Шлакоблоки технология производства: видео, чертежи станков, форм и вибропресса
Шлакоблоки. Технология производства шлакоблока и применение в строительстве.
Шлакоблоки популярный стройматериал. Благодаря своей прочности, удобству кладки и великолепным теплоизолирующим свойствам они используются в любом строительстве. Возведение стен из шлакоблоков может выполнить даже частный застройщик, не прибегая к помощи профессионалов.
Свое название материал получил от доменного шлака, который используется при его производстве в качестве заменителя. Иногда шлакоблоками могут называть блоки с другими заполнителями (гранитный отсев или керамзит).
У этого материала много потребителей, начиная с крупных строительных компаний, занятых промышленным строительством, и заканчивая частным сектором.
Своей популярностью шлакоблоки обязаны тому, что стоимость их кладки в два раза меньше, чем кладка из кирпича или пенобетона.
Шлакоблок это строительный материал, изготовленный путем вибропрессования бетонного раствора в определенной по размерам форме.
Рассмотрим технологию производства шлакоблока:
— производится заготовка бетонного раствора с использованием определенного количества шлака. Заготовка происходит при помощи специальных бетономешалок. Вручную замес также возможен, но это довольно сложно для человека, так как масса тяжелая и вязкая;
— готовый раствор перемещают в специальные формы, которые имеют определенные размеры необходимые для готового продукта. Внутри формы имеется три штыря, которые позволяют образовать пустые образования в готовой продукции;
— далее раствор выравнивают и прессуют с вибрацией для придания наибольшей плотности смеси. В большинстве случаев прессование длится примерно полминуты, благодаря такой обработке шлакоблок обретает форму и необходимую прочность, чтобы не рассыпаться;
— далее шлакоблоки попадают на специальные поддоны и направляются для просушки при естественной температуре на несколько суток. Полное засыхание шлакоблока проходит в течение месяца, температура в помещении не должна быть ниже 20 градусов тепла. Самое главное, чтобы при сушке были влажные условия, иначе материал слишком пересохнет и шлакоблок растрескается.
Вот какая сложная технология производства шлакоблоков.
Применение шлакоблоков в строительстве
Шлакоблоки можно применять при строительстве любых сооружений, иногда их применяют и при строительстве жилых домов, но в ряде случаев это не рекомендуется, так как материал этот очень тяжелый и излишне хрупкий. При нанесении ударов шлакоблок может начать крошиться, хотя многое и зависит от качества его производства. Из шлакоблока идеально строить заборы, хозяйственные постройки или возводить некоторые другие сооружения на участке.
Выбирая такой стройматериал для своих целей, обратите внимание на технологию производства шлакоблоков. На данный момент многие шлакоблоки производятся ручным методом, о качестве таких шлакоблоков сложно говорить что-то положительно, они менее качественны и быстро рушатся.
Достоинства шлакоблоков
Строительство с использованием шлакоблоков популярно, потому что у них есть ряд достоинств:
— стоимость шлакоблока гораздо ниже стоимости кирпича, пеноблока и других строительных материалов, благодаря тому, что его компоненты легкодоступны и дешевые;
— используя шлакоблоки для возведения стен в малоэтажном строительстве, с этой работой справится даже любитель;
— для работы со шлакоблоками потребуется в два раза меньше раствора, чем для других материалов;
— стены из шлакоблоков получаются негорючими, морозостойкими и прочными.
Минусы шлакоблоков
— Основной статьей расходов при строительстве из шлакоблоков является транспортировка монолитных блоков.
— Для возведения обычно используются стеновые монолитные камни и блоки, имеющие сквозные пустоты. Они засыпаются шлаком, что увеличивает их теплоизоляцию, но затрудняет ход строительных работ. Кроме того, постепенно эта сухая засыпка может осесть и в блоках возникнут пустоты, ухудшающие теплоизоляцию стены.
— Стены шлакоблочного дома никогда не бывают теплыми, а с наступлением холодов для его прогрева потребуется несколько дней.
При возведении дома из шлакоблоков следует хорошо позаботиться о гидроизоляции стен, так как они разрушаются из-за обильного воздействия влаги.
Если вы решились строить дом из шлакоблоков, то следует помнить, что этот материал не является экологически чистым. Кроме того, стены из шлакоблока способны выделять ядовитые вещества, которые могут вызвать аллергию и негативно сказаться на дыхательных функциях человека. Кроме того, может так случиться, что некоторые вещества, использовавшиеся при изготовлении блоков в качестве заполнителя (к примеру, доменный шлак), могут дать радиоактивный фон. Поэтому целесообразнее всего перед приобретением шлакоблоков измерить их уровень радиации.
Похожие статьи
- Нерудные строительные материалы Нерудные материалы широко используются в строительстве.
В естественном, необработанном виде чаще всего применяются щебень и песок, которые используют в качестве заполнителей для бетона и […]
- Виды гипсокартонных листов
- Материалы для строительства стен Ныне довольно стремительно развиваются строительные технологии. Постоянно на строительный рынок попадают новые материалы, обладающие лучшими свойствами и высокими качествами в отличие от […]
- Железобетон
Несколько столетий назад, все строения помельче, возводились из дерева, а покрупнее – из камня или кирпича. Естественно, такие здания были не очень большими, так как вышеописанные […]
- Разновидности кровельного материала В настоящий момент на рынке представлен широкий ассортимент разновидностей кровельного материала.
Связан такой широкий ассортимент с тем, что людей в последнее время очень сильно волнует […]
Оборудование для производства шлакоблоков
Оборудование для производства шлакоблока
Предприятие Монолит представляет оборудование для производства блоков: шлакоблока, стеновых блоков, керамзитоблока, термоблока
В последние годы в нашей стране активно развивается строительство. И сегодня шлакоблоки – пожалуй, самый востребованный строительный материал. Они широко применяются как при строительстве крупномасштабных объектов (жилых и промышленных), так и в частных проектах.
Использование шлакоблоков гарантирует оптимальное соотношение цены и качества, к тому же данный материал значительно крупнее кирпича, что не только облегчает и ускоряет процесс кладки, но и экономит раствор.
Изготовление шлакоблоков от Предприятия Монолит
Предприятие Монолит уже третий десяток лет специализируется на выпуске оборудования для производства шлакоблоков, стеновых блоков, керамзитоблока, термоблока и других строительных материалов.
Мы выпускаем следующее оборудование для производства блоков различных типоразмеров и назначения:
Стационарный вибропресс – профессиональное оборудование полного цикла для производства блоков, тротуарной плитки, бордюрного камня и других строительных материалов. Предлагается в различных вариантах: с одним или двумя загрузочными модулями, вертикальным или горизонтальным вариантом распалубки, а также в составе производственной линии с бетоносмесителем на эстакаде, либо с ленточным конвейером.
Для производства строительного блока – используют метод вибропресования полусухой жесткой бетонной смеси. В качестве заполнителя могут используется зола, отходы горения угля, отсев щебня, гравий, песок и другие компоненты.
Помимо высокой теплоизоляции материал отличается:
- звуконепроницаемостью;
- прочностью;
- невысокой ценой: стоимость кладки по сравнению с кирпичом или пенобетоном ниже почти в 2 раза.
Все это делает шлакоблок популярным как у потребителей, так и у производителей строительных материалов. В последнее время все больше компаний начинает заниматься изготовлением шлакоблока. Сегодня рынок предлагает начинающим предпринимателям самое разнообразное оборудование для шлакоблоков. Для запуска требуется лишь небольшое помещение, а некоторые модели техники позволяют производить блоки прямо на стройплощадке. Важно не ошибиться при выборе компании производителя.
Как и в любом производстве здесь главное – качественное оборудование и техническая база для производства шлакоблока. Чтобы выпускаемая продукция соответствовала установленным стандартам качества, необходимо соблюдать все условия сложного технологического процесса, что возможно лишь при наличии современного профессионального оборудования для производства блоков различного назначения.
Более подробно об изготовлении читайте в разделе: Процесс изготовления шлакоблоков.
Виды стеновых камней производимых на оборудовании Предприятия Монолит
Передвижной вибропресс в отличие от стационарного позволяет наладить изготовление шлакоблока непосредственно на строительной площадке. Выпускается также в нескольких модификациях: в облегченном варианте (с верхней загрузкой), с устройством самозагрузки (позволяет обходиться без грузоподъемных механизмов), в составе различных технологических линий.
На все оборудование Предприятие Монолит дает гарантию 12 месяцев. Кроме того, компания помогает в запуске производства, предоставляет комплекс услуг, включающий пусконаладочные работы, консультации в подборе смесей, пробную формовку изделий с использованием местного сырья, обучение персонала.
Оборудование Предприятия Монолит универсально: оно позволяет производить не только шлакоблоки, но и еще более 400 наименований строительных материалов. Организовать производство изделий можно в короткие сроки и с минимальными финансовыми вложениями. Профессиональное оборудование для шлакоблока и других блоков гарантирует высокое качество выпускаемой продукции и, как следствие, – популярность производимых стеновых материалов, доверие покупателей и высокую рентабельность.
Выбираем шлакоблок: технология изготовления, размеры, виды, характеристики, условия транспортировки и хранения, плюсы и минусы
Шлакоблок — довольно дешевый материал, к тому же он прост в работе, его можно изготовить самостоятельно. Благодаря этим качествам шлакоблок пользуется заслуженной популярностью, особенно когда дело касается строительства подсобных помещений. Часто, например, можно встретить гараж из шлакоблоков, или бытовку. Иногда этот материал применяют и при строительстве жилых помещений, но в последнее время такие решения встречаются все реже, в виду несоответствия требованиям по экологии. В данной статье мы рассмотрим основные виды шлакоблоков, расскажем об основных размерах шлакоблоков. Кроме этого, дадим рекомендации о том, как транспортировать данный строительный материал, расскажем, как класть шлакоблоки.
Технология изготовления шлакоблоков, размер шлакоблоков и другие характеристики
Давайте определимся, что такое шлакоблок. Шлакоблок — это искусственный строительный камень,полученный путем заливки и прессовки смеси из цемента и шлака. При производстве шлакоблока используется относительно недорогой материал, что влияет на конечную стоимость.
Основные характеристики шлакоблоков (действительны для продукции промышленного производства)
- Стандартный размер шлакоблока: 188×199×399 мм. (по ГОСТ 6433-99 «Камни стеновые бетонные»)
- Теплопроводность: от 0,27 до 0,65 Вт/м3
- Плотность: от 750 до 1450 кг/м3.
Технология изготовления шлакоблоков
Исходя из названия, понятно, что основной заполнитель в смеси — это шлак, отходы горения из доменных печей. Также могут применяться такие компоненты как отсев щебня, отходы кирпича, гравий, опилки (после обработки). Соотношение компонентов в смеси при заливке в форму: цемент + п.г.с. + шлак, в пропорции 1-3-5, а также вода.
Процесс изготовления шлакоблоков проходит в три этапа:
- Приготовление полусухой цементно-шлачной смеси
- Заполнение формы смесью и прессовка
- Затвердевание конечного продукта.
Виды шлакоблоков
Давайте определимся, какой же вид шлакоблока лучше выбрать для работы. Для того чтобы ответить на этот вопрос, мы рассмотрим виды шлакоблоков, отличающиеся друг от друга по пустотности (наличии полостей и их общий объём).
- Монолитным (полнотелым) называют блок, который изготовлен без полостей ,т.е. цельный. К достоинствам такого вида шлакоблоков можно отнести запас прочности, к недостаткам — низкую теплоизоляцию и большой вес
- Блок с коэффициентом пустотности 30%, самый популярный из всех видов шлакоблоков, так называемая «золотая середина». Такой вид шлакоблоков отличается средними показателями теплоизоляции и прочности
- Блок с пустотностью в 40% за счет большего объёма полостей имеет высокую степень теплоизоляции, но при этом уступает в прочности из-за сравнительно тонких стенок.
Достоинства и недостатки шлакоблоков
По сути, недостатков у шлакоблока больше, чем достоинств.
Достоинства шлакоблоков
К плюсам шлакоблока можно отнести небольшую стоимость и простоту в работе. Шлакоблоки можно изготовить своими руками, для этого не требуется сложного оборудования и дорогих компонентов.
Недостатки шлакоблоков
- Низкая морозостойкость и теплоизоляция
- Низкая относительная прочность и устойчивость к осадкам
- Низкая звукоизоляция
- Несоответствие экологическим требованиям (зависит от наполнителя, используемого при производстве: шлак из доменных печей может быть токсичным).
Из всего вышесказанного можно сделать вывод, что шлакоблок не очень подходит для жилых помещений, зато для подсобных (гараж из шлакоблока, сарай) — самый оптимальный вариант.
Как выбрать шлакоблок
При покупке важно обратить внимание на внешний вид блоков (не должно быть впадин, сколов, блоки должны иметь ровную плоскость со всех сторон) . Геометрия блоков(правильная форма) проверяется простым промериванием нескольких случайно выбранных блоков. Если размеры каждого из выбранных блоков совпадают, геометрия блоков верна.
Условия транспортировки и хранения шлакоблоков
Транспортировать шлакоблоки можно, как на поддоне, так и навалом. Опыт говорит, что проще погрузка и разгрузка проходят шлакоблоков на поддонах с нанятой машиной-манипулятором.
При хранении шлакоблоков нужно обеспечить следующие условия:
- Блоки должны быть изолированы от сырости (например, сложенные под навесом на поддоны)
- Укладывать шлакоблоки нужно полостью вниз.
Как класть шлакоблоки
Кладка шлакоблоков делится на несколько этапов (при условии, что ранее фундамент был выведен «на ноль»):
- Подготовка фундамента
- Выставление первого ряда блоков
- Дальнейшая укладка.
Подготовка фундамента подразумевает очистку фундамента от различного рода загрязнений, при выставлении первого ряда не должно быть никаких помех.
Далее следует укладка гидроизоляционного слоя (обычно используют толь).
Выставление первого ряда производится следующим образом:
на приготовленный слой раствора выставляют в первую очередь углы, затем выравнивают по высоте между собой с помощью уровня (возможно использование гидроуровня или лазерного уровня). Между углами пускают горизонтальный шнур, который служит ориентиром для кладки каждого ряда шлакоблоков. Блоки укладываются полостью вниз, причем раствор накладывается не только на нижнюю поверхность, но и на боковую грань уложенного блока. Толщина слоя раствора не должна превышать 1 см. Маленькая хитрость: если в раствор добавлять небольшое количество обычной древесной золы, которая придаст раствору черный цвет, окончательный вид уложенных блоков будет намного красивее.
Через каждые два-три ряда необходимо прокладывать кладочную сетку для связки.
Советуем также ознакомиться со статьями:
Камень строительный: колпак и ракушечник
Строительство несущих стен дома. Монолитная технология
Производство шлакоблоков оборудование для изготовления шлакоблока строительный блок стеновые камни строительные материалы строительство
Оборудование для изготовления шлакоблока компания МСД производит с 2004 года. За это время мы выпускаем наиболее популярные в СНГ и Дальнем Зарубежье модели станков по производству шлакоблока и тротуарной плитки:
Строительное оборудование, выпускаемое МСД
Самые популярные станки для шлакоблоков:
Станок для двух шлакоблоков производства, МАРС. 600-800 штук в смену, 220В/150Вт.
Другие подобные станки:
МЗ10- ручной подъем матрицы — 120$
1ИКС — один шлакоблок, как на этом видео подъем матрицы — 140$
МАРС(это видео) — 180 дол
Команч, 4 блока, прижим матрицы механический как и подъем — 430$
Все станки для шлакоблока практически всегда в наличии в г.Александрия, более точно по телефону выше.
Тел для заказов:
+38 096 992 9559 Инна
Видео работы станков для шлакоблока:
youtube.com/embed/e1XaUXic_eQ» frameborder=»0″ allow=»accelerometer; autoplay; clipboard-write; encrypted-media; gyroscope; picture-in-picture» allowfullscreen=»»/>
Производство и продажа вибростанков для тротуарной плитки, подробнее
Вибростанок для производства тротуарной плитки, брусчатки методом вибропрессования, цена 7000грн!:
Разные названия станка: Тандем-2, РПБ-1500. В стандартную комплектацию входит два комплекта прижима и матриц(«старый город» и «кирпичик») Стоимость стандартного аналога РПБ-1500 с доставкой в Россию — 30000руб(с двумя комплектами матриц и прижимов, для сравнения в России такая комплектация стоит от 42 000руб и выше)
Обращаться по тел.:
+38 096 992 9559 Инна
Или эл. почта: [email protected]
Видео производство брусчатки — тротуарной плитки:
youtube.com/embed/_xCtsTa3OlQ» frameborder=»0″ allow=»accelerometer; autoplay; encrypted-media; gyroscope; picture-in-picture» allowfullscreen=»»/>
+38 096 992 9559 Инна
Мечта застройщика — МЗ10 — самый малогабаритный и простой станок для производства шлакоблока, ввиду своей малогабаритности популярен среди частных застройщиков, изготавливающих шлакоблоки для себя или для малого домашнего бизнеса:
Цена станка в Украине — 1500 грн, в России — 9000 руб
Видео работы станка МЗ10:
Станок 1ИКС для изготовления шлакоблока — подходит как частным застройщикам, так и предпринимателям, решившим начать шлакоблочный бизнес.
Цена — 1900 грн(Украина), 15000 руб (Россия)
Видео работы за станком 1ИКС:
Станок МАРС — самый популярный вибростанок для изготовления шлакоблока, оптимален по цене-производительности. Одновременно изготавливается два стандартных шлакоблока.
Цена — 2500 грн. в Украине или 20000 руб в России
Видео работы вибростанка МАРС:
Вибропресс Команч — самый популярный станок в среде малых производителей шлакоблоков для бизнеса, в отличии от всех предыдущих моделей более удобен в эксплуатации — прижим встроен в конструкцию.
Цена — 6000 грн в Украине или 40000 руб в России (Таганрог)
Видео станок для шлакоблоков Команч-34
Вибростанок Дракон — более профессиональное оборудование для производства шлакоблока с мощным вибродвигателем, укрепленной рамой.
Цена в Украине — 9000грн, в России (Таганрог) — 60000 руб
Видео станок для шлакоблоков Дракон
youtube.com/embed/5JTHnViJ4hQ» frameborder=»0″ allowfullscreen=»»/>
Стационарный станок изготовления шлакоблока СПРУТ-2 (еще т.н. СКАТ)
Цена — 15000 грн или 75000 руб
Видео станок для шлакоблоков Спрут-2
Автомат для производства шлакоблока СУ-25 — профессиональное автоматическое стационарное оборудование для производства шлакоблока.
Цена — 85000 грн Украина, 450 000 руб Россия
Видео автоматический станок для шлакоблоков СУ-25
Кроме этих станков для изготовления шлакоблоков в МСД производятся специальные станки для изготовления спецблоков типа ТЕРИВА (перегородочные стеновые камни ТЕРИВА) или типа ЕВРОИКС — изготовления больших камней 490×240×240.
По вопросам приобретения станков обращаться:
+38 067 2650755 менеджер по вибро-оборудованию МСД — консультации, продажи шлакоблочного и строительного оборудования
+38 050 4571330 продажи продукции МСД
+38 068 4606147 продажи продукции МСД
Эл. почта: [email protected]
…………….
Разные статьи здесь: http://shlakoblok.com/statji
Как изготавливаются бетонные блоки?
Бетонные блоки или цементные кирпичи являются строительным материалом, используемым для возведения стен в здании. Он также известен как блок бетонной кладки (CMU). Бетонные блоки являются одним из сборных железобетонных изделий, используемых в строительстве. Сборные блоки формируются и затвердевают до того, как они попадут на рабочую площадку. Существуют различные бетонные блоки, имеющие одну или несколько полых полостей, а сторона может быть отлита гладкой или с рисунком. Эти блоки укладываются на бетонный раствор, чтобы получилась стена.
Бетонный раствор впервые использовали римляне в 200 г. до н.э. для крепления фасонного камня в здании. При римском императоре Калигуле в 37-41 гг. н.э. небольшие блоки бетона использовались в качестве строительного материала в современном Неаполе, Италия. Бетонная технология, разработанная римлянами, утрачена с падением Римской империи в пятом веке. Английский каменщик Джозеф Аспдин разработал портландцемент в 1824 году.
Первый пустотелый бетонный блок был разработан Хармоном С. Палмером в 1890 году в США, и после 10 лет исследований и экспериментов он запатентовал конструкцию в 1900 году.Блок, разработанный Палмером, имел размеры 8 x 10 x 30 дюймов и был настолько тяжелым, что для его перемещения использовался кран.
За это время один человек изготовил в среднем 10 блоков и отлил их вручную. С современными машинами и передовыми технологиями это составляет 2000 блоков в час.
Какое сырье используется? Для изготовления бетонных кирпичей или блоков используется сырье, такое как смесь порошкообразного портландцемента, воды, песка и гравия. Вместе эти сырьевые материалы образуют блок светло-серого цвета с мелкой текстурой поверхности и высокой прочностью на сжатие.Вес типичного бетонного блока составляет от 38 до 43 фунтов (от 17,2 до 19,5 кг). Для блоков более высокий процент песка и более низкий процент гравия и воды. Получилась очень сухая, густая смесь, сохраняющая форму при извлечении из блочной формы.
Шлакоблок изготавливается из гранулированного угля или вулканического пепла. Это темно-серый блок с текстурой поверхности от средней до грубой, обладающий хорошей прочностью и хорошими звукоизоляционными свойствами с более высокой теплоизоляцией, чем бетонный блок.Типичный шлакоблок весит около 26-33 фунтов (11,8-15,0 кг).
При наличии гранулированного угля или вулканического пепла вместо песка и гравия с керамзитом, сланцем или сланцем изготавливается легкобетонный блок. Керамзит, сланец и сланец изготавливают с дроблением сырья и нагревом до 2000 o (1093 o ) . Материал раздувается или вздувается из-за быстрого образования газов, вызванного сгоранием мелких частиц органического материала внутри.Блок из легкого бетона весит около 22-28 фунтов (от 10,0 до 12,7 кг) и используется для возведения ненесущей несущей стены и других перегородок. Кроме того, для облегченных блоков используются доменный шлак и природные вулканические материалы, такие как пемза и шлак.
Наряду с основными компонентами для изготовления блоков используется бетонная смесь, содержащая химическое вещество, называемое добавкой, для изменения времени отверждения и повышения прочности на сжатие или для улучшения обрабатываемости. Пигменты добавляются в блоки для однородного цвета или делают поверхность блока однородной.Это также защищает поверхность блока от химических веществ. Глазурь на поверхности блока выполнена на термореактивной смолянистой связке, кварцевом песке и цветных пигментах.
Дизайн бетонных блоков Существуют стандартизированные формы и размеры обычных бетонных блоков для строительства зданий. Обычный размер блока 8 x 8 x 16, высота 8 дюймов, глубина 8 дюймов и ширина 16 дюймов. Это измерение включает в себя валик раствора, а размер блока составляет 7,63 дюйма (19.4 см) в высоту, 7,63 дюйма (19,4 см) в глубину и 15,63 дюйма (38,8 см) в ширину.
Многие производители блоков предлагают варианты блоков, чтобы они выглядели более эстетично для конкретных применений. Например, есть один производитель бетонных кирпичей или блоков, который проектирует блоки специально для водонепроницаемости через наружные стены. Блок с раздвоенной поверхностью с шероховатой каменной текстурой на одной стороне блока, затем гладкая поверхность. Эти бетонные кирпичи придают красивый эстетический вид.
Процесс производства бетонных кирпичей или блоков Процесс производства бетонных кирпичей состоит из четырех этапов: смешивание, формование, отверждение и формирование кубов.Есть бетонные заводы, которые производят только бетонные блоки, в то время как другие производят различные сборные изделия, такие как блоки, плоская брусчатка, декоративные элементы, такие как окантовка газона, бетонные кирпичи и т. Д. С развитием технологий некоторые заводы по производству бетонных кирпичей могут производить 2000 блоков час.
Песок и гравий хранятся в силосах снаружи, а затем при необходимости передаются по конвейерной ленте, а цемент хранится в силосах, чтобы защитить его от влаги.Когда смешивание началось, песок, гравий и цемент выходят из силосов через весовой дозатор, который взвешивает каждый материал. Сухие материалы поступают в смеситель, где они смешиваются в течение нескольких минут. В основном есть два типа миксеров, в которых используется планетарный или тарельчатый миксер, также известный как неглубокий лоток с крышкой. Смесительные лопасти прикреплены к вертикальному вращающемуся валу с мешалкой. Другой тип — горизонтальный барабанный смеситель. Это кофе, перевернутый на бок, с лопастями для смешивания, прикрепленными к горизонтальному вращающемуся валу внутри миксера.
После смешивания сухих материалов в смеситель добавляется небольшое количество воды. Теперь, если завод расположен в теплых местах, вода сначала проходит через нагреватель или чиллер для поддержания температуры. В это время добавляются смешивающие химикаты и цветные пигменты, и бетон перемешивается в течение шести-восьми минут.
После смешивания бетон сбрасывается на ковшовый конвейер и транспортируется в приподнятый бункер, а цикл смешивания начинается после следующей загрузки.После этого он транспортируется в другие бункеры на блок-машине с регулируемой скоростью. Затем бетон снижают до расхода и заливают в формы. В формах есть внешняя коробка формы, в которой находятся другие вкладыши формы. Вкладыши имеют внешнюю форму блока и внутреннюю форму полостей блоков. В зависимости от мощности машины за один раз формуется от 5 до 15 блоков.
После заполнения формы бетоном гидравлический пресс прессует бетон в форму. Сжатие осуществляется воздушным или гидравлическим давлением.Многие машины для производства бетонных кирпичей и бетонных блоков используют вибрацию для завершения процесса.
После этого блоки выталкиваются из формы на плоский стальной поддон. Поддон и блоки выталкиваются из машины на цепной конвейер. Некоторые из машин имеют функцию вращающейся щетки, которая удаляет рыхлый материал с верхней части блоков.
Теперь поддоны блока транспортируются к автоматизированному укладчику или загрузчику, который помещает их в стеллаж для отверждения.На каждой стойке несколько сотен блоков. После заполнения стеллажа его закатывают на рельсы, а затем перемещают в сушильную печь.
Это помещение, вмещающее несколько стоек блоков одновременно. В основном используются два типа отверждения. Во-первых, это печь низкого давления, где блоки выдерживают от одного до трех часов при комнатной температуре для медленного затвердевания. Затем вводят пар с температурой 60°F (16°C в час) для повышения температуры закалки. Блоки стандартного веса отверждаются при 150-165° F (66-74° C), а легкие блоки отверждаются при 170-185° F (77-85° C).После достижения температуры пар отключают и блоки пропитывают горячим влажным воздухом в течение 12-18 часов. Процесс отверждения занимает около 24 часов.
Другой тип печи – паровая печь высокого давления, также известная как автоклав. Температура в этой печи составляет 300-375°F (149-191°C), а давление 80-185 фунтов на квадратный дюйм, примерно от 5,5 до 12,8 бар. Блоки выдерживают от 5 до 10 часов. Давление сбрасывается, и блоки выпускают влагу внутрь. Процесс отверждения в автоклаве потребляет больше энергии и является более дорогим, но он производит больше блоков за меньшее время.
4. КубированиеЗатем стеллажи с отвержденными блоками выкатывают из печи, а поддоны блоков раскладывают и размещают на цепном конвейере. После этого блоки сталкиваются со стальных поддонов, а пустые поддоны возвращаются в блок-машину для получения новых блоков.
Если есть блок с разъемной поверхностью, он сначала отформован как два соединенных блока. После завершения отверждения двойных блоков он проходит через рассекатель, и тяжелое лезвие ударяет между двумя половинками.
Бетонные кирпичи и блоки проходят через кубер, который выравнивает каждый блок и укладывает их в куб три блока по шесть блоков в глубину и три или четыре блока в высоту. Затем кубики выносятся на улицу вилочным погрузчиком и складируются для отправки.
КачествоПроизводство бетонных блоков и кирпичей требует постоянного контроля за получением блоков требуемых свойств. Перед подачей в смеситель сырье взвешивается электронным способом. Содержание воды в песке и гравии измеряется ультразвуковыми датчиками, а количество воды требуется для автоматического измерения.В холодных и теплых условиях вода перед использованием должна пройти через охладитель или нагреватель.
После выхода из машины высота блока должна быть проверена с помощью лазерных датчиков, а в камере отверждения температура, давление и время цикла должны быть проверены должным образом и записаны автоматически, чтобы гарантировать, что блоки должны быть отверждены должным образом для достижения максимальной прочности.
Станок для производства шлакоблоков своими руками, цена
Шлакоблоки давно завоевали популярность в частном строительстве.Во многом это связано с тем, что их можно приготовить в домашних условиях. Для этого нужно знать рецепт и технологию изготовления блоков, а также обзавестись достаточно простым оборудованием.
Шлакоблоками называют строительный материал, который получают после затвердевания бетонной смеси в форме или в процессе вибропрессования. Свое название они получили из-за того, что в качестве наполнителя в их производстве изначально использовался обыкновенный топочный или доменный шлак.
Со временем список наполнителей значительно расширился, но название осталось прежним.От выбора наполнителя зависит, какими эксплуатационными качествами будут обладать блоки, цена за штуку. Шлакоблоки могут быть монолитными или пустотелыми . Монолитные обладают большей прочностью, чем пустотелые. Часто их используют для возведения фундаментов.
В состав бетонной смеси для блоков могут входить зола, шлак и другие отходы от сжигания угля. Изготовление шлакоблоков своими руками в домашних условиях можно осуществлять и с такими бетонными смесями, наполнителями для которых служат кирпичные отходы, опилки, а также керамзит, гравий, перлит, песок и многое другое.
В шлакоблоке может вообще не быть шлака. Наполнители разные, но название остается прежним
Преимущества шлакоблоков:
- Стены из шлакоблока
- обладают отличной тепло- и звукоизоляцией; шлакоблоки
- значительно дешевле кирпича, пеноблоков и других строительных материалов;
- простота и удобство монтажа;
- можно изготовить шлакоблоки своими руками, что позволяет частным застройщикам быстро и легко возводить различные постройки, даже не прибегая к услугам каменщиков (один блок заменяет примерно 3-4 кирпича).
Технология производства шлакоблоков
Многих частных застройщиков интересует вопрос, как сделать шлакоблоки своими руками? Ведь на дачном участке или при строительстве загородного дома всегда могут понадобиться подсобные помещения, подпорные стены или ограждения. Вы можете построить их из самодельных строительных материалов намного дешевле и быстрее.
Условно процесс изготовления шлакоблоков можно разделить на три этапа:
- Приготовление бетонного раствора, состоящего из воды, цемента и любых отсевов.При необходимости в него добавляют пластифицирующие добавки, улучшающие качественные характеристики готовых изделий, повышающие их водостойкость и морозостойкость.
- Заливка свежеприготовленной смеси в специальные формы. Бетонная смесь уплотняется вибрацией. Для этого можно купить профессиональное оборудование или сделать станок для производства шлакоблоков своими руками.
- На последнем этапе происходит затвердевание блоков. При естественной температуре этот процесс длится 36 — 96 часов.Это время значительно сокращается при использовании специальных добавок.
Для производства качественных блоков в домашних условиях вам потребуется:
- вибромашина
- ;
- сырье;
- относительно ровная поверхность;
- напряжение сети 220 В.
В первую очередь необходимо определиться с выбором машины. В том случае когда нужно построить баню или гараж, можно сделать самодельный шлакоблочный станок своими руками.Если кто-то планирует организовать собственный бизнес, то потребуется более производительная профессиональная машина.
Шлакоблоки, изготовленные без вибропрессования, лучше всего использовать для одноэтажных хозяйственных построек, заборов
Формы для производства бетонных блоков
Наиболее важной частью любой машины является пресс-форма. . Все остальные компоненты и детали являются надстройками, позволяющими производить с этой формой различные манипуляции: заполнять, уплотнять раствор, перемещать и т.д.
Для производства шлакоблоков на заводе используются стандартные стальные формы. Форма для шлакоблоков своими руками обычно изготавливается из дерева. . Эта форма представляет собой специальную емкость, куда заливается бетонная смесь и где она находится до полного застывания.
Формы для шлакоблоков должны быть разборными , чтобы можно было легко вынимать готовые изделия. Многие формы для шлакоблоков своими руками, чертежи которых можно найти в интернете, изготавливаются без дна.Если предполагается изготовление пустотелых блоков, то проще всего сделать в них пустоты, погрузив в заливаемую в форму бетонную смесь пластиковые емкости, наполненные водой или бутылки из-под шампанского (последний вариант предпочтительнее). Шлакоблоки своими руками можно делать и таких форм, которые имеют специальные выступы для образования пустот.
деревянные формы
Проще всего сделать шлакоблоки своими руками в деревянных формах . Для изготовления такой формы нужны строганные доски.Их ширина должна соответствовать высоте будущего блока. На продольных сторонах формы делают надрезы с внутренних сторон досок. Глубина этих надрезов должна быть 7 — 8 мм, а ширина должна соответствовать толщине разделительных пластин, которые могут быть изготовлены из железа, текстолита, гетинакса или любого другого материала с гладкой поверхностью. Расстояние между пропилами должно быть равно длине блоков. Все детали формы следует покрасить любой масляной краской.
Такие формы используются без вибраторов . Раствор в них заливается мягкий, с большим содержанием воды. Но если эту простую форму установить на вибростол, то можно получить более совершенный станок для изготовления шлакоблока своими руками.
Металлические формы
Тем, кто собирается делать шлакоблок своими руками, понадобятся металлические формы для изготовления блоков. Детали пресс-формы вырезаются из стального листа толщиной 3–5 мм.Размеры этих деталей должны соответствовать размерам шлакоблока. Блоки размерами 190х190х390 мм считаются стандартными. . Высота формы должна превышать высоту блоков на 5 мм, чтобы можно было залить бетонную смесь и придавить сверху специальной плитой.
При самостоятельном изготовлении шлакоблоков лучше придерживаться стандартного ряда размеров
Если встал вопрос, как сделать шлакоблок с пустотами своими руками, то важно правильно изготовить пустотообразователи. Лучше всего для этого подходят трубы. Но им нужно придать коническую форму, чтобы готовые блоки можно было легко вынуть. Пустообразователи иногда делают прямоугольными. Форма их особого значения не имеет. Главное, чтобы они имели небольшую конусность. Также следует учитывать, что пустоты в шлакоблоках должны составлять не более 30 процентов площади их поверхности.
Все сварные швы должны выполняться снаружи формы, чтобы она оставалась гладкой внутри. и с ровными углами.По нижнему периметру необходимо сделать резиновый или деревянный уплотнитель во избежание деформации краев формы. Даже по краям можно приваривать металлические пластины шириной 20 мм.
Оборудование для производства шлакоблоков
В случае, когда нужно построить одно небольшое здание, шлакоблоки можно изготовить и в простых формах с бутылками. Если планируется масштабное строительство, то без вибромашины не обойтись, пусть даже и самодельной. Шлакоблочный станок своими руками можно сделать из подручных материалов . Такой станок поможет значительно сэкономить время при изготовлении блоков.
Для изготовления шлакоблочного станка своими руками, чертежи которого можно разработать самостоятельно или найти в Интернете, необходимо запастись такими комплектующими, как высокоскоростной электродвигатель с двумя валами мощностью 0,5 — 0,7 кВ т, лист стальной толщиной не менее 3 мм, арматура диаметром не менее 12 мм, пружины, металлические уголки или швеллеры.
Прежде всего, используя чертежи станка для производства шлакоблоков своими руками, необходимо вырезать металлические заготовки.Из полученных деталей сваривается форма для блоков и каркас вибростола. Двигатель будет выполнять в данном оборудовании функции вибратора . Он смонтирован на раме с поддоном и дополнен специальными держателями для обеспечения постоянного контакта с матрицей. Самодельный станок для изготовления шлакоблоков, цена которого в основном будет зависеть от стоимости используемых комплектующих, может быть дополнительно оснащен передвижной площадкой. Это облегчит использование машины на строительной площадке.
Стоимость шлакоблоков своими руками
Любой мелкофракционный строительный мусор обычно выбрасывают в бетонную смесь для шлакоблоков, что не очень правильно, но очень экономно
Стоимость шлакоблоков своими руками зависит в основном от типа блоков (фундаментные, теплоизоляционные, стеновые), их конструкции (пустотные, полнотелые), размеров, наполнителя, используемого при производстве блоков. Тип используемого оборудования также оказывает большое влияние на стоимость. При использовании недорогого самодельного оборудования можно изготовить шлакоблоки своими руками, стоимость которых составит примерно 15-20 рублей.Розничная цена таких блоков 25-50 рублей. Следовательно, самостоятельное производство бетонных блоков обходится в два раза дешевле и позволяет сэкономить довольно внушительную сумму денег.
Устройство для производства шлакоблоков своими руками в домашних условиях показано на видео:
youtube.com/embed/lpu9o-snW-I?feature=oembed» frameborder=»0″ allowfullscreen=»»>
Победители конкурса Carbon XPrizeпроизводят более качественный бетон, сдерживая выбросы CO2
Исследователи, изготовившие 10 000 модифицированных бетонных блоков, содержащих летучую золу угольной электростанции, выиграли международный конкурс на преобразование выбросов углекислого газа в полезные продукты.
CarbonBuilt, команда исследователей, связанных с Калифорнийским университетом в Лос-Анджелесе, является одним из двух победителей NRG Cosia Carbon Xprize стоимостью 20 миллионов долларов. В течение прошлого года исследователи работали на испытательном производственном объекте, используя летучую золу и дымовые газы на станции Dry Fork компании Basin Electric Power Cooperative недалеко от Джиллета, штат Вайоминг, чтобы разработать прибыльный бетонный продукт.
Этот бетонный блок за пределами Комплексного испытательного центра на станции Dry Fork компании Basin Electric входит в число 10 000 блоков, произведенных с использованием технологии улавливания углерода.
«Внедрение их технологий для предотвращения и сокращения выбросов тяжелой промышленности изменит правила игры для глобальной декарбонизации в борьбе с изменением климата», — сказал Марсиус Экставур, вице-президент XPRIZE по вопросам климата и энергетики.
Команда Калифорнийского университета в Лос-Анджелесе, начавшая исследовать этот метод в 2013 году, сократила углеродный след своего бетона более чем на 50 %, постоянно инкапсулируя CO2 в строительном бетоне, вводимом в цемент во время процесса отверждения.
Carbon Cure Technologies, вторая команда, работающая на объекте, связанном с заводом, работающим на природном газе в Канаде, разделит финальный приз в размере 15 миллионов долларов на финансирование дальнейших исследований.
10 команд-финалистов разделили 5 миллионов долларов на реализацию проектов по использованию CO2 в различных продуктах, включая пищевые добавки и пластмассы, но оба победителя были сосредоточены на улучшении качества бетона.
«Бетон — один из самых распространенных материалов в мире и важный рубеж в борьбе с изменением климата», — сказал Экставур.«На производство портландцемента, ключевого ингредиента, связывающего бетон и придающего ему прочность, приходится примерно 7% глобальных выбросов CO2».
Carbon Cure Technologies производит бетон с пониженным содержанием воды без ущерба для его надежности. Состав бетона CarbonBuilt заменяет обычный портландцемент. В нем используются недорогие отходы, что потенциально снижает затраты на хранение и утилизацию.
РаботаCarbonBuilt проводилась в Интегрированном испытательном центре Вайоминга, исследовательском центре, финансируемом штатом Вайоминг при поддержке NRECA, Ассоциации генерации и передачи трех штатов в Денвере и Басмаркского энергоэнергетического кооператива в Северной Дакоте.
«Поиск альтернативных, экономичных способов использования двуокиси углерода имеет первостепенное значение для успеха [улавливания, утилизации и хранения углерода] в Вайоминге и по всей стране», — сказал губернатор Вайоминга Марк Гордон. «Это только первая из многих возможностей для совместной работы над предоставлением технических решений проблем улавливания CO2 в Вайоминге».
Базирующаяся на угле станция Dry Fork мощностью 385 мегаватт компании Basin Electric — это электростанция, работающая на лигните, в бассейне Паудер-Ривер, штат Вайоминг. В настоящее время на этот регион приходится 40% внутреннего потребления угля.
Контроль выбросов CO2 и сокращение отходов летучей золы входят в число целей исследования «чистого угля» и считаются ключом к сохранению ценности угля как самого распространенного в мире ресурса ископаемого топлива.
«Когда мы начали этот процесс, использование углерода и невероятные возможности этой отрасли были относительно неизвестны», — сказал Джейсон Беггер, управляющий директор Интегрированного испытательного центра.
Электрические кооперативы были одними из первых сторонников глобального соревнования по продвижению исследований по использованию углерода. NRECA и его члены-кооперативы по производству и передаче тесно сотрудничали со штатом Вайоминг, чтобы создать Интегрированный испытательный центр и обеспечить исследовательские проекты для объекта.
«Поскольку мы планируем будущее, которое зависит от электричества как основного источника энергии для большей части экономики, стратегические инвестиции в энергетические инновации, которые поддерживают надежность все более сложного портфеля ресурсов, имеют решающее значение», — сказал генеральный директор NRECA Джим Мэтисон.
Два G&T сотрудничают с NRECA для поддержки и продвижения технологии улавливания и хранения углерода, финансируемой из федерального бюджета, которая включает разработку новых соединений и материалов с потенциальной коммерческой ценностью.
«Технический прогресс стимулирует экономическое развитие и более чистую энергию», — сказал генеральный директор Tri-State Дуэйн Хайли. «Углеродная XPRIZE позволила продвинуть новые технологические решения для углеродных проблем, и по мере того, как все больше новаторов приезжает в Вайоминг для оценки технологий, работа ITC будет продолжать приносить важные результаты».
Сухая вилочная станция Basin Electric, одна из самых современных угольных электростанций в стране, поддерживает текущие исследования, направленные на сокращение выбросов и проблем с отходами, связанными со сжиганием ископаемого топлива.«Мы гордимся тем, что внедряем инновации, которые могут проложить путь вперед для угля», — сказал Пол Сукут, генеральный директор и генеральный директор Basin Electric Power Cooperative. «Наш кооператив считает, что вышеперечисленная энергетическая стратегия лучше всего подходит для удовлетворения потребностей наших членов, и уголь как надежный источник топлива является ее частью».
В приведенном ниже видеоролике Марсиус Экставур из XPRIZE объясняет углеродную технологию :
Деррил Холли — штатный писатель NRECA.
(PDF) Инновационный концептуальный проект машины для изготовления бетонных блоков вручную
Проектирование и проектирование инновационных систем www.iiste.org
ISSN 2222-1727 (бумажный) ISSN 2222-2871 (онлайн)
Том 7 , № 7, 2016
41
Инновационный концептуальный проект ручного производства бетонных блоков
Машина для изготовления
Диана Старовойтова Мадара*, Саул Ситати Наманго и Даниэль Арусей
Инженерная школа Университета Мои П.O .Box 3900, Eldoret, Kenya
*Электронная почта соответствующего автора: [email protected]
Abstract
Одной из основных потребностей человека является наличие надлежащего жилья. Из-за быстрого роста населения и урбанизации
растет спрос на доступное жилье в Кении. Это обуславливает необходимость поиска путей снижения затрат на строительство, особенно для малообеспеченной группы населения.
Строительство из бетонных блоков в последнее время приобрело большое значение, однако большинство имеющихся в продаже машин для производства блоков
импортированы и также дороги. Недорогая машина для изготовления блоков местного производства могла бы оказаться полезной в
, снизив стоимость строительства. Таким образом, этот проект был направлен на завершение концептуального проектирования инновационной нетребовательной стационарной машины для производства бетонных блоков с ручным управлением
, которая формирует бетонные блоки
за долю стоимости по сравнению с вариантами с механическим приводом. Целевые спецификации были получены
из данных о потребностях клиентов, собранных во время посещений местных мастерских, и из вторичных источников,
в основном из патентов.Были разработаны три варианта дизайна; альтернативный проект № 3 был выбран с помощью взвешенной матрицы решений инженерного проекта
и методом исключения и повторного голосования (D&R). Оригинальность
этой конструкции в основном заключается в системе выталкивания: в отличие от многих доступных станков для изготовления блоков
, которые выталкивают блоки вместо формы, эта машина выталкивает форму, оставляя блоки на опорной плите
. В качестве материала для машины была выбрана мягкая сталь.Статическое моделирование модели рамы
, которая была закреплена на нижнем креплении, и общая нормальная сила 981 Н или 100 кг, приложенная к базовой плите
, было выполнено с использованием программного обеспечения для проектирования: SolidWorks, 2013 (инструмент проектирования и моделирования). ). Исследование
включало анализ напряжения, смещения и деформации. Концептуальный проект машины для изготовления бетонных блоков вручную
был оптимизирован в соответствии с результатами моделирования, расчетов и фундаментальными принципами проектирования
.Оценка стоимости показывает, что это простое и экономичное оборудование
может потенциально снизить стоимость строительства. Однако для определения потенциала авторы
предлагают провести дальнейшую работу по прототипированию и тестированию.
Ключевые слова: производство блоков, бетон, конструкция, машина.
1. Введение, постановка проблемы и цель исследования
Человечество прежде всего должно есть, пить, иметь кров и одежду, прежде чем оно сможет заниматься политикой, искусством и
религией и т. д.(Фридрих Энгельс, 1883 г.). Действительно, даже после всех новаторских достижений, открытий,
инноваций и разработок, сделанных за последние 130 лет, в науке, технике, технике и других
областях, человечество, все же, остается, по сути, таким же, как и должно быть.
удовлетворить свои основные потребности, такие как еда, кров и одежда, и только затем удовлетворять потребности, требования и желания.
Мы живем в мире, где большинство людей живет в городах, а 1 миллиард человек живет в трущобах, и к 2030 году эта цифра удвоится (UN Habitat, 2007).
Городское население растет гораздо быстрее, чем может быть
освоено и управляемо, в результате чего спрос на услуги и инфраструктуру значительно превышает предложение. Во многих городах с формирующимся рынком это оставляет большинству жителей мало вариантов, кроме как жить в
трущобах. Кения не является исключением; с одним из самых высоких в мире темпов роста населения и урбанизации
. Последняя перепись, проведенная в 2009 году, показала, что население Кении составляет 38 человек.6 миллионов по сравнению с 28,7
миллионами в 1999 году. Двадцать два процента кенийцев живут в городах, и городское население ежегодно увеличивается на 4,2 процента (CIA World Factbook, 2010). При таком уровне роста только в столице Найроби
ежегодно требуется не менее 120 000 новых единиц жилья для удовлетворения спроса, однако строится только 35 000 домов,
в результате чего дефицит жилья растет на 85 000 единиц в год. В результате этого несоответствия предложения и спроса цены на жилье выросли на 100 процентов с 2004 года (Hass Consult Property Index, 2011).Этот
вытесняет малообеспеченных жителей с официального рынка жилья в переполненные трущобы
учреждения (в среднем 5-7 человек живут в одной комнате) или толкает их еще дальше — становиться
полностью бездомными (Союз , 2013).
Миллионы жителей Кении, особенно в городе Найроби, живут в разросшихся
трущобах, а также в других неформальных поселениях вокруг Найроби (UN, 2010). Жилищная проблема Кении носит экстремальный характер.Средняя цена
квартиры в столице Найроби в настоящее время составляет 11,58 млн KES (136 000 долларов США), что на
больше, чем 5,2 млн KES (61 000 долларов США) в декабре 2000 года. На официальном рынке нет скромных домов дешевле
KES 2M (23 000 долларов США), уровень, который по-прежнему совершенно недоступен для населения с низкими доходами (Hass
Consult Property Index, 2011).
Новая конституция Кении 2010 г. включает право на достаточное жилище (статья 22), однако,
это право человека, как показано выше, еще не реализовано и, более того, не гарантировано.
Жилье играет огромную роль в оживлении экономического роста в любой стране, при этом жилье является одним из ключевых
показателей развития (Ireri, 2010). Предоставление адекватного, доступного и достойного жилья для малоимущих
Neptune предлагает передовые технологии для бетонных блоков и брусчатки
Полностью автоматическая машина NeptuneНептун предлагает завод по производству бетонных блоков по европейской технологии, который придает изделию необходимую прочность, а также различные формы и размеры.

Сегодня производство бетонных блоков представляет собой высокоавтоматизированный процесс. Технология бетонных блоков основана на принципе уплотнения тощей бетонной смеси для получения блоков правильной формы, однородных и высокопроизводительных каменных блоков. Эту технологию можно легко адаптировать для удовлетворения особых потребностей пользователей, изменив конструктивные особенности, такие как смесь, пропорции, водоцементное отношение и т. д.Машинная брусчатка Neptune имеет прочность выше М-60, что делает ее наиболее подходящей для использования на дорогах, пешеходных дорожках и в районах с интенсивным автомобильным движением.
Рекомендуется модуль крупности смешанных заполнителей от 3,6 до 4 мм и крупных заполнителей от 6 до 12 мм. Смесь для брусчатки не должна быть богаче одной части цемента на шесть частей объема комбинированных заполнителей.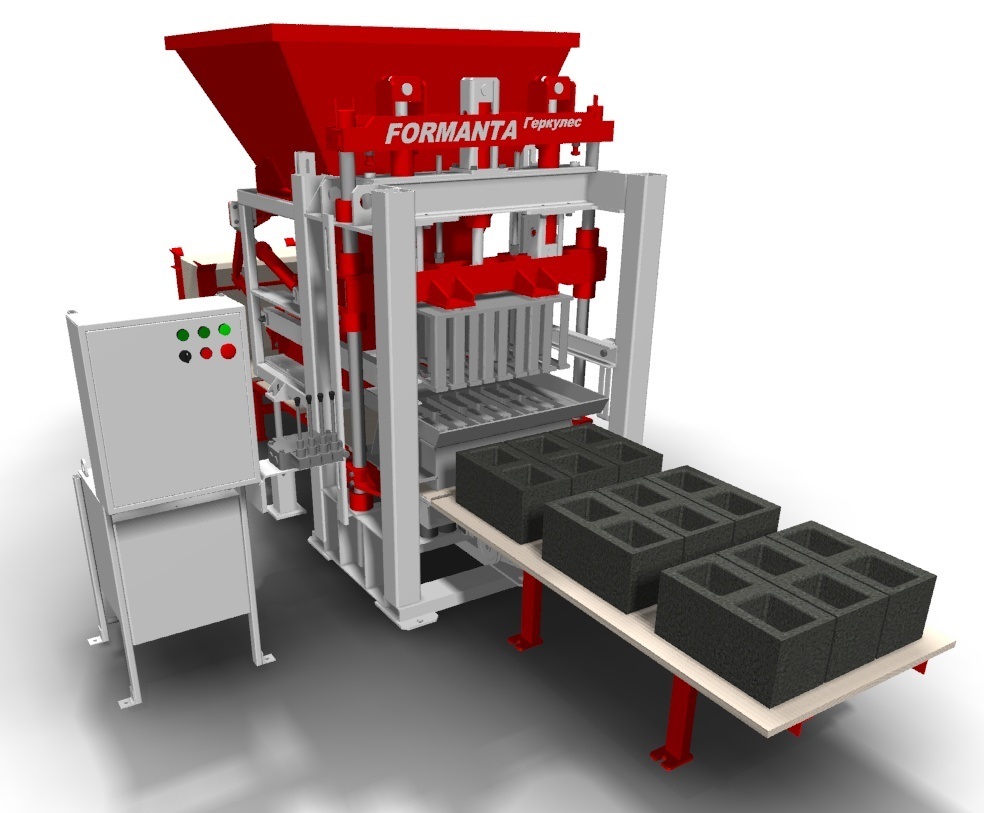
Полностью автоматический высокотехнологичный завод Neptune с автоматической системой дозирования, смесителем специальной конструкции, мощным вибропрессом и асфальтоукладчиком, а также автоматической системой штабелирования блоков, может производить от 10 000 до 1 00 000 бетонных блоков в день и асфальтоукладчиков площадью от 1 000 до 10 000 кв. день.Электрический щит управления с логикой процесса и программой был разработан специалистами компании для желаемого качественного производства и бесперебойной работы завода. Система Auto Synchronized с технологией серводвигателя была разработана для управления скоростью до миллисекунд, при этом частота и амплитуда могут задаваться индивидуально, что делает эту систему очень гибкой. Регенеративное электроснабжение завода повышает энергоэффективность всей системы. Завод по производству мобильных асфальтоукладчиков Neptune предназначен для крупных проектов дорожного строительства.Компании, которые могут инвестировать в неограниченную потребность в асфальтоукладчиках на месте, сэкономят время и энергию.
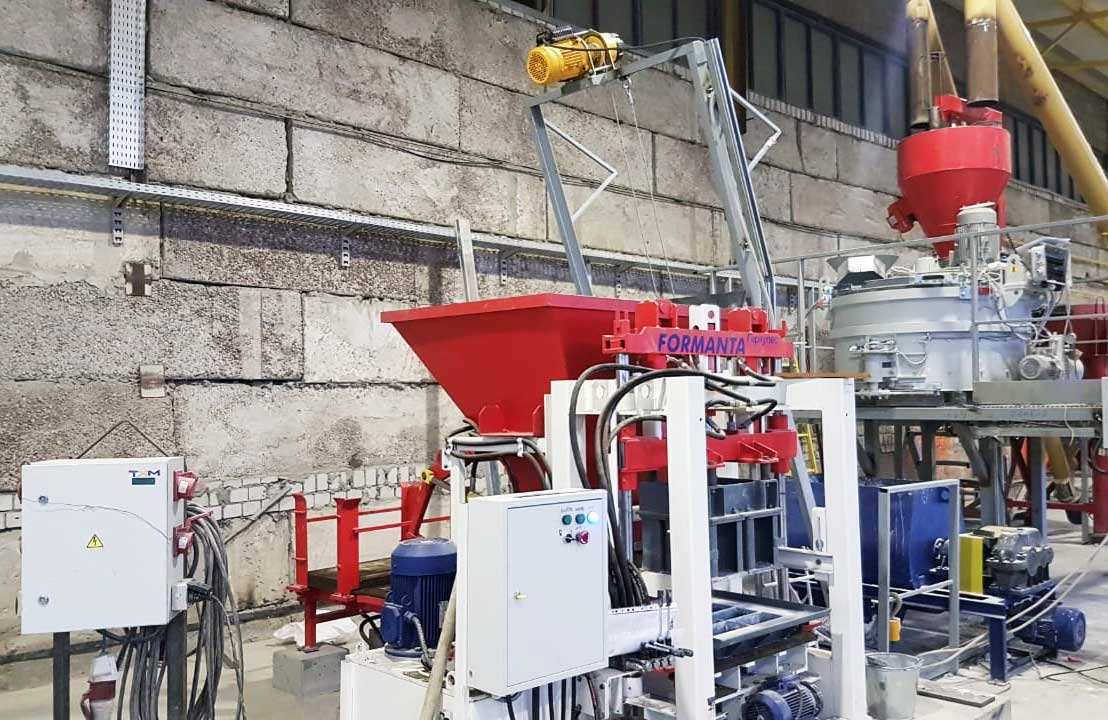
Высокопроизводительная машина для производства бетонных блоков Местное послепродажное обслуживание
Увеличьте производственные мощности с помощью крупнокалиберных машин для производства бетонных блоков , которые не только быстры, но прочны и эффективны. Эти замечательные продукты, доступные на Alibaba.com, продаются ведущими продавцами в отрасли по фантастическим ценам. Они оснащены передовыми технологиями, чтобы предоставить пользователям оптимальную производительность и удобство.Эти машины для производства бетонных блоков могут не только производить кирпичи быстрее, чем когда-либо прежде, но и потреблять мало энергии, что делает их экономически эффективными. Эти передовые машины демонстрируют превосходную производительность и предназначены для оптимального функционирования. Машины для изготовления бетонных блоков , предлагаемые на Alibaba.com, выпускаются в различных вариантах с учетом различных факторов и адаптированы для конкретных целей. Эти машины долговечны и рассчитаны на длительную эксплуатацию, устойчивы к повреждениям, обладают высокой производительностью и потребляют меньше электроэнергии по сравнению с традиционными аналогами.Эти машины для производства цементных блоков созданы для достижения совершенства. Покупатели могут просмотреть полный каталог, чтобы найти подробную информацию о каждой модели, которая поможет им принять обоснованное решение.
Машины для производства монолитных блоков из цемента производятся с использованием лучших материалов и новейших технологий в соответствии с отраслевыми стандартами. Они имеют сертификаты ISO и CE, гарантирующие качество и подлинность, а также гарантию. Продукты оснащены расширенными функциями безопасности, обеспечивающими минимальные риски для пользователей, имеют простые в эксплуатации настройки и требуют минимального обслуживания.Они поставляются с различной производительностью, чтобы удовлетворить потребности всех пользователей.
Посетите Alibaba.com, чтобы купить высокопроизводительные машины для производства бетонных блоков по экономичным ценам. Изучите коллекцию, чтобы найти модель, наиболее подходящую для ваших требований. Воспользуйтесь выгодными предложениями и сниженными ценами прямо сейчас.
Технология производства полистиролбетонных кирпичей
Полистиролбетон как строительный материал известен давно.Однако в настоящее время он вызывает все больший интерес, так как прост и удобен в изготовлении, экономичен и имеет отличные теплотехнические характеристики. Еще одним критически важным преимуществом полистиролбетонных блоков является то, что профессионалам-строителям не требуется применять тяжелую технику. Кирпичи кладут с помощью клея для полистиролбетонных кирпичей.
Технология изготовления полистиролбетонных кирпичей
Он включает в себя несколько этапов:
1.Приготовление полистиролбетона
Это делается путем смешивания сырья в смесителе (вода, химические добавки, цемент, наполнитель и пенополистирол). Сырье подается в смеситель порционно по технологии производства полистиролбетона.
2. Изготовление полистиролбетонных блоков
Это процесс заливки подготовленного полистиролбетона в предварительно смазанные формы для формирования полистиролбетонных блоков.
3. Блоки полистиролбетонные твердеющие
После заливки бетона формы, заполненные полистиролбетоном, помещают в камеру термообработки. Формы находятся в камере до того момента, когда прочность полистиролбетона достаточна для отрыва стенок.
4. Резка полистиролбетонных блоков на кирпичи с заданными размерами
Резка блока на кирпичи производится с помощью автоматизированного раскройного комплекса «АРК».
5. Упаковка и складирование полистиролбетонных блоков
Готовые кирпичи после резки укладывают на поддон и оборачивают стрейч-пленкой.
Оборудование для производства блоков из полистиролбетона
Автоматизированная линия полистиролбетона должна содержать оборудование для вспенивания полистирола, ввода, дозирования и смешивания компонентов, формы для блоков, оборудование для резки блоков на кирпичи.