Технология производства стрелкового оружия – Технология производства стрелково-пушечного и артиллерийского оружия | Туктанов А.Г.
Ружейные стволы. Технология изготовления — Энциклопедия оружия и боеприпасов
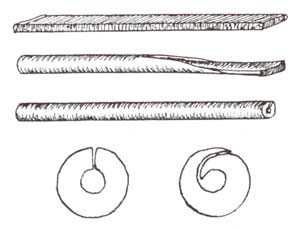
Стадии сворачивания трубки простого ствола.
Вверху — пластина-заготовка для ствола
Вероятно, многие согласятся со мной, что главная часть ружья — стволы. Ведь стреляют именно они. Эффективность пушечных выстрелов вызвала у человека желание сделать маленькую «ручную» пушку. Такую пушку в середине позапрошлого века нашли в замке Таннеберг в Хессене (Германия). Она была отлита в конце XIV века. Стрелять из неё с рук было, конечно, тяжело и неудобно и вскоре к ней приспособили арбалетную ложу. Оказалось, что по точности стрельбы и кучности новое оружие серьёзно уступает хорошему луку, хотя по энергии, а значит и пробивной силе, значительно его превосходит. Довольно быстро выяснилось, что с увеличением длины ствола, выстрелы становятся более точными. С этого момента и начинается история огнестрельного оружия.
Сегодня у нашего «переломного» охотничьего ружья есть три главные части: ствол (или стволы, образующие ствольный блок), колодка, ложа.
Ствол придаёт направление полёту дроби или пули. Чем правильнее и тщательнее он изготовлен, тем лучше дробовая осыпь и выше точность.
Колодка запирает казённый срез стволов, служит связующим элементом между стволами и ложей и является в оружии главным инерционным элементом, поглощающим силу отдачи. В колодке монтируются запирающие, ударно-спусковые и предохранительные механизмы.
Схема получения скрученных ствольных трубок
Ложа обеспечивает удобство наведения оружия на цель, естественность прицеливания и смягчает действие силы отдачи за счёт её частичного превращения во вращательный момент.
Прежде чем рассказать о сегодняшней технологии изготовления оружейных стволов, хочется познакомить читателей с частью оружейной истории, касающейся совершенствования изготовления этой важнейшей части оружия. Ведь изготовить хороший ствол — задача довольно трудная даже при сегодняшнем уровне развития машиностроения. Однако настойчивость, усердие и изобретательность наших далёких предков находила различные варианты решения этой задачи. Причём уровень качества лучших изделий XVIII века сегодняшним специалистам представляется почти загадочным. Нам хочется рассказать, каким путём мастера прошлого создавали замечательное оружие, показать некоторые его образцы и вместе подумать о величии их духа с надеждой, что это укрепит и наш собственный.
В 1811 году Генрих Аншютц (из хорошо известной оружейной династии) издал книгу об оружейной фабрике в г. Зуль. Он пишет о четырёх типах технологий получения ствольных трубок: обычной, скрученной, навитой и стволах из «Дамаска».
Принцип получения навитых стволов
Обычный (простой) ствол получали из полосовой заготовки длиной 32 дюйма (812,8 мм), шириной 4 дюйма (101,6 мм), толщиной 3/8 дюйма (9,525 мм). После разогрева эту полосу кузнечным способом загибали на оправке таким образом, что её продольные кромки прилегали друг к другу встык, параллельно оси канала ствола. Этот стык сваривался кузнечным методом и тщательно проковывался. Есть несомненные указания, что обе длинные стороны прямоугольной заготовки иногда сгонялись «на ус» и сваривались не встык, а внахлёст. После сварки и охлаждения стволы проходили четырёхгранной развёрткой, обтачивали на токарном станке внешнюю поверхность, которую потом шлифовали вручную на большом круге из мягкого песчаника диаметром 1,75 м. С казённой стороны в ствол вкручивалась винтовая заглушка, которая иногда тоже проваривалась. Конечно, «заглушались» стволы всех дульнозарядных ружей, независимо от технологии их получения.
Скрученный ствол. Сварной шов в обычном стволе, располагавшийся параллельно оси ствола, часто был местом разрушения при стрельбе. Чтобы избежать этого, простой сваренный ствол начинали повторно нагревать в центральной части и скручивали вдоль оси по всей длине так, чтобы сварной шов имел форму винтовой линии. Этот приём делал шов значительно менее нагруженным при выстреле.
Навитой ствол получали путём постепенного навивания стальной полосы на оправку в виде стержня или трубы. Винтообразный сварной шов последовательно проковывали кузнечным молотом.
Схема получения полосы дамасской стали
Дамасские стволы. Ещё в средние века в Дамаске (сегодня это Сирия) изготовляли мечи, обладающие исключительно высоким качеством. Как только технология их получения стала понятна европейцам, её попытались применить и для изготовления стволов. Основа секрета состояла в том, что заготовки для клинкового оружия получали кузнечной сваркой полос из тонких элементов, состоящих из сталей различавшихся содержанием углерода. Первоначально сваренную и прокованную полосу многократно складывали и проковывали. По сравнению с обычной однородной заготовкой дамасская обладала тремя принципиальными преимуществами. По сути, она представляла конструкцию, объединяющую свойства отдельных материалов. Кроме того, композиция не только исключала внутренние дефекты, которые бывают в однородной заготовке, но и создавала оптимальную структурную ориентацию. Принципиально дамасские стволы получали методом навивки. Однако для получения исходной полосы приходилось проделать просто титаническую работу. Сначала сваривали брусок из ста прутков сталей разного состава квадратного сечения со стороной 0,7 мм, уложенных в определённом порядке. Брусок получался сечением около 7 мм х 7 мм. Эта процедура требовала невероятно тонкого кузнечного чутья, поскольку пережечь тонкие проволочки было проще простого. Сваренный брусок снова разогревали и скручивали вдоль. Затем брали несколько таких скрученных брусков (чаще три или шесть) сваривали их между собой и расковывали в полосу. В некоторых случаях из этих скруток плели что-то вроде косичек, которые могли состоять из разного числа прядей и иметь разную схему плетения. Косички сваривали и проковывали в полосу. Эту полосу и навивали на оправку. Затем заготовку торцевали, канал проходили развёрткой, наружную поверхность сначала обтачивали на токарном станке, потом шлифовали. Процесс воронения в те времена состоял в обработке довольно сильными кислотами. В результате, малоуглеродистые прутики протравливались значительно сильнее по сравнению с высокоуглеродистыми, и на поверхности ствола появлялся оригинальный мелкий рисунок, отражавший всю предшествующую схему получения полос. Обычно на дамасских стволах ширина полосы видна невооружённым глазом.
Стремительное развитие металлургии в конце XIX века привело к появлению углеродистых сталей с высокими механическими свойствами. Перспективность их использования для изготовления стволов казалась очевидной. Однако ещё в первой четверти XX века многие оружейники Европы продолжали делать стволы по «дамасским технологиям». Сегодня необходимо понимать, что такие стволы, хотя и являются памятниками фантастическому усердию оружейников предыдущих поколений, но всё же уступают по всем важнейшим показателям современным легированным ствольным сталям. Напомним нашим соотечественникам, что сталь 50А и даже 50РА, из которой и в Туле, и в Ижевске делают сегодня стволы, к легированным ствольным сталям не относятся. И ещё о дамасских стволах. Спустя сто и более лет после изготовления весьма вероятно, что кузнечная сварка элементов может значительно разрушиться и прочность стволов может оказаться недостаточной для обеспечения безопасности стрельбы. Будьте очень осторожны при желании пострелять из старого ружья с дамасскими стволами.
Введение в состав углеродистой стали хрома, ванадия, никеля, кремния, марганца и других элементов привело к значительному повышению важнейших свойств ствольных сталей — упругости, прочности при растяжении, поверхностной твердости, коррозионной стойкости. Более того, эти технологии позволяют получать стали с заранее заданными свойствами. Всё это позволило перейти к изготовлению однородных заготовок для ружейных стволов. Этот процесс начался ещё в последней трети XIX века и около полувека сосуществовал с «дамасской» технологией.
Развитие технологии изготовления ружейных стволов.
Рихтовка ствольной заготовки
Новый этап начинается с отказа от стволов, получаемых из полос, и перехода к стволам, канал которых образовывался глубоким сверлением. Эта технология несравненно более производительная, но для её реализации потребовалось решить ряд серьёзных проблем, рассказать о которых нам хочется, чтобы современные читатели могли представить, какой ценой получались ружья, обладающие замечательным боем. Новая технология изготовления ствольных заготовок начинается с ковки, которая не только придаёт заготовке ствола внешнюю форму, приближающуюся к готовому стволу, но и обеспечивает улучшение структуры стали благодаря уменьшению её зернистости. Обычно для поковки отрезают кусок круглого проката диаметром около 50 мм. Длина этой заготовки зависит от будущей длины ствола. Куска длиной 320 мм хватает, чтобы из неё вытянуть ковкой заготовку длиной 750 мм со средним диаметром 30 мм. Конечно, после ковки диаметр заготовки в области патронника заметно больше, чем у дульного среза. Здесь следует отметить, что при обычной ковке около 15% стали уходит в окалину. Кузнецы говорят, что металл «угорает».
Оружейное сверло:
а — режущая пластина,
b и с — направляющие,
d — канал для подвода
охлаждающей жидкости,
е — полость для
удаления стружки
Для снятия внутренних напряжений в откованных заготовках их нагревают до (примерно) 850-860 градусов и выдерживают около получаса. Точные параметры нагрева зависят от марки ствольной стали и толщины заготовки. Задача снятия внутренних напряжений очень важна для всех стадий производства стволов. Особенно важно, чтобы не было напряжений в готовой ствольной трубке, предназначенной для образования ствольных блоков из двух или более стволов. Дело в том, что пайка мягкими и особенно твёрдыми припоями требует значительного и асимметричного нагревания стволов. Неоднородно происходит и охлаждение спаянного блока. Наличие внутренних напряжений приводит к заметной деформации стволов после пайки. Более того, высокий разогрев внутренней поверхности стволов при стрельбе, особенно интенсивной, может вызвать необратимую деформацию ствола, если в нём оставались напряжения. После нормализации проводят закалку. Суть её заключается в получении оптимальных свойств за счёт формирования тонкой структуры металла. Любая сталь является сложной в фазовом отношении системой, содержащей как минимум две кристаллические модификации чистого железа, карбид железа, карбиды металлов-примесей и твёрдые растворы некоторых из этих компонентов друг в друге. Температурная обработка меняет фазовое состояние этой сложной системы и размеры отдельных фаз, что очень существенно влияет на эксплуатационные свойства. Закалка заключается в равномерном разогреве детали до температуры, зависящей от рецептуры стали, из которой она изготовлена. Заготовки из стали Ск 65, которую в Германии часто используют для стволов, нагревают до 840 градусов. После этого её опускают в масло, имеющее комнатную температуру. Затем заготовку «отпускают», для чего её прогревают в муфельной печи около 4 часов при температуре 580-600 градусов. Такой сложной термообработкой можно значительно влиять на твёрдость, вязкость, упругость и предел прочности при растяжении.
Термически обработанную заготовку тщательно рихтуют. Это делают, чтобы при сверлении, которое происходит при вращении заготовки, она не вибрировала. Рихтуют заготовку в горизонтальном положении при вращении, корректируя её форму прижимными роликами. После рихтования заготовку снова подвергают нагреву для снятия внутренних напряжений, затем торцуют с обеих сторон и снимают фаски.
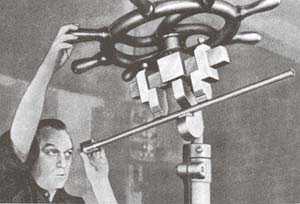
Рихтовка ствола по теневым кольцам
с помощью винтового пресса
После этого приступают к самому тонкому процессу в изготовлении ствола — сверлению. Глубокое сверление, особенно в длинной заготовке с низкой продольной устойчивостью — особая песня. В оружейном деле для этого используют специальные станки, похожие на токарные. В них закреплённая заготовка вращается, а специальное сверло движется поступательно. В этом процессе две главные проблемы: увод сверла от оси заготовки и удаление стружки. Первую проблему можно решить за счёт однородности структуры заготовки и относительно невысокой скорости подачи сверла и скорости резания, чтобы исключить вибрацию заготовки. Разумеется, эти ограничения увеличивают продолжительность сверления. Проблема удаления стружки, которая иногда не только портит поверхность канала, но и заклинивает сверло, решается специальными приёмами. В XIX веке применялись «ружейные свёрла», по конструкции они были близки к развёрткам, то есть в их основе имелась штанга, на всей рабочей длине которой был выбран цилиндрический сектор с углом около 100 градусов. Конструкция сверла достаточно проста и хорошо понятна из чертежа. Через небольшое отверстие в теле сверла в зону резания подаётся охлаждающая эмульсия, которая по желобку, параллельному оси сверла, уносит с собой образующуюся стружку. Такие станки давно стали многошпиндельными и достаточно автоматизированными. Это позволяет одному рабочему контролировать сверление на нескольких станках. Этот процесс всё-таки не гарантировал высокую степень чистоты обработки поверхности канала ствола. Стружка часто была основной причиной этого. Кроме того, производительность сверления была невысокая.
Сверло Байснера —
рабочая и
тыльная части
В 1937 году Бургсмюллер качественно изменил схему сверления. Он предложил вертикальное расположение заготовок и направле¬ние сверления снизу вверх для лучшего удаления стружки. В качестве основы сверла он применил трубу, на рабочей головке которой были прикреплены три направляющие пластины и приварена одна режущая. Процесс резания происходит при охлаждении сжатым воздухом, который подаётся в зазор между поверхностью сверла и стенками образующегося отверстия. Стружка же совсем не контактировала со стенками отверстия и вместе с воздухом уносилась вниз. Значительно больший момент сопротивления скручиванию, которым обладала «труба» по сравнению с профилированной штангой, позволяет, кроме получения хороших поверхностей, использовать при сверлении более высокие скорости резания и подачи.
В 1942 году Байснер усовершенствовал этот метод. Он вернул сверлильному станку горизонтальное положение, предложил использовать масло в качестве охлаждающей жидкости и усовершенствовал сверлильную головку. Масло подавалось под давлением в зазор между сверлом и образующейся цилиндрической поверхностью и выносило стружку через центральный канал в специальный сборник. Поверхность получалась очень гладкой в некоторой мере благодаря полированию направляющими. Тем не менее, после сверления канал ствола обрабатывается развёрткой.
Перед тем как приступить к обработке наружной поверхности ствола его рихтуют: проверяют прямолинейность оси канала и при необходимости выправляют её с помощью винтового пресса. Проверку правильности канала осуществляют по теневым кольцам, что каждый охотник может сделать и сам. А вот процесс правки требует не только хорошего зрения, но и большого чувства металла, приходящего только с опытом. Дело в том, что ствол имеет упругость. Поэтому если под нагрузкой он выпрямился, то после её снятия частично вернётся в исходное состояние. Опытный мастер чувствует, насколько ствол нужно «перегнуть», чтобы после снятия нагрузки он стал безукоризненно правильным.
Проточка шеек для люнетов:
1 — центр, 2 — скользящая муфта,
3 — стойка, 4 — шейка для люнета
После формирования канала ствола встаёт очередная непростая задача: токарно обработать ствол снаружи. При этом главная трудность, чтобы центр наружной поверхности точно совпал с центром канала ствола. Если этого не сделать, то ствольная трубка получится разностенной. Кроме того, из-за большой величины отношения длины ствола к его диаметру при токарной обработке поверхности ствола его необходимо фиксировать двумя люнетами, для каждого из которых нужно предварительно проточить шейки. Для корректного выполнения этой операции на середине длины ствола устанавливают специальную муфту, позволяющую правильно удерживать ствол за его необработанную поверхность при проточке шеек для люнетов. Когда шейки проточены, муфту можно снять и выполнить наружное обтачивание ствола по копиру. Эти токарные обработки могут привести к некоторой деформации ствола. Поэтому ствол в очередной раз контролируют по теневым кольцам и при необходимости рихтуют. Чистовое обтачивание и шлифование производится после того, как отдельно прошлифовываются шейки для люнетов. Заключительная стадия изготовления ствольных трубок — тонкое шлифование, называемое в оружейном деле хонингованием.
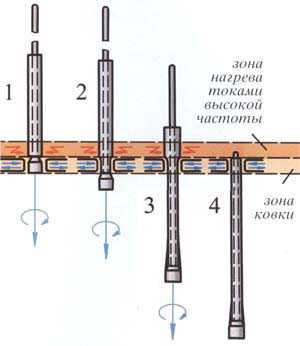
Схема ротационной ковки:
1 — разогрев токами высокой частоты,
2 — начало ковки, 3 — процесс ковки,
4 — окончание ковки
Существенным прогрессом в изготовлении ружейных стволов является их ковка на оправке. Конечно, оборудование для этого процесса стоит недёшево. Поэтому формование стволов ковкой рентабельно только при больших объёмах производства. Однако экономия средств и времени получается тоже значительная. При изготовлении стволов методом ротационной горячей ковки используют заготовки длиной 260-280 мм и диаметром около 35 мм. В ней сверлом Байснера делают сквозное отверстие диаметром 20,5 мм. Заготовку закрепляют на закалённой, тщательно отполированной оправке, имеющей форму внутренней поверхности готового ствола. После электроиндукционного прогрева заготовки до необходимой температуры её подают в зону ковки, где она, вращаясь вдоль своей оси, проходит под ударами крестообразно расположенных молотов. За полторы минуты заготовка принимает внешнюю и внутреннюю форму ствола с патронником. Закалка после такой проковки не проводится. Внешнюю форму ствола доводят токарным обтачиванием и шлифованием. Канал ствола начерно проходится развёрткой. Окончательную обработку канала ствола, включая патронник и дульное сужение, проводят после сборки ствольного блока.
Ещё более прогрессивным методом изготовления стволов является холодная ковка на оправке. Одно из её преимуществ в том, что она экономит около 15% дорогой ствольной стали, уходящей в окалину при горячей ковке. Кроме того, внутренняя поверхность ствола получается точной копией оправки, так что можно получать полностью готовые стволы (с патронником, дульным сужением и нарезами). Поверхность канала ствола требует только полировки. К тому же структура холоднокованого ствола обеспечивает ему высокие механические свойства. Правда, холодная ковка требует более мощных молотов и большей продолжительности. Она длится чуть более трёх минут. Внешнюю форму доводят обтачиванием и полированием. Проверку правильности оси канала проводят и после этой технологии и, если есть необходимость, рихтуют. Завершающей стадией изготовления отдельных ствольных заготовок является отстрел и клеймение.
Владимир Тихомиров
Мастер ружье 10-2004
weaponland.ru
ПРИМЕНЕНИЕ СТАНКОВ С ЧПУ ПРИ ПРОИЗВОДСТВЕ СТРЕЛКОВОГО ОРУЖИЯ
В современном мире каждое государство вынуждено заботиться об обороне своих границ и территорий. Для этого нужна сильная, мощная армия, укомплектованная хорошо обученными солдатами. А каждому солдату нужно оружие. Ежегодно в мире производится несколько сотен тысяч единиц стрелкового оружия. Такие объёмы производства реальны, благодаря современным мощностям производств, значимое место в котором занимают станки с числовым программным управлением. Их использование в массовом производстве оружия позволило значительно повысить производительность изготовления многих сложных и дорогостоящих элементов стрелкового оружия, сократить время изготовления отдельных деталей.
В недалеком прошлом, всё оружие в мире производилось на огромных фабриках, занимавших значительные территории и требующих большой парк специализированного оборудования, а также соответствующий штат высококвалифицированных рабочих[2]. Основными операциями при изготовлении деталей оружия были штамповка и обработка на токарных станках. Такой процесс производства имеет целый ряд недостатков:
1.Большое количество операций и переходов для изготовления одной детали.
2.Значительные временные затраты на изготовление и доводку сложных деталей, типа: ствол, затворно-спусковой механизм.
3.Количество бракованных деталей при массовом производстве штамповкой достигала 25 % от общего плана изготовления отдельной номенклатуры.
4.Количество брака связанного с человеческим фактором.
5.Трудозатраты на исправление дефектов и доводку деталей не соответствующих требованиям контроля качества.
6.Большие затраты на высококвалифицированный персонал.
7.Затраты на новое уникальное оборудование при выпуске нового элемента оружейной оснастки или новейшего типа оружия.
Влияние всех этих факторов сказывалось и на качестве самого производимого оружия. Во многом производимые образцы крупносерийного производства не обладали требуемой точностью и надёжностью. Ручная токарная обработка стволов и нарезание резьб позволяли достичь определённого среднего значения выпуска годной продукции для партии изделий, но для конкретных экземпляров штурмового оружия она оказывалась недостаточной (за исключение высокоточного снайперского вооружения)[1]. Проблемы, связанные с большими допусками на изготовление важнейших элементов стрелкового оружия, влияющие на появления в ряде случаев больших зазоров, проводили к полной поломке оружия или ухудшению качества стрельбы.
С внедрением в производство станков с ЧПУ был решён целый ряд проблем:
1.С внедрением станков с ЧПУ в производство стрелкового оружия были достигнуты заметные улучшения при изготовлении оружейных стволов.
2.Многочисленные методы производства стволов на различных станках позволяют производить наиболее подходящий тип нарезки ствола при минимальном браке.
3.Высокоточные системы станков с ЧПУ так же позволяют избежать многочисленных ошибок, связанных с человеческим фактором.
Повсеместное применение станков с ЧПУ позволило значительно повысить производственные мощности, точность изготовления, качество, уменьшить количество брака, снизить штучное время изготовления отдельных деталей.
В настоящее время в сфере изготовления оружия появился новый сегмент. Это мелкосерийное производство нестандартных деталей или так называемого оружейного кастома (от англ. custom). Наиболее развито это направление в США, где оружие легализовано в большинстве штатов. Небольшие компании занимаются изготовлением особых деталей для профессиональных спортсменов, снайперов и любителей охоты. В своем мелкосерийном производстве они активно используют станки с ЧПУ, на которые загружены, разработанные инженерами этих компаний программы обработки этих самых деталей. Наибольший интерес вызывают их работы по изготовлению облегчённых, эргономичных деталей, таких как пистолетные рукоятки, цевья, приклады различных модификаций. Так же многие из таких компаний занимаются производством целых комплектов деталей для улучшения различных характеристик оружия: усиленных высокоточных бойков, магазиноприёмников, спусковых скоб и затворных групп.
В станках с ЧПУ сочетается точность и производительность станков-автоматов и гибкость универсального оборудования. Применение станков с ЧПУ позволит сократить цикл проектирования и запуска опытных изделий, а также уменьшить цикл подготовки производства серийных изделий за счет централизованной подготовки производства в процессе проектирования и опытного производства с последующей их передачей в серийное производство. В связи с широким спектром требований к конструкции деталей, обрабатываемых на станках с ЧПУ, разумно пользоваться алгоритмом отработки деталей на технологичность, как на качественную методику оценки.
В качестве примеров рассмотрим основные операции, которые применяются для изготовления оружейных стволов стрелкового оружия[3,4]. Определяющим параметром для каждого ствола является кучность попадания пуль. И чтобы достичь оптимального для каждого ствола значения, необходимо использовать технологию, которая исключила бы все негативные факторы и погрешности.
Заготовительная. Абсолютно все производители сходятся в том, что материал для оружейного ствола должен удовлетворять высоким требованиям по качеству.
Рисунок 1. Заготовки для оружейных стволов
Глубокое сверление. При глубоком сверлении заготовки, получаемые отверстия должны быть концентричны наружной поверхности по всей длине.
Рисунок 2. Сверление отверстий
Развёртывание. На данной операции удаляют грубые места в отверстии после сверления, формируются окончательные размеры канала ствола.
Рисунок 3. Развёртывание отверстий
Токарная операция. На токарном станке можно выполнять различные операции точения, нарезания резьбы, вытачивание канавок, фасок.
Рисунок 4. Нарезание резьбы на стволе с применением станка с ЧПУ
Метод ковки. При данном методе полированная стальная труба на специальной оправке на ковочной машине обрабатывается снаружи бойками, движущимися в радиальном направлении и с большими усилиями обжимающими заготовку.
Рисунок 5. Холодная ковка в ковочной машине
Термическая обработка. Применяется для устранения внутренних напряжений, которые возникают по всей длине ствола в основном при ковочных операциях.
Рисунок 6. Нагрев стволов в печи для снятия напряжений
Целесообразность применения станков с ЧПУ в единичном и мелкосерийном производстве оружейных деталей[5]. Для того, чтобы оценить эффективность использования станков с ЧПУ при изготовлении оружейных деталей, необходимо обратиться к их геометрии и конструктивным особенностям, т.е. индивидуально подойти к каждой детали. Единичные или мелкосерийные детали обычно имеют конические поверхности, рёбра жёсткости, канавки, различного типа отверстия, также могут иметь сложную форму со ступенчатыми поверхностями. Некоторые детали должны отвечать требованиям анатомической эргономичности, что требует от станка возможность обработки сложных пространственных поверхностей. В пользу станков с ЧПУ выступают современные CAD/CAM-технологии, т.к. с их помощью можно создать 3D-модель готовой детали, разработать стратегии обработки, используя постпроцессор под конкретный станок написать управляющую программу на конкретную деталь. Так как заказчики предъявляют высокие требования к деталям, и они имеют сложную форму, их целесообразно изготавливать на станках с ЧПУ, более простые можно изготавливать на универсальных станках.
Список литературы
- Арефьев М. Г. и Карпов Л. И. Производство стволов стрелкового оружия. Москва, 1945.-256 с
- Болотин Д. Н. История советского стрелкового оружия и патронов. Санкт-Петербург: Полигон, 1995.-302 с.
- Заводское изготовление оружейного ствола стрелкового оружия //Стрелковый портал Украины. URL: http://www.shooting-ua.com/arm-books/arm_book_248.htm (дата обращение: 12.04.17)
- Как делают оружие для снайперов //Военное обозрение. URL: https://topwar.ru/30854-kak-delayut-oruzhie-dlya-snayperov.html (дата обращение: 11.04.17)
- Шеховцева Т. В. Целесообразность применения станков с ЧПУ в единичном и мелкосерийном производстве на основе показателей технологичности деталей ГТД. Вестник Мурманского государственного технического университета. 2011.Т.14№4.С.690-700.
sibac.info
Производство стволов стрелкового оружия — Литература (Книги)
Название: Производство стволов стрелкового оружия
Автор: Арефьев М.Г., Карпов Л.И.
Издательство: Оборонгиз
Год: 1945
Страниц: 233
В книге описаны все процессы изготовления стволов стрелкового оружия, начиная с выплавки металла и кончая механической обработкой стволов. Металлургические процессы описаны в общих чертах, а механическая обработка детально; в книге рассмотрены принципы построения технологического процесса обработки стволов. Подробно изложены также вопросы приемки ствольной стали и стволов.
Книга должна служить учебным пособием для слушателей Артиллерийской ордена Ленина Академии Красной Армии, а также может явиться пособием для инженерно-технических работников, занимающихся изготовлением стрелкового оружия.
Предисловие
Введение
ЧАСТЬ I. ПРОИЗВОДСТВО СТВОЛЬНОЙ СТАЛИ И ПОЛУЧЕНИЕ СТВОЛЬНЫХ ЗАГОТОВОК
Глава I. Устройство стволов стрелкового оружия
§ 1. Классификация стволов по технологическому признаку
§ 2. Устройство каналов стволов
§ 3. Элементы наружной поверхности стволов
§ 4. Простановка размеров наружных элементов ствола в рабочем чертеже
Глава II. Стали, применяемые для изготовления стволов стрелкового оружия
§ 5. Основные требования, предъявляемые к материалу стволов стрелкового оружия
§ 6. Сорта сталей
Глава III. Производство ствольной стали
§ 7. Выплавка ствольной стали
§ 8. Контрольные испытания слитков
§ 9. Контроль химического состава
§ 10. Механические испытания
§ 11. Проверка условий выплавки и разливки стали
§ 12. Контроль слитков и блюмсов по скорости охлаждения
§ 13. Исследование макроструктуры (СТНВ-75)
§ 14. Контроль по отпечаткам Баумана
§ 15. Контроль по излому шайб
§ 16. Продольное макротравление
§ 17. Контроль неметаллических включений
§ 18. Контроль по величине зерна
§ 19. Проверка закаливаемости
Глава IV. Производство ствольных заготовок
§ 20. Обжим и прокатка слитков
§ 21. Ковка ствольных заготовок
§ 22. Термообработка ствольных заготовок
§ 23. Контрольные испытания отожженных стволов
ЧАСТЬ II. МЕХАНИЧЕСКАЯ ОБРАБОТКА СТВОЛОВ СТРЕЛКОВОГО ОРУЖИЯ
§ 24. Общие сведения о механической обработке стволов
Глава V. Глубокое сверление стволов стрелкового оружия
§ 25. Подготовительные операции, предшествующие глубокому сверлению
§ 26. Основные положения глубокого сверления
§ 27. Инструмент для глубокого сверления
§ 28. Станки для глубокого сверления
§ 29. Смазывающе-охлаждающие жидкости для глубокого сверления
§ 30. Режимы резания при глубоком сверлении стволов стрелкового оружия
§ 31. Анализ основных факторов, влияющих на увод сверла
Глава VI. Развертывание каналов стволов стрелкового оружия
§ 32. Общая характеристика операций по развертыванию каналов стволов
§ 33. Конструкции разверток, применяемых для развертывания каналов стволов
§ 34. Изготовление разверток
§ 35. Способы развертывания каналов стволов
§ 36. Станки для глубокого развертывания
§ 37. Смазывающе-охлаждающие жидкости при развертывании
§ 38. Режимы работы при развертывании
§ 39. Применение броши для протягивания каналов стволов
Глава VII. Образование нарезов в канале ствола
§ 40. Способы образования нарезов в канале ствола
§ 41. Строгание нарезов
§ 42. Стволо-нарезные станки, применяемые для строгания нарезов шпаллером
§ 43. Режимы резания и смазывающие жидкости
§ 44. Основные дефекты при строгании нарезов шпаллером
§ 45. Образование нарезов протягиванием броши
§ 46 Образование нарезов в канале ствола путем выдавливания (дорнование)
§ 47. Исходные факторы для правильной постановки операции дорнования
§ 48. Конструкция пуансона
§ 49. Влияние твердости ствола на величину его деформации и тяговое усилие при дорновании
§ 50. Влияние изменения наружного и внутреннего диаметров ствола на тяговое усилие
§ 51. Влияние смазки на изменение тягового усилия при дорновании
§ 52. Стволопротяжные станки для дорнования
§ 53 Контроль нарезной части ствола
§ 54. Чистовая обработка поверхности канала ствола
Глава VIII. Обработка патронников в стволах стрелкового оружия
§ 55. Характеристика операций обработки патронников
§ 56. Режущий, инструмент, применяемый для обработки патронником
§ 57. Станки для предварительного и чистового развертывания патронников
§ 58. Смазывающе-охлаждающие жидкости
§ 59. Контроль правильности изготовления патронников
Глава IX. Правка стволов стрелкового оружия
§ 60. Назначение правки стволов
§ 61. Теневой метод контроля прямолинейности канала ствола
§ 62. Определение изгиба ствола при помощи прибора „Точка»
Глава X. Наружная обработка стволов
§ 63. Наружное обтачивание стволов стрелкового оружия
§ 64. Особенности нарезания резьб на стволах
§ 65. Подрезание торца пенька ствола и обработка его элементов
§ 66. Обработка дульного среза
Глава XI. Термообработка, хромирование и оксидирование стволов стрелкового оружия
§ 67. Термообработка стволов стрелкового оружия
§ 68. Термообработка пенька ствола ДП и ШВАК
§ 69. Хромирование поверхности каналов стволов стрелкового оружия
§ 70. Подготовка стволов к хромированию
§ 71. Электролитическое хромирование стволов
§ 72. Основные дефекты каналов стволов после хромирования
§ 73. Изоляция патронника при хромировании
§ 74. Химическая окраска наружной поверхности стволов
§ 75. Контроль оксидных покрытий
предназначены исключительно для формирования представления о их сути.
На портале ЛитРес можно получить подробную информацию
о различной литературе, читать и слушать онлайн,
а также приобрести и скачать ее.
weaponland.ru
Ружейные стволы. Технология изготовления — Энциклопедия стрелкового оружия
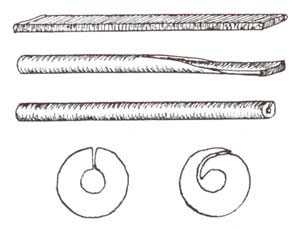
Стадии сворачивания трубки простого ствола.
Вверху — пластина-заготовка для ствола
Вероятно, многие согласятся со мной, что главная часть ружья — стволы. Ведь стреляют именно они. Эффективность пушечных выстрелов вызвала у человека желание сделать маленькую «ручную» пушку. Такую пушку в середине позапрошлого века нашли в замке Таннеберг в Хессене (Германия). Она была отлита в конце XIV века. Стрелять из неё с рук было, конечно, тяжело и неудобно и вскоре к ней приспособили арбалетную ложу. Оказалось, что по точности стрельбы и кучности новое оружие серьёзно уступает хорошему луку, хотя по энергии, а значит и пробивной силе, значительно его превосходит. Довольно быстро выяснилось, что с увеличением длины ствола, выстрелы становятся более точными. С этого момента и начинается история огнестрельного оружия.
Сегодня у нашего «переломного» охотничьего ружья есть три главные части: ствол (или стволы, образующие ствольный блок), колодка, ложа.
Ствол придаёт направление полёту дроби или пули. Чем правильнее и тщательнее он изготовлен, тем лучше дробовая осыпь и выше точность.
Колодка запирает казённый срез стволов, служит связующим элементом между стволами и ложей и является в оружии главным инерционным элементом, поглощающим силу отдачи. В колодке монтируются запирающие, ударно-спусковые и предохранительные механизмы.
Схема получения скрученных ствольных трубок
Ложа обеспечивает удобство наведения оружия на цель, естественность прицеливания и смягчает действие силы отдачи за счёт её частичного превращения во вращательный момент.
Прежде чем рассказать о сегодняшней технологии изготовления оружейных стволов, хочется познакомить читателей с частью оружейной истории, касающейся совершенствования изготовления этой важнейшей части оружия. Ведь изготовить хороший ствол — задача довольно трудная даже при сегодняшнем уровне развития машиностроения. Однако настойчивость, усердие и изобретательность наших далёких предков находила различные варианты решения этой задачи. Причём уровень качества лучших изделий XVIII века сегодняшним специалистам представляется почти загадочным. Нам хочется рассказать, каким путём мастера прошлого создавали замечательное оружие, показать некоторые его образцы и вместе подумать о величии их духа с надеждой, что это укрепит и наш собственный.
В 1811 году Генрих Аншютц (из хорошо известной оружейной династии) издал книгу об оружейной фабрике в г. Зуль. Он пишет о четырёх типах технологий получения ствольных трубок: обычной, скрученной, навитой и стволах из «Дамаска».
Принцип получения навитых стволов
Обычный (простой) ствол получали из полосовой заготовки длиной 32 дюйма (812,8 мм), шириной 4 дюйма (101,6 мм), толщиной 3/8 дюйма (9,525 мм). После разогрева эту полосу кузнечным способом загибали на оправке таким образом, что её продольные кромки прилегали друг к другу встык, параллельно оси канала ствола. Этот стык сваривался кузнечным методом и тщательно проковывался. Есть несомненные указания, что обе длинные стороны прямоугольной заготовки иногда сгонялись «на ус» и сваривались не встык, а внахлёст. После сварки и охлаждения стволы проходили четырёхгранной развёрткой, обтачивали на токарном станке внешнюю поверхность, которую потом шлифовали вручную на большом круге из мягкого песчаника диаметром 1,75 м. С казённой стороны в ствол вкручивалась винтовая заглушка, которая иногда тоже проваривалась. Конечно, «заглушались» стволы всех дульнозарядных ружей, независимо от технологии их получения.
Скрученный ствол. Сварной шов в обычном стволе, располагавшийся параллельно оси ствола, часто был местом разрушения при стрельбе. Чтобы избежать этого, простой сваренный ствол начинали повторно нагревать в центральной части и скручивали вдоль оси по всей длине так, чтобы сварной шов имел форму винтовой линии. Этот приём делал шов значительно менее нагруженным при выстреле.
Навитой ствол получали путём постепенного навивания стальной полосы на оправку в виде стержня или трубы. Винтообразный сварной шов последовательно проковывали кузнечным молотом.
Схема получения полосы дамасской стали
Дамасские стволы. Ещё в средние века в Дамаске (сегодня это Сирия) изготовляли мечи, обладающие исключительно высоким качеством. Как только технология их получения стала понятна европейцам, её попытались применить и для изготовления стволов. Основа секрета состояла в том, что заготовки для клинкового оружия получали кузнечной сваркой полос из тонких элементов, состоящих из сталей различавшихся содержанием углерода. Первоначально сваренную и прокованную полосу многократно складывали и проковывали. По сравнению с обычной однородной заготовкой дамасская обладала тремя принципиальными преимуществами. По сути, она представляла конструкцию, объединяющую свойства отдельных материалов. Кроме того, композиция не только исключала внутренние дефекты, которые бывают в однородной заготовке, но и создавала оптимальную структурную ориентацию. Принципиально дамасские стволы получали методом навивки. Однако для получения исходной полосы приходилось проделать просто титаническую работу. Сначала сваривали брусок из ста прутков сталей разного состава квадратного сечения со стороной 0,7 мм, уложенных в определённом порядке. Брусок получался сечением около 7 мм х 7 мм. Эта процедура требовала невероятно тонкого кузнечного чутья, поскольку пережечь тонкие проволочки было проще простого. Сваренный брусок снова разогревали и скручивали вдоль. Затем брали несколько таких скрученных брусков (чаще три или шесть) сваривали их между собой и расковывали в полосу. В некоторых случаях из этих скруток плели что-то вроде косичек, которые могли состоять из разного числа прядей и иметь разную схему плетения. Косички сваривали и проковывали в полосу. Эту полосу и навивали на оправку. Затем заготовку торцевали, канал проходили развёрткой, наружную поверхность сначала обтачивали на токарном станке, потом шлифовали. Процесс воронения в те времена состоял в обработке довольно сильными кислотами. В результате, малоуглеродистые прутики протравливались значительно сильнее по сравнению с высокоуглеродистыми, и на поверхности ствола появлялся оригинальный мелкий рисунок, отражавший всю предшествующую схему получения полос. Обычно на дамасских стволах ширина полосы видна невооружённым глазом.
Стремительное развитие металлургии в конце XIX века привело к появлению углеродистых сталей с высокими механическими свойствами. Перспективность их использования для изготовления стволов казалась очевидной. Однако ещё в первой четверти XX века многие оружейники Европы продолжали делать стволы по «дамасским технологиям». Сегодня необходимо понимать, что такие стволы, хотя и являются памятниками фантастическому усердию оружейников предыдущих поколений, но всё же уступают по всем важнейшим показателям современным легированным ствольным сталям. Напомним нашим соотечественникам, что сталь 50А и даже 50РА, из которой и в Туле, и в Ижевске делают сегодня стволы, к легированным ствольным сталям не относятся. И ещё о дамасских стволах. Спустя сто и более лет после изготовления весьма вероятно, что кузнечная сварка элементов может значительно разрушиться и прочность стволов может оказаться недостаточной для обеспечения безопасности стрельбы. Будьте очень осторожны при желании пострелять из старого ружья с дамасскими стволами.
Введение в состав углеродистой стали хрома, ванадия, никеля, кремния, марганца и других элементов привело к значительному повышению важнейших свойств ствольных сталей — упругости, прочности при растяжении, поверхностной твердости, коррозионной стойкости. Более того, эти технологии позволяют получать стали с заранее заданными свойствами. Всё это позволило перейти к изготовлению однородных заготовок для ружейных стволов. Этот процесс начался ещё в последней трети XIX века и около полувека сосуществовал с «дамасской» технологией.
Развитие технологии изготовления ружейных стволов.
Рихтовка ствольной заготовки
Новый этап начинается с отказа от стволов, получаемых из полос, и перехода к стволам, канал которых образовывался глубоким сверлением. Эта технология несравненно более производительная, но для её реализации потребовалось решить ряд серьёзных проблем, рассказать о которых нам хочется, чтобы современные читатели могли представить, какой ценой получались ружья, обладающие замечательным боем. Новая технология изготовления ствольных заготовок начинается с ковки, которая не только придаёт заготовке ствола внешнюю форму, приближающуюся к готовому стволу, но и обеспечивает улучшение структуры стали благодаря уменьшению её зернистости. Обычно для поковки отрезают кусок круглого проката диаметром около 50 мм. Длина этой заготовки зависит от будущей длины ствола. Куска длиной 320 мм хватает, чтобы из неё вытянуть ковкой заготовку длиной 750 мм со средним диаметром 30 мм. Конечно, после ковки диаметр заготовки в области патронника заметно больше, чем у дульного среза. Здесь следует отметить, что при обычной ковке около 15% стали уходит в окалину. Кузнецы говорят, что металл «угорает».
Оружейное сверло:
а — режущая пластина,
b и с — направляющие,
d — канал для подвода
охлаждающей жидкости,
е — полость для
удаления стружки
Для снятия внутренних напряжений в откованных заготовках их нагревают до (примерно) 850-860 градусов и выдерживают около получаса. Точные параметры нагрева зависят от марки ствольной стали и толщины заготовки. Задача снятия внутренних напряжений очень важна для всех стадий производства стволов. Особенно важно, чтобы не было напряжений в готовой ствольной трубке, предназначенной для образования ствольных блоков из двух или более стволов. Дело в том, что пайка мягкими и особенно твёрдыми припоями требует значительного и асимметричного нагревания стволов. Неоднородно происходит и охлаждение спаянного блока. Наличие внутренних напряжений приводит к заметной деформации стволов после пайки. Более того, высокий разогрев внутренней поверхности стволов при стрельбе, особенно интенсивной, может вызвать необратимую деформацию ствола, если в нём оставались напряжения. После нормализации проводят закалку. Суть её заключается в получении оптимальных свойств за счёт формирования тонкой структуры металла. Любая сталь является сложной в фазовом отношении системой, содержащей как минимум две кристаллические модификации чистого железа, карбид железа, карбиды металлов-примесей и твёрдые растворы некоторых из этих компонентов друг в друге. Температурная обработка меняет фазовое состояние этой сложной системы и размеры отдельных фаз, что очень существенно влияет на эксплуатационные свойства. Закалка заключается в равномерном разогреве детали до температуры, зависящей от рецептуры стали, из которой она изготовлена. Заготовки из стали Ск 65, которую в Германии часто используют для стволов, нагревают до 840 градусов. После этого её опускают в масло, имеющее комнатную температуру. Затем заготовку «отпускают», для чего её прогревают в муфельной печи около 4 часов при температуре 580-600 градусов. Такой сложной термообработкой можно значительно влиять на твёрдость, вязкость, упругость и предел прочности при растяжении.
Термически обработанную заготовку тщательно рихтуют. Это делают, чтобы при сверлении, которое происходит при вращении заготовки, она не вибрировала. Рихтуют заготовку в горизонтальном положении при вращении, корректируя её форму прижимными роликами. После рихтования заготовку снова подвергают нагреву для снятия внутренних напряжений, затем торцуют с обеих сторон и снимают фаски.
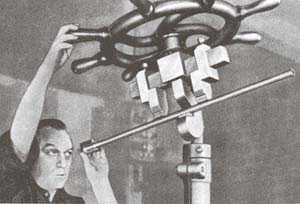
Рихтовка ствола по теневым кольцам
с помощью винтового пресса
После этого приступают к самому тонкому процессу в изготовлении ствола — сверлению. Глубокое сверление, особенно в длинной заготовке с низкой продольной устойчивостью — особая песня. В оружейном деле для этого используют специальные станки, похожие на токарные. В них закреплённая заготовка вращается, а специальное сверло движется поступательно. В этом процессе две главные проблемы: увод сверла от оси заготовки и удаление стружки. Первую проблему можно решить за счёт однородности структуры заготовки и относительно невысокой скорости подачи сверла и скорости резания, чтобы исключить вибрацию заготовки. Разумеется, эти ограничения увеличивают продолжительность сверления. Проблема удаления стружки, которая иногда не только портит поверхность канала, но и заклинивает сверло, решается специальными приёмами. В XIX веке применялись «ружейные свёрла», по конструкции они были близки к развёрткам, то есть в их основе имелась штанга, на всей рабочей длине которой был выбран цилиндрический сектор с углом около 100 градусов. Конструкция сверла достаточно проста и хорошо понятна из чертежа. Через небольшое отверстие в теле сверла в зону резания подаётся охлаждающая эмульсия, которая по желобку, параллельному оси сверла, уносит с собой образующуюся стружку. Такие станки давно стали многошпиндельными и достаточно автоматизированными. Это позволяет одному рабочему контролировать сверление на нескольких станках. Этот процесс всё-таки не гарантировал высокую степень чистоты обработки поверхности канала ствола. Стружка часто была основной причиной этого. Кроме того, производительность сверления была невысокая.
Сверло Байснера —
рабочая и
тыльная части
В 1937 году Бургсмюллер качественно изменил схему сверления. Он предложил вертикальное расположение заготовок и направле¬ние сверления снизу вверх для лучшего удаления стружки. В качестве основы сверла он применил трубу, на рабочей головке которой были прикреплены три направляющие пластины и приварена одна режущая. Процесс резания происходит при охлаждении сжатым воздухом, который подаётся в зазор между поверхностью сверла и стенками образующегося отверстия. Стружка же совсем не контактировала со стенками отверстия и вместе с воздухом уносилась вниз. Значительно больший момент сопротивления скручиванию, которым обладала «труба» по сравнению с профилированной штангой, позволяет, кроме получения хороших поверхностей, использовать при сверлении более высокие скорости резания и подачи.
В 1942 году Байснер усовершенствовал этот метод. Он вернул сверлильному станку горизонтальное положение, предложил использовать масло в качестве охлаждающей жидкости и усовершенствовал сверлильную головку. Масло подавалось под давлением в зазор между сверлом и образующейся цилиндрической поверхностью и выносило стружку через центральный канал в специальный сборник. Поверхность получалась очень гладкой в некоторой мере благодаря полированию направляющими. Тем не менее, после сверления канал ствола обрабатывается развёрткой.
Перед тем как приступить к обработке наружной поверхности ствола его рихтуют: проверяют прямолинейность оси канала и при необходимости выправляют её с помощью винтового пресса. Проверку правильности канала осуществляют по теневым кольцам, что каждый охотник может сделать и сам. А вот процесс правки требует не только хорошего зрения, но и большого чувства металла, приходящего только с опытом. Дело в том, что ствол имеет упругость. Поэтому если под нагрузкой он выпрямился, то после её снятия частично вернётся в исходное состояние. Опытный мастер чувствует, насколько ствол нужно «перегнуть», чтобы после снятия нагрузки он стал безукоризненно правильным.
Проточка шеек для люнетов:
1 — центр, 2 — скользящая муфта,
3 — стойка, 4 — шейка для люнета
После формирования канала ствола встаёт очередная непростая задача: токарно обработать ствол снаружи. При этом главная трудность, чтобы центр наружной поверхности точно совпал с центром канала ствола. Если этого не сделать, то ствольная трубка получится разностенной. Кроме того, из-за большой величины отношения длины ствола к его диаметру при токарной обработке поверхности ствола его необходимо фиксировать двумя люнетами, для каждого из которых нужно предварительно проточить шейки. Для корректного выполнения этой операции на середине длины ствола устанавливают специальную муфту, позволяющую правильно удерживать ствол за его необработанную поверхность при проточке шеек для люнетов. Когда шейки проточены, муфту можно снять и выполнить наружное обтачивание ствола по копиру. Эти токарные обработки могут привести к некоторой деформации ствола. Поэтому ствол в очередной раз контролируют по теневым кольцам и при необходимости рихтуют. Чистовое обтачивание и шлифование производится после того, как отдельно прошлифовываются шейки для люнетов. Заключительная стадия изготовления ствольных трубок — тонкое шлифование, называемое в оружейном деле хонингованием.
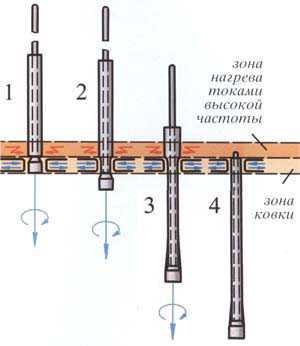
Схема ротационной ковки:
1 — разогрев токами высокой частоты,
2 — начало ковки, 3 — процесс ковки,
4 — окончание ковки
Существенным прогрессом в изготовлении ружейных стволов является их ковка на оправке. Конечно, оборудование для этого процесса стоит недёшево. Поэтому формование стволов ковкой рентабельно только при больших объёмах производства. Однако экономия средств и времени получается тоже значительная. При изготовлении стволов методом ротационной горячей ковки используют заготовки длиной 260-280 мм и диаметром около 35 мм. В ней сверлом Байснера делают сквозное отверстие диаметром 20,5 мм. Заготовку закрепляют на закалённой, тщательно отполированной оправке, имеющей форму внутренней поверхности готового ствола. После электроиндукционного прогрева заготовки до необходимой температуры её подают в зону ковки, где она, вращаясь вдоль своей оси, проходит под ударами крестообразно расположенных молотов. За полторы минуты заготовка принимает внешнюю и внутреннюю форму ствола с патронником. Закалка после такой проковки не проводится. Внешнюю форму ствола доводят токарным обтачиванием и шлифованием. Канал ствола начерно проходится развёрткой. Окончательную обработку канала ствола, включая патронник и дульное сужение, проводят после сборки ствольного блока.
Ещё более прогрессивным методом изготовления стволов является холодная ковка на оправке. Одно из её преимуществ в том, что она экономит около 15% дорогой ствольной стали, уходящей в окалину при горячей ковке. Кроме того, внутренняя поверхность ствола получается точной копией оправки, так что можно получать полностью готовые стволы (с патронником, дульным сужением и нарезами). Поверхность канала ствола требует только полировки. К тому же структура холоднокованого ствола обеспечивает ему высокие механические свойства. Правда, холодная ковка требует более мощных молотов и большей продолжительности. Она длится чуть более трёх минут. Внешнюю форму доводят обтачиванием и полированием. Проверку правильности оси канала проводят и после этой технологии и, если есть необходимость, рихтуют. Завершающей стадией изготовления отдельных ствольных заготовок является отстрел и клеймение.
Владимир Тихомиров
Мастер ружье 10-2004
shooting-iron.ru
Способ изготовления ствола автоматического стрелкового оружия
Изобретение относится к области машиностроения и может быть использовано для изготовления стволов пулеметов калибра 7,62 мм, 12,7 мм, 14,5 мм и т.д с хромированным каналом, толщиной хромового покрытия до 0,3 мм. Для повышения ресурса стволов, живучести в два и более раз заготовки ствола получают из легированной стали, в составе которой легирующие элементы в совокупности обеспечивают высокое положение критической точки AC1, верхний предел содержания углерода в которой ограничивают 0,3%, затем проводят закалку с высокой скоростью охлаждения в перлитном интервале температур и с подавлением процесса выделения карбидов по границам зерен аустенита. Производят механическую обработку наружной и внутренней поверхностей ствольной заготовки. Формируют нарезную часть канала ствола, изготовляют патронник. Осаждают на поверхности канала ствола гальванический хром с последующим прогревом с использованием источника постоянного тока с пульсациями силы тока и напряжения не более 1% от номинала, а затем производят прогрев ствола с хромовым покрытием. 2 пр.
Изобретение относится к области машиностроения и может быть использовано для изготовления стволов пулеметов калибра 7,62 мм, 12,7 мм, 14,5 мм и т.д с хромированным каналом, толщиной хромового покрытия до 0,3 мм.
Известен способ изготовления ствола стрелкового оружия, принятый за прототип (см. М.Г.Арефьев, Л.И.Карпов. «Производство стволов стрелкового оружия» под ред. А.А.Благонравова, НКАП ОборонГИЗ, Главная редакция вооружения и боеприпасов, Москва, 1945, стр.14-15, 210-211, фиг.37). Способ заключается в следующем: ствольную заготовку, например, из стали 30ХН2МФА, подвергают термической обработке для обеспечения требуемого комплекса механических свойств, производят механическую обработку наружной и внутренней поверхности, формируют нарезную часть канала ствола, изготовляют патронник, осаждают на поверхности канала ствола гальванический хром толщиной до 0,3 мм с последующим прогревом для повышения живучести, в том числе для повышения износоустойчивости против механического истирания поверхности канала ствола оболочкой пули, антикоррозионной и эрозионной стойкости.
Недостатками известного способа, выявленными в процессе исследований стволов из стали 30ХН2МФА калибра 7,62 мм, 12,7 мм, 14,5 мм, прошедших испытания на ресурс, являются:
— слой стали казенной части канала ствола калибра 7,62 мм глубиной в несколько десятков микрометров, примыкающий к хрому, претерпевает при стрельбе структурно-фазовые превращения, за которыми при окончании непрерывной очереди в 250 выстрелов следует закалка с образованием участков мартенсита за счет резкого охлаждения на массу, при этом микротвердость образовавшегося мартенсита выше микротвердости мартенсита, полученного обычной закалкой;
— при испытании пулемета калибра 7,62 мм на полный ресурс непрерывных очередей в 250 выстрелов не менее 30. Это означает, что такое количество раз слой стали казенной части канала ствола испытывает мартенситное превращение;
— гальванический хром удерживается в казенной части канала ствола при испытании на ресурс пулемета калибра 7,62 мм при производстве не более 10-11 тыс. выстрелов, затем следует катастрофический износ стали и, как следствие, прорыв пороховых газов, потеря начальной скорости пули и кучности боя, появление в мишени овальных пробоин;
— многократные, быстропротекающие α-γ-α превращения, происходящие в тонком слое стали, граничащем с хромом, растворение карбидных фаз, ранее имеющих атомные связи с покрытием, различие в коэффициентах линейного расширения сменяющих друг друга фаз в процессе превращений по отношению к покрытию с учетом циклических, динамических и ударных нагрузок на канал ствола от действия пороховых газов и механического закручивания пули — причины, приводящие к преждевременной осыпаемости хрома в казенной части канала ствола;
— ударные нагрузки на ствол от действия пороховых газов вызывают образование трещин в закаленном неотпущенном мартенсите, поэтому сколы хрома происходят не только по границе сталь-хром, но и по трещинам в стали;
— α-γ-α превращения, один раз возникнув, в дальнейшем преимущественно протекают в одних и тех же участках слоя стали, примыкающего к хрому, причем при более низкой температуре по причине растворения карбидных фаз в этих зонах — применительно к стволу калибра 7,62 мм;
— стволы оружия калибра 12,7 мм, 14,5 мм имеют те же недостатки, что и стволы калибра 7,62 мм. Отличие в том, что скоростной нагрев при стрельбе приводит к полному α-γ-α превращению в слое стали в несколько десятков микрометров, граничащем с гальваническим хромом. Мартенсит закалки образуется по всему слою казенной части стволов. Естественно, живучесть стволов калибра 12,7 мм, 14,5 мм ниже, чем живучесть стволов калибра 7,62 мм.
Анализ выявленных недостатков при исследовании стволов после испытания на ресурс позволяет сделать однозначный вывод, что достигнутая живучесть стволов определена положением первой критической точки AC1 применяемых сталей.
По прототипу в подавляющем большинстве случаев стволы стрелкового оружия изготовляют из стали 30ХН2МФА. Эта сталь надежно обеспечивает требуемый комплекс механических свойств, технологична при хромировании канала ствола, не пассивируется при анодном травлении при величине пульсаций постоянного тока и напряжения в 8-10% от номинала. Однако, сталь 30ХН2МФА имеет низкое положение первой критической точки AC1=720°С. Поэтому по причинам, изложенным выше, этот факт приводит к преждевременной осыпаемости хрома в казенной части ствола при стрельбе. Сталь оказывается незащищенной и боевые параметры как-то: начальная скорость пули, кучность боя катастрофически ухудшаются. Поэтому пулеметы обозначенных калибров комплектуются запасным стволом.
Предлагаемым изобретением решается задача по повышению качества и улучшению эксплуатационных характеристик автоматического стрелкового оружия, снижению затрат при производстве пулеметов.
Технический результат, получаемый при осуществлении изобретения, заключается в обеспечении повышенного ресурса стволов, повышении живучести в два и более раз.
Указанный технический результат достигается тем, что в предлагаемом способе изготовления ствола автоматического стрелкового оружия, заключающемся в выборе ствольной стали, изготовлении заготовки ствола, термической обработке на заданный комплекс механических свойств, механической обработке наружной и внутренней поверхностей, формировании нарезной части канала ствола, образовании патронника, осаждении на поверхности канала ствола гальванического хрома с последующим прогревом, новым является то, что для изготовления ствольной заготовки применяют легированные стали с содержанием углерода не выше 0,3 мас.%, имеющие критическую точку AC1=790°С и выше, затем заготовку подвергают закалке, при этом охлаждение в перлитном интервале температур осуществляют со скоростью, обеспечивающей подавление процесса выделения карбидов по границам зерен аустенита, используют для гальванического хромирования канала ствола источник постоянного тока и напряжения с пульсациями силы тока и напряжения не более 1% от номинала.
По предлагаемому способу изготовления стволов автоматического стрелкового оружия используют стали, содержащие в своем составе легирующие элементы, которые позволяют не только обеспечить после улучшения ствольной заготовки требуемый комплекс механических свойств, но и значительно повышают положение первой критической точки.
Предлагаются стали, например 25Х4МФ1СА-Ш со значением AC1=820°С, 30Х3М3ФА-Ш с селектом углерода по верхнему пределу не более 0,3%, со значением AC1=815°С, 25Х3М3НБЦА-Ш со значением AC1=790°С.
Очевидно, что структурно-фазовые превращения в слое стали, примыкающем к хрому, которые в первую очередь отвечают за осыпаемость хрома в казенной части стволов, изготовленных из предложенных сталей, начинаются на более поздней стадии стрельбы, и как показывают результаты исследования стволов калибра 7,62 мм, снятых в разные моменты при испытании на ресурс, когда толщина хрома уменьшается с ~0,2 мм до ~0,1 мм. Утоненный слой хрома, полученный в результате его износа из-за сильного разогрева его поверхности горением пороховых газов, падением микротвердости и в результате трения с оболочкой пули уже не является тем барьером, который предохраняет слой стали, граничащий с хромом от нагрева выше точки AC1. С этого момента в казенной части стволов из предложенных сталей развиваются те же процессы, что и в стали 30ХН2МФА.
Испытание стволов калибра 7,62 мм из стали 30Х3М3ФА-Ш на полный ресурс подтверждает факт повышения живучести в три раза. В результате отпадает необходимость комплектации пулемета запасным стволом.
Из изложенного выше также очевидно, что качество нанесения гальванического покрытия является одним из определяющих факторов обеспечения живучести стволов. Перед хромированием канала ствола всегда производят анодное травление — активирование поверхности путем пропускания обратного тока. Этот процесс необходим, так как напрямую влияет на обеспечение качественного сцепления хрома со сталью. Стволы из стали 30ХН2МФА любого калибра надежно хромируются с применением источника постоянного тока ТВР-1600/12, имеющего значительные по величине пульсации тока и напряжения в диапазоне 8-10% от номинала. Анодное травление перед хромированием стволов из сталей 25Х4МФ1СА-Ш, 30Х3М3ФА-Ш, 25Х3М3НБЦА-Ш, имеющих положение точки AC1 выше, чем у стали 30ХН2МФА, с применением указанного источника постоянного тока приводит к окислению поверхности независимо от плотности обратного тока и минимального времени обработки. Естественно, адгезия хрома со сталью будет неудовлетворительной, что подтверждено осмотром канала ствола после анодного травления и методикой проверки осыпаемости хрома испытанием специальных образцов. Образование пассивной пленки на поверхности канала ствола при анодном травлении связано, в первую очередь, с химическим составом сталей. Стали 25Х4МФ1СА-Ш, 30Х3М3ФА-Ш, 25Х3М3НБЦА-Ш, имеющие положение точки AC1 выше, чем у стали 30ХН2МФА, в большей степени легированные, по сравнению со сталью 30ХН2МФА. Сталь 30Х3М3ФА-Ш содержит примерно по три процента хрома и молибдена, а сталь 25Х4МФ1СА-Ш дополнительно легирована четырьмя процентами хрома, примерно одним процентом ванадия и кремния, которые повышают положение точки AC1, сталь 25Х3М3НБЦА-Ш кроме хрома и молибдена дополнительно легирована никелем, ниобием и цирконием.
Атом молибдена имеет радиус значительно больше, чем у железа, поэтому при содержании молибдена в стали примерно три процента образуется ограниченный раствор замещения. Естественно, при этом увеличивается напряжение кристаллической решетки железа. Меньший вклад в увеличении напряжения решетки железа вносят атомы хрома, радиус которых незначительно больше радиуса атомов железа, поэтому хром образует с железом неограниченный твердый раствор замещения. Кроме того, дополнительные напряжения в матрице создают дисперсные частицы специальных карбидов, присутствующие в сталях, например карбида ванадия, а также карбидов ниобия и циркония. Все перечисленные факторы приводят к пассивации поверхности канала ствола в процессе анодного травления при использовании источника тока с большими по величине пульсациями тока и напряжения.
Исключить окисление поверхности канала ствола при анодном травлении и надежно обеспечить качество сцепления хрома со сталью удалось стабилизацией по величине тока и напряжения, то есть применить при гальваническом хромировании источник постоянного тока с пульсациями тока и напряжения, не превышающими 1% от номинала, например «Пульсар ПРО 1600/12», где величина «1600» — номинальное значение силы тока (А), «12» — номинальное значение напряжения (В).
Технические решения с признаками, отличающими заявляемое техническое решение от прототипа, не известны и явным образом из уровня техники не следуют. Это позволяет считать, что заявляемое техническое решение является новым и обладает изобретательским уровнем.
Способ изготовления ствола автоматического стрелкового оружия заключается в следующем.
Для изготовления заготовки ствола выбирают легированную сталь, в составе которой легирующие элементы в совокупности обеспечивают высокое положение критической точки AC1, верхний предел содержания углерода в которой ограничивают 0,3%. Подвергают заготовку термической обработке на заданный комплекс механических свойств, в том числе проводят закалку, обеспечивая высокую скорость охлаждения в перлитном интервале температур, с подавлением процесса выделения карбидов по границам зерен аустенита. Производят механическую обработку наружной и внутренней поверхностей ствольной заготовки. Формируют нарезную часть канала ствола, изготовляют патронник. Осаждают на поверхности канала ствола гальванический хром с последующим прогревом с использованием источника постоянного тока с пульсациями силы тока и напряжения не более 1% от номинала, а затем производят прогрев ствола с хромовым покрытием.
Пример реализации способа изготовления ствола автоматического стрелкового оружия калибра 7,62 мм из стали 30Х3М3ФА-Ш.
Ствольную заготовку из стали 30Х3М3ФА-Ш с селектом углерода по верхнему пределу, имеющей высокое положение точки AC1=815°C, подвергают термической обработке по режиму: закалка с 1025+5°С на воду с последующим отпуском на 705+5°С с охлаждением через воду на воздух. Ограничение верхнего предела углерода в стали не выше 0,3% позволяет производить закалку ствольной заготовки на воду. Высокая скорость охлаждения в перлитном интервале подавляет процесс выделения карбидов по границам зерен аустенита, а значит, обеспечивается требуемое значение ударной вязкости ствольной заготовки. Высокая скорость охлаждения стали в мартенситном интервале с содержанием углерода до 0,3% не вызывает образование закалочных трещин. Максимальная твердость ствольной заготовки после закалки не превышает 53 HRC.
После представленной термической обработки механические свойства стали имеют: предел текучести σ02 не менее 80 кгс/мм2, предел прочности σв не менее 90 кгс/мм2, относительное удлинение δ5 не менее 10%, относительное сужение ψ не менее 40%, ударная вязкость KCU не менее 9 кгс м/см2, что удовлетворяет требованиям технических условий.
Затем ствольную заготовку подвергают механической обработке по наружной и внутренней поверхностям, формируют на радиально-ковочной машине SHR-17 нарезную часть канала ствола, изготовляют патронник, осаждают на поверхности канала ствола гальванический хром с использованием источника постоянного тока с пульсациями тока и напряжения не более 1% от номинала «Пульсар ПРО 1600/12». Для хромирования устанавливают анод внутри ствола по оси канала с помощью специальных приспособлений, которые крепятся на дульной и казенной частях ствола. Располагают полученную сборку в установке для скоростного хромирования. К стволу и аноду подключают токоподводы от источника тока. Производят прогрев ствола пропусканием по каналу водного электролита состава CrO3 180-200 г/л, H2SO4 3-5 г/л с температурой 70-75°С в течение 3-4 минут. Активируют поверхность канала ствола пропусканием обратного тока I=70-85 A в течение 5-7 минут, затем производят хромирование канала ствола прямым током I=135-155 А в течение 139-172 минут. После хромирования прогревают ствол с хромовым покрытием при температуре 480-500°С с целью его стабилизации.
Пример реализации способа изготовления ствола автоматического стрелкового оружия калибра 14,5 мм из стали 25Х3М3НБЦА-Ш.
Ствольную заготовку из стали 25Х3М3НБЦА-Ш, имеющей высокое положение точки AC1=790°С по сравнению со сталью 30ХН2МФА, подвергают термической обработке по режиму: закалка с 1050±10°C на воду с последующим отпуском на 630-645°С с охлаждением через воду на воздух. Высокая скорость охлаждения в воде подавляет процесс выделения карбидов по границам зерен аустенита в перлитном интервале температур, тем самым обеспечивается требуемое значение ударной вязкости ствольной заготовки. Максимальная твердость ствольной заготовки после закалки не превышает 52HRC.
После представленной термической обработки механические свойства стали имеют: предел текучести σ02 не менее 90 кгс/мм2; относительное сужение ψ не менее 65%, ударная вязкость KCU не менее 5 кгс м/см2, что удовлетворяет требованиям механических условий.
Затем ствольную заготовку подвергают механической обработке по наружной и внутренней поверхностям, формируют на радиально-ковочной машине SHR-17 нарезную часть канала ствола, изготовляют патронник, осаждают на поверхности канала ствола гальванический хром с использованием источника постоянного тока с пульсациями тока и напряжения не более 1% от номинала «Пульсар ПРО 1600/12». Для хромирования устанавливают анод внутри ствола по оси канала с помощью специальных приспособлений, которые крепятся на дульной и казенной частях ствола. Располагают полученную сборку в установке для скоростного хромирования. К стволу и аноду подключают токоподводы от источника тока. Производят прогрев ствола пропусканием по каналу водного электролита состава CrO3 160-200 г/л, H2SO4 3-5 г/л с температурой 75±2°С в течение 3-4 минут. Активируют поверхность канала ствола пропусканием обратного тока I=450-480 А в течение 4-6 минут, затем производят хромирование канала ствола прямым током I=600-650 А в течение 108-126 минут. После хромирования прогревают ствол при 500-520°С с целью стабилизации хромового покрытия.
Таким образом изготовление стволов автоматического стрелкового оружия калибра 7,62 мм, 12,7 мм, 14,5 мм и других предложенным способом обеспечивает повышение их живучести в два и более раз, тем самым представляется возможность производить комплектацию пулеметов одним стволом.
Способ изготовления ствола автоматического стрелкового оружия, включающий изготовление заготовки ствола из выбранной стали, термическую обработку заготовки на заданный комплекс механических свойств, механическую обработку наружной и внутренней поверхностей, формирование нарезной части канала ствола, образование патронника, осаждение на поверхности канала ствола хрома путем гальванического хромирования с последующим прогревом, отличающийся тем, что для изготовления заготовки ствола используют легированную сталь с содержанием углерода не выше 0,3 мас.% и легирующих элементов, обеспечивающих в совокупности высокое положение критической точки Ac1, затем заготовку подвергают закалке, при этом охлаждение осуществляют в перлитном интервале температур со скоростью, обеспечивающей подавление процесса выделения карбидов по границам зерен аустенита, а для гальванического хромирования канала используют источник постоянного тока и напряжения с пульсацией силы тока и напряжения не более 1% от номинала.
findpatent.ru
Способ изготовления гильз патронов стрелкового оружия
Изобретение относится к производству патронов стрелкового оружия, в частности к изготовлению гильз патронов различных калибров. Из заготовки, отрезанной от прутка или проволоки, совмещенным поперечно-продольным выдавливанием получают цилиндрический ступенчатый стаканчик. При этом используют матрицу, выполненную с направляющей частью и кольцевой рабочей полостью, и противопуансон. Диаметр кольцевой полости матрицы превышает диаметр ее направляющей части. Диаметр противопуансона равен 0,5…1,5 диаметра направляющей части матрицы. Противопуансон образует с пересечением направляющей части матрицы с внутренней поверхностью рабочей полости зазор. Поперечно-продольное выдавливание производят с частичным или полным вытеснением материала заготовки из направляющей части матрицы в ее кольцевую рабочую полость через упомянутый зазор. Затем осуществляют утонение стенки стаканчика вытяжкой и, штамповку дна с формированием капсюльного гнезда гильзы. В результате обеспечивается сокращение количества технологических операций и снижение нагрузки на инструмент. 1 з.п. ф-лы, 3 ил.
Изобретение относится к производству гильз для патронов стрелкового оружия, а также может быть использовано для изготовления гильз к гражданскому, служебному, боевому ручному стрелковому оружию, пиропатронов, строительно-монтажных патронов и артиллерийских выстрелов, в частности к технологии изготовления гильз.
Гильза — основной конструктивный элемент патрона или артиллерийского выстрела, к которому предъявляют высокие требования по точности формы, размерам, массе, качеству поверхности и др.
Действующая по настоящее время на предприятии технология изготовления гильз, отработанная на протяжении всего прошлого века, не претерпела существенных изменений. См. технологические процессы ИМ 01100.02230, ИМ 01100.01525, ИМ 01100.00327 и др. изготовления гильз патронов стрелкового оружия.
Исходным материалом для изготовления гильз служит либо латунная (Л68 ГОСТ 5362-78, Л63 ГОСТ 2208-2007), либо стальная (18ЮА ГОСТ В 26853-86, 11ЮА ГОСТ 8851-75), либо биметаллическая (биметалл 1 ОСТ 3-6648-91 на основе стали 18КП ГОСТ 1050-88) полоса (лента, лист), из которой разделительными операциями листовой штамповки — отрезкой и вырубкой получают плоскую, как правило, круглую в плане заготовку гильзы. Технологический процесс в дальнейшем включает несколько операций вытяжки, одну или несколько операций штамповки дна с формированием капсюльного гнезда и обжима дульца, термические и сопутствующие им химические операции по очистке поверхности от окалины, образовавшейся в процессе отжига, вспомогательные операции по подготовке поверхности под смазку, нанесение смазки и антикоррозийных покрытий, а также ряд контрольных операций, обеспечивающих контроль требуемых размеров и качества гильз.
Несмотря на стабильность и высокий уровень производства, действующая технология обладает одним существенным недостатком — низким коэффициентом использования металла, равным 0,38-0,54, при этом две трети всех отходов приходятся на высечку — металл, остающийся после вырубки круглых заготовок при многорядном шахматном раскрое полосы или ленты. К недостаткам такого способа можно также отнести сложность технологического процесса и связанную с этим высокую себестоимость изготовления гильз.
Германская фирма «Капп» в конце второй мировой войны приступила к массовому производству стальных 7,92 мм гильз из прутка. Технология формоизменения плоской после осадки заготовки, ничем не отличалась от используемой в России технологии.
Известна технология получения гильз патронов из квадратной (прямоугольной), или шестигранной в плане заготовки, при которой полуфабрикаты гильз после вытяжки приобретают корончатую форму открытого торца. Такая технология снижает расход металла, но впадины у открытого торца, являясь концентраторами напряжений, приводят на последующих операциях вытяжки к образованию трещин, что требует увеличения размеров заготовки, добавляет при этом ряд дополнительных операций, снижая положительный эффект от такого усовершенствования.
Нагрев заготовок перед штамповкой и выдавливанием не дал существенных преимуществ перед холодным деформированием, внося дополнительные технические и технологические трудности.
Известен способ получения гильз патронов стрелкового оружия, включающий отрезку заготовки от прутка, изготовление цилиндрического стакана обратным выдавливанием, утонение стенки вытяжкой с образованием переменной ее толщины заданных размеров, штамповку дна с предварительным и окончательным формированием капсюльного гнезда, механическое образование фланца в дне гильзы и комплекс операций, позволяющих получить окончательное изделие, при этом стакан выполняют ступенчатым с оформленным капсюльным гнездом, путем сочетания обратного и прямого выдавливания, утонение стенки ведут в расширенной части его ступени, после чего формируют фланец — см. заявку на изобретение №96105717 — прототип. Обратным выдавливанием заготовки получают стенку ступенчатого стакана, а прямым выдавливанием с одновременным дополнительным тангенциальным сжатием заготовки образуют его донную часть и формируют капсюльное гнездо. При совмещенном выдавливании заготовки истечение металла в сторону формирования дна и капсюльного гнезда ведут с ограничением на заданный размер по толщине дна. Формообразование фланца с проточкой ведут раскатным роликом. Формообразование фланца, выступающего над диаметром гильзы, производят высадкой. Суженную ступень стакана выдавливают на диаметр проточки гильзы, а после вытяжки фланец с проточкой высаживают в разъемной матрице. Фланец с проточкой высаживают на диаметр, превышающий наибольший диаметр гильзы. При выдавливании ступенчатого стакана размеры капсюльного гнезда выполняют предварительными, а при формообразовании фланца их калибруют до получения окончательных значений. Выдавливание стакана выполняют с внутренним диаметром, равным или больше наружного диаметра гильзы, а вытяжку с утонением стенки ведут с одновременной обрезкой кромки.
Утонение стенки ступенчатого полуфабриката ведут ротационной вытяжкой или выдавливанием, либо многопереходной вытяжкой. Заготовку перед выдавливанием калибруют осадкой. Осадку заготовки ведут в штамповом инструменте, предназначенном для резки прутка. По меньшей мере, перед одной из формоизменяющих операций производят термохимическую обработку заготовки.
Известный способ получения гильз патронов стрелкового оружия включает отрезку заготовки от прутка, калибровку, получение цилиндрического ступенчатого стаканчика выдавливанием, утонение стенки вытяжкой с образованием переменной ее толщины, штамповку дна с формированием капсюльного гнезда путем сочетания обратного и прямого выдавливания.
К недостаткам известного способа-прототипа можно отнести неполное использование возможностей процесса холодного выдавливания и действие высоких удельных сил в процессе формообразования стенок гильзы на инструмент, а также высокую себестоимость изготовления гильз.
Задачей настоящего изобретения является устранение недостатков прототипа, в частности, повышение технологических возможностей процесса холодного выдавливания, снижение нагрузок на инструмент при формообразовании гильзы и снижение себестоимости готовой продукции.
Поставленная задача достигается сочетанием известных признаков, таких как отрезка заготовки от прутка (проволоки), изготовление цилиндрического ступенчатого стаканчика выдавливанием, утонение стенки стаканчика вытяжкой с образованием ее переменной толщины, штамповку дна ступенчатого стаканчика с формированием капсюльного гнезда путем сочетания обратного и прямого выдавливания, и новых, заключающихся в том, что ступенчатый стаканчик получают совмещенным поперечно-продольным выдавливанием заготовки в матрицу, выполненную с направляющей частью и кольцевой рабочей полостью диаметром, превышающим диаметр направляющей части, используют противопуансон диаметром, равным 0,5…1,5 диаметра направляющей части матрицы, образующий с пересечением направляющей части матрицы с внутренней поверхностью рабочей полости зазор, при этом поперечно-продольное выдавливание заготовки производят с частичным или полным вытеснением материала заготовки из направляющей части матрицы в ее кольцевую рабочую полость через зазор.
Используют противопуансон, рабочий торец которого выполнен плоским или фигурным, например, сферической, конической выпуклой, конической вогнутой формы.
Новизной предложенного технического решения является получение ступенчатого стаканчика совмещенным поперечно-продольным выдавливанием в матрицу, выполненную с направляющей частью и кольцевой рабочей полостью диаметром, превышающим диаметр направляющей части, используют противопуансон диаметром, равным 0,5…1,5 диаметра направляющей части матрицы, образующий с пересечением направляющей части матрицы с внутренней поверхностью рабочей полости зазор, при этом поперечно-продольное выдавливание заготовки производят с частичным или полным вытеснением материала заготовки из направляющей части матрицы в ее кольцевую рабочую полость через зазор.
Такой способ исключает технологическую операцию калибровки заготовки, а заготовке придает форму и размеры, благоприятные для выполнения последующих технологических операций и получения заданных свойств. При этом снижается нагрузка на рабочий инструмент.
Указанные отличительные признаки, согласно проведенным патентно-информационным исследованиям, являются новыми, промышленно выполнимыми, неочевидными и направлены на достижение поставленной изобретением задачи.
Дополнительными признаками, которые конкретизируют основные, направленные на получение положительного результата, являются выполнение рабочего торца противопуансона плоским или фигурным, например, сферической или конической вогнутой или выпуклой формы.
На фиг.1 схематично представлены с левой стороны заготовки, установленные в направляющую часть матрицы, а с правой стороны — варианты выполнения стаканчиков.
На фиг.2 — варианты изготовления стаканчиков: а) — с плоской донной частью пуансона, б) — с выпуклой поверхностью торца.
На фиг.3 представлены варианты геометрии кольцевой полости матрицы и боковой поверхности противопуансона: а) — цилиндрическая, б) — коническая, в) — сферическая.
На графических материалах представлена отрезанная от прутка заготовка 1, которая устанавливается в направляющую часть матрицы до упора о торец противопуансона, который может быть выполнен с цилиндрической 2, или конической 3, или ступенчатой 4 рабочими поверхностями. При помощи пуансона 5 осуществляется давление на заготовку 1. После выполнения операции совмещенного поперечно-продольного выдавливания с течением материала заготовки из направляющей части матрицы в рассматриваемом варианте — вниз в кольцевую рабочую полость матрицы большего диаметра, которая может быть выполнена цилиндрической 6 или конической 7, заготовка 1 приобретает цилиндрическую 8 или ступенчатую форму различной конфигурации 9,10, 11, 12, либо коническую ступенчатую 13 или коническую 14 форму стаканчика. Ступенчатая форма стаканчика формируется кольцевой цилиндрической 6 или конической 7 полостью матрицы и наружной и наружной поверхностью противопуансоно 2 или 3, или 4.
Внутренняя поверхность рабочей полости матрицы может быть выполнена иной формы, например, многогранной или криволинейной.
Необходимую по технологии форму торца пуансона выполняют либо в виде плоскости 15, либо вогнутой 16, или выпуклой 17 полусферы, либо в виде вогнутого 18 или выпуклого 19 конуса. Матрица 20 и 21 может быть выполнена с цилиндрической или конической рабочей полостью.
Предлагаемый способ изготовления гильз патронов стрелкового оружия осуществляют следующим образом.
От прутка или проволоки отрезают заготовку заданной длины и подают ее в направляющую часть матрицы до контакта с противопуансоном 2 или 3, или 4. Пуансон 5, воздействуя на заготовку 1, вытесняет материал заготовки, который обтекает противопуансон и вытесняется в рабочую кольцевую цилиндрическую или коническую полость. При этом осуществляется поперечно-продольное выдавливание с стечением материала заготовки из направляющей части матрицы в кольцевую рабочую полость матрицы большего диаметра. Полное вытеснение материала заготовки в кольцевую полость, матрицы с получением ступенчатого стаканчика может осуществляться при ступенчатом выполнении противопуансона 4.
Далее заготовку гильзы (ступенчатый стаканчик) обрабатывают традиционными способами в соответствии с действующими технологическими процессами, придавая заданную форму и размеры. При этом осуществляют утонение стенки стаканчика вытяжкой с образованием ее переменной или постоянной толщины при помощи пуансонов и матриц с соответствующими рабочими размерами, штамповку дна с формированием капсюльного гнезда путем сочетания обратного и прямого выдавливания.
Предлагаемые операции формирования ступенчатого или цилиндрического стаканчика позволяют в дальнейшем получить необходимую длину стенок и толщину донной части стаканчика и качественно в дальнейшем сформировать стенки и капсюльное гнездо.
В зависимости от требуемых формы и размеров заготовки диаметр противопуансона может быть выполнен равным 0,5…1,5 диаметра направляющей части матрицы. При диаметре противопуансона менее 0,5 снижается его стойкость. При диаметре более 1,5 диаметра направляющей части в теле заготовки возникают значительные растягивающие напряжения, что приводит к увеличению брака по трещинам. При расстоянии между нижней кромкой направляющей части матрицы и рабочим торцом пуансона, выполненным меньше 0,1 диаметра направляющей части матрицы, возникают значительные нагрузки на инструмент, снижающие его прочностные свойства, а при расстоянии, равном 3 (трем) диаметрам направляющей части матрицы, необходим большой ход пуансона, нецелесообразное и непредсказуемое деформирование материала заготовки.
Выполнение рабочего торца противопуансона плоским или фигурным, например, сферической или конической формы, выпуклым или вогнутым позволяет приблизить форму заготовки к технологически удобной форме для последующего деформирования.
Конкретный пример осуществления способа.
Стальную заготовку 1, отрезанную от прутка диаметром 10 мм длиной 14 мм, поместили в направляющую часть матрицы 2. Под воздействием (давлением) пуансона 3 металл заготовки вытеснили в кольцевую полость 6 матрицы 2 до полного ее заполнения. При этом полное заполнение кольцевой полости 6 осуществлялось комбинированным продольно-поперечным выдавливанием материала заготовки из направляющей части матрицы с истечением (вытеснением) материала заготовки в кольцевую полость матрицы большего диаметра, чем диаметр ее направляющей части.
Далее заготовку гильзы (ступенчатый стаканчик) обработали традиционным способом в соответствии с действующим технологическим процессом, придав заданную форму и размеры, включая ее донную часть.
В настоящее время на предприятии разработана техническая документация на изготовление из прутка гильз к 5,45 мм-патронам. Изготовлена и испытана на прочность и безотказность работы автоматики оружия опытная партия гильз, изготовленных по предлагаемой технологии. Результаты испытания подтвердили техническую возможность и экономическую целесообразность предлагаемого технического решения. Промышленное освоение новой технологии позволит экономить до 40% металла, повысить стойкость рабочего инструмента, получать качественную продукцию, удовлетворяющую предъявляемым к ней требованиям со значительным сокращением себестоимости ее изготовления.
1. Способ изготовления гильз патронов стрелкового оружия, включающий отрезку заготовки от прутка или проволоки, получение цилиндрического ступенчатого стаканчика выдавливанием, утонение стенки стаканчика вытяжкой с образованием ее переменной толщины, штамповку дна ступенчатого стаканчика с формированием капсюльного гнезда путем сочетания обратного и прямого выдавливания, отличающийся тем, что ступенчатый стаканчик получают совмещенным поперечно-продольным выдавливанием заготовки в матрицу, выполненную с направляющей частью и кольцевой рабочей полостью диаметром, превышающим диаметр направляющей части, с использованием противопуансона, выполненного диаметром, равным 0,5…1,5 диаметра направляющей части матрицы, и образующего с пересечением направляющей части матрицы с внутренней поверхностью рабочей полости зазор, при этом совмещенное поперечно-продольное выдавливание заготовки осуществляют с частичным или полным вытеснением материала заготовки из направляющей части матрицы в ее кольцевую рабочую полость через упомянутый зазор.
2. Способ по п.1, отличающийся тем, что используют противопуансон, рабочий торец которого выполнен плоским или фигурным, например сферической, конической выпуклой, конической, вогнутой формы.
findpatent.ru
Подробное наставление о изготовлении и сбережении огнестрельного и белого солдатского оружия с 6-ю чертежами И.Гогель
Иван Григорьевич Гогель (1770—1834) — генерал от артиллерии, писатель и военный педагог. Закончив в 1793 году Сухопутный Шляхетский кадетский корпус в Санкт-Петербурге, был определен капитаном в армию. Вначале проходил службу в понтонной роте, затем в артиллерийских частях. И.Г. Гогель участвовал в боевых действиях с французами в составе десантного корпуса.
С декабря 1808 года главноприсутствующий в Ученом комитете по артиллерийской части. В ноябре 1810 года был назначен инспектором Сестрорецкого оружейного завода, где исполнял обязанности по апрель 1824 года. Автор книг о артиллерии, соавтор «Артиллерийского журнала» и «Военного журнала». За время службы неоднократно награждался высшими российскими орденами.
Книга «Подробное наставление о изготовлении и сбережении огнестрельного и белого солдатского оружия с 6-ю чертежами» И.Гогеля является пожалуй одной из немногих научных трудов, подробнейшим образом рассказывающая о изготовлении огнестрельного и холодного оружия в России в конце 18 — начале 19 века.
Данное издание можно условно разделить на четыре основные части. Первая часть книги рассказывает о разновидностях и устройстве огнестрельного оружия. Вторая часть посвящена технологии изготовления ручного огнестрельного оружия. Третья часть посвящена внутренней и внешней баллистике и перспективах развития ручного огнестрельного оружия. Последняя часть повествует о холодном оружии, его разновидностях и технологии изготовления.
Подробное описание кремневого пехотного ружья дает четкое представление об устройстве, линейных размерах оружия и его основных частей.
Часть книги, посвященная технологии изготовления ручного огнестрельного оружия, является настоящей настольной книгой для историков, реставраторов и просто любителей оружия. Более подробного описания технологических операций по изготовлению стволов, кремневых замков, прибора и других частей оружия просто не существует.
Процесс изготовления описан начиная с выбора и характеристик материалов, используемых для создания оружия. Далее идет пошаговое описание процесса выделки отдельных частей и деталей оружия, после чего идет порядок сборки, осмотра и проверки оружия. Особенно интересен заводской процесс изготовления деталей кремневого замка. Автор отдельно останавливается на описании термической обработки стальных деталей.
Теория выстрела, различные опыты над винтовками, вероятность попадания пуль, сбережение и починка огнестрельного оружия, вот те вопросы, которые охвачены в главах книги. Помимо общих научных вопросов исследования внутренней и внешней баллистики автор уделяет внимание и практике применения оружия. Разделы о том как узнать на каком расстоянии находится неприятель, причины осечек, правила прицеливания и т.д. безусловно были необходимы для обучения солдат и офицеров действующей армии.
Технология изготовление холодного оружия рассмотрена в последней части книги. И. Гогель описывает металл используемый для клинков, закалку и обточку клинков. Отдельные главы посвящены изготовлению эфесов сабель и ножен. Таблица с размерами частей холодного оружия дает представление о линейных величинах, характеризующих холодное оружие, использующееся в русской армии.
В приложении к книге имеются чертежи огнестрельного оружия и его частей, а так же описание к данным чертежам.
Вы можете купить книгу Ивана Григорьевича Гогеля «Подробное наставление о изготовлении и сбережении огнестрельного и белого солдатского оружия с 6-ю чертежами», посетив Наш магазин.
Электронная версия книги представляет собой файл формата PDF, объем — 25,6 Мб, страниц вместе с чертежами и приложениями — 318. Скан книги «Подробное наставление о изготовлении и сбережении огнестрельного и белого солдатского оружия с 6-ю чертежами И.Гогель» Вы можете скачать из облака бесплатно, кликнув левой кнопкой мыши ниже по ссылке.
Популярность: 12%
Другие материалы сайта:
Перейти на главную страницу сайта Старинное огнестрельное оружие
historypistols.ru