Производство проволоки медной – Производство медной катанки и проволоки: технология и особенности
Медная катанка – как осуществляется производство + Фото, видео
Медная катанка, которая производится по ГОСТ 2010 года Р 53803, является незаменимым сырьем для изготовления разнообразных электротехнических и кабельно-проводниковых изделий.
1 Технологии выпуска катанки из меди
Традиционное производство проволоки предполагает использование методики волочения исходного сырья (медных катодов) через прокатные станы (представлены на фото), имеющие такую конструкцию, которая дает возможность при нагреве эффективно обжимать получаемые изделия со всех сторон. Такие станы оснащаются особыми механизмами под названием моталки. Они сразу же «собирают» катанку в кольца, а затем отправляют ее на участок охлаждения готового материала.
Охлаждение катанки производится либо ускоренными темпами – в этом случае применяются специальные вентиляторы, либо естественным способом – на открытом воздухе. В последние годы производство медной проволоки стало более эффективным и инновационным за счет использования современных линий непрерывного литья и прокатки (сокращенно – НЛП).
Рекомендуем ознакомиться
На них устанавливается в основном зарубежное оборудование:
- итальянское фирмы Проперци;
- немецкое СМС-Майер;
- английское Раутомед;
- американское Саутвайер;
- финское Оутокумпу.
Кроме того, на ряде НЛП монтируется и более дешевое китайское оборудование, которое позволяет снизить себестоимость выпускаемой продукции.
Именно на непрерывных линиях (смотрите фото таких агрегатов) в наши дни выпускается большая часть всего объема катанки, в том числе и проволоки самых популярных размеров 8, 6, 10 мм, которая идет на производство коллекторных проводов, кабельных изделий, шиноприводов, проводов для троллейбусных линий и так далее. За счет высокой технологичности оборудования НЛП готовые изделия обретают следующие важные для катанки свойства:
- высокая прочность в комбинации с высокой отличной пластичностью;
- малый показатель температурного сопротивления, обуславливающий постоянство механических свойств проволоки при разных температурах, в которых она эксплуатируется;
- небольшой показатель электросопротивления;
- простота обработки;
- длительный эксплуатационный потенциал изделий из катанки популярных диаметров (8 мм и других).
2 Особенности технологии непрерывного литья и прокатки
Производство медной проволоки, как было сказано, осуществляется из катодов по ГОСТ 546–2001 – МОК и МООК, а также из меди электротехнического назначения (ГОСТ 859) МО, МОО, МОБ и МООБ. В нашей стране такое сырье выпускается далее указанными предприятиями:
- УГМК – Уральский горно-металлургический комбинат – на нем, кстати, производится и непосредственно медная катанка;
- Норильский ГМК – самый крупный комбинат, производящий за год порядка полумиллиона тонн медных катодов;
- Новгородский и Кыштымский заводы, входящие в структуру Русской медной компании.
Более 60 процентов катодов, которые изготавливаются этими комбинатами, идут на производство медной проволоки для предприятий электротехнической отрасли.
На некоторых линиях НЛП, о которых мы говорим, применяются специальные газовые печи шахтной конструкции (некоторые особенности этих агрегатов хорошо видны на фото). Их достоинство заключается в том, что при выплавке медного сырья к основным материалам («чистым») допускается добавлять до трети отходов изделий кабельной промышленности. Подобная возможность снижает (и весьма существенно) себестоимость готовой продукции.
Качество изготовленной на непрерывных линиях катанки из меди определяется качеством катодов. И готовая продукция, и сырье должно иметь, согласно ГОСТ Р 53803, очень высокие характеристики по той причине, что часть изделий и материалов реализуется за границу. Поэтому, кстати сказать, указанный ГОСТ, принятый в 2010 году, по своим положениям полностью аналогичен строгим стандартам мирового рынка (DIN, ASTM, BS).
Готовая катанка бывает трех марок – КМб, КМ, КМор. Каждая из этих марок, кроме того, подразделяется на три класса (А, В и С). Проволока А-класса обычно выпускается из катодов МОК и МООК, что дает возможность производителям изготавливать продукцию (например, катанку 6 и 8 мм) с минимальным содержанием кислорода. Она пользуется популярностью из-за своей высокой пластичности.
При производстве медной проволоки других классов могут использоваться смеси МОК, МООК с М1К (до 25 %). Из подобного сырья получается катанка с относительным удлинением более 30 %. А для изделий класса А данный показатель должен составлять 35 и более процентов. Отдельно отметим, что проволока сечением 8 мм (ее вы видите на фото) обязана не иметь изъянов литья и не разрушаться при проведении специальной проверки, предполагающей ее десятикратное скручивание и раскручивание.
3 Частные случаи применения катанки из медных катодов
Проволока 8 мм используется для производства электропроводников и других изделий по методике много- и однониточного волочения. Отклонение диаметра готовой катанки не может быть более 0,3 мм, кислорода в ней содержится 210±20 ppm. Поставляется она, как правило, в бунтах, которые упаковываются в оболочку из полиэтилена, а затем размещаются на поддонах из дерева.
Для выпуска автопроводов и кабелей связи применяется катанка сечением от 0,15 до 0,4 мм. Указанные изделия изготавливают на многоходовых волочильных агрегатах, оснащенных специальным экструзионным и крутильным оборудованием. К проволоке малых диаметров предъявляют достаточно высокие требования в части их пластичности и прочности. Производственный опыт показывает, что линии НЛП любой комплектации обеспечивают выполнение этих требований.
Проволока сечением от 14 до 22 мм используется для выпуска проводов под маркировкой МФ (100, 80, 120) и коллекторных прямоугольных форм. К катанке, идущей на их производство, выдвигаются два требования. Во-первых, они должны быть износостойкими, во-вторых, иметь высокие прочностные характеристики. Этими свойствами обладает проволока С-класса и изделия, которые дополнительно легируются серебром, оловом, кадмием, некоторыми иными добавками.
Также катанка С-класса (а иногда и В) идеально годится для выпуска разнообразных кабелей с сечением проволоки 0,5 и более миллиметров. Например, при изготовлении кабелей, которые эксплуатируются предприятиями нефтяной промышленности.
4 Производство катанки из меди в отражательных печах
Сейчас в России начала развиваться технология изготовления проволоки в печах отражательного типа посредством плавки в них отходов от медных изделий. Пока что эта методика используется не очень активно, по ней производится не более 4–5 процентов от всей катанки, выпускаемой в РФ. Но перспективы у технологии, как говорят эксперты, имеются.
В качестве сырья для производства проволоки в отражательных печах используется медный лом не ниже третьего класса. Его обязательно требуется проверять на соответствие необходимому химсоставу, так как многие отходы медной продукции содержат чересчур много свинца и других нежелательных примесей. Именно по этой причине не рекомендуется применять отходы проволоки КМор.
Использование лома обеспечивает снижение расходов на производственный процесс (следовательно, гарантирует и уменьшение стоимости готовой продукции). При этом методика имеет ряд недостатков:
- Отражательные печи должны функционировать по циклическому принципу. Схема их работы следующая: загрузка сырья – 8 часов, процесс его окисления – 8 часов, восстановительная операция, рафинирование жидкой меди и ее разливка – еще 8 часов. Любому видно, что печь эффективно работает лишь треть времени от всего цикла, что неприемлемо для многих предприятий.
- Большой расход газовых смесей, требуемых для ведения процесса в отражательных устройствах, а также необходимость постоянного (и весьма строгого) контроля над степенью расплавления сырья во избежание затвердевших медных «комков».
- Качество катанки, полученной из медного лома, хуже, нежели изделий марок КМб и КМ. Она не подлежит сертификации по международным стандартам.
- Дополнительные затраты на построение специальных комплексов, очищающих отходящие газы, и упорных дымоходов.
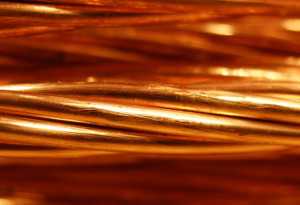
Надеемся, что наша статья, а также фото- и видеоматериалы к ней позволили вам создать максимально полную картину о современной ситуации в сфере производства медной проволоки.
tutmet.ru
Производство медной проволоки. Проволока медная круглая электротехническая 1 2мм. Диаметр медной проволоки. Медная проволока
Производство медной проволоки
Сегодня медная проволока широко применяется в энергетике, электротехнике, автомобильной промышленности, станкостроении и во многих других отраслях. Производство медной проволоки осуществляется на специализированных металлургических комбинатах.
Наиболее распространенным способом изготовления является волочение. Данная технология заключается в холодной деформации заготовки путем протягивания ее через отверстие требуемого размера. Например, данным методом изготавливается проволока медная 2 мм диаметром.
Медь достаточно пластична и легко поддается холодной деформации. Возможность получить постоянный диаметр без каверн и других дефектов особенно важна в производстве такого изделия, как проволока медная электротехническая. Для производства данного вида цветного проката применяются специальные установки – волочильные станы.
Основной рабочей деталью данных станков являются волоки, изготовленные из инструментальной стали повышенной прочности. Волоки имеют одно или несколько отверстий, называемых волочильными глазками. От величины рабочего отверстия зависит диаметр медной проволоки.
На первом этапе из катанки формируют толстую проволоку, если требуется тонкая медная проволока, то заготовку пропускают через несколько постепенно уменьшающихся в диаметре отверстий. Благодаря данной технологии изготавливается проволока медная 0.2 мм с высокой точностью.
Для уменьшения трения между заготовкой и стальной матрицей применяются различные защитные смазки, это позволяет получать качественную поверхность без задиров. Повышение температуры ведет к ухудшению качества изделия, поэтому волоки и заготовки постоянно охлаждаются водой, потоком воздуха или специальными составами. Например, так изготавливается проволока медная круглая электротехническая, к которой предъявляются повышенные требования.
Волочение является высокопроизводительным процессом – изготавливается ли медная проволока 0,5 мм диаметром или любой другой толщины – отходов не остается. Кроме изменения линейных размеров, процесс холодной деформации оказывает воздействие на механические параметры и внутреннюю структуру обрабатываемой детали.
Далее она подвергается дополнительной обработке для придания требуемых свойств. Например, в результате отжига получается медная мягкая проволока. Для электротехнических нужд медная проволока может подвергаться лужению или другим способам обработки.
Готовая продукция складируется или отправляется заказчику. Проволока медная 1 мм и меньшего диаметра поставляется на катушках. Если диаметр изделия больше, то его скручивают в бухты. По предварительной договоренности возможны различные варианты упаковки.
vmkmet.ru
Волочение проволоки – особенности технологии и оборудование
Волочение, посредством которого производят проволочную продукцию, является несложной технологической операцией. Между тем, чтобы в итоге выполнения такой процедуры получить качественное изделие, осуществлять ее необходимо в правильной последовательности и использовать для этого соответствующее оборудование.
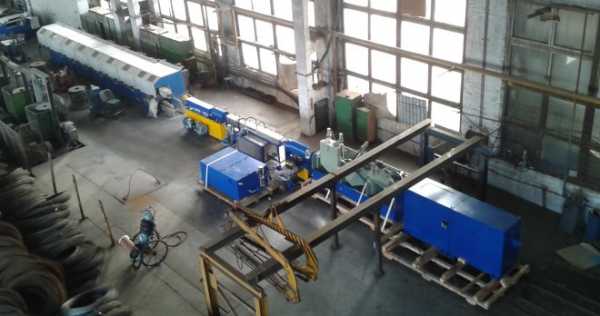
Линия производства проволоки по методу волочения
Основные этапы
Суть технологии, по которой выполняют волочение проволоки, заключается в том, что металлическую заготовку из стали, меди или алюминия протягивают через сужающееся отверстие – фильеру. Сам инструмент, в котором такое отверстие выполнено, называется волокой, его устанавливают на специальное оборудование для волочения проволоки. На то, какими диаметром, сечением и формой будет обладать готовое изделие, оказывают влияние параметры фильеры.
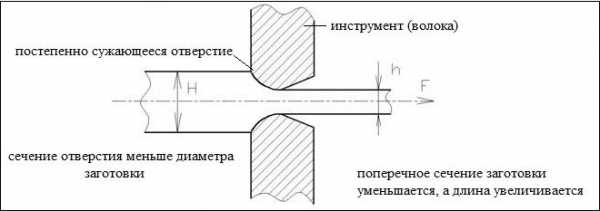
Принцип волочения металла
Выполнение волочения, если сравнивать такую технологическую операцию с прокаткой, позволяет получать изделия, отличающиеся более высокой чистотой поверхности и исключительной точностью геометрических параметров. Такими изделиями могут быть не только различные типы проволоки (электротехническая, используемая для сварки, вязочная и др.), но также фасонные профили, трубы и прутки разного диаметра. Полученные по такой технологии изделия отличаются и лучшими механическими характеристиками, так как в процессе волочения металла с его поверхностного слоя снимается наклеп. Что касается именно производства проволоки, то методом волочения можно получить изделия, диаметр которых находится в интервале от 1–2 микрон до 10 и даже более миллиметров.
Технология волочения сегодня уже хорошо отработана, для ее реализации используются современные модели волочильных станков, работающих без сбоев и позволяющих выполнять технологический процесс на скорости, доходящей до 60 метров готового изделия в секунду. Использование такого оборудования для волочения, кроме того, позволяет обеспечить значительную величину обжатия заготовки.
Технологическая схема волочения проволоки из нержавеющей стали
Изготовление проволоки по технологии волочения включает в себя несколько этапов.
- Исходная заготовка подвергается процедуре травления, для чего используется сернокислый раствор, нагретый до 50 градусов. С поверхности металла, прошедшего такую процедуру, легко снимается окалина, за счет чего увеличивается срок службы матриц волочильных станков.
- Чтобы увеличить пластичность обрабатываемой заготовки, а ее внутреннюю структуру довести до мелкозернистого состояния, выполняют предварительный отжиг металла.
- Остатки травильного раствора, который является достаточно агрессивным, нейтрализуют, после чего заготовку подвергают промывке.
- Чтобы конец заготовки можно было пропустить в фильеру, его заостряют, для чего может быть использован молот или ковочные валки.
- После завершения всех подготовительных операций заготовка пропускается через фильеры для волочения проволоки, где и формируются профиль и размеры готового изделия.
- Производство проволоки завершается выполнением отжига. После волочениия изделие также подвергают ряду дополнительных технологических операций – резке на отрезки требуемой длины, снятию концов, правке и др.
Особенности процедуры
Любой волочильщик проволоки знает такой недостаток волочения, как недостаточно высокая степень деформирования готового изделия. Объясняется это тем, что оно, выходя из зоны обработки волочильного станка, деформируется только до степени, ограниченной прочностью конца заготовки, к которому и прикладывается соответствующее усилие в процессе обработки.
В качестве исходного материала, который подвергают обработке на волочильных станках, служат металлические заготовки, полученные методом непрерывного литья, прессованием и катанием из углеродистых и легированных сталей, а также цветных сплавов. Наибольшую сложность процесс волочения представляет в том случае, если обработке подвергается стальной сплав. В таких случаях для качественного волочения необходимо довести микроструктуру металла до требуемого состояния. Чтобы получить оптимальную внутреннюю структуру стали, раньше использовали такую технологическую операцию, как патентирование. Заключался этот способ обработки в том, что сталь сначала нагревали до температуры аустенизации, а затем выдерживали в свинцовом или соляном расплаве, нагретом до температуры около 500°.
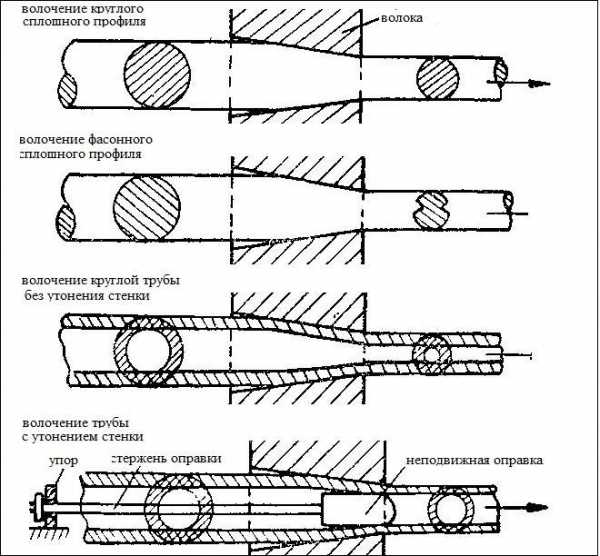
Методы волочения
Современный уровень развития металлургической промышленности, используемые в ней технологии и оборудование для получения металлов и сплавов позволяют не готовить металл к волочению таким сложным и трудоемким способом. Стальная заготовка, выходящая с прокатного стана современного металлургического предприятия, уже обладает внутренней структурой, оптимально подходящей для волочения.
Сама технология волочения и волочильное оборудование также совершенствовались на протяжении многих лет. В результате волочильщик проволоки сегодня имеет возможность применять современные волочильные устройства, позволяющие с минимальными трудозатратами гарантированно получать изделия высокого качества. Качество и точность обработки, выполняемой на таких волочильных специализированных станках, обеспечивается не только их оснащением современным рабочим инструментом, но и использованием при их работе комбинированной системы охлаждения, для которого применяются воздух и вода. Выходя с такого станка для волочения, готовое изделие обладает не только требуемым качеством и точностью геометрических параметров, но и оптимальной микроструктурой.
На каком оборудовании выполняется волочение металлов
Оборудование, которое волочильщик проволоки использует в своей профессиональной деятельности, называется станом. Обязательным элементом оснащения волочильной специализированной машины является «глазок» – волока. Диаметр волоки, разумеется, всегда должен быть меньше, чем размеры поперечного сечения протягиваемой через нее заготовки.
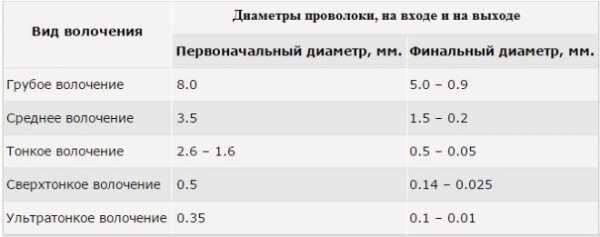
Соотношения первоначального и финального диаметров проволоки при различных типах волочения
На сегодняшний день производственные предприятия применяют волочильные специализированные станки двух основных типов, которые отличаются друг от друга конструкцией тянущего механизма. Так, различают:
- станки, в которых готовое изделие наматывается на барабан, чем и обеспечивается тянущее усилие;
- оборудование с прямолинейным движением готовой проволоки.
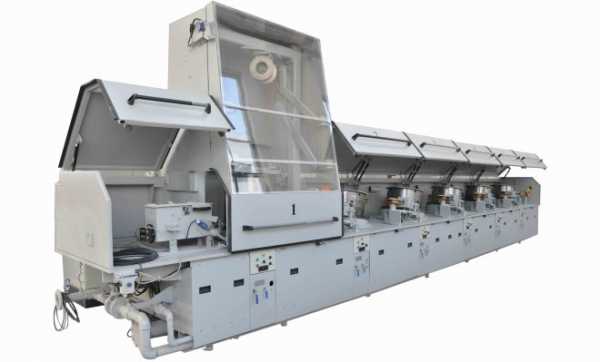
Прямоточный волочильный стан с программным управлением
На устройствах второго типа, в частности, выполняют волочение труб и других изделий, которые не требуют намотки на бухты. Именно проволоку, а также трубные изделия небольшого диаметра производят преимущественно на станках, оснащенных барабанным механизмом. Такие станки в зависимости от конструктивного исполнения могут быть:
- однократными;
- многократными, работающими со скольжением или без него, а также те, в которых используется принцип противонатяжения заготовок.
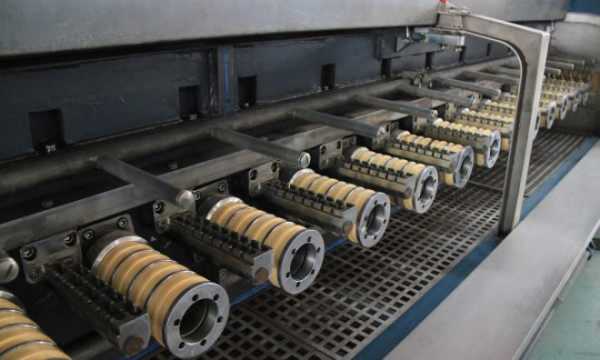
Многониточный волочильный стан обладает большей производительностью и выгоден на крупных предприятиях
Наиболее простой конструкцией отличается однократный станок для волочения. Манипулируя таким оборудованием, волочильщик проволоки выполняет ее протягивание за один проход. На волочильном устройстве многократного типа, которое работает по непрерывной схеме, формирование готового изделия осуществляется за 2–3 прохода. Крупные предприятия, производящие проволоку в промышленных масштабах, могут быть оснащены не одним десятком волочильных станков разной мощности, на которых изготавливается продукция различного назначения.
Основным рабочим органом любой волочильной машины, как уже говорилось выше, является фильера, для изготовления которой используют твердые металлокерамические сплавы – карбиды бора, молибдена, титана, термокорунд и др. Отличительными характеристиками таких материалов являются повышенная твердость, исключительная устойчивость к истиранию, а также невысокая вязкость. В отдельных случаях, когда необходимо изготовить очень тонкую проволоку из стали, фильера может быть изготовлена из технических алмазов.
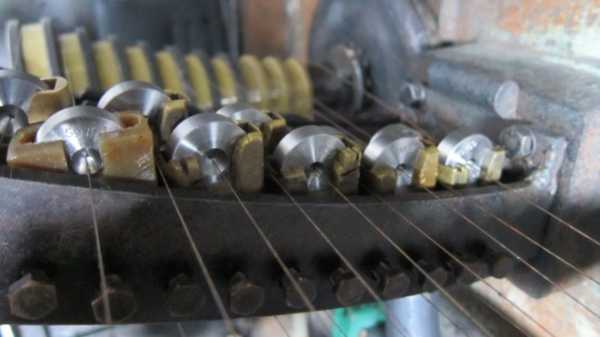
Фильеры волочильной машины
Фильера устанавливается в прочную и вязкую стальную обойму. Это так называемая волочильная доска. За счет своей пластичности такая обойма не оказывает значительного давления на фильеру и одновременно снижает растягивающие напряжения, которые в ней возникают.
На современных предприятиях волочение металлов часто проводят с использованием сборных волок, которые позволяют эффективно выполнять такой процесс даже в условиях повышенного гидродинамического трения. Кроме того, применение такого инструмента снижает расход электроэнергии и увеличивает производительность работы оборудования на 20–30%.
Подготовка металлических заготовок
Волочильщик проволоки, используя специализированное оборудование, только в том случае сможет добиться качественного конечного результата, если поверхность заготовки будет соответствующим образом подготовлена. Такая подготовка заключается в удалении окалины, для чего могут быть использованы следующие методы:
- механический;
- химический;
- электрохимический.
Более простым и экономически выгодным является механический способ очистки от окалины, который используют для заготовок из углеродистых сталей. При выполнении такой очистки заготовку просто гнут в разные стороны, а затем обрабатывают ее поверхность при помощи металлических щеток.
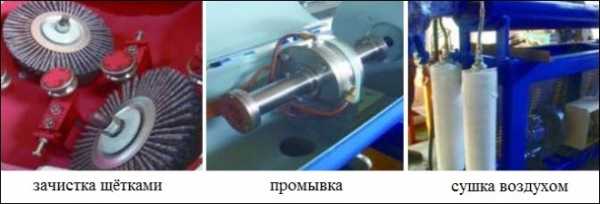
Технология работы окалиноснимателя
Более сложной и затратной является химическая очистка от окалины, для выполнения которой используют растворы соляной или серной кислоты. Специалист, выполняющий такую сложную и достаточно опасную операцию, должен быть хорошо подготовлен и строго соблюдать все правила безопасности работы с агрессивными растворами. Без химического способа очистки не обойтись, если проволоку необходимо сделать из заготовок, выполненных из нержавеющих и других типов высоколегированных сталей. Следует иметь в виду, что сразу после выполнения химической очистки поверхность заготовки следует тщательно промыть горячей, а затем холодной водой.
Электрохимический способ очистки от окалины основан на методе травления в электролитическом растворе. В зависимости от особенностей выполнения такой метод может быть анодным и катодным.
Волочение медной проволоки
Чтобы более подробно познакомиться с технологией волочения, можно рассмотреть ее на примере того, как делают медную проволоку. Заготовки для выполнения такой операции получают методом литья, после чего их сплавляют между собой и прокатывают. Чтобы волочение медной проволоки было выполнено максимально качественно, с поверхности заготовки необходимо удалить оксидную пленку, для чего ее обрабатывают раствором кислоты.
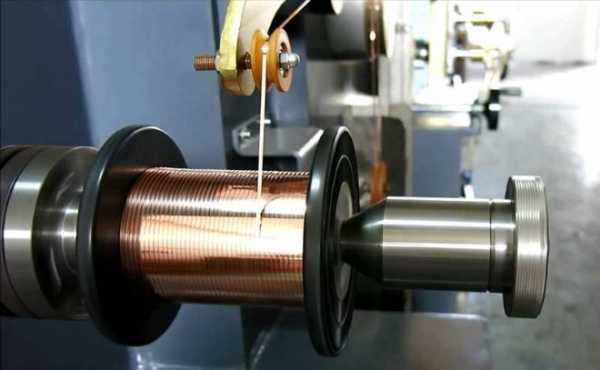
Намотка готовой проволоки на барабан
Сам процесс волочения мало чем отличается от производства сварочной проволоки (или любой другой). Проволочный стан в таком случае тянет заготовку, пропуская ее через фильерные отверстия определенного диаметра. Для изготовления медной проволоки очень небольшого диаметра (до 10 мкм) ее формирование может осуществляться в специальном смазочном составе (погружной метод). В качестве таких составов, в частности, могут использоваться:
- комплексные растворы;
- специальные эмульсии;
- комплексные вещества.
Использование таких составов, через которые проволока проходит в процессе своего формирования, позволяет получать изделия, наружная поверхность которых отличается максимальной чистотой.
Оценка статьи:
Загрузка…Поделиться с друзьями:
met-all.org
Производство медной катанки
ПРОИЗВОДСТВО МЕДНОЙ КАТАНКИ ВВЕДЕНО В ЭКСПЛУАТАЦИЮ В 1999 Г. ВСЯ ПРОДУКЦИЯ ВЫПУСКАЕТСЯ ПО ПРОГРЕССИВНОЙ ТЕХНОЛОГИИ МЕТОДОМ НЕПРЕРЫВНОГО ЛИТЬЯ И ПРОКАТКИ «CONTIROD» НА ОБОРУДОВАНИИ ПРОИЗВОДСТВА ГЕРМАНИИ И США.
Продукция производится в широком диапазоне: номинальный диаметр катанки медной 8 мм, диапазон размеров проволоки медной круглой электротехнической от 1,15 до 4,5 мм, жила токопроводящая медная выпускается диаметрами от 0,196 до 0,64 мм и сечениями от 0,5 до 16 кв. мм.
Постоянная работа по модернизации оборудования и оптимизации режимов производства, собственное высококачественное сырье, в виде катодов медных марки М00к (99,99% Cu), гарантируют высокое качество продукции, соответствующее всем требованиям потребителей.
Планомерно реализуя мероприятия по расширению номенклатуры выпускаемой продукции с высокой степенью готовности, в 2003 году предприятие запустило технологическую линию по производству медной проволоки производительностью 10 тыс. тонн в год, а в 2005-м — линию по производству медного неизолированного гибкого провода и токопроводящей медной жилы с проектной производительностью около 3 тыс. тонн в год.
Производство медной катанки, проволоки медной, провода гибкого неизолированного медного и жилы токопроводящей медной АО «Уралэлектромедь» сертифицирована компанией Lloyd ,s Register Quality Assurance на соответствие требованиям ISO 9001:2015.
За 2018 г. выпущено 170,5 тыс. тонн медной катанки. За 20 лет производства предприятие выпустило 4 млн тонн медной катанки.
Порошковая металлургия
Химико-металлургическое производство
Производство стальных конструкций и горячее цинкование
АО «Уралэлектромедь»
Свердловская область
АО «Уралэлектромедь»
Адрес: 624091, Россия, Свердловская область,
г. Верхняя Пышма, проспект Успенский, д. 1
Факс: +7 (34368) 4-26-26
E-mail: [email protected]
www.elem.ru
Этапы производства медной проволоки (41 фото) » Триникси
Давайте совершим с вами увлекательную фотопрогулку по Новгородскому металлургическому заводу, где при помощи передовых технологий осуществляется переработка вторичного медьсодержащего сырья для производства медной проволоки.Медную проволоку на «Новгородском металлургическом заводе» производят вторичного медьсодержащего сырья.
Процесс очень красивый и громкий. Сначала на завод привозят медный лом.
Лом любой, всё что содержит хоть сколько меди, привозят на переработку.
Этот лом, загружают вот в такую «пушку» и начинают нагревать, чтобы получился «бульон» из расплавленной меди.
Практически все инородные примеси выгорают.
Для создания сверхвысоких температур, в эту пушку, специальным «шприцем» впрыскивают кислород под давлением.
Температура повышается «бульон» начинает вариться.
Вид «пушки» сзади.
Включаются вытяжки и весь этот механизм, начинает вращаться.
Процесс сепарирования. Очень необычно, когда находишься рядом.
После разделения медного мусора на фракции, часть которая содержит медь,
вот такой машиной отправляют на очередную переплавку.
Находится рядом очень тяжело и жарко.
Поставил «горшок» в печь.
С обратной стороны печи. Это уже медь, но она содержит еще очень много примесей.
Расплавленный металл попадает на карусель, где разливается в формы.
При съёмке этих кадров у меня сгорел штатив =)
Пока карусель прокручивается на один оборот, медный сплав успевает застыть.
Один из цехов.
Застывшие заготовки, манипулятор помещает в ванну с водой для охлаждения.
Когда заготовка близко к воде, вода начинает закипать.
После всех этих процессов, получаются вот такие заготовки. Как видим, примесей еще много.
Из заготовок формируют блоки и отправляют в цех где находятся огромные электролизные ванны.
Технологические краны позволяют организовать кассетную загрузку электродов в автоматическом режиме.
Для обработки электродов установлены три автоматизированные линии: машина подготовки анодов,
машина сдирки и машина промывки анодных остатков.
Процесс электролиза ведётся при постоянной циркуляции электролита в электролизных ванных,
в связи с этим в цехе создана система подготовки электролита, приготовления и дозирования реагентов, фильтрации растворов.
После выгрузки ванны очищаются от донного шлама, из которого затем извлекаются золото, серебро, селен, теллур.
Выгрузка кассет.
После ванн, пластины с чистой медью, сортируют и укладывают в брикеты —
роботы манипуляторы в полностью автоматическом режиме для того, чтобы опять отправить на переплавку!
Готовое сырьё.
В этом цеху, уже чистую медь превращают в жидкое состояние для вытяжки из неё проволоки.
Процесс очень красивый.
Поддерживающая газовая горелка.
Из расплавленного состава, получается вот такая заготовка, которой нужно придать определённую форму.
Прокатка.
Срезают всё лишнее.
Охлаждают до определенной температуры и
опять нагревают, но уже вытягивая проволоку нужного диаметра.
Отсюда
trinixy.ru
Медная проволока ММ | «Медник Консалтинг»
Медь считается по праву одним из самых ценных и широко используемых человеком металлов. Обеспечивает высокую проводимость электрического тока и тепловой энергии. По проводимости электрического тока и тепловой энергии уступает пальму первенства только серебру. Подходящий материал для проведения работ любого уровня сложности. Широко применяется в промышленном производстве. Один из лучших проводников электрического тока. Материал отличается высоким уровнем пластичности. Специалисты отмечают доступную цену и высокие эксплуатационные характеристики.
Медную проволоку можно с лёгкостью гнуть и резать. Использовать для производства электрической техники и приборов. Материал обладает высоким уровнем устойчивости к коррозии. Способен выдерживать высокие температуры. Активно применяется в быту и на различных производствах. Устойчива к воздействию высокой влажности и образованию на своей поверхности коррозии. Не содержит вредных для человека веществ. Длительный срок использования делает медную проволоку одним из самых распространённых материалов.
Где может использоваться медная проволока?
Представлено несколько марок материала. Отличаются между собой индивидуальные технологическими параметрами, составом и стоимостью. Традиционно в зависимости от уровня твёрдости делится на твердую и мягкую. Может применяться для создания электротехнической продукции. Создаются контактные провода, кабеля, провода, проволока для заклепок и разнообразные декоративные элементы.
Используется для изготовления мелких фиксирующих элементов, шпилек и фурнитуры. Нашла своё применение в судостроении и телекоммуникации. Применяют при создании трансформаторов и электродвигателей различной мощности. Материал обладает высоким уровнем пластичности. Прост и легок в использовании. Отличается высоким уровнем сопротивления и прочности. Рассчитана на продолжительную эксплуатацию. Может применяться в различного рода сплавах. Способна выдерживать продолжительное время критические температуры.
Преимущества:
- Длительный срок службы.
- Доступная стоимость.
- Устойчивость к коррозии.
- Широкая область для использования.
- Небольшой вес.
Особенности производства медной проволоки
Производство медной проволоки требует использования специального оборудования и качественного сырья. Преимущественно для создания используются сплавы М1 и М2. Намного реже М3. Различаются между собой химическим составом. Для отбора сырья обязательно выполняется отбор проб.
В качестве основного способа производства используется метод волочения. Заготовка протягивается на специальном оборудовании через отверстия различного диаметра. Выполняется холодная деформация заготовки. Можно создавать изделия различного диаметра.
Металл отличается высоким уровнем пластичности. Поддается холодной деформации. Особое внимание наша компания в процессе производства обращает внимание на его качественную составляющую. Происходит создания изделия без дефектов поверхности. Используются современные установки, обеспечивающие высокий уровень производительности. Оборудование проходит регулярное обслуживание, что даёт возможность для создания проволоки высокого качества в любом необходимом для клиента количестве. Выделяют следующие основные этапы производства:
1.Формирование заготовки с использованием медной катанки. С целью получения изделия небольшого диаметра выполняется пропускание заготовки через соответствующее оборудование. Технология даёт возможность получать диаметры с высокой точностью. В процессе производства обязательно применяются специальные смазки. Снижают уровень трения между заготовкой и стальными элементами оборудования. Обязательно выполняется охлаждение материала в процессе обработки. Для охлаждения может использоваться вода или воздух. Не стоит забывать, что повышение температуры от оптимальных величин отрицательно сказывается на качестве продукции.
2.На втором этапе медная проволока подвергается дальнейшей обработке. Нужно отметить, что производство является безотходным. Для создания продукции применяется весь материал полностью. Электротехнические виды проволоки подвергают лужению. Для придания дополнительной мягкости применяется обжиг материала.
В последующем готовый материал с диаметром меньше 1 мм помещается в катушки, а что выше в бухты.
Как купить медную проволоку?
Наша компания занимается производством медной проволоки. Применяется оригинальная технология и сырье высокого качества. Наши клиенты могут сделать заказ на любое количество материала. Предлагаем доступные цены и оперативное выполнение заказа. Оформить заявку можно по телефонам или электронной почте. Наши специалисты находятся на связи. Готовы ответить на интересующие покупателя вопросы. На сайте размещается полезная для покупателя информация.
Мы предлагаем:
- Доступные цены.
- Высокое качество от производителя.
- Выполнение заказа в кратчайшие сроки.
- Индивидуальный подход.
- Различные способы оплаты.
Мы открыты для взаимовыгодного сотрудничества и новых предложений. Предлагаем гибкие условия оплаты для постоянных заказчиков и при больших объёмах поставки продукции. Готовы рассматривать любые предложения.
mednic.ru
Технологический процесс изготовления проволоки из цветных металлов и сплавов :: Технология металлов
- ОБЩИЕ СВЕДЕНИЯ
Технологический процесс изготовления проволоки — это ряд последовательных операций (травление, термообработка, волочение и другие), при осуществлении которых происходит уменьшение сечения заготовки и достигаются необходимые свойства проволоки.
Качество изделия и экономические показатели производства проволоки зависят от технического уровня процесса. Важным условием снижения трудовых затрат в производстве проволоки является сокращение циклов. Это достигают путем волочения проволоки с максимально возможными суммарными обжатиями (табл. 1).
Таблица 1
Допустимые суммарные обжатия
Сплав или металл | Максимальное суммарное обжатие, % | Сплав или металл | Максимальное суммарное обжатие, % |
Медь M1 | 99,9 | Константан | 99 |
Л80 | 95—99 | Никель | 99 |
Л62 | 80—96 | Алюмель | 80-90 |
ЛС 59-1 | 40—50 | Хромель | 80—90 |
БрБ-2 | 35-85 | Монель-металл | 80-95 |
БрКМцЗ-1 | 80—90 | Алюминий | 99,9 |
БрОЦ4-3
| 80—99 | Цинк | 99,9 |
Манганин
| 99 | Титан (ВТ1) | 45-60 |
Они зависят главным образом от пластичности металла и диаметра обрабатываемой проволоки. Чем меньше диаметр, тем больше допустимое суммарное обжатие. Например, при волочении проволоки бериллиевой бронзы из катанки 7,2 мм в начале процесса до размера 4,5 мм допускаются обжатия между отжигами, равные 30—40%, а из заготовки диаметром 1,0—0,5 мм волочение ведется с суммарным обжатием 75—85%.
Важным фактором, определяющим технологию производства проволоки, является заготовка и способ ее получения. От диаметра заготовки, ее качества зависит трудоемкость производства и качество проволоки.
2. ЗАГОТОВКА ДЛЯ ПРОВОЛОКИ
Заготовку для изготовления проволоки получают следующими способами:
1. Прокаткой слитков на проволочно-прокатном стане до диаметра 6,5—19 мм. Этот способ является наиболее производительным и широко используется для получения заготовки из меди, медных сплавов, алюминия, никеля, никелевых и медно-никелевых сплавов, латуней (Л62, Л68, ЛА85-0,5), цинка, бронз (ОЦ4-3, КМЦ-3-1, ББ2), титана и титановых сплавов.
2. Горячим прессованием на гидравлических прессах. Этим способом можно получить заготовку диаметром 5,5—20 мм и выше с высоким качеством поверхности. Однако этот метод менее производителен, чем прокатка, и связан с получением значительных геометрических отходов — от 10 до 25%. В то же время при прокатке эти отходы составляют 2—4%. Прессованием получают заготовку из сплавов, сортовая прокатка которых затруднена, например латуни ЛС59-1, ЛС63-3 и др., а также при необходимости получения проволоки с высоким качеством поверхности и сложным профилем.
3. Разрезкой холоднокатаных дисков по спирали специальными ножницами на прямоугольную заготовку (например, размером 6×8 мм). Этот способ применяется для сплавов, не выдерживающих горячей деформации. К таким сплавам относится фосфористая бронза.
4. Металлокерамическим способом — путем спекания порошков в длинные прямоугольные заготовки и последующей ковки их на ротационно-ковочных машинах. Этот способ применяется для тугоплавких металлов (молибден, вольфрам и др.).
3. ИЗГОТОВЛЕНИЕ ПРОВОЛОКИ ИЗ МЕДИ
Заготовкой для волочения медной проволоки служит катанка диаметром 7,2—19 мм или прямоугольного сечения. Для изготовления проволоки сложного профиля применяется прессованная заготовка соответствующего профиля. Заготовку травят в 8—12%-ном водном растворе серной кислоты, подогретом до 40—50 °С. Волочение катанки диаметром 7,2 мм, предварительно сваренной встык, производят на машинах со скольжением типа ВМ-13 на размер 1,79—1,5 мм. Для смазки и охлаждения применяется мыльно-масляная эмульсия. Далее волочение ведут на 22-кратной машине на размер 0,38—0,2 мм, скорость волочения до 18 м/сек. Затем волочение на 18-кратных машинах на диаметры 0,15—0,05 мм. На последнем переделе волочения применяют алмазные волоки. Угол рабочего конуса волок 16—18°.
Проволоку диаметром 0,15—0,05 мм изготавливают без промежуточного отжига. При необходимости проводится безокислительный отжиг, как правило, на готовых размерах в конвейерных электропечах с водяным затвором или в шахтных электропечах без доступа воздуха.
На некоторых заводах кабельной промышленности эксплуатируются волочильные машины с совмещенным отжигом медной проволоки. Применение таких машин позволяет снизить трудоемкость изготовления проволоки и повысить степень автоматизации производства. В настоящее время работают над улучшением качества отжига проволоки на этих машинах.
4. ИЗГОТОВЛЕНИЕ ПРОВОЛОКИ ИЗ АЛЮМИНИЯ
Алюминиевую проволоку изготавливают из катаной заготовки диаметром 7—19 мм. При горячей прокатке алюминий покрывается очень тонким слоем окислов, влияние которого на процесс волочения незначителен, поэтому горячекатаную заготовку обычно не травят. Но при длительном хранении на металле образуется слой окислов, который рекомендуется стравливать. В этом случае производят травление в водном растворе, содержащем 8—12% H2SO4 .
Изготовление алюминиевой проволоки средних и тонких размеров проводится по следующей схеме.
Волочение катанки диаметром 7,2 мм на 1,8 мм осуществляется на многократных машинах без скольжения типа ВМА-10/450. Далее волочение на размер 0,47—0,59 мм проводится на 15 волочильных машинах со скольжением; скорость волочения до 18 м/сек.
На машинах без скольжения применяется густая смазка, на машинах со скольжением — мыльно-масляная эмульсия.
При многократном волочении алюминиевой проволоки в целях снижения обрывности принимают величину вытяжек на 5% ниже, чем для меди. Волоки применяются с углом рабочего конуса, равным 24—26°.
5. ИЗГОТОВЛЕНИЕ ПРОВОЛОКИ ИЗ ЦИНКА
Цинковая проволока изготавливается из цинка марок ЦО и Ц1. Заготовкой для волочения служит катанка диаметром 7,2 мм, ее протягивают на размер 3,7 мм на 6-кратной машине со скольжением типа 6/480. Смазкой служит мыльно-масляная эмульсия, приготовленная из пасты Ц4 с добавкой серного цвета. Далее волочение на машинах со скольжением типа 8/250, 10/250 с диаметра 3,7 мм на готовые размеры 1,5—2 мм. Смазка та же, что и для предыдущего передела волочения. При волочении цинковой проволоки особое внимание должно уделяться подготовке смазки и волок. Для снижения усилий на преодоление трения рекомендуется уменьшить площадь контактирования проволоки в очаге деформации, для чего угол рабочего конуса волоки увеличивают до 24—26°, а длину рабочего пояска уменьшают до 0,3 диаметра готовой проволоки.
Цинковую катанку обычно не подвергают травлению, так как тонкий слой окислов, покрывающий ее, не оказывает влияния на процесс волочения.
6. ИЗГОТОВЛЕНИЕ ПРОВОЛОКИ ИЗ ТИТАНА
Заготовкой для волочения проволоки из титана служит катанка диаметром 8 мм. Волочение ведут на однократных или многократных машинах без скольжения в твердосплавные металлокерамические волоки. Для смазки применяют сухой порошкообразный графит. Скорость волочения от 20 до 50 м/мин. Допустимые суммарные обжатия при волочении проволоки из титана марки ВТ1 — от 45 до 60%. После такой деформации проводится отжиг в электропечах при температуре 620—640°С, выдержка при данной температуре 20 мин.
Отожженные бухты проволоки погружают в соляноизвестковый раствор следующего состава: 100—150г/л гашеной извести (СаО) и 80—100 г/л поваренной соли (NaCl). Температура раствора 80—90 °С. После обработки в растворе бухты просушивают в токе теплого воздуха. Полученный на поверхности проволоки известковый слой способствует лучшему захвату сухого порошкообразного графита.
Готовую проволоку травят для снятия альфированного слоя. После травления проволоку подвергают вакуумному отжигу для повышения пластичности и снижения содержания водорода. Температура отжига 750— 800 °С, время выдержки 4—6 ч, охлаждение в печи до 250 °С. В печи поддерживается вакуум от 13,3 до 6,65 мн/м2 (от 1 · 10-4 до 5 10-5 мм рт. ст.).
По указанной технологии изготавливается проволока из титана марки BT1 диаметром от 1,2 до 7 мм. Волочение ведут в твердосплавные металлокерамические волоки с углом рабочего конуса 8—10°.
Проволоку из титановых сплавов изготавливают по этой же технологии, но с большим количеством промежуточных отжигов, так как допустимое суммарное обжатие при обработке сплавов снижается до 30—40%.
7. ИЗГОТОВЛЕНИЕ ПРОВОЛОКИ ИЗ НИКЕЛЯ И ЕГО СПЛАВОВ
Проволоку из никеля и его сплавов изготавливают из катаной заготовки. Поверхность катанки из никелевых сплавов и заготовка после отжига имеют весьма плотную окисную пленку, препятствующую процессу волочения, поэтому в производстве проволоки особое внимание уделяется подготовке поверхности. С этой целью применяется комбинированное щелочно-кислотное и кислотно-солевое травление, известково-солевое покрытие поверхности заготовки .
Волочение проволоки из никелевых и медно-никелевых сплавов, обладающих высокой твердостью и прочностью, связано с повышенным износом волок, поэтому в процессе производства этой проволоки вопросу стойкости волок также уделяется большое внимание. С этой целью повышается качество подготовки поверхности металла, подготовки волок и смазки, внедряется волочение проволоки в условиях жидкостного трения. В настоящее время волочение проволоки из никеля, кремнистого никеля, никеля марганцовистого, константана, хромеля на многократных машинах без скольжения ведется в так называемые сборные волоки , создающие условия жидкостного трения.
Проволоку из никеля и его сплавов отжигают в электропечах шахтного типа без доступа воздуха, а также в протяжных электропечах. Для получения светлой поверхности рекомендуется вести отжиг в среде генераторного газа, диссоциированного и неполностью сожженного аммиака, содержащего 5% водорода, или в чистом осушенном водороде. Отжиг термоэлектродной проволоки на готовых размерах ведется в окислительной среде для получения надежной окисной пленки, которая в значительной мере определяет свойства проволоки (стабильность т. э. д. с).
8. ИЗГОТОВЛЕНИЕ ПРОВОЛОКИ ИЗ ВОЛЬФРАМА
Заготовкой для вольфрамовой проволоки служат вольфрамовые штабики квадратного сечения 15X 15 мм, длиной около 0,5 м, полученные металлокерамическим способом.
Перед волочением штабики проковывают на ротационно-ковочных машинах на диаметр 2,5—3,0 мм. Кованую заготовку протягивают на диаметр 1 мм на цепных волочильных станах длиной до 30 м. Волочение горячее, для чего стан оборудован газовой печью. Перед задачей в волоку конец прутка заостряют путем нагрева до вишнево-красного цвета и погружения в коробку с сухим азотнокислым калием или натрием. Под действием высокой температуры соль растворяется и равномерно растворяет концы вольфрамовых прутков на длине 100—120 мм. Следует избегать попадания азотнокислого калия или натрия в канал волоки во избежание его порчи. После заострения с конца прутка смывают остатки азотнокислого калия или натрия водой и смазывают его коллоидно-графитовым препаратом марки B-1. Заостренный конец нагревают в печи и затягивают в волоку на длину до 200 мм. Затем конец прутка прогревают вместе с волокой, быстро устанавливают в волокодержатель и протягивают.
Волочение ведется на скорости 0,1—0,15 м/сек. Волоки твердосплавные с углом рабочего конуса 8—10 град. Перед волочением волоку нагревают до температуры 500 °С, а проволоку до 1000—850 °С в зависимости от диаметра (с уменьшением диаметра снижается температура).
Таким образом процесс повторяют 7—8 раз до диаметра 1 мм, после чего проволоку сворачивают в моток.
Далее волочение на размер 0,5—0,55 ведут на однократных волочильных машинах в 6 протяжек. С фигурки проволока проходит через смазочную коробку с коллоидно-графитовым препаратом марки В-1, разбавленным дистиллированной водой в соотношении 1:1, попадает в газовую печь, где нагревается до температуры 800—750 °С, протягивается в победитовую волоку со скоростью 0,16—0,20 м/сек и принимается на барабан диаметром 500 мм.
Волочение на более тонкие размеры проводится по этой же схеме с приемом проволоки на барабаны диаметром 200 мм или на катушки. Скорость волочения до 0,3—0,4 м/сек. Для смазки применяют препарат марки В-1, разбавленный дистиллированной водой в соотношении 1 : 2. Волочение проволоки диаметром 0,34—0,32 мм и ниже ведется в алмазные волоки типа Т, которые нагревают перед волочением до 400 °С.
9. ИЗГОТОВЛЕНИЕ ПРОВОЛОКИ ИЗ БЛАГОРОДНЫХ И РЕДКИХ МЕТАЛЛОВ
Для изготовления проволоки из серебра применяют катаную или прессованную заготовку диаметром 7—8 мм. Волочение заготовки ведут без промежуточного отжига до размера 0,26 мм по следующей схеме. До диаметра 3—3,5 мм применяют однократное волочение. В качестве смазки используют хозяйственное мыло. Волочение на этом переделе можно вести на многократных волочильных машинах со скольжением типа ВМ-13 или СМВ-П-9. Волочение до размера 1,2 мм ведут на 15-кратной машине со скольжением типа 15/250, затем на машине типа 22/200 до диаметра 0,26 мм. На этом размере проводится отжиг в камерной электропечи при температуре 250 °С, выдержка 30 мин.
Дальнейшее волочение на тончайшие размеры до 0,02 мм проводится на 18 волочильных машинах со скольжением без промежуточного отжига. На машинах со скольжением смазкой служит мыльная эмульсия. Волоки твердосплавные металлокерамические с углом рабочего конуса 16—18 град. Для тончайшего волочения применяют алмазные волоки типа М.
В процессе обработки серебряной проволоки заготовка и промежуточные размеры после отжига травлению не подвергаются. Особое внимание уделяется чистоте рабочего места, качеству поверхности проволоки, подготовке производства с целью исключения обрывности и потерь металла.
Для получения проволоки тончайших диаметров (до 0,001 мм) из золота, платины и сплавов благородных металлов применяют волочение в медной рубашке, для чего пруток из благородных металлов или сплавов диаметром до 2 мм закладывают в .медную трубку диаметром 10 мм и с толщиной стенки 4 мм. Такую биметаллическую заготовку подвергают волочению до расчетного размера.
Так, для получения платиновой проволоки диаметром 0,01 мм волочение биметаллической заготовки ведут до диаметра 0,05 мм, для получения диаметра 0,005 мм — волочение до 0,025 мм, для диаметра 0,004 мм — волочение до 0,02 мм и т. д. Перед применением проволоки из благородных металлов с нее стравливают верхний слой металла (медную рубашку) раствором азотной кислоты в дистиллированной воде в соотношении 1:1.
Проволоку из бериллия и его сплавов диаметром от 1 до 0,12 мм производят волочением при температурах 420—450 °С. Обжатие за проход составляет 25%. В качестве смазки используют коллоидный графит в масле, а также смесь графита с дисульфидом молибдена. После каждого третьего прохода проволоку подвергают промежуточному отжигу при 800 °С в течение 6 ч 30 мин. Очистку поверхности проволоки производят ультразвуковым методом, так как травление снижает ее механические свойства.
10. ИЗГОТОВЛЕНИЕ ПРОВОЛОКИ ИЗ ЛАТУНЕЙ
Пластичность латуней ниже пластичности меди, поэтому в процессе обработки они быстрее нагартовываются и требуются промежуточные отжиги. По пластичности латуни можно условно разделить на три группы: 1) пластичные латуни, содержащие выше 78—80% меди. К ним относятся латуни Л80, ЛА85-0,5, Л90 и др.; 2) латуни средней пластичности, содержащие 60—70% меди. К ним можно отнести Л62, Л68; 3) латуни низкой пластичности. К ним относятся латуни марок ЛС59-1, ЛО60-1.
Изготовление проволоки толстых и средних размеров из латуней первой группы можно вести без промежуточного отжига; тонких размеров—с одним промежуточным отжигом и тончайших—с двумя отжигами.
Из латуней второй группы изготовление проволоки толстых размеров ведется без промежуточных отжигов; средних размеров— с одним и двумя промежуточными отжигами; тонких размеров — с тремя отжигами и тончайших — с четырьмя промежуточными отжигами.
Проволока из латуней третьей группы диаметром выше 5 мм производится из прессованной заготовки соответствующего диаметра без промежуточных отжигов. Проволоку диаметром ниже 5 мм изготовляют с промежуточными отжигами через каждые 30—40% обжатия.
С улучшением технологии подготовки поверхности металла перед волочением, повышением качества волочильного инструмента и смазки, а также улучшением качества заготовки суммарные обжатия при волочении латунной проволоки могут быть повышены и, следовательно, сокращено количество промежуточных отжигов.
В связи с большой градацией латунной проволоки по механическим свойствам термическая обработка в технологическом процессе ряда марок латунной проволоки (Л62, Л68 и др.) имеет важное значение, определяющее качество проволоки (механические свойства) и условия ее дальнейшей обработки. В процессе производства латунной проволоки особое внимание должно уделяться отжигу, с точки зрения его равномерности, и подготовке поверхности проволоки после отжига для дальнейшей обработки. Многократное волочение латунной проволоки средних и тонких диаметров ведется с частными обжатиями 17—18%. Желательно работать на меньших обжатиях, если позволяет машина.
Травление заготовки проволоки и промежуточных размеров после отжига проводится в 5—15%-ном водном растворе серной кислоты. Удовлетворительное качество травления латунной проволоки получается при условии погружения ее в раствор на приспособлении, обеспечивающем равномерное травление каждой бухты .
Для получения светлой поверхности проволоки после отжига в отдельных случая проводится травление в растворе, содержащем 2 ч. серной кислоты, 1 ч. азотной кислоты и 6 ч. воды с последующим пассивированием в водном растворе, содержащем 150 г/л хромпика и 400—450 г/л серной кислоты. После пассивирования производится нейтрализация в щелочном растворе. Латунная проволока отжигается в шахтных электропечах без доступа воздуха и в протяжных электропечах.
Наиболее равномерный отжиг получается в протяжных электропечах, а также в шахтных электропечах с принудительной циркуляцией воздуха. Хорошие результаты по равномерности отжига проволоки Л62 получены в шахтных электропечах колодцевого типа, оборудованных автоматическим регулированием температур по зонам с учетом тепловой инерции печи. При этом достигнуты узкие пределы механических свойств проволоки в одной партии: предел прочности от 400 до 460 Мн/м2 (40— 46 кгс/мм2), а в одном мотке колебания не превышают 30 Мн/м2 (3 кгс/мм2) (проволока была изготовлена из латуни марки Л62 с содержанием меди 62—63%).
Для волочения латунной проволоки применяют твердосплавные металлокерамические волоки с углом рабочего конуса 14— 18 град. Проволоку диаметром ниже 0,2 мм протягивают в алмазные волоки типа П.
Источник:
Хаяк Г.С. Волочение проволоки из цветных металлов и сплавов,Металлургия, 1967.
markmet.ru