Производство блоков – ,
Технология изготовления керамзитобетонных блоков
Керамзит, как сыпучий утеплитель, используется не только для проведения теплоизоляционных мероприятий, связанных с утеплением перекрытий. Его нередко используют для производства бетонных блоков, где он выступает в качестве наполнителя. От этого блоки становятся легкими, потому что керамзит в несколько раз легче гравия или щебня, которые он заменяет в керамзитобетонных блоках, плюс уменьшается теплопроводность самого стенового материала. Изготовление керамзитобетонных блоков ничем от обычных бетонных не отличается, главное – точно соблюсти рецептуру используемого раствора.
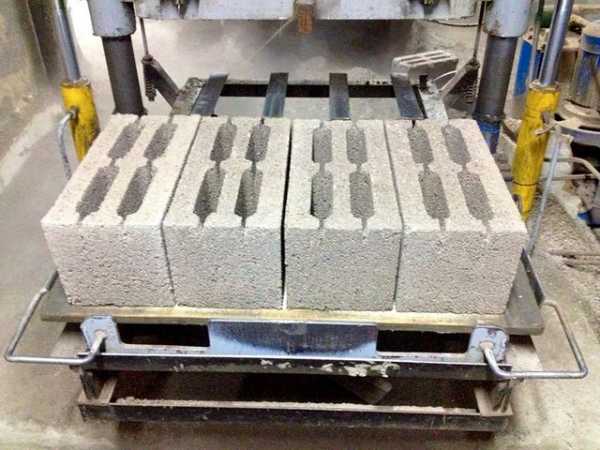
Блоки стеновые из керамзитобетона
Рецептура керамзитобетонного раствора
Обозначим состав керамзитобетона для изготовления блоков из расчета на 1 м³ приготавливаемого раствора.
Материал | Количество, кг |
Цемент марки М400 | 230 |
Песок кварцевый фракции 2-2,5 мм | 600 |
Вода | 190 |
Керамзит (гравий) фракции 5-10 мм | 600-760 |
Вышеобозначенная рецептура соответствует бетону марки М150, что достаточно для сборки стеновых конструкций.
Сегодня большое внимание уделяется такой характеристики, как влагостойкость. Поэтому для производства блоков из керамзитобетона, которые могли спокойно противостоять повышенной влажности и даже прямому воздействию воды (к примеру, косой дождь), в раствор добавляются гидроизоляционные материалы. Один из них – битумная мастика, затворяемая, как 10-процентный водный раствор.
Необходимо отметить, что у такого раствора немного измененная рецептура.
Материал | Количество, кг |
Цемент | 250 |
Керамзитовый гравий | 460 |
Керамзитовый песок (размеры гранул до 5 мм) | 277 |
Вода | 190 |
Битумная эмульсия | 19 |
К производству керамзитобетонных блоков подход разный. Производственная линия с мощным оборудованием и высокой производительностью, где установлены дозаторы, выставленные на пределы веса точно по рецептуре. Второе – ручной способ, где взвешивание компонентов производится чаще ведрами. Поэтому стоит обозначить вес материалов в ведрах (10 л):
- цемент – 13 кг;
- песок – 16;
- вода – 10;
- керамзит (гравий) – 4-4,5;
- керамзит (песок) – 5,5-6.
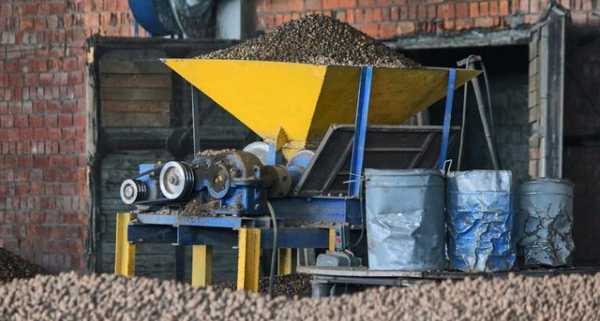
Главное – точная рецептура
Оборудование для производства
Для производства керамзитобетонных блоков (ручным способом) необходимы:
- бетономешалка;
- несколько лопат;
- станок с вибратором;
- несколько форм.
Бетономешалку можно приобрести или взять в аренду. Станки также продаются, хотя это не самое дешевое оборудование. Изготовить их своими руками можно, и если вы неплохой сварщик, то на один станок потребуется один день для сборки. Конструкции станков – огромное количество. В основном это рамные агрегаты, внутрь установлены и жестко закреплены формы. К раме также присоединен жестко вибратор, работающий от сети 220 вольт. Прибор продается в строительных магазинах.
Другой вариант – вибрационный стол, представляющий собой горизонтальную плоскость. Она обычно устанавливается на пружины, к ней же прикрепляется вибратор. Для станка придется изготовить своими руками несколько форм. И чем больше площадь стола, тем больше на нем поместится форм, тем выше производительность самодельного оборудования.
Важно! Не переусердствовать, потому что у вибратора определенная мощность, которой хватает на вибрирование определенной массы.
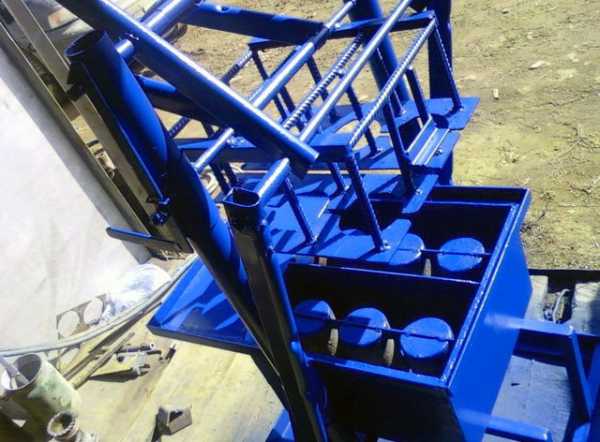
Вибростанок на два блока
Форма для керамзитобетонных блоков
Для изготовления форм используют различные плоские материалы: листовое железо толщиною не менее 2 мм, доски, фанеру, плиты ОСП и прочее. Основная задача производителя работ – подогнать размеры формы под размеры блока: 190х188х390 мм (стандартный несущий стеновой блок). Существуют так называемые полублоки (применяются для возведения перегородок), размеры: 90х188х390.
Стандартные размеры блоков из керамзитобетона
Одна из особенностей керамзитобетонных блоков – пустоты, которые облегчают камень без снижения несущей способности, снижают себестоимость за счет уменьшения используемого объема смеси, увеличивают теплотехнические качества изделия. Поэтому при изготовлении в формы устанавливают жестко три трубы диаметром 40-50 мм, расположенные на одном расстоянии друг от друга и стенками формы.
Трубы соединяются между собой сваркой горизонтальными перемычками (арматура, уголок или стальная лента). К стенкам формы крепятся электросваркой, если форма изготавливается из стального листа, или с помощью саморезов, если применены деревянные изделия.
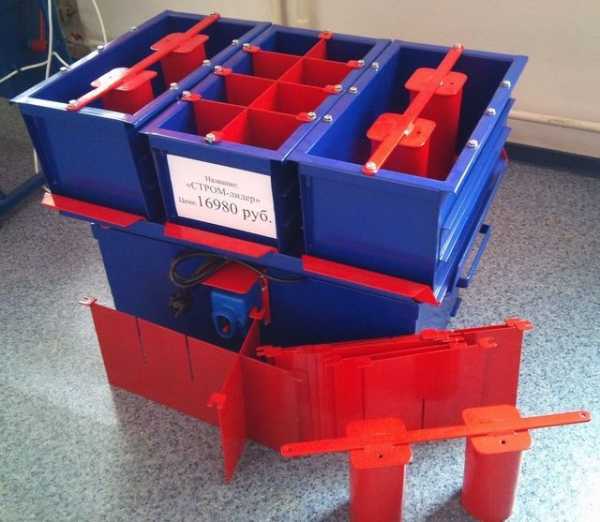
Готовые формы разного вида
Технология производства
Сам технологический процесс проводится в любом помещении с хорошо действующей вентиляционной системой. Размеры помещения зависят от габаритов используемых станков. Керамзитобетонные блоки после изготовления должны пройти процесс сушки, производимую на открытой площадке на улице. Если есть вероятность выпадения атмосферных осадков, то над площадкой лучше возвести навес.
В первую очередь готовится раствор: в бетономешалку засыпается цемент и часть воды. Смесь перемешивается несколько минут до получения однородного состава. Затем в него добавляются порциями песок и керамзит. В конце добавляется оставшаяся часть воды. Конечный раствор должен получиться густым и пластичным.
После чего его из бетономешалки вываливают в подготовленную заранее емкость (корыто), а уже оттуда лопатами перебрасывают в формы, уложенные на вибростол или установленные на вибростанке. Перед этим стенки форм обмазывают отработанным техническим маслом, чтобы блоки легко вышли после затвердевания. Пол вибростола или площадки посыпается мелким песком, чтобы бетон не прилип.
Формы равномерно заполняются раствором, к примеру, пара заброшенных в них лопат смеси. Затем включается вибратор, происходит равномерное распределение бетонного раствора по всему объему формы и его уплотнение. После чего процесс повторяется. Такую процедуру проделывают несколько раз, чтобы заполнить формы полностью. Иногда для придания более точных размеров уложенный и уплотненный раствор дополнительно прижимают сверху металлической крышкой, она на поверхности блока создаст ровную и гладкую поверхность.
В таком виде прямо в формах керамзитоблоки должны простоять не менее суток. После чего их вытаскивают, укладывают на уличную площадку так, чтобы между ними оставался зазор в пределах 2-3 см. Сушиться блоки из керамзитобетона должны 28 суток, что придаст им марочную прочность. Просохнуть материал должен со всех сторон равномерно, поэтому каждый блок в течение сушки переворачивают с боку на бок. Если уложить на сушку их на деревянные поддоны, то переворотами заниматься не надо.
Видео:
Производство блоков из керамзитобетона как бизнес
Начать производить керамзитоблоки, чтобы получать прибыль, не проблема. Главное – все точно просчитать. Как показывает практика, основное требование не к оборудованию, а к размерам помещения и уличной площадке. Чем они больше, тем больше блоков можно уложить на сушку, которая длиться около месяца. Поэтому предлагаются разные варианты проведения сушки. Один из таких показан на фото ниже, где видны специальные стеллажи с укладкой блоков этажами.
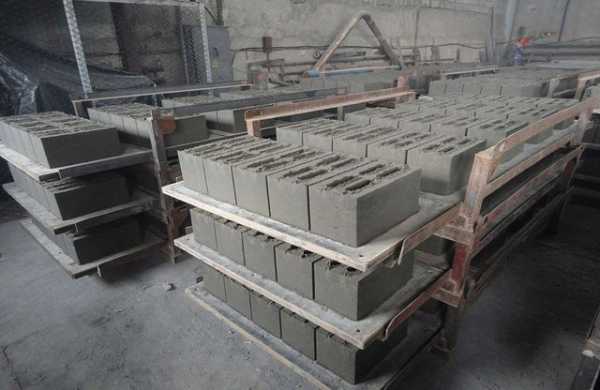
Способ сушки
Все остальное упирается в стоимость сырьевых материалов, которая скачет в зависимости от сезона. Летом цемент стоит всегда выше, потому что спрос на него вырастает за счет увеличения объемов строительства. Особенно это относится к частному сектору.
Кто не первый год в бизнесе такого типа старается все предусмотреть. Кто-то пытается закупить материалы по низкой цене зимой, но есть нюанс – цемент со временем теряет свои свойства, снижается качество. Кто-то, как было описано выше, пытается увеличить производство блоков зимой. В любом случае это прибыльный бизнес пока строительство на пике, пока востребованы строительные материалы. Блоки из керамзитобетона сегодня на пике популярности за счет невысокой цены, высоких теплотехнических качеств и простоты укладки.
viascio.ru
Технологии производства керамзитобетонного блока и бизнес план
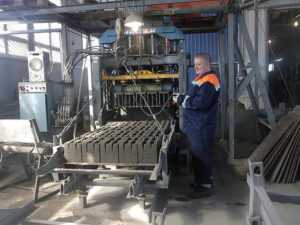
Готовые блоки после вибропрессовки
Одной из высокорентабельных бизнес-идей, не требующих значительных первоначальных инвестиций, является производство керамзитобетонных блоков, которое может быть организовано в любом гараже или подсобной постройке частного дома, в том числе дачного типа.
Принципиальными конструктивными особенностями места для организации собственного производства легковесных строительных блоков являются наличие небольшого помещения, для предохранения от влаги, а также ровной площадки (пола) для установки оборудования и складирования продукции.
Бизнес-план подобного малого производства привлекателен тем, что не требует больших площадей и найма рабочей силы на первоначальном этапе, который может быть реализован одним или двумя крепкими мужчинами, не чурающимися физических нагрузок.
Технология изготовления
Керамзит, будучи продуктом обжига легкоплавкой глины, является легким материалом и достаточно давно используется в качестве утеплителя и наполнителя при обустройстве полов и кровли. Практика применения керамзита в качестве наполнителя конструктивных элементов зданий хорошо себя зарекомендовала при изготовлении легковесных наружных панелей многоэтажных домов. Совместив легкость и хорошие теплоизоляционные свойства с небольшими размерами конструктивных элементов удалось получить технологию, получившую название изготовление керамзитобетонных блоков и нашедшую повышенный спрос в малоэтажном частном строительстве.
Основные технологические этапы изготовления блоков:
- Подготовка и измерение всех компонентов будущей смеси.
- Замес рабочего раствора в бетономешалке.
- Загрузка приготовленной смеси в станок и формовка блока.
- Складирование готовых блоков на складе до полного набора прочности.
Рецептура смеси
Чтобы гарантировать прочность блоков, необходимо соблюсти пропорции и последовательность смешения компонентов:
- сначала заливается одна часть воды;
- следом засыпается шесть частей керамзита, диаметром 4–8 мм;
- далее наступает очередь песка, который, в идеале, должен быть керамзитным, имеющим гранулы менее 4 мм в диаметре, и составлять до трех частей;
- в последнюю очередь засыпается 1 часть цемента.
При замешивании следует учитывать следующие моменты:
- Добавление последующего компонента смеси следует производить после равномерного смачивания или перемешивая ранее добавленных составляющих.
- Объем воды должен быть уменьшен, если песок влажный, для чего первоначально заливается от 50 до 75% необходимого объёма. Необходимость добавления оставшейся части жидкости определяется после добавления и перемешивания песка, по консистенции смеси, которая должна быть полусухой и рассыпчатой.
- Подходящие марки цемента — М400, М500. При использовании менее прочных марок связующего компонента его объем должен быть увеличен на 5–10% для уменьшения на каждые 100 условных единиц (для цемента М300 объем должен составить 110% от исходной пропорции).
- Цемент должен быть свежим, не намокшим, без комков. Использование некондиционного цемента допускается только после повторного измельчения и при условии увеличения его пропорции.
- Для увеличения прочности керамзитобетонных блоков, доля цемента должна быть увеличена.
- Чтобы сократить период высыхания с двух суток до 6–8 часов, в смесь потребуется добавить пластификатор из расчета 5 г. на один блок.
- Для получения глянцевой поверхности готовых изделий, при замешивании частично вместо цемента добавляют плиточный клей.
- Добавление смолы древесно омыленной повышает морозостойкость готовых блоков за счет образования изолированных воздушных полостей.
Как начать собственный бизнес
Составляя план собственного производства керамзитобетонных блоков по технологии без обжигового производства посредством уплотнения смеси керамзита, цемента и песка, следует запланировать следующие затраты:
- покупку станка для ручного производства блоков, который можно приобрести от 2,5–3 тыс. р. при минимальной механизации ручного труда и отсутствии вибратора, обеспечивающего высокое значение показателя плотности;
- покупку бетономешалки, так как ручное перемешивание хоть и позволит удешевить бизнес-план на 15–30 тыс. р., но увеличит длительность производственного цикла, а значит не позволит выйти на расчетную производительность в 120–160 блоков за 8 часовую смену;
- текущие затраты на электроэнергию, водоснабжение и расходные материалы, в том числе керамзит, песок, пластификатор, плиточный клей и прочие добавки, а также бруски и фанеру толщиной 10 мм для организации упорядоченного многоярусного складирования готовых блоков.
Строка переменных издержек бизнес-плана, зависящая от объёма производства, определяется из расчета 20–25 р. за один блок, при его вдвое большей продажной стоимости. А значит ручной станок может быть заменен на устройство с вибратором, передающим высокочастотные колебания на корпус формы и крышки, позволяя получить высокую плотность изделий.
Приобретение более высокопроизводительного станка позволит нарастить объем производства блоков вдвое, за счет увеличения первоначальных инвестиций в бизнес-план на 25–30 тыс. р.
В итоге примерная смета затрат на реализацию бизнес-плана собственного производства керамзитобетонных блоков будет выглядеть следующим образом:
- станок с поверхностным вибратором и набором форм – 25–30 тыс. р.;
- бетономешалка — 20–25 тыс. р.;
- вспомогательный инструмент – 1–2 тыс. р.;
- расходные материалы для изготовления одного блока стандартных размеров:
- цемент — 7 р.;
- песок — 1,5 р.;
- керамзит — 19 р.;
- электроэнергия — 0,2 р.;
- зарплата персонала — 5 р.
Таким образом суммарные инвестиции в бизнес-план по механизированному производству легковесных блоков составят 60–80 тыс. р., а период окупаемости инвестиций — от 3 месяцев до полугода, в зависимости от организации производства (одно-, двухсменное или круглосуточное).
Рентабельность реализации бизнес-плана по производству керамзитобетонных блоков во многом будет зависеть от собственных физических усилий или производительности наемных работников. Снизить зависимость производства от эффективности рабочей силы можно будет инвестировав в проект около полумиллиона, на приобретение автоматизированного поточного производства с конвейерным транспортером, который могут обслуживать два высококвалифицированных работника. Все физические трудозатраты при таком производстве сведены до минимума за счет применения грузоподъёмной техники и конструктивных решений оборудования, а производительность достигает 1500 блоков в смену или до 4500 блоков в сутки. Окупаемость подобного автоматизированного комплекса, при наличии устойчивого сбыта, может составить от двух недель до месяца.
Похожие статьи
kamedom.ru
Производство керамзитобетонных блоков: технология
Керамзитобетонные блоки — легкий стройматериал, который применяется для кладки стен. Продукцию, представленную на рынке, как правило, изготавливает тот или иной завод керамзитобетонных изделий (в частности, алексинский). Также можно приобрести товары компании Еврокам и блоки, выпущенные на заводе керамзитового гравия (Винзили). Несмотря на то, что керамзитобетон имеет сравнительно небольшой вес, он обладает достаточной прочностью. Кроме того, керамзитобетонная поверхность не вредит окружающей среде, а изготовить такой блок можно и в домашних условиях. Технология производства изделий позволяет в значительной степени сократить финансовые затраты. Качество керамзитобетонных блоков будет высоким, если при их производстве применять хорошие материалы.
Технология изготовления
При строительстве малоэтажных строений специалисты часто возводят стены из керамзитобетонного блока. Применение этих стройматериалов обещает большую выгоду, нежели приобретение кирпичей, поскольку блокам свойственны несколько преимуществ. Прежде всего, на кладку керамзитоблоков потребуется меньшее количество времени и цементной смеси. Помимо этого, теплопроводность блоков считается низкой, за счет чего изделия обладают высокой теплоизоляцией. При этом производство керамзитобетонных блоков — несложный процесс. Технология создания керамзитобетонной смеси компании Еврокам схожа с методами изготовления аналогичных стройматериалов. Если есть такая необходимость, то можно сделать раствор своими руками или приобрести материалы, сделанные на заводах Алексина или керамзитового гравия (Винзили). Завод керамзитобетонных изделий выпускает качественную продукцию. Для этого нужно только соблюдать технологию и пропорции компонентов. Перед началом работ важно заранее узнать о преимуществах и недостатках керамзитобетона. Процесс делится на несколько этапов:
- Подготовка оборудования. Технология изготовления изделий предполагает использование специального оборудования. Вам понадобится бетономешалка и вибростанок. Предварительно необходимо расспросить у специалистов об особенностях работы вибростанка. Вместо него можно воспользоваться вибростолом. Стоимость оборудования может быть высокой, но качество на выходе оправдывает такие затраты. При этом его применение предполагает создание одного либо нескольких изделий. Но важно учитывать, что использование оборудования рассчитано и на физический труд рабочих. Вибростанки — сложный механизм, но работать с ними просто даже новичкам. На них необходимо закрепить блок-форму, на которую будет передаваться вибрация. За счет пуансона получаются блоки с гладкой поверхностью. Создание изделий осуществляется при помощи вибропресса, который вмонтирован в станок.
- Подготовка строительных материалов. Прежде всего, необходимо подготовить помещение с хорошей вентиляцией. Кроме того, понадобится уличная площадка для сушки и последующего хранения стройматериалов. В состав блоков из керамзитобетона входит несколько компонентов. Речь идет в первую очередь о главном материале — керамзите. В роли вяжущих веществ выступают цемент (М400), мелкий песок и жидкость. Эти ингредиенты – обязательные компоненты бетонной смеси. Керамзит также должен быть мелким, поскольку такая форма материала является наиболее подходящей для подобных изделий. Чтобы осуществить производство высококачественных и прочных блоков, понадобится приобрести специальные добавки. Для большей морозостойкости в состав подмешивают омыленную смолу деревьев, а для повышения связывания — лигносульфонат. Пластичность материала поможет увеличить стиральный порошок. Необходимо добавить в цементный раствор одну ч. л. на ведро жидкости.
Смешивание компонентов. Бетонную смесь следует изготавливать в бетономешалке. Во время проведения работ важно соблюдать указанные пропорции. Так, цемент должен составлять одну часть, измельченный керамзит — шесть частей, песок — три части, вода — одну.. Чтобы правильно изготовить раствор, внутрь бетономешалки нужно налить жидкость, затем засыпать керамзитовый песок. После впитывания воды в состав можно добавить цементную смесь и мелкий песок. Перемешивание раствора длится примерно две минуты. Необходимо, чтобы консистенция керамзитобетона была однородной.
- Формовка. Следующий этап производства блоков из керамзитобетона – формовка при помощи вибростенда. В углубление установки следует поместить подготовленную смесь, затем включить оборудование. Вибрация поможет ликвидировать пустоты в растворе, одновременно повысив его плотность. После этого смесь можно распределять в формы. Чтобы покрытие получилось максимально ровным, нужно убрать все излишки с поверхности. Завершив этот этап, вы можете начать сушку блоков.
- Сушка. Этот шаг является последним в изготовлении керамзитоблоков. Закончив заливку изделий, рабочие должны оставить блоки, по меньшей мере, на сутки (лучше — на двое). Затем следует разобрать специальные формы, положить блоки на открытую площадку и укрыть изделия от осадков и попадания сора. Сушка длится примерно двадцать восемь дней. Затвердевший керамзитобетон можно применять для укладки стенок.
Укладка
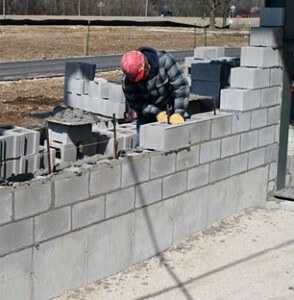
Так как первая линия кладки является основой здания, блоки нужно распределять особенно тщательно и аккуратно. После укладки каждых двух-трех керамзитоблоков нужно проверять, насколько ровной получается кладка. Для этого вам понадобится строительный уровень. Затем следует замазать щели цементным раствором. Каждый последующий слой укладывают таким же образом. Также важно помнить, что швы не должны слишком выделяться. Вместе с тем необходимо, чтобы они надежно удерживали остальные блоки. Так, ширина швов может составлять примерно полтора сантиметра.
Специалисты отмечают, что нельзя заполнять смесью отверстия, имеющиеся внутри керамзитоблоков. Во-первых, вы израсходуете на это большое количество цемента, во-вторых, блоки потеряют изоляционные характеристики. Кроме того, стоит принимать во внимание то, как вы будете отделывать стену. Например, если планируется облицовывать керамзитоблоки кирпичами, можно не заниматься дополнительной отделкой стены. А если вы не намерены облицовывать поверхности, то сделайте «расшивку».
Вернуться к оглавлениюХранение и транспортировка материалов
Керамзитоблоки поставляют на специальных европоддонах, защищают от неблагоприятных воздействий при помощи пленки из полиэтилена. Пакеты можно перевозить любым видом автотранспорта, согласно утвержденным правилам транспортировки грузов. Стройматериалы разгружают всеми способами, которые гарантируют сохранность изделий и не нарушают технику безопасности. На стройплощадке такие поддоны устанавливают горизонтально. Хранить блоки нужно в помещениях с низким уровнем влажности. Важно, чтобы на блоки из керамзитобетона не попадала влага. Керамзитоблоки обычно складируют на специальные поддоны. Они должны находиться под навесом, быть укрыты брезентом.
Соблюдение условий хранения и перевозки поможет сохранить качество продукции.
kladembeton.ru
Строительные блоки. Технология производства блоков
Процесс производства строительных блоков на вибростанках Вибромастер можно представить в виде следующей технологической схемы:
Таким образом, производство строительных блоков включает в себя следующие технологические этапы:
Приготовление жесткой бетонной смеси из цемента, заполнителя и воды
Раствор лучше всего готовить в бетономешалке принудительного типа (т.е. со смешивающими лопастями).
Из предлагаемого нами ассортимента это модели смесителей Вибромастер РП-200 и Вибромастер СБ-80. Бетономешалки гравитационного типа («груши») использовать можно, но получить при этом качественное смешивание не получится.
Смешивать также можно и вручную, лопатой в любой емкости. При этом для приготовления жесткой смеси потребуется значительные физические усилия. Крайне мала будет и производительность такого перемешивания.
В зависимости от использованного заполнителя (керамзит, опилки, шлак, песок) получаем соответственно раствор будущего керамзитобетона, опилкобетона, шлакобетона, пескобетона.
Цикл вибропрессования
Цикл вибропрессования, состоит из следующих этапов:
- Загрузка раствора в форму станка (производится вручную)
- Уплотнение в форме с помощью вибрации и прижима (пуансона).
Уплотнение в форме под действием вибратора занимает обычно 20-30 секунд. Это время и качество уплотнения зависит только от вибратора. На станках «Вибромастер» мы применяем только настоящие сертифицированные вибраторы с большой возмущающей силой. Поэтому качество шлакоблоков и скорость производства гарантируется. - Выемка блока из формы происходит сразу же после уплотнения. Блок остается либо на поддоне, либо прямо на земле (в зависимости от конструкции станка). Жесткий раствор и качественное уплотнение позволяют полученному блоку не рассыпаться и держать форму «самостоятельно» и «не поплыть» во время высыхания. Блок на поддоне можно сразу же перенести на стеллаж для дальнейшей сушки и набора прочности. Некоторые модели вибростанков «Вибромастер» предусматривают распалубку формы непосредственно на месте сушки.
В итоге получаем отформованный стеновой строительный блок. Опять же, в зависимости от состава это может быть:
- керамзитобетонный блок,
- арболитовый блок,
- шлакоблок,
- пескоблок.
Необходимый набор прочности
Набор первоначальной прочности (достаточный для складирования) происходит при естественной температуре от 36 до 96 часов (без применения специальных добавок — ускорителей твердения – ХК, релаксола и других). Это время в данном случае зависит только от свойств цемента и температуры окружающего воздуха.
При использовании указанных ускорителей твердения это время может быть уменьшено до 5-8 часов (в зависимости от дозировки ускорителя).
Очень желательно в первые дни набора прочности предохранять блоки от пересыхания. Для этого достаточно накрывать их пэ пленкой. Также можно время от времени поливать блоки водой.
Набор отпускной прочности (согласно ГОСТ — не менее 50% от расчетной окончательной) происходит при положительной температуре примерно в течение недели. После этого периода блоки уже можно продавать потребителю и использовать на стройплощадке.
Набор 100%-ой прочности протекает в течение 28 суток при положительной температуре.
Технология производства блоков в виде печатной брошюры бесплатно прилагается к любому из станков «Вибромастер». В «Технологии производства строительных блоков» (ее объем — свыше ста страниц текстовой и графической информации) приведены все возможные составы формовочной смеси (в т.ч. и бесцементные, на основе природных вяжущих веществ — извести, гипса, магнезии и их смесей) для изготовления шлакоблоков, керамзитобетонных блоков, арболитовых блоков, пескоблоков, саманных камней из грунтобетона, а также для всех других видов блоков. Используя приведенные в технологии методики, Вы также сможете самостоятельно рассчитать составы смесей с использованием имеющихся в Вашем распоряжении местных заполнителей. Фактически — это целый справочник по всем основным вопросам производства строительных блоков. Отдельно от оборудования он не предоставляется и не продается.
Помимо технологии производства к установкам прилагается подробная инструкция по работе с ними. Для работы на установках не требуется специального обучения и каких-то особенных навыков работы. Будет достаточно внимательно ознакомиться с технологией производства и инструкцией.
Вы также можете посмотреть следующие разделы
- Cтроительные блоки
- Исходные компоненты
- Конструкция станков
- Сертификация
- О нашей марке «Вибромастер»
- Полезные статьи
- ГОСТы и СНиПы
- Термоблок
vibromaster.ru
Производство бетонных блоков и пенобетонных: оборудование
Самые разнообразные изделия из бетона широко используются как в промышленном, так и в частном строительстве. При этом одним из самых главных достоинств является тот фактор, что блоки можно изготовить и своими руками – оборудование для производства бетонных блоков отличается простотой, установки для пенобетонных изделий несколько сложнее, но, тем не менее, их стоимость также достаточно демократична. Освоить все особенности работ не составит большого труда, главное – соблюдать требования технологии.
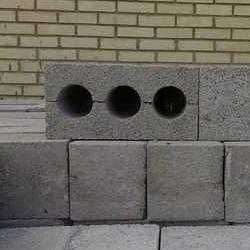
На фото: блоки из бетона, изготовленные самостоятельно, практически не уступают заводским вариантам
Преимущества самостоятельного изготовления блоков
Конечно же, купить готовые изделия гораздо проще, но и у варианта с самостоятельным производством есть свои плюсы:
Цена | Стоимость одного изделия при его изготовлении своими руками получается примерно наполовину ниже. Это особенно важный фактор при нехватке средств, ведь можно провести работы со значительной экономией, хотя это и более трудозатратный вариант |
Качество | Вы точно можете быть уверены, что при изготовлении применялись только качественные компоненты и соблюдались все требования технологии. Очень часто недобросовестные производители продают некачественные изделия, что сказывается на прочности построек |
Соответствие требованиям | Этот пункт особенно актуален, если вам нужны блоки нестандартных размеров. Вы можете самостоятельно изготовить форму любого размера, что сразу же решает любые вопросы по параметрам изделий |
Возможность заработать | Изготовление блоков самостоятельно может не только обеспечить вас строительным материалом, вы можете делать продукцию на продажу. Опять же, средства можно вкладывать в собственную стройку |
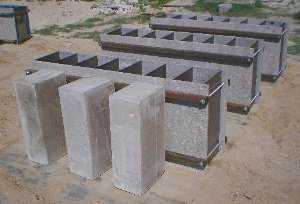
Пенобетонные блоки изготовить гораздо проще, чем кажется на первый взгляд
Особенности технологии
Сразу стоит отметить, что можно проводить два основных варианта работ: изготавливать бетонные с наполнителями или пенобетонные изделия. Обе технологии имеют кардинальные отличия, поэтому мы подробнее рассмотрим каждый из вариантов.
Бетонные блоки с наполнителем
Оборудование для производства бетонных блоков отличается простотой, вам понадобится бетономешалка, формы и вибростол. Причем в самом крайнем случае можно обойтись только формой, но от этого качество несколько снизится.
Сам процесс достаточно прост:
- В первую очередь необходимо подготовить компоненты – песок, цемент, наполнитель (это может быть щебень, шлак, керамзит и многое другое, все зависит от того, какой компонент доступен в вашей местности).
Важно! Правильная консистенция раствора – он должен при сжатии в руке образовывать комок, который при падении на землю разбивается. Такой состав оптимален для производства бетонных блоков.
- Далее стоит определиться с оптимальным размером форм, самый популярный вариант – 20х20х40, при этом стоит помнить, что в процессе работы часто нужны и половинчатые элементы, поэтому форма 20х20х20 также будет очень актуальной. Для изготовления можно использовать металл либо дерево (если применяется дерево, то с внутренней стороны форму лучше всего отделать жестью для идеальной гладкости будущих изделий).
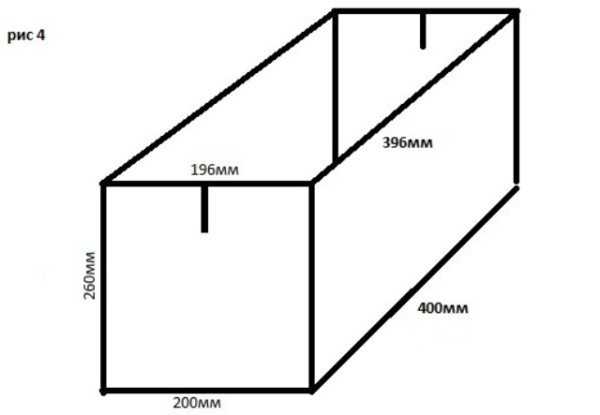
Форма может быть изготовлена из чего угодно, главное – чтобы материалы были плотными
- Для того чтобы изделия проще доставались из форм, все элементы, соприкасающиеся с бетоном, смазываются специальной смазкой либо машинным маслом (подойдет и отработка, это абсолютно не принципиально).
- Установка для производства бетонных блоков представляет собой вибростол, уплотняющий смесь. Как отмечалось, можно работать и без него, но будет страдать качество, поэтому лучше изготовить простейшее приспособление или поступить так: взять оборудование напрокат на несколько дней.
- Инструкция по изготовлению достаточно проста: готовится раствор, после чего форма заполняется и уплотняется каким-либо способом. Если в изделии нужны пустоты, можно воспользоваться бутылками, которые также необходимо смазать. Вынимать блоки можно через 1-2 дня, после чего производится сушка в течение как минимум 2-х, а лучше 4-х недель.
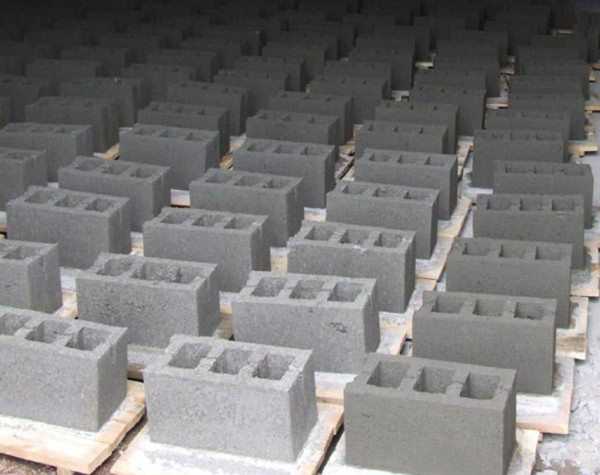
Сушка – ответственный этап работ
Пенобетонные изделия
Технологическая схема производства пенобетонных блоков отличается от обычных изделий:
- Основными компонентами являются цемент, песок и специальный состав для создания пены. В этом случае главное значение имеет обеспечение стойкости образовавшейся пены и ее равномерное распределение по структуре изделий, именно поэтому важно использовать хорошую установку. Самым простым и эффективным вариантом на сегодняшний день является использование бароустановок, они обеспечивают хорошее качество изделий и стоят достаточно мало.
Оборудование для производства пенобетонных блоков отличается компактностью и простотой эксплуатации – особенности работы можно освоить за очень короткое время
- Процесс довольно прост: в оборудование подается необходимое количество компонентов, и в течение нескольких минут производится приготовление состава, который затем можно заливать в формы, а можно заполнять опалубку и создавать монолитные конструкции.
Совет! Такой вариант отлично подходит для заполнения полостей – состав заполнит все пустоты между стенами и после застывания обеспечит отличную теплоизоляцию.
Это отличный вариант для собственного бизнеса – производство пенобетонных блоков отличается высокой окупаемостью, и вы сможете выйти на прибыль уже через 3 месяца нормальной работы.
Мобильная установка позволяет изготавливать пенобетон в нужном месте
Вывод
Изготовление конструкционных элементов на основе бетона по силам практически каждому человеку. Видео в этой статье расскажет и наглядно покажет некоторые важные особенности производственного процесса (см.также статью «Производство газобетонных блоков: обзор технологического процесса»).
masterabetona.ru
Станок для изготовления керамзитобетонных блоков
СодержаниеКерамзитобетонные блоки – это строительный материал, применяющийся для постройки стен жилых и промышленных зданий. Их повсеместное применение началось относительно недавно, но они уже завоевали популярность у большинства строителей.
Бетоносмеситель и станок для изготовления керамзитобетонных блоков
Процесс изготовления керамзитных блоков может быть совершен как на заводе, так и в домашних условиях своими руками. Но во втором случае качество выпускаемых изделий будет существенно ниже.
По способу изготовления и характеристикам они схожи с блоками из чистого бетона, с той разницей, что в качестве тяжелого наполнителя применяют керамзит, а не щебень. За счет легкости керамзита, блоки получаются значительно легче, чем классические бетонные.
Преимущества использования керамзитобетонных блоков
Блоки из керамзита имеют такое прекрасное свойство, как негорючесть. Это справедливо за счет того, что керамзит не может загореться или расплавиться. При высоких температурах он может только растрескаться и разрушиться. Именно избавление от необходимости дополнительного пожарного надзора делает такие блоки популярными во всех видах строительства.
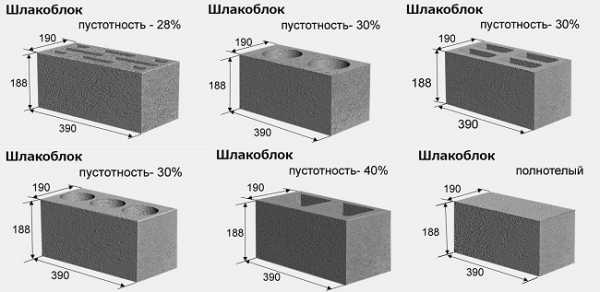
Виды и характеристики наиболее популярных моделей блоков
Высокие показатели керамзит демонстрирует не только при высоких, но и при низких температурах. При постройке в условиях холодного северного климата керамзитобетонные блоки становятся незаменимым подспорьем. Во время частых перемен температуры, керамзит может выдерживать около 50 циклов заморозки и оттаивания.
Используя керамзитобетон, можно быть уверенным в сохранении тепла внутри квартиры. Накопление в течение дня солнечной энергии совместно со свойством медленной отдачи тепла во внешнюю среду сделали керамзит отличным материалом для постройки гражданских зданий.
Дома из керамзита имеют способность «дышать», тем самым сохраняя в помещении оптимальные температурные показатели.
Блоки из керамзита прекрасно справляются с изоляцией от уличного шума, и надобность в установке дополнительной звукоизоляционной системы отпадает сама собой.
Таким образом, можно выделить такие основные преимущества производства керамзитобетонных блоков:
- уменьшенный вес, по сравнению с бетоном, высокая прочность;
- теплоизоляционные свойства;
- устойчивость к агрессивным химическим средам;
- скорость постройки стен с использованием этого материала;
- морозостойкость;
- полная экологичность производства и дальнейшего применения в строительстве.
к меню ↑
Технология изготовления керамзитных блоков
Основной материал производства таких блоков – это керамзит. Его получают способом высокотемпературной обработки глины или глинистых сланцев. Остальные обязательные элементы: вода, цемент, песок.
Читайте также: об особенностях конструкции камнерезного станка.
Иногда добавляются различные пластификаторы, с целью уменьшить расход воды и повысить эластичность смеси. Чаще всего в роли пластификатора выступает жидкое мыло либо клей.
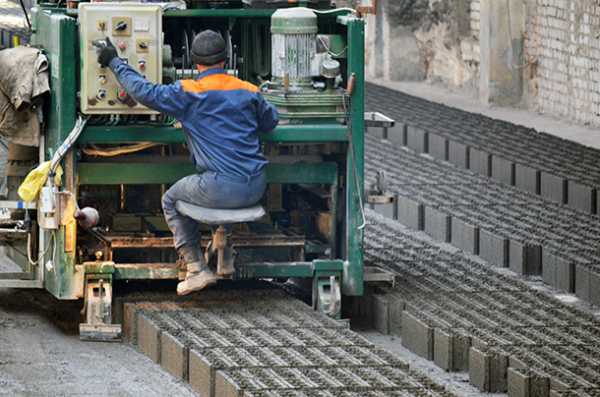
Процесс изготовления керамзитобетонных боков на специальном станке
В зависимости от пропорций составляющих керамзитовой смеси, изготовленный блок может иметь самые разные характеристики. Наиболее распространены в изготовлении керамзитных блоков такие их виды:
- конструкционный;
- конструкционно-теплоизоляционный;
- теплоизоляционный.
Первый вариант, конструкционный блок, можно получить с помощью увеличения доли цемента в общей массе состава. Изготовление таких блоков рационально для строительства многоэтажных жилых домов, где требуется жесткость и прочность несущим конструкциям.
Если же на первом месте стоит сохранение тепла в помещении, то следует подобрать пропорцию в таком варианте: 60% керамзитного песка, 30% обычного речного или морского песка, 10% цемента и 8% воды.
Теперь подробно об этапах изготовления. В первую очередь, необходимо сформировать керамзитобетонную смесь в нужных пропорциях. Диаметр всех фракция не должен превышать 10 миллиметров. Цемент рекомендуется использовать марки М400. Все компоненты тщательно перемешиваются в бетономешалке. Порядок заливки смеси в бетономешалку следующий:
data-ad-client=»ca-pub-8514915293567855″
data-ad-slot=»5929285318″>
- Вода.
- Керамзит.
- Цемент.
- Песок.
Следующим обязательным процессом является формовка блоков. В специальную нишу на вибростанке устанавливается форма, в которую заливается бетонная смесь. После окончания уплотнения формы, излишки смеси удаляются с поверхности формы, и затем сама форма отправляется на сушку.
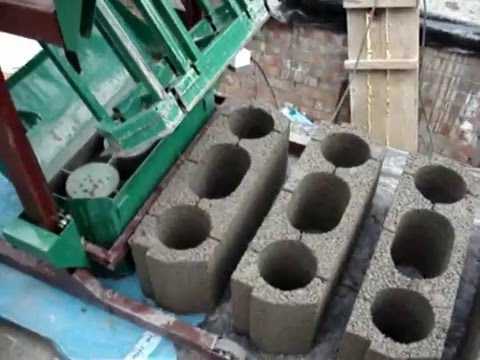
Формовка блоков на станке
Первый отрезок сушки проходит в течение 2 дней в стальных пластинах, при поддерживаемой температуре в 50-60 градусов. По истечении этого срока форма выносится на открытый воздух и проходит второй отрезок сушки длительностью в 7-10 дней. Все эти операции можно произвести и своими руками, не закупая дорогостоящего оборудования.
к меню ↑
Необходимое оборудование
Для полного обеспечения технологии производства, изготовление керамзитобетонных блоков требует полного комплекта оборудования. Для приготовления бетонной смеси потребуются бетономешалки – большие емкости, размещенные на вращающейся оси. Их основное отличие – это вместительность (литраж) и количество оборотов за минуту.
Ручной вибростанок – это идеальные станки для производства блоков своими руками, также как и станок для производства арболитовых блоков. Они малогабаритны, что позволяет осуществить производство в домашних условиях.
Вибратор закрепляется на поверхности корпуса и совершает колебания, способствующие распределению смеси по форме равномерно и без комков. Ручные станки могут иметь стационарные и съемные пустотообразователи. Съемные пустотообразователи позволяют конфигурировать тип блока по своему усмотрению.
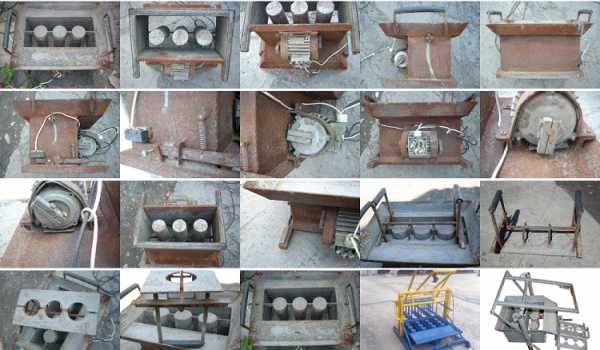
Этапы изготовления станка для формовки керамзитобетонных блоков своими руками
Вибростол представляет собой станок с поддоном толщиной в 3 миллиметра, имеющим бортики. Именно на поддоне формы утрамбовываются вибрацией. Работа за ним несложная и проста для выполнения своими руками, есть возможность изготовить за раз около 6 форм.
За счет расположения вибратора внизу поддона, колебания распространяются равномерно по всей поверхности, что положительно влияет на качество продукции на выходе.
Вибропресс – уже куда более мощный и габаритный станок, который используется при производстве керамзитоблоков в промышленном масштабе. Имеет гидропривод, который прилагает усилия в нескольких тонн для уплотнения изделий.
Пустотообразователи расположены на специальных пандусах и вдавливаются в форму по необходимости.
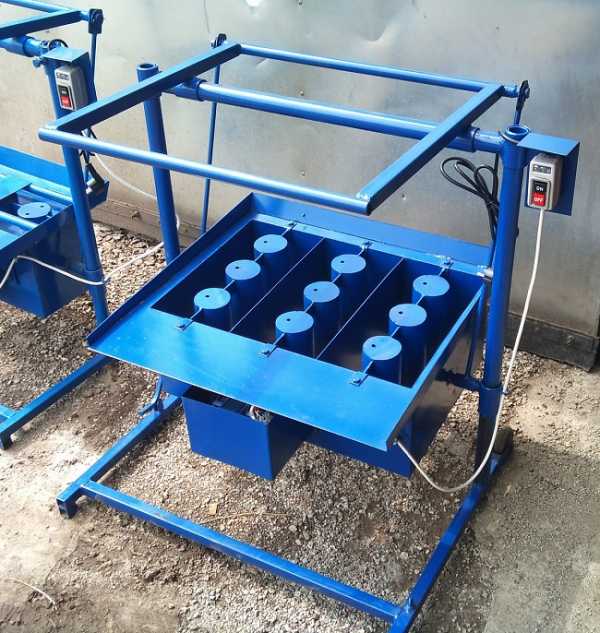
Вибростанок для формовки шлакоблоков
На поддонах происходит окончательная формовка блоков. Вибропресс исключает работу своими руками на всех этапах производства.
к меню ↑
Станок Рифей-Универсал М
Вибростанок Рифей отлично подходит для изготовления бетонных изделий из жестких смесей с таким наполнителем, как керамзит, способом объемного прессования. Максимальные габариты формуемых изделий – 780×390х230 миллиметров. Для каждого отдельного вида блоков необходимо иметь отдельную матрицу.
Используя станок Рифей, можно производить такие строительные изделия:
- стеноблоки, шлакоблоки, керамзитоблоки;
- бордюры;
- камни для облицовки;
- тротуарную плитку.
В странах СНГ и России этот пресс используется прежде всего для создания стройматериалов из керамзита своими руками, а уже потом можно использовать этот станок для производства тротуарной плитки.
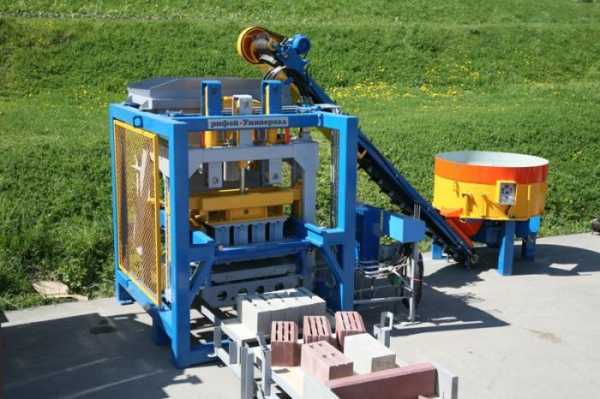
Вибростанок Рифей универсал М
Комплектация станка состоит из модуля подготовки смеси, который включает в себя смеситель на 300 литров и транспортер, который отправляет смесь в вибропресс. А также из формующего модуля с непосредственно вибропрессом, насосом, пультом управления, накопителя и кассеты для подачи поддонов.
Поставка может быть дополнена узлом пуансон-матрица, предназначенным для производства особых форм стенового камня.
Производительность и качество продукции не оставляют равных станку Рифей на рынке вибропрессов. Конструктивные решения дают возможность переоборудования пресса на выпуск других изделий буквально за час, заменой пуансонов-матриц. Надежность, простота в обслуживании, ремонте и уходе минимизирует издержки при производстве керамзитных блоков.
к меню ↑
Технология изготовления станка для производства керамзитобетонных блоков своими руками (видео)
data-full-width-responsive=»true»
data-ad-client=»ca-pub-8514915293567855″data-ad-slot=»8040443333″>
ostanke.ru
Необходимое оборудование в производстве керамзитобетонного блока
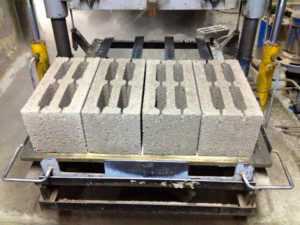
Изготовленные блоки на перед перемещением на место хнанения
Если возникает необходимость построить собственный дом и прочие вспомогательные постройки своими руками, то причин тому может быть две: ограниченный бюджет на строительство или рачительность в сочетании с желанием сделать все самостоятельно.
В обоих случаях траты на покупку конструкционных материалов для возведения стен хочется максимально сократить, а достичь этого можно за счет организации собственного изготовления расходных материалов на основе керамзита или вспененного бетона.
Первый вариант является более бюджетным, а оборудование необходимое для производства керамзитобетонных блоков можно или купить по сходной цене, или сделать своими руками, при наличии надлежащих навыков и желания.
Производственный процесс
Технология производства керамзитобетонных блоков является наиболее простой и заключается в заполнении формовочных элементов, которые подвергаются вибрации, за счет чего происходит уплотнение смеси и достигается требуемая прочность конструкционных материалов. Изготовление блоков с различными наполнителями, в том числе керамзитобетонных, является комбинацией метода заливки смеси в опалубку и кирпичной кладки.
Простейший станок для производства бетонных изделий, который можно изготовить своими руками из металлопроката и стальных листов, представляет собой конструкцию из стола с формовочными элементами, образующими внутренние полости в блоках. На стол устанавливается съемная форма, состоящая из дна и металлической опалубки, ограничивающей периметр и определяющей форму и размер блока. После установки дна и формы она заполняется исходной керамзитобетонной смесью, которая должна быть уплотнена, для чего может быть использована пресс-крышка.
Описанная процедура изготовления блоков не позволяет получить изделия с высокой плотностью, которой можно достичь, только применяя специальное оборудование, включающее вибростол/вибратор, создающие мелкие вибрации формы, за счет чего удаляются воздушные полости и происходит трамбовка исходной смеси.
Оборудование и процедура
Технология производства конструктивных элементов на основе керамзита не предусматривает их обжига или иной термической обработки, поэтому для получения готовых изделий с достаточно высокой прочностью потребуется следующее оборудование:
- бетономешалка — для получения смеси равномерной консистенции;
- станок с вибростолом — для удаления воздушных пустот и максимального уплотнения смеси;
- форма из металла или полимерного материала, определяющая размер и геометрию готовых изделий;
- дополнительные вспомогательные приспособления при необходимости:
- вибрационное сито для просеивания песка или керамзита;
- гидравлическая тележка с вилами, для удобного перемещения готовой продукции.
Самый простой станок, с производительностью 20 блоков в час, можно приобрести за 2,5–3,0 тыс. р. и произвести за два месяца количество материалов достаточное для возведения одноэтажного дома в 100 кв. м.
Планируя производство керамзитобетонных конструкционных блоков своими руками, следует иметь в виду, что высыхание блоков происходит естественным образом, а значит:
- потребуется сухое, вентилируемое помещение с крышей для складирования;
- штабелирование изделий может производиться в несколько рядов в высоту, но для этого потребуется вилочный погрузчик или таль.
Процедура производства блоков из керамзитобетона своими руками предусматривает 2–3 повторяющихся этапа заполнения, при которых:
- форма заполняется раствором сверх бортов формовочного короба;
- закрывается крышка-пресс или его аналог;
- включается вибрационное оборудование и происходит уплотнение массы.
Процедура повторяется необходимое число раз для получения плотного изделия требуемого размера.
После уплотнения форма снимается со стола, переворачивается, удаляется дно, а готовое изделие выгружается на подготовленный поддон или прокладочные бруски, обеспечивающие зазор между слоями блоков в штабеле и гарантирующие равномерное высыхание и затвердевание заготовок.
Разновидности станков
В зависимости от исполнения станочное оборудование для производства блоков из керамзитобетона подразделяется на:
- Ручное — в котором все операции выполняются вручную, а уплотнение смеси осуществляется за счет вибратора закрепленного на корпусе. Стоимость от 2,5–3 тыс. р.
- Передвижные линии — представляющие собой станки для одновременной заливки нескольких блоков, последующих их опускания на опорную поверхность и перемещения далее по зоне складирования. Стоимость от 30 тыс. р.
- Вибростол, на который производится установка форм в количестве до 6 штук за один заход. Стоимость от 60–80 тыс. р.
- Вибропресс, представляющий собой поточную линию для массового производства с автоматизированной загрузкой, обработкой в пресс-формах и перемещением к месту складирования при помощи конвейера. Стоимость в диапазоне 250–350 тыс. р.
Станок своими руками
Оборудования необходимое для производства формуемых конструктивных элементов из разнообразных бетонных растворов, можно изготовить своими руками из подручных материалов, имея под рукой:
- Металлический лист толщиной от 3 мм и более, для изготовления пресс-крышки, форм и поверхности вибростола.
- Уголок или профилированную трубу, для изготовления каркаса и вспомогательных элементов, которые включает в себя станок.
- Электродвигатель мощностью от 0,6 кВт.
- Набор вспомогательного оборудования для преобразования вращения ротора двигателя в вибрацию рамы станка, включающий в себя эксцентрик, набор шкивов — для ременной или звездочек — для цепной передачи.
Для лучшей вибрации, эксцентриситет шкива, насаженного на вал двигателя должен быть небольшим, а частота вращения высокой. При подобном сочетании параметров рама будет мелко и часто вибрировать, обеспечивая лучшее уплотнение раствора в форме. Двигатель крепится к опорной раме и имеет связь с вибростолом только посредством гибкой связи в виде ременной или цепной передачи.
Чтобы блоки получались ровными и имели прямые углы, сварка листов в формы должна производиться снаружи. Для легкого высвобождения блока из формы делать это нужно сразу после изготовления, а поверхность следует протирать и смачивать перед каждой новой операцией.
Рентабельность производства
В зависимости от наличия складских площадей и потенциального спроса на строительные материалы, объем производства может достигать нескольких десятков тысяч блоков ежемесячно, а для этого потребуется автоматизированная линия стоимость в 250–350 тыс. р. Вне зависимости от производительности оборудования, при ритмичном производстве и полной реализации продукции, окупаемость инвестиций в производство керамзитобетонных блоков составляет 6–9 месяцев.
Масса сырого блока составляет примерно 11 кг, уменьшаясь после высыхания до 9,5 кг, а значит процесс изготовления подобных изделий является трудоемким и требует значительных физических усилий. Следовательно, для производства бетонных блоков с наполнением из керамзита и других изделий, уплотняемых методом вибрации, потребуется штат физически крепких мужчин и средства малой механизации для выполнения погрузо-разгрузочных операций.
Похожие статьи
kamedom.ru