Производство блоков: Доступ ограничен: проблема с IP
Оборудование для производства бетона, ЖБИ изделий, заводов ЖБИ, тротуарной плитки Россия
Блок-линии – это оборудование для производства бетонных блоков, брусчатки (тротуарной плитки), дымоходов. Завод по производству блоков способен производить до 2000 блоков/ч.
Линии изготавливают различные виды блоков: пустые блоки, легкие блоки, цельные блоки, изоляционные блоки, бордюрные блоки, блоки для сада.
Оборудование для производства бетонных блоков, брусчатки, тротуарной плитки, вибропрессы.
|
|
|
|
|
|
Компоненты и опции для производства блоков, брусчатки, тротуарной плитки, бордюров.
Изоляционные блоки
Изоляционные блоки состоят из двух обычных легких бетонных блока с изолирующим слоем полиуретановой пены между ними. Толщина обоих бетонных блоков и полиуретана может меняться от степени нужной изоляции.
Подробнее
Стенды
Стенды могут комбинироваться в модули так, как нужно для работы. Доступны с изолированными автоматическими воротами.
Подробнее
Все пресс-штампы делаются по заказу, поэтому изготовленный блок имеет форму, которую Вы хотите, и пресс-штамп походит к Вашей технике. Пресс-штамп состоит из скрученных коробки и деталей. Быстроизнашиваемые части легко заменить после того, как они износились. Они сделаны из закаленной стали. Закаленная сталь обеспечивает возможность долгого использования деталей.
Подробнее
Машина для укладки на поддоны
Гидравлическая автоматическая система для укладки бетонных блоков
Подробнее
Роликовый/цепной конвейер
Роликовые и цепные конвейеры для транпосртировки пустых и полных поддонов и свободных бетонных блоков, специально адаптированных для работы.
Подробнее
Производство газобетонных блоков в Нижнем Новгороде от производителя
Производственные мощности предприятия Poritep располагаются на территории небольшого города Старая Купавна, находящегося в 22 км от Москвы. Производство современных строительных материалов из газобетона осуществляется на высокотехнологичном оборудовании компании HESS AAC Systems B.V. Автоклавный газобетон изготавливается по уникальной технологии, не имеющей аналогов у других российских производителей. Все технологические процессы производства автоматизированы и контролируются специалистами с высокой квалификацией.
Технология изготовления
При производстве газобетон проходит автоклавную обработку. Перед тем как поместить «зеленый массив» в автоклавы, блоки обязательно проходят специальное разделение, то есть в автоклав поступают уже разделенные, а не слипшиеся блоки. Такой метод позволяет избежать появления сколов и трещин на готовом газобетоне.
Виды газобетонных блоков
Вы можете выбрать и купить газоблоки для устройства различных конструкций.
Для несущих стен. Газобетон высокой прочности, имеющий плотность 300, 400 и 500 кг/м
Для внутренних перегородок. Для возведения перегородок можно использовать газобетон плотностью 500 и 600 кг/м3. Длина и высота изделий составляет 600 и 250 мм соответственно, а ширина находится в диапазоне от 500 до 175 мм. Перегородки из газосиликатных блоков имеют высокие звуко- и теплоизоляционные показатели, отличаются огнестойкостью.
Для арок. Для организации арочных проемов используют газобетонные блоки плотностью 500 и 600 кг/м3. Благодаря легкости обработки блоков из газобетона можно изготавливать арки различного радиуса.
Для перемычек. Усиление оконных и дверных проемов возможно с помощью газосиликатных П-образных блоков производства компании Poritep с плотностью 500 кг/м3.
Для навесных фасадов. Для устройства вентилируемых фасадов компания Poritep осуществляет производство газобетона плотностью 600 кг/м Размеры таких газосиликатных блоков – 600х250х200–500 мм.
Преимущества газоблоков Poritep
Точность геометрии. Предельные отклонения в габаритах изделий, изготовленных на резательных линиях HESS, составляют не более +-1 мм.
Экологическая чистота. При изготовлении газобетона используются исключительно натуральные компоненты (гипс, песок, известь, цемент и вода) в соответствии с передовыми стандартами в области экологии. Компания Poritep осуществляет безотходное производство. Цикл использования газобетона позволяет применять выделяемый пар для остальных рабочих процессов производства газобетона.
Высокий уровень качества. Контроль продукции Poritep осуществляется на всех этапах ее изготовления – начиная от закупки качественного сырья и заканчивая высококачественной упаковкой. Производитель имеет собственную сертифицированную лабораторию, оснащенную современным оборудованием, для измерения и испытания газобетона Poritep.
Долгий срок службы. При соблюдении требований к возведению домов из газосиликатных блоков срок их службы превышает 100 лет даже без дополнительной облицовки фасада.
Высокая теплоизоляция. Стены зданий, построенных из газосиликатных блоков от производителя Poritep, обладают высокими способностями теплосбережения. Газобетон Poritep (плотностью 400 кг/м3 и шириной 400 мм) позволяет возводить дом в один ряд без дополнительного утепления.
Плотность (кг/м3) | 300 | 400 | 500 | |
Класс прочности | B 1,5 | В 2,5 | В 3,5 | В 5 |
Теплопроводность (Вт/м*С) | 0,08 | 0,096 | 0,12 | 0,14 |
Паропроницаемость (мг/м*ч*Па) | 0,26 | 0,23 | 0,20 | 0,16 |
Морозостойкость | F75 | F75 | F75 | F75 |
Усадка при высыхании (мм/м) | 0,24 | 0,24 | 0,24 | 0,225 |
Огнестойкость | REI 240 |
Видеоролик о производстве газобетона на нашем сайте позволит Вам получить более полное представление о работе предприятия и наших технологиях. Чтобы купить газосиликатные блоки от производителя, можно оформить заказ на сайте либо связаться с нами по телефонам в Москве: +7 (495) 660-06-50, +7 (495) 660-06-51.
Производство блоков для жилых домов откроется в поселении Внуковское — Комплекс градостроительной политики и строительства города Москвы
Индустриальный комплекс по производству блоков для жилых домов планируется построить в поселении Внуковское в 2021 году, сообщил руководитель Департамента развития новых территорий столицы Владимир Жидкин.
«Здесь будут выпускать высокотехнологичные блоки для строительства домов, в том числе по программе реновации. Проектирование комплекса начнется в конце 2019 – начале 2020 года», – сказал Владимир Жидкин.
По его словам, научно-промышленный потенциал Троицкого и Новомосковского округов (ТиНАО) невозможно представить без инновационных технопарков, кластеров, заводов и промышленных комплексов.
«В Новой Москве уже насчитывается более 60 предприятий пищевой, фармацевтической, радиоэлектронной, машиностроительной и других отраслей», – отметил Жидкин.
Самым ярким проектом он назвал Троицкий инновационный кластер, который специализируется на новых материалах, лазерных и радиационных технологиях. В кластере 65 участников: от НИИ до высокотехнологичных компаний компании малого и среднего бизнеса.
Руководитель Департамента добавил, что большую роль в укреплении производственного потенциала ТиНАО играют зарубежные инвесторы.
«Построен фармацевтический комплекс ООО «Сердикс», предприятие группы компаний Servier в России. Завод «Вика Мера» – дочернее общество немецкой компании WIKA, работающей в сфере производства средств измерения давления и температуры. К этой же категории можно отнести завод ООО «КСБ» по производству промышленных насосов и насосного оборудования – немецкого концерна KSB, а также дочернее производственное предприятие концерна VEKA AG, специализирующееся на разработке и производстве оконных и дверных систем», – рассказал руководитель Департамента.
Более 500 тыс. рабочих мест создадут в Новой Москве к 2025 году
В ТиНАО построят предприятия пищевой промышленности
Семь лет развития Новой Москвы
Завод строительных материалов «ЭКО» | Производство газобетонной, силикатной продукции и ЖБИ в Москве
В сложившихся обстоятельствах к участникам процесса предъявляются повышенные требования в части организации бизнеса. Просто строить — нынче мало. Нужно постоянно следить за инновациями, развивать производство, внедрять в него новые технологии, отвечающие темпам XXI века.
Всеми этими и многими другими необходимыми сегодня качествами лидера отрасли в полной
мере обладает Ярославский завод газобетонных блоков и строительных материалов «ЭКО». Это
единственный в области завод по производству изделий из газобетона. Но перечень
продукции выходит далеко за рамки газобетонных блоков.
В линейке компании «ЭКО» газобетонные изделия различных модификаций, товарный бетон, фундаментные блоки из тяжёлых марок бетона высокой прочности. Применение уникальных технологий и импортных производственных линий позволило наладить выпуск высококачественных армированных железобетонных изделий — свай и пустотных плит перекрытия.
Ассортимент сопутствующих товаров насчитывает десятки позиций — от серии клеев до профессионального обрабатывающего инструмента. А сервисные услуги компании обеспечат покупателям минимум хлопот.
Завод стройматериалов «ЭКО» — это история про то, что всё необходимое для строительства
можно заказать в одном месте, удачно совместив отличное качество материалов с разумной
ценой на них.
Tecolit — Производство блоков Tecolit
Производство блоков Tecolit осуществляется на современном австрийском оборудовании.
При проектировании технологической линии был использован весь передовой европейский опыт по производству блоков из арболита.
Производство блоков Tecolit состоит из следующих этапов:
- производство щепы;
- дозирование и смешение щепы, цемента, минеральных добавок и воды;
- формование в стационарных машинах и установках;
- фрезерование и калибровка изделий;
- вставка теплоизоляционных элементов.
При изготовлении используется машина WSB 1000-S, которая снабжена дополнительным оборудованием для интеграции в систему транспортировки производственных поддонов. Формование осуществляется на поддонах, которые накапливаются в элеваторе и перемещаются для сушки в камеры набора прочности с помощью фингеркара. Пакетировку осуществляет робот.
Щепа мягкой древесины, продукт отхода в деревообрабатывающей промышленности, является исходным материалом для изготовления строительного материала Tecolit. С минимальным расходом электроэнергии щепа измельчается в специальных мельницах до необходимого размера, затем смешивается с минеральными веществами, цементом и водой.
После этого из смеси щепы, цемента, добавок и воды формуются блоки. Конфигурация блоков может быть различной.
После формования блоки выдерживаются на специализированном складе, где происходит процесс гидратации цемента и одновременное испарение избыточной влаги из блока.
После сушки и набора прочности блоки подвергаются тщательной калибровке на фрезерной машине, что придает им точные геометрические размеры.
В блоки Tecolit для наружных ограждающих конструкций вводится термоизоляционный вкладыш.
Отфрезерованные блоки укладываются в штабель без использования поддонов и упаковываются для последующей реализации.
Просмотреть увеличенную карту
Производство пеноблоков в Москве, изготовление блоков на заводе
Цельный пенобетонный массивКомпания ПЕНОБЛОК.РУ в Москве специализируется на производстве сертифицированных пеноблоков, которые востребованы при строительстве различных сооружений. Мы используем при изготовлении материала только высококачественные компоненты и оборудование, поэтому даем 100% гарантию прочности выпускаемой продукции.
Сертифицированное производство пеноблоков осуществляется по специальной технологии, благодаря которой получается экологически чистый, прочный и экономичный строительный материал. При изготовлении блоков из пенобетона осуществляется постоянный контроль качества на каждом производственном этапе. Благодаря многолетнему опыту нашей компании и использованию профессиональных навыков, мы предлагаем нашим клиентам качественный и эффективный в строительстве материал.
Основные преимущества нашей продукции
Распиленный пенобетонный массивПенобетонные блоки являются наиболее востребованным строительным материалом при возведении стен малоэтажных зданий, загородных домов, коттеджей и других сооружений благодаря следующим критериям:
- невысокой стоимости;
- быстроте возведения стен;
- прочности и долговечности материала;
- хорошей тепло- и звукоизоляции;
- высокой степени огнеупорности.
Массовое производство пеноблока в нашей стране вышло на совершенно новый уровень из-за высокого спроса на него. Пенобетон обладает отличными качествами, по которым он во много раз превосходит кирпич и газобетон, при этом материал имеет меньшую стоимость. Пеноблоки долговечны в использовании и на протяжении всего периода эксплуатации не теряют своих свойств и внешнего вида, то есть материал не крошится и не впитывает влагу. Благодаря данному свойству пенобетонный блок не подвержен коррозийным процессам и воздействию грибка.
Автоматизированный процесс изготовления пеноблоков
Производство большого количества пеноблоков требует наличия специализированного автоматического оборудования, которое отвечает высоким техническим требованиям и нормам, а также соблюдения технологии на каждом этапе. Это основа для того, чтобы выпускаемая продукция имела высокие показатели качества, прочности и долговечности в эксплуатации.
Автоматика дозирования
При организации нашего производства пеноблоков мы постарались максимально исключить из процесса человеческое вмешательство, в результате чего созданы идеальные условия для ускорения изготовления продукции и сведены к минимуму возможные сбои. Весь процесс выглядит следующим образом:
- для приготовления пенобетонной смеси компоненты в автоматическом режиме подаются на терминал с автоматическим дозированием каждого компонента;
- после тщательного смешивания и заливки готовой смеси в формы большого размера они транспортируются в специальные камеры, где происходит первоначальное созревание пенобетонного массива при поддержании нужной температуры;
- готовый пенобетонный массив подается на приемную линию, где происходит автоматическое распиливание на отдельные блоки специальными станками;
- после распиливания пеноблоки проходят термовлажностную обработку в камерах для достижения максимальной прочности. Это необходимо для того, чтобы все усадочные процессы в пенобетонной смеси прошли в рамках производственного цикла. Кроме того, наличие пропарочных камер позволяет нам осуществлять производство пеноблоков круглый год;
- готовые блоки упаковываются в пленку, ставятся на поддоны и отвозятся на склад, где дополнительно выстаиваются в течение 2-х недель.
Данная технология позволяет добиться наибольшей прочности материала с максимальной точностью размеров и грубой шершавой поверхностью, что позволяет избежать использования различных растворов для лучшего «прилипания» штукатурных и плиточных растворов к пенобетонным стенам. При этом оборудование можно быстро перенастроить под любой размер блоков.
Наша компания осуществляет производство пеноблоков на высокотехнологичном современном оборудовании, в результате чего достигается высокое качество продукции.
Главные компоненты пенобетона
От качества используемых компонентов зависит качество готовых пеноблоков. В своем производстве мы используем только проверенные составляющие, а именно:
- цемент – не ниже марки М500Д0;
- вода – применяется мягкая техническая вода определенной температуры, отвечающая нормам ГОСТа;
- песок – используется кварцевый или мелкой структуры;
- пенообразователь.
youtube.com/embed/1pxAJgrGNbI» frameborder=»0″ allowfullscreen=»»/>
Пеноблоки только высокого качества
Компания ПЕНОБЛОК.РУ в производстве пеноблоков применяет только высокоэффективные и проверенные годами технологии, поэтому наша продукция всегда высокого качества, прочная и долговечная в эксплуатации. У нас можно приобрести любую партию пенобетонных блоков с доставкой до места назначения и последующей выгрузкой. Мы поможем вам выбрать, каким именно видом транспорта и какими партиями доставить продукцию, чтобы ее было легко разгрузить и сложить в отведенном месте. Мы всегда имеем на складе большое количество блоков, поэтому доставляем нашу продукцию в строго оговоренные сроки и в наиболее удобное для клиентов время.
Производство и испытания песчано-бетонных блоков
🕑 Время прочтения: 1 минута
Пескобетонные блоки и кирпичи представляют собой кладочные элементы, изготовленные из смеси цемента, песка и воды и играющие решающую роль в строительстве зданий.
Рис. 1: Весовой дозатор, используемый для измерения количества каждого материала
2. Смешивание материалов Смешивание материалов осуществляется после дозирования. Это могло быть сделано как вручную, так и механически. Первый метод используется для производства большого количества песчано-бетонных блоков. Однако последний рекомендуется, когда требуется небольшое количество блоков.Цемент и песок необходимо тщательно перемешать, а затем в смесь добавить воду.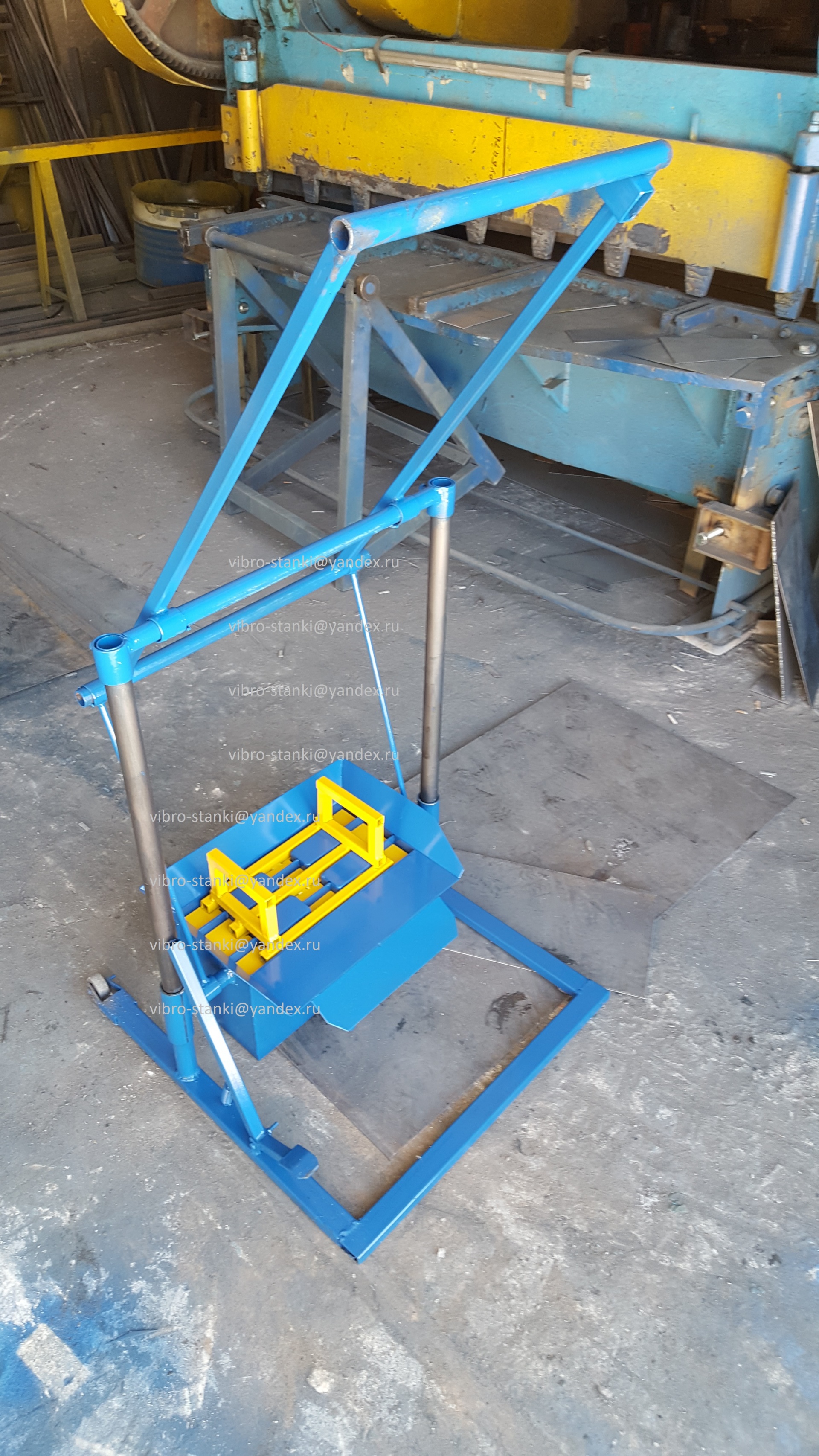
Рис. 2: Ручная формовка песчано-бетонных блоков
Рис. 3: Машинное формование песчано-бетонных блоков
4. Уплотнение После заполнения форм материал уплотняется для устранения пустот внутри смешанных материалов. Процесс уплотнения не только улучшает качество песчано-бетонных блоков, но и повышает их долговечность.
Рис. 4: Извлечение блока из формы
5. Отверждение песчано-бетонных блоков Он включает смачивание блоков водой, чтобы обеспечить надлежащую гидратацию и затвердевание и, в конечном итоге, достичь полной прочности. Обработку можно производить с помощью лейки, резинового шланга или ведра, либо разбрызгивая воду на блоки и накрывая их брезентом или влажными мешками.Рис. 5: Отверждение песчано-бетонных блоков
6.Штабелирование Это расположение блоков один на другом, готовое к продаже или использованию.Рис. 6: Сложенные блоки
Испытания песчано-бетонной составляющей Испытание мелких заполнителей Песок, используемый для производства пескобетонных блоков, должен быть чистым и не содержать вредных примесей. Поэтому необходимо провести испытания образцов, чтобы убедиться в пригодности песка перед его утилизацией.


Процесс производства бетонных блоков — BESS
Бетонный блок
Бетонный блок представляет собой блок из бетона.Для повышения качества блоков нужно применить вибрацию и усилие, чтобы раствор максимально сжался. Бетонный блок является общим названием и включает в себя различные типы блоков. Ниже вы можете увидеть несколько примеров бетонных блоков.
Пустотелые бетонные блоки различных форм и размеров.
Полнотелые бетонные блоки различных форм и размеров.
Тумбы разных форм и размеров.
Брусчатка разных форм, размеров и цветов.
Газобетонные блоки (также называемые газонными камнями).
Бетонные желоба, также известные как водосточные желоба.
Бетонные блоки Lego
Блоки из пенополистирола
Блоки пустотелых перекрытий
Во всех предметах вы можете увидеть бетон, но вы можете спросить, что такое бетон. Бетон формируется из заполнителей, воды и портландцемента, который обычно находится в виде порошка.Существуют разные стандарты соотношения смеси трех компонентов. Кроме того, доступны добавки для придания бетону дополнительных свойств.
Обратите внимание, что существует разница между добавкой и добавкой. Добавки добавляются в цемент во время производства, чтобы получить новые свойства цемента, а добавки добавляются в бетон во время смешивания, чтобы получить новые свойства.
В зависимости от вашей страны вы также можете использовать различные заполнители, наиболее распространенными заполнителями являются известняк, ракушки и мел или мергель в сочетании со сланцами, глиной, сланцем, доменным шлаком, кварцевым песком и железной рудой.Вы можете прочитать больше об этой теме в Concrete Network. Также подробнее о пустотелых бетонных блоках вы можете прочитать в нашей статье «что такое пустотелые бетонные блоки вообще и в деталях».
Процесс производства бетонных блоков состоит из различных этапов в зависимости от системы, в которой вы их производите. Процесс производства бетонных блоков может быть ручным, полуавтоматическим, автоматическим и полностью автоматическим в зависимости от ваших потребностей, страны и бюджета. Ниже вы можете прочитать о них.
1. Ручной процесс изготовления бетонных блоков:
Ручной способ самый простой и дешевый. Все, что вам нужно, это формочки. Бетон перемешивается вручную, а затем заливается в формы для бетонных блоков. Обычно при ручном способе нет вибрации и высокого давления, поэтому качество бетонных блоков низкое.
Так как раствор замешивается вручную, нельзя добиться определенного соотношения и каждый раз оно будет разным, что повлияет на качество конечного продукта.Ручной метод также слишком медленный, поскольку все операции выполняются вручную. Этот метод больше не предлагается, так как он не имеет никаких преимуществ и не является промышленным.
2. Полуавтоматический процесс производства бетонных блоков:
В полуавтоматическом процессе производства бетонных блоков вам нужна машина, которая производит блоки. Эта машина называется машиной для производства бетонных блоков, в ней установлены формы, и она производит бетонные блоки, используя давление и вибрацию в формах.Преимущества полуавтоматического процесса производства бетонных блоков заключаются в том, что качество конечного продукта выше, чем при ручном производстве, поскольку оно производится с использованием гидравлического давления и вибрации.
Недостатком этого метода является то, что процесс смешивания по-прежнему выполняется вручную, и соотношение бетона каждый раз будет разным. Кроме того, поддоны из машины доставляются ручными тележками, и для обработки производства требуется 3 рабочих, поэтому вам потребуется больше рабочих по сравнению с другими методами производства.
Если у вас ограниченный бюджет и вы живете в стране с низкой стоимостью рабочей силы и дешевыми землями, этот вариант — лучший вариант для вашего бизнеса.
3. Автоматический процесс производства бетонных блоков:
По данным нашего отдела продаж, наиболее популярным вариантом является автоматический способ изготовления бетонных блоков. Приготовление раствора в этом методе выполняется автоматически, поэтому качество вашего раствора будет одинаковым с течением времени, поскольку постоянно используется точное соотношение.Производственный процесс также осуществляется роботами, и вместо трех ручных тележек для обработки продукции используется один вилочный погрузчик. Цемент также хранится в цементном бункере и автоматически добавляется в смеситель. Таким образом, вы можете сократить количество рабочих на вашем заводе. Учтите, что в этом методе машиной управляет оператор.
4. Полностью автоматический процесс производства бетонных блоков:
Разница между автоматическим и полностью автоматическим методами заключается в том, что при автоматическом методе вам нужен оператор для управления машиной, а при полностью автоматической машине для производства бетонных блоков машина работает автоматически.Этот дизайн подходит для развитых стран, где стоимость рабочей силы высока, а земля также дорога.
Машина для производства бетонных блоков
Эти машины также называются блокирующими кирпичными машинами. На рынке доступны различные типы машин для производства бетонных блоков. Одни из них мобильные, другие стационарные. Существуют также различные уровни автоматизации для машин.
Эта статья посвящена процессу производства бетонных блоков, поэтому детали оборудования здесь не обсуждаются.Если вы хотите узнать больше о машинах для производства бетонных блоков, вы можете прочитать «Машина для производства бетонных блоков: описание и цена» или «Цена и детали машины для производства кирпича».
Учтите, что выбирать правильную машину для вашего предприятия, выбирая самую дешевую машину, совсем неразумно. Чтобы выбрать лучшую машину, необходимо учитывать техническую информацию, такую как размер поддона, гидравлическое давление, потребляемая мощность и сила вибрации. Bess предлагает вам высококачественные машины для производства бетонных блоков различной производительности и уровня автоматизации.Ниже вы можете увидеть процесс производства бетонных блоков на нашем полуавтоматическом станке. Вы можете получить доступ к большему количеству видео через наши каналы YouTube VESS machine EN и BESS machine EN.
youtube.com/embed/qctx6VdWHWM» allowfullscreen=»allowfullscreen» allow=»accelerometer; autoplay; clipboard-write; encrypted-media; gyroscope; picture-in-picture» frameborder=»0″ loading=»lazy»/>
Как производить бетонные блоки
Для производства бетонных блоков вам необходимо обеспечить завод сырьем, таким как заполнитель, вода и портландцемент. Затем вам нужно смешать их вместе, чтобы получилась однородная кремообразная смесь. Доступны различные соотношения смесей в зависимости от стандартов вашей страны и совокупной доступности.Также в зависимости от выбора машины это делается вручную или автоматически.
После того, как вы приготовите раствор, пора подавать его в машину. Обычно это делается конвейерными лентами. Потом машина позаботится обо всем остальном. раствор сначала заливается в бункер агрегата машины, затем он автоматически подает раствор в формы. Когда форма заполнена раствором, гидравлический пресс выполняет прессование. Вибрация также помогает гидравлической системе сжимать его наилучшим образом.
После того, как бетонные блоки сформированы на поверхности поддонов, машина ведет поддон к выходу машины. Теперь это зависит от вашей машины, если она полуавтоматическая, она доставляется в секцию полимеризации на ручных тележках.
Если ваша машина для производства бетонных блоков является автоматической машиной, то сначала 5 поддонов укладываются друг на друга, а затем они поднимаются вилочным погрузчиком и доставляются в секцию твердения.
Если покупка земли в вашем районе стоит слишком дорого, то лучше выбрать автоматическую систему, чтобы сэкономить землю на участке пролечки до 5 раз.
Ежедневная производительность по производству бетонных блоков
Каждый день состоит из трех смен, каждая смена длится восемь часов. Легче обсуждать мощность в каждую смену, чтобы не было путаницы.
В зависимости от производимого вами бетонного блока мощность вашего завода по производству бетонных блоков различается. Обычно мощность производства брусчатки указывается в квадратных метрах, а пустотелые блоки и полнотелые блоки описываются цифрами.Машины для производства бетонных блоков, предлагаемые Bess, могут производить 4000 штук стандартных блоков (ширина 20 см, длина 40 см, высота 20 см) или 300 квадратных метров брусчатки за восемь часов.
Заключение
Для производства бетонных блоков в соответствии с вашим рыночным спросом и местными возможностями вам необходимо выбрать подходящую машину и подходящий бизнес-план производства бетонных блоков. Инженеры Bess могут помочь вам на каждом этапе этого бизнеса.Все, что вам нужно сделать, это связаться с нами.
Инвестиционные возможности: Производство бетонных блоков
Бетонные блоки изготавливаются из литого бетона, портландцемента и заполнителя, обычно песка и мелкого гравия, для использования в строительстве.
В блоках меньшей плотности в качестве заполнителя могут использоваться промышленные отходы, в то время как легкие блоки также могут производиться с использованием газобетона.
Бетонный блок, построенный в тандеме с бетонными колоннами и временными балками и армированный арматурой, является очень распространенным строительным материалом для несущих стен зданий.
Персидская ежедневная газета Forsat-e Emrooz недавно опубликовала статью о создании завода по производству бетонных блоков и инвестиционном потенциале этого сектора в Иране.
По словам Хоссейна Акбара, председателя Ассоциации производителей и продавцов цементных изделий и металлических строительных материалов, внутренний спрос на жилье в настоящее время составляет около 1,5 млн единиц жилья в год и может еще больше возрасти в ближайшие несколько лет.
Прогнозируемый экономический рост Ирана, возможно, повысит спрос на строительные материалы, начиная от стали и заканчивая цементом.По словам промышленного эксперта, учитывая масштабность строительной отрасли, инвестиции в производство сырья с низкими капитальными затратами и сырьем с низким уровнем риска, такого как бетонные блоки, могут стать отличной возможностью.
Акбар отметил, что сектор производства бетонных блоков является одним из немногих секторов, который полностью самодостаточен с точки зрения производственного оборудования и сырья, что делает его безопасным вариантом для инвестиций.
«Для создания стандартного завода по производству бетонных блоков с производственной мощностью 3000 блоков в день требуется участок земли площадью 6000 квадратных метров, цена которого различается в зависимости от выбранной инвестором провинции», — говорит Хамед. Шарифи, полевой игрок.
Шарифи сказал, что средний первоначальный капитал, необходимый для покрытия расходов на оборудование, покупку земли и трудоустройство примерно семи сотрудников, составляет около 150 000 долларов.
«Чтобы гарантировать хорошую прибыль, производитель должен поддерживать высокое качество на протяжении всего строительного проекта, привлекать крупные строительные компании с помощью таких стимулов, как бесплатная транспортировка, и диверсифицировать портфель продукции завода, чтобы привлечь более широкий круг потребителей», — заключил он.
Испытания подтверждают преимущества переработанного стекла в производстве бетонных блоков
Шотландские производители бетонных блоков Brand & Rae нашли доказательства, которые они искали после успешных испытаний, показавших, что переработанное стекло действительно представляет собой коммерчески выгодную и экологически чистую альтернативу использованию первичных заполнителей при производстве более ценных блоков.
Компания из Файфа получила финансирование от исполнительной власти Шотландии через WRAP (Программу действий по утилизации отходов и ресурсов) для проведения промышленных испытаний на своем основном заводе в Рассел-Милл в Файфе и мобильном заводе в Бонниригге, недалеко от Эдинбурга.
Шестимесячные испытания, включающие изготовление 75 000 бетонных блоков на обоих объектах, подтвердили, что дробленое переработанное стекло можно использовать в качестве замены первичных заполнителей в производственном процессе, и в некоторых случаях блоки, содержащие переработанное стекло, работают лучше, чем обычные с точки зрения прочности и производительности в неблагоприятных погодных условиях.
В ходе испытаний на площадке Бонниригг были протестированы блоки, традиционно используемые в строительстве стандартных или пустотелых стен, произведенных на мобильной системе для производства бетонных блоков, в то время как на площадке Рассел Милл легкие блоки для окраски и кирпичной кладки были произведены на стационарной установке, что позволило сравнение двух методов.
Испытания Bonnyrigg показали, что оптимальный процент переработанного дробленого стекла вместо первичных заполнителей составляет 30%. Это процент, при котором прочность максимальна, а усадка при высыхании минимальна — чем меньше усадка при высыхании, тем меньше склонность бетонного блока к растрескиванию.
Испытания на заводе Russell пришли к выводу, что более высокий уровень замены стекла может быть достигнут на стационарной установке. Результаты показали, что по мере увеличения уровня стекла прочность изготовленных блоков улучшалась. До 80% переработанного стекла использовалось в качестве прямой альтернативы натуральным заполнителям без какого-либо вредного воздействия на производительность или обращение с ним, однако было обнаружено, что лучшим результатом для усадки при высыхании является замена стекла на 45%.
Комментируя испытания, Гэри Белл, управляющий директор Brand & Rae, сказал: «Преимущества были четко продемонстрированы благодаря большей прочности и меньшей усадке при высыхании.Мы уже начали производство в Bonnyrigg блока, содержащего 30% стекла».
Невероятная линия по производству бетонных блоков Низкая стоимость Местное послепродажное обслуживание
Повысьте производительность своего производства кирпича с помощью великолепной линии по производству бетонных блоков . Они доступны на Alibaba.com в заманчивых предложениях, которые вы не можете игнорировать. Линия по производству бетонных блоков премиум-класса обладает непревзойденными качествами, которые были достигнуты благодаря передовым технологиям и изобретениям.Они увеличивают скорость производства кирпича, следовательно, экономят время и энергию. Материалы, используемые в линии по производству бетонных блоков , являются прочными и долговечными, что обеспечивает длительный срок службы и неизменно более высокую производительность.
Существует обширная коллекция линий по производству бетонных блоков , включающая различные модели, которые учитывают различные деловые и личные требования для всех видов строительных работ. Alibaba.com стремится убедить всех покупателей, что на сайте продаются только высококачественные линии по производству бетонных блоков .Соответственно, поставщики тщательно контролируются, чтобы убедиться, что они соответствуют всем нормативным стандартам. Таким образом, покупатели всегда получают линию по производству бетонных блоков , которая выполняет и превосходит обещанное.
Благодаря непрерывному технологическому прогрессу производители внедрили изобретения, которые снижают потребление энергии на этих линиях по производству бетонных блоков . В результате вы экономите больше денег на топливе и других счетах за электроэнергию. Линия по производству бетонных блоков также оснащена исключительными характеристиками безопасности, гарантирующими, что они представляют минимальные риски, связанные с операциями. При относительно низких затратах на их приобретение и обслуживание линия по производству бетонных блоков является разумно доступной и предлагает соотношение цены и качества.
Пришло время сэкономить деньги и время, совершая покупки в Интернете на сайте Alibaba.com. Изучите различные линии по производству бетонных блоков на сайте и выберите наиболее привлекательную и подходящую для вас. Если вы ищете индивидуальную настройку в соответствии с конкретными требованиями, найдите линию по производству бетонных блоков и достигните своих целей.Откройте для себя доступное качество на сайте сегодня.
Объяснение процесса изготовления испытательных блоков Бринелля
Нам потребовались годы, чтобы разработать высоконадежный метод производства стали одинаковой твердости, и, к счастью, Foundrax имеет давние партнерские отношения с подрядчиками, которые готовы работать в соответствии с нашими строгими стандартами. «Необработанная» сталь стоит недёшево, и процесс поставки её в соответствии со спецификациями Foundrax значительно добавляет к этому ещё до того, как мы начнем «обрабатывать» блоки.
Когда я пишу это, грубый блок, который вы видите выше, только что вернулся с первой стадии процесса: термообработки. Он проржавел и отслаивается от ржавчины и прибыл в ящике со 159 почти идентичными экземплярами. Все блоки будут удалены из ящика, их поверхности будут обработаны проволочной щеткой, а их верхние грани помечены знаком «X». Маркировка помогает следующему подрядчику, чья задача состоит в том, чтобы зашлифовать всю коррозию с поверхностей блоков, при этом наиболее интенсивное шлифование выполняется на верхней поверхности, так как это будет «эталонная» поверхность.
Ящик вернётся из плуга через несколько дней. Все края блоков будут скошены (процедура, которая не является строго необходимой, но значительно способствует улучшению пользовательского опыта), а стороны очищены от поверхностных загрязнений.
Следующий этап – плоское шлифование. Менее агрессивное, чем струговое шлифование, и выполняется с гораздо более жесткими допусками, при этом остаются блоки с параллельными гранями (требование Международной организации по стандартизации) и отделка, которая уже достаточно хороша для вдавливания | блок теста Бринелля). Однако «достаточно хорошо» имеет свои недостатки для техников мастерской, поэтому мы приступаем к притирке блоков, а затем полируем их до зеркального блеска.
Сразу после полировки на верхнюю поверхность блока добавляется выгравированная лазером сетка, чтобы помочь техническим специалистам нанести на поверхность как можно больше углублений, не нарушая правила о близости углублений друг к другу.
Каждый блок будет иметь пять углублений, сделанных на его поверхности нашей «главной» машиной Бринелля, и диаметр этих углублений будет измерен фотограмметрически с точностью до субмикрона.Специальное программное обеспечение рассчитает точную твердость по среднему значению этих измерений, и будет создан соответствующий сертификат UKAS, который сопровождает блок на пути к покупателю. Блок оставит нас похожими на тот, что вверху.
В зависимости от частоты использования срок службы каждой мерки Бринелля составляет до пяти лет.
Время производства блоков — Документация Decred
Сложность Decred регулируется таким образом, что новые блоки обнаруживаются в среднем каждые пять минут. Сложность Proof-of-Work (PoW) рассчитывается на основе экспоненциально взвешенного среднего значения различий во времени предыдущих блоков, аналогично PeerCoin . Однако в Decred этот расчет также интерполируется в периоды окон сложности, подобные биткойнам.
Время между блоками можно смоделировать как процесс Пуассона ( Λ=1, k=0 ). Поскольку это частный случай события, происходящего один раз в интервале, вероятность создания блока в заданное время после того, как был произведен последний блок, можно смоделировать с помощью кумулятивной функции распределения (CDF) для экспоненциального распределения.
В таблице ниже показано процентное соотношение блоков, которые мы ожидаем найти для разных временных интервалов, а также фактические процентные значения, полученные при анализе блокчейна основной сети для 231681 блока. Например, ~18,13% блоков должны быть найдены в течение 1 минуты, ~63,21% — в течение 5 минут, ~86,47% — в течение 10 минут и т. д.
Истекший | Ожидается | Фактический |
---|---|---|
10 сек | 3.![]() | 2,30% |
30 сек | 9,52% | 8,46% |
1 мин | 18,13% | 17,81% |
2 мин | 32,97% | 33,42% |
3 мин | 45,12% | 45,54% |
4 мин | 55,07% | 55,58% |
5 мин | 63,21% | 63,74% |
6 мин | 69.88% | 70,38% |
7 мин | 75,34% | 75,74% |
10 мин | 86,47% | 86,72% |
20 мин | 98,17% | 98,09% |
30 мин | 99,75% | 99,70% |
На приведенном ниже рисунке показаны фактические значения в зависимости от CDF, используемого для получения ожидаемых процентов.
Как мы видим, фактическое распределение довольно близко к ожидаемому идеальному распределению, что показывает, что сеть работает нормально.