Производство аммиака – Оборудование + Технология изготовления 2019
Оборудование + Технология изготовления 2019
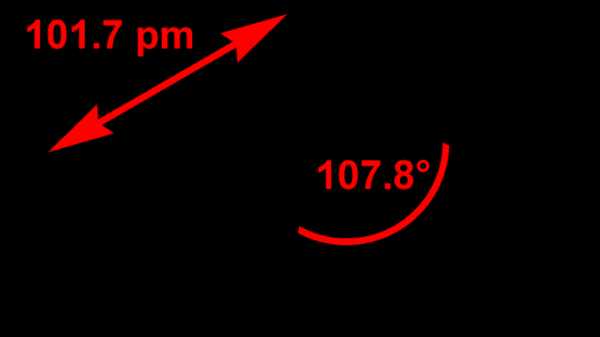
Аммиак (нитрид водорода, формула NH3) при нормальных условиях — это бесцветный газ с резким характерным запахом. Он относится к числу важнейших продуктов химической промышленности. Его ежегодное мировое производство достигает 150 млн. тонн. В основном он используется для изготовлении азотных удобрений (нитрат и сульфат аммония, мочевина), взрывчатых веществ и полимеров, азотной кислоты, соды (по аммиачному методу) и других продуктов химической промышленности. Жидкий аммиак используют в качестве растворителя.
В холодильной технике используется в качестве холодильного агента (R717).
В медицине 10% раствор аммиака, чаще называемый нашатырным спиртом, используется при обморочных состояниях (для возбуждения дыхания), для стимуляции рвоты, а также наружно — при невралгии, миозитах, укусах насекомых, для обработки рук хирурга. При неправильном использовании может вызвать ожоги пищевода и желудка (в случае приёма неразведённого раствора), рефлекторную остановку дыхания (при вдыхании в высокой концентрации).
Технология производства аммиака + видео как получают
В рамках этого направления сегодня многие компании стали заниматься разработкой и проектированием следующих технологий:
- Перевод избыточного количества аммиака на изготовление метанола.
- Разработка производства на основе современных технологий для подмены активных агрегатов.
- Создание интегрированного производства и модернизация.
На производство одной тонны аммиака в России расходуется в среднем 1200 нм³ природного газа, в Европе — 900 нм³. Белорусский «Гродно Азот» расходует 1200 нм³, после модернизации ожидается снижение расхода до 876 нм³. Украинские производители потребляют от 750 нм³ до 1170 нм³. По технологии UHDE заявляется потребление 6,7 — 7,4 Гкал энергоресурсов на тонну.
Промышленный способ получения аммиака основан на прямом взаимодействии водорода и азота:
N2 + 3H2 ⇄ 2NH3+ + 91,84 кДж
Это так называемый процесс Габера (немецкий физик, разработал физико-химические основы метода). Реакция происходит с выделением тепла и понижением объёма. Следовательно, исходя из принципа Ле-Шателье, реакцию следует проводить при возможно низких температурах и при высоких давлениях — тогда равновесие будет смещено вправо. Однако скорость реакции при низких температурах ничтожно мала, а при высоких увеличивается скорость обратной реакции. Проведение реакции при очень высоких давлениях требует создания специального, выдерживающего высокое давление оборудования, а значит, и больших капиталовложений. Кроме того, равновесие реакции даже при 700°C устанавливается слишком медленно для практического её использования. Выход аммиака (в объёмных процентах) в процессе Габера при различных температурах и давлении имеет следующие значения:
100 ат | 300 ат | 1000 ат | 1500 ат | 2000 ат | 3500 ат | |
---|---|---|---|---|---|---|
400 °C | 25,12 | 47,00 | 79,82 | 88,54 | 93,07 | 97,73 |
450 °C | 16,43 | 35,82 | 69,69 | 84,07 | 89,83 | 97,18 |
500 °C | 10,61 | 26,44 | 57,47 | Нет данных | ||
550 °C | 6,82 | 19,13 | 41,16 |
Применение катализатора (пористое железо с примесями Al2O3 и K2O) позволило ускорить достижение равновесного состояния. Интересно, что при поиске катализатора на эту роль пробовали более 20 тысяч различных веществ.
Учитывая все вышеприведённые факторы, процесс получения проводят при следующих условиях:
- температура 500 °C;
- давление 350 атмосфер;
- катализатор.
Выход аммиака при таких условиях составляет около 30%. В промышленных условиях использован принцип циркуляции — аммиак удаляют охлаждением, а непрореагировавшие азот и водород возвращают в колонну синтеза. Это оказывается более экономичным, чем достижение более высокого выхода реакции за счёт повышения давления. Для его получения в лаборатории используют действие сильных щелочей на соли аммония:
NH4Cl + NaOH → NH3↑ + NaCl + H2O
Обычно лабораторным способом аммиак получают слабым нагреванием смеси хлорида аммония с гашеной известью.
2NH4Cl + Ca(OH)2 → CaCl2 + 2NH3↑ + 2H2O
Для осушения аммиака его пропускают через смесь извести с едким натром. Очень сухой можно получить, растворяя в нём металлический натрий и впоследствии перегоняя. Это лучше делать в системе, изготовленной из металла под вакуумом. Система должна выдерживать высокое давление (при комнатной температуре давление насыщенных паров около 10 атмосфер). На промышленном производстве обычно для сушки используют абсорбционные колонны.
Видео как делают:
Производство аммиака не должно обходить стороной технический прогресс. В основном это касается энергосбережения. В ходе разработки современных технологий большое значение отводится программному обеспечению, необходимому для моделирования химических и технологических процессов.
moybiznes.org
Производство аммиака
Азотная промышленность сегодня — одна из ведущих отраслей. Применение аммиака распространилось на холодильную технику (R717, холодильный агент), медицину (раствор аммиака или спирт нашатырный), сельское хозяйство (удобрения).
Первостепенное внимание уделяется именно производству азотных удобрений (а значит — и их основам, в том числе аммиаку, спрос на который вырос за последние два десятилетия на 20%).
Но производство аммиака отличается, в первую очередь, высокой энергоемкостью. Вся история этого производства — борьба за понижение используемых энергий (механической, тепловой, электрической).
Синтез аммиака раскрывает формула:
N2 + 3h3 = 2Nh4 + Q
Реакция экзотермическая, обратимая, с уменьшением объема. Поскольку реакция экзотермическая, понижение температуры сместит равновесие к образованию аммиака, однако скорость реакции значительно снизится. Производство аммиака должно идти при высоких температурах (синтез проходит при 500 градусах Цельсия). Повышение t° приведет к обратной реакции. Давление от 15 до 100 Мпа позволяет противодействовать влиянию температуры (низкое давление — от 10 до 15 Мпа, среднее давление — от 25 до 30 Мпа, высокое давление — свыше 50 МПа). Из них предпочтительнее среднее.
Катализатором служит железо губчатое с добавками кальция, кремния, калия, оксидов алюминия.
Вредные примеси (оксид углерода, вода, сероводород) отрицательно сказываются на скорости течения реакции, отравляя катализатор, снижая тем самым его активность и уменьшая сроки службы. Это означает, что сероводородная смесь должна обязательно пройти тщательную очистку. Но даже после очистки в аммиак превращается лишь часть этой смеси. Поэтому оставшуюся непрореагировавшую долю вновь отправляют в реактор.
Как происходит производство аммиака?
В трубопровод подают уже подготовленную смесь из трех частей водорода и одной азота. Она проходит через турбокомпрессор, где сжимается до указанного выше давления, и направляется в колонну синтеза с катализатором на встроенных полках. Процесс, как мы выяснили, сильно экзотермический. Выделяющимся теплом нагревается азотоводородная смесь. Из колонны выходит около 25 процентов аммиака и непрореагировавшие азот с водородом. Весь состав поступает в холодильник, где смесь охлаждается. Аммиак под давлением становится жидким. Теперь в работу вступает сепаратор, задача которого — отделить аммиак в сборник в нижней части и непрореагировавшую смесь, которая возвращается циркуляционным насосом обратно в колонну. Благодаря такой циркуляции азотоводородная смесь используется на 95 процентов. Жидкий аммиак по аммиакопроводу поступает на специальный склад.
Все аппараты, использующиеся в производстве, максимально герметичны, что исключает утечку. Используется лишь энергия происходящих внутри экзотермических реакций. Схема замкнутая, малоотходная. Затраты снижены благодаря непрерывному и автоматизированному процессу.
Производство аммиака не может не влиять на окружающую среду. Неизбежны газовые выбросы, включающие в себя аммиак, оксиды углерода и азота и прочие примеси. Выделяется низкопотенциальная теплота. Сбрасывается вода после промывки систем охлаждения и самого реактора.
Поэтому в производство аммиака необходимо включать каталитическую очистку с наличием газа-восстановителя. Снижения количества сточных вод можно добиться заменой поршневых компрессоров на турбокомпрессоры. Низкопотенциальная теплота может быть утилизирована вводом теплоты высокопотенциальной. Однако это увеличит загрязненность дымовыми газами.
Энерготехнологическая схема, включающая парогазовый цикл, где используются как тепло пара, так и продукты сгорания топлива, одновременно и повысит эффективность производства, и уменьшит выбросы.
fb.ru
Производство аммиака
Азотное производство играет важнейшую роль в современной химической промышленности. Стоит заметить, что соединения азота применяются как при получении органических, так и неорганических веществ. Особую статью в азотной промышленности составляет производство аммиака. Именно при «участии» этого ценнейшего компонента производятся удобрения, азотная кислота, взрывчатые вещества, хладоагенты и многое другое. При всей своей полезности аммиак является довольно сильным ядом, несмотря на то что применяется в медицине в виде нашатыря.
Сам аммиак как вещество впервые был обнаружен в конце XVIII века. Описал его как отдельное вещество англичанин Джозеф Пристли. Спустя 11 лет французом Клодом Луи Бертолле был изучен химический состав этого вещества. Необходимость получения аммиака в промышленных количествах стала остро возникать в конце XIX века, когда стали истощаться месторождения чилийской селитры, из которой в основном получали азотные соединения. Именно «щелочной воздух» стал самым перспективным компонентом для производства различных химических соединений, которые оказали огромное влияние на разные стороны жизни человека: от военного дела, до сельского хозяйства.
Но эта проблема была решена только в начале XX столетия, когда появился способ производства аммиака путем прямого синтеза из азота и водорода. Таким образом, од возникновения проблемы до ее решения прошел довольно длительный период, в ходе которого было сделано несколько открытий, позволивших «сказку сделать былью».
Особенности и этапы производственного процесса
Процесс производства аммиака характеризуется большой энергоемкостью, что является главным его недостатком. Именно поэтому постоянно ведутся научные разработки, которые призваны решить проблемы экономии энергии. В частности разрабатываются способы утилизации выделенной энергии, а также совмещение, например, производства аммиака и карбамида. Все это способствует удешевлению деятельности предприятий и повышению их полезной отдачи.
В основу производства аммиака положены принцип циркуляции, согласно которому процесс идет непрерывно, причем остатки исходных компонентов отделяются от конечного продукта и используются вновь, непрерывности: процесс синтеза происходит без остановки, принцип теплообмена, а также принцип цикличности. Как видно, все эти принципы между собой тесно взаимосвязаны.
Сама технологическая схема производства аммиака зависит, прежде всего, от сырья, из которого получается конечный продукт. Дело в том, что, в отличие от азота, который содержится в воздухе в больших количествах, водород в чистом виде в природе практически не присутствует, а выделять его из воды — довольно трудоемкий и энергозатратный процесс.
Поэтому в качестве сырья для производства аммиака в основном используются углеводороды, содержащиеся в природном газе. В настоящее время именно природный газ является одной из основ аммиачной промышленности. Прежде чем попасть в колонну синтеза, газ проходит несколько стадий обработки. Начинается процесс с того что производится очистка исходного сырья от серы при помощи десульфуратора.
Далее идет так называемый процесс риформинга, который заключается в том, что в его ходе углеводороды сначала превращаются в метан, потом происходит довольно сложный процесс превращения метана в смесь водяного пара, угарного газа, углекислого газа и водорода. При этом также происходит очистка смеси от углекислого газа, после чего водород попадает в колонну синтеза под большим давлением вместе с азотом. Таким образом, прежде чем начать непосредственно производство аммиака, технология предполагает предварительную обработку сырья.
Все процессы риформинга, как и непосредственно сам синтез конечного продукта, происходят при высоком давлении и большой температуре. Именно это приводит к большой их энергозатратности. При этом указанные параметры на всех стадиях производства изменяются.
Сама колонна обычно изготавливается из стали. В ней размещен катализатор, состав которого может быть разным. После прохождения цикла синтеза смесь попадает в холодильник, где от нее оделяется аммиак в жидком виде, а оставшиеся после реакции компоненты снова идут в производство. Такая особенность технологического процесса вызвана тем, что реакция синтеза аммиака является обратимой и в ходе технологического процесса часть конечного продукта распадается на исходные компоненты.
Таким образом, производство аммиака в промышленности, несмотря на кажущуюся простоту реакции, которая лежит в основе процесса, на самом деле является довольно сложной технологической задачей.
Создание интегрированных производств и разработка новых технологий имеют особое значение
Как уже было сказано выше, технология постоянно совершенствуется и главным направлением мероприятий по ее улучшению является снижение энергоемкости самого процесса. А там, где это сделать по разным причинам сложно, применяются способы утилизации тепла, которое также способно принести пользу. Кроме того некоторые заводы по производству аммиака используют побочные продукты для других химических производств. Так может совмещаться, например, производство метанола и аммиака. Этот способ заключается в том, что из образующегося в ходе риформинга из угарного газа и воды синтезируется метанол.
Также было уже сказано про совмещенное производство аммиака и карбамида. Данное совмещение возможно, например, путем реакции полученного при риформинге углекислого газа с полученным аммиаком. Данный способ, конечно же, требует установки дополнительного оборудования. Тем не менее, он позволяет повысить полезную отдачу конкретного предприятия.
Еще одна особенность производства аммиака в промышленности состоит в том, что его цикличность также способствует и безотходности. Причем в ход идут как полученная энергия, так и побочные продукты. Даже сера, полученная при очистке исходного сырья, находит применение в других химических производствах. Помимо перечисленных мер происходит также постоянный поиск оптимального сочетания давления и температуры, при котором происходит процесс. Ведь от сочетания этих параметров зависит конечный выход основного продукта.
Учитывая все вышесказанное, можно с полной ответственностью сделать вывод,что современный завод по производству аммиака представляет из себя довольно сложный комплекс сооружений. Но в основе такого комплекса всегда состоит установка, разработанная в 1909 году немецким ученым Фрицем Габером, который помимо этого изобретения прославился тем, что стал «отцом химического оружия». По иронии судьбы этот ученый получил Нобелевскую премию Мира. Тем не менее, очевидно, что ценность его вклада в развитие современной химической промышленности сомнению не подлежит.
Таким образом, на примере промышленного производства аммиака можно увидеть, как годами можно совершенствовать, казалось бы, неизменный процесс. Также можно проследить, как одно изобретение может на многие года заложить развитие целой отрасли производства (причем, немаловажной) современного производства.
В настоящее время заводы по производству аммиака расположены по всему миру. Более того: постоянно строятся новые предприятия. Данный факт еще раз подчеркивает важность этого вида химического производства. Ведь во многих регионах земного шара наличие, например, азотных удобрений, стало жизненной необходимостью. Можно привести и много других примеров, но факт остается фактом. Кроме того, огромная часть продукции газодобывающей промышленности востребована именно в производстве аммиака, что позволяет ей устойчиво развиваться. На этих немногочисленных примерах достаточно хорошо видно, что роль производства аммиака переоценить довольно трудно. Поэтому можно сделать вывод, что азотная промышленность будет существовать еще долго, а продукция ее будет всегда пользоваться устойчивым спросом.
Таким образом, говоря о производстве аммиака, следует понимать, что речь идет об очень серьезном производстве, которое оказывает огромное влияние на функционирование различных сфер, как хозяйственной деятельности, так и просто жизни людей. И вполне возможно, что важность данной отрасли в будущем будет расти.
promplace.ru
Современный процесс производства аммиака.
Современный процесс получения аммиака основан на его синтезе из азота и водорода при температурах 380 — 450 0C и давлении 250 атм с использованием железного катализатора:
N2 (г.) + 3h3 (г.) = 2Nh4 (г.)
Азот получают из воздуха. Водород получают восстановлением воды (пара) с помощью метана из природного газа либо из лигроина. Лигроин (нафта) представляет собой жидкую смесь алифатических углеводородов, которая получается при переработке сырой нефти (см. гл. 18).
Работа современного аммиачного завода очень сложна. На рис. 7.2 показана упрощенная схема действия аммиачного завода, работающего на природном газе. Эта схема действия включает восемь стадий.
1-я стадия. Удаление серы из природного газа. Это необходимо, поскольку сера представляет собой каталитический яд (см. разд. 9.2).
2-я стадия. Получение водорода восстановлением пара при 750 0C и давлении 30 атм с помощью никелевого катализатора:
Ch5 (г.) + h3O (г.) = СО (г.) + ЗН 2 (г.)
3-я стадия. Впуск воздуха и сгорание части водорода в кислороде вводимого воздуха:
2h3 (г.) + O2 (г.) = 2h3O (г.) В результате получается смесь водяного пара, моноксида углерода и азота. Водяной пар восстанавливается с образованием водорода, как на 2-й стадии.
4-я стадия. Окисление моноксида углерода, образующегося на стадиях 2 и 3, до диоксида углерода по следующей реакции «сдвига»: СО (г.) + h3O (г.) = CO2 (г.) + h3 (г.)
Этот процесс проводится в двух «реакторах сдвига». В первом из них используется катализатор из оксида железа и процесс проводится при температуре порядка 400 0C Во втором используется медный катализатор и процесс проводится при температуре 220°С.
5-я стадия. Вымывание диоксида углерода из газовой смеси при помощи буферного щелочного раствора карбоната калия или раствора какого-либо амина, например этаноламина Nh3Ch3Ch3OH. Диоксид углерода в конце концов сжижают и используют для производства мочевины, либо выпускают в атмосферу.
6-я стадия. После 4-й стадии в газовой смеси остается еще около 0,3% моноксида углерода. Поскольку он может отравлять железный катализатор во время синтеза аммиака (на 8-й стадии), моноксид углерода удаляют путем конверсии водородом в метан на никелевом катализаторе при температуре 325°С.
7-я стадия. Газовую смесь, которая теперь содержит приблизительно 74% водорода и 25% азота, подвергают сжатию; при этом ее давление возрастает от 25-30 атм до 200 атм. Поскольку это приводит к повышению температуры смеси, ее сразу же после сжатия охлаждают.
8-я стадия. Газ из компрессора поступает теперь в «цикл синтеза аммиака». Схема, приведенная на рис. 7.2, дает упрощенное представление об этой стадии. Сначала газовая смесь попадает в каталитический конвертер, в котором используется железный катализатор и поддерживается температура 380-450°С. Газовая смесь, выходящая из этого конвертера, содержит не более 15% аммиака. Затем аммиак сжижают и направляют в приемный бункер, а непрореагировавшие газы возвращают в конвертер.
Оглавление:
www.himikatus.ru
Производство аммиака: краткая характеристика
Муниципальное образовательное учреждение
Новосафоновская средняя общеобразовательная школа
Производство аммиака: краткая характеристика
Прокопьевский район 2006
Содержание
Введение
1.Способы получения аммиака
2. Современный процесс получения аммиака
Список использованной литературы
Введение
Общей экономической задачей каждого химического предприятия является получение химических веществ высокого качества и в достаточном количестве, чтобы их реализация приносила прибыль. С этим связано требование, чтобы все ресурсы использовались как можно более эффективно. Однако этого можно достичь лишь в том случае, если максимально эффективен сам химический процесс. В химической промышленности вместо понятия «реагенты» гораздо чаще используются термины «исходные материалы», «сырьевые материалы» или просто сырьё», иногда — «руда». Чтобы какой-либо процесс был экономически оправдан, необходимо достичь оптимального выхода целевого продукта из сырьевых материалов. Оптимальный выход не обязательно совпадает с теоретическим выходом или даже с максимально достижимым выходом. Получение максимально достижимого выхода может, например, потребовать слишком большого расхода какого-либо дорогостоящего исходного материала, или же слишком длительного проведения процесса, или же создаются экстремальные условия (очень высокие температуры или давления), чреватые опасными аварийными ситуациями и т.п., — всё это может сделать максимально достижимый выход экономически невыгодным.
Фактический выход каждого конкретного химического процесса может зависеть от целого ряда факторов, главные из них — температура, давление, присутствие катализатора, чистота исходных материалов, эффективность извлечения конечного продукта. Промышленное производство веществ подразумевает отличное знание теоретических закономерностей протекания химических реакций (энергетика химических реакций, химическая кинетика и катализ, химическое равновесие).
Все перечисленные ниже факторы важны, в особенности, если речь идёт о таких многотоннажных производствах, таких, как, например, производство аммиака.
Проектировщики химических предприятий создают сверхмощные установки по производству аммиака. Так, например, созданы установки, производящие 1000-1200 тонн аммиака в сутки. В настоящее время во всём мире ежегодно производится около 5 млн. тонн аммиака.
1. Способы получения аммиака
аммиак цианамидный процесс десульфуратор
Первым промышленным процессом, который использовался для получения аммиака, был цианамидный процесс. При нагревании извести СаО и углерода получали карбид кальция СаС2. Затем карбид нагревали в атмосфере азота и получали цианамид кальция СаСN2; далее аммиак получали гидролизом цианамида:
СаСN2(тв) + 3Н2О = 2NН3↑ + СаСО3(тв)
Этот процесс требовал больших затрат энергии и экономически был невыгоден.
В 1908 г. Немецкий химик Ф. Габер обнаружил, что аммиак можно получать из водорода и атмосферного азота на железном катализаторе. Первый завод по производству аммиака этим методом использовал водород, который получали электролизом воды. В последствии водород стали получать из воды путём восстановления коксом. Такой способ получения водорода намного экономичнее. После открытия Габера стремительно стало расти производство аммиака, это неудивительно, поскольку огромные количества аммиака необходимы для получения азот содержащих удобрений. На изготовление их используется приблизительно 80% всего получаемого в мире аммиака. Вместе с азотсодержащими удобрениями в почву вносится в растворимой форме азот, в котором нуждается большинство растений. Остальные ≈20% производимого аммиака используются для получения полимеров, взрывчатых веществ, красителей и других продуктов.
Современный процесс получения аммиак основан на его синтезе из азота и водорода с использованием специального катализатора:
N2 + 3Н2 ↔ 2NН3 ↑ + 45,9 кДж (1)
Поскольку данная реакция обратимая, возникает вопрос: при каких температурах и давления выгоднее всего добиваться максимального выхода
продукта? Так как реакция экзотермическая, то исходя из принципа Ле Шателье ясно, что чем ниже температура процесса, тем больше равновесие будет сдвигаться в сторону образования аммиака, и можно предположить, что следует максимально понижать температуру. Но в действительности всё обстоит сложнее: при низких температурах реакция практически не идёт, поэтому приходится принимать компромиссное решение. Поскольку для установления оптимального состояния равновесия реакции требуется низкая температура, а для достижения удовлетворительной скорости — высокая температура, на практике процесс проводят при температуре ≈ 400 – 500 оС.
Но даже при такой высокой температуре для достижения достаточной скорости реакции требуется присутствие специального катализатора. В качестве катализатора используется губчатое железо, активированное оксидами калия и алюминия.
Из уравнения реакции видно, что общее число молей уменьшается от 4 до 2. Согласно принципу Ле Шателье в таком случае процесс выгодно проводить, повышая давление. Но этот вывод лишь качественный, анна практике нужно точно знать, насколько увеличится выход NН3 (на 10% или всего на 0,1%) при увеличение давления. В таблице 1 количественно показано влияние температуры и давления на выход аммиака (процентное содержание аммиака в равновесной смеси) по реакции.
Из этой таблицы видно, что повышение температуры при любом давлении заметно снижает содержание аммиака в газовой смеси, однако при температурах ниже 500 оС скорость реакции очень мала, поэтому на практике процесс обычно проводят при температуре 450 оС.
Таблица 1
Что касается давления, то здесь используется давления порядка 300 – 100 атм, но чаще всего «среднее» давление ≈ 250 атм. Хотя при этих условиях только около 20% исходных веществ превращается в аммиак, однако в результате использования циркуляционной технологической схемы (введение непрореагировавших Н2 и N2 вновь в реакцию) суммарная степень превращения исходных веществ в аммиак является очень высокой.
2. Современный процесс получения аммиака
Работа современного аммиачного завода очень сложна. Это утверждение кажется удивительным, если «ориентироваться» только лишь на достаточно просто выглядящее уравнение реакции (1), являющееся основой синтеза аммиака. Однако утверждение о сложности промышленного синтеза аммиака не покажется чрезмерным уже после первого ознакомления со схемой действия аммиачного завода, работающего на природном газе (рис.1). Первая стадия в процессе синтеза аммиака включает десульфуратор. Десульфуратор — техническое устройство по удалению серы из природного газа. Это совершенно необходимая стадия, поскольку сера представляет собой каталитический яд и «отравляет» никелевый катализатор на последующей стадии получения водорода.
Вторая стадия промышленного синтеза аммиака предполагает конверсию метана (промышленное получение водорода). Конверсия метана — это обратимая реакция, протекающая при 700 – 800 оС и давлении 30 – 40 атм с помощью никелевого катализатора при смешивании метана с парами воды:
СН4 + Н2О ↔ СО + 3Н2 (2)
Образовавшийся по данной реакции водород, казалось бы, уже можно использовать для синтеза аммиака по реакции (1) — для этого необходимо запустить в реактор воздух содержащий азот. Так и поступают на стадии (3), однако на этой стадии происходят другие процессы.
Происходит частичное сгорание водорода в кислороде воздуха:
2Н2 + О2 = Н2О(пар)
В результате на этой стадии получается смесь водяного пара, оксида углерода (II) и азота. Водяной пар, в свою очередь, восстанавливается снова с образованием водорода, как на второй стадии по торой стадии по им образом, после первых трёх стадий имеется смесь водорода, азота и «нежелательного» оксида углерода (II).
На рис.1 стадия (4) обозначена как реакция «сдвига», но проходить она может при двух температурных режимах и разных катализаторах. Окисление
СО, образующегося на двух предыдущих стадиях, до СО2 проводят именно по этой реакции:
СО + Н2О(пар) ↔ СО2 + Н2 (3)
Процесс «сдвига» проводят последовательно в двух «ректорах сдвига». В первом из них используется катализатор Fe3О4 и процесс проходит при достаточно высокой температуре порядка 400 оС. Во втором процессе используется более эффективный медный катализатор и процесс удаётся провести при более низкой температуре.
На пятой степени оксид углерода (IV) «вымывают» из газовой смеси при помощи поглощения щелочным раствором:
КОН + СО2 = К2СО3.
Реакция «сдвига» (3) обратимая и после 4-й стадии в газовой смеси на самом деле остаётся ещё ≈ 0,5% СО. Этого количества СО вполне достаточно, чтобы загубить железный катализатор на главной стадии синтеза аммиака(1). На 6-й стадии оксид углерода (II) удаляют реакцией конверсии водородом в метан на специальном никелевом катализаторе при температурах 300 – 400 оС:
СО + 3Н2 ↔ СН4 +Н2О
Газовую смесь, которая теперь содержит ≈ 75% водорода и 25% азота, подвергают сжатию; давление её при этом возрастает от 25 – 30 до 200 – 250 атм. В соответствии с уравнением Клайперона-Менделеева такое сжатие приводит к очень резкому повышению температуры смеси. Сразу же после сжатия приходиться охлаждать до 350 – 450 оС. Именно этот процесс и описывается с точностью реакцией (1).
Список использованной литературы
1.Н.Е. Кузьменко, В.В. Ерёмин, В.А. Попков. Химия. Теория и задачи. — М.: ОНИКС 21 век», «Мир и образование», 2003.
mirznanii.com
Тема №7: Производство аммиака.
Перечислите основные способы фиксации азота.
Под фиксацией азота понимаются реакции в ходе которых молекулярный азот образует различные соединения— например, реакция образования аммиака при взаимодействии азота с водородом.
Интересы ученых-биологов сфокусированы на конкретных научных направлениях, из которых можно выделить следующие:
1) поиск новых микробно-растительных азотфиксирующих сообществ и определение их роли в глобальной азотфиксирующей системе планеты;
2) исследование молекулярных механизмов взаимоотношения растений и азотфиксирующих микроорганизмов;
3) исследование физических и физико-химических основ явления азотфиксации;
4) изучение генетики азотфиксации и создание генноинженерным путем азотфиксирующих растений;
5) разработка комплекса агробиологических технологий с целью повышения продуктивности азотфиксации в растениеводстве.
Как изменилась структура сырьевой базы по мере развития азотной промышленности? Какой вид природного сырья находил практическое применение вначале для получения технологического сырья?
В чем преимущество природного газа перед другими видами природного сырья?
Преимущество природного газа(СН4):
Горение метана сопровождается незначительным выделением загрязняющих веществ, как твердых пылевых, так и газообразных: окисей азота, серы и углерода.
Метан может служить промежуточным топливом при постепенном переходе на такие альтернативные источники электроэнергии, как ветер, солнечная энергия, гидроэлектрическая энергия, энергия приливов и геотермальные источники энергии.
Метан широко распространен и доступен в большинстве городов и населенных пунктов, в непосредственной близости от конечных потребителей электроэнергии. Это значит, что для таких электростанций проще подобрать место, и они не требуют протяженных линий высоковольтных передач.
Электростанции смешанного типа, работающие на метане, достаточно эффективны.
Постоянное снабжение метаном можно организовать с помощью подземных газопроводов, экономя на энергопотреблении поездов и грузовиков, доставляющих горючее от перерабатывающего завода на электростанцию.
Электростанции, работающие на метане, можно переоборудовать для использования водорода в качестве топлива, когда водород будет доступен в достаточных количествах по приемлемым ценам.
Составьте химическую и функциональную схемы получения технологического газа для синтеза аммиака из природного газа.
Химическая схема:
Функциональная схема:
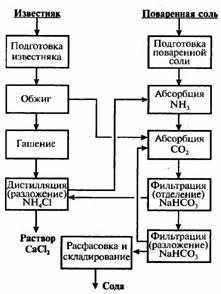
Функциональная схема синтеза аммиака: А – синтез Nh4; Б – выделение Nh4; В – компрессия и рециркуляция
Почему необходима очистка природного газа от сернистых соединений? Как и при каких условиях она осуществляется?
Очистка природного газа от серосодержащих соединений адсорбцией сероводорода, который мешает дальнейшим превращениям:
h3S + ZnO = ZnS + Н20
Конверсия метана с водяным паром. И природный газ (СН4), и вода (Н2О) являются сырьем для получения одного из компонентов для синтеза аммиака – водорода Н2. В этом превращении протекают одновременно две реакции:
СН4 + Н2О = СО + ЗН2;
СО + Н2О = СО2 + Н2.
Конверсия оксида углерода с водяным паром (в предыдущем процессе оксид углерода СО не полностью превращается в СО2 из-за равновесных ограничений):
СО + Н2О = СО2 + Н2.
После этого процесса достигается максимально возможное извлечение водорода из исходного сырья – метана СН4 и воды Н2О.
Проанализируйте химическую и функциональную схемы сероочистки.
Какими соображениями руководствуются при выборе технологического режима основных стадий паровоздушной конверсии природного газа?
Какие катализаторы применяют на стадии конверсии метана и оксида углерода? Какие примеси в газе вызывают отравления катализаторов? Каков срок их службы?
Все реакции протекают с участием катализаторов и при высоких температурах. При осуществлении процесса конвекции СН4 проводят очистку природного газа от соединений серы, которые являются каталитическими ядами, а также очистку азотоводородной смеси от оксидов углерода.
Конверсию метана осуществляют при температуре 800-900 °С на никелевом катализаторе.
Что собой представляют отходящие газы агрегатов синтеза аммиака? Как осуществляется их очистка?
Конвертированный газ, получаемый после конверсии метана, содержит 20-40% оксида углерода.
Для увеличения выхода водорода, газ после конверсии метана восстанавливают водяным паром.
Какие методы нашли практическое применение для очистки конвертированного газа от диоксида углерода? Перечислите их достоинства и недостатки.
Напишите химические реакции, лежащие в основе моноэтаноламиновой очистки. Что является побочным продуктом процесса и какое практическое применение он находит?
Абсорбция диоксида углерода – удаление СО2, полученного при получении водорода. Его поглощают раствором моноэтаноламина:
СО2 + 2RNh3 + Н2О = (RNh4)2CО3.
Обоснуйте выбор технологического режима на стадиях абсорбции CO2 и регенерации растворителя в процессе моноэтаноламиновой очистки технологического газа.
МЭА очистка – низкая стоимость, стабильность процесса, легко регенерируется, высокая поглотительная способность. При очистке газа 17-21% раствором МЭА идет 2 реакции:
2NOCH2CH2NH2+CO2+H2O=(RNH3)2CO3;
(RNH3)2CO3+CO2+H2O=2RNH3HCO3.
Какие методы очистки от оксида углерода применяют в современных технологических установках производства синтез-газа?
Очистка газа от оксида углерода СО. После конверсии СО небольшое количество СО остается, и он мешает дальнейшим превращениям. Освобождаются от него, превращая в метан:
СО + ЗН2= СН4+ Н2О.
Как осуществляется тонкая очистка конвертированного газа от оксидов углерода?
Селективными являются железо-хромовый и медьсодержащий катализаторы: первый обеспечивает достаточную скорость реакции при температуре 450-500 °С, второй активно работает при 250-300°С. Остаточная концентрация СО составляет 0,3-0,5%.
После очистки газа от оксидов углерода он поступает на синтез аммиака.
Назовите важнейшие области применения аммиака.
Аммиак относится к числу важнейших продуктов химической промышленности, ежегодное его мировое производство достигает 150 млн тонн. В основном используется для производства азотных удобрений (нитрат и сульфат аммония, мочевина), взрывчатых веществ и полимеров, азотной кислоты, соды (по аммиачному методу) и других продуктов химической промышленности. Жидкий аммиак используют в качестве растворителя.
В холодильной технике используется в качестве холодильного агента (R717)
В медицине 10 % раствор аммиака, чаще называемый нашатырным спиртом, применяется при обморочных состояниях (для возбуждения дыхания), для стимуляции рвоты, а также наружно — невралгии, миозиты, укусах насекомых, для обработки рук хирурга. При неправильном применении может вызвать ожоги пищевода и желудка (в случае приёма неразведённого раствора), рефлекторную остановку дыхания (при вдыхании в высокой концентрации).
Применяют местно, ингаляционно и внутрь. Для возбуждения дыхания и выведения больного из обморочного состояния осторожно подносят небольшой кусок марли или ваты, смоченный нашатырным спиртом, к носу больного (на 0,5-1 с). Внутрь (только в разведении) для индукции рвоты; также, в составе нашатырно-анисовых капель — в качестве муколитического (отхаркивающего) средства. При укусах насекомых — в виде примочек; при невралгиях и миозитах — растирания аммиачным линиментом. В хирургической практике разводят в тёплой кипяченой воде и моют руки.
Поскольку аммиак является слабым основанием, при взаимодействии с кислотами он их нейтрализует.
Физиологическое действие нашатырного спирта обусловлено резким запахом аммиака, который раздражает специфические рецепторы слизистой оболочки носа и способствует возбуждению дыхательного и сосудодвигательного центров мозга, вызывая учащение дыхания и повышение артериального давления.
Противоморозная добавка для сухих строительных растворов, относящаяся к ускорителям. Рекомендуемая дозировка — 2…8 % массы компонентов сухой смеси в зависимости от температуры применения. Аммиачная вода — продукт (Nh4*h3O), представляющий собой газообразный аммиак NН3, растворенный в воде.
Составьте функциональную схему синтеза аммиака.
Агрегат синтеза аммиака (технологическая схема).
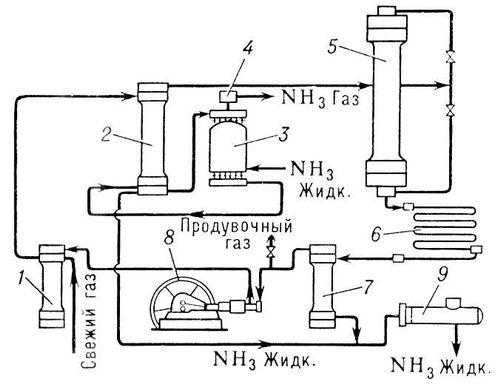
Каковы основные физико-химические особенности реакции синтеза аммиака из азота и водорода, влияющие на выбор технологического режима процесса? Учитывая эти особенности, обоснуйте выбор давления, температурного режима процесса, тип технологической схемы.
Какими соображениями руководствуются при выборе объемной скорости газа в колоннах синтеза аммиака?
Объясните механизм гетерогенно-каталитического процесса синтеза аммиака. Какими стадиями он может быть описан?
Какие катализаторы применяют при синтезе аммиака?
При синтезе аммиака из простых веществ — азота и водорода — используют в качестве катализатора используют пористое железо с примесями Al2O3 и K2O
Какие методы выделения аммиака из циркуляционного газа применяют в установках среднего давления?
Циркуляционный газ при температуре 50°С поступает в систему вторичной конденсации, включающую конденсационную колонну и испарители жидкого аммиака. В конденсационной колонне газ охлаждается до 18°С и в испарителя за счет кипения аммиака в межтрубном пространстве до — 5°С. Из трубного пространства испарителей смесь охлажденного циркуляционного газа и сконденсировавшегося аммиака поступает в сепарационную часть конденсационной колонны, где происходит отделение жидкого аммиака от газа и смешение свежей азотоводородной смеси с циркуляционным газом. Далее газовая смесь проходит корзину с фарфоровыми кольцами Рашига, где отделяется от капель жидкого аммиака, поднимается по трубкам теплообменника и направляется в выносной теплообменник, а затем в колонну синтеза.
Что собой представляют продувочные и танковые газы? Какое применение они находят?
Объясните устройство колонны синтеза. Проанализируйте режим ее работы.
Принципиальная технологическая схема синтеза аммиака в агрегате мощность 1360 т/сут на отечественном оборудовании.
Свежая азотоводородная смесь после очистки метанированием сжимается в центробежном компрессоре до давления 32 Мпа и после охлаждения в воздушном холодильнике поступает в нижнюю часть конденсационной колонны для очистки от остаточных примесей СО3, Н2О и следов масла. Свежий газ барботирует через слой сконденсировавшегося жидкого аммиака, освобождается при этом от водяных паров и следов СО2. и масла, насыщается аммиаком до 3-5% и смешивается с циркуляционным газом. Полученная смесь проходит по трубкам теплообменника конденсационной колонны и направляется в межтрубное пространство выносного теплообменника, где нагревается до 185-1950°С за счет теплоты газа, выходящего из колонны синтеза. Затем циркуляционный газ поступает в колонны синтеза.
Сформулируйте основные требования к колоннам синтеза аммиака.
Какие технологические мероприятия способствуют охране окружающей среды в производстве аммиака?
Крупнотоннажное производство аммиака характеризуют следующие выбросы в окружающую среду:
1) газовые, содержащие в своем составе аммиак, оксиды азота и углерода и другие примеси
2) сточные воды, состоящие из конденсата, продуктов промывки реакторов и систем охлаждения;
3) низко потенциальную теплоту.
Относительная концентрация токсичных примесей производства аммиака в виде оксида углерода и оксидов азота в отходящих газах невысока, но когда происходит восстановление оксидов азота до элементного азота, для устранения даже незначительных выбросов разрабатываются специальные мероприятия. Полное исключение токсичных выбросов возможно при использовании каталитической очистки в присутствии газа-восстановителя.
studfiles.net
Производство аммиака
ОГЛАВЛЕНИЕ
1. Введение
2. Характеристика исходного сырья
З. Характеристика целевого продукта
4. Физико-химические основы процесса
5. Технологическое оформление процесса синтеза аммиака
6. Охрана окружающей среды в производстве аммиака
Список использованной литературы
1. Введение
Во всех индустриально развитых странах азотная промышленность является в настоящее время одной из основных ведущих отраслей. Доказательством этого служат цифры, характеризующие стремительный рост производство связанного азота. В 1955г во всем мире было произведено аммиака около 8 млн. т, в 1965г — 20 млн. т, в 1975г — 66 млн. т, в 1980г — 100 млн. т, в 1985 — 120 млн. т.
Такое бурное развитие азотной промышленности диктуется в первую очередь необходимостью удовлетворения неудержимо растущего населения земного шара продуктами земледелия. Без минеральных удобрений, и в первую очередь азотных, невозможно решить задачи интенсификации сельского хозяйства.
Производству азотных удобрений и их основы, аммиака, в нашей стране всегда уделялось первостепенное внимание. Среднегодовой прирост темпа аммиака за последние 20 лет составлял 10-19%.
Производство аммиака, как известно, отличается большой энергоемкостью. Историю развития производства аммиака можно рассматривать как борьбу за повышение полезного использования электрической, тепловой, и механической энергии. На первых установках производства аммиака к. п. д. на превышал 10-11%. Использование природного газа в производстве аммиака увеличило общий энергетический к. п. д. до 40%. Современные энерготехнологические агрегаты аммиака практически автономны и имеют производительность 450-500 тыс. т. в год и общий энергетический к. п. д.50-52%. Это обеспечено достижениями химической технологии, химического и энергетического машиностроения, металлургической и приборостроительной промышленности, а также высокой квалификацией строителей, монтажников, эксплуатационников.
2. Характеристика исходного сырья
Сырьем для получения продуктов в азотной промышленности является атмосферный воздух и различные виды топлива.
В число постоянных составляющих воздуха входят следующие газы (в% по объему): азот — 78,16; кислород — 20,90; аргон — 0,93; гелий, неон, криптон, ксенон и другие инертные газы — 0,01. В технических расчетах принимают, что воздух содержит 79% азота и 21% кислорода.
Для синтеза аммиака в некоторых схемах необходима азотоводородная смесь в соотношении N2: h3=1: 3. Азот получают разделением воздуха или же совместно с водородом в виде азотоводородной смеси. В других схемах используют и чистый жидкий азот для тонкой очистки синтез — газа от вредных примесей, и газообразный, вводя его в строго корректируемом соотношении в конвертированный газ. В последнем случае воздух подвергают разделению методом глубокого охлаждения.
Поскольку ресурсы атмосферного азота огромны, то сырьевая база азотной промышленности в основном определяется вторым видом сырья — топливом, применяемым для получения водорода или водородсодержащего газа.
В настоящее время основным сырьем в производстве аммиака является природный газ.
Синтез-газ из твердых топлив. Первым из основных источников сырья для получения синтез — газа явилось твердое топливо, которое перерабатывалось в газогенераторах водяного газа по следующим реакциям:
C+h3O ↔ CO +h3; ΔH>0
C+O2 ↔CO2; ΔH<0
Такой способ получения заключается в попеременной подаче через слой крупнокускового твердого топлива (антрацита, кокса, полукокса) воздушного и парового дутья. Синтез — газ получают на стадии парового дутья, а необходимая температура слоя топлива достигается в течение стадии воздушного дутья. Цикл работы генератора составляет 3-5 мин. Полученный водяной газ содержит 50-53% Н2 и ~365 СО.
Для дальнейшего использования в производстве водяной газ необходимо очистить от сернистых соединений и провести конверсию оксида углерода по реакции:
CO+h3O↔CO2+h3; ΔH<0
а затем удалить диоксид углерода полностью в случае его применения для синтеза аммиака.
Недостатками процесса являются его периодичность, низкая единичная производительность газогенератора, а также высокие требования к сырью по количеству и температуре плавления золы, его гранулометрическому составу и другим характеристикам.
Другим направлением является газификация топлива в виде пыли. Этот процесс позволяет использовать практически любые виды топлива. Его особенностями является высокая турболизация в зоне реакции за счет подачи встречных потоков топливной смеси и хорошее смешение парокислородной смеси с топливной пылью.
Синтез — газ из жидких углеводородов. По технологическим схема переработки в синтез — газ жидкие топлива можно разделить на две группы. Первая группа включает топливо, перерабатываемые высокотемпературной кислородной конверсией. Сюда относятся тяжелые жидкие топлива — мазут, крекинг — остатки и т.п. Вторая группа — легкие прямоточные дистилляты (нафта), имеющие конечную температуру кипения не выше 200-220°С; она включает бензин, лигроины, смеси светлых дистиллятов. Вторая группа жидких топлив перерабатывается в синтез — газ каталитической конверсией водяным паром в трубчатых печах.
Достоинством этого метода является возможность получения синтез — газ под давлением, легкость регулирования состава синтез — газа, малый расход электроэнергии. К недостаткам можно отнести высокие требования к углеводородному составу исходного сырья по содержанию в нем непредельных и циклических углеводородов, серы и других примесей, большой удельный расход углеводородов.
Синтез-газ из природного газа. Синтез — газ из углеводородных газов (природного, попутного, газов переработки других топлив) в настоящее время является основным источником получения аммиака. По использованию окислителя и технологическому оформлению можно выделить следующие варианты процесса получения водородосодержащих газов:
высокотемпературная кислородная конверсия, каталитическая парокислородная конверсия в шахтных реакторах, каталитическая паро-углекислотная конверсия в трубчатых печах.
Окисление метана (основного компонента углбеводородных газов) при получении синтез — газа протекает по следующим основным суммарным реакциям:
Ch5+0,5O2 = CO+2h3; ΔH=-35,6 кДж
Ch5+h3O = CO+3h3; ΔH=206,4 кДж
Ch5+CO2 = 2CO+2h3; ΔH=248,3 кДж
Аналогичным образом осуществляются реакции окисления гомологов метана.
Физические постоянные № 2.
Молекуляр. вес | Мольный объем | 760 мм рт ст | Критические константы | |||
(0 С, 760 мм рт ст) | Тпл | Ткип | Ткр 0С | Ркр атм | Vкрсм3/моль | |
28,0134 | 22403 | -210 | -195 | -47,0 | 33,5 | 90,1 |
Физические постоянные h3
Молекуляр. вес | Мольный объем | 760 мм рт ст | Критические константы | |||
(0 С, 760 мм рт ст) | Тпл | Ткип | Ткр 0С | Ркр атм | Vкрсм3/моль | |
2,0149 | 22412 | -259,2 | -252,5 | -239,9 | 12,8 | 65,0 |
З. Характеристика целевого продукта
Аммиак в обычных условиях представляет собой бесцветный газ с резким запахом. Хорошо растворим в воде и других растворителях, образует геми — и моногидраты. В жидком состоянии аммиак — бесцветная подвижная ассоциированная жидкость, практически не проводить электрического тока.
Физические постоянные аммиака.
Молекуляр. вес | Мольный объем | 760 мм рт ст |
coolreferat.com