3D принтер печать металлом – 3D-печать металлами
3D-печать металлами — технологии и принтеры / Top 3D Shop corporate blog / Habr
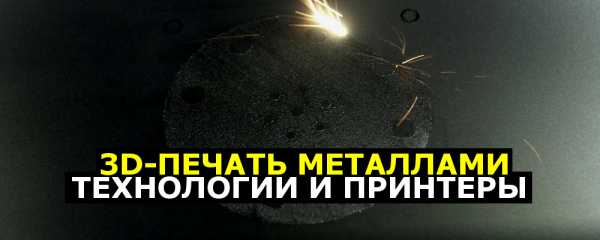
3D-печать металлом становится все более популярной. И это не удивляет: каждый металлический материал для печати предлагает уникальное сочетание практических и эстетических свойств для того, чтобы удовлетворить требования предъявляемые к различным продуктам, будь то прототипы, миниатюры, украшения, функциональные детали или даже кухонные принадлежности.
Причины печатать металлами настолько веские, что 3D-печать металлами уже внедряется в серийное производство. На самом деле, некоторые 3D-печатные детали уже догнали, а какие-то и превзошли своими свойствами те, что производятся традиционными методами.
Традиционное производство из металлов и пластиков очень расточительно — в авиапромышленности, например, до 90% материалов уходит в отходы. Выход продукции, в некоторых отраслях, составляет не более 30% от использованного материала.
3D-печать металлами потребляет меньше энергии и сокращает количество отходов до минимума. Кроме того, готовое 3D-печатное изделие может быть до 60% легче, по сравнению с фрезерованной или литой деталью. Одна лишь авиационная промышленность сэкономит миллиарды долларов на топливе — за счет снижения веса конструкций. А ведь прочность и легкость нужны и в других отраслях. Да и экономичность тоже.
3D-печать металлом дома
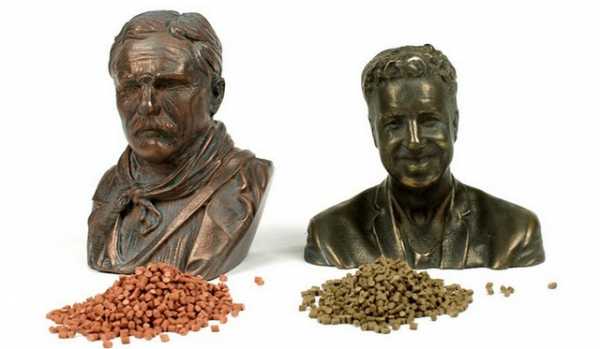
Что можно сделать, если появилось желание попробовать 3D-печать металлом в домашних условиях? Для печати металлом необходимы чрезвычайно высокие температуры, вряд ли вы сможете использовать обычный FDM 3D-принтер для этого, по крайней мере пока. Ситуация может измениться через несколько лет, но сейчас домашней 3D-технике это недоступно.
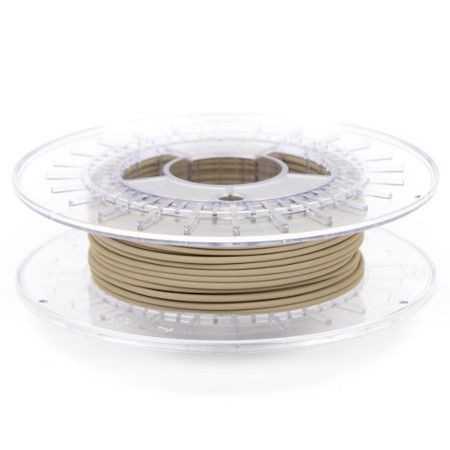
Такого например, как Colorfabb Bronzefill или Bestfilament Bronze.
Эти филаменты содержат значительный процент металлических порошков, но и достаточно пластика — для печати при низкой температуре любым 3D-принтером. В то же время, они содержат достаточное количество металла, чтобы соответственно выглядеть, ощущаться и иметь вес близкий к весу металлического предмета.
Изделия из филамента содержащего железо даже покрываются ржавчиной в определенных условиях, что добавляет правдоподобности, а вот проржаветь насквозь и испортиться от этого не смогут — и в этом их преимущество перед настоящими металлическими предметами.
Плюсы таких материалов:
- Уникальный внешний вид распечаток
- Идеально подходит для бижутерии, статуэток, предметов домашнего обихода и декора
- Высокая прочность
- Очень малая усадка во время охлаждения
- Подогреваемый стол не обязателен
Минусы:
- Низкая гибкость изделий, зависит от конструкции распечатки
- Не считается безопасным при контакте с пищей
- Требует тонкой настройки температуры сопла и скорости подачи филамента
- Необходима постобработка изделий — шлифовка, полировка
- Быстрый износ сопла экструдера — филамент с металлом очень абразивен, по сравнению с обычными материалами
Общий температурный диапазон печати обычно составляет 195°C — 220°C.
3D-печать металлом в промышленности
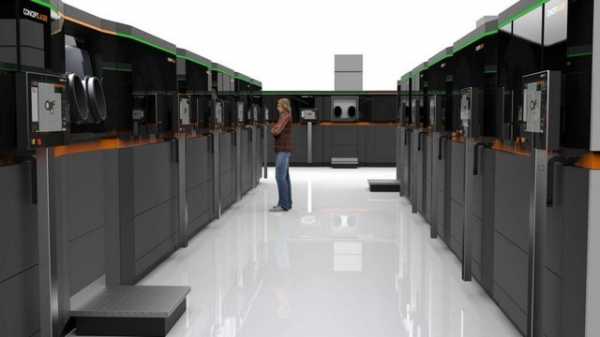
Если вы хотите приобрести 3D-принтер печатающий настоящим металлом, для использования на предприятии, то тут для вас две новости — хорошая и плохая.
Хорошая новость состоит в том, что их ассортимент достаточно широк и продолжает расширяться — можно будет выбрать такой аппарат, который соответствует любым техническим требованиям. Далее в статье можно убедиться в этом.
Плохая же новость одна — цены. Стоимость профессиональных печатающих металлом принтеров начинается где-то от $200000 и растет до бесконечности. Кроме того, даже если вы выберете и приобретете самый недорогой из них, отдельным ударом станет покупка расходников, плановое обслуживание с заменой узлов, ремонт. Не забываем и о персонале, и расходах на постобработку изделий. А на стадии подготовки к печати понадобится специальное ПО и умеющие обращаться с ним люди.
Если вы готовы ко всем этим тратам и трудностям — читайте дальше, мы представим несколько очень интересных образцов.
https://youtu.be/20R9nItDmPY
3D-печать металлом — применение
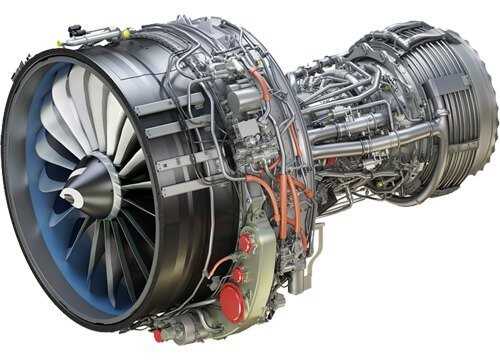
В некоторых промышленных секторах уже используют металлические 3D-принтеры, они стали неотъемлемой частью производственного процесса, о чем обычный потребитель может и не подозревать:
Наиболее распространенным примером являются медицинские импланты и стоматологические коронки, мосты, протезы, которые уже считаются наиболее оптимальным вариантом для пациентов. Причина: Они могут быть быстрее и дешевле изготовлены на 3D-принтере и адаптированы к индивидуальным потребностям каждого пациента.
Второй, столь же часто встречающийся пример: ювелирное дело. Большинство крупных производителей постепенно переходит от 3D-печати форм и восковок к непосредственной 3D-печати металлом, а печать из титана позволяет ювелирам создавать изделия невозможного ранее дизайна.
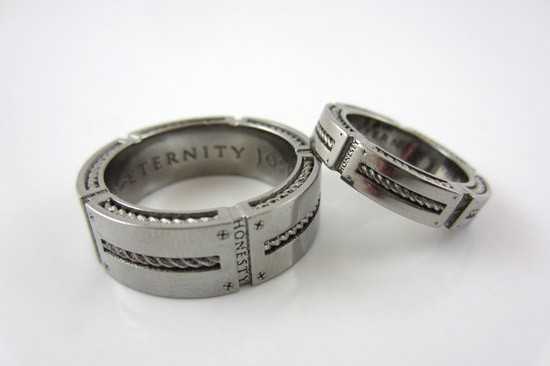
Кроме того, аэрокосмическая промышленность становится все более и более зависима от 3D-печатных металлических изделий. Ge-AvioAero в Италии — первая в мире полностью 3D-печатная фабрика, которая выпускает компоненты для реактивных двигателей LEAP.
Следующая отрасль использующая 3D-принтеры по металлу — автопром. BMW, Audi, FCA уже серьезно рассматривают применение технологии в серийном производстве, а не только в прототипировании, где они используют 3D-печать уже многие годы.
Казалось бы — зачем изобретать велосипед? Но и здесь 3D-печать металлом нашла применение. Уже несколько лет производители велосипедных компонентов и рам применяют 3D печать. Не только в мире, но и в России это получило распространение. Производитель эксклюзивных велосипедов Triton заканчивает проект с 3D-печатным элементом титановой рамы, это позволило снизить ее вес без ущерба прочности.
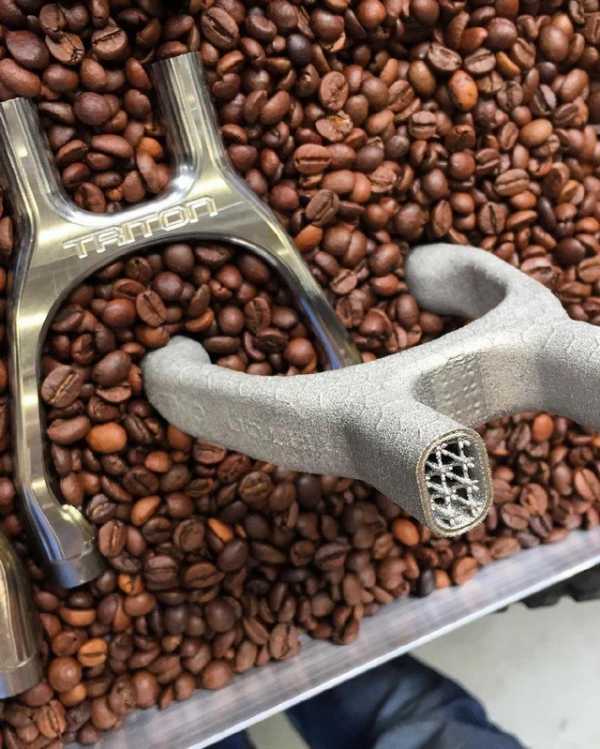
Но прежде, чем 3D-печать металлами действительно захватит мир, необходимо будет преодолеть несколько серьезных проблем. В первую очередь — это высокая стоимость и низкая скорость производства больших серий этим методом.
3D-печать металлом — технологии
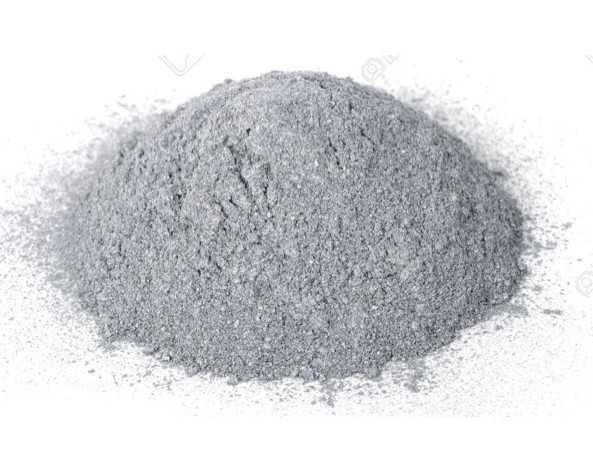
Многое можно сказать о применении печатающих металлом 3D-принтеров. Есть своя специфика, но основные вопросы такие же, как и с любыми другими 3D-принтерами: программное обеспечение и аппаратные ограничения, оптимизация материалов и печать несколькими материалами. Мы не будем говорить о программном обеспечении много, упомянем лишь, что наиболее крупные издатели, такие как Autodesk, SolidWorks и SolidThinking — все разрабатывают программные продукты для использования в объемной печати металлами, чтобы пользователи могли воплотить в жизнь изделие любой вообразимой формы.
Посмотрим же на имеющиеся металлические технологии 3D-печати:
Процесс # 1: Послойное сплавление порошка
Процесс 3D-печати металлами, которым наиболее крупные компании пользуются в наши дни, известен как сплавление или спекание порошкового слоя. Это означает, что лазерный или другой высокоэнергетический луч сплавляет в единое целое частицы равномерно распределенного металлического порошка, создавая слои изделия, один за другим.
В мире есть восемь основных производителей 3D-принтеров для печати металлом, большинство из них расположены в Германии. Их технологии идут под аббревиатурой SLM (выборочное лазерное плавление) или DMLS (прямое спекание металла лазером).
Процесс # 2: Binder Jetting
Еще один профессиональный метод с послойным соединением — склеивание частиц металла для последующего обжига в высокотемпературной печи, где частицы сплавляются под давлением, составляя единое металлическое целое. Печатная головка наносит соединительный раствор на порошковую подложку послойно, как обычный принтер на листы бумаги, после чего изделие отправляется в обжиг.
Еще одна похожая, но отличающаяся технология, в основе которой лежит FDM печать — замешивание металлического порошка в металлическую пасту. С помощью пневматической экструзии, 3D-принтер выдавливает ее, подобно тому, как строительный 3D-принтер делает это с цементом, чтобы сформировать 3D-объекты. После того, как нужная форма напечатана, объекты также спекают в печи. Эту технологию использует Mini Metal Maker — возможно, единственный более-менее доступный 3D-принтер для печати металлом ($1600). Прибавьте стоимость небольшой печки для обжига.
Процесс # 3: Наплавление
Можно подумать, что среди технологий печатью металлом отсутствует похожая на обычную FDM, однако, это не совсем так. Вы не сможете плавить металлическую нить в хот-энде своего 3D-принтера, а вот крупные производители владеют такой технологией и пользуются ею. Есть два основных способа печатать цельнометаллическим материалом.
Обычно это делается внутри закрытой камеры, однако, на примере компании MX3D, мы видим возможность реализации подобной технологии в сооружении настоящего полноразмерного моста, который должен быть распечатан в 2017 году в Амстердаме.
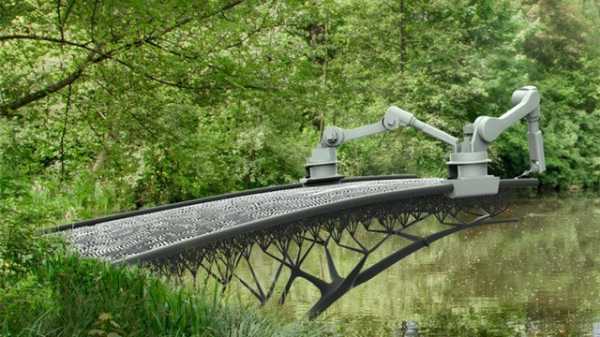
Другой называется EBM (Electron Beam Manufacturing — производство электронным лучом), это технология формирования слоев из металлического сырья под воздействием мощного электронного луча, с ее помощью создают крупные и очень крупные конструкции. Если вы не работаете в оборонном комплексе РФ или США, то вряд ли увидите эту технологию живьем.
Еще парочка новых, едва появившихся технологий, используемых пока только их создателями, представлена ниже — в разделе о принтерах.
Используемые металлы
Ti — Титан
Чистый титан (Ti64 или TiAl4V) является одним из наиболее часто используемых металлов для 3D-печати, и безусловно — одним из самых универсальных, так как он является одновременно прочным и легким. Он используется как в медицинской промышленности (в персонализированом протезировании), так и в аэрокосмической и автомобильной отрасли (для изготовления деталей и прототипов), и в других областях. Единственная загвоздка — он обладает высокой реакционной способностью, что означает — он может легко взорваться, когда находится в форме порошка, и обязательно должен применяться для печати лишь в среде инертного газа Аргона.
SS — Нержавеющая сталь
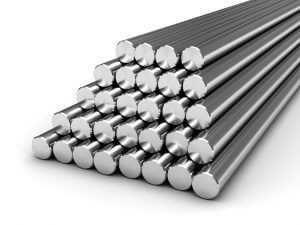
Нержавеющая сталь является одним из самых доступных металлов для 3D-печати. В то же время, она очень прочна и может быть использована в широком спектре промышленных и художественных производств. Этот тип стального сплава, содержащий кобальт и никель, обладает высокой упругостью и прочностью на разрыв. 3D-печать нержавейкой используется, в основном, лишь в тяжелой промышленности.
Inconel — Инконель
Инконель — современный суперсплав. Он производится компанией Special Metals Corporation и является запатентованным товарным знаком. Состоит, по большей части, из никеля и хрома, имеет высокую жаропрочность. Используется в нефтяной, химической и аэрокосмической промышленности (например: для создания распределительных форсунок, бортовых “черных ящиков”).
Al — Алюминий
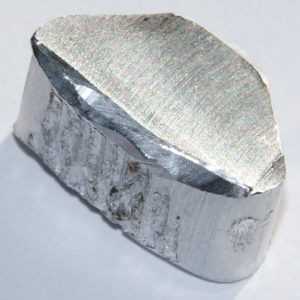
Из-за присущей ему легкости и универсальности, алюминий является очень популярным металлом для применения в 3D-печати. Он используется обычно в виде различных сплавов, составляя их основу. Порошок алюминия взрывоопасен и применяется в печати в среде инертного газа Аргона.
CoCr — Кобальт-хром
Этот металлический сплав имеет очень высокую удельную прочность. Используется как в стоматологии — для 3D-печати зубных коронок, мостов и бюгельных протезов, так и в других областях.
Cu — Медь
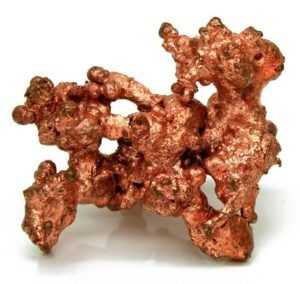
За редким исключением, медь и ее сплавы — бронза, латунь — используются для литья с использованием выжигаемых моделей, а не для прямой печати металлом. Это потому, что их свойства далеко не идеальны для применения в промышленной 3D-печати, они чаще используются в декоративно-прикладном искусстве. С большим успехом они добавляются в пластиковый филамент — для 3D-печати на обычных 3D-принтерах.
Fe — Железо
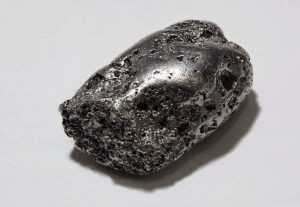
Железо и магнитный железняк также, в основном, используются в качестве добавки к PLA-филаменту. В крупной промышленности чистое железо редко находит применение, а о стали мы написали выше.
Au, Ag — Золото, серебро и другие драгоценные металлы
Большинство сплавляющих слои порошка 3D-принтеров могут работать с драгоценными металлами, такими как золото, серебро и платина. Главная задача при работе с ними — убедиться в оптимальном расходе дорогостоящего материала. Драгоценные металлы применяются в 3D-печати ювелирных и медицинских изделий, а также при производстве электроники.
3D принтеры печатающие металлом
# 1: Sciaky EBAM 300 — титановый прут
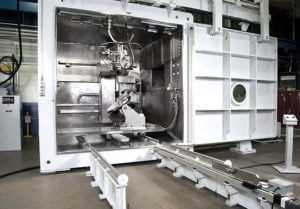
Для печати действительно больших металлических конструкций лучшим выбором будет EBAM от Sciaky. Этот аппарат может быть любого размера, на заказ. Он используется, в основном, в аэрокосмической и оборонной промышленности США.
Как серийную модель, Sciaky продает EBAM 300. Он имеет размер рабочей области со сторонами 5791 х 1219 х 1219 мм.
Компания утверждает, что EBAM 300 является одним из самых быстрых коммерчески доступных промышленных 3D-принтеров. Конструкционные элементы самолетов, производство которых, по традиционным технологиям, могло занимать до полугода, теперь печатаются в течение 48 часов.
Уникальная технология Sciaky использует электронно-лучевую пушку высокой мощности для плавки титанового филамента толщиной 3мм, со стандартной скоростью осаждения около 3-9 кг/час.
# 2: Fabrisonic UAM — ультразвуковой
Другой способ 3D-печати больших металлических деталей — Ultrasound Additive Manufacturing Technology (UAM — технология ультразвукового аддитивного производства) от Fabrisonic. Детище Fabrisonic является трехосевым ЧПУ-станком, имеющим дополнительную сварочную головку. Металлические слои сначала разрезают, а затем сваривают друг с другом с помощью ультразвука. Крупнейший 3D-принтер Fabrisonic — “7200”, имеет объем сборки 2 х 2 х 1,5 м.
# 3: Laser XLine 1000 — металлический порошок
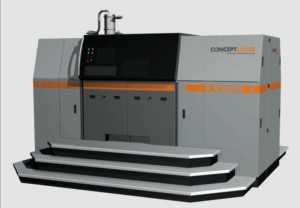
Одним из самых крупных, на рынке 3D-принтеров печатающих с помощью металлического порошка, долго являлся XLine 1000 производства Concept Laser. Он имеет область сборки размером 630 х 400 х 500 мм, а места занимает как небольшой дом.
Изготовившая его немецкая компания, которая является одним из поставщиков 3D-принтеров для аэрокосмических компаний-гигантов, таких как Airbus, недавно представила новый принтер — XLine 2000.
2000 имеет два лазера и еще больший объем сборки — 800 х 400 х 500 мм. Эта машина, которая использует патентованную технологию LaserCUSING (тип селективного лазерного плавления), может создавать объекты из сплавов стали, алюминия, никеля, титана, драгоценных металлов и из некоторых чистых материалов (титана и сортовых сталей.)
Подобные машины есть у всех основных игроков на рынке 3D-печати металлом: у EOS, SLM, Renishaw, Realizer и 3D Systems, а также у Shining 3D — стремительно развивающейся компании из Китая.
# 4: M Line Factory — модульная 3D-фабрика
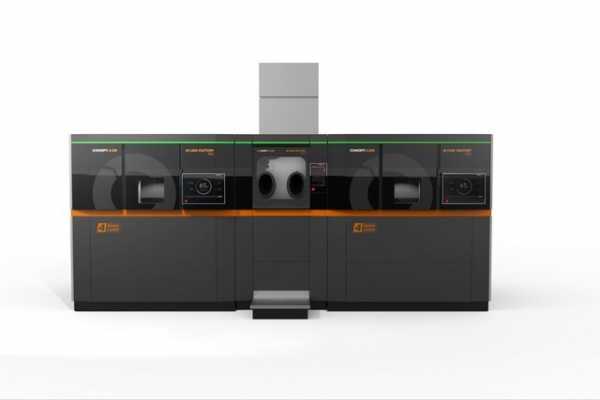
Рабочий объем: 398,78 х 398,78 х 424,18 мм
От 1 до 4 лазеров, 400 — 1000 Вт мощности каждый.
Концепция M Line Factory основана на принципах автоматизации и взаимодействия.
M Line Factory, от той же Concept Laser, и работающий по той же технологии, делает акцент не на размере рабочей области, а на удобстве производства — он представляет собой аппарат модульной архитектуры, который разделяет производство на отдельные процессы таким образом, что эти процессы могут происходить одновременно, а не последовательно.
Эта новая архитектура состоит из 2 независимых узлов машины:
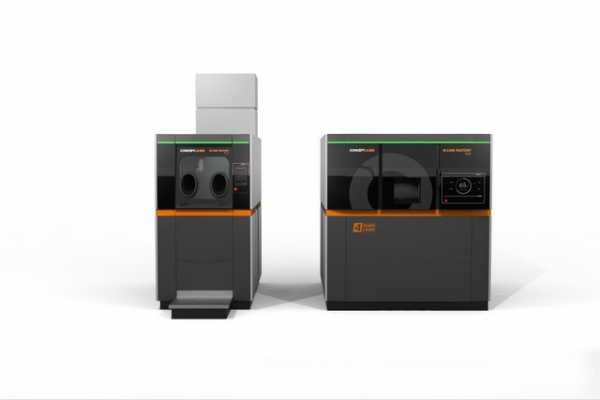
M Line Factory PRD (Production Unit — производственная единица)
Production Unit состоит из 3-х типов модулей: модуль дозирования, печатный модуль и модуль переполнения (лоток для готовой продукции). Все они могут быть индивидуально активированы и не образуют одну непрерывную единицу аппаратуры. Эти модули транспортируются через систему туннелей внутри машины. Например, когда новый порошок подается, пустой модуль хранения порошка может быть автоматически заменен на новый, без прерывания процесса печати. Готовые детали могут быть перемещены за пределы машины и немедленно автоматически заменяются следующими заданиями.
M Line Factory PCG (Processing Unit — процессинговая единица)
Это независимый блок обработки данных, который имеет встроенную станцию просеивания и подготовки порошка. Распаковка, подготовка к следующему заданию печати и просеивание происходят в замкнутой системе, без участия оператора.
# 5: ORLAS CREATOR — 3D-принтер готовый к работе
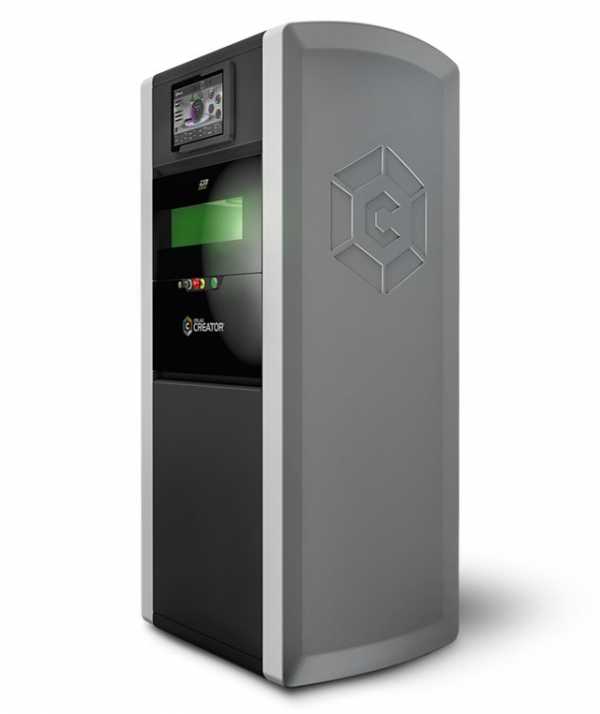
Создатели ORLAS CREATOR позиционируют этот 3D-принтер как максимально доступный, простой в обращении и готовый к работе, не требующий установки никаких дополнительных комплектующих и программ сторонних производителей, способный печатать прямо из файла комплектной CAD/CAM их собственной разработки.
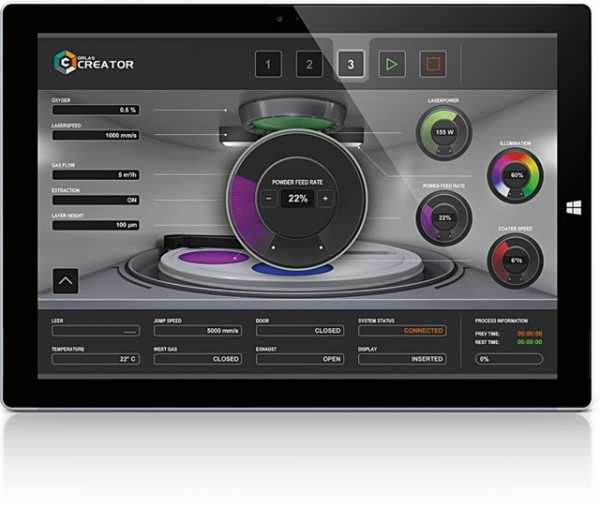
Все необходимые компоненты установлены в относительно компактном корпусе, которому необходимо пространство 90х90х200 см. Много места он не займет, хоть и выглядит внушительно, да и весит 350 кг.
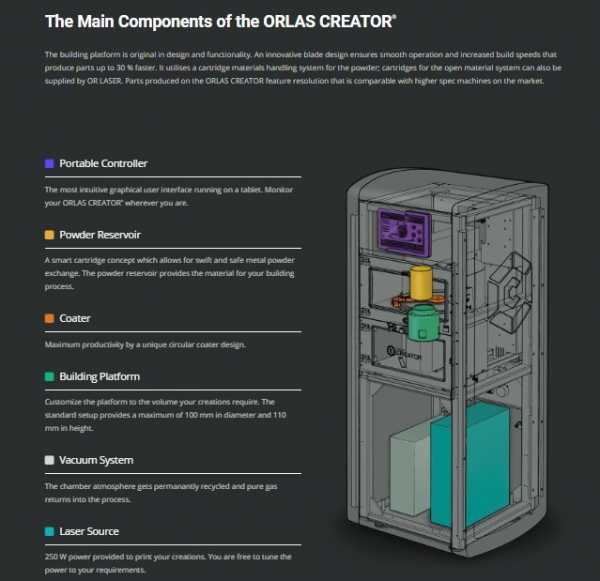
Как можно понять из приведенной производителем таблицы, металлический порошок спекается вращающейся лазерной системой, слоями 20-100 мкм толщиной и с размером “пикселя” всего в 40 мкм, в атмосфере азота или аргона. Подключить его можно к обычной бытовой электросети, если ваша проводка выдержит нагрузку в 10 ампер. Что, впрочем, не превышает требований средней стиральной машины.
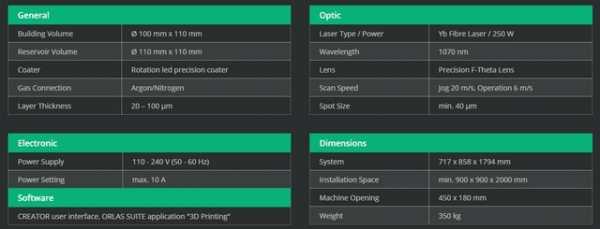
Мощность лазера — 250 Ватт. Рабочая область составляет цилиндр 100 мм в диаметре и 110 в высоту.
# 6: FormUp 350 — Powder Machine Part Method (PMPM)
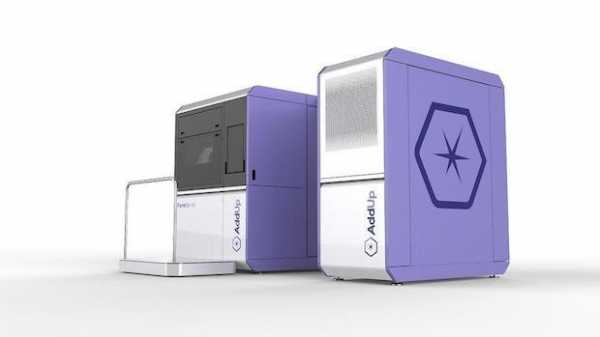
FormUp 350, работающий в системе Powder Machine Part Method (PMPM), создан компанией AddUp — совместным проектом Fives и Michelin. Это новейший аппарат для 3D-печати металлами, впервые представленный в ноябре на Formnext2016.
Принцип работы у этого 3D-принтера тот же, что и у приведенных выше коллег, но его главная особенность в другом — она заключается в его включенности в PMPM.
Принтер предназначен именно для промышленного использования, в режиме 24/7, и рассчитан именно на такой темп работы. Система PMPM включает в себя контроль качества всех комплектующих и материалов, на всех стадиях их производства и распространения, что должно гарантировать стабильно высокие показатели качества работы, в чем у Мишлена огромный многолетний опыт.
# 7: XJET — NanoParticle Jetting — струйная печать металлом
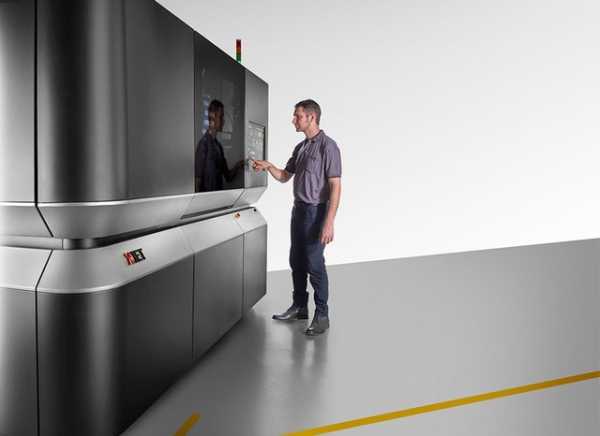
Технология впрыска наночастиц предполагает использование специальных герметичных катриджей с раствором, в котором находится взвесь наночастиц металла.
Наночастицы осаждаются и образуют собой материал печатаемого изделия.
Учитывая заявленные особенности технологии (применение металлических частиц наноразмера), несложно поверить создателям аппарата, когда они утверждают о его беспрецедентных точности и разрешении печати.
# 8: VADER Mk1 — MagnetoJet — струйная печать металлом
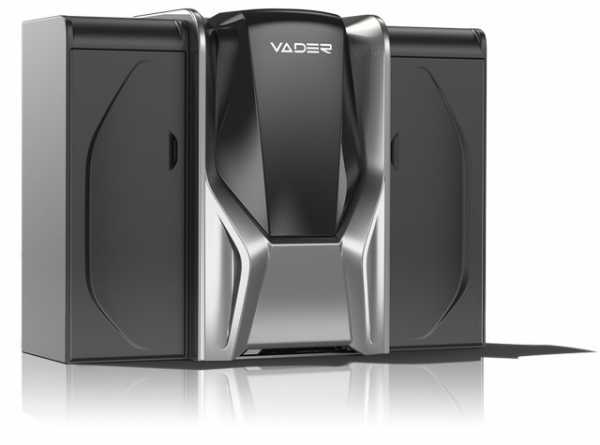
Технология Зака Вейдера MagnetoJet основана на изучении магнитной гидродинамики, а конкретнее — возможности управлять расплавленным металлом с помощью магнитных полей. Суть разработки в том, что из расплавленного алюминия формируется капля строго контролируемого размера, этими каплями и осуществляется печать.
Размер такой капельки — от 200 до 500 микрон, печать происходит со скоростью 1000 капель в секунду. Рабочая область принтера: 300 мм х 300 мм х 300 мм
Рабочий материал: Алюминий и его сплавы (4043, 6061, 7075). И, пусть пока это только алюминий, но принтер в 2 раза быстрее порошковых и до 10 раз дешевле.
В 2018 году планируется выпуск Mk2, он будет оснащен 10 печатающими головками, что должно дать прирост скорости печати в 30 раз.
# 9: METAL X — ADAM — атомная диффузия
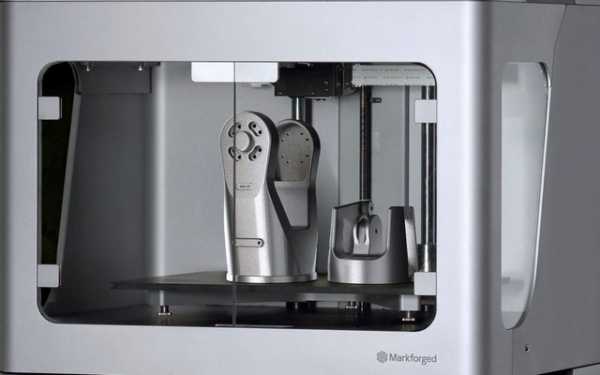
Компания Markforged представила новую технологию 3D-печати металлом — ADAM, и 3D-принтер работающий по этой технологии — Metal X.
ADAM (Atomic Diffusion Additive Manufacturing) — технология атомной диффузии. Печать производится металлическим порошком, где частицы металла покрыты синтетическим связующим веществом, которое удаляется после печати, позволяя металлу соединиться в единое целое.
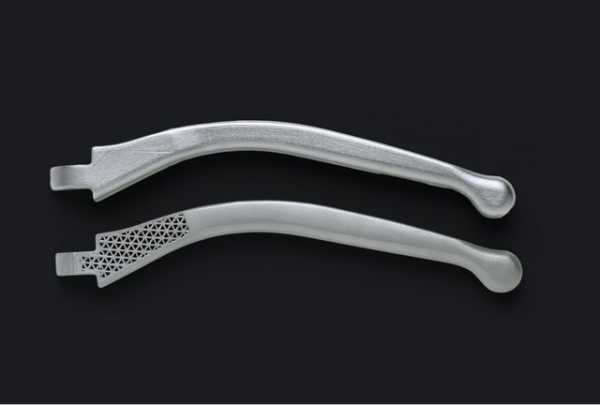
Главное преимущество технологии — отсутствие необходимости применения сверхвысоких температур непосредственно в процессе печати, а значит — отсутствие ограничений по тугоплавкости используемых для печати материалов. Теоретически, принтер может создавать 3D-модели из сверхпрочных инструментальных сталей — сейчас он уже печатает нержавейкой, а в разработке титан, Инконель и стали D2 и A2.
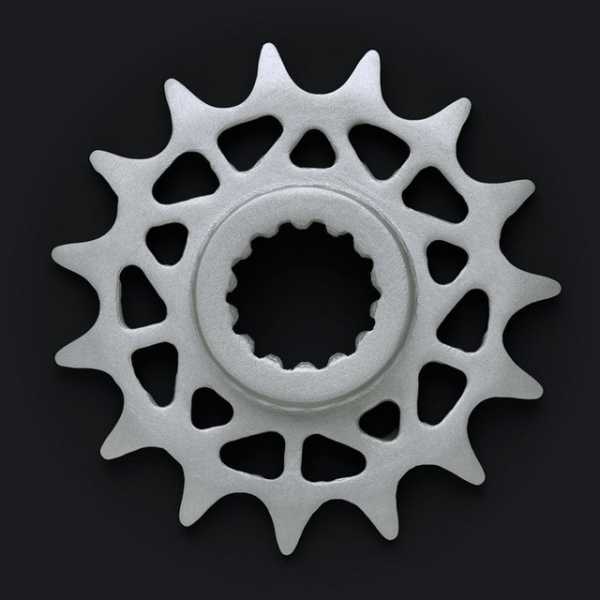
Технология позволяет создавать детали со сложной внутренней структурой, такой как в пчелиных сотах или в пористых тканях костей, что затруднительно при других технологиях 3D-печати, даже для DMLS.
Размер изделий: до 250мм х 220мм х 200мм. Высота слоя — 50 микрон.
Того гляди, скоро можно будет распечатать высококачественный нож — с нуля, за пару часов, придав ему любой самый замысловатый дизайн.
Хотите больше интересных новостей из мира 3D-технологий?
Подписывайтесь на нас в соц. сетях:
habr.com
Точная 3D печать металлом на заказ в Sprint 3D
3D печать металлом – аддитивное производство металлических изделий, которое по праву является одним из наиболее перспективных и стремительно развивающихся направлений в трехмерной печати как таковой. Сама технология берет свое начало еще с обычного спекания материалов, применяемого в порошковой металлургии. Но сейчас она стала более совершенной, точной и быстрой. И сегодня компания SPRINT3D предлагает вам печать металлом на 3D принтере на действительно выгодных условиях. Но для начала – немного информации о самом производственном процессе и его возможностях.
Технология селективного лазерного сплавления
SLM или технология селективного сплавления – это тип прямой печати металлом, при котором достигается плотность 99,5%. Разница особенно ощутима, если сравнивать с моделями, полученными обычным литьем. Достигается такой показатель благодаря внедрению новейших технологий именно в аппаратной части:
- Применение специальных роликов для утрамбовки порошков и, как следствие, возможность использования порошков с размером частиц от 5 мкм.
- Повышение насыпной плотности, способствующее уплотнению конечных изделий.
- Создание разреженной атмосферы инертных газов, при которой достигается максимальная чистота материала, отсутствует окисление и исключаются риски попадания сторонних химических соединений в состав.
Но самое главное – современный 3D принтер для печати металлом позволяет легко подобрать индивидуальную конфигурацию для печати конкретным металлическим порошком. Таким образом даже с недорогим материалом можно получить первоклассный результат. Но только при условии использовании качественного современного оборудования. И здесь мы тоже готовы вас удивить!
3D-печать металлом В SPRINT 3D
Установки для 3D печати металлом, которые мы используем
Качество производства – ключевое требование, которое мы ставим перед собой. Поэтому в работе используем только профессиональное оборудование, обладающие широкими возможностями для печати металлом. Рассмотрим подробнее каждую из производственных установок.
Производственная установка SLM 280HL
SLM 280HL – разработка германской компании SLM Solutions GmbH, использующая технологию послойного лазерного плавления порошковых металлических материалов. Установка оснащена большой рабочей камерой и позволяет создавать 3D объекты размерами 280х280х350 мм. Среди главных преимуществ печати данной установкой можно выделить:
- Малую минимальную толщину наносимого слоя – 20 мкм.
- Заполнение рабочей камеры инертным газом, что позволяет работать с различными реактивными металлами.
- Скорость печати составляет до 35 см/час.
- Толщина слоя построения – 30 и 50 мкм.
- Мощность – 400 Вт.
Отдельно отметим запатентованную систему подачи порошкового материала, благодаря которой скорость печати значительно выше, чем на большинстве производственных установок в той же ценовой категории. В производстве мы используем следующие материалы:
- Нержавеющая сталь (отечественная 07Х18Н12М2 (Полема) и импортная 316L).
- Инструментальная сталь (импортная 1.2709).
- Жаропрочные сплавы 08ХН53БМТЮ (аналог Inconel 718, про-во Полема) и ЭП 741 (производства ВИЛС).
- Кобальт-Хром (COCR)
3D-принтер SLM 280HL может использоваться для создания разного рода металлических компонентов, прототипов и конечных изделий. При необходимости мы можем обеспечить мелкосерийное производство.
Производственная установка ProX 100
ProX 100 – компактная установка для 3D печати металлом, разработанная американской компанией 3D Systems. Она работает по технологии прямого лазерного спекания, благодаря чему обеспечивает высокую скорость и точность производства. Среди основных характеристик стоит выделить:
- Размер рабочей камеры – 100х100х80 мм.
- Толщина слоя построения – 20 и 30 мкм.
- Мощность – 50 Вт.
ProX 100 позволяет создавать прототипы, которые невозможно разработать стандартными методами, обеспечивает короткие сроки изготовления, гарантирует отсутствие пористости материала и высокую плотность деталей. Кроме того, отметим стандартизированное качество всех изделий вне зависимости от их структуры. На данный момент модель активно используется в стоматологии при создании высокоточных протезов, но нашла широкое применение и в других отраслях:
- Производство двигателей и отдельных их деталей.
- Разработка медтехники.
- Печать ювелирных изделий и даже предметов современного искусства.
В печати мы используем сплав кобальт-хром КХ28М6 (производство Полема), изначально разработанный для аддитивных технологий при создании эндопротезов.
3D печать металлом – применение в настоящее время
Многие специалисты утверждают, что 3D печать как таковая еще полностью не раскрыла свой потенциал. К примеру, Илон Маск планирует использовать технологию в колонизации Марса для строительства административных и жилых зданий, оборудования и техники прямо на месте. И это вполне реально, ведь уже сейчас технология трехмерной печати металлом активно применяется в различных отраслях:
- В медицине: изготовление медицинских имплантов, протезов, коронок, постов и т.д. Высокая точность производства и относительно доступная цена сделали 3D печать очень актуальной в данной отрасли.
- В ювелирном деле: многие из ювелирных компаний используют технологию 3D печати для изготовления форм и восковок, а также непосредственно создания ювелирной продукции. К примеру, печать титаном позволяет создавать изделия, которые ранее представлялись невозможными.
- В машинной и даже аэрокосмической отраслях: BMW, Audi, FCA и другие компании не первый год используют 3D печать металлом в прототипировании и всерьез рассматривают ее использование в серийном производстве. А итальянская компания Ge-AvioAero уже сейчас печатает компоненты для реактивных двигателей LEAP на 3D принтерах.
И это лишь малая часть того, что можно создавать на современном оборудовании. Практически все металлические изделия, которые вам необходимы, можно создать при помощи технологии 3D печати металлом. И если данная услуга актуальна для вас, обратитесь в SPRINT3D. Мы возьмемся за работу любой сложности и объемов. А главное – предоставим первоклассный результат!
Будущее уже здесь!
sprint3d.ru
3D-печать из металла набирает обороты / Top 3D Shop corporate blog / Habr
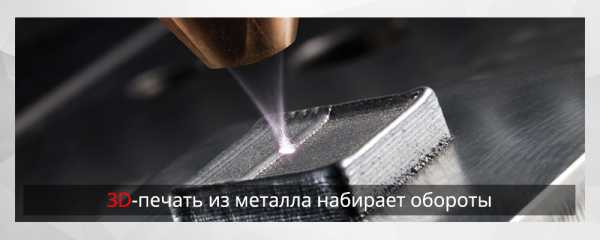
Пока дизайнеры и инженеры добиваются успеха в 3D-печати при создании прототипов и производстве частей в малом объеме из пластиков и полимерных материалов, недавний прогресс в изготовлении деталей из металла с использованием аддитивной металлической технологии позволил создать одни из самых потрясающих 3D-напечатанных частей за всю историю 3D печати.
Интересно, что срок основных патентов на 3D-печать из металла истекает в конце 2016 года. И хотя массовое использование FDM 3D печати рядовым потребителем пока не оправдывает ожидания большинства, 3D-печать из металла дает возможность разработчикам изделий использовать весь потенциал 3D-печати, не уступающий традиционным методам литья или механической обработки, а в ряде случаев и превосходящим их в цене и скорости изготовления серии.
3D-печать из металла подразумевает аддитивную технологию производства с использованием металлического порошка. Мы имеем дело либо с методом прямого лазерного спекания металлов (DMLS) либо с методом выборочной лазерной плавки (SLM), что называется по разному, исключительно из-за патентных войн.
В отличии от традиционной техники изготовления металлических конструкций, основанной на резке, фрезеровке и штамповке, при 3D-печати из металла детали создаются послойно, посредством наплавления материала под действием лазерного луча, который буквально вырисовывает форму каждого слоя до полной готовности объекта.
Совмещение современных средств проектирования, оптимизирующих моделирование и анализ для создания оптимальной конструкции, – например изготовление легковесных решетчатых конструкций, функционально оптимизированных и подходящих для производства с использованием аддитивной технологии – позволяет не только сократить время изготовления частей, но и получать гораздо более прочные и легкие изделия по сравнению с частями, изготовленными с использованием традиционных способов производства.
Так, в сфере космических исследований лидеры индустрии компания SpaceX Илона Маска и НАСА используют все возможности 3D-печати из металла для производства частей ракетных кораблей, что позволяет им значительно сократить расходы и одновременно улучшить эксплуатационные характеристики. SpaceX широко использует металлические детали для камеры сгорания двигателя SpaceX SuperDraco.
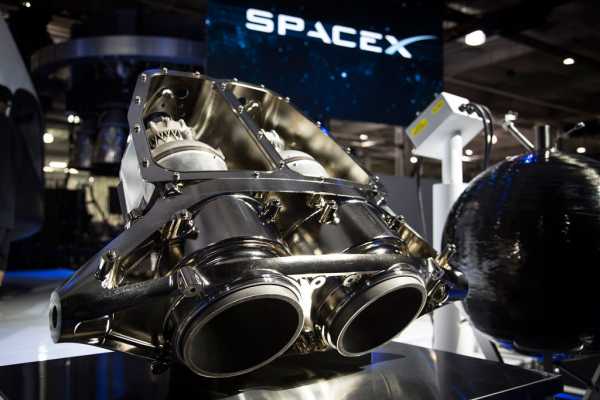
НАСА смогло разработать турбонасос для своего ракетного двигателя, содержащий на 45% меньше деталей, чем насосы, изготовленные по традиционным технологиям производства. Похоже, вскоре весь ракетный двигатель можно будет «собрать» на 3D-принтере. Это только вопрос времени.
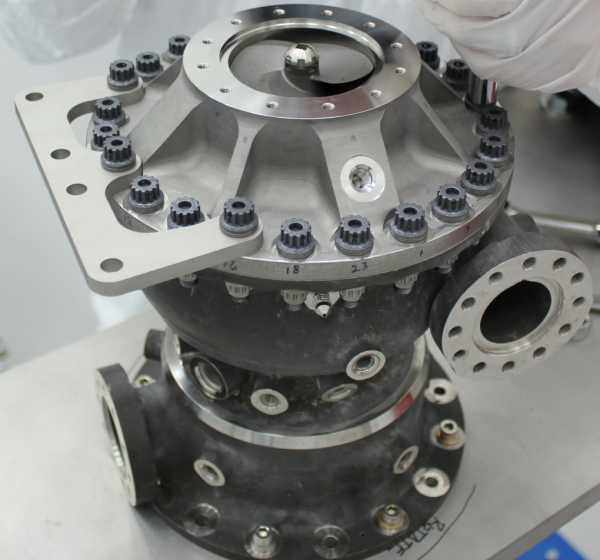
Таким образом, в одних отраслях успехи 3D-печати могут быть преувеличены, однако ее заслуги нельзя не признать в других.
Вернемся на Землю. Авиационно-космическая промышленность является одной из самых быстро развивающихся отраслей, использующих 3D-напечатанные металлические части, позволяющие значительно уменьшить общий вес самолёта и в то же время повысить эффективность сборки с возможностью кастомизации конструкции. На сегодня гигант самолётостроения корпорация Boeing выпустила более 20 000 деталей, изготовленных по аддитивной технологии для успешно реализованных самолётов.
Аналогично компания Airbus широко использует различные 3D-напечатанные детали в своих самолетах. Компания даже поделилась своей уникальной технологией с другими профессионалами, не работающими в Airbus. Бионический дизайн стандартных изделий набирает все большие обороты с применением 3D-печати в виду значительного облегчения конструкции и при равных прочностных характеристиках нужных элементов.
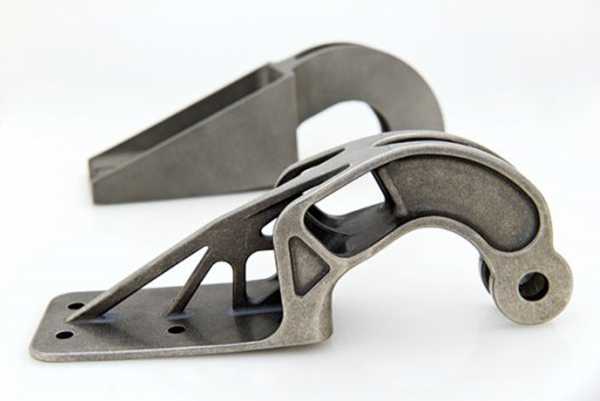
Точно так же как напечатанные на 3D-принтере металлические части полностью изменяют то, как мы путешествуем по воздуху, и в космосе, так и на Земле, они обеспечивают выдающиеся достижения в сфере здравоохранения. Перспективы настолько многообещающие, что Управление по контролю за продуктами и лекарствами США одобрило использование 3D-напечатанных металлических имплантов для медицинских процедур. В России появляются компании, делающие уникальные индивидуальные эндопротезы с применением систем селективного лазерного плавления
металла.
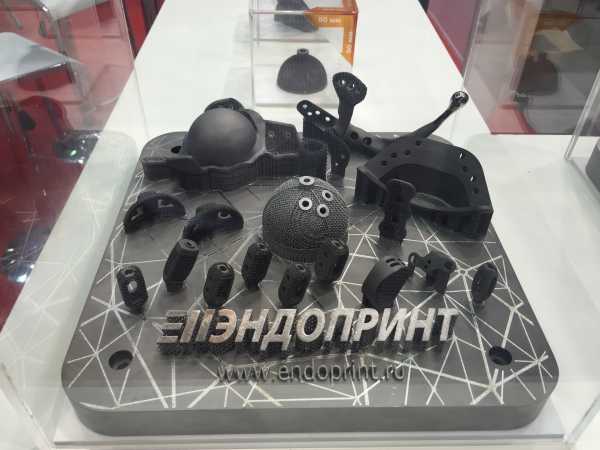
Среди недавних достижений 3D-печати из металла в медицинском секторе стоит упомянуть имплант черепа из титана и рёберную клетку, напечатанные на 3D-принтере. Имплант черепа и рёберная клетка были изготовлены по индивидуальным заказам для больных раком с использованием цифровых снимков после операций по удалению опухоли.

Субтрактивные методы изготовления металлических деталей, включая точение, обтачивание и дробление, помогли нам создать самые удивительные продукты и технологии за последние 200 лет, однако нам хватило всего нескольких лет, чтобы понять, насколько эффективной может быть аддитивная технология изготовления металлических деталей.
Вместе с мощными функциональными возможностями современного программного обеспечения — CAD и возможностью создавать новые геометрические элементы, которые не могли бы быть созданы иным образом, отрасли, широко применяющие сложные металлические изделия — в особенности космическая и авиакосмическая промышленность, здравоохранение — переживают настоящую революцию в производстве, благодаря возможностям 3D-печати.
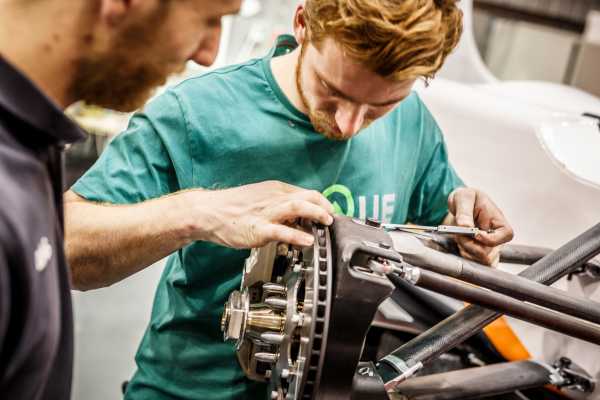
3D-печать отвечает требованиям этих отраслей в производстве сложных металлических деталей, изготавливаемых по индивидуальному заказу и в относительно малом объеме. С новыми 3D-принтерами и материалами, появляющимися то тут, то там, нет ничего удивительного в том, что спрос на 3D-печать из металла продолжает расти.
Пока установки для селективного лазерного плавления остаются дорогими и громоздкими, требуют квалифицированного персонала и особых требований к месту инсталляции, а гиганты отрасли борются за увеличение размера области построения, команда стартап-проекта Desktop Metal пошла другим путем. Их идея — произвести принтер, доступный не только корпорациям-гигантам, но и небольшим инжиниринговым компаниям.
Стартап по созданию доступного SLM принтера на сегодня привлек почти 100 миллионов долларов, а среди инвесторов оказались такие известные компании как СВА, Kleiner Perkins Caufield Byers, Lux Capital, GE, Stratasys и другие. Кроме того, соседи Desktop Metal — успешные и уже набравшие обороты стартапы: Formlabs, MarkForged и Voxel8, что дает дополнительную надежду в скором появлении бюджетного DMLS принтера, вслед за бюджетными SLA и FDM системами.
Хотите больше интересных новостей из мира 3D-технологий?
Подписывайтесь на нас в соц. сетях:
habr.com
3D печать металлом — 3D печать
Товарищи, разъясните пожалуйста!
Посмотрел красивые видюшки 3d печати принтерами, а также технические характеристики 3d принтеров EOS и 3D-system.
Там используются лазеры в младших моделях по металлу 3D-system — 50W fibre laser, а в EOS Yb-fibre laser 200W
CO2 лазеры используются в моделях для работы с пластиками.
Интересно возможно ли такое повторить с сравнительно дешевыми китайскими CO2 лазерами… хотя бы в теории.
Появилось несколько вопросов. Помогите, пожалуйста, разобраться…
1) Почему в 3D принтерах по металлу применяют волоконные лазеры? Читал что у них выше КПД, но, насколько я понял, и цена намного выше. Также читал что спектр излучения CO2 лазера плохо поглощается металлами, но почему тогда на CO2 лазерах работает множество cnc резаков?
3) Какая минимальная мощность необходима для работы с металлом? Пусть не очень быстро, тонким слоем плавить металлический порошок. В младшей модели принтера используется 50W fibre laser… Достаточно ли одной 80W-100W CO2 трубы для простых экспериментов, сможет ли она плавить порошок (например: ПМ-НЮ50 никель-53%, алюминий-47% Фракция 40-160мкм) ?
4) Можно ли соединить несколько отдельных трубок по 80 Ватт для получения большей мощности?
По аналогии как тут:
Либо объединить и сфокусировать несколько лучей в один? Если есть для этого оптика не по космическим ценам…
5) Не знаю порядок цен на не CO2 лазеры, подскажите, пожалуйста, по каким ключевым словам поискать… fibre laser, yag laser, Yb-fibre laser очень плохо гуглится.
Какое-то предложение порошка для печати нашел тут: http://rusthim.ru/poroshki и еще на каких-то забугорных сайтах… вроде бы цена не особо высокая.
Очень жду появления открытых проектов 3д принтеров по металлу… надеюсь ответы на эти вопросы помогут и мне и сообществу в этом)
www.chipmaker.ru
3D принтер по металлу — как это работает?
Аппарат для стереолитографии SLA-250
Объемная печать начала развиваться в середине XX века. В 1948 году американец Чарльз Халл (Charles Hull) изобрел технологию, которая получила название SLA (Stereolithography), или стереолитография. Процесс основан на свойстве жидкого фотополимера отвердевать под лазерным излучением. Выращивание модели ведется аддитивным методом, рабочая площадка опускается на 0,05-0,15 мм и покрывается новым слоем фотополимеризующейся композиции, а лазерный луч засвечивает участки, соответствующие стенкам виртуальной детали, заставляя их отвердевать.
Чарльз Халл оформил патент на изобретение в 1986 году и основал компанию 3D Systems (крупнейший производитель отрасли до настоящего времени). Тогда еще не было понятия 3D печать, и машину назвали аппаратом для стереолитографии. Но это первое устройство, создавшее реальный объект по виртуальному образцу методом послойного выращивания. С того времени направление бурно развивается, делаются открытия, основываются компании. Появились лазерные и струйные принтеры для объемной печати, использующие в качестве сырья пластики, полимеры, биоматериалы, продукты питания, и, конечно, металлы.
Область применения
Цельная металлическая деталь сложной формы
Подавляющее большинство 3D принтеров по металлу – огромные модели весом более тонны. Они используются в промышленных целях и служат для выращивания деталей сложной геометрии, которые затруднительно изготовить литьем или механической обработкой. Цена такого 3d-принтера может достигать нескольких сотен тысяч долларов.
На 3D устройствах изготавливаются:
- прототипы для тестирования и испытания деталей серийного производства;
- индивидуальные медицинские имплантаты;
- зубные коронки и мосты в стоматологии;
- ювелирные изделия.
Существует несколько технологий 3D печати металлами и их сплавами. Одни из них успешно применяются для работы с разными материалами, а другие предназначены исключительно для выращивания металлических изделий.
Послойное наплавление и ламинирование
Фигурка из BronzeFill до и после полировки
Самый популярный способ выращивания объемных моделей – технология FDM (Fused Deposition Modeling), называемая также FFF (Fused Filament Fabrication). Печать ведется методом послойного наложения расплавленного материала, поставляемого в виде нити. Использование здесь тугоплавких металлов невозможно, слишком высока температура, которую должен выдерживать экструдер принтера, но в филамент можно добавить какое-то количество металлического порошка. Один из таких материалов – BronzeFill – состоит из термопластика и бронзы. В процессе изготовления детали металл, естественно, не плавится, только основная составляющая нити. Благодаря содержанию бронзового порошка готовый предмет поддается полировке и выглядит как металлическое изделие, хотя прочность, и другие свойства модели, ограничиваются характеристиками пластика.
Технология LOM (Laminated Object Manufacturing), или ламинирование, заключается в последовательном наложении друг на друга тонких листов, в частности, может быть использована металлическая фольга. В каждом слое лазером вырезается контур, соответствующий сечению прототипа на соответствующем уровне. Соединяются же листы между собой связующим веществом на клеевой основе. Визуально полученные изделия напоминают металлические, но их целостность зависит от возможностей клея.
Струйная 3D печать
Принтеры, работающие по этой технологии, используют любые материалы, которые могут быть превращены в порошок, в том числе металлы и их сплавы. Из струйной печатающей головки на тонкий слой композита поступает жидкое связующее вещество, которое скрепляет основной материал. Затем в рабочую зону подается новый слой порошка и выращивание продолжается. Распечатанное 3D принтером изделие по-прежнему нельзя назвать металлическим, ведь его прочность зависит от свойств полимера. Но такую деталь можно подвергнуть термической обработке, в процессе которой металлический порошок начинает спекаться, а связующее вещество выгорает. На этом этапе изготовления, хотя в составе модели исключительно металл, она крайне хрупка из-за своей пористости. Для повышения прочности проводят пропитку изделия бронзой. Несмотря на сложность и продолжительность работ цельнометаллическая модель, полученная таким способом, не обладает свойствами, позволяющими использовать ее в каких-то механизмах. Однако технология широко применяется для производства предметов очень сложной формы, к которым такие требования не предъявляются:
- ювелирных изделий,
- сувениров,
- предметов интерьера.
Лазерное спекание порошковых материалов
Схема работы 3D принтера по технологии SLS
Два метода 3D печати, разработанные разными компаниями, отличаются друг от друга техническими решениями, но приводят к одному результату: лазер принтера разогревает порошок до температуры, близкой к точке плавления, и спекает гранулы вместе для получения твердой структуры. По технологии SLS (Selective Laser sintering), или выборочное (селективное) лазерное спекание, используется углекислотный лазер. Иногда для увеличения скорости работ конструкцией может быть предусмотрено два лазера. В качестве сырья используются порошки из полимеров, керамики, стекла, металлов. Часто гранула представляет собой ядро из металлического порошка, покрытое оболочкой из легкоплавкого материала. Чем ниже температура спекания – тем менее мощным может быть лазерный излучатель. Владелец патента – компания 3D Systems – в качестве сырья для своих принтеров серии sPro, работающих этому методу, заявляет прочные инженерные пластики.
3D принтер EOSINT M280 по металлу
Технология DMLS (Direct Metal Laser Sintering), или прямое лазерное спекание металла, изобретена компанией EOS из Германии и позиционируется как способ спекания именно металлических порошков:
- инструментальных и нержавеющих сталей,
- титановых и никелевых сплавов,
- легких металлов,
- кобальт хрома.
Используются оптоволоконные лазеры 200 или 400 Вт, их мощность и количество зависит от комплектации конкретной модели принтера. Построение модели происходит в закрытой камере, наполненной инертным газом для предотвращения окисления металла. Кроме того, порошок подогревается до температуры, близкой к точке плавления. Линейка 3D принтеров компании EOS, использующих технологию DMLS, предназначена для промышленного производства, так же как и устройства серии ProX компании 3D Systems.
Лазерная и электронно-лучевая плавка
3D принтер Arcam Q10 для производства имплантатов
Металлы подвергаются не спеканию, а полной плавке до образования гомогенной массы по технологии SLM (Selective Laser Melting), или селективное лазерное плавление. Компания Phenix Systems выпускает линейку принтеров Phenix PL, использующих этот метод. Устройства оснащены мощными иттербиевыми волоконными лазерами, позволяющими значительно повысить температуру луча. Самое существенное отличие от технологии SLS, что при лазерном плавлении структура полученной детали по своим свойствам практически не отличается от литых изделий.
По технологии EBM (Electron beam melting), или электронно-лучевая плавка, место лазера занимают электронные излучатели, выращивание модели идет в глубоком вакууме при температурах до 1000°C. На этом методе основана работа 3D устройств компании Arcam, Швеция. Принтеры предназначены для промышленного производства ортопедических имплантатов, деталей аэрокосмической продукции, изделий из титановых сплавов и других материалов, требующих повышенной температуры для обработки.
Видео (Промышленный 3D принтер по металлу)
printerprofi.ru
Технология и принтеры компании Desktop Metal
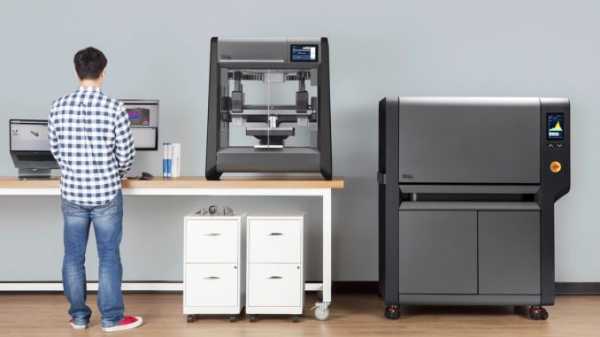
Компания Desktop Metal создала новую технологию и первый компактный принтер для 3D-печати металлом. Первые поставки систем начнутся уже осенью этого года. Один принтер будет компактным, благодаря чему его можно будет разместить даже на столе.
В 2015 году четыре профессора из MIT основали компанию Desktop Metal. Среди них был и знаменитый Эмануил Сакс – тот самый изобретатель, который и придумал в 1989 году первый 3D-принтер. В прошлом году они в первые представили устройства для печати металлом. Всего их на данный момент будет два. Компактный комплект DM Studio по цене 120 000$ и DM Production (420 000$), предназначенный для использования промышленными компаниями. Production способна печатать 8200 кубических сантиметров изделия за час, что в 100 раз быстрее нынешних способов изготовления.
Технология
Суть заключается в использовании аддитивной технологии 3D-печати, позволяющей выращивать заготовку из металлического порошка с использованием связующего вещества. Один слой печати по толщине равен человеческому волосу. После нанесения слоя принтер его подсушивает и наносит следующий слой за слоем.
После того, как заготовка готова, она для спекания помещается в миниатюрную плавильную печь, использующую дополнительно микроволны, благодаря которым ускоряется процесс и сама деталь существенно усиливается. Сама заготовка не плавится, так как нагрев происходит при температуре ниже точки плавления металла, во время которой из детали удаляется связующее вещество.
Видео как работает такой принтер:
Оба устройства способны использовать на данный момент чуть более 200 сплавов.
Почему технология 3D-печати от DM является подрывной? Минусом всех подобных других устройств является то, что скорость печати металлом очень низкая и сам процесс настолько неудобный, что их использование в промышленных целях было нецелесообразным. Причем детали, получаемые из них, чаще всего, либо просто не подходят для использования в каких-то серьезных целях, либо еще и требуют существенной дополнительной обработки.
Пример работы 3D-принтера ExOne:
ExOne до появления принтеров от DM считался одним из самых передовых и инновационных.
Также существуют и другие технологии печати, путем выращивания детали из расплава, а также наплавки, но точность их очень низкая и, как говорилось выше, требует последующей обработки.
Благодаря своим инновациям, подтвержденным 138 патентами, компании Desktop Metal удалось в октябре 2015 года привлечь инвестиций размером в 97 000 000$ от Google, BMW Group, GE, Lowe’s, NEA, Kleiner Perkins Caufield & Byers, Lux Capital, Saudi Aramco и лидера в сфере 3D-печати Stratasys.
Загрузка…moybiznes.org
3D-принтер и металл — настоящее и будущее трехмерной печати металлом. 3D-принтеры сегодня!
Друзья, небольшое вступление!
Перед прочтением новости, позвольте пригласить вас в крупнейшее сообщество владельцев 3D-принтеров. Да, да, оно уже существует, на страницах нашего проекта! Подробнее >>>
Несмотря на то, что первой технологией аддитивного производства, примененной для создания металлических трехмерных прототипов, стал метод экструзионного послойного наплавления (FDM), наибольшую популярность при производстве металлических деталей завоевали технологии лазерного и электронно-лучевого спекания и плавки. Данные методы весьма схожи – настолько, что даже в профессиональных кругах иногда возникает определенная путаница. И все же, попробуем разобраться в терминах, а также рассмотрим возможности данных технологий – существующие и потенциальные.
Технологии лазерного спекания и лазерной плавки (SLS, DMLS и SLM)
В основе метода «выборочного лазерного спекания» (SLS или Selective Laser Sintering) лежит использование лазерных излучателей высокой мощности (как правило, углекислотных) для частичного сплавления, или «спекания», расходного материала в единое целое. Перед использованием расходный материал измельчается до консистенции пудры с помощью шаровых мельниц. Минимальный размер частиц может достигать двух микрон.
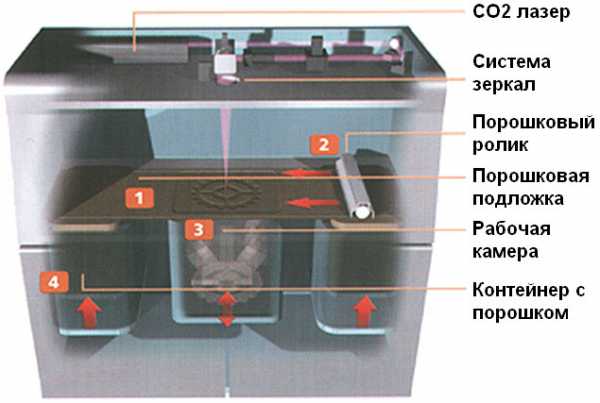
Схема устройства для селективного лазерного спекания
В качестве материала могут использоваться различные полимеры и, что особенно интересно, металлы и металлические сплавы с высокой температурой плавления. В отличие от стандартной экструзионной печати (FDM), технология позволяет спекать однородный материал без связующих добавок. Таким образом, нет необходимости в термической обработке, фактически спеканию, готовых моделей после печати, а сами модели обладают высокой прочностью, приближающейся к показателям литых образцов. Данный метод постройки металлических моделей без применения связующих материалов получил название «прямого лазерного спекания металлов» (DMLS или Direct Metal Laser Sintering).
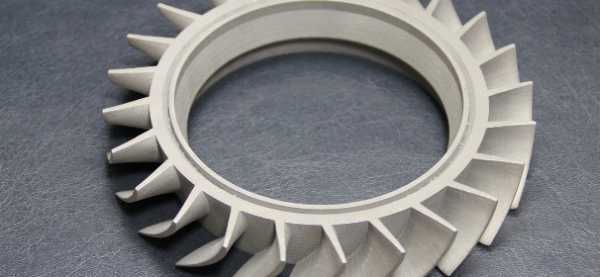
Образец металлической детали турбины, созданной с помощью устройства
3D System ProX 200 методом прямого лазерного спекания
Как и другие технологии 3D-печати, лазерное спекание создает модели послойно. Процесс в чем-то схож с лазерной стереолитографией: в случае со стереолитографическими принтерами модели погружаются в жидкую фотополимерную смолу на глубину, соответствующую толщине одного слоя, с последующим «вычерчиванием» нового слоя лазерным лучом. При лазерном спекании на модель наносится слой порошка толщиной в один слой (толщина слоя может регулироваться), в котором вычерчивается новый контур, а высокая температура позволяет частично расплавлять порошок в местах касания луча, спекая частицы между собой и с предыдущим слоем. И в том и в другом случае модель окружена неизрасходованным материалом до окончания печати. Этот момент немаловажен для «порошковой» печати: при спекании неизрасходованный материал служит в качестве поддерживающей поверхности для последующих слоев моделей сложной формы. Отсутствие необходимости печатать «опоры» облегчает обработку готовых моделей и способствует экономии материала, который в случае с титаном или специальными сплавами может быть весьма дорог. Весь неиспользованный материал может быть собран и использован для печати последующих моделей.
Единственным существенным недостатком лазерного спекания металлических материалов считается пористость готовых моделей. Однако плотность можно повысить за счет повышения энергии лазера и замедления скорости печати. В результате, рабочий материал можно не просто «спекать» в местах касания гранул, а фактически расплавлять, создавая однородное вещество. Именно этот подход и получил название «выборочной лазерной плавки» (SLM – Selective Laser Melting).
Ведущей компанией в сфере печати лазерным спеканием и плавкой можно считать 3D Systems – промышленного гиганта, в 2013 году прибравшего к рукам компанию-разработчика SLS-технологий Phenix Systems.
Технология электронно-лучевой плавки (EBM)
Первопроходцем и лидером по производству аппаратов для аддитивного производства методом «электронно-лучевой плавки» (EBM – Electron Beam Melting) стала шведская компания Arcam. Компания была официально основана в 1997 году, но рождению коммерческого проекта предшествовали четыре года исследований, проведенных совместно с учеными из Технического университета Чалмерса в Гетеборге.
Фактически, EBM основана на том же принципе, что и технология лазерной плавки, за исключением использования электронных пучков высокой мощности вместо лазерных лучей.
Стоит выделить преимущества данной технологии над лазерной плавкой:
Более высокое возможное разрешение в горизонтальной плоскости. Корректировка траектории электронного луча происходит за счет манипуляции магнитными полями, создающими так называемые «магнитные зеркала». Этот метод позволяет добиться более высокой точности, чем манипулирование оптическими зеркалами, используемыми для управления лазерными лучами.
Конструкция оптических зеркал и лазерных линз требует использования дорогих материалов: в зависимости от мощности лазера, поверхность зеркал покрывается серебром или золотом, а линзы могут быть германиевыми или даже алмазными. В случае же с EBM используются относительно недорогие материалы для производства электромагнитных компонентов.
Кроме того, отсутствие необходимости манипулировать физическими объектами позволяет добиться более высокой скорости отклонения пучка, что вкупе с повышением энергии позволяет добиться более высокой производительности.
Наконец, электронный пучок подлежит рассеиванию при необходимости, что позволяет подогревать расходный материал без использования дополнительных нагревательных элементов, характерных для лазерных систем. Подогрев материала необходим для достижения более высокой плотности моделей и облегчения спекания или плавки.
Минусом же применения электронных лучей можно считать наличие рентгеновского излучения, возникающего при бомбардировке металлов высокоэнергичными электронами (т.н. «тормозное излучение»), что требует установки поглощающего покрытия вокруг рабочей камеры.
В целом, электронно-лучевая плавка несколько более сложна, чем лазерная, но обладает более высоким производственным потенциалом. Компания Arcam добилась широкого успеха среди производителей ортопедических имплантатов и авиационных деталей. Ортопедические имплантаты, изготовленные методом EBM, привлекательны не только прочностью, легкостью и износоустойчивостью используемых титановых сплавов, но и возможностью создания полых или пористых металлических структур. Подобная архитектура напоминает строение костной ткани и способствует остеоинтеграции, то есть сращиванию костных тканей с имплантатом аналогично натуральному физиологическому процессу. Что же касается авиационной и нефтегазовой промышленности, электронно-лучевая плавка позволяет создавать жаростойкие форсунки и лопатки газовых турбин, включая реактивные двигатели. Кроме того, метод успешно используется для создания несущих титановых элементов крыла.
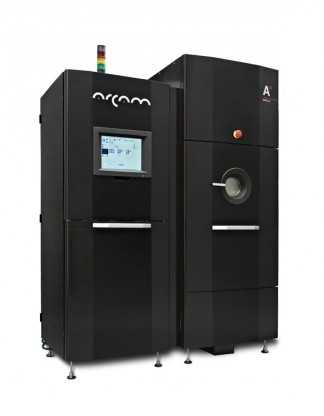
Arcam A2X – новейший промышленный принтер для печати по металлу,
созданный для нужд аэрокосмической отрасли
Аддитивное производство привлекло внимание и космической отрасли, включая НАСА. В первую очередь это касается разработки систем космических аппаратов и ракет-носителей. Ярким примером можно считать использование технологий лазерной и электронно-лучевой плавки для создания элементов ракетных двигателей: камер сгорания и форсунок со стойкостью к температурам свыше 3000°С. Высокое давление и температура требуют использования тугоплавких и прочных материалов – таких, как титан. Проблема заключается в том, что детали могут иметь весьма сложную геометрическую форму, делающую изготовление цельных образцов методом литья или механической обработки невозможным или исключительно дорогостоящим. Как следствие, детали приходится изготовлять из нескольких составных частей, подлежащих сварке в единое целое. Именно сварочные швы, как правило, оказываются слабым звеном за счет нарушения однородности структуры материала или оксидации при сварке.
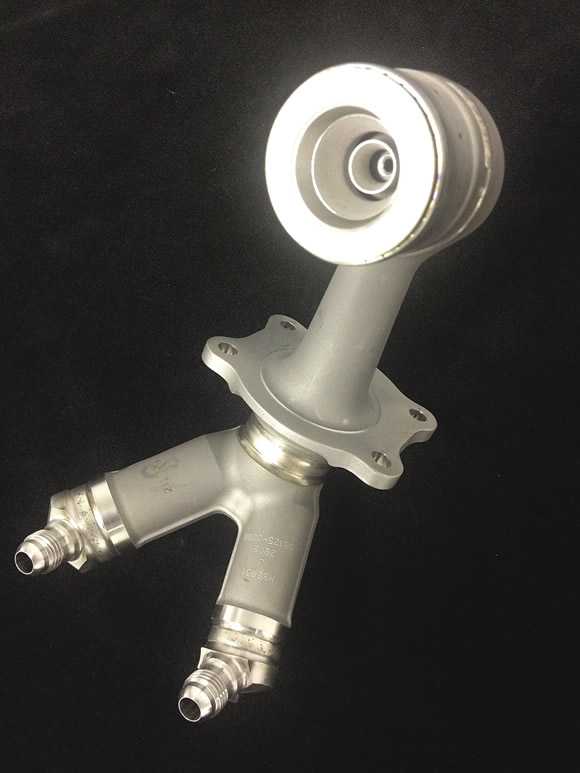
Топливная форсунка реактивного двигателя производства компании
General Electric Aviation, выполненная методом аддитивного производства
Аддитивное производство же не ограничено геометрической сложностью изготовляемых деталей – практически любая форма может быть выполнена без необходимости последующей сборки или сварки. Единственным реальным ограничением является размер рабочей камеры печатающего устройства. В то же время, конструктивных ограничений по размеру рабочей камеры не существует. Вопрос лишь в спросе на технологию, ведь такого рода устройства весьма дороги, а чем больше, тем дороже. Тем не менее, китайская компания Nanfang Ventilator Co., Ltd уже берется за создание промышленных печатных устройств аддитивного производства крупногабаритных металлических деталей – вплоть до шести метров в длину и весом до 300 тонн!
Производство произвольных форм электронно-лучевой плавкой (EBFȝ)
Но при всех достоинствах традиционной лазерной и электронно-лучевой плавки, амбиции НАСА привели к тому, что даже эти новаторские технологии оказалась недостаточны. Дело в том, что инженеры НАСА предложили рассмотреть возможность применения аддитивного производства на орбите. С точки зрения снабжения, идея абсолютна логична. Зачем везти с собой набор запасных деталей или ждать доставки с Земли при экстренной ситуации, когда те же детали можно произвести на орбите?
И здесь НАСА столкнулась с серьезной проблемой: как мы уже выяснили, традиционный метод электронно-лучевой плавки подразумевает использование порошкообразного расходного материала, и не только для создания самой детали, но и использования в качестве поддерживающих слоев при печати деталей сложной формы. Но как удержать порошок на месте в условиях невесомости? Слои наносимого материала должны плотно прилегать к уже изготовленной части детали, что невозможно гарантировать механическим воздействием. Использование магнитных полей теоретически возможно, но технологически сложно, неприменимо в случае с электронно-лучевой плавкой ввиду воздействия на сами электронные пучки, да и не все материалы обладают необходимыми магнитными свойствами.
В итоге, инженеры НАСА решили позаимствовать конструктивный элемент привычных экструзионных 3D-принтеров – подачу расходного материала в виде нити или проволоки. И если использование экструдера для подачи расплавленного тугоплавкого металла непрактично ввиду сложностей с нагревом головки до необходимой температуры и бесперебойной экструзией, то бомбардировка расходного материала электронным пучком вполне подходит для плавки материала в точке соприкосновения с моделью. Кроме того, устраняется и необходимость очищать готовые модели от остаточного материала, что в условиях невесомости опять-таки было бы проблематично. Новая разновидность электронно-лучевой плавки получила название «производства произвольных форм электронно-лучевой плавкой» (EBFȝ — Electron Beam Freeform Fabrication).
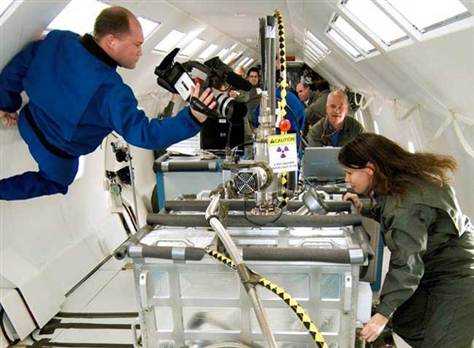
Специалисты НАСА проводят испытания прототипа EBFȝ в условиях искусственной невесомости
Кроме возможности функционирования в условиях невесомости, технология EBFȝ обладает еще одним важным преимуществом над своими предшественниками – возможность одновременной печати разными материалами. Использование нескольких экструдеров может даже позволить создавать электронные и электромеханические компоненты благодаря попеременной печати керамических/пластиковых и металлических слоев. В случае успеха, разработчики невольно приведут к логическому завершению программу RepRap – проект создания устройств, способных воспроизводить самих себя. Практической же целью проекта является возможность производства всех необходимых устройств в открытом космосе или даже на поверхности других планет, используя только местные материалы. В частности, аддитивное производство может стать ключевым фактором в создании постоянных колоний на Луне и Марсе.
Будущее аддитивного производства с использованием металлов
А каковы перспективы аддитивного производства с использованием металла на Земле? Несомненно, отрасль будет развиваться. В последнее время данные технологии привлекают внимание промышленных гигантов – таких, как Boeing, General Electric, Lockheed Martin, Mitsubishi, General Motors. Экономичность и практичность – два качества, которые не могут быть не оценены по достоинству. В некоторых случаях использование технологий спекания и плавки уже достигает больших масштабов: по словам представителей компании Arcam, произведенные ими устройства были использованы для создания более 30000 титановых имплантатов для реконструкции тазобедренных суставов. И это всего лишь начало.
Единственным сдерживающим фактором является себестоимость. Стоимость устройств, несомненно, снизится в соответствии с повышением спроса. Однако сам спрос регулируется достаточно высокой ценой некоторых расходных материалов. Но есть хорошие новости: компания Metalysis недавно обнародовала планы по постройке фабрики для производства титанового порошка, применяемого в аддитивном производстве. Стоимость проекта оценивается в $500млн, что говорит об огромном интересе со стороны промышленности и инвесторов. На данный момент титановый порошок продается по цене от $200 до $400 за килограмм, что не идет ни в какое сравнение с алюминием по цене $30-$40 за 1кг. Соответственно, объем производства титана в 2012 году составил всего 140000 тонн, в то время как алюминия – 48млн тонн. Metalysis прогнозирует возможное снижение стоимости титанового порошка на 75% благодаря применению новаторской электролитической технологии производства. Нетрудно догадаться, что существенное снижение стоимости высоко востребованного титана приведет к значительному росту спроса на 3D-печатные устройства, способные воспроизводить металлические модели. Двумя компаниями, которые выиграют от такого развития событий больше всех, станут 3D Systems и Arcam – лидеры по производству лазерных и электронно-лучевых устройств, соответственно.
Вполне возможно, что повышенный промышленный спрос на устройства для лазерной и электронно-лучевой плавки сделает данные технологии доступными и для бытового использования. Технология EBFȝ даже обладает необходимым потенциалом для создания полноценных «домашних фабрик». Если сделать настенный крючок для половника уже не представляет никаких трудностей для обладателя бытового 3D-принтера, то EBFȝ сможет создавать не только пластиковые крючки, но и сами стальные половники, причем с пластиковой ручкой.
Более того, печать электронных и электромеханических компонентов фактически ограничит возможности пользователей их собственной фантазией, а заодно создаст сущий кошмар для производителей по всему миру. Если соблюдение авторских прав уже становится проблемой, то полноценная печать с комбинированным использованием пластиков и металлов может теоретически позволить создание почти любого устройства. Конечно же, такой уровень останется недостижимым еще долгое время, и не только потому, что сама технология 3D-принтеров, печатающих металлом, достаточно малоразвита, но и ввиду недоступности определенных материалов: мало кто сможет достать порошкообразный германий для производства трансивера сотового телефона.
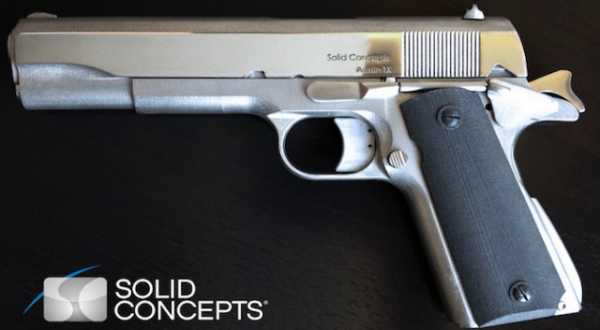
Цельнометаллическая реплика пистолета Colt M1911, изготовленная методом аддитивного производства
С другой стороны, пластика и стали вполне хватит для создания полноценного огнестрельного оружия, тем более что компания Solid Concepts уже создала прецедент в виде металлической реплики пистолета Colt M1911, а Пентагон рассматривает возможность печати оружия на кораблях экспедиционных групп, вместо дорогостоящей доставки к театру действий из США. США и Великобритания уже приняли законодательные меры по запрету нелицензионного производства оружия с помощью 3D-печати. Как сильно соображения безопасности повлияют на развитие бытового применения технологии аддитивного производства, покажет лишь время.
3dtoday.ru