Оборудование для производства дсп – оборудование (станок, линия), технология изготовления
Мини линии для производства ДСП (100-1000 л/сутки), МЛД-110-1287 серии 32 цена 2 000 000 руб
Описание
Уважаемые, господа! Предлагаем Вашему вниманию линию по производству ликвидного материала с высоким качеством и степенью прочности . Основным сырьем , для производства являются опилки и отходы древесины. Линия снабжена сушкой и дробилкой для измельчения техсырья (древесины). Предлагаемая линия — это выгодное решение по утилизации отходов лесоперерабатывающего производства. Превратите отходы своего производства в сырье. Готовый продукт- шлифованная мебельная, ламинированная ДСП. Производительность мини-линии от 100 до 1000 листов в сутки .Размер ДСП 16 х 50500 х 1750 Формат листа может быть другим. РАСЧЕТ ПРИБЫЛИ НА ИЗГОТОВЛЕНИЕ ДСП ПО ПРОЕКТНОЙ МОЩНОСТИ на производительность 200 листов в сутки Цикл формования 13,8 мин. В час — 4, 35 листа на один этаж. На 23 часа работы 200 листов в сутки. Годовая производительность 62400 листов. Обслуживающий персонал : 6 человек – 1 смена; 6 человек – 2 смена. Данные для расчета рентабельности производства: — Расход связующего на 1 м. куб. ДСП составляет 40-67 л (КФМТ-15 или аналог). Основа связующего карбамид-формальдегидная смола. — Электрозатраты, в зависимости от конфигураций линии, 128,5 кВт/ч. — Тепловой агент от сжигания древесных отходов 20 кг на один лист -Расход древесины на один лист ДСП 0,4 м ³.(в древесных частицах) , при влажности 12 %.
Изготавливается по индивидуальному проекту «под ключ» От 100 до 1000 листов в сутки. Формат листа до 1750х5040 мм.
Габариты участка под мини-линию 30 х 15 х 4 м.
Блок
№ А Блок
№ 1 Блок
№ 2 Блок
№ 3 Блок
№ 4 Блок
№ 5 Блок
№ 6 Блок
№ 7
древесины сортировка
подсуши-вание осмоление
внесение вяжущих формование
ковра прессование шлифовка обрезка
ТЕХНИЧЕСКИЕ ХАРАКТЕРИСТИКИ ЛИНИИ
1.ОБЩИЕ ХАРАКТЕРИСТИКИ
Максимальные размеры мини-линии, м 30 х 15 х 4
Базовая толщина плит ДСП, мм 16
Плотность плиты ДСП, кг/м.куб. 600-880
Базовая мощность, в листах (в сутки) 200 листов, 16 мм. толщины
Сырье любой тип древесины
Удельное давление, МПа Экв.2,8
Тип гидравлики гидравлическое масло
Тип рабочего тела высокотемпературное масло
Параметры электропитания 380В, 50 Гц.
Лицензии и сертификаты
Связаться с продавцомДоставка и оплата
По договоренности сторон.
Связаться с продавцомwww.equipnet.ru
Оборудование производства ДСП
Сейчас ДСП является самым распространенным материалом в производстве мебели, строительства (перегородки, крыши), оформления интерьеров. Главные достоинства ДСП – его экономичность и легкость обработки. Продукция из ДСП имеет привлекательный внешний вид, проста в эксплуатации и обладает значительно меньшей себестоимостью чем аналогичные изделия, которые производятся из цельных пиломатериалов.
ДСП имеет равную с цельными пиломатериалами механическую прочность, лучше сохраняет форму при переменной влажности, он намного легче обрабатывается. ДСП может иметь декоративное покрытие из пленок, ламината, лака и шпона. Часто используют меламиновое покрытие, которое отличающееся устойчивостью к воздействию высоких температур и влаги, высокой прочностью. Цветовая гамма декоративныз покрытий ДСП крайне разнообразна..
ДСП – практичный, безопасный и практичный материал, он пользуется спросом у широкого круга потребителей.
Оборудование линии производства ДСП
1 лист 16 мм ДСП равен 0,082 куб.м, то есть для производства 1 плиты необходимо 0,097 куб.м дерева, клея необходимо 78 кг/куб.м.Клей для ДСП (фенольные смолы) производитлегко, данное оборудование работает на любом клее, Вы можете делать его сами из предоставленных нами данными.
Оборудование производства ДСП (цех 1):
Оборудование производства ДСП (цех 2):
Оборудование производства ДСП (цех 3):
Оборудование производства ДСП (цех 4):
Оборудование производства ДСП (цех 5):
Транспортеры и вентиляция для производства ДСП:
Технология производства ДСП
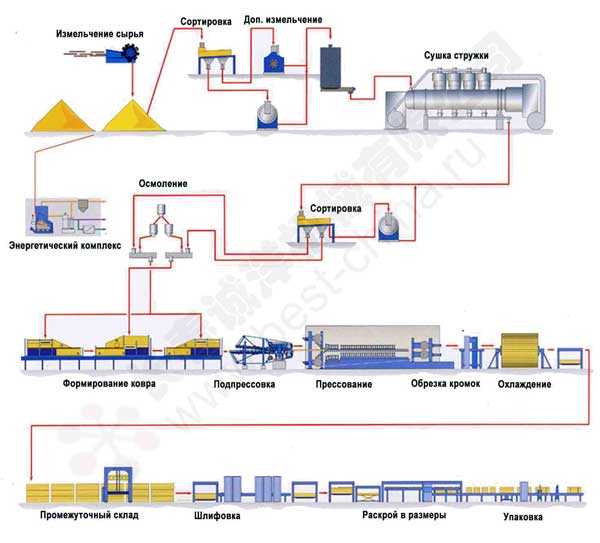
Процесс производства ДСП
ДСП изготавливается с помощью горячего прессования крупно-дисперсной стружки. Сторужка получается из неделовой древесины, отходов деревообработки (любых пород) и введения синтетической термореактивной смолы (клея), а также других добавок для придания качеств плите.
Сначала происходит переработка (измельчение) сырья. Объём круглой древесины сокращается за счет использования вторичной древесины, опилки, щепы. Все виды сырья идут в производство ДСП одновременно или в смешанных видах.
Стружку сортируют, очищают и сушат. Затем её смолят и из просмоленной стружки формируется ковёр, в результате пресования которого получается плита. Затем плиты кромкуются (обрезаются края) и подвергаются конечной обработки — шлифованию, нанесению покрытий и другим.
- Переработка сырья
- Сушка
- Осмоление
- Формирование ковра
- Формирование наружных и внутренних слоев смешанным поток стружки
- Подрессовка
- Прессование
- Обрезка кромок
- Охлаждение
- Шлифование
- Разрезка по размеру
- Ламинирование
- Складирование/упаковка
Читать: Оборудование производства древесных плит
Видео оборудования
best-china.ru
Технология по изготовлению плит дсп. Технология изготовления дсп
Для многих успешных бизнесменов не секрет, что производство ДСП в современное время — дело весьма прибыльное. Исходным материалом для изготовления ДСП являются отходы деревообрабатывающей промышленности — опилки, щепки и другие мелкоизмельченные древесные остатки. Применение такого материала во многих отраслях строительства и мебельного производства позволяет сохранять леса от дополнительной вырубки. Таким образом, сберегается зеленая зона на больших территориях, а это чистый кислород для всего человечества.
К сожалению, человек еще не придумал полноценного заменителя древесины для различных производств, вот и рубят лес, и щепки летят. В плане доступного исходного материала бизнес на производстве ДСП, безусловно, выгоден — дешевые отходы деревообрабатывающей промышленности, лесопильных цехов и большая сфера применения произведенной продукции. Процесс сбыта изготовленной продукции будет обеспечен спросом на 100 %.
При производстве ДСП можно организовать бизнес с различными направлениями: есть возможность сформировать широкомасштабный процесс производства, или же разбить его на составляющие по отдельным видам:
- Вначале, можно предложить подготовительный процесс автоматизировать.
- Отходы древесно-стружечного производства должны быть доставлены в цех подготовки. В этом цеху находится отлаженная непрерывная линия из рубильных машин и стружечных станков.
- В конце такой линии выходит технологическая щепа.
- Цикл подготовки производства закончен, и щепа может направляться в цех по производству ДСП.
Сам цех подготовки является экологически чистым, и может быть выделен отдельной структурой бизнеса.
Оборудование для производства ДСП
Следующим этапом пути отходов будет завод по производству дсп.
- Технология изготовления плиты заключается в смешивании технологической щепы и термореактивной смолы — загустителя.
- Далее смесь поступает в специальные формы различных видов и под воздействием температуры и высокого давления происходит прессование плиты, где она склеивается в единый и прочный пакет.
- После охлаждения изделия, его достают из формы и обрезают края.
- Плита готова к употреблению.
- Ее шлифуют, сортируют и, при необходимости, ламинируют.
На всех этапах необходимо технологическое оборудование для производства дсп, которое применяется в цехе подготовки производства, в основном цехе и цехе шлифования.
- В цехе подготовки производства устанавливается дробительная установка и стружечный станок.
- В основном цехе — термические пресса, веерные охладители и станки автоматической обрезки краев листа по ширине и длине.
- Для выполнения шлифовальных операций устанавливаются шлифовальные станки.
Расчет мощности и ширины обработки рассчитывают для каждой партии отдельно или вводится стандарт по данным показателям, от которого зависит сортность выпускаемого листа — это оборудование относится к основному.
К дополнительному оборудованию относят вибросита и транспортеры — ленточные, роликовые, спиральные и цепные. Применяются подъемные столы для укладки листов в пачки. Во всех цехах устанавливается вентиляционная система для сбора и удаления технологической пыли. Производство ламинированного дсп является, можно сказать, завершающим этапом. Из первого сорта шлифованной плиты изготавливают ламинированный лист или покрывают шпонкой. Ламинированный лист по цене на порядок выше шлифованного. Поэтому для производства экономически выгодно изготовление ламинированного листа. Его широко применяют отделочники для монтажа различных настилов.
Мебельная промышленность является основным потребителем ламината для изготовления дверей, фасадов, в вагоностроении он применяется как отделочный материал для перегородок, готовят из него заготовки для модульной мебели.
Ламинированный ДСП изготавливается на основе исходного материала, который значительно дешевле других материалов, технологически выгоден, а кроме того, требует меньше труда и затрат. Подготовленную и осмоленную щепу закладывают в формы, додают затвердители и необходимые в технологическом процессе добавки, после чего подают в станок для производства дсп — термические пресса. Под высоким давлением и высокой температурой происходит прессование и склеивание смеси в однородную плиту. При закладке материалов в смесители строго регламентируются весовые доли смолы и щепы. При изменении весовых долей вкладываемых материалов резко меняются физические и механические свойства полученного листа. Это приводит к изменению качества и прочности плиты. Чтобы качество изготовленной плиты соответствовало стандартам, термические пресса необходимо подбирать с автоматической настройкой, те, что обеспечивают более высокие технологические характеристики произведенных листов.
Приблизительные затраты на организацию производства ДСП
Выпуском линий для производства ДСП за
jtcase.ru
Основные станки для производства ДСП. Оборудование из Китая
Станок для переработки бревен в технологическую щепу
Строгальный станок серии RX
Сушильные камеры UGX-50
Вибросито серии TS
Машина для дозировки, взвешивания и клеесмешения LU6000
Формирующая машина BHPZJ-III
Термопресс LURYJ511-08
Станок для грубой шлифовки BSG2613D
Станок для тонкой шлифовки BSG2813
Станок для шлифовки торцов LURXP-04
Станок для распила боковин LURXP-01
Поперечный распиливатель боковин LURXP-03
Шредер для выравнивания верхней поверхности LURXP-02
Моющая машина с ветровым удалением влаги LUAS25
Машина для 2-стороннего нанесения ламинирующего слоя с механизмом обрезания LUASR13
Пресс для двусторонней ламинации LUAS-SA5
Пресс для односторонней ламинации LUAS-SA6
Роликовый транспортер для стандартного листа LUAS-SA1
Роликовый транспортер для листа длиной до 6 м LU RYJ-03
Ленточный транспортер ZD-75
Спиральный транспортер LSY — 100
Роликовый подъемный стол LUSA75Y
Цепной транспортер LUZT15
Охладитель звездчатый LULCY360
Принудительная вентиляционная система удаление тонкой фракции пыли при грубом и тонком шлифонии PPRU-50000
Цех №1
Станок для переработки бревен в технологическую щепу
Производительность — 20 м3/час.
Производительность — 10 м3/час.
Производительность — 7 м3/час.
Производительность — 4 м3/час.
Технические данные станка для линии 100 000 м3 серии RХ:
Мощность | 110 кВт |
Ширина | 1570 мм |
Длина | 1614 мм |
Высота | 3000 мм |
Объем | нет |
Вес | 4585 кг |
Производительность | 20 куб. м в час |
Требования к фундаменту | требуется |
Кем изготавливается фундамент | заказчик |
Хар-ка пульта | индивидуальный |
Кем изготавливается подвод энергии | заказчик |
Процент площади в контейнере | 10% |
Технические особенности | диаметр ножей — 1220 мм, скорость вращения ножей — 740 вращений в мин., кол-во ножей — 4 шт., макс. диаметр полученного сырья — 200 мм, макс. длина полученной щепы — 20-35 |
Строгальный станок серии RX
Мощность | 130 кВт |
Ширина | 2380 мм |
Длина | 2512 мм |
Высота | 3130 мм |
Объем | нет |
Вес | 6363 кг |
Производительность | 7 куб. м в час |
Требования к фундаменту | требуется |
Кем изготавливается фундамент | заказчик |
Хар-ка пульта | индивидуальный |
Кем изготавливается подвод энергии | заказчик |
Процент площади в контейнере | 70% |
Технические особенности | диаметр ножей — 800 мм, кол-во ножей — 28, длина ножей — 300 мм, скорость вращения ножей — 50 вращений в мин., толщина стружки — 0,4-0,7 мм.Для линий производительностью 30 — 50 тыс. м3 в год необходим 1 станок. Для линий производительностью 60 — 100 тыс. м3 — 2 станка. |
Сушильные камеры UGX-50
Мощность | 75 кВт |
Ширина | 3000 мм |
Длина | 9000 мм |
Высота | 6000 мм |
Объем | 48 куб.м |
Вес | 18000 кг |
Производительность | 45000-50000 кг (200 м3) |
Требования к фундаменту | требуется |
Кем изготавливается фундамент | заказчик |
Хар-ка пульта | индивидуальный |
Кем изготавливается подвод энергии | заказчик |
Процент площади в контейнере | генеральный груз |
Технические особенности | присутствует система аварийного сброса пара и механизм перемешивания сырья и автоматической выгрузки.Возможна поставка сушильного оборудования как напольного размещения, так и вертикального. При вертикальном размещении высота цеха должна быть не менее 25000мм.Для линий производительностью 30 — 50 тыс. м3 в год необходим 1 станок. Для линий производительностью 60 — 100 тыс. м3 — 2 станка |
Вибросито серии TS
Мощность | 1,5 кВт |
Ширина | 2200 мм |
Длина | 5700 мм |
Высота | 1450 мм |
Объем | 1 куб.м |
Вес | 1000 кг |
Производительность | 30 куб. м в час |
Требования к фундаменту | требуется |
Кем изготавливается фундамент | заказчик |
Хар-ка пульта | индивидуальный |
Кем изготавливается подвод энергии | заказчик |
Процент площади в контейнере | 50% |
Технические особенности | размер рабочей поверхности — 10 кв. м, разделение на 3 фракции. |
Продолжительность цикла | 2 мин |
Машина для дозировки, взвешивания и клеесмешения LU6000
Мощность | 60 кВт |
Ширина | 2100 мм |
Длина | 11000 мм |
Высота | 2900 мм |
Объем | 1,5 м3 |
Вес | 2300 кг |
Производительность | 1000 кг в час |
Требования к фундаменту | требуется |
Кем изготавливается фундамент | заказчик |
Хар-ка пульта | индивидуальный |
Кем изготавливается подвод энергии | заказчик |
Процент площади в контейнере | 100% |
Технические особенности | включает в себя аппараты контроля, качества сырья, качества клея, весовой контроль, контроль влажности, контроль работы фильтров, контроль работы вентиляции. Предусматривает дублирующую аварийную систему отключения.В комплект любого завода входит 2 машины подобного типа. 1 машина отвечает за производство верхнего и нижнего слоев ДСП из тонкой фракции опилок, обычно имеет мощность на 45 — 50% меньшую, чем вторая машина. Другая машина отвечает за формирование среднего слоя ДСП. |
Цех №3
Формирующая машина BHPZJ-III Суммарные параметры линии формирования:
Мощность общая | 200 кВт |
Максимальная ширина | 3500 мм |
Максимальная длина | 18000 мм |
Максимальная высота | 6200 мм |
Общий вес | 60000 кг |
Параметры формирующей машины:
Мощность | 30,25 кВт |
Ширина | 3500 мм |
Длина | 14000 мм |
Высота | 6000 мм |
Объем | нет |
Вес | 35000 кг |
Производительность | 20000 кг в час |
Требования к фундаменту | требуется |
Кем изготавливается фундамент | заказчик |
Хар-ка пульта | индивидуальный |
Кем изготавливается подвод энергии | заказчик |
Процент площади в контейнере | генеральный груз |
Технические особенности | максимальная толщина ковра — 45 мм. Размер рабочей поверхности — 1870 х 2750 мм. |
Мощность | 200 кВт |
Ширина | 4500 мм |
Длина | 3300 мм |
Высота | 8800 мм |
Объем | нет |
Вес | 45000 кг |
Производительность | 15 циклов в час |
Требования к фундаменту | требуется |
Кем изготавливается фундамент | заказчик |
Хар-ка пульта | индивидуальный |
Кем изготавливается подвод энергии | заказчик |
Процент площади в контейнере | генеральный груз |
Технические особенности | давление — 1200 мра, 15 этажей |
Охладитель звездчатый LULCY360
Диаметр | 6000 мм |
Мощность | 50 кВт |
Ширина | 3500 мм |
Объем | 60 листа |
Вес | 4000 кг |
Производительность | 200 листов в час |
Требования к фундаменту | требуется |
Кем изготавливается фундамент | заказчик |
Хар-ка пульта | индивидуальный |
Кем изготавливается подвод энергии | заказчик |
Процент площади в контейнере | 2 контейнера |
Технические особенности | нет |
Станок для шлифовки торцов LURXP-04
Мощность | 10 кВт |
Ширина | 2900 мм |
Длина | 580 мм |
Высота | 2100 мм |
Объем | нет |
Вес | 2800 кг |
Производительность | 500 погонных метров в час |
Требования к фундаменту | требуется |
Кем изготавливается фундамент | заказчик |
Хар-ка пульта | коллективный |
Кем изготавливается подвод энергии | заказчик |
Процент площади в контейнере | 25% |
Технические особенности | толщина листа-заготовки — 10-80 мм, скорость вращения пилы — 2840 оборотов в минуту, диаметр пилы — 400 мм |
Станок для распила боковин LURXP-01
Мощность | 10 кВт |
Ширина | 2900 мм |
Длина | 580 мм |
Высота | 2100 мм |
Объем | нет |
Вес | 2800 кг |
Производительность | 1500 погонных метров в час |
Требования к фундаменту | требуется |
Кем изготавливается фундамент | заказчик |
Хар-ка пульта | коллективный |
Кем изготавливается подвод энергии | заказчик |
Процент площади в контейнере | 25% |
Технические особенности | толщина листа-заготовки — 10-80 мм, скорость вращения пилы — 2840 оборотов в минуту, диаметр пилы — 400 мм. |
наверх
Поперечный распиливатель боковин LURXP-03
Мощность | 10 кВт |
Ширина | 2900 мм |
Длина | 580 мм |
Высота | 2100 мм |
Объем | нет |
Вес | 2800 кг |
Производительность | 500 погонных метров в час |
Требования к фундаменту | требуется |
Кем изготавливается фундамент | заказчик |
Хар-ка пульта | коллективный |
Кем изготавливается подвод энергии | заказчик |
Процент площади в контейнере | 25% |
Технические особенности | толщина листа-заготовки — 10-80 мм, скорость вращения пилы — 2840 оборотов в минуту, диаметр пилы — 400 мм |
наверх
Шредер для выравнивания верхней поверхности LURXP-02
Мощность | 25 кВт |
Ширина | 3100 мм |
Длина | 1000 мм |
Высота | 2300 мм |
Объем | нет |
Вес | 1200 кг |
Производительность | 2300 кв. м |
Требования к фундаменту | нет |
Кем изготавливается фундамент | нет |
Хар-ка пульта | коллективный |
Кем изготавливается подвод энергии | заказчик |
Процент площади в контейнере | 10% |
Технические особенности | нет |
Цех №4
Станок для грубой шлифовки BSG2613D
2 работающих ленты
Мощность | 122,5 кВт |
Ширина | 3000 мм |
Длина | 1800 мм |
Высота | 2200 мм |
Объем | нет |
Вес | 1500 кг |
Производительность | 1200 кв. м в час |
Требования к фундаменту | требуется |
Кем изготавливается фундамент | заказчик |
Хар-ка пульта | индивидуальный |
Кем изготавливается подвод энергии | заказчик |
Процент площади в контейнере | 50% |
Технические особенности | 2 ленты; грубая шлифовка с 2-х сторон |
наверх
Станок для тонкой шлифовки BSG2813
4 работающих ленты.
Мощность | 287,7 кВт |
Ширина | 3500 мм |
Длина | 3700 мм |
Высота | 2200 мм |
Объем | нет |
Вес | 3000кг |
Производительность | 1200 кв. м в час |
Требования к фундаменту | требуется |
Кем изготавливается фундамент | заказчик |
Хар-ка пульта | индивидуальный |
Кем изготавливается подвод энергии | заказчик |
Процент площади в контейнере | 100% |
Технические особенности | 4 ленты, 2-сторонняя тонкая шлифовка. |
Цех №5
Моющая машина с ветровым удалением влаги LUAS25
Мощность | 5 кВт |
Ширина | 1200 мм |
Длина | 2700 мм |
Высота | 1700 мм |
Объем | нет |
Вес | 1000 кг |
Производительность | 1000 кв.м в час |
Требования к фундаменту | требуется |
Кем изготавливается фундамент | заказчик |
Хар-ка пульта | индивидуальный |
Кем изготавливается подвод энергии | заказчик |
Процент площади в контейнере | 20% |
Технические особенности | нет |
наверх
Машина для 2-стороннего нанесения ламинирующего слоя с механизмом обрезания LUASR13
Мощность | 20 кВт |
Ширина | 2000 мм |
Длина | 1800 мм |
Высота | 3000 мм |
Объем | нет |
Вес | 1000 кг |
Производительность | 2000 кв. м в час |
Требования к фундаменту | требуется |
Кем изготавливается фундамент | заказчик |
Хар-ка пульта | индивидуальный |
Кем изготавливается подвод энергии | заказчик |
Процент площади в контейнере | 25% |
Технические особенности | включен нож для обрезания поверхностного слоя, максимальная высота барабана с ламинирующим слоем до 1200 мм, барабаны располагаются в верхнем и нижнем секторах станка, по желанию заказчика возможна поставка станков только с нижним, либо только с верхним размещением барабанов с ламинирующими слоями, подача и установка барабанов ручная. |
наверх
Пресс для двусторонней ламинации LUAS-SA6
Давление | 25 мра |
Количество цилиндров | 6 шт. |
Диаметр цилиндров | 320 мм |
Толщина верхней плиты | 140 мм |
Толщина нижней плиты | 120 мм |
Мощность | 22 кВт |
Ширина | 2550 мм |
Длина | без навесного оборудования — 5000 мм. Полная длина — 5700 мм |
Высота | 1500 мм |
Объем | нет |
Вес | 32000 кг |
Производительность | 4000 кв. м в час |
Требования к фундаменту | требуется |
Кем изготавливается фундамент | заказчик |
Хар-ка пульта | индивидуальный |
Кем изготавливается подвод энергии | заказчик |
Процент площади в контейнере | 100% |
Технические особенности | Максимальная ширина: 1900мм. Максимальная толщина: 3-70мм. Мощность главной установки: 18 КВт Мощность нагревания: 25 КВт Рабочее давление пневматики: 4 kgf |
наверх
Пресс для односторонней ламинации LUAS-SA6
Давление | 25 мра |
Количество цилиндров | 6 шт. |
Диаметр цилиндров | 280 мм |
Толщина верхней плиты | 140 мм |
Толщина нижней плиты | 120 мм |
Мощность | 22 кВт |
Ширина | 2550 мм |
Длина | без навесного оборудования — 5000 мм. Полная длина — 5700 мм |
Высота | 1500 мм |
Объем | нет |
Вес | 25000 кг |
Производительность | 4000 кв. м в час |
Требования к фундаменту | требуется |
Кем изготавливается фундамент | заказчик |
Хар-ка пульта | индивидуальный |
Кем изготавливается подвод энергии | заказчик |
Процент площади в контейнере | 100% |
Технические особенности | Максимальная ширина: 1900мм. имальная толщина: 3-70мм. Мощность главной установки: 18 КВт Мощность нагревания: 25 КВт Рабочее давление пневматики: 4 kgf |
Вспомогательное оборудование
Транспортеры и вентиляция Роликовый транспортер для стандартного листа LUAS-SA1
Мощность | 7 кВт |
Ширина | рабочей поверхности — 1870 мм |
Длина | 2750 мм |
Высота | 1450 мм |
Объем | нет |
Вес | 500 кг |
Производительность | ограничена скоростью подачи материала, необходимого для перемещения |
Требования к фундаменту | нет |
Кем изготавливается фундамент | нет |
Хар-ка пульта | коллективный |
Кем изготавливается подвод энергии | заказчик |
Процент площади в контейнере | 15% |
Технические особенности | максимальная единовременная нагрузка — 4000 кг |
наверх
Роликовый транспортер для листа длиной до 6 м LU RYJ-03
Мощность | 14 кВт |
Ширина | рабочей поверхности — 1870 мм |
Длина | 5550 мм |
Высота | 1450 мм |
Объем | нет |
Вес | 1000 кг |
Производительность | ограничена скоростью подачи материала, необходимого для перемещения |
Требования к фундаменту | нет |
Кем изготавливается фундамент | нет |
Хар-ка пульта | коллективный |
Кем изготавливается подвод энергии | заказчик |
Процент площади в контейнере | 25% |
Технические особенности | максимальная единовременная нагрузка — 4000 кг |
Мощность | 10 кВт |
Ширина | 650 мм |
Длина | 8000 мм |
Высота | 1450мм |
Объем | нет |
Вес | 1500 кг |
Производительность | 20 куб. м в час |
Требования к фундаменту | нет |
Кем изготавливается фундамент | нет |
Хар-ка пульта | коллективный |
Кем изготавливается подвод энергии | заказчик |
Процент площади в контейнере | 30 % |
Технические особенности | нет |
Мощность | 7,5 кВт |
Ширина | 450 мм |
Длина | 3500 мм |
Высота | 1450 мм |
Объем | нет |
Вес | 600 кг |
Производительность | 8 куб.м в час |
Требования к фундаменту | требуется |
Кем изготавливается фундамент | заказчик |
Хар-ка пульта | коллективный |
Кем изготавливается подвод энергии | заказчик |
Процент площади в контейнере | 20% |
Технические особенности | нет |
наверх
Роликовый подъемный стол LUSA75Y
Мощность | 5,5 кВт |
Ширина | 2900 мм |
Длина | 3200 мм |
Высота | 1450 мм |
Объем | нет |
Вес | 900 кг |
Производительность | 200 листов в час |
Требования к фундаменту | нет |
Кем изготавливается фундамент | нет |
Хар-ка пульта | коллективный |
Кем изготавливается подвод энергии | заказчик |
Процент площади в контейнере | 25% |
Технические особенности | нет |
Мощность | 15 кВт |
Ширина | 650 мм |
Длина | 15000 мм |
Высота | 1450 мм |
Объем | нет |
Вес | 1025 кг |
Производительность | 20 куб. м в час |
Требования к фундаменту | нет |
Кем изготавливается фундамент | нет |
Хар-ка пульта | коллективный |
Кем изготавливается подвод энергии | заказчик |
Процент площади в контейнере | 35% |
Технические особенности | нет |
наверх
Принудительная вентиляционная система удаление тонкой фракции пыли при грубом и тонком шлифонии PPRU-50000
Мощность | 10 кВт |
Ширина | 2200 мм |
Длина | 1700 мм |
Высота | 1000 мм |
Объем | нет |
Вес | 1500 кг |
Производительность | 26 куб. м в сек |
Требования к фундаменту | нет |
Кем изготавливается фундамент | нет |
Хар-ка пульта | коллективный |
Кем изготавливается подвод энергии | заказчик |
Процент площади в контейнере | 15% |
Технические особенности | нет |
Объем меламиновой пленки определяет заказчик, в зависимости, с 2-х сторон или с 1-й стороны обклеивается ДСП. Исходя из качества пленки, мы спроектируем изменения в машине. Пленка для отделки торцов поставляется в барабанах.
Меламин для верхней и нижней поверхности поступает в рулонах. Лучше, чтобы пленка была однородной и ее не надо склеивать, это повышает качество.
1 лист 16 мм ДСП равен 0,082 куб.м, то есть для производства 1 плиты необходимо 0,097 куб.м дерева, клея необходимо 78 кг/куб.м.
Фенольные смолы (клей для ДСП) в Китае производят более 40 заводов, у каждого своя марка. Наше оборудование работает на любом клее, сами из предоставленных нами данных.
Например для того чтобы вычислить производительность линии перевести метраж в кубаж, нужно взять 100 куб.м в сутки и разделить на 0,087 куб.м, объем 1 плиты ДСП, нужно умножить 1870 на 2750 Х16 и разделить на 1000, то есть линия производит 16 мм ДСП от 1150 листов до 1200 листов.
www.luniwei.com
Пресс для изготовления дсп. Технология изготовления дсп
Древесно-стружечные плиты невероятно популярны, несмотря на свою нефункциональность и непрочные характеристики. В чем секрет популярности? В низкой цене, в широкой сфере применения, в разнообразии и большом выборе. Ведь древесно-стружечные плиты можно назвать плохим материалом для двери, для стены. Но что может быть лучше ДСП для украшения и отделки старой двери? Чем можно визуально разграничить пространство, если законы и планировка квартиры или дома не позволяют выгнать полноценную кирпичную стену? С помощью материала проще всего восстановить внешний вид комода, буфета или пуфика? Ответ на все эти вопросы один – ДСП.
Сырье для древесно-стружечных плит
Сырьевые материалы для производства ДСП недороги и объясняется это очень просто. Древесно-стружечные плиты изготавливают из опилок, отходов лесообработки и лесозаготовок. В ход идут гнилые или сухие сучья, низкокачественная древесина, из которой просто недопустимо изготавливать мебель. В этом есть особый смысл. Благодаря производству ДСП ни одно дерево в лесах не срубается просто и не выбрасывается на свалку – в ход идет любой лесопродукт.
Производственный процесс по изготовлению ДСП
Первая стадия производства древесно-стружечной плиты – измельчение всех древесных отходов на специальных рубительных машинах. В ходе измельчения получается продукт, который называется щепа. Рубительные машины делают все древесные отходы равномерными, одной консистенции, они все становятся щепой. Затем щепу поставляют на роторные станки, где из нее получается стружка. Эта схема называется сырье – щепа – стружка. Есть и немного другая схема – например, с бревнами: бревно – стружка. Там бревна укладывают на специальные станки с ножевым валом, который сразу же нарезает бревна в стружку.
Технология производства ДСП (древесно-стружечной плиты) задает точные размеры, которые обязательны для любой заводской стружки – ее толщина должна составлять 0,5мм, ширина – 8мм, длина – от 5 до 40мм. Понятно, что соблюсти такие параметры с точностью до 1мм даже на современном оборудовании тяжеловато, поэтому допустимы небольшие отклонения и колебания в размерах. На каждом заводе по изготовлению древесно-стружечной плиты свои допустимые параметры отклонения. Они высчитываются, исходя из возможностей конкретного оборудования.
Требования предъявляются и к форме и структуре стружки. Она должна быть абсолютно плоской (чтобы ее легко было наклеить на плиту) и равномерной толщины. Ее поверхность также должна быть ровной и гладкой. Кстати, толщина стружки измеряется в специальных устройствах, так как это очень важный момент, особенно для тех плит, которые будут отделываться ламинированием. Сырую стружку отвозят в бункеры, где она хранится все время, предшествующее сушке. В бункеры ее поставляют с помощью системы пневматического транспорта. Потом стружку передают на сушку. Сушильные камеры высушивают древесную стружку до степени 5% влажности. Внутренние слои стружки должны иметь влажность не более 25%, поэтому стружку для разных слоев сушат в раздельных сушильных установках. Конвективные сушилки барабанного типа сжигают сжиженный газ или мазут и имеют среднюю температуру около +1000 0 С.
Стружку для внешнего слоя нагревают и остужают быстрее. Стружку для внутренних слоев нагревают медленнее, держат в сушилке дольше, остужается она постепенно. Пневматические агрегаты сортируют стружку для внешних и внутренних слоев. Пневматика различает их как раз по степени влажности. Далее стружку смешивают со связующими веществами, которые представляют собой синтетические смолы. Эти смолы превращают разрозненные стружки в единую массу. Связующие смолы подаются к стружке в состоянии жидких растворов.
Далее просмоленная стружка отправляется в формовочные агрегаты. Они высыпают просмоленную стружку на ленточные транспортеры. Иногда вместо транспортеров в составе линии используются поддоны, но это уже устаревающая деталь линий – там из стружки формируют стружечный ковер. Ковер разделяют на пакеты, которые потом подвергают горячей прессовке. После прессовки пакеты из стружки становятся очень плотными, твердыми, их можно транспортировать. Кстати, это только в последние годы ДСП делают исключительно из стружки, которые склеивают смолами и прессуют горячим прессом, после чего и получается готовая плита. Ранее, когда еще не было таких мощных горячих прессов и синтетических смол, стружки склеивали специальным клеем, долго ждали пока они застынут, и приклеивали едва держащуюся стружечную конструкцию на тонкую деревянную плиту.
Технология производства ДСП (древесно-стружечной плиты) изменялась с течением времени, все больше совершенствуясь. Теперь после прессовки плиты поставляют на разгрузочную линию, где их обрезают до нужного размера, затем их охлаждают, потом шлифуют и покрывают специальными закрепителями и смолами. После этого запаковывают в упаковки от производителя и развозят по магазинам. Ранее технология производства ДСП (древесно-стружечной плиты) подразумевала ручную нарезку и ручную упаковку готовых изделий.
Видео технологического проце
mirhat.ru
Оборудование для производства дсп
В наше время многие начинающие предприниматели, которые гонятся за прибылью, делают ставку на производстве современных строительных материалов, даже не обращая внимания на ДСП и считая данный продукт устаревшим.
ДСП – это древесно-стружечная плита, которая является композиционным листовым материалом. Изготовление данного стройматериала осуществляют методом горячего прессования любых деревообрабатывающих отходов: стружек, опилок и так далее. Чтобы получить особые свойства ДСП, в её состав включают необходимые добавки, объем которых может составлять 6-8% от массы самого основного наполнителя.
Применение древесно-стружечной плиты
ДСП используют в строительстве, отделке и в производстве дверей. Также древесно-стружечную плиту применяют в автомобилестроении и вагоностроении. На сегодняшний день ДСП очень широко используют в изготовлении мебельной продукции.
Изготовление ДСП является очень прибыльным делом. Имея доступ к дешевому сырью (деревообрабатывающие отходы) и располагая необходимыми денежными средствами, можно организовать производство древесно-стружечной плиты, спрос которой на строительном рынке есть всегда. Благодаря этому проблем со сбытом продукции у Вас не возникнет.
Оборудование и технология производства ДСП
Основным сырьем в производстве ДСП является стружка, в которую добавляют термореактивную смолу. Изготавливается древесно-стружечная плита методом горячей прессовки. В производстве ДСП главным сырьевым материалом может быть использована любая недорогая древесина. Также можно применять щепу, опилки или любую вторичную древесину. Долговечность и прочность материала зависит от наличия добавок (антисептические, гидрофобизирующие и прочие).
Изготовление ДСП происходит по следующей схеме:
- Прежде всего, древесную стружку необходимо смешать вместе с термореактивной смолой.
- Используя полученную массу, наполняются специально подготовленные формы.
- Благодаря большому давлению и высокой температуре происходит склеивание всей технологической смеси в единое целое.
- Готовую плиту можно доставать из формы, остудить и заняться дальнейшей обработкой (шлифуют края).
Процесс производства ДСП можно разбить на этапы:
- сырье подготавливают к производству;
- происходит изготовление необходимой технической массы;
- форму заполняют полученной массой из древесной стружки и термореактивной смолы;
- плиты прессуют и склеивают;
- полученную продукцию охлаждают и обрезают по размерам;
- торцы и плоскость шлифуют.
Используя привозной материал, можно сразу же отбросить первые два этапа, иначе придется покупать специальную дробилку, чтобы измельчать сырье.
Процесс производства ДСП
- Технологическую смесь стружки вместе с необходимым клеевым составом подготавливают в специальном смесителе, который является немаловажным оборудованием для данного производства. Подготавливая технологическую массу, нужно всё время следить за пропорциями всех компонентов, что входят в её состав. От этого будет зависеть качество материала.
- Используя специальные машины, проводят формировку ковра. Это оборудование укладывает полученную массу в специальные формы для прессовки.
- Прессование материала – это следующий процесс в изготовлении ДСП, который проводится с помощью термопресса.
- Используя установку автоматической обрезки, осуществляют обработку листа по размеру.
- Завершающим этапом в изготовлении ДСП является шлифовка. От данного процесса, который осуществляют с использованием шлифовального оборудования, напрямую зависит сортность материала.
Если у Вас есть желание открыть свой небольшой бизнес по производству ДСП, группа компаний «Ловел» готова помочь Вам в этом прибыльном деле. Мы сотрудничаем с такими известными фирмами, как: «HABASIT», «Bruks», «BRANDENBURGER», «PERSKE», «ANTHON», «Mesutronic», «Eurotech», «MINK-BUERSTEN», «WANDRES», «RIEGLER», «EWS», «BAUMER», которые производят высококачественное оборудование.
lovel.ru
Производство ДСП
Древесно-стружечная плита, или ДСП, представляет собой композиционный листовой материал. Производится он из отходов древесины и неминеральных связующих веществ методом горячего прессования. Состав ДСП может меняться в зависимости от нюансов технологических процессов или желаемых свойств. Но в целом, ДСП это прессованные древесные отходы, что четко выражает английский перевод – «particle board», то есть «доска из частиц».
В настоящее время ДСП является одним из наиболее популярных материалов для производства мебели, при оформлении интерьера помещений, в строительстве конструкций, не требующих повышенной прочности. Неопровержимыми достоинствами такого материала являются его экономичность и простота обработки.
У разных производителей технология производства ДСП практически не различается. Различие состоит лишь в качестве используемых материалов и стоимости исходного сырья.
На любом предприятии производство ДСП состоит из нескольких последовательных этапов.
Этап I – подготовка необходимого сырья
Происходит процесс смешивания различных древесных материалов исходя из желаемых характеристик качества готового изделия. При этом используются древесные стружки, щепа и опилки.
Этап II – измельчение древесных компонентов
Для получения необходимой плотности готового материала сырье должно иметь максимальную однородность. Поэтому производится дробление древесных отходов и дальнейшее их измельчение до нужного размера.
Этап III – просушивание сырья
Для повышения эффективности воздействия клея, подготовленные древесные составляющие нужно избавить от излишней влаги. Для этого измельченное сырье просушивается.
Этап IV – смешивание компонентов
Подготовленное, измельченное и просушенное, сырье тщательно перемешивают с клеящими ингредиентами. В результате получается масса готовая для формирования ДСП-плит.
Этап V – формирование ДСП-плит
Клейкая масса выливается в специальную движущуюся ленту с предварительно определенной шириной. Далее масса прессуется до необходимой толщины. При этом в течение всего процесса прессования соблюдается высокий температурный режим.
Этап VI – нарезка готового полотна ДСП
Прессованное полотно ДСП режется на листы заданного размера, и получившиеся изделия проходят дополнительную просушку.
Этап VII – обработка поверхности ДСП-плит
На завершающей стадии обрабатывается поверхность изготовленных листов ДСП: изделия ламинируются или поверх полотна наносится тонкий слой шпона и получается шпонированная ДСП. Для ламинирования готовых плит применяется специальная пленка, которой и покрываются листы. Может применяться для дополнительной обработки ДСП и бумага или пластик. Себестоимость дополнительно обработанных ДСП-листов невысока, но в итоге цена их намного превосходит стоимость ДСП с просто шлифованной поверхностью.
Непосредственные сырьевые ингредиенты для изготовления ДСП, технологическую щепу и стружку, получают в процессе переработки дерева лиственных и хвойных пород, различных деревянных отходов лесопильного, деревообрабатывающего, спичечного и фанерного производств.
Технологическая щепа вырабатывается при размельчении исходного сырья в рубительных машинах. При этом в зависимости от желаемой кондиции готовой щепы применяются разные типы рубительного оборудования.
Более высокими качественными характеристиками располагает стружка. Используют ее для формирования наружного пласта трехслойных ДСП-плит. Изготавливается такая стружка на специальных стружечных станках, после чего произведенная тоненькая стружка с длинноволокнистой структурой переправляется в дробилку для создания нужной ширины.
На следующем этапе производства щепа и стружка проходят обязательную сортировку. При необходимости компоненты измельчаются и сортируются дополнительно.
Вся сортированная щепа и стружка просеивается электромагнитными сепараторами, что дозволяет удалить металлические частицы, в случае их наличия. Далее технологическое сырье окончательно очищается, то есть промывается водой для удаления возможной грязи и примесей песка, а также для приумножения уровня влажности до требуемого показателя. Излишняя влага из кондиционного сырья удаляется путем сушки его в роторных, барабанных, пневматических или ленточных сушилках.
Сухие стружку и технологическую щепу, отсортированные, очищенные от различных примесей и просушенные, конвейерной системой отправляют в специальные хранилища – бункеры. Объем бункеров рассчитан для обеспечения беспрерывного производства на протяжении трех рабочих смен как минимум.
Кроме древесного сырья, необходимыми в процессе изготовления ДСП являются и химические материалы. Их предназначение состоит в связывании и склеивании под воздействием высоких температур и давления подготовленных древесных частиц. В качестве связывающих материй выступают карбамидо- и феноло-формальдегидные смолы, разнящиеся по цвету, уровню токсичных испарений и влагостойкости.
Смолы феноло-формальдегидные обладают темно-коричневым цветом, что влияет на конечный окрас готового изделия, высокой токсичностью и резким запахом. При их применении время прессования требует более длительных сроков. Преимущество применения таких смол заключается в повышенной стойкости к влаге, вода практически не воздействует на подобные клеевые соединения.
Менее экологически вредными считаются смолы карбамидоформальдегидные, но они обладают меньшей прочностью и клеевой слой разрушается при температуре 60 °С. ДСП, в состав которых входит данный вид смол, применяются в условиях незначительно перепада уровня влажности.
Помимо клеющих компонентов используются при производстве ДСП упрочняющие и водоотталкивающие (гидрофобные) добавки. Их применение способствует сохранению формы готовых изделий при перепадах влажности, поскольку без дополнительной обработки пористая структура древесных материалов впитывает влагу из воздуха либо при погружении в воду.
Гидрофобные вязкие вещества в расплавленном виде способны закрывать поверхностные поры материала, что становится препятствием для проникновения влаги вовнутрь. Такими веществам являются церезин, парафин, дистиллятный гач. В древесную массу они вводятся как щелочные эмульсии, разбавленные горячей водой. Осаждение гидрофобных веществ на древесных волокнах осуществляется посредством водных растворов сернокислого алюминия или серной кислоты.
В качестве упрочняющей добавки применяется феноло-формальдегидная смола, применяемая и для склеивания. Ее присутствие в составе увеличивает прочность ДСП при наличии в составе плит древесины лиственных пород более 30% либо при содержании волокон, более коротких, чем требуется.
На любом этапе производства ДСП требуется оборудование, соответствующее выполняемому процессу, среди которого выделяется основное и дополнительное.
Основное оборудование
К основному оборудованию по производству ДСП относится технологическое оборудование, устанавливаемое в главных цехах предприятия по изготовлению ДСП: подготовительном цехе, цехе основном и шлифовальном цехе.
Цех подготовки производства оснащается дробительной установкой и стружечным станком. Для оснащения основного цеха требуются термические прессы, охладители веерного типа, а также станки для обрезки в автоматическом режиме краев изделия по заданным длине и ширине. Шлифовальный цех оборудуется шлифовальными станками.
Все необходимые показатели ширины и мощности обработки определяются отдельно для каждой партии изделий, от выбранных показателей зависит конечная сортность изготовленных ДСП-листов.
Дополнительное оборудование
Оборудованием второстепенной важности считаются вибросита и транспортеры – роликовые, цепные, ленточные или спиральные. При укладке готовых листов в пачки используются подъемные столы. Все производственные цеха оснащаются вентиляционными системами для избавления от технологической пыли, ее сбора и удаления.
Применение современных технологий, качественного оборудования и необходимых добавок при изготовлении ДСП позволяет производителю изготовить ДСП с повышенной огнестойкостью, влагоустойчивостью и высокой прочностью. В результате получается материал, чья стоимость намного ниже иных аналогов, что и делает ДСП столь востребованным в широком кругу покупателей.
www.lam-dsp.ru