Технология производство бетона – технология, завод, процесс. Советы по организации бизнеса
Технология производства бетона
Технология производства бетона подразумевает смешивание воды, цемента, заполнителей в виде песка или щебня и, в некоторых случаях, различных химических добавок. Не существует одной единой технологии изготовления бетона, поскольку в каждом отдельном случае свойства готового продукта должны опираться на условия окружающей среды, требования по прочности и твёрдости бетона.
Вопросом «рецептуры» цемента занимались русские учёные Н.М. Беляев, С.А. Миронов, Н.А. Попов и другие. Сформулированные ими принципы сделали возможным изготовление бетона с заранее известными свойствами. Качество итогового продукта определяется химическими и физическими параметрами составных частей смеси.
Производство бетона в Москве – востребованный, динамично развивающийся бизнес, одним из бесспорных лидеров которого является компания «СтройПоставка». Молодая компания, которая накопила огромный опыт в производстве качественного строительного материала, создала мощную производственную базу и готова выполнить заказы любых объемов с высоким качеством.
Состав бетонной смеси
Крупный заполнитель: гравий (естественные обломки горных пород, имеют обкатанную, овальную форму) и щебень (продукт искусственного дробления камня). Крупный заполнитель имеет функцию «скелета» будущего бетонного изделия, а значит, гранулы должны быть прочными. Гравий для этой роли предпочтительнее по причине своей естественной формы. Также в качестве крупных заполнителей могут использоваться пемза и шлаки. Они буквально всасывают из цемента лишнюю воду, что положительно сказывается на прочности, но требует добавления большего количества цемента. |
Мелкий заполнитель: песок. Следует отметить, что песок бывает различного происхождения и в каждом случае это совершенно отдельный строительный материал. Пески разделяются по минералогическому составу (кварцевые, полевошпатные, известняковые и доломитовые), и по происхождению (горные, овражные, речные, морские, гравийные, валунные, дюнные и барханные). Различные пески имеют разную структуру, и, что более важно, набор химических примесей и частиц, которые могут быть вредны для бетона. Следует тщательно промывать песок, прежде чем он будет замешан в состав, в противном случае сульфаты и частицы гипса неизбежно скажутся на качестве готового продукта, вплоть до его полной непригодности. |
Вода. При производстве бетона используется вода, по возможности очищенная от химических примесей (сульфаты, кислоты, жиры и т.д.). Запрещается использовать морскую воду для строительства: высокая концентрация солей делает раствор хрупким. |
Цемент. Его функция в связывании между собой частиц заполнителя. Чем выше вяжущее свойство цемента, тем качественнее получится раствор. Цемент изготавливается из клинкера — обожжённого естественного сырья или искусственной смеси. На цементных заводах клинкер мелко перемалывается в шаровой мельнице, иногда в него добавляются гидравлические добавки (гипс, диатомит, трепел). Чем мельче перемолот цемент, тем больше удельная поверхность его частиц, а значит — тем выше его вяжущее способность. |
Технология производства
В лаборатории составляется точная пропорция всех компонентов, которые необходимо загрузить в бетономешалку для получения продукта оптимального качества. Смешивание компонентов с водой происходит в течение длительного времени, после чего бетонная смесь достигает полной однородности. В случае, если производство смеси осуществляется не на строительной площадки, необходимо доставить продукт к месту назначения, не допустив расслоения состава. Для этого применяются специальные машины — автобетоносмесители.
Подготовленный таким образом бетон отгружается получателям. Во избежание расслаивания смеси во время транспортировки и потери свойств, доставку готового бетона необходимо осуществлять с использованием специального транспорта осуществляющим перемешивание, предотвращающим замерзание смеси в холодное время и потерю влаги при высоких температурах.
Условий поставки бетона, аналогичных существующим в компании «СтройПоставка» не предложит никто!
Технология и производство бетона и бетонных смесей
Оглавление:
Состав бетонной смеси
Рецептура приготовления бетона
Этапы изготовления бетона
Производство и изготовление бетона – это сложный технологический процесс, независимо от того, где он производится – в «домашних» условиях или на заводах. Сравнивая качество заводского материала и изготовленного самостоятельно, предпочтение отдаётся первому. Причём это не зависит от качества компонентов, так как они одни и те же, хотя и в заводской практике бывают случаи использования заведомо более дешёвых недоброкачественных составляющих. Однако, первостепенную роль в производстве бетонной смеси играет именно процесс ее приготовления – технология и качество смешивания, степень однородности массы и особенно тщательное соблюдение рецептуры.
Состав бетонной смеси
В состав бетона входит четыре компонента:
- Цемент (вяжущее вещество)
- Заполнитель (песок, щебень)
- Вода
- Добавки
Порой заполнитель разделяют на две отдельные группы: песок и щебень. Это происходит, так как в стройке используется и другой вариант строительной смеси – цементный (смесь цемента, воды и песка). Бетонная же смесь имеет более высокую прочность и долговечность за счёт наличия в составе щебня или гравия, то есть заполнителя более крупной фракции, нежели песок. Использование щебня мелких фракций делает бетон более прочным, так как его частицы ют в смеси более плотно друг к другу.
Рецептура приготовления бетона
Рецептура производства бетонной смеси сводится к чёткому соблюдению требуемого состава и технологии изготовления. Если состав определяется количеством и долей присутствия того или иного компонента в зависимости от марки бетона и класса, то технология определяется условиями обработки бетона (температура, влажность), механическими воздействиями (частота и тщательность замешивания), последовательностью включения компонентов в смесь.
Этапы изготовления бетона
Весь процесс подразделяется на ряд этапов. Заводское производство бетона может включать дополнительные мероприятия по обработке смеси или отдельного компонента, особенно это касается приготовления специальных составов с нестандартным набором включений. Мы рассмотрим технологию производства товарного бетона, наиболее распространённый и упрощённый вариант.
Подготовка компонентов
Сначала приготавливают компоненты состава: промывают, прочищают и просеивают песок и щебень, удаляют взвеси из воды (если таковые имеются). Недостаточное очищение компонентов приводит к присутствию в бетоне посторонних веществ, влияющих на процесс схватывания, на последующую прочность состава. Очень важно использование свежего цемента, это существенно повысит показатели смеси. Долевое соотношение цемента к песку зависит от требуемой прочности состава и последующей нагрузки на бетон, оно колеблется от 1:2 до 1:5 (чем меньше песка, тем ниже прочность).
Смешивание компонентов
Смесь сначала смешивают в твёрдом состоянии, потом добавляя воду продолжают процесс. В индивидуальном строительстве замес производят вручную, при большом количестве бетона его замешивают в бетономешалках. Бетономешалки могут использоваться и в частном строительстве, они бывают гравитационного принципа действия и принудительного. Преимущество у второго типа оборудования, так как замешивание происходит более эффективно. Тщательность такой обработки определяет прочность бетона, так как равномерность распределения компонентов состава – залог его надёжности при застывании.
Соблюдение условий при изготовлении и хранении смеси
Мы говорили о выполнении необходимых условий в процессе изготовления бетона: поддержании оптимальной температуры в районе 20 С и влажности. Но еще важнее сохранить эти условия уже после приготовления состава, к ним необходимо добавить необходимость постоянного перемешивания раствора во избежание отслоения компонентов и потере свойств. Смесь после замешивания приобретает определённую текучесть, которую необходимо поддерживать вплоть до заливки. Бетон, который поставляется с завода на объект необходимо перенести в оптимальные условия для транспортировки. Поэтому для его перевозки используют специальные транспортные средства типа бетоновозов и миксеров.
Определяясь с выбором покупки готового бетона и самостоятельного изготовления, учитывайте риски несоблюдения как рецептуры (это сложно выполнить в «домашних» условиях, не имея специальных измерительных приборов) а также технологию замешивания (ручное смешивание не сравнится с механической обработкой). Беря во внимание, что для достижения качественного результата приготовления материала логичнее использовать уже готовый состав (добавив на месте лишь воду) и применение электрических бетономешалок, просчитайте, будет ли это экономнее заказа готовой бетонной смеси и сделайте правильный выбор.
rus-stroy.net
Технология производства тяжелого бетона
1. Приготовление бетонной смеси.
2. Укладку и уплотнение бетона.
3. Твердение бетона.
4. Контроль его качества.
1-ый этап Приготовление бетонной смеси.
Приготовление бетонной смеси включает в себя точное дозирование материалов по массе или объему и перемешивание. Перемешивание компонентов бетонной смеси осуществляются в бетоносмесителях. По принципу перемешивания различают бетоносмесители 2 типов:
с принудительным перемешиванием;
роторная
противоточная
2. с перемешиванием при свободном падении материала.
В роторной бетономешалке (рис.1) материалы перемешиваются в неподвижном смесительном барабане при помощи вращающихся лопастей, насаженных на вал. В противоточной бетономешалке (Рис.2) барабан вращается в одном направлении, а лопасти в противоположном. Противоточная бетономешалка предназначена в основном для жестких смесей.
Рис. 1 Роторная бетономешалка.
Рис.2 Противоточная бетономешалка.
В бетономешалках с перемешиванием при свободном падении материала (или их еще называют гравитационные) перемешивание происходит с помощью барабана, на внутренней поверхности которого имеются лопасти Рис.3
Рис.3 Гравитационная бетомешалка
При вращении барабана лопасти захватывают бетонную смесь, поднимают ее на некоторую высоту и сбрасывают, чем обеспечивается интенсивное перемешивание. Время перемешивания от 1 до 5 минут в зависимости от объема бетоносмесителя (от 100 л до 9000 л) и подвижности бетонной смеси. Транспортирование бетонной смеси осуществляется вагонетками, транспортерами, бетононасосами, автотранспортом.
2-ой этап Укладка и уплотнение бетонной смеси.
Укладка бетонной смеси в формы осуществляется специальными бетоноукладчиками, движущимися по рельсовому пути, или коробами, транспортируемыми мостовыми кранами. Для формования бетонных изделий их, как правило, необходимо уплотнять (кроме высокопористых ячеистых бетонов).
Способы уплотнения:
а) вибрирование. При вибрировании бетонной смеси передаются колебания, создаваемые вибромеханизмом, в результате чего она становится подвижной, текучей и заполняет все профили формы. Используют:
1.1 поверхностные вибраторы с плоской плитой (Рис.4)
1.2 глубинные вибраторы (Рис.4)
1.3 стационарные виброплощадки.
Рис.4 Поверхностный вибратор и глубинный
б) Вибропрессование и виброштампование. Вибрирование сочетается с прессующими воздействиями плоской (вибропрессование) или профилированной (виброштампование) плиты. Методом виброштампования формуют ребристые плиты, лестничные марши и др.
в) Центрифугирование. При формовании изделий на центрифугах форма с бетонной смесью вращается с определенной скоростью вокруг своей продольной оси, в результате чего центробежные силы распределяют бетонную смесь по стенкам формы. Изделия получаются полые, с внутренней полостью круглого сечения и любым внешним очертанием, в зависимости от формы. Этим методом формуют трубы, круглые сваи и другие полые изделия.
3-ий этап Твердение бетона.
При нормальных условиях (комнатной температуре и влажности, близкой к 100%) твердение бетона протекает 28 суток. В условиях промышленного производства твердение бетона ускоряют.
Методы ускорения твердения:
а) термовлажностная обработка (ТВО). Она осуществляется в пропарочных камерах ямного типа (глубиной ≈ 2 метра) (Рис.5) в атмосфере насыщенного водяного пара при температуре 90-100о в течение 12-15 часов.
Режимы ТВО:
Выдержка 2-3 часа
Подъём t-ры со скоростью 25-300С в час
Изотермический прогрев (t=80-900С) в течении 6-8 часов
Охлаждение со скоростью 30-400С в час
Общее время ТВО 12-15 часов
Рис. 5 Пропарочная камера ямного типа
После пропаривания, в зависимости от применения различных цементов, продолжительности пропаривания и температуры, изделия приобретают от 70% до 100% 28-суточной прочности бетона.
б) Электропрогрев. Он производится переменным электрическим током Рис.6. В бетоне электрическая энергия преобразуется в тепловую и разогревает бетон, ускоряя его твердение. Существуют несколько таких способов: внутренний прогрев за счет теплоты, выделяющейся при прохождении электрического тока через бетон; обогрев изделия инфракрасными излучателями, прогрев в электромагнитном поле, применение контактных электронагревателей. Изделия для предотвращения испарения воды необходимо закрывать.
Рис.6 Электропрогрев бетона
г) Контактный обогрев. Он осуществляется путем контакта изделия с обогреваемой опалубкой или формой. При этом изделия плотно укрывают, чтобы предотвратить потерю воды.
д) Введение добавок-ускорителей твердения. Особенностью использования добавок–ускорителей твердения является то, что эффективность их действия на твердение бетона и набор прочности проявляется в основном в течение первых 3-4 суток. В дальнейшем эффект ускорения твердения и возрастания прочности ослабевает, и в 28-суточном возрасте прочности бетонов с добавками и без добавок становятся одинаковыми (рис.4).
Рис. 7 — Влияние добавок-ускорителей твердения на набор прочности цементных бетонов во времени
Следует отметить, что ускорители твердения на основе хлоридов могут вызвать коррозию стальной арматуры в армированных бетонах, поэтому их не рекомендуется вводить в количестве более 2% от массы цемента.
studfiles.net
Технология производства бетона. ООО «Ника-Н» Россия, Тульская обл., г. Новомосковск.
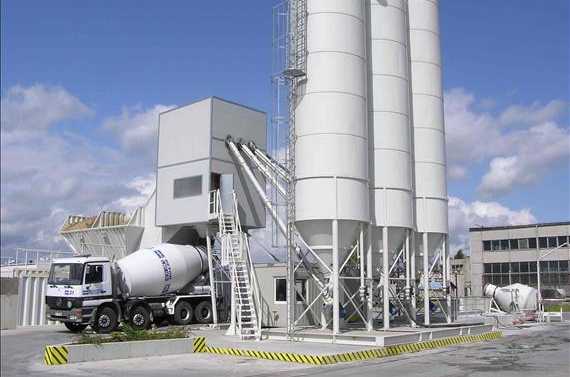
Бетон изготавливают на строительных предприятиях, в цехах железобетонных заводов, на БСУ.
Создание бетона проходит поэтапно:
- заготовка сырья;
- вымешивание доз;
- замес готового раствора.
Предприятия по производству строительных материалов зачастую самостоятельно занимаются процессом по переработке необходимого сырья. Изначально дробят наполняющие вещества (щебень, песок, гравий), очищают от ненужного мусора. Стройки и заводы выполняют только конкретные задачи: цемент перемалывают, смешивают химические примеси, а зимой наполнитель доводят до нужной температуры предварительно.
Перемол цемента осуществляется двумя способами: сухим и мокрым. Это часто сопровождается добавлением химических смесей для быстрого затвердения бетона. Делают эту операцию предприятия, у которых в наличии специализированное оборудование и недорогая электроэнергия. Уплотнение цемента происходит быстрее, когда общая площадь поверхности зерен увеличивается на 15-30%. На 30-100% прочнее бетон, подготовленный за сутки.
Вымешивают химикаты так: соединяют их с водой и доводят раствор до нужной субстанции. Берут емкость с трубопроводной системой для соединения химических ингредиентов и посредством спрессованного воздуха или парового воздействия подогревают смесь до нужного состояния. В оснащенную уровневым датчиком расходную емкость заливают готовый состав раствора, а далее через дозатор переправляют в бетоносмеситель.
Наполнители подогревают в подземных помещениях или на специальных открытых площадях. Тут два варианта:
— методом подогрева через паровые трубы и гребенки под землей;
— методом паровой или газовой обработки.
Чтобы не затрачивать много энергии, лучше использовать второй вариант. Главное следить, чтобы пара было достаточно.
В технологии изготовления бетона играют важную роль весы для точного распределения доз воды, цемента, примесей. Наполнители не обязательно взвешивать так тщательно. Возможно незначительное отклонение.
В процессе создания бетона уходит 2 л воды (до 5 л для полевых составов), цемента – 5кг, инертных материалов – 10 кг. Сверхточности не добиться. Пока что нет точных дозаторов для этого.
Объемные дозаторы для вывешивания бетонных наполнителей подходят в неприспособленных условиях. Здесь важно брать в расчет вес песка, который имеет свойство тяжелеть при повышенной влажности воздуха.
Возьмем примерные составляющие бетонной смеси: цемент, вода, песок, щебень в значениях – 300/170/560/1200. Отнимая влажность песка на 30% от увеличения объема, получаем в сухом виде 430 кг (560/1,3=430) введенного материала. Возьмем влажный песок – 400 кг (430(1-0,03)=400). Итоговый объем песка будет составлять 153 литра (400/2,63=152). А должен был иметь значение 212 литров (560/2,63=213). Теряет из-за влажности 59 литров (212-153=59). Чтобы восполнить нехватку объема, понадобиться дополнительный ресурс цемента и составляющих. Выходит перерасход в 17 кг (300*59/1000=17).
В результате, из-за неправильного соразмерения наполняющих элементов, возможно загустение бетонного раствора. Это воспрепятствует его правильной укладке в формы.
Зернистая масса заполнителя для легкобетонной смеси предусматривает объемное дозирование. Погрешность примерно 30 л/куб.м.
Если использовать объемно-весовой дозатор, то гравий, щебень дозируют по объемным характеристикам, а песок взвешивают с допустимой погрешностью 1-2%.
Перемешивание составных компонентов представляет следующий этап изготовления бетона. Все составляющие ингредиенты раствора бетона соразмерено распределяются между собой. В итоге, выходит однородная смесь цемента, воды и наполняющих веществ с одинаковыми свойствами по всему объему будущего бетона.
Вид и состав бетона влияют на определенные требования к перемешиванию. Жидкие растворы бетона более податливы для смешивания, чем густые; плотные лучше, чем тонкие. Крупные зерна примесей заполнителей выгоднее для усадки раствора.
Бетонный раствор имеет свойство реагировать на замес, зависимо от типа и качества составляющих. Щебень и гравий крупных фракций в составе бетонной смеси требует применения специального бетоносмесителя. Барабан с лопастями многократно перекидывает смесь в гравитационном порядке.
С помощью вращения лопастных валов происходит принудительное смешение раствора. Но работает данная система конвективным способом. Есть метод виброперемешивания, при котором компоненты, как бы вибрируют в процессе. Недавний замес бетона становится прочнее и лучше, все компоненты удачно растворяются.
Таблица 1. Продолжительность перемешивания тяжелых бетонных смесей
Объем приготовляемой бетонной смеси, л |
Осадка конуса, см |
|
2-6 |
более 6 |
|
300 |
60 |
45 |
800 |
120 |
90 |
1600 |
150 |
120 |
Замес бетонной смеси должен иметь достаточную продолжительность. От этого зависит качество готовой продукции. Загружая составные элементы в бетоносмеситель цикличного типа, следует определять момент выгрузки. Заметно ухудшает качество прочности бетона малая продолжительность перемешивания. В то время как превышение времени замеса ничуть не влияет на прочность. Тип бетоносмесителя, состав и технические характеристики раствора сами определяют длительность перемешивания. Плотность более чем 2200 кг на кубометр в смесителях цикличного типа предполагает длительность замеса не более 2 минут. Умеренно загущенные, плотные смеси перемешивают больше двух раз.
В бетоносместителях принудительного типа замес смесей крупного зерна длится максимум 3 минуты. Мелкозернистые фракции требуют от трех до пяти минут времени.
Отличается время замеса легкобетонных смесей качеством заполнителя, дозами расходуемых в процессе веществ и зависит от марки бетона.
Таблица 2. Продолжительность перемешивая легкобетонных смесей, мин.
Объемная насыпная масса крупного заполнителя, кг/м3 |
Смесь |
|
||||||
для плотного бетона с жесткостью 20-60 с при предельной крупности зерен заполнителя, мм |
для поризованного бетона при предельной крупности зерен заполнителя, мм |
для крупнопористого бетона |
|
|||||
10 |
20 |
40 |
20 |
40 |
||||
До 300 |
6 |
5 |
4 |
6 |
5 |
5 |
||
300-700 |
5 |
4 |
3 |
5 |
4 |
4 |
||
Более 700 |
4 |
3 |
2 |
4 |
3 |
3 |
nika-beton.ru
Технология изготовления бетона
Бетон – самый распространенный стройматериал, представляющий собой искусственно созданное путем смешения ингредиентов до их застывания окаменелое образование. Изготовители предлагают множество сортов бетона, различающихся по составу, маркировке, целевому признаку, виду и количеству добавок.
Типичный раствор бетона включает в себя вяжущее вещество (цемент), воду и заполнители (песок, щебень). Марка зависит от соотношений ингредиентов, в особенности вода–цемент, а также наличия дополнительных составляющих.
Технология приготовления
Производственный процесс заключается в определении нужного количества составных частей и перемешивании. Каждая марка бетонного раствора имеет свой состав и соотношение: для верного исполнения необходима безошибочная дозировка. С этой целью бетонные производства оснащены специальными дозаторами. Самые точные – автоматические: они функционируют в безостановочном режиме и укладываются в допустимые пределы несоответствия.
Производство бетона: оборудование
Стандартное оборудование для производства бетона для усиления качественной составляющей раствора состоит из большого числа элементов, в том числе автоматизированных линий. Вот некоторые из возможных мини-заводских линеек:
- силосная;
- дозаторная;
- смесительная;
- конвейерная;
- линия снижателей;
- шнековая;
- подъемная;
- погрузочная;
- линейка кабин, оснащенных пультами управления.
Заводская аппаратура
Крупные заводы для изготовления бетонного раствора пользуются бетоносмесителями, работающими непрерывно или периодически. Принцип работы бетонных смесителей с периодическим процессом основан на загрузке нужных доз компонентов, перемешивании и выемке. Бетонные смесители непрерывные функционируют на постоянной основе.
Для получения высокожестких смесей заводские производства используют вибросмесители, основанные на смешении и вибрации.
Смысл наличия вибрации в том, что при специальных параметрах настройки происходит нарушение сцепляющих связей между компонентами смеси. В результате увеличивается мобильность перемешивания раствора благодаря полученной взвешенности.
Современно оборудованные заводы добавляют технологию «смешивание плюс нагревание», добавляя в бетоносмеситель горячий пар (до 60 °C), действующий эффективнее электрообогрева или горячей воды.
Производство
ВИБРО-М, уже 15 лет являющаяся крупнейшим изготовителем вибрационного оборудования, изготавливает бетоносмесители с различными узловыми схемами, оснащенные дозаторами разных типов: информацию о компании можно посмотреть на сайте vibro-m.ru. Дополнительно поставляются насосы, активаторная, побудительная, распределительная аппаратура, транспортные устройства.
Произведенный заводским путем бетон отличается повышенными характеристиками при малой себестоимости. Любая партия раствора бетона поставляется с приложенным сертификатом качества и паспортным документом с указанием классификации и структуры смеси.
promdevelop.ru
Технология производства бетона — материалы для изготовления раствора
Ни одно современное строительство не обходится без применения самого распространённого на сегодняшний день строительного материала — бетона. Данный строительный материал обладает уникальными свойствами, благодаря которым он и стал столь популярным:
- Прочность. Если соблюдена технология производства бетона, то получающийся в результате искусственный камень не уступает по прочности натуральным. Она напрямую зависит от марки применяемого цемента.
- Удобоукладываемость. Незастывшая масса легко заполняет всё пространство, ограниченное опалубкой.
- Долговечность. Срок службы бетонных конструкций и изделий исчисляется десятками и сотнями лет.
- Стойкость к воздействию агрессивных сред и природных явлений.
Неудивительно, что ответ на вопрос как изготовить бетон волнует многих людей, занимающихся индивидуальным строительством.
Материалы
Цемент. Является связующим веществом в составе бетонной смеси, застывающим после взаимодействия с водой и определяющим все основные свойства будущего строительного материала. От марки применяемого цемента будет зависеть, в конечном счёте, и марка бетона (основная характеристика его прочности). Статья о цементе и технологии его производства.
Инертные наполнители. Соединение одного цемента с водой также со временем затвердеет, но получившийся цементный камень, во-первых, будет слишком дорог, во-вторых, его прочность вряд ли будет удовлетворять строителей. Поэтому в смесь цемента и воды добавляют так называемые инертные наполнители (чаще всего это песок и щебень), которые выполняют несколько функций.
- Щебень, обладая значительной собственной прочностью, существенно увеличивает и прочность получающегося искусственного камня.
- Песок способен увеличивать подвижность смеси, что является несомненным преимуществом в процессе строительства. Для получения более крепкого материала технология бетона предусматривает использование гранитного щебня.
В случае если к готовому искусственному камню не предъявляются серьёзные требования по прочности и не предусматривается его использование в несущих конструкциях, вполне можно обойтись щебнем известняковым, кирпичным боем или дроблёными шлаками.
Вода для смеси может быть самой обыкновенной, единственным требованием к ней будет чистота. А вот к количеству воды для приготовления смеси требования куда жёстче. При недостатке воды в процессе кристаллизации будет участвовать не весь цемент, а при избытке — снижаются прочностные характеристики.
Технология самостоятельного изготовления бетона
Для приготовления бетонной смеси, которая впоследствии превратится в монолитный бетон, удовлетворяющий всем требованиям, необходимо соблюдение пропорций всех входящих в неё материалов.
Наиболее оптимальным способом будет предварительное перемешивание сухих составляющих в пропорции приблизительно 3:5:10 (цемент: песок: щебень). Количество воды зависит от разных факторов, в том числе от первоначальной влажности ингредиентов, и может быть указано лишь приблизительно (10–15% от массы сухих составляющих). В любом случае количество воды должно обеспечивать необходимую пластичность смеси и полное смачивание цемента.
Изготовление бетона своими руками лучше всего производить с использованием средств механизации, имеется в виду электрическая бетономешалка. Она позволит самым тщательным образом перемешать смесь до получения однородной пластичной массы.
Заливать смесь необходимо при положительных температурах окружающего воздуха, в противном случае следует добавлять в смесь специальные антиморозные добавки.
Строительный раствор
Попросту говоря строительный раствор — это та же самая бетонная смесь, в которой отсутствует наполнитель крупной фракции. Технология его производства точно такая же, как технология приготовления бетона, естественно без добавления крупнофракционного наполнителя.
В строительстве раствор применяется в качестве связующего вещества между готовыми строительными формами (кирпичи, пеноблоки, железобетонные плиты), для выравнивания участков поверхностей (устройство стяжек).
Поскольку покупка бетонной смеси дело накладное, особенно при больших объёмах, допускается предварительное изготовление раствора с последующим добавлением щебня и тщательным перемешиванием в небольшой бетономешалке или вручную. Таким образом, можно существенно сэкономить при строительстве.
hardstones.ru
Новые технологии в производстве бетона
Бетон уже на протяжении полутора века занимает главную позицию среди строительных материалов. Это искусственный камень, получаемый при затвердевании композитной массы на основе цемента, песка заполнителя и воды. Сегодня новые технологии производства бетона сильно отличаются от времен его изобретения. Применяется новое оборудование, специальные добавки, а широкий выбор заполнителей позволяет получать материал различных марок и модификаций. Кроме того, ведутся разработки абсолютно новых бетонов способных к самовосстановлению. Учитывается также экология производства.
Требования и классификация
Конечно, главное требование – это прочность. При этом имеется ввиду прочность на сжатие, так как на растяжение он сопротивляется плохо. В железобетонных конструкциях этот недостаток устраняется армированием. Металлическая или стеклопластиковая арматура закладывается в зону, где при эксплуатации будет возникать растяжение, принимая эту нагрузку на себя.
Испытания на сжатие
На производстве образец каждой партии заливается в кубическую форму, а в Европе и США ‒ в цилиндрическую. После его затвердевания и набора прочности, в возрасте 21 суток, образец сжимают до разрушения. Сила давления при этом фиксируется и сравнивается с расчетной. Марка указывается в акте испытаний в виде буквы «М» и числа. Например, М-400 означает, что образец разрушился при давлении 400 кг сил/см2.
Вторым важным требованием является плотность. Чем выше плотность, тем меньше водопоглощение. Как известно, вода при замерзании расширяется и, если водопоглощение высокое, при замерзании в строительном материале будут образовываться микротрещины, разрушая его при каждом климатическом цикле. Плотность определяется экспериментальным путем и записывается в «кг/м3». Бетоны с высокой плотностью относятся к тяжелым и применяются в производстве дорожных, а также аэродромных плит, фундаментных блоков и других изделий, подверженных воздействию влаги/воды.
Тяжелый бетон также испытывают на морозостойкость. Этот показатель обозначается буквой «F» и числом климатических циклов, после которых образец потерял не более 5% прочности.
Производство ЖБИ
Несмотря на большой спрос, конкуренция среди производителей железобетонных изделий остается высокой. Стремление повысить качество и снизить себестоимость стимулирует производителей не только применять современное оборудование, но и новые технологии в производстве бетона. Главная задача ‒ ускорить процесс без потери качества, достигается техническим оснащением и конвейерным способом производства.
Очередность процессов
Сначала производится приготовление бетонной смеси. Весь процесс происходит на БСУ (бетоносмесительной установке) с соблюдением последовательности и точной дозировки. В это же время подготавливается форма, которая устанавливается на вибростоле. Форма смазывается и в нее укладывается арматура. При необходимости арматура предварительно напрягается путем пропускания через нее электрического тока. При этом арматура нагревается, вследствие чего удлиняется. Концы арматуры закрепляются в специальных пазах формы и, после остывания, она натягивается подобно струне. Готовая бетонная смесь подается в специальном контейнере с помощью мостового или другого крана. При заполнении формы включают вибраторы, за счет чего смесь укладывается равномерно, из неё выходит воздух и обеспечивается отличное сцепление с арматурой. Чтобы изделие не высохло преждевременно, форму закрывают крышкой и помещают в пропарочную камеру. В зависимости от массы, изделие держат в камере при повышенной температуре и влажности. Этот процесс ускоряет затвердевание и сокращает срок набора прочности от 21 суток до 10-12.
Любые ЖБИ должны строго соответствовать нормам СНиП, поэтому испытания производятся в обязательном порядке.
Мобильные заводы
При строительстве в отдаленных районах доставка ЖБИ или сырого бетона для монолитных конструкций вызывает дополнительные затраты. С целью избежать этих затрат в России все чаще применяются мобильные заводы. Ярким примером применения таких установок стало строительства моста через Керченский пролив. Благодаря мобильности, завод оперативно перебазируется в нужное место, что экономит время и средства на доставку продукта.
Применение пластификаторов
Время, когда в бетонную смесь добавляли известковое молоко уже в прошлом. На сегодняшний день широкое применение нашли современные суперпластификаторы. Вещества на основе поликарбоксилатов и полиакрилатов показывают просто чудеса науки. При незначительных добавках этих веществ в бетонную смесь раствор становится особо подвижный при уменьшении в нем воды. В результате это положительно влияет на процесс заполнения формы или опалубки, повышает устойчивость материала к растрескиванию и колоссально повышает его прочность. Например, при добавке пластификатора на основе белого цемента М-400, который не отличается особым качеством, его прочность возросла в полтора раза, а водопоглощение снизилось на 3%.
Микрокремнезем
Это аморфный порошок микроскопической фракции. Его вводят в бетонный состав вместе с пластификатором. Цель его применения заключается в заполнении пространства между более крупными частицами. В результате снижается пористость, повышается плотность, а также водонепроницаемость. Технология применяется в производстве дорожных покрытий, делая их долговечней при эксплуатации в любой неблагоприятной среде.
Применение микрокремнезема без пластификаторов не имеет смысла.
Кубовидный щебень и песок
В РФ производство бетона с заполнителями кубовидной формы – новинка. Первыми технологию начали применять в Санкт-Петербурге. За счет своей кубической формы щебень образует плотное соединение, снижает расход цемента и увеличивает плотность. Первые образцы отлично зарекомендовали себя в строительстве дорог.
С кубовидным песком ситуация подобная, но первопроходцем стало предприятие в Приморском крае. На сегодня у них единственная установка по производству такого песка, которая была приобретена в Японии.
Поиск новых решений
Не только качество материла играет роль в покупательском спросе. Новые технологии изделий из бетона начинают приобретать инновационный формат. Здесь родоначальником опять выступил Санкт-Петербург. Колодезные кольца из железобетона почти сразу приобрели популярность на рынке. Секрет оказался в форме торцов, которые имели специальные замки. Соединять такие кольца намного быстрей и проще, а качество соединения превосходит традиционные методики. В настоящий момент в России производят множество ЖБ-конструкций с подобными новшествами.
Кевларобетон
Технология позволяет производить декоративные и одновременно сверхпрочные изделия с глянцевой поверхностью. Искусственный камень визуально напоминает мрамор, а с применением пигментов может представляться в любых цветовых тонах.
Этот бетон относится к армированным мелкими волокнами, в данном случае кевлара, но основная суть его получения заключается в процессе. Перемешивание производится в гравитационных смесителях с поочередным добавлением всех ингредиентов. Главный момент – добавление воды, количество которой строго дозируется. В результате в смесителе образуются шарики (скатыши) размером 2-5 см, которые исключают в своем составе воздух. Эти шарики и засыпают в форму, а в процессе вибрирования они равномерно ее заполняют, как бы растекаясь по всему объему.
В России новые технологии по производству бетона внедряются в основном на малых предприятиях, в то время как в Европе это считается перспективным направлением.
Бетон будущего
«Вечный» бетон решили создать голландские ученые и это им весьма удалось. В состав на основе белого цемента были введены бактерии, а в качестве их пропитания – молочнокислый кальций. Микроорганизмы охотно поедают его, вырабатывая известняк, чем и пломбируют микротрещины.
Вторым вариантом материала, обладающий способностью к самовосстановлению, стал эластичный бетон. Его эластичность достигается благодаря содержащейся в нем группе минералов, за счет чего он более устойчив к динамике. Восстановление достигается за счет его химической реакции с углекислым газом в атмосфере. Реакция активируется дождевой водой, а ее продуктом становится карбонат кальция, который и является «главным доктором бетона».
Интересный вариант предложили канадцы. Экобетон – такое название материал получил из-за способа производства, основным ингредиентом которого стала углекислота. Причем углекислоту они брали на предприятиях, где она получалась как побочный продукт. Другими словами, производство такого экобетона способствует снижению парникового эффекта.
qwizz.ru