Технология производство газобетона – Изготовление газобетона: обзор процесса производства
Технология изготовления автоклавного газобетона | gazobeton.org
Газобетон – это легкий искусственный материал, полученный в результате твердения поризованной смеси, состоящей из гидравлических вяжущих веществ, тонкомолотого кремнеземистого компонента, воды и добавки газообразователя.
Для изготовления изделий из ячеистого бетона можно применять различные сырьевые материалы, но наибольшее распространение получили следующие:
— портландцемент ПЦ 400 – ПЦ 500, без активных минеральных добавок;
— известь негашеная кальциевая с содержанием CaO не менее 70%;
— кварцевый песок с содержанием кварца SiO2 не менее 85%, а глинистых примесей не более 3%;
— газообразователь алюминиевая пудра (паста) с содержанием активного алюминия не менее 80%.
Технологический процесс изготовления автоклавного газобетона включает в себя:
— прием и подготовку сырьевых материалов;
— приготовление газобетонной смеси;
— формование массивов газобетона;
— разрезку массивов на изделия;
— автоклавную обработку;
— упаковку изделий.
Сырьевые материалы могут поступать на завод различными видами транспорта (чаще всего автомобильным и железнодорожным). Хранение вяжущих предусматривается в специальных силосах. Количество и объем силосов выбирается в зависимости от мощности завода, удаленности от поставщиков материалов и вида транспорта.
Кварцевый песок выгружаются в приемный бункер, откуда по ленточному конвейеру поступает на помол для приготовления шлама. Помол производится в шаровых мельницах. Далее песчаный шлам транспортируется в шламбассейны, где гомогенизируется с помощью постоянного механического перемешивания.
Негашеная известь на предприятие поступает в тонкомолотом или комовом виде.
В первом случае, тонкомолотая негашеная известь хранится, по аналогии с портландцементом, в силосах и уже готова к употреблению. Во втором случае, если поступает комовая негашеная известь, на предприятии используется технология приготовления известково-песчаного вяжущего путем совместного сухого помола в шаровых мельницах извести и кварцевого песка.
Приготовление газобетонной смеси производится в дозаторно-смесительном отделении. Портландцемент, известь (известково-песчаное вяжущее), песчаный шлам, шлам из отходов резки, вода и алюминиевая суспензия дозируются в соответствии с установленной рецептурой в специальный смеситель, обеспечивающий высокую гомогенность смеси.
Процесс формования включает разгрузку (заливку) смеси из смесителя в форму и вспучивание смеси. Окончание процесса формования наступает после достижения максимальной высоты вспучивания смеси и прекращения активного газовыделения.
После вспучивания формы с газобетонной смесью выдерживаются на постах, желательно при температуре воздуха не менее +15-20oС до приобретения требуемой пластической прочности сырца. Для ускорения процесса набора первоначальной прочности формы со смесью могут выдерживаться в специальных термокамерах при температуре до +70-80
После достижения сырцом пластической прочности 0,04-0,12 МПа (в зависимости от технологии) формы подаются на резательный комплекс. Газобетонный массив калибруется со всех сторон и разрезается проволочными струнами в продольном и поперечном направлениях на изделия требуемых размеров. Метод резки газобетонных массивов в полупластическом состоянии с помощью тонких проволочных струн хорошо зарекомендовал себя и на современных резательных машинах позволяет получать изделия точных размеров с отклонениями от номинальных до ±1,0-1,5 мм. Такая точность позволяет осуществлять кладку блоков на тонкослойную клеевую смесь вместо традиционного цементно-песчаного раствора.
Разрезанные на изделия массивы устанавливаются на автоклавные тележки и загружаются в автоклав. После полной загрузки автоклава начинается тепловлажностная обработка по определенному режиму, включающему плавный набор температуры и давления, изотермическую выдержку при температуре около 190°С и давлении 12 атм, плавный спуск давления и подготовка изделий к выгрузке.
Из компонентов CaO и SiO2, вяжущих материалов и кварцевого песка, а также воды, в условиях автоклавной обработки (высокое давление и температура) происходит образование новых минералов – низкоосновных гидросиликатов кальция, что предопределяет более высокие физико-механические характеристики автоклавного газобетона в сравнении с неавтоклавными ячеистыми бетонами (пенобетон, газобетон).
После завершения цикла тепловлажностной обработки изделия подаются на участок деления и упаковки, а затем на склад готовой продукции.
Основные моменты технологии производства блоков из автоклавного газобетона показаны на видео одного из участников ассоциации ВААГ:
Производства газобетонных блоков: оборудование, технология
Газобетон обладает высокими прочностными и теплоизоляционными характеристиками. Строительный материал является удачным выбором застройщиков в сфере индивидуального и коллективного строительства. Его изготовление может стать выгодным бизнес-проектом, к тому же цена мини завода по производству газобетона, не отличается высокими отметками и напрямую зависит от решения предпринимателя о выпуске конкретного вида материала.
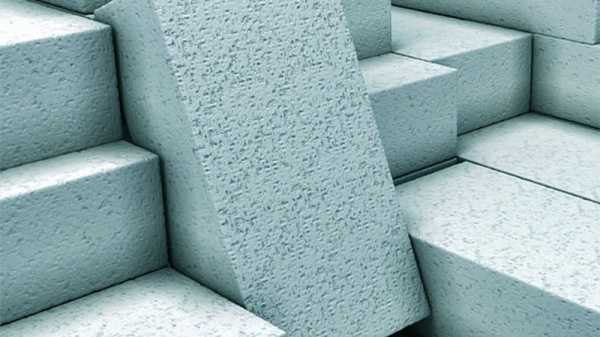
Газобетон
Общая информация о материале
В названии строительного материала, газобетон или автоклавный ячеистый бетон, заложены его характеристики и технологии производства.
Строительный материал может быть использован для возведения несущих конструкций сооружения или его внутренних перегородок. Он не подходит для промышленных объектов и высотных зданий, однако отлично зарекомендовал себя в сфере индивидуального строительства. Использование газоблоков обеспечивает оперативное строительство, по причине того, что они имеют большой размер. Их легкость позволяет сократить расходы на закладку фундамента, поскольку ему не нужно претерпевать большие нагрузки.
Состав
Уникальные характеристики строительного материала обусловлены его составом.
Сырьем для его изготовления являются цемент, кварцевый песок и алюминиевая пудра, выполняющая роль газообразователя. Для придания специфичных свойств газоблокам, некоторые производители в состав добавляют дополнительные ингредиенты, такие как известь, зола и гипс.
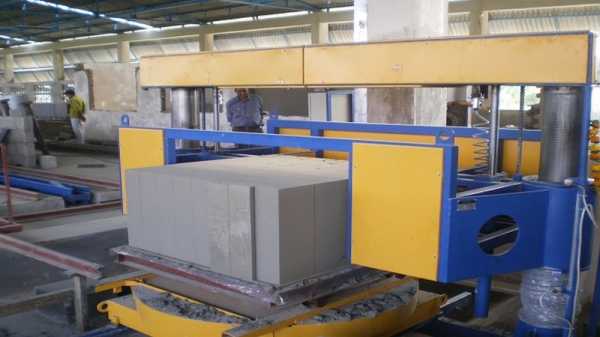
Цеховое производство
Сырье
Газобетон изготавливается на основе сухих компонентов, в смесь которых добавляется вода, с температурой не ниже 45°С. Такие условия обеспечивают быстрое твердение блоков и их прочности. Соблюдение технологии способствует увеличению производительности, улучшению качества материала и уменьшению количества используемого сырьевого цемента, поскольку соответствующий температурный режим обеспечивает стимулирование активности сухих компонентов смеси.
В производстве может быть использован карьерный или речной песок с размером зерен до 2 мм. В нем не должны содержаться илистые и глиняные включения. Сырьевой материал может быть заменен шлаком или золой, являющимися отходами металлургического производства. Такое решение производителя сократит его расходы и позволит получить продукцию с меньшей плотностью.
Планируя производство, следует закупать цемент, имеющий маркировку М 400 или М 500. Алюминиевая пудра должна быть марки ПАП-1 или ПАП – 2. Она может быть заменена на специальную пасту или суспензию, что считается более удобным для производства, ввиду упрощения этапа замешивания. Компонент вступает в реакцию в растворе, имеющем щелочной состав, в ходе которой образуется соль алюмината и выделяется водород, обеспечивающий формирование пор.
Соотношение веществ
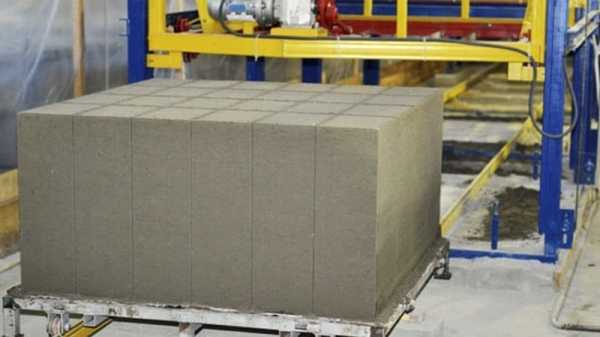
Резка изделия
Качество строительного материала зависит от правильного подбора соотношения составляющих компонентов. Стандартные рекомендации определены только для газоблоков, изготавливаемых автоклавным способом. В них предусмотрено регламентированное соотношение сырьевых компонентов по отношению к общему объему смеси:
- цемент – 50–70 процентов;
- песок – 20–40 процентов;
- алюминиевый порошок – 0,04–0,09 процентов;
- вода – 0,25–0, 8 процентов;
- известь – 1–5 процентов.
Пример
Для получения одного кубического метра газобетона необходимо взять 90 килограмм цемента, долить до 300 литров воды. В полученную смесь добавить 35 килограмм извести, 375 килограмм песка и 50 грамм алюминиевого порошка. В условиях конкретного производства все значения могут быть скорректированы в соответствии с качественными характеристиками сырьевых материалов.
Оборудование для производства газоблоков
Несмотря на то что технология производства строительного материала не отличается сложностью, без специального оборудования и соблюдения алгоритма действий, невозможно получить газобетон хорошего качества. Для этого, до открытия цеха, необходимо приобрести автоматизированную линию. При ее покупке с завода-производителя или его официального представителя, дополнительно обычно предоставляются консультационные услуги в сфере монтажа оборудования, его настройки и подборе оптимального состава сырьевой смеси. Линия содержит оборудование и устройства:
- печь-автоклав;
- формы;
- передвижные поддоны для транспортировки;
- смесители;
- дозаторы;
- аппарат резки готового изделия.
Каждый составляющий элемент комплекса может быть приобретен отдельно, поэтому при выходе его из строя, восстановить линию не составит труда. Она также может быть сформирована из отдельных устройств, однако при таком решении предпринимателю важно учесть соответствие их параметров, которые позволили бы обеспечить гармоничное взаимодействие всей аппаратуры.
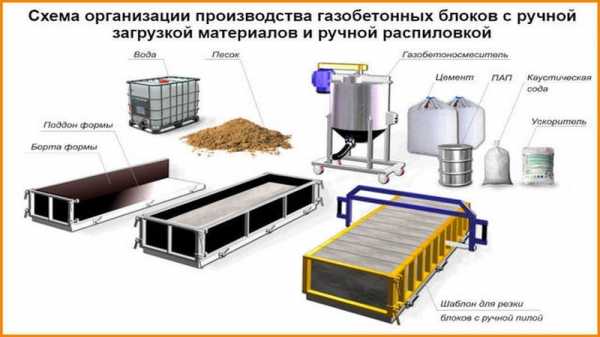
Схема производства
Оборудование для производства газобетонных блоков бывает нескольких типов. При его выборе учитывается планируемая суточная производительность, количество обслуживающего персонала и порядок организации работы.
Для стационарных линий характерна суточная производительность до 60 м3 готовых изделий. Для обеспечения бесперебойной работы, необходимо арендовать или купить производственные и складские помещения, площадью, не меньше 500 м2. Один человек вполне сможет обслужить такую линию, поскольку все операции в ней производятся в автоматическом режиме. Принцип ее функционирования заключается в подаче в стационарно расположенный смеситель сырьевых материалов, в перемешивании их и в заполнении формы смесью с последующим выполнением всех технологических этапов в автоматическом режиме.
При планировании суточной производительности до 150 м3, предпринимателю рекомендуется рассмотреть вариант приобретения конвейерных линий, позволяющих обеспечить оперативное производство строительного материала. Поскольку сроки созревания остаются прежними, необходимо позаботиться об увеличении производственного помещения в отсеке дозревания готовой продукции. Несмотря на то что большинство процессов проводится в автоматическом режиме, для обслуживания устройств понадобится штат работников в минимальном количестве до 8 человек.
Мини-линии актуальны при производстве блоков для реализации собственных потребностей при обеспечении строительных работ, а также при наличии небольшого объема заказов.
На них не получится изготавливать более, чем 15 м3 готовых изделий в сутки. В конструкции стационарно установлены формы, а подвижной частью является смеситель. Преимуществом линии является отсутствие необходимости в больших площадях. На начальном этапе достаточно до 160 м2, поэтому мини-линии пользуются популярностью в качестве стартового варианта.
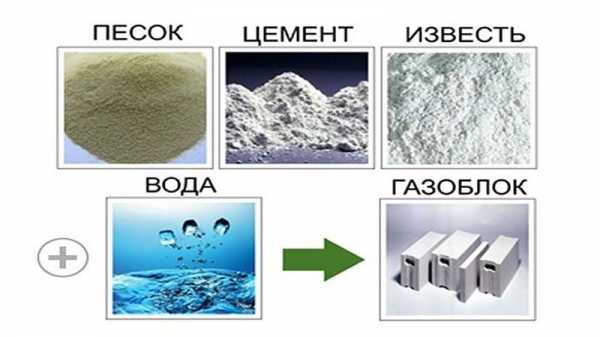
Упрощенная схема
В сфере частного строительства применяются мобильные установки, с помощью которых можно самостоятельно изготавливать газоблоки. Они продаются в комплекте с компрессором и могут функционировать от бытовой электросети. Их приобретение окупается в кратчайшие сроки, поскольку расходы на строительные работы снижаются на 30 процентов.
Технология производства газобетона
Технология производства зависит от решения производителя относительно вида и характеристики готового изделия.
Газобетон бывает автоклавный и неавтоклавный. Неавтоклавный строительный материал стоит дешевле, поскольку для него характерна хрупкость, а для обеспечения производства материала затрачивается меньше средств, поскольку не нужно приобретать дорогостоящее оборудование- автоклав, оплачивать электроэнергию на его функционирование, а также вкладывать деньги в его содержание. Неавтоклавная технология производства проводится в соответствии с определенным алгоритмом:
- Взвешивание компонентов смеси в соответствии с рецептурой.
- Перемешивание вручную или при помощи специального оборудования.
- Выгрузка в формы.
- Выдержка изделия.
- Извлечение готовой продукции из формы.
В связи с тем, что в результате химических реакций, происходящих в смеси, будет происходить газообразование, формы заполняются только наполовину. Ожидание окончания реакции занимает до четырех часов, за которое компоненты полностью занимают объем формы. После отбора из форм излишек состава, его оставляют на вызревание, которое будет длиться до 16 часов, по истечении которых происходит распалубка и перегрузка на поддоны для набирания отпускной прочности, что длиться три дня. После завершения всех операций, изделие отправляется на склад, однако продавать его можно только через месяц, когда оно наберет марочную прочность.
В бизнес-план производства газобетона следует включить расходы на приобретение профессионального оборудования.
Технология производства на первых этапах работ практически не отличается от безавтоклавного метода. Набирается необходимое количество всех компонентов при помощи дозаторов, загружается в смеситель и перемешивается. Для выполнения этой задачи допускается использование бетономешалки. Через 15 минут после окончания смешения исходных ингредиентов, вводится алюминиевый порошок, являющийся газообразователем. Вещество вступает в реакцию с базовой смесью без автоклава.
Смесь сырьевых компонентов разливают по формам и выдерживают 6 часов, после чего проводится нарезка газоблоков, которые впоследствии должны набрать плотность на протяжении 18 часов. После завершения базовых операций, проводится автоклавирование. Сформированные блоки газобетона загружаются в герметичную камеру печи, в которой при высокой температуре каждый блок обрабатывается водяным паром под давлением до 12 кг/см2.
Неавтоклавное изделие сушится в естественных условиях. Автоклавная продукция не требует сушки, однако ее все равно нужно выдержать месяц до набора прочности.
Важным этапом производства обеих видов газобетона, является сохранение целостности в процессе транспортировки к потребителю. Для реализации этой задачи необходимо готовое изделие упаковать в термоусадочную пленку и транспортировать на деревянных поддонах.
Вконтакте
Одноклассники
Google+
101biznesplan.ru
Неавтоклавный газобетон: характеристики, технология производства
Газобетон, или искусственный камень, относится к легким ячеистым бетонам. Свое название они получили из-за наличия в структуре небольших сферических пор от 1 до 3 мм в диаметре, равномерно распределенных по всему объему. Замкнутые ячейки образуются в результате химической реакции между порообразователем, например, алюминиевой пудрой и водой. Их наличие и объясняет положительные технические характеристики газобетона, привлекающие строителей.
Оглавление:
- Технические параметры неавтоклавного бетона
- Процесс изготовления
- Как сделать газоблок в домашних условиях?
Существуют и другие технологии создания пор в структуре материалов, например, введение в цементно-песчаную смесь технической пены, которая приготавливается в соответственном агрегате. В результате получается не менее популярный неавтоклавный пенобетон. Далее будет рассмотрены его свойства и способы производства.
Характеристики и особенности
Автоклавы – это специальные печи, где согласно технологии создается повышенная температура и избыточное давление для спекания бетонной смеси. Изготовленный таким образом стройматериал называется автоклавным. Естественно, что для этого процесса необходимо наличие оборудования промышленного предприятия.
Неавтоклавный газобетон твердеет естественным путем под действием атмосферного давления. Иногда, особенно в первые сутки, на производстве создают повышенную температуру для лучшего «созревания». Технология изготовления не представляет трудности, поэтому этим можно заниматься дома самостоятельно. Тем более что по цене газобетонные блоки своими руками обойдутся более чем на 30 % меньше заводских, без учета транспортных расходов.
Правда, бюджетность этого стройматериала сопровождается характеристиками, уступающими искусственному камню, созданному в автоклавах. Речь идет о следующих свойствах:
- Небольшая прочность. Невозможно добиться автоклавной твердости, создавая газобетон своими руками в домашних условиях.
- Длительный период твердения.
- Отсутствие твердости влечет за собой значительную усадку неавтоклава: 2-3 мм против 0,3 автоклавного.
- Необходимость использования армопоясов в местах наибольшей нагрузки.
- Несовершенная поверхность, которая сказывается при возведении стен и требует дополнительных затрат.
Неавтоклавный и автоклавный газобетон отличаются друг от друга многими параметрами, но первый все-таки обладает преимущественными характеристиками, в том числе:
1. в его составе имеются только природные компоненты, которые не выделяют вредностей;
2. неподвластен воздействию влаги;
3. способен сохранять тепло;
4. обладает высокой звукоизоляцией;
5. огнестоек и сохраняет прочность при термических нагрузках и открытом огне;
6. экологичен и стоек к гниению;
7. оказывает противодействие микробным и грибковым образованиям;
8. имеет низкую стоимость производства;
9. легкий и удобный для механической обработки различными инструментами, при этом сохраняет значимые свойства, что облегчает прокладку через него коммунальных сетей;
10. значительные габариты блоков способствуют увеличению скорости монтажа;
11. возможность изготовления на полигоне рядом со строительной площадкой, что позволяет снизить расходы на транспортировку;
12. легкий вес избавляет от необходимости в подъемных механизмах, а это удешевляет стоимость строительного объекта;
13. возможность использования в качестве монолитного бетона;
14. стойкость при землетрясениях.
Производство неавтоклава обходится без больших затрат электроэнергии, а стоимость базового оборудования вполне приемлема даже для частного лица, планирующего изготавливать этот материал своими силами.
Схема производства
В состав базовой линии для изготовления неавтоклавного ячеистого бетона входит следующее оборудование:
- смеситель для ручной загрузки компонентов, который передвигается вдоль поддонов на колесах;
- поддоны-формы, куда разливается готовая смесь;
- борта для форм, легко снимающиеся с поддонов;
- специальные пилы для удаления горбушки и нарезания блоков.
Кроме этого при покупке поставляется информационная документация: чертежи, инструкции, руководство по эксплуатации, схема работы.
Схематично технологический производственный процесс выглядит таким образом:
Дозированный цемент | Просеянный и взвешенный песок | Определенное количество воды с температурой 40–50°C | Дозированный порообразователь – алюминиевая суспензия (вода, пудра, синтетическое моющее средство) |
↓ | |||
Поступают в смеситель для перемешивания | |||
↓ | |||
Смесь заливается в поддоны-формы | |||
↓ | |||
Подъем, созревание смеси и предварительный набор прочности около 2-х часов | |||
↓ | |||
Удаление горбушки пилой | |||
↓ | |||
Освобождение поддонов от бортов (распалубка) | |||
↓ | |||
Нарезание блоков из массива | |||
↓ | |||
Прогревание теплоизолирующим колпаком разрезанных блоков 6-10 часов | |||
↓ | |||
Перенос блоков на транспортный поддон, упаковка, отправление на склад | |||
↓ | |||
Очистка смазка, установка бортов на освободившуюся форму для подготовки к следующей заливке |
Согласно инструкции песок и цемент вначале отмеряют, а затем загружают. Суспензию предварительно готовят в небольшом объеме, смешивая компоненты дрелью с насадкой.
Количество и состав оборудования зависит от мощности, которою определяет заказчик. Также, при желании, можно к базовой комплектации купить вспомогательные технологические элементы за дополнительную стоимость (весы, колпаки, водонагреватель и прочее).
Как сделать в домашних условиях?
Будущему хозяину небольшого дома изготовить такой газобетон самому очень привлекательно, с точки зрения экономии стоимости строительства. Правда, для получения нужных характеристик необходимо иметь помощников, соответствующее оборудование (хотя бы бетономешалку, формы для заливки, резательные струны), четкое соблюдать этапы, грамотно дозировать ингредиенты.
Для получения газобетона марки D600 нужно придерживаться следующих пропорций состава:
- портландцемент ПЦ500 D0 – не менее 65 %;
- очищенного песка должно быть 30 %;
- известковой муки – 5–10 %.
Разброс в содержании последнего компонента объясняется цветовым предпочтением. Большее количество извести дает более светлую окраску. Еще добавляется алюминиевая пудра до 0,48 % для выделения водорода, образования пены и, в дальнейшем, получения сферических пор в готовом ячеистом бетоне.
Количество необходимого материала, чтобы своими руками сделать 1 м3 неавтоклавного искусственного камня представлено в таблице:
Чистая питьевая вода | 250 – 300 л |
Мелкий, до 2 мм чистый песок | 250 – 350 кг |
Цемент марки M500D0, M400D0 | 260 – 320 кг |
Алюминиевая пудра | 0,5 – 0,7 кг |
Смазка для контейнеров | 0,3 – 0,5 кг |
Добавки для улучшения характеристик, в том числе прочности | 1– 3 кг |
Пошагово этот процесс будет выглядеть так:
- Тщательное взвешивание сухих компонентов.
- Замешивание ингредиентов в бетономешалке с добавлением предварительно подготовленной алюминиевой эмульсии.
- Заливка полученной смеси в контейнеры до половины, так как масса увеличивается в объеме из-за образования ячеек. Заполненные формы должны находиться на защищенной от непогоды территории.
- Через 6–8 часов снятие горбушки массива металлическим прутом или специальной пилой.
- Через 12 часов полуготовые блоки извлечь из контейнеров и оставить на 48 часов на ровной поверхности набирать твердость.
- Через 28 суток газобетонные блоки будут готовы для эксплуатации.
Очевидно, что для изготовления блоков бетона лучше применять спецоборудование, которое обеспечит отличное качество, и процесс займет меньше времени. А аренда агрегатов, даже для личного домостроения, ненамного увеличит стоимость искусственного камня.
stroitel-lab.ru
мини завод, расчет и технология
Продажа строительных материалов считается одним из наиболее прибыльных дел. Вне зависимости от обстоятельств строительные работы никогда полностью не останавливаются. Иными словами, на такую продукцию всегда будет спрос. Опытные строители отмечают, что использование и производство газобетона позволяет снизить финансовые затраты на проведение работ. Блоки из этого стройматериала не причиняют вреда окружающей среде.
Газоблоки универсальны, они могут применяться на частных и на промышленных строительных площадках. Они обладают рядом положительных свойств, которых можно добиться в ходе производства, при добавлении определенных компонентов в состав раствора. Если вы намерены сделать мини бизнес на продаже блоков, то лучше всего стать владельцем небольшого завода, специализирующегося на производстве таких изделий. Приобретя такой завод, вам удастся самостоятельно производить газобетон. Затраты на оборудование, материалы и другие нужды вполне приемлемы: они не превысят расходы на закупку готовых изделий.
Какой тип производства выбрать?
Перед тем как начать заниматься производствами стройматериалов на мини предприятии, необходимо определиться и записать в бизнес план способ, с помощью которого будут выпускаться блоки. В частности, существует неавтоклавный, а также автоклавный метод. Применение первой методики считается менее затратным, так как смеси затвердевают естественным путем, без применения оборудования. Поэтому нет необходимости приобретать спецтехнику и расходовать электроэнергию. Но данный способ влечет за собой существенную усадку изделия. Так, у автоклавных блоков усадка составляет меньше миллиметра на метр, а у неавтоклавных несколько миллиметров на метр. Кроме того, для этого способа требуется больше цементного раствора.
Вместе с тем у этого способа есть и свои преимущества. Например, изделия обладают повышенными теплоизоляционными характеристиками. При применении автоклавного метода под воздействием температур и значительного давления в изделиях образуется тоберморит, придающий блокам высокую прочность. Данная особенность позволяет расширить сферы применения материала, однако для создания пеноблоков понадобится доставить мини заводы спецтехнику, нанять квалифицированных работников.
Производство неавтоклавного газобетона с прогревочными камерами.При производстве средних партий стройматериала высок риск банкротства мини предприятия. Поэтому, для масштабных работ и выпуска больших партий изделий, желательно изготавливать автоклавные газоблоки. Все ваши шаги должны быть прописаны в бизнес плане.
Если же вы намерены открыть мини предприятие, можно применять неавтоклавный способ при работе с газобетоном. В то же время существуют методы, помогающие улучшить характеристики неавтоклавных блоков. При этом вам не потребуется закупать оборудование. Следует лишь воспользоваться специальными добавками, к которым относят микрокремнезем, разные виды стекловолокна и другие средства.
Вернуться к оглавлениюЧто нужно для бизнеса?
Чтобы начать работу с небольшим заводом, специализирующимся на выпуске газобетонных блоков, нужен определенный финансовый капитал, значительная часть которого будет потрачена на покупку оборудования и специальной техники. Чистый доход, начисляемый таким заводам, способен достигать 2000 долларов. При этом завод окупается за один год, но только при условии выпуска высококачественных и актуальных газоблоков, использование которых поможет строить безопасные и надежные здания.
Вернуться к оглавлениюПримерный расчет затрат
Первоначальные финансовые расходы, прописанные в бизнес плане, выглядят приблизительно так:
- аренда – 250 долларов;
- оборудование – 10 000 долларов;
- заработная плата – 1600 долларов;
- ремонт на предприятии – 750 долларов;
- сырье – 1500 долларов.
Если не учитывать финансовые затраты на приобретение оборудования, то себестоимость кубометра блоков из газобетона составляет около 25 долларов (рыночная цена – около 40 долларов). За одну смену предприятие может сделать 2500 м3 стройматериала. В общей сложности инвестиции должны составить около 50 800 долларов. Таким образом, в соответствии с планом, ваш бизнес может окупиться всего за несколько месяцев.
Вернуться к оглавлениюТехнология изготовления
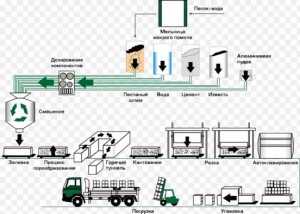
При изготовлении газоблоков специалисты пользуются такими ингредиентами:
- вода;
- пудра из алюминия;
- гипсовая добавка;
- известка;
- строительный песок;
- цемент.
Весь план изготовления изделий состоит из нескольких этапов. Прежде всего, сырье необходимо тщательно просеять, дабы очистить материалы от примесей. После этого следует смешать песок с водой. Затем необходимое количество компонентов загружают в оборудование, за счет применения которого при смешивании происходят нужные реакции: получается раствор с ячеистой структурой. Готовую смесь формируют, согласно плану.
Чтобы материал приобрел необходимую высоту и форму, его помещают в оборудование для формовки. Завершительная стадия формирования наступает, когда состав достигает требуемой высоты. При этом должно выделяться минимальное количество газов. После затвердения газоблоков их можно достать из форм, после чего разрезать по параметрам, прописанным в плане. Остатки применяются в производстве новых изделий. Следующая стадия предполагает обработку с помощью жидкости и тепла. Затем газоблоки можно запаковывать и отправлять на склад.
Вернуться к оглавлениюМатериалы и оборудование
На небольшое предприятие нужно закупать оборудование. Для более точного расчета в плане можно указать каждое устройство. Вместе с тем на современном рынке представлен укомплектованный набор оборудования. Приобретя его, вы сможете сэкономить средства. В такую линию входят:
- емкость;
- шаровая мельница;
- парогенератора;
- растворосмеситель;
- автопогрузчик;
- станок для фрезерования;
- емкости для формовки газоблоков;
- дозатор;
- автоклавный аппарат;
- специальное сито.
Оборудование необходимо производству для работы с цементом, пастой, известкой, песком.
Вернуться к оглавлениюПомещение и персонал
Для выполнения плана на небольшом предприятии в одну рабочую смену нанимают бригадира, а также нескольких работников. В свою очередь, заводские помещения размещаются на территории, минимальная площадь которой составляет 1000 квадратных метров. Предприятие нужно зонировать на следующие отделения:
- бытовые;
- складские помещения;
- комнаты, предназначенные для того, чтобы запаковывать и комплектовать продукцию;
- отделение для формовки;
- отделение для приготовления смесей;
- складское помещение для используемого сырья.
Кому продавать продукцию?
Чаще всего газоблоки приобретают строительные фирмы, занимающиеся возведением зданий и отделочными работами. Но для продажи больших объемов изделий необходимо завязать деловые отношения со специализированными магазинами. Если вам удастся регулярно поставлять продукцию в такие точки, то в складских помещениях товар не будет долго залеживаться.
Вернуться к оглавлениюИтоги
Технология изготовления газоблоков требует привлечения профессионалов. Однако для небольшого предприятия вам не понадобится нанимать множество рабочих и тратить крупные суммы денег на поддержку бизнеса. При наличии партнерских отношений и правильном ведении дел предприятие будет приносить вам стабильный доход.
kladembeton.ru
Технология производства газобетона — АлтайСтройМаш
С изобретения технологии начал свою работу весь завод. А сейчас её легко приобретают все заказчики в комплекте со своим оборудованием. Для начала расскажем о преимуществах нашей технологии перед аналогами:
- быстро окупает производство – от пары недель до нескольких месяцев;
- производит газобетон высшего качества — по ГОСТ;
- даёт отличный результат с минимальными ресурсами — даже без ускорителей твердения и фиброволокна.
Технология как план действий
Для каждой линии описан свой порядок работы. Его соблюдение – одна их составляющих наивысшего качества. Соблюдать технологию просто, потому что она похожа на план:
- подготовить формы – монтаж и смазка;
- приготовить смеси из компонентов;
- заполнить формы смесью;
- нарезать застывший массив;
- прогреть блоки;
- разобрать массив и упаковать блоки – обернуть полиэтиленом.
При покупке линии вы получаете массу подробностей по каждому этапу и приступаете к практике — она важнее любых советов.
Об особенностях работы с каждой линией читайте в разделах:
- мини-линии;
- стационарное оборудование;
- конвейерное производство.
Линии отличаются по производительности и степени автоматизации, поэтому для каждой линии — своя технология. Мы также делаем линии на заказ, по индивидуальным пожеланиям клиента. Таких примеров на сайте нет, но знайте, что заказы на оборудование по вашей задумке мы тоже принимаем. В таких случаях технологию пишем специально под изготовленную линию.
Главное преимущество технологии «АлтайСтройМаш»
Это простота.
Технология считается совершенной, когда её можно объяснить даже ребёнку. И сейчас вы уже понимаете, что производство газобетона на оборудовании «АлтайСтройМаш» — действительно простой процесс.
Заказчики оборудования сами справляются и со сборкой линии, и с запуском производства. Кроме иллюстраций и видео-инструкций, у каждого клиента есть свой технолог. Он контролирует запуск, отвечает на все вопросы, а при необходимости – лично налаживает производство.
Прочитайте, какие минимальные требования нужно соблюсти для производства. Может у вас уже всё готово к производству?
Читать о Требованиях к производству
asm.ru
Неавтоклавный газобетон: технологии производства, фото
Газобетон в последнее время является очень популярным строительным материалом, благодаря ряду своих достоинств. Зачастую застройщики отдают предпочтение более дешевому его варианту – неавтоклавному газобетону. Но что представляет собой этот материал, чем отличается автоклавный и неавтоклавный газобетон и стоит ли на нем экономить?
Далее мы постараемся ответить на все эти вопросы и дать исчерпывающую информацию по данному типу ячеистого бетона.
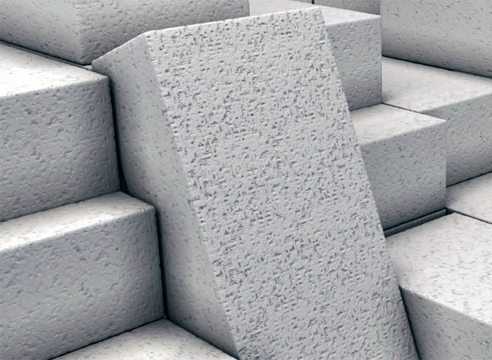
Полученные неавтоклавным способом газобетонные блоки
Общие сведения
Многие люди считают, что газобетон – это современный материал. Однако,на самом деле он был запатентован впервые еще в 1889 г. в Праге неким изобретателем Гофманом. Он придумал изготавливать материал на основе газа, получаемого в результате химической реакции между бикарбонатом натрия и соляной кислотой.
В Голландии в начале прошлого века была запатентована технология приготовления газобетона с использованием дрожжей. Немного позже в Германии предложили применять в качестве газообразующего вещества металлическую пудру.
Практически современная технология изготовления пористого бетона была разработана в Швейцарии изобретателем Эриксоном в 1923 г. Уже в 1925 году было налажено промышленное производство неавтоклавного газобетона как строительного материала. Очень скоро его производство появилось и во многих других странах.
В то время материал приготавливали на основе портландцемента, а немного позже стали использовать и вяжущие на основе зол и шлаков. Изначально материал был придуман как утепляющий, однако уже в 30-х годах удалось получить и конструкционный газобетон. Его применяли для ограждающих конструкций в малоэтажных зданиях.
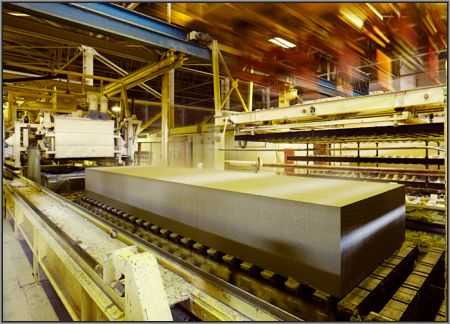
Современная линия производства неавтоклавного газобетона
Таким образом, материал сложно назвать совсем новым, так как он прошел уже достаточную и вполне успешную проверку временем.Конечно, на сегодняшний день используют современное технологическое оборудование для производства неавтоклавного газобетона, с новыми видами тепловлажностной обработки. Кроме того, подобраны самые оптимальные составы, что значительно повысило качество изделия.
Технология производства
Состав
В составе данного типа ячеистого бетона используют следующие основные компоненты:
- Портландцемент – является вяжущим элементом;
- Наполнители – песок в чистом виде, либо с добавлением золы-уноса ТЭЦ, мела, гипса и пр.
- Алюминиевая пудра – используется при формировании материала в качестве парообразующего вещества.
Кроме того, для улучшения характеристик, в состав неавтоклавного газобетона добавляют различные модифицированные добавки, к примеру, полуводный микрокремнезем или гипс. Для ускорения процесса твердения используют хлорид кальция.
На фото — структура изделия
На сегодняшний день ведутся работы по увеличению прочностных характеристик изделия выполненного неавтоклавным методом. Самым перспективным считается использование различных армирующих добавок, представляющих собой волокна разного происхождения.
Это могут быть:
- Стекловолокна;
- Полимерные волокна;
- Базальтовые;
- Асбестовые и пр.
Кроме того, положительный результат дает и увеличение на 5-10 процентов содержания наполнителя в составе, к примеру, золы-уноса или микрокремнезема. Причем, это позволяет не только повысить прочность ячеистого бетона, но и уменьшить его стоимость.

Формы для изготовления блоков
Изготовление
Технология производства неавтоклавного газобетона основана на том, что в результате химической реакции алюминиевой пудры и щелочи в составе смеси, внутри нее образуются поры, которые заполняются воздухом. Получившуюся пористую смесь оставляют застывать в естественных условиях, т.е. без применения автоклавов (специальных печей).
Иногда оборудование для неавтоклавного газобетона содержит пропарочные печи. Благодаря качественному пропарочному режиму, тоже улучшаются прочностные характеристики изделия.
Надо сказать, что неавтоклавному ячеистому бетону свойственны сквозные поры, в результате чего он обладает плохими гидроизоляционными свойствами. Однако, благодаря внедрению современных технологий, этим параметром материал стал приближаться к автоклавному газобетону.
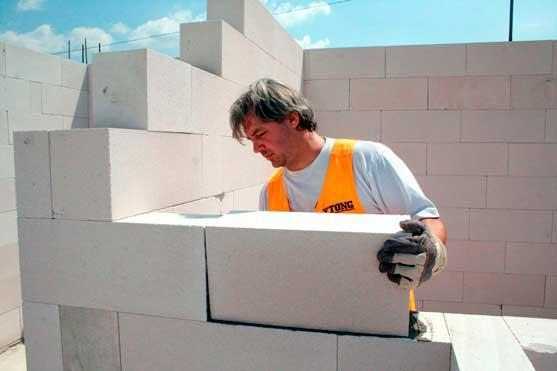
Легкий блок удобно укладывать своими руками
Особенности материала
Достоинства
Характеристики неавтоклавного газобетона во многом схожи с автоклавным материалом.
В частности, можно выделить следующие моменты:
- Низкая плотность при высокой прочности. Благодаря пористости материала снижается его цена, за счет уменьшения расхода компонентов.
- Небольшой вес, в результате чего с материалом легко работать. Кроме того, снижается нагрузка на фундамент здания.Это обеспечивает не только долговечность строения, но и экономию при его возведении, так как можно использовать менее мощную основу.
- Отличные теплоизоляционные свойства благодаря пористости. Данное свойство обеспечивает энергосбережение при отоплении помещений.
- Легко обрабатывается.Если обычно выполняется резка железобетона алмазными кругами, то для газобетона можно использовать обычную ножовку.
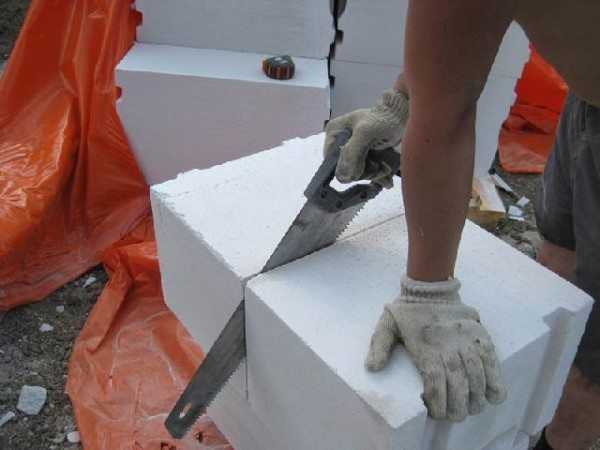
Разрезка блока ножовкой
Соответственно, чтобы подвести коммуникации в помещении не понадобится алмазное бурение отверстий в бетоне, так как можно воспользоваться обычными сверлами.
- Пожаростойкость. Материал является абсолютно не горючим. Поэтому его можно использовать для обшивки стен, когда необходимо обеспечить надежную пассивную пожаробезопасность. (См. также статью Облицовка газобетона: как сделать.)
- Экологичность. Материал не только выполнен из экологически чистых компонентов, но еще и обладает отличной паропропускной способностью, что обеспечивает благоприятный микроклимат внутри зданий, построенных из газобетона.
- Инструкция по укладке, такая же, как и при работе с более традиционным материалом, к примеру, кирпичом.
Совет!
Газобетон является отличным материалом для межкомнатных перегородок, так как обладает хорошими шумоизоляционными свойствами.
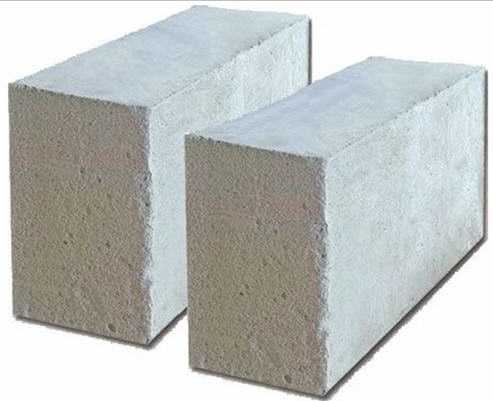
Автоклавные блоки
Отличия между материалами, выполненными по разным технологиям
Теперь рассмотрим в чем отличие автоклавного газобетона от неавтоклавного.
А заключаются они всего в нескольких моментах:
- Неавтоклавный материал обладает большей усадкой, которая составляет примерно 2-3 мм/м, в то время как автоклавный имеет усадку не более 0,3 мм/м. Если при заливке монолитных изделий данный недостаток практически незаметен, то при возведении сборных конструкций он проявляется гораздо больше. (См. также статью Шпаклевка по бетону: особенности.)
- Время твердения – как не сложно догадаться, у материала изготовленного неавтоклавным методом время твердения значительно больше. Однако,этот недостаток имеет значение только при производстве изделия.
- Выполненный автоклавным методом газобетон более прочный, так как в его составе образуется минералтоберморит. При изготовлении неавтоклавного ячеистого бетона, образование тоберморита невозможно. Поэтому изделие используют в тех случаях, когда на него не предполагаются большие нагрузки.
- Теплоизоляционные свойства неавтоклавного газобетона немного лучше, что связано с большей его пористостью.
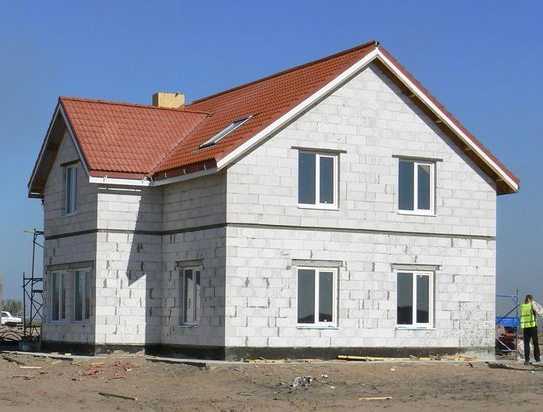
Дом из газобетонного блока
В остальном же характеристики изделий очень схожи.
Обратите внимание!
В продаже зачастую можно встретить газобетон низкого качества, изготовленный «кустарным» способом.
Определить его не сложно, так как он сильно крошится.
Вывод
Не смотря на то, что полученный неавтоклавным методом газобетон появился достаточно давно, благодаря постоянному совершенствованию технологии его изготовления, он может считаться вполне современным материалом. В ряде случаев его использование является более целесообразным, чем применение автоклавного газобетона. Однако, если важна высокая прочность материала, то автоклавный более предпочтителен.
Из видео в этой статье вы можете получить дополнительную информацию по данной теме.
masterabetona.ru
Производство газобетона
Производство газобетона
Введение
Газобетон используется в строительной индустрии более 100 лет. В России наиболее интенсивное развитие он получил в последние пять лет.
Газобетон является современным перспективным строительным материалом, наиболее часто используемым при строительстве жилых и нежилых зданий.
При производстве газобетона вредные для здоровья примеси не используются. Он находится на втором месте по экологической чистоте после дерева.
Газобетон — разновидность ячеистого бетона <#»justify»>.Номенклатура выпускаемой продукции и требования к ней
Стеновые блоки соответствуют ГОСТ 21520-89 классу В2,5 и В3,5 по прочности при величине средней плотности равной соответственно 600 и 700 кг/м3.
Допустимые отклонения для линейных размеров мелких стеновых блоков составляют: по длине и толщине ± 2-4 мм, по высоте ± 1-3 мм. в зависимости от категории качества изделий.
Коэффициент теплопроводности газобетонных изделий в сухом состоянии не должен превышать значений, установленных ГОСТ 31359-2007: для марки D600 коэффициент теплопроводности равен 0,14 Вт/(м), для марки D700 коэффициент теплопроводности равен 0,17 Вт/(м).
Морозостойкость газобетонных изделий — F75, отпускная влажность — 25%.
Рисунок 1.1. Блоки стеновые
Предназначены для выполнение несущих и самонесущих, внутренних и наружных стен зданий и сооружений.
Объём поддона 0.75 м3. Размеры поддона с продукцией: L=1.0 м, B=0.625 м, H=1.305 м.
Таблица 1.1.
Условная маркаРазмеры блока, ммКоличество блоков в поддонеВес поддона, кг (при влажн. 25% — 30%.)Количество м² в поддонеlBH Б1-D600-В2,5 62510025048 560 — 5857,50 Б1,2-D600-В2,5 625120250406,25 Б1,5-D600-В2,5 625150250325,00
Рисунок 1.2. Блоки стеновые
Предназначены для выполнения несущих и самонесущих, внутренних и наружных стен зданий и сооружений.
Таблица 1.2.
Условная маркаРазмеры блока, ммКоличество блоков в поддонеВес поддона, кг (при влажн. 25% — 30%.)Количество м² в поддонеlbhБ2-D600-В2,566002200225024450 — 4703,6Б2-D700-В3,5Б3-D600-В2,566003300225016450 — 4702,4Б3-D700-В3,5Б4-D600-В2,566004400225012450 — 4701,8Б4-D700-В3,5
2. Характеристика сырьевых материалов
.1 Вяжущее
Вяжущие содержат оксид кальция (CaO), имеющий решающее значение в производстве газобетона. Содержание активных СаО+МgО в извести должно быть не менее 70%, скорость гашения — 5-15 минут.
В качестве основного вяжущего используется строительная комовая известь воздушного твердения, отвечающая требованиям ГОСТ 9179-77 (1989). Влажность гидратной извести не должна быть более 5%. Используется известь II сорта, количество пережога у которой 2%, скорость гашения менее 8 минут, удельная поверхность 5500 см2/г. В этом случае, при приготовлении растворной смеси для получения газобетонной массы, выделяется большое количество теплоты, что способствует процессу порообразования, предохранению оседания газонасыщенной массы до ее затвердевания и повышению прочности готовых изделий ячеистой структуры. Известь доставляется автотранспортом. Месторождение г. Искитим (Новосибирская область) ЗАО «Искитимский известняковый карьер».
Также в качестве второго компонента вяжущего используется высококачественный бездобавочный портландцемент М500 производства ОАО «Искитимцемент» (г. Искитим, Новосибирская область).
.2 Кремнеземистый компонент
Песок для производства используется только карьерный, промытый и обогащенный, с содержанием кварца не менее 85%. Не допускается содержание в песке избыточных примесей по ГОСТ 8736-93: слюды не более 0,5 %, илистых и глинистых примесей не более 3 %.
Применяется Марусинский песок, имеющий истинную плотность 2,7 г/см3, насыпную плотность 1,3-1,6 г/см3. Производитель ЗАО «Левобережный песчаный карьер».
.3 Газообразователь
В качестве газообразователей главным образом используется алюминиевая пудра марок ПАП-1 и ПАП-2, отвечающая требованиям ГОСТ 5494-95 Пудра алюминиевая пигментная с содержанием активного алюминия 91,1…93,9 % с временем активного (максимума) газовыделения в течение 3…4 мин. от начала смешивания компонентов газобетонной массы. Для получения водной алюминиевой суспензии используется сульфанол, обладающий свойствами ПАВ из расчета 25 г на 1 литр воды .Общий расход газообразователя 0,25…0,86 кг на 1 м3 бетона плотностью 500…800 кг/м3. Применяется алюминиевая пудра марки ПАП-1. Производитель «Сибирский лакокрасочный завод» г. Новосибирск.
.4 Добавки
Добавки используются в качестве ускорителей твердения бетона и в качестве стабилизаторов структуры поризованной массы. В качестве добавки стабилизатора структуры поризованной массы используется гипсовый камень (ГОСТ 4013-82).
.5 Вода
Применяется пресная вода, отвечающая требованиям ГОСТ 23732-79.
Содержание в воде органических поверхностно-активных веществ, сахаров и фенолов, каждого не должно быть более 10 мг/л.
Окисляемость воды не должна превышать 15 мг/л.
3. ВЫБОР СПОСОБА И ТЕХНОЛОГИЧЕСКОЙ СХЕМЫ ПРОИЗВОДСТВА
.1 Характеристика существующих способов производства
Технология производства изделий из ячеистых бетонов состоит из следующих этапов: подготовка сырьевых материалов, приготовление формовочной массы, изготовление арматурных каркасов, формование изделий, тепловая обработка, контроль качества и складирование.
Технологии производства стеновых изделий из ячеистых бетонов различаются:
- по способу подготовки сырьевых материалов;
- по способу формования изделий;
- по условиям твердения изделий;
- по способу организации технологического процесса.
Технология подготовки сырьевых материалов осуществляется по нескольким схемам:
- сухой совместный помол компонентов;
- мокрый помол компонентов;
- комбинированный способ.
Сухой совместный помол и гомогенизация обеспечивают хорошее смешение составляющих исходных материалов, при этом достигается высокое качество получаемого вяжущего. Достоинство этого способа — простота дозировки исходных материалов, наиболее полное использование оборудования, надежный контроль за производством. Недостаток этого способа — относительно большой расход энергии на помол.
На рисунке 3.1. приведена схема, подготовки сырьевых материалов путем сухого совместного помола компонентов.
Рисунок 3.1. Подготовка сырьевых материалов путем сухого совместного помола компонентов
Схема с мокрым помолом компонентов. Недостаток этой схемы — более низкое качество перемешивания, чем в первом варианте, однако при мокром помоле кремнеземистого компонента снижаются затраты на устройство обеспечивающих установок, повышается производительность мельниц. Кроме того, отсутствие сушки для большей части материалов, снижает энергозатраты.
На рисунке 3.2 приведена схема подготовки сырьевых материалов путем мокрого помола компонентов.
Рисунок 3.2. Подготовка сырьевых материалов путем мокрого помола компонентов
Комбинированный способ подготовки сырьевых материалов предусматривает применение песка карьерной влажности. К недостаткам этого способа следует отнести трудности получения вяжущего со стабильными свойствами. В практике заводского производства изделий из ячеистого бетона широкое применение получили схемы с сухим совместным и раздельным мокрым помолом компонентов, при этом решающее значение для выбора схемы имеет вид сырья.
Технология формования изделий:
- литьевая технология;
- вибрационная технология;
- резательная технология.
Литьевая технология предусматривает отливку изделий, как правило, в отдельных формах из текучих смесей, содержащих до 50…60% воды от массы сухих компонентов (В/Т=0,5-0,6). При изготовлении газобетона применяемые материалы — вяжущее, песчаный шлам и вода, дозируют и подают в самоходный газобетоносмеситель, в котором их перемешивают 4-5 минут; затем в приготовленную смесь вливают водную суспензию алюминевой пудры и после последующего перемешивания тесто с алюминевой пудрой газобетонную смесь заливают в металлические формы на определенную высоту с таким расчетом, чтобы после вспучивания формы были заполнены доверху.
Избыток смеси («горбушку») после схватывания срезают проволочными струнами. Для ускорения газообразования, а также процессов схватывания и твердения применяют «горячие» смеси на подогретой воде с температурой в момент заливки в формы около 40°С.
Вибрационная технология газобетона заключается в том, что во время перемешивания в смесителе и вспучивания в форме смесь подвергается вибрации. Тиксотропное разжижение, происходящее вследствие ослабления связей между частицами позволяет уменьшить количество воды затворения на 25-30% без ухудшения удобоформуемости смеси. В смеси, подвергающейся вибрированию, ускоряется газовыделение — вспучивание заканчивается в течение 5-7 мин вместо 15-20 мин при литьевой технологии. После прекращения вибрирования газобетонная смесь быстро (0,5-1,5 ч) приобретает структурную прочность, позволяющую разрезать изделие на блоки, время автоклавной обработки также сокращается.
Резательная технология изготовления изделий из ячеистого бетона предусматривает формование вначале большого массива (объемом 10-12 м3, высотой до 2 м). После того как бетон наберет структурную прочность, массив разрезают в горизонтальном и вертикальном направлениях на прямоугольные элементы, а затем подвергают тепловой обработке. Полученные элементы калибруют на специальной фрезерной машине, а затем отделывают их фасадные поверхности. Из готовых элементов имеющих точные размеры, собирают на клею плоские или объемные конструкции, используя стяжную арматуру. Таким путем получают большие стеновые панели размером на одну или две комнаты и высотой на этаж .
Способ твердения изделий.
В зависимости от вида вяжущего твердение изделий из ячеистых бетонов может осуществляться двумя способами: автоклавным, когда тепловлажностная обработка производится в автоклавах при давлении 0,8…1,3 МПа и температуре 175…200 0С, и неавтоклавным, когда твердение происходит при температуре 60…90 0С при повышенной влажности воздуха (пропарочные камеры, электропрогрев и др.).
Тот и другой способ твердения имеет свои технические преимущества, однако с экономической точки зрения неавтоклавный способ твердения можно считать предпочтительным.
3.2 Обоснование выбора способа производства
В данном проекте для проектирования завода по производству газобетонных блоков был выбран автоклавный способ твердения, при подготовке кремнеземистого компонента по мокрому способу.
3.2.1 Выбор технологической схемы производства
Технологические схемы в принятом к разработке автоклавном способе с формованием изделий методом резки массива различаются подготовкой сырьевых материалов. Технологические схемы бывают: с подготовкой сырьевых материалов путем мокрого помола компонентов и сухого совместного помола компонентов.
Технологическая схема должна предусматривать переработку возможных отходов собственного производства, обеспечивать поточность и компактность производства, а также систему очистки технологических выбросов (воды, воздуха, газов).
Техническая и экономическая эффективность технологической схемы устанавливается по следующим показателям: энерго-топливо и металлоемкость на единицу продукции; получение продукции более высокого качества; количеством технологических отходов и выбросов; степенью обеспечения безопасных условий труда; экологической чистотой производства и др.
Систематизация основных существующих технологических схем получения газобетонных блоков и их анализ дает возможность проанализировать достоинства и недостатки технологических линий и выявить оптимальные варианты.
Учитывая достоинства и недостатки рассмотренных выше технологических схем производства газобетонных блоков принимаем к разработке технологическую схему с мокрым помолом компонентов, которая приведена на рисунке 3.3.
На рисунке 3.3. показан один из вариантов производства газобетонных блоков.
Со склада сырья песок, гипс, цемент пневмотранспортом подается на дозировку. Известь дробится до кусков размером не более 20 мм и также подается на дозирование.
Известь и 20% песка направляются в шаровую мельницу на сухой помол; 30% песка измельчается в шаровой мельнице мокрым способом. Плотность песчаного шлама должна быть не менее 1,68 кг/л. песчаный шлам транспортируется в шламбассейны, расположенные над дозаторами смесительного отделения. В шламбассейне песчаный шлам в течении 4-5 часов выдерживается при непрерывном перемешивании, а затем насосами подается в расходные баки бетоносмесительного отделения.
Газобетонная смесь готовится следующим образом. Отдозированные компоненты смеси загружаются в вертикальный самоходный газобетоносмеситель емкостью 4 м3 при включенном перемешивающем механизме. Загрузка производится в такой последовательности: песчаный шлам и вода, перемешиваются 30 сек, а затем добавляется вяжущее и водная суспензия алюминевой пудры. Перемешивается еще две минуты, а затем газобетонная масса разливается в формы.
Алюминиевая пудра для обезжиривания обрабатывается раствором ПАВ (сульфанолом). Сульфанол применяется в данном случае не только для обезжиривания пудры, но и как пластифицирующая добавка.
Для интенсификации взаимодействия алюминиевой пудры с Са(ОН)2 вода подогревается до 40°С. Затем 3,5 часа идет выдержка отформованных изделий для того, чтобы произошло газовыделение и изделия набрали структурную прочность. После чего, срезается образовавшаяся горбушка. Шлам от горбушки вторично используется для приготовления формовочной массы.
Рисунок 3.3. Технологическая схема производства газобетонных блоков
Затем у формы откидываются борта и производится резка массива вдоль и поперек по вертикале. Борта формы закрываются и изделия кран-балкой отправляются на тепловлажностную обработку.
Тепловлажностная обработка изделий проводится в ямных пропарочных камерах в течении 13 часов по режиму приведенному на рисунке 3.4.
Рисунок 3.4. Режим ТВО
После ТВО формы поступают на распалубку. Производится разделение и отбраковка не качественных изделий, затем готовые блоки транспортируются на склад готовой продукции.
После распалубки формы очищаются, смазываются и подаются для дальнейшего формования изделий.
блок газобетон производство
4. ТЕХНОЛОГИЧЕСКИЕ РАСЧЕТЫ
.1 Режим работы предприятия
Готовой фонд рабочего времени технологического оборудования рассчитывается по формуле:
Тф=(Тн-Тр)*n*t*Ки
где Тф — годовой фонд рабочего времени, ч;
Тн — количество рабочих суток в год, Тн=365 сут.;
Тр — длительность плановых остановок в сутках на ремонт оборудования,
Тр=7;
n — количество рабочих смен, n=2;
t — продолжительность рабочей смены, t=8 час.;
Ки — коэффициент использования технологического оборудования, Ки=0,92.
Тф=(365-7)*2*8*0,92=5269,76 ч
.2 Расчет материального потока
Подбор состава газобетона осуществляется в следующей последовательности: устанавливается значение отношения кремнеземистого компонента к вяжущему в смеси «С», которое принимается в зависимости от вида вяжущего и способа твердения по таблице.
Таблица 4.1
Выбор показателя «С»
Вид вяжущегоСпособ твердениябезавтоклавныйАвтоклавныйЦементные и цементо-известковые0,75;1;1.250.75;1;1.5;1.75;2Известковые-3;3.5;4;4.5;5.5;6Известково-шлаковые0,6;0.8;10.6;0.8;1
В нашем производстве мы используем смешанное вяжущее (известь:цемент=75:25) и, учитывая автоклавный способ производства, принимаем С = 1,5.
Водотвердое отношение (В/Т), обеспечивающее заданную текучесть растворной смеси с учетом температуры смеси в момент выгрузки, определяется по таблице в зависимости от величины средней плотности ячеистого бетона (с) и вида вяжущего.
В/Т принимаем 0,5 (при литьевой технологии на смешанном вяжущем).
Определим пористость бетонной смеси, которая должна быть создана порообразователем для получения ячеистого бетона заданной с и В/Т:
Пр = 1 — с / Кс*(Vуд + В/Т)
где с — плотность бетона в высушенном состоянии, с = 0,7 т/м3;
Кс — коэффициент увеличения массы в результате твердения за счет химически связанной воды, Кс = 1,1;уд — удельный объем сухой смеси, определяемый опытным путём;
уд =0,34 (при использовании ПЦ)
Пр = 1 — 0,7 / 1,1*(0,34 + 0,5) = 0,33%.
Определим расходы материалов (на 1 м3)
Расход порообразователя:
Рп = (Пр*V) / (*К),
Рп = 1000*0,33 / 0,85*1390 = 0,28 кг
где — коэффициент использования порообразователя, = 0,85;- объем одновременно заливаемых изделий, увеличенный на 10%, л;
К — коэффициент выхода пор. Это отношение объема пор к массе порообразователя: К = Пр / Рп ; для расчетов принимают К = 1390 л/кг при использовании алюминиевой пудры.
На практике количество порообразователя увеличивают на 40% (Рп=0,392 кг).
Расход сухих компонентов:
Рсух = с*V / Кс
Рсух = 0,7*1000 / 1,1 = 636,36 кг.
Расход вяжущего вещества:
Рвяж = Рсух / (1 + С)
Рвяж = 636,36 / (1 + 1.5) = 254.54 кг.
Расход цемента:
Рц = Рвяж*n
Рц = 254,54*0,25 = 63,64 кг.
где n — доля цемента в смешанном вяжущем, n = 0,25;
Расход извести:
Ри = Рвяж*(1 — n)
Ри = 254,54*(1 — 0,25) = 190,905 кг.
Ри.ф. = (Ри / Аф)*100
Ри.ф. = (190,905/ 80)*100 = 238,63 кг.
где Ри — масса извести, содержащей 100% активного СаО, кг;
Ри.ф. — масса извести с фактическим содержанием СаО ;
Аф — активность, %.
Расход кремнеземистого компонента (песка):
Рк = Рсух — Рвяж;
Рк = 636,36 — 254,54 = 381,82 кг.
Расход воды:
Рв = Рсух*В/Т
Рв = 636,36*0,5 = 318,18 кг.
Расход стабилизатора (гипса) — 3% от массы цемента:
Рг = 63,64*0,03 = 1,91 кг
Расход материалов на 1 м3 представлен в таблице 4.2.
Таблица 4.2
Расход материалов на 1 м3 газобетона
Наименование материалаЕдиница измеренияРасход на 1 м3Цемент Известь Песок Гипс Алюминиевая пудра Сульфанол ВодаКг кг кг кг кг кг кг63,64 190,905 381,82 1,91 0,392 0,1 318,18
Для расчета материального производственного потока уточняем деление производственного процесса на технологические зоны и нормы неизбежных потерь материалов по зонам.
Производительность технологических переделов, м3/год:
Пn=Пn+1/(1-Qn/100)
где Пп — производительность в зоне n, м3/год;
Пп+1 — производительность в зоне, следующей за рассчитываемой (для зоны 6:
П6+1=Пзавод), м3/год;
Qп — производственные потери в зоне, %.
Потребность в материалах подсчитывается по формулам:
Р=(Пi*М)/(1-Qi/100)
где Р — фактическая потребность в материалах, кг;
Пi — производительность в данной зоне;
М — расход материала на 1 м3 газобетона, кг;
Qi — потери компонента в данной зоне, %.
Суточные (м3/сут) и часовые (м3/ч) производительности в зонах рассчитываются по формулам:
Псут=Пп/((Тн-Тр)*Ки)
Пч=Пп/Тф
где Тн — нормальное количество рабочих суток в году, Тн=365 сут;
Тр — длительность плановых остановок на ремонт, Тр=7 сут;
Тф — годовой фонд рабочего времени оборудования, Тф=5269,76 ч;
Ки — коэффициент использования технологического оборудования, Ки=0,92.
Результаты расчетов материалов на проектную производительность с учетом режима работы предприятия с технологическими потерями приведены в таблица 4.3.
Таблица 4.3
Материально-производственный поток
№ п/п№ зоныПеределПотери,%Ед.изм.Потребность в материалахГодсуткиЧас10Реализация стеновых блоков0м3 80000203,8915,1826Склад готовой продукции0,5м3 80402244,1615,2635Термообработка 0,5м3 80806245,3415,3344Формовочная линия цеха0,5м3 81212246,5815,4153Массозаготовительный узел1,0м382032249,0715,5762Подготовка сырья: Песок Известь Гипс 2,0 1,0 1,0 т т т 32612,91 15977,77 159,84 99,01 48,51 4,85 6,19 3,03 3,03-0271Склад сырья: Цемент Песок Известь Гипс Алюминевая пудра Сульфанол 1,0 2,0 1,0 1,0 0,5 0,1 т м3 т т т кг 5273,25 31960,66 15818 158,25 32,31 8211,41 25,86 97,03 48,03 4,8-01 9,80-02 24,93 1,00 6,05 3 3,0-02 6,13-03 1,56
5. Расчет технологического оборудования
.1 Расчёт оборудования
Для производства автоклавного газобетона используется немецкое оборудование фирмы HESS линии СBT.
Заводы по производству автоклавного газобетона фирмы Hess полностью автоматические и управляются при помощи компьютеров. За счет уникальной функции «обратное опрокидывание массива на раму для автоклавной обработки» удается избежать появления 5% отходов после автоклавной обработки.AAC выпускает заводы для производства газобетона разной производительности от 200 до 2000 м3 газобетонных изделий в сутки. Основные принципы всех линий — это резка вертикально стоящих массивов с последующим обратным кантованием на решётку и автоклавная обработка в горизонтальном положении.
Рисунок 5.1. Склад извести
Общая высота приямка H=1,4м
Вместимость склада извести определяется с учетом
Vприямка=61 м3;
Vи.п.=61×1,2=73,2 т
Vси = (3*6) / 0,9 = 20 т.
Количество приямков:
n = 20/73,2 = 0,27.
Принимаем 1 приямок для складирования извести на 6 суток размером
*4*1,5 м.
Принимаем 1 приямок для складирования извести на 6 суток с размером 9,5×4,6×1,4 м. Склад для извести имеет размеры 12×6 м.
Склад готовой продукции.
Площадь склада готовой продукции рассчитывается по формуле:
А=Qсут*Ткр*К1*К2 ,
где Qсут — объем изделий, поступающих на склад в сутки, м3;
Ткр — запас готовых изделий на складе, Ткр=12 сут;
К1 — коэффициент, учитывающий проходы между поддонами блоков,
К1=1,2;
К2 — коэффициент, учитывающий площадь для путей выкатных тележек, К2=1,3;
А=244,16*12*1,2*1,3=4570 м2.
6. Описание технологии производства
Линии типа СВТ производительностью от 200 до максимально 400 м³ газобетонных изделий в сутки разработаны и предусмотрены для покрытия потребностей небольших региональных рынков.
Массив имеет размер 3000 х 1500 х 600 мм и объем 2,7 м³. Формы, манипуляторы, столы и другие модули соответствуют размерам массива, а также оборудование дозаторно-смесительного отделения соответствует уменьшенным объемам.
Рис. 6.1 Форма под смесителем Рис. 6.2 Заливка в форму
Кантующий манипулятор выполняет операции: устанавливает формы на места созревания, забирает с них и кантует форму с массивом на линию резки. Особая конструкция форм позволяет поставить их друг на друга в зоне созревания, тем самым, увеличивая мощность завода, без изменений в конструкционном решении данной секции.
Рис. 6.3. Кантующий манипулятор
Станции проходной линии резки включают в себя предварительную резку и профилирование, горизонтальную и поперечную резку. Резка производится аналогично пневматически натянутыми проволочными струнами.
После резки многофункциональный манипулятор поднимает форму и переставляет ее к столу кантования, на котором массив кантуется на решетку в горизонтальном положении. Освобожденный от массива, борт-платформа возвращается после чистки к кантующему манипулятору и там присоединяется к свободной форме.
Массив на решетке переставляется тем же манипулятором на разделительное устройство, где происходит разделение зелёного массива по уже описанной технологии. Отсюда уже манипулятор переносит массивы на решетках в зону накопления и ставит на тележку. На одну тележку устанавливаются четыре решётки с массивами, две друг за другом и по одной на каждую решетку сверху.
Загрузка и разгрузка автоклавов происходит посредством приводов накопительных путей и поперечного траверсного транспортёра, находящегося перед автоклавами.
Сами автоклавы имеют диаметр 2,30 м и длину 32 м. В них входит 20 массивов, уложенных в два уровня, общим объемом 54 м³ продукта.
Рис. 6.5. Автоклавы
После разгрузки автоклавов и накопления тележек на накопительных путях многофункциональный манипулятор снова собирает массивы с решетками с тележек и переставляет их на разгрузочно-упаковочную линию.
Рис. 6.6 Разгрузочный манипулятор
7. Техника безопасности
Строгое соблюдение правил техники безопасности должно соблюдаться при работе на основных технологических переделах.
Помещение для приготовления газобетонной смеси должно иметь вытяжную вентиляцию. Все оборудование по транспортированию извести, песка, гипса необходимо укрывать кожухами и оборудовать также вытяжной вентиляцией. При установке сит, мельниц и силосов для перемешивания необходимо принимать меры по снижению интенсивности шума и вибрации оборудования и пола. Температура наружной поверхности мельниц не должна превышать 350С. Дозировку песка, извести, гипса, цемента необходимо автоматизировать, а узлы и соединения механизмов тщательно герметизировать. Операции по помолу, смешиванию, выгрузки и загрузки алюминиевой пудры должны быть механизированы и по возможности автоматизированы, с применением устройств, препятствующих запылению рабочей зоны помещения и прямому контакту тела рабочего с указанными веществами и соединениями. Не допускается прокаливание алюминиевой пудры в электропечах для снятия пленки парафита. В помещении, где производятся работы с алюминиевой пудрой, запрещается курить, вести сварочные работы, применять электрические искрообразующие аппараты.
Операции закрывания боковых сторон формы, заливки ячеистой массы в формы, а также срезку «горбушки» должны быть полностью механизированы. Очистка, смазка форм — перед заливкой ячеистой смеси. Выгрузка изделий также должна быть механизирована.
Концентрация пыли в помещениях нормируется в зависимости от содержания свободного кремнезема в воздухе рабочей зоны, особенно должно уделяться внимание помещениям, где во взвешенном состоянии находятся цемент, известь и др. на складах цемента и в бетоносмесительных цехах для пылеосаждения используют пылеосадители и матерчатые фильтры, которые обеспечивают очистку воздуха до 97-99%.
В качестве индивидуальной защиты в помещениях с большой концентрацией пыли необходимо пользоваться респираторами Ф-45 или ПРБ-1, герметичными защитными очками и спецодеждой.
Формование изделий осуществлять при включенной сигнализации, управление формовочными машинами должно быть дистанционным. При тепловой обработке изделий следует не допускать утечки пара из камер, загружать и выгружать камеры с помощью автоматических траверс.
При проектировании, реконструкции или перепрофилировании предприятий промышленности строительных материалов для решения охраны окружающей среды должны решаться следующие основные задачи: рециркуляция технологической воды и воздуха без очистки или после очистки для производственных целей; сокращение выхода отходов от собственного производства и их переработка; использование в технологии отходов других производств. После соответствующей обработки отходы могут быть использованы как вторичное сырье или как вторичные носители энергии. Если по техническим или технологическим причинам это невозможно или экономически невыгодно, то их необходимо выводить в атмосферу таким образом, чтобы не наносить вреда окружающей среде.
ЛИТЕРАТУРА
1.Елфимов А.И. Концепция развития производства и рынков стеновых материалов в рамках средне срочной програмы социального и экономического развития Российской Федерации / А.И. Елфимов // Строительные материалы. — 1998. — №6. -С.2-3.
2.Хихлуха Л.В. Ресурсосбережение при строительстве и реконструкции жилья / Л.В. Хихлуха // Строительные материалы. — 1995. — №5. — С.2-3.
.Семченков А.С. Энергосберегающие ограждающие конструкции зданий / А.С. Семченков // Бетон и железобетон. — 1996. — №2. — С.6-9.
.Муромский К.П. Ячеистый бетон в наружных стенах здания / К.П. Муромский // Бетон и железобетон. — 1996. — №5. — С.30-31.
.Соловей Ж.Б. Исследование теплофизических качеств ограждающих стен из ячеистого бетона домов в Ленинграде. / Ж.Б. Соловей, Э.О. Кесли // В сб.: Применение ячеистых бетонов в жилищно-гражданском строительстве. — Л.: — 1991.
.Фоменко О.С. Производство и применение ячеистобетонных изделий в условиях рыночной экономики / О.С. Фоменко// Строительные материалы. -1993. -№8. -С.2-3.
.Ахманицкий Г.Я. Пути совершенствования технологии и оборудования для производства изделий из неавтоклавного ячеистого бетона / Г.Я. Ахманицкий и др.// Бетон и железобетон. -1997. — №2. — С.9-12.
.Удачкин И.Б. Повышение качества ячеистых изделий путем использования комплексного газообразователя / И.Б. Удачкин и др. // Строительные материалы. -1983. — №6. — С.11-12.
.Баженов Ю.М. Технология бетонных и железобетонных изделий. / Ю.М. Баженов, А.Г. Комар // — М.: Стройиздат. — 1984. — 672с.
.Завадский В.Ф. Производство стеновых материалов и изделий / В.Ф. Завадский, А.Ф. Косач // Учебное пособие. — Новосибирск. НГАСУ. — 2000. — 168с.
.Завадский В.Ф. Технология изделий стеновой и кровельной керамики /В.Ф. Завадский и др.// Методическое пособие. — Новосибирск. НГАСУ. — 1998. — 80с.
.Баженов Ю.М. Технология бетона. / Ю.М. Баженов //- М.: Высшая школа. — 1987. — 415с.
.Попов Л.Н. Технология железобетонных изделий в примерах и задачах. / Л.Н. Попов // — М.: — 1987.
.Бауман В.А. Механическое оборудование предприятий строительных материалов изделий и конструкций. / В.А. Бауман и др. // — М.: Машиностроение. — 1981. — 324с.
.Горобец М.И Строительные машины / Под ред. М.И. Горобца. Том 2. Оборудование для производства строительных материалов и изделий. — М.: Машиностроение. — 1991. — 496с.
.Силенок С.Г. Механическое оборудование предприятий строительных материалов, изделий и конструкций/ Под ред. С.Г. Силенка. — М.: — 1990. — 390с.
.Тимофеев А.И. Проектирование предприятий сборного железобетона для районов Сибири и Крайнего Севера. / А.И. Тимофеев, В.А. Безбородов, В.В. Коледин // — Новосибирск: НИСИ. — 1991. — 23с.
.Кудяков А.М. Основы технологического проектирования заводов сборного железобетона./ А.М. Кудяков // — Томск: — 1986.
.Журавлев В.П. Охрана окружающей среды в строительстве. / В.П Журавлев. и др. //- М.: издательство АСВ. — 1995. — 328с.
.Шевцов К.К. Охрана окружающей природной среды в строительстве. / К.К. Шевцов // — М.: Высшая школа. — 1994. — 240с.
.Ливчак И.Ф. Охрана окружающей среды. / И.Ф. Ливчак, Ю.В. Воронов // — М.: Стройиздат. — 1988. — 191с.
.Пальгунов П.П. Утилизация промышленных отходов. / П.П. Пальгунов, М.В. Сумароков // — М.: Стройиздат. — 1990. — 352с.
Теги: Производство газобетона Курсовая работа (теория) Строительство
Просмотров: 49033
Найти в Wikkipedia статьи с фразой: Производство газобетона
diplomba.ru