Производство серной кислоты схема и описание – | — Pandia.ru
Статья по химии на тему: Описание схемы производства серной кислоты
Описание схемы производства серной кислоты
Процесс производства серной кислоты можно описать следующим образом.
Первым этапом является получение диоксида серы окислением (обжигом) серосодержащего сырья (необходимость в этой стадии отпадает при использовании в качестве сырья отходящих газов, так как в этом случае обжиг сульфидов является одной из стадий других технологических процессов).
Обжиговый газ 350-400оС поступает в полую промывную башню где охлаждается до 80оС орошающую башню 60-70% серной кислотой.
Получение обжигово газа. Для стабилизации процесса обжига в кипящем слое автоматически регулируется: концентрация SO2 в газе, количество воздуха, поступающего в печь, высота кипящего слоя и разрежение в печи. Постоянство объема сернистого газа и концентрации в нем SO2 на выходе из печи поддерживается путем автоматического регулирования подачи воздуха и колчедана в печи в зависимости от температуры отходящего газа. Количество воздуха, подаваемого в печь, регулируется при помощи регулятора, воздействующего на положение дроссельной заслонки в патрубке воздуходувки. Стабильность концентрации SO2 в газе перед электрофильтром обеспечивается автоматическим регулятором путем изменения оборотов питателя подающего колчедан в печь. Высота кипящего слоя в печи регулируется скоростью удаления огарка путем изменения регулятором скорости вращения разгрузочного шнека или степени открытия секторного затворена выгрузке огарка. Постоянное разрежение в верхней части печи поддерживается регулятором, который соответственно изменяет положение дроссельной заслонки перед вентилятором.
Обжиговый газ 350-400оС поступает в полую промывную башню где охлаждается до 80оС орошающую башню 60-70% серной кислотой.
Из полой промывной башни газ поступает на вторую промывную башню с насадкой где орошается 30% серной кислотой и охлаждается до 30 оС.
В промывных башнях газ освобождается от остатков пыли в каплях серной кислоты растворяются оксиды мышьяка и селена, которые присутствуют в обжиговом газе и являются ядом для катализатора в контактном аппарате. Туман серной кислоты с растворенными в нем оксидами мышьяка и серы осаждается в мокрых электрофильтрах.
Окончательная осушка обжигового газа после электрофильтра осуществляется в абсорбционном колоне с насадкой
концентрированной серной кислотой (93-95%).
Отчищенный сухой газ SO2 подается в теплообменник. где подогревается горячими газами из контактного аппарата.
Газ поступает в контактный аппарат и окисляется до SO3. Катализатором является пентооксид ванадия.
Горячий газ SO3 (450-480оС), выходящий из контактного аппарата поступает в теплообменник, отдает тепло свежему газу, далее поступает в холодильник и затем направляется на абсорбцию.
Абсорбция SO3 происходит в двух последовательно расположенных башнях. Первая походу башня орошается олеумом. Содержащем 18-20% SO3 (своб.) Вторая башня орошается концентрированной серной кислотой. Таким образом, в процессе производства образуется два продукта: олеум и концентрированная серная кислота.
Отработанные газы, содержащее остатки SO2 пропускают через щелочные абсорберы, которые орошаются аммиачной водой и в результате сульфит аммония.
1.3 Основное основного технологического оборудования
В процессе производства серной кислоты используют следующее технологическое оборудование:
1. Промывная башня.
2. Промывная башня с насадкой.
3. Мокрый фильтр.
4. Сушильная башня.
5. Турбокомпрессор.
6. Трубчатый теплообменник.
7. Контактный аппарат.
8. Трубчатый холодильник газа.
9. Абсорбционная башня.
10. Холодильник кислоты.
11. Сборник кислоты.
12. Центробежный насос.
13. Печь кипящего слоя.
14. Топка.
Основной фазой процесса производства серной кислоты является окисление двуокиси серы в контактном аппарате.
Описание конструкции основных узлов контактного аппарата /11/.
Рисунок 1 — Схема контактного отделения с двойным контактированием
На рисунке 1 представлена схема контактного отделения с двойным контактированием. Газ проходит теплообменники 1 и 2 и поступает на первый, а затем на второй и третий слой контактной массы аппарата 3. После третьего слоя газ подается в промежуточный абсорбер 8, из него – в теплообменники 5 и 4, а затем – в четвертый слой контактной массы. Охлажденный в теплообменнике 5 газ проходит абсорбер 6 и из него выводится в атмосферу. На рисунке 2 представлен современный контактный аппарат в пересчете на h3SO4 в зависимости от их размеров составляет от 50 до 1000 т/сут h3SO4. В аппарат загружают 200-300 л контактнй массы на 1т суточной выработки. Трубочные контактные аппараты применяются для окисления SO2 реже, чем полочные.
Рисунок 2 — Схема контактного аппарат с выносным теплообменником
Для окисления двуокиси серы повышенной концентрации рационально применять контактные аппараты с кипящими слоями катализатора. Для уменьшения содержания SO2 в отходящих газах широко применяется способ двойного контактирвания, сущность которого состоит в том, что окисление SO2 на катализаторе осуществляется в два этапа. На первом этапе степень превращения составляет около 0,90. Перед вторым этапом контактирования из газа выделяют трех-окись серы; в результате в оставшейся газовой смеси увеличивается соотношение O2:SO2, а это повышает равновесную степень превращения (хр). В результате в одном или двух слоях контактной массы второго этапа контактирования достигают степени превращения оставшейся двуокиси серы 0,995-0,997, а содержание SO2 в отходящих газах снижается до 0,003%. При двойном контактировании газа нагревается от 50 до 420-440оС два раза — перед первой и перед второй стадией контактирования, поэтому начинается концентрация двуокиси серы должна быть выше, чем при однократном контактировании в соответствии с уровнем адиабаты.
1.4 Параметры нормального технологического режима
В технологическом процессе производства серной кислоты имеются величины, характеризующие этот процесс, так называемые параметры процесса.
Совокупность значений всех параметров процесса называют /12/ технологическим режимом, а совокупность значений параметров, обеспечивающих решение целевой задачи – нормальным технологическим режимом.
Определены основные технологические параметры, подлежащие контролю с обоснованием их влияния на качество выпускаемого продукта и безопасность ведения процесса.
Контролю подлежат /2/ следующие параметры:
- Температура обжигово газа, подаваемого в первую промывную башню. При отклонении температуры от заданного диапазона: в меньшую сторону — реакция концентрации SO2 будет замедляться, отклонении в большую сторону – приведет к неоправданному расходу теплоты.
- Температура в 1, 2, 3, 4, 5 сборнике кислоты. При отклонении температуры от заданного диапазона: в меньшую сторону – концентрация SO2 будет замедляться, отклонении в большую сторону – приведет к неоправданному расходу теплоты.
- Температура обжигово газа при выходе из трубчатого теплообменника. При отклонении температуры от заданного диапазона: в меньшую сторону – концентрация SO2 до SO3 будет замедляться, отклонении в большую сторону – приведет к неоправданному расходу теплоты.
- Температура SO3 в холодильнике. После выхода из контактного аппарата SO3 должен охладится для продолжения реакции в абсорбционной башне.
- Давление газа, подаваемого в печь КС. Контроль давления природного газа необходим для правильного и эффективного ведения процесса горения. Колебания давления в газовой сети могут сделать процесс горения неустойчивым и привести к неполному сгоранию топлива, и как следствие произойдет неоправданный перерасход газового топлива. Полное сжигание газа важно не только для достижения высокого КПД печи, но и для получения безвредной смеси отходящих газов, не влияющих на здоровье людей.
- Давление воздуха, подаваемого в турбокомпрессор. Контроль давления воздуха необходим для правильного и эффективной работы компрессора. Отклонение давления воздуха от заданного диапазона приведет к малой эффективности его работы.
- Давление воздуха, подаваемого в холодильник. Контроль давления воздуха необходим для максимальной производительности холодильника.
- Расход воздуха, подаваемого в топку. Контроль расхода воздуха необходим для правильного и эффективного ведения процесса горения. При малых избытках воздуха в топочном пространстве будет происходить неполное сгорание топлива, и как следствие произойдет неоправданный перерасход газового топлива. Полное сжигание газа важно не только для достижения высокого КПД печи, но и для получения безвредной смеси отходящих газов, не влияющих на здоровье людей.
- Расход обжигово газа выходящего из печи КС. Количество обжигово газа должно быть постоянным так как отклонение от нормы может навредить производству в целом.
- Расход колчедана в топочную печь. При недостатке продукта — приведет к неоправданному расходу теплоты
- Уровень на 1, 2, 3, 4, 5 сборнике кислоты нужен для получения необходимого количества кислоты и дальнейшей ее концентрации. При недостатке или избытке кислоты не будет достигнута нужная концентрация.
- Концентрация на первой промывной башне. Кислота поступающая на орошение первой промывной башни должна быть нужной концентрации (75% серная кислота) в противном случаи реакция в целом будет проходить не правильно.
- Концентрация на второй промывной башне. Кислота поступающая на орошение второй промывной башни должна быть нужной концентрации (30% серная кислота) в противном случаи реакция в целом будет проходить не правильно.
- Концентрация в сушильной башне. Кислота поступающая на орошение сушильной башни должна быть нужной концентрации (98% серная кислота) в противном случаи реакция в целом будет проходить не правильно.
Таблица 1 — Технологические параметры, подлежащие контролю
серная кислота производство
2. Выбор и основание параметров контроля и управления
2.1 Выбор и основных параметров и средств контроля
2.1.1 Контроль температуры
Необходимо производить контроль температуры в промывной башне. В контактном аппарате необходимо контролировать температуру в 450ºС, так как /2/ только лишь при данной температуре происходит выгорание серы из колчедана. Так же при повышении данной температуры возможен выход из строя аппаратуры и приборов
2.1.2 Контроль расхода
Контроль топочного газа необходим так как его количество влияет на сгорание серы в печи КС. Для того чтобы процесс протекал правильно мы ставим датчик контроля расхода в трубопровод перед входом обжигового газа в печь КС так как именно он контролирует степень выгорания серы в печи.
2.1.3 Контроль концентрации
Необходим постоянный контроль концентрации серы в сборнике кислоты.
Необходимый уровень концентрации серы равен 30% от общей массы смеси.
Понижение или увеличение данного параметра приведёт к браку продукции уже на начальном её этапе производства.
Так же необходим контроль концентрации серной кислоты в промывной башне с насадкой равной, 75%, а так же концентрация сушильной башне, равной 92%.
2.1.4 Контроль уровня
Контроль уровня необходим в контейнере для сбора кислоты, если кислоты будет много она может вытечь наружу и тем самым навредить оборудованию и людям находящимся неподалеку.
2.2 Выбор и обоснование параметров управления и каналов воздействия
2.2.1 Управление температурой в ПКЦ
Необходимо регулировать температуру в ПКС, которая должна быть равна 450ºС. Повышение данной температуры ведёт к неполному выгоранию серной кислоты, а из-за недостаточно низкой температуры происходит брак продукции. Регулирование температуры на данном участке технологического процесса осуществляется посредством управления подачи топочного газа в ПКС – с помощью исполнительного механизма.
2.2.2 Управление концентрации в промывной башне
Необходим постоянный контроль концентрации серы в сборнике кислоты, которая должна быть равна 92%. Понижение или увеличение данного параметра приведёт к неправильному протекание реакции, что нарушит весь технологический процесс. Регулирование концентрации на данном участке технологического процесса осуществляется посредством управления подачи воды в сборник кислоты – с помощью исполнительного механизма.
2.2.3 Управление давлением в ПКС
Необходим постоянный контроль давления в ПКС, которое должно быть равным 250 кПа. Понижение или увеличение данного параметра приведёт к браку продукции уже на начальном её этапе производства. Регулирование давления на данном участке технологического процесса осуществляется посредством управления подачи атмосферного воздуха – с помощью исполнительного механизма.
2.2.4 Управление уровня в сборнике кислоты
Необходимо постоянно контролировать уровень в сборнике кислоты который не должен превышать 75 см. Понижение или увеличение этого параметра может не вредит технологическому процессу.
3. Описание АСР и технических средств автоматизации, выбор и обоснование законов регулирования
3.1 АСР температуры обжигового газа после – ПКС
Основными параметрами влияющими на процесс в ПКС являются: Fк- расход колчедана, Т- теплопотери, Тп- температура греющего пара, Тк- температура колчедана, Тв- температура воздуха, Рп- давление греющего пара.
Рисунок 1 — Структурная схема печи кипящего слоя как объекта управления
Температура обжигового газа на выходе из ПКС является основным контролируемым параметром. Для достижения необходимой температуры, в соответствии с нормальным технологическим режимом, регулируется расход топочного газа, используется при этом регулирование по отклонению, как самый эффективный способ в данном случае.
Рисунок 2 — Принципиальная схема регулирования температуры обжигово газа
Рисунок 3 — Структурная схема регулирования температуры обжигово газа
3.2 АСР концентрации в промывной башне
Основными параметрами влияющими на процесс в промывной башне:
Fоб.г- расход обжигового газа, Fк- расход кислоты, Qк- концентрация кислоты, Fв- расход воды, Q- концентрация примесей, Q SO2- концентрация SO2
Рисунок 4 — Структурная схема промывной башни
Концентрация серной кислоты подаваемая на орошение промывной башни является основным контролируемым параметром. Для достижения необходимой концентрации, в соответствии с нормальным технологическим режимом, регулируется подача воды в сборник кислоты.
Рисунок 5 — Принципиальная схема регулирования концентрации серной кислоты
Рисунок 6 — Структурная схема регулирования концентрации серной кислоты
3.3 АСР давления в ПКС
Основными параметрами влияющими на процесс в ПКС, являются:
Fк- расход колчедана, Т- температура в ПКЦ, Fв- температура воздуха, Fк- температура колчедана.
Рисунок 7 — Структурная схема ПКЦ
Расход воздуха подаваемого в ПКС является основным контролируемым параметром. Для достижения необходимого давления, в соответствии с нормальным технологическим режимом, регулируется расход воздуха, используется при этом регулирование по отклонению, как самый эффективный способ в данном случае.
Рисунок 8 — Принципиальная схема регулирования давления
Рисунок 9 — Структурная схема регулирования давления в ПКЦ
3.4 АСР уровня в сборнике кислоты
Основными параметрами влияющими на процесс в сборнике кислоты являются: Fк- расход колчедана, Т- температура в ПКЦ, Fв- температура воздуха, Fк- температура колчедана.
Рисунок 10 — Структурная схема сборника уровня
Расход воды подаваемой в сборник кислоты является основным контролируемым параметром. Для достижения необходимого уровня, в соответствии с нормальным технологическим режимом, регулируется расход воды, используется при этом регулирование по отклонению, как самый эффективный способ в данном случае.
Рисунок 11 — Принципиальная схема регулирования уровня
Рисунок 12 — Структурная схема регулирования уровня
nsportal.ru
Тема №9: Производство серной кислоты.
Дайте характеристику серной кислоты. Укажите облась применения.
Среди минеральных кисло, производимых химической промышленностью, серная кислота по объему производства и потребления занимаетпервое место. Ее мировое производство составляет в настоящее время ~ 150 млн. т в год. Объясняется это тем, что серная кислота — одна из самых сильных и самая дешевая из всех кислот. Серная кислота не дымит, в концентрированном виде не разрушает черные металлы, в широком диапазоне температур (от – 40 ÷ — 200 С) находится в жидком состоянии.
Область
применения серной кислоты чрезвычайно
обширны. Существенная ее часть используется
как полупродукт в различных отраслях
химической промышленности, прежде
всего, для получения минеральных
удобрений, минеральные пигменты,
минеральные кислоты HF,
H
Составьте химические функциональные схемы производства серной кислоты контактным способом из серы, серного колчедана и из отходов цветной металлургии.
Как влияет выбор сырья для производства серной кислоты на технологическую схему процесса? Каковы основные различия в технологических схемах получения серной кислоты из серы и из колчедана?
Исходным реагентами для получения серной кислоты могут быть элементарная сера и серосодержащие соединения, из которых можно получить либо серу, либо диоксид серы. Такими соединениями являются сульфиды железа, сульфиды цветных металлов (меди, цинка и др.), сероводород и ряд других сернистых соединений.
Традиционно основными источниками сырья является элементарная сера и железный (серный) колчедан. Значительное место (15%) в сырьевом балансе занимают отходные газы цветной металлургии, содержащие диоксид серы.
Дайте характеристику реакции сжигания серы в промышленных печах.
Сжигание серы проводят в промышленности следующим образом. Серу предварительно расплавляют (для этого можно использовать водяной пар). Так как температура плавления сыры сравнительно низка, то путем отстаивания и последующей фильтрации от серы легко отделить механические примеси, не перешедшие в жидкую фазу, и получить исходное сырье достаточной степени чистоты. Для сжигания расплавленной серы используют два типа речей – форсуночные и циклонные. В них необходимо предусмотреть распыленние жидкой серы для ее быстрого испарения и обеспечения надежного контакта с воздухом во всех частях аппарата.
Каковы основные элементы конструкции печей для сжигания серы? Как в них обеспечивается необходимый технологический режим?
Циклонная печь для сжигания серы. Она состоит из двух горизонтальных цилиндров – форкамеры и двух камер дожигания. Печь имеет воздушный короб (рубашка) для снижения температуры наружной обшивки печи и предупреждения утечки диоксида серы. В форкамере через две группы сопел тангенциально подают воздух; через форсунку механического типа также тангенциально поступает расплавленная сера. Образующийся при сжигании жидкой серы обжигание газа всесте с парами серы поступает через пережимное кольцо из форкамеры в первую камеру досжигателя, в которой также расположены воздушные сопла и форсунки для подачи серы. Из первой камеры дожигания газ через пережимное кольцо поступает во вторую камеру дожигания, где сгорают остатки серы.
Обоснуйте выбор технологического режима сжигания серы.
При
адиабатическом сжигании серы температура
обжига для реакционной смеси
стехиометрического состава состоит ~
15000С.
В практических условиях возможности
повышения температуры в печи ограничены
тем, что выше 1300
Обоснуйте выбор температурного режима, состава обжигового газа, конструкции реакторов на стадии контактного окисления диоксида серы в производстве серной кислоты. Дайте характеристику используемых катализаторов.
Реакция (׀׀׀) окисления диоксида серы характеризуется очень высоким значением энеггии активации и поэтому практическое ее осуществление возможно лишь в присуствии катализатора.
В промышленности основным катализатором окисления SO2 является катализатор на основе оксида ванадия V2O5. Каталитическую активность в этой реакции проявляет и другие соединения, прежде всего – платина. Однако платиновые катализаторы чрезвычайно чувствительны даже к следам мышьяка, селена, хлора и других примесей и поэтому постепенно были вытеснены ванадиевым катализатором.
Каталитическую активность проявляется также оксид железа (׀׀׀) Fe2O3, однако лишь в области высоких температур. Каталитической активностью Fe2O3, входящие в состав огарка, можно объяснить наличие в обжигомом газе, выходящим из печей КС, небольших количеств триоксида серы.
Реакция
окисления диоксида серы – обратимая
экзотермическая. Тепловой эффект реакции
составляет при 500
В чем состоят преимущества схемы двойного контактирования и двойной абсорбции (ДКДА) перед схемами с одинарным контактированием? За счет чего достигается увеличение степени превращения диоксида серы при проведении процесса по схеме ДКДА?
Почему оптимальным абсорбентом для поглощения триоксида серы является серная кислота концентрацией 98,3%?
Последней
стадией процесса производства серной
кислоты контактным способом является
абсорбция триоксида серы из газовой
смеси и превращение его в серную кислоту.
При выборе абсорбента и условий проведения
стадии абсорбции необходимо обеспечивать
почти 100%-ное извлечение SO
Туман плохо улавливается в обычной абсорбционной аппаратуре и в основном уносится с отходящими газами в атмосферу, при этом загрезняется ОС и возростают потери серной кислоты.
Высказанные
соображения позволяют решить вопрос о
выборе абсорбента. Диаграмма фазового
равновесия пар – жидкость для системы
показывает, что оптимальным абсорбентом
является 98,3%-ная серная кислота
(техническая название – моногидрат),
соответствующая азеотропному составу.
Действительно, над этой кислотой
практически нет ни паров воды, ни паров
SO
Почему в схемах получения серной кислоты, где одним из продуктов является олеум, после олеумного абсорбера расположен моногидратный абсорбер?
Использование в качестве поглотителя серной кислоты с концентрацией ниже 98,3% может привести к образованию сернокислотного тумана, а над 100%-ной серной кислотой или олеумом в паровой фазе значительно равновесное парциальное давление SO3, поэтому он будет абсорбироваться не полностью. Однако если в качестве одного из продуктов процесса необходимо получить олеум, можно совместить абсорбцию олеумом (1–й абсорбер) и абсорбцию 98,3%-ной кислотой (2–й абсорбер).
Над 98,3%-ной кислотой, может быть значительное парциальное давление паров самой кислоты. Что также снижает степень абсорбции SO3. Но при температурах ниже 1000С равновесное давление паров H2SO4 очень мало и может быть достигнута практически 100% — ная степень абсорбции (степень абсорбции SO3 в моногидратном обсорбире при различных температурах: при 600С, 800С, 1000С,1200С).
Дайте характеристику реакциям обжига колчедана. Обоснуйте выбор температурного режима обжига колчедана.
кДж/моль , или 7117 кДж/кг. Фактически она протекает через несколько последовательно — паралельных стадий. Сначала происходит медленная эндотермическая реакция термического разложения дисульфата железа, а затем начинаются сильно энзотермичаские реакции горения паров серы и окисления сульфата железа FeS.
Часть кислорода воздуха расходуется в реакции на окисление железа и поэтому максимально возможная концентрация диоксида серы в обжиговом газе в этом случае ниже, чем при сжигании серы. В воздухе на каждый моль кислорода приходится 79/21 молей азота и инертов.
Температура процесса должна быть достаточно большой для обеспечения высокой скорости реакции. При низких температурах (ниже 5000С) не сможет протекать эндотермическая реакция термического разложения дисульфита железа. С другой стороны, проведение процесса при очень высоких температурах может вызвать нежелательный физический процесс спекания частиц горящего материала, приводящий к увеличению их размеров. Следствием этого явится увеличение времени полного превращения твердых частиц и понижение производительности печи. Температура спекания колеблется в зависимости от состава (сорта) колчедана в пределах от 8000С до 9000С.
В чем преимущества печей кипящего слоя (КС) при осуществлении процесса обжига колчедана перед другими типами печей? Как в этих печах регулируют температуру обжига?
В настоящее время в сернокислотной промышленности для обжига колчндана применяют в основном печи КС с псевдоожиженным слоем твердого материала. В псевдоожиженном слое обеспечиваются высокая скорость диффузионных и теплообменных процессов (подвод кислорода к поверхности колчедана, отвод диоксида серы в газовый поток, отвод теплоты от поверхности сырья к газовому потоку). Отсуствие тормозящего влияния массо — и теплообменных процессов позволяет проводить обжиг колчедана с высокой скоростью. Печи КС характеризуются максимальной интенсивностью в сравнении с другими конструкциями, применяемами для обжига колчедана. К недостаткам печей КС можно отнести высркую зыпыленность обжигового газа.
Проведение процесса в адиабатическом режиме привела бы к созданию более высоких температур. Поэтому часть теплоты обжига приходится отводить внутри печи. Удобнее всего это сделать в печах КС, так как в псевдоожиженном слое твердого материала достаточно велик коэффициент теплоотдачи от колчедана к поверхности охлаждающих элементов [~1000 кДж/(м2·ч·К)] и в «кипящий» слой можно ввести змеевики охлаждения.
Какие задачи решаются на стадиях сухой и мокрой очистки обжигового газа? Каковы физико-химические основы стадии очистки? Оборудование для очистки.
Подготовка обжигового газа к контактному окислению заключается в удалении из него примесей, присутствие которых может вызвать затруднения при проведении последующих стадий, а также нагрев (или охлаждение) до температуры, при которой начинается контактное окисление.
Обжиговый газ, полученный сжиганием колчедана в печах КС, содержит большое количество огарковой пыли, соединения мышьяка, селена и фтора. Очистка обжигового газа начинается в печном отделении, где в циклонах и сухих электрофильтрах осаждают огарковую пыль. Содержание пыли в газе после сухой очистки не должнопревышать 50 мг/м3. Последующая очистка осуществляется на стадии мокрой очистки в промывном отделении. При этом из обжигового газа удаляют остатка пыли, каталитические яды (соединения мышьяка и фтора), а также соединения селена.
Наличие в газе пыли, даже в небольших количествах оставшейся после сухой очистки, может привести к повышению гидравлического сопротивления аппаратов и отравлению катализатора соединениями As, адсорбированными на огарковой пыли. Отравление катализатора произойдет и в том случае, если в газовой фазе останутся оксиды мышьяка As2O3 или соединения фтора (HF и SiF4). Диоксид селена SeO2 не являются ядом для катализатора контактного окисления, однако он представляет собой ценное исходное сырье для промышленности полупроводников.
Мокрая очистка обжигового газа заключается в промывке его разбавленной серной кислотой. При этом происходит ряд физических процессов: конденсация, абсорбция и т. п.
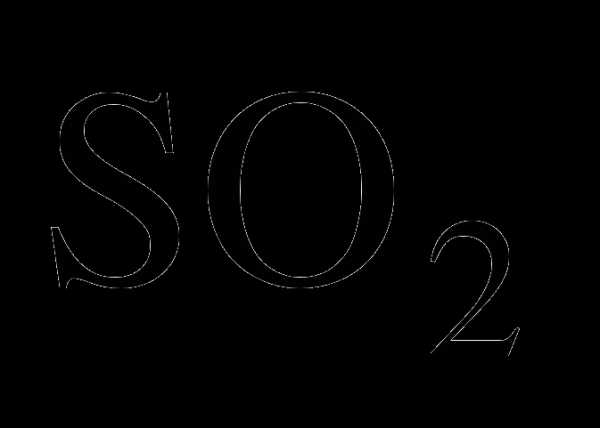
Какие можно предложить методы снижения содержания в отходящих газах установок получения серной кислоты?
Каковы технико-экономические характеристики производства серной кислоты?
В чем состоит отличие технологической схемы производства серной кислоты на Бийском олеумном заводе от классических схем?
Охрана окружающей среды при производстве серной кислоты.
Увеличение единичной мощности агрегатов по производству серной кислоты и удобрений может привести к загрязнению ОС даже при сравнительно невысоких концентрациях вредных выбросов. Поэтому основной тенденцией в развитии технологических процессов является создание замкнутых малоотходных или безотходных схем, сокращение до минимума сброса вредных веществ в атмосферу и в сточные воды.
Для очистки от триоксида серы, а особенно от серной кислоты в форме аэрозоля (тумана) отходящие газы пропускают через брызгоуловители и специальные фильтры. При необходимости на выхлопе сернокислотной системы предусматривают электрофильтры. Сточные воды сернокислотного производства должны быть подвергнуты тщательной очистке от соединений мышьяка.
21
studfiles.net
Подборка по базе: 12.Внешние эффекты рынка и производство общественных товаров..do, Амино кислоты.doc, Химическая схема получения серной кислоты из колчедана включает , Продукты восстановления азотной кислоты.docx, малоотходное производство в птицеводстве.docx, Тема 23. Ароматические карбоновые кислоты.docx, Тема 23. Ароматические карбоновые кислоты.docx, СНиП РК 1.03-06-2002 Строительное производство. Организация стро, СН РК 1.03-00-2011 Строительное производство. Организация строит, СН РК 1.03-00-2011 Строительное производство. Организация строит. Московский государственный университет тонкой химической технологии им. М.В. Ломоносова. Курсовая Работа Кафедра Общей Химической Технологии Тема: Производство серной кислоты из серы. Преподаватель: Цыганков Владимир Николаевич Студент: Лыкошин Дмитрий Дмитриевич Группа ХТ-409 Москва 2013
Серная кислота — H2SO4 (мол. Масса 92,082) бесцветная маслянистая жидкость без запаха. Не дымит, в концентрированном виде не разрушает черные металлы, в то же время является одной из самых сильных кислот, в широком диапазоне температур (от -40…-20 до 260 – 336,5 ˚С) находится в жидком состоянии. Области применения серной кислоты чрезвычайно обширны. Существенная ее часть используется как полупродукт в различных отраслях химической промышленности, прежде всего для получения минеральных удобрений, а также солей, кислот, взрывчатых веществ. Серная кислота применяется и при производстве красителей, химических волокон, в металлургической, текстильной, пищевой промышленности и т.д. В технике серной кислотой называют безводную H2SO4 , ее водные растворы (смесь H2SO4 , H2O и H2SO4nH2O) и растворы триоксида серы в безводной H2SO4 – олеум ( смесь H2SO4 и соединений H2SO4nSO3 ). Безводная серная кислоты – тяжелая маслянистая бесцветная жидкость, смешивающаяся с водой и триоксидом серы в любом соотношении. Безводная 100%-ая серная кислота имеет сравнительно высокую температуру кристаллизации (10,7˚С).
Серная кислота и вода образуют азеотропную смесь: 98,3% H2SO4 и 1,7% H2O с максимальной температурой кипения (336,5 ˚С).
Исходными реагентами для получения серной кислоты могут быть элементарная сера и серосодержащие соединения, из которых можно получить либо серу, либо диоксид серы. Например, сульфиды железа, сульфиды цветных металлов (меди, цинка и др.), сероводород и ряд других сернистых соединений. Традиционно основные источники сырья – сера и железный (серный) колчедан. Значительное место в сырьевом балансе производства серной кислоты занимают отходящие газы цветной металлургии, содержащие диоксид серы. Производство серной кислоты включает в себя несколько этапов:
S+О2 = SO2
SO2 + 0,5O2 = SO2 (Процесс ведут на ванадиевом катализаторе при t = 420-550˚С)
SO3 + H2O H2SO4
SO3 + N2O3 + H2O H2SO4 + 2NO В промышленности в основном применяют контактный метод получения серной кислоты, позволяющий использовать аппараты с большей интенсивностью. Рассмотрим процесс получения серной кислоты контактным методом из двух видов сырья: серного (железного) колчедана и серы. Первой стадией процесса является окисление сырья с получением обжигового газа, содержащего диоксид серы. В зависимости от видов сырья протекают экзотермические химические реакции обжига: FeS2 + 11O2 2Fe2O3 + 8SO2 (I) При протекании реакции (I) помимо газообразного диоксида серы образуется твердый продукт Fe2O3, который может присутствовать в газовой фазе в виде пыли. Колчедан содержит различные примеси, в частности соединения мышьяка и фтора, которые в процессе обжига переходят в газовую фазу. Присутствие этих соединений может вызвать отравление катализатора. Поэтому реакционный газ после стадии обжига колчедана должен быть предварительно направлен на стадию подготовки к контактному окислению, на которой помимо очистки от каталитических ядов выделяются пары воды (осушение), а также получаются побочные продукты (Se и Te). Если обжиговый газ получают сжиганием серы, то отпадает необходимость очистки от примесей. Стадия подготовки будет включать в себя лишь осушку газа и утилизацию теплоты. На третьей стадии протекает обратимая экзотермическая химическая реакция контактного окисления диоксида серы: SO2 + 0,5O2 = SO3 (III) Последняя стадия процесса – абсорбция триоксида серы концентрированной серной кислотой или олеумом. В зависимости от комбинации этапов получения серной кислоты, существуют различные функциональные схемы:
H2SO4 (серная кислота) тяжёлая маслянистая жидкость без цвета и запаха, с кислым «медным» вкусом с температурой кипения 279,6°C, температурой кристаллизации 10,7°C и плотностью 1,8356 г/см3. Длины связей в молекуле S=O 0,143 нм, S—OH 0,154 нм, угол HOSOH 104°, OSO 119°. Кипит, образуя азеотропную смесь (98,3 % H2SO4 и 1,7 % H2О с температурой кипения 336,5оС). Серная кислота, отвечающая химически чистому, имеет состав (%): H2SO4 (не менее) – 93.6-95.6, остаток после прокаливания (не более) – 0.0006 (0.001), массовая доля хлоридов (не более) – 0.0002, нитратов (не более) – 0.00002 (0.00005), аммонийных солей (Nh5) (не более) – 0.0001, тяжелых металлов (Pb) (не более) – 0.0001, железа (Fe) (не более) – 0.00002 (0.00005), мышьяка (As) (не более) – 0.000001, селена (Se) (не более) – 0.0001, веществ восстанавливающих KMnO4 (не более) – 0.0002 (0.0003). (ГОСТ 4204 — 77). Смешивается с водой и SO3, во всех соотношениях. В водных растворах серная кислота практически полностью диссоциирует на H3О+, HSO3+, и 2НSO₄−. Образует гидраты H2SO4·nH2O, где n = 1, 2, 3, 4 и 6,5.
Рассмотрим стадии контактного метода получения серной кислоты:
При сжигании серы протекает необратимая экзотермическая реакция с выделением очень большого количества теплоты ∆H = -362.4 кДж/моль, или в пересчете на единицу массы 362,4/32 = 11,325 кДж/г = 11325 кДж/кг. Расплавленная жидкая сера, подаваемая на сжигание, испаряется (кипит) при температуре 444,6 ˚C; теплота испарения составляет 288 кДж/кг. Как видно из приведенных данных, теплоты реакции горения серы вполне достаточно для испарения исходного сырья, поэтому взаимодействие серы и кислорода происходит в газовой фазе (гомогенная реакция). При аддиабатическом сжигании серы температура обжига для реакционной смеси стехиометрического состава составит примерно 1500 ˚C. В практических условиях возможности повышения температуры в печи ограничены тем, что выше 1300 ˚C быстро разрушается футеровка печи и газоходов. Обычно при сжигании серы получают обжиговый газ, содержащий 13-14% SO2.
FeS2 + 11O2 2Fe2O3 + 8SO2 ∆H = -853,8 кДж/моль FeS2, или 7117 кДж/кг. Сначала происходит медленная эндотермическая реакция термического разложения дисульфида железа, а затем начинаются сильно экзотермические реакции горения паров серы и окисления сульфида железа FeS. Обычно воздух берется в избытке к стехиометрическому количеству, тогда концентрация SO2, в обжиговом газе будет тем меньше, чем больше коэффициент избытка. При низких температурах (ниже 500 ˚C) не сможет протекать эндотермическая реакция термического разложения дисульфида железа. Однако проведение обжига при очень высоких температурах может вызвать нежелательный физический процесс спекания частиц горящего металла, приводящий к увеличению их размеров. Температура спекания колеблется от 800 до 900 ˚C. Проведение процесса в адиабатическом режиме привело бы к разогреву до более высоких температур, поэтому часть теплоты обжига приходится отводить внутри печи. При производстве серной кислоты для обжига колчедана применяют, в основном, печи кипящего слоя с псевдоожиженным слоем твердого материала.
Обжиговый газ, полученный сжиганием колчедана в печах КС, содержит большое количество огарковой пыли, соединения мышьяка, селена и фтора. Очистка обжигового газа начинается в печном отделении, где в циклонах и сухих электрофильтрах осаждают огарковую пыль. Затем газ направляют на стадию мокрой очистки (в промывное отделение), где из обжигового газа удаляют остатки пыли, каталитические яды (соединения мышьяка и фтора), а также соединения селена.
SO2 + 0,5O2 = SO3 Данная реакция характеризуется очень высоким значением энергии активации и поэтому практическое ее осуществление возможно лишь в присутствии катализатора. В промышленности основным катализатором является ванадиевая контактная масса V2O5. Каталитическую активность проявляет также оксид железа (III) Fe2O3, однако лишь в области высоких температур. Реакция окисления диоксида серы – обратимая экзотермическая, поэтому температурный режим проведения реакции должен приближаться к линии оптимальных температур. При 500˚C тепловой эффект реакции ∆H = -94,23 кДж/моль. Скорость реакции и вид кинетического уравнения зависят от типа применяемого катализатора. В промышленности это в основном ванадиевые контактные массы БАВ, СВД, СВС, ИК, в составе которых примерно 8% V2O5, нанесенного на пористый носитель. Скорость реакции повышается с ростом концентрации кислорода, поэтому процесс в промышленности проводят при его избытке.
Для полного извлечения SO3, необходимо, чтобы его равновесное парциальное давление над растворителем было ничтожно малым, так как при этом будет велика движущая сила процесса абсорбции. Оптимальным абсорбентом является 98,3%-ная серная кислота, при температуре ниже 100 ˚C, (техническое название – моногидрат), соответствующая азеотропному составу.
Рис. 15-11. Технологическая схема производства серной кислоты из колчедана по методу ДКДА: /- печь; 2- система гидроудаления огарка; 3- котел-утилизатор; 4- циклон с пересыпным устройством; 5-сухой электрофильтр; 6-полая промывная башня: 7 — насадочная промывная башня; 8, 9 — мокрые электрофильтры; 10 — сушильная башня; 11 — фильтр-брызго уловитель; 12 гаэодувка; 13 — теплообменники контактного узла; 14 — контактный аппарат; 15 — пусковой подогреватель; 16 — теплооб-менник; второй моногидратный абсорбер; 18—сборники кислоты: 19- холодильники: 20 — первый многогидратный абсорбер; 21 — олеумный абсорбер; холодильник воздушного охлаждения кислоты. Исходная сера поступает в плавитель, где плавясь нагревается до температуры 1200С и уже в виде жидкости поступает в печь циклонного типа 1 и нагревается до температуры 13000С, затем в котел-утилизатор 2, поступает сверху в пятислойный контактный аппарат 7 с температурой 4400С и концентрацией SO2 10%. В трех верхних слоях катализатора происходит окисление диоксида серы примерно на 60 % в каждом и адиабатическое повышение температуры. Охлаждением газа в теплообменниках между полками достигается ступенчатое приближение к оптимальной кривой. На выходе из третьего слоя достигается степень превращения SO2 в SO3 на 93 – 95 %, при этом адиабата приближается к равновесной кривой и скорость реакции сильно уменьшается Воздух осушается в сушильной башне 9, орошаемый 98%-ной кислотой. После подогрева в теплообменниках 8б и 8в в межтрубном пространстве направляется в печь 1. Газ после первого слоя теплообменника 8а по трубам снова возвращается в контактный аппарат. После 2-го слоя газ поступает в теплообменник 8г по трубам и снова возвращается в контактный аппарат 7. После 3-го слоя газ поступает на абсорбцию по трубам теплообменников 8д, 8б, 8в в первый моногидратный абсорбер 10. После абсорбции газ выходит сверху и через теплообменники 8д, 8б, 8в направляется на 4-й слой контактного аппарата 7, где содержащийся в газе диоксид серы (около 0,5 %) окисляется на 90 – 95 %. Перед 4-ым слоем вводится дополнительное количество воздуха. После 5-го слоя (где селективность процесса составляет 99,5 % и выше) газ используется для подогрева воды в экономайзере 3 и уже оттуда направляется во второй моногидратный абсорбер 11, где происходит окончательное поглощение и выдача 93% H2SO4.
Структурная блок-схема: Операторная схема ХТС: 1 — (серная печь) сжигание серы S + O2 = SO2 2 – (контактный аппарат) контактное окисление 2SO2+ O2 = 2SO3 3 – (абсорбер) абсорбция SO3 SO3 + h3O = h3SO4 Исходные данные для расчета
Составляем систему уравнений: Блок 1: 1) 0,08= 28,75 2) = Блок 2: 1) ,5 2) Блок 3: 1) 0,925 2) Соответствие переменных потока Переименование и упорядочение переменных 1) 0,08 Х1 = 28,75 2) 0,881 Х1 – Х2 = 0 3) 8,374 Х1 – Х3 = 0 4) 1,423 Х1 – Х4 = 0 Матрица коэффициентов
Решение матрицы при помощи ЭВМ: Х1 = 359,4 Х3 = 3009 Х2 = 316,6 Х4 = 511,4 Расход воздуха: Расход кислорода: Расход азота: Расход воды на абсорбцию: Количество полученной серной кислоты: Количество полученных выхлопных газов: Общее количество: Азота: Кислорода: Оксида серы (IV): Оксида серы (VI):
Также определяем: Количество O2 в газе, поступающем в контактный аппарат (2-ой блок): Количество N2 в газе, поступающем в контактный аппарат (2-й блок): Количество SO2 в газе, поступающем в контактный аппарат (2-й блок): Количество SO3 в газе, поступающем на абсорбцию (3-ий блок): Количество O2 в газе, поступающем на абсорбцию (3-ий блок): 32,5 кмоль Количество N2 в газе, поступающем на абсорбцию (3-ий блок): Количество SO2 в газе, поступающем на абсорбцию (3-ий блок): Поточная диаграмма: Масса потоков: Сырье: Масса потока перед контактным окислением: Потери серы на стадии сжигания: Масса потока перед абсорбцией: Масса выхлопных газов: Масса серной кислоты: Масса воды для абсорбции: 1– сжигание серы 2 — контактное окисление 3 — абсорбция а – сырье б – потери в – вода г – серная кислота (92,5%) е – выхлопные газы Масштаб: 1см = 2000 кг
Расходные коэффициенты по сырью S + O2 = SO2 По сере: = = По кислороду: = = Степень конверсии: По сере: По кислороду Выход: По сере: По кислороду: Селективность: По сере: = По кислороду: = Выход целевого продукта (серной кислоты): Селективность: Выводы: Разница коэффициентов по сырью (стех. и прак.) обусловлена неполнотой превращения серы, а также ее потерями на стадии подготовки сырья, которые были отнесены к стадии сжигания серы. Для кислорода эта разность обусловлена его избыточным количеством для окисления серы, по сравнению со стехиометрическим. В данной ХТС использованы технологические принципы и приемы их реализации:
Увеличение полноты превращения сырья Уменьшение количества отходов.
Использование тепла экзотермических реакций Использование тепла высокотемпературных процессов
Список литературы.
|
topuch.ru
Общие сведения
Московский государственный университет тонкой химической технологии им. М.В. Ломоносова.
Курсовая Работа
Кафедра Общей Химической Технологии
Тема: Производство серной кислоты из серы.
Преподаватель: Цыганков Владимир Николаевич
Студент: Лыкошин Дмитрий Дмитриевич
Группа ХТ-409
Москва 2013
Серная кислота — H2SO4 (мол. Масса 92,082) бесцветная маслянистая жидкость без запаха. Не дымит, в концентрированном виде не разрушает черные металлы, в то же время является одной из самых сильных кислот, в широком диапазоне температур (от -40…-20 до 260 – 336,5 ˚С) находится в жидком состоянии.
Области применения серной кислоты чрезвычайно обширны. Существенная ее часть используется как полупродукт в различных отраслях химической промышленности, прежде всего для получения минеральных удобрений, а также солей, кислот, взрывчатых веществ. Серная кислота применяется и при производстве красителей, химических волокон, в металлургической, текстильной, пищевой промышленности и т.д. Серная кислота может существовать как самостоятельное химическое соединение h3SO4, а также в виде соединений с водой: H2SO42H2O, H2SO4H2O, H2SO44H2O, H2SO4 SO3, H2SO42SO3.
В технике серной кислотой называют безводную H2SO4 , ее водные растворы (смесь H2SO4 , H2O и H2SO4nH2O) и растворы триоксида серы в безводной H2SO4 – олеум ( смесь H2SO4 и соединений H2SO4nSO3 ).
Безводная серная кислоты – тяжелая маслянистая бесцветная жидкость, смешивающаяся с водой и триоксидом серы в любом соотношении. Безводная 100%-ая серная кислота имеет сравнительно высокую температуру кристаллизации (10,7˚С). Выпускают три вида серной кислоты:
Концентрация | Температура кристаллизации, ˚С | |
Башенная кислота | 75% | -29,5 |
Контактная кислота | 92,5% | -22,0 |
Олеум | 20% свободного SO3 | +2 |
Серная кислота и вода образуют азеотропную смесь: 98,3% H2SO4 и 1,7% H2O с максимальной температурой кипения (336,5 ˚С).
Исходное сырье
Исходными реагентами для получения серной кислоты могут быть элементарная сера и серосодержащие соединения, из которых можно получить либо серу, либо диоксид серы. Например, сульфиды железа, сульфиды цветных металлов (меди, цинка и др.), сероводород и ряд других сернистых соединений. Традиционно основные источники сырья – сера и железный (серный) колчедан. Значительное место в сырьевом балансе производства серной кислоты занимают отходящие газы цветной металлургии, содержащие диоксид серы. Производство серной кислоты включает в себя несколько этапов:
Подготовка сырья: а) очистка и плавление серы; б) очистка, сушка и дозировка воздуха;
Сжигание серы. Получение диоксида серы окислением (обжигом) серосодержащего сырья. Процесс ведут с избытком воздуха.
S+О2 = SO2
Контактное окисление оксида серы (IV) в оксид серы (VI). Этот процесс характеризуется очень высоким значением энергии активации, для понижения которой необходимо, как правило, применение катализаторов.
SO2 + 0,5O2 = SO2 (Процесс ведут на ванадиевом катализаторе при t = 420-550˚С)
Абсорбция. В зависимости от того как проводится процесс окисления SO2 в SO3 , различают два основных метода получения серной кислоты:
Контактный – процесс окисления SO2 в SO3 проводят на твердых катализаторах. Триоксид серы переводят в серную кислоту на последней стадии процесса – абсорбции триоксида серы, которую можно представить уравнение реакции:
SO3 + H2O H2SO4
Нитрозный (башенный) – в качестве переносчика кислорода используют оксиды азота. Окисление диоксида серы осуществляется в жидкой фазе и конечным продуктом является серная кислота:
SO3 + N2O3 + H2O H2SO4 + 2NO
В промышленности в основном применяют контактный метод получения серной кислоты, позволяющий использовать аппараты с большей интенсивностью.
Рассмотрим процесс получения серной кислоты контактным методом из двух видов сырья: серного (железного) колчедана и серы.
Первой стадией процесса является окисление сырья с получением обжигового газа, содержащего диоксид серы. В зависимости от видов сырья протекают экзотермические химические реакции обжига:
FeS2 + 11O2 2Fe2O3 + 8SO2 (I) S + O2 SO2 . (II)
При протекании реакции (I) помимо газообразного диоксида серы образуется твердый продукт Fe2O3, который может присутствовать в газовой фазе в виде пыли. Колчедан содержит различные примеси, в частности соединения мышьяка и фтора, которые в процессе обжига переходят в газовую фазу. Присутствие этих соединений может вызвать отравление катализатора. Поэтому реакционный газ после стадии обжига колчедана должен быть предварительно направлен на стадию подготовки к контактному окислению, на которой помимо очистки от каталитических ядов выделяются пары воды (осушение), а также получаются побочные продукты (Se и Te).
Если обжиговый газ получают сжиганием серы, то отпадает необходимость очистки от примесей. Стадия подготовки будет включать в себя лишь осушку газа и утилизацию теплоты.
На третьей стадии протекает обратимая экзотермическая химическая реакция контактного окисления диоксида серы:
SO2 + 0,5O2 = SO3 (III)
Последняя стадия процесса – абсорбция триоксида серы концентрированной серной кислотой или олеумом.
В зависимости от комбинации этапов получения серной кислоты, существуют различные функциональные схемы:
Из колчедана методом одинарного контактирования
Из серы методом двойного контактирования
Циклическим методом из серы.
studfiles.net
Производство серной кислоты — Мегаобучалка
Серная кислота — один из основных многотоннажных продуктов химической промышленности.
Области применения. Области применения серной кислоты и олеума весьма разнообразны. Значительная часть ее используется в производстве минеральных удобрений (от 30 до 60 %), а также в производстве красителей (от 2 до 16 %), химических волокон ( от 5 до 15 %) и металлургии (от 2 до 3 %). Она применяется для различных технологических целей в текстильной, пищевой и других отраслях промышленности.
Сырье. Сырьем в производстве серной кислоты могут быть элементарная сера и различные серосодержащие соединения (железный колчедан, сероводород и др.), а также отходящие газы цветной металлургии, содержащие оксиды серы. Преимущественно в качестве сырья используют элементарную серу и железный колчедан.
Теоретические основы синтеза. Общую схему сернокислотного производства можно представить тремя основными стадиями:
1 — сжигание или обжиг исходного сырья. Аппаратурное оформление этой стадии существенно зависят от природы сырья.
4FеS2 + 11О2 = 2Fе2S3 + 8SО2 (8.5.1)
S + О2 = SО2 (8.5.2)
Н2S + 1,5О2 = SО2 + Н2О (8.5.3)
2 — стадия каталитического окисления оксида серы (IV) до оксида серы (VI):
SО2+ 0,5О2 = SО3 (8.5.4)
3 — абсорбции оксида серы (VI) (переработка в серную кислоту):
SО3 + Н2О = Н2SО4 (8.5.5)
В реальном производстве к этим химическим процессам добавляются процессы подготовки сырья, очистки печного газа и другие механические и физико-химические операции.
В зависимости от типа катализатора, применяемого на стадии окисления оксида серы (IV) до оксида серы (VI), различают два основных метода получения серной кислоты:
— контактный, при котором используются твердые катализаторы;
— нитрозный (башенный), при котором в качестве катализаторов используют газообразные оксиды азота.
В настоящее время в промышленности в основном применяют контактный метод получения серной кислоты, при этом используют ванадиевые катализаторы, которые содержат V2O5, щелочные промоторы и носитель — силикатный материал природного или синтетического происхождения.
Рассмотрим принципиальные схемы процесса получения серной кислоты контактным методом из двух видов сырья: серного (железного) колчедана и серы.
Колчедан, применяемый для обжига, предварительно обогащают флотацией. Флотационный колчедан кроме пирита FeS2 содержит ряд примесей (в частности, соединения мышьяка, селена, теллура, фтора), которые при обжиге переходят в состав обжигового газа в виде оксидов As2O3, SeO2,TeO2 и фторсодержащих газообразных соединений HF, SiF4. Наличие этих соединений обусловливает необходимость последующей очистки газа.
Обжиг колчедана проводят в печах с псевдоожиженным слоем колчедана (печь «кипящего слоя» КС) при температурах 800 — 9000C.
Обжиговый газ, полученный сжиганием колчедана в печах КС, содержит большое количество огарковой пыли, соединения мышьяка, селена и фтора. Очистка обжигового газа от пыли осуществляется в циклонах и сухих электрофильтрах, затем газ направляют на стадию мокрой очистки (в промывное отделение), где из обжигового газа удаляют остатки пыли, каталитические яды (соединения мышьяка и фтора), а также соединения селена.
Мокрая очистка обжигового газа заключается в промывке его разбавленной серной кислотой. Примеси частично растворяются в серной кислоте, но большая их часть переходит в состав сернокислотного тумана, поэтому предусмотрена стадия осушки и удаления тумана.
Очищенный газ поступает в контактное отделение. Реакция окисления оксида серы (IV) в оксид серы (IV), лежащая в основе процесса контактирования обжигового газа, представляет собой гетерогенно-каталитическую, обратимую, экзотермическую реакцию. С понижением температуры и повышением давления контактируемого газа равновесная степень превращения Хр возрастает, что согласуется с принципом Ле-Шателье. В то же время, при постоянных температуре и давлении равновесная степень превращения тем больше, чем меньше содержание оксида серы (IV) в газе, то есть чем меньше соотношение SО2 : О2. Это отношение зависит от вида обжигаемого сырья и избытка воздуха. Фактическая степень превращения оксида серы (IV) зависит от активности катализатора, температуры, давления, состава контактируемого газа и времени контактирования.
Так как реакция окисления SO2 относится к типу экзотермических, температурный режим ее проведения должен приближаться к линии оптимальных температур. На выбор температурного режима дополнительно накладываются два ограничения, связанные со свойствами катализатора. Нижним температурным пределом является температура зажигания катализаторов, составляющая в зависимости от конкретного вида катализатора (в настоящее время в качестве катализатора используют пентоксид ванадия промотированный щелочными металлами) и состава газа 400 — 4400C. Верхний температурный предел составляет 600 — 6500C и определяется тем, что выше этих температур происходит падение активности катализатора.
Реакторы или контактные аппараты для каталитического окисления оксида серы (IV) по своей конструкции делятся на аппараты с неподвижным слоем катализатора (полочные или фильтрующие), в которых контактная масса расположена в 4-5 слоях, и аппараты кипящего слоя. Отвод тепла после прохождения газом каждого слоя катализатора осуществляется путем введения в аппарат холодного воздуха или газа, или с помощью встроенных в аппарат или вынесенных отдельно теплообменников.
После каталитического окисления газ подается на адсорбцию в поглотительную башню. Для того чтобы не образовывалось сернокислотного тумана, используют 98%-ную концентрированную серную кислоту. Оксид серы очень хорошо растворяется в такой кислоте, образуя олеум: H2SO4·nSO3. Уравнение реакции этого процесса
nSO3 + H2SO4 H2SO4·nSO3 (8.5.6)
а – из колчедана методом одинарного контактирования;
б — из серы методом двойного контактирования;
в – циклическая из серы.
Рисунок 8.5.1 – Принципиальные схемы получения серной кислоты.
Промышленный способ синтеза серной кислоты.Для увеличения выхода продукта в настоящее время в производстве серной кислоты и олеума контактным методом наиболее распространенной является технологическая схема с использованием принципа двойного контактирования «ДКДА» (двойное контактирование — двойная абсорбция). Сущность двойного контактирования состоит в том, что процесс окисления SO2 на катализаторе проходит в два этапа. На первом степень превращения составляет около 90%. Затем из газа выделяют SO3, направляя газ в дополнительный, промежуточный абсорбер. В результате в газе увеличивается соотношение О2: SO2, что позволяет на втором этапе увеличить степень превращения оставшегося диоксида серы до 95—97%. Общая степень превращения достигает 99,5— 99,7%, а содержание SO2 в отходящих газах составляет около 0,03% (при одинарном контактировании — десятые доли процента).
При двойном контактировании сернистый газ дважды нагревается от начальной температуры около 50° С (после осушки в сушильной башне и выделения серного ангидрида в первой стадии абсорбции), поэтому для обеспечения автотермичности процесса концентрация SO2 в газе на входе в первую стадию контактирования должна поддерживаться 9—10%.
Схема контактного отделения с двойным контактированием изображена на рис. 8.5.2.
Газ проходит теплообменники 1 и 2 ипоступает на первый, а затем на второй и третий катализаторные слои аппарата 3. После третьего слоя газ подают в промежуточный абсорбер 6, из него в теплообменники 4и 8, а затем в четвертый слой катализатора. Охлажденный в теплообменнике 4газ проходит абсорбер 7 и из него выводится в атмосферу. В случае возможных нарушений режима абсорбции очистка газа от сернокислотного тумана и брызг производится в волокнистом фильтре 5.
1, 2, 4, 8 – теплообменники, 3 – контактный аппарат, 5 – волокнистый фильтр, 6, 7 – абсорберы.
Рисунок 8.5.2 – Контактное отделение с двойным контактированием получения серной кислоты
megaobuchalka.ru
ПРОИЗВОДСТВО СЕРНОЙ КИСЛОТЫ КОНТАКТНЫМ СПОСОБОМ. Исходным сырьём для производства серной кислоты могут быть сера, сероводород, сульфиды металлов. Принципиальная схема получения серной кислоты. Процесс состоит из трех стадий:
|
edushk.ru
3.2 Технологическая схема производства серной кислоты и ее описание. Физические и химические свойства серной кислоты
Похожие главы из других работ:
Автоматизация тепловлажностной обработки бетона
1. Технологическая схема производства
Установки для тепловлажностной обработки предназначены для ускоренного твердения изделий. Обычно тепловлажностную обработку ведут до достижения 70% полной проектной прочности бетона…
Алкилирование изобутана изобутиленом до изооктана
5. Технологическая схема и краткое описание процесса производства по заданию проекта
В промышленности алкнлирование н-бутиленов (смесь 1- и 2-изомеров) с изобутаном дают алкилат, богатый углеводородами С8 и часто называемый просто изооктаном. Нередко в качестве сырья берут бутан-бутилеповую фракцию крекинг-газов…
Модернизация конструкции и технологии котла-утилизатора
1.1 Технология производства серной кислоты и продуктов на ее основе
Серная кислота представляет собой соединение одной молекулы триоксида серы SО3 с одной молекулой воды Н2О. В технике под серной кислотой подразумевают любые смеси триоксида серы с водой. Смеси, в которых на 1 моль SО3 приходится больше 1 моля воды…
Проект нормативно-технического обеспечения производства лечебно-столовой минеральной воды
2 Технологическая схема производства минеральной воды и ее описание
2.1 Технологическая схема производства минеральной воды 2.2 Описание технологической схемы производства Технологический процесс, обеспечивающий выпуск минеральных вод бутылочного розлива…
Проект цеха древесноволокнистых плит марки Т-400 производительностью 145 т/сут
1.4.5 Приготовление раствора серной кислоты
Серная кислота вводится после тщательного перемешивания массы со смолой и служит для создания активной кислотности, соответствующий порогу коагуляции смолы. Концентрированная серная кислота 92…
Производство рыбных консервов «Сайра натуральная»
1.2 Технологическая схема производства, ее обоснование и описание
Для пищевых технологий характерно многообразие свойств сырья, полуфабрикатов и готовых пищевых продуктов. Преобразование исходного сырья в пищевую продукцию происходит на технологической линии…
Разработка лабораторного регламента производства изотонического раствора натрия хлорида 0,9% для инъекций (на 1000 л в ампулах по 10 мл)
3 Технологическая схема производства
…
Разработка проекта технологической линии производства на примере ОАО «Молочный завод «Уссурийский»
1.2 Технологическая схема производства, ее обоснование и описание
В пищевой отрасли производство глазированных сырков осуществляется в строгом соответствии с действующими нормативными документами. Технологическая схема производства — это сочетание отдельных технологических операций…
Разработка технологии монтажа гидравлического пресса «Лайс»
1.2 Технологическая схема производства ЦМИ-1
Рисунок 1 — Технологическая схема ЦМИ-1 С бункеров магнезит, пыль и хром поступают на дозаторы. На бункере объёмом 10 тонн дозатор типа АД-125. На бункере объёмом 30 тонн дозатор типа АД-500, АД-250, БДП-600. На бункере объёмом 15 тонн дозаторы типа АД-500, АД-250…
Сквозной цикл производства блока цилиндров двигателя
2.1 Технологическая схема производства
…
Технология производства кислоты на ЗАО ГХК «Бор»
7. Производство серной кислоты
Производство серной кислоты контактным методом введено в эксплуатацию в декабре 1977года. Проектная мощность производства 240000т/год в перерасчете на моногидрат…
Физические и химические свойства серной кислоты
3 ТЕХНОЛОГИЯ СЕРНОЙ КИСЛОТЫ
…
Физические и химические свойства серной кислоты
3.3 Отходы в технологии серной кислоты и способы их утилизации
При производстве серной кислоты в атмосферный воздух вследствие негерметичности оборудования и неполноты превращения диоксида серы в серный ангидрид выбрасываются значительные количества оксидов серы. Например…
Физические и химические свойства серной кислоты
3.4 Предельно-допустимые концентрации газов, паров и пыли в производстве серной кислоты
Вещества В воздухе рабочей зоны производственных помещений, мг/м3 В атмосферном воздухе населенных мест максимальная разовая, мг/м3 среднесуточная, мг/м3 Аммиак 20 — — Минеральная и растительная пыль…
Цех по производству сыра производительностью 18000 тонн в год, в том числе сыра — 5000 т/год в поселке с населением 20000 человек
2.1 Технологическая схема производства
На сыродельные предприятия молоко в основном доставляется специализированным автомобильным транспортом — в цистернах различной вместимости — от 1,5 м3 до 15 м3 и лишь небольшое количество — во флягах…
prod.bobrodobro.ru