Производство батарей аккумуляторных батарей – Бизнес на производстве аккумуляторов (февраль 2019) — как открыть с нуля, примеры и готовый план с расчетами для начинающих
Производство АКБ — современные технологии в действии
Можно отметить растущий интерес потребителей к гибридной технике и электромобилям. Но на данный момент батареи для тяговых электроприводов пока еще не получили массовое распространение. Общее соотношение между электромобилями и автомобилями с ДВС остается ничтожно малым. Поэтому традиционные АКБ для автомобилей с бензиновыми и дизельными двигателями будут оставаться актуальными еще на протяжении многих лет.
Аккумулятор «устал»
Аккумулятор или стартерная батарея выполняет в конструкции автомобиля функцию накопителя электрической энергии. Вопреки названию «стартерная батарея» электроэнергия в современном автомобиле расходуется не только на запуск двигателя. С каждым годом количество электронных систем в конструкции автомобиля увеличивается, следовательно, растет число потребителей энергии. Нередко возникает ситуация, в которой общее потребление одновременно включенных электронных систем превышает мощность генератора, работающего в определенном режиме. Чаще всего такая ситуация возникает при работе двигателя на холостом ходу. Применение микропроцессорных систем породило еще одно применение аккумулятора – теперь за счет накопленной энергии гасятся скачки напряжения, которые могут быть вредны для сложных электронных компонентов, таких как шаговые электромоторы или полупроводники.
Все это стало причиной повышения требований к аккумуляторам, в том числе со стороны потребителей. Если раньше севший аккумулятор становился для автолюбителя лишь причиной проблем с запуском двигателя, то сейчас круг негативных последствий такого происшествия заметно расширился. Достаточно вспомнить о том, что некоторые современные автомобили не рекомендуется «прикуривать», в то время как на некоторых других распространенных моделях даже банальная замена АКБ требует изменения настроек в электронных модулях с помощью специального сервисного оборудования. Дополнительные неудобства доставляет «поведение» современных электронных охранных систем при разрядке батареи. В то же время при современном ритме городской жизни слишком короткие поездки не позволяют зарядить аккумулятор до полного восстановления емкости.
К сожалению, многие автолюбители, даже лично столкнувшись с проблемами в работе АКБ, не делают надлежащих выводов и при замене часто выбирают продукт, который не отвечает в полной мере условиям эксплуатации. Основных причин здесь две: естественная тяга к экономии и лень, мешающая разобраться в проблеме выбора действительно подходящего для их автомобиля аккумулятора. Поэтому при выборе автолюбители часто руководствуются иррациональным желанием не выходить за рамки определенной суммы, критериями, которые устарели еще в двадцатом веке, и неквалифицированными советами, основанными на заблуждениях.
Подобные подходы к выбору АКБ совершенно неприемлемы при современном уровне развития автомобилей, буквально начиненных электронными устройствами. Соответственно, крупнейшие производители рекомендуют выбирать батарею исходя из условий применений. Для старых моделей автомобилей с малым количеством дополнительного электрического оборудования предназначены одни АКБ, а для современных автомобилей премиум-класса с большим количеством электроники – другие.
Например, линейка аккумуляторных батарей Bosch представлена тремя цветами этикетки: серым, синим и черным. Серая этикетка, линейка S3, подскажет, что данные аккумуляторы можно устанавливать на подержанные автомобили с небольшим уровнем энергопотребления. Аккумуляторы серии S4 с синей этикеткой подходят для автомобилей среднего ценового сегмента с повышенным потреблением электроэнергии, в том числе и для азиатских моделей. Для автомобилей с высоким уровнем энергопотребления Bosch предлагает линейку S5 с черной этикеткой. Дополнительные пиктограммы на этикетках этих АКБ помогут автолюбителям сделать правильный выбор нужной батареи.
А они у вас «свежие»?
Еще одним из распространенных заблуждений потребителей является зависимость срока службы аккумулятора от даты производства.
Как известно, заблуждения никогда не возникают на пустом месте. Хотя аккумулятор – не скоропортящийся продукт, как йогурт, например, еще пятнадцать – двадцать лет назад вопрос «свежести» при его покупке был актуален. Современные АКБ являются необслуживаемыми – это значит, что они не требуют контроля состояния электролита, в том числе при подзарядке. В прежние же времена наиболее распространенными были обслуживаемые свинцовые аккумуляторы, имевшие тенденцию к значительному саморазряду. Он является следствием гальванических процессов внутри аккумулятора. Процессы возникают из-за наличия посторонних примесей в свинце, из которого сделаны электроды, и в электролите. Нормальный саморазряд таких АКБ обычно не превышает 0,7 – 1% емкости в сутки, однако и этого достаточно, чтобы после хранения на складе производителя, транспортировки и нахождения в магазине аккумулятор нуждался в подзарядке сразу после покупки. 2-3 месяца на полке – и батарея оказывалась практически полностью разряженной. Естественно, что основной «недуг» аккумуляторов – сульфатация пластин – прогрессировал при длительном хранении и отсутствии подзарядки, что и побуждало наших родителей искать «свежие» аккумуляторы.
Сейчас автомобили практически не комплектуются обслуживаемыми свинцовыми батареями. Дело в том, что помимо регулярной подзарядки в случае, если автомобиль не используется, они требуют периодического технического обслуживания. Уровень электролита в процессе саморазряда падает, поэтому в обслуживаемый аккумулятор необходимо время от времени подливать дистиллированную воду. Затем необходимо проверить плотность электролита, при необходимости добавить серной кислоты…
Современного автолюбителя трудно представить себе в гараже, в окружении банок с серной кислотой и в защитных очках. По этой причине производители, чутко реагирующие на изменение конъюнктуры, постоянно работают над улучшением характеристик аккумуляторов, особенно, в отношении склонности к саморазряду. Приобретая современный аккумулятор от известного производителя, вы получаете почти необслуживаемое устройство, не требующее в процессе эксплуатации практически никаких манипуляций. Обратите внимание, что термин «необслуживаемый аккумулятор» подразумевает, что в него не надо доливать воду на протяжении всего периода эксплуатации. Однако это не исключает контроль состояния заряженности и подзарядки АКБ в случае необходимости.
«Бывалые» автолюбители порой жалуются, что теперь не могут заглянуть внутрь АКБ, использовать ареометр для измерения плотности, следить за состоянием электролита. Но современные технологии как раз и призваны избежать любых проблем, связанных с обслуживанием АКБ.
Какими бывают современные аккумуляторы?
Одно из основных достижений последних двух десятилетий – применение в производстве аккумуляторов сплава свинца с каким-либо другим элементом, позволяющим значительно снизить деградацию решеток-электродов при контакте с электролитом. Используемые добавки придают различные свойства решеткам. В настоящее время при промышленном производстве используется несколько сплавов свинца с другими элементами, каждый из которых обладает своими достоинствами и недостатками. Деление аккумуляторов на необслуживаемые и частично обслуживаемые – результат применения различных сплавов с их специфическими свойствами.
В принципе, ограниченное количество элементов, используемых в сплаве со свинцом, известно уже давно. Это сурьма и кальций, которые применяются в сплавах в различных пропорциях. Существуют также «гибридные» сплавы, в которых присутствуют оба элемента. Состав и процентное содержание добавки в сплаве существенно влияет на его свойства. Можно сказать, что их применение и стало тем толчком, за которым последовало бурное технологическое развитие, приведшее к появлению аккумуляторов, не нуждающихся в обслуживании на протяжении всего срока эксплуатации.
Производство положительных и отрицательных решеток-электродов, основного элемента конструкции аккумулятора, из сплавов позволило изменить их прочность, что привело к упрощению и удешевлению производства. Появление решеток из сплавов позволило избавиться от некоторых недостатков, свойственных аккумуляторам старого образца. В первую очередь, от возникновения коротких замыканий между электродами в результате их деформации и последующего соприкосновения. Результатом стало существенное увеличение срока службы при почти полном отсутствии обслуживания.
Решетки из свинцово-сурьмяного сплава изготавливаются методом литья под давлением. Это позволяет добиться достаточно высокой точности производства, поэтому большинство аккумуляторов начала 2000-х годов обладали свинцово-сурьмяными решетками. К сожалению, протекание гальванических процессов приводит к тому, что сурьма постепенно выделяется из положительных электродов в результате коррозии, что постепенно приводит к деградации аккумулятора, выраженной в потере емкости.
Недостатки свинцово-сурьмяного сплава побудили производителей искать новые элементы, позволяющие улучшить эксплуатационные характеристики. Выяснилось, что повысить жесткость аккумуляторных решеток можно, если добавить в сплав полтора процента кадмия, а для уменьшения коррозии в сплав добавляют кальций и олово. Однако выяснилась и одна неприятная деталь – использование кальция сопряжено с технологическими трудностями из-за свойства кальция выгорать при изготовлении решеток методом литья. Выход из ситуации был найден – вместо литья при производстве решеток начали использовать технологию просечки-растяжки, а затем и технологию штамповки, при которой из сплава формируется сплошная лента, которую позже подвергают перфорированию. Помимо прочего, штамповка позволяет сохранить внешнюю рамку пластин и делать более сложную оптимизированную форму решетки. Это особенно актуально для пластин положительных электродов, на которые приходятся основные нагрузки. В частности, подобная технология используется на АКБ Bosch с технологией PowerFrame.
Однако в связи со сложностью в производстве решеток с добавлением кальция, свинцово-сурьмяной сплав не стал «технологией прошлого». В настоящий момент необслуживаемые аккумуляторы производятся как на основе решеток с пониженным содержанием сурьмы, так и на основе решеток из свинцово-кальциевого сплава. Многие аккумуляторы изготавливаются с применением обоих типов решеток: у гибридов для производства положительных решеток используется сплав свинец-кальций, тогда как отрицательные решетки делаются из сплава свинца с сурьмой.
Кроме того, для защиты пластин АКБ применяются специальные сепараторы-конверты, которые препятствуют осыпанию активной массы, приводящей к короткому замыканию.
Аккумуляторы класса «премиум»
Дальнейшее развитие технологии производства аккумуляторов связано с совершенствованием как сплава для производства решеток, так и конструкции всего изделия. Безусловно, «венцом творения» на данный момент можно считать полностью необслуживаемые аккумуляторы, к примеру, топовые батареи S5A с технологией AGM производства компании Bosch (раньше назывались S6).
В аккумуляторах класса «премиум» применяется технология Absorbent Glass Mat (AGM). Ее использование дало возможность существенно увеличить число циклов разряд/заряд. В соответствии с технологией AGM в конструкции аккумулятора используются специальные сепараторы из стекловолокна, которые полностью впитывают в себя электролит. Таким образом, он находится в нетекучем состоянии. Микропоры материала заполнены электролитом не полностью. Свободный объем используется для рекомбинации газов, что позволило сделать корпус аккумулятора полностью герметичным. Применение технологии AGM обеспечивает хорошую устойчивость аккумулятора к вибрации и наклону. Глубокий разряд не приводит к необратимым последствиям для батарей Bosch S5A.
Аккумуляторы с технологией AGM часто путают с гелевыми, в которых электролит находится в состоянии геля. Основными достоинствами этих аккумуляторов также являются возможность использования батареи при любом ее положении в пространстве, устойчивость к вибрациям, а также то, что даже при повреждении корпуса батареи электролит не вытекает наружу. Однако технология AGM является более совершенной, так как электролит в свободной форме обладает преимуществами в эксплуатации. У гелевых аккумуляторов скорость химических реакций ниже, кроме того, они не переносят сильных морозов. Таким образом, АКБ с технологией AGM обладают всеми достоинствами гелевых, при этом недостатки последних в них отсутствуют.
Как долго можно хранить современный аккумулятор?
Из-за низкого саморазряда все полностью необслуживаемые аккумуляторы заполняются электролитом в условиях производства и герметизируются. Это позволяет избежать опасных утечек кислоты и необходимости в обслуживании. Конструкция герметизированных аккумуляторов подразумевает длительное хранение батареи в заряженном состоянии. Если батарея долго не используется, достаточно изредка проверять уровень ее напряжения. Для напоминания об этом на обновленных этикетках всех АКБ Bosch нанесены соответствующие пиктограммы – напряжение разомкнутой цепи должно составлять не менее 12,4 В, в противном случае необходимо произвести зарядку АКБ. Это не потребуется выполнять чаще, чем раз в полгода. А при хранении аккумулятора в соответствующих условиях – сухих прохладных местах с температурой от 0 до +15°С – интервал может увеличиваться вплоть до 12 месяцев для АКБ с гибридными решетками и до 18 месяцев для батарей на основе решеток из свинцово-кальциевого сплава. Таким образом, аккумулятор, произведенный год назад, хранившийся в надлежащих условиях и прошедший хотя бы один цикл обслуживания, в силу своей конструкции и герметичности может спокойно храниться второй год до новой подзарядки и так далее. В этой связи поиски «свежего» аккумулятора теряют свою актуальность и всякий смысл.
В качестве итога хотелось бы отметить следующие моменты:
- Выбирать подходящий аккумулятор нужно исходя из модели и модификации автомобиля, а также условий его эксплуатации. При этом предпочтение стоит отдавать продукции крупных мировых производителей, таких как Bosch. Для облегчения поиска информации Bosch указывает на этикетках соответствующие обозначения и пиктограммы (например, АКБ для систем «Start-Stop», тип автомобиля, режим эксплуатации ТС, минимальное значение напряжения АКБ для зарядки и др.).
- Современные аккумуляторы в процессе хранения и эксплуатации не требуют практически никаких манипуляций. Достаточно лишь осуществлять контроль над показателем напряжения батареи и подзаряжать ее в случае необходимости.
- Дата производства для современных необслуживаемых аккумуляторов не является важным показателем.
- При любых сомнениях в выборе подходящей АКБ нужно обратиться к специалистам. Они поделятся информацией по применяемым технологиям и помогут сделать правильный выбор нужного аккумулятора.
a-kt.ru
Какие заводы производят аккумуляторы в России.
Прежде чем начать цикл статей с обзором аккумуляторов, кратко ознакомимся с российскими производителями аккумуляторных батарей для автотранспорта.
Российская аккумуляторная промышленность относится к числу лидеров по скорости развития. Это связано с тем, что всё большее количество батарей используется для комплектации автомобилей как российских, так и иностранных моделей.
По качеству продукция российских производителей АКБ оценивается на среднеевропейском уровне, поэтому зарубежные европейские и азиатские партнеры используют наши батареи для укомплектования своей автомобильной продукции.
Россия равномерно распределяет продукцию на экспорт и внутренние нужды. Половина батарей российских производителей отправляется за рубеж, остальные же остаются на внутреннем рынке.
Итак, в список основных производителей аккумуляторов входят:
ЗАО МПКФ «АЛЬКОР»
Проходя по цехам завода Алькор сейчас, сложно себе представить, что становление началось в далёком 90-м году с аренды 10 кв. метров под офис, маленького кооператива «Пластик», где изготавливали вёдра, горшки для рассады и даже мебельные выдвижные ящики.
Но вскоре купили кооператив «Борн», основным видом деятельности которого являлась отвёрточная сборка аккумуляторных батарей из комплектующих Тюменского аккумуляторного завода. Для реализации продукции создали торговую сеть на территории России.
Вскоре кооперативы реорганизовались в товарищество «Алькор», а позднее в закрытое акционерное общество – многопрофильную коммерческую фирму. С этого момента и началось его развитие.
В 2003-04гг. запущены цеха по формированию батарей и очистные сооружения, затем сборочный цех, а также участки приготовления очищенной воды и высококачественных электролитов. О электролитах можно почитать здесь.
В 2009 году завод приступил к выпуску АКБ в гибридном исполнении.
Производственный цикл завода оснащен современными технологиями ведущих мировых фирм, производящих аккумуляторное оборудование.
Изготовление непрерывной свинцово-кальциевой ленты литьевым методом с последующим перфорированием и растягиванием позволило производить прочные качественные электроды для широкой линейки АКБ.
Повышенная коррозионная стойкость электродов новыми оловянно-кальциевыми сплавами.
Современное оборудование позволило автоматизировать трудоёмкий процесс и выполнять все технологические операции с высокой точностью.
Автоматическая отбраковка позволяет производить контроль всех производственных операций и выпускать только качественные и надежные аккумуляторы.
Сегодня на рынке представлены торговые марки: TYUMEN BATBEAR (21 модель), Аrctic Batbear (17 моделей), Тюменский медведь (33 модели), Ямал (22 модели), Space CA/CA (55 моделей), Buran Ca/Ca (11 моделей), Тюменский медведь Ca/Ca (59 моделей). Подробней о продукции компании АЛЬКОР можно прочесть в отдельной статье.
Аккумуляторные технологии (АкТех)
История завода прослеживается с 1938 года, когда в г. Свирск построили аккумуляторный завод «ВостСибЭлемент».
В период 1996-98гг. завод разделился на три небольшие компании и производство аккумуляторов в небольших объёмах возобновилось под различными торговыми марками.
В 1999 году в цехе серебряно-цинковых батарей на оборудовании EXIDE возобновлен полный технологический цикл. С этого времени появилось название «АККУМУЛЯТОРНЫЕ ТЕХНОЛОГИИ (АКТЕХ)».
С 2002 года начались поставки для Ижевского, Горьковского, Волжского автомобильных заводов.
С 2003 года «АкТех» становится первым представителем России в европейской ассоциации производителей АКБ — EUROBAT. Кампания запускает торговую марку «Зверь» с кремниевой технологией «SiO2-эффект», заключен контракт с Министерством Обороны РФ на поставку аккумуляторной продукции для военной техники.
В 2006 году начато производство аккумуляторных батарей по гибридной технологии Кальций Плюс (Ca/Sb).
В настоящее время для легковых автомобилей выпускаются аккумуляторы марок ЗВЕРЬ, ЗВЕРЬ Asia, DUO EXTRA, R-Line, AKTEX EXTRA, AKTEX EXTRA ASIA, АКТЕХ, АКТЕХ в низком корпусе, АКТЕХ Asia, АКТЕХ CLASSIC, AKTEX CLASSIC ASIA, Crossfire, SOLO, SOLO в низком корпусе, SOLO Asia, ОРИОН, АКТЕХ ECO, VSA, HIBREED, ActiveFrost, SmartElement, Spark, Пульс.
Для грузовых автомобилей — ЗВЕРЬ ТТ, AKTEX EXTRA TT, DUO EXTRA TT, R-Line TT, АКТЕХ ТТ, AKTEX CLASSIC TT, Crossfire TT, SOLO ТТ, ОРИОН ТТ, AKTEX ECO TT, VSA TT, HIBREED TT, ActiveFrost TT, SmartElement TT, Spark TT, Пульс ТТ.
Тюменский аккумуляторный завод (ТАЗ)
Это наверно единственное российское предприятие, которое производит аккумуляторные батареи из собственных комплектующих. Все необходимые компоненты для производства изготавливают прямо в стенах завода.
На 100% решен вопрос с импортозамещением комплектующих материалов. На всех этапах изготовления аккумуляторов используется новое российское и зарубежное оборудование. Все этапы процесса тщательно контролируются, что положительно влияет на работоспособность и долговечность АКБ.
АО «Тюменский аккумуляторный завод» производит аккумуляторные батареи для легковых автомобилей емкостью 38-100 Ач и грузовых автомобилей емкостью 132-230 Ач.
Модельный ряд PREMIUM (11 моделей), STANDARD (15 моделей), Сибирь (8 моделей), ASIA (7 моделей), Тайга (6 моделей).
На заводе выпускаются не только батареи для легкового и грузового транспорта.
Тяговые батареи производятся в намазном и панцирном исполнении по стандарту DIM. Ёмкость аккумуляторов от 100 до 1200 Ач. Благодаря применению комплектующих собственного производства завод может выполнять заказы любой сложности с минимальными сроками. Тяговые АКБ используются на электропогрузчиках и штабелёрах таких фирм как Toyota, Komatsu. Типоразмерный ряд представлен 31 моделью.
Владельцы частных домов также используют подобные батареи в качестве альтернативных источников энергии.
Завод также выпускает два типа стационарных аккумуляторов для энергогенерирующих объектов. В намазном варианте изготавливается 6 типоразмеров батарей от 350 до 500 Ач ёмкости. В панцирном возможно изготовление до 20 типоразмеров ёмкостью от 200 до 3000 Ач. Аккумуляторы рассчитаны на 20 лет безотказной работы, при этом стоимость их гораздо ниже зарубежных аналогов.
Помимо остальных видов продукции предприятие освоило выпуск батарей для тяжелой гусеничной техники. Данная продукция отправляется во многие страны мира. Заказывают подобную продукцию вооруженные силы различных государств. Выпускается три вида батарей.
ТАЗ не зависит от конъюнктуры, резких скачков цен, внешнеэкономической и политической ситуации.
Аккумуляторный завод Аком
Группа компаний «Аком» — один из лидеров в производстве и продаже аккумуляторных батарей в России. Сегодня в состав группы входят производство Аком, производство пластмассовых компонентов, металлургическое производство и торгово-маркетинговая кампания TMC.
5 ноября 2001 года в Министерстве юстиции РФ была зарегистрирована кампания ЗАО АКОМ. Уже спустя год при технической помощи и непосредственном участии специалистов кампании Todor запускается завод по производству аккумуляторных батарей в г. Жигулёвск.
К 2003 году продукция начала поставляться на ИжМаш, РосЛада, АвтоВаз и GV-AvtoVAZ. В этот же период создается региональная торговая сеть.
Январь 2005г. стал знаковым для кампании – в Ганновере был подписан пакет соглашений с немецкими коллегами из корпорации Johnson Controls, в результате чего было создано совместное предприятие и начат выпуск батарей Varta Standart. В том же году осваивается производство полного цикла, при котором основная часть комплектующих производится на заводе «Аком».
Проектная мощность на этом этапе – 1 000 000 аккумуляторов в год.
В 2006г. Начато строительство завода по производству свинца.
К следующему году в составе группы кампаний появляются предприятия по производству пластмассовых компонентов и торгово-маркетинговая кампания TMC.
В 2009г. начато освоение производства аккумуляторов для грузовых автомобилей и специальной техники.
В 2010г. производственные мощности модернизированы до 1 500 000 аккумуляторов в год.
АКОМ – это динамично развивающаяся кампания, которая ставит перед собой самые высокие планки. Для достижения поставленных задач в кампании разработана единая стратегическая концепция развития.
Продукция данного предприятия представлена пятью линейками:
- — АКОМ+EFB – 7 моделей в легковой группе
- — АКОМ – 11 моделей в легковой группе, 2 модели в грузовой группе
- — REACTOR – 4 модели для легковой группы
- — ULTIMATUM – 3 модели
- — BRAVO – легковая группа – 4 модели, грузовая группа – 2 модели
Саратовский аккумуляторный завод (Электроисточник)
Завод основан в 1929 году и в настоящее время является одним из старейших заводов России.
На производстве используются современные виды оборудования от лучших мировых производителей, что позволяет использовать инновационные решения и современные технологии.
На сегодняшний день освоен выпуск 25 различных моделей четырех серий аккумуляторов для легкового транспорта: АЭРОФОРСАЖ, ПИЛОТ, СТАНДАРТ, СКАТ.
Курский аккумуляторный завод (Аккумулятор)
Датой основания завода считается октябрь 1944 года.
Уже в 1952г. началось производство свинцово-кислотных АКБ, а в 1954-м – щелочных батарей различных типов.
С 1956г. завод приступил к выпуску герметичных никель-кадмиевых батарей.
В 1980г. началось выполнение государственного заказа для космических нужд СССР.
В 1995г. была смонтирована технологическая линия для производства стартерных свинцово-кислотных АКБ.
В 1998г. запущена в работу печь для выплавки свинца и свинцовых сплавов, что позволило обеспечить потребности завода на 100 %.
Завод специализируется на выпуске промышленных АКБ и стартерных для авто-мототехники.
Типоразмерная линейка для легкового и грузового автотранспорта представлена двумя модельными рядами: «Исток» и «Курский аккумулятор».
В заключение хотелось бы отметить, что российские производители аккумуляторных батарей не сидят “сложа руки” и динамично развиваются, внедряют в производство новые технологии и активно замещают импортные компоненты на отечественные. В нашей стране для успешного развития у них все есть.
akkumir.ru
Оборудование + Технология изготовления 2019
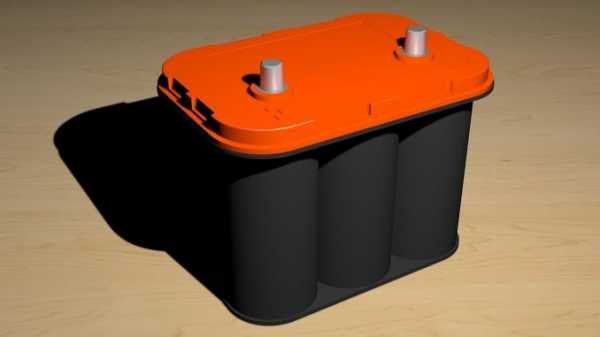
Электрический аккумулятор — это химический источник тока, источник ЭДС многоразового действия, основная специфика которого заключается в обратимости внутренних химических процессов, что обеспечивает его многократное циклическое использование (через заряд-разряд) для накопления энергии и автономного электропитания различных электротехнических устройств и оборудования, а также для обеспечения резервных источников энергии в медицине, производстве, транспорте и в других сферах.
Производство свинцово-кислотных аккумуляторов + видео
Именно аккумуляторы глубокого заряда и разряда применяются в машинах, автомобилях и железнодорожных локомотивах.
Обычно, такие аккумуляторы имеют напряжение от двух вольт до сорока восьми вольт. Внутри аккумуляторов таких находится серия пластин из свинца, а покрывается они кислотой и окисью свинца. Первое, что по технологии начинают производить, это решетки из свинца. Специальное оборудование расплавляет свинец до температуры его плавления и выливает необходимого размера решеточки. Литые решеточки станут позже пластинами элементов питания в аккумуляторах.
Технология производства аккумуляторов предусматривает литье и необходимо специальное литейное оборудование. Когда свинец заливается в форму, то в нее сразу поступает вода, что помогает за короткое время залитый свинец охладить и переместить его на конвейерную ленту. Происходит отлив разных по заряду решеток, одни из них будут служить положительным зарядом, а другие отрицательным. Далее, решетки перемещаются на следующий этап, который предполагает покрытие решеток окисью свинца, а также, кислотой. Составы разноименно заряжены, поэтому решетки разделяются на положительно и отрицательно заряженные. После этого, принято решетки называть пластинами, и они укладываются в поочередности положительных и отрицательно заряженных пластин. Важно, чтобы они размещались попеременно, и чтобы аккумулятор был работоспособным. Сложенные пластины в маленькие контейнеры далее погружаются в небольшие резервуарчики, которые наполнены кислотным раствором. Это поможет пластинам зарядиться. Зарядка может продолжаться сутками и это зависит от того в какую модель аккумулятора попадут пластины. Далее, проходят пластины промывку, причем она делается для того, чтобы частицы кислоты не остались на пластинах.
После этого, цвет пластин меняется, и они теперь становятся темными. На этом этапе пластины теперь меняют свое название на «пластины сухого заряда». Далее, те пластины, которые имеют положительный заряд, обволакиваются материалом содержащим стекловолокно. Далее происходит обволакивание в пластиковый слой. Именно такая одежка помогает предотвратить возникновение короткого замыкания. Пластины соответственно двум зарядам складываются в стопки. Попеременное расположение пластин одетых в пластик и раздетых складывают как коржи торта попеременно. Количество пластин соответствует модели аккумулятора. Далее происходит отчистка пластин. Этот этап отчищает выступающие частицы пластин, которые именуются контактами. После отчистки, контакты покрываются оловом, что позволяет хорошо соединить контакты. Далее проходит еще отчистка контактов покрытых оловом, а после сверху покрывается контакт слоем свинца.
Далее происходит спайка всех контактов в клеммы в определенном порядке. После этого, сборная конструкция именуется элементом. Его вставляют в пластиковую оболочку называемую полипропиленом. После этого, происходит этап проверки на правильность работы элемента. Все заряды должны отвечать своему заряду. Это необходимо, прежде всего, чтобы разметка на корпусе аккумулятора соответствовала заряду. Далее происходит герметизация крышки при помощи запаивания. Клеммы выступают на верху и их заливают дополнительно свинцовым слоем. Далее происходит еще одна проверка на герметичность упаковки элемента. Для этого используют воздух и мыльный раствор. Если появляются места пропуска воздуха, то они повторно пропаиваются.
Параллельно, в других цехах происходит производство маленьких деталей, которые будут участвовать в сборке аккумуляторов. Разъемы производятся для связки различных элементов между собой. Они спаиваются с элементами. После этого, сверху накладывается крышка, что сформирует цельную коробку для элементов аккумулятора. Далее необходимо сделать так, чтобы в местах клеем не попадала влага. Это уязвимое место укомплектовывают прокладкой, например, резиновой. А теперь наступает этап заливки электролита. В роли его участвует кислота. И она заливается в необходимой дозе прямо в только что собранный по частям аккумулятор. Кислота помогает проводить электрический ток, который образуется между пластинами.
Видео как делают:
Некоторые заводы по производству аккумуляторов используют свои технологии. И для автоматизации производства необходимы научные разработки, но все производители роботов и автоматизированного оборудования готовы провести исследования и разработать необходимое оборудование.
Производство литий-ионных аккумуляторов + видео
Литийионный аккумулятор (Li-ion) — тип электрического аккумулятора, который широко распространён в современной бытовой электронной технике и находит своё применение в качестве источника энергии в электромобилях и накопителях энергии в энергетических системах. Это самый популярный тип аккумуляторов в таких устройствах как сотовые телефоны, ноутбуки, цифровые фотоаппараты, видеокамеры и электромобили. Первый литийионный аккумулятор выпустила корпорация Sony в 1991 году.
Литийионный аккумулятор состоит из электродов (катодного материала на алюминиевой фольге и анодного материала на медной фольге), разделённых пористым сепаратором, пропитанным электролитом. Пакет электродов помещён в герметичный корпус, катоды и аноды подсоединены к клеммам-токосъёмникам. Корпус иногда оснащают предохранительным клапаном, сбрасывающим внутреннее давление при аварийных ситуациях или нарушениях условий эксплуатации. Литийионные аккумуляторы различаются по типу используемого катодного материала. Переносчиком заряда в литийионном аккумуляторе является положительно заряженный ион лития, который имеет способность внедряться (интеркалироваться) в кристаллическую решётку других материалов (например, в графит, окислы и соли металлов) с образованием химической связи, например: в графит с образованием LiC6, окислы (LiMnO2) и соли (LiMnRON) металлов.
Первоначально в качестве отрицательных пластин применялся металлический литий, затем — каменноугольный кокс. В дальнейшем стал применяться графит. Применение оксидов кобальта позволяет аккумуляторам работать при значительно более низких температурах, повышает количество циклов разряда/заряда одного аккумулятора. Распространение литий-железо-фосфатных аккумуляторов обусловлено их относительно низкой стоимостью. Литийионные аккумуляторы применяются в комплекте с системой контроля и управления — СКУ или BMS (battery management system), — и специальным устройством заряда/разряда.
В настоящее время в массовом производстве литийионных аккумуляторов используются три класса катодных материалов:
- кобальтат лития LiCoO2 и твёрдые растворы на основе изоструктурного ему никелата лития
- литий-марганцевая шпинель LiMn2O4
- литий-феррофосфат LiFePO4.
Электро-химические схемы литий-ионных аккумуляторов:
- литий-кобальтовые LiCoO2 + 6C → Li1-xCoO2 + LiC6
- литий-ферро-фосфатные LiFePO4 + 6C → Li1-xFePO4 + LiC6
Видео как делают литий-ионные аккумуляторы:
Благодаря низкому саморазряду и большому количеству циклов заряда/разряда, Li-ion-аккумуляторы наиболее предпочтительны для применения в альтернативной энергетике. При этом, помимо системы СКУ они укомплектовываются инверторами (преобразователи напряжения).
moybiznes.org
Аккумуляторные заводы России — 9 предприятий
Предприятия по выпуску аккумуляторов относятся к одной из важных отраслей российского промышленного комплекса, продукция которой находит применение в самых разных видах хозяйственной деятельности и деятельности вооруженных сил. Она необходима на всех видах гражданского и военного транспорта, в военной и вычислительной технике, при эксплуатации бытовых приборов, средств связи, для создания систем бесперебойного и автономного питания.
От основания первого аккумуляторного завода в России в 1897 году и до настоящего времени аккумуляторная промышленность проделала большой путь. Сегодняшние предприятия обладают высоким производственным и развитым научным потенциалом, позволяющим разрабатывать и производить разнообразные виды аккумуляторов и аккумуляторных батарей.
Аккумуляторы представляют собой химические накопители энергии, выделяющейся в результате химической реакции, и позволяющие использовать ее для работы различных приборов, делая их мобильными и независимыми от постоянных источников электроэнергии. Особенно широко применяются они в сотовой связи и автомобильном транспорте. Крупные предприятия отрасли оснащены современными автоматизированными линиями, позволяющими изготавливать аккумуляторы самого разного назначения, конструкции и размеров.
Кроме изготовления аккумуляторов и аккумуляторных батарей, предприятия отрасли занимаются разработкой новых и современных их видов. Также на аккумуляторных заводах производится восстановление, зарядка, сборка и утилизация использованных аккумуляторов.
Продукция предприятий: аккумуляторы серебряно-цинковые, литиевые, кислотные, никель-металлогидридные, щелочные, свинцово-кислотные, гелиевые, никель-цинковые; по материалу корпуса карболитовые, пластиковые; по особенностям эксплуатации: обслуживаемые и необслуживаемые.
По предназначению: промышленные, стартерные, тяговые, батареи аккумуляторов для тепловозов, аккумуляторы в источниках бесперебойного питания (ИБП), стационарные батареи для систем телекоммуникации, для компрессорных станций газопроводов, других энергетических объектов, разные виды аккумуляторов для сотовой связи, бытовых приборов, для источников аварийного электроснабжения.
www.wiki-prom.ru
Новые технологии в производстве аккумуляторов
Более 200 лет назад немецким физиком Вильгельмом Риттером был создан первый в мире аккумулятор. По сравнению с уже существующей тогда батареей А. Вольты, накопительное устройство Вильгельма можно было многократно заряжать‒разряжать. В течение двух столетий аккумулятор электричества сильно изменился, но в отличие от «колеса» его продолжают изобретать и по сей день. Сегодня новые технологии в производстве аккумуляторов продиктованы появлением новейших устройств, нуждающихся в автономном питании. Новые и более мощные гаджеты, электромобили, летающие дроны ‒ все эти устройства требуют небольших по размерам, легких, но более емких и долговечных аккумуляторных батарей.
Принципиальное устройство аккумулятора можно описать в двух словах – это электроды и электролит. Именно от материала электродов и состава электролита зависят характеристики аккумулятора и определяется его тип. В настоящее время существует более 33 типов переряжаемых источников электропитания, но наиболее применяемые из них:
- свинцово-кислотные;
- никель-кадмиевые;
- никель-металл-гидридные;
- литий-ионные;
- литий-полимерные;
- никель-цинковые.
Работа любого из них заключается в обратимой химической реакции, то есть происходящая при разрядке реакция восстанавливается при зарядке.
Область применения аккумуляторов довольно широка и в зависимости от вида устройства, которое от него работает, к батарее питания предъявляются определенные требования. Например, для гаджетов он должен быть легким, минимально габаритным и иметь достаточно большую емкость. Для электроинструмента или летающего дрона важен ток отдачи, так как потребление электрического тока достаточно высокое. При этом есть требования, которые предъявляются ко всем элементам питания – это высокая емкость и ресурс циклов зарядки.
Над этим вопросом работают ученые во всем мире, проводится масса исследований и испытаний. К сожалению, многие образцы, показавшие превосходные электрические и эксплуатационные результаты, оказались слишком дорогими по стоимости и не были запущены в серийное производство. С технической стороны, лучшими материалами для создания аккумуляторов становятся серебро и золото, а с экономической ‒ цена такого изделия будет недоступна для потребителя. При этом поиск новых решений не прекращается и первым значимым прорывом стал литий-ионный аккумулятор.
Литий-ионный аккумулятор
Впервые он был представлен в 1991 году японской компанией Sony. Батарея характеризовалась высокой плотностью и низким саморазрядом. При этом у неё были недостатки.
Первое поколение таких источников питания было взрывоопасным. Со временем эксплуатации на аноде накапливались дендриды, которые приводили к замыканию и возгоранию. В процессе усовершенствования в следующем поколении применили графитный анод и этот недостаток был устранен.
Вторым минусом стал эффект памяти. При постоянной неполной зарядке аккумуляторная батарея теряла емкость. Работа над устранением этого недостатка была дополнена новой тенденцией стремления к миниатюризации. Желание создавать ультратонкие смартфоны, ультрабуки и другие устройства требовало от науки разработок нового источника питания. К тому же уже устаревшая ионно-литиевая батарея не удовлетворяла запросы моделистов, которым нужен был новый источник электричества с гораздо большей плотностью и высоким током отдачи.
В результате в литий-ионной модели был применен полимерный электролит, а эффект превзошел все ожидания.
Литий-полимерный аккумулятор
Усовершенствованная модель не только была лишена эффекта памяти, но и в разы превосходила своего предшественника по всем параметрам. Впервые удалось создать батарею толщиной всего в 1 мм. При этом её формат мог быть самым разнообразным. Такие элементы питания стали пользоваться большим спросом сразу и у моделистов, и у производителей мобильных телефонов.
Но недостатки все же были. Элемент оказался пожароопасным, при перезарядке нагревался и мог воспламениться. Современные полимерные батареи оснащаются встроенной схемой, предотвращающей перезаряд. Рекомендуется также заряжать их только специальными зарядными устройствами, идущими в комплекте или аналогичными моделями.
Не менее важная характеристика элемента питания – себестоимость. На сегодня это самая большая проблема на пути развития аккумуляторов.
Питание электромобиля
Компания Тесла Моторс создает аккумуляторы по новым технологиям на основе комплектующих торговой марки Панасоник. Окончательно секрет не раскрывается, а вот результат испытаний радует. Экомобиль Tesla Model S, оснащенный аккумулятором всего 85 кВт*ч, на одном заряде проехал чуть больше 400 км. Конечно, мир не без любознательных, поэтому одну из таких батарей, стоимостью 45 000 USD, все же вскрыли.
Внутри оказалось множество литий-ионных ячеек Панасоник. При этом вскрытие не дало всех ответов, которые хотелось бы получить.
Технологии будущего
Несмотря на длительный период застоя, наука находится на грани великого прорыва. Вполне возможно уже завтра мобильный телефон будет работать месяц без подзарядки, а электромобиль преодолевать по 800 км на одном заряде.
Нанотехнологии
Ученые Южно-Калифорнийского университета утверждают, что замена графитовых анодов на кремниевые провода диаметром 100 нм увеличит емкость батареи в 3 раза, а время зарядки сократит до 10 минут.
В Стэнфордском университете предложили принципиально новый вид анодов. Пористые углеродные нанопровода, покрытые серой. По их утверждению такой источник питания аккумулирует в 4-5 раз больше электроэнергии, чем Li-ion батарея.
Ученый из США Дэвид Кизайлус заявил, что аккумуляторные батареи на основе кристаллов магнетита будут не только более ёмкими, но и сравнительно дешевыми. Ведь добывать эти кристаллы можно из зубов панцирного моллюска.
Учёные Вашингтонского университета смотрят на вещи более практично. Они уже запатентовали новые технологии для аккумуляторов, в которых вместо графитного электрода применен анод из олова. Все остальное не изменится и новые батареи смогут легко заменить старые в наших привычных гаджетах.
Революция уже сегодня
Снова электромобили. Пока они еще уступают автомобилям по мощности и пробегу, но это ненадолго. Так утверждают представители корпорации IBM, которые предложили концепцию литий-воздушных аккумуляторов. Более того, новый превосходящий по всем параметрам источник питания обещано представить потребителю уже в этом году.
qwizz.ru
Производство литий-ионных аккумуляторов — технология и сложности
Любой прибор для превращения химической энергии в электрическую должен иметь активный металл с большим отрицательным потенциалом. То есть разность потенциалов на катоде и аноде должна быть максимальной. Оптимальными свойствами обладает литий.
Устройство аккумуляторов
Легкий металл используется в виде химических соединений графита и литий-кобальт-оксида (LiCoO2), нанесенных в виде обмазки на медную и алюминиевую фольгу. Могут использоваться другие соли на основе лития. Весь процесс производства li-ion аккумуляторов состоит из этапов:
- изготовление электродов;
- сборка активной части и создание защиты;
- упаковка, внесение электролита;
- проверка работоспособности.
Две ленты сматываются в рулон или собираются из листов в корпус. Свободное пространство заливается электролитом, выполняются клеммные выводы в герметичном контуре. Литий-ионные аккумуляторы залиты жидким электролитом, литий-полимерные – гелевым.
В результате получаются приборы разных форм и габаритов. В пересчете на объем активной массы, характеристики:
- плотность 150-200 Вт-ч/кг или 350-450 Вт-ч/л;
- напряжение 3,6-3,7 В;
- потеря 20 % емкости после 500-1000 циклов зарядки;
- рабочие температуры -20 ~ +50 0.
Применение компактные батарейки получили в ноутбуках, сотовых телефонах, фотоаппаратах. Ими оснащают электромобили. Производство литиевых аккумуляторов несложное, не требует больших площадей. Основные производственные площадки расположены в Азии, развивается производство литиевых аккумуляторов в РФ. Здесь построен самый большой «Ли-ион» завод в мире, в пригороде Новосибирска – Толмачево.
Технология производства литий-ионных аккумуляторов
Аноды и катоды в элементах сходны по форме, но имеют разное содержание. Смешение мелких компонентов до нанесения на анод или катод недопустимо. Поэтому, в производстве разнозаряженных полос для литиевых батарей, оборудование используется одно, а производственные площадки разные.
Этап 1.
Подготовка активного слоя для нанесения на фольгированную основу. В трубчатой печи состав спекается в однородную массу при температуре 1200 0 С. Полученное сырье размалывается на мельницах до мелкодисперсного состояния и тщательно перемешивается для полной однородности. Состав наносят на проводящую ленту, закрепляют в термопечи. Прецизионным прессом прокатывают заготовку и направляют с цех сборки.
Этап 2.
На высокоточном оборудовании нарезают материал на ленты или листы, снова сушат при 250 0, собирают в последовательности катод, анод в многослойную конструкцию определенной формы. Соединяют ультразвуковой сваркой отдельно катодные и анодные лепестки, выводят контакт на токосъемник. Происходит придание нужной формы и проверка элемента на КЗ.
Этап 3.
Приваривается отрицательная клемма и создается углубленный контур для последующей впайки крышки. В атмосфере инертного газа в корпус закачивается порция электролита, крышка устанавливается, центруется и сваривается, проверяется герметичность корпуса. Готовый элемент обертывается термоусадочной пленкой. На поверхности остаются только выводы полюсов. Здесь же проводится первичная зарядка батареи.
Этап 4.
На заключительном этапе производства литий-ионных батарей выполняют контроль качества, проверку емкости и замеры сопротивления. Сохранность батарей обеспечивается при температуре 0-10 градусов. За 2 года батарея без употребления может потерять 20 % от первоначальной емкости. При периодической разрядке – зарядке батарея выдерживает до 1000 циклов.
Производство литий-ионных аккумуляторов в России
Производством, разработкой и исследованием литиевых аккумуляторов в России занимаются международные корпорации. Одна из них «НПО ССК (SSK group) создана на предприятиях «Радуга», расположенным в г, Сасово Рязанской области, на Украине и в Индии. Здесь освоена технология изготовления батарей емкостью до 1000 А-ч и напряжением до 300 В. Они могут работать в диапазоне температур -40 +90 , выдерживать до 3000 циклов разряда.
Есть Научный центр «Автономные источники тока». Располагается он в Сколково. Продукция рассчитана для систем накопления большой мощности (СНЭ), выпускается на крупногабаритный транспорт.
Крупнейшее в мире производство li-ion аккумуляторов в России построено в Новосибирске, как российско-китайское производство. Завод «Лиотех» производит изделия емкостью 200-700 А-ч, работающие при температурах от -45 до +65 градусов. Промышленное производство в 1 млн. штук в год призвано обеспечить 5 000 автобусов.
Характеристики продукции «Лиотех»
Развиваются производства, по ассортименту и количеству продукции уступающие зарубежным компаниям:
- АК «Ригель»;
- ОАО»Энергия»;
- НИИХИТ-2.
Россия может производить литиевые батареи с довольно низкой себестоимостью – металл получают в Новосибирске, остальные компоненты также отечественные.
Видео
Предлагаем познакомиться с производством литиевых аккумуляторов в России на крупнейшем предприятии «Лиотех»
batts.pro
Технология производства литий-ионных аккумуляторов | Генераторы для каждого
от generator-prosto.
К нам почту приходило довольно много вопросов о том, как производятся литий-ионные аккумуляторы. Сегодня постараемся рассмотреть этот вопрос подробнее. Поскольку литиевые аккумуляторы выпускаются различных форм-факторов и характеристик, производство и технология их производства существенно отличаются. В этой статье мы расскажем о производстве наиболее распространённых Li-Ion аккумуляторах, а также сделаем обзор производителей литиевых АКБ.
Содержание статьи:
Производство литий-ионных аккумуляторов
В общем случае производство Li-Ion аккумуляторов можно разделить на следующие этапы:
- Производство электродов;
- Сборка электродов в батарею, установка защиты;
- упаковка в корпус, заливка электролита;
- Тестирование, заряд.
Как правило, эти этапы присутствуют при сборке литий-ионных батарей всех форм-факторов. В роли анода используется медная фольга с нанесённым слоем графита (в некоторых случаях угля). В качестве катода применяется алюминиевая фольга со слоем материала, содержащего литий. Здесь возможны варианты в зависимости от характеристик конечного изделия: LiCoO2, LiFePO4, LiNiO2, LiMn2О4.
Намотка алюминиевой фольги с литийсодержащим материалом в рулон
Что касается сборки электродов в единую батарею, здесь есть различия для разных типов Li-Ion аккумуляторов. При производстве цилиндрических литий-ионных аккумуляторов (например, 18650) используется скручивание электродов в рулон. При этом они разделяются сепаратором. То есть, подготовленные ленты катода и анода разделяются сепаратором и наматываются в рулон. Чем меньше толщина электродов, тем более ёмкий и мощный можно собрать аккумулятор. Вся сборка помещается в стальной или алюминиевый корпус, заливается электролитом и герметично запечатывается. Снаружи остаются только выводы плюс и минус.
В призматических литий-ионных аккумуляторах используются прямоугольные электроды, которые укладываются друг на друга через сепараторы. Конструкция в этом случае получается такой же, как в случае свинцово-кислотных аккумуляторов для автомобилей. В этом случае производство электродов немного отличается от тех, что используются в цилиндрических моделях. Сначала также изготавливаются ленты катода и анода, а затем из них вырубаются прямоугольные пластины.
Электроды для призматических литий-ионных аккумуляторов
После сборки электродов они помещаются в пластиковый корпус, к ним привариваются токовыводы, заливается электролит и герметично закрываются.
В некоторых призматических литий-ионных аккумуляторах используется сборка электродов в виде эллиптической спирали. Такую конструкцию могут иметь литиевые батарейки для аккумуляторов телефонов.
После сборки, заливки электролита и герметизации проводится тестирование, при котором выявляется производственный брак. После этого проводится первый заряд аккумулятора, во время которого происходит формирование поверхности электродов. В качестве сепаратора используется полиэтиленовый сепаратор. При температуре 130-150 градусов он плавится и тем самым прекращает обмен ионами между катодом и анодом. Это определённая защита при перегреве литиевого аккумулятора.
Кроме того, при производстве Li-Ion аккумуляторов на определённые модели устанавливаются дополнительные виды защиты. Например, цилиндрические аккумуляторы 18650 имеют в торце корпуса специальный клапан. Он открывается, когда давление внутри превышает определённый предел.
Защитный клапан
На все литий-ионные аккумуляторы, используемые в электронике, ставятся контроллеры заряда-разряда. Они предохраняют банку от глубокого разряда и излишнего заряда. Кроме того, часто устанавливается термистор, который размыкает цепь и отключает банку от внешнего мира при увеличении температуры выше определённого предела.
Контроллер заряда-разряда литиевых аккумуляторов
Производители литий-ионных аккумуляторов
Зарубежные компании
За границей производство Li-Ion батарей очень развито. Многие крупные компании выпускают литиевые аккумуляторы. В качестве примера можно привести следующие:
- Altair Nanotechnologies. Фирма занимается производством материала для анода Li-Ion батарей из титаната лития. В продуктовой линейке Altair Nanotechnologies есть аккумуляторные системы для электроэнергетики, транспортных средств и источников бесперебойного питания. Такие компании из Южной Кореи, как Eig Ltd и Kokam занимаются выпуском для Altair аккумуляторных ячеек;
- A123 Systems. Компания занимается производством аккумуляторных ячеек и модулей. На их основе делаются аккумуляторы для ТС, сферы электроэнергетики. В производстве литий-железо-фосфатных АКБ компания использует собственную технологию Nanophosphate. Аккумуляторы выпускаются как цилиндрического, так и призматического форм-факторов;
- Ener1 Battery Company. Компания занимается выпуском Li-Ion аккумуляторных систем для транспортных средств, потребительской электроники и сферы энергетики. Производство размещено в США и Южной Корее;
- Samsung SDI. Основное производство фирмы ориентировано на выпуск аккумуляторов для электроники. Также выпускаются аккумуляторы для энергетических систем. Компания самостоятельно выпускает литий-железо-фосфатные ячейки ёмкостью 50 Ач, которые используются в распределительных сетях;
- Saft Batteries. Выпускает накопители Intensium Max, которые созданы на базе Li-Ion аккумуляторов собственного производства. Они применяются для поддержания функционирования возобновляемых источников энергии. В основу аккумуляторных батарей компании положены аккумуляторные ячейки VL41M цилиндрической формы. Катод делается на основе никелевого оксида. Из нескольких VL41M формируют аккумуляторный модуль, который используется в различных системах;
- Dow Kokam. Эта фирма является совместным предприятием Южной Кореи и США. Они выпускают аккумуляторные системы, модули, ячейки Li-Pol. Их продукция используется в промышленности, транспортных средствах, ИБП, военной сфере. У фирмы есть свои производственные мощности в Южной Корее, Франции, США;
- BYD. Эта китайская компания занимается выпуском автомобилей, электротранспорта, солнечных батарей, инверторов, а также литий-ионных аккумуляторов. В основе аккумуляторных систем BYD лежат литий-железо-фосфатные ячейки.
Отдельно можете прочитать подробный материал про литий-ионный аккумулятор.
Российские производители
В настоящее время в интернете можно найти информацию о таких компаниях, занимающихся выпуском АКБ в России:
- НПО ССК;
- Лиотех;
- АК Ригель;
- НИИХИТ-2;
- ОАО «НИАИ «Источник»;
- ОАО Энергия.
Стоит сказать, что по своим производственным мощностям и ассортименту выпускаемой продукции российские производители значительно уступают зарубежным компаниям.
Если статья оказалась для вас полезной, распространите ссылку на неё в социальных сетях. Это поможет развитию сайта. Голосуйте в опросе ниже и оценивайте материал! Исправления и дополнения к статье оставляйте в комментариях.
Популярные статьи:
Опубликовано в Аккумуляторыgenerator-prosto.ru