Сырье для производства искусственных волокон: Искусственные волокна
Искусственные волокна
Искусственные волокна – один из видов сырья, применяющегося в производстве медицинских изделий различного назначения. Их получают из высокомолекулярных природных соединений (силикатного стекла, металлов и сплавов, белков, целлюлозы).
Применение искусственного волокна в производстве медицинских изделий позволяет придать им особые свойства, например, увеличить впитывающую способность (актуально для салфеток, гигиенических средств и т.п.), придать прочность, обеспечить устойчивость к размоканию.
Виды искусственных волокон
Сегодня изготавливаются различные типы сырья для медицинской промышленности. Все виды искусственных волокон объединяет гигиеничность. Наиболее распространенными материалами являются:
- вискозное волокно;
- ацетатное волокно;
- триацетатное волокно.
Каждый материал имеет свои преимущества. Так, вискозное волокно гигроскопично, отличается высокой термостойкостью, устойчивостью к щелочам.
Свойства искусственных волокон ацетатной группы – это низкая термостойкость (до 90°С), высокая степень мягкости. Триацетатные материалы отличаются упругостью. Они превосходят ацетатные по степени термостойкости, однако обладают низкой гигроскопичностью.
Особенности производства искусственных волокон
Производство искусственных волокон – сложный, многоэтапный процесс. Его специфика обусловлена типом сырья и конечной целью производителя. Вискозные волокна, например, изготавливают из целлюлозы (преимущественно еловой). Для этого сырье расщепляется, обрабатывается химическими составами, превращается в прядильный раствор. Искусственный материал имеет вид комплексных нитей.
Металлосодержащие волокна изготавливаются полностью металлическими и металлизированными (имеют соответствующее покрытие). Первые представлены в виде плоских и круглых мононитей.
В современном текстильном и специальном производстве используются также медно-аммиачные искусственные нити. Процесс их изготовления очень сложен, затратен. Волокна являются достаточно дорогими. Это ограничивает сферу их использования. Сырье применяется преимущественно для изготовления трикотажа специального назначения. Материал обладает особыми свойствами: повышенной прочностью, высоким коэффициентом растяжения, способностью восстанавливать форму.
Купить Искусственные волокна, а также узнать стоимость и возможность доставки вы можете, позвонив по телефонам:
+7 (495) 505 — 6773,
+7 (495) 505 — 6772,
или заполнить форму заявки ниже.
Искусственные волокна — производство искусственных волокон, сырье для синтетических нитей
Легкая индустрия давно использует органические и неорганические компоненты для производства тканей. Они недорогие, удобны в использовании. Для этих целей идут отходы дерева, хлопка, смолы, кислоты и прочее.
Содержание
Виды искусственных волокон
Все искусственно созданные ткани обладают гигиеничностью. Большое распространение имеют полотна из вискозного, ацетатного, триацетатного волокна. Каждый материал имеет свои преимущества и недостатки.
Вискоза
Изготавливается из комплексного сырья, включающего: древесину различных видов, бамбук. Технология состоит из измельчения, обработки теплом, щёлочью и фильтрация.
Присутствуют следующие достоинства:
- высокая гигроскопичность — до 12 %;
- устойчивость к воздействию щелочей;
- хорошая термостойкость.
Недостатки:
- сильно мнется при эксплуатации;
- большая усадка;
- влажное полотно рвётся от физических воздействий, поэтому нельзя сильно выкручивать изделие.
Чтобы улучшить структуру волокна, применяют синтетические пропитки.
Ацетат
Образующим волокно веществом, является очищенная целлюлоза. Вырабатывается с помощью специальной технологии, где в реакцию вступают древесина, уксус и серная кислота.
Искусственные волокна имеют следующие преимущества:
- Приятный вид и осязаемость.
- Многообразие палитры цветов.
- Податливость при драпировке.
- Отсутствие усадки, устойчивость к поеданию молью.
Недостатки:
- Низкая прочность ткани.
- Повышенная статичность (наэлектризованность).
- Дискомфорт в жаркую погоду.
- Растворяется от ацетона, щёлочи, кислоты, от контакта раскалённых предметов.
- Может выцветать от воздействия солнца, пота.
- Для ацетатных тканей изобрели стойкие краски, которые позволяют одежде долго оставаться в первозданном виде.
Триацетат
Для изготовления искусственного полотна используется хлопковая или древесная целлюлоза, путем сложных химических манипуляций.
Продукт органического соединения обладает положительными свойствами:
- Стойкость к влажности, солнечным лучам, и прочим влияниям окружающей среды.
- Схожесть с натуральным шелком из-за удивительного блеска, струящейся фактуры.
- Прикосновение передает ощущение гладкости, материал не вызывает раздражений.
- Идеально подходит для драпированных, плиссированных изделий.
- Обладает прочностью, износостойкостью.
- Не подвергается деформации от стирки и глажения.
- Недостатки:
- Ткань из триацетатных ниток не поглощает влагу.
- Не «дышит», значит, не пропускает воздух.
- Отсутствуют свойства терморегуляции — в такой одежде жарко летом.
Где применяются искусственные волокна
Вискоза. Иногда используется в естественном виде, также его добавляют к другим нитям. Полотно из вискозного волокна можно встретить в бельевом трикотаже, подкладках верхней одежды, декоративных тканях, галантерейных изделиях. Из вискозных нитей получается изящная вышивка. Как ни странно звучит, сырье востребовано для производства искусственного меха. Ворсинки шуб и других изделий создают эффект натуральности материала.
Ацетат. Материя из данного волокна получается нежная, легкая, из нее шьют летние платья, майки, плиссированные юбки. Ацетатные ткани также идут для производства нижнего белья, они безопасны для здоровья и хорошо отстирываются. В мебельной промышленности данное полотно используется в качестве декоративной обшивки.
Триацетат. Входит в число популярных искусственных материалов. Часто дизайнеры используют его из-за легкости и уникальных свойств. Волокно обладает низкой теплоотдачей, поэтому подходит для подкладок в зимнюю верхнюю одежду типа курток, пальто и так далее. Материал прекрасно смотрится в качестве штор разных расцветок, форм, драпированных занавесок, портьер.
#волокноСырье для производства химических волокон
из «Общая химическая технология Том 2»
Для производства волокон и пленок пригодны природные и синтетические высокомолекулярные соединения со сравнительно большим молекулярным весом.

Основное количество искусственных целлюлозных волокон получается путем переработки древесной целлюлозы, преимущественно сульфитной целлюлозы. [c.667]
Состав хлопковой и древесной целлюлозы сопоставлен в табл. 43. [c.667]
Физико-химические и технологические свойства целлюлозы удовлетворяют основным требованиям, предъявляемым к исходным материалам для производства искусственных волокон. Целлюлоза является высокомолекулярным соединением, в макромолекуле ее содержатся полярные группы. Изменяя условия выделения целлюлозы из растительных материалов и дальнейшей ее переработки, можно получать продукты с различной степенью полимеризации. Молекулы целлюлозы имеют линейную, относительно сильно вытянутую, неразветвленную форму. Целлюлоза и особенно ее эфиры растворимы в доступных растворителях. [c.667]

Эластичность их недостаточна, они обладают повышенной теплопроводностью и мало устойчивы к действию кислот и щелочей. [c.668]
Вследствие недостаточной эластичности и повышенной теплопроводности искусственные целлюлозные волокна не являются полноценными, заменителями шерсти. Волокна, по свойствам наиболее близкие к шерсти, могут быть получены из материалов, сходных по структуре и химическому составу с природным белковым волокном. Таким исходным материалом могут являться различные фибриллярные белки, т. е. белки, молекулы которых имеют сравнительно вытянутую форму. К фибриллярным белкам относятся казеин, выделяемый из обезжиренного молока, зеин, выделяемый из кукурузы, а также белки, выделяемые из сои, земляного ореха и т. д. [c.668]
Искусственные белковые волокна сильно набухают в воде.
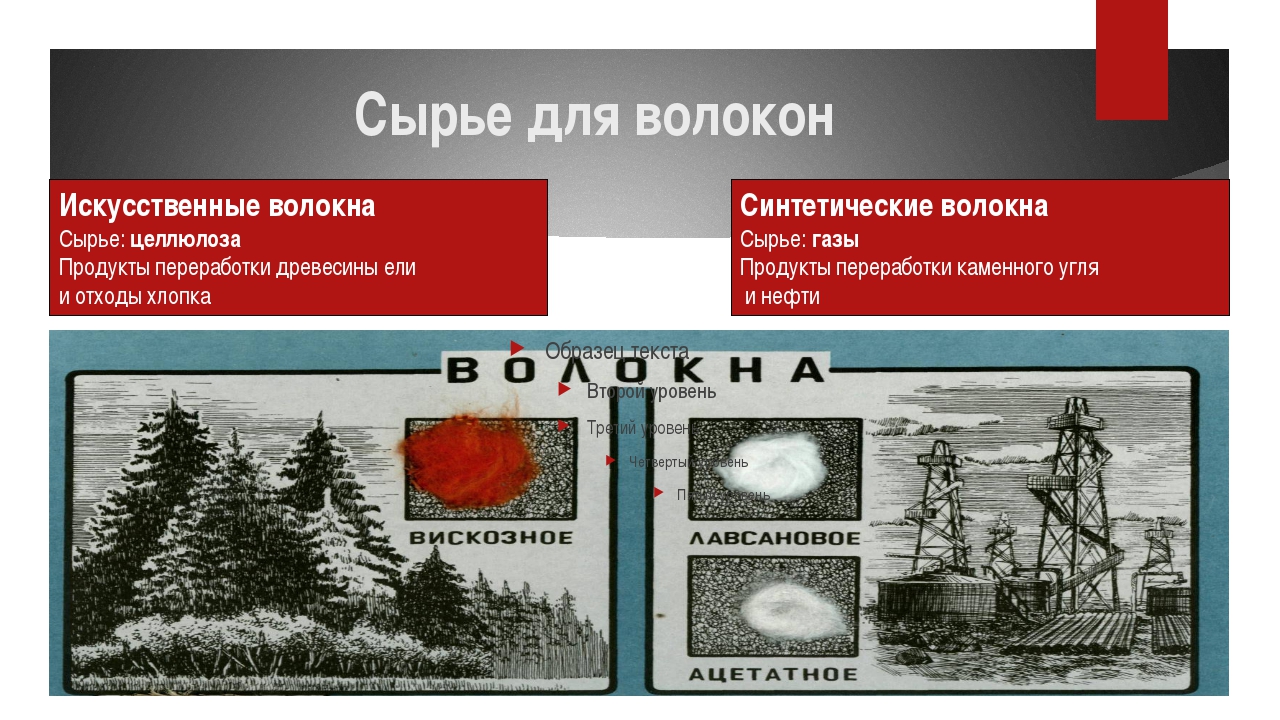
Значительно большие возможности изменения свойств получаемых волокон, в соответствии с требованиями различных отраслей народного хозяйства, появляются при производстве синтетических волокон. [c.668]
Для синтеза полимеров, применяемых в производстве синтетических волокон, используются различные мономеры, важнейшими из которых являются капролактам, гексаметилендиамин, адипиновая кислота (производство полиамидных волокон), терефталевая кислота и этиленгликоль.

Вернуться к основной статье
Искусственные волокна мировое производство — Справочник химика 21
Искусственные волокна на основе клетчатки ныне занимают видное место в общем балансе текстильного сырья. Так, к концу 50-х годов мировое производство текстильных волокон составило около 19 млн. т. Из них около 10 млн. т составляло хлопковое волокно и около 2,5 млн. т искусственное волокно на базе клетчатки. Все остальные виды текстильного сырья — шерсть, натуральный шелк, лубяные волокна (лен, пенька, джут), синтетические волокна — производятся в меньших масштабах, чем искусственное волокно из клетчатки.
Масштабы производства кордных нитей. В наиболее развитых странах для производства К. н. используются в основном химич. волокна, к-рые в этой отрасли промышленности неуклонно вытесняют природные волокна. При этом следует отметить тенденцию к дальнейшему росту потребления синтетических К. н. по сравнению с искусственными. Так, если в 1964 доли мирового производства К. н. из синтетических и искусственных волокон составляли соответственно 48 и 52 %, то в 1970 эти показатели достигли 65 и 35%. [c.558]
Медно-аммиачный шелк занимает четвертое место в мировом производстве искусственного волокна. [c.131]
Большое и важное место в мировом производстве искусственного волокна занимают вискозный и ацетатный щелка. Но так как на основные технологические процессы производства этих видов искусственного волокна не используются азотная кислота, аммиак или их соли, мы не будем на них останавливаться. [c.132]
В результате мировой войны 1914 г. и гражданской войны и эта слабо развитая химическая промышленность была почти полностью разрушена. Химическую промышленность в Советском Союзе фактически пришлось создавать заново. В короткие сроки были созданы такие отрасли химической промышленности, как азотно-туковая, анилинокрасочная, пластических материалов, искусственного волокна, лакокрасочная. Впервые в мире были построены заводы по производству синтетического каучука способом, разрабо- [c.9]
В настоящее время производятся искусственные и синтетические волокна различных видов (рис. 127), число которых непрерывно увеличивается. Мировое производство искусственных и синтетических волокон достигает в настоящее время величины около 2 млн. т в год из этого количества около 10% приходится на долю синтетических волокон. [c.419]
Ацетатное волокно занимает в общем мировом производстве искусственных и синтетических волокон второе место после вискозного волокна и вырабатывается главным образом в виде ацетатного шелка. Ацетатное штапельное волокно также представляет собой ценное сырье для текстильной промышленности. Технология ацетатного шелка и штапельного ацетатного волокна одинакова. [c.439]
Диафрагменный метод первоначально получил наибольшее развитие во всех странах, в том числе в СССР. В США до второй мировой войны диафрагменным методом вырабатывалось около 92% электролитического хлора и каустической соды. Усовершенствование технологии ртутного способа, разработка мощных и более экономичных электролизеров, а также возможность получения чистой каустической соды, необходимой для производства искусственного волокна, привели в дальнейшем к преимущественному развитию этого способа. Так, в США в 1967 г. более одной трети каустической соды производилось ртутным способом. В Японии, ФРГ, Франции, Италии ртутным способом вырабатывается от 80 до 95% каустической соды. [c.11]
Искусственные волокна составляют пока еще очень малую долю в мировом производстве волокон.

Лесные богатства нашей страны —неиссякаемый источник сырья для получения природных и синтетических полимеров. Более Vs мировых запасов всей древесины и /з запасов хвойной древесины концентрируется в Советском Союзе. По уровню лесозаготовок СССР занимает первое место в мире, значительно опережая США. Общий объем вывозки леса в нашей стране составил в 1960 г. 247 млн. м , а в 1965 г. он достигнет 372— 378 млн. ж . Однако количество древесины, направляемой на химическую переработку, еще незначительно и не достигает 5% общего объема лесозаготовок. Вместе с тем известно, что при механической обработке древесины используется лишь около одной трети ее массы. Химизация же позволяет почти полностью использовать все отходы лесозаготовок и лесопиления для производства целлюлозы, искусственного волокна, пластических масс, уксусной кислоты, скипидара, ацетона. Химическая переработка одного кубометра древесины на этиловый спирт высвобождает около 700 кг картофеля или 250 кг зерна и дополнительно дает ряд ценных продуктов. [c.24]
Мировое производство искусственного волокна увеличилось за последние 20 лет (1933— 1953) в 6 раз и продолжает расти быстрыми темпами. По масштабам производства искусственные волокна занимают второе место (после хлопка) среди всех видов текстильных волокон. Из 1200 тыс. г годового производства новых химических волокон 94% приходится на долю искусственных и пока еще только 6% на долю синтетических волокон. [c.66]
Мировое производство искусственного и натурального волокна в тысячах тонн (5) [c.66]
Производство нитрошелка прекратилось еще до второй мировой войны, вследствие относительной дороговизны сырья (хлопковая целлюлоза) и химикатов (азотная кислота, спирт, эфир). Поэтому возникновение промышленности искусственного волокна надо отнести к началу XX века, а именно к 1905—1906 годам, когда начал выпускаться вискозный шелк. [c.68]
Около 50% мировой добычи серы используется для производства серной кислоты, около 25% применяется в бумажной промышленности в виде сернистого ангидрида, 10—15% расходуется в сельском хозяйстве и остальные 10—15% применяются в резиновой промышленности, в производстве искусственного волокна и др. [c.8]
В структуре общего мирового производства химических волокон следует обратить внимание па соотношение объемов выпуска нити и штапельного волокна. Доля штапельных волокон все время возрастает и в 1972 г. составила 52,4% против 45% в 1960 г. При этом доля штапельных волокон в производстве искусственных волокон возросла с 46% в 1950 г. до 60% в 1972 г., а в производстве синтетических волокон доля штапельных волокон увеличилась с 20% в 1950 г. до 48% в 1972 г. [c.19]
Промышленное производство волокон из растворов ацетатов целлюлозы началось около пятидесяти лет назад. Благодаря сравнительной простоте и безвредности технологического процесса, а также качественным преимуществам ацетатного волокна (перед некоторыми другими химическими волокнами) производство искусственного волокна этого вида получило широкое развитие в ряде стран. К настоящему времени мировое производство волокон из первичного и вторичного ацетатов целлюлозы достигло 500 тыс. т в год (с учетом волокна для сигаретных фильтров). [c.6]
Ацетатное волокно — общее название искусственных волокон (диацетат-ного и триацетатного), получаемых из ацетатов целлюлозы. Мировое производство на 1971 г. 582 тыс. т, из них штапельного волокна 23 тыс. т, жгута для сигаретных фильтров 159 тыс. т. См. диацетатное волокно и триацетатное волокно. [c.17]
Выпуск ацетатного волокна, составлявший в 1940 г. около 9% мирового производства искусственных волокон, в 1960 г. превысил 250 тыс. т (7,5% от мирового производства), а в 1970 г. в результате резкого увеличения выпуска синтетических волокон снизился до 5%, несмотря на увеличение количества вырабатываемого волокна до 402 тыс. т. [c.20]
Мировое производство медноаммиачного волокна составило в 1927 г. 8 тыс. т, в 1962 г. — 60 тыс. т, а в 1970 г. увеличилось примерно до 80 тыс. т. В настоящее время этот тип гидратцеллюлозного волокна производится только в пяти странах. Основное количество медноаммиачного волокна в виде комплексной нити и штапельного волокна вырабатывается в США, СССР, Японии. Объем производства медноаммиачного волокна значительно уступает производству других типов искусственных и синтетических волокон и составлял в 1970 г. около 1% мирового производства химических волокон и около 2% общего количества вырабатываемых гидратцеллюлозных волокон. [c.436]
Выпуск ацетатного волокна, составляющий в 1941 г. около 9% мирового производства искусственных волокон, в 1962 г. составлял 7,5%. [c.18]
В 1962 г. в общем мировом производстве искусственных волокон на долю филаментной нити приходилось 46,2%, а на долю штапельного волокна — 53,8%. У нас в стране успешно развивается производство как филаментной нити, так и штапельного волокна. [c.31]
Производство искусственного волокна непрерывно развивается. Данные о динамике мирового производства искусственных волокон приведены в табл. 46. [c.160]
Как видно нз табл. 46, мировое производство искусственного волокна за последние 20 лет увеличилось в 18 раз. В 1950 г. количество произведенного искусственного волокна значительно превышало количество полученного натурального шелка, шерсти и лубяных волокон. По масштабам производства искусственные волокна в настоящее время занимают второе место среди всех типов текстильных волокон. [c.160]
В странах с высоким уровнем развития химической промышленности к 70-м годам нашего столетия соотношение между выпуском искусственных и синтетических волокон станет равным 2 1 и даже 1 1. Общее же мировое производство химических волокон к этому времени достигнет 4 миллионов тонн в год. В балансе сырья эти волокна заняли второе место (после хлопка). Однако, несмотря на быстрый рост производства [c.7]
В настоящее время несмотря на исключительно быстрое развитие химии полимеров изучена лишь небольшая часть этих соединений. Но и то немногое, что уже известно о полимерах, позволило создать огромную промышленность синтетических материалов. Уже к концу 50-х гг. мировое производство полимерных материалов значительно превысило выпуск алюминия, меди, цинка, свинца, керамики, кожи, натурального волокна и каучука. На основе синтетических полимерных материалов изготовляют сотни различных видов пластических масс, волокон, синтетических каучуков, клеев, пленок и лакокрасочных материалов. Значение каждого из этих направлений в настоящее время настолько велико, что все они выросли в самостоятельные отрасли производства пластических масс, искусственного волокна, синтетического каучука и лакокрасочных материалов. [c.185]
Целлюлоза и ее производные являются основным видом сырья для бумажной и текстильной промышленности, для производства искусственного волокна, бездымного пороха, кинопленки и частично для получения пластических масс, лаков и др. Мировое потребление целлюлозы в указанных отраслях промышленности в последние годы превышает 20 млн. т в год. [c.649]
Из общего объема мирового производства химических волокон в 1957 г. 45,5% составляли искусственный шелк и кордная нить и 54,5% штапельное волокно. [c.677]
Преимуш,ествами полиамидных волокон являются их высокая прочность, устойчивость к истиранию, действию бактерий (гниение), сохранение прочности во влажном состоянии. Полиамидные волокна широко применяются для изготовления чулок и других трикотажных изделий, тканей, ш,етины, шинного корда, парашютов, рыболовных снастей, искусственной кожи и т. и. Опп труднее загрязняются и легче моются, чем хлопковые волокна. В связи с этими ценными свойствами и доступностью сырья для полиамидов мировое производство наплоиового волокна неуклонно растет. Оно составляло в 1953 г. 77 тыс. т, 1954 г. — 79 тыс. т, 1955 г. — 113 тыс. т, 1956 г. — 114 тыс. т [19] и в 1957 г. превышало 200 тыс. т [10]. [c.670]
В. с. выпускают в виде моноеолокон, текстильных или технич. нитей и штапельного волокна. Прочность В. с. может достигать 1,2 Гн/м (120 кгс/мм ), высокоэластич. деформация составляет от 2 до 1000%, Текстильные и физико-химич. показатели В. с. гораздо разнообразнее, чем у волокон искусственных. Производство В. с. развивается быстрее производства искусственных волокон, что объясняется доступностью исходного сырья, быстрым развитием производства разнообразных полимеров и, особенно, разнообразием свойств и высоким качеством В. с. В 1970 мировое производство В. с. составило ок. 4900 тыс. т, в СССР — ок. 160 тыс. те причем в СССР ок. 80% всех В. с. вырабатывают из полиамидов. В ближайшие годы намечается быстрое развитие в нашей стране производства полиэфирных и полиакрилонитрильных волокон. [c.249]
Установлено, что если для кордной ткани вместо высших сортов хлопкового волокна использовать иокусствен ное или синтетическое волокно, прочность шины повышается на 50 процентов. На изготовление кордной ткани используется от 20 до 45 процентов всего мирового производства искусственного и синтетического волокна. [c.136]
Благодаря высокой реакционной способности и структуре элементарная сера широко применяется в химической промышленности около 50% мирового производства — для получения серной кислоты, 25% —для получения сульфитцеллюлозы. Много серы идет на вулканизацию каучука, производство взрывчатых веществ, спичек, черного пороха, красителей, ультрамарина ( синька ), сероуглерода, искусственного волокна и т. д. Применяется она в сельском хозяйстве для борьбы с вредителями культур, в медицине (серные мази и др.). [c.113]
Применение. Ок. 50% мирового производства С. расходуется для производства серной кислоты, ок. 25% — для получения сульфитцеллюлозы, 10—15% — в с. х-ве. Остальное количество С. потребляется в резиновой пром-сти, в производстве искусственного волокна, взрывчатых веществ, в пром-сти органич. синтеза, в медицине и др. [c.402]
Лигнин следует рассматривать как вещество, склеивающее волокна целлюлозы и придающее им повышенное сопротивление боковым нагрузкам. После осторожного удаления этого клеящего вещества остаются волокна чистой целлюлозы, обладаюнхие высоким сопротивлением растяжению, гибкостью и жесткостью. По свойствам они близки к хлопковым волокнам, которые, как известно, являются природными чисто целлюлозными волокнами. Целлюлозу не изготовляют из хлопка вследствие относительно высокой стоимости этого сырья. Годовой выход чистой целлюлозы с 1 га леса во много раз превышает выход целлюлозы с 1 га посевов хлопчатника например, из еловой древесины получается в пять раз больше целлюлозы. Кроме того, лес может расти в значительно худших климатических условиях, чем хлопчатник. Во всех странах, не имеющих возможности культивировать хлопчатник из-за недостатка земельной площади или из-за отсутствия соответствующих климатических условий, в качестве сырьевой базы для производства искусственного шелка приходится использовать древесную целлюлозу. Поэтому с развитие.м мирового производства искусственного шелка расширилось и производство целлюлозы. Искусственный шелк представляет собой регенерированную целлюлозу, т. е целлюлозу, переведенную [c.327]
Делия из ацетатов целлюлозы обладают хорошими механическими производства ацетатов целлюлозы для получения искусственного волокна, кинопленки, лаков и пластических масс стали возможны благодаря простоте методов производства, невысокой стоимости и доступности уксусной кислоты и уксусного ангидрида, а также возможности их регенерации. В 1971 г. мировое производство ацетатов целлюлозы превысило 600 тыс. т. [c. 314]
Едкий натр, или каустическая сода, называемая сокращенно каустиком, имеет широкое применение в различных отраслях промышленности в производстве мыла, искусственного волокна, бумаги, в промышленности органического синтеза, нефтяной, металлургической и многих других. Наиболее распространен известковый способ получения едкого натра (98% всей мировой продукции NaOH, получаемой химическими методами). Основное сырье для получения каустической соды этим методом — раствор соды и известь. [c.276]
Еще в самый ранний период развития производства искусственного волокна, в 1907 г., А. Пеллерин (Франция) запатентовал способ производства коротких искусственных волокон из целлюлозы однако в то время получение искусственного волокна с удовлетворительными свойствами было вообще трудной задачей, поэтому наибольший интерес проявляли к получению искусственного шелка. В период первой мировой войны в Германии начали переработку вискозного шелка в виде коротких отрезков. Однако удовлетворительных результатов получено не было, так как этот метод в то время еще не был достаточно тщательно разработанi [c.458]
Самые первые промышленные установки для извлечения меди были организованы на германских заводах по производству искусственного волокна медно-аммиачным способом. Большая промышленная установка для той же цели построена в Соединенных Штатах сразу же по окончании второй мировой войны и работает до сих пор. На этой установке нейтрализованные медно-аммиачные промывные воды, содержащие около 25 мг/л меди и несколько тысяч мг1л сульфатов натрия и аммония, пропускаются снизу вверх через цео-карб-продукт сульфирования угля. Таким путем из раствора удаляется вся медь, и после насыщения катионита последний регенерируют путем пропускания [c.308]
Параллельно с производством вискозного волокна в конце XIX в. был разработан способ получения искусственного волокна из медноаммиачных растворов целлюлозы — так называемого медноаммиачного волокна. Этот способ не получил широкого промышленного применения. В 1970 г. объем производства медноам-миачногб волокна составлял всего лишь около 1 % мирового производства искусственных волокон. Сравнительно незначительные масштабы производства медноаммиачного волокна, которое по отдельным показателям превосходит вискозное, в известной степени объясняются несовершенством технологического процесса. [c.19]
До сих пор речь шла о волокнах, получаемых из природных высокомолекулярных -веществ. Примерно к концу 30-х годов началось производство волокон, вырабатываемых из синтетических полимеров. Эти волокна в отличпе от искусственных были названы синтетическими. Особенно бурно промышленность синтетических волокон начинает развиваться в послевоенный период. К концу 1962 г. их удельный вес в мировом производстве химических волокон уже достиг 27,2% и продолжает увеличиваться. [c.15]
Сведений о применении различных сополимеров винилхлорида для получения волокна с повышенной теплостойкостью мало. Еще перед второй мировой войной в США было освоено производство волокна из сополимера, винилхлорида (60%) и акрилонитрила (40%). Волокно, известное под названиями дайнел (США) и канека-лон (Япония), имеет меньшую усадку (при 100 °С около 20%), чем волокно из ПВХ, и широко применяется в смесях с полиакрилонит-рильными и другими волокнами при производстве искусственного меха и объемного трикотажа . Эти волокна представляют большой интерес, но в литературе имеется очень мало сведений об особенностях технологии их производства . [c.186]
Отечественная промышленность химических волокон в 2017 г. и мировые тенденции в создании «умного текстиля»
Сообщение Минпромторга РФ о том, что по итогам 9 месяцев 2017 г. по сравнению с аналогичным периодом предыдущего года индексы производства текстильных изделий составили 107,6% и одежды – 102,5% [1], прозвучало некоторым утешением. Однако, по мнению Торгово-промышленной палаты [2], в 2017 г. легкая промышленность не возродилась, а, наоборот, спрос на отечественную одежду упал, что вынудило оставшихся производителей уйти с рынка. Следовательно, остается по-прежнему рассчитывать на дорогую качественную одежду, либо – на дешевый китайский ширпотреб.
Подобной точки зрения придерживается авторитетный руководитель химической промышленности С.В. Голубков [3], утверждающий, что все тканые материалы – импортные или, в редких случаях, отечественные созданы из привозного сырья, а в стоимости изделия ткань составляет 70–80%, отсюда и «оптимистические» итоги в рублях.
C нашей точки зрения, наблюдаемая ситуация будет, помимо иных, менее важных причин, продолжаться до тех пор, пока рынок не будет обеспечен отечественным волокнистым сырьем, в первую очередь получаемым путем химических превращений. Поэтому от развития производства химических волокон и нитей в стране (уже далеко не новость) зависит состояние потребительского рынка в различных сферах современного хозяйства. Анализу этой ситуации в 2017 г. посвящено настоящее сообщение, содержащее также краткий обзор наиболее интересных мировых новинок в сфере «умных волокон».
Весьма осторожный оптимизм
В указанный период производство химических волокон в России составило 189,7 тыс. т и, по сравнению с предыдущим 2016 г., выросло на 4,8%, в том числе искусственных (вискозных, ацетатных и др.) – на 0,8% и синтетических (полиамидных, полиэфирных, полиакрилонитрильных, полипропиленовых, арамидных, углеродных, полиуретановых и др.) – на 5,3% [4]. При этом доля последних увеличилась на 0,4% в балансе всех химических волокон за 2017 г. и составила 90,3% против 89,9% в 2016 г. Обобщенное представление о сегодняшнем российском рынке химических волокон сконцентрировано в табл. 1, которая составлена на основе данных региональных статистических управлений, направляемых ежегодно в ОАО «НИИТЭХИМ».
Таблица 1. Промышленность химических волокон в России в 2017 г.
Как следует из этой таблицы, по химическим волокнам в исследуемом году выросли все показатели – спрос, потребление, производство, импорт и экспорт – и довольно заметно: соответственно на 6,7, 6,5, 4,8, 9,3 и 8,7% (правда, памятуя о недалеком прошлом, радоваться здесь нечему – эти цифры в четыре-пять раз уступают доперестроечным годам!!!).
Это произошло, главным образом, благодаря синтетическим волокнам, где аналогичные показатели также оказались весьма высокими – соответственно 6,8, 6,5, 5,3, 11,6 и 11,2%. В то же время для искусственных волокон спрос, потребление, импорт и экспорт несколько упали – соответственно на 2,4, 2,2, 2,0 и 6,4%, кроме объемов производства, которые чуть прибавили за счет ацетатного сигаретного жгутика, выпускаемого полностью в ООО «Сартов» (г. Серпухов). Гидратцеллюлозные (вискозные) штапельное волокно и комплексные нити у нас, некогда лидирующей в этой области стране, сплошной импорт (13,5 тыс. т) и вряд ли в ближайшие годы здесь что-то изменится.
Рост спроса и потребления химических волокон в значительной мере обязан увеличению импорта (+9,3%), который оказался на 30% выше собственного производства, а доля его в объеме потребления (около 60%) сохранилась практически на уровне 2016 г. [5]. Решающую роль здесь отводится синтетическим волокнам, где резко вырос не только импорт (+11,6%), но и (что в большей степени отрадно) экспорт (+11,2%). У искусственных волокон наоборот: снизился импорт (-2,0%) и экспорт (-6,4%), тот и другой распространяется в основном на ацетатный сигаретный жгутик, поскольку импортные поставки вискозного штапельного волокна немного поднялись (+0,5%) и достигли в 2017 г. 13,5 тыс. т.
Из указанного в табл. 1 объема потребления около 81% идет в легкую промышленность, 9% – на пищевые продукты и табачные изделия, 6% – в промышленность РТИ и 4% – прочие направления. Внутри легкой промышленности наибольшее потребление химических волокон отмечено в сфере изделий бытового назначения (23%), строительства (21%), автомобилестроения (17%), медицины и гигиены (13%), сельского хозяйства (8%), горнодобывающей промышленности (4%), ВПК и нужд обороны (3%), спорта и туризма (2%), торговли (2%), машиностроения (1%), рыболовства (1%), прочее (5%).
Таким образом, для оценки нынешней ситуации с химическими волокнами в России в первую очередь необходимо проанализировать общий рынок синтетических волокон по отдельным их видам и формированию баланса, исходя из табл. 1. Сразу отметим, что столь подавляющее преимущество по объемам потребления и, особенно, производства синтетических волокон над искусственными, в первую очередь гидратцеллюлозными (вискозными или типа лиоцелл), не вызывает чувства удовлетворения, памятуя о невоспроизводимых природой источников сырья для синтетики и отсутствия ряда важных комфортных для человека свойств у последних. Не случайно в последние годы мировое производство всех видов гидратцеллюлозных волокон непрерывно растет, например в Китае и Индии, где и натуральных, в частности хлопка, в избытке [6].
Итак, возвращаемся к синтетическим волокнам в России в 2017 г. Среди полиамидных (ПА) превалируют комплексные нити из ПА-6 (капрон) текстильного и технического ассортиментов (нити из ПА-66) в небольших объемах закупаются по импорту). Потребление ПА текстильных нитей заметно (на 6,5%) возросло, главным образом за счет увеличения импорта на 27,2% и сокращение экспорта на 22,3%. При этом их производство, преимущественно (более 80%) сосредоточенное в ООО «Курскхимволокно», практически сохранилось на уровне 2016 г.
За счет очевидного падения производства (-8,3%), импорта (-4,8%) и резкого подъема экспорта (на 27,2%) заметно сократился спрос (-7,6%) и особенно потребление (-22,7%) ПА кордных и технических нитей, идущих в значительной степени для изготовления шин и РТИ (45%), а также в горно-добывающую отрасль (35%). Производство упало сразу у двух ведущих предприятий (хотя одно входит в состав другого) – ОАО «КуйбышевАзот» (на 8,8%) и ООО «Курскхимволокно» (на 10%) и суммарно уменьшилось в 2017 г. на 2,2 тыс. т по сравнению с предыдущим годом. Вероятно, одной (а может быть, и главной) из причин этому является отражение общемировой тенденции на российском рынке – постепенное вытеснение ПА нитей полиэфирными (ПЭФ) из традиционных областей их применения – шины, РТИ, бельтинги и т.п. [7].
ПЭФ штапельное волокно и жгут, судя по табл. 2, – самый крупный представитель химволокон в стране и поэтому, наверное, с ним связаны первоочередные задачи развития отрасли.
Таблица 2. Доля полиэфирного штапельного волокна и жгута в балансе всех видов химических волокон (%)
Сегодня около половины спроса, потребления, производства и импорта от всех видов химических волокон и нитей в стране приходится на ПЭФ штапельное волокно и жгут и более половины от объема синтетических волокон и нитей, а внутри других видов синтетического штапельного волокна и жгута их доля выше 90%. И это еще при том, что их производство полностью базируется на переработке отходов бутылок из полиэтилентерефталата (ПЭТ), т.е. из вторичного сырья (рециклинг), что обуславливает ограниченное и далеко не традиционное текстильное использование такого волокна, преимущественно в виде нетканых материалов (НМ) для строительства, сельского хозяйства, автомобиле- и машиностроения. Наиболее крупные производители штапельного волокна из вторичного ПЭТ – ОАО «Комитекс» (г. Сыктывкар), ООО «Селена-Химволокно» (Карачаево-Черкесская Республика) и ООО «Номатекс» (Ульяновская область). Последнее предприятие, например, против 2016 г. увеличило выпуск продукции на 75%. На нужды текстильной и легкой промышленности в основном идет импорт, где преобладает ПЭФ волокно хлопкового типа тонких титров. Непонятно, однако, почему в официальной статистической отчетности, в том числе по Центральному федеральному округу, не фигурирует ООО «Термопол», а лишь – в рекламных изданиях и мероприятиях, где постоянно приписываются уникальные тепло-, физические и химические свойства аморфно-кристаллического ПЭТ собственному материалу «холлофайбер» [8].
Пока еще медленно, но устойчиво возрождается отечественное производство ПЭФ комплексных нитей: текстильных – в ООО «Завидово-Текс» (Тверская область), технических и кордных – в ЗАО «Газпромхимволокно» (г. Волжский). Первое увеличило выпуск в 2017 г. на 2,9%, второе – на 23,8% (и это не предел: до полного освоения проектной мощности осталось еще 4 тыс. т/год). Основной объем потребления ПЭФ текстильных нитей приходится пока на импорт (91%), главным образом из Белоруссии (Светлогорское ПО «Химволокно») и стран Азиатского региона. Отрадно, что спрос на них растет (+13,6%) – пока за счет импорта (+15,5%), который был бы более эффективен с технико-экономической точки зрения (да и социально-политической тоже), будучи максимально ориентирован на Светлогорский завод, в освоение которого вклад российских специалистов достаточно весом, а продукция хорошо известна.
Благодаря отмеченному выше приросту выпуска ПЭФ кордных и технических нитей на предприятии в г. Волжском спрос и потребление их возросло по сравнению с 2016 г. на 7,3% и достигло почти 31 тыс. т (см. табл. 1). При этом импорт вырос немного – на 2,7%. В дальнейшем, до 2020 г. потребление планируется увеличить до 50 тыс. т (на 60%), производство – до 13,0 тыс. т (на 65%) и импорт – на 52%. Основные потребители этой продукции в стране – шины и РТИ (55%) и легкая промышленность (45%). Внутри последней преобладают сферы торговли (37%), горнодобывающей отрасли (21%), изделия бытового назначения, спорт и туризм (21%), машиностроение (9%) и др.
Среди химических волокон полипропиленовые (ПП) наиболее обеспечены исходным сырьем – ПП, мощности которого в России около 1 млн т (потребление его в 2017 г. выросло на 60%, а производство – на 120%), включая практически все волоконные марки гомополимеров и сополимеров с индексом текучести от 10 до 20. Тем не менее, различные виды ПП волокон, судя по табл. 1, развиваются по-разному. Например, в 2017 г. ПП штапельное волокно показало заметный прирост потребления и производства (соответственно на 11 и 6%), а текстильные и технические нити наоборот: у первых потребление и производство упали на 20%, у вторых потребление и импорт – соответственно на 8 и 14%. Последнее трудно объяснить, принимая во внимание растущее значение ПП нитей в мире, упомянутую выше доступность отечественного сырья и то, что ПП текстильные нити, в частности, более чем на 90% используются у нас для товаров бытового назначения. Еще более негативная ситуация сложилась в анализируемый период с ПП пленочными нитями, зарекомендовавшими себя успешно в виде упаковочного и сельскохозяйственного шпагатов, на долю которых приходится более 80% таких нитей. И непонятно, с чем связаны столь значительный спад спроса, потребления и производства этой востребованной продукции (соответственно на 15,2, 19,8 и 20,2%) и рост ее импорта аж на 44%. Какой-то парадокс: имея свободные мощности на прекрасно зарекомендовавших себя комплектных линиях фирмы Oerlikon Barmag (г. Хемниц, Германия), российские заказчики ПП пленочных нитей вынуждены их закупать по импорту(?!).
Полиакрилонитрильные (ПАН) штапельное волокно и жгут в настоящее время, к сожалению, в России не производятся, хотя в СССР работали три крупных завода – в гг. Навои (Узбекистан), Ново-Полоцке (Белоруссия) и Саратове. Последний в рамках ООО «Композит Волокно» сейчас сосредоточен на выпуске небольшого объема ПАН-жгутика в качестве прекурсора для получения углеродных волокон. Потребление ПАН штапельного волокна и жгута полностью реализуется за счет импорта, который вырос на 10% относительно 2016 г. Интерес к этому волокну во многом обусловлен растущим дефицитом натуральной шерсти и поиском ей альтернативы в полушерстяных тканях и трикотаже, куда сегодня уходит 77% ПАН волоконной продукции.
В области малотоннажных волокон в 2017 г. принципиальных изменений не обнаружено: спрос, потребление, производство и импорт сохранились на прежнем уровне, за исключением углеродных, где при умелой организации работ «Гипрохиминжениринг» и Umatex Groop значительно выросли объемы потребления и производства благодаря успешной эксплуатации установки в г. Алабуга (Татарстан).
Рассматривая «Стратегию развития легкой промышленности»
Ну, а что делать дальше, как ответить на «Стратегию развития легкой промышленности в Российской Федерации на период до 2025 г.» [9]? Если всерьез рассматривать эту Стратегию, то, например, предусмотренный там объем российского рынка ПЭФ волокон к 2025 г. должен достичь 1,0–1,1 млн т, гидратцеллюлозных – 80–90 тыс. т. Если говорить о нынешней ситуации в данной области, то фактически у нас нет ни тех, ни других: ПЭФ штапельное волокно делаем из вторичного полимера и тем самым не обеспечиваем требуемое качество, а о гидроцеллюлозном (вискозном) вообще забыли. По первому еще теплится надежда «продлить старость» Ивановскому кластеру, практическая реализация которого на протяжении уже шести лет меркнет с каждым днем и часом, подпитываясь лишь изредка лозунгами и прожектами в печати [1] и на многочисленных форумах и конференциях. Перед глазами стоит пример соседней братской страны: в декабре минувшего года ОАО «Могилевхимволокно» (Белоруссия) подписан контракт с фирмой Oerlikon Neumag (Германия), а в июле текущего года запланирован пуск нового производства ПЭФ штапельного волокна мощностью 50 тыс. т [4]. Без лишних слов и популизма – реально и эффективно. По второму (гидратцеллюлозному-лиоцеллу) планы и обещания ушли в небытие вместе с их главным «оракулом» – НТЦ «Эльбрус».
Тем не менее, актуальность задачи магистрального подъема производства и потребления химических волокон в нашей стране неоспорима и к ее решению должны быть привлечены ведущие предприятия отрасли, подобные ОАО «КуйбышевАзот» (где из года в год наглядно осуществляется ощутимая инновационная политика), и властные структуры, не на словах, а на деле готовые возродить сырьевой потенциал легкой промышленности. Не оставляя радужных перспектив, частично сформулированных в «дорожной карте», ОАО «НИИТЭХИМ» сделало предварительный оценочный прогноз развития химических волокон в России до 2025 г., оптимистично иллюстрируемый рисунком. Из него очевидно, что потребление химволокон в стране будет в первую очередь расти за счет собственного производства, а не импорта. За уровень этих показателей взяты не нижний или верхний предел, а среднеоценочный – исходя из планируемых целей. Цифры указаны на рисунке, комментарии к ним пока излишни, хотя некая уверенность в их достижении при этом сохраняется.
Ориентировочный прогноз развития химических волокон в России
Вышеперечисленными обстоятельствами не исчерпываются все проблемы в отечественной подотрасли химических волокон: простой не только в промышленности, но и в науке. Нет былой активности в теоретических и практических изысканиях в ведущих отраслевых центрах НПО «Химволокно» (ныне ООО «Лирсот», г. Мытищи) и ВНИИСВ (г. Тверь), в вузах и институтах сопутствующих направлений. И вопрос здесь не только в низком качестве выпускаемой продукции, ограниченном ассортименте, отсутствии предложений по модернизации действующих производств, совершенствовании технологии и оборудования вновь проектируемых, а в значительной мере – в отсутствии новых технологических процессов, отвечающих на появление волокон с уникальными свойствами, нахождение прогрессивных сфер их применения и многое другое.
«Умные волокна»: мировые достижения
А в мировом сообществе все более активно проявляют себя «умные волокна» [10, 11], или (названный с легкой руки профессора Г.Е. Кричевского) «умный текстиль». В этом отношении любопытны и поучительны прогнозы специалиста германской фирмы Oerlikon Barmag Р. Дольманса [10], который считает, что в названии «умный текстиль» объединены два совершенно разных слова: первое характеризует высокофункциональные технологии и цифровую электронику, а второе связано с модой, модной одеждой и функциональным текстилем. Перспективы у этих «умных» супер-тканей просто феноменальные. Они, по мнению того же автора [10], могут, в частности, вырабатывать тепло, свет и электричество, измерять температуру и жизненные функции, залечивать раны и уменьшать боль, модернизировать промышленность и делать автомобили и здания более безопасными и комфортными. Эксперты уверены [11], что подобные сценарии станут возможными уже в течение следующих 10–15 лет, а по ряду из них в настоящее время ведутся исследования, и число таких разработок постоянно увеличивается, прежде всего – в Европе, США и странах Азии, где они либо уже успешно реализуются на рынке, либо находятся близко к нему. Neoficialios paskolos internetu su vekseliu iš žmonių automobiliui be užstato, paskolų refinansavimas, SMS greitieji kreditai nuoroda
Прогнозируется огромный рост «умного текстиля» в мировом масштабе: c 544,7 млн долл. в 2015 г. до 9,3 млрд долл. в 2024 г., т.е. почти в 18 раз (а мы пока думаем лишь о наращивании объемов традиционных волокон, да и то с большой доли фантазии)! Движущими силами роста здесь выступают такие сферы применения, как мода и предметы одежды, промышленность и безопасность, медицина и спорт, строительство и архитектура и т. п. Приведем несколько примеров, ибо считаем, что это – путь в будущее химволокон четвертого поколения (по классификации З.А. Роговина: первое – искусственные, второе – синтетические, третье – химически и физически модифицированные) – а следовательно, новые предметы одежды и электронная ткань – и Россия должна быть к нему причастна. Проводящие нити являются основой многих «умных» применений и были созданы (в том числе и российскими учеными во ВНИИВе, ВНИИСВе, Серпуховском ПО «Химволокно» и др.) уже более 30-ти лет назад – например, благодаря электрохимической модификации, поверхностной обработке волокон или с электропроводимым ядром в случае бикомпонентных систем. В частности, нить Elitex (TITV Greiz, Германия), имеющая в своем составе ПА с серебряной оболочкой, перерабатывается без затруднений в таких процессах, как ткачество, вязание или вышивка. Один из самых популярных проектов в сфере текстильной одежды был основан американскими компаниями Google и Levis. В 2016 г. они объявили о выпуске джинсовой куртки «электронными нитями» Elitex, при помощи которой можно осуществлять звонки со смартфона и слушать музыку.
К перспективным направлениям относится святящаяся и нагреваемая одежда. Производитель ее – компания Covesto использует светодиоды, которые размещаются на гибких пленках, сделанных из термопластичного полиуретана, вместо схемных плат. Некоторые зарубежные компании (Warmx, Reusch и др.) успешно продают нагреваемое и устойчивое к стирке нижнее белье, которое вырабатывает тепло от интегрированного ПА волокна с использованием батареи, а также перчатки с подогревом для катания на лыжах (стоимостью всего 270 долл.). Другие перчатки, будучи оснащены сенсором радиочастотной идентификации, обеспечивают автоматическое сканирование строительных компонентов. Появился новый ремень безопасности для автомобиля, изготовленный из полиэфира с проводящими нитями и встроенным микрофоном для гарнитуры голосовой беспроводной связи. Также имеется потенциал для самосветящихся текстильных поверхностей, которые можно использовать в автомобилях или воздушных транспортных средствах для панелей потолочной обивки или сигнальных целей.
В данном случае на многослойные материалы печатается и наносится покрытие с интегрированными светодиодами (очевидно, полимерными), чтобы обеспечить равномерное распределение освещения. «Умный текстиль» также участвует в изготовлении защитной одежды, начиная с комбинезона для младенцев, способного передавать сигналы, до высокотехнологичной защитной куртки для пожарных и сотрудников служб по чрезвычайным ситуациям. Термостойкая, самосветящаяся куртка собирает информацию по жизненным параметрам и движениям ее носителя, по условиям окружающей и рабочей среды и передает ее в центр.
От спорта и здоровья – к медицине. «Умный текстиль» вносит свой вклад в систему удаленного медицинского контроля над пожилыми людьми, пациентами, подверженными риску, проходящими реабилитацию. Для спортсменов созданы специальные футболки, которые измеряют частоту сердечных сокращений, кровяное давление, пульс и дыхание, информируют о возможной опасности спотыкания о ковер, об уровне влаги в белье, шаговую интенсивность при ходьбе. Сенсорная технология, разработанная для этих целей, простирается вплоть до миниатюрных датчиков на волокнах, способных отслеживать состояние хронических ран. Компанией Bomedus осуществляется продажа специальных электронных бандажей для спины, плеч, колен и локтей, вместе с чулками для культи (часть ампутированной ноги или руки). Особенностью данной продукции является стимулирование болевых нервных окончаний, расположенных на поверхности кожи, посредством электродов, вырабатывающих слабые электрические импульсы. Таким образом, внутри самого процесса возникновения болей происходит воздействие на «болевую память», что помогает снизить хронические боли.
Строительные технологии с применением «умного текстиля» – широкое и эффективное поле деятельности для интеллектуальных новаций. В данной области в 2017 г. появилась совместная разработка специалистов из Германии и Южной Кореи в виде переносной подушки безопасности, которая защищает строителей от опасности падения во время работ. В этом устройстве датчик отмечает соответствующие движения и приводит в действие газовый картридж, который в течение миллисекунд заполняет прочную «сумку». В Германии также выпущен в продажу продукт в виде чувствительной к влаге и вырабатывающей тепло ткани, способной предотвращать образования плесени: при достижении критического уровня влаги ленты из данной ткани начинают нагреваться и согревают при этом окружающие стены. Архитекторы и дизайнеры интерьеров также активно используют преимущества «умных волокон». В этом направлении специальные ткани и светодиоды можно использовать, в частности, для изготовления трехмерных, очень крупных световых экранов для проведения презентаций или торгово-промышленных выставок. Технологическую основу для данной продукции создала германская фирма Ettlin, а один немецко-бельгийский проектный консорциум преуспел в сочетании текстильных и святящихся поверхностей. В результате электролюминесцентный рисунок и проводящий слой были напечатаны прямым способом на текстильную подложку, что предопределило применение этой технологии для создания святящихся обоев и мебельных световых инсталляций.
Будущее обещает выработку энергии из волокон.« Умный текстиль» до сих пор имеет один важный недостаток: он потребляет энергию от батарей. Исследователи из Южной Кореи изобрели материал, состоящий из двух слоев: грубая силиконовая решетка и специальная серебряная пленка. Они трутся друг о друга во время движения, обуславливая появление электростатического заряда и вырабатывая тем самым энергию. Тюрингский институт исследования текстиля и пластиков (Германия) концентрирует свою работу на тонких пьезоэлектрических нитях, которые формируют в виде бесконечных филаментов, сердечник которых состоит из наполненного сажей ПП, и они могут в последующем использоваться для вшивания в ткани или вышивания на них. В результате растяжения, давления и вибраций, которые возникают, когда их применяют в качестве сенсоров, вырабатывается электрическое напряжение. Сочетание многочисленных пьезоэлектрических нитей, как утверждают авторы, должно обеспечить богатый «энергетический урожай». Компания Oerlikon Barmag, хорошо известная российским предприятиям как поставщик высококлассного оборудования для производства химических волокон (преимущественно для формования, вытяжки и текстурирования синтетических нитей) и будучи интеллектуально на передовых позициях и в технологии, выступила инициатором проекта по созданию процесса трехмерной печати на классических или новых инновационных тканях, что обеспечит дополнительную привлекательность и продвижение товара.
* * *
Разумеется, все возможности «умных волокон» здесь перечислить невозможно, да и это не является нашей целью в настоящей статье. Мы лишь хотели привлечь внимание к тому, что помимо роста объемов производства и потребления химических волокон в России отечественный рынок ждет от химиков и текстильщиков нового скачка в эксплуатационном потенциале своей продукции. И здесь, прежде всего, надо обратиться к синтетическим волокнам, формирование и модификация свойств которых в большей степени зависит от человеческого разума, а не от даров природы, и тем самым поднять их преимущества на достойную высоту.
Литература
- Комсомольская правда//14–21 декабря 2017 г., с. 15–16.
- Аргументы и факты//№ 1–2, 2018, с. 6.
- С.В. Голубков//Аргументы и факты № 8, февраль 2018, с. 19.
- Вестник химической промышленности № 1(100), январь 2018, с. 30–35.
- Э.М. Айзенштейн, Д.Н. Клепиков//Вестник химической промышленности № 4(97), август 2017 г., с. 18–21.
- Э.М. Айзенштейн//Химические волокна № 1, 2018, с. 73–80.
- Э.М. Айзенштейн//Neftegaz № 4, 2017, с. 49–55.
- Научно-производственное партнерство: взаимодействие науки и текстильных предприятий и новые сферы применения технического текстиля./Сборник докладов, Союзлегпром. – М., 2018, Изд-во «БОС». 484 стр.
- Стратегия развития легкой промышленности в Российской Федерации на период до 2025 г. (проект)//Союзлегпром. – М., 2018, 66 стр.
- R.
Dolmans//Fibers and Filaments, No. 25, October 2017, pg. 10–14.
- K. Yansen//Fibers and Filaments, No. 25, October 2017, pg.15.
История первого производства синтетических тканей в мире
История первого производства синтетических тканей в мире
Для получения синтетических материй применяется сырье разного состава – целлюлозы, стекловолокна, металлов, волокна из нефтепродуктов и т.д.
Синтетические ткани имеют короткую историю по сравнению с натуральными материями, которые производились и использовались людьми еще тысячи лет назад до нашей эры.
Первые мысли о том, как получить нить аналогичную нити шелкопряда, пришла ученому из Франции Реомюру еще в 1734 году. В 1890 году также во Франции в городе Безансоне было открыто производство по переработке нитрата целлюлозы, в результате чего получили первое в мире синтетическое волокно.
С 1891 года технология производства вискозного претерпевает изменения. Благодаря разработкам английских ученых Кросса и Бивана началось промышленное производство вискозного полотна, и уже к 20 веку выпуск расширился до промышленных объемов.
Конец 19 века и вплоть до 40-50 гг. 20 столетия шла разработка и совершенствование способов производства волокон из синтетических материалов из растворов натуральных полимеров. Но следует заметить, что объемы производства данных вида материала были незначительны.
1940-70 годы дали толчок развитию синтеза волокнообразующих полимеров и мономеров, а также началу разработки способов изготовления волокон из расплавов искусственных полимеров. Основное производство этих волокон находилось в странах с развитой промышленностью. В это же время появились так называемые классические искусственные волокна. На этом этапе развития волокна играют роль дополнительных волокон, которые частично заменяют натуральные волокна. Начинается разработка модифицированных волокон.
Следующий этап развития химических волокон с 1970 г. по 1990 г. характеризуется расширением производства волокон данного вида. Модифицированные волокна улучшают свои потребительские свойства. В это же время искусственные волокна становятся самостоятельным видом продукции, их используют во многих сферах промышленности, в том числе и в смесовых материях. Началась разработка волокон из синтетических материалов третьего поколения, отличающихся абсолютно иными свойствами. Новый вид волокнистых материалов отличается сверхпрочностью, сверхмодульностью, термостойкостью, невозгораемостью, устойчивостью к воздействию химических соединений, эластомерностью и т.д.
С 1990 годов и до наших дней продолжается разработка новых технологий производства синтетических волокон. Появились новые методы модифицирования, создаются многотоннажные волокна, так называемые волокна четвертого поколения, в том числе на основе растительного сырья, новейшие полимеры и мономеры, созданные на основе биохимического синтеза. В это же время проходят исследования новых методов производства полимеров, а также волокон на основе процессов биомиметики и генной инженерии.
Все синтетические материи имеют свои преимущества и недостатки, каждая из них предназначена для получения определенных изделий. Но разнообразие материй на основе химических волокон поражает своим разнообразием.
Страница не найдена — Портал Продуктов Группы РСС
Сообщите нам свой адрес электронной почты, чтобы подписаться на рассылку новостного бюллетеня. Предоставление адреса электронной почты является добровольным, но, если Вы этого не сделаете, мы не сможем отправить Вам информационный бюллетень. Администратором Ваших персональных данных является Акционерное Общество PCC Rokita, находящееся в Бжег-Дольном (ул. Сенкевича 4, 56-120 Бжег-Дольный, Польша ). Вы можете связаться с нашим инспектором по защите личных данных по электронной почте: .
Мы обрабатываем Ваши данные для того, чтобы отправить Вам информационный бюллетень — основанием для обработки является реализация нашей законодательно обоснованной заинтересованности или законодательно обоснованная заинтересованность третьей стороны – непосредственный маркетинг наших продуктов / продуктов группы PCC .
Как правило, Ваши данные мы будем обрабатывать до окончания нашего с Вами общения или же до момента, пока Вы не выразите свои возражения, либо если правовые нормы будут обязывать нас продолжать обработку этих данных, либо мы будем сохранять их дольше в случае потенциальных претензий, до истечения срока их хранения, регулируемого законом, в частности Гражданским кодексом.
В любое время Вы имеете право:
- выразить возражение против обработки Ваших данных;
- иметь доступ к Вашим данным и востребовать их копии;
- запросить исправление, ограничение обработки или удаление Ваших данных;
- передать Ваши персональные данные, например другому администратору, за исключением тех случаев, если их обработка регулируется законом и находится в интересах администратора;
- подать жалобу Президенту Управления по защите личных данных.
Получателями Ваших данных могут быть компании, которые поддерживают нас в общении с Вами и помогают нам в ведении веб-сайта, внешние консалтинговые компании (такие как юридические, маркетинговые и бухгалтерские) или внешние специалисты в области IT, включая компанию Группы PCC .
Больше о том, как мы обрабатываем Ваши данные Вы можете узнать из нашего Полиса конфиденциальности.
синтетических волокон | О сырье | Поиск продукта
Синтетические волокна производятся из органических синтетических высокомолекулярных соединений и производятся синтетическим путем из таких сырьевых материалов, как нефтяное масло. Использование этого волокна отдельно или его смешивание с натуральной целлюлозой придает продуктам полезные характеристики волокна.
Полиэфирное волокно (ПЭТ волокно)
Полиэфирное волокно производится в наибольшем количестве среди синтетических волокон и часто используется для изготовления бумаги.Полиэстер — это общий термин для высокомолекулярных соединений со структурой сложноэфирной связи, но в случае волокна относится к полиэтилентерефталату (ПЭТ).
Он отличается высокой прочностью и превосходной термостойкостью и водостойкостью. Мы не только смешиваем это волокно с другим сырьем, но и предлагаем ИСТИННО изготовленное из 100% полиэфирного волокна.
Полиолефиновое волокно (полипропиленовое волокно, полиэтиленовое волокно)
Полиолефиновое волокно изготовлено из высокомолекулярных углеводородов, таких как полипропилен и полиэтилен.Этот материал характеризуется чрезвычайно малым удельным весом ниже 1 (приблизительно 0,90–0,96) и превосходной химической стойкостью к кислотам и щелочам. В частности, среди композитных волокон часто используются волокна с сердцевиной и оболочкой (волокно с сердцевиной оболочки), сердцевина которого сделана из полипропилена, а оболочка — из полиэтилена, и параллельное волокно, состоящее из полипропилена и полиэтилена примерно наполовину. как термоядерное связующее волокно. Мы не только смешиваем это волокно с другим сырьем, но также предлагаем ALT из 100% полиолефинового волокна.
Акриловое волокно
Акриловое волокно — это волокно, изготовленное из полиакрилонитрила, которое отличается термостойкостью, окрашиваемостью, стабильностью размеров и химической стойкостью. Кроме того, помимо акрилового волокна, модакриловое волокно содержит лишь небольшую долю полиакрилонитрила и других сырьевых материалов, обеспечивающих различные функции (огнестойкость, антимикробные свойства и свойство сохранения тепла).
Арамидное волокно
Арамидное волокно — это волокно, молекулярная структура которого состоит из ароматических рядов и амидных связей, и доступно двух типов: пара-арамид и мета-арамид.Это волокно отличается высокой прочностью и модулем упругости, а также превосходной стойкостью к ударам, износу, высоким температурам и химическим воздействиям. Поэтому он часто используется из-за его высокой функциональности, хотя и стоит дорого.
Винилоновое волокно (ПВС)
Винилоновое волокно изготовлено из полицинилового спирта. Это волокно отличается светостойкостью, гидрофильностью и адгезией и используется в различных областях производства бумаги.
Synthetic Fiber — обзор
5.

Адгезионные свойства и долговечность поверхностного покрытия зависят от свойств поверхности и конкретного химического состава на границе раздела между волокном и покрытием. Перед изменением текстильной поверхности полезно знать о смачиваемости, поверхностной энергии и поверхностных загрязнениях, которые часто присутствуют на поверхности текстильных тканей. Многие волокна обладают сродством к воде, особенно те, которые содержат свободный гидроксил (C-OH), амид и амин (O = C-NH, C-NH 2 ), а иногда и кислотные (O = C-OH) группы, такие как хлопок и регенерированная целлюлоза (C-OH), полиамид или нейлон (O = C-NH) и шерсть (C-Nh3, O = C-OH), причем последняя состоит из аминокислот, как и другие волокна животного происхождения.Эти химические группы способны быстро связываться с водородом, процесс, известный как водородная связь, и, следовательно, с молекулами воды. При рассмотрении метода модификации поверхности тканей, содержащих такие волокна, необходимо учитывать водопоглощение, диффузию и абсорбцию через текстильные поверхности. Существует несколько стандартных методов испытаний для оценки влажности / влажности, таких как Американское общество испытаний и материалов (ASTM) D2495–07 «Стандартный метод испытаний на влажность хлопка путем сушки в печи». 28
Как пример важности подготовки ткани, модификация поверхности с использованием такой техники, как плазма низкого давления, выполняется, когда ткань тщательно сушится перед плазменной обработкой. На рис. 5.1 давление измерено, чтобы показать эффект газовыделения, создаваемый рулоном арамидной ткани, установленным в вакуумную камеру, при поддержании постоянного потока N 2 (20 см3 / см3). Эффект дегазации в основном обусловлен высвобождением захваченного воздуха внутри текстильной структуры и десорбированной воды.В показанном примере после 20 минут откачки разница давлений в обеих ситуациях все еще составляет около 20 Па.
5.1. Изменение давления в пилотной линии плазмы низкого давления, без и с тканевым валком, движущимся со скоростью 1 м / мин. Давление измеряется по времени, чтобы показать эффект дегазации.
Текстильные изделия изготовлены из натуральных и / или синтетических волокон, которые содержат на своей поверхности множество различных видов остаточных примесей (размеров). Перед активацией поверхности или модификацией таких текстильных материалов может быть необходимо удалить и очистить эти загрязнения, чтобы добиться успешной модификации поверхности.Процесс удаления и очистки этих загрязнений называется очисткой. Подробный обзор методов очистки был опубликован Tomasino. 29 Очистка используется для удаления натуральных и синтетических масел (включая прядильные, конусные и вязальные масла), жиров, воска, минералов, пыли и грубых материалов. Очистка может быть достигнута с использованием:
- •
экстракции путем растворения примесей в органических растворителях,
- •
эмульсии путем образования стабильных суспензий примесей в воде,
- •
омыления путем преобразования на масляной основе превращается в водорастворимые компоненты.
В настоящее время большинство поверхностей из биотекстиля состоит из тканей, изготовленных из искусственных волокон, таких как полиэстер, нейлон, полипропилен, полиуретан и вискоза, хотя хлопок все еще широко используется. 30 Удаление синтетических масел и смазок, используемых при прядении, ткачестве и вязании этих синтетических волокон, имеет особое значение для обеспечения долговечности и оптимальных характеристик модифицированной текстильной поверхности. Если оставить эти примеси, они могут вызвать слабую адгезию нанесенных покрытий, наносимых для модификации поверхности.Для получения прочных адгезионных покрытий на полимерных волокнах важно, чтобы поверхности волокон были чистыми. Hegemann et al. 31 недавно опубликовали сравнительное исследование плазменной и влажной химической очистки синтетических волокон, иллюстрирующее сложность выбора подходящих методов очистки для удаления производственных размеров. Сложность является результатом оценки различных критериев, таких как эффективность, гибкость, экология и промышленная применимость.
Полиэфирное волокно — сырье для будущего
Полиэфирное волокно История, сырье, производственный процесс, Характеристики, свойства, Смесь , Care, Будущее
Название ткани | Полиэстер | |
Ткань, также известная как | Полиэтилентерефталат, ПЭТ, микроволокно | |
Состав ткани | Полимеры, полученные из ископаемого топлива или органических источников | |
Возможные варианты количества нитей в ткани | 200- 1,000 | |
Воздухопроницаемость ткани | Очень воздухопроницаемость | |
Способность отводить влагу | Высокая | |
Способность удерживать тепло | Средняя | |
Растяжимость (дает) | Средняя | / пузырящийся 901 01Средняя |
Страна, в которой ткань была впервые произведена | США | |
Самая большая страна-экспортер / производитель на сегодняшний день | Китай | |
Рекомендуемые температуры стирки | Холодная, теплая или горячая | |
Обычно используется в | Рубашки, брюки, худи, платья, куртки, нижнее белье, носки, одеяла, шляпы, простыни, веревки, обивка |
Полиэстер (полиэтилентерефталат ПЭТ) представляет собой синтетическое волокно, полученное из угля, воздух, вода и нефть. Это искусственное волокно состоит из очищенной терефталевой кислоты (PTA) и монотелуенгликоля (MEG).
Разработанные в лаборатории 20-го века полиэфирные волокна образуются в результате химической реакции между кислотой и спиртом. В этой реакции две или более молекулы объединяются, образуя большую молекулу, структура которой повторяется по всей ее длине. Полиэфирные волокна могут образовывать очень стабильные и прочные молекулы.
Полиэфирное волокно — это промышленное волокно, в котором волокнообразующее вещество представляет собой любой длинноцепочечный синтетический полимер, состоящий не менее чем из 85% по массе сложного эфира замещенной ароматической карбоновой кислоты, включая, но не ограничиваясь ими, замещенные терефталевые звенья, p ( -RO-CO- C6h5-CO-O-) x и паразамещенные гидроксибензоатные звенья, p (-RO-CO-C6h5-O-) x.
Полиэстер используется в производстве многих товаров, включая одежду, предметы интерьера, промышленные ткани, компьютерные и записывающие ленты, а также электроизоляцию. Полиэстер имеет ряд преимуществ перед традиционными тканями, такими как хлопок. Не впитывает влагу, но впитывает масло; это качество делает полиэстер идеальной тканью для водо-, грязе- и огнестойких покрытий. Его низкая впитывающая способность также делает его естественным устойчивым к пятнам. Одежду из полиэстера можно предварительно усадить в процессе отделки, после чего ткань сопротивляется усадке и не теряет форму.Ткань легко окрашивается и не повреждается плесенью. Текстурированные полиэфирные волокна — эффективный неаллергенный изолятор, поэтому материал используется для набивки подушек, стеганых изделий, верхней одежды и спальных мешков.
История
В 1926 году компания E.I. Компания du Pont de Nemours and Co. начала исследования очень крупных молекул и синтетических волокон. Это раннее исследование, возглавляемое W.H. Карозерс, сосредоточился на том, что стало нейлоном, первым синтетическим волокном. Вскоре после этого, в 1939-41 годах, британские химики-исследователи заинтересовались исследованиями Дюпона и провели свои собственные исследования в лабораториях Calico Printers Association, Ltd. Эта работа привела к созданию полиэфирного волокна, известного в Англии как терилен.
В 1946 году компания du Pont приобрела право на производство этого полиэфирного волокна в Соединенных Штатах. Компания провела дальнейшие разработки и в 1951 году начала продавать волокно под названием Dacron. В последующие годы несколько компаний заинтересовались полиэфирными волокнами и выпустили свои собственные версии продукта для различных целей. Сегодня существует два основных типа полиэфира: ПЭТ (полиэтилентерефталат) и ПХДТ (поли-1,4-циклогексилендиметилентерефталат).ПЭТ, более популярный тип, может найти широкое применение. Он прочнее ПХДТ, хотя ПХДТ более эластичен и эластичен. PCDT подходит для более тяжелых потребительских нужд, таких как драпировки и мебельные покрытия. ПЭТ можно использовать отдельно или в смеси с другими тканями, чтобы сделать одежду устойчивой к складкам и пятнам, а также сохранить свою форму.
Определение полиэфира
Федеральная торговая комиссия определяет полиэфир как «промышленное волокно, в котором волокнообразующее вещество представляет собой любой длинноцепочечный синтетический полимер, состоящий не менее чем из 85 процентов по массе сложного эфира замещенной ароматической карбоновой кислоты. , включая, но не ограничиваясь ими, замещенные терефталевые звенья, p (–R – O – CO – C 6 H 4 –CO – O–) x и паразамещенные гидроксилбензоатные звенья, p (- R – O – CO – C 6 H 4 –O–) x ”(Collier and Tortor, p.179). Полиэстер, наиболее часто используемый для изготовления волокон, — это ПЭТ.
Сырье
Полиэстер — это химический термин, который можно разделить на поли, , означающий многие, и сложный эфир, , основное органическое химическое соединение. Основным ингредиентом, используемым при производстве полиэстера, является этилен, который получают из нефти. В этом процессе этилен является полимером, химическим строительным блоком полиэфира, а химический процесс, в результате которого получается готовый полиэфир, называется полимеризацией.
Производственный процесс
Полиэстер изготавливается одним из нескольких способов. Выбор зависит от формы, которую примет готовый полиэстер. Четыре основные формы:
- Filament,
- Staple,
- Tow и
- Fibrefill.
В форме нити каждая отдельная прядь полиэфирного волокна имеет непрерывную длину, что позволяет получать ткани с гладкой поверхностью. В форме штапеля нити нарезаются на короткие заданные отрезки.В таком виде полиэстер легче смешивать с другими волокнами. Жгут — это форма, при которой непрерывные волокна неплотно стянуты вместе. Fibrefill — это объемная форма, используемая при производстве лоскутных одеял, подушек и верхней одежды. Чаще всего используются две формы: нитевидная и штапельная.
Производство полиэфирной филаментной пряжи (PFY)
Полимеризация
- Для образования полиэфира диметилтерефталат сначала реагирует с этиленгликолем в присутствии катализатора при температуре 302-410 ° F (150- 210 ° С).
- Полученное химическое вещество, мономер (одиночная неповторяющаяся молекула) спирта, объединяют с терефталевой кислотой и нагревают до температуры 472 ° F (280 ° C).
Вновь образованный полиэстер, прозрачный и расплавленный, экструдируется через прорезь, образуя длинные ленты.
Сушка
- После выхода полиэстера после полимеризации длинным расплавленным лентам дают остыть, пока они не станут хрупкими. Материал нарезается на мелкие кусочки и полностью сушится, чтобы предотвратить неровности консистенции.
Прядение из расплава
- Полимерная крошка плавится при 500-518 ° F (260-270 ° C) с образованием сиропообразного раствора. Раствор помещается в металлический контейнер, называемый фильерой, и проталкивается через его крошечные отверстия, которые обычно круглые, но могут иметь пятиугольную или любую другую форму для получения специальных волокон. Количество отверстий в фильере определяет размер пряжи, так как выходящие волокна объединяются в одну прядь.
- На стадии прядения к раствору могут быть добавлены другие химические вещества, чтобы сделать полученный материал огнестойким, антистатическим или более легким для окрашивания.
Вытягивание волокна
- Когда полиэстер выходит из фильеры, он становится мягким и легко удлиняется до пятикратной длины по сравнению с исходной длиной. Растяжение заставляет молекулы неупорядоченного полиэфира выстраиваться в параллельную структуру. Это увеличивает прочность, прочность и упругость волокна. На этот раз, когда волокна высыхают, волокна становятся твердыми и прочными, а не хрупкими.
- Тянутые волокна могут сильно различаться по диаметру и длине в зависимости от желаемых характеристик готового материала.Кроме того, когда волокна вытягиваются, они могут быть текстурированными или скрученными, чтобы создавать более мягкие или тусклые ткани.
Намотка
- После вытягивания полиэфирной пряжи она наматывается на большие бобины или пачки с плоской намоткой, готовые к вплетению в материал.
Производство полиэфирного штапельного волокна (PSF)
При производстве полиэфирного штапельного волокна полимеризация, сушка и прядение из расплава (этапы 1–4 выше) во многом аналогичны производству нитей. Однако в процессе формования из расплава фильера имеет намного больше отверстий, если продукт представляет собой штапельное волокно. Возникающие веревочные пучки полиэстера называются паклей.
Жгут вытяжной
- Вновь сформированный жгут быстро охлаждается в банках, в которых собираются толстые волокна. Собирают несколько кусков жгута, а затем протягивают на нагретых роликах до трех-четырехкратной длины их первоначальной длины.
Обжим
- Вытянутый жгут затем подается в компрессионные коробки, которые заставляют волокна складываться гармошкой со скоростью 9–15 витков на дюйм (3–6 на см).Этот процесс помогает волокну удерживаться вместе на более поздних этапах производства.
Настройка
- После обжима жгута его нагревают до 212–302 ° F (100–150 ° C) для полного высыхания волокон и закрепления обжима. Некоторые изгибы неизбежно будут вытягиваться из волокон во время следующих процессов.
Резка
- После термофиксации паклю разрезают на более короткие отрезки. Полиэстер, который будет смешиваться с хлопком, разрезается на 1 часть.Кусочки по 25-1,50 дюйма (3,2-3,8 см); для смесей искусственного шелка отрезают куски длиной 2 дюйма (5 см). Для более тяжелых тканей, таких как ковер, полиэфирные нити разрезают на отрезки длиной 6 дюймов (15 см).
Характеристики полиэфирного волокна
Прочная
- Устойчивость к растяжению и усадке
- Устойчивость к большинству химикатов
- Быстросохнущая
- Хрустящая и эластичная во влажном или сухом состоянии
- Устойчивость к образованию складок Устойчивость к образованию складок
- Устойчивость к истиранию
- Сохраняет складки и складки после термофиксации
- Легко стирается
- Легкий
- Рыночный спрос
- Низкие эксплуатационные расходы
Свойства полиэфирного волокна
- Длина разреза: Доступны 32, 38, 44, 51 и 64 мм для прядения хлопкового типа и смесь 76, 88 и 102 мм — средняя длина реза 88 м для камвольного прядения.
Наиболее распространенная длина реза — 38 мм.
Для смешивания с другими искусственными волокнами прядильщики предпочитали 51 мм для повышения производительности, поскольку T.M. будет всего от 2,7 до 2,8 по сравнению с 3,4 до 3,5 для 38-миллиметрового волокна. Если длина волокна больше, тенденция к срыву также больше, поэтому компромиссная длина резки составляет 44 мм. С такой длиной обрезки T.M. будет составлять от 2,9 до 3,0, и может быть получена пряжа с меньшим количеством дефектов на 35-40% по сравнению с аналогичной пряжей с волокном 51 мм. В будущем прядильные машины будут стандартизированы для волокна 38 мм, когда скорость кольцевого прядения достигнет 25000 об / мин для синтетической пряжи.
Для оригинального прядения предпочтительно использовать волокно диаметром 32 мм, поскольку оно позволяет использовать ротор меньшего диаметра (38 мм), который может работать со скоростью от 80000 до 100000 об / мин.
В системе пневмомеханического прядения используется волокно диаметром 38 мм.
2. Свойства при растяжении:
Полиэфирные волокна доступны с 4 уровнями прочности.
Волокна с низким содержанием таблеток — обычно с плотностью 2,0 / 3,0 D, подходящей для конечного использования, с плотностью от 3,0 до 3,5 галлонов в сутки (граммов на денье). Эти волокна обычно используются для камвольной системы и 1,4D для вязания
Средняя прочность — 4.От 8 до 5,0 галлонов в сутки
Высокая прочность — диапазон от 6,0 до 6,4 галлонов в сутки и
Сверхвысокая прочность — 7,0 галлонов в сутки и выше
Для конечного использования одежды используются волокна средней и высокой прочности. В настоящее время большинство производителей волокна предлагают только волокна высокой прочности. Спиннеры предпочитают их, поскольку их использование позволяет кольцевым каркасам работать на высоких скоростях, но при этом красящая способность этих волокон на 20-25% хуже, также они имеют более низкий выход при влажной обработке, имеют тенденцию образовывать пилюли и, как правило, дают более жесткое ощущение.
Волокна сверхвысокой прочности используются в основном для прядения швейных ниток из 100% полиэстера и другой промышленной пряжи. Более высокая вязкость достигается за счет использования более высоких степеней вытяжки и более высоких температур отжига до 225–230 ° C и небольшого дополнительного растяжения, составляющего 2% или около того, в последней зоне отжига.
Относительное удлинение обратно пропорционально прочности, например
Упругость —– Удлинение при разрыве —— Значения T10 Низкая таблетка–
3,0–3,5 ——— 45–55% ——————– 1,0–1.5 Средний—
4,8-5,0 ——— 25-30% ——————– 3,5-4,0 Высокий ——-
6,0-6,4 ——— 16-20% ——————– 5,2-5,5 Super Hi—-
7.0 плюс ——— 12-14% ——————– 6.0 плюс ————
T10 или прочность на разрыв при 10% удлинении важны при смешанном прядении и напрямую связаны с смешанной пряжей сила. При прядении 100% полиэфирной пряжи это не имеет значения. Решающий фактор — упорство в перерывах.
3. Свойства обжима:
Обжимы вводятся для придания сцепления волоконной сборке, кроме обжимов / см. Стабильность обжима является более важным критерием, и это значение должно быть выше 80%, чтобы обеспечить бесперебойную работу. Простая проверка стабильности обжима — количество обжимов на дюйм в ленточном волокне финишера. Это значение должно быть в пределах от 10 до 11, если оно ниже, волокно будет давать высокие обороты, приводящие к притиркам и большим разрывам при намотке. Отделка центрифугированием также дает сцепление, но сцепление за счет обжима намного превосходит сцепление, полученное при чистовой обработке. Приведу конкретный пример: у одного производителя волокна возникла серьезная проблема с получением мухи с трехлепестковым волокном, окрашенным в заводских условиях.Волокно Trilobal сложно гофрировать как таковое, поэтому было с большим трудом, что растение могло сделать изгибы на дюйм от 10 до 11. Окрашивание при 130 ° C в красильной машине HTHP снизило cpi до 6-8. 0,8% не помогли. Загрузка карты происходила, но муха была неконтролируемой, в конечном итоге производитель волокна добавил паровой резервуар, чтобы довести две температуры до 100 градусов плюс перед обжимом, а затем смог установить нормальное количество циклов в минуту и хорошую стабильность обжима.
Затем окрашенное волокно хорошо растеклось с нормальным 0.От 15 до 0,18% добавлено окончание отжима.
4. Окончание отжима:
Доступно несколько типов отделки отжимом. Производителей центрифуги немного — Takemoto, Matsumoto, Kao из Японии, Henkel, Schill & Scheilacher, Zimmer & Schwarz и Hoechst из Германии и Джордж А. Гулстон из США. Эффективность финишного отжима может быть установлена только на заводских испытаниях.
Предполагается, что финишная отделка обеспечивает высокое трение между волокнами от 0,4 до 0.45, чтобы контролировать движение волокна, особенно по кромке, низкое трение между волокном и металлом от 0,2 до 0,15, чтобы обеспечить более низкое натяжение при прядении кольца и обеспечить адекватную статическую защиту при любой скорости работы текстильной машины, а также обеспечить достаточную когезию для контроля разлета и притирки. тенденции и смазка для обеспечения более плавного черчения.
Покрытие центрифугированием обычно состоит из двух компонентов: один обеспечивает смазку / сцепление, а другой обеспечивает защиту от статического электричества. Каждый из этих компонентов содержит до 18 различных компонентов, которые придают желаемые свойства, а также обладают противогрибковыми, антибактериальными антивспенивающими свойствами и стабилизаторами.
Большинство производителей волокна предлагают 2 уровня отделки отжимом. Отделка более низкого уровня для смесей хлопка и 100% полиэстера и отделка более высокого уровня для смесей вискозы. Причина в том, что вискоза имеет тенденцию лишать полиэстер отделки. Однако на большинстве фабрик даже более низкое центрифугирование лучше подходит для низких уровней производства, а если уровень производства высокий, требуется окончательное центрифугирование при высоком уровне производства, если оно смешано с вискозой.
Для оригинального прядения, где частота вращения ротора составляет примерно от 55000 до 60000 об / мин, стандартная отделка отжима подходит, но если на фабрике установлены новые прядильные машины оригинального производства с вращающимися роторами при 80000 об / мин, тогда совершенно другая отделка прядения со значительно меньшим содержанием волокна — волокно. и трение между волокном и металлом дало очень хорошие результаты.Необходимость чистки роторов была увеличена с 8 часов до 24 часов, а количество перерывов уменьшилось до 1/3.
В заключение необходимо отметить, что, хотя степень отделки волокна при отжиме находится только в диапазоне от 0,105 до 0,160, она определяет судьбу волокна, так как его способность к работе с волокном контролируется чистовой обработкой прядения, поэтому самый важный компонент волокна
Эффективность отделки прядением непросто измерить на фабрике по производству волокна. Dupont использует инструмент для измерения статического поведения и измеряет Log R, который дает хорошее представление о статическом покрытии.Также есть японский прибор Honest Staticmeter, в котором пучок хорошо подготовленных волокон вращается с высокой скоростью в статическом поле в 10000 вольт. Прибор измеряет заряд, полученный образцом волокна, когда заряд достигает максимального значения, это регистрируется, и машина выключается. Затем отмечают время, необходимое для утечки заряда до половины своего максимального значения. Как правило, с этим прибором для нормальной работы волокна максимальный заряд должен составлять около 2000 вольт, а время затухания периода полураспада — менее 40 секунд.Если используется максимальный заряд 5000 и время спада полураспада 3 мин, будет сложно кардочесать волокно, особенно на высокопроизводительной карте.
5. Сухая термоусадка:
Обычно измеряется при 180 ° C в течение 30 мин. Значения колеблются от 5 до 8%. При DHS около 5% реализация готовой ткани будет составлять около 97% подаваемой серой ткани, а при DHS около 8% это значение снижается до 95%. Следовательно, имеет коммерческий смысл удерживать DHS около 5%.
Цвет L и B
Цвет L для большинства волокон записывает значения от 88 до 92.Цвет «b» — это мера желтизны / голубизны. Цвет b для полутусклого волокна колеблется от 1 до 2,8 у разных производителей волокна. Чем ниже значение, тем меньше химическая деструкция полимера. Волокна с оптической яркостью дают значения цвета b от 3 до 3,5. Это с 180 ppm оптического отбеливателя.
Прием красителя
Каждый производитель волокна имеет пределы от 100 + — 3 до 100 + -8. Даже при предельном содержании красителя 100 + -3 в трикотажных тканях все же появляются полосы. Единственное средство — смешать тюки разных дней в партии и настоять на том, чтобы прядильные фабрики брали тюки с нескольких грузовиков.
Сплавленные волокна
Правильный способ измерения — это кардочесать 10 кг волокна. Соберите все плоские полоски (95% сросшихся волокон собираются в плоские полоски). Разложите его на темном плюше, возьмите расплавленные и невытянутые волокна и взвесьте их. Верхний допустимый предел составляет 30 мг / 10 кг. Идеальный предел должен составлять около 15 мг / 10 кг. DUpont называет слитые / невытянутые волокна DDD или Deep Dyeing Defect.
Полиэстер Lustre — Полиэфирные волокна доступны в цветах
Bright: 0. От 05 до 0,10% TiO2
Полупрозрачный: от 0,2 до 0,3% TiO2
Тусклый: 0,5% TiO2
Очень тусклый: 0,7% TiO2 и оптически осветленный обычно 180 ppm OB, OB доступен в красноватых, зеленоватых и голубоватых тонах оттенки. Самый популярный глянец — полутусклый, за ним следуют OB (100% в США) и яркий.
Смесь полиэстера
Полиэфирная пряжа доступна не только в 100% -ном размере, но и в другой мягкой ткани в соответствии с требованиями к конечному продукту.Смеси следующие:
Полиэстер — Хлопок
Полиэстер — Акрил
Полиэстер — Шерсть — Вискоза
Полиэстер — Модал
Полиэстер — Шерсть — Акрил
Черный Полиэстер — Вискоза
AA Полиэстер — Хлопок
— Лайкра
Полиэстер — Шерсть — Хлопок
Уход за полиэстером
Полиэстер часто смешивают с другими волокнами, которые требуют различных процедур по уходу.По этой причине процедуры по уходу могут отличаться в зависимости от ткани.
Для тканей из 100% полиэстера перед стиркой следует удалить масляные пятна. Как правило, их можно стирать в стиральной машине в теплой или холодной воде в щадящем режиме. Их можно сушить в сушильной машине на низком уровне мощности, и их следует вынуть из сушилки, как только цикл будет завершен. Одежду следует сразу же повесить на вешалку или сложить. При таком обращении ткани из 100-процентного полиэстера редко нуждаются в глажке.Если требуется подкраска, ее следует проводить на изнаночной стороне ткани при умеренной температуре.
Для некоторых вещей, сделанных из полиэстера или его смесей, может потребоваться химчистка. Сшитую на заказ одежду из нескольких компонентов, например костюмы, может потребоваться химчистка. Важно соблюдать инструкции по уходу и не думать, что химчистка лучше стирки. Пигментные отпечатки на полиэстере не следует подвергать химической чистке, поскольку растворитель растворяет клей, удерживающий пигмент на поверхности ткани.
Будущее
После появления в США в 1951 году полиэстер быстро стал самым быстрорастущим волокном в стране. Простота ухода за тканью для перманентного прессования сделала двойные трикотажные изделия из полиэстера чрезвычайно популярными в конце 1960-х годов. Мужские костюмы для отдыха из полиэстера и женские брючные костюмы двойной вязки из полиэстера были популярны среди людей среднего и пожилого возраста. Студенты же колледжа ненавидели полиэстер. В 1970-х они даже называли это проклятием «П».Они считали это дешевым и уж точно не «с этим».
Однако с тех пор у полиэстера возникли «проблемы с имиджем», и одежду из полиэстера часто обесценивали и даже высмеивали.
Чтобы бороться с этим имиджем, Tennessee Eastman Company запустила кампанию «полиэстер», чтобы возродить свой имидж. Ассоциация производителей искусственного волокна, которая превратилась в Ассоциацию производителей искусственного волокна — Совет моды из полиэстера, начала свою собственную кампанию. Обе группы сосредоточились на простоте ухода за полиэстером, а не на его дешевизне.В 1984 году Ассоциация производителей искусственного волокна и Совет модельеров одобрили коллекции, сделанные почти исключительно из полиэстера или их смесей. Участвовали такие известные дизайнеры, как Оскар де ла Рента, Перри Эллис, Кельвин Кляйн и Мэри Макфадден. Такая огласка немного помогла.
Вероятно, более важным фактором улучшения имиджа полиэстера стали технологические достижения производителей. Несколько новых форм полиэстера, представленные в начале 1990-х годов, могут помочь оживить имидж полиэстера.Новая форма полиэфирного волокна, называемая микроволокном, была представлена публике в 1991 году. Высокотехнологичные волокна из полиэстера произвели революцию на рынке спортивной одежды для активного отдыха. Ткани из микроволокна, более роскошные и универсальные, чем традиционные полиэфирные, трудно отличить от шелковых. Переработанный полиэтилентерефталат из бутылок из-под газировки превращается в удобный флис, что делает его привлекательным для тех, кто заботится об окружающей среде.
Полиэстер можно назвать тофу из промышленных волокон, поскольку его внешний вид принимает разные формы.В зависимости от фактического производственного процесса полиэстер может напоминать шелк, хлопок, лен или шерсть. При смешивании с другими волокнами полиэстер приобретает еще больше форм, сочетая в себе хорошие качества каждого из волокон. Полиэстер также является наиболее часто используемым промышленным волокном. По оценкам компании DuPont, 17,7 миллионов метрических тонн, потребленных во всем мире в 1995 году, вырастут почти до 40 миллионов метрических тонн к 2005 году.
Полиэфиры — это полимеры, образованные из дикарбоновой кислоты и диола.У них много применений, в зависимости от того, как они были произведены, и в результате ориентации полимерных цепей.
Полиэстер используется в любой форме одежды:
Полиэстер используется для всех видов одежды, как отдельно, так и в смесях. Он присутствует в любом типе одежды, от домашней одежды до вечерней одежды. Некоторые распространенные смеси включают полиэстер и хлопок для рубашек и полиэстера, а также шерсть для костюмов. Полиэстер обеспечивает легкость ухода за обеими этими смесями, а хлопок и шерсть обеспечивают комфорт. Еще одно применение полиэфирного волокна можно найти в некоторых предметах одежды. Лыжная куртка с полыми полиэфирными волокнами между внешней тканью и подкладкой обеспечивает тепло без утяжеления.
Мебель для дома:
В домашней обстановке, такой как ковры, шторы, драпировки, простыни и наволочки, настенные покрытия и обивка, а также постельные принадлежности. Простыни и наволочки из смесей полиэстера и хлопка не нужно гладить, но они не так удобны, как изделия из 100-процентного хлопка.Ковры из 100-процентного полиэстера дешевле нейлона, более склонны к износу и позволяют значительно накапливать статическое электричество в сухие зимние месяцы.
Другое использование:
Другое использование может включать промышленные изделия. Низкая впитывающая способность и высокая прочность полиэстера даже во влажном состоянии делают его идеальным для изготовления зонтов, палаток и спальных мешков. Некоторые промышленные применения полиэстера обладают теми же характеристиками. Следовательно, полиэстер используется для изготовления шлангов, приводных ремней, веревок и сетей, ниток, шинного корда, автомобильной обивки, парусов, подкладок для гибких дисков и волоконного наполнителя для различных продуктов, включая подушки и мебель.Для вышивания ниток используется полиэстер, но нить из 100-процентного полиэстера имеет тенденцию нагреваться и образовывать узлы при быстром шитье. Полиэфирная нить, покрытая хлопком, решает эту проблему.
Дизайнеры одежды, такие как Мэри Макфадден, создали линию одежды с использованием этой новой формы полиэстера. Исследователи текстиля из Университета штата Северная Каролина разрабатывают форму полиэстера, которая может быть такой же прочной, как кевлар, суперволоконный материал, используемый для изготовления пуленепробиваемых жилетов. Этот тип полиэстера со временем может быть использован в качестве композитных материалов для автомобилей и самолетов.
——————————————————————————————————
Статья г-жи Хетал Мистри
Ссылка :
https://books. google.co.in/books?id=a6GjAgAAQBAJ&pg=PA8&lpg=PA8&dq=Polyester+Fibre:+From+Its+Invention+to+Its+Present+Position&source=bl&otsRBZBZ&source=bl&ots=061gziql2source&source=bl&ots=061gzfql&source=bl&ots=061gq1 = en & sa = X & ved = 2ahUKEwj3q63u5LDqAhUoxzgGHWCIDZ4Q6AEwD3oECAgQAQ # v = onepage & q = Polyester% 20Fibre% 3A% 20From% 20Its% 20Invention% 20to% 20Its% 20Present% 20Present% 20Present% 20Positiongoogle.co.in/books?id=GA2kAgAAQBAJ&pg=PA225&lpg=PA225&dq=Polyester+Fibre:+From+Its+Invention+to+Its+Present+Position&source=bl&ots=dA4fnz40su&sig=ACfU3U1kmYCfVGy72qEwZAIGiJ3EnAif0A&hl=en&sa=X&ved=2ahUKEwj3q63u5LDqAhUoxzgGHWCIDZ4Q6AEwDnoECAcQAQ#v=onepage&q = Полиэстер% 20Fibre% 3A% 20From% 20Its% 20Invention% 20to% 20Its% 20Present% 20Position & f = false
http://www.madehow.com/Volume-2/Polyester.html
https://fdocuments.in / документ / полиэфирное волокно от своего изобретения до настоящего положения.html
https://textilelearner.blogspot.com/2011/07/polyester-fibre-characteristics-of_11. html
https://www.fibre2fashion.com/yarns/SearchResult.aspx?Pid=2198&P=Polyester+ Смеси и тип = Поставщики
https://www.encyclopedia.com/sports-and-everyday-life/fashion-and-clothing/textiles-and-weaving/polyester#:~:text=Polyester%20is%20a%20synthetic% 20фибра, структура% 20повторов% 20всё% 20% 20длина.
https://barnhardtcotton.net/blog/know-fibres-difference-between-polyester-and-cotton/
https: // sewport.com / fabrics-directory / polyester-fabric
http://textilefashionstudy.com/polyester-physical-and-chemical-properties-of-polyester/
https://www.textileadvisor.com/search?q=polyester + волокно + свойства
Профиль автора
- Миллионеры
Текстильное сырье
2 Натуральные волокна
Натуральные волокна делятся на три основных класса в зависимости от природы источника (происхождения), т.е. е. растительные волокна, волокна животного происхождения и минеральные волокна, как показано на рис. 2. Натуральные волокна, такие как конопля, кенаф, джут, сизаль, банан, лен, масличная пальма и т. Д., Пользовались значительным спросом в последние годы из-за их экологической и возобновляемой природы. Кроме того, натуральные волокна имеют низкую плотность, лучшие механические и термические свойства и биоразлагаемы.
Рис. 2
Классификация натуральных волокон.
Растительные волокна включают наиболее важное из всех текстильных волокон «хлопок» вместе с льняными, конопляными, джутовыми, сизалевыми и другими волокнами, которые производятся растениями.Они основаны на целлюлозе, материале, который природа использовала в качестве конструкционного материала в растительном мире. Их можно собирать с разных частей растений, и поэтому их можно классифицировать на основе источника их сбора с растения. Волокна животного происхождения включают шерсть и другие подобные волосам волокна, а также волокна, такие как шелк, производимые шелкопрядами. Эти животные волокна основаны на белке, сложном материале, из которого состоит большая часть тела животных. Минеральные волокна имеют меньшее значение в текстильной торговле. Асбест — самое полезное волокно этого класса.Выдающимся свойством асбестового волокна является его устойчивость к нагреванию и горению. Они также обладают высокой устойчивостью к кислотам, щелочам и другим химическим веществам. Из этих волокон делают специальные огнестойкие и промышленные ткани.
2.1 Хлопковые волокна
Хлопок — это мягкое штапельное волокно, которое растет в защитной капсуле, известной как коробочка, вокруг семян хлопчатника. Из волокна прядут пряжу, из которой делают мягкий, дышащий текстиль, который является наиболее широко используемым видом текстиля для одежды.Самые ранние свидетельства использования хлопка получены из Индии, и этой ткани присвоена дата — 3000 г. до н.э.. Были также раскопки хлопчатобумажных тканей сопоставимого возраста в Южной Америке. Выращивание хлопка сначала распространилось из Индии в Египет, Китай и южную часть Тихого океана. Несмотря на то, что хлопковое волокно было известно уже в Южной Америке, крупномасштабное выращивание хлопка в Северной Америке началось в 16 — веках с прибытием колонистов в южные части сегодняшних Соединенных Штатов. Наибольший рост производства хлопка связан с изобретением Эли Уитни в 1793 году хлопкоочистителя с зубчатым колесом. Благодаря этой новой технологии стало возможным производить больше хлопкового волокна, что привело к большим изменениям в прядильной и ткацкой промышленности.
Сбор хлопка вручную по-прежнему практичен почти во всех странах. Обычная практика ручного сбора хлопка — это собрать семена хлопка и коробочку и положить их в мешок. Опытный взрослый может набрать 300 фунтов. семян хлопка в сутки при нормальных условиях.В случае автоматического подбора используются два типа подборщиков, а именно съемник и подборщик шпинделя. Сбор вручную предпочтительнее машинного, так как волокна отбираются только из полностью созревших капсул. После сбора хлопок отправляется на хлопкоочистительную фабрику, где волокна отделяются от семян. Взбиватели, используемые для джина, могут быть либо пильными, либо роликовыми. Пила более экономична за счет усовершенствованной автоматизации и механизации. Отделенные семена используются для экстракции масла для пищевых продуктов или для производства мыла / свечей.Фунт хлопка-сырца можно получить из 50–100 коробочек в зависимости от природы растения и условий, в которых оно выращивается.
Хлопок классифицируется по тонкости, длине волокна, зрелости, степени загрязнения и прочности. Тонкость волокна обозначается в дтекс, то есть в граммах на 1000 метров. Тонкость хлопкового волокна чаще всего выражается в микронейрах, т.е. е. количество микрограмм на дюйм. Длина штапельного волокна определяет тонкость пряжи.Чем длиннее хлопковое волокно, тем тоньше получается пряжа. Незрелый и непрочный хлопок имеет мутный вид, тогда как зрелый хлопок выглядит ярким и имеет толстую клеточную стенку. Эти параметры описывают, что волокна должны быть достаточно гибкими, чтобы выдерживать непрерывную перегруппировку при прядении; имеют высокое отношение длины к диаметру, обеспечивают эффективное уплотнение и межволоконную когерентность.
Под световым микроскопом хлопковые волокна распознаются по наличию просвета и извилин, т. е.е. скручивает по длине волокна. Еще одна уникальная особенность хлопковых волокон — это разворот спиральной (фибриллярной) структуры или спирали по длине волокна. Важные характеристики хлопкового волокна приведены в таблице 1.
Таблица 1
Свойства хлопкового волокна.
Параметр | Значение | |
---|---|---|
Тонкость | 1–4 дтекс / 2,3–6,9 мкм | |
Длина волокна | 10–60 мм | |
Плотность 1 | Плотность | .5–1,54 г / см 3 |
Восстановление влаги | 8,5% | |
Предел прочности на разрыв | 25–50 сН / текс | |
Удлинение | 5–10% | |
Цвет | Кремово-желтый |
Хлопковое волокно желтеет при температуре выше 110 ° C. Его нелегко повредить солнечный свет; постепенная потеря прочности происходит при более длительном пребывании на солнце. Являясь целлюлозным по своей природе, он растворяется в концентрированном растворе кислот, но обладает отличной устойчивостью к щелочам.Сильный щелочной раствор вызывает набухание волокон. Грибки и бактерии атакуют хлопок и портят его. Он служит пищей для грибка. Он содержит минеральные вещества (соли Na, K, Mg и Ca) и крахмал, которые способствуют росту грибка и плесени. Плесень растет при высокой относительной влажности. Бактерии и грибки выделяют ферменты, которые атакуют целлюлозу и превращают ее в сахар. Для защиты хлопок обрабатывают материалами, которые либо подавляют рост, либо убивают эти микроорганизмы.
Смешивание — это процесс смешивания различных волокон в одну пряжу, как правило, для повышения прочности пряжи и придания ей желаемых свойств.Хлопок легко смешивается с другими волокнами; в основном из полиэстера и вискозы. Его прочность и впитывающая способность делают его идеальной тканью для изделий медицинского назначения и личной гигиены, таких как бинты и тампоны. Он имеет низкую теплопроводность и поэтому является идеальным материалом как для летней, так и для зимней одежды. Летом предохраняет кожу от жара, а зимой сохраняет тепло тела. Хлопок часто используется при производстве штор, палаток и брезентовых покрытий. Он также широко используется для изготовления одежды, включая блузки, рубашки, платья, детскую одежду, одежду для активного отдыха, купальники, костюмы, куртки, юбки, брюки, свитера, чулочно-носочные изделия и галстуки.Модные предметы домашнего обихода из хлопка — это шторы, драпировки, покрывала, простыни, полотенца, скатерти, скатерти и салфетки. Некоторые из промышленных применений этого волокна включают веревки, сумки, обувь, конвейерные ленты, фильтровальную ткань, медицинские принадлежности и т. Д.
2.2 Лен
Лен, вероятно, является самым старым текстильным волокном, известным человечеству. Волокно получают из стебля растения Linum usitatissimum высотой 80–120 см. Ткань из льна еще называют полотном. Первое хорошо задокументированное применение льняной ткани было египтянами для обертывания своих мумий. Его также находили в могилах в Египте, датируемых 5000 годом до нашей эры. Но еще задолго до этого лен использовался в различных целях. На раскопках жилищ каменного века в Швейцарии, датируемых примерно 7000 г. до н.э., были обнаружены семена льна, шпагаты и рыболовные сети. Считается, что льняное растение пришло в Европу вместе с первыми фермерами, а в каменном веке люди обычно носили льняную одежду [2].В Нидерландах выращивание льна предположительно непрерывно существовало с 2500 г. до н. Э.
В настоящее время выращивают два типа льна: для волокон и семян (масла). Льняное волокно оптимизировано для производства тонких прочных волокон, в то время как семя льна дает гораздо больше льняного семени и более грубых волокон. Скрещивание этих двух крайних типов привело к выращиванию маслобойного льна, называемого комбинированным льном. Лен растет в умеренном климате и в настоящее время возделывается на большей части территории Западной и Восточной Европы, Канады, США и России. Лен-долгунец растет во влажных, умеренных областях, а масличный лен — в сухих, теплых областях. Характеристики льна различаются в зависимости от условий посева и выращивания; влияет на длину стебля, толщину и количество ветвлений.
Сбор урожая льна осуществляется путем выдергивания стебля вручную или механическим съемником. Иногда растения срезают близко к земле, но предпочтительнее тянуть, чтобы сохранить самую длинную длину волокон. Затем пучкам льняных стеблей дают высохнуть.Рябь — это следующий процесс, в результате которого со стебля удаляются цветочные головки и листья. Далее растения раскладывают по земле для вымачивания. Это процесс, при котором слой пектина, удерживающий пучки волокон вместе в стебле, разрушается под действием бактерий и влаги.
Типы вымачивания, обычно применяемые для льна, — это вымачивание водой, ферментное вымачивание и вымачивание росой. При вымачивании водой пучки стеблей льна погружают в проточную воду (реки) или стоячую воду (пруды или специально подготовленные ямы). Анаэробные бактерии вызывают брожение, разлагая пектин и другие связующие вещества. Ферментное вымачивание использует теплую воду и ферменты для разложения пектина. Этот метод был разработан для производства очень тонких волокон. Это контролируемый, но довольно трудоемкий процесс. При мокке росой стебли льна раскладывают по полю. Влажность окружающей среды вызывает рост местных аэробных грибов, которые частично разрушают стебель. Это недорогой процесс, который занимает от трех до семи недель в зависимости от погодных условий.
Пучки льна сушат, и к этому моменту волокна должны отделиться от стебля. Шток ломается, пропуская жгуты между рифлеными роликами. Затем сломанные части стержня удаляются из пучков волокон в процессе трепания. Трепальная машина состоит из двух взаимопроникающих роликов, оснащенных тремя и более ножами. Ножи соскребают по волокну, чтобы удалить деревянный стержень. Пучки трепанных волокон все еще относительно крупные, толстые и ленточные.После трепания волокна расчесываются (процесс взбивания), в результате чего получается более тонкое волокно с круговой структурой волокон. Элементарное волокно содержит около 65–75% целлюлозы, 15% гемицеллюлозы и 10–15% пектина, а также 2–5% восков. Остальные свойства льноволокна приведены в таблице 2.
Таблица 2
Свойства льноволокна.
Параметр | Значение | ||
---|---|---|---|
Тонкость помола | 10–40 дтекс | ||
Диаметр | 10–80 мкм | ||
Длина волокна | 200–4000 Плотность1 | 1.43–1,52 г / см 3 | |
Восстановление влаги | 12% | ||
Предел прочности на разрыв | 30–55 сН / текс | ||
Удлинение | 2–3% |

2.3 Джут
Джут известен как «золотое волокно» из-за его золотисто-коричневого цвета и его важности. Джут относится к категории лубяных волокон и обычно прядется в виде грубых нитей. В отличие от большинства растительных волокон, которые состоят в основном из целлюлозы, джутовые волокна состоят частично из целлюлозы и частично из лигнина. Джутовое волокно отличается прочностью, низкой стоимостью, высокой прочностью и универсальностью. Это дешевое натуральное волокно, имеющее множество конечных целей, например, для изготовления мешков из гессиана, садового шпагата, веревок и ковров.Он наиболее популярен в сельском хозяйстве для борьбы с эрозией почвы, защиты семян и борьбы с сорняками. Он используется для технических применений в области геотекстиля. Джут заменяется синтетическими материалами для многих из этих применений, но биоразложение и устойчивость являются основными преимуществами джута по сравнению с синтетическими волокнами.
Джутовое растение становится готовым к уборке через 120 дней, и его либо вытаскивают вручную, либо режут за острый край. Затем эти стебли связывают в пучки для вымачивания.Процесс вымачивания включает погружение стебля в воду до тех пор, пока действие бактерий не позволит высвободить волокна внутри стебля. Для завершения вымокания требуется около 12–25 дней. Зачистка означает удаление волокон джута со стебля. Самый распространенный метод — это ручная зачистка, выполняемая осторожным ударом по коре деревянным молотком, начиная с основания стебля. Затем волокна отделяются и сушатся. Свойства джутового волокна приведены в таблице 3.
Таблица 3
Свойства джутового волокна.
Параметр | Значение | |||||||||||||||||||||||||||||||||||||||
---|---|---|---|---|---|---|---|---|---|---|---|---|---|---|---|---|---|---|---|---|---|---|---|---|---|---|---|---|---|---|---|---|---|---|---|---|---|---|---|---|
Тонкость | 2–3 дтекс | |||||||||||||||||||||||||||||||||||||||
Диаметр | 15–25 мкм | |||||||||||||||||||||||||||||||||||||||
Длина волокна | 650–71050 мм | 9010 9010–750 мм Плотность1,44 г / см 3 | ||||||||||||||||||||||||||||||||||||||
Восстановление влажности | 13,75% | |||||||||||||||||||||||||||||||||||||||
Предел прочности на разрыв | 30–34 сН / текс | |||||||||||||||||||||||||||||||||||||||
Удлинение | 2–8.![]() Масличная пальма — самая урожайная масличная культура в мире. Ствол, вайя и пустая плодовая гроздь (EFB) масличной пальмы могут использоваться для экстракции лигноцеллюлозных волокон. EFB может давать до 73% волокон, поэтому он предпочтительнее с точки зрения доступности и стоимости. Волокно сизаля получают из листьев растения сизаль. Обычно его получают путем машинной декортикации, при которой лист раздавливается между валками, а затем механически соскабливается.Затем волокно промывают и сушат механическими или естественными способами. Высушенное волокно составляет всего 4% от общего веса листа. Банан не только дает вкусные плоды, но и дает клетчатку для текстильных изделий. Волокно получается после сбора плодов. Небольшие кусочки ствола бананового растения подвергаются процессу размягчения для механического извлечения волокон с последующим отбеливанием и сушкой. Полученное волокно имеет внешний вид, похожий на шелк, который стал популярным в качестве пряжи из бананового шелкового волокна. В недавнем прошлом банановое волокно находило очень ограниченное применение для изготовления таких предметов, как веревки, циновки и некоторые композитные материалы. Стебель растения конопли дает два типа волокон: длинные (лубяные) волокна и короткие (сердцевинные) волокна. Лубяные волокна можно чистить, прядать, а затем ткать или вязать во многие ткани, подходящие для изготовления прочной и удобной одежды и домашней утвари. Ткани с содержанием конопли не менее 50% более эффективно блокируют солнечные лучи, чем другие ткани.По сравнению с хлопком волокна конопли более длинные, прочные, блестящие, впитывающие и более устойчивые к плесени. Текстиль из конопли чрезвычайно универсален — он используется в производстве одежды, обуви, одежды, холста, ковров и обивки. Рами — одно из старейших растительных волокон; использовался для изготовления салфеток для мумие в Египте в течение 5000–3000 лет до нашей эры. Он относится к категории лубяных волокон и требует химической обработки для удаления смол и пектина, обнаруженных в коре. Таблица 4Свойства других растительных волокон.
2.5 Шерсть Шерсть — это волокно животного происхождения, получаемое путем стрижки волокнистого покрова овец и производимое почти во всех частях мира. Овец обычно стригут для получения шерсти один или два раза в год, а полученная необработанная шерсть известна как шерсть. Эффективная стрижка удалит шерсть с овцы за 2 минуты. Шерсть также удаляется из шкур забитых овец с помощью химической обработки или бактериального воздействия, не повреждая шкуру. Порода овец, а также условия окружающей среды сильно влияют на качество шерсти. Шерсть также различается по тонкости, длине и чистоте в зависимости от части тела овцы, от которой она взята. Шерсть можно широко разделить на тонкую шерсть, среднюю шерсть, длинную шерсть и ковровую шерсть. Из шерсти обычно производят пряжу двух типов: i. е. шерстяные и камвольные. Шерстяная пряжа обычно изготавливается из коротких штапельных волокон, которые свободно удерживаются и слегка перекручиваются во время прядения.Камвольная пряжа намного тоньше, ровнее, плотно скручена и более гладкая, чем шерстяная. Обычно они производятся из более длинных штапельных волокон. Шерстяное волокно имеет естественную извитость благодаря своей уникальной химической и физической структуре. Это заставляет волокно изгибаться и поворачиваться, придавая шерсти естественную трехмерную извитость [5]. 2.6 Шелк Шелк — это белковое волокно насекомого происхождения, получаемое в виде тонких волокон большой длины из телесной жидкости тутового шелкопряда (Bombyx Mori) .Тутовые шелкопряды питаются только листьями тутового дерева. Шелк — это полипептид, состоящий из четырех разных аминокислот. Шелковые волокна относительно жесткие и демонстрируют хорошее или отличное восстановление после деформации в зависимости от условий температуры и влажности. Четыре стадии жизненного цикла тутового шелкопряда — это яйцо, гусеница, личинка (кокон) и бабочка.Гусеницы выходят из яиц после вылупления в течение 12 дней. В период роста гусеницы пищей ей служат свежие листья шелковицы. Через 35 дней гусеницы готовы к прядению шелка. Они перестают есть и через несколько дней образуют кокон. Шелкопряд делает свой кокон из двойной нити, которая выходит из двух шелковых желез в его голове. Эти нити покрыты и склеены липким веществом, называемым серицином. Червь постепенно покрывается и улавливается сильно структурированным коконом, состоящим из непрерывной шелковой нити (может достигать мили в длину).Эта шелковая нить раскручивается от коконов. Свойства шелкового волокна приведены в таблице 5. Таблица 5Свойства шелкового волокна. Параметр | Значение | | |||||||||||||||||||||||||||||||||||||
Тонкость | 1–3,5 дтекс | |||||||||||||||||||||||||||||||||||||||
Диаметр | 10–13 мкм | |||||||||||||||||||||||||||||||||||||||
Длина волокна1 | 700–1500 Density | 1,37 г / см 3 | ||||||||||||||||||||||||||||||||||||||
Восстановление влаги | 9–11% | |||||||||||||||||||||||||||||||||||||||
Предел прочности на разрыв | 25–50 сН / текс | |||||||||||||||||||||||||||||||||||||||
Удлинение | 10–25% | |||||||||||||||||||||||||||||||||||||||
Цвет | Блестящий белый |
Фиброин шелка разлагается концентрированными кислотами на составляющие аминокислоты.Шелк более устойчив к щелочам и органическим растворителям, за исключением растворителей, разрушающих водородные связи. Постоянное воздействие солнечных лучей на шелковое волокно приводит к потере прочности. Он начинает желтеть при высоких температурах и распадается при температуре выше 165 ° C. Поглощение влаги приводит к временной потере прочности шелкового волокна на 10–25%. Легко поражается молью и плесенью.
5 Синтетические волокна
Синтетические волокна являются результатом обширных исследований, направленных на улучшение свойств природных волокон животного и растительного происхождения.Эти синтетические волокна получают экструзией полимерного материала синтетического происхождения через фильеру в воздух или воду. Эти волокнообразующие полимеры обычно получают из нефтехимии. Поэтому эти волокна называют синтетическими.
5.1 Нейлон
Нейлон 6.6 был первым синтетическим волокном, произведенным в 1935 году в США. Параллельная разработка в Германии привела к производству непрерывной нити (нейлон 6) в 1939 году [7]. Нейлоновые волокна состоят из линейных макромолекул, структурные единицы которых связаны амидной (–NH – CO–) группой. Поэтому эти волокна называют полиамидами. Наиболее распространенный способ производства нейлоновых полимеров — конденсация диаминов с двухосновными кислотами. В нейлоне 6 молекулы направлены со всеми амидными связями в определенном направлении, например. г. –NH – CO–, в то время как в нейлоне 6.6 существует обратный порядок альтернативных амидных связей.
Нейлон 6
–NH – Ch3 – Ch3 – Ch3 – Ch3 – Ch3 – CO–
Нейлон 6.6
–NH – CH 2 –CH 2 –CH 2 –CH 2 –CH 2 –CH 2 –NH –OC– CH 2 –CH 2 –CH 2 –CH 2 –CH 2 –CO–
нейлоновые волокна производятся путем экструзии расплавленного полимера без использования растворителей.Полимерная крошка плавится с помощью нагретой решетки или с помощью экструдера, в котором шнек проталкивает стружку по нагретой трубе. Расплавленный полимер подается в регулируемый дозирующий насос, который помогает контролировать линейную плотность волокна. Расплав полимера подают в фильеру при температуре 280–300 o C и давлении до 50–70 МПа. Мундштук представляет собой пластину из нержавеющей стали толщиной 5 мм и более, имеющую ряд небольших отверстий (диаметром 100–400 мкм). Количество отверстий соответствует количеству нитей, необходимых в конечной пряжи.Полимер, выходящий из отверстий фильеры, вытягивается приемной бобиной и испытывает значительное ускорение. Ускоренные нити затвердевают на холодном воздухе. Свойства нейлонового волокна приведены в Таблице 7.
Таблица 7
Свойства нейлонового волокна.
Параметр | Нейлон 6,6 | Нейлон 6 |
---|---|---|
Точка плавления | 255–260 ° C | 215–220 ° C |
Точка размягчения | 235 ° C ° C | |
Модуль упругости | 20–35 сН / текс | 15–35 сН / текс |
Разрывная нагрузка | 40–60 сН / текс | 40–60 сН / текс |
Удлинение | 20–30% | 20–40% |
При температуре 21 ° C с R. H. 65%, нейлон 6.6 или 6 содержит 3,5–4,5% воды по массе в пересчете на массу сухого волокна. Воздействие на нейлон 6.6 и 6 воздуха при температуре выше 100 ° C приводит к потере прочности и удлинения при разрыве. Воздействие солнечного света и других источников УФ-излучения также приводит к ухудшению свойств нейлона. Вода при температуре кипения медленно воздействует на нейлон. Нейлон 6.6 инертен к раствору щелочи, но чувствителен к кислотам. Нейлон 6 и 6.6 инертны по отношению к большинству обычных органических растворителей, но они растворяются в концентрированной муравьиной кислоте и фенолах.
5.2 Полиэстер
Полиэтилентерефталат (ПЭТ), также называемый полиэфирным волокном, доминирует в мировой индустрии синтетических волокон. Они недороги, легко производятся из нефтехимических источников и обладают желаемым диапазоном физических свойств. Они прочные, легкие, устойчивые к складкам и хорошо стираются. Полиэфир, полученный конденсационной полимеризацией дикарбоновой кислоты с диолом, содержит внутрицепочечные сложноэфирные звенья в качестве важнейших звеньев цепи, образующих полимер [8].
Спирт (R – OH) + карбоновая кислота (R – COOH) → сложный эфир
, где R представляет собой алкильную группу.
Нить из полиэфирного волокна получают путем формования из расплава в различных условиях. Полимер плавят при температуре на 15–25 ° C выше его температуры плавления в шнековом экструдере. Расплав полимера точно дозируется шестеренчатым насосом прямого вытеснения, который подает фиксированное количество расплава полимера за один оборот. Расплавленный полимер проталкивается через крошечные отверстия (0.180–0,400 мм) в плите фильеры. Полимер затвердевает, когда выходит из фильеры. Процесс охлаждения ускоряется контролируемым потоком воздуха. Полимер также вытягивается, т.е. е. растянут в полурасплавленном состоянии, чтобы вызвать молекулярный порядок и ориентацию в волокне. Свойства полиэфира приведены в таблице 8.
Таблица 8
Свойства полиэфирного волокна.
5.3 Другие синтетические волокна
Наиболее распространенными среди других синтетических волокон являются полиолефины, акрилы и эластан. Олефиновое волокно — это промышленное волокно. В этих волокнах волокнообразующее вещество представляет собой любой длинноцепочечный синтетический полимер, состоящий по меньшей мере из 85% по массе этилена, пропилена или других олефиновых мономеров. Олефиновые волокна — это общее описание, которое охватывает термопластические волокна, полученные из олефинов.Полипропилен (PP) и полиэтилен (PE) — два наиболее распространенных члена этого семейства. Полипропилен дает наибольший объем волокна для данного веса из-за его низкого удельного веса, то есть 0,90–0,91 г / см 3 . Полипропилен не проявляет статических свойств в нормальных условиях. Как и другие синтетические волокна i. е. нейлон, акрил и полиэстер — полипропиленовые волокна не подвержены воздействию бактерий и микроорганизмов; они также устойчивы к моли и гниению и по своей природе устойчивы к росту плесени и плесени.Полипропилен гидрофобен и не впитывает воду из волокна. Сравнение свойств приведено в таблице 9.
Таблица 9
Свойства синтетических волокон.
Параметр | Полиэтилен | Полипропилен | Эластан |
---|---|---|---|
Длина волокна | 38–200 мм | 38–200 мм | — | текс | 15–60 сН / текс | 4–12 сН / текс |
Удлинение | 10–45% | 15–200% | 400–800% |
Плотность | 0.95–0,96 г / см 3 | 0,9 г / см 3 | 1,1–1,3 г / см 3 |
Модуль | 15–30 сН / текс | 13–15 сН / текс | 0,05–0,1 сН / текс |
Точка плавления | 125–135 ° C | 160–175 ° C | 230 ° C |
5,4 Стекловолокно
Стекло — неметаллическое волокно , широко используемый в наши дни в качестве промышленного материала. Обычно состояние стекла определяется как замороженное состояние переохлажденной и, следовательно, затвердевшей жидкости.Основное сырье для стекловолокна включает множество природных минералов и промышленных химикатов. Основными ингредиентами являются кварцевый песок, известняк и кальцинированная сода. В качестве стеклообразователя используется кварцевый песок, а кальцинированная сода и известняк помогают снизить температуру плавления. Низкий коэффициент теплового расширения в сочетании с низкой теплопроводностью делают стекловолокно стабильным по размерам материалом, который быстро рассеивает тепло по сравнению с асбестом и органическими волокнами.
Они производятся путем прямого плавления, включающего процессы дозирования, плавления, формования, нанесения покрытия, сушки и упаковки.Дозирование — это начальный этап производства стекла, на этом этапе количество материалов тщательно перемешивается. Затем смесь отправляют в печь при высокой температуре 1400 ° C для плавления. Эта температура достаточно высока, чтобы превратить песок и другие ингредиенты в расплавленное состояние. Затем расплавленное стекло поступает в рафинер, где его температура снижается до 1370 ° C. Прядение стекловолокна включает сочетание экструзии и вытяжки. Во время этого процесса расплавленное стекло выходит через втулку с очень мелкими отверстиями.Пластины втулки нагреваются электронным способом, а их температура регулируется для поддержания постоянной вязкости. Водяные форсунки используются для охлаждения волокон на выходе из проходного изолятора примерно при 1204 ° C.
Затухание — это процесс механического вытягивания экструдированных потоков расплавленного стекла в волокна диаметром от 4 мкм до 34 мкм. Высокоскоростная намоточная машина используется для обеспечения натяжения и втягивания расплавленной струи в тонкие волокна. На заключительном этапе на волокна наносится химическое покрытие из смазочных материалов, связующих и / или связующих веществ.Смазка поможет защитить нити от истирания при сборе и намотке в пакеты. Пакеты, еще влажные после водяного охлаждения и калибровки, затем сушат в печи. После этого волокна готовы к дальнейшей переработке в рубленое волокно, ровинг или пряжу.
Это неорганический материал, который не горит и не поддерживает горение, сохраняя примерно 25% своей первоначальной прочности при 540 ° C. Большинство химикатов практически не влияют на стекловолокно. Неорганические стеклотекстильные волокна не образуют плесени и не портятся.Стекловолокно подвержено действию фтористоводородной, горячей фосфорной кислоты и сильных щелочных веществ. Это отличный материал для электроизоляции. Сочетание таких свойств, как низкое влагопоглощение, высокая прочность, термостойкость и низкая диэлектрическая проницаемость, делает стеклоткани идеальными для армирования печатных плат и изоляционных лаков.
Высокое соотношение прочности и веса стекловолокна делает его превосходным материалом в тех областях, где требуются высокая прочность и минимальный вес.В текстильной форме эта прочность может быть однонаправленной или двунаправленной, что обеспечивает гибкость конструкции и стоимости. Он широко используется на автомобильном рынке, в гражданском строительстве, спортивных товарах, в авиации и космонавтике, на лодках и кораблях, в электронике, в быту и в ветроэнергетике. Они также используются в производстве конструкционных композитов, печатных плат и широкого спектра изделий специального назначения.
5.5 Углеродное волокно
Углеродное волокно представляет собой длинную тонкую нить диаметром около 5–10 мкм, состоящую в основном из атомов углерода.Атомы углерода связаны вместе в микроскопические кристаллы, которые более или менее выровнены параллельно оси волокна. Такое выравнивание кристаллов делает волокно невероятно прочным. Несколько тысяч углеродных волокон соединяются в пряжу. Углеродные волокна были разработаны в 1950-х годах путем нагревания нитей вискозы до карбонизации. Этот процесс был неэффективным, поскольку полученные волокна содержали только около 20% углерода и имели низкие характеристики прочности и жесткости. В начале 1960-х годов был разработан процесс с использованием PAN в качестве сырья. В результате получилось углеродное волокно, которое содержало около 55% углерода и имело гораздо лучшие свойства.
В 1970-х годах экспериментальные работы по поиску альтернативного сырья привели к внедрению углеродных волокон, изготовленных из нефтяного пека, полученного при переработке нефти. Эти волокна содержат около 85% углерода и обладают отличной прочностью на изгиб. Но они имели ограниченную прочность на сжатие и не получили широкого распространения. Около 90% производимых углеродных волокон производится из ПАН. Остальные 10% сделаны из искусственного шелка или нефтяного пека.Все эти материалы представляют собой органические полимеры, характеризующиеся длинными цепочками молекул, связанных вместе атомами углерода. Типичный процесс, используемый для формирования углеродных волокон из PAN, включает прядение, стабилизацию, карбонизацию, обработку поверхности и калибровку.
В процессе формования порошок акрилонитрила смешивается с другим материалом, таким как метилакрилат или метилметакрилат, и реагирует с катализатором в суспензии с образованием ПАН-пластика. Затем он либо превращается в волокна посредством коагуляции, либо нагревается и закачивается через крошечные форсунки в камеру, где растворители испаряются, образуя твердое волокно.Затем волокна промывают и растягивают до желаемого диаметра волокна. Эти волокна стабилизируют путем нагревания в присутствии воздуха примерно до 200–300 ° C в течение 30–120 минут. Волокна поглощают кислород из воздуха и изменяют структуру атомных связей, что приводит к термически стабильной лестничной связи.
Стабилизированные волокна нагревают до температуры 1000–3000 ° C в течение нескольких минут в печи, заполненной газовой смесью, отличной от кислорода. Недостаток кислорода предотвращает горение волокон при очень высокой температуре.Нагретые волокна теряют свои неуглеродные атомы в виде различных газов, таких как водяной пар, аммиак, окись углерода, двуокись углерода, водород, азот и другие. Остальные атомы углерода образуют прочно связанные кристаллы углерода, расположенные параллельно длинной оси волокна. Обработка поверхности этих волокон выполняется для улучшения свойств сцепления волокон. В процессе проклейки волокна покрываются, чтобы защитить их от повреждений при намотке или ткачестве. Типичные материалы покрытия включают эпоксидную смолу, полиэстер, нейлон, уретан и другие.Волокна с покрытием наматываются на цилиндры, называемые бобинами.
Углеродные волокна являются важной частью многих продуктов, и каждый год появляются новые области применения. Композитные материалы, армированные углеродным волокном, используются в автомобильной и авиакосмической промышленности, в спорте и во многих других компонентах, где необходимы легкий вес и высокая прочность. Углеродные волокна обладают высокой электропроводностью (объемным сопротивлением) и в то же время обладают отличными свойствами экранирования электромагнитных помех. Это успешно применяет углепластик (пластик, армированный углеродным волокном) в области защиты от электромагнитных помех.Углеродные волокна имеют низкий коэффициент теплового расширения и высокую стабильность размеров, а также сохраняют свои механические характеристики даже в области высоких температур. Углепластик превосходит пластик, армированный сталью или стекловолокном (GFRP), по своей удельной прочности на разрыв и удельному модулю упругости (удельной жесткости). Углеродное волокно по устойчивости к усталости превосходит другие конструкционные материалы.
Сырье, используемое в текстильной промышленности — видео и стенограмма урока
Хлопок
Хлопок , член семейства гибискусов, является важным растительным сырьем для текстильных изделий.Другие включают джут, коноплю и сизаль. Хлопок поступает из семян внутри плода, покрытого похожей на шелуху емкостью, называемой коробкой . Когда хлопок созреет, коробочка открывается, обнажая внутри мягкие пушистые белые волокна.
Затем собирают коробочки и отделяют волокна. Многие сырые волокна затем прессуются в большие тюки (они могут весить до 500 фунтов!), Которые затем отправляются на хлопчатобумажные фабрики и открываются. Затем волокна дополнительно обрабатываются и прядут в пряжу, которая затем используется для хлопка и текстильных смесей из хлопка.
Шерсть
Шерсть производится овец. Сегодня многие овцы разводятся специально для того, чтобы получить как можно больше пригодной для использования шерсти. Раз в год с овец стригут шерсть, которую удаляют с помощью инструмента, похожего на большую электрическую бритву. Это не повредит им, и их шерсть отрастет в следующем сезоне. Лучшая шерсть идет с плеча овцы, а затем с бока.
Стриженная шерсть калибруется, сортируется и затем очищается от грязи и жира.Потом из него можно будет сплести нитки для текстиля. Новая шерсть, из которой раньше никогда не делались текстильные изделия, называется натуральной шерстью. Большинство текстильных изделий из шерсти на самом деле представляют собой смесь натуральной шерсти и шерстяных волокон, переработанных из старых шерстяных тканей.
Шелк
Шелк получают от насекомых, в частности гусениц, называемых тутового шелкопряда. На крупных шелковых фабриках большое количество яиц тутового шелкопряда раскладывают на подносах. Когда черви появляются, они съедают листья тутового дерева, пока не будут готовы плести шелковые коконы.Когда коконы готовы, их собирают и нагревают, чтобы уничтожить существо внутри. Затем коконы замачивают в горячей воде и разматывают. Затем длинные тонкие шелковые нити промывают водой с мылом, чтобы удалить липкие остатки, созданные червями. Затем они наматываются на катушки и вплетаются в пряжу.
Нейлон
Нейлон не создан природой. Все начинается с химикатов, состоящих из таких веществ, как уголь и нефть. Химические вещества смешиваются в лаборатории, образуя клейкое вещество, которое затем продавливается через сопло с небольшими отверстиями, называемыми прядильными отверстиями .С другой стороны, материал растягивается, образуя нити. Их сушат, а затем используют для текстильных изделий и других вещей. Синтетику также можно производить из таких сырьевых материалов, как масло, резина и даже стекло и цемент.
Итак, теперь вы знаете больше о нескольких видах сырья, используемом в текстильном производстве. Посмотрите на этикетку на своей одежде. Вы можете сказать, из чего он сделан?
Резюме урока
Для обзора, сырье или вещества, еще не превращенные в нити, используются в текстильной промышленности.Из них изготовлены и сотканы ткани или материалы, изготовленные из волокон или нитей, которые сотканы вместе. Некоторые виды сырья поступают из природных источников, а другие — синтетические, или искусственно созданные в лаборатории. Штапельные волокна — короткие, обычно натуральные волокна, которые поступают из таких источников, как шерсть и хлопок. Филаментные волокна представляют собой длинные тонкие нити бесконечной длины, например шелк или нейлон.
Хлопок , важный природный материал, получают из зрелых плодов хлопчатника. Шерсть также натуральная, овечья. Шелк — это натуральное волокно, которое происходит из кокона тутовых шелкопрядов. Нейлон является синтетическим и начинается с химикатов в лаборатории.
искусственного волокна | Britannica
искусственное волокно , волокно, химический состав, структура и свойства которого значительно изменяются в процессе производства. Искусственные волокна прядут и ткут в огромное количество потребительских и промышленных товаров, включая одежду, такую как рубашки, шарфы и чулочно-носочные изделия; предметы домашнего обихода, такие как обивка, ковры и шторы; и промышленные детали, такие как шинный корд, огнестойкие накладки и приводные ремни.Химические соединения, из которых производятся искусственные волокна, известны как полимеры, класс соединений, характеризующихся длинными цепочечными молекулами большого размера и молекулярной массы. Многие полимеры, из которых состоят искусственные волокна, аналогичны или аналогичны соединениям, из которых состоят пластмассы, каучуки, клеи и поверхностные покрытия. Действительно, полимеры, такие как регенерированная целлюлоза, поликапролактам и полиэтилентерефталат, которые стали привычными для домашнего использования под торговыми наименованиями вискоза, нейлон и дакрон (торговая марка), соответственно, также превращаются в многочисленные изделия из нетканых материалов, от окон для целлофановых конвертов до оконных коробок. прозрачные пластиковые бутылки для безалкогольных напитков.Как волокна, эти материалы ценятся за их прочность, ударную вязкость, устойчивость к нагреванию и плесени, а также способность удерживать прессованную форму.
Искусственные волокна следует отличать от натуральных волокон, таких как шелк, хлопок и шерсть. Натуральные волокна также состоят из полимеров (в данном случае из соединений, полученных биологическим путем, таких как целлюлоза и белок), но они появляются в процессе производства текстиля в относительно неизменном состоянии. Некоторые искусственные волокна также получают из природных полимеров.Например, вискоза и ацетат, два из первых когда-либо произведенных искусственных волокон, сделаны из тех же целлюлозных полимеров, из которых состоит хлопок, конопля, лен и структурные волокна древесины. Однако в случае вискозы и ацетата целлюлоза приобретается в радикально измененном состоянии (обычно в результате операций с древесной массой) и далее модифицируется, чтобы регенерировать в практичные волокна на основе целлюлозы. Таким образом, вискоза и ацетат относятся к группе искусственных волокон, известных как регенерированные волокна.
Британская викторина
Строительные блоки повседневных предметов
Из чего сделаны сигары? К какому материалу относится стекло? Посмотрите, из чего вы на самом деле сделаны, проанализировав вопросы в этой викторине.
Другая группа искусственных волокон (и гораздо большая группа) — это синтетические волокна.Синтетические волокна изготавливаются из полимеров, которые не встречаются в природе, а вместо этого производятся полностью на химическом заводе или в лаборатории, почти всегда из побочных продуктов нефти или природного газа. Эти полимеры включают нейлон и полиэтилентерефталат, упомянутые выше, но они также включают многие другие соединения, такие как акрилы, полиуретаны и полипропилен. Синтетические волокна могут производиться серийно практически с любым набором требуемых свойств. Ежегодно производятся миллионы тонн.
В этой статье рассматривается состав, структура и свойства искусственных волокон, как регенерированных, так и синтетических, а затем описываются способы их прядения, вытягивания и текстурирования в полезные волокна.Для полного понимания материала, из которого сделаны эти волокна, читателю рекомендуется начать со статьи «Промышленные полимеры, химия».
Процесс производства синтетического волокна — Textile Apex
Система производства синтетического волокна При производстве любого синтетического волокна три основных этапы процесса необходимы для производства готового продукта —а. Промежуточные химические соединения полимеризуются;
б. Нити прядут из полимеров; и
c.Необработанные волокна обрабатываются для подготовки их для использования в текстильной промышленности.Система производства синтетического волокна |

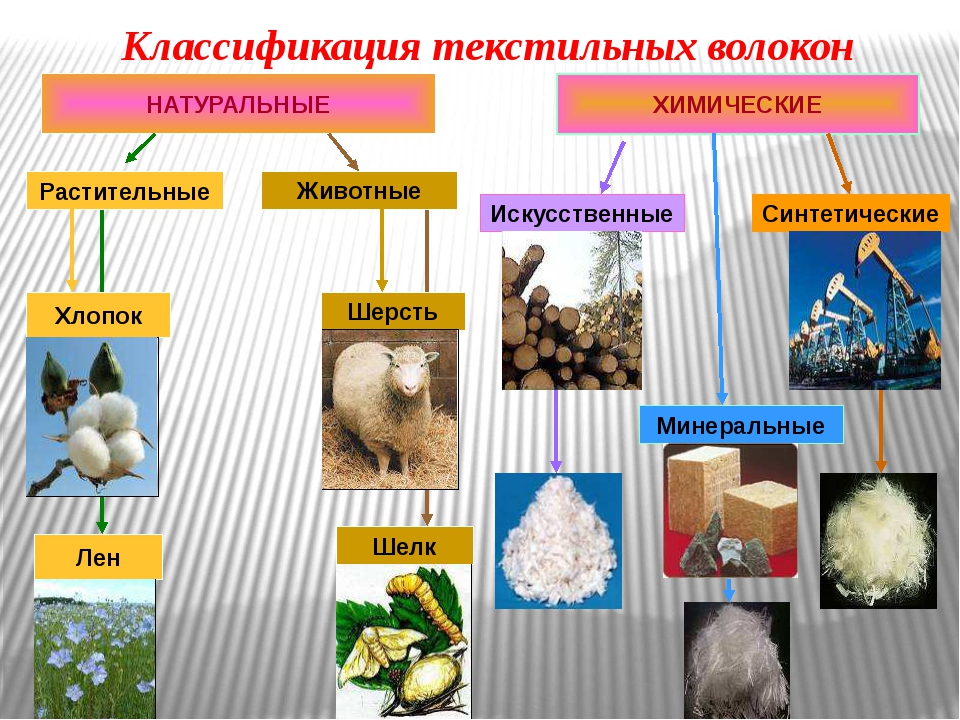
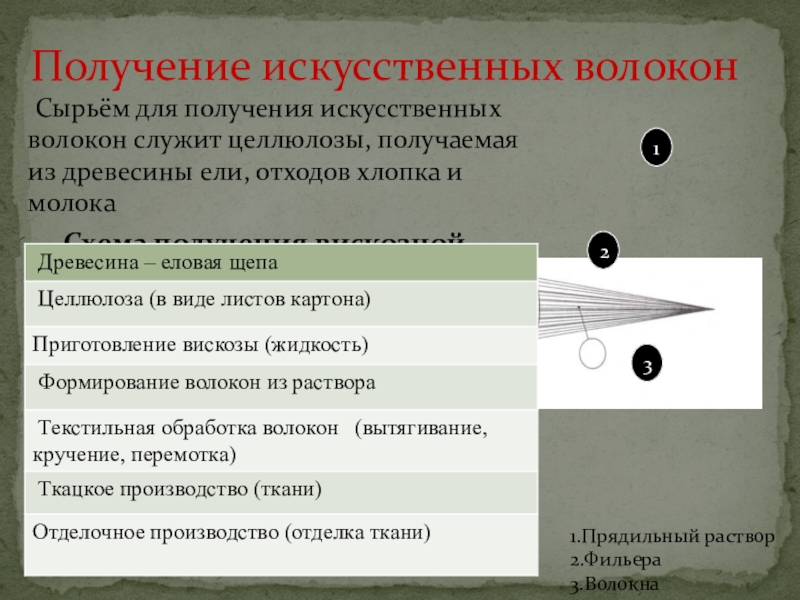
Прядильная площадка синтетического волоконный завод состоит из нескольких прядильных машин или прядильных батарей, каждая с несколько ячеек для производства филаментов.
Обработка волокон После полимеры прядут, этапы процесса зависят от выходной смеси волокна растение. В рассматриваемых производственных единицах здесь используются искусственные волокна. производятся в трех различных формах для продажи в текстильной промышленности — как непрерывные филаментная пряжа в виде штапельного волокна или жгута.
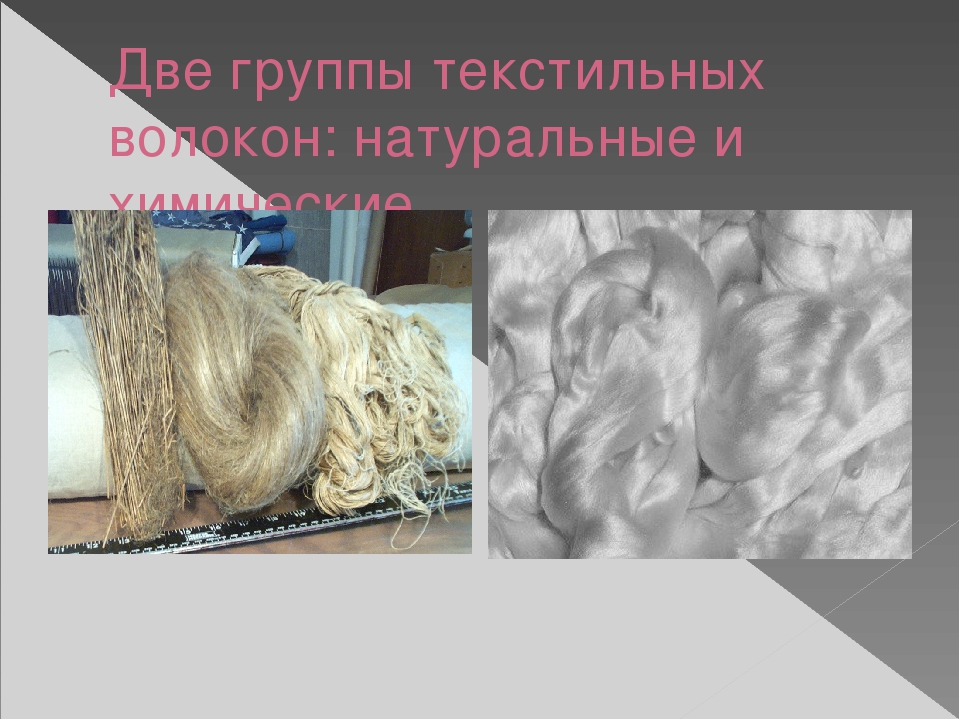