Производство керамзитобетонные блоки – состав, пропорции Строительство домов и конструкций из пеноблоков
Технология производства керамзитобетонных блоков
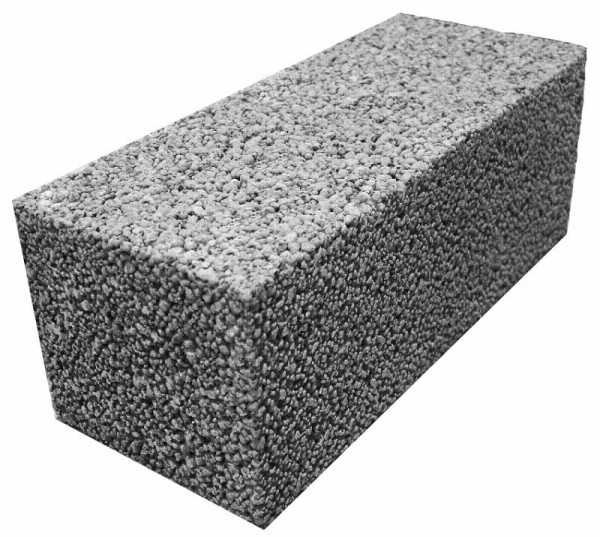
В частном строительстве домов малой этажности, довольно часто выбирают стеновые керамзитобетонные блоки, как основной материал для возведения стен. Во многом использование таких блоков является более выгодным, поскольку кермизитобетонные блоки имею несколько преимуществ перед кирпичом, связано это с тем, что для кладки керамзитобетонных блоков требуется меньше времени, меньше расход цементного раствора.
Так же керамзитобетонные блоки имеют низкую теплопроводность, благодаря которой стены имеют высокие теплоизоляционные характеристики. Учитывая все это, технология производства керамзитобетонных блоков не так сложна, как технология производства других стеновых материалов, при желании сэкономить (или заработать) их можно изготовить даже у себя на участке,необходимо лишь знать пропорции компонентов входящих в состав керамзитобетона и порядок выполнения действий. Конечно, блоки из керамзитобетона, как и почти любой строительный материал, имеют свои недостатки, о которых лучше узнать заранее.
Производство керамзитобетонных блоков
Производство керамзитобетонных для удобства разделяют на несколько шагов.
Приготовление керамзитобетонной смеси
Первым шагом является изготовление специальной керамзитобетонной смеси в бетономешалке.
Пропорции для приготовления следующие: Цемент — 1 часть, керамзит — 6 частей, 3 части песка, вода — 1 часть. Для правильного приготовления в бетономешалку в первую очередь наливают воду, после чего засыпают керамзит, после того как керамзит пропитается водой добавляют цемент и песок. Перемешивать смесь в бетономешалке следует 1.5-2 минуты, смесь должна получиться однородной.
Формовка блоков
Сушка блоков
Сушка блоков и есть самый последний шаг технологии производства керамзитобетонных блоков. После заливки блоков, необходимо дать постоять блокам как минимум одни сутки (а лучше 2е суток), после чего можно разобрать формы, и продолжить сушку блоков на открытом воздухе, укрыв их от попадания атмосферных осадков, в течении 28 дней. По истечении этого срока блоки наберут максимальную прочность, после чего можно приступать к возведению стен.
betonobeton.ru
Производство керамзитобетонных блоков своими руками: станки, оборудование (+видео)
Простота изготовления и дешевизна компонентов позволяют освоить производство керамзитобетонных блоков самостоятельно. В состав керамзитобетона входит глиняный гранулированный керамзит, который после обжига становится очень легким и прочным. К тому же гранулы керамзита обладают низкой способностью к впитыванию влаги, поэтому данный строительный материал идеально подходит для возведения стен и пола в слабо отапливаемых помещениях. Высокая теплопроводность керамзитобетона и звукоизоляция делают его востребованным материалом для строительства жилых домов и хозяйственных построек. Цена на керамзитобетонные монтажные блоки приблизительно на треть получается ниже стоимости кирпича (при равных условиях для возведения определенного типа здания).
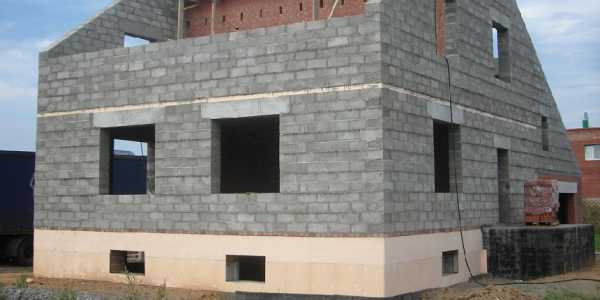
Фото: дом из керамзитобетонных блоков
Как правильно приготовить смесь для производства блоков
Чтобы приготовить керамзитобетонные блоки своими руками, необходимо знать, каким образом составляются пропорции для состава. Данный материал считается абсолютно безопасным для человека, поскольку в состав керамзитобетона входят только натуральные компоненты. Рекомендуется для изготовления использовать гранулы керамзита, не превышающие в диаметре 1 см. Этот стройматериал используют для приготовления пола в качестве утеплителя.
Простота изготовления керамзитобетонных строительных блоков открывает возможность для масштабного кустарного производства, поэтому можно сделать блоки и самому. Это связано с тем, что несоблюдение пропорций компонентов и их экономия приводит к низкому качеству готовой продукции (цена не соответствует качеству блоков). Помимо этого необходимо использовать песок с улучшенной зернистостью (обогащенный), поскольку применение речного песка может сказаться на прочности материала.
Технология приготовления рабочей смеси представляет собой смешивание всех ее компонентов в определенной последовательности и с точным соблюдением пропорций. Для этого необходимо взять:
- портландцемент (рекомендуется марка М-400), который по технологии исполняет роль связующего компонента – 1 часть;
- вода – 1 часть;
- керамзит мелкофракционный – в пропорции 8 частей;
- песок (обогащенный) – 3 части.
Чтобы приготовить керамзитобетонные блоки своими руками, необходимо знать, что 100-килограммовая приготовленная смесь может быть использована для производства 10 блоков. По ГОСТу размер керамзитобетонного блока составляет 190*390*188 мм. Вес керамзитобетонного блока может колебаться от 7 до 20 кг, в зависимости от объема пустот. В состав керамзитобетона по технологии добавляют древесную омыленную смолу, что позволяет увеличить устойчивость материала к воздействию низких температур, а также лигносульфонат для лучшей связки компонентов состава.
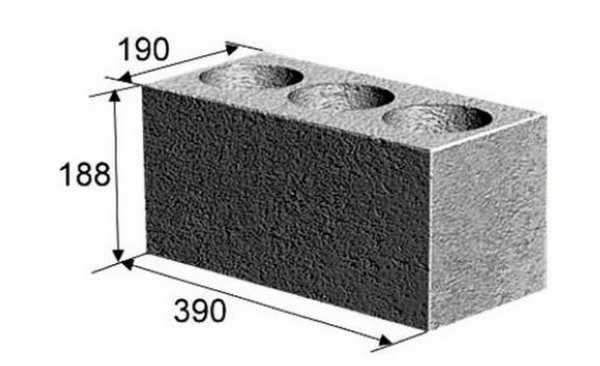
Стандартный размер керамзитобетонного блока
Совет прораба: для улучшения пластических характеристик керамзитобетонных монтажных блоков, в рабочий состав можно добавить 1 ст. ложку обычного стирального порошка.
Какое потребуется оборудование
Чтобы самостоятельно сделать керамзитобетонные монтажные блоки, потребуется использование определенного оборудования. Цена его невелика, поэтому вибрационный станок можно приобрести для личного пользования. Также можно использовать арендные станки и оборудование, цена которого обговаривается на определенный срок. Станок позволяет в специальной форме равномерно распределить массу рабочего состава для того, чтобы готовое изделие получилось максимально прочным. Есть модели, которые оснащаются пустотообразователями, благодаря которым можно приготовить полые блоки (без них получаются цельные).
Также потребуется электрическая бетономешалка, в которую необходимо в определенных пропорциях поместить все компоненты, где они тщательно перемешиваются (бетономешалку необходимо неподвижно установить на полу). Для получения блоков потребуются специальные формы, которые можно приобрести. Цена на них невысока, к тому же можно выбрать модели с различной конфигурацией полостей. Формы можно сделать и самостоятельно, для чего используются деревянные доски и жесть.
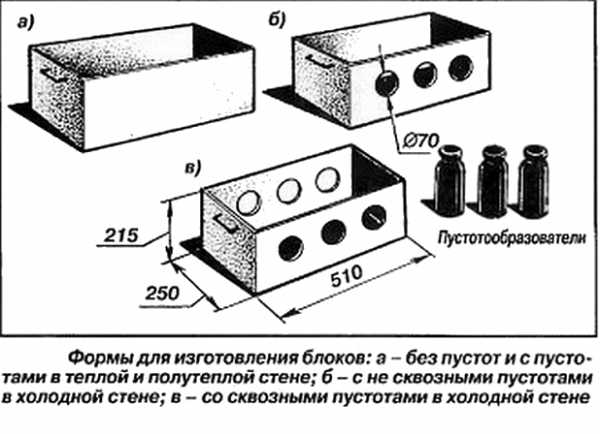
Изготовление формы для керамзитобетонных блоков
Совет прораба: покупки оборудования можно избежать. Для этого производится ручное замешивание рабочей смеси с обязательным соблюдением пропорций. Можно обойтись и без вибростанка, для чего залитый состав тщательно утрамбовывают, а затем выравнивают по границе формы. Более подробную информацию о ручном производстве блоков можно посмотреть в видео.
Особенности технологии самостоятельного приготовления керамзитобетона
Наверняка Вы неоднократно задумывались над тем, для чего нужны пустоты внутри керамзитобетонных монтажных блоков. Несложно догадаться, что в первую очередь они необходимы для существенного снижения веса изделия. К тому же пустоты при кладке образуют так называемые воздушные колодцы, которые уменьшают теплопроводность.
Рекомендуется тщательно перемешивать раствор до тех пор, пока не получится мягкая пластическая масса. После ее приготовления можно приступать к заполнению форм, в которых раствор будет застывать в течение 24 часов. Полное время застывания блоков составляет 3 недели (28 дней). Спустя сутки после застывания блоки укладывают на поддонах на поверхности пола.
Нельзя допускать прямого попадания лучей солнечного света на готовые изделия. Поэтому в период полного застывания рекомендуется сложенные на полу блоки периодически поливать водой, а затем укрывать полиэтиленовой пленкой. Использовать готовые изделия можно будет спустя месяц, когда цемент полностью наберет свою крепость.
Видео
Производство керамзитобетона
Московский институт коммунального хозяйства и строительства
филиал в г. Люберцы
Кафедра «Вяжущие материалы и бетоны».
Курсовая работа
по предмету
«Технологии производства стройматериалов»
Выполнила:
студентка 3 курса
33 ЭУП-05-037л
Яруллина Г.Р.
Проверил:
доцент
Филимонова Т.И.
Люберцы 2008
ВВЕДЕНИЕ
Преимущественное производство мелких стеновых блоков в нашей стране в последние десятилетия было обусловлено простотой и технологичностью их конструктивного решения, низкой трудоемкостью производства. Распространению этой конструкции в определенной степени способствовал ограниченный объем производства высокоэффективных теплоизоляционных материалов.
Развитие рыночных отношений в экономике страны вызвало резкий рост цен на энергоносители. В связи с этим встала задача экономии энергоресурсов, в том числе и снижения энергозатрат при эксплуатации зданий. Для ее решения в Казахстана введены в действие Изменения № 3 к СНиП II-3-79* «Строительная теплотехника», которыми нормативное сопротивление теплопередаче стен с 2000 г. увеличивается примерно в 3,3-3,4 раза с целью довести нормы требования к теплозащите стен до уровня норм стран Северной Европы. Планируемая экономия тепла от этих мероприятий должна составить 20-35 %.
Преимущественное производство керамзитобетонных мелких стеновых блоков в нашей стране в последние десятилетия было обусловлено простотой и технологичностью их конструктивного решения, низкой трудоемкостью производства. Распространению этой конструкции в определенной степени способствовал ограниченный объем производства высокоэффективных теплоизоляционных материалов.
1. КЕРАМЗИТОБЕТОН
Представляет собой легкий бетон, в котором заполнителем является керамзит — ячеистый материал в виде гранул. Керамзит производится на крупных предприятиях и занимает ведущее место в применении твердых пористых заполнителей. Керамзитобетон приобрел распространение в Казахстане более 60 лет назад и уже успел пройти проверку временем в наших климатических условиях. Изделия из керамзитобетона используются в качестве несущих конструкций в жилищном и промышленном строительстве. Керамзит, кроме того, используют как заполнитель и теплоизоляционный материал.
Объемный вес керамзитобетона высоких марок примерно в 1,5 раза меньше, чем тяжелого. Таким образом, применение керамзитобетона позволяет снизить вес зданий и конструкций до 30%. У керамзитобетона принципиально выше показатели по морозостойкости, прочности и долговечности по сравнению с другими ячеистыми бетонами. При этом несколько хуже показатели по теплопроводности. Этот недостаток зарубежные строители восполняют применением многослойных технологий при возведении стеновых панелей. Керамзитобетон по сравнению с тяжелыми бетонами обладает высокой пористостью, его нельзя разрезать пилой. Этот, по мнению строителей малоэтажных домов, «недостаток» превращается в преимущество уже при эксплуатации зданий: всевозможный крепеж в таких стенах держится прочнее. Керамзитобетон пользуется большой популярностью в Германии, Голландии, Финляндии, Норвегии, Чехии. Причем блоки керамзитобетона называют «биоблоками», поскольку в качестве исходного сырья используются только природные компоненты (суглинки, вспученная и обожженная глина).
1.1 Номенклатура
По своему назначению и физико-техническим свойствам керамзитобетон разделяется на теплоизоляционный, теплоизоляционно-конструктивный и конструктивный.
Теплоизоляционный керамзитобетон в сухом состоянии имеет объемный вес 300— 900 кг/м3 и коэффициент теплопроводности до 0,2 ккал/м•ч•град.
К теплоизоляционному керамзитобетону не предъявляются требования высокой прочности и его низкий объемный вес целиком зависит от качества керамзита.
Для получения теплоизоляционного керамзитобетона с малым объемным весом можно использовать керамзит наиболее крупных и легких фракций (20—40 мм и более), обжигаемый по специальному режиму, обеспечивающему усиленное вспучивание гранул и образование крупных пор. Объемный вес такого керамзита достигает 150—200 кг/м3 . Из него получают крупнопористый керамзитобетон с объемным весом 350—400 кг/м3 и пределом прочности при сжатии до 10 кГ/см2 .
Теплоизоляционно-конструктивный керамзитобетон имеет марки 35, 50, 75, и объемный вес его колеблется от 700 до 1 400 кг/м3 .
Повышенная прочность по сравнению с теплоизоляционным керамзитобетоном при невысоком коэффициенте теплопроводности (до 0,5 ккал/м•ч•град) позволяет применять этот керамзитобетон в ограждающих конструкциях зданий. Однако к нему предъявляются требования морозостойкости (до 25 циклов замораживания и оттаивания для зданий I категории — см. главы СНиП П-А.1.1, И.Б.2.2, II-B.4, СН 35-68). ГОСТ 11024-64 на керамзитобетонные панели нормирует морозостойкость керамзитобетона, которая должна быть для наружных стеновых панелей не ниже Мрз 25, для цокольных панелей — не ниже Мрз 35.
Конструктивный керамзитобетон имеет высокую прочность и сравнительно небольшой объемный вес и применяется в сооружениях, в которых необходимо облегчить несущую конструкцию. Его объемный вес до 1 700 кг/м, прочность при сжатии до 400 кГ/см2 .
Конструктивный керамзитобетон может быть армирован обычной или предварительно напряженной арматурой (в последнем случае марка керамзитобетона не должна быть менее 200). Для изготовления стеновых панелей конструктивный керамзитобетон не применяется.
1.2 СТРУКТУРА
По структуре (степени пористости) бетона различают плотный, крупнопористый (беспесчаный) и поризованный керамзитобетон.
Для повышения прочности и модуля упругости керамзитобетона в керамзитобетонную, смесь добавляют кварцевый песок.
В ряде случаев в последнее время изготовляют керамзитобетон из керамзитного крупного заполнителя (гравия) и кварцевого песка без добавок керамзитового песка.
В качестве вяжущего в керамзитобетоне применяется преимущественно портландцемент марки не ниже 400 с наименьшим количеством пуццоланизирующих добавок, без пластификаторов. Возможность применения пуццолановых и шлакопортландцементов, должна устанавливаться опытным путем для каждого материала в связи с тем, что в дробленом керамзите содержится значительное количество пыли, повышенное содержание которой как гидравлической добавки может снизить воздухостойкость и водостойкость, бетона.
Увеличение расхода цемента в керамзитобетоне приводит к повышению прочности, но одновременно к увеличению объемного веса керамзитобетона. Таким образом, сокращение (до определенных пределов) расхода цемента для керамзитобетона является средством снижения его объемного веса. Это определяет необходимость применения для керамзитобетона портландцемента марки не ниже 400.
Пластифицированный ССБ цемент использовать не следует, так как при этом снижается прочность бетона в раннем возрасте. Целесообразно применять гидрофобный цемент, снижающий водопоглощение бетона. В керамзитобетонах, подвергающихся тепловой обработке, желательно применять алитовые цементы (содержащие трехкальциевого силиката не менее 45%) с содержанием трехкальциевого алюмината 10—12%.
Марка бетона и объемный вес не полностью характеризуют свойства керамзитобетона. В зависимости от зернового состава, его структуры изменяются свойства ‘бетона: керамзитобетон может быть крупнопористый, с межзерновой пористостью, умеренно плотный и плотный.
Керамзитобетон с межзерновой пустотностью (М/М + К=0,2) имеет меньшую прочность при растяжении, чем крупнозернистый бетон, из-за меньшего расхода цемента по сравнению с крупнозернистым бетоном при наличии большой межзерновой пустотности.
Увеличение объема растворной части бетона приводит к повышению его пластичности, при растяжении, от чего увеличивается отношение RpM/Rp.
Исключение межзерновой пустотности при минимальных расходах керамзитового песка и цемента (М/М + К—Q,3) обеспечивает максимальную прочность при растяжении на изгиб.
Дальнейшее увеличение показателя М/М + + К приводит к уменьшению прочности как при осевом растяжении, так и при изгибе.
Объемный вес керамзитобетона в зависимости от изменения содержания керамзитового песка имеет минимум при полном заполнении межзернового пространства гравия растворной частью.
Мелкозернистый керамзитобетон имеет такое же значение коэффициента теплопроводности, что и крупнозернистый, несмотря на то, что объемный вес его больше на 24%.
Обеспечивая на производстве целенаправленную и однородную структуру керамзитобетона, можно резко повысить эксплуатационные качества ограждающих конструкций и снизить их стоимость.
Необходимость снижения веса керамзитобетонных конструкций требует назначения минимально допустимых прочностных показателей. Поэтому на производстве должно уделяться серьезное внимание соблюдению всех требуемых параметров керамзитобетона.
Принципы подбора состава и основные правила приготовления керамзитобетона аналогичны изложенным выше общим положениям по легким бетонам.
При назначении объемного веса керамзитобетона надо учитывать, что влажность его в производственных условиях 12%, а равновесная эксплуатационная влажность 5—7% (ГОСТ 11024-64).
Бетонная смесь должна иметь требуемую удобоукладываемость при минимальном расходе воды. Для уменьшения расхода воды, улучшения формовочных свойств бетонной смеси (повышения связности и начальной структурной прочности), а также комплексного улучшения свойств затвердевшего бетона (уменьшения усадки, повышения водостойкости, морозостойкости, трещиностойкости и др.) рекомендуется вводить с водой затворения в небольших количествах добавки (0,1—0,2%) от вeca цемента гидрофобизующих кремнийорганических жидкостей.
mirznanii.com
Бизнес на производстве керамзитобетонных блоков. Специфика и тонкости.
Керамзитобетонные блоки являются экологически чистым строительным материалом, так как для их изготовления используются натуральные компоненты – цемент, песок и керамзит.
Применение керамзитобетонных блоков для выкладки стен зачастую превышает случаи использования керамического кирпича, потому как последний уступает керамзитоблокам по своим эксплуатационным свойствам.
В частности, основные преимущества керамзитоблоков заключаются в легкости и, как следствие, возможности снизить вес конструкции на 40% по сравнению с кирпичной кладкой, в отсутствии усадки и трещин, неплохих показателях по морозостойкости, в хорошей теплоизоляции, более доступной цене.
Небольшие габариты (каждый блок по стандарту имеет размер 19х19х39 см) и вес обеспечивают удобство и экономию при транспортировке и хранении, простота в укладке не требует дополнительных приспособлений.
Этими факторами обусловлено широкое применение керамзитобетонных блоков при малоэтажном и бескаркасном строительстве, при выкладке плит перекрытий в не отапливаемых помещениях, в сельском хозяйстве, судостроении, постройках в шахтах, в качестве опор для ЛЭП.
Для воплощения бизнес-идеи по выпуску керамзитобетонных блоков в жизнь потребуется небольшой стартовый капитал, сам же технологический процесс достаточно прост.
Конкуренция в данном сегменте пока совсем невысока, а продукция, уже представленная на рынке, часто не отличается хорошим качеством, поскольку многие недобросовестные производители, пытаясь снизить себестоимость, используют несоответствующие стандарту материалы, к примеру, не кварцевый или обогащенный песок, а дешевый речной или карьерный, что существенно влияет на прочность и эксплуатационные свойства изделия.
Кроме того, важно, чтобы используемое для производства сырье не содержало радионуклидов, поэтому к выбору поставщика материалов нужно отнестись со всей серьезностью. Выпуск качественных керамзитных блоков обеспечит успех бизнесу, устойчивый спрос и высокую прибыль.
Пройдемся немного по цифрам.
Стоимость сырья
Мешок цемента марки М400/М 500 – 6,5-6,9 $;
Песок – 6 у.е. за 1 тонну;
Керамзит – 30 долларов за 1 куб. м.;
Вода – согласно действующему тарифу.
Соблюдение пропорций, регламентируемых в ГОСТе и технических условиях, обязательно для получения качественных, прочных блоков.
Технология изготовления
Где взять деньги для начала собственного бизнеса? Именно с этой проблемой сталкивается 95% начинающих предпринимателей! В статье «Где взять деньги на бизнес» мы раскрыли самые актуальные способы получения стартового капитала для предпринимателя. Так же рекомендуем внимательно изучить результаты нашего эксперимента в биржевом заработке: «посмотреть результаты эксперимента»
Керамзитобетонные блоки получают методом объемного вибропрессования. Технологический процесс состоит из 4 основных этапов: подготовка смеси, формовка, передача на обработку вибропрессом, просушка.
Перечень оборудования и его стоимость
Основной компонент – вибропрессовочная установка. Для выполнения крупнообъемных заказов рациональнее приобрести сразу мощное оборудование, позволяющее выпускать до 800 единиц блоков за смену. Такой вибропресс обойдется в сумму минимум 2000 долларов, представляет собой аппарат габаритными размерами 2,5 на 1,5 м, позволяет производить как керамзито-, так и бетонные, и шлакоблоки.
Помимо вибропессовочной установки потребуется вибростол — от 930 у.е., бетономешалка – 3 125 $, формовочные поддоны в количестве 3 штуки – 100 долларов/шт., гидростанция – от 3 100 у.е.
Для обслуживания оборудования необходимо нанять 2-3 человек.
В продаже представлены и полностью укомплектованные готовые автоматические линии для производства керамзитобетонных блоков. Стоимость такой конвейерной установки составляет 45 000 долларов. Обслужить ее под силу 1 работнику. Требуемая площадь для установки – 100 кв.м. Высота потолков – от 5,5 метров.
Помещение
В зависимости от типа используемого оборудования необходимая площадь помещения под производство составит от 70 до 150 кв. м. Желательно наличие свободных площадей для хранения и просушки, допустимо, чтобы блоки располагались на улице в паллетах под оборудованными навесами. Требования к помещению – ровный пол, высокие потолки, хорошее освещение, система отопления и промышленная вентиляция.
Себестоимость, прибыль, срок окупаемости
Суммарные затраты на реализацию бизнес-идеи составят от 19 тысяч долларов (в случае использования бюджетного варианта — сборного оборудования в виде отдельных узлов). Себестоимость выпуска одного блока составляет 0,55 $, цена реализации – от 1$ за шт.
Чистая прибыль при активном сбыте через сети строительных магазинов и гипермаркетов, напрямую крупным заказчикам – строительным корпорациям, фермерским хозяйствам, муниципальным службам – может достигать 3300-3500$ в месяц. Срок окупаемости бизнес-проекта при благоприятных условиях — 6-7 месяцев.
Нюансы бизнеса
Еще раз подчеркнем основные секреты успешности бизнеса по производству керамзитобетонных изделий:
— точное соблюдение пропорций добавления материалов;
— выбор надежного поставщика качественного сырья, проверка каждой партии на уровень радиации;
— использование обогащенного и кварцевого песка из чистых месторождений;
— соблюдение технологии просушки в естественных условиях в течение 7-8 дней, без использования ускоряющих этот процесс тепловых пушек, к которым прибегают некоторые производители, что увеличивает хрупкость блоков и ведет к их последующему быстрому износу.
Видео о производстве керамзитобетонных блоков:
bizoomie.com