Производство обуви технологический процесс: Конструирование и технология изделий из кожи
Конструирование и технология изделий из кожи
Первое, что делает человек утром, встав с постели, обувается. И в обуви проводит весь день, сменив домашние тапочки на уличные ботинки, туфли или сапоги, их — на рабочую обувь или спортивную, или выходные туфли…
Многие думают, что труд на обувной фабрике тяжелый, скучный и не престижный. Неправда! Наша профессия творческая и, можно даже сказать, лирическая. В каждую модель автор вкладывает частицу своей души. Разве может такая профессия быть скучной?
Каждое утро многочисленный отряд обувщиков принимается за работу. Рассыпаются по плитам раскройных прессов вагоны кож, раскатываются бесконечные рулоны синтетических материалов. Растекаются реки клеев, ручейки красок и аппретур; разматываются пестрые километры ниток, рассыпаются тонны разнокалиберных гвоздей. Всё это нужно, для того чтобы снова как вчера, как месяц, год и много лет назад заработал конвейер, начали свою ежедневную суету иглы, принялись сжимать и разжимать челюсти затяжные машины, вгрызаться в края подошвы фрезы.
Специальность обувщика была и будет необходима всегда и повсюду. Ведь не было ещё цивилизованного общества без обувщиков. Обувное дело — выгодный, стабильный бизнес. При знакомстве друг с другом бизнесмены обращают внимание на три предмета туалета собеседника: часы, очки, ботинки. Эти вещи непременно должны быть высокого качества.
В дело повышения качества белорусской обуви наша специальность старается внести самый непосредственный вклад. Мы учим учащихся, мыслить оригинально, «заражаем вирусом творчества». Наши выпускники работают ведущими специалистами на обувных и кожгалантерейных фабриках Республики Беларусь и ближнего зарубежья, возглавляют собственные фирмы.
Обучение по данной специальности позволит приобрести современные и глубокие теоретические знания и практические умения по дисциплинам:
- технология и оборудование обувного производства;
- технология индивидуального пошива и ремонта обуви;
- моделирование и конструирование обуви;
- товароведение обуви;
- основы менеджмента, маркетинга и деловой документации;
- информационные технологии и др.
Выпускники владеют навыками и знаниями разработки технологической документации по проектированию технологических процессов обувного производства и смогут занимать должности: контролёра, мастера, технолога.
Выпускники специальности будут востребованы в следующих сферах деятельности:
- на предприятиях различных организационно-правовых форм, осуществляющих производство обуви и ремонт.
Специалисты будут обладать навыками и знаниями в области:
- разработки технологических процессов производства обуви;
- наладки и настройки оборудования и систем обувного производства;
- контроля качества и соблюдения трудовой дисциплины;
- реализации менеджмента качества продукции в соответствии со стандартами ИСО 9000.
Выпускники будут знать:
- сырье, используемое для производства обуви;
- технологические процессы производства и ремонта обуви.
Выпускники будут уметь:
- характеризовать свойства материалов, используемых для производства обуви;
- определять основные показатели качества кожевенных материалов;
- рассчитывать и подбирать новейшее оборудование для осуществления производства обуви;
- размещать технологическое оборудование в цехах;
- расставлять рабочих по рабочим местам с учетом квалификации и индивидуальных способностей в соответствии с технологической схемой процесса;
- владеть приемами выполнения работ при обслуживании технологического оборудования и обучать им рабочих.
В процессе прохождения производственной практики получают одну из профессий рабочего:
- раскройщик материалов;
- затяжчик обуви;
- контролер изделий полуфабрикатов и материалов;
- сборщик обуви; обувщик по ремонту обуви.
Квалификация специалиста — техник.
Специализации:
- Технология обуви и ремонт. Конструирование обуви и кожгалантерейных изделий
3.5 Производство обуви методом литья под давлением
3.5 Производство обуви методом литья под давлением
Во многих странах широко применяется метод литья обуви из резины и термопластичных материалов. Ленинградский завод резиновой обуви ЛПО «Красный треугольник» был одним из создателей этого метода в отечественной практике. Сущность его заключается в том, что в закрытую полость пресс-формы впрыскивают дозу разогретого и пластифицированного полимерного материала. Если материал является эластомером (резиновая смесь), в пресс-форме происходит вулканизация изделия, если же материал термопластичен (ПВХ, ТЭП), то пресс-форма интенсивно охлаждается для устранения излишней пластичности термопласта.
Существует много конструкций литьевых машин, но все они имеют следующие узлы и механизмы: литьевую головку, устройство для дозирования, пресс-форму, системы обогрева и охлаждения, привод литьевой машины и пульт автоматической системы управления.
Литьевые машины выпускает ряд зарубежных фирм: «Штюббе» и «Десма» (Германия), «Сефом» (Франция), «Энгель» (Австрия), «Оттогалли» (Италия) и др.
Производство обуви методом литья под давлением имеет важные преимущества перед другими существующими методами: повышается производительность за счет сокращения времени вулканизации; улучшается качество резиновой обуви; ликвидируются операции изготовления заготовок; уменьшаются отходы материалов; появляется возможность полной механизации и автоматизации процессов.
Применение термопластичных материалов исключает необходимость подготовительного процесса. Изготовление обуви из них начинается на литьевом автомате и на нем заканчивается. Метод литья обуви из термопластичных материалов дает значительную экономию энергетических затрат, так как исключается процесс вулканизации. Производительность труда на одного работающего при этом методе в 2 раза выше, чем при методе формования, и в 9 раз выше, чем при методе клейки.
3.5.1 Производство обуви из резиновых смесей методом литья
При реализации процесса литья под давлением отпадает необходимость в изготовлении и сборке резиновых деталей, так как резиновая смесь в виде заготовки простой конфигурации (ленточка, жгут, гранулы) автоматически подается в литьевой узел.
В цилиндре литьевой машины резиновая смесь пластицируется, разогревается и после перехода в вязкотекучее состояние под давлением впрыскивается в закрытую нагретую пресс-форму, которая движется по кругу и автоматически размыкается после окончания цикла вулканизации.
Рекомендуемые файлы
До последнего времени в мировой практике не имелось опыта изготовления цельнорезиновой обуви на текстильной подкладке методом литья под давлением, за исключением отдельных экспериментов по литью галош на ЛПО «Красный треугольник» еще в 30-х годах, и рекламных данных немецких фирм «Штюббе» и «Десма» о разработке оборудования для литья сапог.
Сложность проблемы литья высокой резиновой обуви состоит в том, что в отличие от термопластов, которые при переработке методом литья под давлением вследствие разогрева переходят в истинно вязкое состояние (расплав), каучук и резиновые смеси характеризуются высокой вязкостью вследствие большой молекулярной массы эластомеров, и при их переработке развиваются большие высокоэластические деформации релаксационного характера.
В связи с этим для переработки резиновых смесей применяется литьевое оборудование, обеспечивающее более высокие давления литья при заполнении пресс-формы, а запирающее формы устройство обеспечивает при этом повышенные усилия смыкания в момент литья и вулканизации. Вулканизация требует выдержки изделия в течение определенного времени при высоких температурах нагрева формы.
Наличие текстильной подкладки с высокоразвитой поверхностью, а также сложная форма высокой резиновой обуви оказывает существенное влияние на реологическое поведение резиновых смесей и параметры процесса переработки, что в свою очередь требует как создания специального литьевого оборудования, так и синтеза резиновых смесей со сложным –комплексом свойств.
Эти трудности являются основными причинами отсутствия в мировой практике опыта изготовления эластичной резиновой обуви на текстильной подкладке методом литья под давлением.
3.5.2 Производство обуви из термопластичных материалов
Процесс переработки термопластичных материалов при литье обуви под давлением состоит в пластикации и плавлении гранулированного полимера в инжекторе литьевой машины, впрыске расплава в форму при высоком давлении и окончательном формировании изделия при охлаждении расплава в форме.
Применение высокого давления при литье необходимо не только для осуществления впрыска материала в форму, но и в основном для компенсации усадки при охлаждении. Чем выше давление литья, тем в меньшей степени происходят усадочные явления, так как за счет сжимаемости полимерного расплава при высоком давлении частично или полностью компенсируется уменьшение объема при резком охлаждении. Если эта компенсация происходит лишь частично, то применяют дополнительное нагнетание в пресс-форму расплава полимера давлением на начальной стадии охлаждения (дополнительную подпитку).
Наряду с давлением расплава полимера важнейшим технологическим параметром работы литьевых установок является температура материала, которая существенно меняется на разных стадиях процесса переработки, начиная с предварительного подогрева холодных гранул материала в специальном устройстве.
Еще одним важнейшим параметром процесса является продолжительность цикла литья—основной фактор, определяющий не только технологический режим литья, но и производительность установки. Резервы времени для увеличения производительности заключены в технологической части цикла, которая в основном определяется временем литья и охлаждения.
В качестве материала для литья обуви в отечественной и зарубежной практике в основном используются пластифицированные композиции поливинилхлорида.
При литье обуви используются две основные схемы литья: простое однослойное литье и многослойное, так называемое сэндвич-литье. Однослойное литье может применяться при изготовлении относительно простой по конструкции обуви, например полусапожек, невысоких туфель, сандалий, детской обуви. При этом в составе агрегата находится одна литьевая машина, а материал заполняет пресс-форму через один литьевой канал (литник). Примером такого оборудования являются агрегаты типа ТПН-10 и Н-6.
Многослойное литье состоит в поочередном впрыскивании двух и более расплавов полимеров из двух и более литьевых устройств в литьевую форму.
Принципиальное отличие процесса производства обуви из композиций ПВХ методом литья под давлением заключается почти в полном исключении закройно-заготовительного и подготовительного производства. Обувь, выпускаемая методом литья из ПВХ, состоит из внутреннего текстильного каркаса и наружного слоя ПВХ. Но так как требования к верху обуви и подошве различны, для их изготовления применяют ПВХ разных марок: для верха—ПЛ-1, для подошвы и каблука—ПЛ-2 (таблица 3.8).
Т а б л и ц а 3.8—Рецептуры композиций ПВХ
Наименование компонентов | Количество компонентов | |
ПЛ-1 | ПЛ-2 | |
ПВХ М-64 или С-63 | 100 | — |
ПВХ С-70 | — | 100 |
Диоктилфталат | 100 | 100 |
Стеараты | 1 | 1 |
Дифенилпропан | 0,1 | 0,1 |
Эпоксидная смола | 2 | 2 |
Красители (технический углерод, пигменты, титановые белила и т.д.) в зависимости от цвета и оттенка | 0,01¸0,50 | 0,01¸0,50 |
Композиции ПВХ поступают на предприятия в виде гранул различных цветов. Гранулы ПВХ упакованы в двухслойные мешки (внутренний из полиэтилена, наружный из бумаги или текстиля), для защиты ПВХ от влаги. Перед пуском в производство ПВХ проверяют следующие его показатели:
ПЛ-1 | ПЛ-2 | |
Термостабильность при температуре 175±10С, мин | 100 | 100 |
Показатель текучести расплава при 1700С | 20 | 1 |
Перед тем как засыпать ПВХ в расходные бункеры литьевого автомата, его выдерживают в производственном помещении не менее 12 часов.
Технологическая схема производства сапог из ПВХ методом литья под давлением представлена на рисунке 3.10.
В качестве подкладки сапога применяют чулок, сшитый или из трикотажной трубки плюшевого переплетения, или из кроя трикотажного двухластичного технического полотна. Трикотажная трубка поступает на завод в рулонах. Перед раскроем она раскатывается в настил и подвергается вылежке в течение суток. При раскрое подкладки делают два реза: под углом 450 и поперечный по шаблонам, указанным в спецификации на изделие. Сборку подкладки-чулка производят на двух швейных машинах фирмы «АЛИМАТ», расположенных под углом 900 друг к другу. На первой швейной машине выполняется продольный шов по всей длине отреза, а на второй—поперечный, перпендикулярный первому. Сшитая подкладка в пачках по 10 штук подается к литьевому автомату.
Для изготовления сапог методом литья из ПВХ применяют литьевые автоматы «Десма 609/10». После запуска автомата в работу технологический процесс протекает автоматически в определенном рабочем цикле. Длительность рабочего цикла определяется временем, затрачиваемым на перемещение формоносителя из одного положения в другое. В зависимости от типа выпускаемой обуви время такта составляет 17¸23 с. Рабочий цикл включает в себя:
надевание подкладки-чулка на сердечник пресс-формы,
; подтяжку подкладки на штыри,
; смыкание полуформ,
; впрыск композиции ПВХ для верха обуви,
; перемещение пуансонного щита в положение впрыска подошвы,
; впрыск композиции ПВХ для подошвы,
; открытие пресс-формы, снятие сапога с сердечника и навешивание его на штырь тележки.
1—участок сборки подкладки-чулка на швейных машинах ф. «Алимат»,
2—склад композиций ПВХ,
3—бункер для загрузки ПВХ,
4—литьевой агрегат,
5—карусельный стол,
6—машины для обрезки излишков подкладки и ПВХ по верху голенища,
7—ленточный конвейер,
Ι—контроль качества,
ΙΙ—вкладывание стелек,
ΙΙΙ—подбор в пары,
ΙV—упаковка в короба,
V—упаковка в ящики, маркировка, отправка на склад.
Рисунок 3.10—Схема технологического процесса литья сапог из ПВХ
Основные технологические параметры литья приведены в таблице 3.9
Т а б л и ц а 3.9—Основные технологические параметры литья
Показатели | Композиции на основе ПВХ для | ||
верха обуви | низа обуви | ||
импортные | отечественные | ||
Температура обогрева литьевых машин по зонам шнека, 0С: | |||
первая зона | 165±10 | 165±10 | 165±10 |
вторая зона | 170±10 | 170±10 | 175±10 |
третья зона | 180±10 | 180±10 | 185±10 |
сопло | 175±10 | 175±10 | 175±10 |
Давление впрыска, МПа | 4,2±0,3 | 1,5±0,3 | 1,2±0,3 |
Давление пластикации, МПа: | |||
1 ступень | 1,5 | 1,0 | 1,0 |
2 ступень | 2,5 | 1,5 | 1,5 |
Время дополнительного нагнетания, с | 2,0±1,0 | 2,0±1,0 | 2,0±1,0 |
Давление дополнительного нагнетания, МПа | 1,5 | 0,5 | 0,5 |
Режим литья ПВХ при производстве сапог следующий:
Температура смеси при впрыске, 0С | 180±10 |
Время цикла, с | |
для сапог | 21±2 |
для сапожков | 19±2 |
Температура эмульсии при охлаждении сердечников, 0С | 20 |
Давление эмульсии при охлаждении сердечников, МПа | 0,4 |
Температура сердечников, 0С: | |
пяточная часть | 20±5 |
носочная часть | 40±5 |
Температура полуформ, 0С: | |
верх | 60±5 |
низ | 50±5 |
Литьевой автомат обслуживают 3 оператора. Они выполняют ручные операции рабочего цикла, пускают и останавливают литьевой автомат, контролируют параметры технологического процесса.
Первый оператор берет подкладку и натягивает ее на носочную часть сердечника, не закрепляя на шпильки. После поворота стола сердечник с подкладкой подходит ко второму оператору. Пресс-форма с готовым сапогом открывается на рабочем месте у первого оператора, который снимает сапог, проверяет его качество и вешает на штырь стоящей рядом тележки.
Второй оператор натягивает подкладку-чулок, расправляет, чтобы не было складок и натягивает подкладку на шпильки. Он же извлекает отходы ПВХ из литниковых отверстий пресс-формы. После размельчения на специальной машине литники снова используют в производстве.
Третий оператор засыпает гранулы ПВХ в бункер литьевых машин, обеспечивает первого оператора подкладкой-чулком, останавливает и пускает литьевой автомат, следит за параметрами технологического процесса.
Чтобы физическая нагрузка операторов была более равномерна, они через 1,5¸2 ч меняются рабочими местами.
Надетый на стержень тележки сапог находится в таком положении не менее 40 мин для охлаждения и стабилизации. В это время не следует изделие брать в руки и перемещать, так как возможна его деформация.
Готовые изделия поступают в сортировочно-упаковочное отделение для обрезки излишков по верху голенища и разбраковки. В годную продукцию вкладывают утепленную стельку, после чего сапоги подбирают в пары. Обувь укладывают в картонные коробки или деревянные ящики и отправляют на склад готовой продукции.
Несомненными преимуществами ТЭП по сравнению с ПВХ являются высокая эластичность при пониженных температурах эксплуатации, низкая плотность, а также относительно низкий уровень выделения летучих и токсичных веществ в процессе переработки. Однако низкая температуростойкость ТЭП, особенно бутадиен-стирольных, даже при относительно небольшом повышении температуры требует особо тщательного подхода при выборе как состава композиций, так и области их применения в производстве резиновой обуви.
По реологическому поведению термоэластопласты также существенным образом отличаются от ПВХ.
Изучение особенностей реологического поведения расплавов ТЭП позволило более обоснованно подойти к выбору режимов их переработки на литьевом оборудовании. Так, при переработке ТЭП, по-видимому, нет необходимости чрезмерно повышать давление литья, так как это не обеспечивает такого резкого повышения объемного расхода материала, как в случае переработки резиновых смесей.
В то же время относительно высокое значение кажущейся энергии активации вязкого течения ТЭП, наоборот, свидетельствует о целесообразности использования фактора температуры для интенсификации пластикации в червячной литьевой машине.
Еще более мощным средством для улучшения литьевых свойств ТЭП является его пластификация, причем значительный эффект достигается уже при относительно небольшом содержании пластификатора. Для снижения их вязкости применены те же методы, что и при разработке маловязких резиновых композиций для процессов литья и штампования обуви.
Т а б л и ц а 3.10— Техническая характеристика литьевых агрегатов для
Показатели | Тип агрегата, изготовитель | |||||||
G-2S, «Оттогалли» | U78/2, «Унион» | Sanpak-500 «Бата» | 611/10б «Десма» | TRN/10 Супер, «Нуова Дзарине» | F2C/14, «Оттогалли» | D2/14, «Оттогалли» | Delta 110, «Лоренцин» | |
Число формоносителей | 6; 8 | 12; 14 | 10 | 10 | 10 | 14 | 14 | 10 |
Число литьевых машин: червячно-плунжерных | 2 | 2 | 1; 2 | 2 | 1 | 1 | 1 | 1 |
червячных с дополнительным цилиндром | — | — | — | — | — | 1 | 1 | — |
Число пар обуви на формоносителе | 1 | 1 | 0,5 | 0,5 | 0,5 | 1 | 1; 0,5 | 0,5 |
Вид выпускаемой обуви | Сапоги, сапожки,сандалии | Сапоги, сапожки | Сапоги | Сапоги, сапожки | Сапожки, галоши, сандалии | Сапоги, сапожки | Сапожки, галоши | Сапоги, сапожки, сандалии |
максимальная высота, мм | 490 | 480 | 480 | 470 | 200 | 470 | 400 | 450 |
Производительность G, пар/ч | 90¸105 | 120¸160 | 90¸100 | 90¸130 | 80¸130 | 92¸105 | 92¸140 | 92¸140 |
Максимальная скорость пластикации Qmax, г/с | ||||||||
ЛМ-1 | 144,0 | 61,0 | 50,0 | 50,0 | 55,5 | 61,1 | 50,0 | 69,4 |
ЛМ-2 | 96,0 | 61,1 | 50,0 | 50,0 | — | 38,8 | 45,8 | — |
Максимальный объем впрыска Vmax, см3 | ||||||||
ЛМ-1 | 2350 | 2160 | 2160 | 1900 | 1420 | 2350 | 1400 | 1400 |
ЛМ-2 | 1250 | 2160 | 2160 | 760 | — | 1100 | 1100 | 1100 |
Максимальное давление впрыска Р, МПа | ||||||||
ЛМ-1 | 60 | 95 | 70 | 86 | 69 | 45 | 45 | 80 |
ЛМ-2 | 60 | 95 | 70 | 95 | — | 60 | 45 | 80 |
Максимальное усилие запирания форм F1, кН | 1600 | 2200 | 1600 | 1500 | 1500 | 1620 | 1200 | 2000 |
Диаметр червяка d, мм | ||||||||
ЛМ-1 | 100 | 100 | 75 | 90 | 85 | 100 | 100 | 80 |
ЛМ-2 | 80 | 100 | 75 | 65 | — | 80 | 80 | 80 |
Отношение L/d | ||||||||
ЛМ-1 | 20 | 20 | 22 | 18 | 17 | 13 | 13 | 15 |
ЛМ-2 | 18 | 20 | 22 | 18 | — | 18 | 18 | 15 |
изготовления цельнополимерной обуви
Робототехнологические комплексы | |||||||||
Delta 214 «Лоренцин» | Bipak, «Бата» | T2S/6 «Оттогалли» | Н/6, НЕ/6 «Оттогалли» | AZ-250, «Нуово Дзарине» | Sanpak-1, «Бата» | 603/10 «Десма» | 618S/10, «Десма» | U78/2C-8, «Унион» | U76/2D-8, «Унион» |
14 | 10 | 6 | 6 | 10 | 10 | 10 | 10 | 8 | 8 |
2 | 2 | 2 | — | 2 | 1 | 2 | 2 | 2 | 2 |
— | — | — | 1 | — | — | — | — | — | — |
0,5 | 0,5 | 1 | 1 | 0,5 | 0,5 | 0,5 | 0,5/1 | 0,5/1 | 0,5/1 |
Сапоги, сапожки, сандалии | Сапожки, галоши | Сапожки, сандалии | Галоши, сандалии | Сапожки, сан-далии, галоши | Сапоги, сапожки | ||||
450 | 370 | 320 | 210 | 320 | 200 | 180 | 300 | 450/380 | 360/240 |
120¸160 | — | 100¸160 | 90¸120 | 80¸180 | 80¸150 | 90¸110 | 100¸150 | 110¸170 80¸130 | 70¸110/ 90¸150 |
69,4 | 27,7 | 96,0 | 50,0 | 50,0 | 50,0 | 55,5 | 50,0 | 61,0 | 50,0 |
— | 37,5 | 96,0 | — | 30,5 | — | 33,3 | 50,0 | 61,0 | 50,0 |
1400 | 1320 | 1250 | 1200 | 1420 | 600 | 495 | 1900 | 2350 | 1360 |
1400 | 1560 | 1250 | — | 900 | — | 760 | 800 | 1360 | 1360 |
80 | 70 | 60 | 45 | 45 | 70 | 70 | 90 | 90 | 58 |
80 | 70 | 60 | — | 45 | — | 95 | 90 | 58 | 58 |
2000 | 1600 | 830 | 1080 | 1200 | 550 | 300 | 1500 | 2200 | 1600 |
80 | 70 | 80 | 100 | 70 | 50 | 55 | 90 | 100 | 90 |
80 | 70 | 80 | — | 70 | — | 55 | 90 | 90 | 90 |
15 | 22 | 18 | 13 | 16 | 20 | 18 | 18 | 20 | 18 |
15 | 22 | 18 | — | 16 | — | 18 | 18 | 18 | 18 |
Продолжение таблицы 3. 10
Показатели | Тип агрегата, изготовитель | |||||||
G-2S, «Оттогалли» | U78/2, «Унион» | Sanpak-500 «Бата» | 611/10б «Десма» | TRN/10 Супер, «Нуова Дзарине» | F2C/14, «Оттогалли» | D2/14, «Оттогалли» | Delta 110, «Лоренцин» | |
Общая установленная мощность, кВт | ||||||||
электродвигателей | 99 | 75 | 57 | 109 | 50 | 75 | 83 | 60 |
нагревателей | 40 | 21 | 30 | 50 | 16 | 47 | 39 | 18 |
Масса, кг | 30000 | 36000 | 10000 | 39000 | 10240 | 39000 | 21700 | 25000 |
Габаритные размеры, мм | ||||||||
длина | 9200 | 9170 | 6200 | 9800 | 5600 | 7800 | 6300 | 32000 |
ширина | 4500 | 7180 | 3080 | 9000 | 2700 | 7100 | 4200 | 4000 |
высота | 3900 | 2050 | 2280 | 2345 | 2000 | 3950 | 3300 | 1870 |
Примечания.
1. Перерабатываемые материалы: пластикаты ПВХ, композиции на основе ТЭП, гранулированные полиуретаны.
2. ЛМ-1 и ЛМ-2 литьевые машины соответственно для первого и второго слоя.
3. Максимальная скорость пластикации приводится по пластикату ПВХ.
4. В состав РТК входят промышленные роботы для извлечения литников и съема обуви.
5. Максимальная температура переработки 2500С.
Для получения композиций, удовлетворяющих этим требованиям и обеспечивающим необходимый уровень физико-механических и эксплуатационных свойств материала, необходимо использовать α-метилстирольные ТЭП. При одной и той же степени наполнения и одинаковом количестве пластификатора композиции на основе α-метилстирольных ТЭП имеют существенно более высокие физико-механические показатели (в том числе при повышенных температурах) по сравнению с композициями на основе бутадиен-стирольных ТЭП . Кроме того, как показали проведенные исследования, более высокая температуростойкость α-метилстирольных ТЭП (особенно радиальной структуры) обеспечивает улучшение эксплуатационного качества (прочности связи полимерной обсоюзки с текстильным верхом) полимернотекстильной обуви.
Исследования структурной пластификации эластомеров и термоэластопластов применительно к задачам создания композиций ТЭП для расширения ассортимента материалов, используемых для литья обуви, оказались особенно плодотворными при разработке композиций на основе маслонаполненных ТЭП. Используя маслонаполненный полимер, содержащий пластификатор оптимальной молекулярной массы, и вводя в состав композиции
Робототехнологические комплексы | |||||||||
Delta 214 «Лоренцин» | Bipak, «Бата» | T2S/6 «Оттогалли» | Н/6, НЕ/6 «Оттогалли» | AZ-250, «Нуово Дзарине» | Sanpak-1, «Бата» | 603/10 «Десма» | 618S/10, «Десма» | U78/2C-8, «Унион» | U76/2D-8, «Унион» |
102 | 100 | 80 | 50 | 93 | 45 | 46 | 110 | 90 | 66,5 |
32 | 50 | 30 | 18 | 23 | 20 | 28 | 50 | 40 | 23 |
38000 | 15000 | 24400 | 7900 | 17500 | 8000 | 20000 | — | 28000 | 20500 |
8500 | 4280 | 6800 | 4500 | 7080 | 6200 | 8400 | — | 13000 | 11400 |
8000 | 6850 | 3670 | 2300 | 7000 | 3090 | 6500 | — | 7000 | 7000 |
1900 | — | — | 2800 | 2050 | 2280 | Рекомендуем посмотреть лекцию «Физическая характеристика газов нефтяных и газовых месторождений». — | — | 2200 | 2200 |
олигомерный пластификатор (атактический полипропилен), удалось создать композиции, приближающиеся по реологическим свойствам к композициям ПВХ. Вследствие этого можно перерабатывать эти композиции на многопозиционных литьевых автоматах и получать различные виды обуви типа галош и сапожек.
Развитие технологии литья и более широкий круг материалов для обуви обусловили появление разнообразных конструкций литьевых агрегатов. Ведущие машиностроительные фирмы «Десма» (Германия), «Оттогалли», «Лоринцин» (Италия) и другие— выпускают в настоящее время роторные литьевые полуавтоматы различного назначения для переработки на них монолитных и вспененных композиций ПВХ, термоэластопластов. Сравнительная характеристика современных литьевых установок приведена в таблице 3.10.
Особенности обувного производства и их влияние на организацию учета затрат
ПЛАН
Введение
1. Особенности обувного производства
и их влияние на организацию учета затрат
2. Объекты учета затрат и калькулирования
3. Учет затрат по статьям
4. Сводный учет затрат и калькулирование себестоимости обуви
Заключение
Список литературы
ВВЕДЕНИЕ
Обувная промышленность является
одной из ведущих отраслей легкой
промышленности, производящей один из
самых важных и сложных в изготовлении
товаров народного потребления, оказывающих
влияние на здоровье человека. В СССР
обувная промышленность представляла
собой хорошо развитую часть национальной
экономики. Переход к рыночным отношениям
поставил предприятия обувной промышленности
в тяжелое положение. Предприятия
оказались не готовыми к резкому изменению
условий хозяйствования, и как следствие
этого – полное прекращение работы
отдельных обувных фабрик, спад производства
обуви более чем на 90%.
Переход к рынку выявил не только неконкурентоспособность продукции отечественных обувных фабрик, но и обусловил резкое изменение условий их функционирования. На смену плановому, четко сбалансированному производству обуви, контролируемому рядом специализированных ведомств, как по структуре ассортимента, так и по количеству и качеству, пришли новые формы организации производства.
В этих условиях значительно усложнился процесс управления обувным предприятием, существенно возросла роль экономической информации о затратах для принятия наиболее рациональных управленческих решений по регулированию объема производства, обновлению ассортимента и повышения качества продукции, осуществлению эффективной ценовой политики, что в свою очередь является залогом успешной работы всей обувной промышленности.
Обувное производство характеризуется
высоким удельным весом расхода материалов;
доля сырья и материалов составляет
около 80% всех издержек производства. Это свидетельствует о том, что экономное
хозяйствование и достижение высокой
эффективности работы на обувных
предприятиях в значительной мере
определяется экономией, достигнутой в
расходе материалов, и, главным образом,
кожевенных товаров.
Цель моей работы – изучение особенностей учета затрат и калькулирования себестоимости в обувной промышленности. Поставленная цель предусматривает решение следующих задач:
изучить технологические особенности обувного производства;
описать учет затрат и калькулирование себестоимости продукции обувной промышленности
1. ОСОБЕННОСТИ ОБУВНОГО ПРОИЗВОДСТВА И ИХ ВЛИЯНИЕ НА ОРГАНИЗАЦИЮ УЧЕТА ЗАТРАТ
Производство обуви — одна из ведущих отраслей легкой промышленности, на долю которой приходится около 20% объема всей ее продукции.
Обувное производство характеризуется
высоким удельным весом расхода материалов;
доля сырья и материалов составляет
около 80% всех издержек производства. Это свидетельствует о том, что экономное
хозяйствование и достижение высокой
эффективности работы на обувных
предприятиях в значительной мере
определяется экономией, достигнутой в
расходе материалов, и, главным образом,
кожевенных товаров.
По своему характеру обувное производство сложное и массовое. На одном предприятии одновременно в больших количествах выпускаются различные виды обуви. Массовость и крупносерийность обувного производства, а также особенности технологического процесса явились объективной предпосылкой его конвейеризации, широкого распространения конвейерно-поточной организации производства. Сложность и массовость обувного производства, поточность его организации оказывают влияние на постановку учета затрат и калькулирование себестоимости продукции.
Вся выпускаемая обувь классифицируется по различным признакам, в частности:
по назначению — на модельную, спортивную, домашнюю, специальную и т.
д.;
по половозрастному признаку — на мужскую, женскую, школьную, детскую, молодежную;
по видам — туфли, сандалеты, полуботинки, сапоги;
по методам крепления — клеевому, рантовому, литьевому, гвоздевому и др.
В настоящее время для всей обувной промышленности характерно преимущественное применение механических способов изготовления обуви.
Обувная фабрика представляет собой сложное предприятие с технологическим процессом, который насчитывает до 400 различных операций. Технологический процесс изготовления обуви состоит из раскроя и разруба сырья и материалов на детали для верха и низа обуви, сшивания деталей верха в «заготовку» и соединения различными методами в зависимости от технологии, предусмотренной для данного вида (клеевым, литьевым, рантовым, гвоздевым и др.) в готовое изделие.
На первой стадии технологического
процесса осуществляется раскрой
кожевенных, текстильных и других
материалов на детали для верха и подкладки
обуви. На второй стадии происходят
разруб жестких натуральных и искусственных
кож, резины на детали для низа обуви и
их обработка. Эти операции осуществляются
в закройных и штамповочных цехах.
Швейно-пошивочные цехи предназначены
для механического соединения разрозненных
деталей верха и низа обуви и выпуска
готовых изделий. Таким образом, при
данной технологии путем параллельной
обработки различных материалов
изготавливают отдельные детали, а затем
путем механической сборки получают
готовую продукцию — обувь.
При существующих способах
производства обуви механизация и
автоматизация отдельных операций
технологического процесса не дают
заметного эффекта. Технический прогресс
и, в частности, химизация производства
в обувной промышленности неизбежно
приводят к созданию новой технологии,
которая базируется преимущественно на
использовании искусственных материалов.
Это дает возможность заменить подетальную
сборку обуви цельно-штамповочным и
литьевым производством методами
объединения процессов создания
искусственной кожи из полимеров и
формирования самой обуви, усовершенствовать
и упростить технологию производства,
упростить организацию учета затрат на
производство.
На организацию учета издержек производства определенное влияние оказывают структура предприятия и технология производства.
В обувной промышленности производство охватывает весь технологический процесс начиная от раскроя и разруба материалов и кончая сборкой и отделкой обуви. Это предопределило цеховую структуру обувных предприятий, причем цеховая структура характерна как для крупных, так и для мелких обувных фабрик. Каждый цех основного производства выполняет лишь определенную часть процесса производства обуви. Кроме цехов основного производства обувные предприятия имеют вспомогательные цехи: ремонтно-механический, химический (выработка клея), энергоцех и другие. Наличие разных видов производств требует организации учета затрат отдельно по основному и вспомогательному производствам, а цеховая структура управления делает необходимой организацию учета затрат в цеховом разрезе.
С созданием в обувной промышленности
производственных объединений появилась
возможность развития подетальной формы
специализации на обособленных
специализированных предприятиях по
изготовлению деталей обуви.
Наряду с подетальной осуществлена предметная специализация: выпускается обувь, характеризующаяся каким-либо определенным признаком (применяемыми материалами для верха и низа обуви, назначением, родом, методом крепления).
Таким образом, организационно-технические особенности обувной отрасли и своеобразие выпускаемой продукции открывают возможность для развития различных форм специализации и превращения обувных предприятий в сборочные.
Специализация обувного производства тесно связана с кооперированием кожевенного и обувного производства. Рациональное кооперирование предприятий кожевенной и обувной промышленности должно обеспечить удовлетворение запросов каждого обувного предприятия в нужных ему кожах определенного ассортимента при минимальном объеме перевозок и наименьшем числе поставщиков кож одного вида.
2. ОБЪЕКТЫ УЧЕТА ЗАТРАТ И КАЛЬКУЛИРОВАНИЯ.
Учет затрат на производство в
данной отрасли организуют исходя, с
одной стороны, из требования достоверного
исчисления себестоимости продукции, с
другой — организации внутрихозяйственного
хозрасчета.
На обувных предприятиях, выпускающих обувь большого ассортимента, затраты на ее производство подразделяются по каждому виду обуви. Такой группировке, как правило, поддаются лишь прямые затраты, косвенные же расходы учитываются в основном только по местам их возникновения с последующим условным распределением между отдельными видами обуви.
Для организации внутрихозяйственного расчета, его углубления и расширения необходимо учитывать затраты на производство по каждому структурному подразделению (раскройному, пошивочному и другим цехам), а внутри них — по отдельным участкам, бригадам, рабочим местам. Эти затраты обобщаются затем по цехам и предприятию в целом.
Объектом учета затрат является артикул обуви, изготовленной из конкретных видов материалов. Выбор объекта калькулирования зависит от характера производства и его специализации.
На предприятиях с полным циклом
производства, а также на специализированных
фабриках, выпускающих обувь определенного
метода крепления, обувь мужскую и
женскую, объектом калькулирования
является модель готовой обуви определенного
артикула, пошитая из конкретного
материала. Например, полуботинки мужские,
артикул 140134 ЧЛ (черный лицевой хром),
модель 6734. К этому артикулу относятся
полуботинки различных размеров (от 24,0
до 27,0). Иными словами, калькулируется
средний размер обуви данного артикула
и модели. Такая практика обосновывается
тем, что оптовая цена на все размеры
этих полуботинок одинакова.
Число объектов калькулирования зависит от количества выпускаемых артикулов и моделей обуви и видов материалов, используемых для производства обуви данного артикула. На фабрике может изготавливаться обувь 20—25 артикулов, а на каждый из них идет 10—15 видов материалов. Следовательно, число объектов калькулирования может колебаться от 200 до 400 наименований.
На предприятиях, специализирующихся
на производстве деталей обуви (подошвы,
стельки и др.), объектом калькулирования
являются полуфабрикаты, которые
используются на предприятиях своего
объединения либо реализуются на сторону
в порядке кооперации. На таких предприятиях
производят полуфабрикаты до 200 различных
фасонов, причем каждый фасон может
включать 5—6 деталей (стельки, задники
и т. д.). Таким образом, число объектов
калькулирования на этих предприятиях
может насчитывать до 1000 и более.
Важным вопросом калькулирования себестоимости обуви является правильный выбор калькуляционной единицы. В отличие от объекта калькулирования, представляющего собой определенный вид продукции предприятия, калькуляционная единица — измеритель этой продукции.
Калькуляционной единицей на предприятиях обувной промышленности с полным циклом производства являются 100 пар готовой обуви, на специализированных—100 пар деталей обуви определенного фасона.
3. УЧЕТ ЗАТРАТ ПО СТАТЬЯМ
В отличие от типовой номенклатуры
калькуляционных статей затрат на
производство, предусмотренной Основными
положениями по планированию, учету и
калькулированию себестоимости продукции
на промышленных предприятиях, в обувной
промышленности дополнительно выделена
статья «Вспомогательные материалы на
технологические цели». Это связано с
тем, что вспомогательные материалы в
данной отрасли, с одной стороны, имеют
довольно высокий удельный вес в
материальных затратах (6—10%), с другой
стороны, вызвано необходимостью
обеспечить строжайший контроль за их
использованием. По этой статье отражают
расходы на фурнитуру, клей, нитки,
отделочные материалы (химикаты, краски,
воск), шнурки, коробки для упаковки и
др.
Производство спецобуви Техноавиа для любой отрасли
За последние годы на фабрике проведено масштабное техническое переоснащение: значительно обновлен парк оборудования, усовершенствован технологический процесс производства обуви, повысилась квалификация сотрудников.
В настоящее время производственные мощности ООО «Йошкар-Олинская обувная фабрика» располагают пятью литьевыми машинами немецкой фирмы Desma для производства высокотехнологичной обуви. Наличие высокопроизводительного литьевого оборудования позволило увеличить выпуск современной защитной обуви и значительно расширить модельный ряд.
1 100 000 пар обуви выпускается под маркой «Техноавиа» в год.В настоящее время на фабрике выпускаются следующие серии обуви литьевого метода крепления подошвы:
серия «Техногард» с металлическими защитными носками (Мун 200) серия «Неогард» с защитными носками из композитного материала (Мун 200) серия «Капитан» с защитными носками из композитного материала (Мун 200) серия «Неогард-Лайт» с защитными носками из композитного материала и алюминия (Мун 200) серия «Неогард-Лайт Антистат» с защитными носками из композитного материала и алюминия (Мун 200) серия «Юнигард» с металлическими защитными носками или с защитными носками из композитного материала (Мун 200) серия «Альбус» с металлическими защитными носками или с защитными носками из композитного материала (Мун 200)
Для совершенствования технологического процесса изготовления защитной обуви и повышения производительности труда на фабрике установлены современные швейные автоматы фирмы Pfaff (Германия), позволяющие с минимальным количеством работающих изготавливать большее количество заготовок верха обуви высокого качества сборки.
Также внедрены в производство комплексы для автоматического раскроя материалов верха и текстильных материалов подкладки фирмы ATOM (Италия), раскройное и затяжное оборудование фирмы Schoen (Германия), швейно-заготовочные участки усилены швейными машинами фирмы Duerkopp-Adler (Германия).
5 литьевых машин Desma установлены на Йошкар-Олинской обувной фабрике.Высокопроизводительные литьевые машины фирмы Desma, установленные на фабрике, позволяют выпускать современную защитную обувь литьевого метода крепления подошвы из полиуретана с ходовым слоем из термопластичного полиуретана или из нитрильной резины, которая обеспечивает защиту от нефти, нефтепродуктов, агрессивных сред, механических воздействий. Подошва с ходовым слоем из нитрильной резины, кроме этого, обеспечивает защиту от контакта с нагретыми поверхностями (+300° С/60 секунд).
При производстве специальной обуви мы используем термоустойчивые водоотталкивающие кожевенные материалы, воздухопроницаемые и дышащие подкладочные полотна, проколозащитные металлические или неметаллические прокладки из проколозащитного материала – всё это позволяет значительно повысить защитные характеристики обуви.
Мы изготавливаем обувь от единичных образцов до партий в несколько тысяч пар. Многолетнее сотрудничество с крупными компаниями позволяет нам глубже изучать требования, предъявляемые к защитной обуви, и удовлетворять потребности заказчиков в поставке обуви, изготовленной в корпоративном стиле. Так, обувь может быть изготовлена из материалов различной цветовой гаммы, с применением цветной фурнитуры (шнурки, нитки), с логотипом компании-заказчика.
Инновационная политика модернизации и развития производства позволяет нам выпускать защитную обувь, соответствующую требованиям Технического регламента Таможенного союза, российских и европейских стандартов.
Выпуская на собственном производстве более миллиона пар обуви в год, мы имеем большой опыт разработки моделей обуви с учетом специфики работы в различных отраслях промышленности.
Технология производства обуви | Бизнес Промышленность
В нынешнее время современнее технологи получения какого-либо продукта идут большими шагами. До высокого уровня дошла автоматизация практически все основных процессов, в том числе и технология изготовления обуви
Человек уже не должен прикладывать руку к этому виду производства – он лишь управляет. В автоматизированном производстве – это простота и удобство управления.
Описание технологического процесса
Более детальная информация о том, как выполняется технология производства обуви и о процессах производства обуви:
— происходит обработка паром под давлением носочной и пяточной части заготовка для упрощения и размягчения надевания на колодку.
— колодка рассоединяется для заготовки и происходит смыкание, ожидая установки в конвейере. За этим всем выполняется контроль, оператор видит весь процесс на дисплее при помощи встроенной видеокамеры.
— затем происходит снятие головки при помощи нагревательного тоннеля, который использует горячий воздух. Скорость этого этапа напрямую зависит от вида и типа обуви.
— рабочая машина выполняет взъерошивание заготовки по контуру четко до линии оттиска так, чтобы не было попадания пыли на место литьевых пресс-форм.
— после этого робот прикрепляет металлические стельки к низу самой заготовки, при использовании теремоплавкого клея.
— затем робот снимает уже готовую обувь со стола и выполняет установку следующей колодки на позицию, чтобы совершить прилив подошвы.
— в свою очередь другой робот выполняет распыление разделительной смазки на поверхности пресс-формы. Это выполняется очень аккуратно и точно, что позволяет полностью быть уверенным, что разделительная смазка не сможет попасть на остальные части заготовки.
— затем в реакционном блоке происходит смешивание системы полиуретанов. В этом процессе технология производства обуви дает возможность выполнить смешивание самоочищающимся шнеком. Довольно часто специалисты добавляют различные краски и др. добавки.
— после этого выполняется охлаждение подошвы, это происходит в холодном туннеле, так как может возникнуть риск остаточной деформации при снятии.
— на следующем этапе автоматизированное оборудование обрезает остаточную промежуточную или ходовую подошву при использовании специального чипа, на который до этого произвели запись информации.
Последний этап
В завершении технология производства обуви предусматривает снятие уже готовой продукции с колодки. Это все сопровождается автоматизированным раскрывающимся механизмом для простоты операции.
Социальные закладки
Как делают обувь? Производство группы компаний «Обувь России»
В Новосибирске есть российская обувная компания «Обувь России», которая уже 15 лет занимается производством и продажей обуви. Все началось в 2003 году из небольшой региональной розничной сети, а выросло в один из крупнейших федеральных обувных ротвейлеров страны по числу магазинов.
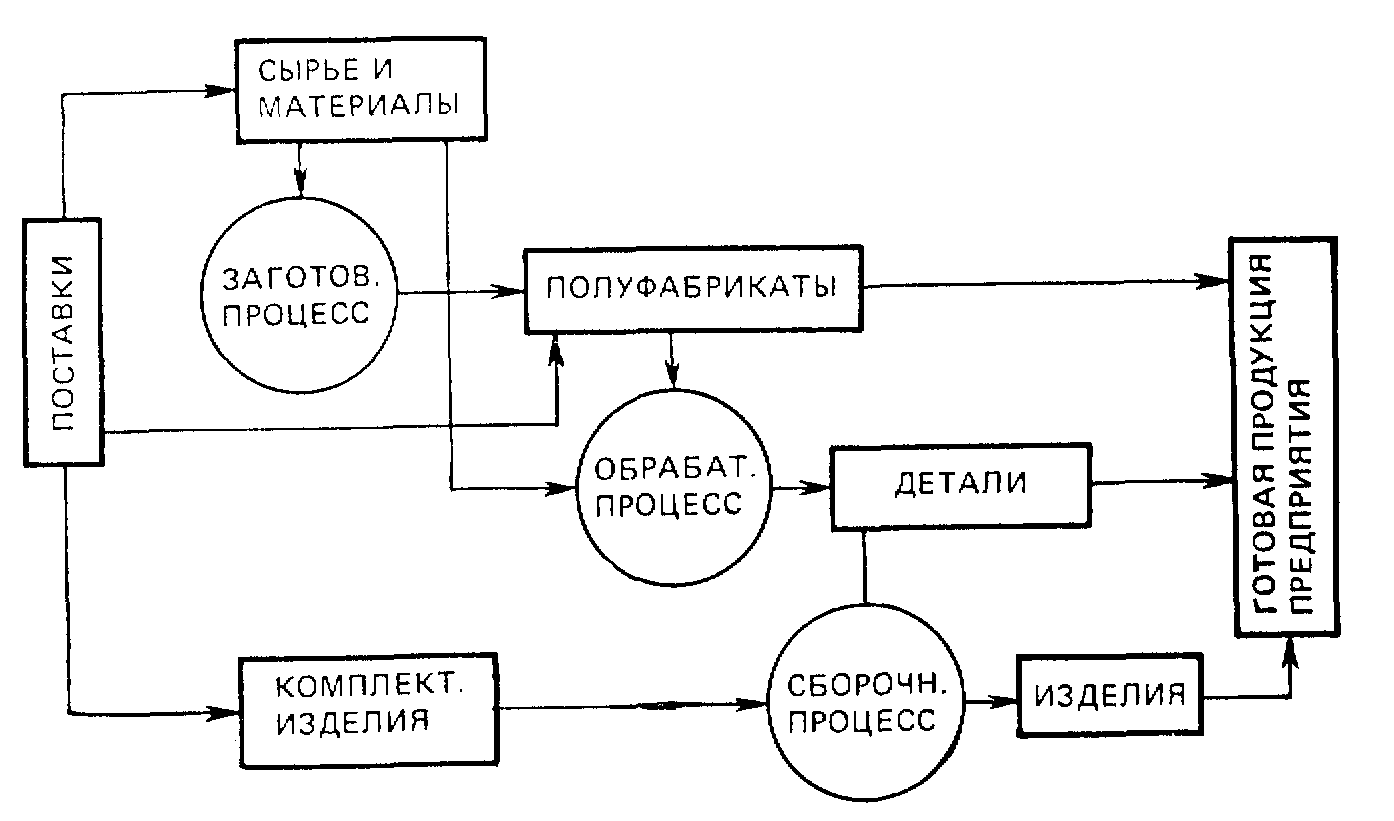
Честно признаюсь тоже услышал это название впервые и не понимал, как такая большая компания может быть не на слуху. Оказывается, на рынке она представлена брендами: Westfalika, Пешеход, Emilia Estra, Rossita, Lisette, S-TEP, ALL.GO. «Обувь России» сама создает продукт для своих брендов и контролирует все этапы его создания, начиная от разработки коллекции и заканчивая продажей конечному потребителю. Построить такую систему помогает существенный производственный опыт.
Компания имеет две производственные площадки — в Новосибирске, где работают автоматизированные комплексы по изготовлению обуви из ЭВА, и Бердске, где базируется производство обуви со всеми основными методами крепления подошвы. Общие производственные мощности составляют 500 тыс. пар обуви в год.
«Обувь России» производит ready-to-wear — это обувь, сшитая по готовым стандартизированным лекалам и продающаяся в магазинах. У компании три основных направления: обувь из натуральной кожи клеевым методом, цельноформованная обувь литьевым методом из материла ЭВА и обувь из натуральной кожи методом прямого литья на заготовку. Именно с последним я и познакомился. Пора узнать, как в России делают обувь!
1. Путь обуви начинается с дизайна. Для этого в компании существует целый отдел во главе с немецким дизайнером Томасом Франком. Опираясь на мировые тенденции моды, анализ рынка и результаты продаж предыдущей коллекции, придумываются новые модели, которые будут востребованы на рынке. После утверждения создаются технологические карты и выкройки, и обувь поступает в массовое производство.
Эталонным размером ноги считается 42 для мужчин и 37 для женщин. От этого размера идет расчет других размеров. Чтоб получить другие размеры, базовый размер увеличивают или уменьшают. Так, например, в России, чтобы получить следующий размер, к каждой детали прибавляют 1,2мм, в Китае прибавляют 1мм, в Европе примерно 1,1мм. Именно поэтому в разных магазинах и возникает разница в размерах.
2. Производство делится на заготовочный (раскройно-швейный) и литьевой (сборочный) цеха. Начнем с первого. Сюда поступает кожа, ткань и другие материалы, необходимые для производства обуви. В этом цехе вырезаются детали будущих ботинок, обрабатываются, сшиваются и передаются в следующий.
3. «Обувь России» использует современные технологии в обувном производстве. Производство отличается высокой степенью автоматизации. Раскройный станок анализирует размеры полотна и рассчитывает оптимальные места для выреза.
4. Из большого меха с помощью острых форм и пресса буквально выдавливают нужные заготовки. Основная сложность здесь заключается в том, чтобы правильно расположить формы и отправить в отходы минимальное количество материала. Без опыта и сноровки будет сложно.
5. Форм для резки много, для каждой выпускаемой модели.
6. Используются современные высокотехнологичные швейные системы Orisol. Они позволяют отшивать сложные модели обуви, верх которой состоит из множества элементов и собирается из материалов разных фактур, например, обувь стиля полуспорт и спортивная обувь. Производительность таких систем в 5-6 раз выше, чем у традиционных швейных машин. Кроме того, они позволяют добиваться высокого качества конечного продукта — уровень возврата по браку в розничных сетях «Обуви России» в последние 10 лет не превышает 1%.
7. Это подготовительный этап. Тут обрабатываются вырезанные ранее детали.
8. Проклеивают.
9. Заготовки.
10. На следующем этапе отшиваются верх и подкладка обуви. Здесь происходят процессы отсрочки, прострочки, проклейки деталей, обрезание лишнего, добавление кнопок и застёжек. У некоторых деталей стачивают края, чтобы потом обувь не натирала.
11. Этот этап делается в ручную. Работают быстро, четко — чувствуется опыт. В компании работает профессиональная команда, у ключевых сотрудников опыт работы в отрасли – 10-15 лет.
12.
13. Добавляют кнопки.
14. Не вся обувь отшивается в Новосибирской области. Что-то отдано на аутсорсинг российским партерам, что-то делается в Китае. Отшитый вверх будущей обуви и стелька из обувной целлюлозы отправляется в литьевой цех.
15. В литьевом цеху стелька и верх обуви сшивается.
16. Следующие этапы связаны с приданием формы ботинку. Для этого сначала вшивается стелька из обувной целлюлозы. На один ботинок у женщин уходит в среднем 15 секунд. Я засекал!
17. Затем заготовку надевают на колодку. С помощью молоточка придается правильная форма.
18. Для закрепления формы ботинок проходит через специальную печку, где заготовки несколько раз резко нагревают и охлаждают. В результате формируется окончательная форма обуви. Тканевый верх обуви готов. Переходим к подошве.
19. Следующий этап — соединение верха ботинка с подошвой. В этом процессе участвует две карусельных немецких литьевых машины Desma. Ее особенность состоит в том, что материал для подошвы заливается в жидком виде в пресс-форму и застывает в непосредственном контакте с кожей. Таким образом, подошва «сцепляется» с заготовкой верха обуви на молекулярном уровне. Обувь с натуральным мехом по такой технологии изготавливается в нашей стране только на фабрике «Обувь России».
20. Проверка качества.
21. Дальше из ботинка вынимают колодку, удаляют лишние куски резины и устраняют мелкие дефекты с помощью паяльника.
22.
23. На последнем этапе обувь попадет на конвейер, где ее очищают от грязи, дополнительно шлифуют, обрабатываю кремом, вставляют стельки и шнурки. Больше всего удивило, что шнурки вставляются вручную! Никогда бы не подумал.
24. По моим примерным подсчетам над каждым ботинком трудится минимум 20 человек.
25.
26. Готово! Обувь упаковывается и отправляется в магазины. В день компания производит около 2000 штук. Про работу магазинов и обувной ритейл я расскажу подробнее в следующем посте.
Расскажите друзьям:
Добавить в друзья
Подписывайтесь на социалки:
По вопросам проведения съемок пишите на электронную почту [email protected]
Разработка технологического процесса производства летних женских туфель (Курсовая работа)
ФЕДЕРАЛЬНОЕ АГЕНТСТВО ПО ОБРАЗОВАНИЮ ГОСУДАРСТВЕННОЕ ОБРАЗОВАТЕЛЬНОЕ УЧРЕЖДЕНИЕ ВЫСШЕГО ПРОФЕССИОНАЛЬНОГО ОБРАЗОВАНИЯ ГОСУДАРСТВЕННЫЙ ТЕХНОЛОГИЧЕСКИЙ УНИВЕРСИТЕТ ИНСТИТУТ ТЕХНОЛОГИИ ЛЕГКОЙ ПРОМЫШЛЕННОСТИ, МОДЫ И ДИЗАЙНА
Кафедра моды и технологии
Курсовая работа
по дисциплине «Технология изделий из кожи»
Тема: Разработка технологического процесса производства летних женских туфель
Исполнитель: студент группы
Руководитель:
Казань, 2009
Содержание
Введение
1 Литературный обзор
2. Конструкторско-технологическая
характеристика модели
2.1 Технический паспорт женских туфель с открытыми носочной и пяточной частями
3. Обоснование выбора: материалов, технологии, оборудования
3.1 Обоснование выбора материалов
3.1.1 Кожи для верха обуви
3.1.1.1 Искусственная и синтетическая кожа для верха обуви
3.1.1.2 Натуральные кожи для верха обуви
3.1.2 Материалы для подкладки обуви
3.1.3 Материалы для промежуточных деталей
3.1.4 Низ обуви. Виды подошв
3.2 Обоснование выбора технологии
3.3 Обоснование выбора оборудования. Техническая характеристика оборудования
4. Проектирование технологического процесса сборки заготовки верха обуви
4.1 Принципы построения технологического процесса
4. 2 Перечень
операций технологического процесса
сборки заготовки верха летних женских
туфель
5. Проектирование технологического процесса сборки и отделки обуви
5.1 Обоснование выбора метода формования заготовки на колодке
5.2 Перечень технологических операций по сборке обуви женских туфель с открытыми пяточной и носочной частями клеевого метода крепления
Заключение
Литература
Приложение
Введение
Цель работы – разработка технологического процесса производства женских туфель с открытыми пяточной и носочной частями клеевого метода крепления.
В гардеробе
современной женщины обувь занимает
ведущее положение и является предметом
первой необходимости. Она предназначена
для защиты ног человека от неблагоприятных
воздействий внешней среды — холода,
чрезмерного нагрева, сырости, пыли,
грязи, механических повреждений, а также
служит предметом украшения человека.
Изменения, происходящие в последние годы в экономике страны, затрагивают и обувную промышленность. Глубокое и всестороннее изучение конкретной ситуации на рынке современного товара и перспектив его изменения являются одной из важнейших предпосылок для развития производства обуви и повышения его эффективности.
В последнее время в продаже стало появляться много новых, более модных моделей женской кожаной обуви, как отечественного, так и импортного производства, стали более полнее удовлетворяться возросшие требования населения на многие виды обуви. Проблема заключается в необходимости обеспечить полноту ассортимента кожаной обуви, улучшения качества и внешней отделки, создания условий, при которых покупатель имел бы возможность без лишних затрат времени приобрести изделия нужного размера, модели.
В связи с
этим, в условиях жёсткой конкуренции,
для торгового предприятия важно правильно
выбрать ассортиментную политику, а
также более полно удовлетворить возросшие
требования населения в конкурентоспособной
обуви высокого качества.
1. Литературный обзор
В настоящее
время на рынке легкой промышленности
существует огромное количество различных
предприятий, которые являются
производителями современной обуви.
Благодаря отсутствию дефицита в этой
области потребитель имеет возможность
выбора. Но известно, что увеличение
предложения не всегда влечет за собой
увеличение спроса. Большое разнообразие
ассортимента изделий не гарантирует
удовлетворение потребностей населения.
Современный покупатель предъявляет к
обуви, параллельно с требованиями
технологичности, долговечности такие
требования, как неординарный подход к
конструированию в сочетании с практичностью
и комфортностью. Отдельные обувные
фирмы самостоятельно руководствуются,
в основном, направлением моды, не
учитывают фактическую половозрастную
и видовую потребность, а также выпускают
обувь без учета ростовочно-полнотных
шкал для различных возрастных групп.
Это привело к тому, что у большинства
производителей обуви в сезоне 1999 — 2000
гг. товарные остатки значительно
превысили ожидаемые, что сказалось на
снижении объемов производства в сезоне
2000 — 2001 гг.
При определенной видовой структуре ассортимента следует учитывать климатические условия страны и непосредственно условия носки. Несоблюдение особенностей формы и размеров стоп россиян, условий эксплуатации и многих других факторов создает целый ряд проблем, связанных, с одной стороны с невпорностью произведенной обуви, а с другой — с неудовлетворенным спросом на обувь очень больших групп населения.
Большая часть производимой в настоящее время обуви изготавливается из импортных комплектующих остро модного направления, имеет качественную сборку и поэтому дорогая. Это, в свою очередь, препятствует удовлетворению спроса на обувь населения со средним и ниже среднего достатком.
В настоящее
время отмечается тенденция возрастания
интереса кожевенных заводов к отечественным
химическим материалам. Лабораторией
технологии нового ассортимента кож
ЦНИИКП был выполнен комплекс исследований
по разработке и освоению производства
новых химических материалов для
красильно-жировальных процессов в
производстве натуральных кож. Эти
химические материалы используются в
работе более 20 кожевенных предприятий
из 40 реально работающих, например, ОАО
«Вахрушин-Юфть», ООО «Кожсервис», ЗАО
«Хромтан», ООО «Фирма «Кожа», ООО «Шевро»,
кожевенные заводы в г. Ростове-на-Дону,
Омске, Новосибирске и др.
Работы зарубежных обувных специалистов выдвигают новые технические решения способов изготовления и конструкции обуви.
В моде
последних лет, в том числе обувной, все
чаще прослеживаются новые веяния.
Классическая мода отходит от
функциональности в сторону декоративных
излишеств. Удобство и комфорт отходят
на второй план, не выделяются, афишируется
же изысканная роскошь и элегантность.
Богатство и роскошь буржуазного шика
подчеркивается материалами, используемыми
для сумок, ремней и обуви. Становятся
модными натуральные и искусственные
кожи с лаковой поверхностью, блестящие
кожи под золото и серебро, с рисунками
и тиснениями печати под кожу страуса,
крокодила, питона и других экзотических
животных.
Сильное влияние моды 60-х и 80-х гг. на современную обувную моду выдвигает на первое место в ассортименте высокие сапоги с прямыми голенищами, облегающие в икрах и свободными в щиколотках, отчего в этом месте образуются складки в виде гармошки. Они напоминают популярные в 80-е годы сапоги «казачок».
По-прежнему остаются модными сапоги, облегающие всю ногу, иногда очень высокие, за колено.
По сравнению с прошлыми годами, роль сапог неизмеримо возрастает, и теперь они предлагаются в качестве дополнения не только верхней одежды, но и платьев, и даже дорогих туалетов.
Для решения
основной задачи обувной отрасли —
обеспечения населения опорной
конкурентоспособной обувью — необходимо,
прежде всего, наладить производство
оснастки и комплектующих деталей для
производства обуви, а именно: обувных
колодок, геленков, подносков, задников,
каблуков, формованных подошв, подошвенных
узлов, стелек. При этом понятно, что без
наличия координирующих технических
документов невозможно наладить четкий
выпуск упомянутой обуви в должном
количестве и ассортименте.
Учитывая изложенное, по мнению специалистов пересмотр ГОСТа 39927 «Колодки обувные» и разработка нового стандарта становятся безусловной необходимостью, как первый шаг к решению существующих проблем в отрасли.
Развитие цифровых технологий в обувной промышленности
FUTURECRAFT 4D: ТВОРИТЕ – adidas
По мере того, как цифровизация становится модным словом в мире моды, перед производителями обуви встают новые задачи. Сократите время отклика и повысьте гибкость, эффективность и качество, учитывая, что безопасность и окружающая среда — это лишь верхушка айсберга
В то время как обувная промышленность, как и многие другие отрасли, переживает небывалые преобразования, компании сталкиваются с проблемами, которые можно превратить в возможности, если правильное решение будет принято в нужный момент.
Сегодня мы представляем вам концепцию аддитивного производства , которая относится к процессу, с помощью которого цифровые данные 3D-проектирования используются для построения компонента слоями путем нанесения материала.
Крупные мировые игроки уже давно внедряют аддитивное производство в свой процесс разработки продуктов , особенно в бизнесе кроссовок . Они делают собственные 3D-принтеры, которые используются для принятия решений об эстетике и функциональности продукта, а также для креплений и других деталей.
3D-печать оказалась особенно полезной для изготовления деталей индивидуальной обуви , таких как пластины — формованная деталь в нижней части спортивной обуви — и амортизирующих материалов, таких как стельки, промежуточная подошва или подошва.
Текущие ограничения для 3D видны в завершении набора полностью пригодных материалов для обуви и внедрении технологии в действие на производственной линии. Кроме того, существует еще не широкий спектр различных материалов , которые могут работать с 3D-печатью, а количество отходов материалов значительно дорого, хотя в последние годы были достигнуты огромные успехи.
Преобразование верхней части обуви из 2D в 3D — сложная задача, которая потребует нового подхода к конструированию продукта и автоматизации.В операции сшивания по-прежнему много вырезанных деталей, и до полного удаления всех деталей, изготовленных вручную, еще далеко.
Говоря об этом, следует отметить, что такие компании, как adidas, начинают внедрять 3D-печать на более глубоком уровне, исследуя новые способы изменения производственной среды с помощью так называемой «Скоростной фабрики», которой будут управлять роботы и будет использовать технологию 3D-печати, позволяющую массово настраивать обувь, которая будет производиться в соответствии с конкретными требованиями без дополнительных производственных затрат.
Изображение предоставлено adidas
Texprocess представляет новые технологии для производства обуви
Новые технические разработки, такие как CAD, 3D-принтеры и Smart Shoes , открывают перед производителями обуви новые возможности для решения таких задач рынка, как оптимизация процессов.
В следующем сообщении освещаются наиболее важные тенденции, которые также можно увидеть на Texprocess, ведущей международной выставке по обработке текстиля и гибких материалов, которая пройдет с 4 по 7 мая следующего года.
Посещение международных выставок Texprocess и Techtextil позволит получить широкое представление о технологиях производства обуви и моде. Технический текстиль, который также можно использовать для производства обуви, оптимизация ИТ-процессов для специальных решений для обувного производства и технология склеивания — это лишь некоторые из тем, которые демонстрируются на ведущих выставках технического текстиля, нетканых материалов и обработки текстиля. и эластичные материалы.
Одной из самых современных технологий производства обуви является быстрое прототипирование.Быстрый расчет стал доступен даже небольшим компаниям и офисам разработчиков благодаря производительным настольным компьютерам стоимостью менее 3000 евро и цветным расходным материалам.
Данные для прототипа генерируются программами автоматизированного проектирования, которые постоянно предлагают все больше отраслевых решений. Центральным пунктом обсуждения является прямое объединение в сеть разработки продуктов (автоматизированное проектирование), управления данными о продуктах (PDM) и планирования ресурсов (планирование ресурсов предприятия ERP) посредством эффективной базы данных.Судя по их истории, многие компании имеют изолированные приложения в этих подразделениях, что может привести к потерям из-за трения, дублированию работы и отсутствию прозрачности процессов.
Это стоит компаниям больших денег и отравляет экономическую эффективность. Несмотря на то, что кредиты в Германии сейчас дешевы, а конкуренты на Дальнем Востоке борются с ростом стоимости рабочей силы, сектор производства обуви банкиры оценивают как рискованный и не заслуживающий доверия.Это означает, что спрятанные сокровища должны быть подняты, сообщают организаторы.
Благодаря информационным технологиям (ИТ) возможны быстрое вычисление и короткое производство. Однако это не помогло бы без оптимизации планирования последовательности операций. По словам Тео Куффлера, директора RG Technologies, Фельдкирхен-Вестерхам (Германия), оптимизация процессов по-прежнему предлагает большой потенциал для сокращения затрат для компаний Центральной Европы. Ключевые слова: контроль и мониторинг процессов, воспроизводимость качества и гибкая автоматизация .
Эти вещи кажутся проблемой в производственном процессе даже в наши дни. Разработки машиностроительной отрасли могут внести свой вклад в аспект гибкой автоматизации : технология вырезания, напрямую связанная с системой CAD и программируемыми швейными и сборочными машинами. С одной стороны, оба подхода могут сократить рабочие процессы, время настройки и, таким образом, упростить обеспечение качества. С другой стороны, оба подхода означают инвестиции в оборудование и установки, а также обучение персонала для работы по программированию.
Розничная торговля предлагает огромное разнообразие моделей обуви. Тем не менее, индивидуалисты хотят создавать свою обувь онлайн, что является массовой кастомизацией.
Это не проблема благодаря промышленному штучному производству. Первопроходец был производителем спортивной обуви Nike в 1999 году, и вскоре за ним последовали другие поставщики. Можно только догадываться о текущей доле рынка массовой кастомизации в обувной промышленности.
Тем не менее, он предлагает преимущество прямого взаимодействия с владельцем обуви, который, по-видимому, не только зависим от Интернета, но и является пионером в области обувной моды. Анализ заказов проливает свет на предпочтения целевой группы, а результат можно использовать в следующем ассортименте.
www.texprocess.messefrankfurt.com
Цифровизация — это настоящее и будущее дизайна обуви
Прогноз Highsnobiety Footwear — это ежемесячная колонка редактора Highsnobiety Footwear Фабиана Горслера, в которой более подробно рассматриваются самые важные сюжетные линии, тенденции и события в мире, насчитывающем несколько миллиардов долларов. долларовая индустрия кроссовок.
Производство обуви и спортивной одежды живет и умирает благодаря инновациям. Будь то амортизирующие технологии, производственные процессы или инновации в материалах, в индустрии кроссовок всегда идет гонка вооружений — быть самыми легкими, быстрыми, самыми удобными и лучшими.
За прошедшие годы цифровизация ускорила эту гонку, а новые технологии ускоряют прогресс и меняют ландшафт дизайна обуви с головокружительной скоростью. Цифровизация всегда была важной частью отрасли, но с учетом того, что 3D-печать и робототехника оптимизируют процессы и становятся все более распространенным явлением, цифровизация во всех ее формах станет основным фактором, определяющим движение отрасли вперед.
Дэниел Бэйли, соучредитель CONCEPTKICKS и самостоятельный дизайнер, считает, что цифровизация в дизайне обуви уже стала обычным явлением с точки зрения дизайнера, но именно то, как с ней взаимодействует потребитель, приведет к самым большим изменениям. «Я думаю, что в ближайшие пару лет покупка кроссовок NFT станет нормой, сбалансированной с физическими версиями того же файла/дизайна. Это, без сомнения, настоящее и будущее отрасли», — объясняет он.
Бейли, у которого есть обувные проекты с Heron Preston и adidas на его имя (результаты которых имеют очень оцифрованную, футуристическую эстетику), объясняет, что оцифровка затрагивает его работу во многих отношениях. Делает ли он наброски на планшетах WACOM или создает 3D-модели во время изучения дизайна продукта, эволюция технологий обеспечивает Бейли большую гибкость и повышенную точность при использовании инструментов, которыми он занимается.
«Это то, чем я очарован, и я постоянно пытаюсь изучить новейшее программное обеспечение и новые возможности конструирования, которые с ним связаны», — говорит он. «Мои личные творения имеют тенденцию быть более концептуальными, поэтому возможность создания NFT моих проектов возникала довольно много раз. Это то, что меня интересует, я просто жду возможности реализовать это так, чтобы это было органично для меня как дизайнера».
Зеллерфельд — новички на сцене — работали с Бейли над вышеупомянутым проектом Heron Preston. Они являются примером того, как цифровизация может обогатить отрасль, и наделали много шума благодаря использованию круговой 3D-печати.«Цифровизация снижает входной барьер для новых дизайнеров и более творческих дизайнеров. То, что мы видим сейчас, — это самое начало», — говорит команда Highsnobiety. «Цифровизация дизайна в сочетании с аддитивным производством (3D-печать) — неизбежное будущее производства. Каждый день мы видим невероятные достижения в лаборатории, и нам не терпится поделиться ими с большим количеством дизайнеров».
Этот более низкий барьер для входа является прямым результатом оцифровки, позволяющей сократить затраты и время выполнения заказа. Если раньше создание образцов или прототипов было дорого и требовало доступа к фабрикам и специализированному оборудованию, которое было не у всех, то никогда еще это не было так просто, как сейчас.Это то, что крупные бренды, такие как adidas и его проекты 4D и Strung, подчеркивают и извлекают из этого выгоду. Тем не менее, небольшие бренды и независимые креативщики теперь также могут извлечь выгоду. «Цифровизация устраняет необходимость в первоначальных вложениях денег и времени и позволяет любому создавать, масштабировать и печатать обувь за считанные часы с помощью всего лишь программного обеспечения», — говорит Целлерфельд.
Бейли добавляет, что процесс проектирования и разработки значительно улучшился после многолетнего застоя.«В прошлом цифровизация в основном играла роль в создании доказательства концепции в процессе разработки обуви, но она быстро меняется благодаря постоянным инновациям в пространстве и становится все более коммерчески жизнеспособным способом создания конечного продукта». он говорит.
Соучредитель CONCEPTKICKS и Целлерфельд — два самых интересных игрока в игре, но есть еще несколько имен, за которыми нужно следить, поскольку поле и его кадровый резерв продолжают расти.Бэйли выделяет Scry, основанную Цзысюн Вей, чьи проекты охватывают цифровой и органический мир, стирая границы и делая невозможным отличить одно от другого. RTFKT — еще один крупный игрок, на которого указывает Бейли, поскольку компания подходит к цифровизации с точки зрения инвестиций и перепродажи. RAL7000Studios, как и Bailey, работали с adidas над проектом обуви, на который сильно повлияла цифровизация, и они бросают вызов тому, как собираются компоненты кроссовок. Финн Раш-Тейлор — еще одно имя, упомянутое Зеллерфельдом, который считает дизайнера и его склонность к работе в виртуальной реальности будущим создания обуви.
Уже есть много имен, которые можно добавить в этот список, что говорит о направлении, в котором движется индустрия. Нет лучшего сочетания, чем молодые, голодные креативщики, имеющие доступ к технологиям и инструментам для реализации своего видения. Если дизайн обуви продолжит развиваться, как это было в последние пару лет, для индустрии в целом нас ждут захватывающие времена — как для многих брендов , так и для потребителей .
Сертификат дизайна и разработки обуви
Сертификат дизайна и разработки обуви – это 13-недельный профессиональный сертификат, состоящий из 4 курсов , которые дают студентам всесторонний обзор обувной промышленности, а также развивают необходимые навыки, ведущие к успешному дизайну продукции.Отраслевые партнеры и инструкторы с большим опытом в области дизайна, материалов и производства обуви предоставят ключевые элементы от концепции до маркетинга для создания функциональной и модной обуви для современных потребителей.
Кто должен получить этот сертификат?
- Дизайнеры одежды, мерчендайзеры, дизайнеры обуви и дизайнеры аксессуаров, которые хотят расширить свое понимание дизайна, маркетинга и производства обуви
- Студенты и соискатели, которые хотят обновить свое портфолио, включив в него провокационные дизайнерские доски с использованием передовых инструментов, материалов и цветовых решений.
Подход, основанный на навыках
Узнайте обо всех этапах проектирования и производства обуви, от введения в процессы проектирования до биомеханики, лучших практик, тенденций и аналитики рынка, что приведет к целостному пониманию того, как работает отрасль. После получения сертификата студенты, имеющие опыт проектирования, адаптируют свой набор навыков, включив в него уникальную область дизайна продукта. Студенты без опыта дизайна приобретут важную основу основных компонентов дизайна обуви, производства и маркетинга.
Часто задаваемые вопросы
Нужны ли мне Adobe Illustrator и Photoshop перед началом сертификационных курсов?
Нет, вам не нужно покупать Adobe Illustrator или Photoshop, чтобы пройти этот курс.
Можно ли пройти эти занятия с Chromebook?
Да, эти курсы можно пройти на компьютере/ноутбуке или Chromebook.
Нужно ли мне приобретать учебные материалы и/или программное обеспечение для этих занятий?
Различается по классам, но нет необходимых материалов, которые нужно покупать. Для всех занятий вам не нужно будет покупать какое-либо программное обеспечение и материалы. В FASH910 Shoe Design Basics есть дополнительные пакеты материалов для прототипов, которые можно приобрести за 50 долларов.
Требует ли программа посещения синхронных совещаний в реальном времени?
Нет, синхронные сеансы Zoom в реальном времени являются необязательными и могут быть записаны для тех учащихся, чьи часовые пояса и/или рабочие графики не позволяют участвовать в синхронном контенте.
Могу ли я пройти один или два курса программы или мне нужно пройти все четыре курса?
Вы можете пройти столько курсов, сколько пожелаете.Но курсы дополняют друг друга, и есть полная выгода от завершения всей программы, чтобы получить сертификат и оценить различные возможности карьерного роста в отрасли.
Сколько времени в неделю я должен тратить на выполнение курсовой работы?
Каждый класс немного отличается, но рассчитывайте тратить в среднем около 5-6 часов в неделю на посещение или просмотр занятий, чтение и выполнение заданий
ECCO и Stratasys: технологические инновации в обувной промышленности
Хотя известно, что несколько известных обувных брендов, таких как Adidas и Nike, используют 3D-технологии для производства обуви, они не единственные. В 2018 году мы рассказывали вам о ECCO, датском производителе обуви, который использует как 3D-сканирование, так и 3D-печать для создания индивидуальных продуктов. И чтобы продолжить свой рост, компания недавно объявила о крупном партнерстве. Ecco будет сотрудничать с американским гигантом Stratasys, и компания надеется, что благодаря этому она сможет ускорить разработку своих будущих продуктов и обуви.
Неслучайно датская компания обратилась к аддитивному производству и к 3D-принтеру Origin One, основанному на запатентованной технологии Stratasys P³ (программируемое светоотверждение). «Наш инновационный подход к разработке обуви и стремление сделать опыт клиентов приоритетом сделали аддитивное производство логическим следующим шагом в эволюции нашего процесса разработки», — прокомментировал Якоб Меллер Хансен, вице-президент по исследованиям и разработкам в ECCO. Далее он отметил: «В поисках подходящего партнера мы протестировали различные 3D-принтеры на предмет качества поверхности, скорости печати и точности. Среди протестированных нами принтеров Stratasys Origin One был 3D-принтером, который лучше всего соответствовал нашим строгим требованиям.
3D-принтер Origin One (фото предоставлено Origin)
ECCO и Stratasys используют инновационные технологии для обуви
Используя процесс прямого впрыска (DIP) и 3D-печать, ECCO стремится упростить процесс разработки и повысить уровень автоматизации. В то время как DIP предлагает возможность улучшить метод крепления верхней части обуви к межподошве, аддитивное производство позволяет быстро производить формы из фотополимеров с меньшими затратами, чем обработка алюминия с ЧПУ.С помощью 3D-печати DIP-форм одну пару вкладышей можно напечатать за ночь, что, по понятным причинам, значительно более экономично. Кроме того, дизайнеры и разработчики могут тестировать функциональную обувь на ранних этапах процесса разработки.
Для изготовления этих пресс-форм компании используют специальные материалы, разработанные Henkel. Согласно пресс-релизу, специальные материалы Henkel дали ECCO возможность создавать формы для обуви, способные выдержать тысячи выстрелов без видимых повреждений.А с помощью 3D-печати ECCO надеется добиться значительной экономии средств при одновременном сокращении времени производства. Цели, которые разделяют многие компании, использующие аддитивное производство для разработки товаров повседневного спроса. Вы можете узнать больше об этом ЗДЕСЬ.
*Фото на обложке: Stratasys
Что вы думаете о партнерстве между ECCO и Stratasys? Сообщите нам об этом в комментариях ниже или на наших страницах в LinkedIn, Facebook и Twitter! Не забудьте подписаться на нашу бесплатную еженедельную рассылку здесь, чтобы получать последние новости о 3D-печати прямо в свой почтовый ящик! Вы также можете найти все наши видео на нашем канале YouTube .
Adidas построил высокопроизводительную «Скоростную фабрику» для производства своей обуви — Quartz
Ансбах, Германия
Кроссовки производятся не на одной фабрике. Они являются продуктом разветвленной сети специализированных поставщиков, часто в разных городах или даже в разных странах, которые собирают различные компоненты в спортивную обувь. Всего одна часть, например подошва, могла пересечь большие участки Азии, прежде чем стать частью кроссовок, которые вы купили.
«На одной фабрике вы создаете свою резину, а затем резине придают определенную форму. Межподошва создана. В другом месте межподошва и нижняя часть объединены», — объясняет Ульрих Штайндорф, старший директор по производству Adidas.
Изготовление обуви с использованием этого традиционного процесса от начала до конца может занять 60 дней. Люди до сих пор выполняют большую часть сшивания, склеивания и других трудоемких процессов вручную. Даже после того, как обувь будет готова, потребуется еще 60 дней, чтобы отправить ее из Азии, где производится большинство кроссовок, в магазины Западной Европы или США.
«Если мы хотим быстрее и гибче делать то, что хотят и в чем нуждаются наши спортсмены, мы должны переосмыслить то, как мы производим продукты».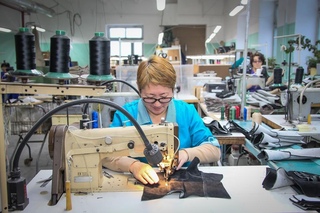
Пару лет назад высшие умы Adidas решили, что эта неуклюжая и неэффективная модель слишком ограничена. «Вот почему мы изучили доступные технологии и решили: «Эй, если мы хотим быть быстрее и гибче в выполнении того, чего хотят и в чем нуждаются наши спортсмены, тогда мы должны переосмыслить то, как мы производим продукты», — говорит Герд Манц. руководитель отдела технологических инноваций в команде Adidas Future, которая определяет курс компании на три-семь лет вперед.
Инновации, которые Adidas внедрила с тех пор, в значительной степени объединяют в Speedfactory. Это новаторская концепция, которая концентрирует процесс производства кроссовок в одном пространстве и на рынке, где продается обувь. На Speedfactory Adidas в Ансбахе, Германия, роботы выполняют большую часть работы. По сравнению с тем, что изготовление кроссовок в традиционной цепочке поставок может занять месяцы, Speedfactory завершает производство за считанные дни.
Новые фабрики — лишь часть большой смены. В течение примерно 40 лет производство кроссовок практически не менялось. Но теперь эксперты считают, что отрасль достигла переломного момента, чему способствовало распространение электронной коммерции и социальных сетей, которые ускорили циклы моды и научили покупателей ожидать мгновенного доступа к постоянному потоку новых продуктов. Adidas тестирует различные идеи, работая над тем, чтобы сделать свою работу быстрее и гибче, чтобы соответствовать требованиям этой новой эры. Сегодня она объединяет практически все основные тенденции, преобразующие цепочки поставок, включая 3D-печать, массовую настройку на заказ, близость к источникам и оцифровку операций.
И не только. Adidas противостоит своему заклятому сопернику Nike, который аналогичным образом трансформирует свою работу с помощью Flex, новатора в области цепочки поставок и логистики. Два лейбла идут ноздря в ноздрю в авангарде инноваций в разработке и производстве спортивной обуви. По оценкам Morgan Stanley, к 2023 году они смогут производить почти 20% своих кроссовок на «более автоматизированных» фабриках.
Технологии развиваются так быстро, что трудно предположить, как будут выглядеть ближайшие несколько лет.Но Speedfactory — это попытка преодолеть пустоту.
«Мы хотели создать фабрику будущего, — говорит Манц. «Это должно быть репрезентативным для всех наших заводов через 5-10 лет».
Внутри фабрики будущего Adidas
Два года назад, когда компания задумала идею Speedfactory, участок земли, на котором Adidas хотел построить здание, был картофельным полем. Сегодня на этом месте стоит невзрачное белое здание, носящее имя Охслер, немецкая фирма Adidas сотрудничала при его строительстве.
Охслер сыграл важную роль в создании роботов и производстве, организованном в здании площадью около 4600 квадратных метров (около 49 500 квадратных футов), задачах, выходящих за рамки специальных знаний Adidas. Партнерство, по сути, является примером одного из новых руководящих принципов производителя кроссовок, который он называет «открытым исходным кодом». Это означает обмен идеями и, при необходимости, сотрудничество со сторонними экспертами. На самом деле Oechsler начал свою деятельность в середине 19-го века как производитель роговых пуговиц, но теперь специализируется на явно более современной области литья пластмасс под давлением.Компания разрабатывает и производит детали для автомобильных, медицинских и промышленных компаний по всему миру и уже много лет сотрудничает с Adidas. Adidas заявляет, что у него есть опыт и стремление к инновациям, которые Adidas хотел найти в партнере для создания своего автоматизированного завода.
Это, несомненно, было дорогостоящим мероприятием, хотя ни одна из компаний не сообщила, сколько стоило строительство Speedfactory. (Они разделили расходы.) Adidas указал только на 164 миллиона евро (около 173 миллионов долларов на тот момент), которые он потратил на исследования и разработки в 2016 году.Speedfactory является частью этой суммы, которая представляет собой резкий рост затрат на НИОКР по сравнению с предыдущими годами (pdf, стр. 75).
Сама идея построить завод в Германии была смелым шагом для Adidas. Бренды кроссовок обычно занимаются дизайном, маркетингом и долей продаж, но оставляют фактическое производство кому-то другому. Этот кто-то почти всегда находится в Азии, где в 1980-х годах стало нормой передавать трудоемкую производственную работу на аутсорсинг, поскольку стоимость рабочей силы низка, а сейчас создана огромная инфраструктура, особенно в Китае.Согласно последним данным, полученным от компании, в 2016 году Adidas закупил 97% своей обуви в Азии, и именно там в обозримом будущем останется основная часть производства.
Speedfactory — почти полная противоположность этому стандарту. Adidas по-прежнему приходится импортировать сырье и отдавать на аутсорсинг некоторые процессы, такие как вязание ткани для верха. В остальном вся работа происходит на фабрике Adidas, прямо здесь, в Германии, а теперь и в США, где недавно открылась фабрика Speedfactory в Атланте.Adidas также говорит, что процессы, которые в настоящее время не являются частью установки, такие как вязание ткани для верха или 3D-печать промежуточных подошв, могут быть легко интегрированы. Это делает Adidas значительно быстрее и гибче в производстве обуви.
От идеи к реальности
Кроссовки в Speedfactory собраны так просто, что трудно понять, почему никто не пробовал эту концепцию раньше. Но Adidas пришлось немало потрудиться, чтобы воплотить это в жизнь. «Многих из этих процессов [в производстве кроссовок] не существует», — говорит Манц.
Adidas пришлось создавать новые способы обработки материалов машинами и решать другие основные проблемы. Используемые роботы, возможно, уже широко используются в других отраслях, но их нужно было адаптировать для изготовления кроссовок. Для производства автомобилей, электроники или полупроводников роботы могут использовать магниты, пылесосы или механические захваты для перемещения деталей. Но материалы в этих отраслях, как правило, жесткие или довольно однородные. Эти методы плохо работают при работе с различными мягкими и гибкими тканями.Adidas и его партнеры должны были создать новые способы обработки материалов для машин и решения других основных проблем. (Столкнувшись с той же проблемой, Nike недавно начала устанавливать роботизированные технологии на некоторых контрактных фабриках, которые используют электроадгезию — в основном статическое сцепление — для обработки деталей кроссовок.)
Цифровые технологии также были неотъемлемой частью создания Speedfactory. Adidas в партнерстве с технологической компанией Siemens построил виртуальную копию завода в Ансбахе. «Мы можем смоделировать каждый аспект вплоть до машинного уровня того, как мы можем оптимизировать настройку и компоновку на заводе и, следовательно, производственный поток, что в конечном итоге должно помочь нам, с одной стороны, оптимизировать затраты, а с другой стороны, иметь качество продукта», — говорит Майкл Фогеле, директор по информационным технологиям Adidas.
По мере того, как Speedfactory работает, каждая деталь, которую он производит, помечается сканируемым QR-кодом. Во время проверки контроля качества, если возникает проблема, они могут отследить деталь до машины, на которой она была изготовлена, и узнать, какие настройки были на машине. По мере того, как Speedfactory производит все больше и больше обуви, Adidas сможет постоянно совершенствовать свои процессы, сокращая количество бракованных деталей, которые не соответствуют стандартам, и повышая качество конечного продукта.
Никто другой в отрасли не делает ничего подобного, по словам Маника Арьяпади, директора розничной практики A.T. Kearney, глобальная консалтинговая фирма по вопросам стратегии и управления, работающая с крупнейшими игроками индустрии спортивных товаров. Бренды обуви и одежды часто заставляют своих поставщиков встраивать RFID-метки в готовую продукцию, чтобы в случае обнаружения дефектов они знали, какая фабрика несет за это ответственность. Но делать это на уровне компонентов — это практика, которую вы видите в высокотехнологичных отраслях, таких как полупроводники.Ни один другой бренд не реализовал настолько полную автоматизацию и не воспроизвел фабрику в цифровом виде, чтобы оптимизировать ее. «Adidas находится на переднем крае, — говорит он.
Автоматизация имеет преимущества помимо скорости; он также предлагает механизированную точность. Джеймс Карнс, вице-президент Adidas по стратегии, сказал во время тура по Speedfactory, что на обычной обувной фабрике в Китае подошва и верх соединяются клеем вручную. «Процесс заключается в том, что кто-то стоит там и идет…» — говорит он, имитируя человека, пытающегося на глаз выровнять подошву и верх.«Это действительно неточный процесс». Adidas также по возможности избегает использования клея. Это грязно и медленно, нужно время, чтобы высохнуть, поэтому Adidas предпочитает сплавлять части, когда это возможно.
Поскольку большая часть работы автоматизирована, Adidas нуждается в меньшем количестве рабочих, чем на многих фабриках по производству кроссовок в Азии. В Ансбахе работает 160 сотрудников. На фабриках в Китае и Вьетнаме обувные фабрики обычно имеют более 500 рабочих или даже более 1000 (pdf, стр.9).
Работники Ансбаха тоже, как правило, работники совсем другого склада. Профили должностей, которые Adidas и Oechsler использовали для найма, были распространены в других отраслях, таких как автомобилестроение, где автоматизация распространена, но новы для мира кроссовок, говорит Штайндорф. Компания Oechsler, работающая в автомобильной промышленности, помогла с подбором персонала. Многие из претендентов были сотрудниками Oechsler, жаждущими попробовать что-то новое.
Настоящая инновация — это не продукт, а процесс
Первые кроссовки Speedfactory поступили в продажу в сентябре 2016 года.Названные Futurecraft MFG, как в «Сделано для Германии», поскольку они были эксклюзивными для страны, они были своего рода публичным бета-тестированием всего 500 пар. С тех пор Adidas выпустила пары, предназначенные для Лондона и Парижа, AM4LDN и AM4PAR, и в других городах.
В настоящее время Speedfactory сосредоточена на таких кроссовках премиум-класса. Фактически, линия AM4 была разработана для автоматизированной установки Speedfactory. Обувь состоит всего из нескольких компонентов и может быть собрана за минимальное количество шагов. В настоящее время Adidas все еще наращивает производство, но ожидает, что фабрики в Ансбахе и Атланте вскоре будут производить по 500 000 пар кроссовок в год.
Однако эти количества показывают один из пределов Speedfactory. Один миллион пар кроссовок — это лишь малая часть из примерно 360 миллионов пар обуви (pdf, стр. 69), которые поставщики Adidas произвели для компании в 2016 году. Хотя это число, вероятно, будет еще больше в 2018 году, когда Speedfactories, наконец, заработают на полную мощность. объем производства.
Speedfactory также не может производить многие другие стили кроссовок Adidas, такие как популярные ретро-модели, которые были самыми продаваемыми за последние несколько лет. «Если вы возьмете пример Superstar или Stan Smith, то это резиновая подошва», — говорит Стейндорф. «За этим стоит другой вид процесса присоединения, где у нас просто еще нет решения». Инфраструктура, которая уже существует в Азии для создания этих типов кроссовок, также просто делает более выгодным их производство там. В настоящее время Speedfactory в Ансбахе настроена только на производство подошв Boost. Вскоре он также добавит процесс 3D-печати «цифровой синтез света», разработанный Carbon.
Несмотря на все, что Adidas делает со Speedfactory, производство кроссовок также вряд ли вернется в Европу или США в больших масштабах. «Я не верю, и это полная иллюзия верить, что производство может вернуться в Европу с точки зрения объема», — публично заявил генеральный директор Adidas Каспер Рорстед во время недавней поездки в Азию (платный доступ).«И это касается всей отрасли, я говорю не только об Adidas».
Так может ли Speedfactory серьезно повлиять на бизнес Adidas?
Мэтт Пауэлл, вице-президент и аналитик спортивной индустрии исследовательской компании NPD Group, является известным экспертом по кроссовкам и, как известно, скептически относится к ценности разрекламированных, но ограниченных усилий. Но он считает, что Speedfactory в сочетании с другими инновациями, над которыми работает Adidas, особенно с партнерством с инновационной фирмой Carbon, занимающейся 3D-печатью, может дать огромные преимущества.
«Сейчас требуется 18 месяцев от концепции до розничной продажи, прежде чем продукт попадет на рынок, если все пойдет хорошо — а это никогда не идет хорошо», — объясняет он. «И то, что мы видели за последние несколько лет, это то, что циклы моды действительно сжимаются. В качестве примера я использую результативный баскетбол. [Это] действительно началось в начале 2012 года, и эта тенденция закончилась к середине 2015 года.Если подумать, в индустрии, где циклы моды длятся всего три года, а на то, чтобы довести продукт от концепции до розничной продажи, уходит 18 месяцев, эти две вещи действительно противоречат друг другу».
Пауэлл говорит, что Speedfactories должны помочь Adidas адаптироваться к этому сокращенному циклу таким образом, чтобы это имело значение, даже если они не производят десятки миллионов кроссовок в год. Во-первых, они позволяют Adidas быстро создавать и тестировать новые продукты. (В этом также помогает 3D-печать: она позволяет Adidas просто печатать подошвы для прототипов и отказаться от инструментов — дорогостоящего и трудоемкого этапа изготовления металлической формы, используемой для изготовления подошв при обычном производстве кроссовок.) Во-вторых, вскоре они позволят Adidas быстро реагировать на то, как люди совершают покупки на рынках, где расположены Speedfactory.
Поскольку Speedfactory позволяет компании быстро экспериментировать с новыми кроссовками, Манц описывает ее как «инновационную платформу». Adidas не обязательно производить 50 000 экземпляров одного стиля и иметь полный план маркетинга и дистрибуции на 18 месяцев вперед. Он может придумать концепцию, создать несколько сотен или нескольких тысяч пар и посмотреть, как все пойдет.
Масштабирование Speedfactory — это не просто создание большего их количества. Scaling Speedfactory — это не только создание большего их количества. Там они могут тестировать и оптимизировать методы производства, а затем внедрять то, чему они научились на контрактных фабриках, которые они используют в Азии, повышая их устойчивость и производительность. Они уже работают над установкой определенных процессов за границей.
Не менее важно и то, что Speedfactories скоро смогут быстро пополнять запасы в Западной Европе и США.Эта возможность позволила бы Adidas пополнить запасы стилей или размеров всего за несколько недель или дней, а не месяцев. Это также может означать, что Adidas не нужно будет заранее производить огромный объем запасов и вкладывать деньги в акции, не будучи уверенными, что они будут проданы.
Эта бизнес-модель помогла брендам быстрой моды доминировать и трансформировать остальную часть индустрии одежды, и она может дать значительный толчок бизнесу Adidas. В своем отчете о том, как производители кроссовок ускоряют производство, Morgan Stanley подсчитал, что переход на эту модель производства может дать брендам дополнительный 15-процентный рост продаж, а также всевозможные логистические преимущества.Adidas заявил, что к 2020 году планирует получать 50% своих продаж за счет продукции, обеспечивающей скорость.
«Бизнес-модель, я думаю, это то, что меня волнует», — говорит Карнс, вице-президент по стратегии. Если компания может достичь точки производства значительной доли продуктов, которые она продает по запросу, объясняет он, а не производить их заранее, «у нее будут совершенно другие последствия для бизнес-модели с точки зрения времени доставки, денежного потока. , настройка вашего бизнеса, как вы можете управлять запасами.
Именно благодаря таким преимуществам Пауэлл считает, что Speedfactory может существенно повлиять на прибыль Adidas, даже если цифры еще не приблизились к критической точке продаж.
В конце концов, цель Adidas состоит в том, чтобы иметь возможность производить обувь по индивидуальному заказу, где 3D-печать снова может стать незаменимой. Если Adidas не нужно создавать инструменты для подошвы, внезапно становится возможным адаптировать кроссовки к ноге клиента. Кроссовки будут дорогими и вряд ли будут массовым продуктом.Но для спортсменов с особыми потребностями это может стоить затрат.
Для Adidas этот сдвиг лежит в основе эволюции самих инноваций. «Инновации полностью изменились, — говорит Манц, отметивший в ноябре свое 20-летие в Adidas. «Это полностью изменилось — и это также, вероятно, представитель отрасли, которую мы пытаемся возглавить в инновациях — от ингредиентов к продуктам, больше к процессам и бизнес-моделям.
Другими словами, создание более качественного продукта сегодня зависит не столько от того, какой новый амортизирующий материал сейчас популярен, сколько от того, чтобы весь бизнес был настроен так, чтобы быстро определять, чего хотят клиенты, и быстро доставлять им это.
Использование дизайна обуви в качестве примера
Развитие 3D-технологии принесло возможности и проблемы в обувную промышленность, поскольку уровень жизни людей повышается благодаря экономическому развитию, и люди предъявляют более высокие требования к дизайну модной обуви и ботинок. Использование технологии 3D-печати в дизайне модной обуви и ботинок может обеспечить более быстрое формование обувных изделий, обогатить форму обуви и удовлетворить эстетические потребности людей в модной обуви. В этой статье мы сначала описываем преимущества 3D-печати формованных моделей обуви, а затем используем 3D-лазерный сканер стопы и измерительный прибор для сканирования и получения облачной карты обувных колодок и данных, связанных со стопой. Во-вторых, мы осуществляем цифровое управление обувными колодками, создавая базу данных твердых моделей.Исходя из этого, мы применяем алгоритм усовершенствования машины опорных векторов технологии наименьших квадратов, чтобы внести частичные модификации в колодки в соответствии с необходимостью оставить соответствующие степени вспомогательной и подкладочной подошвы. Наконец, на основе этой технологии мы применяем технологию алгоритма улучшения машины опорных векторов методом наименьших квадратов, чтобы внести частичные изменения в форму колодки в соответствии с необходимостью соответствующих степеней подкладки подкладки и подкладки для реализации процесса изменения конструкции колодки.
Последняя модель и образец для подражания также могут быть изготовлены с помощью технологии 3D-печати, которую можно использовать в качестве формы для облегчения обработки вырезанного последнего 2D-разворачивающегося материала для последующего производства обуви и ботинок. Поэтому в статье изучается и анализируется процесс проектирования и производства цифровых обувных колодок на основе индивидуальной формы стопы и с использованием технологии CAD/CAM для реализации оцифровки дизайна обувных колодок.
1. Введение
С постоянным улучшением качества жизни людей требования людей к обуви и ботинкам становятся все выше и выше, а также люди выдвигают более высокие требования к дизайну модной обуви [1].С развитием технологии 3D-печати люди осознают важность технологии 3D-печати, и уровень признания также растет. Технология 3D-печати может сыграть важную роль в области производства обуви [2].
В настоящее время обувные колодки, выпускаемые в больших количествах обувными предприятиями и фабриками, проектируются и изготавливаются по соответствующим моделям обувных колодок и стандартам проектирования. Соответствующие данные, приведенные в этих последних стандартах проектирования, в основном сформулированы в соответствии со статистическими законами и опытом [3, 4, 5].В результате получается одна и та же модель туфель и сапог, изготовленных из одной и той же модели обувных колодок. Кто-то носит их по размеру, а кто-то не по размеру. Длительное ношение обуви, не соответствующей физиологическому состоянию стопы человека, не только вызовет ощущение дискомфорта, но и серьезно повлияет на развитие и формирование костей стопы человека, а для людей с заболеваниями стоп неподходящая обувь и ботинки могут даже ухудшить их симптомы и привести к серьезным последствиям [6].Для спортсменов и других специальных групп неподходящая обувь может существенно повлиять на спортивные результаты. Кроме того, обувь и сапоги постепенно становятся модным трендом, который является преподнесением тела и носителем красоты. При разработке моделей туфель и ботинок необходимо учитывать не только их удобство, но и требование эстетического оформления, когда они производятся как товары повседневного пользования [7, 8], но способов количественной оценки красоты пока не хватает.
в текущем производстве обувных колодок, что объективно затрудняет достижение идеального дизайна.С постепенным улучшением жизненного уровня людей соответственно возрастают требования к обуви и ботинкам. Мода и персонализация стали тенденцией развития, и разумное использование 3D-технологий может сделать их более совершенными.
Технология 3D-печати зародилась в США в 1980-х годах. В начале этого века, с развитием основных технологий, таких как светоотверждаемое стереоскопическое литье, селективное лазерное спекание и моделирование осаждения расплавленных нитей, технология 3D-печати постепенно развивалась [9, 10].В 2007 году Objet Geometries выпустила систему Connex500TM, которая поддерживает одновременную печать нескольких модельных материалов. Objet Geometries запустила систему Connex500TM, которая поддерживает одновременную печать нескольких модельных материалов. В настоящее время 3DSystems, Stratasys, HP Inc., MakerBot, EOS, SLM Solutions в Германии и Objet в Израиле находятся в авангарде в этой области [11, 12]. В развитых странах, таких как Европа и США, технология 3D-печати широко применяется в различных областях; с развитием технологии 3D-печати в Китае она стала применяться в различных областях, таких как биология, медицина, национальная оборона, аэрокосмическая промышленность, образование, культура и творчество, архитектура, одежда, продукты питания, и продемонстрировала превосходную производительность и хорошие рыночные перспективы. [13].
По сравнению с традиционными методами производства 3D-печать может значительно сократить производственный цикл, что способствует удобной и эффективной разработке продуктов. Однако, с другой стороны медали, мы также должны увидеть, что после быстрого развития 3D-печати в последние несколько лет и погони за рынком возник ряд проблем, таких как высокая стоимость, узкие места в массовом производстве, ограничительные технологии. и материалы, а также быстрое увеличение капитала и рыночная шумиха — всем этим еще предстоит вернуться к рациональному и прагматическому отношению.
2. Related Progress
Использование технологии 3D-печати для верхней части спортивной обуви все еще очень ограничено, но эта технология является актуальной задачей в области производства спортивной обуви, и Nike в настоящее время находится в авангарде . Будучи первым спортивным брендом, внедрившим технологию 3D-печати, Nike в 2013 году разработала первое поколение 3D-печатных футбольных бутс, «новый Nike Vapor LaserTalon» и бутсы для регби «Vapor Laser Talon». После этого Nike выпустила «Vapor Carbon 2014». элитные кроссовки и футбольные бутсы VaporHyperAgility [14, 15].Он предоставил известному американскому спринтеру Эллисон Феликс футбольные бутсы, напечатанные на 3D-принтере. Перед Олимпийскими играми в Рио Nike разработала эксклюзивную пару высокопроизводительных шиповок «Zoom Superfly Flyknit» для известной американской спринтерки Эллисон Феликс, чтобы удовлетворить ее потребности в соревнованиях, что в конечном итоге помогло «женщине-летчику» выиграть олимпийский чемпионат [16]. В 2016 году Nike объявила о стратегическом партнерстве с гигантом печати Hewlett-Packard, чтобы использовать принтер HPJet Fusion3D для повышения эффективности прототипов обуви и снижения затрат.
В 2018 году Nike даже открыла новые горизонты, выпустив кроссовки Flyprint, которые отличаются от предыдущих кроссовок, напечатанных на 3D-принтере, тем, что в них используется технология твердотельного моделирования (SDM) для создания верха [17]. .
В 2015 году компания Adidas выпустила кроссовки Futurecraft 3D, напечатанные на 3D-принтере, а в конце 2016 года поступила в продажу ограниченная серия 3D Runner. Эти кроссовки можно адаптировать к строению стопы пользователя и личным спортивным привычкам [18]. , 19].Обувь может быть адаптирована к структуре стопы пользователя и личным спортивным привычкам с верхним плетением «Primeknit», а подошва и полая промежуточная подошва изготовлены с использованием технологии 3D-печати.
Следуя за волной технологии 3D-печати, Andromeda также выпустила кроссовки «UA Architech» ограниченной серии в марте 2016 года и пару 3D-печатных кроссовок для американского пловца Майкла Фелпса в том же году [20]. В 2017 году компания выпустила новое поколение 3D-печатных кроссовок ArchiTech Futurist, которые имеют 3D-печатную промежуточную подошву с блокирующей сетчатой структурой, которая обеспечивает «платформу динамической стабильности» для лучшей устойчивости и амортизации, а также цельный, цельный. бесшовный верх для превосходной посадки.Reebok использует технологию 3D-рисования, чтобы четко и точно «рисовать» компоненты обуви на уровне 3D. Эта запатентованная технология наслоения обеспечивает эффективное, быстрое и простое создание персонализированной обуви без использования пресс-форм. Кроссовки оснащены подошвой с высоким отскоком и шнурками, напечатанными на 3D-принтере, которые объединяют подошву с верхом для всестороннего комфорта стопы и отзывчивой обратной связи энергии [21].
В апреле 2016 года компания New Balance усовершенствовала свои напечатанные на 3D-принтере концептуальные кроссовки «Fresh Foam Zante», переименовав их в «Zante Generate» для ограниченного публичного выпуска.
В начале 2018 года Anta также представила печатное оборудование Uniontech, которое в основном используется для исследований и разработок обувной продукции. В июне 2018 года Li Ning представила последнюю версию своей серии «Reignited» на Неделе моды в Париже с каркасной подошвой, изготовленной с помощью технологии 3D-печати, и прозрачным пластиком для внешнего слоя верха. Использование обоих материалов в самый раз, создавая впечатление моды, технологичности и молодости [22, 23].
В дополнение к крупным брендам спортивной обуви в стране и за рубежом существует множество связанных организаций в стране и за рубежом, проводящих аналогичные исследования, в том числе многие компании и бренды, которые разрабатывают нишевые профессиональные спортивные товары, также стараются изо всех сил использовать технологию 3D-печати в области дизайна и производства обуви как можно раньше.
2.1. Преимущества и ограничения технологии 3D-печати в дизайне и производстве спортивной обуви
Технология 3D-печати является типичным «аддитивным производством». Это может быть высокоэффективный, энергосберегающий, распределенный, персонализированный способ производства продукции по требованию, изменяющий предыдущую крупномасштабную и централизованную промышленную модель, что способствует снижению затрат на рабочую силу в обрабатывающей промышленности низкого уровня и быстрому развитие инновационных малых предприятий [24].В то же время технология 3D-печати позволяет избежать сложного и трудоемкого процесса разработки и производства пресс-форм. С дальнейшим развитием этой технологии эффективность и качество печати будут улучшаться, поэтому цикл производства спортивной обуви будет еще больше сокращаться, что также означает дальнейшее увеличение скорости итерации продукта.
В последние годы технология 3D-печати стала горячей темой в области проектирования и производства, объединив множество специализированных исследовательских институтов и специалистов.Связанные с ним технологии постоянно развиваются. Например, до кроссовок Nike Flyprint почти вся 3D-печать была сосредоточена на подошвах спортивной обуви. Тем не менее, они использовали производство методом твердого осаждения, чтобы создать идею перевода данных о форме стопы и движениях спортсменов в геометрию ткани и сбора данных с помощью инструментов вычислительного проектирования для достижения идеального соотношения материалов [25]. Данные также были собраны с помощью инструментов вычислительного проектирования для достижения идеального соотношения материалов.Производительность обуви также можно регулировать на более позднем этапе, добавляя или удаляя «основную и уточную пряжу» по мере необходимости, а процесс печати примерно в 16 раз эффективнее, чем предыдущие производственные процессы.
Благодаря углубленному исследованию технологии 3D-печати считается, что с ее новыми технологиями и методами некоторые трудности в производстве спортивной обуви могут быть решены и оптимизированы, чтобы помочь достичь лучших характеристик продукта и эффектов дизайна внешнего вида [26]. .
3. Преимущества технологии 3D-печатного моделирования для моделирования обуви
Традиционный производственный процесс при производстве обуви и сапог состоит в основном из проектирования, изготовления моделей, раскроя, шитья и формовки. Весь процесс производства книги занимает много времени и очень сложен. Сочетание технологии 3D-моделирования и технологии 3D-печати позволяет быстро реализовать первоначальное производство пресс-форм и проверить эффект, тем самым сократив время, затрачиваемое на производство обуви, повысив конкурентоспособность обувных и обувных предприятий в жесткой рыночной конкуренции и способствуя дальнейшему развитию. родственные предприятия [1, 9, 27].
(2) Преимущества моделирования обуви имеют большие преимущества с точки зрения свободы. Использование программного обеспечения и технологий 3D для моделирования обуви позволяет создавать и изменять форму обуви или ботинка в соответствии с требованиями дизайна. Некоторые продукты имеют сложную форму формы перед производством, и технология 3D-моделирования может использоваться для их лучшего проектирования. Технология 3D-моделирования необходима для более быстрой и качественной интеграции элементов моды [13, 28].
При изготовлении модной обуви и сапог трудно сочетать некоторые традиционные формы традиционными методами ручного проектирования, а многоугольные структуры поперечного сечения нельзя использовать в качестве моделей для изготовления обуви. Кроме того, обувь изготавливается из открытых панелей, которые подвержены проблеме неравномерного комбинирования форм и, следовательно, плохой интеграции геометрии [3]. Таким образом, технология обработки, по-видимому, играет большую роль в производстве обуви в современном обществе и является реалистичной и важной движущей силой в ее развитии и продвижении, которая может эффективно продвигать отрасль вперед.
3.1. Алгоритм усовершенствования машины опорных векторов методом наименьших квадратов
SVM по сути является моделью классификации на основе машинного обучения [7], которая широко используется в области статистической классификации и регрессионного анализа [29].Он достигает классификации набора данных, находя гиперплоскость, которая удовлетворяет требованиям классификации, так что различные типы точек выбранного обучающего набора находятся как можно дальше относительно плана классификации (см. рисунок 1).
Алгоритм метода опорных векторов наименьших квадратов (LS-SVM) представляет собой вариант стандартного SVM, который преобразует SVM для решения линейной системы уравнений, избегая использования нечувствительных функций потерь и значительно снижая вычислительную сложность .
Конкретный вывод алгоритма LS-SVM выглядит следующим образом.
Для заданных N обучающих выборок, где – вход n-мерной обучающей выборки, а – выход обучающей выборки, в данной статье , где обозначает первый переменный фактор в i-й обучающей выборке, обозначает второй переменный фактор в i -й обучающей выборки, а обозначает второй переменный фактор в i-й обучающей выборке.
Целевая функция оптимизации алгоритма LS-SVM имеет вид, где φ ( ) — функция отображения пространства ядра, — весовой вектор, — переменная ошибки, b — смещение, µ и γ являются регулируемыми параметрами.Чтобы найти минимум функции, постройте функцию Лагранжа: где множитель Лагранжа.
Частная производная уравнения (3) дает
Путем исключения и e решенная задача оптимизации преобразуется в решение линейного уравнения:где
LS-SVM для оценки функции получается путем решения уравнения (5) а затем, где k ( x , ) — это функция ядра. Обычно используемые функции ядра в основном полиномиальные, RBF (радиальный базис), сигмовидные и так далее.Обычно используется функция ядра радиального базиса:
LS-SVM, основанный на функции ядра радиального базиса, должен определить два параметра: штрафной коэффициент γ и параметр ядра [8]. Параметр ядра является автономным параметром функции ядра радиального базиса, который в основном определяет фактический размер размерности результирующего эффекта после отображения. Чем больше, тем быстрее уменьшается вес признаков более высокого уровня, что эквивалентно отображению в низкоразмерное подпространство; и наоборот, чем он меньше, тем более линейно делимыми будут результаты произвольного отображения данных.Выбор γ , в основном для процесса сегментации, может заключаться в особенности введения мягкой интервальной гиперплоскости и определять степень допуска точности поверхности сегментации. γ больше, что указывает на то, что процесс сегментации для выбора допуска ошибки опорного вектора увеличивается, что приводит к неточной сегментации; в противном случае это может привести к тому, что сегментация не будет завершена.
Для определения γ и , традиционный алгоритм обычно использует метод поиска по сетке.Здесь мы улучшаем генетический алгоритм для оптимизации выбора параметров γ и используем точность классификации с трехкратной перекрестной проверкой в качестве функции приспособленности. Диапазон значений γ составляет (0,01–100), а диапазон значений — (0,01–100).
Генетический алгоритм (GAA) — это эвристический алгоритм, основанный на естественном отборе и естественных генетических механизмах в биологии. Он удобнее, надежнее и проще в параллельной обработке, чем традиционные методы, такие как поиск по сетке.При работе с двумя параметрами модели γ и σ машины опорных векторов мы сначала инициализируем параметры модели, устанавливаем двоичный код, рандомизируем начальную совокупность параметров модели и обучаем модель машины опорных векторов. Генетический алгоритм представляет собой максимизацию функции пригодности для оптимизации, в то время как выбор параметров модели опорного вектора представляет собой задачу оптимизации минимизации, поэтому выполняется следующее преобразование:
После вычисления функции пригодности оценивается глобальное оптимальное решение. , и если условие выполняется, определенные параметры γ и σ включаются в обучение модели машины опорных векторов.В противном случае регенерация популяции, отбор, скрещивание и вариация выполняются итеративно до тех пор, пока не будет выполнено условие окончания, а вычислительные эффекты сравниваются в таблице 1. . метод
3.2. Цифровая колодка Дизайн и производственный процесс
Колодка сложна. Разнонаправленная неравномерно скрученная свободно-замкнутая поверхность с длинными краевыми линиями, множеством характерных областей и резкими изменениями кривизны [2] вызывает трудности в процессе ее проектирования, в том числе (1) плохой контроль внешней формы и плохой плотности и (2) не способствует к быстрой локальной модификации колодки и неудобному дизайну персонализированных колодок в соответствии со специальной формой стопы. Таким образом, проектирование обувных колодок с помощью автоматизированного проектирования (CAD) и автоматизированного производства (CAM) стало проблемой и горячим вопросом для обсуждения в последние годы. Процесс проектирования и производства обувных колодок основан на характеристиках обувных колодок и опыте традиционного процесса производства обуви. В этом документе процесс проектирования и производства обувных колодок резюмируется в следующие этапы: (1) Возьмите человеческую ногу в качестве прототипа конструкции: сначала используйте трехмерный лазерный сканирующий измерительный прибор для измерения данных о форме человеческой стопы, а после обработки данных сформируйте обувь. последняя облачная модель для завершения оцифровки человеческой стопы.(2) После изменения модели стопы человека в соответствии с требованиями данные будут переданы в CAM для создания программы ЧПУ и переданы в управляющий компьютер режущего станка. Для резки будет использоваться вибрационная машина для резки, и может быть обработана последняя секция 2D развернутой обуви.
(3) Различные форматы файлов (например, шпилька, ее форматы файлов) генерируются САПР. Обувные колодки можно вырезать с использованием передовой технологии производства CAM, или модели обувных колодок могут быть изготовлены на 3D-принтерах, в соответствии с которыми изготавливаются соответствующие формы обувных колодок, и формы используются для восстановления обувных колодок.
Конкретные этапы проектирования показаны на рисунке 2.
3.3. Методы измерения и обработка данных
Процесс от человеческой стопы до обувной колодки относится к разновидности обратного проектирования; то есть в качестве объекта проектирования используется стопа человека, а колодка проектируется и изготавливается, в свою очередь, для получения обувной колодки [4]. В этом процессе используются две ключевые технологии: (1) метод получения данных, относящихся к поверхности стопы человека; (2) технология построения поверхности колодки на основе данных о стопе человека и необходимость решения технической проблемы передачи необработанных данных, полученных при измерении, в систему CAD/CAM. В настоящее время существует два метода измерения данных, связанных с геометрией стопы: измерение контактным датчиком (например, механическим измерительным прибором КИМ) и бесконтактным измерением датчика (например, фотоэлектрическим сканером и лазерным сканером) [5, 6]; учитывая особенности мышц стопы человека, более целесообразно использовать измерение лазерным сканером, который характеризуется высокой скоростью сканирования и удобным измерением размера стопы и может проводить интенсивное сканирующее измерение поверхности стопы человека.Лазерный сканер характеризуется высокой скоростью сканирования, удобным измерением размера стопы и интенсивным сканированием поверхности стопы человека, что позволяет получить множество значений исходных данных в виде «облака точек». При обработке данных, во-первых, бесполезные и плохие точки в исходных данных оцениваются и устраняются в соответствии с опытом; во-вторых, файлы точек данных программируются для извлечения полезных данных, необходимых для моделирования в САПР, и передаются в систему САПР для моделирования кривых, поверхностей и твердых тел; и, наконец, получается цифровая CAD-модель прототипа, как показано на рисунках 3 и 4.
3.4. Колодка для обуви Моделирование дизайна Анализ
Анализируя строение стопы человека, мы видим, что ее ладонной поверхность плоская, но не совсем плоская, а поверхность стопы человека неровная и совершенно неровная. Тогда, как модель стопы человека, поверхности на последней форме везде разные, и кривизна сильно меняется. Имеются как гладкие участки поверхности, так и острые углы и грани, поэтому это типичная нерасширяемая поверхность произвольной формы.Для такой сложной формы, очевидно, если геометрическое моделирование полностью соответствует форме стопы человека [7], технически достаточно сложно и практически не нужно, и процесс можно соответствующим образом упростить. Как правило, длина и обхват стопы человека (обычно от верха до обхвата и переднего обхвата предплюсны) являются двумя основными параметрами, определяющими конструкцию колодки. Исходя из этого, для определенного типа стопы человека изменения колодки, необходимые для различных типов обуви, в основном основаны на изменениях колодки и высоты каблука, как показано на рисунке 4. Эти изменения приведут к изменению последней поверхности, и соответственно изменится поверхность точечной линии, описывающая последнюю поверхность. Таким образом, в качестве основных переменных параметров определяются тип носка и высота каблука. При моделировании последнюю поверхность можно разделить на различные части поверхности, такие как последняя поверхность подошвы, часть передней поверхности и часть задней поверхности. После их моделирования по отдельности каждая часть поверхности будет собрана вместе, чтобы сформировать последнюю форму. В процессе проектирования, учитывая, что обувь будет царапать лодыжки, чтобы позже производить обувь и ботинки на физической лодыжке без трения, вызванного пяткой обуви, кривизна и степень стопы помощника рассчитаны на пятку последний, кривизна пятки и линия стопы помощника изменяются в соответствии с характеристиками и потребностями стопы разных людей, так что можно сохранить соответствующую кривизну и угол стопы помощника [8], как показано на рисунке 5.
3D-эффект обуви, полученный с помощью программного обеспечения, показан на рис. 5.
4. Производительность 3D-печати
Как показано на рис. Эффект готовой печати все еще относительно ограничен, обычно для постобработки продукта используется шлифовка и цветное распыление, но в цвете и текстуре обработка текстурного эффекта все еще плохая, а насыщенность очень недостаточна.Несмотря на то, что текущая многоцветная многоцветная печать может быть достигнута, количество цветов и типов материалов расходных материалов по-прежнему относительно ограничено, часто высокая насыщенность цвета, что совершенно не соответствует характеристикам различных требуемых тонких межцветных, многоцветных, плашечных и популярных цветов. для спортивной обуви. Конечно, сложно добиться сложных цветовых эффектов и эффектов рисунка. Кроме того, из-за ограниченного количества материалов и многослойного способа плавления, что приводит к текстуре 3D-печатных изделий, производительность также является относительно монотонной, что не позволяет имитировать текстуру различных материалов для обуви, таких как аппаратные аксессуары, текстиль или кожа и другие материалы. различные декоративные процессы, отсутствие изменения фактуры.Следовательно, как печатать продукты на изысканной постобработке, чтобы обувь представляла более богатые и разнообразные визуальные эффекты для удовлетворения разнообразных потребностей потребительского рынка, также является одной из проблем, требующих решения.
Как показано на рис. 7, 3D-дизайн и технология печати могут максимально удовлетворить индивидуальные требования в отношении размера стопы, осанки и занятий спортом. В результате производители спортивной обуви, которые всегда стремились использовать технологии, изо всех сил пытаются внедрить технологию 3D-печати для улучшения характеристик обуви и повышения спортивных результатов.Однако, в целом, некоторые проблемы еще предстоит преодолеть.
5. Выводы
Новая технология производства, представленная 3D-печатью, вносит далеко идущие изменения в традиционную модель производственной отрасли. Это может помочь дизайнерам обуви более удобно преобразовывать дизайнерские идеи, значительно повышать эффективность дизайна продукта, значительно расширять творческое пространство дизайна обуви и быстро создавать прототипы продуктов. Формы и конструкции, которые трудно изготовить традиционными методами формования, производятся эффективным и малозатратным способом, чтобы улучшить оригинальный и инновационный дизайн, способы обработки и производства, а также экологическую среду обрабатывающей промышленности.
Под крещением технологии 3D-печати индустрия спортивной обуви также претерпит значительные изменения в оригинальном дизайне, методах разработки и производства, что будет полезно для разработки продуктов спортивной обуви, инноваций продуктов, внешнего вида и функций. исследования и разработки, а также разработка индивидуальных услуг. Это поможет предприятиям лучше адаптироваться к текущим моделям потребления и рыночным тенденциям быстрой моды, персонализации, мелкосерийного производства и диверсификации; способствовать адаптации обувных предприятий в Китае к режиму проектирования и производства в рамках модели «Интернет +» и «большие данные»; познакомиться с интернет-маркетингом и возможной моделью распределенного производства в будущем; и постепенно культивировать и развивать и развивать свои собственные бренды.