Технология производства керамзита: Технология производства керамзита — Как производят керамзит
Технология производства керамзита — Как производят керамзит
Технология производства керамзита и сущность технологического процесса производства состоит в обжиге глиняных гранул по оптимальному режиму.
Для вспучивания глиняной гранулы нужно, чтобы активное газовыделение совпало по времени с переходом глины в пиропластическое состояние.
Между тем, в обычных условиях газообразование при обжиге глин происходит в основном при более низких температурах, чем их пиропластическое размягчение.
Например, температура диссоциации карбоната магния — до 600°С, карбоната кальция — до 950 °С, дегидратация глинистых минералов происходит в основном при температуре до 800 °С. А выгорание органических примесей еще ранее, реакции восстановления окислов железа развиваются при температуре порядка 900 °С, тогда как в пиропластическое состояние глины переходят при температурах, как правило, выше 1100 °С.
Схема вращающейся печи для производства керамзита:
1—загрузка сырцовых гранул; 2— вращающаяся печь; 3— форсунка; 4— вспученный керамзитовый гравий; 5—поток горячих газов
В связи с этим при обжиге сырцовых гранул в производстве керамзита необходим быстрый подъем температуры. Так как при медленном обжиге значительная часть газов выходит из глины до ее размягчения и в результате получаются сравнительно плотные маловспученные гранулы. Но чтобы быстро нагреть гранулу до температуры вспучивания, ее сначала нужно подготовить, т. е. высушить и подогреть. В данном случае интенсифицировать процесс нельзя. Так как при слишком быстром нагреве в результате усадочных и температурных деформаций, а также быстрого парообразования гранулы могут потрескаться или разрушиться (взорваться).
Оптимальным считается ступенчатый режим термообработки по С. П. Онацкому: с постепенным нагревом сырцовых гранул до 200—600 °С (в зависимости от особенностей сырья) и последующим быстрым нагревом до температуры вспучивания (примерно 1200 °С).
Обжиг осуществляется во вращающихся печах (рис.), представляющих собой цилиндрические металлические барабаны диаметром до 2,5—5 м и длиной до 40— 75 м, футерованные изнутри огнеупорным кирпичом. Печи устанавливаются с уклоном примерно 3% и медленно вращаются вокруг своей оси. Благодаря этому сырцовые гранулы, подаваемые в верхний конец печи, при ее вращении, постепенно передвигаются к другому концу барабана, где установлена форсунка для сжигания газообразного или жидкого топлива. Таким образом, вращающаяся печь работает по принципу противотока: сырцовые гранулы перемещаются навстречу потоку горячих газов,подогреваются. И, наконец, попав в зону непосредственного воздействия огненного факела форсунки,вспучиваются. Среднее время пребывания гранул в печи — примерно 45 мин.
Технология производства керамзита — оптимальный режим термообработки.
Чтобы обеспечить оптимальный режим термообработки, зону вспучивания печи, непосредственно примыкающую к форсунке, иногда отделяют от остальной части (зоны подготовки) кольцевым порогом. Применяют также двухбарабанные печи, в которых зоны подготовки и вспучивания представлены двумя сопряженными барабанами, вращающимися с разными скоростями.
В двухбарабанной печи удается создать оптимальный для каждого вида сырья режим термообработки.
Промышленный опыт показал, что при этом улучшается качество керамзита, значительно увеличивается его выход, а также сокращается удельный расход топлива.
В связи с тем, что хорошо вспучивающегося глинистого сырья для производства керамзита сравнительно мало, при использовании средне- и слабовспучивающегося сырья необходимо стремиться к оптимизации режима термообработки.
Из зарубежного опыта известно, что для получения заполнителей типа керамзита из сырья (промышленных отходов), отличающегося особой чувствительностью к режиму обжига. Используют трехбарабанные вращающиеся печи или три-четыре последовательно располагаемые печи. В которых обеспечиваются не только оптимальные скорость и длительность нагрева на каждом этапе термообработки, но и различная газовая среда.
Значение характера газовой среды в производстве керамзита обусловлено происходящими при обжиге химическими реакциями. В восстановительной среде окись железа Fe2O3 переходит в закись FeO. Это является не только одним из источников газообразования, но и важнейшим фактором перехода глины в пиропластическое состояние.
Внутри гранул восстановительная среда обеспечивается за счет присутствия органических примесей или добавок, но при окислительной среде в печи (при большом избытке воздуха) органические примеси и добавки могут преждевременно выгореть.
Поэтому окислительная газовая среда на стадии термоподготовки, как правило, нежелательна, хотя имеется и другая точка зрения, согласно которой целесообразно получать высокопрочный керамзитовый гравий с невспученной плотной корочкой. Такая корочка толщиной до 3 мм образуется (по предложению Северного филиала ВНИИСТ) при выгорании органических примесей в поверхностном слое гранул, обжигаемых в окислительной среде.
По мнению автора, при производстве керамзита следует стремиться к повышению коэффициента вспучивания сырья, так как невспучивающегося или маловспучивающегося глинистого сырья для получения высокопрочного заполнителя имеется много, а хорошо вспучивающегося не хватает.
С этой точки зрения наличие плотной корочки значительной толщины на керамзитовом гравии свидетельствует о недоиспользовании способности сырья к вспучиванию и уменьшении выхода продукции.

В восстановительной среде зоны вспучивания печи может произойти оплавление поверхности гранул, поэтому газовая среда здесь должна быть слабоокислительной. При этом во вспучивающихся гранулах поддерживается восстановительная среда, обеспечивающая пиропластическое состояние массы и газовыделение, а поверхность гранул не оплавляется.
Характер газовой среды косвенно, через окисное или закисное состояние железистых примесей, отражается на цвете керамзита. Красновато-бурая поверхность гранул говорит об окислительной среде (Fe2O3), темно-серая, почти черная окраска в изломе — о восстановительной (FeO).
Технология производства керамзита: 4 основных схемы
Различают четыре основные технологические схемы подготовки сырцовых гранул, или четыре способа производства керамзита: сухой, пластический, порошково-пластический и мокрый.
Сухой способ используют при наличии камнеподобного глинистого сырья (плотные сухие глинистые породы, глинистые сланцы). Он наиболее прост: сырье дробится и направляется во вращающуюся печь. Предварительно необходимо отсеять мелочь и слишком крупные куски, направив последние на дополнительное дробление.
Этот способ оправдывает себя, если исходная порода однородна, не содержит вредных включений и характеризуется достаточно высоким коэффициентом вспучивания.
Наибольшее распространение получил пластический способ. Рыхлое глинистое сырье по этому способу перерабатывается в увлажненном состоянии в вальцах, глиномешалках и других агрегатах (как в производстве кирпича). Затем из пластичной глиномассы на дырчатых вальцах или ленточных шнековых прессах формуются сырцовые гранулы в виде цилиндриков, которые при дальнейшей транспортировке или при специальной обработке окатываются, округляются.
Качество сырцовых гранул во многом определяет качество готового керамзита.
Поэтому целесообразна тщательная переработка глинистого сырья и формование плотных гранул одинакового размера.
Размер гранул задается исходя из требуемой крупности керамзитового гравия и установленного для данного сырья коэффициента вспучивания.
Гранулы с влажностью примерно 20% могут сразу направляться во вращающуюся печь или, что выгоднее, предварительно подсушиваться в сушильных барабанах. В других теплообменных устройствах с использованием тепла отходящих дымовых газов вращающейся печи. При подаче в печь подсушенных гранул ее производительность может быть повышена.
Таким образом, технология производства керамзита по пластическому способу сложнее, чем по сухому.
Более энергоемко, требует значительных капиталовложений. Но, с другой стороны, переработка глинистого сырья с разрушением его естественной структуры, усреднение, гомогенизация, а также возможность улучшения его добавками позволяют увеличить коэффициент вспучивания.
Порошково-пластический способ отличается от пластического тем, что вначале помолом сухого глинистого сырья получают порошок, а потом из этого порошка при добавлении воды получают пластичную глиномассу, из которой формуют гранулы, как описано выше. Необходимость помола связана с дополнительными затратами. Кроме того, если сырье недостаточно сухое, требуется его сушка перед помолом. Но в ряде случаев этот способ подготовки сырья целесообразен: если сырье неоднородно по составу, то в порошкообразном состоянии его легче перемешать и гомогенизировать; если требуется вводить добавки, то при помоле их легче равномерно распределить.
Если в сырье есть вредные включения зерен известняка, гипса, то в размолотом и распределенном по всему объему состоянии они уже не опасны.
Если такая тщательная переработка сырья приводит к улучшению вспучивания, то повышенный выход керамзита и его более высокое качество оправдывают произведенные затраты.
Мокрый (шликерный) способ заключается в разведении глины в воде в специальных больших емкостях — глиноболтушках. Влажность получаемой пульпы (шликера, шлама) примерно 50%. Пульпа насосами подается в шламбассейны и оттуда — во вращающиеся печи. В этом случае в части вращающейся печи устраивается завеса из подвешенных цепей. Цепи служат теплообменником: они нагреваются уходящими из печи газами и подсушивают пульпу, затем разбивают подсыхающую «кашу» на гранулы, которые окатываются, окончательно высыхают, нагреваются и вспучиваются. Недостаток этого способа — повышенный расход топлива, связанный с большой начальной влажностью шликера. Преимуществами являются достижение однородности сырьевой пульпы, возможность и простота введения и тщательного распределения добавок, простота удаления из сырья каменистых включений и зерен известняка. Этот способ рекомендуется при высокой карьерной влажности глины, когда она выше формовочной (при пластическом формовании гранул). Он может быть применен также в сочетании с гидромеханизированной добычей глины и подачей ее на завод в виде пульпы по трубам вместо применяемой сейчас разработки экскаваторами с перевозкой автотранспортом.
Керамзит, получаемый по любому из описанных выше способов, после обжига необходимо охладить. Технология производства керамзита.
Установлено, что от скорости охлаждения зависят прочностные свойства керамзита. При слишком быстром охлаждении керамзита его зерна могут растрескаться или же в них сохранятся остаточные напряжения, которые могут проявиться в бетоне. С другой стороны, и при слишком медленном охлаждении керамзита сразу после вспучивания возможно снижение его качества из-за смятия размягченных гранул. А также в связи с окислительными процессами, в результате которых FeO переходит в Fe2O3, что сопровождается деструкцией и снижением прочности.
Сразу после вспучивания желательно быстрое охлаждение керамзита до температуры 800—900 °С для закрепления структуры и предотвращения окисления закисного железа. Затем рекомендуется медленное охлаждение до температуры 600—700 °С в течение 20 мин для обеспечений затвердевания стеклофазы без больших термических напряжений, а также формирования в ней кристаллических минералов, повышающих прочность керамзита. Далее возможно сравнительно быстрое охлаждение керамзита в течение нескольких минут.
Технология производства керамзита
Первый этап охлаждения керамзита осуществляется еще в пределах вращающейся печи поступающим в нее воздухом. Затем керамзит охлаждается воздухом в барабанных, слоевых холодильниках, аэрожелобах.
Для фракционирования керамзитового гравия используют грохоты, преимущественно барабанные — цилиндрические или многогранные (бураты).
Внутризаводской транспорт керамзита — конвейерный (ленточные транспортеры), иногда пневматический (потоком воздуха по трубам). При пневмотранспорте возможно повреждение поверхности гранул и их дробление. Поэтому этот удобный и во многих отношениях эффективный вид транспорта керамзита не получил широкого распространения.
Фракционированный керамзит поступает на склад готовой продукции бункерного или силосного типа.
Технология производства керамзита, раскрыта не в полной мере в данной статье. Но, если у Вас появились вопросы, то можете задать их нашим менеджерам в любое удобное время.
Керамзит – состав и технология производства, свойства, виды, область применения
Керамзит – легкий гранулированный материал с пористой структурой, продукт ускоренного обжига при сверхвысоких температурах глины и глинистых сланцев. Представляет собой керамические шарики с плотной спекшейся оболочкой темно-бурого цвета, почти черного на изломе.
Технология получения керамзита
Сырьем для его производства являются определенные сорта глины – легкоплавкие, имеющие в составе до 30 % кварца, вспучивающиеся – с повышенным содержанием окислов железа (не менее 6 %) и органических веществ. При необходимости для усиления вспучивания проводят обогащение сырца мазутом или соляровым маслом.
Наиболее распространены два варианта производства керамзитовой продукции.
Пластичный (мокрый) способ
Подготовленная природная глина с влажностью не более 30 % проходит два этапа помола специальными зубчатыми вальцами – грубый и тонкий. В результате получают первичные гранулы диаметром в 5–10 мм, которые подают в сушильный барабан. Здесь полуфабрикат подсушивается и проходит окончательную обкатку, приобретая овальную форму. Только после этого начинается обжиг в печи с помощью высоких температур (800–1350⁰ С) и при постоянном вращении.
Сухой способ
В случае получения керамзита из плотного материала – каменистых глинистых пород, сланца – используют сухую технологию. Исходное сырье размельчают на специальном дробильном оборудовании до зерен размером в 1–20 мм. Сырец обжигают в барабанных печах, охлаждают и разделяют по фракциям. При таком способе производства отсутствует этап формовки зерна, поэтому продукт имеет кубические угловатые очертания.
Изготовление керамзита в промышленных объемах
Технические и эксплуатационные свойства
Благодаря техническим параметрам и рабочим показателям, керамзит выгодно выделяется в категории инертных материалов.
- Обладает оптимальным сочетанием прочности и веса. Продукцию М500, М700, М800 используют для изготовления стенового материала, перекрытий, в мостостроении, т. е. там, где особенно важны прочностные характеристики наряду с уменьшением массы конструкций.
- Благодаря пористой структуре, обладает хорошей гигроскопичностью, обеспечивает естественную циркуляцию воздуха.
- Является универсальным утеплителем, который по теплоизоляционным свойствам сравним с натуральной древесиной, а в отдельных случаях и превосходит ее на 10–15 %. Теплопроводность в пределах 0,07– 0,16 Вт/м позволяет избегать до 70 % потерь тепла.
- Пройдя обработку при сверхвысоких температурах, материал полностью огнеустойчив и пожаробезопасен.
- Имеет низкий уровень водопоглощения (не более 25 %), выдерживает до 50 циклов сезонного замораживания.
- Характеризуется минимальным уровнем усадки – коэффициент не более 0,14 мм/м.
- Состоит только из экологически чистых компонентов натурального происхождения.
Классификация
По параметрам и конфигурации зерен различают следующие виды керамзита.
- Керамзитовый щебень. Отличительная черта – зерно произвольной, чаще кубической угловатой формы размером от 5 до 40 мм.
Получают сухим способом дробления вспученных глинистых масс.
- Керамзитовый гравий. Имеет сферическую окатанную форму, делится на три фракции (5–10 мм, 10–20 мм, 20–40 мм).
- Керамзитовый песок. Получают путем отсева мелкой фракции – до 5 мм, с самым большим насыпным весом (до 1300 кг/м3).
В зависимости от насыпной плотности керамзит подразделяют на очень легкий (250–300 кг/м3), легкий (до 500 кг/м3), средний (до 700 кг/м3), тяжелый (свыше 700 кг/м3).
Прочность, а, значит, и сферы использования керамзита зависят от насыпного веса. Легкая продукция годится для применения насыпом, тяжелая – в качестве заполнителя в бетоны, стеновые блоки, панели, плиты.
Сферы использования
Этот инертный материал искусственного происхождения востребован в строительной индустрии, сельском хозяйстве, ландшафтной планировке территорий.
Более 60 % производимого продукта уходит на изготовление керамзитобетона, бетонной стяжки, несущих строительных конструкций – стеновых панелей, блоков, межэтажных перекрытий.
Керамзитобетонные блоки – достойная альтернатива тяжелым бетонам
На теплоизоляционные засыпки расходуется примерно четверть продукции, как правило, более крупного размера. Идеально подходит для утепления насыпом полов, чердаков, отмостки, теплотрасс. В качестве теплоизоляционного заполнителя популярен в каркасном домостроении.
Благодаря высоким дренажным возможностям находит широкое применение в садоводстве – при разбивке газонов как составляющая часть грунта для посадки комнатных растений и субстрат для гидропоники, а также в декоративных целях в ландшафтном проектировании.
Технология производства керамзита — процесс изготовления и способы получения
- Керамзит
- — легкий и прочный заполнитель, не содержащий никаких вредных для бетона примесей и не вызывающий коррозии стальной арматуры. Он отличается высокой морозостойкостью и огнестойкостью.
Объемный вес его зависит от характера сырья и условий обжига и может изменяться от 300 до 1000 кг/м3; при повышении объемного веса прочность керамзита увеличивается. Керамзит был предложен и впервые получен проф. Е. В. Костырко, а методы заводского изготовления керамзитового гравия разработаны С. П.Онацким.
Керамзит, применяемый для изготовления керамзитожелезобетона, представляет собой пористый заполнитель ячеистого строения, получаемый ускоренным обжигом легкоплавких глин при температуре их вспучивания (1100—1.400°С).
Отличительной особенностью керамзита по сравнению с другими пористыми заполнителями является его относительно высокая прочность при малом объемном весе. В зависимости от принятой технологии производства зерна керамзита могут иметь различную форму (гравия или щебня, а также песка). Свойства керамзита зависят от свойств исходного глинистого сырья и условий его подготовки, обжига, охлаждения и последующей обработки (например, путем дробления, рассева).
Сырье для керамзита
Сырьем для керамзита являются легкоплавкие глинистые породы. Добывают её в карьере открытом способом. Из карьера глина транспортируется в глинозапасник, где она отлёживается перед обработкой. После их добычи до обжига глинистые породы могут подвергаться различным способам подготовки для получения полуфабриката в виде цилиндриков (жгутов), сфероидов или крошки.
Для приготовления керамзита применяют обычно глинистую породу с коэффициентом вспучиваемое при обжиге не менее 2,5 и объемным весом в куске после обжига не более 1200 кг/м3. Используют разнообразные глинистые породы: сланцы, обычные глины, лессы, бентониты и т. д.
Глинистая порода, применяемая для производства керамзита, ориентировочно должна содержать:
- 6—10% окислов железа,
- 10—25% глинозема,
- 50—60% кремнезема,
- не более 8% карбонатов
- не более 2,5—5% щелочей.
В минералогическом отношении сырье для приготовления керамзита характеризуется наличием глинистого минерала монтмориллонита, слюды и гидрослюдных минералов. Благоприятным признаком является присутствие в глине таких минералов, как мусковит, биотит, маловыветренные гидрослюды, роговая обманка.
Допускается также примесь в сырье тонкодисперсных органических веществ, так как это позволяет снижать расход топлива для обжига керамзита.
Способы подготовки сырья
Различают
- пластический,
- сухой
- мокрый способы подготовки сырья.
Наиболее экономичным является сухой способ подготовки сырья, наиболее дорогим — мокрый, хотя он позволяет получить более однородный полуфабрикат для обжига. Способ подготовки выбирают в зависимости от свойств сырья и требований к готовой продукции.
Если необходимо получить готовый продукт
- в виде керамзитового гравия — то для обжига сырья применяют короткие (длиной 11- 40 м) вращающиеся одно- или двухбарабанные печи;
- для изготовления керамзитового дробленого щебня можно применять и другие тепловые агрегаты (например, агломерационные машины).
Обычно температура материала в зоне вспучивания вращающейся печи находится в пределах от 1100 до 1200°С. Температуру зоны вспучивания керамзита устанавливают в зависимости от свойств исходного сырья и условий его подготовки.
После обжига керамзит охлаждают и рассеивают на отдельные фракции. Крупные зерна в ряде случаев дополнительно подвергают дроблению для получения керамзитового песка или керамзитового щебня.
Технология подготовки, обжига и охлаждения керамзита существенно влияет на его свойства и на качество приготовленного на данном заполнителе керамзитожелезобетона. Но в первую очередь на качество керамзита влияют свойства исходного сырья.
При изготовлении керамзита устанавливают допустимый предел вспучивания сырья, который позволит получить готовый продукт с требуемой прочностью и объемным весом. Чрезмерное вспучивание, хотя и дает легкий продукт, но резко снижает прочность зерен. Огнеупорность глинистых пород, обжигаемых во вращающихся печах, должна быть не более 1350°, а обжигаемых на решетках— не более 1450°С.
В некоторых случаях вспучиваемость глинистой породы при обжиге можно улучшить введением в шихту следующих добавок (по весу): древесных опилок, солярового масла, молотого каменного угля, мелкого торфа или пылевидной железной руды — от 1 — 4%, глины охристой — от 6 до 15% или глины огнеупорной — от 10 до 20% и других добавок.
Для повышения вспучиваемости обжигаемого сырья, кроме выбора глиняной породы и введения в нее добавок, необходимо правильно выбрать газовую среду в печи, так как в зависимости от содержания в среде кислорода вспучиваемость может изменяться 2—3 раза, а необходимая температура обжига отклоняется на 100—200°.
Кроме того, важно выбрать и обеспечить правильный режим обжига для данного вида сырья (например, температуру обжига, время нахождения сырья в различных зонах обжига, скорость вращения печи, объем заполнения топочного пространства, длину факела, режим охлаждения и т. д.).
Для обжига керамзита применяют твердое, жидкое или газообразное топливо. Продолжительность обжига сырья колеблется, как правило, в пределах 25—50 мин.
Процесс изготовления керамзита для производства бетона
Керамзит — материал ячеистого строения, получающийся из глин при особом режиме их обжига, который способствует их вспучиванию и характеризуется тем, что в период появления в обжигаемых глинах эвтектических расплавов одновременно происходит газообразование.
Для производства керамзита пригодны многие виды глин, обладающих свойством вспучиваться. Это свойство зависит главным образом от наличия в глинах достаточного количества окислов железа и органических примесей.
Производство керамзитового гравия состоит из следующих операций
- подготовки глиняной массы;
- формования из нее жгутов, разрезаемых на небольшие цилиндры;
- окатывания цилиндров в сфероиды;
- обжига (обычно при 1100—1200°) в восстановительной среде и при быстром подъеме температуры;
- сравнительно медленного остывания.
При обжиге глиняных сфероидов в коротких вращающихся печах получают пористый керамзитовый гравий, имеющий округлую форму со сравнительно гладкой поверхностью. Гравий менее правильной формы и керамзитовый песок получаются при обжиге дробленых глинистых сланцев или подсушенной глины. В этом случае подготовка сырья упрощается, так как отпадает необходимость в изготовлении сфероидов.
Видео производство керамзита
Технология производства керамзита
Как известно, слово “керамзит” имеет греческое происхождение и означает “обожженная глина”. Технология производства материала заключается в подготовке глины и последующем тепловом ударе, в результате которого она приобретает вид вспученных гранул, ее внешняя оболочка оплавляется и таким образом герметизируется. Так можно описать процесс вкратце, но давайте рассмотрим его поподробнее.
Керамзит изготавливают из осадочных глинистых и метаморфических камнеподобных пород (глинистые сланцы, аргиллит и т.п.). Они неоднородны, в их составе есть включения кварца, полевого шпата, гидрослюды, железистых и органических примесей. Из всего многообразия сырья лучше всего использовать глины, содержание кварца в которых не превышает 30%.
Для того, чтобы узнать, насколько определенный материал подходит для изготовления качественного керамзита, проводят специализированные исследования — проверяют легкоплавкость, возможность и уровень вспучивания во время обжига, а также его интервал.
Для увеличения коэффициента вспучивания в состав добавляют разнообразные натуральные и искусственные компоненты — мазут, соляровое масло, алунит, перлит и др.
В процессе переработки материалов из сырца получают гранулы. Их сушат, обжигают в печи и охлаждают. Гранулы имеют различный размер и состав, поэтому их сортируют, а при необходимости дробят для получения более мелких фракций. После этапа сортировки керамзит можно складировать, фасовать и отправлять на место использования.
Керамзитовые гранулы получают четырьмя способами: сухим, мокрым, пластическим и порошково-пластическим. Выбор напрямую зависит от качества исходного сырья.
Сухой способ применяют для камнеподобных составов, однородных пород, в которых нет вредных компонентов. Сырье подвергают дроблению и помещают в печь с вращающимся барабаном.
Мокрый способ (иначе — шликерный) заключается в том, что глину укладывают в специальные емкости и разводят водой. Полученную массу называют шликером. Его подают сначала в шламбассейн и далее в печь. В барабане печи материал дробится на гранулы, сушка происходит посредством выделяемого газа. Данный способ более затратный, поэтому его применяют в том случае, когда исходное сырье чрезмерно влажное.
Наиболее распространен пластический способ. Рыхлое сырье увлажняют и перерабатывают в вальцах. Далее из полученной массы изготавливают гранулы и запекают их в печи. Пластика позволяет создавать материал с самыми лучшими эксплуатационными свойствами, его структура гомогенизируется и имеет довольно высокий коэффициент вспучивания.
В случае использования порошково-пластического способа сухое сырье в виде порошка разводят водой. Из полученного состава формируют гранулы, запекают и сушат. Этот способ предполагает дополнительные затраты, т.к. глинистые породы нужно предварительно измельчить, а готовый материал высушить.
Финальным этапом производства керамзита является охлаждение гранул. Оно начинается еще в печах, т.к. в барабан поступает воздух извне, а далее материал перемещают в аэрожелоба, барабанные холодильники и другие установки.
Прочность керамзита также во многом зависит от скорости охлаждения. Необходимо строго придерживаться технологии, ведь если процесс будет слишком быстрым, гранулы потрескаются, а если наоборот, медленным — керамзит размягчится.
В идеале охлаждение должно происходить по следующей схеме: непосредственно после вспучивания гранул их нужно охладить до 800-900 градусов Цельсия, а далее в течение 20 минут постепенно понижать температуру до 600-700. После этого охлаждать материал можно в любом темпе. В таком случае нет высокого термического напряжения. Это приводит к тому, что в керамзите формируются кристаллические минералы, увеличивающие его прочность.
Керамзитовый завод: технология производства керамзита
3. Сушка сырьевых гранул
Технология производства керамзита
1. Добыча и хранение сырья
Разработка месторождений глинистых пород обычно выполняется открытым способом. Выделяют месторождения мягких и камнеподобных глинистых пород.
Для переработки мягкого глинистого сырья обычно используют различного рода ковшовую технику (экскаваторы, фронтальные погрузчики), которые, как правило, ведут разработку по всей высоте уступа, без разделения на отдельные пласты.
В случае разработки камнеподобных глинистых пород (аргеллиты, сланцы) первоначально производятся буровзрывные работы.
Разработка и добыча мягких глинистых пород производится сезонно (в период промерзания не производится), разработка камнеподобного сырья ведется круглогодично.
Вылеживание глиняного сырья в течение нескольких месяцев происходит в промежуточных конусах на открытом воздухе, благодаря чему в результате температурных воздействий (переменного увлажнения, высушивания, мороза) и выветривания происходит разрушение естественной структуры глиняного сырья, что в дальнейшем существенно облегчает его обработку.
Для обеспечения непрерывности производственного процесса, а также для производства керамзита в зимний период (предотвращение промерзания), хранение запасов сырья осуществляется в глинохранилищах.
2. Переработка исходного сырья
Способ переработки исходного сырья зависит от его характеристик. Существует четыре технологические схемы переработки исходного сырья (производства керамзитового гравия):
сухой способ — самый простой способ производства керамзита, который заключается в дроблении исходного материала с последующим обжигов во вращающихся печах.
Как правило, данный способ применим только к камнеподобному глинистому сырью, которое должно иметь однородный состав (исключать вредные включения), достаточно высокий коэффициент вспучивания и влажность не более 9%.
мокрый (шликерный) способ — данный способ заключается в разведении глины в воде в специальных емкостях (глиноболтушках), в результате чего получают глиняную жижу — шликер (влажностью не менее 50%), который в последствии подается в шликербассейны, а затем во вращающиеся печи. Во вращающихся печах устанавливаются «бьющие» цепи, за счет нагрева которых происходит высушивание шликерной массы и дальнейшее ее размельчение на керамзитовый гранулы.
пластический способ — способ, получивший наибольшее распространение. Данный способ напоминает производство керамического кирпича. Первоначально разрыхленное исходное сырье в увлажненном состоянии перерабатывают в вальцах (или глиномешалках), затем из полученной пластичной массы на ленточных шнековых прессах, либо дырчатых вальцах, формуются гранулы (похожие на цилиндр), которые при дальнейшей обработке окатываются и округляются.
порошково-пластичный способ — способ, который отличается от пластичного лишь структурой исходного сырья. В данном случае исходное сырье не рыхлится, а производится его помол. Затем глиняный порошок увлажняется и формуется в гранулы.
Сушка и обжиг сырьевых керамзитовых гранул производится во вращающихся пачах керамзитового завода. С целью исключения слипания сырьевых гранул в печи может производится дополнительная сушка гранул в сушильных барабанах, где сырьевые гранулы окатываются и становятся прочнее. Также возможно применение слоевых подготовителей, которые также выполняют первоначальную подсушку сырья до нулевой влажности и предварительный нагрев перед обжигом.
Обжиг сырьевых гранул на заводе керамзитового гравия является основным технологическим звеном производства керамзита.
Очень важное значение имеет момент совпадения активного газовыделения с переходом гранул в пиропластическое состояние глины (заьвердевание). Как правило, данный момент происходит при температуре свыше 1100° С.
При обжиге сырьевых гранул необходим быстрый подъем температуры, чтобы влага, находящаяся в сырье, не успела выпариться. В противном случае, гранулы получатся более мелкими и тяжелыми (не вспученными).
Самыми распространенными на керамзитовых заводах считаются однобарабанные вращающиеся печи диаметром 2,0-2,5 метра, длиной 35-40 метров, имеющие уклон 3-5%.
Благодаря чему гранулы постоянно перемешиваются, окатываются и обжигаются, передвигаясь вниз по барабану печи на встречу потоку горячего воздуха.
4. Сортировка керамзита по фракциям
Сортировка полученной продукции по фракциям осуществляется в установках типа «грохот». Обычно применяют барабанно-циллиндрические грохоты, реже — многогранные (бураты).
После сортировки керамзит направляют к месту хранения (складирования) используя конвейерные (ленточные) транспортеры, либо пневматические. Последние не получили особого распространения в силу того, что при данном виде транспортирования возможно повреждение гранул и даже их дробление.
Технология производства керамзита
Получение керамзита осуществляется путем обжига гранул глины при соблюдении режимных параметров. Для этого необходимо применение ступенчатой термообработки, что означает последовательное нагревание гранул сырца до 200—600 °С, а затем быстрое нагревание до 1200 °С.
Процесс обжига гранул
Выполнение обжига гранул, как это предусматривается технологией производства керамзита, происходит в печах, которые представляют собой барабаны из металла и имеют цилиндрическую форму и размеры: диаметр 2,5—5 м и длину 40— 75 м. Внутри печи футерованы огнеупорным кирпичом. Они располагаются под уклоном около 3% и вращаются вокруг собственной оси. Иногда зона вспучивания может отделяться от подготовительной зоны при помощи кольцевого порога. Гранулы находятся в печи около 45 минут.
Могут использоваться печи, имеющие два барабана, которые вращаются в разные стороны, в них расположены зоны вспучивания и подготовки. Опыт показывает, что обжиг в таких печах улучшает качество керамзита, увеличивает выход материала и сокращает расход технологического топлива.
Способы подготовки гранул
Гранулы сырца проходят подготовительный этап перед отжигом путем применения четырёх технологических способов:
- Сухой — применяется для камнеподобного сырья глины, подлежащего дроблению и поступающего в печь;
- Пластический — наиболее распространен: сырьё подлежит переработке в увлажненном состоянии, затем происходит формирование гранул сырца. Гранулы при влажности до 20% могут направляться в печь или, что более выгодно, их надо подсушивать в сушильных барабанах. Это позволяет повысить производительность печи;
- Порошково-пластический — заключается в получении порошка из глины, а затем после добавки воды получается пластичная масса, из которой формуются гранулы;
- Мокрый(шликерный) — глина разводится в спецёмкостях, с подачей пульпы в печи.
Процесс охлаждения
Технологическим процессом предусмотрено, что продукт, полученный по любому из приведенных методов, после обжига должен быть охлажден. Причем, скорость охлаждения гранул оказывает влияние на качественные характеристики керамзита: рекомендуется быстро охладить массу до 800—900 °С, а затем в течение 20 минут продолжить ее медленно охлаждать до 600—700 °С, и снова – быстро охлаждать несколько минут.
Получение керамзита определенных фракций осуществляется с помощью барабанных грохотов. После всех технологических операций керамзит во фракциях доставляется на склад для отправки потребителю.
Похожие материалы:
Технология производства керамзита | Новости в строительстве
Технология производства керамзита основана на способе термоудара с обжигом гранул в монослое, при этом для его получения используется кольцевая (карусельная) печь с вращающимся подом. Такая печь применяется в металлургической промышленности с некоторыми конструктивными изменениями, для закладки стального литья.
Керамзит является основным видом искусственных пористых заполнителей используемых в строительстве, на долю которого приходится свыше 68% объема производства. Получают керамзит из слабовспучивающихся глин, но с повышенным содержанием карбонатных примесей. Технология производства легкого керамзитового гравия, предложенная ЦНИИЭПсельстроем исходит из следующих предпосылок:
1. Скорость нагрева должна быть максимальной, так как это способствует сохранению большей части паров и газов, обусловливающих поризацию.
2. Оптимальная температура обжига гранул ограничивается верхним пределом интервала вспучивания и температурой размягчения глин.
Технология производства керамзита основана на способе термоудара с обжигом гранул в монослое, при этом для его получения используется кольцевая (карусельная) печь с вращающимся подом. Такая печь применяется в металлургической промышленности с некоторыми конструктивными изменениями, для закладки стального литья.
Читать далее на http://stroivagon.ru азерит
Такая печь считается более удачной в технологическом плане. так как она лишена тех недостатков, которые возникают во вращающихся печах, в пересыпающемся слое во время обжига. При этом удается избегать перетирании гранул керамзита и значительные теплопотери в процессе производства.Технология производства керамзита способом термоудара состоит из следующих основных операций:
Читать далее на http://stroivagon.ru -гравий керамзитовый
1. Изготовление сырцовых гранул, сушку сырцовых гранул и предварительную термоподготовку гранул на оборудовании существующих керамзитовых заводах.
2. Обжиг керамзитовых гранул в кольцевой печи и охлаждение керамзита.
Керамзит имеющий наименьшую среднюю плотность образуется в условиях термоподготовки гранул при температуре 200…250°С в течении 25…35 минут.Термоподготовка гранул керамзита в течении 25 минут и более при температуре 300 °С и выше увеличивает плотность гранул на 60…70 %. Установлены следующие оптимальные режимы предварительной термоподготовки гранул керамзита:
1. Сушка в сушильном барабане при температуре 100…120°С в течении 30 минут до остаточной влажности в пределах 12…17 %.
2. Термообработка в течении 25 минут при температуре 200…250°С до остаточной влажности 0…3 %.
Определение оптимальных параметров вспучивания гранул производилось для способа термического удара. При этом замечено что обжиг гранул керамзита из курского суглинка способом термического удара в температурном интервале вспучивания позволяет получить легкий керамзитовые гранулы со средней плотностью 400 кг/м³. То есть на 32 % ниже средней плотности керамзитовых гранул полученных во вращающихся печах (570…600 кг/м³).
Для наглядности основные физико-механические свойства керамзита, полученного способом термоудара в кольцевой печи, приведены в таблицу № 1.
Таблица № 1. Основные физико-механические свойства керамзита, полученного способом термоудара в кольцевой печи
При обжиге гранул керамзита из глины способом термоудара получен керамзит со средней плотностью 280…425 кг/м³. Такие гранулы имеют величину средней плотности значительно ниже, чем керамзитовые гранулы полученные во вращающихся печах. при этом поверхность гранул керамзита получается частично оплавленной но шероховатой и структура равномерно пористая.
Легкий керамзит полученный из слабовспучивающихся глин способом термоудара в кольцевой печи (смотри рисунок-1) выдерживает более 400 циклов замораживания-оттаивания без признаков разрушения (ГОСТ 9753-81*). При этом керамзит имеет сравнительно низкое водопоглощение которое можно объяснить частичным оплавлением его поверхности в процессе производства.
При этом кислотостойкость керамзитовых гранул составляет примерно 90…98 %, а щелочестойкость в пределах 50…60 %. Керамзитовые гранулы показали высокую водостойкость, а коэффициент размягчения составляет всего 0,95…0,96. С использованием в строительстве этого керамзита был получен конструктивный теплоизоляционный керамзитобетон со средней плотностью 850…950 кг/м³, имеющий прочность при сжатии в пределах 3,5…6 МПа.
Предварительный технико-экономический анализ эффективности производства керамзитового гравия способом термоудара показал что снижение средней плотности керамзита в два раза позволит снизить его заводскую себестоимость примерно на 50 %. Разработан проект технологической линии производства керамзитовых гранул способом термоудара в кольцевой (карусельной) печи производительностью 100 тысяч м³ в год.
Производство керамзита
Предложенный способ производства включает сушку и трехстадийную скоростную термообработку гранул керамзита:
1. Предварительная термоподготовка в течении 20…40 минут до 200…400°С.
2. Скоростной подъем температуры до 800…1100°С и изотермическая выдержка при конечной температуре до 10 минут.
3. Вспучивание-скоростной подъем температуры до 1150…1250 °С и изотермическая выдержка при конечной температуре до 5 минут.
Дополнительная термоподготовка при температуре 800…1100°С обеспечивает образование в гранулах окисленной оболочки различной толщины. Характерной особенностью обжига в неподвижном монослое является то, что окисленная оболочка не подвергается абразивному истиранию как при обжиге в пересыпающемся слое и сохраняется до стадии вспучивания.
Это обеспечивает вспучивание гранул при оптимальной температуре без межзернового агрегирования.
Рисунок-1. Технологическая схема обжигового агрегата. Кольцевая печь для получения керамзита способом термоудара.
1- кладка печи, 2-газовоздухопроводы, 3-выгружатель слоев, 4-вентиляционная система, 5- дутьевые вентиляторы , 6-аэрожелоб, 7 вращающийся под печи, 8-привод пода.
Кольцевая печь с внешним диаметром 15 м состоит из стационарных стен и свода, вращающегося футерованного пода , опорно-упорной системы и ванн гидрозатвора. Толщина стационарных ограждений печи 0,8 м, футеровка пода -0,5 м. Диаметр средней окружности пода и ее длина соответственно- 11,2 и 35,5 м( в том числе 30 метров -зона обжига ), ширина канала печи -2,4 м, высота от поверхности пода до замка свода -0,75 м.
Кольцевой канал заканчивается дымоотборной шахтой, из которой дымовые газы подаются в слоевой подготовитель и далее выбрасываются в атмосферу с помощью концевого дымососа. В обжиговом агрегате технологический процесс осуществляется следующим образом:
Термоподготовительные сырцовые гранулы подаются монослоем барабанным разгружателем на вращающийся под печи и перемещаются в зону горения топлива где происходит их вспучивание. Керамзит с поверхности пода удаляется выгружателем и охлаждается в холодильнике. Полученные в период эксплуатации технологические и теплотехнические показатели опытно-промышленного агрегата приведены в таблицу№ 2, в сравнении с аналогичными характеристиками однобарабанной печи 2,5 х 40 м Кольчугинского ССК.
Таблица №2. Физико-механические показатели печных агрегатов
Эти данные а также результаты испытаний привозных глин свидетельствуют о снижении насыпной плотности керамзита на 25…40 % и удельного расхода топлива на 35…45 % по сравнению с производством в однобарабанных печах. Более высокие показатели обжигового агрегата с кольцевой печью обусловлены его следующими тепло-технологическими особенностями.
Обжиг монослоя гранул в стационарных условиях осуществляется при оптимальных температурах вспучивания с перепадом по ширине канала печи ± 5°С без опасности интенсивной агломерации материала. Небольшие конгломераты, образованные точечными сварами гранул, легко разрушаются при падении в приемную течку.
Стабильность температурного режима в печи позволяет использовать для производства керамзита глины с короткими ( менее 50°С) температурными интервалами вспучивания. Следствием интенсификации процесса теплообмена является повышение скорости нагрева материала до 300…350°С/мин, чем обеспечивается скоростной режим обжига-термический удар.
Данные факторы обеспечивают снижение насыпной плотности керамзита на 25…40 % по сравнению с производством во вращающихся печах. Более совершенная тепловая схема кольцевой печи по сравнению с барабанными обеспечивает снижение расхода топливана обжиг в результате снижения теплопотерь с отходящими печными газами при сжигании топлива при относительно небольших коэффициентах избытка воздуха (а=1,3…1,35).
Это объясняется наличием многочисленных горелочных устройств и хорошей герметизацией печного пространства. А также увеличением толщины теплоизоляции, рекуперацией тепла отходящих печных газов путем подогрева первичного воздуха до 300…350°С.
Эти факторы, а также применение эффективного запечного теплообменника-слоевого подготовителя -обеспечивают снижение удельного расхода топлива на 52…60 кг/м³условного топлива. Конструктивные особенности кольцевой печи обеспечивают более высокие эксплуатационно -технические показатели по сравнению с барабанными печами.
При этом существенным преимуществом является сокращение эксплуатационных расходов на ремонт футеровки печи, что обусловлено долговечностью стационарной кладки печи и футеровка пода.
***** РЕКОМЕНДУЕМ выполнить перепост статьи в соцсетях! *****
Вращающиеся печи по производству керамзитового агрегата
Керамзитовый заполнитель, также называемый exclay, или легкий керамзитовый заполнитель (LECA), является полезным материалом во все большем числе отраслей промышленности, в первую очередь в строительстве и садоводстве, на очереди которых, вероятно, будут приложения для очистки воды и фильтрации.
Уникальная структура и физические свойства керамзита, которые позволяют использовать его в различных областях, производятся в результате тщательно контролируемой термической обработки (обычно называемой прокаливанием или спеканием), проводимой во вращающейся печи.
Термическая обработка керамзитового заполнителя (прокаливание или спекание)
Свойства керамзита, которые делают его идеальным для использования в определенных областях, достигаются благодаря высокотехнологичному производственному процессу.
Глины обычно измельчают, агломерируют и / или сушат в качестве средства подготовки сырья, хотя этот процесс может варьироваться. Экструзия кажется предпочтительным методом агломерации в этой обстановке, но можно также изучить другие методы.
В то время как подготовка исходного сырья важна для производства заполнителей керамзита, ключевым процессом, лежащим в основе заполнителей керамзита, является термическая обработка.От этой термической обработки произошло название керамзитового заполнителя, поскольку он используется для физического расширения частиц глины.
Для описания таких методов термической обработки используются различные термины. В таких условиях обработка обычно называется прокаливанием или спеканием. Хотя эти два термина часто используются как синонимы, важно отметить, что технически они относятся к разным методам. Поскольку спекание технически происходит при гораздо более высоких температурах, для целей этой статьи мы будем называть его прокаливанием, хотя в некоторых случаях расширенные агрегаты могут быть действительно спеченными.
В случае керамзита прокаливание играет важную роль в создании продукта, который может служить заполнителем керамзита. Температура, обычно от 1050 ° C до 1250 ° C, вызывает выделение газов в результате различных изменений в материале, включая разложение и восстановление оксидов трехвалентного железа, горение органических веществ, продувку захваченной воды и разложение карбонаты .³
Это выделение газов вызывает физическое расширение или вздутие глины, в результате чего она имеет более низкую плотность, более высокую пористость и гораздо большую площадь поверхности внутри материала, а также более твердую поверхность — все характеристики, которые делают ее идеальной для использования. как легкий заполнитель.
Факторы, влияющие на расширение глины при прокаливании
Как и в случае с большинством материалов, для достижения наилучших результатов в производственном процессе необходимо оптимизировать различные факторы. Обширное исследование, проведенное на трех разных источниках глины, показало, что, хотя ряд факторов важен, параметры процесса расширения, которые, возможно, являются наиболее важными, включают: 4
Температура обработки
Температура обработки является наиболее важным фактором в процессе расширения.Было обнаружено, что расширение увеличивается вместе с температурой, чуть ниже температуры плавления конкретной глины (температура плавления варьируется в зависимости от типа глины).
Размер зерна глины
Исследование показало, что размер зерна глины также является определяющим фактором, причем расширение увеличивается по мере уменьшения размера зерна.
Размер пеллет
Также было обнаружено, что размер гранул или агломератов влияет на расширение, причем расширение увеличивается вместе с размером гранул. Следовательно, уменьшение размера гранул коррелирует с меньшим расширением.
Время удерживания
Было обнаружено, что оптимальное время удерживания зависит от типа обрабатываемой глины. Оптимальное время удерживания было важным, поскольку наблюдались последствия как несоответствующего, так и чрезмерного времени.
Вращающаяся печь
Предпочтительным оборудованием для проведения процесса расширения глины является вращающаяся печь.
Вращающиеся печи доступны в конфигурации с прямым или косвенным нагревом, и их часто называют декарбонизатором.Производство керамзита обычно осуществляется в печи с прямым нагревом, в которой глина и продукты сгорания находятся в прямом контакте друг с другом.
Обжиговые печис прямым нагревом можно настроить для прямоточного или противоточного воздушного потока, но противоток, как правило, является более эффективной настройкой процесса при этой настройке.
3D Модель вращающейся печи с прямым обогревом
Почему глина как легкий заполнитель
Как и многие легкие заполнители (LWA), использование вспученных глин может обеспечить широкий спектр как экономических, так и экологических преимуществ:
Экономическая выгода
Использование легких заполнителей предлагает множество экономических стимулов, в том числе:
- Снижение затрат на конструкции в строительстве
- Снижение транспортных расходов
- Снижение затрат и уменьшение зависимости от импорта, где это применимо
Экологические преимущества
По данным Европейской ассоциации керамзитовой глины (EXCA), керамзит является экологически чистым материалом с рядом экологических преимуществ:
- Снижение выбросов CO 2 при использовании вместо ископаемого топлива
- Сниженные выбросы CO 2 в строительстве и на транспорте
- Повышение энергоэффективности зданий
- Возможность 100% вторичной переработки
- Химически инертен (без вредных компонентов и, следовательно, без возможности выделения ЛОС или вымывания загрязняющих веществ
- Преимущества фильтрации воды и воздуха
- Высокое соотношение продукта к сырью (из одного кубометра глины можно получить пять кубометров керамзита)
Кроме того, возможность заключается в использовании восстановленных или переработанных глиняных материалов, что еще больше повышает экологичность этого материала.
Использование LECA
Хотя области применения легкого керамзитового заполнителя (LECA) продолжают расти, в настоящее время существует два основных направления для продуктов LECA:
Строительство
Строительство — наиболее распространенное приложение для LECA. Керамзит можно найти во всех видах бетона, наполнителя и конструкционных компонентов в строительстве и промышленности строительных материалов. Преимущества, которые он может предложить в этой настройке, включают: ²
- Высокая износостойкость при минимальных затратах на обслуживание и долгий срок службы
- Прочность и устойчивость
- Полностью негорючие (огнестойкие)
- Возможность 100% вторичной переработки снижает проблемы утилизации
- Легкий вес без ущерба для прочности
- Служит теплоизолятором
- Обеспечивает снижение шума
- Обеспечивает отвод воды
- Нетоксичный
Садоводство
Использование LECA в садоводстве — сравнительно новое применение, но все еще развивающаяся область. Керамзитовые наполнители могут принести множество преимуществ при различных условиях выращивания. Сюда входят:
- Улучшенная аэрация (особенно при использовании в качестве субстрата при выращивании в коммерческих контейнерах) и пониженное уплотнение
- Способность к увеличению содержания воды и питательных веществ
- Повышенная катионообменная емкость
- Устойчивость к разрушению со временем
- Возможно использование в качестве барьера от сорняков
Помимо строительства и садоводства, LECA также изучается на предмет использования в системах очистки и фильтрации воды.
Испытания: залог успеха с керамзитом
Как и во многих случаях термической обработки, испытания являются критическим элементом успешной операции расширения глины. Исследования показали, что идеальные параметры процесса зависят от типа обрабатываемой глины.
Тестирование образцов глины в серийном масштабе для сбора исходных данных процесса — первый шаг в успешной программе тестирования. Данные, собранные во время пакетного тестирования, затем можно использовать для масштабирования тестирования до непрерывных пилотных запусков.Испытания также могут быть использованы для поиска баланса между идеальными параметрами процесса и тем, что является экономически целесообразным.
Инновационный центр FEECO предлагает различные испытательные печи для проведения как периодических, так и пилотных испытаний. Печи могут быть оснащены различным вспомогательным оборудованием для моделирования различных условий коммерческой эксплуатации.
Испытания различных методов агломерации также могут быть объединены для получения идеальных характеристик гранул для рассматриваемого уникального источника глины.
Печь периодического действия, использованная для испытаний в инновационном центре FEECO
Система автоматизации инновационного центра собирает широкий спектр данных, которые можно отслеживать и анализировать в режиме реального времени для непревзойденной прозрачности процесса. Сюда входят точки данных, такие как скорость подачи и продукта, соответствующие показания температуры, давления в системе, отбор проб и анализ газа и многое другое.
Заключение
Керамзитовый заполнитель — полезный материал в строительной индустрии, находит применение в садоводстве и водоочистке.Вращающиеся печи — это предпочтительное устройство для переработки глиняных агломератов в керамзит.
Возможность оптимизации параметров процесса для производства продукта из керамзита высшего качества имеет решающее значение для успеха операции. FEECO предлагает обширные возможности тестирования для тех, кто находится на этапах процесса и разработки продукта. Затем мы используем данные, собранные в ходе испытаний, для проектирования и производства на заказ коммерческих вращающихся печей высочайшего качества. Для получения дополнительной информации о наших возможностях в отношении керамзитовых заполнителей свяжитесь с нами сегодня!
(PDF) Производство вспененного заполнителя для легкого бетона из несамораскрывающихся глин
В последнее время постоянно проводятся исследования по производству искусственного легкого заполнителя из отходов. Хотя были проведены различные исследования механизма вздутия агрегата с использованием отходов, существует много недостатков в объяснении существующей теории, поскольку она отличается от керамзитового материала. И нет исследований, которые предлагали бы модель для установления механизма вздутия для отходов. В этом исследовании были исследованы характеристики существующего керамзита, чтобы установить механизм вздутия легкого заполнителя с использованием отходов, и были смоделированы оптимальные условия активации вздутия для вздутия легкого заполнителя.Физические и химические условия сырья и формованных изделий были изучены для массового производства и предотвращения плавления заполнителя.
Кислая глина, используемая в этом исследовании, представляет собой глинистые минералы, состоящие из монтмориллонита в качестве основной фазы, а минералы монтмориллонита являются подходящими материалами для производства агрегатов из-за удаления кристаллической воды при высоких температурах. Большинство керамзитов, используемых при производстве легкого заполнителя, изготовлены из сырья на основе пирофиллита и подходят для объяснения механизма вздутия с помощью существующего керамзита и подходят для разработки модели исходного материала для легкого заполнителя.
Затем, чтобы исследовать характеристики вспучивания легкого заполнителя при нормальных условиях спекания, механизм вспучивания искусственного легкого заполнителя при нормальных условиях спекания и условиях быстрого спекания сравнивали с использованием кислых глинистых материалов. Результаты экспериментов показали, что в условиях быстрого спекания не наблюдалось черной сердцевины. И при нормальных условиях спекания плотность достигала пика при 1150 ℃, а при нормальных условиях спекания было три зоны в зависимости от времени спекания, независимо от температуры на входе.Ⅰ. Участок, на котором плотность увеличивается по мере того, как время спекания
становится длиннее. (Зона спекания)
Ⅱ. В секции, где плотность внезапно снижается, когда
время спекания увеличивается. (Зона активации вздутия живота)
Ⅲ. На участке, где плотность постепенно снижается по мере того, как
время повышения температуры увеличивается. (Зона чрезмерного спекания)
Когда время спекания составляло менее 60 минут при температуре на входе 300 ℃, плотность увеличивалась, и агрегат спекался по мере увеличения времени спекания.
Наблюдалась оптимальная зона активации вспучивания, в которой плотность внезапно снижалась при времени спекания 210 минут. Когда время спекания превышало 210 мин, плотность постепенно уменьшалась, и этот участок представлял собой зону чрезмерного спекания. Независимо от температуры инъекции появлялась зона активации вздутия живота. Для того, чтобы оптимизировать вздутие агрегата, на этом участке необходимо спекание.
Чтобы найти оптимальные условия процесса спекания для управления оптимальной зоной активации вспучивания легкого заполнителя, каждая часть процесса нагрева была разделена на комнатную температуру до 300 ℃, от 300 ℃ до 600 ℃, от 600 до 900 ℃, от 900 до 1200. ℃, 1200 ℃ соответственно.Время эксперимента составляло 10-40 минут, после чего измеряли плотность агрегата и наблюдали поры. Время в секции сушки и предварительного нагрева (комнатная температура ∼600 ℃) не влияло на вздутие агрегата. Секция прокаливания (от 900 ℃ до 1200 ℃) короткая, чем дольше время выдержки при 1200 ℃, тем больше активировалось вздутие живота, и она легкая.
При более высоких температурах, чем температура начала вздутия, чем выше температура, тем ниже плотность конечного заполнителя. Переменными, которые имеют наибольшее влияние на активацию легкого заполнителя, были температура спекания и время выдержки в секции.Тенденция экспериментальных результатов, предсказанных методом Тагучи, хорошо согласуется с фактическими результатами измерений. Благодаря этому эксперименту стало возможным установить единичный процесс спекания для оптимизации условий активации вздутия живота. Чтобы подтвердить применимость оптимального единичного процесса и механизма вспенивания в реальном процессе массового производства, была исследована пригодность пилотной вращающейся печи. Когда легкий заполнитель производился с использованием только кислой глины, он плавился во вращающейся печи перед вспучиванием.Чтобы найти зону активации вздутия, которая может предотвратить слияние, были добавлены Fe2O3 и углерод, чтобы вызвать сочетание с механизмом вздутия черной сердцевины, и был подтвержден оптимальный химический состав для вздутия легких агрегатов.
Чтобы понять влияние образования давления внутри агрегата на вздутие и найти подходящий способ формования для массового производства, были исследованы характеристики вздутия агрегата и изменение температуры активации вспучивания путем изменения способа формования.И мы подтвердили возможность серийного производства с использованием пилотной вращающейся печи. Оптимальное содержание добавок составляло 8 ~ 13 мас.% Fe2O3 и 2 ~ 3 мас.% Углерода. При содержании указанных добавок механизм вспенивания черной сердцевиной работал в широком диапазоне, снижая температуру вздутия. Плотность сырых тел различалась в зависимости от способа формования. Размер пор 1㎛ был измерен как очень маленький в сырце, образованном экструдером и компрессионным формованием. По этой причине можно обеспечить более высокое внутреннее давление, необходимое для вздутия в зеленом теле, сформированном экструдером, и, в конечном итоге, раздуть агрегат при более низкой температуре.Разработав рецептуру с оптимальной комбинацией, как описано выше, и агрегаты формируются с использованием экструдера, было подтверждено, что температура активации вспенивания была снижена, и связывание плавлением было предотвращено во вращающейся печи.
Поскольку температура активации вздутия живота понижена, можно ожидать также эффекта энергосбережения.
В ходе этого исследования было обнаружено, что оптимальные параметры процесса для химического состава сырья, формования сырого материала, сушки, предварительного нагрева, прокаливания и прокаливания сырья для вздутия легкого заполнителя были подтверждены.Я надеюсь, что это исследование будет использовано в качестве важной модели для проектирования всего процесса легкого заполнителя.
Линия по производству легкого вспененного глиняного агрегата (LECA)
Что такое легкий керамзитовый заполнитель (LECA)?
Определение : свет заполнитель керамзита или заполнитель керамзита (LECA или ECA), также называемый керамическим окатыши — один из самых популярных легких заполнителей, получаемых путем спекания глины. во вращающейся печи примерно до 1200 ° C.
Вращающаяся печь для спекания глины
Сырье и применение : существуют различные типы легкого керамзитового заполнителя,
а основные материалы — глина, сланец, сланец, угольный порошок, хвосты и т. д.
LECA в основном применяется в строительстве, внутренняя отделка, сельское хозяйство, садоводство, садоводство, детская площадка, гидропоника, и Т. Д.
Оценка (мм) | Плотность (кг / м 3 ) | Приложения |
0-4 | ≤710 | Легкий бетон, легкий кирпич, сборная плита, легкая плитка, система очистки воды, сельское хозяйство |
4-10 | ≤480 | Легкий бетон, легкая плитка, сборные конструкции плита, аквакультура, шумозащитный барьер |
10-20 | ≤380 | Легкий бетон, канализация, садоводство, дренажная система |
0-25 | ≤430 | Отделка пола, светлая набивка, дорога строительство, аквакультура |
Перспектива разработки керамзита легкого керамзита
Текущий легкий керамзитовый заполнитель
рыночные данные показывают, что рынок LECA изменил свое направление с
традиционная строительная техника для изготовления изделий и садоводства
поддержание.
Перспектива развития LECA
Материалы для производства из традиционных материалов такие как глина и сланец были заменены остатками промышленных отходов и илом и тенденция развития машин превратилась в крупномасштабные и автоматизация.
В связи с тенденцией глобализации защиты окружающей среды, ресурсосберегающая экономика и устойчивая промышленность будут активно продвигаются в разных странах и регионах.
В будущем, сосредоточив внимание на экономического развития, поставщики LECA должны обратить внимание на сокращение загрязнения и растраты ресурсов для обеспечения быстрого и стабильного развития производственные линии.
Технологии производства LECA
Обычно существует два типа LECA. Технология изготовления: спекание и спекание-вспенивание. Разница между ними находится в процессе спекания-расширяется, агрегат расширяется на больший объем.
Производительность LECA при спекании
Агломерационная машина для процесса спекания LECA
- Прочность на сжатие : на сжатие
прочность агломерата относительно высокая, достигая 3,0-7,0 МПа,
а прочность на сжатие высокоспеченных агрегатов может достигать 25-40 МПа.
- Плотность : плотность спеченного заполнитель крупнее, обычно больше 600 кг / м3, даже некоторые из которых более 900 кг / м3.
- Водопоглощение : водопоглощение обычного спеченного заполнителя немного выше, чем у спеченного вспененного материала. продукт, а высокопрочные изделия аналогичны спеченному вспененному продукту.
- Устойчивость к карбонизации : спеченный заполнитель обладает высокой устойчивостью к карбонизации, поэтому его прочность на сжатие не уменьшится даже под действием углекислого газа.
Характеристики LECA при спекании-расширении
Вращающаяся печь для спекания-расширенного процесса LECA
- Прочность на сжатие : на сжатие прочность спеченно-вспененного заполнителя обычно ниже 2,0 МПа, поэтому он в основном используется для внутренней отделки, например, для шумоизоляции и садоводства.
- Теплоизоляционные характеристики : спеченный-вспененный
продукт имеет закрытую микропористую структуру с очень высокой пористостью, что обычно
составляет 48% -70% от общего объема агрегата, что дает только 0.
08-0,15 Вт /(m.k) теплопроводности.
- Низкая плотность : в слое много пор спеченно-вспененный материал, поэтому плотность преимущественно 300-500 кг / м 3 , что составляет лишь половину от спеченного заполнителя. Однако у него есть значительное преимущество в легкой производительности, поэтому его также можно использовать для различных декоративная промышленность и строительство с более низкими требованиями к плотности в строительстве материалы.
- Превосходное звукопоглощение и изоляция : среди всех видов агрегатов звукопоглощающие и изоляционные характеристики из спеченно-вспененного заполнителя является наиболее выдающимся.
Когда звук проходит через материал, большое количество звуковых волн поглощается его порами, что уменьшает распространение звука.
Для разных процессов требуется разное оборудование.
Агломерационная машина обычно используется в процессе спекания, в то время как роторная
Печь используется в процессе спекания с расширением.
По сравнению с агломашиной роторный печь более эффективна и экологична, поэтому предпочтительное оборудование для поставщиков LECA.
Производственная линия LECA и основные машины
Производство LECA в целом требует семи шагов: дробление, смешивание, измельчение, гранулирование, спекание, охлаждение и просеивание.
Производственная линия LECA
Основное оборудование на производстве LECA Линия включает в себя щековую дробильную машину, смесительную машину, шаровую мельницу, гранулятор, роторная сушилка, грохот, вращающаяся печь, охлаждающая машина.
Щековая дробилка — первичное дробление
Щековая дробилка — это основная машина, которая применяется для крупного, среднего и тонкого измельчения различных руд и горных пород с комплексная прочность от 147 до 245 МПа и переработка их в небольшие куски 10-350 мм.
Зубодробилка, мордоворот
Преимущества : В последние годы FTM
специально разработанная мощная щековая дробилка для нужд дробления
высокопрочный и высокотвердый микроуглеродистый феррохром в металлургии,
горнодобывающая, строительная и другие отрасли промышленности.
Шаровая мельница — дальнейшее измельчение
Шаровая мельница — ключевое оборудование для измельчения материал после измельчения. Шаровая мельница широко используется при производстве цемента, силикатные изделия, новые строительные материалы, огнеупорные материалы, удобрения, шлифовка черных и цветных металлов и стеклокерамика, сухое или мокрое шлифование различных руд и других измельчаемых материалов.
Шаровая мельница
Преимущества : Энергосбережение, гибкий дизайн разгрузочной части, большой порт подачи, высокая эффективность измельчения, хорошая качество футеровки и закрытая система для уменьшения запыленности.
Дисковая грануляционная машина — контроль размера частиц
Диск — это ключевая машина, определяющая частицы керамзитового заполнителя.
Диск гранулирования имеет общую круглую форму.
структура дуги, а степень грануляции может достигать 93% и более. Гранулирование
лоток имеет три выпускных отверстия, которые облегчают прерывистое производство
операций, значительно снижая трудоемкость и повышая эффективность труда.
Дисковая грануляционная машина
Преимущества : Высокая скорость образования шариков, большие округлая прочность частиц, интуитивное управление и простота обслуживания.
Сушилка — удаление воды из LECA
Сушилка в основном используется для сушки определенных влажность или крупность материалов переработки минерального сырья, строительных материалов, металлургия и химическая промышленность, а работа оборудования проста и надежный.
Сушилка
Adv anta ges : длительный срок службы деталей, износостойкость, высокая прочность на сушку, высокая эффективность, простота в эксплуатации, экологичность защита и энергосбережение, усовершенствованная структура и сильная сушильная способность.
Барабанный грохот — отделяющий неквалифицированный LECA
Барабанный сетчатый фильтр часто используется для измельчения
порошкообразных материалов, который имеет хороший просеивающий эффект и стабильную работу
и он производит низкий уровень шума во время рабочего процесса.
Барабанный экран
Преимущества : Оборудование имеет диапазон применения, а также его можно настроить. Имеет низкий уровень шума, высокий эффективность и защита окружающей среды, усовершенствованная система смазки, долгая срок службы, малый угол наклона установки и хороший экранирующий эффект.
Вращающаяся печь — спекание LECA
Вращающаяся печь — самая необходимая машина и играет важную роль в процессе спекания, что определяет производительность LECA.
Вращающаяся печь
Преимущества : Осевое перемещение цилиндр регулируемый, скорость гибкая, установка и обслуживание удобное, а герметичность хорошая.
Кулер — быстрое охлаждение LECA
Одноцилиндровый кулер — один из
важное оборудование в системе вращающейся печи. Клинкер из вращающейся печи
(1000-1200 ° C) полностью обменивается с воздухом через вращающийся цилиндр.
лента для охлаждения материала до температуры ниже 200 ° C, в то же время улучшения клинкера
качество и шлифуемость.
Кулер
Преимущества : Высокая термическая эффективность, высокая качество клинкера, быстрое охлаждение и повышенная производительность.
Спецификация производственной линии LECA (для только для справки)
- 01 тип : 0,45-0,9 мм (20-40 меш) Высокая прочность при средней плотности
- 02 тип : 0,9-1,25 мм (16-20 меш) Высокая прочность при средней плотности
- 03 тип : 1.0-1,70 мм (12-18 меш) Высокая прочность при средней плотности
- 04 тип : 0,224-0,65 мм (40-60 меш) Высокая прочность при средней плотности
Производитель оборудования LECA рекомендовано — FTM
Fote Mining Machinery (FTM), расположенная в
Хэнань — один из самых известных поставщиков горнодобывающего оборудования, который стремится
для производства горнодобывающих машин из экологически чистых строительных материалов и обеспечивает
интеллектуальные продукты для горнодобывающей промышленности и передовые решения.
Обладая более чем 30-летним опытом, FTM добился замечательных результатов в производственной линии LECA за счет непрерывного разведка и исследования.
FTM — профессиональный поставщик машины и оборудование для легкого керамзита, а также все оборудование имеет высокое качество и значительные преимущества, а также очень разумные цены.
Одним словом, Fote Mining Machinery — хороший выбор поставщиков LECA для выбора легкого керамзитового заполнителя производители оборудования.Добро пожаловать, чтобы проконсультироваться с нами, если у вас есть какие-либо требования о производственной линии LECA.
Керамзит — о сырье и процессе производства
Керамзит из-за своей традиции более распространен и широко распространен, чем можно предположить в современных строительных технологиях. С геологической точки зрения, сырьевая глина — это сначала просто определение размера минеральных частиц. Эти крошечные частицы образовались и возникают, с одной стороны, в результате выветривания и эрозии различных горных пород, а с другой — в результате минерализации и осаждения органических материалов. Высокое давление и температура могут вызвать превращение этих отложений в различные, так называемые метаморфические породы. Таким образом, например, долгое воздействие давления и тепла превращает известняк в мрамор, а глину — в сланец. Таким образом, глина является сырьем, которое возникло и до сих пор геологически возникает в результате непрерывных процессов. Это неисчерпаемое сырье было известно с древних времен как исключительно подходящий материал для строительства и других целей. Дохристианские постройки или знаменитые армии в натуральную величину, воспроизведенные из глины, свидетельствуют о прочности этого материала.
От побочного эффекта к 100-летней истории систематического производства керамзита
Систематическое и контролируемое производство керамзита — до тех пор нежелательного побочного продукта производства глиняного кирпича — возникло только ближе к концу 19 века. Первый патент на производство экономичного и структурного керамзита был получен в США в 1918 году. Колыбелью европейского производства керамзита является Дания, где с середины прошлого века керамзит почковидной формы производился в больших масштабах. век.Преимущества этого легкого и, тем не менее, прочного и долговечного строительного материала неуклонно возрастали в ходе его разработки. Помимо изначально преследуемой главной цели снижения веса, сегодня решающими причинами для использования керамзита являются превосходная теплоизоляция, сбалансированный микроклимат в помещении и постоянно растущее внимание к строительной биологии. На нашем веб-сайте представлен соответственно широкий спектр продуктов, а также многочисленные преимущества и различные потенциальные области применения.
Принцип производства нашего керамзита
Неочищенная глина, добытая открытым способом и состоящая из отборной природной эоценовой глины, содержащей более 60% монтмориллонитовой глины, предварительно смешивается, очищается при подготовке, гомогенизируется и затем подается в одну ряда различных вращающихся печей в зависимости от индивидуального производственного процесса по принципу Лека. После того, как глина сушится при температуре от 300 до 800 ° C и одновременно измельчается и гранулируется оборудованием внутри печи, фактический процесс расширения происходит при температуре прибл.1200 ° С. Оболочка глиняных гранул достигает точки плавления и спекается, а это означает, что они плавятся и становятся более компактными. Одновременно органические компоненты (соединения углерода) внутри газифицируются или сгорают, повышая температуру и превышая точку плавления глины. Дополнительный эффект расширения достигается за счет высвобождения кислорода из оксидов, содержащихся в глине, которое начинается при этих высоких температурах. Это происходит в течение относительно короткого времени, поэтому газы не могут достаточно быстро диффундировать и образовывать газовые поры, которые расширяют глину.В результате получается частица в форме почки со стабильной оболочкой и мелкопористым аэрированным ядром для различных потенциальных применений.
Агрегаты Альфа | Керамзитовый наполнитель
Керамзит Альфа — эффективный и легкий заполнитель с выдающимися
огнестойкими и изоляционными свойствами.
На нашем заводе в Кингсли в Стаффордшире производятся три особых типа легкого керамзита; EFG, REFAG и K25.Широкий ассортимент высококачественных глин выбирается со всего Соединенного Королевства и из карьера Кингсли. Эти глины тщательно перемешиваются и перемешиваются, чтобы обеспечить постоянный и стабильный химический состав, а затем спекаются на движущемся поде с образованием пористого керамического агломерата. После периода охлаждения агломерат измельчается и просеивается на фракции, в результате чего получается зерно разного размера в соответствии с требованиями заказчика. Все наши огнеупорные заполнители обладают низкой насыпной плотностью, высокой теплоизоляцией и огнеупорностью.
Приложения
Все марки продаются по всему миру для различных областей применения, в том числе:
- Изоляционные огнеупорные бетоны для литья и торкретирования
- Добавки к глиняным смесям для производства полуизоляционного огнеупорного кирпича
- Опорная изоляция в виде рыхлого и мелкозернистого бетона
- Состав покрытия высокотемпературных ковшей
- Наполнитель для черепицы в сталеплавильном производстве
- Фильтрация
Упаковка
Доступен в:
- Полиэтиленовые клапанные мешки по 20-25 кг в зависимости от размера зерна, упакованные в термоусадочную пленку на
поддонах 1.0-1,2 тонны на поддон
- IBC по 1,0–1,2 тонны в мешке. Также доступна сумка половинного размера
- Сыпучие материалы поставляются самосвалом или цистерной-силосом
- Специальная упаковка доступна по запросу заказчика
Экспорт
Мы экспортируем наши материалы по всему миру, и мы можем оперативно предоставить расценки по всем направлениям. Контейнеры, идущие в глубоководные пункты назначения, заполнены до отказа, чтобы минимизировать транспортные расходы.40-футовые контейнеры могут быть заполнены IBC или мешками на поддонах.
Изоляционные огнеупорные заполнители
K25 | EFG | EFG с низким содержанием железа | REFAG | |
A2 2 O3 | 20-22% | 31-35% | 25–27% | 39-42% |
Fe 2 O3 | 6.![]() | 2,0–3,5% | 1,8–2,0% | 1,9–2,3% |
Эквивалент пирометрического конуса | Конус 10 1300C | Конус 23-26 1610C-1645C | Конус 17-18 1512C-1522C | Конус 32-33 1717C-1745C |
Насыпная плотность кг / м 3 | 600-1050 | 625-1100 | 625-1100 | 630-1100 |
Доступные размеры | 10-5 мм 5-2 мм 5-0 мм 2-0 мм Специальные сорта по желанию заказчика |
Производство керамзита на установке вихревого слоя
Производство керамзита основано на гомогенизации и измельчении частиц глинистого сырья, формировании и дальнейшем обжиге гранул. Учитывая такие процессы, целесообразно использовать устройство вихревого слоя (АВС) от GlobeCore .
Актуальность производства керамзита
Керамзит — востребованный строительный материал, недорогой теплоизолятор, наполнитель и декоративное изделие. Выпускается в виде шаров, гравия, щебня, песка с толстой оболочкой и пористой внутренней структурой. Сырьем для получения керамзита служат легкоплавкие, вздувающиеся глины, сланцы и суглинки.
Зерно получается в результате гомогенизации, перемешивания шихты и выпечки. Их отличает низкая теплопроводность, инертность к воздействию щелочей, кислот, долговечность, экологичность, звукопоглощающая способность. В основном они используются в строительстве и при производстве строительных материалов:
- Производство пористых бетонов
Наполнитель для легкого и сверхлегкого пористого бетона, который используется в стяжках, монолитных стенах и конструкциях.
- Производство керамзитоблоков
Основной наполнитель стеновых блоков из керамзита. Также они содержат цемент, песок и воду. Конструкционные элементы используются в малоэтажном строительстве при возведении стен и перегородок в домах.
- Теплоизоляция зданий, сооружений
Высокопористые разновидности керамзита применяют в качестве теплоизолятора в полах, стенах, межэтажных покрытиях.
- Строительство фундаментов
Применяется для заливки во избежание промерзания. Это позволяет снизить материалоемкость при возведении конструкций.
Хорошая основа для чернового выравнивания пола. Материал легкий; Таким образом, он не оказывает отрицательного воздействия на межэтажные перекрытия. Повышает теплоизоляционные характеристики внутреннего пространства.
Материал относительно низкой пористости используется в насыпях при строительстве дорог и водоотводных систем, при обработке почвы и подготовке почвы.
- Теплоизоляция инженерных сетей
Трубы системы теплоснабжения, подводимые к домам и строениям, покрыты гранулами. Они обеспечивают качественную теплоизоляцию и легкий доступ к системе.
Столь широкая сфера применения керамзита делает его востребованным на рынке строительных материалов, в промышленности и сельском хозяйстве. Перспективной и актуальной выглядит модернизированная технология производства керамзита с использованием устройства вихревого слоя.Но сначала обсудим, какими недостатками обладают существующие линии по производству этого материала.
Производство керамзита традиционными методами, недостатки этих методов
Практически на каждом современном заводе по производству керамзита в процессе смешивания и измельчения сырья используются смесители для глины, ролики и краевые направляющие. Выпечка осуществляется в барабанах печи. Обработка гранул в устройстве занимает около 45 минут.
Однако обычное оборудование для подготовки, гомогенизации и диспергирования сырья не измельчает и не смешивает ингредиенты качественным образом.Это отрицательно сказывается на прочности готового изделия.
При низкой степени гомогенизации и плохой диспергируемости частиц даже 3% карбонатных примесей в вздувающихся легкоплавких глинах отрицательно сказываются на качестве материала. Гидратация CaO сопровождается деградацией керамзита и потерей прочности при хранении.
Обычное производство керамзита с использованием валков, краевых направляющих и смесителей для глины также не имеет значения для обработки глиняных масс с высоким содержанием песка.Если в смеси содержится 10–30% свободного SiO2, из сырья невозможно получить качественный, прочный продукт.
Обработка сырья в аппарате вихревого слоя помогает в решении этих задач классическими методами. Кроме того, появляется возможность производить качественный керамзит даже из изначально неподходящих глиняных масс.
Кроме того, по общепринятой технологии отсортированное сырье можно смешивать с веществами, улучшающими его вздутие — мазутом, соляркой.Применение AVS помогает свести к минимуму использование добавок или отказаться от них, что имеет положительный экономический эффект и влияет на чистоту и экологичность готового продукта.
Производство керамзита на установке вихревого слоя
Производство керамзита с помощью устройства вихревого слоя основано на обработке сырья в электромагнитном поле с ферромагнитными частицами. Устройство может работать как с сухой, так и с влажной влажной средой.В рабочей камере устройства наблюдаются процессы диспергирования и перемешивания, сопровождающиеся активацией частиц. Это влияет на прочность готового изделия. Процессы происходят под действием электромагнитного поля, акустических колебаний, высокого местного давления и электролиза.
В вихревом слое ферромагнитные иглы превращаются в смесители и дробилки. При этом они перемещаются по камере, вращаются, сталкиваются с обрабатываемым материалом, друг с другом и со стенками устройства.Все это способствует эффективному перемешиванию, измельчению и активации загрузки и смеси.
Эффект от обработки глинистого сырья для керамзита средствами АВС описан и экспериментально исследован Д. Д. Логвиненко. В результате мы получаем материал с меньшим объемным весом и лучшими прочностными характеристиками. Результаты представлены в таблице 1.
Таблица 1 — Характеристики керамзита при переработке сырья в AVS
Эксперимент № | Характеристика сырья и продолжительность обработки в АВС | Характеристики керамзита | |||||
Обработка сырья в АВС | Обработка сырья без АВС | ||||||
Объемный вес (γ), г / см3 | Предел прочности на выкрашивание (σс * 10-5), Па | Предел прочности | Объемный вес (γ), г / см3 | Предел прочности на выкрашивание (σс * 10-5), Па | Предел прочности | ||
1 | Глина, содержащая 26% свободного SiO2 (30 от обработки глиняного шликера) | 0.![]() | 2,25 | 10,3 | 0,38 | 1,60 | 5,1 |
2 | Глина, содержащая 41% свободного SiO2 (30 от обработки глиняного шликера) | 0,34 | 2,45 | 7,8 | 0,84 | 3,24 | 4,1 |
3 | Монотермит (7 минут сухой обработки) | 0,85 | 29,4 | 36 | 1,6 | 9,81 | 6.5 |
4 | Глина, содержащая угольную золу в соотношении 50/50 (7 минут сухой обработки) | 0,57 | 10,7 | 18 | 0,58 | 4,32 | 8,4 |
5 | Глина, содержащая угольную золу в соотношении 50/50 при опудривании полуфабриката каолином (7 минут сухой обработки) | 0,74 | 27,9 | 32,0 |
Для сравнения, глиняный шликер, содержащий до 40% свободного диоксида кремния, был подвергнут обработке. Производство керамзита с применением АВС отличается уменьшением объемной массы в 2 раза и одновременным увеличением прочности материала. Соотношение прочности и веса изделия, полученного из шихты после обработки в устройстве с вихревым слоем, в два раза выше, чем у материала, изготовленного традиционным способом.
Этому результату способствует тщательная обработка сырья в вихревом слое с активацией кварцевого песка, входящего в состав смеси.При обработке в АВС наблюдается разрыв силоксановой связи Si-O. Следовательно, на поверхности частиц появляются активные центры в виде свободных радикалов. Это стало причиной повышения качества конечного продукта. Активация песка происходит по тому же принципу, что и при диспергировании в дезинтеграторах на высоких скоростях.
Из-за активации кварцевого песка происходят реакции стеклования и образования силикатов, в которых участвует диоксид кремния. После того, как производство керамзита завершено путем обжига продукта, он не содержит крупных песчинок SiO2, в которых могло бы быть сконцентрировано напряжение. А в составе стекла кварцевый песок влияет на повышение прочности и термического сопротивления материала.
Кроме того, была изучена сухая технология производства керамзита с использованием вихревого слоя. Для исследования был взят монотермит. Наполнитель, прочность которого в три раза выше, чем у материала, изготовленного классическим способом, был получен из сырья, обработанного в сухой среде с помощью АВС. При этом объемная масса огнеупорного заполнителя была вдвое меньше, чем в образце.
Сухая переработка многокомпонентных шихт, состоящих более чем из золы ТЭС (золы ТЭС), также дала положительный результат.
Полученные данные свидетельствуют о том, что технология производства керамзита с использованием вихревого слоя позволяет получать высокопрочный строительный материал даже из глин с высоким содержанием песка или карбонатных примесей.
Преимущества использования устройства вихревого слоя при производстве керамзита
Устройство вихревого слоя — это современное оборудование, которое можно использовать для оптимизации как компактного завода по производству керамзита, так и крупного предприятия по следующим причинам:
Готовый материал отличается повышенной прочностью и термической стойкостью даже при большом содержании в глинистых массах песчано-карбонатных примесей. Также АВС позволяет использовать отходы энергетики, в том числе золу ТЭС, в производстве керамзита.
Оборудование отличается низким потреблением электроэнергии и в несколько раз выгоднее традиционных агрегатов. Потребляемая мощность моделей AVS-100 и AVS-150 составляет 4,5 кВт и 9,5 кВт соответственно.
Устройство компактное, простое в эксплуатации и может быть интегрировано в существующую производственную линию. При этом нет необходимости делать постамент или дополнительные конструкции для этого оборудования.AVS легко перемещается по мастерской.
Таким образом, АВС от GlobeCore — универсальное, удобное, высокоэффективное оборудование, которое позволит расширить и оптимизировать производство качественного керамзита. Кроме того, снижаются требования к качеству сырья, а значит, появляется больше возможностей с точки зрения производства легких наполнителей, на которых основано производство керамзитобетонных блоков, легкого бетона и т. Д.Себестоимость материала можно снизить за счет повышения его эксплуатационных качеств.
Для получения консультации и заказа моделей AVS-100 или AVS-150 для завода по производству керамзита обращайтесь к торговым представителям GlobeCore.
Превратить глину в строительный материал — это тяжелая работа.
Каждый день конвейерная лента перемещает около 1000 тонн необработанной глины из глиняного карьера Leca в Дании на завод компании в Хинге. Здесь влажное сырье подвергается жесткой обработке, которая в конечном итоге превратит глину в широко известные коричневые шары Leca ® и другие продукты Leca ® .
«Конвейерная лента транспортирует сырую глину в большие вращающиеся печи. Попутно глина проходит несколько процедур формования, так что в конечном итоге сгустки оказываются между размером руки и большим валуном. Это чрезвычайно тяжелая отрасль, в которой, помимо прочего, используются электродвигатели, редукторы и муфты », — объясняет менеджер по техническому обслуживанию Тонни Хедеванг.
Обжиговые печи выключают только два раза в год
Температура во вращающихся печах составляет около 1200 градусов Цельсия.Тепло высвобождает тысячи маленьких пузырьков газа, которые задерживаются в глине и придают материалу характерную легкость, когда глина превращается в шарики за счет кругового движения печи. Остановка и запуск печей — чрезвычайно дорогостоящая операция, поэтому Leca Дания уделяет особое внимание предотвращению сбоев в производственном процессе.
«Мы закрываем печи только на Рождество и на летние каникулы, чтобы провести регулярное техническое обслуживание. В остальное время их нужно постоянно кормить.Механизмы и двигатели очень тяжело работают, поэтому нам необходимо иметь надежное оборудование. Продукты и оборудование низкого качества и с коротким сроком службы просто не подходят », — объясняет Тонни.
Тесный контакт с Хойером
Из-за того, что компания уделяет особое внимание эксплуатационной надежности и быстрому обслуживанию, Leca Дания поддерживает тесные контакты со своими поставщиками, включая Hoyer, которые поставляют электродвигатели, шестерни и другие детали трансмиссии.
«Мы не можем быть экспертами во всем, поэтому очень приятно знать, что Хойер знает фабрику и наше оборудование и может быстро отреагировать в случае возникновения проблем.Например, несколько месяцев назад у нас возникли проблемы с некоторыми муфтами. Что ж, вышло наше постоянное контактное лицо из Хойера, которое осмотрело детали и быстро нашло решение, — вспоминает Тонни.
Факты о Leca Дания
Leca Дания является частью международного концерна Saint-Gobain
Завод в городе Хинге отвечает за производство всей продукции Leca ® в Дании.
Первые продукты Leca ® были разработаны в Дании в 1939 году.
Leca ® используется в качестве изоляционного строительного материала и легкого строительного наполнителя, используемого в зданиях, на дорогах, мостовых пандусах, велосипедных дорожках и портовых сооружениях.
.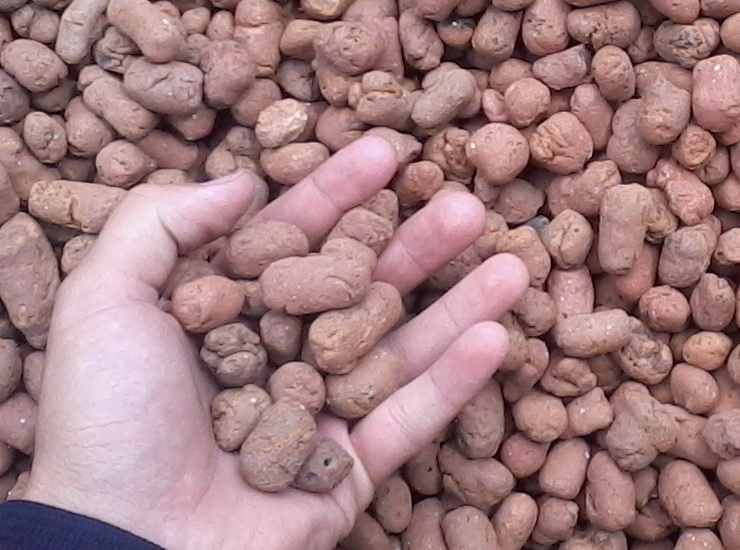