Производство подшипников: Производство подшипников | Полезные статьи
🥇 Производство, изготовление подшипников в Самаре
АО «Завод «Самарский Подшипник» — это команда профессионалов, которые любят и знают свое дело!
Конструктивные группы наших подшипников:
- Конические 1-рядные, 2-рядные, 4-рядные,
- Цилиндрические 1-рядные,2-рядные, 4-рядные,
- Сферические,
- Упорные (роликовые, шариковые),
- Радиальные (роликовые, шариковые),
- Упорно-радиальные шариковые,
- Радиально упорные роликовые.
Основные направления производства
Разработка технической документации
Высококвалифицированные специалисты инженерно-технологического отдела разрабатывают технологическую документацию, чертежи и обеспечивают согласование технических требований выпускаемых подшипников. По результатам работы сервисной службы и потребностям заказчиков, наши конструкторы могут внести допустимые, соответствующие требованиям ГОСТ, изменения в чертежи и техническую документацию. Это позволяет производить уникальные крупногабаритные подшипники по техническим требованиям заказчика, ориентированные на фактические, индивидуальные эксплуатационные характеристики оборудования.
Гарантия качества
Качественные подшипники производятся на предприятии по системе прослеживания:
- Начальный этап – разработка технической документации. Производство продукции проходит строго по согласованным чертежам и требованиям под контролем специалистов инженерно-технологического отдела, в строгом соответствии с ГОСТ.
- Входной контроль деталей. Все детали проходят обязательный контроль специалистов ОТК на соответствие требованиям конструкторской документации, строго соответствующую ГОСТ. Специалисты осуществляют межоперационный контроль на всех технологических этапах производства.
- Окончательный этап – выходной контроль изделия и полная отслеживаемость подшипников.
Информация о выпускаемой продукции (фактические размеры, дата выпуска, номера подшипников (партии), наименование потребителя) сохраняется в базе данных предприятия. Цель — обеспечить возможность сверить всю произведенную продукцию ТЗ «Самарский Подшипник» и максимально защитить потребителей от работы с контрафактом.
Метрологическая лаборатория
Входной контроль комплектующих и выпускаемых деталей подшипников на предмет соответствия: геометрических размеров по чертежам завода, твердости и марки стали производится специалистами метрологической лаборатории. Высокая квалификация персонала, регулярные поверки средств измерений, подтвержденных свидетельствами, также является гарантом качества и надежности подшипников.
Метрологическая лаборатория оснащена необходимым оборудованием:
- спектрометр эмиссионный
- длинномер ИЗМ-11Э
- твердомер стационарный
- индикаторы
- измеритель шероховатости
- твердомеры ультразвуковые
- микрометры
- штангенциркули
- угломеры
- измеритель магнитного поля
Метрологическое оборудование аттестовано и проходит необходимую периодическую поверку.
Обработка деталей
Мы производим обработку деталей подшипников различных конструктивных групп с
высоким классом точности, которые полностью отвечают требованиям ГОСТ 520-2011 и
сертификатам соответствия.
АО «Завод «Самарский Подшипник» имеет собственное мощное, современное,
высокотехнологичное оборудование.
Все процессы производства выполняют и контролируют высококвалифицированные
Процесс шлифовки
Технологическое оборудование предприятия и высокая квалификация персонала
позволяют производить крупногабаритные подшипники 5 и 6 класса точности.
Окончательная шлифовка подшипниковых колец производится на карусельно-
шлифовальных двухшпиндельных станках BERTHIEZ VGM-125 (производства Франции,
система ЧПУ SIEMENS 840D), BERTHIEZ ROP 125 (производства Франции, система ЧПУ
SIEMENS 828D), карусельно-шлифовальный BERTHIEZ VGM-180,(производства Франции,
оснащён системой ЧПУ MITSUBISHI), 3Н763Ф с системой ЧПУ, 3Н762Ф1 с системой ЧПУ.
Аналогичное оборудование установлено на предприятиях известных иностранных
производителей – лидеров подшипниковой отрасли мирового уровня, что является
подтверждением их надежности, точности и высокой производительности.
Дополнительно в обработке колец задействованы плоскошлифовальные станки NAXOS-
UNION FR1800 (производства Германии), 3Е756, внутришлифовальные станки SI8S с
системой ЧПУ (производства Германии), плоскошлифовальный станок 3Б756Н9.
Обработка деталей
На предприятии внедрена система обработки деталей методом твердого точения на
высокотехнологичном, современном оборудовании:
— токарно-карусельный станок 1512МФ3 с системой ЧПУ;
Твердое точение позволяет ускорить процесс предварительной шлифовки и избежать
ожогов на изделии.
Это способствует производству высококачественных, современных и конкурентоспособных
подшипников.
Роликовый участок
Мы осуществляем 100% контроль и сортировку по размерным группам роликов,
ориентируясь на конструкторские чертежи предприятий.
Участок оснащён сверхточным оборудованием:
— Магнитнопорошковый дефектоскоп CJW – 2000, позволяющий производить как
циркуляционное, так и полюсное намагничивание для выявления дефектов на
— Демагнитизатор CTD-600, позволяющий размагничивать тела качения после
проверки на наличие трещин.
— Приборы типа 494, 925, позволяющие производить сортировку роликов по
размерным группам с точностью до 1мкм.
Все используемые в производстве ролики проходят обязательный входящий
контроль.
Мы дорожим доверием наших клиентов.
Технологические возможности производства
Мы производим качественные подшипники сложной конструкции, что позволяет удовлетворить потребности большего количества клиентов.
Изготовление сепараторного блока производится методом аргоно-дуговой сварки и позволяет выпускать -одно, -двух, -четырех рядные подшипники.
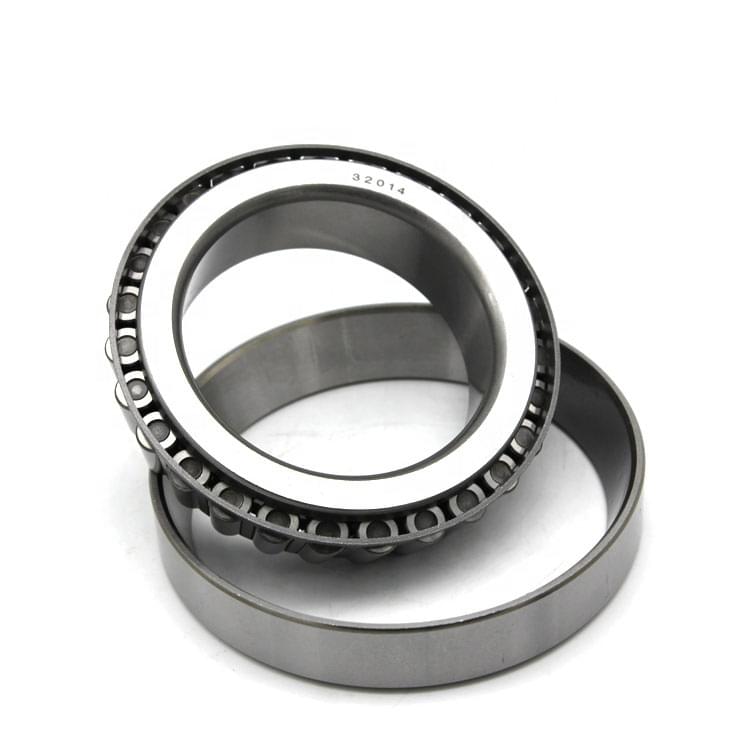
Маркировка и консервация подшипников
На лазерных установках мы осуществляем маркировку всех произведенных подшипников уникальным товарным знаком «Самарский Подшипник» и подтверждаем качество продукции. Поэтому наши клиенты уверены в том, что они приобретают подшипники со 100% гарантией качества.
Мы обрабатываем все подшипники на консервационной установке проходного типа (TY-1500) маслом, с добавлением ингибитора коррозии. Установка позволяет качественно, в автоматическом режиме проводить обработку большого количества и различных по габариту подшипников. Это обеспечивает длительный срок хранения подшипников и защиту при транспортировке.
Упаковка
Мы упаковываем наши подшипники в строгом соответствии с требованиями ГОСТ 520-2011, и обеспечиваем необходимую гарантийную сохранность продукции. Для упаковки подшипников используются автоматические установки: упаковочная машина GW – 1200, стреппинг ТЗ-6000 и надежная обвязочная лента Гелиос Н-45. Это позволяет качественно и быстро упаковать все, в том числе и крупногабаритные подшипники.
Подшипники малой и средней серии упаковываются в прочную, брендированную,
картонную тару. При перевозке используется деревянная обрешетка.
Склад готовой продукции и комплектующих
Наши складские помещения соответствуют высоким требованиям к хранению подшипниковой продукции и ее комплектующим: помещения защищены от попадания прямого солнечного света и газов, установлен ежедневный контроль за температурой и влажностью воздуха. Складские помещения оборудованы стеллажами повышенной грузоподъемности и необходимыми подъемно транспортировочными механизмами, что обеспечивает бережное и долгое хранение.
Завод по производству подшипников SZPK
Подшипник – центральный элемент в любом устройстве и механизме где предполагается движение элементов конструкции относительно друг друга.
Качество, долговечность и стоимость подшипников во многом определяют эксплуатационные расходы при пользовании любой техникой.
ООО «СЗПК» начала промышленный выпуск подшипников российского производства в 2006 году. Используя высококачественные комплектующие отечественного и импортного производства, ООО «СЗПК» выпускает широкий модельный ряд подшипников различных модификаций конструктивных исполнений под зарегистрированным товарным знаком «SZPK».
ООО «СЗПК» выпускает:
- подшипники качения шариковые наружным диаметром от 9 до 2000 мм;
- подшипники качения шариковые закрытого типа наружным диаметром от 9 до 250 мм;
- подшипники качения роликовые с короткими цилиндрическими роликами радиальные наружным диаметром от 35 до 1500 мм;
- подшипники качения роликовые с коническими роликами наружным диаметром от 47 до 2300 мм;
- подшипники качения роликовые со сферическими роликами радиальные наружным диаметром от 80 до 1660 мм;
- подшипники качения шариковые радиальные сферические двухрядные;
- подшипники качения шариковые радиально-упорные;
- подшипники качения шариковые упорные и упорно-радиальные;
- подшипники качения роликовые игольчатые с массивными кольцами;
- подшипники качения роликовые игольчатые карданные;
- подшипники качения шариковые и шарико-роликовые радиальные двухрядные с двусторонним уплотнением и валиком вместо внутреннего кольца;
- подшипники качения роликовые со штампованными кольцами и без колец;
- подшипники шарнирные.
Перейти в раздел: ПРОИЗВОДСТВО ВЫСОКОКАЧЕСТВЕННЫХ ПОДШИПНИКОВ
СКАЧАТЬ Буклет СЗПК — «Производство и поставка подшипников»
*******************************************************************************
По вопросам приобретения подшипников торговой марки SZPK просим обращаться в Северо-Западную Подшипниковую Компанию — Тел.: (812) 334-35-55, 596-36-05
WWW.SZPKBEARING.RU
Ознакомиться со справочно-информационным каталогом
подшипниковой продукции можно на сайте
Поиск подшипников по обозначению и/или параметрам
Изготовление подшипников на заказ — Подшипник-Маркет
Компания ООО «Подшипник-Маркет» предлагает услуги по производству на заказ подшипников качения или вращения. Работы производятся на современном оборудовании по договору с закреплением спецификаций и гарантийных обязательств.
Поскольку подшипники являются ключевыми элементами оборудования, отвечающими за обеспечение беспрепятственного вращения или качения компонентов агрегата, они подвергаются существенным нагрузкам и время от времени выходят из строя. При этом обычно удается подобрать сходный подшипник из числа имеющихся на рынке, но не всегда это возможно.
Как правило, под заказ подшипники изготовляются в тех случаях, когда подбор аналогов затруднителен или готовое фирменное изделие имеет несоразмерно высокую стоимость.
Этапы изготовления подшипников
- Прием технической документации от заказчика или разработка с нуля с последующим согласованием.
- Нарезка подшипниковых колец с задействованием токарных операций. Термическая обработка, шлифование.
- Производство тел качения. Сырьевым материалом обычно выступает металлический прут. Для тел качения также выполняется термообработка, шлифовка.
- Создание сепараторов.
Методы разнообразны и зависят от характеристик будущего изделия. Среди них: штамповка, отливка, фрезеровка.
- Обследование деталей подшипника на предмет соответствия геометрических и физических показателей заявленным. Отбраковка неподходящих элементов. Сборка подшипников на заказ, итоговая проверка. Смазывание при необходимости.
Это лишь основные этапы, выполняющиеся вне зависимости от типоразмера и вида выходных изделий. Конкретные операции зависят от подвида подшипника (газостатические, гидростатические, газодинамические, магнитные, гидродинамические, роликовые, шариковые, радиальные, игольчатые, винтовые, линейные, с одним, двумя и многими рядами качения и т.п.).
Как заказать подшипники?
Стоимость подшипников на заказ в ООО «Подшипник-Маркет» вычисляется индивидуально, исходя из технической документации, количества изделий в партии, наличия предварительно разработанных чертежей и так далее.
Оформите заявку на сайте или позвоните нам по телефону +7 (812) 703-00-16 для получения первичной бесплатной консультации.Укажите нужное количество изделий, вышлите пакет документов или образец для изготовления чертежа нашими инженерами, узнайте методику ценообразования и срок поставки.
ОАО «ОК-Лоза» — производство прецизионных приборных шариковых подшипников
Уважаемые партнеры, коллеги, дорогие друзья!
Открытое акционерное общество «ОК-Лоза» – правопреемник Загорского филиала Всесоюзного научно-исследовательского конструкторско-технологического института подшипниковой промышленности (ЗФ ВНИПП), созданного на базе Специальной технологической лаборатории Опытного завода (ЛОЗа) Центрального конструкторского бюро Главподшипника, основанной в 1949 году – специализируется на разработке, изготовлении, модернизации и исследованиях прецизионных приборных шариковых подшипников и совмещенных подшипниковых опор.
Сложившийся коллектив конструкторов, технологов и других специалистов, высокий профессионализм рабочих, современное высокоточное технологическое оборудование позволяют решать самые сложные проблемы разработки и производства приборных подшипников, как стандартных конструкций, так и специальных, совмещающих детали подшипников и подшипниковых узлов изделий спецтехники и гироскопических приборов.
Отработка технологических процессов производства, технических требований к подшипникам, применение новых материалов для изготовления деталей подшипников, методов и средств контроля деталей и собранных подшипников обеспечивают их высочайший уровень качества, не уступающий зарубежным аналогам и отвечающий самым жестким требованиям потребителей.
ОАО «ОК-Лоза» – это передовые технологии, современные разработки и оборудование, большой научный и производственный опыт, а также коллектив высококлассных специалистов, которые являются самым главным активом завода. Все это собрано воедино, чтобы решение каждой конкретной задачи отвечало требованиям общемировых стандартов качества и работало на повышение экономической эффективности всего производственного процесса.
История нашего завода – это история трудолюбия, целеустремленности, сплочённости коллектива и верной стратегии. Нашему трудовому коллективу есть чем гордиться!
ОАО «ОК-Лоза» придерживается принципов служебной этики и основных правил служебного поведения.
Основные виды деятельности
Радиальных, радиально-упорных с внутренним диаметром от 1мм и наружным диаметром до 35 мм, двухрядных и трёхрядных подшипников, подшипников специальных конструкций по техническим заданиям заказчиков, из подшипниковой стали двойного переплава, коррозионностойких, жаропрочных сталей и немагнитных сплавов
Для систем навигации и стабилизации космической, авиационной, наземной и морской техники, конструкция которых интегрирована в узел прибора, с применением особо чистой подшипниковой стали, коррозионностойких сталей и немагнитных сплавов
Подшипники стоматологических турбинных наконечников с частотой вращения до 400 тысяч оборотов в минуту, подшипниковые узлы аппаратов искусственного кровообращения, самосмазывающиеся подшипники узлов рентгеновских трубок, подшипники с керамическими шариками и с сепараторами из различных полимерных материалов
Подшипники шпиндельных узлов шлифовальных и сверлильных станков, подшипниковые узлы оборудования для шлифовки и огранки алмазов, детали турбокомпрессоров двигателей автомобилей и тракторов, прецизионные детали банковских машин
Из различных подшипниковых сталей и сплавов, цветных металлов, из титана, высокопрочной керамики, шарики для прецизионных узлов 5 степени точности, свободные шарики всех степеней точности, шарики из твёрдых сплавов
ОАО «ОК-Лоза» проводит научно-исследовательские и опытно-конструкторские работы с целью повышения качества, надёжности и долговечности подшипников, создания новых конструкций, совместно с ведущими научно-исследовательскими институтами и с предприятиями приборостроительной отрасли
Производство подшипников по ГОСТ
Контроль на всех стадиях
Продукция по специальным техническим условиям
Разработано свыше 300 типоразмеров подшипников
Уникальный парк станков производства США, Японии, Германии
Продукция востребована предприятиями, производящими высокоточную гироскопическую и навигационную технику, системы управления для космической, авиационной, наземной и морской техники, а также приборостроительными, автомобилестроительными, текстильными, медицинскими и ювелирными предприятиями.
Основными заказчиками являются предприятия, входящие в состав корпорации «Объединенные машиностроительные заводы» и многие другие ведущие предприятия России в области приборостроения.
ОАО «ОК-Лоза» выполняет функцию по ведению дел секретариата технического комитета по стандартизации «Приборные подшипники качения» (ТК 218) и является членом Международного Технического Комитета 307 и Технического Комитета 307, которые рассматривают, корректируют и принимают межотраслевые и государственные стандарты, стандарты ISO.
Подшипники ОАО «ОК-Лоза» – это проверенные временем технологии изготовления приборных подшипников высокого качества, которые гарантируют их надежность и безотказность в работе, высочайшие точность вращения, жесткость и равножесткость в осевом и радиальном направлениях, минимальные параметры износа рабочих поверхностей и момента сопротивления вращению, уровня шума и вибрации.
Изготовление подшипников — Токарный, измерительный инструмент, оснастка станков.
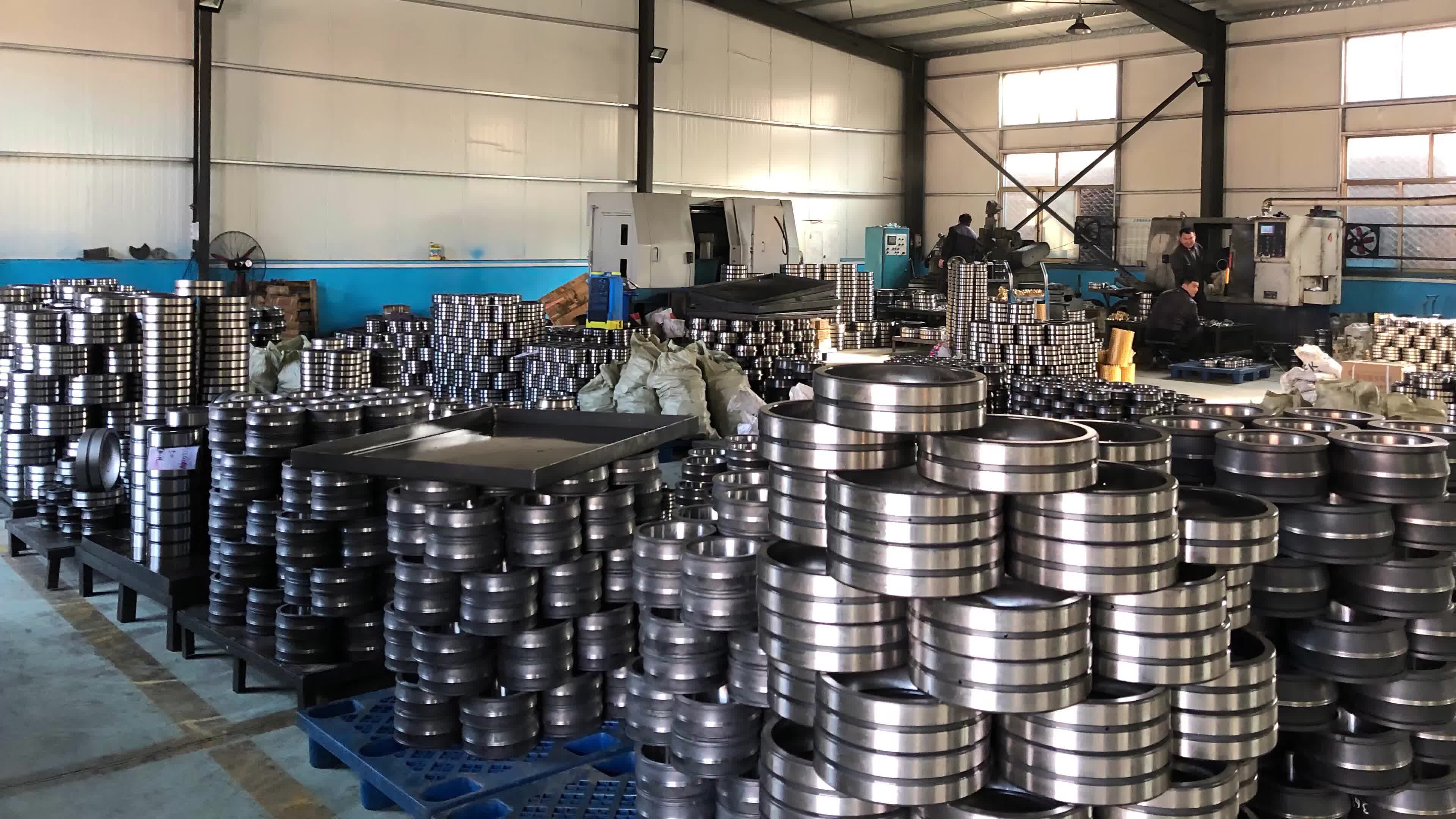
Подшипник состоит из двух составляющих « под» и « шип» — что в переводе обозначает сборочный узел, который может являться частью опоры или упора и который в свою очередь поддерживает ось, вал или иную подвижную конструкцию с определенно заданной жесткостью. Именно эта деталь дает возможность зафиксировать положение в пространстве и дает беспрепятственное вращение. Именно эта деталь с наименьшим сопротивлением распределяет и передает нагрузку от подвижного узла на другие части конструкции.
Подшипники можно разделить на два типа:- Подшипник скольжения
- Подшипник качения
- Подшипник скольжения подразделятся на подвиды:
- Газостатические подшипники
- Гидростатические подшипники
- Газодинамические подшипники
- Магнитные подшипники
- Гидродинамические подшипники
- Роликовые — ( ролики длинные и тонкие, так же игольчатые)
- Шариковые
- Подшипник качения, подраздел типы воспринимаемой нагрузки
- Упорные ( подшипник не допускает нагрузки вдоль вала оси)
- Линейные (обеспечение подвижности вдоль оси)
- Радиальные (подшипник не допускает нагрузки вдоль оси вала)
- Радиально – упорные, упорно-радиальные (подшипник воспринимает различные нагрузки как поперек , так и вдоль вала оси)
- Шариковое –винтовые передачи.
(обеспечение качения через сопряжение винт-гайки)
- Линейные подшипники(обеспечение подвижности вдоль оси. Есть разновидности – рельсовые, вальные или телескопические)
Подшипник качения, подраздел число рядов качения
Однорядные, двухрядные, многорядные.
Самоустанавливающиеся и несамоустанавливающиеся.
Подшипник качения считают высокотехничным и высокоточным, именно они проходят в процессе производства через многие операции.
Состав подшипника: кольцо, тело качения ( ролик или шарик)защитные шайбы, сепаратор и заклепки. Производство подшипника производство деталей.
Шарикоподшипниковая сталь.
Для изготовления подшипников применяют высокоуглеродистые стали.
Подшипники которые работают в обычных условиях
Сталь хромистая, хромомарганцевая с добавками молибдена, хромистая с молибденом, хромомарганцевокремнистая, хромомарганцевая с добавлением молибдена.
Подшипники которые работают в агрессивной среде при высоких температурных режимах
Сталь теплостойкая и коррозионно-стойкая
Марки стали ШХ15, ШХ 9, ШХ4, ШХ6, ШХ15СГ, 52100, 100С6, SKF – 24, SUJ2 и другие.
Марки стали 95Х18Ш( «Ш» сталь была выплавлена по методу электрошлакового переплава . «ШД» вакуумно-дуговая переплавка стали электрошлакового переплава. 11Х18-ШД, ЭИ760, М50,Z89WDCV6, 8DCV40 и другие. Так же широко применятся низкоуглеродистые цементируемые стали.
Подшипники которые работают в температурном режиме от 60 * до 300* изготавливают из хромомарганцевокремнистой стали и из хромистой стали.
На немецких предприятиях проблему недостаточности прокаливаемости изделий и их теплостойкости решили путем создания различных модификаций где в таль добавляли небольшие порции молибдена, ванадия и вольфрама. Марка Х90CrMoV18
Подшипники делятся на шариковые и роликовые.
Завод подшипников скольжения — ВЕСТИ / Тамбов
Автор ГТРК «ТАМБОВ» На чтение 2 мин. Просмотров 34 Опубликовано
Тамбовское акционерное общество “Завод подшипников скольжения” — одно из старейших промышленных предприятий Тамбова и уникальное в своем роде.
“Завод подшипников скольжения” ведет свою историю с августа 1932 года, когда на базе тракторных мастерских предпринимателя Махова был создан Тамбовский завод “Автотрактородеталь”. Развитие завода шло большими темпами. В июле 1954 года в целях концентрации производства и объединения смежных отраслей к нему был присоединен расположенный рядом механический завод Министерства совхозов.
В 1958 году, после принятия решения о специализации Тамбовского завода “Автотрактородеталь” на производстве вкладышей коленчатых валов дизельных автотракторных моторов и алюминиевых поршней к ним, начался новый этап в развитии предприятия по пути комплексной механизации и автоматизации производства. В настоящее время оно оснащено современным отечественным оборудованием.
За успехи, достигнутые в сохранении производства в условиях затяжного экономического кризиса, коллектив ОАО “Завод подшипников скольжения” был удостоен в 1995 году международной награды “Факел Бирмингема”. За самое короткое время на заводе было перепрофилировано производство: перестроен целый ряд автоматизированных технологических линий и оборудования для производства подшипников скольжения высокого технологического качества не только для тракторов, но и автомобилей, грузовых и легковых, как отечественного так и импортного производства.
В 2000 году комплект вкладышей подшипников скольжения к двигателю автомобиля «Москвич-412» получил диплом финалиста всероссийской программы-конкурса «100 лучших товаров России».
В 2001 году комплект вкладышей подшипников скольжения к двигателю автомобиля «Газ-24» получил диплом всероссийской программы-конкурса «100 лучших товаров России».
В 2004 году ОАО «Завод подшипников скольжения» был награжден Почетным дипломом лучшего российского экспортера 2004 года – за выдающийся вклад в расширение внешних экономических связей Российской федерации, развитие отечественного производства и высокую профессиональную культуру.
Диплом подписал министр экономического развития и торговли РФ Г.О. Греф.
В настоящее время “Завод подшипников скольжения” является крупнейшим производителем в СНГ вкладышей подшипников скольжения коленчатого вала, упорных полуколец и втулок для тракторных, комбайновых, судовых, тепловозных, автомобильных грузовых и легковых двигателей, промышленных компрессоров с применением технологии и оборудования английской фирмы “Glacier” , австрийской фирмы “Miba”, немецкой фирмы “Blazberg”, а также ведущих предприятий СНГ и России.
Конструкторское бюро и в его структуре опытное производство имеет возможность в разработке и изготовлении подшипников скольжения для двигателей тракторов, автомобилей и промышленных компрессоров иностранного производства.
В разработке новых сплавов “Завод подшипников скольжения” активно работает с Институтом железнодорожного транспорта г. Москва, институт цветметобработка и различных других научных организациях.
Узнавайте о новых публикациях как вам удобнее:
Инициативы NSK пресекают производство фальшивых подшипников
Будучи уважаемым и престижным производителем премиальных подшипников, компания NSK уже многие годы является мишенью беспринципных имитаторов. Намереваясь обмануть как производителей оригинального оборудования, так и пользователей, изготовители поддельных подшипников ни перед чем не останавливаются, чтобы ввести в заблуждение покупателей и повысить доход от своей незаконной деятельности. Однако NSK ведет постоянную борьбу, принимая ряд мер для ее пресечения.
Вот несколько фактов для понимания масштабов проблемы: около 23 000 поддельных упаковок и этикеток NSK недавно были обнаружены в провинции Хэбей, Китай, а контрольный рейд на другом заводе, принадлежащем тому же нарушителю, выявил свыше 90 000 поддельных коробок для подшипников и 10 печатных пластин для имитации этикеток продукции четырех крупнейших производителей подшипников, включая NSK.
Ассортимент обнаруженных на заводе станков и оборудования демонстрирует масштабы технических средств, доступных многим производителям поддельной продукции. Было найдено несколько станков для печати, ламинирования, вырубки, биговки и резки. Кроме фальшивых коробок, правоохранительные органы также обнаружили несколько штабелей неразрезанных упаковок, большая часть которых имела маркировку NSK.
Все продукты были конфискованы и переданы в Наблюдательную комиссию по контролю рынка (MSB), местный орган по работе с нарушениями товарных знаков.
Какова реальная цена
Приобретение поддельных подшипников экономически невыгодно. Хотя эти продукты и могут быть дешевле, но из-за таких проблем, как низкое качество обработки и использование низкосортного сырья, они почти наверняка выйдут из строя раньше положенного срока. А преждевременный отказ подшипников сказывается на надежности всей системы, приводя к незапланированным расходам на техническое обслуживание и ремонт, которые, в свою очередь, повышают совокупную стоимость владения. Также в значительную сумму обойдется последующий ущерб репутации компании/бренда.
NSK стремится защитить покупателей, устраняя с рынка незаконных игроков и продукты, которые могут выйти из строя преждевременно, а главное, представляют неминуемую угрозу безопасности. Основные задачи заключаются в том, чтобы ликвидировать выпускающие фальшивки синдикаты, остановить производство и распространение подделок и преследовать правонарушителей в суде.
Значительная часть этих мероприятий подразумевает сотрудничество с органами власти в Китае. Например, работая совместно с таможенной службой и пограничной охраной, можно предотвратить вывоз поддельных подшипников. В дополнение к этим мерам центральные и местные правительственные организации проводят рейды.
Пусть приложения сделают все за вас
Технологии играют ключевую роль в борьбе с подделками подшипников. Хорошим примером служит недавно разработанное бесплатное приложение NSK Verify, которое позволяет удостовериться в подлинности подшипников для обрабатывающих станков с помощью смартфона, нужно только отсканировать размещенный на коробке уникальный двухмерный штрихкод.
Следующим этапом деятельности NSK по устранению поддельных подшипников стало объединение усилий с Международной ассоциацией производителей подшипников (WBA) для создания нового приложения, применимого для продукции различных производителей, под названием WBA Bearing Authenticator: WBA Check. WBA работает по всему миру, чтобы обеспечить соблюдение закона по борьбе с подделками и устранить фальшивые подшипники, в том числе с помощью разработки приложений. Это некоммерческая и не являющаяся юридическим лицом промышленная организация представляет общие законные интересы мировых производителей подшипников, такие как открытое экономическое взаимодействие, экологичное развитие и защита законных прав. И NSK — ее активный участник.
Аналогично функциональности NSK Verify приложение WBA Check оценивает подлинность подшипников компаний — участников WBA, сканируя двухмерный штрихкод, что особенно удобно для покупателей, приобретающих подшипники различных производителей. Более того, если обнаруживается незарегистрированный подшипник, приложение автоматически уведомляет NSK.
Используйте авторизованные источники
В то время как приложения прекрасно подходят для определения фальшивых подшипников, которые уже прибыли к конечному пользователю, предупредительным способом борьбы с подделками является осуществление закупок исключительно у авторизованных дистрибьюторов и дилеров NSK. Такие торговые предприятия получают оригинальные продукты непосредственно от группы компаний NSK и обеспечивают дополнительную ценность за счет предоставления рекомендаций, послепродажного обслуживания и гарантий.
Одновременно со всеми этими мерами NSK регулярно повышает ценность своего бренда на рынке с помощью действий по защите товарных знаков наряду с проведением программ обучения для дистрибьюторов и коллег.
NSK стремится положить конец производству подделок и помочь покупателям насладиться всеми преимуществами оригинальных высококачественных и надежных подшипников.
Приложение WBA Check можно скачать с официального веб-сайта WBA по адресу www.stopfakebearings.com/#buysafely
Рис.1 — NSK объединила усилия с WBA для создания общего с другими производителями подшипников приложения по борьбе с контрафактом
Как изготавливают шарикоподшипники
Задний план
С тех пор, как человеку стало необходимо перемещать вещи, он использовал круглые ролики, чтобы
облегчить работу. Вероятно, первыми катками были палки или бревна, которые
были большим улучшением по сравнению с перетаскиванием вещей по земле, но все же
довольно тяжелая работа. Египтяне использовали бревна для скатывания огромных каменных блоков.
для пирамид. В конце концов, кому-то пришла в голову идея защитить
каток к тому, что перемещалось, и построил первый
«транспортное средство» с «колесами.«Однако эти еще
были подшипники, сделанные из материалов, трущихся друг о друга, а не катящихся
друг на друга. Лишь в конце восемнадцатого века
разработана базовая конструкция подшипников. В 1794 году валлийский мастер по металлу Филип
Воан запатентовал конструкцию шарикоподшипников для поддержки оси
перевозка. Развитие продолжалось в девятнадцатом и начале двадцатого
столетий, чему способствовало развитие велосипеда и автомобиль.
Существуют тысячи размеров, форм и видов подшипников качения; мяч
подшипники, роликовые подшипники, игольчатые подшипники и конические роликоподшипники
являются основными видами. Размеры варьируются от достаточно малых для запуска миниатюрных двигателей.
к огромным подшипникам, используемым для поддержки вращающихся частей в гидроэлектростанциях
растения; эти большие подшипники могут быть десять футов (3,04 метра) в диаметре и
для установки требуется кран. Наиболее распространенные размеры легко помещаются в
одной рукой и используются в таких вещах, как электродвигатели.
В этой статье будут описаны только шариковые подшипники. В этих подшипниках
часть качения представляет собой шарик, который катится между внутренним и наружным кольцами, называемыми
скачки. Мячи удерживаются клеткой, которая удерживает их на равномерном расстоянии друг от друга.
гонки. В дополнение к этим частям, есть много дополнительных частей
для специальных подшипников, таких как уплотнения для удержания масла или смазки и попадания грязи, или
винты, чтобы удерживать подшипник на месте. Мы не будем беспокоиться об этом
модные дополнения.
Сырье
Почти все детали всех шарикоподшипников изготовлены из стали. Поскольку подшипник должен выдерживать большие нагрузки, он должен быть сделан из очень прочного стали. Стандартная отраслевая классификация стали в этих подшипников 52100, а это значит, что в них один процент хрома и один процент углерода (называемый сплавами при добавлении к основной стали). Эта сталь можно сделать очень твердым и жестким путем термической обработки.Где ржавчина может быть проблема, подшипники сделаны из 440C нержавеющая сталь.
Клетка для шаров традиционно изготавливается из тонкой стали, но некоторые подшипники теперь используют литые пластмассовые сепараторы, потому что они дешевле в изготовлении и вызывают меньшее трение.
Производство
Процесс
Стандартный шарикоподшипник состоит из четырех основных частей: наружного кольца,
катящиеся шарики, внутреннее кольцо и сепаратор.
- 1 Обе расы сделаны практически одинаково. Так как они оба кольца
стали, процесс начинается со стальных труб соответствующего размера.
Автоматы, подобные токарным станкам, используют режущие инструменты для резки основных
форму гонки, в результате чего все размеры немного преувеличены. То
Причина, по которой они оставлены слишком большими, заключается в том, что расы должны быть подвергнуты термической обработке.
до завершения, и сталь
Удивительно, но катящиеся шарики изначально представляют собой толстую стальную проволоку.Затем в процессе холодной высадки проволока разрезается на мелкие кусочки. разбился между двумя стальными плашками. В результате получился шар, похожий на планета Сатурн с кольцом вокруг середины, называемым «вспышка.»
обычно деформируется во время этого процесса.Их можно обработать обратно готовый размер после термообработки.
- 2. Черновые кольца помещаются в печь для термообработки при температуре около 1550 градусов по Фаренгейту (843 градуса по Цельсию) в течение нескольких часов (в зависимости от размера деталей), затем погружают в масляную баню для охладите их и сделайте их очень твердыми.Это закаливание также делает их хрупкие, поэтому следующим шагом будет их отпуск. Это делается путем нагрева их во второй духовке примерно до 300 градусов по Фаренгейту (148,8 градусов по Фаренгейту). Цельсия), а затем дать им остыть на воздухе. Вся эта термообработка процесс делает детали, которые являются одновременно твердыми и жесткими.
- 3 После термической обработки дорожки готовы к отделке.
Однако теперь расы слишком трудно резать режущими инструментами, поэтому
остальная работа должна быть выполнена с шлифовальные круги.
Это очень похоже на то, что вы найдете в любом магазине для заточки. сверла и инструменты, за исключением нескольких различных видов и форм. необходимо для завершения гонок. Почти все места в гонке заняты путем шлифовки, которая оставляет очень гладкую, аккуратную поверхность. Поверхности место, где подшипник входит в машину, должно быть очень круглым, а стороны должны быть ровными. Поверхность, по которой катятся шарики, сначала шлифуется, а потом лопнул.Это означает, что для полировать гонки в течение нескольких часов, чтобы получить почти зеркальный блеск. В На этом этапе гонки завершены и готовы к сборке с мячи.
- 4 Шары сделать немного сложнее, хотя их форма
очень просто. Удивительно, но шарики начинаются как толстая проволока. Этот
проволока с рулона подается на станок, который отрезает короткий кусок, и
затем разбивает оба конца по направлению к середине.
Этот процесс называется холодным Заголовок. Свое название он получил из-за того, что провод не
Выпуклость вокруг середины катящихся шариков удаляется за один раз. процесс обработки. Шарики помещаются в шероховатые канавки между двумя чугунные диски. Один диск вращается, а другой неподвижен; трение удаляет вспышку. Отсюда шары жаркие обработаны, отшлифованы и притерты, что оставляет шарики с очень гладкая отделка.
нагревают перед тем, как разбить, и что первоначальное использование для процесса заключалась в том, чтобы надеть головки на гвозди (как это и делается до сих пор). В любом скорость, шары теперь выглядят как планета Сатурн, с кольцом вокруг средний называется «вспышка». - 5 Первый процесс обработки удаляет этот заусенец. Шариковые подшипники
положить между сторонами двух чугунных дисков, где они едут в
канавки.
Внутренняя часть канавок шероховатая, что отрывает вспышку шаров.Одно колесо вращается, а другое остается неподвижным. То стационарное колесо имеет сквозные отверстия, чтобы шарики можно было подавать в и выведены из канавок. Специальный конвейер подает шарики в один отверстие, шарики гремят по канавке, а затем выходят из другого отверстие. Затем они подаются обратно на конвейер для множества проходов. колесные канавки, пока они не станут достаточно круглыми, почти до нужного размера, а вспышки совсем нет.Снова, шары оставляют большего размера, чтобы их можно было измельчить до готового состояния Размер после термической обработки. Количество стали, оставшейся на доводку, не много; всего около 8/1000 дюйма (0,02 сантиметра), что примерно равно толщиной с два листа бумаги.
- 6 Процесс термической обработки шаров аналогичен
гонки, так как вид стали одинаков, и лучше иметь
все детали изнашиваются примерно с одинаковой скоростью.
Как гонки, мячи становятся твердыми и жесткими после термической обработки и отпуска. После тепла обработка, шарики возвращаются в машину, которая работает так же как средство для удаления заусенцев, за исключением того, что вместо этого используются шлифовальные круги. режущих кругов. Эти колеса перемалывают шарики так, что они круглые и в пределах нескольких десятитысячных дюйма от их готового размер.
- 7 После этого шары перемещаются на притирочный станок, который отлил
железные колеса и использует тот же абразивный притирочный состав, что и на
гонки.Здесь их будут притирать 8-10 часов, в зависимости от
Четыре части готового шарикоподшипника: внутреннее кольцо, внешнее кольцо, клетка и мяч.
насколько точен подшипник, для которого они сделаны. И снова результат это сталь, которая очень гладкая.
- 8 Стальные сепараторы штампуются из довольно тонкого листового металла,
формочкой для печенья, а затем сгибаются до их окончательной формы в штампе.
Кубик состоит из двух соединенных друг с другом кусков стали с отверстием в форме готовой детали, вырезанной внутри. Когда клетка помещается между и матрица закрыта, клетка изогнута по форме отверстия внутри. То Затем штамп открывается, и готовая деталь вынимается, готовая к использованию. собран.
- 9 Пластиковые клетки обычно изготавливаются методом литья под давлением. В этом процессе полая металлическая форма заполняется путем разбрызгивания расплавленного металла. пластик в него, и позволяя ему затвердевать.Форма открывается, и готовая клетка вынимается, готова к сборке.
- 10 Теперь, когда все детали изготовлены, нужно установить подшипник.
вместе. Во-первых, внутренняя обойма помещается внутрь внешней обоймы, только снаружи.
в одну сторону насколько это возможно. Это делает пространство между ними на
противоположная сторона достаточно большая, чтобы между ними можно было вставлять мячи.
Требуемый вставлено количество шаров, затем беговые дорожки перемещаются так, чтобы они оба по центру, и шарики равномерно распределены вокруг подшипника.В В этот момент устанавливается клетка, удерживающая шары отдельно друг от друга. разное. Пластиковые сепараторы обычно просто защелкиваются, в то время как стальные сепараторы обычно приходится вставлять и заклепывать вместе. Теперь, когда подшипник собран, покрыт средством от ржавчины и упакован для перевозки.
Контроль качества
Изготовление подшипников — очень точный бизнес. Испытания проводятся на образцах
стали, поступающей на завод, чтобы убедиться, что она имеет
нужное количество легированных металлов в нем.Испытания на твердость и ударную вязкость
также осуществляется на нескольких стадиях процесса термообработки. Это также
множество проверок по пути, чтобы убедиться, что размеры и формы
правильный. Поверхность мячей и места, где они катятся по беговым дорожкам, должны быть
исключительно гладкая. Мячи не могут быть вне круга более 25
миллионные доли дюйма даже для недорогого подшипника. Высокоскоростной или
прецизионные подшипники допускаются только с пятимиллионными долями дюйма.
Будущее
Шариковые подшипники будут использоваться еще много лет, потому что они очень просты и стали очень недорогими в производстве.Некоторые компании экспериментировал с изготовлением шаров в космосе на космическом челноке. В космосе, капли расплавленной стали можно выплюнуть в воздух, а невесомость позволяет им парить в воздухе. Капли автоматически образуют идеальные сферы. пока они остывают и твердеют. Однако космические путешествия по-прежнему дороги, поэтому много полировки можно сделать на земле по цене одной «космический шар».
Однако на горизонте находятся и другие виды подшипников. Подшипники, где два
объекты никогда не соприкасаются друг с другом, эффективны в работе, но сложны
делать. Один вид использует магниты, которые отталкиваются друг от друга и могут быть
используется для разделения вещей. Вот так «маг-лев» (для
магнитной левитации) построены поезда. Другой вид нагнетает воздух в
пространство между двумя плотно прилегающими поверхностями, заставляющее их парить в воздухе
друг друга на подушке сжатого воздуха. Однако оба этих подшипника
гораздо дороже построить и эксплуатировать, чем скромный, надежный шар
несущий.
Где узнать больше
КнигиСотрудники Deere & Company, ред. подшипники и уплотнения, 5-е изд. Р. Р. Боукер, 1992.
Эшманн, Пол. Шариковые и роликовые подшипники: теория, конструкция и применение, 2-е изд.
Харрис, Тедрик А. Анализ подшипников качения, 3-е изд. Джон Вили и сыновья, Inc., 1991.
Хоутон, П.С. Шариковые и роликовые подшипники. Elsevier Science Publishing Company, Inc., 1976.
Нисбет, Т.С. Подшипники качения. Издательство Оксфордского университета, 1974.
Шигли, Дж. Э. Подшипники и смазка: конструктор-механик Рабочая тетрадь. Макгроу-Хилл, Инк., 1990.
ПериодикаГарднер, Дана. «Керамика оживляет диски» Новости дизайна. 23 марта 1992 г., с. 63.
Ханнуш, Дж. Г. «Керамические подшипники становятся популярными». Новости дизайна. 21 ноября 1988 г., с. 224.
Маккарти, Лайл Х. «Новый сплав обеспечивает более тихий мяч» Подшипники», Новости дизайна. 20 мая 1991 г., с. 99.
Другие статьи, которые могут вам понравиться:
Как правильные подшипники могут улучшить ваш производственный процесс
Хороший производственный процесс – это бесперебойный производственный процесс.Налаженный производственный процесс является более прибыльным. Хотя невозможно избежать всех производственных проблем до того, как они возникнут, есть шаги, которые вы можете предпринять, чтобы снизить риск. Одной из самых упускаемых из виду областей возможностей в этом отношении является выбор подшипника. В этой статье основное внимание будет уделено подшипникам с низким коэффициентом трения и тому, как они могут помочь вам сократить производственные затраты, повысить производительность и сделать ваш производственный процесс более прибыльным.
Предотвратить сбой машины
Проще говоря, сбой машины означает, что машина (или компонент) перестала функционировать так, как предполагалось изначально.Это может быть катастрофический сбой или потеря эффективности все еще работающей машины. Например, насос, который был разработан для подачи 100 галлонов воды в минуту, теперь может перекачивать только 50 галлонов в минуту, будет классифицироваться как отказ машины.
Подсчитано, что 70 процентов отказов машин происходят из-за износа поверхности, и что большинство проблем с износом поверхности возникает из-за механического износа.
Хотя любой подшипник по своей природе уменьшает трение, микроскопический взгляд на поверхность подшипника выявит грубые дефекты, которые на самом деле создают трение.По сравнению со стандартными подшипниками подшипники с низким коэффициентом трения уменьшают фрикционное движение на 30 и более процентов. Это снижает деградацию поверхности, что снижает риск отказа машины.
Наиболее очевидным преимуществом использования подшипников с низким коэффициентом трения является стоимость. Поскольку вы тратите меньше средств на запасные части и сотрудники не теряют производительность в периоды простоя, вы можете снизить общую стоимость владения машиной.
Существует также меньше альтернативных издержек.Если машина работает с 50-процентной эффективностью, вы просто не сможете произвести как можно больше изделий за заданный период времени. Это не только создает скрытое узкое место, которое затрудняет удовлетворение производственных потребностей, но также означает, что виджеты, которые можно было бы сделать, не годятся. Другими словами, у вас меньше продукта для продажи и меньше дохода, который вы можете показать за свои усилия.
Энергоэффективность
По данным Международного энергетического агентства (МЭА), цена удовлетворения мировых потребностей в энергии до 2030 года составит 26 долларов.3 трлн. Чтобы оплатить этот повышенный спрос, растут затраты на энергию.
Вполне вероятно, что на машины, которые вы используете в производственном процессе, приходится значительная часть энергопотребления вашей компании. Именно здесь потребность в энергии влияет на ваш производственный процесс. По сути, создание того же продукта обходится дороже, поэтому у вас есть несколько вариантов: поднять цены на конечный продукт и/или найти способы сократить производственные затраты. К счастью, подшипники с низким коэффициентом трения могут помочь вам справиться с этой задачей.
Машины, в которых используются подшипники с низким коэффициентом трения, требуют меньше энергии и, следовательно, меньше денег. Это улучшит денежный поток вашей компании, а это означает, что вы можете инвестировать в новые или модернизированные машины, новых сотрудников или какую-то другую важную область бизнеса.
В качестве дополнительного бонуса, поскольку выбросы парниковых газов напрямую связаны с потреблением энергии, подшипники с низким коэффициентом трения лучше для окружающей среды.
Производительность сотрудников
Все работающие машины создают отработанное тепло.Это повышает температуру воздуха, что, если его не остановить, может негативно сказаться на производительности труда сотрудников.
По данным Управления по охране труда и здоровья (OSHA), оптимальная рабочая температура составляет от 68 до 76 градусов по Фаренгейту. Рабочая среда выше этого диапазона температур затрудняет концентрацию внимания работников и вызывает у них чувство усталости.
Поскольку подшипники с низким коэффициентом трения уменьшают истирание, оборудование вашего завода производит меньше тепла.Это упрощает и удешевляет поддержание условий труда при комфортных и более продуктивных температурах. Другими словами, комфортные сотрудники — это счастливые сотрудники. Счастливые сотрудники — более продуктивные сотрудники.
Выбор правильного подшипника для вашего применения очень важен. Когда дело доходит до производственного процесса на вашем заводе, подшипники с низким коэффициентом трения обеспечивают возможность снижения затрат в течение длительного времени после того, как первоначальный заказ сделан, поскольку они ограничивают отказ оборудования, являются более энергоэффективными и обеспечивают удобство и производительность сотрудников.
Об авторе
Крис Уилсон (Chris Wilson) — менеджер по корпоративным операциям в Ritbearing Corporation, международном дистрибьюторе шариковых и роликовых подшипников, который также специализируется на изготовленных по индивидуальному заказу подшипниках для уникальных применений. С Крисом можно связаться по телефону 1-800-431-1980 или по электронной почте [email protected].
Huisman удваивает производственные мощности по производству опорно-поворотных устройств в Нидерландах
Huisman, мировой поставщик технических решений со ступенчатым изменением, удвоил производственные мощности по производству опорно-поворотных устройств на своем предприятии в Схидаме, Нидерланды.Благодаря такому значительному увеличению производственных мощностей Huisman может удовлетворить растущий спрос на опорно-поворотные подшипники большого диаметра, неотъемлемую часть и ключевой компонент кранов большой грузоподъемности.
С 2010 года компания Huisman занимает уникальное положение на рынке, успешно разрабатывая и производя опорно-поворотные подшипники большого диаметра собственными силами. Huisman производит собственные опорно-поворотные подшипники, чтобы обеспечить высочайшее качество и защитить собственные технологии производства. Учитывая значительный объем заказов на большие морские краны, инвестиции во второй фрезерный станок обеспечивают компании Huisman достаточную производственную мощность в будущем.
Опорно-поворотные подшипники являются неотъемлемым и ключевым компонентом всех кранов Huisman. В отличие от решений, требующих сложного технического обслуживания, таких как тележки или системы поворота на больших колесах, которые подвергаются воздействию суровых морских условий, опорно-поворотный подшипник Huisman способствует существенному снижению веса крана и подконструкции, позволяя крановым судам работать более эффективно и экономично. эффективно. Благодаря уникальной сегментной конструкции поворотного подшипника Huisman осмотр и техническое обслуживание можно проводить на месте без разборки подшипника, что приводит к значительному снижению эксплуатационных расходов.
Дэвид Руденбург, генеральный директор Huisman: «Стремление к морскому ветроэнергетике привело к высокому спросу на тяжелые подъемные краны. Чтобы обеспечить нашим клиентам высочайшее качество и своевременную доставку, мы расширили наши производственные мощности. Мы решили развернуть второй фрезерный станок Zayer в Нидерландах, чтобы гарантировать непрерывность наших проектов здесь и инвестировать в опыт наших людей. Поскольку наши поворотные подшипники являются неотъемлемой частью уникальной облегченной конструкции наших кранов, инвестиции в производственные мощности позволяют нам укреплять наши позиции в качестве мирового лидера на рынке кранов большой грузоподъемности.
После выпуска серии все более крупных опорно-поворотных устройств в 2018 году компания Huisman спроектировала и поставила самые большие в мире опорно-поворотные устройства для кранов Heerema Sleipnir грузоподъемностью 10 000 тонн. Эти опорно-поворотные устройства имеют диаметр 30 м. На сегодняшний день в послужном списке Huisman около 25 опорно-поворотных устройств.
Ранее в этом году компания Huisman расширила свой покрасочный цех в Китае на 1 675 м2 до общей площади более 6 000 м2. Это необходимо для увеличения производительности распыления, что устраняет критическое узкое место в производственном процессе тяжелой строительной техники.
Массовое производство подшипниковой промышленности набирает обороты — Азиатско-Тихоокеанский регион Новости металлообрабатывающего оборудования | Производство | Автоматизация
Растущий спрос на специализированные подшипники вызывает стремительные изменения в технологиях массового производства, нацеленные на качество и цену. Роби Нудельман, менеджер по производству подшипников, и Яир Фераро, инженер по применению в Iscar.
Подшипники необходимы практически для любой механической системы и многих других элементов, требующих вращательного движения.Если что-то крутится, скручивается или двигается, скорее всего, в этом есть подшипник. Сегодня наиболее популярным типом подшипников на рынке являются шарикоподшипники, но также довольно распространены роликоподшипники, игольчатые, конические, сферические и упорные подшипники. Размеры подшипников варьируются от очень малых диаметров до
Стремительно растущий спрос на специализированные подшипники приводит к быстрым изменениям в технологиях массового производства, ориентированных на качество и цену.
ch как 2 мм для электронных систем диаметром до 6000 мм, в основном для ветряных турбин.Линейные подшипники и корпуса подшипников также являются частью отрасли, но с другими геометрическими характеристиками.
Ключдля автомобильной промышленности
Говоря о подшипниках, сегодня одной из самых требовательных отраслей является автомобильная промышленность. Каждый автомобиль имеет в среднем 100-150 подшипников, а мотоциклы — 25-30. При годовом объеме производства более 93 миллионов автомобилей и 140 миллионов мотоциклов в год спрос на подшипники высок как никогда и продолжает расти.
Потребность в подшипниках также возрастает в других отраслях промышленности, таких как машиностроение, электроприборы, строительная и инфраструктурная техника, авиация, производство электроэнергии. Наряду с заметным увеличением производства подшипников производители подшипников вынуждены снижать затраты. Из-за спроса на более низкие цены несколько ведущих компаний строят новые производственные предприятия в таких странах, как Китай, Индия и Восточная Европа, где производственные затраты ниже.
Более быстрые циклы обработки
Кроме того, многие производители подшипников ищут более быстрые циклы обработки и более эффективные процессы, чтобы соответствовать требованиям рынка. Они также пытаются найти варианты минимизации потерь сырья за счет оптимизации своих методов обработки и замены старых технических инструментов, которые больше не могут выдерживать высокие условия обработки и требования к длительному сроку службы.
В мире производства подшипников очень важно быть хорошо подготовленным с использованием самых инновационных инструментов, поскольку конкуренция является агрессивной, а неэффективные процессы обработки могут привести к потере бизнеса.
Опытные инженеры Iscar способны поддержать любую конструкцию подшипника с помощью передовых решений по обработке, которые могут обеспечить максимальную производительность, эффективность и точность. Большинство подшипников малого и среднего диаметра производятся серийно на многошпиндельных станках или на простых однозадачных станках, которые способны выполнять только одну или две операции на обработанных кольцах, и для завершения необходимо несколько станков этого типа. целая часть.
Знания и опыт
Необходимы знания и опыт, чтобы предоставить комплексные решения для различных областей применения с очень эффективными инструментами для операций отрезки, трепанации, обработки канавок, профилирования и токарной обработки.
Многие пластины Iscar разработаны как многогранные пластины, такие как Penta, и имеют экономические преимущества благодаря пяти режущим кромкам. Эти вставки в основном используются для операций отрезки; обработка канавок уплотнения и канавок дорожек качения, среди прочего.
Уникальная структура пластин Penta позволяет шлифовать неограниченное количество пластин различной формы и геометрии по очень привлекательной цене за кромку; тем самым помогая клиентам Iscar снизить производственные затраты, что позволяет им легко конкурировать со своей продукцией.
ВставкиPenta также можно использовать для трепанации, которая представляет собой осевую операцию разделения одного толстого кованого кольца на два отдельных наружного и внутреннего кольца. Для таких операций Iscar также предлагает другие типы вставок, такие как BGR и BGMR, для более широких колец, требующих глубокого разделения.
Многосекционные системы
Теперь предлагаются разработанные для клиентов системы многоразъемного отрезания, включающие в себя собранный набор отрезных лезвий или адаптеров, предназначенных для отрезания нескольких колец за раз.Такие наборы снабжены очень популярными вкладышами Tang-Grip и Do-Grip, а также вкладышами Penta. Такие системы разъемов резко сокращают одну из самых распространенных операций в производстве подшипников.
Уникальные отрезные изделия Iscar представлены в очень узких размерах, что позволяет производителям значительно уменьшить ширину пластин до 0,7 и 1,0 мм и, следовательно, сэкономить на сырье. Такая экономия помогает производить до 15 процентов больше колец из существующих стальных труб.Подразделение Iscar по токарной обработке предлагает широкий выбор новейших геометрий и марок твердого сплава, а также пластины из керамики и эльбора для чистовой токарной обработки закаленных колец подшипников твердостью до 64 HRc. Пластины из CBN со стружколомами являются решением Iscar для таких операций и могут легко заменить дорогостоящие процессы шлифования.
Для широких операций профилирования на многошпиндельных станках Iscar предлагает пластины V-Lock и FTB, которые подходят для широких профилей шириной от 10 до 51 мм.
Для больших колец подшипников компания Iscar разработала уникальные сверла на основе популярных сверл Sumo-Cham и уникальных вставок FCP, которые обеспечивают выдающуюся производительность и превосходное качество поверхности при таких тяжелых операциях сверления.
Большинство производителей подшипников (за исключением специальных) требуют массового производства и точной точности при соблюдении сроков и качества. Iscar обладает знаниями и опытом для предоставления комплексных решений для различных областей применения, таких как отрезка, обработка канавок и профилирование, токарная обработка, сверление и фрезерование.
ПОСМОТРЕТЬ ДРУГИЕ СТАТЬИ
● Технология покрытия igus делает металлические компоненты устойчивыми к истиранию
ХОТИТЕ БОЛЬШЕ ИНСАЙДЕРСКИХ НОВОСТЕЙ? ПОДПИСАТЬСЯ НА НАШ ЦИФРОВОЙ ЖУРНАЛ ПРЯМО СЕЙЧАС!
ПОДПИСЫВАЙТЕСЬ НА НАС В: LinkedIn, Facebook, Twitter
Элементы для успешного торцевого фрезерования Лучшие методы выбора с многозадачными системами обработки
Шариковые подшипники — обзор
1.7.4 Инжиниринг включения в практическое сталеплавильное производство — случай шарикоподшипниковой стали
Шарикоподшипниковые стали являются выдающимся примером для обсуждения чистоты стали, поскольку в этом приложении была четко установлена связь между чистотой и усталостными свойствами [47]. Общие уровни содержания кислорода в шарикоподшипниковой стали, произведенной на заводе Ovako Steel Hofors (бывшая сталь SKF) с использованием кислотного мартеновского процесса (1964 г.), а затем с использованием электродуговой печи и печи-ковша ASEA-SKF с последующей разливкой в слитки, представлены на рисунке. 1.7.11. Содержание кислорода в мартеновском процессе в 1964 году составляло в среднем 35 частей на миллион, в то время как при переходе на ковшовую печь ASEA-SKF в 1980-х годах уровень кислорода снизился с 11 в 1985 году до менее 5 частей на миллион в 1994 году, и этот уровень все еще действителен. Соответствующий прогресс также был отмечен японскими производителями стали со средним содержанием O to ≤ 5 частей на миллион в подшипниковых сталях [48]. Общее содержание кислорода дает простую меру чистоты стали, но его недостаточно, по крайней мере во многих случаях, для прогнозирования конечных свойств стали.
Рисунок 1.7.11. Общее содержание кислорода в шарикоподшипниковых сталях (1,0 % C, 0,35 % Si, 0,35 % Mn, 1,5 % Cr), произведенных в мартеновском кислом процессе (<0,001 % Al) и в ЭДП-ASEA-SKF (0,040 % Al) .
Помимо общего содержания кислорода в стали, очень важен тип включений. Включения в стали после кислотного мартеновского процесса представляли собой пластичные силикаты, которые при горячей прокатке удлинялись до чрезвычайно тонких включений, которые почти исчезали при производстве полосовой стали или тонкой проволоки.Однако в более крупных шариках и кольцах подшипников степень обжатия при качении остается умеренной, а удлиненные силикаты могут влиять на усталостные свойства. Таким образом, переход от кислотной мартеновской технологии к существующей технологии, при которой сталь раскисляется алюминием и подвергается вторичной металлургии, включая ковшовую печь и вакуумную обработку, был весьма значительным: общее содержание кислорода было снижено почти на одну десятую, а тип включения изменены с пластичных на недеформируемые. Отливка в слитки по-прежнему используется некоторыми производителями, такими как Ovako Steel Hofors в Швеции, но большинство сталелитейных заводов в настоящее время используют большие блюмы непрерывного литья даже для шарикоподшипников. Общим для всех этих производственных маршрутов является то, что важно предотвратить повторное окисление стали путем тщательной защиты от атмосферы и предотвращения загрязнения реокислительными шлаками, огнеупорными материалами, ковшовой глазурью или другими возможными загрязняющими веществами.
В практическом сталеплавильном производстве на количество, число и состав неметаллических включений влияют многочисленные параметры. Хотя разработка новых производственных маршрутов должна основываться на разумных «металлургических ограничениях» (термодинамика и кинетика, материальный и тепловой поток, конструкция реактора, выбор материалов), производственные системы очень сложны, и окончательная корректировка часто во многом основывается на опыте.На заводе требуется много специальных ноу-хау, особенно при производстве сложных сталей. Одной из проблем многих сталелитейных заводов является крайне диверсифицированное производство. В специальной сталелитейной компании производство сталей со строгими требованиями к чистоте включений может быть совмещено с производством сталей с превосходной обрабатываемостью, и в этом случае желательна гораздо более многочисленная популяция включений. Поскольку металлургическая практика в этих двух случаях совершенно различна, необходимы очень квалифицированные и хорошо образованные операторы.Важно понимать всю производственную линию от первичной печи до литья и их взаимодействия. Здесь обсуждаются некоторые общие аспекты.
В главе 1.6 были даны теоретические аспекты образования, роста и удаления продуктов раскисления. Учитывались только эндогенные включения, образующиеся в результате реакций между добавленными раскислителями и кислородом, растворенным в ванне металла. Однако в действительности фазы, окружающие сталь и в конечном итоге контактирующие со сталью на различных этапах производства, всегда имеют некоторое влияние.В качестве примера рассмотрим сталь с требованием не более 5 частей на миллион общего содержания кислорода, т. е. от O до ≤ 5 г/т стали. Для очистки стали необходимо интенсивное перемешивание для удаления включений. В результате перемешивания (барботаж газа, индукционное перемешивание) не избежать сильного взаимодействия с верхним шлаком. Следовательно, верхний шлак должен быть правильно спроектирован без нестабильных восстанавливаемых оксидов. Если, например, в верхней части ковша находится 15 кг шлака на тонну стали, каждый процент «FeO» в этом шлаке будет восстанавливаться алюминием в соответствии с реакцией:
(1.7.19)3FeO+2Al=Al2O3+3Fe
Это приводит к уменьшению содержания алюминия на 39 частей на миллион с соответствующим увеличением содержания кислорода на 35 частей на миллион (если предполагается, что образовавшийся Al 2 O 3 остается в стали). Таким образом, в случае переокисления колошникового шлака, что может быть результатом слишком большого уноса шлака из первичной печи, чистота включения может быть полностью нарушена из-за реокисления расплава. К счастью, реакция (1.7.19) происходит на границе раздела сталь/шлак, и предполагается, что большая часть образовавшегося Al 2 O 3 удаляется непосредственно в шлак.В любом случае, риск попадания в сталь новых включений достаточно серьезный. Реокисление будет более выраженным при высокой интенсивности перемешивания в ванне металла, даже если это способствует росту и удалению неметаллических включений. Также всегда существует риск образования «открытых глазков», когда поверхность стали обнажается шлаком и вступает в непосредственный контакт с атмосферой. Вообще говоря, содержание восстанавливаемых оксидов, таких как FeO и MnO, должно поддерживаться в верхнем шлаке на как можно более низком уровне.Вся производственная линия должна рассматриваться аналогичным образом. При производстве легкообрабатываемых сталей условия в ковше должны отличаться от производства особо чистых марок стали. Здесь часто используется окислительный колошниковый шлак, чтобы поддерживать достаточно высокий уровень кислорода.
Даже в промежуточном ковше и кристаллизаторе непрерывного литья заготовок необходимо учитывать возможность реакции стали с расплавленным шлаком. Было установлено четкое взаимодействие с реакциями между сталью с низким содержанием кремния и крышкой разливочного устройства с высоким содержанием SiO 2 , что приводит к потерям [Al] в стали и росту [Si] в стали соответственно [49,50]. Можно записать центральную реакцию, показывающую обменную реакцию между байпасной сталью и шлаком промежуточного ковша:
(1.7.20)2Al+3/2SiO2шлак=Al2O3шлак+3/2Si
марки стали, где реакция между флюсом для литейной формы и [Ti], растворенным в стали, может изменить состав и, следовательно, физические свойства флюса для литейной формы, что затем приведет к поверхностным дефектам [51]. Неправильная схема перемешивания в литейной форме также может привести к захвату экзогенных включений из флюса литейной формы в жидкую сталь.
При производстве специальных сталей с низким содержанием включений обычно желательно предотвратить образование включений с размером, превышающим определенный критический размер, обычно 10 мкм. В этих случаях поглощение экзогенных включений очень важно. На производственной линии необходимо проделать большую работу, чтобы получить как можно более строгие процедуры. Это включает в себя предотвращение захвата верхнего шлака из ковша во время ковшовой обработки и особенно в конце операции разливки, захвата промежуточного и литейного порошка во время разливки, захвата песка из шиберных затворов в ковшах, очистки изложниц при разливке слитков, и Т. Д.Поздние добавки в ковш влияют в том же направлении, так как новые включения образуются на очень поздней стадии и имеют меньше времени для роста и удаления перед разливкой.
Также стабильность огнеупоров очень важна для чистоты стали. Этот фактор становится все более важным по мере снижения активности кислорода в производимых марках стали. Разработка в этой области заключалась в футеровке ковшей более устойчивыми огнеупорами. Шамотный и «высокоглиноземистый» кирпичи с высоким содержанием SiO 2 использовались 30 лет назад, но уже не используются.В настоящее время распространены более стабильные огнеупоры, такие как футеровка из чистого глинозема (Al 2 O 3 ), доломита (CaO–MgO), магнезии (MgO) и типа шпинели (MgO-Al 2 O 3 ).
Как соблюдать стандарты качества при производстве шарикоподшипников
Шариковый подшипник представляет собой вращающийся элемент, который состоит из комбинации шариков, обойм подшипника и всего, что сделано из материалов, снижающих трение и поддерживающих радиальные и осевые нагрузки. Эти шарикоподшипники играют важную роль в машинах.Шариковый подшипник состоит из четырех основных частей: внешней обоймы, внутренней обоймы, шариков качения и сепаратора. Существует строгая необходимость поддерживать стандарты качества материалов, используемых и собранных для этих подшипников, из-за их использования в чувствительных зонах.
Их испытание важно и необходимо, если шарикоподшипники будут использоваться в оборудовании, используемом в космосе, медицинском оборудовании или других областях, где точность этих элементов обеспечивает точную работу оборудования.
«Комитет инженеров по кольцевым подшипникам» (ABEC) разработал различные классы, которые обеспечивают стандарты качества различных деталей подшипников, созданных для конкретных машин. Качество шарикоподшипников проверяется путем проверки их допуска, крутящего момента, жесткости, точности и смазки. Они рассчитаны и протестированы с точностью до мельчайших единиц точности. Это делает шарикоподшипник более предсказуемым и экономичным.
Допуск : Шариковый подшипник должен соответствовать требованиям допуска ABEC.Когда размер и форма шарикоподшипников откалиброваны и соответствуют указанному стандартному коду или классу, тогда они соответствуют требуемым спецификациям стандарта качества.
Крутящий момент : Крутящий момент подшипника можно рассчитать и проверить с помощью устройств для проверки качества крутящего момента. Когда требуется очень точное оборудование, производительность элементов должна быть высокой, а техническое обслуживание должно быть минимальным или минимальным. Производители должны убедиться, что подшипники созданы с учетом высоких эксплуатационных характеристик и низких эксплуатационных расходов.
Жесткость : При изготовлении шарикоподшипника важно сохранять жесткость компонентов. Очень важно проверить жесткость подшипника при длительном интенсивном использовании в различных погодных условиях. Испытания подшипника в различных условиях, таких как жара, холод или колебания температуры, предоставляют необходимые данные для того, чтобы он функционировал в различных погодных условиях, выполняя этапы исправления в процессе производства.
Точность : ABEC уделяет большое внимание тому, чтобы шарикоподшипники были максимально точными по размеру, размерам и весу.Учитывая это, все подшипники, которые часто изготавливаются из нержавеющей стали или других сплавов, не обязательно должны быть точными. Чтобы получить точный подсчет, детали подшипников проходят строгий производственный процесс, прежде чем они будут объявлены готовыми. Нельзя не подчеркнуть, почему эти детали должны быть точными до мельчайших миллиметров. Поскольку наибольшая чувствительность элементов ожидается в определенных отраслях, где он используется.
Смазка : Некоторые шарикоподшипники поставляются со смазкой.В таком случае производители должны очень внимательно следить за тем, чтобы никакие загрязнения не попали в смазываемые части шарикоподшипника. Если шариковый подшипник собирает пыль, он может работать неправильно. Поэтому важно протестировать их в среде без пыли.
Курс обзора экзамена FE уточняет соответствующие темы, перечисленные NCEES для их экзамена FE, и с помощью этого экзамена NCEES может оценить знания студента, связанные с контролем качества и обеспечением качества производства.

Полная история подшипников, которую необходимо знать
Эти жизненно важные элементы технологии не появились в одночасье, когда началось создание металлических машин.На самом деле подшипники имеют долгую историю использования, которая восходит к каменному веку.
Поскольку подшипники имеют жизненно важное значение для удовлетворения потребностей ваших клиентов, важно иметь всестороннее представление о том, как подшипники были созданы и как они развивались, чтобы предоставить нам современное решение для различных нагрузок и задач.
В Bearing & Drive Systems мы знаем, что беспокойство по поводу предоставления некачественной продукции вашим клиентам реально, но это не обязательно.
Мы стремимся предоставлять глобальные сетевые решения, которые помогут вам найти подлинные подшипники и продукты PT, которые нужны вашим клиентам прямо сейчас.
В этой статье мы обсуждаем полную историю подшипников и их эволюцию до современных технологий.
Краткая хронология истории подшипников
youtube.com/embed/AKJXDuOKE20″ frameborder=»0″ allowfullscreen=»» data-service=»youtube»/>
Источник: «Краткая история подшипников» от JVN Bearings FZE через YouTube
2600 г. до н.э. — Древние египтяне использовали роликовые подшипники для перемещения больших каменных блоков, которые предназначались для строительства пирамид.
40 г. до н.э. — Ранний известный пример деревянного шарикоподшипника использовался для поддержки вращающегося стола.Этот пример был найден среди останков затонувшего римского корабля в озере Неми, Италия.
1500 г. н.э. — Чертежи чертежей и ранний концептуальный дизайн вертолета Леонардо да Винчи использовали шарикоподшипники. Это первое известное зарегистрированное использование подшипников в аэрокосмической технике.
17 век — Галилей впервые описывает подшипник с сепаратором
1740 — Джон Харрисон изобретает первый роликовый подшипник с сепаратором для морского хронометража h4. Он и не подозревал, что использовал тот же подшипник в современных регулирующих часах.
1794 — Первый патент на беговые мячи был выдан Филипу Вону из Кармартена, Уэльс. Его конструкция включала шарик, движущийся по канавке в узле оси.
1869 — Парижский веломеханик Жюль Сурирэ получает первый патент на радиальный шарикоподшипник, который он установил на велосипеде-победителе первой в мире велогонки в Париже.
1898 — выдан первый патент на конические роликоподшипники Timken.В следующем году Генри Тимкен основал свою компанию.
1907 — Свен Вингквист из SKF изобретает новые самоустанавливающиеся шарикоподшипники. Это установило новый стандарт конструкции, и благодаря ему появились инновации, такие как подшипник с проволочной обоймой в 1934 году и подшипник с клиновидной канавкой в 1968 году соответственно.
1917 — Во время Первой мировой войны производители подшипников в США решили создать неформальную группу для оказания помощи в производстве подшипников. Это привело к созданию Американской ассоциации производителей подшипников (ABMA).
1980-е годы — Здесь мы увидели первый двухкомпонентный подшипник скольжения, который изобрел Роберт Шредер. Шредер был основателем Pacific Bearing.
2000-е годы — Теперь мы видим шариковые и роликовые подшипники, используемые во всех видах промышленного применения, от колесных подшипников в автомобильной промышленности до сверхвысокоскоростных подшипников, используемых в стоматологических бормашинах, и во всем, что между ними.
Теперь, когда мы рассмотрели хронологию истории подшипников, давайте углубимся в более глубокую историю того, как возникла идея первого подшипника и как она превратилась в современные типы подшипников, которые мы используем каждый день.
Древние истоки рождения
Хотя многие считают колесо первым изобретением ранних цивилизаций, концепция подшипника технически превосходит его. С древних времен человечество работало над поиском и разработкой новых способов уменьшения трения.
Изучив древнеегипетские настенные росписи, историки определили, что пирамиды были построены из массивных тяжелых камней, поставленных друг на друга.
Но как они двигали эти тяжелые камни? Благодаря примитивным телам качения.
Верно. Согласно ряду настенных росписей, изображающих строительство пирамиды, ученые обнаружили изображения бревен, закатываемых под массивные камни. Это было сделано, чтобы уменьшить трение и упростить транспортировку тяжелых камней за счет приложения меньшего усилия. [источник]
Этот метод транспортировки проложил путь к идее использования тел качения, также известных как ролики, в подшипниках.
Несмотря на то, что это первый зарегистрированный случай уменьшения трения человечеством, на протяжении всей истории человечества существует множество других записей, которые различаются по периодам времени и используемым методам.
Это показывает, насколько важным было снижение трения для обеспечения более плавного движения на протяжении всей истории человечества.
Леонардо да Винчи, отец современного подшипника
Леонардо да Винчи, известный как один из самых влиятельных людей эпохи Возрождения в Италии, считается «отцом» современной осанки». Благодаря своему ненасытному любопытству он оставил значительный след в мире искусства, а также в области механики дизайн.
В одной из его тетрадей ученые нашли рисунок подшипника, который теперь считается символом изобретательности, создавшей подшипники, уменьшающие трение.
Структура, которую набросал да Винчи, состояла из двух колец (известных как дорожки), которые были сверху и снизу, а также катящихся шариков (известных как элементы качения), застрявших между кольцами, и «клетки», чтобы шарики не попадали внутрь. контакт друг с другом. [источник]
Эскиз, созданный да Винчи, практически идентичен конструкции подшипников, которые мы используем в наши дни. Эта «базовая несущая конструкция» из дорожек, тел качения и сепаратора была придумана почти 500 лет назад благодаря гению Леонардо и продвинула подшипниковую технологию вперед в монументальных масштабах.
Хотя мы приписываем Леонардо да Винчи открытие основной несущей конструкции, создание и массовое производство подшипников все еще оставалось нетронутым делом. Только во время промышленной революции подшипники стали широко использоваться в машинах.
Как подшипники способствовали промышленной революции
Промышленная революция длилась с середины 18 века по 19 век. Этот период примечателен для подшипников из-за большого количества производства стали.Это позволило впервые в истории начать массовое производство высокопрочных подшипников, что сделало подшипники пригодными для использования в самых разных областях промышленности.
Кроме того, подшипники стали неотъемлемой частью промышленной революции благодаря их роли в обеспечении эффективной работы оборудования.
Одним из самых заметных открытий промышленной революции были оси, использующие подшипники. Первоначально шарикоподшипник использовался для осей в велосипедах, в которых в качестве элемента качения использовался шарик, получивший широкую популярность.
Первый зарегистрированный современный патент на шарикоподшипники был выдан британскому изобретателю и мастеру по металлу Филипу Вогану. В 1794 году он запатентовал первую конструкцию шарикоподшипников, предназначенных для поддержки оси вагона. [источник] Конструкция позволяла шарикоподшипникам перемещаться по направляющей или шариковой дорожке в узле оси, что позволяло колесам свободно вращаться.
Парижский веломеханик Жюль Сурирэ в 1869 году получил патент на радиальный шарикоподшипник, устанавливаемый на металлические велосипеды.Успех его улучшенной конструкции привел к созданию нескольких новых типов металлических шарикоподшипников.
Позже был разработан роликовый подшипник, в котором в качестве тела качения использовался ролик, и который использовался для осей в конных повозках. Открытие оси на основе подшипников привело к скачку в движении и транспортировке.
Подшипники в наши дни
В 20 веке усовершенствование подшипников напрямую привело к прогрессу в военной, автомобильной и станкостроительной промышленности. Ассортимент элементов качения расширился от шариков до роликов, сферических роликов и конических роликов. Не говоря уже о том, что подшипники теперь могут выдерживать комбинированные нагрузки (осевые и радиальные) и выдерживать большие нагрузки.
Свен Винквист известен своей ролью в разработке конструкции самоустанавливающихся шарикоподшипников, которая произвела революцию в новом стандарте с точки зрения дизайна. Изобретение Винквиста в 1907 году привело к быстрой череде инноваций в этой области, от подшипника с проволочной обоймой до подшипника с клиновидным пазом.[источник] Растущий спрос на шарикоподшипники побудил основать несколько специализированных подшипниковых компаний.
В 1917 году производители подшипников в США создали неофициальную группу для оказания помощи в производстве подшипников во время Первой мировой войны. Основание ABMA (Американской ассоциации производителей подшипников) привело к созданию системы нумерации, которая до сих пор используется во всем мире для производства подшипников. и производство всех типов стандартных подшипников. [источник]
По данным Hartford Technologies, металлургические процессы совершенствовались по мере расширения нашего понимания химии.Это привело к созданию более твердых и износостойких материалов и улучшенных смазочных материалов, что позволило подшипникам работать при более высоких температурах и скоростях, чем когда-либо прежде.
Сегодня подшипники используются по-разному, как в малых, так и в больших масштабах. Некоторые примеры включают автомобили Формулы-1, стоматологические бормашины, коробки передач и ступичные подшипники в автомобильной промышленности, изгибные подшипники в механизмах оптического выравнивания, ступицы велосипедных колес и многое другое. [источник]
Заключение
Хотя в повседневной жизни подшипники часто остаются незамеченными, можно с уверенностью сказать, что без изобретения подшипников наш мир был бы другим.Инновация, которую принесли подшипники, позволила человечеству с легкостью перемещать тяжелые предметы и создала удобства с помощью современного оборудования.