Производство брикетов древесных – Топливные брикеты (евродрова) своими руками, оборудование для производства пеллет (древесных гранул) из опилок
изготовление своими руками, технология и варианты
Уголь и дрова всегда считались самыми востребованными типами топлива. Но сегодня они понемногу уступают место брикетам для отопления. Чтобы изготовить такие материалы, используют отходы промышленности. Вот почему, с экологической точки зрения, это наиболее предпочтительный вариант. Также он предоставляет немало выгод в плане экономии средств. Эти изделия доступны по минимальной стоимости, а энергоэффективность их находится на высоком уровне.
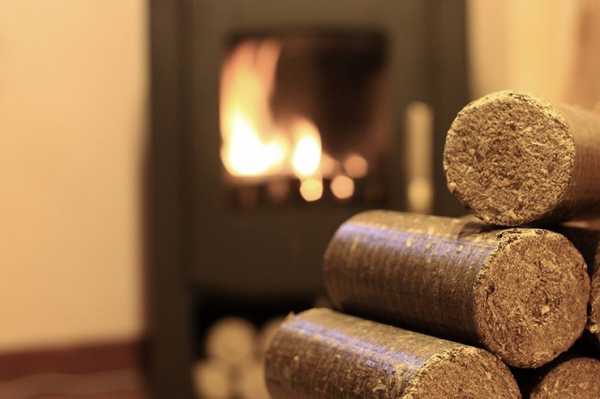
Деревянные изделия
У каждого типа такого топлива есть свои характерные особенности. В любом случае все они подходят для использования в домашних условиях. Древесные брикеты для отопления содержат различные отходы:
- стружку;
- опилки;
- сухостой.
Также это древесина, которая не прошла испытания в плане качества и не была допущена для использования в других отраслях производства.
Сырье необходимо нагреть до определенной температуры, прежде чем отправить материал под пресс. В процессе обработки отопительные брикеты будут вырабатывать вещество под названием лигнин. Именно он обеспечивает такие качества, как:
- высокая прочность;
- сохранность формы;
- простота хранения и транспортировки.
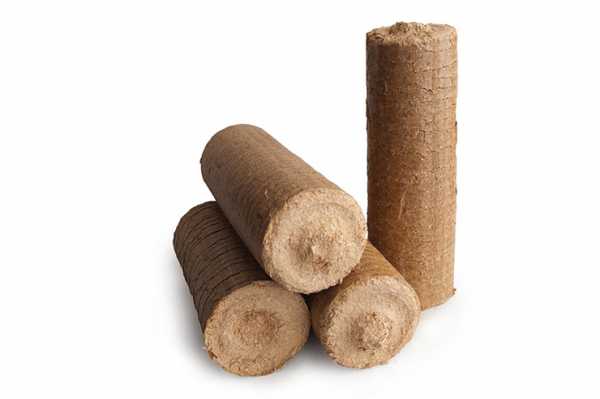
Плотность прессованных брикетов для отопления зависит от того, какой сорт древесины был использован. В готовом виде материал имеет влажность не более 10%.
У древесных вариантов плюсы следующие:
- не формируют искр при горении и выделяют относительно мало дыма;
- время горения составляет 4 ч;
- при сжигании отмечается постоянная температура внутри котла;
- угли, оставшиеся после сгорания, подходят для приготовления еды на открытом огне;
- изделия имеют правильную форму.
Такое топливо можно приобрести как в килограммах, так и кубометрах. Первый вариант выгоднее.
В этом видео вы узнаете, как делают брикеты:
Каменноугольные брикеты
Эти изделия получают из каменного угля. Отсев измельчают, после чего перемешивают со специальным связывающим компонентом. После прессования под давлением формируются угольные брикеты для отопления. Они не дымят и не источают угарный газ. В обычных котлах эти изделия могут гореть от 5 до 7 ч, если воздух поступает регулярно. Допускается применение такого топлива в бытовых условиях. Они компактные, способны поддерживать постоянное температурные отметки, хранятся долго. После сгорания образуется не более 28% золы.
Это оптимальный выбор для зимнего времени года. В этот период в бытовых газовых системах отмечается понижение давления. Для горения подходит любая температура. Главное условие для них — это приток воздуха.
Торфяные материалы
Торф для отопления сначала высушивают и нагревают. После этого отправляют его под пресс. Формируются аккуратные кубики темного цвета. Если отмечается постоянное поступление воздуха, такие брикеты могут поддерживать комфортные температуры в помещении на протяжении 10 ч. Это очень удобно для ночного времени суток.
Производство такого материала можно назвать безотходным, так как помимо самих брикетов, можно использовать золу, остающуюся после их сгорания. Это универсальное удобрение под растения.
Эти изделия отличаются универсальностью применения и подходят для любых печей. Теплоотдача составляет 5500 кКал на кг. Примеси содержатся в минимальном количестве. Сами брикеты доступны по демократичной цене. Это незаменимое средство для владельцев частных хозяйств. Вместе с тем торф считается легковоспламеняющимся материалом, потому надо размещать его на некотором расстоянии от источников огня. Опасность может представлять даже пыль, которая высыпалась из упаковки.
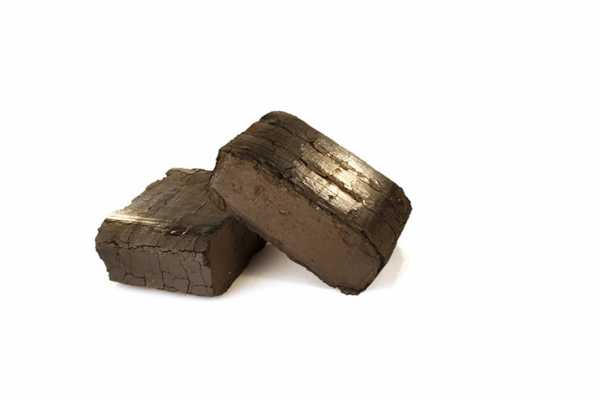
Торфяные брикеты небольших размеров — хороший вариант для растапливания печи. Если требуется нагревать воду, достаточно закладывать новые изделия через равные промежутки времени.
Примечательно, что уровень влажности брикетов по сравнению с дровами значительно меньше. Это важно, так как покупая влажный товар, человек фактически переплачивают за воду. Если речь идет о свежих дровах, то указанный показатель может достигать у них более 50%. Это говорит о том, что половина купленного материала просто испарится. По уровню теплоотдачи один кубический метр древесных топливных брикетов равен 6 кубометрам обычных дров.
Применение лузги
Для создания топливных брикетов допустимо использовать даже такие материалы, которые, казалось бы, уже ни на что не годны. Отходы овса, шелуха гречихи, лузга подсолнечника — всё это применяется для производства прессованного топлива. Такие изделия имеют повышенную теплоотдачу и минимальное время возгорания.
Лузга для прессования имеет влажность не более 8%. Вредные примеси в таких изделиях отсутствуют, а сами они доступны по цене. Брикеты горят продолжительное время. Они сделаны таким образом, что их удобно хранить и перевозить с места на место.
Критерии выбора
Прессованные материалы отличаются эффективностью. Об этом свидетельствует сравнение их характеристик с традиционными типами топлива. Выбирая между самими брикетами, надо учитывать их свойства. Если хочется меньше уделять внимания закладыванию топлива, то подойдут каменноугольные изделия.
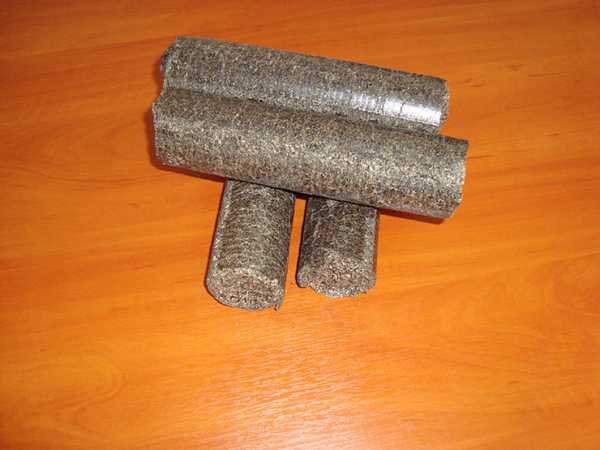
Желая получить золу для удобрения, рекомендовано останавливать свой выбор на брикетах из шелухи или древесины. Они же — самые дешевые по цене. Но лучше всего закупить по несколько пакетов каждого вида и сравнить, каким пользоваться удобнее. Такой подход позволяет выявить точную продолжительность горения, прочность изделий, объем выделяемого тепла.
Изготовление своими руками
Жители китайских деревень самостоятельно изготавливают угольные брикеты. Они берут резиновые тазы и замешивают липкую смесь. Из неё они формируют кубики, используя пресс на длинной ручке. После придания необходимых форм, материалы высушиваются на солнце. Как только они будут готовы, их кладут в печь-таганку и поджигают.
Можно взять опилки и измельченную газетную бумагу. Это сырье надо будет хорошо перемешать. Для этого лучше всего подходит дрель со специальной насадкой. Далее получившуюся массу необходимо положить в форму, утрамбовать и накрыть крышкой. Вслед за этим производят прессование специальным оборудованием и сушат на солнце.
Брикеты из опилок можно использовать для отопления складских, производственных, жилых помещений, подвижного состава железнодорожного транспорта. Также это популярный вариант у дачников и туристов, которые используют евродрова для розжига мангала, костра.
Предотвращение проблем
Если брикеты были изготовлены в соответствии с технологией, для возгорания им достаточно бумаги и нескольких прутиков. Они горят ровно, с одинаковой силой, выдавая большие объемы тепловой энергии при подаче воздуха. По этой же причине любители банных процедур, которые привыкли отапливать печи поленьями, быстро приводят их в негодность, сжигая брикеты.
По сравнению с кирпичиками из опилок, угольные брикеты горят ещё жарче. Они обеспечивают температуру в 900°C против 700°C, которые выдают опилки. Вот почему они не годятся для стальных печей. Последние предназначаются только для древесины.
В последнее время брикеты стали выпускать повсеместно. Появилось немало недобросовестных производителей. Они используют практически любые материалы, попадающиеся под руку, чтобы изготавливать дешёвое топливо. Неудивительно, что уже на этапе транспортировки эти материалы рассыпаются в пыль. Домовладельцам остается только удивляться, почему низкокачественное горючее даёт так мало тепла и оставляет внушительные объемы золы. Получается, что при покупке ни в коем случае нельзя искать самые дешёвые варианты, так как есть риск наткнуться на низкокачественное сырье.
‘; blockSettingArray[0][«setting_type»] = 1; blockSettingArray[0][«element»] = «h2»; blockSettingArray[0][«elementPosition»] = 1; blockSettingArray[0][«elementPlace»] = 1; blockSettingArray[4] = []; blockSettingArray[4][«minSymbols»] = 0; blockSettingArray[4][«minHeaders»] = 0; blockSettingArray[4][«text»] = ‘
‘; blockSettingArray[4][«setting_type»] = 5; blockSettingArray[9] = []; blockSettingArray[9][«minSymbols»] = 0; blockSettingArray[9][«minHeaders»] = 0; blockSettingArray[9][«text»] = ‘
‘; blockSettingArray[9][«setting_type»] = 6; blockSettingArray[9][«elementPlace»] = 90; var jsInputerLaunch = 15;
kaminguru.com
Производство топливных брикетов Технология, виды брикетов, использование
Топливными брикетами называют отходы деревообработки, продуктов переработки сельскохозяйственной деятельности, торфяных продуктов, подготовленными в специальные сжатые формы, имеющие вид брикетов для дальнейшего их применения как топливный материал. Производство топливных брикетов регионально распространено на территории России, а изделия вполне доступны гражданам.
Составляющие компоненты отходов из древесных материалов:
Отходы от деятельности сельского хозяйства:
- Злаковая шелуха;
- Кукурузные отходы;
- Помельченная солома;
- Уголь древесный;
- Торфяные продукты;
- Отходы подсолнуха.
Особенности использования брикетов в качестве топлива
Главное назначение спрессованных отходов — использование в качестве альтернативы жидким горючим материалам, включая другие твердые, для различных каминных сооружений, печей, котлов отопительных систем. Высокие показатели экологичности, возможность гореть, не выделяя много дыма, являются преимущественной особенностью топливных брикетов. Таким продуктом можно отапливать дома, палатки, бани, тепличные конструкции. Безвредность такого вида отапливания жилых зданий не принесет вреда для человека. Небольшие размеры, удобная форма позволяет легко перевозить, выгружать и загружать этот вид топливного материала. Свою популярность благодаря удобству использования, безопасности, экологичности топливные брикеты обрели во многих странах мира.
Типы опрессованных изделий
Выпуск топливных брикетов осуществляется в трех композициях:
1. Прямоугольные. По своей форме напоминает кирпич средних размеров. Производится путем давления гидравлического пресса до 400 бар.
2. Цилиндрические. Цилиндр выпускается с радиальным отверстием и без. Производится под влиянием давления гидравлического (ударно-механического) прессов до 600 бар.
3. Пини-кей. Брикеты с четырьмя или шестью гранями с радиальным отверстием. Их изготовление происходит под давлением шнекового пресса порядка 1100 бар и под термическим воздействием. По итогам термической обработки пини-кей — брикеты обретают черный или насыщенный коричневый цвет. Они обладают высокой устойчивостью к влажности, механическим влияниям, долговременности в процессе горения, высокой калорийностью.
Какой бы вид не имели топливные брикеты, это не влияет на их назначение. Стандартов и специальной технологии для производства этого вида топлива не существует. Достаточно индивидуальной рецептуры для использования тех или иных составляющих в исходном сырье, дальнейшая их обработка.
Технология производства топливных спрессованных брикетов
Основу всего процесса составляет воздействие пресса под давлением, иногда с применением термической обработки до 3500 °C, на отходы сельскохозяйственного производства, измельченных отходов деревообработки. Базовым соединительным компонентом в топливных брикетах считается лигнин. Это вещество имеет высокую концентрацию в отходах растительного происхождения.
При масштабном производстве топливных брикетов из сельскохозяйственных отходов, использование их в качестве соединительных компонентов весьма обоснованно. Высокие температуры при спрессовывании сырья в брикеты помогают оплавлять поверхность готовой продукции, обеспечивая ей необходимую прочность для удобства дальнейшей транспортировки. Соблюдение пропорций компонентов, контроль за показаниями влажности и плотности делают готовое изделие высокого качества функциональным и конкурентноспособным на рынке. Производство топливных брикетов даже из простых опилок доступно рядовому предпринимателю, не требует больших расходов.
Изготовление топливных брикетов намного легче технологически, чем производство тех же гранул.
Критерии прочности брикетов
Определяющим фактором в калорийности, стойкости к влаге и механическим воздействиям является показатель плотности. Качество брикета, его калорийность напрямую зависят от того, какую плотность он имеет.
Для примера: Если плотность брикета достигает 770 кг/см³, то его калорийность составит до 15 МДж/кг. Если плотность готового продукта определяется в 1400 кг/м³, то показатель калорийности соответствует 32 МДж/кг.
Уровень влаги в изначальном сырье тоже считается определяющим показателем в прочности будущего изделия. Их разделяют на оптимальные (допустимо до 10%) и критические (10-17%) нормы. Высокие механические качества топливных брикетов могут проявиться лишь при таких значениях.
Критический показатель содержания влаги в сырье способствует появлению в готовой продукции трещин, расколов, поверхность обретает нетоварный вид. Показатель от 10 до 17% определяется, исходя из верхнего предела нормы содержания влаги в отдельных видах исходного материала в 8%. Если у сырьевого материала для производства топливных брикетов влажность превышает порог в 15%, то их изготовление будет бессмысленным процессом.
Это обусловлено тем, что влага, возникающая от прессования измельченной сырьевой массы попросту разорвет готовое изделие под давлением изнутри. Если соблюдать все необходимые нормы, чтобы организовать производство брикетов, цена на них будет обоснованной, а бизнес рентабельным.
Виды топливных брикетов
Брикеты разделяют по двум направлениям:
1. По типу сырья, используемому в качестве исходного материала в готовом изделии (продукты отходов сельскохозяйственной деятельности, измельченная стружка и щепа, опилки без коры, лигнин, фанера, шлифовочная пыль, МДФ обрезки, измельченная шелуха, хлопковые отходы, сухой камыш и другие).
2. По методам опрессования и создания формы:
- Форма кирпича;
- Вид цилиндра;
- Экструдерные брикеты.
Оборудование для производства брикетов может быть различным. Именно механизмы и агрегаты обеспечивают выпуск заданной формы по итогам изготовления.
Топливный материал с формой кирпича
Изготавливается способом опрессовывания под воздействием гидравлического пресса и высокого давления. Изделия имеют вид параллелепипеда прямоугольной формы со скошенными уголками. Такой вид топлива имеет огромный спрос среди потребителей Белоруссии, Азербайджана, Узбекистана, Казахстана и в государствах Евросоюза. Доступность и практичность топливного материала определяет такую популярность у потребителей всего мира.
Брикеты, имеющие форму цилиндра
Технология изготовления заключается в воздействии ударно-механического пресса на исходный материал. На выходе получается готовая продукция с длинным стволом, что позволяет затем ее разрезать специальным инструментом на поленья или круги в форме шайбы. Получившаяся форма зависит от пожеланий заказчика и оборудования, которым располагает исполнитель. Также, наличие необходимого оборудования может осуществить практически любое нужное формирование брикета.
Готовому изделию можно придать вид круга, квадрата или восьмиугольника, брикет может подразумевать наличие или отсутствие радиальное отверстия. Страны Евросоюза предпочитают именно этот вид топливных брикетов. Получил максимальное признание и распространение. На российском рынке топливного сырья представлены, зачастую, кусковые изделия, которые предназначаются для использования в твердотопливных котлах.
Экструдерные топливные брикеты
Процесс изготовления осуществляется путем опрессовывании исходного материала шнеком под воздействием высокого давления и нагреванием сырья до 3500 °C. Высокая температура позволяет оплавлять поверхность изделия, чтобы повысить его прочность и упростить дальнейшее перемещение. Экструдерные брикеты обязательно имеют радиальное отверстие и обожженный верх. Закладка в печную топку или котел исходного сырья осуществляется вручную. Топливные экструдерные брикеты признаны странами Прибалтики и городами Российской Федерации.
incomeeasily.ru
Древесно-угольные брикеты: особенности производства | ЛПК Сибири
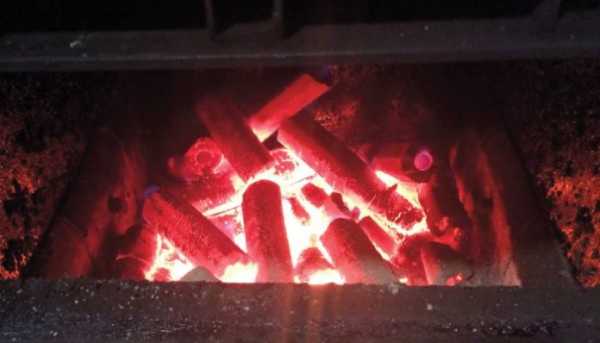
В предыдущих номерах «ЛПК Сибири» рассказывалось о линии по переработке отходов лесопиления в древесноугольные брикеты, построенной в п. Качуг Иркутской области. Кратко о технологии: опилки (микрощепа) подаются фронтальным погрузчиком на вибросито, просеиваются и шнековым конвеером подаются в кольцевой аэродинамический реактор сушки-подготовки сырья к прессованию. Из сушильного реактора опилки с влажностью 2–3% пневмотранспортом передаются к циклону, осаждаются и шнековым конвеером подаются в бункер-накопитель прессов-экструдеров. Два пресса экструдера производят 3 т/ч сполимеризованного брикета. Брикет одевается на специальные вагонетки и вилочным погрузчиком перевозится к печи карбонизации. В печь загружаются 4 вагонетки с брикетами. Печь имеет мощный тепловой регенератор и высокопроизводительный жаростойкий вентилятор, обеспечивающие термостабилизированный пиролиз брикетов. В печи карбонизации пиролизные газы не сжигаются, а сгорают в теплогенераторе сушильного реактора, тепловая энергия используется для сушки опилок, печь работает только за счет тепла экзотермической реакции термораспада древесины. Количество тепловой энергии от сжигания пиролизных газов меняется в зависимости от режимов работы печи. Оптимальные режимы работы печи карбонизации, когда в пиролизные газы почти не выделяется смола и газ горит синим пламенем.
Разным потребителям древесно-угольных брикетов нужны разные свойства. Для ресторанов BBQ важна высокая температура (больше 800 градусов) горения угля и длительное время горения, для частного применения угля в мангалах важен быстрый и легкий розжиг и высокая температура горения. При высокой температуре горения угля, инфракрасное излучение проникает на глубину 2–3 см в стейк, прогревая мясо изнутри, мясо быстро приготавливается, получается сочным и вкусным. В зимнее время легко жарить шашлыки на углях горящих с высокой температурой. Для получения угля с высокой температурой используется режим печи – термостабилизированный оксипиролиз, такой уголь горит с температурой 900 градусов.
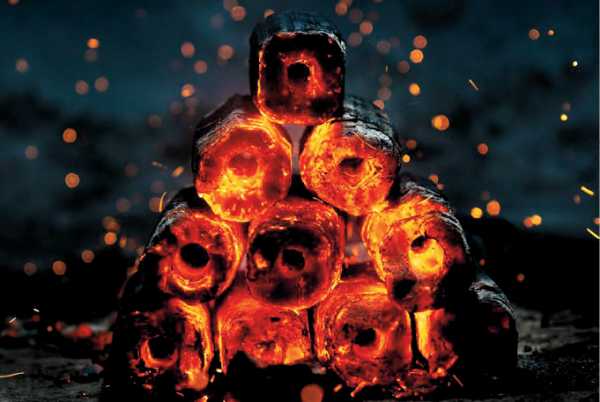
SiC – карбид кремния, является твердым, очень ценным промежуточным звеном в процессе получения кремния. Поэтому очень важна такая харатеристика, как реакционная способность угля, то есть какой процент газа SiO(газ) будет уловлен древесным углем. Высокой реакционной способностью обладает уголь с развитой поверхностью с микропорами, которые не закрыты смолой, такой уголь можно получить, используя термостабилизированный пиролиз.
В целях отопления удобно использовать древесно-угольный брикет, полученный при низкотемпературном термостабилизированном пиролизе, теплотворная способность такого угля составляет 8 кВт*час на килограм угля, а у древесных брикетов, только 5 кВт*часов на килограмм брикетов. В бункер котла Будерус загружается 60 кг древесноугольных брикетов, которые горят в течении суток, выдавая 20 кВт тепловой мощности. Твердотопливный котел длительного горения при использовании древесноугольных брикетов может служить альтернативой пеллетным котлам. Древесноугольные брикеты достаточно компактны, не занимают много места.
Журнал «ЛПК Сибири» №1 / 2018
3.3.2 Технологический процесс для изготовления топливных брикетов
Схема технологического процесса производства топливных брикетов представлена на рисунке 3.3.
Рисунок 3.3 – Схема технологического процесса производства топливных брикетов
Технологический процесс производства брикетов из древесных частиц включает стадии: подачи и сушки сырья; прессования методом экструзии и торцевания брикетов.
Процесс брикетирования топливных брикетов из древесной стружки включает операции подготовки и складирования стружки и штампования брикета в прессе. Топливный брикет делают со сквозным отверстием по длине диаметром 17 мм.
Масса брикета около 1 кг, размер 400х50х50 мм. Пакет размером 420x210x160 мм из 12 топливных брикетов (поленьев) заворачивают в упаковочную бумагу с напечатанными на ней правилами пользования и крест на крест перевязывают полипропиленовой лентой. Пакеты укладывают на поддон разового пользования форматом 1300х850 мм по принципу кирпичной кладки. Масса одного поддона с грузом около 960 кг. Топливные брикеты можно получать из коры, стружки, опилок, костры и др. При влажности измельченных отходов выше 10 % необходимо подсушивать их в сушильной камере, что на 25 % удорожает получение брикета. Брикеты реализуют населению и экспортируют.
3.4 Анализ оборудования для брикетирования
Для производства топливных брикетов используются специальные пресса-экструдеры. Решение — какой пресс приобрести и какие брикеты выпускать, должно основываться не только на стоимости оборудования, но и на четком понимании того, на какой рынок сбыта готовых брикетоввы ориентируетесь. Количество и вид сырья для брикетирования может также накладывает свои ограничения. Ниже представлены передовые марки прессов, имеющие лучшее соотношение цена\качество.
Пресс датской компании «C.F.Nielsen a/s», в отличие от гидравлических и шнековых прессов, может выпускать не только потребительские брикеты, предназначенные для частного рынка, но индустриальные для больших котельных (рисунок 3.4). Топливные брикеты различной формы и для различных применений. Брикет выдавливается поршнем через фильеру определенной формы в виде непрерывной «колбасы», затем нарезается в размер с помощью автоматической пилы или отламывается, в зависимости от предназначения.
Рисунок 3.4 – Пресс-экструдер компании «C.F.Nielsen a/s»
Кроме того, только эти пресса могут изготавливать брикеты круглой формы (в сечении), квадратной, восьмигранной, а также с центральным отверстием или без. Эта продукция пользуется высоким спросом, как на европейском рынке, так и на отечественном,
Пресс «C.F.Nielsen» используется при значительном количестве сырья (2-3 тыс.м3/мес), которое, в случае индустриальных брикетов, может быть не обязательно высокого качества. Технология наиболее дорогая из рассматриваемых, но, в то же время, инвестиции быстро окупаются.
Оборудование полностью автоматическое, имеется возможность эксплуатировать пресс в режиме авто-запуска и останова в зависимости наличия сырья в бункере. Коэффициент использования оборудования за длительный период составляет 0,9. Влажность сырья для брикетирования (стандарт для брикетирования) должна быть в диапазоне 8-12%. Материал должен быть не только высушен, но и равномерно измельчен.
Таблица – 3.1 Модели прессов «C.F.Nielsen»
Модель | Производительность | Размер брикета | Тип пресса |
BPH 60 | 80-120 кг/ч | 60, мм | Гидравлический |
BPH 70 | 100-150 кг/ч | 70, мм | Гидравлический |
BPH 2000 | 150-225 кг/ч | 50, мм | Механический |
BPH 3200 | 400-600 кг/ч | 60, мм | Механический |
BPH 4000 | 600-750 кг/ч | 60, мм | Механический |
BPH 5000 | 900-1200 кг/ч | 75, мм | Механический |
BPH 6500 | 1200-1800 кг/ч | 90, мм | Механический |
Гидравлический пресс «RUF» производится в Германии. Пресс выпускает известные во всем мире брикеты в форме «кирпичика».
Рисунок 3.5 – Пресс-экструдер компании «RUF»
Брикеты формируются гидравлическим способом поштучно, обычно 400- 600 штук в час (300-500 кг/ч), в зависимости от модели. Пресс RUF можно использовать при наличии не нуждающихся в сушке древесных отходов, которые получаются при обработке предварительно высушенного пиломатериала, например, отлично подходят опилки и стружка от четырехстороннего станка и т.п.
По сравнению с оригинальным RUF более предпочтителен с точки зрения цены пресс UMP BP420A, Прибалтика.
Пресс работает с производительностью до 500 кг в час и делает брикеты стандарта RUF 150 х 60 мм в сечении (немецкий стандарт DIN 51731). Оборудование отличается высоким качеством исполнения, пресса UMP хорошо зарекомендовали себя в Европе, России, США и др странах.
Рисунок 3.6 – Пресс-экструдер пресс UMP BP420A.
В сравнении с механическими прессами производства C.F.Nielsen, пресс «RUF» делает несколько менее плотный брикет и с небольшой производительностью, что обусловлено особенностями гидравлического способа прессования. В целом по стоимости и эксплуатационным характеристикам оборудование «RUF» сравнимо с ударно-механическими прессами «C.F.Nielsen» на небольшие мощности. На мощность 1000 кг/ч и выше имеются 2 модели — RUF-1100 и RUF-1500, однако размер выпускаемого этими прессами брикета чрезмерно увеличен (до 260 х 100 мм), что делает такой брикет неудобным для потребителя и продаются они плохо.
В целом если сравнивать один пресс «C.F.Nielsen» BP6500 мощностью до 1500 кг/ч на потребительских брикетах и связку из трех прессов RUF-600 для достижения той-же производительности, последняя обойдется дороже. Однако на мощности до 500 кг в час, модель RUF-400 или RUF-600, пожалуй, оптимальный выбор.
Использование пресса «RUF» особенно эффективно при наличии сухих опилок или стружки, поскольку пригодные для бесперебойной работы сушилки для опилок стоят дорого и их имеет смысл использовать при больших мощностях. Из преимуществ перед прессами других типов также следует отметить отсутствие охладителя, из пресса сразу выходит готовый к упаковке брикет, вследствие чего пресс может работать в совсем небольших помещениях.
В шнековом прессе брикеты выдавливаются через фильеру вращающимся шнеком. Данный вид оборудование представляет собой простую конструкцию, поэтому его изготовление с незначительными вариациями освоили несколько предприятий в Белоруссии, Украине и РФ. Также пресса подобного типа широко распространены в Китае, Малайзии и других странах региона. В Европе это оборудование не производится, так как не поддается автоматизации.
studfiles.net
Линия брикетирования 500 кг/ч (сырьё — опилки, стружка)
Линия предназначена для производства древесных брикетов из древесных отходов различной фракции и влажности. Основное сырье — опилки, стружка и мелкая щепа фракцией до 20 мм, срезки, баланс и т. п.
Сделать запрос ×Форма обратной связи
Пожалуйста, задайте любой интересующий Вас вопрос по оборудованию.
Вы также можете отправить сообщение на e-mail: [email protected]
Или сделать запрос по телефону (4822) 382-182 (многоканальный)
Линия для производства древесных брикетов производительностью 500 кг/ч (сырьё — опилки, стружка, щепа, срезки, горбыль, баланс)
Линия предназначена для производства древесных брикетов из древесных отходов различной фракции и влажности. Основное сырье — опилки, стружка и мелкая щепа фракцией до 20 мм, срезки, баланс и т. п.
Основные технические характеристики линии.
Наименование | Значение |
---|---|
Продукт линии | брикеты |
Производительность по готовому продукту | 500 кг/ч; |
Сырье | опилки, стружка, щепа фракцией до 20 мм |
Топливо для теплогенератора | щепа |
Влажность сырья | относительная — 55 % (абсолютная влажность 122 %) |
Потребность в сырье при его влажности 55 % | 1,2-1,5 т/ч |
Необходимая площадь для установки | 25 х 16 м |
Необходимая высота для установки | Для участка сушки, измельчения -7 м, для участка гранулирования — 10 м. |
Установленная электрическая мощность | 126 кВт |
Потребляемая электрическая мощность | 70% от установленной |
Непосредственно обслуживающий персонал | 2 человека в смену |
Линия брикетирования состоит из четырех участков: участок измельчения крупных отходов, участок сушки, участок вторичного измельчения, участок брикетирования.
Так как участок сушки сырья линии имеет максимальную производительность 2 т/ч, то производительность линии может быть увеличена добавлением оборудования участка брикетирования и участка вторичного измельчения.
Описание работы участка сушки
Горбыль, срезки, баланс подается в рубительную машину, откуда на транспортерах щепа идет в бункер сушильного барабана и в бункер теплогенератора.
Мелкофракционное сырье подается в бункер сушильного барабана и в бункер теплогенератора.
В теплогенераторе топливо, сгорая, образует сушильный агент, который подается в сушильный барабан. В сушилке сырье высыхает до влажности 8-10 % и удаляется из нее циклоном пневмотранспорта со встроенным вентилятором.
В циклоне пневмотранспорта высушенное сырье отделяется от отработанного сушильного агента и через шлюзовый питатель подается на потребителя.
Описание участка вторичного измельчения
Участок вторичного измельчения построен на базе двух молотковых дробилок АВМ-57. Производительность каждой дробилки не менее 1 т/ч.
Описание брикетирующего пресса
Электрическая система — управляет гидравлической частью пресса. Есть три электрических двигателя: первый 30 кВт, он вращает большой гидравлический насос, второй 1,1 кВт — вращает маленький гидравлический насос охлаждения, третий 1,5 кВт — вращает редуктор шнека подачи опилок. Работой двигателей и гидравлических клапанов через магнитные пускатели управляет микропроцессор с модулем расширения. Он взаимодействует с усилителем полупроводника и вторым микропроцессором, который управляет работой аналогового датчика давления.
Гидравлическая система — управляет работой гидравлических цилиндров. Есть три гидравлических цилиндра: первый — большой, он используется, чтобы сжать опилки, второй — вертикальный, используется, чтобы уплотнить опилки из подачи, третий — формы, он используется, чтобы переместить форму брикета. Их работа зависит от гидравлических насосов управляемых электрической схемой через гидравлические клапаны.
Подача опилок — выполняется бункером подачи опилок, смонтированным на прессе. Попадающие в бункер опилки размешиваются и при помощи шнека подаются под поршень вертикального цилиндра. Управление электродвигателем привода редуктора внешнего шнека (устанавливает владелец) предусмотрено в схеме пресса и обеспечивает непрерывную подачу материала из внешней ёмкости до бункера пресса.
Управление — предназначены два типа управления, ручной и автоматический. Всё оборудование управления установлено в электрошкафе. Автоматическое управление — нормальная работа пресса без участия оператора. Ручное управление предназначено для наладки пресса, возвращать цилиндры в начальное положение в случае, если исчезает электричество или в случае несчастного случая, для управления прессом в течение обслуживания. Три контрольных лампы делают работу с прессом легче. Первая предупреждает о перегревании двигателей. Вторая о нехватке опилок в бункере и третья показывает засорение в масленых фильтрах.
Для перехода прессования с одного материала на другой (с опилок на бумагу, солому, костру или другие материалы) может потребоваться только коррекция из пульта управления, другого переоборудования не требуется.
Получаемый материал идеально подходит для использования в промышленных твердотопливных котлах большой мощности.
Порядок оплаты, срок поставки, гарантийное обслуживание
Срок изготовления 45-65 рабочих дней.
Оплата оборудования поэтапная (30% — 30% — 30% — 10%).
Возможны лизинговые схемы.
Гарантийный срок эксплуатации 12 месяцев.
Послегарантийное обслуживание.
Описание решения в формате pdf
ekodrev-tver.ru
Технология производства топливных брикетов из древесных отходов
Экотехнологии сегодня осваиваются практически во всех сферах народного хозяйства. Главными принципами стали использование вторсырья, безопасное производство и минимизация ущерба окружающей среде. Одной из таких технологий является производство топливных брикетов из древесных отходов. В основе производства заложен метод прессования древесной муки, которую получают из отходов деревообрабатывающей промышленности.
Производимые брикеты отличаются повышенной плотностью и пониженной влажностью. По температуре горения их можно поставить на одно место с углем, но при этом продукты сгорания содержат меньше вредных веществ, чем натуральная древесина. К тому же топливо оставляет меньше золы, выделяет меньше смол и горит дольше.
Сырье
В качестве сырья в основном применяется древесина, лузга подсолнечника, шелуха риса и гречихи. Могут также использоваться добавки торфа, угольной пыли, соломы и тырсы. От состава брикета зависят такие качества как теплотворная способность, зольность и выделение сажи.
По этим качествам брикеты условно можно разделить по предназначению. Для каминов используется топливо с наименьшей зольностью и выделением сажи, чтобы не засорять дымоход. Твердотопливные котлы менее «капризны», поэтому баланс качеств смещается в пользу теплотворной способности. Для промышленных печей главным параметром является выделение температуры, а остальные качества отходят на второй план. Брикеты также могут использоваться для приготовления пищи на открытом огне, а здесь важна чистота продукта. Для этих целей используют евродрова из лиственной древесины.
Для того чтобы получить брикеты с заданными параметрами, технологи учитывают качества каждого элемента в отдельности и составляют необходимые пропорции.
- Древесина – калорийность 5043 ккал/кг, зольность 0,5-2,5%
- Лузга подсолнечника – 5151 ккал/кг, зольность 2,9-3,6%
- Солома – 4740 ккал/кг, зольность 4,8-7,3%
- Тырса – 4400 ккал/кг, зольность 0,7%
- Шелуха риса и гречихи – 3458 ккал/кг, зольность 20%
Добавки торфа и угольной пыли применяются только для промышленных печей.
Производство
Технология производства брикетов из опилок разделяется на 2 вида ‒ холодного и горячего прессования.
Холодное производство
Холодное прессование больше относится к частному производству и характеризуется малой производительностью, а также более низкой плотностью изделий. Зато такая технология изготовления топливных брикетов из опилок менее затратная и позволяет организовать производство для собственных нужд непосредственно на малом деревообрабатывающем предприятии.
Стружка не нуждается в дополнительном измельчении и просушке. Напротив, перед прессованием ее увлажняют до 40%, а в качестве связующего добавляют 2-3% крахмала. Прессование производится на ручном гидравлическом оборудовании, которое напоминает домкрат. Подготовленная стружка засыпается в цилиндр и сжимается поршнем. Затем брикет просушивается.
Горячее производство
Эта технология является промышленным способом и требует серьезного подхода. Для изготовления брикетов из опилок применяется целый ряд оборудования, включающий дробилки, сушки, измельчители и конвейерные ударные прессователи.
Подготовка сырья
Древесные отходы в составе с другими предусмотренными добавками загружаются в дробильные агрегаты, где дробятся до фракции не более 25 мм. Этот процесс предусмотрен для крупных древесных отходов, если же в качестве сырья применяется стружка, его можно пропустить.
Далее дробленая древесина попадает в барабанные сушилки, где высушивается горячим воздухом до состояния влажности 4%. Технологи отмечают, что этот процесс ‒ один из важных, поэтому влажность должна точно соответствовать параметрам.
После просушки сырье загружается в измельчитель, где доводится до консистенции древесной муки. В таком виде древесина готова к прессованию.
Прессование
Непрерывный процесс прессования производится на специальном оборудовании, выполняющем 20 ударов поршня в секунду. Сила сжатия, в зависимости от вида оборудования, варьирует от 300 до 1400 кгс/см².
При таком сильном сжатии материал нагревается до 200°C. При нагреве древесина выделяет смолы, которые служат естественным связующим, поэтому введение сторонних вяжущих не требуется. Сжатая древесная мука проходит через фильеру, которая формирует брикет.
Нарезка
Из прессовального агрегата брикет выходит сплошным и сразу нарезается. При нарезке автоматически брикеты отделяются и по транспортерной ленте отправляются на остывание и упаковку.
Если опустить брикет в воду, он тонет, что свидетельствует о большой плотности. Для сравнения плотность дуба ‒ 0,81 г/см³, в то время как плотность брикета ‒ 0,8-1,4 г/ см³.
Формат
Брикеты различаются по формату и плотности. Это зависит от оборудования, на котором их прессуют. В зависимости от фильеры – выходной насадки, разделяют 3 вида.
- Пини-кей – имеют четырех или шестигранный формат с продольным круглым отверстием в середине. Отверстие предусмотрено для улучшения качеств горения. Этот вид лидирует по плотности 1,4 г/см³.
- Нестро – имеет сплошное круглое сечение. Некоторые производители специально подрезают грань, чтобы упростить выкладку в камине и евродрова не скатывались. По плотности нестро идут на втором месте 1,15 г/см³.
- Руф – прямоугольный параллелепипед. Формат удобный для топки твердотопливных котлов и печей. Плотность ‒ 0,8 г/см³.
Все 3 вида не отличаются по качеству, составу и массовой теплотворности. Единственный их недостаток ‒ цена, хотя если сравнивать с дровами не в массовом эквиваленте, а в тепловом, то выходит одинаково.
qwizz.ru