Технология пошив обуви – Технология производства обуви | ПромЭлектроАвтомат
Обувь ручной работы: этапы производства
Туфли и ботинки, сделанные полностью вручную, встречаются сегодня очень редко и стоят дорого — примерно от 400 евро, если мы говорим о Венгрии, и примерно от 600 евро, если речь идёт о Западной Европе и более или менее известных мануфактурах. На производство такой обуви затрачивается много времени, но оно того стоит: у туфель полностью ручной работы, например, можно большее число раз заменять подошву; они немного по-другому выглядят, а зачастую ещё и более комфортны. В этой статье мы опишем ключевые этапы создания туфель ручной работы на ранту.
Раскрой кожи
Естественно, кожа для обуви ручной работы кроится только вручную. Если речь идёт о пошиве обуви на заказ, то используются индивидуальные, специально созданные лекала для вырезания кусков кожи. Для готовой обуви используются стандартные лекала, обычно изготовленные из плексиглаза или другого современного материала.
Для раскраивания шкур обувщики используют нож-кликер, а сама эта процедура называется кликингом (clicking).
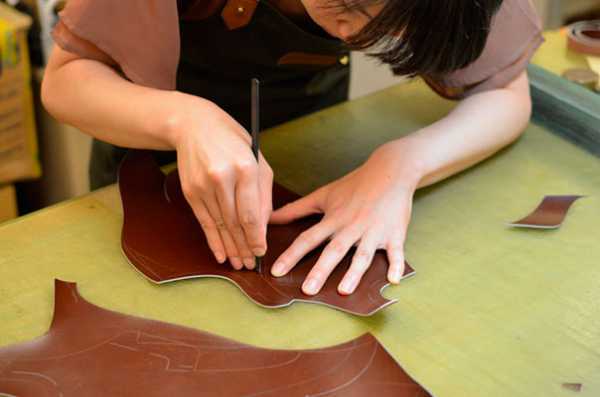
Перед выполняющим её работником стоит непростая задача: нужно использовать шкуру максимально рационально, отбраковав при этом все участки с дефектами. В случае с очень дорогой обувью, сшитой на заказ, используются лишь самые лучшие участки шкуры, причём многие шкуры отбраковываются ещё на этапе закупки.
Сшивание частей верха
На следующем этапе, который называется клоузингом (closing), вырезанные части кожи сшиваются друг с другом — и получается верх обуви.
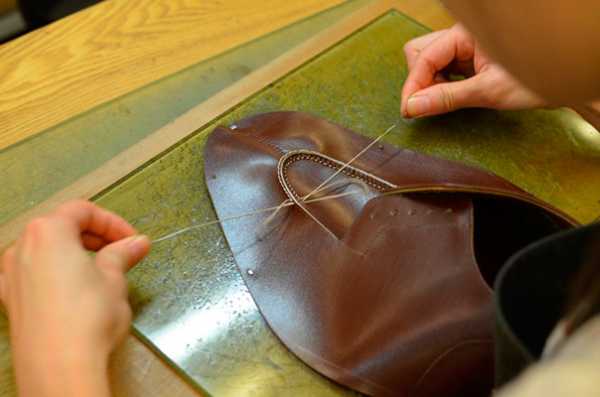
Помимо этого, верх сшивается с подкладкой, а также осуществляется декорирование отдельных частей верха — например, брогирование. На обуви полностью ручной работы брогирование делается вручную, без использования машин — и это занимает довольно много времени по сравнению с брогированием на фабричной обуви, где одна машина может делать дырочки одновременно на десяти кусках кожи.
Натягивание верха на колодку
Готовый верх обуви нужно натянуть на колодку, и эту операцию — ластинг (lasting) — делает ластер (laster). В случае с фабричной обувью ластинг обычно осуществляется полностью или частично с помощью специальных машин, что заметно сокращает издержки.
Как пишет немецкий эксперт по мужскому стилю Бернхард Ретцель, «ластер — это ремесленник, натягивающий кожу на деревянную колодку и временно прибивающий её гвоздиками. Позже, когда верх накрепко пришивается к ранту, гвозди снова вынимаются. Молоток часто намагничивается для облегчения манипуляций с множеством мелких гвоздей».
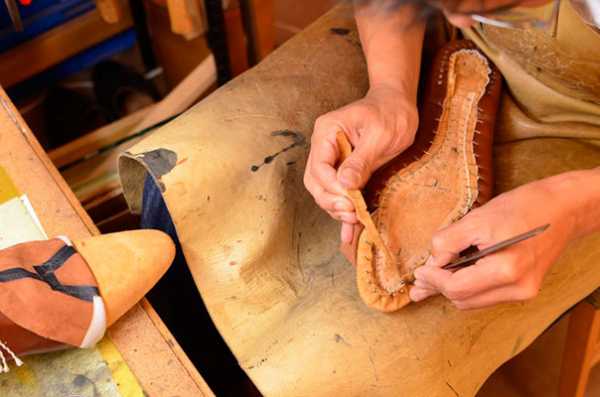
Стоит добавить, что раньше колодки изготавливались исключительно из дерева, но сегодня в ряде случаев даже для обуви на заказ (bespoke) используются колодки из пластика. У производителей готовой обуви имеются готовые колодки, а мастера, которые шьют заказную обувь, либо вытачивают колодки под клиента, либо используют готовые колодки разных размеров и форм, к которым по мере надобности прикрепляют в необходимые места куски кожи, чтобы добиться соответствия формы колодки форме стопы клиента.
Подготовка внутренней подмётки и пришивание ранта
Обувь полностью ручной работы часто шьётся с использованием ранта, причём этот рант пришивается вручную. Во внутренней подмётке (insole) вручную вырезается гребень, и после этого к нему и к верху вручную пришивается рант; сама подмётка тоже вырезается вручную. Это довольно трудоёмкая операция, и в случае с фабричной обувью сам процесс упрощают: гребень не вырезают в самой подмётке, а приклеивают к ней, используя заметно более тонкие подмётки (а сам гребень при этом сделан из текстиля). Рант к подмётке и верху на фабричной обуви пристрачивает машина, и делает это очень быстро.
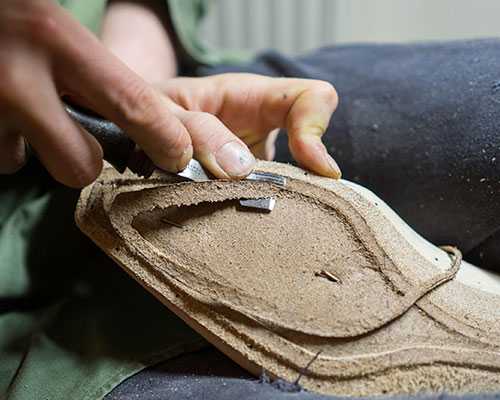
Вырезание гребня на внутренней подметке
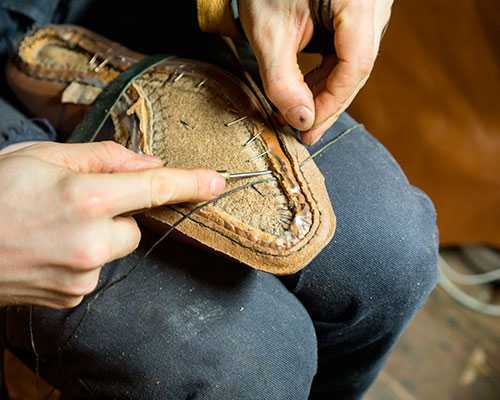
Сшивание ранта, гребня и верха обуви
В чем же заключается преимущество ручной работы на данном этапе? Знатоки говорят, что ручное крепление ранта (hand-welting) позволяет большее число раз заменять подошву; кроме того, hand-welted обувь при прочих равных оказывается более комфортной.
Пришивание подошвы и крепление каблука
После того, как рант соединен с внутренней подмёткой и верхом, на подмётку помещают пробковый наполнитель (cork filling) — это могут быть пробковые брикеты или же вязкая смесь на основе пробковой крошки.
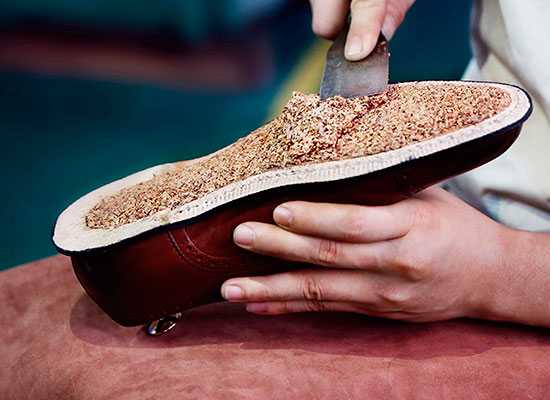
На следующем этапе — soling — рант сшивается с внешней подошвой (outsole).
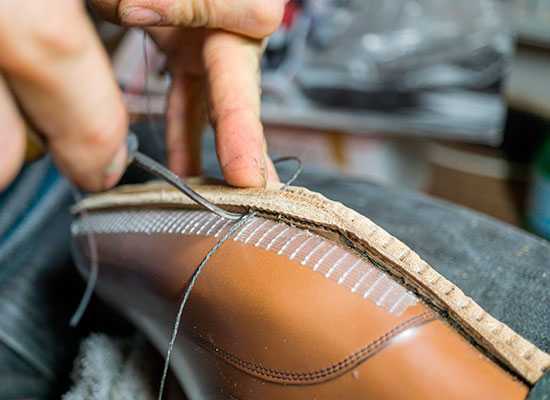
На обуви полностью ручной работы это делается вручную, иглой и нитью — такая операция трудоёмкая и длительная, и поэтому даже на hand-lasted и hand-welted обуви шов, соединяющий рант и внешнюю подошву, довольно часто выполняется с помощью машины. После крепления к верху «талия» (средняя часть) подошвы на туфлях ручной работы обычно изящно закругляется.
Далее осуществляется сборка каблука. На классических туфлях каблуки наборные — они сделаны из нескольких слоев кожи и резины, которые крепятся друг к другу и к подошве при помощи клея и маленьких гвоздиков. На сравнительно недорогих фабричных туфлях часто используются слои не из кожи, а из кожкартона — это обходится дешевле.
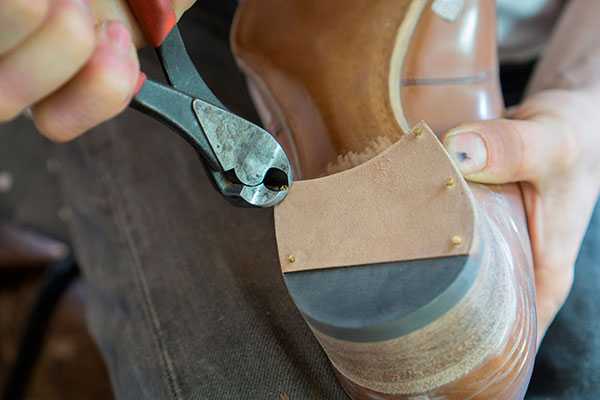
Финишинговые процедуры
После крепления подошвы и каблука туфли проходят ещё несколько процедур. В частности, ребро подошвы и каблука, и сами каблук и подошва шлифуются, вручную окрашиваются и полируются. Верх туфель вручную полируется, на него может наноситься уникальная патина с помощью красок и кремов.
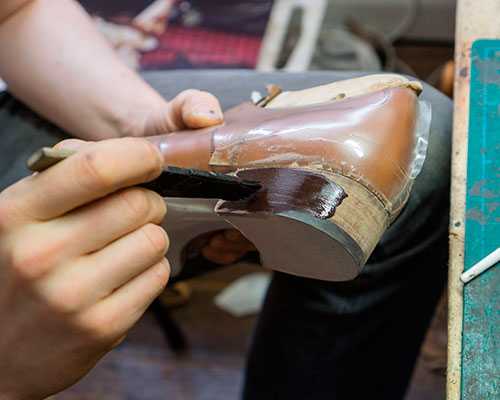
Окрашивание каблука
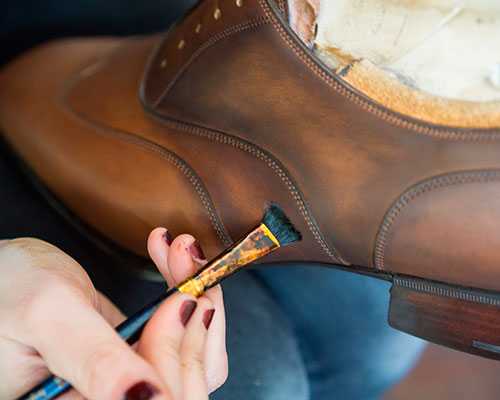
Окрашивание верха обуви
Внешняя сторона подошвы и её верхний край иногда обрабатываются вручную зубчатыми колесиками. Затем в туфли вставляются стельки, обувь проверяют на отсутствие дефектов, после чего зашнуровывают и упаковывают.
string(0) «»
О проекте
Проект «Обувь своими руками» — это развивающаяся площадка, имеющая несколько целей, которые вращаются вокруг одной популярной идеи — предоставить новичкам в этой области широкий спектр базовых понятий, терминологии и навыков, для того чтобы процесс их погружения в эту сферу протекал быстро и увлекательно. Большинство перспективных начинаний, как известно, глохнут на начальных этапах, когда большой объем непредвиденной мелочевки сводит на нет все услилия. Особенно это касается тех людей, кто не имеет возможности в любой момент времени добраться до магазина обувных принадлежностей, чтобы срочно пополнить тот или иной недостаток в материалах, инструментах или расходниках. Именно для того чтобы избежать всех этих досадных препятствий возникла идея как-то сгруппировать весь объем информации по пошиву обуви в некоторые смысловые блоки, для того, чтобы у новичка быстро сложилась целостная картина этого дела, так сказать дать ему возможность увидеть это занятие во всех его измерениях, чтобы он смог, пусть и виртуально, прочувствовать или почувствовать себя в роли мастера и ответить себе на вопрос: «Действительно ли мне это нравится и хватит ли у меня драйва преодолеть всевозможные мелкие препятствия, чтобы не «затухнуть» уже на взлете?».
Другое направление проекта — популяризовать само направление индивидуального пошива обуви. За 70 лет существования Советского Союза индивидуальный пошив обуви оказался, мягко говоря, на задворках социалистического прогресса, причем даже сейчас, спустя 25 лет с восстановления свободного предпринимательства, мало кто задумывается над тем, что кроме покупной обуви существует еще и возможность обувь заказать, а, с появлением данного сайта, появилась возможность без больших усилий шить обувь самой себе (или самому себе), своей семье, причем такую, какая нравится душе и сердцу. Надеемся, что наш труд на данной площадке будет заметным вкладом в эту сторону.
Сфера ручного пошива обуви похожа на дерево, например яблоню, у которого есть ствол — центральное направление, а есть и множество веток — дополнительных направлений, без которых пошив обуви невозможен. Сюда относятся и такие направления как изготовление инструментов для пошива, выделка кож, произвоство химии для производства и отделки изделий, производство мини станков для минимальной механизации ручного труда. Все эти «подтемы», как мы надеемся, получат достойное освещение на страницах этого ресурса. Это, безусловно, натолкнет некоторых наиболее предприимчивых людей углубиться именно в эти «ответвления», чтобы создать свою личную или семейную бизнес-площадку.
obuv-svoimi-rukami.ru
![]() |
![]() |
![]() |
![]() |
![]() |
![]() |
![]() |
![]() |
![]() |
![]() |
![]() |
![]() |
![]() |
![]() |
![]() |
![]() |
![]() |
![]() |
![]() |
![]() |
![]() |
![]() |
![]() |
![]() |
![]() |
![]() |
![]() |
![]() |
![]() |
![]() |
![]() |
![]() |
![]() |
![]() |
![]() |
![]() |
obuv-svoimi-rukami.ru
Основы производства кожаной обуви
Все операции обувного производства можно объединить в шесть групп: 1) раскрой обувных материалов; 2) предварительная обработка деталей обуви перед их скреплением; 3) сборка заготовки; 4) формование заготовки; 5) прикрепление низа обуви; 6) заключительная отделка обуви.
Раскрой обувных материалов. Перед раскроем проверяют соответствие сортности и деформационно-прочностных свойств обувных материалов требованиям нормативных документов. Натуральные кожи раскраивают на детали каждую в отдельности; это связано с наличием дефектов (различных по виду, размеру и месту расположения на коже) и с неоднородностью свойств кожи по площади, в продольном и поперечном направлениях. Ответственные детали выкраивают из чепрака. Для искусственных и синтетических кож, текстильных и трикотажных материалов применяют многослойный раскрой. Долевое направление наружных деталей должно соответствовать направлению наименьшей тягучести (продольному направлению — в кожах, основе — в тканях и искусственных кожах на тканевой основе).
Предварительная обработка деталей. Обработка деталей низа включает общие и специальные операции. К общим относят:
1) выравнивание деталей низа по толщине;
2) клеймение — нанесение маркировки, предусмотренной ГОСТ 7296-81;
3) формование.
Подошвам и основным стелькам придают профиль следа колодки, жестким задникам и подноскам — форму пяточной и носочной части колодки. До формования детали низа подвергают специальным обработкам, которые зависят от вида детали, материала и метода крепления низа. Специальная обработка основных стелек включает дублирование тонких стелек с полустелькой для их упрочнения, соединение стельки с теленком, утонение стельки в пучках для увеличения гибкости обуви, получение натуральной или искусственной губы в стельках для обуви рантового метода крепления. Специальная обработка подошв включает соединение подошву с обводкой, подложкой или подметкой, утонение крокульной части подошвы, фрезерование уреза подошв и каблуков из натуральной кожи и резины; взъерошивание подошв клеевого крепления с изнаночной стороны, промазывание их клеем и подсушивание. Специальная обработка жестких задников и подносков заключается в утонении краев по всему периметру и просекании нижнего края, идущего под загибку при формовании обуви. Просекание краев предупреждает возникновение грубых складок по грани следа, утонение — предохраняет стопу от натирания.
Предварительная обработка деталей верха осуществляется одновременно с пошивом (сборкой) заготовки. Она включает клеймение в соответствии с ГОСТ 7296-81, спускание краев деталей, отделку видимых краев, дублирование наружных деталей верха с межподкладкой, украшение деталей. Спускание или утонение проводится для всех краев деталей верха, кроме затяжной кромки заготовки, идущей под загибку при формовании обуви. В результате спускания краев при сострачивании деталей не образуются грубые толстые швы. Видимые края деталей загибают, окрашивают, подвергают горячему формованию или обжигу, окантовывают для улучшения внешнего вида обуви и повышения прочности швов соединения деталей заготовки. Дублирование наружных деталей верха с межподкладкой проводят с целью упрочнения деталей верха и повышения формоустойчивости верха обуви. Украшение деталей верха проводят для повышения уровня эстетических свойств обуви.
Сборка (или пошив) заготовки. Заготовка — это комплект наружных, внутренних и промежуточных мягких деталей верха обуви, скрепленных между собой. Детали заготовки сшивают ниточными швами, склеивают, сваривают токами высокой частоты (ТВЧ). ТВЧ сваривают детали из искусственных и синтетических кож. Склеивают наружные детали верха с межподкладкой (дублирование). Сшивают детали настрочным, тачным, переметочным и выворотным швами (рис.).
Рис. Заготовочные швы:
а — настрочной; б — тачной; в — переметочный; г — выворотный
Настрочным швом скрепляют носок с союзкой, союзку с берцами и задинками, перед с голенищем. Тачным и переметочным швами сшивают голенища, задние края берцев и задинок. Переметочный шов менее прочный, чем тачный, поэтому его укрепляют задним наружным ремнем. Выворотным швом сшивают наружные детали верха с подкладкой по верхнему краю заготовки.
Формование заготовки — придание заготовке формы и размеров колодки, которые должны сохраняться и после снятия обуви с колодки, при ее хранении и носке. Различают три способа формования: 1) обтяжно-затяжной; 2) беззатяжной; 3) комбинированный.
Обтяжно-затяжной называют способом внешнего формования, так как растягивающие усилия прилагаются к заготовке извне (с помощью клещей или пластин обтяжно-затяжной машины). Обувь внешнего формования имеет высокую формоустойчивость, поэтому его широко используют для формования обуви.
При беззатяжном способе формования растягивающие усилия прилагаются к заготовке изнутри (за счет раздвижения колодки). Поэтому его назвали способом внутреннего формования. Способ менее трудоемкий и материалоемкий, чем обтяжно-затяжной, однако применяется для узкого ассортимента обуви (домашней, легкой, летней) из-за ее низкой формоустойчивости.
Комбинированный способ формования является комбинацией первых двух.
Окончательное закрепление формы и размеров обуви осуществляется в процессе ее влажно-тепловой обработки и сушки на колодке.
Прикрепление низа обуви. Все методы крепления деталей низа обуви к заготовке верха можно разделить на 4 группы: 1) шпилечные, 2) ниточные, 3) химические, 4) комбинированные (рис.).
Рис. Методы крепления низа обуви:
а — гвоздевой; б — прошивной; в — сандальный; г — доппедьный; д — рантовый; е — рантопрошивной; ж — парко; з — выворотный; и — клеевой;
к — горячей вулканизации; л — рантово-клеевой; м — строчечно-клеевой;
1 — заготовка; 2 — стелька; 3 — простилка; 4 — подошва; 5 — подложка;
6 — гоздь; 7 — ниточный шов; 8 — мягкая стелька
Шпилечные методы представлены двумя: винтовым и гвоздевым. Их используют для изготовления производственной обуви, обуви для армии и флота, реже повседневной. Обувь тяжелая, жесткая, негибкая, крепление обеспечивает ей высокую прочность, водостойкость, надежность.
К ниточным методам крепления относят рантовый, сандальный, доппельный, метод парко, прошивной, рантопрошивной, бортовой, выворотный, втачный и другие. Подошву скрепляют с заготовкой с помощью одно- и двухниточных швов. Используют капроновые, нейлоновые, реже льняные нитки. Обувь ниточных методов крепления более легкая, мягкая, гибкая, гигиеничная, но менее прочная и надежная, чем винтовая и гвоздевая. Прочность ниточного крепления подошвы зависит от плотности и толщины скрепленных деталей. Эти методы используют для изготовления повседневной, модельной, домашней и спортивной обуви для детей и взрослых.
При рантовом методе подошву прикрепляют к заготовке и основной стельке через рант, применяют рантовую стельку с губой. Внешние отличительные признаки — наличие ранта, отсутствие крепителей на поверхности основной стельки в носочно-пучковой и геленочной части. Рантовая обувь самая надежная, теплозащитная и ремонтопригодная в сравнении с обувью других ниточных методов. Но из-за повышенной трудоемкости рантовый метод применяется ограниченно для изготовления мужской и женской обуви, повседневной и модельной, летней и утепленной.
Сандальный метод применяют для изготовления сандалий. Отличительные признаки — отсутствие подкладки и основной стельки, мягкие носки, затяжная кромка заготовки отгибается наружу и выходит в урез подошвы, наличие накладного ранта, подошвенный шов скрепляет подошву, затяжную кромку заготовки и накладной рант. Обувь очень легкая и гибкая, но деформируется при увлажнении и высушивании, недостаточно надежная.
Доппельный (полусандальный) метод отличается от сандального наличием стельки и подкладки, нижний край которой загибают и прикрепляют к стельке; обувь менее гибкая, но более надежная в носке и меньше деформируется при увлажнении и высушивании. Выпускают летнюю и утепленную обувь для детей и взрослых.
Метод парко разработан на обувной фабрике «Парижская Коммуна». Его особенность состоит в том, что рант пришивают к затяжной кромке заготовки еще до ее формования, после чего заготовку формуют, затем подошву пришивают к ранту. Этим методом изготавливают детскую обувь. Внешне она похожа на рантовую. Но если сильно отжать верх от ранта, можно увидеть ниточный шов, скрепляющий рант с заготовкой. Метод парко имеет три разновидности. В обуви парко I отсутствует основная стелька; вынув из обуви вкладную стельку можно увидеть шов, скрепляющий рант с заготовкой. В обуви парко II (рант доходит до каблука) и парко III (рант круговой) нижний край заготовки и рант, пришитый к нему, скрепляют с основной стелькой тексами (маленькими гвоздиками), которые видны на стельке внутри обуви. Обувь парко I более легкая, гибкая, но менее формоустойчивая и надежная, чем парко II и III, поэтому ее выпускают для детей младшего возраста, а обувь парко II и III — для более взрослых детей.
Прошивной метод отличается наличием сквозного ниточного шва на подошве и стельке, отсутствием ранта, его применяют для изготовления спортивной, домашней и дорожной обуви.
Рантопрошивной метод. Применяют обычную стельку без губы. Рант пришивают к заготовке и стельке сквозным швом, затем к ранту пришивают подошву. Этот метод менее трудоемкий и материалоемкий, чем рантовый. Однако обувь уступает рантовой по надежности и удобству; ее легко отличить по наличию шва на стельке.
Бортовой метод отличается тем, что используется подошва с бортиком, и шов, скрепляющий подошву с заготовкой, располагается выше грани следа. Обувь легкая, гибкая, удобна в носке. Выпускают опанки, туфли и полуботинки летнего и весенне-осеннего назначения.
Выворотным методом изготавливают чувяки, туфли комнатные и дорожные. Они не имеют основной стельки, подошва кожаная или войлочная. Подошву подрезают с бахтармы на расстоянии 12-14 мм от края по всему периметру — получают губу. Заготовку выворачивают на изнанку, и затяжную кромку сшивают с губой. После скрепления обувь выворачивают на лицевую сторону, внутрь обуви вкладывают картонную стельку, обклеенную тканью. Обувь легкая, мягкая, гибкая.
Втачным методом изготавливают пинетки (обувь для новорожденных) и чешки. Для подошвы используют мягкие кожи для верха обуви и подкладки, фетр, ткани, трикотажные полотна. Подошву с заготовкой соединяют тачным швом. В обуви отсутствует основная стелька, жесткие задники и подноски. Это легкая, мягкая, гибкая обувь.
К химическим методам крепления относят клеевой, метод горячей вулканизации, литьевой.
Наиболее широко применяют клеевой метод. Подошву прикрепляют к заготовке клеем. Применяют наиритовый, перхлорвиниловый, нитроцеллюлозный, полиуретановый и др. клеи. Достоинство этого метода — в его универсальности. Им можно изготовить обувь любого целевого назначения (повседневную, модельную, спортивную, домашнюю), разного сезонного и поло-возрастного назначения, из различных материалов. Прочность клеевого крепления не зависит от толщины скрепляемых деталей. Обувь легкая и гибкая, имеет низкую материалоемкость, проста в исполнении. Конечно, она менее надежна, чем обувь гвоздевого крепления; ее гигиенические свойства ниже по сравнению с обувью ниточных методов.
Метод горячей вулканизации позволяет получить очень прочное, герметичное соединение подошвы с заготовкой. Обувь отличается высокими влагозащитными свойствами, надежностью в носке. Материалы для верха обуви должны быть термостойкими. Для подошвы и каблука используют резины. Выпускают повседневную обувь (летнюю и утепленную), домашнюю и производственную. Для модельной обуви не применяют. Метод горячей вулканизации имеет две разновидности: прессовую и котловую вулканизацию. В первом случае, формование подошвы, ее вулканизация и прикрепление к заготовке осуществляются в одной пресс-форме. Обувь прессовой вулканизации можно отличить по наличию следов выпрессовок от стыка полуматриц пресс-формы в носочной и пяточной частях подошвы, а также по фирменному знаку обувной фабрики на геленочной части подошвы с ходовой стороны. В случае котловой вулканизации, детали из сырой резиновой смеси (подошву, каблук, обсоюзку и другие) сначала приклеивают к заготовке. Затем проводят вулканизацию в специальных котлах. Обувь котловой вулканизации можно распознать по резиновым деталям, наклеенным на детали верха.
Литьевой метод. В одной пресс-форме осуществляются формование подошвы и ее прикрепление к заготовке. Для подошв используют термопластичные полимеры: полиуретан, поливинилхлорид, термоэластопласты, полиэтилен и др. Применяют для изготовления повседневной, модельной, домашней, спортивной и производственной обуви. По свойствам близка к обуви прессовой вулканизации. Отличается наличием следа от литника на подошве, подошва имеет более четкие грани и зеркальный блеск, можно получить более тонкие подошвы и более изящную обувь.
Комбинированные методы крепления представляют собой сочетание двух различных методов, чаще ниточных с химическими. Например, рантово-клеевой (рис.), доппельно-клеевой, сандально-клеевой, клеепрошивной, строчечно-клеевой (рис.), гвозде-клеевой и др. методы крепления.
Каблуки приклеивают или прикрепляют с помощью штифтов (гвоздей, шурупов, металлических втулок). Средние и высокие каблуки прикрепляют комбинированным способом (штифто-клеевым). Набойки приклеивают, прикрепляют гвоздями или специальными штифтами.
Заключительную отделку обуви проводят чтобы: придать обуви красивый внешний вид; устранить дефекты, возникшие при изготовлении; повысить водостойкость кожаных деталей. Отделка низа обуви включает фрезерование уреза (торцевой поверхности) подошвы, каблука, набойки, шлифование отфрезерованных поверхностей, окраску и полирование уреза и опорной поверхности подошвы и каблука. Использование предварительно обработанных деталей низа упрощает или исключает заключительную отделку низа обуви. Отделка верха обуви включает чистку (удаление загрязнений с деталей верха механическим или химическим способом), заделку мелких поверхностных дефектов (царапин, пятен, осыпания покрытия), разглаживания складок и морщин утюжкой, аппретирование, создание теневых эффектов на наружных деталях верха распылением краски через трафарет.
Похожие статьи
znaytovar.ru
Пошив обуви вручную: vizioner25 — LiveJournal
В этом посте я расскажу как начиналось и выложу фотоисторию последнего проекта.Когда 2 года назад я решил развивать новое хобби, то столкнулся с несколькими проблемами:
1) на русском языке информации об этом ремесле нет вообще, а если есть то в основном описываются устаревшие методы работы;
2) найти русскоязычных специалистов через интернет практически невозможно, потому что основной массив людей, которые умеют это делать уже приклонного возраста и им не до интернета;
3) купить инструмент вообще проблема, так же как и материал.
Долгие поиски привели меня к нескольким мастерам, с которыми я общаюсь до сих пор. Эти люди активно помогают, да и вообще классные ребята. Средни них — Олег Заремба из Киева, мастер очень высокой категории, его работы просто фантастика!
Здесь можно посмотреть небольшую презентацию работ (фото с fb) http://www.youtube.com/watch?v=YpvZ9kS5Mx4
А в России я общаюсь с Андереем Кавешниковым. Он так же как и я давно загорелся этим делом и весьма преуспевает в нем, правда периодически просит за советы закинуть «пятихатку на мобилку», ну или «соточку» :)) Ну, это юмор конечно у нас такой (Андрюха, не обжиайся). Андрей живет в Москве и часто помогает с покупкой материалов или инструмента. Вот его страничка в вк http://vk.com/id957804
Сейчас круг знакомств расширяется и в принципе становится проще.
В фейсбуке есть хорошее сообщество, где общаются наверно почти все европейские и американские ремесленники.
Во Владивсотоке я нашел хорошего человека и мастера из области ремонта. Вместе с Виктором Ивановичем мы учимся и пробуем новые технологии, спорим и обсуждаем о разных процессах. Вообще повезло, что здесь есть человек, которому тоже интересно. В свое время я зашел почти в каждую мастерскую по ремонту обуви с просьбой помочь — везде приклеили бороду, кроме отелье «Петелька» в центре. Поэтому если вам нужен качественный ремонт обуви — идите туда. Там спец с тридцатилетним опытом работы:)
Вот такая фабула. Далее я покажу фотки с процессами последнего пошива. Я пока учусь и мне далеко до совершенства. Каждая пара — это опыт, ошибки, позитив и работа. Пока не было проектов, которыми я 100% был бы доволен. В процессе описания каких-то процессов у меня могут быть ошибки (это для снобов «мастеров). Просто у меня есть цель в этом направлении и пока не добьюсь ее — не отступлю. Надеюсь, что эти картинки будут интересны новичкам и вообще всем, ведь это ремесло только начинает возрождаться в нашей стране.
Цель была такая — попробовать новый метод сборки, да и фасон «дерби» еще раз попрактиковать, так как Кавешников А. меня постоянно троллит оксвордами 🙂
Метод сборки называет Strom welt, картинка ниже:
В общем, обычно я пользовался верхним способом — когда рант (welt) уходил под затяжную кромку. Сейчас же я хочу оставить его снаружи, пришив де просто строчкой, а декоративной строчкой, так называемой «косичкой» (goiser stich).
Фото косички (не мое, для примера, мое будет ниже):
Итак, процесс пошел:
Делаю лекала
Перфорирую вручну
Исрпользую специальную серебрянную ручку, легко стирается и хорошо видна. Вырезаю ножом
Для зигзага использую ножницы, сейчас ищу меньший размер
Тоже самое делаю с деталями подклада, а справа лежит материал на межподклад, так как кода верха мягковата, нужно уплотнить
Помечаю линии для строчки
Под перфорацию подкладываю кожу, чтобы сохранить цвет
Приклеиваю межподклад и прошиваю детали верха
Клею тесьму, чтобы кант ботинка не растягивался
Далее приклеиваю бизик (точное название не помню 🙂 ), придает хороший вид
Сшиваю детали подклада
Тесьма ставится для того, чтобы клей при затяжке не просачивался сквозь строчку
Прошил берцы к задней части подклада
Примеряю 🙂
Сшиваю оставшиеся части
Нужно сказать, что эта машинка сделана не для машина, а для ремонта обуви — она очень грубая и большая. Поэтому я купил новую супер-секси машинку, которая предназначена для пошива 🙂 ее фото будет ниж.
Вот что получилось
Делаю предварительную затяжку, чтобы наметить место под рисунок на носу
Тем временем пробую плести косичку. Нужно сказать, что на всем видео и фото с косичками используется нить почти в 2 раза толще, чем есть у меня. Так как моя нить тоньше, то пришлось и длину стежка делать меньше, всего 5 мм. И на прошивании ранта время таким образом увеличивается в 2 раза.
Пробую деформировать так, как будет при сборке. Появились морщинки в связи с тем, что рант толстый. Поэтому я его благополучно сузил.
Был 2,5, стал вот такой
Пришло время работать со стелькой
Тем временем заготовка сформовалась и пора делать рисунок на нос, заготовка у меня уже была
Наметил и вручную выбиваю
Получилось вот так
Обязательно подкладку, иначе под перфорацией будет белая подкладка. Некоторые просто подклад красят, но на мой взглдя это не очень.
Продолжаю возиться со стелькой
Вырезал «губу» — это та часть, за готорую будет «цепляться» рант с помощью ниток.
Эластичный бинт помогает сформовать стельку, чтобы она идеально приняла форму следа колодки.
Пока стелька формуется делаею жесткие задники. Вставляются между верхом и подкладом для придания жесткоски и формоустойчивости. Потрогайте свою пару — у вас тоже есть, но скорее всего не из кожи :). В этой паре есть небольшой косяк с высотой задника, обусловлено это сборкой верха. В след раз учту
Проверяю толщину.
Вот все детали для придания формоустойчивости. Белый материал — это термопласт. При нагревании становится мягким, принимая заданную форму (ставится на носок). Так же его называю «пинг-понг», потому что он возвращается назад при нажатии. Очень удобно. Обычно я ставлю кожу на подносок, но пока не определился, что нравистя больше.
Вот так выглядит стелька после бинта — идеально прилегает к колодке
Пришло время готовить рант
Намечаю канавку под стежок с помощью специального грувера
Потом делаю разметку под стежок с помощью этого колесика (расстояние 5 мм)
Это я сравниваю разные варианты, как сделать рант еще и красивым, интересным.
В итоге вот такая штука, но в дальнейшем я использовал зиг-заг (будет видно). Вообще в процесс пошива пары проводишь много экспериментов, это увлекает 🙂
Пришло время затягивать пару и я вставляю жетский задник на свое место — между верхом и подкладом
Тоже самое с остальными деталями
Подтягиваем материал
Фиксируем гвоздями. Может показаться, что это простая операция, но на самом деле одна из самых сложных и долгих.
Получилось вот так
Между делом мне приехала профессиональная швейная машинка для пошива верха обуви Garudan, это было торжество! 🙂ё
Вот такую строчку дает 🙂
Просто шик! Жду следующую пару с нетерпением
А вот как раз установка термопласта на подносок
Вот такой цвет и фасон ранта я решил сделать
Готовлю рант — пробиваю отверстия для стежков
И вырезаю зиг-заг
Начал прошивать
Именно здесь я понял, что рант у меня толстый (2,5) — получаются морщинки на сгибе
Поэтому я сделал новый рант, а старый отпорол. Вот здесь видно, как он крепиться к стельке
Обувь изнутри
Супинатор для поддержания свода стопы + устойчивать (дада, у вас тоже такой есть в ботинке) 🙂
Пробка придает комфорт и эастичность.
А потом клеиться подошва
Подошва вид сверху
Далее делается специальный надрез с торца уреза, кожа отгинается и с помощью этого уникального инструмента делается канавка под строчку, которая сшивает подошву и рант.
Вот так и сшивается
После прошивки кожа заклеивается, таким образом строчка прячется и ей не грозит порыв из-за соприкосновения с землей (асфаль и тд).
Между делом сделал приятно Жене 🙂
После набирается каблук. К сожалению, у меня нет фото процесоов набора фликов, потому что эту черновую работу (со станком) дома я делать не могу, а в мастерской у Виктора как-то не фотографируется (забываешь).
Срезаются лишние участки и боковой урез красится
Обработка уреза для меня самая великая проблема, так как нужна специальная химия и двигатель с возможностью регулирования оборотов. Пока этот процесс у меня приметивен — натираю воском и полирую сукном + катушкой с конским волосом. Вообще у меня есть все необходимые катушки, нет химии (спиртовые грунты и тд) и 800 оборотов в минуту. Но это всего лишь дело времени, как-то так.
Пока не вощеный урез
Решил сделать такую стельку :))))) внутри полустелька из паралончика
Цвет подкала не самый лучший, но Андрей предложил хорошую идею — в следующий раз покрашу кожу
Урез после обработки
Конечный результат
И крупнее
В целом, я доволен результатом. Потратил на это дело около 1,5 месяцев. Буду продолжать выкладывать посты, потому что это позволяет структурировать работу. Помимо этого всем рекомендую вести дневник, где можно записывать всякие спорные моменты, чтобы потом проверить на паре и либо продолжать делать так же, либо не делать никогда :))
Есди вам было интересно — подпсиывайтесь
http://instagram.com/itskov
https://www.facebook.com/sergey.itskov
vizioner25.livejournal.com
Умная обувь.Технологии и материалы в обувной индустрии
Сегодня практически у всех российских и зарубежных производителей, если только они не работают в сегменте дорогой элегантной женской обуви, в портфеле коллекций обязательно найдутся «морозостойкие», «влагостойкие», «ветронепродуваемые», «грязенезапачкивающиеся» — словом, в огне не горящие, в воде не тонущие ботинки, сапоги, туфли, ботильоны, слипоны, кроссовки, сникерсы, лоферы и прочие виды обуви. При этом, такая обувь теперь выглядит современно, элегантно и очень модно, она легкая и очень удобная в носке.У нее есть, пожалуй, только один существенный минус — ее высокая стоимость. Основная часть себестоимости инновационной обуви складывается из дорогих материалов и лицензии на использование запатентованных технологий, которых, как правило, сами обувщики не имеют, и поэтому покупают у разработчиков – многопрофильных компаний, холдингов, специализирующихся на инновационных материалах и технологиях. Лидерами этого рынка являются крупнейшие производители спортивной одежды и обуви, компании W.L. GORE&Associates, DuPont, GEOX Breathes и другие.
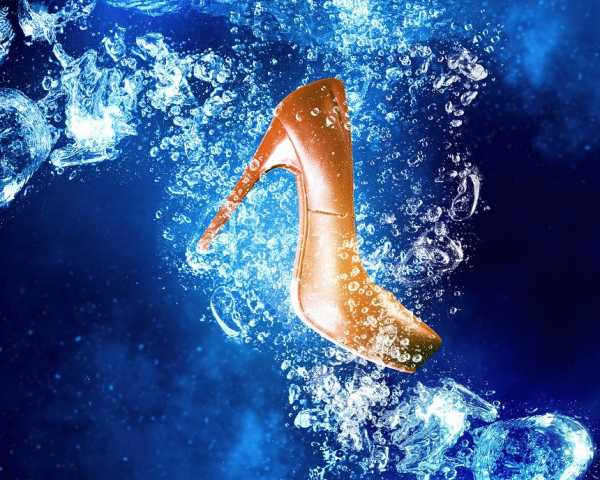
Дышащие ботинки и вязаные кроссовки
Наши ноги большую часть дня находятся в замкнутом, закрытом пространстве – то есть, в обуви. И какая бы она ни была замечательная, мягкая и удобная, все равно лучше без нее. Но поскольку в современной жизни это невозможно, от обуви мы отказаться не можем.
Если обувь качественная, из натуральной кожи, подобрана по размеру и с удобной колодкой, дискомфорта от нее немного, ноги, как говорят, спят, отдыхают в ней. Единственная проблема, которую очень долго дизайнеры и технологи не могли решить, заключалась в том, что ноги потели и не дышали. Особенно это ощущалось в походах, во время продолжительных прогулок, при больших физических нагрузках. По результатам опросов, в основном только две вещи портят впечатления от пешего туризма: плохая погода и неподходящая обувь. Наука помогла решить эту проблему. На рынке появились первые в мире со всех сторон дышащие водонепроницаемые ботинки GORE-TEX с технологией SURROUND – в общей сложности более 200 моделей в коллекциях 29 брендов-партнеров (Lowa, Salewa, Ecco, Hanwag, La Sportiva, Mammut, Meindl, Scarpa, а также бренды-новички — итальянские Aku, Asolo и Garmont, норвежский Viking, американский Kamik). Одной из самых ярких новинок сезона-2016 станут первые в мире вязаные кроссовки X-SO Wave GTX с технологией GORE-TEX SURROUND от Meindl для мужчин и женщин. Производитель называет эту модель «вязаные ботинки», но это все-таки именно кроссовки, вязка в комбинации с бесшовной конструкцией в передней части обеспечивает большую гибкость и удобство модели. Инновационная, доходящая до подошвы система шнуровки обеспечивает ноге необходимые поддержку и устойчивость.
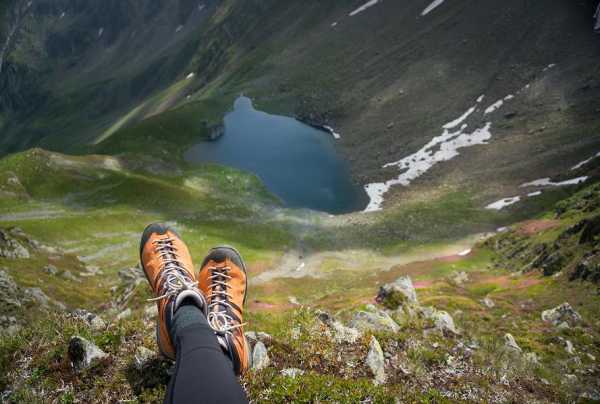
Обувь с технологией GORE-TEX SURROUND является самой последней инновацией для поддержания комфортного климата для ног и защиты от плохой погоды. Основные отличительные особенности — продолжительная водонепроницаемость и дышащая способность. Обувь дышит со всех сторон, включая подошву, благодаря тому, что в ботинок интегрирована водонепроницаемая, «дышащая» мембрана GORE-TEX, полностью охватывающая стопу. Между стопой и подошвой предусмотрена «прокладка» с открытой конструкцией. Пот проходит через мембрану и попадает в открытую конструкцию «прокладки», а уже оттуда выводится через боковые отверстия в подошве наружу. В результате мозоли и натертости, появляющиеся на потных или разгоряченных ногах во время длительных походов, исключены. Эта технология успешно адаптирована производителями и для повседневной и детской обуви. Но здесь техническое решение выглядит немного иначе: излишняя влага и тепло отводятся непосредственно через отверстия в подошве вниз или, как у Ecco, вбок. 17 брендов-партнеров предлагают обувь GORE-TEX SURROUND на каждый день в своих коллекциях (Lowa, Salewa, Viking и другие).
Уникальные технологии, делающие обувь «дышащей», есть не только у W.L. GORE&Associates. Так, итальянская марка GEOX применяет при изготовлении обуви и собственные разработки, способствующие уменьшению перегрева ног: зимой ноги остаются в тепле, летом – в прохладе и всегда – сухими. Одна из запатентованных технологий – GEOX AMPHIBIOX, это специальная микропористая влагозащитная мембрана, устанавливаемая в резиновую подошву. Она защищает от дождя и снега, улучшает дышащие свойства обуви, обеспечивая естественную терморегуляцию. Любопытный факт: в 2012 году, чтобы продемонстрировать качества и высокий уровень влагозащищенности, обувь с подошвой, в которой использована мембрана AMPHIBIOX, проверили на прочность в самом дождливом месте на планете – регионе Черрапунджи (Индия). Обувь успешно прошла испытания и затем, в 2013 году, производитель решил проверить ее в обычных городских условиях: «создали дождь» сделали так, что человек жил под непрекращающимся дождем 7 дней. И в этот раз обувь выдержала экстремальную «влагонагрузку».
Еще одна запатентованная технология – GEOX NEBULA – обеспечивает обуви легкость и дышащие свойства. Специальная внутренняя подкладка с воздушными карманами создает пустое пространство между стопой и верхом обуви, избыточное тепло при этом выводится вверх. Технология обеспечивает отвод избыточного тепла, оптимальную амортизацию и гибкость подошвы, защиту от скольжения (за счет комбинации каучуков и специально смоделированной капсульной подошве). Вообще инновационная форма подошвы (плоская под пяткой и сферическая в других местах), обеспечивающей стабильность – гордость бренда.

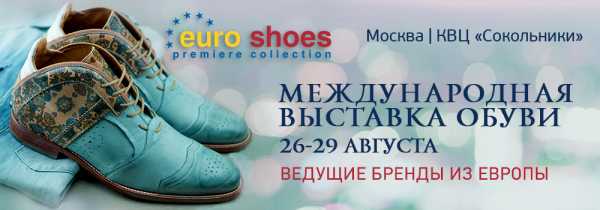
Все лучшее — детям
В детском сегменте новые технологии особенно востребованы. Дети постоянно ищут приключений, их ноги всегда в движении. Родители стараются выбирать своим мальчикам и девочка самую функциональную и качественную обувь. С другой стороны, все родители хорошо знают: чтобы ребенок с удовольствием носил обувь, она должна быть не только функциональной, но яркой, красивой, она должна нравиться мальчику или девочке по дизайну.
Наиболее важные критерии для современной детской обуви – качество, комфорт, натуральные материалы. Поэтому перед разработчиками детских моделей стоит непростая задача: создать красивую, модную модель, но при этом такую, в которой бы детские ножки чувствовали себя комфортно очень длительное время, на улице и в помещении. Для этого используются разные хитрости, одна из них — инновационная подошва с технологией SURROUND – с применением многослойного материала, в основе которого лежит водонепроницаемая и дышащая мембрана GORE-TEX. В ней 1, 4 миллиарда микропор на 1 кв. см. Эти поры в 20 000 раз меньше капель воды, но в 700 раз больше молекулы водяных испарений. Мембрана окружает детскую ногу, позволяя избыточному жару и поту проходить через отверстия в подошве с инновационной структурой и препятствуя проникновению влаги снаружи. Покупатели могут сами определить наличие этой технологии в обуви: если в структуре подошвы есть отверстия, это явно говорит о том, что данная обувь дышит. Партнеры GORE-TEX создают модели самых разных стилей и цветов, и теперь используют «дышащую» подошву в качестве элемента дизайна. Такую функциональную детскую обувь, в которой всегда тепло и сухо, можно найти у таких детских брендов, как Primigi и Superfit.
Детские бренды активно сотрудничают с медицинским сообществом и разрабатывают собственные технологии. Так, австрийский бренд Superfit постоянно работает с врачами-ортопедами и европейскими институтами ортопедии, в результате чего были разработаны такие собственные технологии, как амортизирующая пяточная подушечка, предотвращающая заваливание маленького ребенка назад, удлиненный задник для надежной фиксации ступни, усиленная боковая часть ботинка, широкая носочная часть, не деформирующая и не сжимающие детские пальчики. В детской обуви для зимы очень важны детали – чтобы подошва не скользила, чтобы шнуровка была анатомически правильной, плотно прижимающей обувь к ноге, но при этом не очень тугой. Этой зимой бренд сделал ставку на практичность: при создании моделей зимней коллекции использованы водоотталкивающая натуральная кожа и замша, микрофибра, полиэстер – материалы, позволяющие сохранить внешний вид обуви, делающие ее более долговечной и простой в уходе.
Немаловажным является и то, из каких материалов произведена детская обувь. Многие производители детской обуви сегодня используют в производстве размягченную без хрома кожу. Серьезные производители сами проверяют используемые материалы на токсичность и не боятся отдавать свою обувь на исследования сторонним контролирующим организациям. Если обувь прошла тестирование на содержание вредных веществ, на ней должна стоять маркировка «нетоксично», или информации о соответствии экологическим стандартам будет в сертификате, инструкции, на сайте производителя. Многие производители выпускают специальные эколинейки или коллекции обуви с «зеленым» ярлычком.
Эта статья была опубликована в номере 132 печатной версии журнала.
Сегодня практически у всех российских и зарубежных производителей, если только они не работают в сегменте дорогой элегантной женской обуви, в портфеле коллекций обязательно найдутся «морозостойкие»,…
www.shoes-report.ru
Как они это делают: Технолог по обуви
Елена Качоровская об особенностях профессии
Выбирая новую обувь, мы в первую очередь прислушиваемся к внутреннему голосу, который шепчет, что эта пара пусть и 120-я, но очень нужна в нашем гардеробе (и что еще точно получится протянуть неделю на гречке). Мы по памяти прикидываем, с чем можно надеть новую обувь, проверяем застежки, определяем на запах кожу, несколько раз прохаживаемся взад-вперед, чтобы понять, удобно ли села нога, достаточно ли блестят камни на носке или подрагивают перья на щиколотке. Но на самом деле мы никогда не задумываемся над тем, как делают обувь и что происходит после того, как дизайнер придумал пару и нарисовал свой эскиз.
Знакомьтесь: Елена Качоровская, технолог по обуви с 20-летним стажем, одна из основательниц украинского бренда Kachorovska_Atelier. Елену сложно поймать — она, как призрачный гонщик, носится из цеха в цех, контролируя процессы на всех этапах производства. При виде Елены сотрудники улыбаются и расправляют плечи. Заметно, что ее здесь любят.
Как вы пришли к этой профессии?
Мне кажется, это судьба для нашей семьи. Я уже в этой профессии больше 20 лет. Моя мама занималась обувью, она швея, у нее стаж более 30 лет, суперпрофессионал своего дела. Когда я была маленькая, мама работала в государственном ателье и шила мне туфли на заказ. Брат тоже занимается обувью. Сейчас мы работаем с ним вместе — он шьет для нас мужскую обувь по старинным технологиям.
Помните свою первую пару, которую для вас пошили?
Да, я никогда ее не забуду. Это был 8 класс, ярко-желтые босоножки на невысоком каблуке и с кожаной подкладкой, практически такие, как мы сейчас делаем. Это была моя первая взрослая пара, и я очень долго ее носила.
С чего началась ваша карьера?
Я окончила восьмой класс с золотой медалью, и мне захотелось взрослой жизни. Я поехала в Киев поступать в техникум обувной промышленности на самый простой конкурс, чтобы 100% попасть и остаться учиться. Кстати, я сейчас единственная со всего курса, кто после выпуска работает по профессии. (Смеется.) Потом продолжила учебу в институте легкой промышленности [сейчас КНУТД. — Buro 24/7].
После университета — сразу на работу ?
Да, на фабрику. Я пришла как технолог, а потом стала замдиректора по качеству. Институт дает только корочку и навыки, практические знания я получила в процессе работы. Во времена перестройки на нашей фабрике заказывали обувь чехи, немцы, итальянцы. Они привозили полностью все свое сырьё, а мы изготавливали обувь. Для меня это был огромный опыт, я научилась делать все, включая документацию.
Параллельно я начала вести свой небольшой бизнес. После работы я приходила домой, и мы с мамой вдвоем шили заготовки, а утром приходил сапожник и их забирал. Готовые пары я ездила продавать по воскресеньям на рынок.
Однажды к нам приехала на фабрику технолог из Болгарии делиться опытом — и я ей рассказала про свой маленький «бизнес». Тогда она мне посоветовала уйти с фабрики и начать развивать свое дело, потому что параллельно ничего не получится, и это дало мне невероятный толчок, добавило уверенности.
В то время моды как таковой в Советском Союзе не существовало — как вы придумывали модели?
Было очень сложное время. С 1995-го по 2000-й нужно было крутиться, чтобы выжить и прокормить семью и двоих детей. В нашем районе Малёванка [в Житомире. — Buro 24/7] через дом живут сапожники. По городу всегда было много ателье по пошиву на заказ, и я тоже построила свою маленькую мастерскую. Затем 4 раза ее перестраивала — расширяла.
Для меня самым важным всегда было качество, и этим мы старались отличаться. Я сейчас когда вспоминаю наши модели того времени – мне кажется это чем-то нереальным. Ничего не было, трудно было достать качественные подошвы и каблуки. Журналов особо не было. Я ходила в дорогие магазины, чтобы посмотреть на привезенную итальянскую обувь.
Получается, что вы как учились на технолога, так и продолжили работать по профессии. У вас никогда не было амбиций стать дизайнером?
Нет, я совершенно не умею рисовать. У меня даже нет представления, как это делается правильно. В те времена, когда я делала обувь сама и у меня не было возможности нанять модельера, самым важным было показать на эскизе линию, ее я чувствую. Причем это «ощущение линии» происходит на уровне интуиции. Если, к примеру, вывели не ту форму, я это вижу сразу, еще на этапе колодки, когда обувь только подтягивают. Или могу, например, проходя мимо, посмотреть на рисунок модельера и тут же сказать, что мне не нравится пропорция, подкорректировать.
Сколько времени уходит на изготовление одной пары — от эскиза до готовой обуви?
Два-три дня.
А сколько этапов в производстве?
Четыре. Заготовка, затяжка, колодка, подошва, все вместе и получается — готова пара. Если учитывать прием заказа — то пять. Это отдельный процесс — с клиентом работать очень сложно, если мы говорим об индивидуальном пошиве, не о массовом.
Отдельным этапом в пошиве обуви на заказ также идет изготовление колодки. К мастеру приходят мерки клиента, и он уже смотрит, все ли пальцы на одном уровне, какие есть особенности ноги, где какой выступ. Все это нужно учитывать, чтобы готовая пара была максимально комфортной, нигде не терла, не жала. После первой сборки мы отправляем пару на примерку клиенту, чтобы учесть все замечания. Потом снова забираем на производство и уже доделываем.
То есть на handmade-пару уходит еще больше времени?
Да, это еще и ручная затяжка. Сейчас я объясню. Во-первых, обуви нужно выстояться — как говорят, «чтобы звенело», — нужно, чтобы заготовка побыла на колодке минимум два-три дня, тогда кожа высохнет естественным путем, без сушки. Таким образом кожа, у которой есть свойство растягиваться, примет нужную форму и она не деформируется — это залог качественной пары. Такую обувь можно носить годами. Но тут еще все зависит от кожи. Для хорошей обуви нужна хорошая кожа.
У кожи есть разные виды, как вы их отбираете и где заказываете?
Да, все верно, для летних пар — одна кожа, для зимних — совсем другая. Для модельной обуви, к примеру, идет совсем тонкая кожа толщиной в 0,8 см, для мужской обуви — более грубая, плотная. Это выкраивается с разных участков шкуры закройщиками уже согласно полученному заданию.
Допустим, клиентка приходит в ателье в Киеве, и ей нравится цвет кожи. Она говорит: «Я хочу лодочки из этой кожи в этом цвете». Когда заказ приходит к нам на производство, мы уже смотрим, соответствует ли кожа модели, и это не всегда совпадает. Тогда приходится объяснять клиенту, почему она не подходит, и искать компромиссы. Всю кожу мы везем из Италии.
В Украине нет производств по коже?
Все материалы, которые делаются для обуви в Украине, неидеальные. Сколько лет мы работаем на этом производстве, столько у нас проблемы с местными поставщиками комплектующих. Производители — безответственные. На мне лежит ответственность за конечный продукт. Если треснул или лопнул супинатор — это происходит из-за некачественной стельки, лопнул каблук — значит, гвозди были недостаточно закалены. Материалы некачественные, а отвечать потом за них мне — от этого страдает имидж.
То есть не только кожу, но и составляющие заказываете за границей. Но это дороже по себестоимости?
Ненамного, но это время — доставка, растаможка. Мы пользуемся услугами перевозчиков, но за это тоже платим большие деньги. А до этого это все нужно найти, съездить посмотреть образцы, заказать. Если мы хотим, чтобы лодочка в итоге была как у Prada, мы не можем работать с отечественными производителями — нет таких каблуков.
Итальянцы — законодатели моды и качества. Я, когда туда приезжаю, просто «тащусь» от того, как классно они все делают, как у них налажено производство, есть любые материалы. Мы никогда не сделаем лучше, чем в Италии. Мы стараемся делать как они, но…
Сейчас большинство дизайнерской обуви итальянской делают на замшевой или кожаной внешней подошве. Но это абсолютно непрактично, потому что в ней нужно ходить по улице, а не дома по ковру.
Считается, что это очень хорошо для ног, — это такая «прихоть для богатых». Мы ставим после кожаной подкладки еще искусственный картон и кожволон, а это все искусственные материалы. А тут кожа и внутри, и снаружи. В такой обуви нога никогда не будет потеть, будет «дышать». Это очень гигиенично.
Поэтому оно столько стоит?
Да, такая обувь дорогая, очень дорогая. И вообще, я хочу вам сказать, что хорошая обувь не может стоить дешево. У меня сапожники делают полторы-две пары в день. Над каждой моделью нужно помудрить, должны быть идеальные строчки (миллиметр от края), а для этого нужно мастерство и время. Поэтому я не могу подгонять мастеров и требовать от них высокого качества одновременно. Это ручная работа.
Какими качествами должен обладать мастер, кроме усидчивости?
Усидчивость, усидчивость, усидчивость. А еще глазомер и желание. Нужно очень любить свою работу. Бывает так, что мы берем нового человека в команду, а человек не любит эту профессию. Ну не то чтобы не любит, просто для него это обычная работа, он просто «отбывает» рабочее время, без особого желания. А если у тебя есть к этому способности, талант — тогда будет получаться, будешь делать красивую, интересную обувь.
Молодежь идет осваивать эту профессию? Все же хотят быть программистами.
Молодежь очень тяжело идет, но если уже приходят — остаются. Вот работает молодой парень у нас (показывает в цеху) со вчерашнего дня и так стремится, что мы дали ему уже затягивать пару самостоятельно. А вот, например, Толик, он пришел полгода назад. По профессии он «компьютерщик», но я увидела в нем талант и смогла переубедить работать у нас.
Мы стараемся привлекать молодежь, передавать знания. Эта профессия не популярна, про нее не говорят, о ней не знают. На самом деле сапожником не каждый сможет работать — это творческая профессия.
Старшее поколение охотно делится секретами мастерства?
Я курирую этот процесс, и такой проблемы нет. Наоборот, мы должны друг друга тянуть: работы очень много и нужно все успеть. Поэтому никто не боится остаться на улице. Наоборот, нам негде взять еще больше людей, кадров нет.
У меня в коллективе есть люди, с которыми мы работаем вместе 15-18 лет, каждый день. Мы уже как одна большая семья.
Есть какие-то национальные технологии – украинские, «особенные»?
В принципе, нет, базовая технология одинаковая по всему миру. Есть, конечно, свои маленькие нюансы.
Авторский секрет Качаровских?
Качество, что бы там ни было. Будут умирать, просить сделать обувь быстрее, потому что пустуют магазины, — мы будем отказывать. Некоторые люди в погоне за деньгами теряют бдительность, но не мы. Для нас важен конечный продукт, чтобы было приятно смотреть на пару. Поэтому я считаю, что у нас нет конкурентов.
Какие украинские дизайнеры отшивают у вас обувь?
Ой, их так много, всех и не вспомню: Катя Сильченко, Елена Рева, Андре Тан. Когда начинается подготовка к неделе моды, мы практически работаем на них. Когда-то делали капсульную серию для Надежды Мейхер [сейчас Грановская. — Buro 24/7].
Но это все женская обувь, а как обстоят дела с мужской?
Мужская — это 20-30 % из индивидуального пошива. Заказы в основном приходят из-за границы: Франция, Англия. Причем заказывают частным образом по десять пар сразу. Там очень ценят ручную работу.
В магазинах сейчас сказочный выбор обуви. Какой совет вы дадите человеку, который приходит в магазин ее покупать, на что обратить внимание?
В первую очередь вам должно быть комфортно, когда надеваете пару, чтобы вам не хотелось тут же ее снять. Не думайте, что пара разносится. Если сразу неудобно — колодка не ваша, не лег правильно подъем. Потом ничего не поменяется.
Какая в среднем гарантия у хорошей пары обуви, с учетом того, что ее адекватно носят?
У меня был случай, когда пришла клиентка и сказала: «Я ношу вашу пару 8 лет, она не рвется, просто мне она уже надоела, а рука не поднимается выбросить». Вот вам и ответ. Если обувь сделана из качественной кожи, выстояна по технологии, она может прослужить и 10 лет. Но для этого у женщины должно быть как минимум 5-6 пар обуви, чтобы она их могла чередовать, а не носить одну постоянно.
Какая модель, на ваш взгляд, сейчас на пике популярности?
Лодочка с каблуком от 5 до 10 см. В том количестве, как мы в Украине, наверное, никто не производит лодочки. Они популярны вне сезона. Мы были на фабрике в Италии и показывали свои лодочки. На что нам один из дизайнеров сказал: «Все красиво, только я бы чуть-чуть опустил носок».
А вес человека при ходьбе должен распределяться на пучках, а не на носочках. Поэтому он нам и сделал замечание — у них носки стоят идеально ровно, а у нас — вздернутый носок, чтобы нога не зажималась и было комфортно не только стоять, но и ходить в лодочках.
Сейчас стремительно развиваются технологии, обувь уже начали даже печатать на 3D-принтере. В будущем будет популярна обувь ручной работы или это все канет в Лету?
Никакие компьютеры не заменят ручной труд. Поэтому мне так хочется сохранить этот сегмент, не уходить полностью в массовое производство. В 90% случаев у клиентов «нестандартные» ноги. Они могут позволить себе и дорогую итальянскую обувь, но не могут в ней ходить. На «лубутенах» можно простоять не более получаса. Поэтому обувь на заказ будет актуальна всегда.
Учитывая все моменты с качеством и «безответственностью производителей», какое будущее у обувной индустрии в Украине?
Поменяется, если придет новое поколение. Я смотрю на своих коллег, которые работают в Житомире, — конечно, они стали работать лучше, по сравнению с тем, что было, но все еще нет ощущения профессионализма. Нет вот этой эстетики линии, про которую я рассказывала, если речь идет о моделях.
Нужно менять все: отношение к работе, отношение к людям, отношение к культуре. Нужно все новое. Наша мечта — построить фабрику, чтобы у людей там были максимально комфортные условия, чтобы им нравилось приходить на работу. Пока большая часть людей просто «отбывает» на своих местах — будущего нет.
И напоследок дайте один совет начинающему технологу.
Нужно быть профессионалом. Знать все про кожу, колодки, подошвы и т. д. И получить образование в этой сфере, хотя бы базовое.
Читайте также: Как они это делают: Конструктор одежды.
www.buro247.ua