже готовой продукции.
В секции подачи гибкая упаковочная пленка разматывается из рулона на подающем валу. Втягивающие валы используются для перемещения пленки через машину и соблюдения постоянной силы натяжения. Подача обычно пошаговая, и другие операции, такие как уплотнение и резка, выполняются при кратковременном приостановлении перемещения пленки. В секции герметизации работают терморегулируемые электрические элементы, вступающие в контакт с полотном пленки на доли секунд, за которые осуществляется сварка швов. Температура сварки и длительность процесса зависят от типа материала, и они должны поддерживаться постоянными для разных скоростей машины. Конфигурация сварочного элемента и, следовательно, формат машины зависит от типа сварки, продиктованного конструкцией мешка. В большинстве форматов машины сварка сопровождается резанием. Готовые пакеты штабелируются на приемном столе.
Машины для производства пакетов с боковой сваркой являются самым распространенным типом таких станков. Материал из двух разматывателей складывают вместе и подают в машину. Ленту обычно разрезают с помощью горячего ножа, который одновременно сваривает и режет. Пакеты герметизируются только по бокам. Дно мешка закрывается из-за операции складывания, а верхняя часть мешка может оставаться открытой или закрытой застежкой-молнией, или аналогичным креплением. Простая конфигурация этого типа машин имеет сервоприводы только для фидеров и VFD для всех других осей. В более современных версиях такого оборудования сервоприводы используются для фидеров, сварочных механизмов и штабелеров.
paketodel.ru
Экструзия при производстве пластиковых пакетов, процесс обработки
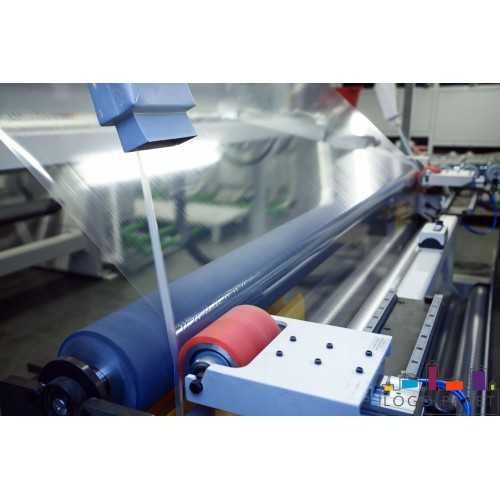
Экструзия – это изготовление полимерной пленки, заключающееся в плавлении полимера (например, полиэтилена), в результате которого он превращается в изделие заданной формы и размера, например, пакет-майка.
Применяется экструзия литой пленки и с выдуванием.
Литая пленка используется для упаковки пищевых продуктов и текстиля, обертывания цветов, ламинации других материалов и т.п. Получение литой пленки сочетается с операцией соэкструзии, представляющей собой одновременную экструзию двух и более материалов из одной матрицы для образования многослойного материала. Применение пластиковой пленки требует высокого уровня прочности. Если пленка состоит только из одного материала, то необходимой прочности невозможно достигнуть.
Процесс экструзии литой пленки заключается в прохождении расплавленного полимера через плоскую матрицу, чтобы принять нужную форму. Матричная система состоит из матрицы и блока подачи, если процесс основан на технологии соэкструзии, или обычной матрицы при монослойной экструзии. Процесс заключается в подаче гранул с применением гравиметрической системы подачи на один или несколько экструдеров. После этого материалы расплавляют, перемешивают с экструдерами, фильтруют и подают в матричную систему. После выхода из матрицы расплавленное сырье поступает в охлаждающий блок, его температура снижается при взаимодействии с холодной водой через охлаждающий валик.
При получении литой пленки степень вытяжки и ориентации ниже, чем в процессе изготовления выдувной.
При изготовлении пакетов отсутствует необходимость в применении плотных пленок для первичного материала. Экструзия с выдуванием пленки — самый распространенный процесс, с помощью которого осуществляется изготовление материала именно для пакетов.
В производственной линии на начальном этапе применяется один или несколько экструдеров для нагрева гранул полиэтиленового пластика до высокой температуры и их расплавления.
После этого осуществляется непрерывное выдувание пластика до размеров, в несколько раз превышающих первоначальный диаметр матрицы с образованием тонкой трубчатой пленки. Пластиковый расплав экструдируется через матрицу вертикально снизу наверх, а в полученный пузырь вводится воздух через отверстие в центре формующей головки для наполнения объема пузыря как воздушного шара.
Для охлаждения пленки сверху матрицы размещается воздушное кольцо, поступающее через каналы от мощного вентилятора. Трубчатый пузырь, внутри которого поддерживается постоянное атмосферное давление, передвигается вверх, остывает на открытом воздухе, затем проходит через прижимные валики, которые сплющивают трубку в полотно, образовывая единую ленту.
Коэффициент расширения между матрицей и выдувной трубой пленки в 1,5-4 раза больше диаметра матрицы.
При необходимости автоматическая линия производства пакетов оснащается машиной для флексографической печати для графического оформления упаковки. Для облегчения качественного прилипания красок на поверхность проводится предварительная поверхностная обработка. Коронирование самый распространенный метод, увеличивающий поверхностную энергию пленки и натяжение.
Намоточные машины применяются для преобразования экструдированной пленки в рулоны. Материал должен сохранять свои свойства и размеры, т.к. на следующем этапе из этих рулонов формируют пакеты.
Компонентами линии управляет компьютеризированная система.
Главный компьютер – центр, объединяющий и управляющий всеми компонентами линии в организованном порядке.
Основные задачи компьютера:
- Управление запуском, выключением и скоростью линии.
- Контроль массы материала, направляемой в экструдеры, контроль скорости работы экструдера, что важно для поддержания его постоянной пропускной способности.
- Управление температурным режимом.
- Контроль натяжения полотна.
- Хранение и анализ данных.
- Управление системой сигнализации.
Обработка пакетов после экструзии
С внешней стороны края такого рукава обрабатывает специальное устройство – коронатор, обрабатывающий поверхность рукавов коронными разрядами тока. Необходимо при последующем нанесении флексопечати.
При нанесении краски на поверхность пленки без применения коронаторов она не будет долго держаться. При обработке коронаторами между поверхностью и слоем наносимой краски возникает валентная связь, позволяющая удерживать краску в нужном месте пленки, и сохраняющая первоначально созданную форму.
logopaket.ru
Производство пакетов с вырубной ручкой
Технология производства фирменных пакетов из полиэтилена включает в себя три этапа:
- Экструзия (выдувка) полиэтиленовой пленки
- Нанесение изображения (логотипа) на полиэтиленовую основу будущего пакета
- Сборка (сварка или вырубка) готового пакета
Каждый из этих этапов имеет свои особенности, о чем мы популярно расскажем далее.
Экструзия (выдувка) полиэтиленовой пленки
Начальный этап производства пакетов – это процесс экструзии или выдувки полиэтиленовой пленки определенной толщины, размера и цвета при заданных параметрах качества. Сырьем для пленки служат полупрозрачные гранулы диаметром 5-7 мм, которые подаются на линию экструзии. После экструзии получают полиэтиленовую прозрачную пленку. Для придания цвета пленке в технологическую цепочку добавляют от 3 до 5% гранулированного суперконцентрата (красителя). Этот суперконцентрат и окрашивает полиэтиленовую пленку в любой цвет. Чаще всего пакеты окрашивают в белый цвет, порядка 80-90% от всех тиражей. Причина довольно простая — на белую основу можно нанести любое изображение любого цвета – картинка будет смотреться ярко и эстетично. Меньше заказывают и цветные пакеты – не на каждом цветном полиэтилене красиво и качественно будет смотреться изображение или логотип компании. Примечательно, что на малых производственных линиях для окраски полиэтиленовых гранул применяют мини-бетономешалки, куда добавляют суперконцентрат.
Гранулы могут быть как ПНД (полиэтилена низкого давления), так и ПВД – полиэтилена высокого давления. Но часто, и те и другие гранулы смешивают в определенной пропорции для получения заданных свойств пленки и получают полиэтилен среднего давления (ПСД) или так называемый смесовой полиэтилен. Ознакомиться с характеристиками каждого из этих видов полиэтилена можно в статье «Полиэтилен высокого давления (ПВД) и низкого давления (ПНД) – в чем отличия?».
Все компоненты – гранулы полиэтилена низкого и высокого давления, суперконцентрат-краситель – тщательно смешиваются и поступают в расплавленном виде на выдувку в экструдер. На выходе экструдера мы получаем тонкий полиэтиленовый рукав, который, еще горячим, поступает вверх, охлаждается по пути, и в форме эластичной пленки сматывается на бобины в рулоны. Таким образом мы получаем основа для изготовления пакетов, размер основы-рукава соответствует размеру заказанного пакета. Толщина и состав полученной пленки влияет на грузоподъемность, прочность на разрыв и другие характеристики будущего изделия. Например, пакеты из ПНД легко мнутся и шуршат, однако они более прочные. Пакеты из ПВД получаются более красивые, гладкие, они имеют блеск и мягкие на ощупь – из них получаются хорошие фирменные имиджевые пакеты, в них можно презентовать продукцию на выставках, дарить подарки и сувениры на различных бизнес-мероприятиях.
Следующий после экструзии подэтап в изготовлении пакетов, так называемая активация пленки – это процедура нанесения коронарного электрического заряда на поверхность пленки. Активация увеличивает впитывающие качества пленки, что значительно повышает стойкость нанесенной краски на готовом пакета.
Наконец, полиэтиленовый рукав рубится поперек, под высоту пакета, и сваривается с помощью горячих ножей. Одна сторона рубленного рукава обычно будет иметь донную складку, а на противоположной стороне сделают ручки – либо вырубкой, либо сваркой или по типу «майки». Так как со стороны ручки пакет должен раскрываться, то после процесса экструзии рукав режут пополам – получается заготовка на два пакета, или просто надрезается один край со стороны ручек. Таким образом, получается полурукав, ширина которого и будет в дальнейшем высотой пакета.
2. Нанесение изображения (логотипа) на полиэтиленовую основу будущего пакета
Для печати изображения на полиэтилене существует два способа: шелкография или трафаретная печать и флексопечать. При трафаретной печати или шелкографии, изображение наносится на готовый полиэтиленовый пакет при помощи трафарета. Это простая, почти ручная операция, она применяется на небольших тиражах пакетов – до 2-3 тысяч штук.
Что касается флексографии или флексопечати, то это автоматизированная операция для изготовления пакетов быстрыми темпами и массовыми тиражами. Флексопечать используется при тиражах от 5-10 тысяч экземпляров пакетов и более.
Далее мы расскажем о технологии флексопечати поподробнее. Первым делом, перед подготовкой к процессу печати на пакетах, изготавливаются флексоформы – это такие полимерные клише, похожие на большую печать без оснастки. Эти клише и будут печатать на полиэтиленовом полурукаве изображение, перенося на него краску с поддонов флексомашин. Изготовленный выдувкой рулон полурукава поступает во флексомашину. В машине флексоформа смачивается краской и наносит оттиск на полурукав. Само клише крепится на цилиндрическом валу и за один оборот вала поучается один оттиск одного цвета. При многоцветной печати сложного изображения полурукав пропускается последовательно через два, три, четыре и более печатных валов. Количество прохождений валов зависит от количества цветов в наносимом изображении. Периодичность повторения изображения пропорционально ширине пакета. При печати на полурукав в 50см. шириной изображение будет повторяться через каждые 40 см. Таким образом, можно получить полиэтиленовый пакет размером 50х40см., без учета донной складки.
Существуют нюансы, если, например, требуется нанести простую штриховую картинку, то печать выполняют на недорогих компактных флексомашинах. Сложные полноцветные изображения с полутонами и другими дизайнерскими особенностями печатаются на оборудовании высокого класса с большой производительностью. Такое оборудование достаточно трудоемко и сложно, оно требует особой наладки. В связи с этим, нанесение сложных полноцветных изображений на пакеты осуществляется только при средних и крупных тиражах, так как малые тиражи будут иметь высокую стоимость в расчете на один пакет.
После процесса печати, по желанию заказчика, могут проводиться некоторые дополнительные операции над пакетами. Например, ламинирование – оно придает изделию дополнительный блеск и защищает картинку от истирания. Процесс ламинирования осуществляется после печати, обычно на белом полиэтилене, когда под нагревом на изделие с изображением наносится тонкий слой прозрачного полимера. Полимером может быть лавсан, линейный ПВД или полипропилен. Стоит заметить, что технологическое выражение «печать пакетов» имеет смысл при трафаретном способе нанесения изображения, в этом случае изображение действительно печатается на пакете. При флексопечати картинка наносится не на пакет, а на рулон полиэтилена – сырье для пакетов — практически в конвейерном порядке.
3. Сборка (сварка или вырубка) готового пакета
Итак, мы получили рулон пленки с отпечатанными изображениями. Дальнейшие операции зависят от конструкции заказанного пакета. Если требуется сделать вместительный пакет для объемных вещей, то в изделии делается донная складка. Она расширяет объем пакета, и там становится возможным переносить, например, верхнюю одежду. Чтобы сделать донную складку, полиэтиленовый полурукав пропускают сквозь особый уголок. Для плоских предметов донную складку в пакете не делают.
Пакеты большой грузоподъемности изготавливают обычно из плотной и более толстой полимерной пленки. Однако в целях экономии, проще усилить ручку пакета. Такая операция проводится на одной из стадий изготовления пакета – на внутреннюю сторону будущего пакета крепится, при помощи сварки или клея, усилитель – прямоугольный кусок плотного прозрачного полиэтилена. Если усилитель приваривается, то ручка называется сварной – она более прочная, но страдает эстетическая составляющая пакета, лицевая сторона которого деформируется от нагрева. Если требуется сделать аккуратную, прочную и гладкую поверхность ручки, когда картинка занимает всю поверхность пакета, усилитель крепят при помощи клея. После крепления усилителя в полурукаве горячими ножами вырубаются отверстия-ручки. Далее рулон полурукавов режется на единичные пакеты, тут же происходит сварка боковых швов. Полностью готовые фирменные полиэтиленовые пакеты машина-автомат укладывает в пачки. Из этих пачек они фасуются вручную комплектами в коробки или мешки.
Заключение
Вы ознакомились с полной технологией изготовления фирменных полиэтиленовых пакетов. Согласитесь, ничего сложного в этом нет. Разумеется, как и на всяком производстве, в изготовлении пакетов существуют свои нюансы. Каждый этап, из описанных, имеет свои технологические изюминки – от них зависит качество изделия, от них зависит количество отбракованной продукции. Только высокопрофессиональным специалистам, с большим опытом работы на современном технологическом оборудовании, можно доверить заказ на изготовление полиэтиленовых пакетов с вашей фирменной символикой.
www.vikpack.ru
Бутылки из полимеров изготавливают методом выдувного формования двумя разными способами. В первом случае, который называют экструзией с раздувом (ЭР) (рис. 1, а), полимер расплавляют до состояния густого меда в специально подогреваемых шнековых насосах — экструдерах, выдавливают из него полый цилиндр — трубную заготовку (рис. 1, б), которая поступает в форму. Расплавленный полимер раздувается воздухом и остывает на холодных стенках пресс-формы. В другом случае — инжекционно-выдувного формования (ИВ) (рис. 1, в) — сначала методом литья под давлением изготавливают заготовку в виде пробирки — преформу. Преформу нагревают до состояния эластичной резины, помещают в пресс-форму и в резиноподобном состоянии раздувают сжатым воздухом. Далее готовое изделие остывает на холодных стенках пресс-формы. Исторически экструзионно-выдувное формование бутылок возникло раньше второго способа. Однако в последнее десятилетие метод инжекционно-выдувного формования значительно потеснил первый, и даже некоторые крупные фирмы прекратили выпуск оборудования для экструзионно-выдувного формования. Но в самое последнее время, буквально в последние год-два, наблюдается резкий рост интереса к этому методу производства пластмассовых бутылок. Статья представляет собой попытку объяснить, почему это происходит. Каковы особенности и области применения этого метода и каковы тенденции развития производства бутылок из пластмасс методом экструзионно-выдувного формования в России. Введем коэффициент капитальных затрат (ККЗ) — отношение стоимости оборудования к его часовой производительности. При близкой цене сырья и прочих равных условиях оборудование окупается тем быстрее, чем выше его производительность. Десять лет назад полиэтилентерефталат (PET) — полимер, из которого делают подавляющее количество преформ, стоил в 5 раз дороже полиэтилена, полипропилена и других полимеров, и поэтому тогда большинство бутылок из полимеров производили методом экструзионно-выдувного формования. Но именно тогда были удешевлены методы синтеза PET и построены мощные заводы по его производству. Машиностроители отреагировали мгновенно — сразу же началось производство оборудования для литья преформ и выдува бутылок из PET. Эти высокопроизводительные агрегаты способны производить до 40 тыс. преформ в час и выдувать в час до 24 тыс. бутылок. Коэффициент капитальных затрат в случае выдува бутылок из преформ стал ниже, чем ККЗ для экструзионно-выдувного формования. Четыре-пять лет назад началось интенсивное развитие производств ИВ и в России. Построено несколько мощных заводов по производству преформ. Из-за дешевизны рабочей силы в России выгодно поставить пять-шесть очень дешевых полуавтоматов для выдува, чем один дорогостоящий автомат. Поэтому быстро возникли фирмы — производители таких полуавтоматов. Крупнейшая из них — «Продвижение». Но, как правило российский потребитель приобретает один выдувной полуавтомат со средней производительностью выдува 600 бутылок в час. Эта величина соответствует средним показателям производительности экструзионно-выдувных агрегатов. По коэффициенту капитальных затрат оборудование такой мощности для ЭР проигрывает аналогичному оборудованию для ИВ в 1.5 -2 раза, но этот недостаток сторицей окупается благодаря более широким возможностям метода ЭР. Для того, чтобы аргументировать это утверждение, рассмотрим более подробно процесс выдува бутылок методом ЭР в сравнении с методом ИВ (рис. 1). Рис. 1, а. Схема экструзионно-выдувного формования: 1 — пресс-форма; 2 — трубная головка; 3 — трубная заготовка Рис. 1, б. Схема получения трубной заготовки: 1 — тело трубной головки; 2 — мундштук; 3 — дорн; 4 — трубная заготовка Рис. 1, в. Схема инжекционно-выдувного формования: 1 — пресс-форма; 2 — преформа; 3 — шток Рис. 2. Способы экструзионно-выдувного формования: а — выдув сверху; б — выдув снизу; в — выдув иглой
Источник: http://www.sabsay.ru/articles/sabsay_2000_extrusion-blow-molding.htm |
www.taraplast.ru
Изготовление полиэтиленовых пакетов: Этапы производства
Полиэтиленовые пакеты на протяжении многих лет стали незаменимым атрибутом нашей жизни. Они служат не только отличным рекламным элементов для множества компаний, но и прекрасным упаковочным материалом. Поэтому если вы находитесь на стадии выбора подрядчика по производству пакетов и хотите, чтобы ваши клиенты были довольны их качеством, очень важно понимать все тонкости процесса их изготовления. Одним из лидеров отрасли по изготовлению полиэтиленовых пакетов в Украине (Киев) является компания NEMO M.B., которая обеспечивает не только большие объемы производства за счет современных линий, но и хорошее качество продукции.
На качество полиэтиленовых пакетов может повлиять много различных факторов. Например, оборудование, первичное сырье, расходные материалы, которые используются в процессе изготовления, квалификация специалистов.
Давайте рассмотрим все этапы изготовления пакетов более детально.
Изготовление флексоформ
Согласованный с заказчиком макет логотипа или другого изображения отправляется в репроцентр. Здесь, в репроцентре, на основе специального светочувствительного полимера, будет производиться клише (флексоформа), которую в дальнейшем используют для печати пакетов. Флексоформу также еще называют печатной формой.
Это выступающие рельефные элементы на гибкой пластине.
За счет этих выступающих элементов при печати краска будет переноситься на на полиэтилен, создавая оттиск нужного изображения.
При печати пакетов используется столько флексоформ, сколько цветов хочет получить заказчик на готовой продукции. Каждому цвету будет соответствовать одно клише. Если речь идет о двусторонней печати пакетов, количество флексоформ умножается на два, так как изображение будет наносится на две стороны пакета. Соответственно и цена производства пакетов будет дороже.
Экструзия или выдувка пленки
Независимо от того, какой материал будет в дальнейшем использоваться при печати — полиэтилен высокого или низкого давления, все сырье в производство поступает в виде гранул. Для того, чтобы гранулы превратить в полиэтилен или пленку, используется экструдер (extrusion — вытеснение). Отсюда и название следующего этапа — “экструзия” — процесс переработки твердых гранул в рулоны полиэтилена под воздействием температуры. В экструдере гранулы вначале проходят через специальные отверстия, в результате чего расплавляются. В дальнейшем с расплавленной массы происходит формирование пленки нужной толщины, размеров и цветов. Эта пленка твердеет и сматывается в рулоны, на которые в дальнейшем будет наноситься изображения.
На экструдере можно получать три вида полиэтилена: рукав, полурукав и полотно. Рукав используется для производства пакетов майка, полурукав — для изготовления пакетов «банан», полотно — для технических пленок.
Нужно также отметить, что в процессе экструзии используются прозрачные гранулы полиэтилена. Чтобы на выходе получить пакету нужного цвета, в экструдер добавляется суперконцентрат — краситель нужного цвета в виде гранул.
Для того, чтобы получить качественные прочные пакеты с равномерно нанесенной краской, очень важно использовать качественные полиэтиленовые гранулы и точное экструзионное оборудование.
Нанесение изображения на пакеты
На этом этапе происходит нанесение нужного изображения или логотипа на полученные в результате экструзии рулоны с пленкой. Для печати на пакетах используются специальные печатные машины — флексомашины.
Флексомашины имеют специальный пульт управления, на котором задаются размеры будущей продукции и интервал между изображениями. Полученные в первом этапе печатные формы крепятся на печатных валах и подается заранее подготовленная краска. Как уже было указано выше, в зависимости от нужного количества цветов используется определенное количество клише.
Вырубка пакетов
После печати пленка с готовым изображением скручивается в рулон и отправляется на завершающий этап — вырубку. Рулоны пленки загружаются в специальные аппараты для резки.
В зависимости от функционала оборудования, получаем тот или иной тип продукции. На этом этапе происходит процесс вырубки, приварки, наклейки или укрепления ручек, спайки и формирование пакетов — в зависимости от исходных данных.
Современное оборудование для вырубки очень автоматизированы. Они обладают специальным сканером, что позволяет распознавать швы и отрезы и пересчитывать готовую продукцию.
pechatnick.com
Краткий экскурс в техпроцесс изготовления полиэтиленовых пакетов
Краткий экскурс в техпроцесс изготовления полиэтиленовых пакетов.
http://www.tulapack.ru/
Вы уже регулярно заказываете фирменные полиэтиленовые пакеты или только собираетесь это сделать, и Вам интересно, что остается для Вас «за кадром» — на различных стадиях производства? Мы попытались кратко и понятно описать техпроцесс.
1. Изготовление фотополимерного клише для нанесения изображения на пакет.
На первом этапе мы высылаем согласованный с Вами, проверенный и полностью подготовленный оригинал-макет в репроцентр. Там изготавливается фотополимерное клише или, как его часто называют, флексоформа. Изготавливается она из светочуствительного фотополимера и напоминает обыкновенную печать, только без оснастки. Выступающие части клише впоследствии будут переносить краску на пакет.
Количество изготавливаемых флексоформ соответствует количеству красок, наносимых на пакет. Например, при печати с цветностью 2+2 (по 2 цвета с каждой стороны пакета) необходимо изготовить 4 флексоформы. Как правило, клише изготавливается за 1 сутки, после чего оперативно попадает непосредственно на производственный участок. Этот этап мы стараемся проводить параллельно с экструзией.
2. Экструзия.
Базовым сырьем для изготовления полиэтиленовых пакетов является гранулированный полиэтилен. Изначально он представляет собой маленькие прозрачные гранулы. Экструзия – это процесс их превращения в пленку. Специальная машина – экструдер – расплавляет гранулы, после чего расплав выдувается через тонкие щели. Пока еще горячая пленка, проходя несколько метров в воздушном пространстве, охлаждается и застывает, после чего сматывается в рулон. Для того, чтобы вместо прозрачного полиэтилена «выдуть» белый или цветной, еще до расплавления в него добавляются гранулы красителя, называемого «суперконцентрат». На выходе получается полиэтиленовый «рукав» (как правило, будущая «майка), полурукав (из которого, вероятно, сделают пакет с вырубной ручкой) или полотно (возможно, будущая промупаковка) заданной толщины, ширины и цвета. Качество исходного сырья и технологичность процесса экструзии определяют прочность и равномерность окраски будущего пакета.
Подробнее об экструзии — в статье «Все начинается с экструзии»
3. Флексопечать
Здесь на первом этапе свою роль выполняет колеровщик. Его задача в том, чтобы приготовить для печати краски, точно соответствующие согласованным с Вами цветам. Краски смешиваются из большого числа компонентов, прием возможный цветовой охват значительно шире, чем при использовании стандартной офсетной полноцветной полиграфии (модели CMYK). Подбор цветов осуществляется в строгом соответствии со шкалой Pantone Formula Guide. В отличие от CMYK, здесь используется 14 базовых красок плюс металлики («золото», «серебро», «бронза» нескольких оттенков), а также флуорисцентные цвета.
Возможно, Вас это удивит, но, при изготовлении пакетов методом флексографии, печать на них наносится до того, как получится пакет в привычном виде. На этапе флексопечати вышедший из экструдера рулон полиэтиленовой пленки подается в флесомашину. Флексоформы, наклеенные на печатные валы, оставляют на пленке отпечатки с заданной периодичностью. Количество задействованных печатных валов соответствует красочности печати и количеству изготовленных флексоформ. К примеру, при печати с цветностью 2+2 (по 2 цвета с каждой стороны пакета), необходимо использовать, как минимум, четырехкрасочную флексомашину и, соответственно, 4 печатных вала. Далее отпечатанная пленка снова сматывается в рулон.
4. Вырубка, сварка, упаковка.
Далее отпечатанные рулоны пленки подаются в т.н. пакетоделательные машины. Тип машины и ее настройки соответствуют типу требуемого пакета. Здесь осуществляется сварка швов пакета, вырубка, приклейка (или приварка) ручек, формирование т.н. спаек или просто пачек пакетов. Машины обладают сканерами, которые после требуемой настройки сами анализируют изображение и определяют места, в которых должен находиться отрез, вырез или сварной шов. Пересчет пакетов также осуществляется электроникой на этой же стадии. Остается лишь аккуратно, по возможности, не сминая, свернуть пакеты и поместить их в групповую упаковку.
Качество пакетов всегда определяется характеристиками исходного сырья, возможностями и состоянием оборудования и квалификацией персонала, обслуживающего все участки производственного процесса.
Глупо было бы заявлять: «Мы изготавливаем самые качественные на свете пакеты!» В реальности, характеристики сырья и класс применяемого оборудования должны максимально четко соответствовать классу выпускаемой продукции. Стрелять из пушки по воробьям, так же, как изготавливать сравнительно низкотехнологичные пакеты, (к примеру, «майки») используя космические материалы и технологии, не рационально. Более важную роль играет количество и качество разноплановых машин и опыт работы с различными типами сырья. И здесь круг наших возможностей практически безграничен! Благо, квалификация персонала сомнений не вызывает.
Автор: © 2008 tulapack.ru
pechatnick.com
Изготовление полиэтиленовых пакетов — экскурс в техпроцесс.
Краткий экскурс в техпроцесс изготовления
Вы уже регулярно заказываете фирменные полиэтиленовые пакеты или только собираетесь это сделать, и Вам интересно, что остается для Вас «за кадром» на различных стадиях производства? Мы попытались кратко и понятно описать техпроцесс изготовления пакетов.
1. Изготовление фотополимерного клише для нанесения изображения на пакет
На первом этапе мы высылаем согласованный с Вами, проверенный и полностью подготовленный оригинал-макет в репроцентр. Там изготавливается фотополимерное клише или, как его часто называют, флексоформа. Изготавливается она из светочувствительного фотополимера и напоминает обыкновенную печать, только без оснастки. Выступающие части клише впоследствии будут переносить краску на пакет.
Количество изготавливаемых флексоформ соответствует количеству красок, наносимых на пакет. Например, при печати с цветностью 2+2 (по 2 цвета с каждой стороны пакета) необходимо изготовить 4 флексоформы.
Как правило, клише изготавливается за 1 сутки, после чего оперативно попадает непосредственно на производственный участок. Этот этап мы стараемся проводить параллельно с экструзией.
2. Экструзия
Базовым сырьем для изготовления полиэтиленовых пакетов является гранулированный полиэтилен. Изначально он представляет собой маленькие прозрачные гранулы.
Экструзия – это процесс превращения гранулированного полиэтилена в пленку. Специальная машина — экструдер – расплавляет гранулы, после чего расплав выдувается через тонкие щели. Пока еще горячая пленка, проходя несколько метров в воздушном пространстве, охлаждается и застывает, после чего сматывается в рулон.
Для того, чтобы вместо прозрачного полиэтилена «выдуть» белый или цветной, еще до расплавления в него добавляются гранулы красителя, называемого «суперконцентрат». На выходе получается полиэтиленовый «рукав» (как правило, будущая «Майка»), полурукав (из которого, вероятно, сделают пакет с вырубной ручкой) или полотно (возможно, будущая промупаковка) заданной толщины, ширины и цвета. Качество исходного сырья и технологичность процесса экструзии определяют прочность и равномерность окраски будущего пакета.
Подробнее об экструзии — в статье «Все начинается с экструзии»
3. Флексопечать
На первом этапе флексопечати важную роль выполняет колеровщик. Его задача в том, чтобы приготовить для печати краски, точно соответствующие согласованным с Вами цветам. Краски смешиваются из большого числа компонентов, причем возможный цветовой охват значительно шире, чем при использовании стандартной офсетной полноцветной полиграфии (модели CMYK). Подбор цветов осуществляется в строгом соответствии со шкалой Pantone Formula Guide. В отличие от CMYK, здесь используется 14 базовых красок плюс металлики («золото», «серебро», «бронза» нескольких оттенков), а также флуорисцентные цвета.
При изготовлении пакетов методом флексографии, печать на них наносится до того, как получится пакет в привычном виде. На этапе флексопечати вышедший из экструдера рулон полиэтиленовой пленки подается в флексомашину.
Флексоформы, наклеенные на печатные валы, оставляют на пленке отпечатки с заданной периодичностью. Количество задействованных печатных валов соответствует красочности печати и количеству изготовленных флексоформ. К примеру, при печати с цветностью 2+2 (по 2 цвета с каждой стороны пакета), необходимо использовать, как минимум, четырехкрасочную флексомашину и, соответственно, 4 печатных вала. Далее отпечатанная пленка снова сматывается в рулон.
4. Вырубка, сварка, упаковка.
После флексопечати рулоны пленки подаются в т.н. пакетоделательные машины. Тип машины и ее настройки соответствуют типу требуемого пакета. Здесь осуществляется сварка швов пакета, вырубка, приклейка (или приварка) ручек, формирование спаек или просто пачек пакетов. Машины обладают сканерами, которые после требуемой настройки сами анализируют изображение и определяют места, в которых должен находиться отрез, вырез или сварной шов. Пересчет пакетов также осуществляется электроникой на этой же стадии. Остается лишь аккуратно, по возможности, не сминая, свернуть пакеты и поместить их в групповую упаковку.
От чего зависит качество пакета?
Качество пакетов всегда определяется:
- характеристиками исходного сырья;
- возможностями и состоянием оборудования;
- квалификацией персонала, обслуживающего все участки производственного процесса.
В реальности, характеристики сырья и класс применяемого оборудования должны максимально четко соответствовать классу выпускаемой продукции. Стрелять из пушки по воробьям, так же, как изготавливать сравнительно низкотехнологичные пакеты, (к примеру, пакеты «Майка») используя космические материалы и технологии, не рационально.
Более важную роль играет количество и качество разноплановых машин и опыт работы с различными типами сырья. И здесь круг наших возможностей практически безграничен! А квалификация персонала сомнений не вызывает, убедитесь в этом сами!
© 2008 tulapack.ru
Вернуться в каталог статей Энциклопедии
Компания ТулаПак |
Мы в соцсетях: | Поделиться: | |||
звоните бесплатно: тел./факс в Москве: тел./факс в Туле: |
8 800 700-05-65 +7 (495) 960-87-78 +7 (4872) 35-87-75 |
|
www.tulapack.ru