Производство вата: Медицинская вата. Производство и продажа хирургической ваты.
Технология производства минеральной ваты, производители в России
Каменная вата — это разновидность утеплителя, изготовленного на основе габбро-базальтовых горных пород, который позволяет выполнять тепло- и звукоизоляцию различных сооружений или же осуществлять противопожарную защиту.
Благодаря своим физико-химическим свойствам данный тип утеплителя служит в качестве основной энергосберегающей технологии при отделке фасадов, кровли, полов и инженерных сетей как промышленных, так и полупромышленных и бытовых объектов.
Технология производства каменной минеральной ваты
Производство минеральной (базальтовой) ваты заключается в плавке горных пород при температуре 1500 С. После чего, жидкая лавоподобная масса с помощью центрифуги, специальных фильтров на основе платины или других тяжело плавких металлов и сильных воздушных потоков вытягивается в каменные волокна.
Далее в полученные волокна добавляются различные водоотталкивающие добавки и пластификаторы, после чего, при температуре порядка 200 С происходит процесс полимеризации в результате чего оборудование для производства минеральной ваты выпускает готовые базальтовые плиты, которые разрезаются в соответствии с необходимыми размерами.
Химический состав каменной ваты
Поскольку производство теплоизоляционных материалов данного класса осуществляется исключительно из горных пород, полученные базальтовые волокна имеют следующий химический состав:
- Диоксид кремния SiO2 в количестве от 45 до 55%.
- Диоксид титана TiO2 с массовой долей от 1.36 до 2%.
- Оксид кальция CaO в количестве от 7 до 11%.
- Окислы железа FeO и Fe2O3 с массовой долей от 5,38 до 13,5%.
- Оксид мангана MnO в диапазоне от 0,25 до 0,5%.
- Оксид алюминия Al2O3 с процентной долей от 14 до 20%.
- Оксид марганца MgO в количестве от 3 до 8%.
- Оксида натрия и калия (Na2O, K2O) в количестве от 2,7 до 7,5%.
- Прочие вещества составляют не более 5%.
Все вышеуказанные оксиды связываются между собой при помощи битумных, синтетических или композиционных связующих, или же при помощи бентонитовой глины.
Основной показатель качества полученного базальтового волокна — это модуль кислотности, который зависит от соотношения между кислотными и основными (лужными) окислами. Его значение регламентируется согласно требованиям ГОСТ 4640-93 «ВАТА МИНЕРАЛЬНАЯ. Технические условия».
Согласно вышеуказанному документу, каменная вата подразделяется на 3 категории:
- Категория «А» с показателем модуля кислотности от 1,6 и выше.
- Категория «Б» с показателем модуля кислотности в диапазоне от 1,4 до 1,6.
- Категория «С» с показателем модуля кислотности ниже 1,4.
Как видно из вышеуказанной категорийности, чем выше показатель модуля кислотности, тем высшего качества получается базальтовая вата, поскольку она является более долговечной и влагостойкой.
Очень часто для регулирования вышеуказанного показателя производители применяют различные добавки на основе карбонатных соединений.
Виды и сфера применения базальтовых волокон
Оборудование для производства минеральной ваты позволяет изготавливать следующие виды каменного (базальтового) волокна:
- Микротонкие волокна для изготовления фильтров тонкой очистки воздушной или жидкостной среды с диаметров волокон менее чем 0.
6 мкм.
- Ультратонкие каменные волокна применяются в фильтрах тонкой очистки воздушной, газовой или жидкостной среды, или же при изготовлении сверхлёгких звуко- и теплоизоляционных материалов с диаметров волокна в диапазоне от 0,6 до 1 мкм.
- Супертонкие (микрокристаллические) базальтовые волокна служат для изготовления теплозвукоизоляционных гидрофобизированных изделий (матов или рулонов), различных жгутов и фильтров. Данный тип волокон считается наиболее популярным, поскольку благодаря специальной термической обработке, полученные микрокристаллы способны выдерживать температуру на 200 С выше чем предыдущие типы волокон. Также супертонкое микроволокно (диаметр от 1 до 3 мкм) не усаживается в процессе эксплуатации, что значительно увеличивает спектр применения данного материала.
- Тонкие волокна на минеральной основе представляют собой хаотические структуры с диаметром волокна в диапазоне от 9 до 15 мкм. Длинна отдельных волокон колеблется в диапазоне от 3 до 2000 мм.
- Утолщенные каменные волокна в большинстве случаев применяются в качестве основных систем фильтрации дренажных систем. Толщина данного типа волокон колеблется в диапазоне от 15 до 25 мкм, а длинна от 5 до 1500 мм.
- Толстые волокнистые структуры представляют собой хаотически расположенные волокна с диаметром от 25 до 150 мкм и длинной одного волокна от 0,05 до 3 м. Благодаря этому полученный материал может выдерживать колоссальные нагрузки на разрыв до 650 МПа.
- Грубые волокна — дисперсионно волокнистая масса из волокнистых структур толщиной от 150 до 500 мкм. Данная разновидность утеплителя может применяются в качестве армированного слоя при помощи специальных вяжущих элементов.
Сфера применения базальтовой (каменной) ваты
В связи с тем, что каменная вата является натуральным негорючим и долговечным материалом (поскольку на 95% состоит из натурального камня) она широко стала применятся в строительстве еще с начала 20-го века.
Благодаря своим отменным свойствам, которые заключаются в снижении потерь тепловой энергии в холодный период времени, и в сокращении попадания тепловой энергии вовнутрь здания летом, каменная вата широко применяются в следующих сферах:
- При утеплении фасадов зданий с последующей штукатуркой или монтаже сайдинга или профильного листа.
- При утеплении помещения изнутри (балконы, лоджии, наружные стены и т.д.).
- При возведении перегородок из листов ГКЛ в квартирах, промышленных или офисных зданий для звукоизоляции.
- При утеплении основания пола с последующей заливкой стяжки.
- Для звукоизоляции «плавающего пола».
- При устройстве кровли или утеплении мансардных этажей.
- Для огнезащиты инженерных конструкций и сетей (данный материал способен выдерживать температуру до 700 С).
Достоинства каменной ваты (базальтового утеплителя)
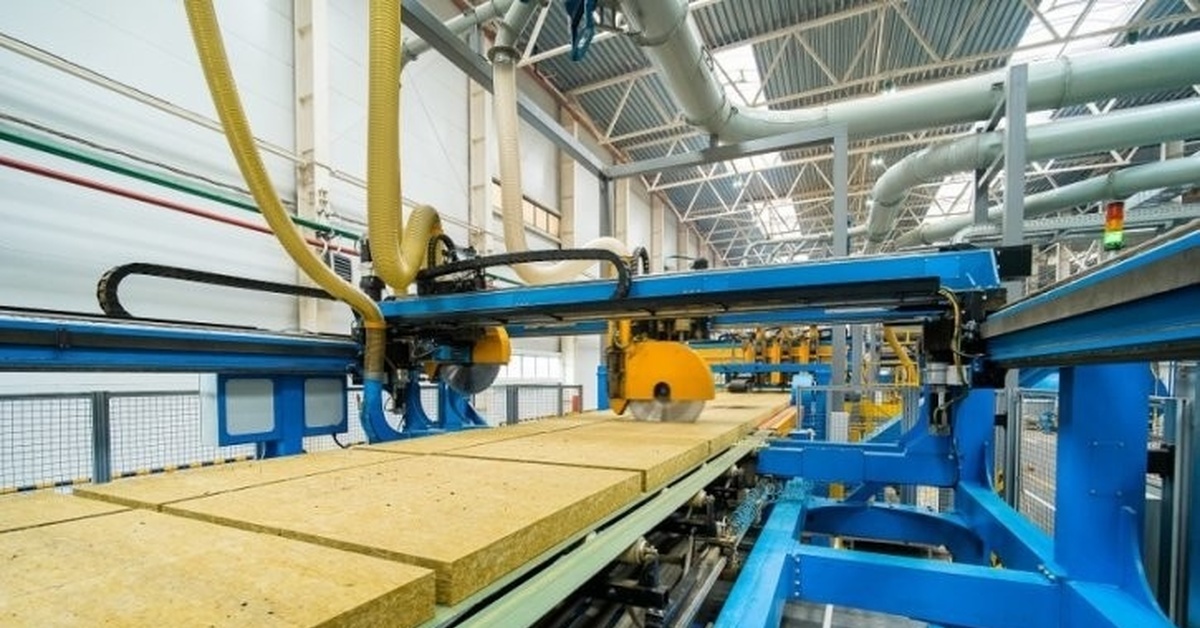
Пористая структура. Благодаря данному свойству волокна составляют всего 70% от общего объема материала. Остальная часть — это прослойки воздуха, которые обеспечивают низкую теплопроводность полученного материала.
Огнеупорность. Данное свойство позволяет производить утепление как паропроводов, так и промышленного оборудования с высокими температурами. Поскольку материал изготавливается из натурального камня, он способен выдерживать температуру до 7000С.
Высокая паропроницаемость. Благодаря этому свойству материал не впитывает, а пропускает через себя влагу без образования конденсата.
Основные производители каменной ваты
На современном рынке, существует 3 основных производителя минеральной ваты на базальтовой основе:
- Технониколь.
- Knauf.
- Rockwool.
Минеральная вата Технониколь
Данный материал служит для тепло- и звукоизоляции фасадов, кровли, перегородок и технологических трубопроводов. Плотность данного материала находится в диапазоне от 30 (РОКЛАЙТ и ТКХНОЛАЙТ Экстра) до 145 кг/м3 (ТЕХНОФАС).
На современном рынке России, данный продукт представлен следующими разновидностями:
Наименование | Номинальная плотность, кг/м3 | Тепловая характеристика, Вт/м*0С | Область применения |
РОКЛАЙТ | 30 | 37-41*10-3 | Теплоизоляция стен и перегородок внутри помещения, утепление скатной кровли и полов на лагах |
ТЕХНОЛАЙТ ЭКСТРА | 35 | 36-41*10-3 | Устройство звуко- и теплоизоляции перегородок офисных и бытовых помещений |
ТЕХНОФАС | 145 | 36-42*10-3 | Утепление фасадов перед последующей штукатуркой или отделкой с помощью сайдинга |
ТЕХНОФЛОР | 90-170 | 34-47*10-3 | Утепление плавающих, теплых или наливных полов с последующим устройством цементно-песчаной стяжки |
ТЕХНОРУФ | 140-190 | 36-42*10-3 | Основной теплоизоляционный слой при новом строительстве или проведении реконструкции кровельного покрытия без необходимости в последующей стяжке |
ТЕХНОБЛОК СТАНДАРТ | 45 | 34-39*10-3 | Утепление и звукоизоляция всех типов зданий и сооружений, в которых слой утеплителя не подвержен высоким статическим нагрузкам |
ТЕХНОВЕНТ СТАНДАРТ | 80-90 | 33-40*10-3 | Устройство вентилируемых фасадов |
Базальтовая вата Knauf
Каменная вата Кнауф — это эффективная тепло- и звукоизоляция на основе горных пород, которая обладает высокой паропроницаемостью, химической стойкостью к кислотам, лугам и продуктам нефтепереработки.
На рынке России данный материал выпускается под маркой Knauf Insulation и представлен следующим ассортиментом:
Наименование | Номинальная плотность, кг/м3 | Тепловая характеристика, Вт/м*0С | Область применения |
Insulation DDP | 150-200 | 40*10-3 | Утепление и звукоизоляция плоской кровли, угол наклона которой не превышает 150 |
Insulation DDP-K | 105-110 | 37-41*10-3 | Утепление и звукоизоляция плоской кровли, угол наклона которой не превышает 150, а также для утепления плавающих полов |
Insulation FKD | 140-150 | 39*10-3 | Утепление наружных фасадов здания или устройство вентилируемых фасадов |
Insulation FKD-S | 100-140 | 36*10-3 | Утепление стен снаружи и устройство скрепленных фасадов |
Insulation FKL | 85 | 40*10-3 | Наружное утепление стен перед монтажом сайдинга |
Insulation HTB | 35-150 | 37-39*10-3 | Утепление инженерных сетей, трубопроводов и воздухопроводов с температурой от -180 до 7000С |
Insulation LMF AluR | 35-90 | 40*10-3 | Утепление инженерных сетей, трубопроводов и воздухопроводов с температурой от -180 до 7000С |
Insulation PVT | 175 | 40*10-3 | Утепление перекрытий и плавающих полов |
Insulation WM 640 GG/WM 660 GG | 80-100 | 35*10-3 | Утепление технологического оборудования и трубопроводов |
Insulation цилиндры | 75 | 40*10-3 | Техническая изоляция инженерных сетей и трубопроводов |
Базальтовая вата Rockwool
Продукция концерна Роквул — это высокоэффективные гидрофобизированные минеральные плиты, изготавливаемые из базальтовой породы с добавлением специальных добавок для улучшения технических характеристик.
Компания предлагает на территории России следующий ассортимент:
Наименование | Номинальная плотность, кг/м3 | Тепловая характеристика, Вт/м*0С | Область применения |
EPIROCK | 20 | 45*10-3 | Утепление вентилируемых перекрытий, а также деревянных полов на лагах |
ROCKROLL | 22 | 44*10-3 | Утепление вентилируемых перекрытий, а также деревянных полов на лагах |
ROCKSLAB ACUSTIC | 50 | 36*10-3 | Звукоизоляция перекрытий и перегородок помещений различного назначения |
ROCKSLAB | 26 | 42*10-3 | Утепление стен, потолков и полов без нагрузки на слой каменной ваты |
STEPROCK HD | 140 | 39*10-3 | Утепление строительных конструкций и перекрытий с высокими динамическими нагрузками |
ROCKMIN | 26 | 39*10-3 | Устройство не нагружаемого теплоизоляционного слоя |
STEPROCK HD4F | 140 | 39*10-3 | Устройство динамического модуля упругости для производственных и жилых зданий |
FRONTROCK S | 110 | 39*10-3 | Утепление фасадов зданий и сооружений с последующим нанесением армированного слоя и штукатурки |
MONROCK MAX E | 115-220 | 37*10-3 | Утепление всех типов перекрытий без необходимости в последующем устройстве цементно-песчаной стяжки |
FIREROCK | 80 | 42*10-3 | Теплоизоляция поверхности каминов и технологического оборудования |
Выводы
Оборудование для производства минеральной ваты позволяет изготавливать высокоэффективные утеплители для любых типов помещений, а также обеспечивать надёжную тепло- и звукоизоляцию как кровли, так и полов, и стен.
На современном рынке можно найти большое разнообразие минеральных утеплителей на основе базальтовых пород, которые обладают не только высокими техническими характеристиками, но и обеспечивают огнеупорность технологическим трубопроводам в соответствии с мировыми стандартами.
Как производят каменную вату — Как это сделано, как это работает, как это устроено — LiveJournal
В сентябре этого года мы с Наталей Меелис 13vredina, Анастасией Сергеевой yaginya и Евгением Вовнеем vovney побывали в г. Юрга Кемеровской области, на заводах по производству рулонных кровельных материалов, экструзионных пенополистирольных плит и каменной ваты.
Сегодня мой рассказ и показ о третьем заводе — заводе по производству каменной (базальтовой) ваты.
«Быстрее! Быстрее пойдемте смотреть на процесс!» — позвали нас, увлекшихся вырезанием лего из экструзионного пенополистирола (мне из ЭПП сердечко вырезали!).
Заинтригованные, мы думали, что сейчас из этих серых полистирольных кубиков еще что-нибудь забабахают, но нас посадили в машину и помчали к другому заводу.
Завод по производству каменной ваты стал третьим заводом корпорации ТехноНИКОЛЬ в Сибири и на юргинской площадке в частности. В 2013 году с конвеера только этого завода сети вышло почти 900 тысяч кубов продукции.
Каменная вата является высокоэффективным теплоизоляционным материалом. По термической эффективности она готова соперничать с эталонным теплоизолятором – воздухом в неподвижном состоянии. Высокое сопротивление теплопередачи достигается за счёт удержания большого количества воздуха в неподвижном состоянии внутри утеплителя при помощи тесно переплетённых тончайших волокон минеральной ваты.
Наталя 13vredina с плодами трудов из XPS.
На заводе мы нарядились в респираторы и пошли в цех. Каски и жилеты уже были на нас.
Такого, конечно, я не видела никогда. Для кого-то это трудовые будни, а для меня это было завораживающее зрелище: мужчины в серебряных костюмах и шлемах колдовали у вагранки (это такая шахтенная печь). Почему-то в голове вертелась песня Чичериной: пожаааарные в серебряных касках добрые и ласссковые…
Производство каменной ваты — это сложный, многоступенчатый технологический процесс.
Горные породы габбро-базальтовой группы (сырье) доставляются на склад сырья.
В начале производственного цикла сырье просеивается и крупная фракция подается на дозаторы, которые тщательно взвешивают сырьевые компоненты.
Только после этого шихта (смесь исходных компонентов) подается в вагранку — вертикальную шахтную печь. Установленные на заводе коксогазовые вагранки на горячем дутье позволяют получить расплав требуемой температуры (около 1500 °С) и нужной вязкости.
Это жерло той самой вагранки. Там внутри порядка 1500 градусов по Цельсию!
Схематично вагранка выглядит примерно так:
Почти что дверь в Нарнирю.
а потом из печи полился расплавленный металл!
После тележку с чашей быстро оттаскивает второй прекрасный мужчина в серебряных одеяниях.
Это выплавленный из базальта металл — отходы производства. Потом на этом же заводе из него сделают брикеты, которые потом также будут пущены в расход.
Итак, полученный расплав направляется на многовалковую центрифугу, где под действием центробежной силы капли расплава вытягиваются в волокно. Исходное сырье и стабильность состава расплава позволяют получить качественную минеральную вату с высокой химической стойкостью и долговечностью. В момент волокнообразования через форсунки, установленные на центрифуге, подается связующее с добавками гидрофобизатора и обеспыливателя по новейшей технологии, разработанной в собственном научном центре компании.
Нам не удалось увидеть этот процесс собственными глазами, но нам рассказали, что это похоже на то, как получается сахарная вата.
Многовалковая центрифуга
Только из базальта.
Процесс выплавки закончился, а мы все стояли завороженные и продолжали щелкать камерами фотоаппаратов и телефонов. Нас вывели из транса и пока в недрах машин вытягивались каменные волокна, мы последовали в цех, где происходит остальное действо.
Безопасности на заводе уделяется очень много внимания. Повсюду — в цехах, на погрузочных площадках и на территории заводского комплекса развешаны мотивирующие плакаты.
Не знаю как брутальных мужчин, а меня пробрало и я даже старалась не сходить с пешеходных дорожек. Вот эти белые зебры — это траектория движения пеших посетителей.
Так вот, из многовалковой центрифуги базальтовое волокно, обработанное связующим, охлаждаясь потоком воздуха, попадает на транспортер. Так образуется первичный «ковер» из минеральной ваты, который поступает на маятниковый раскладчик, обеспечивающий равномерную плотность производимой продукции.
Маятниковый раскладчик.
После маятникового раскладчика «ковер» поступает на гофрировщик-подпрессовщик, который придает будущему изделию гофрированную структуру за счёт частичной вертикальной ориентации волокон, что позволяет добиться высоких механических свойств готовой продукции.
Гофрировщик-подпрессовщик.
Сформированный таким образом «ковер» поступает в камеру термообработки, где при температуре 200-250°С происходит отверждение связующего и задаются основные физико-механические характеристики.
От качества проведения этого процесса зависит качество продукции в целом. Все технологические процессы на линии контролируются автоматикой. В условиях повышения норм, регламентирующих отклонения от заданных геометрических размеров строительных материалов, большое внимание уделяется точности резки готовых изделий.
Наталя 13vredina радуется жизни
Кстати, резать можно не только по прямой. Вот пример затейливой фигурной резки. Жаль, нам не дали повырезать как в лаборатории пенополистирола, а то мы бы ух!
Готовая к применению продукция упаковывается в специальную термоусадочную пленку, которая позволяет хранить поддоны с продукцией под открытым небом, без потери товарного вида и ухудшения эксплуатационных качеств продукции.
Кстати, заводы поразили меня обилием естественного света в производственных помещениях. Я ожидала чего-то другого, видимо исходя из моих представлений о полузаброшенных цехах на заводах где десятилетиями не мылись пыльные окна.
Из цеха нас повели в испытательную лабораторию, где минвату рвали, топили, жгли, а также показывали фокусы.
Лаборатория проверки качества продукции
Сначала рвали. Вот такими машинами.
[результат испытания в кПа и прочих цифрах]результат испытания в кПа и прочих цифрах
[результат испытания в кПа и прочих цифрах]
Потом топили
Как видно, вода скаталась на поверхности в кругляши, внутрь не впиталась.
Потом нас привели в большую комнату и отожгли стали жечь вату газовой горелкой, отчего на ней образовалось коричневое пятно, но загореться она так и не загорелась. Технология.
Тепловизор нам говорит, что под струей горелки горячо.
Чтобы все было без обмана, с обратной стороны поджигаемой плиты ее можно было трогать руками.
Кстати тут видно, что сквозное пятно от огня не образовалось.
На тепловизоре все учтено и зафиксировано. Плита с обратной стороны нагрелась только от соприкосновения с рукой.
Потом было самое любопытное для меня испытание. Самое — потому что я адепт тишины. Будь моя воля, я бы звукоизолировала все, потому что меньше всего я хочу знать о чем говорят иностранные штукатуры-маляры за стеной и о чем плачет соседский ребенок. Ну еще не люблю, когда топают над головой. Поэтому тест на звукоизоляцию был для меня интересен более других. Я даже не пожалела телефона для такого мероприятия.
В гипсокартонный бокс с минватой добровольцы сложили свои любимые звонилки.
Ларчик закрывается
В этот момент остальные, кто зажал мобилку с камерой позвонить, набирают нам. В комнате звенящая тишина, в которую врываются только гудки дозвона.
Ящик открывается и вуаля! Кому-то не повезло и 5й айон превратился в будильник и трубку гороского телефона. Шутка. Для чистоты эксперимента мы складывали туда всё шумящее, что было в лаборатории.
Я не удержалась и задала в лаборатории вопрос: «а правда ли, что расположенная вертикально, каменная вата со временем оседает?» (Это я прочитала, когда выбирали входную дверь)
«Нет, не правда,» — сказали мне. Продукция бывает для горизонтальной укладки и для вертикального размещения. Правильно подобранный по назначению материал гарантированно сохраняет свои свойства несколько десятков лет. При этом в глазах не было ни тени сомнения. Я в уме стала просчитывать расход на звукоизоляцию стен с соседями.
Евгений vovney делает серьезное лицо, как будто сам придумал каменную вату )))
Кстати, весь цикл производства каменной ваты выглядит примерно вот так:
Производство и экологическая безопасность
Завод по производству каменной ваты (как и другие заводы этой компании в Юрге — по производству рулонных гидроизоляционных материалов и экструзионного пенополистирола) является безотходным и бессточным производством.
Что это значит?
Бессточные технологические системы и водооборотные циклы — это когда технологические воды предприятия не выходят из производства минеральной ваты. Вся техническая вода используется в приготовлении связующего раствора внутри самого производства.
Для реализации безотходности внедрена система утилизации отходов производства как вторичный материальный ресурс. В производственных цехах установлено высокоэффективное газо- и пылеулавливающие оборудование. На заводе используются в дальнейшем производстве образующиеся отсевы камня, кокса, отходы и брак минераловатных изделий, уловленная отфильтрованная пыль от установок газоочистки, использованные фильтрующие элементы кассетных фильтров газоочистки.
Для уменьшения общей массы образующихся отходов и для экономии сырья, предусмотрен участок изготовления брикетов цеха сырья и переработки отходов производства. На установке брикетирования из отходов производства получают брикеты для их использования вместе с исходным сырьем в вагранках для производства минеральной ваты.
В совокупности эти мероприятия позволяют обеспечить экологическую безопасность производства.
[кнопочки]
Производители ваты минеральной из России
Продукция крупнейших заводов по изготовлению ваты минеральной: сравнение цены, предпочтительных стран экспорта.
- где производят вата минеральная
- ⚓ Доставка в порт (CIF/FOB)
- вата минеральная цена 11.01.2022
- 🇬🇧 Supplier’s Cotton wool mineral Russia
Страны куда осуществлялись поставки из России 2018, 2019, 2020, 2022
- 🇰🇿 КАЗАХСТАН (145)
- 🇺🇦 УКРАИНА (119)
- 🇲🇩 МОЛДОВА, РЕСПУБЛИКА (38)
- 🇦🇿 АЗЕРБАЙДЖАН (36)
- 🇨🇿 ЧЕШСКАЯ РЕСПУБЛИКА (20)
- 🇺🇿 УЗБЕКИСТАН (19)
- 🇫🇮 ФИНЛЯНДИЯ (15)
- 🇹🇯 ТАДЖИКИСТАН (11)
- 🇹🇲 ТУРКМЕНИЯ (9)
- 🇩🇪 ГЕРМАНИЯ (9)
- 🇱🇻 ЛАТВИЯ (8)
- 🇳🇴 НОРВЕГИЯ (8)
- 🇰🇬 КИРГИЗИЯ (7)
- 🇧🇬 БОЛГАРИЯ (6)
- 🇪🇪 ЭСТОНИЯ (6)
Выбрать вату минеральную: узнать наличие, цены и купить онлайн
Крупнейшие экспортеры из России, Казахстана, Узбекистана, Белоруссии, официальные контакты компаний. Через наш сайт, вы можете отправить запрос сразу всем представителям, если вы хотите купить
вату минеральную.
🔥 Внимание: на сайте находятся все крупнейшие российские производители ваты минеральной, в основном производства находятся в России. Из-за низкой себестоимости, цены ниже, чем на мировом рынке
Поставки ваты минеральной оптом напрямую от завода изготовителя (Россия)
Крупнейшие заводы по производству ваты минеральной
Заводы по изготовлению или производству ваты минеральной находятся в центральной части России. Мы подготовили для вас список заводов из России, чтобы работать напрямую и легко можно было купить вата минеральная оптом
шлаковата
Изготовитель смеси и изделия из теплоизоляционных
Поставщики панели
Крупнейшие производители металлоконструкции
Экспортеры Части машин и механических устройств
Компании производители фрикционные материалы и изделия из них(листы
Производство Феноло-альдегидные смолы
Изготовитель Изделия из стекловолокна: нетекстильные волокна навалом или в пучках
ISOVER в России | Компания «Сен-Гобен» (Saint-Gobain)
ISOVER – первый и единственный в России производитель минеральной ваты как на основе кварца, так и на основе базальта.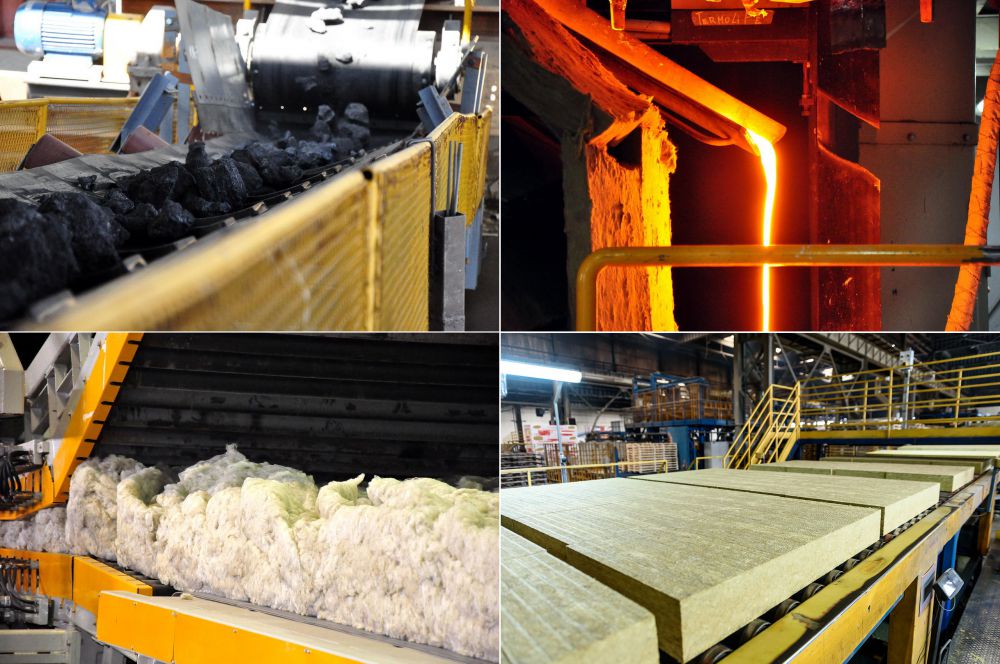
Продукция ISOVER на основе кварца производится по собственно разработанной технологии, которую сейчас успешно применяют по всему миру.
В России минеральную теплоизоляцию и шумоизоляционные материалы производят на заводе в г. Егорьевск (Московская область) — одном из крупнейших предприятий ISOVER в мире. Ежегодно здесь выпускается более 70 000 тонн утеплителей и звукоизоляции. Это единственное в России предприятие, которое может производить продукты из кварца с высокой механической прочностью. В 2011 году завод успешно прошел сертификацию по международному стандарту экологического менеджмента ISO 14001-2004.
ISOVER первый в России производитель минеральной ваты, который прошел сертификацию на соответствие ГОСТ 32314-2012 (EN 13162:2008).
ЗАО «Завод Минплита» успешно прошел сертификационный аудит интегрированной системы менеджмента (ИСМ), соответствующий требованиям международных стандартов:
- ISO 45001:2018 – система менеджмента охраны труда и промышленной безопасности,
- ISO 9001:2015 – система менеджмента качества,
- ISO 14001:2015 – система экологического менеджмента.
Историческая справка:
25 лет назад в России появились утеплители ISOVER и зарекомендовали себя как надежные, эффективные и качественные материалы. С ними в доме, на даче и в квартире тепло и тихо.
15 лет назад в России (г. Егорьевск) построен первый завод по производству минеральной ваты ISOVER.
7 лет назад приобретен завод «Минплита» по производству минеральной ваты на основе базальта в г.Челябинск.
5 лет назад стартовало производство новой широкой продуктовой линейки ISOVER на основе базальта.
Уже год базальтовую вату ISOVER успешно выпускает завод в г. Тамбов.
Продукция ISOVER обеспечивает эффективную защиту от холода и шума, повышает комфорт и энергоэффективность дома, сокращает затраты на его эксплуатацию. Большинство частных домов в России относятся к классу энергоэффективности D, на отопление которых затрачивается большое количество энергии. Материалы ISOVER позволяют улучшить теплозащиту дома в несколько раз и достичь уровня энергоэффективности от B до А+. Благодаря этому решается проблема промерзания стен и затраты на отопление сокращаются до 3х и более раз — применение утеплителя ISOVER на основе кварца позволяет экономить на отоплении дома до 67%.
ISOVER неоднократно отмечен премией Правительства г. Москвы «Берегите энергию!» в номинации «Технология года» и имеет самые высокие баллы за экологичность выпускаемой продукции, отмеченной двумя экомаркировками. В 2016 году ISOVER первым на рынке строительных материалов России верифицировал экологическую декларацию EPD (Environmental Product Declaration) на теплоизоляцию. Верификация экологической декларации означает подтверждение международной экспертной организацией, что все установленные требования были выполнены (ISO 9000:2005).
За 25 лет ISOVER стал ведущим игроком на российском рынке строительных материалов и заслужил доверие и уважение миллионов людей.
секрет производства позаимствовали у блондинок
На одном из омских предприятий наладили выпуск необычной продукции – льняной ваты. По стоимости она не дороже обычного аналога из хлопка, но более качественна и обладает несравненными антисептическими свойствами. Отбеливать вату из льна будут не вредным хлором, а обычной перекисью водорода.
Партиями по четыреста килограммов в ёмкости загружают льняное волокно. Через 10 часов – после варки, отбеливания и сушки – будет готова инновационная льняная вата.
Она только внешне почти не отличается от своего собрата. Но по свойствам разница колоссальная. Эксперимент показал: переработанный лён тонет мгновенно. Насколько быстро такой материал впитывает влагу, для медиков – один из главных показателей качества.
«И антисептические свойства, и кровоостанавливающие свойства, что очень важно в работе медперсонала», – говорит Наталья Фомина, старшая медсестра Омского Областного клинического медико-хирургического центра.
Как сохранить все эти характеристики во время переработки, было главной проблемой для технологов ватного завода. Например, хлор, который обычно используют для отбеливания, полезные свойства льна убивает. Идею невредного для ваты обесцвечивания заимствовали у блондинок. Вместо хлора используют перекись водорода.
«Появляются новые нюансы, с которыми нам приходится сталкиваться, чтобы в результате сохранялись положительные свойства льна», – говорит технолог Алексей Хорошилов.
Отработанную на вате технологию уже планируют применить в производстве других материалов. Из льняного сырья начнут выпускать бинты – это следующий этап производства.
«Будет делаться целый ряд новых инновационных продуктов. Это и перевязочные материалы медицинского назначения, и целлюлоза для волохов и много-много чего еще можно делать», – рассказывает Геннадий Смыслов, президент льноперерабатывающего холдинга «Леном».
Сейчас на ватном заводе разрабатывают бактерицидное покрытие – им будут пропитывать материалы для перевязки. Производство льняной ваты уже налажено. И хотя ничего нанотехнологичного в ней нет, новинку будут продавать именно с приставкой нано-. Если не особые свойства, то эти четыре буквы точно помогут ей оказаться на прилавках.
Сферы применения медицинской ваты | Статья от специалистов компании «Фарм-Глобал»
03.09.2014Вата медицинская представляет собой пушистую хлопковую массу, имеющую слабопереплетенную волокнистую структуру. Применяется в клинических и домашних условиях при выполнении различных лечебных и косметических процедур, в том числе перевязок, компрессов, инъекций. Благодаря сочетанию хорошей впитывающей способности и гигиеничности этот материал стал незаменимым в работе перевязочных, процедурных, хирургических отделений, а также стоматологических, физиотерапевтических и офтальмологических кабинетов.
Вата медицинская бывает следующих видов:
- Гигроскопическая. Используется при перевязках ран.
- Компрессная. Предназначена для согревающих компрессов.
- Глазная. Обладает наивысшей капиллярностью и поглотительной способностью.
- Хирургическая. Предназначена для перевязок ран.
- Гигиеническая. Используется для ежедневного гигиенического ухода и различных медицинских манипуляций.
Вату выпускают как стерильной, так и нестерильной. Срок годности первой составляет не менее 5 лет.
К вате предъявляют определенные требования:
- Она должна иметь слоистую структуру и обладать высокой степенью сорбции для аккуратного и эффективного впитывания жидких выделений при обработке и перевязке ран (вата накладывается поверх слоев марли или перевязочных бинтов).
- Стерильность, необходимая для обеспечения возможности работать с поврежденной поверхностью кожи или открытой раной.
- Однородность материала.
- Отсутствие посторонних добавок и примесей. Это обеспечит безопасную обработку раневой поверхности без риска возникновения вторичных инфекций и раздражения.
- Высокая степень белизны и капиллярности.
- Гипоаллергенность.
Производство ваты осуществляется из сырья, получаемого после переработки плода хлопчатника мохнатой. Внутри коробочки этого растения, которая раскрывается после созревания плода, находится мягкое волокно белого цвета вместе с семенами. Это волокно собирается на специальных пунктах, упаковывается и далее отправляется на хлопкоочистительный завод, где происходит отделение волокон от семян и разделение их по длине. При этом длинные волокна (2 – 2,5 см) идут на изготовление тканей, короткие же, называемые линт, — на производство ваты. Далее происходит расщепление, разрыхление и очищение от примесей волокон, и полученная в результате масса с помощью разрыхлительно-трепального агрегата формируется в так называемые холсты. Холсты отправляются на чесальные машины, с помощью которых превращаются в съем ваты – это сырье подвергается щелочной варке под давлением и обработке гипосульфитом натрия. В результате волокно приобретает характерные ему свойства (быстрого смачивания и поглощения жидкостей), белизну и эстетический вид.
В настоящее время используются новейшие методы производства, позволяющие при отбелке не использовать хлорсодержащие химические реагенты. Благодаря экологичным бесхлорным технологиям исключается возможность появления аллергии у пациентов, снижается загрязнение окружающей среды.
Произведенная вата пакуется в кипы по 20, 30, 40 и 50 кг. Вата фасуется в индивидуальную упаковку по 25, 50, 100, 200 и 250 грамм.
Медицинская гигроскопическая вата должна быть изготовлена в соответствии со стандартами ГОСТ 5556-81 1.3. Согласно этому ГОСТу, медицинская гигроскопическая глазная вата должна быть выработана только из 100% хлопкового волокна, хирургическая – из хлопкового волокна или смеси хлопкового волокна с вискозным штапельным волокном. Вата должна быть хорошо прочесанной, легко расслаиваемой на слои произвольной толщины и при этом сохраняющей связь между волокнами.
В последнее десятилетие российское ватное производство, да и в целом текстильная промышленность, испытывает трудности в поставках сырья для производства ваты. Значительная часть ваты в нашу страну импортируется из Китая, Индии, США, Пакистана, Бразилии, Узбекистана. Возникший дефицит сырья компенсируется использованием отечественного лубяного волокна низкого сорта, а также его отходов и целлюлозных химических волокон (в частности вискозного волокна).
Вата на основе целлюлозного волокна, для производства которой используется льняное волокно, по некоторым показателям имеет низкие эксплуатационные свойства. Гигроскопическая вата, состоящая из волокнистой смеси на основе хлопкового и вискозного волокон, имеет на ощупь неприятный скрип. Именно поэтому находящиеся в поисках альтернативных материалов производители все чаще склоны отдавать предпочтение льну, выращиваемому во многих регионах России. Лен характеризуется большей гигроскопичностью и стоит дешевле. Единственная сложность при работе с ним возникает на этапе производства: лен имеет грязноватый оттенок и требует отбеливания, а хлор как наиболее известный промышленный отбеливатель нивелирует природные дезинфицирующие свойства льна, за которые и ценится.
В настоящее время появилось много косметической продукции, в состав которой входит медицинская вата. Это ватные диски, шарики, валики, палочки и тампоны. Также в продаже имеется вата «Зиг-Заг», поставляемая в удобном виде фасовки, позволяющем отрывать нужное количество от ватной ленты, не затрагивая находящийся в пакете остаток.
Вата медицинская — виды и производство
Вата — самое известное перевязочное средство, выпускаемое медицинской промышленностью. Применять вату в медицине начали на рубеже XIX и XX веков, используя её высокую гигроскопичность. Первые ватные хлопковые повязки для лечения кровоточащих ран успешно применялись в военной хирургии. Вата зарекомендовала себя качественным абсорбентом отделяемого при лечении ранений различной этиологии.
Виды ваты медицинской
Вату получают как натуральным, так и искусственным путём. Медицинскую вату производят из растительных волокон хлопчатника. Медицинская вата бывает гигроскопической и компрессной. В зависимости от качества волокна и наличия примесей гигроскопическая вата выпускается в нескольких вариантах:
- Глазная — из первосортного хлопка;
- Хирургическая — из третьесортного хлопка с возможными добавками (не более трети объёма) первосортной вискозы;
- Гигиеническая — из низкосортного хлопка с незначительными примесями линта (остаточного волокна).
Гигроскопическая вата также бывает стерильной и нестерильной. При производстве её отбеливают. Волокно легко разделяется на части и обладает высокой впитываемостью. Цвет компрессной ваты — серовато-бежевый. Материал предназначен для изготовления многослойных повязок и компрессных аппликаций. Также используется в качестве мягкой основы, амортизирующей гипсовые шины.
Производство ваты
Основа производства ваты — хлопковое волокно, которое собирают из коробочек хлопчатника. Волокнистое сырьё доставляется в производственные цеха, где расщепляется, прочёсывается и очищается от различных включений. Из хлопковой массы формируют холсты фиксированной толщины, после чего они сматываются в рулоны. При получении ваты медицинской обработанную хлопковую массу отбеливают и разрыхляют под действием щелочных растворов и тиосульфата натрия.
Чтобы добиться стерильности, сырьё просушивают в жарочных шкафах. Стерильную вату используют в операционной хирургии, лечении заболеваний глаз и наложении на открытые раны. При упаковке холсты разрезают на ленты определённой ширины и сматывают в стандартные рулоны массой от 25 до 250 грамм. Нестерильные холсты отправляют в упаковочные цеха сразу после первичной обработки. Чаще всего из них производят перевязочную продукцию для косметологических и гигиенических целей — ватные шарики, диски, спонжи, тампоны для ухода за кожей.
USDA ERS — хлопок и шерсть
На этой странице представлена информация о:
Хлопок является одним из самых важных текстильных волокон в мире, в среднем на его долю приходится около 25 процентов от общего мирового потребления волокна. Соединенные Штаты являются третьим по величине производителем хлопка в мире и ведущим экспортером хлопка, на долю которых приходится треть мировой торговли хлопком-сырцом. Хлопковая промышленность США ежегодно производит товары и услуги на сумму более 21 миллиарда долларов, создавая более 125 000 рабочих мест в различных отраслях промышленности, от фермы до текстильной фабрики.
ERS предоставляет ряд отчетов и данных о рынках хлопка, включая внутреннее и международное предложение, спрос, торговлю и цены.
Периодические запланированные выходы
- Обзор хлопка и шерсти A отчет , опубликованный за 9 месяцев года, в котором представлены прогнозы предложения и использования для рынков хлопка США и мира на основе самых последних мировых оценок спроса и предложения в сельском хозяйстве.
- Краткий обзор WASDE Ежемесячная интерактивная визуализация, в которой представлены ключевые данные и основные моменты из оценок мирового спроса и предложения сельского хозяйства Министерства сельского хозяйства США по полевым культурам, а также животноводству и молочным продуктам.
- Таблицы Ежегодника хлопка и шерсти Ежегодный продукт данных, содержащий статистику производства, поставок, использования, торговли и цен на хлопок и шерсть в США. Таблицы также включают ряды и индексы внутренних и мировых цен; Государственные данные о посевных площадях, урожайности и производстве хлопка; и преобразование импорта и экспорта текстиля США.
- Данные о торговле текстильными изделиями в эквивалентах необработанных волокон в США Годовой продукт данных, который обеспечивает объем эквивалентов необработанных волокон в торговле текстилем в США.Эти данные используются для отслеживания и оценки потребительского спроса в США на текстиль, отслеживания тенденций доли волокна и получения информации об уровне использования хлопка мировыми фабриками.
Этот набор данных содержит исторические годовые данные, а ежемесячные данные публикуются в «Хлопок и шерсть» Outlook .
- Товарные затраты и возврат s Продукт данных, предоставляющий годовые оценки производственных затрат и доходов от основных полевых культур, включая хлопок.
- Сельскохозяйственный базовый прогноз Министерства сельского хозяйства США Годовой отчет, опубликованный в феврале, который предлагает 10-летние прогнозы для сельскохозяйственного сектора на основе ежегодного долгосрочного анализа Министерства сельского хозяйства США.Соответствующая базовая база данных охватывает прогнозы по четырем основным фуражным зернам (кукуруза, сорго, ячмень и овес) в дополнение к другим основным кормовым культурам и животноводству.
Другие публикации ERS, относящиеся к хлопку и шерсти
В дополнение к периодическим отчетам Outlook и информационным продуктам ERS публикует отчеты, охватывающие вопросы, важные для рынка хлопка в Соединенных Штатах и во всем мире. Недавние отчеты ERS, касающиеся хлопка, включают:
Производство хлопчатобумажной пряжи
Хлопок составляет почти 50% мирового потребления текстильного волокна.Китай, Соединенные Штаты, Российская Федерация, Индия и Япония являются основными странами-потребителями хлопка. Потребление измеряется количеством сырого хлопкового волокна, закупаемого и используемого для производства текстильных материалов. Мировое производство хлопка ежегодно составляет от 80 до 90 миллионов тюков (от 17,4 до 19,6 миллиардов кг). Китай, США, Индия, Пакистан и Узбекистан являются основными странами-производителями хлопка, на долю которых приходится более 70% мирового производства хлопка. Остальное производится примерно в 75 других странах.Хлопок-сырец экспортируется примерно из 57 стран, а хлопчатобумажные ткани — примерно из 65 стран. Многие страны делают акцент на внутреннем производстве, чтобы уменьшить свою зависимость от импорта.
Производство пряжи — это последовательность процессов, в ходе которых волокна хлопка-сырца превращаются в пряжу, пригодную для использования в различных конечных продуктах. Для получения чистой, прочной и однородной пряжи, необходимой на современном рынке текстиля, требуется ряд процессов. Начиная с плотной упаковки спутанных волокон (кипы хлопка), содержащей различное количество неворсистых материалов и непригодных волокон (посторонние вещества, растительный мусор, пылинки и т. д.), непрерывные операции вскрытия, смешивания, смешивания, очистки, прочесывания, вытягивания , ровница и прядение выполняются для преобразования хлопковых волокон в пряжу.
Несмотря на то, что нынешние производственные процессы высокоразвиты, конкурентное давление продолжает побуждать отраслевые группы и отдельных лиц к поиску новых, более эффективных методов и машин для обработки хлопка, которые однажды могут вытеснить сегодняшние системы. Однако в обозримом будущем по-прежнему будут использоваться существующие традиционные системы смешивания, чесания, вытягивания, ровницы и прядения. Только процесс сбора хлопка явно обречен на ликвидацию в ближайшем будущем.
Производство пряжи производит пряжу для различных тканых или трикотажных конечных продуктов (например, одежды или технических тканей), а также для швейных ниток и канатов. Пряжа выпускается разного диаметра и разного веса на единицу длины. В то время как основной процесс производства пряжи оставался неизменным в течение ряда лет, скорость обработки, технология контроля и размеры упаковки увеличились. Свойства пряжи и эффективность обработки связаны со свойствами перерабатываемых хлопковых волокон.Свойства конечного использования пряжи также зависят от условий обработки.
Процессы производства пряжи
Вскрытие, смешивание, смешивание и очистка
Как правило, фабрики выбирают смеси для кип со свойствами, необходимыми для производства пряжи для конкретного конечного использования. Количество тюков, используемых разными заводами в каждой смеси, колеблется от 6 или 12 до более чем 50. Обработка начинается, когда тюки, которые нужно смешать, доставляются в помещение для вскрытия, где удаляются мешки и обвязки.Слои хлопка снимаются с тюков вручную и укладываются в питатели, оборудованные конвейерами с шипами, или целые тюки укладываются на платформы, которые перемещают их вперед и назад под или над ощипывающим механизмом. Цель состоит в том, чтобы начать последовательный производственный процесс путем преобразования уплотненных слоев тюкового хлопка в маленькие, легкие, пушистые пучки, которые облегчат удаление посторонних частиц. Этот начальный процесс называется «открытием». Поскольку тюки поступают на завод с разной степенью плотности, обвязки тюков обычно обрезают примерно за 24 часа до обработки тюков, чтобы они «распустились».Это увеличивает раскрытие и помогает регулировать скорость кормления. Очистительные машины на мельницах выполняют функции вскрышной и первой ступени очистки.
Кардочесание и чесание
Кардочесальная машина является наиболее важной машиной в процессе производства пряжи. Он выполняет функции очистки второго и последнего уровня на подавляющем большинстве хлопчатобумажных текстильных фабрик. Кардочесальная машина состоит из системы из трех покрытых проволокой цилиндров и ряда плоских покрытых проволокой стержней, которые последовательно обрабатывают небольшие комки и пучки волокон до высокой степени разделения или открытости, удаляя очень высокий процент мусора и других веществ. инородных тел, соберите волокна в жгутообразную форму, называемую «лентой», и доставьте эту ленту в контейнер для использования в последующем процессе (см. рис. 1).
Рисунок 1. Кардочесание
Wilawan Juengprasert, Министерство здравоохранения, Таиланд
Исторически хлопок подавался на чесальную машину в виде «подборочного круга», который формируется на «подборщике», комбинации подающих валков и битеров с механизмом, состоящим из цилиндрических сит, на которых раскрываются пучки хлопка. собирают и скатывают в войлок (см. рис. 2). Войлок снимается с экранов ровным плоским листом, а затем сворачивается внахлест.Однако потребность в рабочей силе и доступность автоматизированных систем обработки с потенциалом повышения качества способствуют устареванию комплектовщика.
Рисунок 2. Современный сборщик
Wilawan Juengprasert, Министерство здравоохранения, Таиланд
Устранение процесса комплектования стало возможным благодаря установке на карты более эффективного оборудования для вскрытия и очистки, а также систем желобной подачи. Последние распределяют открытые и очищенные пучки волокон на карды пневматическим способом по воздуховодам.Это действие способствует согласованности обработки и повышению качества, а также сокращает количество необходимых рабочих.
Небольшое количество фабрик производит гребенную пряжу, самую чистую и однородную хлопчатобумажную пряжу. Прочесывание обеспечивает более обширную очистку, чем кард. Целью расчесывания является удаление коротких волокон, узелков и мусора, чтобы полученная щепка была очень чистой и блестящей. Гребнечесальная машина представляет собой сложную машину, состоящую из подающих валиков с канавками и цилиндра, частично покрытого иглами для вычесывания коротких волокон (см. рис. 3).
Рисунок 3. Расчесывание
Wilawan Juengprasert, Министерство здравоохранения, Таиланд
Волочение и ровница
Волочение — это первый процесс в производстве пряжи, в котором используется вытягивание валиком. На чертеже практически вся тяга возникает от действия роликов. Контейнеры с чесальной лентой закрепляются в шпулярнике ленточной рамы. Вытягивание происходит при подаче ленты в систему парных валков, движущихся с разной скоростью.Вытяжка выпрямляет волокна в ленте путем вытягивания, чтобы сделать больше волокон параллельными оси ленты. Распараллеливание необходимо для получения желаемых свойств, когда волокна впоследствии скручиваются в пряжу. Волочение также дает ленту, которая более однородна по весу на единицу длины и помогает достичь лучших возможностей смешивания. Волокна, полученные в процессе окончательной вытяжки, называемой финишной вытяжкой, почти прямые и параллельны оси ленты.Вес на единицу длины ленты финишной вытяжки слишком велик, чтобы ее можно было вытягивать в пряжу на обычных системах кольцевого прядения.
Процесс ровницы уменьшает вес ленты до подходящего размера для прядения в пряжу и вставки крутки, что сохраняет целостность тяговых прядей. Банки с лентами после финишной вытяжки или гребнечесания помещаются в шпулярник, а отдельные ленты подаются через два комплекта валков, второй из которых вращается быстрее, уменьшая таким образом размер ленты примерно с 2. 5 см в диаметре до диаметра стандартного карандаша. Волокнам придают крутку путем пропускания пучка волокон через ровничную «рогульку». Продукт теперь называется «ровинг», который упакован в бобины длиной около 37,5 см и диаметром около 14 см.
Прядение
Прядение — самый дорогостоящий этап преобразования хлопкового волокна в пряжу. В настоящее время более 85% пряжи в мире производится на кольцепрядильных машинах, которые предназначены для вытягивания ровницы до нужного размера пряжи и придания ей желаемой степени крутки.Величина крутки пропорциональна прочности пряжи. Отношение длины к подаваемой длине может варьироваться в пределах от 10 до 50. Бобины ровницы размещаются на держателях, позволяющих свободно подавать ровницу в тянущий валик кольцепрядильной машины. После зоны вытягивания пряжа проходит через «путешественник» на прядильную катушку. Веретено, удерживающее эту катушку, вращается с высокой скоростью, в результате чего пряжа вздувается при скручивании. Пряжа на бобинах слишком короткая для использования в последующих процессах, и ее сбрасывают в «прядильные коробки» и отправляют на следующий процесс, которым может быть намотка или намотка.
В современном производстве более тяжелой или грубой пряжи кольцепрядильное прядение заменяется прядильной нитью. Лента волокон подается в высокоскоростной ротор. Здесь центробежная сила превращает волокна в нити. Шпулька не нужна, и пряжа наматывается на упаковку, необходимую на следующем этапе процесса.
Значительные усилия в области исследований и разработок направлены на радикально новые методы производства пряжи. Ряд новых систем прядения, разрабатываемых в настоящее время, могут произвести революцию в производстве пряжи и вызвать изменения в относительной важности свойств волокна, как они теперь воспринимаются.В целом четыре из различных подходов, используемых в новых системах, кажутся практичными для использования на хлопке. Системы сердечникового прядения в настоящее время используются для производства различных видов специальной пряжи и швейных ниток. Бескруточная пряжа производится в ограниченном количестве в промышленных масштабах с помощью системы, которая связывает волокна вместе с поливиниловым спиртом или каким-либо другим связующим веществом. Система бескруточной пряжи предлагает потенциально высокую производительность и очень однородную пряжу. Трикотаж и другие одежные ткани из безкруточной пряжи имеют превосходный внешний вид.В воздушно-вихревом прядении, которое в настоящее время изучается несколькими производителями машин, волочильная лента подается на открывающий валик, аналогично роторному прядению. Воздушно-вихревое прядение обеспечивает очень высокие производственные скорости, но прототипы моделей особенно чувствительны к изменениям длины волокна и содержанию посторонних веществ, таких как частицы мусора.
Намотка и намотка
После того, как пряжа спрядена, производители должны подготовить правильную упаковку. Тип упаковки зависит от того, будет ли пряжа использоваться для ткачества или вязания. Намотка, наматывание, скручивание и квиллинг считаются подготовительными этапами плетения и вязания пряжи. Как правило, продукт намотки будет использоваться как основные нити (пряжи, которые идут вдоль ткани), а продукт намотки будет использоваться как уточные нити или уточные нити (нити, которые проходят поперек ткани). фабрика). Изделия из открытого прядения обходят эти этапы и упаковываются либо для наполнения, либо для основы. Кручение производит многослойную пряжу, где две или более пряжи скручиваются вместе перед дальнейшей обработкой.В процессе квиллинга пряжа наматывается на маленькие бобины, достаточно маленькие, чтобы поместиться внутри челнока ткацкого станка. Иногда процесс квиллинга происходит на ткацком станке. (См. также статью «Плетение и вязание» в этой главе.)
Обращение с отходами
На современных текстильных фабриках, где важна борьба с пылью, больше внимания уделяется обращению с отходами. В классических текстильных операциях отходы собирались вручную и доставлялись в «свалку», если они не могли быть переработаны в систему.Здесь он накапливался до тех пор, пока одного вида не становилось достаточно, чтобы сделать тюк. В настоящее время центральные вакуумные системы автоматически возвращают отходы от вскрытия, подбора, чесания, вытягивания и ровницы. Центральная вакуумная система используется для очистки машин, автоматического сбора отходов из-под машин, таких как мухи и пылинки от чесания, а также для возврата непригодных подметальных машин и отходов из конденсаторов фильтров. Классический пресс-подборщик представляет собой пресс с вертикальным ходом вверх, который по-прежнему формирует типичный тюк весом 227 кг.В современной технологии удаления отходов отходы накапливаются из центральной вакуумной системы в приемном резервуаре, который питает горизонтальный пресс для тюков. Различные отходы производства пряжи могут быть переработаны или повторно использованы в других отраслях.
Например, прядение можно использовать в прядильном производстве отходов для изготовления пряжи для швабры, расчесывание можно использовать в производстве хлопкового ватина для изготовления ватина для матрасов или мягкой мебели.
Вопросы безопасности и охраны здоровья
Машины
Несчастные случаи могут происходить на всех типах машин для производства хлопчатобумажной ткани, хотя их частота невелика.Эффективная защита множества движущихся частей сопряжена со многими проблемами и требует постоянного внимания. Обучение операторов безопасным методам также имеет важное значение, в частности, чтобы избежать попыток ремонта во время движения оборудования, что является причиной многих несчастных случаев.
Каждая часть оборудования может иметь источники энергии (электрические, механические, пневматические, гидравлические, инерционные и т. д.), которые необходимо контролировать перед выполнением любых ремонтных работ или работ по техническому обслуживанию. На объекте следует определить источники энергии, предоставить необходимое оборудование и обучить персонал отключению всех опасных источников энергии во время работы с оборудованием.Следует регулярно проводить проверки, чтобы убедиться, что все процедуры блокировки/маркировки соблюдены и правильно применяются.
Вдыхание хлопковой пыли (биссиноз)
Было показано, что вдыхание пыли, образующейся при переработке хлопкового волокна в пряжу и ткань, вызывает профессиональное заболевание легких, биссиноз, у небольшого числа текстильщиков. Обычно требуется от 15 до 20 лет воздействия более высоких уровней пыли (выше 0.от 5 до 1,0 мг/м 3 ) для рабочих, которые станут реакторами. Стандарты OSHA и Американской конференции государственных специалистов по промышленной гигиене (ACGIH) устанавливают 0,2 мг/м 3 вдыхаемой хлопковой пыли, измеренной с помощью вертикального отстойника, в качестве предела профессионального воздействия хлопковой пыли при производстве текстильной пряжи. Пыль, переносимая по воздуху частица, выбрасываемая в атмосферу при обработке или переработке хлопка, представляет собой гетерогенную сложную смесь ботанического мусора, почвы и микробиологического материала (т.э., бактерии и грибы), которые различаются по составу и биологической активности. Этиологический агент и патогенез биссиноза неизвестны. Отходы хлопковых растений, связанные с волокном и эндотоксином грамотрицательных бактерий на волокне и растительных остатках, считаются причиной или содержат возбудитель. Само хлопковое волокно, состоящее в основном из целлюлозы, не является причиной, поскольку целлюлоза представляет собой инертную пыль, не вызывающую респираторных заболеваний. Надлежащий технический контроль на участках обработки хлопкового текстиля (см. рис. 4) наряду с методами работы, медицинским наблюдением и средствами индивидуальной защиты может по большей части устранить биссиноз.Мягкая промывка хлопка водой с помощью систем периодической мойки и систем непрерывного действия снижает остаточный уровень эндотоксина как в ворсе, так и в пыли, переносимой по воздуху, до уровней ниже тех, которые связаны с острым снижением функции легких, измеряемым объемом форсированного выдоха за 1 секунду.
Рисунок 4. Система пылеудаления для кардочесальной машины
Шум
Шум может быть проблемой в некоторых процессах производства пряжи, но на нескольких современных текстильных фабриках уровень шума ниже 90 дБА, что является стандартом США, но превышает стандарты шумового воздействия во многих странах.Благодаря усилиям производителей машин и инженеров по снижению промышленного шума уровень шума продолжает снижаться по мере увеличения скорости машин. Решением проблемы высокого уровня шума является внедрение более современного и более тихого оборудования. В Соединенных Штатах требуется программа сохранения слуха, когда уровень шума превышает 85 дБА; это будет включать мониторинг уровня шума, аудиометрическое тестирование и предоставление средств защиты органов слуха всем сотрудникам, когда уровень шума не может быть ниже 90 дБА.
Тепловой стресс
Поскольку для отжима иногда требуются высокие температуры и искусственное увлажнение воздуха, всегда необходим тщательный контроль, чтобы не допустить превышения допустимых пределов. Хорошо спроектированные и обслуживаемые установки кондиционирования воздуха все чаще используются вместо более примитивных методов регулирования температуры и влажности.
Системы менеджмента безопасности и гигиены труда
Многие из более современных фабрик по производству текстильной пряжи считают полезным иметь какую-либо систему управления безопасностью и гигиеной труда для контроля опасностей на рабочем месте, с которыми могут столкнуться работники.Это может быть добровольная программа, такая как «В поисках лучшего в области здравоохранения и безопасности», разработанная Американским институтом производителей текстиля, или программа, предусмотренная нормативными актами, такими как Программа штата Калифорния по предотвращению производственного травматизма и заболеваний (Раздел 8, Свод правил Калифорнии, раздел 3203). Когда используется система управления безопасностью и здоровьем, она должна быть достаточно гибкой и адаптируемой, чтобы завод мог адаптировать ее к своим потребностям.
Спинка
Хлопчатобумажная пряжа – обзор
12.2.12 Трение
Трение хлопчатобумажной пряжи особенно важно при машинном вязании, особенно при вязании относительно тонкой пряжи на высокоскоростных вязальных машинах. В целом измеряются два типа трения пряжи или их комбинация, а именно трение пряжи о металл (или иногда трение пряжи о керамику) и трение пряжи о нить (ASTM D3412), поскольку они представляют собой типы трения, чаще всего встречающиеся на практике. Трение пряжи определяет силы трения и натяжения, развиваемые пряжей, например, когда она скользит по нитеводителям, натяжным устройствам, вязальным спицам и грузилам, самой пряже или другим нитям.Если трение пряжи чрезмерное, натяжение пряжи может превысить ее прочность на разрыв, что приведет к обрыву пряжи, например, во время намотки или вязания. Наиболее эффективным и широко используемым средством уменьшения трения является нанесение смазки, например, с помощью диска из твердого парафина, на пряжу, когда она наматывается на паковку, во время намотки или во время роторного прядения. Иногда смазку (или пластификатор) наносят на красильную ванну после окрашивания паковки, а в некоторых случаях эмульсионную смазку наносят во время намотки, например, с помощью лизирующего валика.
Доступны различные коммерческие тестеры трения и методы испытаний (например, ASTM D3108), большинство из которых измеряют натяжение, возникающее в пряже, когда она проходит по цилиндрической или плоской металлической поверхности, или сам коэффициент трения пряжи по металлу (μ) можно оценить, измерив натяжение нити (T 1 ) до поверхности и натяжение (T 2 ) после поверхности (рис. 12.6), используя следующее классическое уравнение шпиля:
12,6. Схемы, показывающие способы натяжения нитей: (а) плоская пластина; (б) кабестан; (c) и (d) система с двумя плоскими пластинами.
(источник: PJ Kruger, Text . Месяц , февраль 1970 г.)12,8T2/T1=eμΘandT2=T1eμΘ
, где Θ = общий угол контакта (в радианах) между нитью и цилиндром и e = основание (2. 718) натуральных (напьеровых) логарифмов. Для фрикционной поверхности литникового (плоского) типа соответствующее уравнение:
12,9T2=T1+2µN
где N — нормальная сила (давление), приложенная к пряже.
В идеале коэффициент трения хлопчатобумажной пряжи, предназначенной для вязания, должен быть равен 0.15 (или ниже), хотя фактическое значение в некоторой степени зависит от условий, в которых оно измеряется. Примеры коммерческих измерителей трения включают Lawson-Hemphill (ручной, со статистикой), Schlafhorst Friction Tester Textechno H. Stein, Zweigle µ-Meter G 532 I, Rothschild F-Meter R-2088 и SAWTRI Yarn Friction Meter (WIRA). .
Технологическая схема производства хлопчатобумажной пряжи
Пряжа представляет собой непрерывную и однородную массу волокон, связанных вместе путем вставки поворота.Пряжа является сырьем для ткани. То толщина пряжи варьируется в широких пределах. Обычно толщина пряжи выражается в количестве. Количество может быть определено как число, которое выражает тонкость или грубость пряжи.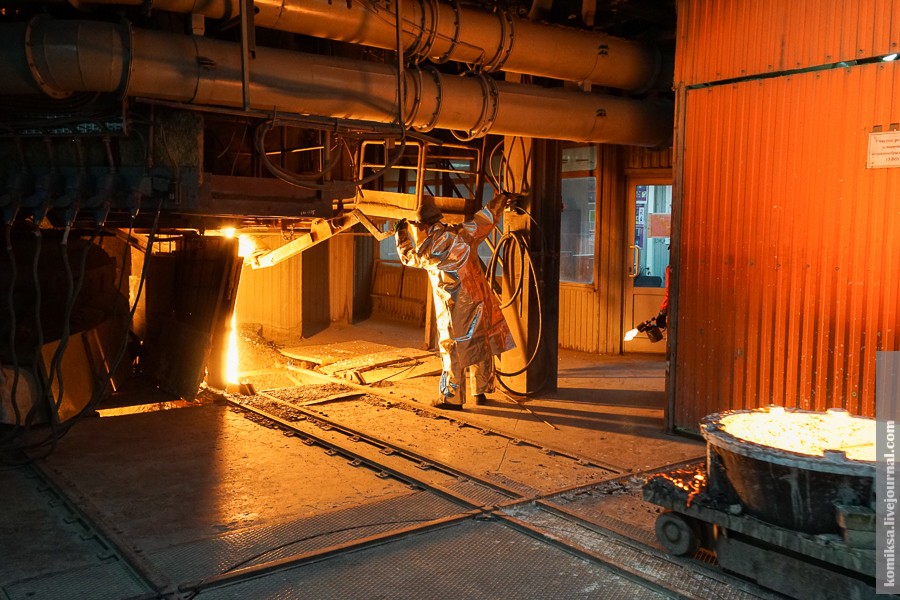
Технологическая схема прядильных машин и пошаговая последовательность производства хлопчатобумажной штапельной пряжи показана ниже:
Хлопок в тюках
↓
Выдувная машина
↓
Кардочесальная машина
↓
Чертежная машина
↓
Ровничная машина
↓
Прядильная машина
↓
Пряжа х/б
Теперь кратко опишу этапы так —
Хлопок в форме тюка | Тюки хлопка-сырца всегда содержат определенное количество примесей, называемых «мусором».Мусорные материалы — сломанные семена, шелуха,
сломанные листья, грязь, короткие волокна и т. |
минет номер | Продувочная – это начальная часть прядильной фабрики по производству хлопчатобумажной пряжи. А используется ряд различных типов машин для открывания, очистки и смешивания согласно последовательности в этом разделе. |
Чесание | Кардочесание можно определить как преобразование перепутанной или спутанной массы волокон в пленчатое полотно путем их обработки между двумя близко расположенными,
относительно подвижные поверхности, покрытые острыми наконечниками. Кардочесальное действие достигается, когда зубья на двух поверхностях заставляют работать от точки к точке. Когда их заставляют работать острием к спине, это действие называется зачисткой.![]() |
Чертежная рамка | Лента, доставленная из кардочесальной машины в виде рулона в лотке для ленты, подается в волочильный станок.Рамка для рисования может быть 1, 2, 3, 4, или 5-ти головные машины. Двухголовочная машина означает, что на этой машине будут доставлены две ленты. |
Скоростная/передвижная рама | Лента, доставленная из ленточной машины в ленточный бак, подается в скоростную раму. Скоростная рама также называется подвижной рамой. |
Кольцо спиннинг | Кольцевое вращение – это универсальная система спиннинга. Процесс, связанный с кольцевым прядением, включает в себя наматывание, вытягивание, скручивание, намотку, наращивание и снятие.В обычных кольцевых рамах количество шпинделей 400-500, но 1000
поставка, т. е. шпиндель на кольцевую раму, также доступна. Поставляемые ровницы в бобинах подаются в шпулярники кольцевой рамы.![]() |
Пряжа | Комплект поставки, представляющий собой бобин с пряжей, находится на шпинделе.То доставленная пряжа наматывается на бобину пряжи. |
• Мировое производство хлопка по странам 2019
• Мировое производство хлопка по странам 2019 | StatistaДругая статистика по теме
ХлопокПожалуйста, создайте учетную запись сотрудника, чтобы иметь возможность отмечать статистику как избранную. Затем вы можете получить доступ к своей любимой статистике через звездочку в шапке.
Зарегистрироваться Пожалуйста, авторизируйтесь, перейдя в «Мой аккаунт» → «Администрирование». Затем вы сможете пометить статистику как избранную и использовать оповещения о личной статистике.
Базовая учетная запись
Знакомство с платформой
У вас есть доступ только к базовой статистике.
Однозначный аккаунт
Идеальная учетная запись входа для отдельных пользователей
- мгновенный доступ до 1 м.
- Скачать
- Скачать в XLS, PDF и PNG Формат
- Подробный Ссылки
$ 59 $ 39 / месяц *
в первые 12 месяцев
Корпоративный счет
Полный доступ
Корпоративное решение со всеми функциями.
* Цены не включают налог с продаж.
Самая важная статистика
самая важная статистика
самая важная статистика
Самая важная статистика
Самая важная статистика
Дальнейшая дополнительная статистика Узнать больше о как Statista может поддержать ваш бизнес.
Министерство сельского хозяйства США. (12 августа 2021 г.). Ведущие страны-производители хлопка в мире в 2020/2021 гг. (в 1000 метрических тонн) [График]. В Статистике. Получено 11 января 2022 г. с https://www.statista.com/statistics/263055/cotton-production-worldwide-by-top-countries/
Министерства сельского хозяйства США. «Ведущие страны-производители хлопка в мире в 2020/2021 гг. (в 1000 метрических тонн)». Диаграмма. 12 августа 2021 г. Статистика. По состоянию на 11 января 2022 г. https://www.statista.com/statistics/263055/cotton-production-worldwide-by-top-countries/
Министерство сельского хозяйства США.(2021). Ведущие страны-производители хлопка в мире в 2020/2021 гг. (в 1000 метрических тонн). Статистика. Statista Inc.. Дата обращения: 11 января 2022 г. https://www.statista.com/statistics/263055/cotton-production-worldwide-by-top-countries/
Министерство сельского хозяйства США. «Ведущие страны-производители хлопка в мире в 2020/2021 гг. (в 1000 метрических тонн)». Statista, Statista Inc., 12 августа 2021 г., https://www.statista.com/statistics/263055/cotton-production-worldwide-by-top-countries/
Министерство сельского хозяйства США, Ведущие страны-производители хлопка в мире в 2020 г. /2021 (в 1000 метрических тоннах) Statista, https://www.statista.com/statistics/263055/cotton-production-worldwide-by-top-countries/ (последнее посещение 11 января 2022 г.)
Ведущие производители хлопчатобумажной пряжи в мире
Хлопковая текстильная промышленность довольно широко распространена в мире, и целых 90 стран производят хлопчатобумажную пряжу и/или ткани в различных количествах. Но основная концентрация текстильной промышленности ограничена несколькими странами.
Существует два вида производства, связанных с хлопковым текстилем: производство хлопчатобумажной пряжи и производство хлопчатобумажной ткани.Хотя многие страны производят и то, и другое.
В следующей таблице указаны основные производители хлопчатобумажной пряжи и их производство:
Таблица 10. 2 Ведущие производители хлопчатобумажной пряжи в мире:
Страны | Производство (в тысячах метрических тонн) | Процент мирового производства |
Китай | 284.0 | 26,4 |
Индия | 226,7 | 21,0 |
США | 158,8 | 14,7 |
Пакистан | 115,0 | 10,7 |
Индонезия | 75,4 | 7. |
Бразилия | 40,5 | 3,8 |
Турция | 40,0 | 3,7 |
Южная Корея | 23,7 | 1.2. |
Италия | 21,2 | 2,0 |
Египет | 16.4 | 1,5 |
Япония | 15,8 | 1,5 |
Помимо вышеперечисленных стран, Германия, Португалия, Греция, Узбекистан, Сирия, Франция, Бангладеш, Туркменистан и Иран также являются известными производителями хлопчатобумажной пряжи.
Ведущими производителями хлопчатобумажной ткани в мире являются Китай, Индия, Россия, США, Япония, Италия, Германия, Гонконг, Египет, Франция и Румыния.
Производство хлопчатобумажной ткани в этих странах следующее:
Таблица 10.3 Основные производители хлопчатобумажной ткани в мире:
Страны | Производство (в тысячах квадратных метров) | Процент мирового производства |
Китай | 2256 | 25.7 |
Индия | 1250 | 14,2 |
Россия | 865 | 9,8 |
США | 373 | 4,2 |
Япония | 177 | 2,0 |
Германия | 90 | 1. |
Гонконг | 82 | 0,9 |
Египет | 61 | 0,7 |
Франция | 81 | 0,9 |
Румыния | 54 | 0,6 |
Другими производителями хлопчатобумажной ткани в мире являются Бразилия, Испания, Пакистан, Турция, Узбекистан, Боливия, Вьетнам, Республика Корея, Чехия, Португалия, Бельгия, Польша, Южная Африка и Сирия.
Хлопковая текстильная промышленность довольно широко распространена в мире; однако есть области концентрации. Краткое описание важных областей хлопчатобумажной текстильной промышленности дается здесь, чтобы объяснить общую картину распределения.
Хлопчатобумажный текстиль – один из старейших видов промышленности Китая. С давних времен ткачество и прядение были обычным занятием деревенских ткачей, и большая часть продукции производилась хлопчатобумажной промышленностью.Несколько характеристик этой отрасли помогают объяснить такое географическое разнообразие и концентрацию.
Во-первых, есть готовый рынок для своего продукта. С его огромным населением Китай имеет обширный внутренний рынок для дешевых хлопчатобумажных изделий, а его низкая стоимость рабочей силы, основанная на большом количестве рабочей силы, позволяет продавать текстиль за границу.
Первой современной фабрикой была текстильная фабрика в Шанхае, построенная в 1888 году. Вскоре Шанхай стал крупным текстильным центром наряду с Южной Маньчжурией.
Помимо преимуществ местных поставок сырья, дешевой рабочей силы и региональных рынков сбыта, хлопководческие районы Маньчжурии имели дополнительное преимущество наличия замечательных угольных копей в пределах государства.
Первая материковая хлопчатобумажная фабрика была расположена за пределами прибрежного Китая – в хлопководческом районе Маньчжурии в Цинцзяне. Благодаря удачному географическому положению в долине реки Ляо выращивается большое количество хлопка.
Хлопчатобумажная промышленность сохраняет здесь свое первенство: в 1949 г. было 247 фабрик, а к 1957 г. было открыто еще около пятидесяти, занимавшихся прядением, ткачеством, крашением и ситцевой печатью. К 1965 г. количество веретен увеличилось вдвое.
Несколько центров текстильного производства также создаются на различных новых участках во внутренних районах Китайской Народной Республики.
Раньше текстильная промышленность была сосредоточена в Шанхае и Тяньцзине. Улучшилось производство, открылись новые центры в хлопкосеющем поясе в Хэнани, Хэбэе, Шанси и Шэньси, а также отдельные фабрики, обслуживающие местные нужды, в Лань Чоу, Урумчи, Кашгаре, Чэнду, Тайюане, Чэнчжоу, Хунчжоу, Нанкин, Кайтенг, Тяньцзинь и др. Ткань теперь производится в Тайюане, а ткацкие станки строятся в Чэнчжоу.
Теперь Китай стал крупнейшей страной-производителем хлопчатобумажной ткани в мире. Промышленный центр Пекин-Ханькоу, включающий такие центры, как Паотин, Сингтай и Чэнчжоу, превратился в ведущий текстильный центр. Конечно, среди всех центров текстильного производства Шанхай был самым важным. В какой-то момент в этом регионе производилось более 70% текстильной продукции Китая.
Появление различных текстильных центров снизило относительное значение Шанхая, но он по-прежнему сохраняет доминирующую роль в текстильной промышленности.Соседний район Ханькоу теперь производит огромное количество текстильной продукции.
Ушаньские интегрированные текстильные фабрики производят значительное количество хлопчатобумажной продукции. Совсем недавно были созданы текстильные подразделения Canton. Поскольку заводы современные, выпуск текстильных изделий на одного работника в этом регионе очень высок.
2.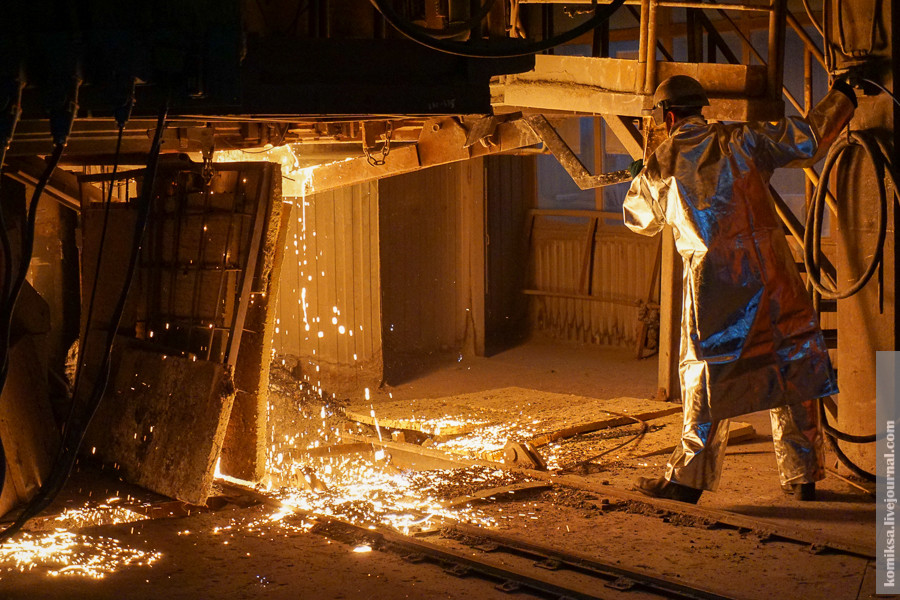
Индия является вторым по величине производителем хлопчатобумажной ткани в мире. Первая хлопчатобумажная фабрика в Индии была построена в Калькутте в 1818 году, а первая фабрика в Бомбее (ныне Мумбаи) была открыта в 1854 году, и ей суждено было стать домом для хлопчатобумажной промышленности.
Ранняя концентрация хлопчатобумажной текстильной промышленности в Мумбаи определялась не столько естественными и постоянными факторами, сколько другими преимуществами, такими как изобилие капитала и кредитных средств, наличие дешевых и быстрых транспортных средств и временный рост спрос на пряжу из Китая, который Мумбаи был в исключительно благоприятном положении для удовлетворения.
1877 год знаменует собой поворотный момент в развитии отрасли с точки зрения ее распространения.Это положило начало быстрому строительству фабрик в отдаленных центрах, таких как Нагпур, Ахмадабад, Шолапур, Колхапур и т. Д., Расположенных прямо в центре хлопководческих районов.
На это более позднее распространение в гораздо большей степени повлияли естественные факторы, такие как близость источников сырья, изобилие рабочей силы и крупных торговых центров, и оно стало возможным благодаря развитию железнодорожного сообщения.
Значительный стимул хлопчатобумажной промышленности получили условия, созданные войной.Большое покровительство, оказанное правительству фабрике в связи с их военными потребностями в хлопчатобумажных изделиях на восточных театрах военных действий, наряду с сокращением импорта Ланкашира в Индию из-за занятости фабрик Ланкашира военными работами и резкое повышение цен на импортное сукно из-за отсутствия судоходства привело к значительному увеличению внутреннего потребления, хотя трудности с ввозом машин помешали быстрому развитию, которое в противном случае имело бы место.Недавно там было
наблюдается тенденция индийских фабрик к увеличению производства более тонких изделий, и для этой цели из США и других стран ввозится определенное количество длинноволокнистого хлопка. Ситуации поможет улучшение качества отечественного хлопка.
Важно отметить, что даже в пределах этих конкретных областей или регионов промышленность преимущественно локализована в нескольких важных промышленных центрах, таких как Мумбаи, Ахмедабад, Шолапур, Вадодара, Пуна, Канпур, Дели, Индор, Гвалиор, Коимбатур, Калол, Бхагалпур. , Варангал, Калькутта, Ховра, Серампур, Коннагар, Содепур, Панихати и др.
В настоящее время в Индии насчитывается более 1220 хлопчатобумажных фабрик; из них 283 — это композитные фабрики, а остальные — прядильные фабрики. Что касается производства, Махараштра лидирует с 16,4% пряжи и 52,3% производства ткани в стране, за ней следуют штаты Тамил Наду (30,4% пряжи и 8,8% ткани), Гуджарат, Уттар-Прадеш, Мадхья-Прадеш, Западная Бенгалия, Раджастхан, Пенджаб. , Карнатака и др.
3. Россия : Россия занимает третье место в мире по производству хлопчатобумажных тканей и производит около десяти процентов всего хлопчатобумажного полотна в мире. Хотя в России текстильная промышленность не получила приоритета в планах развития.
До революции (1917 г.) хлопчатобумажная промышленность была локализована в Москве и Ивановской области, но в настоящее время она получила развитие и в других регионах.
Важные регионы:
(i) Московско-Ивановская область – старейший и важнейший текстильный регион. В Иваново находится большое количество хлопкопрядильных и ткацких центров, также известных как «Манчестер России».
Другие центры этого района — Йорослав, Костромов, Шуя, Ковров, Уро-Хаво-Зуево и др. Москва — еще один центр, вокруг которого развились Ногинск, Павловский, Егорьевск, Серпухов и др.
(ii) Ленинградская или Санкт-Петербургская область также известна хлопчатобумажной текстильной промышленностью. Санкт-Петербург, Нарва и Таллин являются важными центрами этого региона.
(iii) Калининская область простирается к западу от Москвы. Калинин, Вишние, Волочак — важные текстильные центры.
(iv) Сибирский регион развивался за счет наличия дешевой гидроэлектроэнергии, транспорта и рабочей силы. Ряд центров, таких как Омск, Новосибирск, Барнаул, Брянск, Камарово, Канск, Ленинск-Кузнецкий, Кустной, имеют хлопчатобумажную текстильную промышленность.
Поволжье и Уральский регион также имеют хлопчатобумажные текстильные производства. Развитие текстильной промышленности в России обусловлено огромным внутренним рынком, гидроэлектроэнергией, развитой транспортной системой и квалифицированной рабочей силой.
4.США :США является ведущим производителем хлопчатобумажной ткани в мире. Он занимает третье место в мире по производству хлопчатобумажной пряжи и четвертое место по производству хлопчатобумажной ткани. Двумя факторами, ответственными за его рост и развитие, являются: (а) капитал и (б) местный рынок.
В США хлопковая текстильная промышленность локализована в следующих регионах:
(i) Новая Англия: Новая Англия еще несколько лет назад была крупнейшим центром, но теперь Юг превзошел его. В Новой Англии фабрики разбросаны, хотя большое количество веретен сосредоточено в пределах тридцати миль от Провиденса на юге Новой Англии.
Фолл-Ривер — крупнейший центр, а Нью-Бедфорд всего в 30 км от него — второй по величине центр. Этот регион развивался раньше из-за наличия гидроэнергии и подходящего климата. В этом регионе температура менее изменчива, а атмосфера более влажная, чем в соседних регионах.
Мануфактуры характеризуются изысканными товарами, а отделка является характерной чертой промышленности Новой Англии.Большое количество ткани поступает для отделки, крашения, набивки и т. д. с юга и других хлопкопроизводящих районов США.
(ii) Средняя Атлантика: Хлопковые фабрики Среднеатлантических штатов расположены в Пенсильвании, Нью-Йорке и Мэриленде. Но Филадельфия — единственная точка концентрации. Существование этих фабрик в Филадельфии и характер их продукции обусловлены главным образом предложением рабочей силы, дополненным механическими мастерскими и рыночными предприятиями.
Среднеатлантические штаты занимают лидирующие позиции в производстве трикотажных изделий. И в Нью-Йорке, и в Пенсильвании есть локализация трикотажной промышленности, вокруг Кохоуса в долине могавков и в Филадельфии. Филадельфия была основным центром чулочно-носочной промышленности в Соединенных Штатах с тех пор, как немцы поселились в Немецком городе.
(iii) Южные штаты:Рост хлопковой промышленности в южных штатах увеличился в последние годы.Наиболее масштабное строительство заводов на юге было в трех штатах — Северной Каролине, Южной Каролине и Джорджии.
У южных штатов есть такие преимущества, как близость хлопка-сырца, гидроэнергия и дешевая рабочая сила. Другим преимуществом Юга по сравнению со штатами Новой Англии являются более низкие эксплуатационные расходы.
5. Япония : После Китая и Индии Япония занимает третье место в Азии по производству хлопчатобумажных тканей.Первая хлопчатобумажная фабрика в Японии была основана в 1862 году в Кагосиме, но примерно 15 лет спустя хлопчатобумажные фабрики начали быстро запускаться, особенно в городе Осака и его окрестностях.
Основными географическими факторами, способствующими созданию успешного хлопкового производства в Японии, являются:
(i) Подходящий климат,
(ii) Дешевая гидроэнергетика,
(iii) Транспортные средства,
(iv) Предложение дешевой и квалифицированной рабочей силы и
(v) Близость к крупным рынкам Китая и Индии.
Говорят, что японская промышленность имеет следующие преимущества перед конкурентами:
(i) Более дешевая и эффективная рабочая сила
(ii) Большая близость к крупным потребительским рынкам
(iii) Лучшая организация
(iv) Лучшее обслуживание с завода
Японии приходится импортировать почти все сырье, необходимое для текстильной промышленности. Первые попытки создания промышленности были предприняты вокруг хлопководческих массивов районов Ноби и Канто.В настоящее время основные текстильные центры расположены в Тюкё, Хансине, Тояме, Кюсю и Кэйхине, а также в Осаке и Нагое.
Пространственно большинство хлопчатобумажных фабрик расположены в северной части Японии.
Основная часть текстильных изделий производится в следующих регионах:
(i) Равнина Кванто,
(ii) Нагова,
(iii) Равнина Кинки и
(iv) Вдоль северного побережья.
По мере того, как промышленность становилась все более ориентированной на экспорт, текстильное производство постепенно смещалось в сторону побережья.В начале 1990-х старые морально устаревшие заводы закрыли свои производства. Появились новые мельницы с обновленным оборудованием. Большинство японских текстильных фабрик в настоящее время используют новейшие технологии.
Приоритет был отдан снижению себестоимости продукции. Вскоре Япония стала экспортером не только текстильной продукции, но и текстильных машин. В настоящее время наблюдается здоровая конкуренция между мелкими отраслями и крупными промышленными комплексами текстильной промышленности.
6.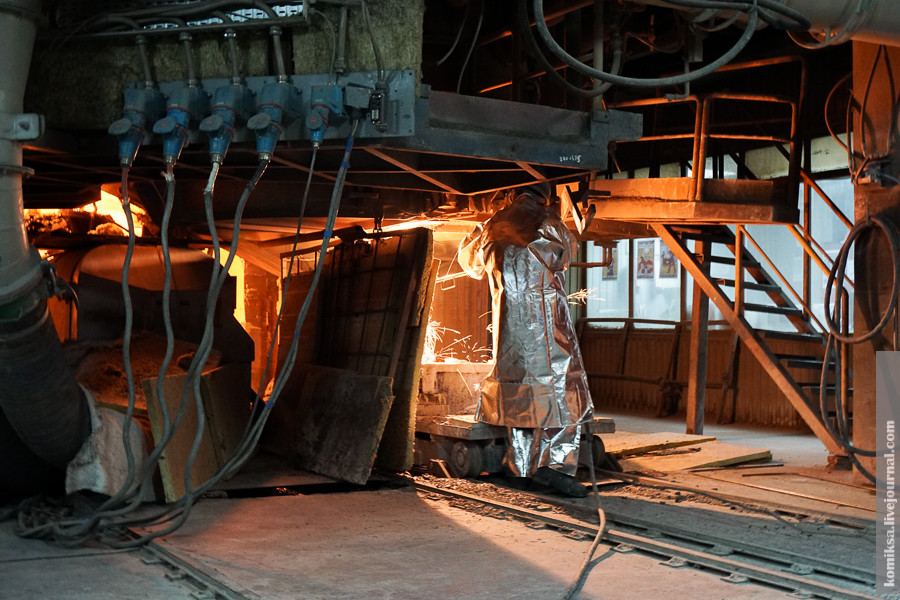
Германия является одним из ведущих производителей хлопчатобумажных тканей. История хлопчатобумажной текстильной промышленности в Германии довольно давняя. Первоначально промышленность была основана на импортном хлопке, и большинство отраслей промышленности было развито в долине реки Рейн. Но Рурский промышленный район вскоре стал ведущим текстильным центром.
Центры производства хлопка в Германии сгруппированы в следующие три группы:
1.Северо-Западный:Состоит из городов Рейнского региона, таких как Бармен и Эльберфилд, и городов Эмс-Фехта, таких как Файне и Гронау.
2. Центральный:Состоит из городов, расположенных вдоль трех горных хребтов, отделяющих Богемию от Германии, Райхенбаха, Хемница, Лейпцига и Дрездена
3. Юго-Западный:Состоит из таких городов, как Аугсбург, Штутгарт и Мюлуз.
Северо-Западный регион имел преимущество местного рынка в промышленном населении, которое также обеспечивало его дешевой рабочей силой. Другие центры имели преимущество в виде гидроэнергии, чистой воды и дешевой рабочей силы горного населения.
Гонконг занимает 7-е место в мире по производству хлопчатобумажной ткани. Промышленность в Гонконге была создана беженцами из коммунистического Китая в 1949 году. Гонконг является зоной свободной торговли и одним из основных перевалочных портов мира. Промышленные товары, особенно текстиль, обеспечивают три четверти общих экспортных поступлений.
Три основные части гигантской текстильной промышленности Гонконга — прядильная, ткацкая и отделочная — находятся в состоянии упадка, от которого они, возможно, никогда полностью не оправятся. Занятость в отрасли резко сократилась в последние годы.
Заводы останавливаются или простаивают. Местные швейники импортируют все больше и больше пряжи и тканей для своих нужд. Текстильная промышленность вместе с швейной промышленностью по-прежнему является крупнейшей обрабатывающей промышленностью с точки зрения продаж и занятости.
Проблема отрасли в основном заключается в затратах. Более высокие затраты на рабочую силу, землю и энергию сделали пряжу и ткани из Гонконга более дорогими, чем из Тайваня, Южной Кореи и Китая.
8. Соединенное Королевство :Великобритания была ведущей страной-производителем хлопка в мире, но она больше не доминирует в мире по производству хлопчатобумажной ткани. История хлопчатобумажной текстильной промышленности не может быть завершена без описания вклада Соединенного Королевства.Промышленная революция 18 века дала толчок развитию хлопчатобумажной текстильной промышленности в Великобритании. Последующее изобретение прядильных машин способствовало росту.
Влажный климат и местная квалифицированная рабочая сила очень помогли в начальный период развития.
Хлопковая текстильная промышленность в Соединенном Королевстве достигла такой высокой известности, что в конце 19 века страна стала бесспорным лидером хлопчатобумажной текстильной промышленности.
Ранние центры были развиты вокруг Шотландской низменности, Ноттингема, Ирландии и Ланкашира. Постепенно Ланкашир стал самым развитым текстильным центром мира.
Факторами, которые помогли раннему развитию текстильной промышленности в Великобритании, особенно в регионе Ланкашир, были — подходящий влажный климат, квалифицированная местная рабочая сила, богатые водные ресурсы, наличие местного угля, дешевая цена на землю и возможность импорта хлопка и т. д. Помимо Ланкашир, Манчестер также стал ведущим текстильным центром.
Города по производству хлопка Боттом, Бери, Рочдейл, Олдем и Стокпорт (в Чешире) расположены полукругом вокруг Манчестера.
Относительное положение Великобритании в текстильной промышленности значительно уменьшилось из-за общего снижения потребления хлопчатобумажных изделий, потери зарубежных рынков и появления новых стран-производителей текстиля, таких как Китай, Индия, Япония и т. д.
9. Другие страны : Другими странами-производителями хлопкового текстиля в Европе являются Франция, Италия, Швейцария, Румыния, Чехия, Бельгия, Польша и Испания. Хлопковая текстильная промышленность Франции имеет долгую историю.
Текстильная промышленность Франции развивалась на импортном хлопке, в частности, из США. Промышленность сосредоточена в северо-восточном промышленном районе. Крупнейшие центры текстильного производства — Белфорд, Колман и Науси.
Италия также стала важным производителем хлопчатобумажной ткани в Европе. Крупные центры текстильной промышленности расположены в бассейне реки По и в альпийских долинах. Милан, Корно, Бергамо, Турин, Генуя, Брекчия, Верона и Комо являются основными центрами хлопчатобумажной текстильной промышленности.
Швейцария имеет хлопчатобумажную текстильную промышленность в северной части страны. Наиболее важным центром является Санкт-Гален.
Румыния также занимает важное место в производстве хлопчатобумажных тканей. Его важные центры расположены в Питеси, Бирладе, Орадя, Гиргуи, Бухаресте, Брашове, Сибиу, Байе, Маре и Тимишоаре.
В Латинской Америке Мексика, Бразилия, Аргентина и Перу играют важную роль в производстве хлопчатобумажных тканей. Мексика является крупнейшей страной-производителем хлопка не только в Латинской Америке, но и в мире.
Текстильная промышленность сначала была развита в районе Орисаба, а затем в Мехико. Основными центрами производства хлопчатобумажных тканей в Мексике являются Герико, Ногалес, Сьюдад-Хуарес, Пьедрас-Неграс, Сан-Луи-Потос, Кудад-де-Мехико, Толука-де-Лердо и Куэрнавака.
Бразилия – еще одна страна Латинской Америки, занимающаяся производством хлопчатобумажных тканей, также играет важную роль в мире. Важными центрами хлопкового текстиля в Бразилии являются: Риу-Гранди-ду-Сул, Минасжерайс и Рио-де-Жанейро.
В Аргентине текстильная промышленность развивалась в Буэнос-Айресе, Ла-Плате и Азуле, а в Перу она развивалась в Трухильо, Лиме, Калао, Леа и Куско.
В Африке основными производителями хлопчатобумажной ткани являются Египет и Южная Африка, хотя Нигерия, Эфиопия и Танзания также производят некоторое количество хлопчатобумажной ткани.
Египет славится высоким качеством хлопка, а также развитой текстильной промышленностью в Искандарии, Танте и Думиате. Египет занимает 10-е место в мире по производству хлопчатобумажной пряжи и 8-е место по производству хлопчатобумажной ткани.
В Южной Африке также развита текстильная промышленность из хлопка в Йоханнесбурге, Блумфонтейне, Дурбане, Восточном Лондоне и Вустере.
В Азии, помимо Китая, Индии и Японии, Пакистан, Южная Корея, Индонезия и Турция являются ведущими производителями хлопчатобумажных тканей.
Пакистан является крупной страной-производителем хлопка в Азии, где также развита хлопковая текстильная промышленность. Хлопковые фабрики в Пакистане расположены в Лахоре, Лайаллпуре, Мултане, Карачи, Сахадре, Монтгомери и Пешаваре.
В последние годы Южная Корея добилась значительных успехов в хлопчатобумажной текстильной промышленности. Крупнейшими центрами хлопкового текстиля являются Инчоу, Тэгу, Масан, Пусан, Кванджу и Сеол.
Индонезия также является экспортером текстиля в Азии. Аналогичная ситуация с Филиппинами.
Турция – еще одна азиатская страна с развитой хлопчатобумажной текстильной промышленностью. Турция является производителем хлопка хорошего качества. Измир, Измит, Сивас, Кисери, Бурса, Эрзурум, Усак и др. являются основными центрами хлопчатобумажной текстильной промышленности Турции.
Текстильная промышленность — Энциклопедия New Georgia
Грузия была лидером текстильной промышленности в девятнадцатом и двадцатом веках.Региональное производство шелка и хлопка давало сырье, необходимое для производства широкого спектра материальных предметов. Строительство текстильных фабрик и мельничных городков в девятнадцатом веке привело к развитию особого промышленного наследия.
Возникновение текстильной промышленности в Грузии было значительным историческим событием, оказавшим глубокое влияние на жителей штата. Нарративы, связанные с текстилем, в частности, с выращиванием и переработкой хлопка, образуют своеобразное промышленное наследие, которое начинается с основания колонии Джорджия в 1732 году, до того, как хлопок доминировал в сельскохозяйственной экономике штата, и за много лет до того, как Джорджия стала ведущим производителем текстиля на Юге.
Производство шелка
В семнадцатом веке шелк стал модной тканью для европейских высших классов, и Англия надеялась конкурировать с процветающей шелковой промышленностью во Франции и Италии.
Тутовое деревоФотография Wikimedia
Колониальные попечители разработали план производства текстиля в колонии в Джорджии, а в 1734 году генерал Джеймс Эдвард Оглторп основал Сад попечителей в Саванне для сельскохозяйственных экспериментов.Среди выращиваемых в саду растений были тутовые деревья, листья которых шли на корм тутовым шелкопрядам. Однако производство шелка оказалось трудным для неподготовленных колонистов Джорджии, поэтому были приглашены опытные итальянские производители шелка, чтобы научить их этому процессу. Колонисты добились успеха в течение года; записи показывают, что в 1735 году английская королева Каролина носила платье из шелка Джорджии.
Примерно в двадцати пяти милях к северо-западу от Саванны немецкоязычные жители Зальцбурга из Эбенезера также пытались производить шелк, и к концу 1730-х годов у них были шелковые производства. Однако сезонные температурные колебания нанесли ущерб чувствительным тутовым шелкопрядам и препятствовали производству шелка. К 1780-м годам вместо шелка выращивали более выносливый и прибыльный хлопок, но производство шелка в Грузии не исчезло полностью. Еще в 1830-х годах некоторые общины, в том числе город Кантон в округе Чероки, все еще пытались производить его. Названный в честь одноименного города шелка в Китае, Кантон в конечном итоге не смог создать центр шелка.
Возникновение производства хлопка
Хлопкоочиститель был изобретен в 1790-х годах Эли Уитни на плантации Кэтрин Грин Малберри Гроув в графстве Чатем. Этот инструмент экономии труда постепенно превратил хлопок в прибыльную культуру, и в течение девятнадцатого века выращивание хлопка быстро росло по всему штату. Белые плантаторы, в свою очередь, использовали порабощенных чернокожих рабочих, чтобы сажать и собирать урожай хлопка с акра на акр. В последующие десятилетия постепенно возникло промышленное производство хлопка в штате.
Изображение из Национального музея американской истории, Смитсоновский институт
После войны 1812 (1812-1815) некоторые южные лидеры, пытаясь воспроизвести процветание хлопчатобумажных фабрик в Новой Англии, построили на Юге текстильные фабрики. Самыми ранними из этих фабрик в Джорджии были фабрика Antioch в округе Морган и фабрика Bolton в округе Уилкс. Обе фабрики, построенные примерно в 1810 году, к началу 1820-х годов пришли в упадок, в основном из-за сельской экономики региона, малонаселенности и слаборазвитой транспортной сети.Идея текстильных фабрик как средства торговли вновь всплыла на поверхность, когда экономическая депрессия 1837 года потребовала от южных бизнесменов альтернативных источников дохода. В то же время, после насильственного и насильственного переселения индейцев крика в центральной и западной Джорджии стало доступно больше земли для выращивания хлопка.
Ранние текстильные фабрики состояли из небольших фабрик, ограниченных по размеру и масштабу, которые производили грубые ткани для мешков для зерна. Расположение этих фабрик было ограничено районами, в которых быстро движущиеся водные пути можно было использовать для питания мельничного оборудования.В результате мельницы часто располагались вдоль быстрых рек или вдоль линии падения, участка земли шириной в несколько миль, который проходит вдоль границы между холмистым регионом Пьемонт и Верхней прибрежной равниной, от Колумбуса до Огасты. Линия падения отмечает береговую линию доисторического океана; земля к северу от него выше по высоте, чем земля к югу. В результате водные пути вдоль линии падения набирают скорость по мере того, как они опускаются на более низкую высоту.
Фотография andrewI04
Топография вдоль линии падения, возможно, подходила для работы фабрики, но отсутствие легкого доступа к белой рабочей силе заставило первых фабрикантов, а также владельцев плантаций, использовать порабощенных людей в качестве текстильных рабочих.На других фабриках работали члены местных белых фермерских семей, когда они были доступны.
Два видных грузина участвовали в первых успешных мельницах государства. В 1829 году Огюстен Смит Клейтон, известный юрист и судья, и его деловые партнеры открыли фабрику в Джорджии в Афинах, на берегу северной реки Окони. Это место мельницы также стало местом Уайтхолла, первой мельничной деревни в Джорджии, когда собственность была продана Джону Уайту в 1835 году. Примерно в то же время Уильям Шлей, губернатор Джорджии, построил Ричмондскую фабрику на Спирит-Крик в Огасте в 1834 году.Воодушевленные этими прибыльными предприятиями, другие бизнесмены также отважились заняться этой отраслью. К 1840 году в Грузии работало девятнадцать текстильных фабрик. Мельницы тоже становились больше; одним из крупнейших было производство Розуэлла в округе Кобб, открытое в 1839 году.
Магазин Whitehall Mill StoreПредоставлено библиотекой Оуэнса, Школой окружающей среды и дизайна, Университет Джорджии
Почувствовав появление прибыльного предприятия для своего штата, политические лидеры приняли закон, облегчающий потенциальным операторам заводов регистрацию своего бизнеса. Промышленность начала процветать, и к 1850 году в Грузии было тридцать восемь текстильных фабрик. Ткань, производимая на фабриках, превратилась из ранних грубых тканей, иногда называемых «шерстью Джорджии», в хлопчатобумажную утку, более тяжелый материал, похожий на холст. Большинство действующих в то время региональных фабрик были небольшими, с менее чем 2000 веретен и 100 рабочими. Часто эти мельницы располагались рядом с местными мельницами, мукомольными и лесопилками.
Однако в развивающихся городах Джорджии фабрики, как правило, были крупнее.Одним из примеров была компания Eagle Manufacturing Company в Колумбусе, открытая в 1851 году Уильямом Х. Янгом, уроженцем Нью-Йорка. Рост текстильной промышленности в Джорджии, наряду с ростом населения и расширением железных дорог в штате, побудил Уильяма «Парсона» Браунлоу, редактора газеты из Теннесси, назвать Джорджию «Южной Новой Англией» в 1849 году.
В течение 1850-х годов владельцы заводов в Джорджии сосредоточились на улучшении, а не на расширении своих заводов. Сотрудники, которые к тому времени состояли исключительно из белых сельских жителей из близлежащих районов, превратились в квалифицированную рабочую силу.Некоторые владельцы в штате поощряли опытных северных фабричных рабочих переезжать на фабрики в Джорджии, где они могли передать свой опыт местным рабочим; некоторые опытные фабричные рабочие приехали даже из Англии.
Гражданская война и ее последствия
Когда разразилась Гражданская война (1861–1865 гг.), оставшиеся в эксплуатации фабрики начали производить униформу, одеяла и другие товары для войск Конфедерации. Поскольку большая часть ее рабочей силы была истощена армией, обученная рабочая сила стала в основном белыми женщинами.К 1864 году опыт и лояльность рабочих фабрики считались проблемой для армии Союза. Две крупнейшие фабрики Джорджии, Нью-Манчестер в округе Кэмпбелл (позже графство Дуглас) и фабрика Розуэлл в округе Кобб, были среди тех, которые были уничтожены войсками генерала Союза Уильяма Т. Шермана во время кампании в Атланте. Чтобы гарантировать, что рабочие этих фабрик не будут искать работу в других местах Конфедерации, силы Союза переместили в основном женщин-рабочих фабрики в Нью-Манчестере на фабрику в Розуэлле, а оттуда обвинили женщин в государственной измене и депортировали их на север поездом.Затем войска сожгли мельницы.
Фотография Евангелио Гонсалеса
Однако не все мельницы в Джорджии были уничтожены войсками Союза. Фабрика «Трион» в округе Чаттуга, первая хлопчатобумажная фабрика, построенная на северо-западе Джорджии, не пострадала. Один из владельцев, Эндрю Олгуд, убедил генерала Союза Уильяма Т. Шермана в том, что его фабрика производила ткань для Конфедерации в знак протеста и что он на самом деле был «человеком Союза». В результате Шерман выдал заводу документы о защите.
После окончания Гражданской войны в 1865 году производство хлопка в Грузии вновь стало единственным важнейшим фактором экономики штата. Когда Реконструкция в штате пошла на убыль, экономическая депрессия 1873 года заставила мелких фермеров и предприятия страдать от нехватки капитала. Отмена рабства и освобождение чернокожих рабочих уже привели к прекращению работы многих плантаций, и по мере дальнейшего расширения южной железнодорожной сети в штате начали происходить серьезные преобразования.Сельскохозяйственная финансовая база Грузии сместилась в сторону новой промышленной направленности, а текстильные фабрики стали гораздо более жизнеспособным средством торговли.
Новое южное расширение
В 1870-х и 1880-х годах Генри У. Грейди из Конституции Атланты поощрял индустриализацию в штате и подразумевал, что гражданская ответственность требует строительства хлопчатобумажной фабрики в каждом городе Джорджии. Лидеры общин, вдохновленные риторикой Грэди и серией хлопковых выставок, проведенных в 1880-х годах в Атланте, выступили с новым сплачивающим лозунгом: «Принесите хлопковые фабрики на хлопковые поля.За этим последовал трехдесятилетний бум строительства хлопчатобумажных фабрик; новое стремление к индустриализации было названо «Кампанией хлопкопрядильных фабрик Нового Юга».
Помимо строительства новых мельниц, часть мельниц, поврежденных или заброшенных в военное время, была восстановлена. В Колумбусе Уильям Янг восстановил свою фабрику Eagle, переименовав ее в Eagle and Phenix Mills. Название относилось к мифическому фениксу, который, как и фабрика Янга, восстал из пепла войны. Лафайет и Уорд Ланье, оба ветераны Конфедерации, основали West Point Manufacturing в Вест-Пойнте, когда они купили старую производственную компанию Chattahoochee.По всей Джорджии и остальной части Юга эти недавно возникшие фабрики служили не только производственными предприятиями; они были символами выживания и роста для отдельных сообществ и региона в целом.
Eagle and Phenix MillsПредоставлено Библиотекой Конгресса, Отдел эстампов и фотографий
После 1880 года, когда многие заводы Джорджии достигли прибыльности, северные деловые круги начали инвестировать в южные предприятия. Северные инвесторы часто предпочитали размещать свои заводы на юге, где налоги были ниже, климат мягче, а рабочая сила дешевле, чем на севере. Добавленный капитал инвесторов позволил расширить ряд фабрик, и несколько городов превратились в основные центры текстильного производства штата. Augusta, Columbus, LaGrange и Macon освоили новую отрасль с быстрым ростом и положительной финансовой отдачей.
К 1900 году текстильное производство было основной отраслью промышленности Грузии; согласно переписи населения США, в том году в штате действовало девяносто восемь текстильных фабрик. Молодых людей поощряли приобретать навыки в школах торговли хлопком, которые появлялись по всему штату, и в 1899 году открылся текстильный факультет Технологической школы Джорджии (позже Технологический институт Джорджии).(Позже кафедра стала известна как Школа текстильной и волокнистой инженерии, а в 2003 году название было изменено на Школу полимерной текстильной и волокнистой инженерии.)
Паросиловая технология
В 1830-х годах появилась технология для приведения мельниц в действие паром, но использование пара не пользовалось популярностью в Грузии до 1850-х годов. Энергия пара, полученная путем сжигания древесины или угля, освободила мельницы от зависимости от энергии воды и позволила владельцам размещать свои предприятия в городских районах, а не в тех, которые расположены вдоль линии падения.В годы после Гражданской войны, когда в паровой двигатель были внесены усовершенствования, паровые мельницы стали конкурировать с мельницами, работавшими исключительно за счет энергии воды.
Одним из примеров паровой фабрики была фабрика Fulton Bag and Cotton Mills в Атланте, основанная в 1868 году для производства тканевых и бумажных мешков. Владелец мельницы Джейкоб Эльзас всегда использовал пар для работы своей фабрики. По мере расширения операций в 1880-х годах он установил огромный паровой двигатель, который, как говорили, был одним из крупнейших на Юге.
В то время как некоторые владельцы мельниц начали использовать силу пара, другие испытали водяное колесо нового типа — турбину. Турбины были более эффективными и меньше по размеру, чем старые водяные колеса; они могли обрабатывать больше воды, вращаясь намного быстрее. Некоторые владельцы южных заводов сочли турбины настолько эффективными, что продолжали использовать их до 1930-х годов.
В Огасте канал, построенный в 1845 году, служил альтернативным источником энергии для мельниц, построенных вдоль его берегов. В то время город получил прозвище «Южный Лоуэлл» в честь успешного промышленного города Лоуэлл, штат Массачусетс.В 1875 году были наняты китайские рабочие по контракту, чтобы расширить канал, чтобы увеличить трафик.
Милл Виллидж
Мельничная деревня, часть семейного рабочего механизма, широко используемого мельниками в Джорджии, была адаптирована из системы, разработанной примерно в 1810 году Сэмюэлем Слейтером, владельцем мельницы из Новой Англии. В системе Слейтера целые семьи работали на фабрике и получали собственный дом. Северным бизнесменам, вложившим средства в южные заводы, понравилась идея сохранить семьи вместе, чтобы получить лояльную рабочую силу, которая будет работать на заводе в течение нескольких поколений. Сообщества домов, принадлежащих компаниям, которые выросли вокруг фабрик, назывались мельничными деревнями. Владельцы обычно собирали ренту с рабочих; размер арендной платы иногда определялся тем, сколько членов семьи работало на фабрике.
В течение 1880-х годов вдовы с детьми, обеспеченные приличным жильем, массово прибывали на фабрики. Поскольку в Грузии все еще существовала широко распространенная бедность, получение работы на фабрике часто было лучшим способом трудоустройства.Часто матери присматривали за домом, пока дети работали на фабрике. В 1890 г. среди рабочих текстильной фабрики мужчины составляли 37%, женщины — 39%, дети — 24%. К 1910 году на 116 заводах Джорджии работало более 27 000 человек, многие из которых жили в служебных домах. Согласно публикации Georgia Railway and Power от 1923 года, «в этих заводских сообществах Джорджии есть дух. . . . он представляет собой один из наиболее ценных элементов производства хлопка в этом штате». Два примера известных мельничных деревень в Джорджии включают Cabbagetown, мельничную деревню Fulton Bag и Cotton Mills и Уайтхолл в Афинах.
Предоставлено Библиотекой Конгресса США, Отдел эстампов и фотографий
Расширение двадцатого века
После 1900 г. в Грузии продолжался мельничный бум, когда компании расширялись в другие области и производили новые виды текстиля. К 1908 году компания Bibb Manufacturing Company of Macon управляла семью фабриками, которые производили различные хлопчатобумажные изделия, в том числе чулочно-носочные изделия, ковровую пряжу, шпагат, хлопчатобумажную ткань и шинную ткань для зарождающейся автомобильной промышленности.К 1915 году Фуллер Э. Каллауэй-старший владел девятью прибыльными фабриками, работающими в Лагранже или его окрестностях; они также расширились за счет производства продукции для автомобильной промышленности.
Небольшие фабрики по всему штату производили хлопковое полотно, сорочечные ткани, различные виды шпагата и веревок. Они также экспериментировали с текстильными вариациями. В районе Далтона Кэтрин Эванс (Уайтнер) начала продавать покрывала из синели в 1900 году, тем самым создав текстильную промышленность, которая позже превратилась во всемирную ковровую промышленность.
Первая мировая война (1917-18) стала поворотным моментом в текстильной промышленности. Вступление Соединенных Штатов в войну создало высокий спрос на ткани для экипировки американских войск, и многие фабрики в Джорджии получили государственные контракты. Однако по мере того, как рабочая нагрузка на фабриках начала увеличиваться, рабочие-мужчины были призваны в вооруженные силы, а некоторые работницы фабрик отправились домой, чтобы помогать на семейных фермах; в результате возникла нехватка рабочей силы. На Crown Mills в Далтоне менеджеры потребовали, чтобы правительство освободило некоторых их рабочих от призыва, а владельцы фабрик по всей Джорджии, зная о конкуренции между заводами, предложили более высокую заработную плату и лучшие дома, чтобы привлечь рабочих на свои фабрики.
После войны перед отраслью встали новые задачи. По всему штату фабричные семьи потеряли членов семьи, одни во время войны, другие во время эпидемии гриппа 1918 года. Хлопковые фермеры были опустошены долгоносиком. Даже изменения в моде повлияли на производство на фабриках; новые более короткие юбки требовали меньше ткани и, в свою очередь, меньше рабочих. Несмотря на то, что нанимались новые чулочно-носочные фабрики, на более крупных фабриках, столкнувшихся с излишками ткани во время войны, было слишком много сотрудников.
Дополнительные проблемы для рабочих включали внедрение нового оборудования, для работы которого требовалось очень мало людей. Владельцы фабрик, стремясь повысить эффективность производства, привлекли внешних консультантов для проведения исследований времени. Результатом стало то, что рабочие завода назвали растяжкой . Растяжение означало, что меньшее количество рабочих отвечало за большее количество машин и большее производство, и у них было мало времени для выполнения своих задач. Процветание, существовавшее до Первой мировой войны, закончилось, и рабочие изо всех сил пытались сохранить свои рабочие места, часто безрезультатно.
Предоставлено Библиотекой Конгресса, Отдел эстампов и фотографий
Для отдельных заводов популярность автомобилей означала новые возможности и конкуренцию. Даже более мелкие текстильные фабрики подписали контракты на производство компонентов для автомобилей, в том числе шинного корда и резинотехнических изделий. Многие фабрики добавили производственные мощности по производству каучука к своим существующим заводам. Однако их эксплуатация часто оказывалась дорогостоящей, и к 1930-м годам некоторые заводы были вынуждены закрыть или продать свои производственные мощности по производству каучука.Так было на Старк-Миллс в Хогансвилле в северном округе Троуп; фабрика была продана фирме U.S. Rubber, которая позже стала Uniroyal.
Расовая сегрегация
Для афроамериканцев жизнь на юге Джима Кроу означала ограниченные возможности трудоустройства. Текстильная промышленность в Грузии была строго обособлена; Чернокожие рабочие-мужчины выполняли только черную работу на фабриках, и им не разрешалось жить в фабричных деревнях. До 1950-х годов чернокожие женщины практически не участвовали в работе на фабрике.Их нанимали мельничные семьи, чтобы они готовили, убирали и присматривали за младшими детьми в мельничной деревне.
В отрасли, которая часто изо всех сил пыталась оставаться платежеспособной, белые рабочие рассматривали возможность трудоустройства чернокожих на фабриках как угрозу своим рабочим местам и, в свою очередь, запугивали афроамериканцев. Во время Первой мировой войны многие отрасли в северных штатах испытывали нехватку рабочей силы, и рабочие из числа меньшинств смогли найти хорошую работу в этой части страны. После войны промышленный рост на Севере продолжился, а текстильные фабрики на юге остановились.Знание того, что хорошую работу можно получить за пределами региона, побудило большое количество афроамериканцев покинуть страну в результате исхода, который стал известен как Великая миграция.
Трудовые волнения
С началом Великой депрессии в 1929 году небольшие фабрики в Джорджии были вынуждены закрыться, что привело к значительной безработице для многих семей фабрикантов. В 1933 г. был принят Закон о восстановлении национальной промышленности, составлявший часть «Нового курса» президента США Франклина Д. Рузвельта, который требовал от операторов заводов соблюдения правил, касающихся как продолжительности рабочего дня, так и заработной платы и пособий сотрудников.Дети в возрасте до шестнадцати лет больше не могли быть приняты на работу. Когда некоторые операторы фабрик решили проигнорировать кодексы, рабочие протестовали, полагая, что кодексы обеспечивают защиту от несправедливого обращения, а также право на объединение в профсоюзы.
По мере того, как заводчане становились более уверенными в себе, по всему штату вспыхивали протесты против нарушений кодекса. Протесты достигли точки кипения, когда рабочие объявили забастовку 1 сентября 1934 года. Эта всеобщая текстильная забастовка 1934 года, позже названная Восстанием 34 года, охватила более 200 000 северных рабочих и 170 000 южных рабочих и стала крупнейшим рабочим протестом в история Юга; в Грузии участвовало около 44 000 рабочих.Некоторых уводили с фабрик «летающими эскадрильями» или караванами автомобилей, заполненными рабочими, которые путешествовали между фабриками и призывали других присоединиться к забастовке.
В некоторых случаях между пикетчиками и охранниками, нанятыми заводскими начальниками, вспыхивали столкновения. В Джорджии отдельные эпизоды насилия были зафиксированы на заводах в Сидартауне, Колумбусе, Мейконе и Портердейле; Сообщалось о смертельных случаях в Трионе и Августе. Эти инциденты, наряду с другими жертвами в Северной Каролине и Южной Каролине, разозлили рабочих в Джорджии, многие из которых присоединились к местным отделениям национального профсоюза United Textile Workers (UTW).В 1934 году в Грузии было шестьдесят местных отделений UTW.
Callaway Mills StrikeПредоставлено архивом округа Троуп
Губернатор Джорджии Юджин Талмадж, опасаясь, что в штате вспыхнет массовое насилие, объявил военное положение, а забастовщики, продолжавшие протесты, были арестованы. Первые аресты, многие из которых были работницами, были произведены на хлопчатобумажных фабриках Сарджент и Ист-Ньюнан в округе Коуэта. Члены Национальной гвардии Джорджии, вооруженные штыками, перевезли забастовщиков на военных грузовиках в Форт Макферсон в Атланте, где рабочие были заключены в камеры на открытом воздухе, ранее занимаемые немецкими военнопленными во время Первой мировой войны.Арестованных держали там до окончания забастовки через три недели после того, как UTW получил от правительства заверения в том, что проблемы на южных текстильных фабриках будут расследованы.
После забастовки большинство жителей Грузии считали, что фабриканты победили. Бастующие были вынуждены вернуться к неулучшенным условиям труда, а многим бастующим, особенно забастовочным активистам, было запрещено возвращаться к работе на текстильных фабриках. Некоторых также выгнали из фабрики в одной одежде на спине.Рабочие, опасаясь занесения в черный список, отказались от профсоюзов, и многие из них больше никогда не обсуждали забастовку. Хотя проблемы на заводах в конечном итоге будут решены, большинство этих положительных изменений не произошло до вступления Америки во Вторую мировую войну (1941-45).
Годы Второй мировой войны
Когда Соединенные Штаты вступили во Вторую мировую войну, контракты военного времени вернули предприятиям прибыльность. Они снова смогли нанять больше рабочих. Различные волокна, такие как нейлон, пошли в производство для использования в войсках.Американская корпорация Chatillon, итальянская компания, расположенная в районе Рима, производила синтетический шелк для парашютов. Крупнейшим производителем текстиля для военной промышленности в стране была компания Bibb Manufacturing Company, которая производила такие предметы, как камуфляжные сети, спасательные плоты, противогазы и униформу.
Рабочий хлопковой фабрикиПредоставлено Библиотекой Конгресса, Отдел эстампов и фотографий
Среди рабочих возобладал патриотизм. Многие рабочие активно участвовали в мероприятиях в тылу, таких как сбор металлолома, а некоторые текстильные фабрики Джорджии сделали все возможное, чтобы произвести ткань для военной формы. Когда война закончилась, некоторые заводы получили награду президента США «Е» за выдающиеся заслуги перед военными действиями.
Модернизация, упадок и адаптация
После войны производство текстильных фабрик какое-то время продолжало процветать, и к середине 1950-х годов южные фабрики перерабатывали 90 процентов хлопка, производимого в Соединенных Штатах. Но отрасль в очередной раз была вынуждена терпеть изменения.
По мере развития новых технологий заводы становились все более автоматизированными.Чтобы оставаться прибыльным, были сокращены расходы и резко сокращена рабочая сила. Мельничники начали распродавать дома в мельничных поселках еще в 1940-х годах. Сначала дома были выставлены на продажу рабочим, которые смогли купить их по разумной цене. К 1970-м годам все текстильные компании продали свои дома; некоторые деревни, которые ранее были отдельными образованиями, вошли в состав близлежащих городов.
Заводы были преобразованы и другими способами. С введением новых роботов, компьютеров и высокоскоростного оборудования рабочая сила еще больше сократилась.В 1971 году Конгресс США учредил Управление по безопасности и гигиене труда, федеральное агентство, отвечающее за обеспечение соблюдения законодательства в области охраны труда и техники безопасности на всех фабриках. У старых заводов, многие из которых были с устаревшим и опасным оборудованием, не было капитала для инвестиций в новое оборудование, и они были вынуждены закрыться.
В 1994 году Североамериканское соглашение о свободной торговле (НАФТА) отменило квоты между США, Канадой и Мексикой на текстильные изделия, производимые в этих трех странах.Некоторые крупные текстильные корпорации рассматривали НАФТА как возможность глобализировать разнообразную текстильную промышленность Грузии, в то время как другие опасались потери рабочих мест и снижения заработной платы. НАФТА стимулировало торговлю и развитие в некоторых отраслях, но производство текстиля в Грузии продолжало сокращаться. Аутсорсинг работы недорогим азиатским текстильным компаниям стал более жизнеспособным финансовым вариантом для некоторых испытывающих трудности заводов в 1990-х годах, что в конечном итоге привело к закрытию дополнительных заводов.
Предоставлено Институтом ковров и ковровых покрытий
Закрытие заводов затронуло города по всему штату.В Доусоне, в округе Террелл, рабочие Almark Mills поняли, что компания обанкротилась, получили ссуды и сформировали кооператив, принадлежащий рабочим Доусона, чтобы выкупить завод. Три года спустя, в 2001 году, группа распалась, а завод закрылся.
Thomaston MillsПредоставлено архивом Thomaston-Upson
В 1996 году общая занятость в текстильной промышленности США упала до 4 процентов от всех промышленных рабочих по всей стране. В Грузии в текстильной промышленности осталось всего 16,5% промышленных рабочих, что на 50% меньше, чем в 1950-х годах.Однако в северо-западной части штата, включая округа Бартоу, Гордон, Мюррей и Уитфилд, уровень безработицы остается ниже из-за процветающей ковровой промышленности. В 1980-х годах производители, нуждавшиеся в большем количестве рабочих, начали нанимать латиноамериканских иммигрантов, которые затем обосновались в районе Рима. Некоторые руководители заводов считают, что отрасль продолжает процветать благодаря труду этого населения.
Другие текстильные фабрики в Джорджии закрыли свои двери во время и после Великой рецессии.В 2008 году компания Georgia Narrow Fabrics перенесла производство из Джесупа в Гондурас. В феврале 2020 года Mount Vernon Mills в Альто объявила о своем предстоящем закрытии и уволила 600 сотрудников. Поскольку в регионе работает все меньше и меньше заводов, многие из этих рабочих с минимальной квалификацией переходят в другие области, некоторые из них находят работу на близлежащих мясоперерабатывающих фабриках или других производственных предприятиях. По данным Бюро статистики труда США, в 2017 году в Грузии осталось всего 19 300 рабочих мест на текстильных фабриках, что на 60,5% меньше, чем в 2001 году.Несколько небольших фабрик по-прежнему работают в штате, но хлопок больше не является главным в Грузии. Китай в настоящее время является крупнейшим производителем текстиля.
Фотография Эда Шипула
Стремясь спасти некоторые мельничные постройки от сноса, местные жители по всему штату начали участвовать в движениях по восстановлению заброшенных мельничных построек. В Ньюнане хлопковая фабрика в Ист-Ньюнане была преобразована в сдаваемые в аренду помещения и получила название «Лофты Ньюнана».В Атланте фабрика, в которой разместились Fulton Bag and Cotton Mills, стала «лофтами Fulton Cotton Mill Lofts» в результате одного из крупнейших преобразований лофтов в Соединенных Штатах. Бывший завод Enterprise Mill в Огасте был перестроен в апартаменты-лофт, офисные и торговые помещения. Небольшие заводы, расположенные рядом с живописными ручьями, теперь являются желательными местами для размещения гостевых коттеджей, уединенных мест для руководителей и спа-комплексов. Одним из примеров является Historic Banning Mills, гостиница, расположенная на Снейк-Крик, рукаве реки Чаттахучи в округе Кэрролл.