Технология производства зеркал – Производство зеркал
Современные методы производства зеркал
ИстокиС незапамятных исторических времен, отражения приводили человечество в восторг. Якобы Нарцисс был околдован своим собственным отображением в водной глади, а в сказках магические силы были сосредоточены в зеркалах. Зеркала берут свое начало от отражаемых водных поверхностей и полированных металлических пластин до портативного зеркальца и зеркал для ванных комнат. Зеркала используются в декорировании интерьеров с 17 века, а отражающие поверхности на машинах и на лобби отелей до сих пор достаточно популярны в современном дизайне. Зеркала используются практически везде: зеркала, в которые мы смотримся, зеркала заднего вида на автомобилях, в строительстве небоскребов, в изготовлении приборов для научных исследований, таких как микроскопы и лазеры.
В сущности, отличие современного зеркала от отражения в водной гладит не так фундаментально. Когда свет попадает на какую-либо поверхность, большинство из них будут отражаться. Зеркала это просто гладкие поверхности с глянцевыми, непрозрачными задними фонами, которые очень хорошо отражают. Вода отражает хорошо, стекло отражает недостаточно, полированный металл отражает очень хорошо. Степень отражаемости (как много света отражается от поверхности, коэффициент диффузии поверхности, каково направление светового отражения от поверхности) может варьироваться. Тем не менее, данные вариации всего лишь тонкости. Обычно все отражающие поверхности и зеркала имеют одинаковые свойства. Зеркала, сделанные человеком, существовали с древних времен. Первые зеркала представляли чаще всего кусок полированного железа и использовались только высшей знатью. Внешний вид отражал, а в некоторых случаях, и устанавливал положение и власть в обществе, поэтому потребность в отражаемом стекле была очень высока, точно так же как и потребность в усовершенствовании техники производства зеркал. Серебрение — процесс нанесения на заднюю поверхность стекла расплавленного серебра — стало очень популярным методом в изготовлении зеркал в 17 веке. Стекло, используемое в этих ранних зеркалах, очень часто было покоробленным, тем самым искажало картинку. Иногда отражения в таких зеркалах напоминали отражения в сегодняшних «Комнатах смеха». Современное изготовление зеркал и металлургические технологии позволяют делать лист стекла очень гладким с равномерным покрытием задней поверхности, придавая поверхности идеальную четкость. До сих пор качество зеркал зависит от времени и материалов, затраченных на их производство. Портативное зеркало для сумочки может искажать изображение, тогда как хорошее зеркало для ванной комнаты вряд ли будет иметь видимые недостатки. Зеркала для науки изготавливаются практически без дефектов и искажающих свойств.
Свойства материалов оказывает большое влияние на качество зеркала. Свет лучше отражается от не диффузионных, гладких и непроницаемых поверхностей, чем от прозрачных. Малейшее отклонение от этих постулатов уменьшает эффективность зеркала.
Инновации в производстве зеркал направлено непосредственно на придание стеклу гладкости и нанесения металлического покрытия одинаковой толщины, потому что свет, проникая через разные толщины стекла, может создавать искаженную картинку в отражении.
Сырье
Стекло, основной элемент зеркала, плохой отражатель. Оно отражает лишь 4% света, падающего на него. Но, тем не менее, стекло обладает хорошим свойством однородности, особенно в полированном виде. Это значит, что после полировки на стекле практически не остается углублений, что создает прекрасную базу для нанесения отражающего металлического покрытия. Когда слой металла нанесен, покрытие становится очень ровным, без выпуклостей и впадин. Есть еще одна причина тому, что стекло это отличный материал для зеркал. Дело в том, что стекло можно формовать, придавая ему различные формы для специфических зеркал. Пластины стекла делаются из диоксида кремния, добытого или очищенного из песка. Стекло, сделанное из природных кристаллов диоксида кремния, известно как плавленый кварц. Существуют так же синтетические стекла, которые относятся к синтетическому плавленому кварцу. Диоксид кремния или кварц расплавляются при высокой температуре и отливаются в листы.
Эти базовые материалы должны иметь покрытие, чтобы получилось зеркало. Металлическое покрытие является общепринятым. Разнообразные виды металлов, такие как серебро, золото, хром, используются для этого. Серебро было наиболее популярно сто лет назад. Отсюда и происхождение термина «серебрение». На старых зеркалах, имеющие серебряную основу, часто видны темные полосы на стекле, это из-за того, что материал был покрыт толстым неоднородным слоем, что приводило к напластовыванию, царапанью и тусклости. До 1940 года, производители зеркал использовали ртуть. Она идеально ровно ложилась на поверхность и не тускнела. Но такая практика вскоре забылась, так как было проблематично хранить токсичную жидкость. Сегодня, алюминий является общепризнанным металлическим покрытием для зеркал.
Научные зеркала иногда покрывают другими металлами, например, диоксидом кремния и нитридом кремния. Эти типы покрытия используется как изолирующие покрытия, и используются в качестве, как отражателей, так и защитной отделкой на металлическом покрытии. Они меньше подвержены повреждениям, чем металл. Научные зеркала так же покрывают серебром или золотом, чтобы иметь возможность отражать определенные цвета света.
Структура
Поверхность — это наиболее важная часть в дизайне зеркала. Зеркала, используемые в домашнем хозяйстве, имеет приблизительно те же характеристики, как и оконное стекло или стекло для фото рамки. Используемое стекло должно быть достаточно ровным и прочным. Конструктору достаточно только определить желаемую толщину стекла, например, более толстое стекло — более прочное, но и более тяжелое. Научные зеркала обычно имеют специальную структуру покрытия. Такие покрытия идеально гладкие, в несколько тысячных дюймов, со специально сконструированным искривлением, почти как в линзах для очков. Структура таких зеркал так же важна, как и для линз, использующихся в офтальмологии. Зеркало может быть предназначено как для фокусирования света, так и для его рассеивания. Конструкция зеркала также должна соответствовать типу покрытия, нанесенного на него. Покрывающий материал выбирается, исходя из требований прочности и степени отражения, и может зависеть от предназначения зеркала. Покрытие может наноситься на переднюю и на заднюю часть зеркала. Каждый последующий защитный слой должен быть точно определен соответственно каждому этапу нанесения. Для большинства зеркал, отражающее покрытие наносится на заднюю часть поверхности стекла, так как она менее подвержена повреждениям. Задняя поверхность зеркала чаще всего защищена пластиковой или металлической пластиной, что позволяет защищать покрытие от доступа воздуха и острых предметов.
Производственный процесс
Порезка и придание формы стеклу
Первый шаг в производстве зеркала — вырезка по эскизу стекла — заготовки для придания ей в последствие желаемой формы. Если зеркало вырезается для автомобиля, например, то стекло будет вырезано по шаблонам зеркал для машины. Некоторые производители зеркал сами режут стекло, некоторые получают уже готовые заготовки. Не зависимо от того, кто режет стекло, для порезки используются высокотвердые, хорошо заостренные ножи. Алмазные резцы или пилы — острые металлические наконечники или дисковые пилы с алмазным напылением на них- используются чаще всего, так как алмаз не изнашивается стеклом. Метод порезки стекла напрямую зависит от формы, которую хотят придать зеркалу. Например, по одному методу ножи прорезают зеркало в нескольких местах (точечно), а потом под давлением стекло выдавливается по прорезанным контурам. По другому методу специальная машина с алмазными дисками режет стекло по всей длине и ширине по принципу автоматической ленточной пилы. Порезка осуществляется всегда перед нанесением покрытия. Как альтернатива порезки стекла на заготовки существует формовка стекла в расплавленном виде.
Далее заготовки помещаются в оптическую шлифовальную машину. Эта машина состоит из широких плит-оснований с выемками, которые удерживают заготовки стекла. Закрепленную заготовку располагают вплотную к другой металлической плите, которая содержит желаемое покрытие: плоское, выпуклое или вогнутое. Шлифовальная смесь – жидкость с абразивом — распределяется на стеклянной заготовке вращательными и втирательными движениями. Процесс очень похож на размалывание специй в ступке. Шлифовальные зерна постепенно стирают слой поверхности стекла до тех пор, пока оно не примет форму шлифовальной пластины. В процессе шлифования диаметр абразивных зерен каждого номера уменьшают до тех пор, пока поверхность гладкая и ровная. Отшлифованный слой стекла снимается с помощью полировки.
Существует ручной способ шлифовки, но он очень трудоемкий и трудно контролируемый. Этот способ используется в тогда, когда механическое шлифование невозможно, например, в случае если стекло очень широкое или специфической формы. Заводские шлифовальные машины могут размещать одновременно от 50 до 200 заготовок, полируя их вместе. Это более эффективно, чем ручная шлифовка. Даже специализированную оптику изготавливают механически, с помощью специальных приспособлений.
Нанесение отражающего материала
Когда зеркалу придали нужную форму и отполировали, конструктор выбирает желаемое отражающее покрытие. Независимо от того, какое покрытие выбирается, наносится оно на одной и той же машине, которая называется выпариватель. Выпариватель — это широкая вакуумная камера, сверху которой находится плита, поддерживающая заготовку зеркала, а снизу находится контейнер-кристаллизатор для плавления покрывающего металла. Машина называется так, потому что металл нагревается в контейнере — кристаллизаторе до температуры, при которой он выпаривается в вакуум, распределяя покрытие на поверхность стекла. Заготовки помещают по центру над отверстиями верхней удерживающей плиты, так чтобы пары металла достигли поверхности стекла. Металлы могут нагреваться до сотни и тысячи градусов (в зависимости от точки кипения того или иного металла), прежде чем начнется выпаривание. Температурный и временной режимы контролируются очень тщательно, это нужно для того, чтобы достичь правильной толщины покрытия. Такой метод нанесения создает однородную и качественную отражающую поверхность.
Форма отверстий в верхней плите передает металл на стекло, как краски через трафарет. Этот эффект используется для придания зеркалу заданного узора.
Диэлектрическое покрытие наносится аналогичным образом. В качестве диэлектрического покрытия чаще всего используются диоксид кремния и нитрид кремния. Когда газы этих металлов смешиваются при экстремальном нагревании, они вступают в реакцию, образуя при этом очень твердую субстанцию. Такая реакция создает формы покрытия по прочности, не уступающие металлическим.
Некоторые этапы выпаривания могут комбинироваться для создания сложно структурных слоев покрытия. Прозрачные диэлектрические материалы могут наноситься поверх металлов или других диэлектриков, чтобы изменить рефлективные или механические качества поверхности.
Зеркала с серебряным покрытием на задней части стекла, например, имеют матовое диэлектрическое покрытие, чтобы улучшить отражающие свойства и уберечь металлическое покрытие от повреждений.
Наконец, когда покрытие нанесено, зеркало аккуратно упаковывается в противоударную упаковку для транспортировки.
Контроль качества
Как определить насколько хорошо зеркало, и насколько хорошим оно должно быть? Достаточно ли того, что оно отражает 80% света? И все ли 80% света отражаются в одном направлении? Ответ зависит от применения. Карманные зеркала отражают на 80 или 90% и могут иметь небольшие неровности в толщине стекла (подобие водной ряби). Картинка может быть слегка искажена в таком случае, но дефекты не видны невооруженным глазом. Если зеркало предназначается для использования в научных целях, например для телескопа, форма стекла и рефлективная способность рассчитывается до мелочей, дабы быть уверенным, что отражаемый свет пройдет именно там, где нужно конструктору и с определенной интенсивностью. Устойчивость зеркал определяется затратами на изготовление, насколько сложным или простым был процесс производства.
Однородность партии зеркал первостепенная задача обеспечения качества. Зеркала, произведенные с помощью разных производственных аппаратов, могут иметь различную поверхность. Если в одной партии товара широкий диапазон толщин или гладкость покрытия, то нужно улучшать способы производства, чтобы достигать максимальной однородности в одной партии.
Некоторые методы направлены на проверку целостности зеркала. Качество поверхности сначала определяется визуально: царапины, неровность, точки или разводы. Это можно сделать невооруженным глазом или с помощью микроскопа или фотографического процесса с инфракрасным светом, благодаря которому определяется разница в толщине металлического покрытия.
Для более точного контроля качества поверхности, используется метод прогона иглы по всей длине поверхности. Как только игла натыкается на препятствие, этот шаг сразу же записывается. Но при таком способе тестирования игла может механически повредить поверхность. Производители зеркал пришли к единому мнению: нужно использовать лазер. Лазер будет использоваться для бесконтактного тестирования поверхности, по принципу как СD диск проигрывается в музыкальном центре. Вдобавок к таким механическим тестам существуют тесты на восприимчивость к окружающей среде. Например, зеркала для машин проверяют в условиях экстремального холода и жары, проверяя, как они поведут себя в различных погодных условиях, тогда как зеркала для ванных комнат тестируют на водостойкость.
Будущее
Так как производство стекла усовершенствуется, зеркала находят применения во многих отраслях искусства и архитектуры. Более прочные и светлые зеркала наиболее привлекательны для дизайнеров. Некоторые технологии производства односторонних зеркал позволяют изготавливать окна с внешней зеркально стороной, тогда как внутренняя сторона остается прозрачной. Это придает интересный и необычный вид зданиям. Мало того, делает систему кондиционирования здания более эффективной, так как зеркало отталкивает жару в летний период. Такой вид окон стал наиболее популярен в офисных строениях.
j-mirror.ru
Из чего состоит зеркало: технология производства зеркал.
Человека всегда интересовало собственное отражение. Ещё в древности люди с интересом изучали свою внешность, рассматривая отражение в воде. По прошествии времени изобрели такой незаменимый предмет, как зеркало. Отражение в первых подобных изделиях было не очень ясным, ведь они представляли собой полированные пластинки, которые были сделаны из бронзы, серебра или меди. На руинах древних городов находят эти предметы из платины или олова, богато украшенные драгоценностями.
Технология производства зеркал
Содержание статьи
Когда люди научились делать стекло, изменилась и технология изготовления зеркал. В Риме, например, под разноцветное стекло подкладывали металлические пластинки. С XIII века научились заливать стеклянную пластинку расплавленным оловом. При таком способе изображение было сильно искажено, но всё же он просуществовал до XVI века.
СПРАВКА! Первыми производителями зеркал в Средние века были стеклодувы. Именно они придумали технологии, подобные современным.
В XVI веке изобрели сплав – амальгаму. Ей покрывали изнанку стеклянного листа, что затемняло поверхность и позволяло увидеть тёмное отражение. Вещество было сильно ядовито, что делало работу по производству зеркал опасной. Рабочие, занятые в производстве, часто умирали, а сами предметы служили недолго. Через какое-то время от этой технологии пришлось отказаться.
СПРАВКА! Амальгама – ядовитый сплав олова и ртути. Даже пары, выделяемые им смертельны для человека.
Только в XIX веке было придумано безопасное покрытие. Из чего оно состояло? На пластину стекла наносили слой серебра, который закрепляли краской. Этот способ позволял получить светлое и чёткое отражение.
Устаревшая технология
Есть несколько видов производства зеркал. По старой технологии зеркала делали таким образом:
- стекло нарезали на части нужного размера;
- получившиеся заготовки полировали и шлифовали, придавая абсолютную гладкость;
- наносили технологические отверстия для крепления ручек и рамок;
- заготовки промывали специальным средством, чтобы удалить даже стойкую грязь;
- напыляли слой алюминия или титана — иногда применяли и другие металлы;
- сверху наносили слой лаковой краски.
Такой способ мало чем отличается от придуманного в XIX веке. Производство малозатратно, но позволяет производить изделия только небольших размеров.
Современное производство зеркал
Как и древнее, современное зеркало состоит из стекла, покрытого снизу отражающим слоем. Для производства стекла используют:
- соду;
- доломит;
- кварцевый песок;
- уголь;
- полевой шпат;
- осколки стекла, полученного от вторсырья.
Все компоненты очищаются, расплавляются и смешиваются в нужной пропорции. Готовую стеклянную пластину тщательно полируют, чтобы устранить искажения. Когда стеклянная пластина готова, переходят к производству зеркала:
- на станках неотшлифованными алмазами производится резка;
- затем следует фацетировка т. е. правильная обработка края стекла — фацет бывает крутой и широкий, в зависимости от желаемого вида зеркала;
- стекло хорошо моется и обезжиривается — для этого его обрабатывают паром, чистят щётками с порошком мела, сушат, потом протирают спиртом или бензином;
- чтобы получить отражающий слой, наносят серебряное покрытие;
- новейшим способом является нанесение алюминия в вакууме под давлением — в вакууме, куда помещается стекло, испаряется алюминий и оседает на него ровным слоем, поэтому покрытие получается более стойким и качественным;
- затем на слой металла наносят покрытие, оберегающее его — обычно это плёнка из меди;
- слой меди покрывают непрозрачным слоем лаковой краски;
- готовое изделие заключают в оправу или рамку.
СПРАВКА! Если слой серебра нанесён два или три раза, это увеличивает качество изделия, но значительно повышает его стоимость.
Для обычных зеркал используют алюминий, а для более дорогих мебельных – серебро.
setafi.com
Как открыть производство зеркал
В России при правильной постановке бизнес-процесса изготовление зеркал может быть довольно прибыльным предприятием.
Спрос на зеркала с каждым годом только увеличивается. А зеркало на заказ, сейчас, довольно популярно. Зеркала применяются не только в повседневном обиходе, но еще и в промышленности. Если зеркала продавать оптовым покупателям, а не только розничным потребителям, то это совсем другой уровень в бизнесе.
При монтаже цеха по изготовлению зеркал требуются небольшие вложения, которые может позволить себе начинающий предприниматель.
Материалы для зеркала
В основном используют стекло в листах, которое бывает отполированное и неотполированное.
При изготовлении стекла потребуется:
— сода;
— известняк;
— песок;
— железо с малым количеством соли – оно дает зеленый оттенок.
Такой состав стекла дает гарантию качества.
При изготовлении зеркал на заказ сырьевой материал можно получать двумя методами – просто закупать или наладить производство в цеху. Это понизит первоначальную стоимость продукции на выходе, но при этом потребуются значительные затраты при монтаже.
Требуемый материал для создания зеркала:
— очищенная вода;
— азотная кислота;
— щелочь;
— йод;
— олово;
— азотнокислое серебро;
— нашатырь.
В изготовлении зеркал не применяются ингредиенты, которые дорого стоят. Все, что требуется, можно покупать у производителей большими партиями.
Изготовление зеркал
Технологический процесс изготовления разбивается на этапы:
— раскроить листовое стекло;
— разрезать его;
— обработать края;
— очистить;
— пройти металлизацию;
— если нужно, сделать оправу.
Раскрой стекла происходит при помощи нешлифованных алмазов, у которых множество граней. Это происходит на специализированных станках. Следующий этап – полировка и шлифовка граней, который называют фацет. Делается для безопасности во время транспортировки и для эстетического вида.
Края зеркала обрабатывается в три этапа:
— рубая фацетировка;
— отшлифовка;
— полировка дисками из войлока.
За полировкой происходит процедура очищения от пыли и обезжиривания поверхности для следующей металлизации. Очищение делается на полуавтоматических конвейерах. Стекло ставится вертикально между валиками из резины. Во время движения стекло подвергают воздействию пара, натирают губками порошком из мела, омывают водой и сушат под потоком горячего воздуха. Обезжиривают стекло спиртом или иным растворителем.
Процесс металлизации
Металлизацию можно проводить 2 способами:
— при помощи алюминирования;
— серебрением.
При серебрении накладывается пласт серебра – этот процесс длится 10 минут. Если требуется получить слой плотнее, то процесс нужно повторять до нужного результата, но не стоит забывать, что это отражается на стоимости продукции.
Серебрение можно делать двумя методами: погружать стекло в раствор полностью или лицом вверх.
Технология серебрения имеет несколько стадий:
— необходимо отполировать, помыть и подготовить стекло;
— погрузить его в ванну, где находится жидкость с серебрением;
— наложить защитную изоляцию.
В производстве зеркал на заказ, при алюминировании используют температурное выпаривание в вакууме с повышенным давлением и жгут проволочки вольфрама. Плоскость стекла необходимо подготовить более тщательным способом. После обезжиривания используют электрический разряд, а потом стекло определяют в камеру, где находится вакуум. При повышении температуры молекулы алюминия выпариваются и остаются на стекле тоненькой пленкой. Процесс занимает 20 минут. Изделие нужно проверить на брак.
Зеркала такой обработки стоят дешевле, но при этом обладают хорошими свойствами – не боятся влажности и химических веществ. Недостаток заключается в худшем качестве отражения.
Оборудование:
— стол для резки стекла – 40000 р.;
— сушка для обработанного стекла – в основном изготавливают сами;
— сосуд, где будет происходить серебрение (изготавливается из любого материала кроме металла) – 40000 р.;
— шлифовка – 10000 р.;
— весы – 1000 р.
Площадь помещения под производство должна быть не менее 15 м/кв.
Вложения на первом этапе складываются:
— аренда – 20000 в месяц;
— закупка реагентов;
— стекло с привозом;
— техническое оснащение;
— заработная плата.
Для первоначального вложения потребуется не больше 300 000 р. Эту сумму можно уменьшить, если сделать своими руками стол и сушилку.
Следует помнить, что некоторые затраты будут ежемесячными, а также прибавятся и непредвиденные. Рассчитывайте на это, когда обдумываете свой бизнес-план.
Прибыль зависит от объемов сбыта. Стоимость товара на рынке намного выше его себестоимости. С 1 м/кв. можно получать до 2000 р. прибыли. Цех небольшого размера может изготавливать 25 м/кв. за смену. Около часа потребуется для нанесения защитного слоя, в течение ночи изделия будут сохнуть. Если сбыт будет хорошо налажен, то окупить все вложения можно через 3-6 месяцев.
enciklopediya-tehniki.ru
Технология производства зеркал | Бизнес Промышленность
История изготовления зеркал насчитывает далеко не одно столетие, и первая технология производства зеркал основывалась на нанесении тонкого слоя ртути, золота, серебра или олова на тыльную сторону тонкой стеклянной пластины.
Современную историю производства зеркал отсчитывают с тринадцатого века, когда была освоена первая кустарная технология изготовления зеркал.
Современные зеркала представляют собой стекло, покрытое отражающим слоем, который защищен слоем лака или краски. Это всегда отшлифованное стекло высокого качества, не имеющее каких-либо изъянов.
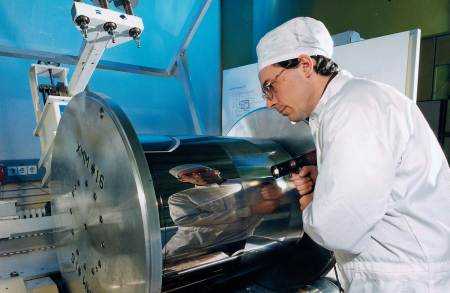
Технология изготовления зеркал – основные этапы
Основная технология производства зеркал, широко используемая сегодня, включает в себя несколько основных этапов. На первом этапе листовое стекло при помощи специального оборудования режут на части определенных заданных размеров, ориентируясь на габариты будущего зеркала.
После этого с поверхности стекла удаляются продукты коррозии и загрязнения, и выполняется декоративная обработка краев. Обычно, ширина боковой грани зеркала располагается в пределах от 5 до 30 мм, а угол его наклона по отношению к лицевой части стекла варьируется в пределах от 5 до 25 градусов.
Далее начинается самый ответственный этап изготовления. На подготовленную поверхность листового стекла наносят центры осаждения алюминия или серебра. После чего выполняется само нанесение тонкого отражающего слоя на заднюю поверхность будущего зеркала.
В данном случае серебро и алюминий выступают в качестве наилучших отражателей, как в ультрафиолетовом, так и в инфракрасном диапазоне.
Следующий этап заключается в нанесении на алюминиевый или серебряный слой медной пленки, необходимой для защиты отражающего слоя от разнообразного электрохимического воздействия. Медную пленку в свою очередь покрывают специальным лакокрасочным материалом, который предупреждает ее механические повреждения.
И наконец, на заключительном этапе, уже после того, как зеркало полностью готово, его окантовывают пластмассой, металлом или любыми другими материалами и оформляют в папки.
Альтернативный способ производства зеркал
Альтернативная технология производства зеркал, так называемая, «металлизация стекла», основывается на катодном распылении и термичном испарении алюминия. Все эти процессы происходят в вакууме под большим давлением.
При этом толщина алюминиевой пленки составляет всего около 0,10 – 0,15 мкм. Зеркала, получаемые таким способом, характеризуются повышенной химической стойкостью и применяются для наружного отражения.
Социальные закладки
www.business-equipment.ru
ИСТОРИЯ СОЗДАНИЯ И ТЕХНОЛОГИЯ ПРОИЗВОДСТВА
Зеркало — настолько распространенный предмет нашего обихода, что сложно представить себе СЕБЯ без него. Каких только видов этого предмета быта не существует: маленькие и большие, круглые и квадратные, напольные, настольные и настенные, дома и в машине, на улице и в магазине… Зеркало — это источник информации.
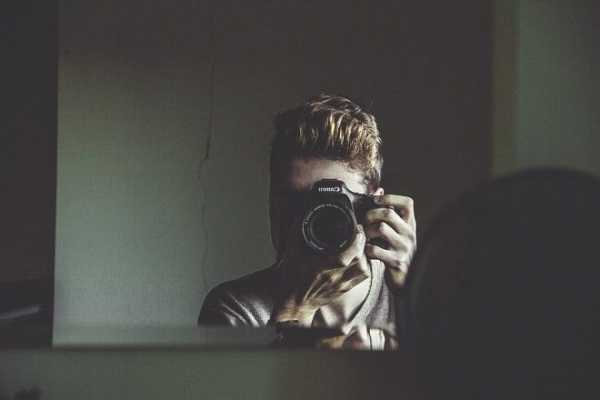
Когда-то очень давно единственным источником отражения служили водоемы или случайные предметы с отражающей поверхностью.
Позже люди стали пользоваться начищенными до блеска медными, бронзовыми или другими металлическими пластинами.
В настоящее время зеркало производят:
из обычного стекла;
на основе серебра.
Первая технология изготовления зеркала представляет собой очищенное стекло, которое покрыто отражающим слоем. Для этого берут полированное стекло нужной формы, обрабатывают края, отмывают растворами до максимальной чистоты. Затем делают напыление алюминия, сплавов железа с титаном, хромом и другими металлами. После чего наносится специальное покрытие. Такой метод считается устаревшим и является очень дешевым, но изготовление таких зеркал возможно только при небольших размерах.
Применение серебряного раствора заключается в том, что на стекло наносится медный слой и клейкие химикаты, затем дважды лакируется. Качество изделия в данном случае будет выше.
Иногда стекло привозят на фабрику по изготовлению зеркал уже в готовом виде, но чаще всего его производят здесь же. Для этого все необходимые для его производства компоненты:
● доломит,
● сода,
● кварцевый песок,
● полевой шпат,
● уголь,
● битое стекло
перемалывают и тщательно перемешивают до получения однородного порошка стекольной шихты. Затем перемещают в печь для плавления (при температуре свыше 1500°С) и превращения в однородную жидкую массу. Из печи выходит полотно (3-4 метра ширина и около 4 мм толщина), которое направляется на этап нарезки. Охлажденное стекло нарезается и проверяется на наличие брака.
Затем материал отправляется на этап нанесения металла, а бракованный — на переработку. При изготовлении зеркала важна высокая степень очистки стекла, на нем не должно быть примесей, поскольку любые сторонние частицы влияют на качество отражающей поверхности.
Для этого стекло полируют, моют, сушат, наносят химические составы. Процесс окисления альдегидов через контакт с аммиачными соединениями серебра окисление альдегидов, аммиачным раствором оксида серебра длится 20 секунд. После окончания химической реакции раствор высыхает, и результате на стекле появляется отражающая поверхность.
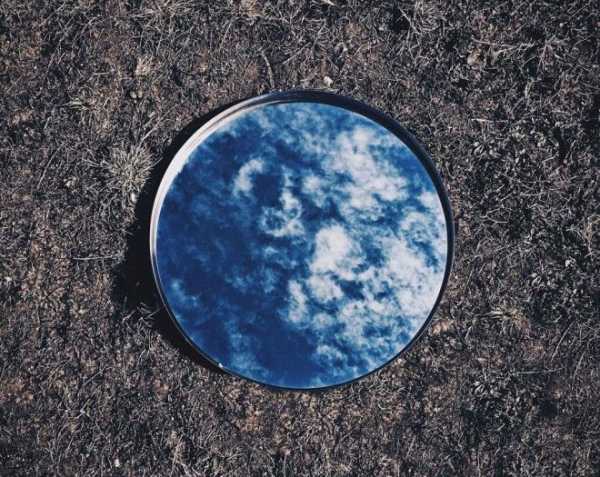
Готовое изделие проходит тщательную проверку на наличие сколов, трещин, царапин, любых дефектов. После чего упаковывается и направляется к заказчику.
Кстати:
Современная история зеркал начинается с XIII века (с 1240 года), когда в Европе научились выдувать сосуды из стекла. А само изобретение настоящего стеклянного зеркала датируется 1279 годом, когда итальянский монах-францисканец Джон Пекам в ходе экспериментов со стеклом и металлами покрыл кусок прозрачного стекла тонким слоем жидкого олова и в результате чего получилось изделие, приближенное к современному зеркалу.
prikolno.cc
Технология изготовления зеркал | Компания «Зерцало»
Функции светоотражающих полотен в интерьере разнообразны: визуальное расширение пространства, создание оптических иллюзий, украшение комнаты и т. д. На данный момент существует обширный выбор этих аксессуаров.
Наша компания не занимается производством зеркал. Ниже представлен материал для ознакомления.
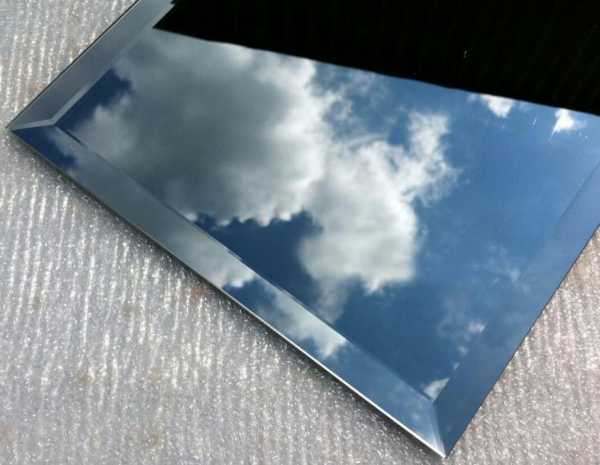
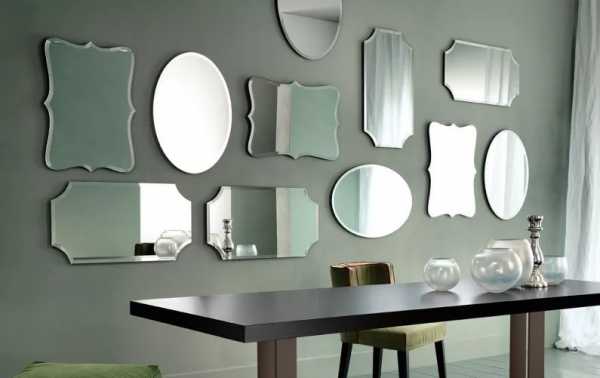
Процесс производства светоотражающих полотен включает следующие этапы:
- Резка стекол. Листовому стеклу придают нужную форму с помощью ручных инструментов, гидроабразивных установок или лазера. Возможно создание типичных прямоугольных элементов или более сложных фигурных решений. Далее специалисты обрабатывают кромки — это исключает распространение трещин и предотвращает травмирование о них. В зависимости от желания заказчика края могут быть прямыми, трапециевидными, скругленными, скошенными, глянцевыми или матовыми.
- Подготовка поверхностей. Стекла обезжириваются, обрабатываются абразивными частицами для достижения идеальной гладкости. Далее заготовки моются горячей дистиллированной водой, не оставляющей пятен и разводов.
- Нанесение напыления. Сначала создаются центры осаждения: на заготовку наносятся частицы олова, позже вступающие в реакцию с отражающим слоем. В современных зеркалах используется серебро или алюминий (эти металлы обладают высокой отражающей способностью). Толщина слоя — 0,15–0,3 мкм. Далее полотна проходят проверку: наблюдение в темном помещении позволяет выявить малейшие участки, которые не отражают свет. В некоторых случаях используется альтернативная технология — это катодное распыление и термическое испарение алюминия.
- Нанесение защитного слоя. Серебряное покрытие неустойчиво, он легко разрушается под влиянием механических, термических, электрохимических воздействий. Для защиты поверхности используется тончайшая медная пленка. Когда покрытие высыхает, на заготовку наносится 1–2 слоя краски. Далее проводится проверка полотен на наличие малейших точечных пузырьков.
- Декоративная отделка. Сегодня доступно немало способов такой обработки — окраска, нанесение пескоструйного рисунка, искусственное состаривание. В некоторых случаях требуется сверление отверстий для установки подсветки. Готовое полотно крепится к пластиковой, металлической или иной основе.
Дополнительная информация по теме:
Закажите изготовление изделий из зеркал специалистам компании «Зерцало»!
zertsalo.ru
Основные этапы изготовления зеркал
Добавил(а): Оксана 4 апреля
На первый взгляд зеркало может показаться довольно незамысловатым изделием. В нем нет никакой электроники — лишь полотно да рама. Однако зеркальное производство было и остается до сих пор сложной, высокотехнологичной отраслью промышленности, даже если речь идет о продукции, предназначенной для домашнего использования.
От заготовки к готовому изделию
Прежде всего, следует иметь в виду, что стекло, используемое для изготовления зеркал, должно отвечать высочайшим стандартам качества. Причем речь идет о наличии не только видимых дефектов, к числу которых относятся свили, пузырьки воздуха, волнистость и т.д. Специалисты отдельно оценивают прозрачность стекла, его отражающую способность и другие характеристики, которые можно проверить только с помощью специального оборудования.
Зачастую стекла дополнительно подвергают полировке, позволяющей сделать их поверхность по-настоящему гладкой. Не имеет значения, что неровности могут быть незаметны человеческим глазом. Они приводят к рассеиванию света, что негативно сказывается на качестве отражения. Кроме того, проверке подлежит и цвет заготовок (присутствие явно выраженных оттенков считается нежелательным).
Входным контролем дело никогда не ограничивается. Купить зеркала можно будет лишь после того, как всю партию проверят на наличие дефектов. Такой подход обусловлено хрупкостью стекла (из-за этой особенности малейшее механическое воздействие оборачивается сколом или царапиной).
Другой важный момент, подлежащий контролю, связан с качеством отражающего слоя. Его нанесение по праву считается важнейшим этапом в процессе изготовления зеркала. Для этого применяются сегодня два основных способа: серебрение и катодное напыление алюминия. Цель каждого из них — создать однородный, достаточно толстый отражающий слой.
Завершающая стадия
Вставка готового зеркального полотна в раму и его закрепление — заключительный этап, предшествующий выходному контролю. Однако нельзя забывать о такой операциих, как отделка. Еще до нанесения зеркального слоя кромки заготовки нередко полируют для того, чтобы сделать их более гладкими.
Кроме того, сегодня все чаще украшают саму поверхность стекла, используя для этого разнообразные методы: пескоструйную обработку, фьюзинг, термопечать и другие. С их помощью удается заметно улучшить эстетические характеристики готового изделия.
Оцените статью: Поделитесь с друзьями!prorab.guru