Автоклав для газобетона своими руками – Оборудование для производства газобетона и технология его изготовления
Инструмент для газобетона — особенности автоклавного, безавтоклавного производства.Тонкости технологии
Можно смело утверждать, что газобетон в настоящее время находится на пике своей популярности. Материал легкий и удобный в обработке, благодаря чему технология возведения доступна не только профессионалам, но и любителям. Хотя есть один нюанс, для быстрого и главное качественного строительства требуется специальный инструмент для работы с газобетоном.
Фото блоков из газобетона.
Прежде чем говорить об инструменте, разберемся, что такое газобетон. Этот материал появился на рынке сравнительно недавно и представляет собой один из ячеистых видов бетона.
В основе его лежит цементно-песчаная смесь с добавлением извести. В качестве разрыхлителя и пенообразователя выступает алюминиевая пудра. В результате получается легкий и достаточно прочный блок.
Деревянный рубанок для газобетона.
Инструмент для монтажа
Этот строительный материал укладывается на специальный клеевой раствор, он легко обрабатывается своими руками и, хотя для этого можно использовать традиционные инструменты, но имея специализированный инвентарь, скорость выполнения работ увеличивается в разы (читайте также статью «Смета на дом из газобетона – особенности проведения расчетных работ»).
Стандартный набор инструмента
Набор ковшей.
- Чтобы кладка была равномерной клеящий состав должен наноситься однородным тонким слоем. Для этого применяется ковш-кельма. Этот инструмент делается в виде емкости с ручкой, одинаковая толщина нанесения состава обеспечивается за счет зубчатого среза, с высотой зуба 3 – 5 мм. В зависимости от ширины блока выпускается несколько видов ковшей.
- Резать блоки можно при помощи обычной ножовки, но ножовка по дереву очень быстро садится, поэтому для таких работ существует специальная ножовка, зубья которой имеют победитовые напайки. Серийная модель рассчитана на резку 25м³ материала. Также выпускаются подобные режущие цепи для электропил. Теоретически блок можно разрезать болгаркой с алмазным диском, но пыли будет много.
- Блоки объемные и для обеспечения точной разметки и ровного разреза применяется специальный угольник. Можно конечно использовать стусло, но профессионалы, чаще всего, обходятся только угольником.
Резка блока ножовкой при помощи угольника.
- Так как толщина клеевого состава минимальна, верхний срез кладки не должен иметь перепадов по высоте. Поэтому перед укладкой следующего ряда поверхность должна быть выровнена, для этого используется терка для газобетона, ее еще называют рубанок для газобетона.
Инструмент похож на большой штукатурный полутерок. Снизу, на плоскости он оборудован металлическими режущими элементами.
Схема гибкой связи.
- В работе обязательно понадобиться штроборез, это режущий инструмент, который предназначен для вырезания в блоках канавок под гибкие связи для газобетона, закладку арматуры или монтаж электропроводки. При малых объемах можно обойтись ручной версией, профессионалы предпочитают использовать электрический штроборез с двумя алмазными дисками.
Каретка для клея.
- Для нанесения больших объемов клея на длинные прямые участки стен может использоваться каретка для газобетона. Это приспособление можно назвать усовершенствованной версией кельмы. Инструмент относят к узкопрофессиональным и используют на больших стройках.
- Также тяжело будет обойтись без резиновой киянки. Это не что иное, как резиновый молоток, с его помощью легче производить точную укладку блоков в ряду, не опасаясь их повредить.
Ручной штроборез.
Совет: профессиональным ковшом или кареткой, конечно, работать удобнее, но цена у них выше. Поэтому зачастую используется кельма для газобетона своими руками сделанная. Точнее работают набором из обычной строительной кельмы и широкого зубчатого шпателя.
На видео в этой статье показана работа кельмой сделанной своими руками.
Электрический штроборез.
Тонкости технологии
Разговор об инструменте будет неполным, если не упомянуть о производстве. Общая технология производства материала не отличается большой сложностью.
Блоки можно делать как в заводских условиях на специальном оборудовании, так и дома своими руками. В профессиональном производстве для повышения качества используется автоклав, а в домашних условиях обходятся и без него.
Ячеистый бетон.
Автоклавное производство
Если описывать технологию в общих чертах, то изначально компоненты закладываются в смеситель для газобетона и тщательно перемешиваются. После этого смесь разливается в формы, где происходит первый этап набора прочности.
Далее сырые, но уже сформированные брикеты загружаются в автоклав. Автоклав представляет собой большую, герметично закрывающуюся камеру, в которой под давлением и при высокой температуре происходит закаливание газобетона.
Промышленный автоклав.
После закрытия крышки, внутри агрегата создается давление в 0,5бар. Далее, постепенно в течение 2 часов давление доводится до уровня в 12бар, плюс температура повышается до 190ºС. Влага, из массива выпаривается и материал набирает проектную прочность.
Процесс понижения температуры и нормализации давления также длится около 2 часов. Блоки в среднем набирают проектную прочность в течение 12часов, это с учетом включения и выключения агрегата.
Но для придания материалу товарного вида еще необходимо его разрезать на стандартные блоки согласно ГОСТ. На производстве для этого используется резательный комплекс для газобетона.
Это отдельный станок, который согласно заданным параметрам разрезает затвердевший массив. После порезки, блоки можно использовать.
Резательный комплекс.
На видео в этой статье показано как работает резательный комплекс для газобетона.
Безавтоклавное производство
Общая технология производства в домашних условиях напоминает вышеописанную. Но в виду того, что автоклав для газобетона своими руками изготовить практически невозможно, набор прочности происходит в естественных условиях. Конечно, качество таких блоков будет существенно ниже, но для домашнего, небольшого строительства вполне достаточно.
Формы для отливки.
Дорогостоящий смеситель для газобетона, при этом, заменяется стандартной бетономешалкой. Формы можно изготовить самостоятельно, но мы советуем приобрести готовый заводской вариант. Цена у таких форм доступная, плюс четко выдержаны все размеры.
Профессиональный смеситель.
Совет: не пытайтесь перемешать раствор собственноручно. От уровня смешивания напрямую зависит качество и по опыту можно сказать, что вручную хорошо размешать невозможно.
При изготовлении своими руками, резательный комплекс для газобетона заменяется обычной стальной струной. После загрузки раствора в формы и первичного набора прочности, натянутой струной убираются излишки.
На видео в этой статье показаны некоторые приемы работы с газобетоном.
Вывод
Мы перечислили лишь основные инструменты, без которых обойтись трудно. Но кроме них используется еще ряд вспомогательных, так например, для монтажа розеток и выключателей используются круглые коронки на электродрель из тугоплавких металлов, плюс на профессиональном производстве применяется множество дополнительных агрегатов (см.также статью «Дома из газобетона: особенности материала, стоимость, порядок проведения строительства»).
Минимальный набор инструмента.
rusbetonplus.ru
Производство газобетона своими руками — Промышленные автоклавы для производственных линий. АВТОКЛАВ.com
Сегодня газобетон занимает лидирующее место по использованию строительных материалов в мире. Все благодаря положительным характеристикам газосиликата, которые во многом превосходят кирпич, обыкновенный бетон и прочие стройматериалы.
Характеристика газоблоков:
- малый удельный вес;
- высокая прочность;
- морозостойкость;
- огнеупорность;
- относится к экологически чистым материалам;
- требует малых вложений при изготовлении;
- может производиться в домашних условиях;
- требует минимальных компонентов для производства;
- имеет большой спрос.
Впрочем, газобетон всегда будет востребован, потому как дешевые и качественные материалы пользуются успехом даже во время экономического кризиса.
Производство газобетона своими руками – технология
Производство газобетона может осуществляться, как в промышленных зонах, так и в домашних условиях. В первом случае используется специализированное оборудование, которое увеличивает объемы конечного продукта и ускоряет весь технологический процесс.
С другой стороны, при наличии свободного гаража или склада производство можно наладить без задействования специальных установок. Сам процесс включает в себя несколько этапов:
- Подготовка и дозирование начальных компонентов. К таким веществам относят воду, известь, кварцевый песок, цемент и водную суспензию алюминиевой пудры. Также подготавливают различные химические реактивы.
- Первые четыре вещества вливаются в скоростной смеситель или бетономешалку и смешиваются на протяжении 5 минут.
- Затем в полученный раствор вмешивается алюминиевая пудра. Она необходима для старта реакции, конечным продуктом которой является водород. Именно этот элемент делает блоки легкими и прочными.
- Следующий шаг – разлитие приготовленной суспензии по формам и термическая обработка в автоклаве. Данный агрегат наделяет бетон теми свойствами, о которых упоминалось выше.
- После термовоздействия блоки должны остыть, тогда они будут готовы к транспортировке.
В условиях домашнего производства используются те же аппараты, что и для промышленного с той лишь разницей, что они имеют небольшие габариты. Кроме того, многие устройства могут быть заменены на подручные средства. Единственное, на чем не желательно экономить – это пропарочная камера.
Домашнее производство имеет несколько достоинств, среди которых:
- домашнее производство позволяет изготавливать блоки различных типоразмеров. Ведь именно от размеров блока зависит его применение в конструктивных элементах. При желании можно изготавливать блоки любой геометрической формы на заказ покупателя, тогда ассортимент будет стремительно увеличиваться. Ну, а, как известно: довольный покупатель не останется в долгу;
- постоянный спрос на дешевый и качественный материал не даст бизнесу «сгореть». Кроме того, необходимое количество блоков всегда больше расчетного числа, так как есть риск погрешности вычислений и особенностей кладки. Это значит, что прибыль также будет выше.
Необходимые для затвердевания формы можно также сделать вручную. Один из вариантов их изготовления заключается в составлении из досок некого пенала с отсеками. При этом необходимо учитывать, что внутренняя часть древесины должна быть идеально гладкой, чтобы бетон принял правильную форму. Рекомендуется в качестве внутренних вставок использовать влагонепроницаемую фанеру, которая со временем не испортится от воздействия влаги. Сделайте несколько различных видов пеналов, интересным решением станут регулируемые задвижки, которые позволят самостоятельно изменять длину блоков.
www.xn--80aafb2bgt5a.com
гибкие связи, рубанок, автоклав, кельма
Можно смело утверждать, что газобетон в настоящее время находится на пике своей популярности. Материал легкий и удобный в обработке, благодаря чему технология возведения доступна не только профессионалам, но и любителям. Хотя есть один нюанс, для быстрого и главное качественного строительства требуется специальный инструмент для работы с газобетоном.
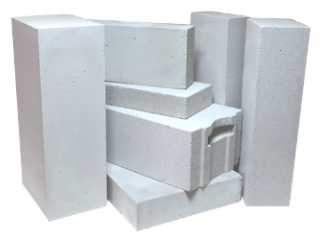
Фото блоков из газобетона.
Прежде чем говорить об инструменте, разберемся, что такое газобетон. Этот материал появился на рынке сравнительно недавно и представляет собой один из ячеистых видов бетона.
В основе его лежит цементно-песчаная смесь с добавлением извести. В качестве разрыхлителя и пенообразователя выступает алюминиевая пудра. В результате получается легкий и достаточно прочный блок.
Деревянный рубанок для газобетона.
Инструмент для монтажа
Этот строительный материал укладывается на специальный клеевой раствор, он легко обрабатывается своими руками и, хотя для этого можно использовать традиционные инструменты, но имея специализированный инвентарь, скорость выполнения работ увеличивается в разы (читайте также статью «Смета на дом из газобетона – особенности проведения расчетных работ»).
Стандартный набор инструмента
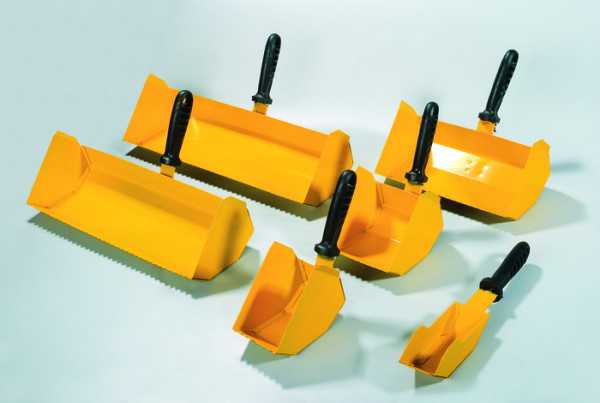
Набор ковшей.
- Чтобы кладка была равномерной клеящий состав должен наноситься однородным тонким слоем. Для этого применяется ковш-кельма. Этот инструмент делается в виде емкости с ручкой, одинаковая толщина нанесения состава обеспечивается за счет зубчатого среза, с высотой зуба 3 – 5 мм. В зависимости от ширины блока выпускается несколько видов ковшей.
- Резать блоки можно при помощи обычной ножовки, но ножовка по дереву очень быстро садится, поэтому для таких работ существует специальная ножовка, зубья которой имеют победитовые напайки. Серийная модель рассчитана на резку 25м³ материала. Также выпускаются подобные режущие цепи для электропил. Теоретически блок можно разрезать болгаркой с алмазным диском, но пыли будет много.
- Блоки объемные и для обеспечения точной разметки и ровного разреза применяется специальный угольник. Можно конечно использовать стусло, но профессионалы, чаще всего, обходятся только угольником.
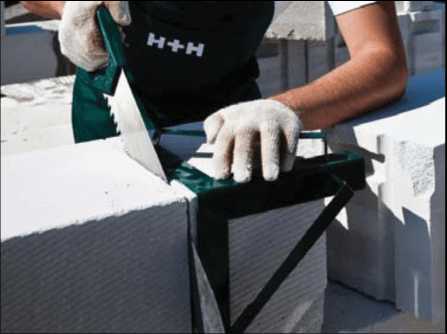
Резка блока ножовкой при помощи угольника.
- Так как толщина клеевого состава минимальна, верхний срез кладки не должен иметь перепадов по высоте. Поэтому перед укладкой следующего ряда поверхность должна быть выровнена, для этого используется терка для газобетона, ее еще называют рубанок для газобетона.
Инструмент похож на большой штукатурный полутерок. Снизу, на плоскости он оборудован металлическими режущими элементами.
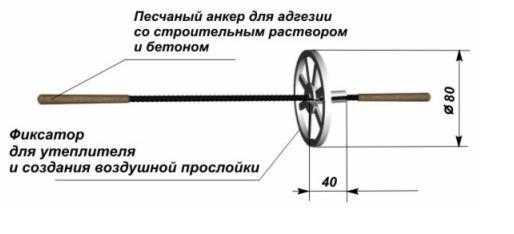
Схема гибкой связи.
- В работе обязательно понадобиться штроборез, это режущий инструмент, который предназначен для вырезания в блоках канавок под гибкие связи для газобетона, закладку арматуры или монтаж электропроводки. При малых объемах можно обойтись ручной версией, профессионалы предпочитают использовать электрический штроборез с двумя алмазными дисками.
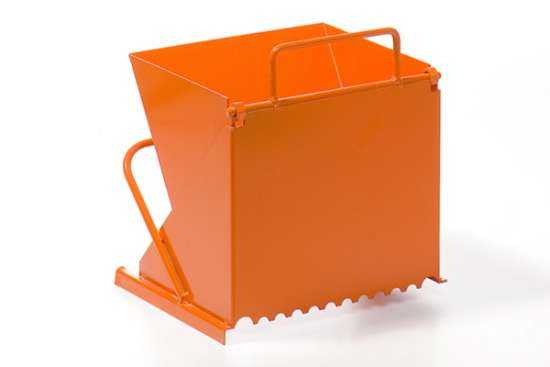
Каретка для клея.
- Для нанесения больших объемов клея на длинные прямые участки стен может использоваться каретка для газобетона. Это приспособление можно назвать усовершенствованной версией кельмы. Инструмент относят к узкопрофессиональным и используют на больших стройках.
- Также тяжело будет обойтись без резиновой киянки. Это не что иное, как резиновый молоток, с его помощью легче производить точную укладку блоков в ряду, не опасаясь их повредить.
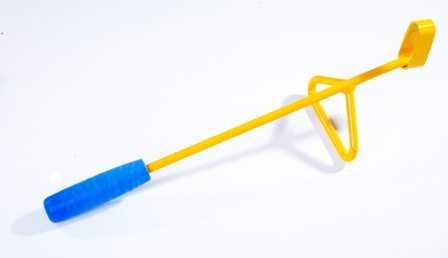
Ручной штроборез.
Совет: профессиональным ковшом или кареткой, конечно, работать удобнее, но цена у них выше. Поэтому зачастую используется кельма для газобетона своими руками сделанная. Точнее работают набором из обычной строительной кельмы и широкого зубчатого шпателя.
На видео в этой статье показана работа кельмой сделанной своими руками.
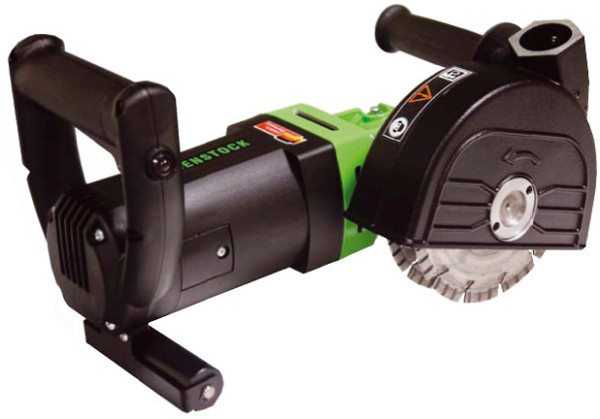
Электрический штроборез.
Тонкости технологии
Разговор об инструменте будет неполным, если не упомянуть о производстве. Общая технология производства материала не отличается большой сложностью.
Блоки можно делать как в заводских условиях на специальном оборудовании, так и дома своими руками. В профессиональном производстве для повышения качества используется автоклав, а в домашних условиях обходятся и без него.

Ячеистый бетон.
Автоклавное производство
Если описывать технологию в общих чертах, то изначально компоненты закладываются в смеситель для газобетона и тщательно перемешиваются. После этого смесь разливается в формы, где происходит первый этап набора прочности.
Далее сырые, но уже сформированные брикеты загружаются в автоклав. Автоклав представляет собой большую, герметично закрывающуюся камеру, в которой под давлением и при высокой температуре происходит закаливание газобетона.
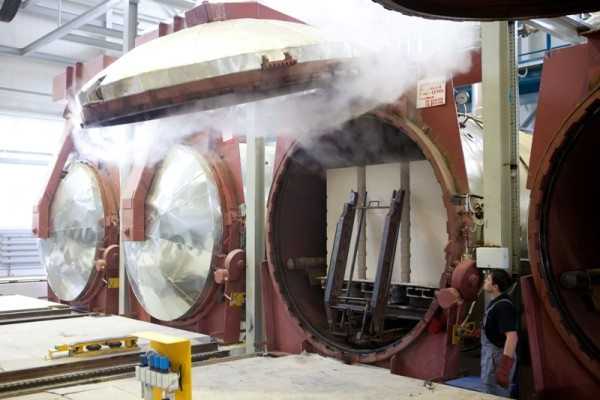
Промышленный автоклав.
После закрытия крышки, внутри агрегата создается давление в 0,5бар. Далее, постепенно в течение 2 часов давление доводится до уровня в 12бар, плюс температура повышается до 190ºС. Влага, из массива выпаривается и материал набирает проектную прочность.
Процесс понижения температуры и нормализации давления также длится около 2 часов. Блоки в среднем набирают проектную прочность в течение 12часов, это с учетом включения и выключения агрегата.
Но для придания материалу товарного вида еще необходимо его разрезать на стандартные блоки согласно ГОСТ. На производстве для этого используется резательный комплекс для газобетона.
Это отдельный станок, который согласно заданным параметрам разрезает затвердевший массив. После порезки, блоки можно использовать.
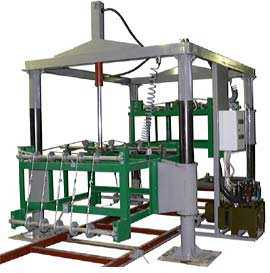
Резательный комплекс.
На видео в этой статье показано как работает резательный комплекс для газобетона.
Безавтоклавное производство
Общая технология производства в домашних условиях напоминает вышеописанную. Но в виду того, что автоклав для газобетона своими руками изготовить практически невозможно, набор прочности происходит в естественных условиях. Конечно, качество таких блоков будет существенно ниже, но для домашнего, небольшого строительства вполне достаточно.
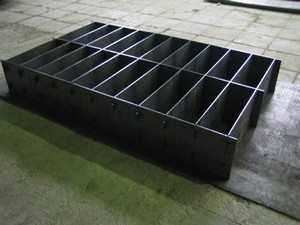
Формы для отливки.
Дорогостоящий смеситель для газобетона, при этом, заменяется стандартной бетономешалкой. Формы можно изготовить самостоятельно, но мы советуем приобрести готовый заводской вариант. Цена у таких форм доступная, плюс четко выдержаны все размеры.
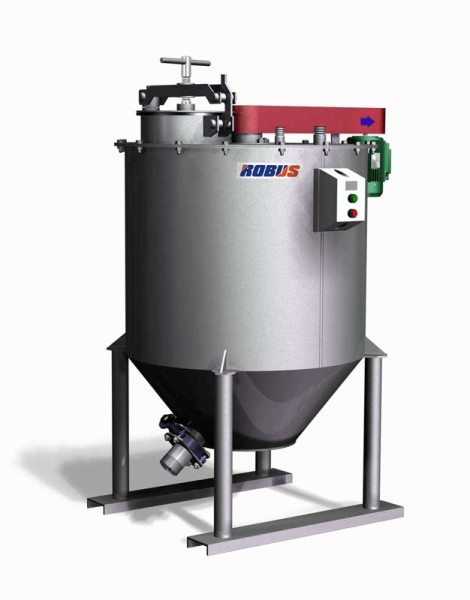
Профессиональный смеситель.
Совет: не пытайтесь перемешать раствор собственноручно. От уровня смешивания напрямую зависит качество и по опыту можно сказать, что вручную хорошо размешать невозможно.
При изготовлении своими руками, резательный комплекс для газобетона заменяется обычной стальной струной. После загрузки раствора в формы и первичного набора прочности, натянутой струной убираются излишки.
На видео в этой статье показаны некоторые приемы работы с газобетоном.
Вывод
Мы перечислили лишь основные инструменты, без которых обойтись трудно. Но кроме них используется еще ряд вспомогательных, так например, для монтажа розеток и выключателей используются круглые коронки на электродрель из тугоплавких металлов, плюс на профессиональном производстве применяется множество дополнительных агрегатов (см.также статью «Дома из газобетона: особенности материала, стоимость, порядок проведения строительства»).
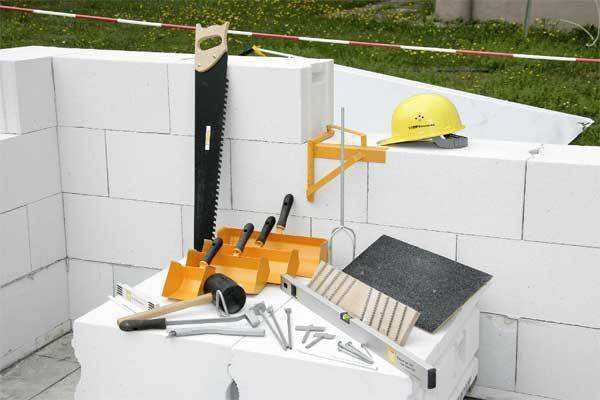
Минимальный набор инструмента.
masterabetona.ru
обзор типов линий и установок
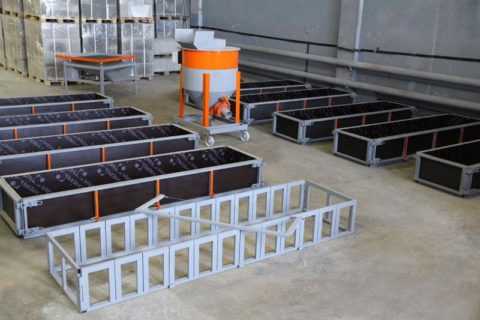
Производство блоков из газобетона
Еще не так давно, производство популярного материала в виде строительного камня было возможно лишь в условиях завода. Но с усовершенствованием технологий такая возможность появилась не только у мелких предпринимателей, но и у самих застройщиков.
На данный момент существует большое количество различного оборудования, предназначенного для изготовления данного представителя ячеистых бетонов. Комплекты отличаются между собой по ряду признаков, а в первую очередь ценовой категорией и объемом выпуска.
В данной статье мы будем рассматривать оборудование для производства газобетонных блоков разного типа, и проанализируем сам процесс изготовления изделий. А также сравним материал, произведенный в домашних и заводских условиях.
Содержание статьи
Общая технология производства газобетона
Предварительно, пожалуй, рассмотрим общий принцип технологического процесса. Ведь для полноценного обзора линий оборудования, нам нужно иметь представление о том, как именно изготавливается газобетонный блок.
Необходимое сырье
Для приготовления газобетонной смеси, понадобится наличие следующего сырья:
- Цемент марки не менее М400;
- Вода;
- Известь негашеная;
- Гипс;
- Песок кварцевый;
- Алюминиевая пудра.
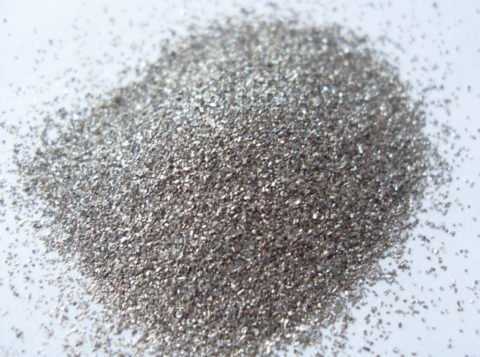
Алюминиевая пудра
Также не помешает добавить в раствор пластификатор. Основное его предназначение – повышение пластичности раствора, что предотвращает растрескивание изделий на стадии сушки и твердения.
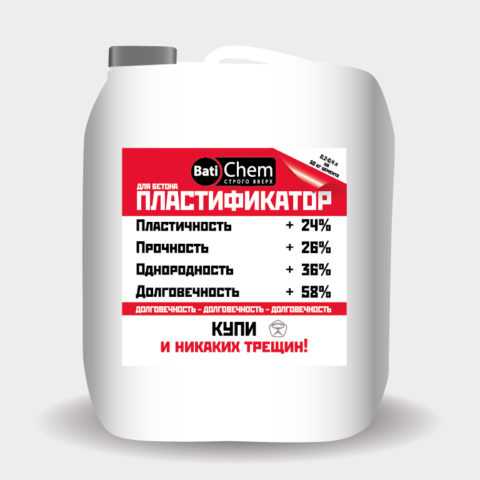
Пластификатор
Другие химические добавки также используются. Как правило, они добавляются с целью повышения качеств готовых изделий.
Пропорции сырья вместе с добавками
Обратите внимание! Вышеуказанный состав является классическим. Многие компоненты могут заменяться. В этом случае набор числовые значения свойств также будут варьироваться.
- Кремнеземистый компонент может быть представлен в виде: песка, золы и иных вторичных продуктов промышленности;
- Тип вяжущего также может быть разным: цементным, шлаковым, известковым, смешанным, зольным.
Примерное содержание пропорций – следующее:
- 50-60% — цемент;
- 20-40% — песок;
- 1-10% — известь;
- До 1% — вода.
На заметку! При желании повысить плотность изделий, следует увеличить количество цемента. В этом случае также изменится и масса готового материала, и коэффициент теплопроводности.
Пропорции в зависимости от желаемой плотности
Основные этапы
Краткая инструкция выглядит следующим образом:
- Первым делом взвешиваются компоненты и смешиваются в необходимых пропорциях. При изготовлении своими руками это делается вручную, в заводских условиях, как правило, в автоматическом режиме.
- Все ингредиенты попадают в смеситель, где и происходит смешивание.
- Следующим этапом станет формовка. Формы наполняются примерно на 1/3, так как при порообразовании смесь попросту может вытечь.
- Следом, после завершения процесса вспучивания, выжидается некоторое время до частичного застывания.
- Далее производят резку единого пласта или просто распалубку, если формы используются уже готовых типоразмеров.
- Последним этапом станет автоклавирование либо отправление блоков на сушку при неавтоклавном способе производства.
Обратите внимание! Ход процесса может несколько отличаться в зависимости от того, какое оборудование для изготовления газобетонных блоков используется. Однако в целом, общий принцип будет аналогичным.
Типы установок и линий
Теперь перейдём непосредственно к обзору типов оборудования.
Конвейерный тип
Оборудование для газобетона конвейерного типа отличается:
- Максимальной автоматизацией производства;
- Минимальным участием работников;
- Высокой стоимостью;
- Большими объемами производства;
- Полной комплектацией;
- И, как правило, наибольшей рентабельностью.
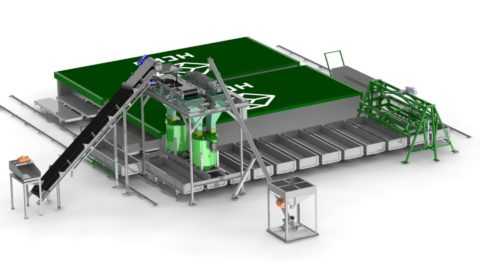
Большая конвейерная линия
Рассмотрим подробнее комплектацию и возможности такого газобетонного оборудования на примере линии популярного китайского производителя, являющегося дилером компании Премиум Кирпич Плюс.
В стандартный комплект входят:
- Емкости и бункеры для сырья;
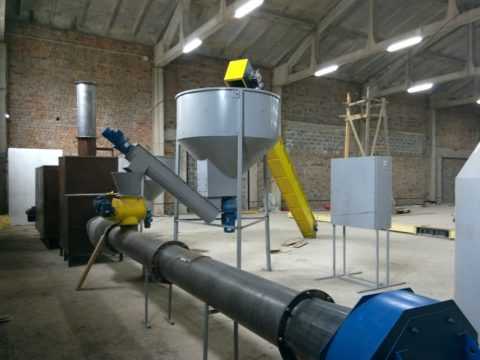
Бункер для сырья
- Ленточные конвейеры для транспортировки компонентов;
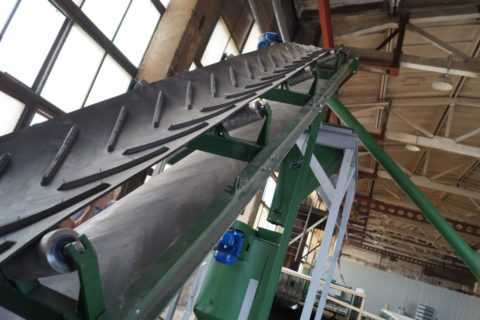
Ленточный конвейер
- Узел растворосмесительный;
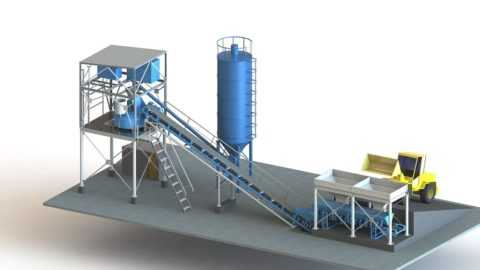
Узел бетоно-растворный
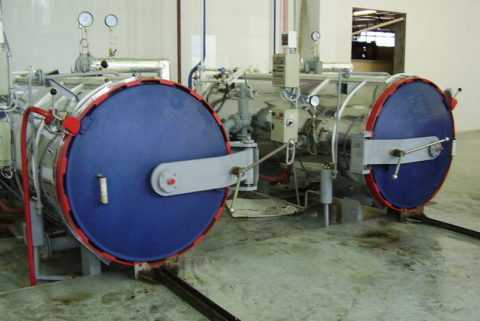
Автоклавы
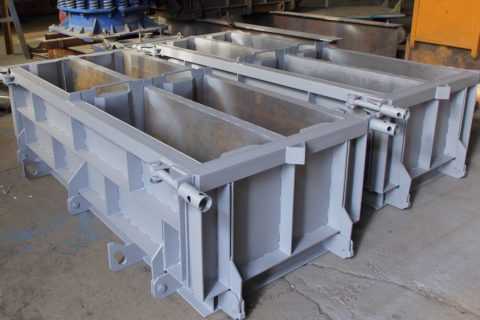
Сборная форма для блоков
- Резательный комплекс;
- Транспортер перемешивающий;
- Дробилки;
- Тележки;
- Узел для автоматического управления линией;
- Погрузчик вилочный.
Такое оборудование для производства стоит около 55 000 000. Согласитесь, сумма, не маленькая. Однако при этом, производительность составляет около 300 тысяч метров кубических в год. Площадь, необходимая для размещения такой линии должна быть около 4000 м2.
В качестве альтернативы, можно рассмотреть возможность приобретения конвейерной линии в бывшем употреблении. Это – своеобразный риск, однако стоимость ее значительно ниже.
Также стоит обратить внимание на мини линию конвейерного типа «Иннтех-100». Ее производительность значительно ниже и составляет 100 м3 в сутки. Цена ее – около 3 000 000.
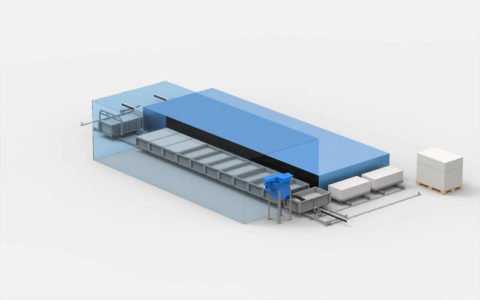
Мини конвейерная линия
Данная линия характеризуется неподвижным смесителем. Формы передвигаются по рельсовому транспортеру как тележка. Компоненты подаются и дозируются в автоматическом режиме. Резательный комплекс – механический.
Больше всего среди производителей ценятся линии известных немецких производителей оборудования. Они отличаются высокой продуктивностью, долговечность в использовании. С их помощью можно изготавливать блоки самого высокого качества.
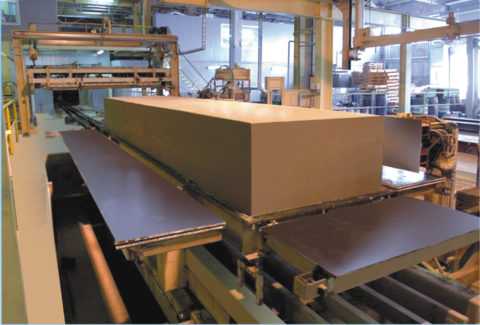
Немецкое оборудование для изготовления газоблока
Видео в этой статье продемонстрирует принцип работы оборудования для изготовления газобетона.
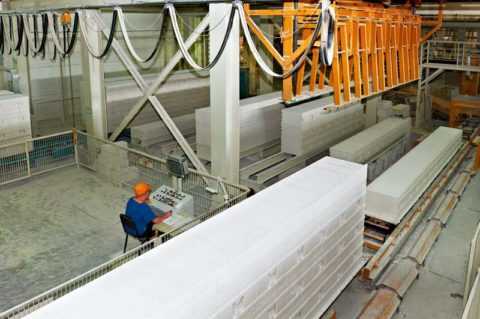
Производство газобетона Поревит
Стационарный тип
- Такой тип оборудования гораздо менее дорогостоящий. Однако и производительность ее гораздо ниже и составляет около 50 м3 в сутки.
- Как правило, в комплект таких линий входят дозаторы компонентов и ленточный транспортер, который и подает ингредиенты в смеситель.
- Однако полностью автоматизированным такой комплект назвать уже нельзя. Для полноценной работы требуется наличие как минимум нескольких человек.
- Необходимая квадратура для размещения производства и склада составляет около 500 м2.
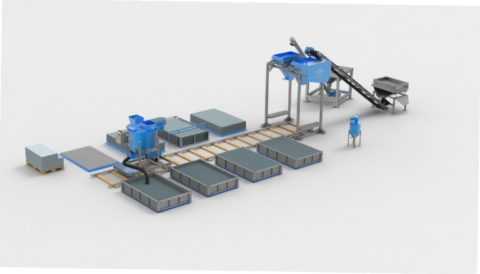
Линия стационарного типа для производства газобетонного блока
В качестве примера, кратко рассмотрим комплектацию и возможности линии АСМ-1МС.
- Производительность составляет около 60 м3;
- Для работы потребуется привлечение 3-4-х человек;
- Песок и цемент подаются в автоматизированном режиме.
Комплектация:
- Смеситель для вяжущего и иных компонентов;
- Конструкция для резки блочного массива с пилами;
- Формы и поддоны;
- Транспортер.
Мобильные установки и мини-линии
Такое оборудование для производства блоков газобетонных идеально подойдет для начинающих предпринимателей либо застройщиков, желающих изготовить изделия для собственных нужд.
При помощи мобильной установки можно произвести исключительно только газоблок неавтоклавного твердения. Ниже мы рассмотрим основные его отличия от основного конкурента.
Такой оборудование требует наличия сети в 220 Вт, в то время как другие типы машин требуют подключения к сети в 360 Вт. Объем производства составляет около 2-10 м3 в сутки.
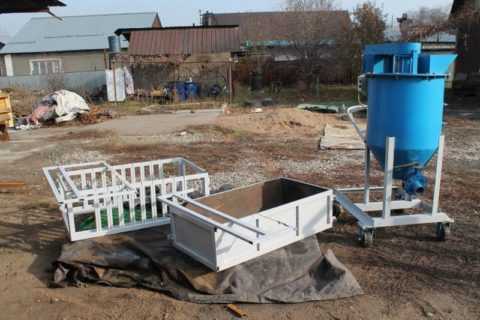
Установка мобильная для изготовления газобетона
Рассмотрим характеристики установки на примере комплекта Газобетон 500Б.
Установка газобетон 500 Б
- В комплект входит: смеситель, соединительные рукава и компрессор. Для производства необходимо участие нескольких человек.
- Практически весь процесс работ происходит с участие человека. В автоматическом режиме производится только смешивание.
- Дозирование также придется производить самостоятельно.
- Объем выпуска 3 м3 пористой смеси.
- Емкость для смешивания- 500 литров.
Мини-линии более производительны. С их помощью возможно изготовление вплоть до 25 м3 в сутки. Для мелких предпринимателей – отличный вариант начать свое дело.
Принцип их устройства – аналогичен мобильным установка, больше – мощность и объем смесителя.
Подробнее об автоклавировании
Теперь давайте более подробно поговорим об автоклавной обработке газоблока и разберемся, в чем заключаются основные различия между изделиями самостоятельного производства и материалом, выпущенным в условиях завода.
Что представляет собой автоклавная обработка?
При помощи автоклавной обработки удается повысить качества готовых изделий.
- Разрезанные на типоразмеры блоки помещаются в автоклав и обрабатываются под действием давления выше атмосферного водяным паром, при этом преобладает высокая температура.
- Обработка длится в течение 12-ти часов.
- По окончании обработки, блоки практически сразу можно использовать в строительстве, ведь марочной прочности они уже достигнут.
- Неавтоклав же набирает прочность в течение 4-х недель.
- При автоклавной обработке повышаются такие качества как: прочность, плотность, долговечность. Изделия становятся менее хрупкими
Стоит отметить, что изготовление блоков автоклавного твердения возможно только в заводских условиях.
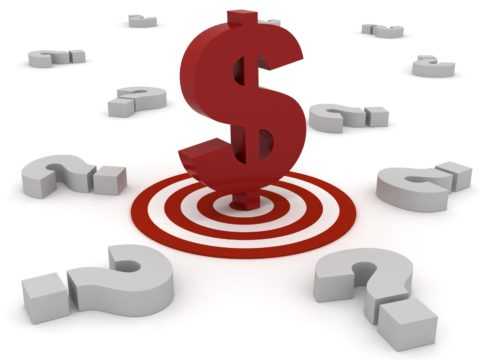
Процесс автоклавирования
Сравнение автоклавного и неавтоклавного газоблока
А теперь сравним свойства автоклавного газобетона и изделий, достигающий прочности естественным способом.
Характеристика | Сравнительный анализ |
![]() Сочетание плотности и теплопроводности | За счет специализированной обработки в автоклаве, изделия синтезного твердения отличаются лучшим сочетанием показателей плотности и теплопроводности. |
![]() Морозостойкость и долговечность | В соответствии с ГОСТ, требования к марке по морозостойкости к неавтоклавному блоку несколько ниже. Точные сроки долговечности обоих изделий не установлены опытным путем, в силу недостаточного времени существования материала на рынке строительных материалов. |
![]() Внешний вид и геометрия изделия | Автоклав имеет практически идеальную геометрию. Неавтоклавный блок, изготовленный в домашних условиях в данном отношении серьезно ему уступает. |
![]() Требования к оборудованию и сложность производства | Оборудование для газобетона автоклавного, в целом, отличается лишь наличием автоклавов. Технология производства – аналогична, порядок – тоже. |
![]() Хрупкость | Неавтоклавные блоки больше уязвимы к механическому воздействию, они более хрупкие. |
![]() Стоимость | Автоклавные изделия дороже примерно на 10%. |
![]() Усадка | Неавтоклавные блоки больше подвержены усадке. Показатель составляет до 1 мм/м2. |
В заключение
На современном рынке существует большое количество различных комплектов оборудования для производства газобетонных блоков, начиная от дорогостоящих крупномасштабных конвейерных линий и заканчивая бюджетными мобильными установками. Именно поэтому производство данного материала стало еще более популярным.
beton-house.com
Необходимое оборудование для производства газобетона
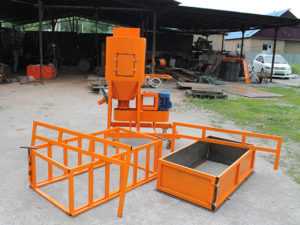
Мини-завод по производству неавтоклавного газобетона
Раньше изготовление газобетонных изделий было только на заводах. Теперь оборудование для производства газобетона может устанавливаться на небольших площадках или даже во дворе собственного дома.
В зависимости от количества необходимых блоков можно приобрести оборудование в виде мини-завода, поставить мобильную установку для получения блоков различной плотности.
Технология получения газобетона
Газобетон относится к разряду ячеистых бетонов. Состоит он из смеси нескольких компонентов:
- песок — 20-40%;
- известь — 1-5%;
- цемент — 50-70%;
- вода чистая — 0,25-0,8%;
- пудра алюминиевая — 0,04-0,09%.
Песок используется просеянный, его фракции не превышают 2,1 мм. Глины в нем должно содержаться не больше 7%. Цемент нужен качественный — марки М400 или М500. Алюминиевая пудра применяется в качестве газообразователя. В состав могут включаться еще некоторые компоненты: пластификаторы, ускорители твердения. Для изменения свойств газоблоков в смесь добавляют шлак, гипс или опилки. Этими добавками можно изменить плотность блоков. Ведь материал для изготовления фундамента должен быть прочнее, чем для перегородок. Теплоизоляционные блоки желательно делать более легкими и пористыми. Для этого можно полностью исключить из его состава песок.
Производство газобетонных изделий бывает автоклавное и неавтоклавное. Второй вариант производится гораздо проще, но имеет низкую прочность, недостаточную точность геометрических размеров. Автоклавные изделия бывают обычно более однородной структуры и низкой теплоемкости. Такие блоки используются в условиях России для возведения стен толщиной до 400 мм.
Изготовление блоков
Для производства газоблоков не требуются особо сложные установки. Нужно лишь точное выполнение технологических циклов. Изготовление может выполняться в следующем порядке:
- подготовка компонентов;
- введение газообразователя;
- укладка раствора в формы;
- разрезание блоков;
- созревание изделий;
- автоклавирование.
Все необходимые компоненты взвешиваются и всыпаются для перемешивания в смеситель. Минут через 10-15 к ним добавляют алюминиевую пудру, которая сразу же вступает в химическую реакцию с находящейся в смеси известью. В результате реакции смесь наполняется газом в виде пузырьков по всему объему. Это является сигналом к выкладке раствора в формы для газобетона или на специальный лоток толстым слоем. На лотке производят разрезку массы на блоки особыми пилами. Созревают полуготовые блоки в течение 10-18 часов. После этого блоки помещаются в автоклав. Это особая печь, состоящая из герметичной камеры с температурой 190°C. В ней материал обрабатывается горячим паром под высоким давлением. Далее готовый материал вынимается из автоклава и раскладывается для просушки.
Неавтоклавный строительный материал просушивается в течение 3-7 суток естественным образом. Далее блоки складируются в помещение для набора полной прочности. Происходит это обычно 30 суток. Только по истечении этого срока можно перевозить газобетон к потребителю, упаковав его в специальную термоусадочную пленку.
Оборудование для изготовления блоков
Для газобетонных блоков обычно комплектуется технологическая линия, состоящая из:
- смесителя;
- активатора;
- дозатора;
- режущего приспособления;
- автоклава;
- форм.
Все это оборудование бывает разной мощности. Она обычно варьируется в пределах 10-150 м³ в сутки. Самое дорогое в этом наборе — автоклав. От него и зависит стоимость готового продукта. В домашних условиях это производство чаще всего становится нерентабельным.
Оборудование можно разделить на такие виды:
- стационарная линия;
- конвейерная линия;
- мини-линия;
- мини-завод;
- мобильная линия.
Стационарная линия оборудования для газобетона может производить от 60 м³ продукции в сутки. Для ее складирования требуется примерно 500 м² площади. С управлением линией вполне справятся 2 человека.
Конвейерная линия может выпускать за сутки 75-150 м³ готовой продукции. Размещения оборудования для производства газобетонного блока требует площади более 600 м². Обслуживают его 8 человек.
Мини-линия рассчитана на суточный выпуск около 15 м³ изделий. В состав линии входит смеситель и формы. Для организации производства и установки оборудования требуется 2 человека и 140-160 м² площади.
Установка мини-завода гарантирует выпуск готовых блоков от 25 м³ в сутки. Это немного больше, чем с помощью мини-линии. Отличает мини-завод лишь наличием в его составе поддонов, бака с водой, оборудования для разрезания газобетона.
Мобильные линии часто используются при строительстве личных домов. Они позволяют снизить расходы на треть. Для получения качественного газобетона оборудование подключается к розетке 220 В. В составе линии может быть:
- неподвижный смеситель;
- передвижные формы для заливки раствора;
- установка для разрезания блоков.
Производительность линии достигает 100 м³ в сутки.
Заключение по теме
На протяжении многих тысячелетий человек строит для себя жилье. За эти годы значительно изменились технологии и материалы для строительства. В наше время актуальным стало строительство с использованием газобетона в виде блоков. Раньше блоки выпускались только на заводах, сегодня их производство можно наладить дома. Для этого нужно иметь желание, приобрести оборудование и установить все это на подготовленной площадке. Для выпуска газобетона нужно иметь чистую теплую воду, кварцевый песок, алюминиевую пудру марки ПАП-1, известь, портландцемент М400 или М500 и еще несколько добавок для улучшения качества продукции. Получив все это, можно начинать собственный бизнес по выпуску стройматериалов, имеющих большой спрос. При строительстве собственного дома материал сократит расходы примерно на треть.
Для собственного производства лучше всего приобрести небольшую стационарную линию, с помощью которой можно делать неавтоклавный газобетон. Обслуживать установку могут 2 человека. При таких силах можно ежесуточно выпускать около 60 м³ отличных блоков. Каждый такой искусственный камень весит примерно 30 кг и заменяет собой около 30 стандартных кирпичей. Газоблок весит в несколько раз легче кирпича, поэтому не требует строительства капитального фундамента и использования грузоподъемной техники. Материал отлично обрабатывается ручными инструментами: пилой, стамеской, сверлом. В наше время газобетон занимает ведущее место среди других строительных материалов.
Похожие статьи
kamedom.ru
Технологический процесс производства газобетонных блоков
Сегодня технология производства газобетонных блоков интересует всех, кто планирует строить загородный дом или открывать бизнес по производству ячеистых бетонов. Ведь этот строительный материал является очень удачным выбором в плане прочностных и теплоизоляционных характеристик, и к тому же изготовление газобетона может быть достаточно выгодным бизнес-проектом.
Что нужно знать о ячеистом бетоне?
Газобетон представляет собой искусственный камень с микроскопическими воздушными порами. Еще одно его название — автоклавный ячеистый бетон, и оно само по себе говорит о технологии его производства. Газоблоки обладают прекрасными энергосберегающими характеристиками именно благодаря своей пористой структуре. Кроме того, они отличаются относительно небольшим весом, в том числе по сравнению с кирпичом и другими видами строительной керамики.
Газобетонные блоки — это строительный материал, который может использоваться как для возведения внутренних перегородок, так и для несущих конструкций. Он не подойдет для высотных зданий или промышленных объектов, но в индивидуальном строительстве он прекрасно себя зарекомендовал. Относительно легкие газоблоки не оказывают большой нагрузки на фундамент, что позволяет сократить расходы на устройство основания. Кроме того, они обладают большими размерами, и это позволяет ускорить процесс строительства.
Состав газобетонных блоков
Все перечисленные преимущества этого строительного материала обусловлены его составом. Все, из чего состоит газобетон, — это цемент, кварцевый песок и газообразователь, в роли которого выступает алюминиевая пудра. Некоторые производители добавляют в состав гипс, известь, золу, другие ингредиенты.
Таким образом, газобетон делается на основе сухих компонентов, которые размешиваются с водой. Для этих целей подходит любая техническая чистая вода, соответствующая требованиям ГОСТа 23732-79. При этом важна температура воды. Желательно, чтобы она была не ниже 45°С, поскольку это ускорит твердение блоков, повысит их прочность, а для предприятия это выгодно тем, что увеличится производительность линии в целом. Таким образом, многие производители подогревают воду, поскольку более высокая температура означает лучшее качество материала. А еще это помогает уменьшить количество используемого цемента, поскольку нагрев воды стимулирует активность сухих компонентов смеси.
Производство газобетона требует довольно серьезного подхода к выбору песка. Теоретически для этих целей подойдет как карьерный, так и речной песок, но важно, чтобы в нем содержалось как можно меньше илистых или глиняных частиц. Также важно выбрать размер зерен — не более 2 мм. Технология производства газобетона автоклавным способом позволяет заменить песок шлаком или золой, полученным от металлургических производств. Золы ТЭС помогают получить газобетон с меньшей плотностью. Это помогает дополнительно сократить расходы на производство материала.
Для изготовления газобетонных блоков необходим портландцемент марок М400 и М500. Лучше всего, чтобы портландцемент соответствовал требованиям ГОСТа 10178-85. А вот алюминиевая пудра должна быть марок ПАП-1 или ПАП-2 — она и выполняет роль газообразователя. Иногда для тех же целей применяется специальная паста. Это может быть и суспензия, поскольку пылевидный алюминий не так удобен при замешивании раствора. Могут применяться и суспензии на его основе.
На чем основано действие алюминиевого порошка? Он вступает в реакцию с цементным или известковым раствором, обладающим свойствами щелочи, и в ходе этого химического процесса образуются соли (алюминаты) кальция и газообразный водород, обеспечивающий формирование пор.
Для производства газобетона очень важно сделать правильный расчет расхода по каждому компоненту исходного сырья. Существуют стандартные рекомендации для автоклавных газоблоков. Исходя из такой рецептуры, на весь объем смеси берут 50-70% цемента, 0,04-0,09% алюминиевого порошка и до 20-40% песка. Кроме того, понадобятся вода (0,25-0,8%) и известь (1-5%). Таким образом, для того чтобы получить 1 кубометр газобетона, нужно взять до 90 кг цемента, до 300 л воды, извести — 35 кг, песка — 375 кг, алюминиевого порошка — 0,5 кг. Но это количество может быть скорректировано уже в условиях конкретного производства в зависимости от качественных характеристик самого сырья.
Какое оборудование понадобится?
Технология изготовления газобетона относительно проста. Тем не менее кустарными методами здесь обойтись не получится. Нужно приобрести специальное оборудование, которое обычно заказывают в комплексе у производителя или его официального представителя, — это наиболее выгодный вариант. Это не одна какая-то установка, это целый автоматизированный мини-завод. Иногда производитель даже предоставляет услуги специалиста, который проконсультирует относительно монтажа такой линии, поможет ее наладить и подобрать оптимальный состав для смеси, используемой для такого оборудования.
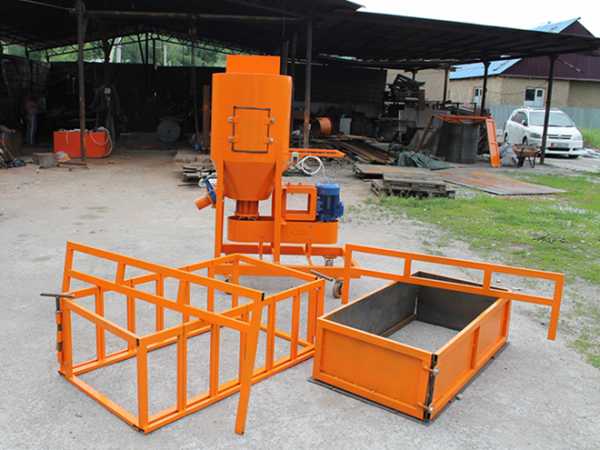
Мини-завод по производству неавтоклавного газобетона
В линию входят различные устройства, и теоретически каждое из них можно купить по отдельности, если по каким-то причинам одно выйдет из строя. Речь идет о таких вещах, как формы и предназначенные для их транспортировки передвижные поддоны, устройства для резки готовых блоков, смесители для газобетона, дозаторы для сыпучих материалов и т.д. Но главное — это печь-автоклав, ведь речь идет именно о производстве автоклавных газоблоков, отличающихся наиболее высокими качественными характеристиками.
Оборудование для производства газобетона делится на несколько типов. Выбор конкретного варианта зависит от требуемой суточной производительности, от того, сколько работников планирует нанимать предприниматель, и как будут организованы смены. Возможны следующие варианты:
- Стационарные линии обладают суточной производительностью до 60 кубометров готовой продукции. Как правило, для них нужны складские и производственные помещения площадью не менее 500 м². Главной особенностью таких линий является то, что формы подъезжают к стационарно установленному смесителю и там заполняются раствором, после чего выполняются все остальные технологические этапы. Это очень простая технология, для того чтобы обслуживать такую линию, достаточно нанять одного дополнительного работника.
- Конвейерные линии нужны там, где требуется большая производительность — до 75-150 м³ в сутки. Здесь производство осуществляется более быстрыми темпами (конечно, сроки созревания изделия не меняются, от линии это не зависит). Однако конвейерные линии требуют больших по площади производственных помещений, а для их обслуживания понадобится не менее 8 человек, хотя большинство технологических процессов здесь происходит в автоматическом режиме.
- Мини-линии не могут похвастаться высокой производительностью, до 15 кубометров готовых блоков в сутки. Отличием от стационарных линий является то, что движется в них смеситель, а формы установлены стационарно. Главное преимущество — им не нужны большие производственные площади, достаточно 140-160 м², так что в качестве стартового варианта они пользуются популярностью.
В частном строительстве часто используют мобильные установки, которые нужны для самостоятельного изготовления газоблоков. Это окупается, причем по расчетам специалистов расходы на строительство снижаются примерно на 30%. Мобильные установки поставляются в комплекте с компрессором. Работают они даже от бытовой электросети.
Этапы производства
Газобетон бывает двух видов — автоклавный или неавтоклавный. Последний вариант стоит дешевле, хотя полученный материал и отличается более низкой прочностью. Тем не менее из-за того, что себестоимость его изготовления ниже (не нужно покупать автоклав, содержать его, платить дополнительно за энергию), он является довольно популярным вариантом, поэтому его стоит рассмотреть подробнее. Если предприниматель намерен выпускать неавтоклавный газобетон, технология производства для него должна сводиться к следующим основным этапам:
- Точная дозировка всех описанных выше компонентов, а затем тщательное их перемешивание. При наличии соответствующего оборудования этот этап отнимает не более 10 минут.
- Подготовленную массу с помощью специального оборудования выгружают в специальные формы (их заполняют только наполовину, поскольку смесь будет увеличиваться в объеме в процессе газообразования). Этот процесс будет протекать в течение 4-х часов. За это время смесь заполняет отведенный ей в форме объем, а иногда даже его ей бывает мало. Тогда через 2 часа излишки можно будет убрать.
- Процесс выдержки изделий занимает около 16 часов, и по истечении этого срока происходит их распалубка и перегрузка на поддоны, где они будут набирать так называемую отпускную прочность. Этот этап отнимает еще 2-3 дня. После этого изделия можно отправлять на склад, но продавать их еще рано, поскольку свою марочную прочность они наберут только на 28-е сутки.
Изготовление газобетонных блоков с применением автоклава на первых этапах практически ничем не отличается от описанной выше технологии. Сначала нужно отмерить необходимое количество всех компонентов (желательно, чтобы это было сделано с помощью дозаторов, это поможет повысить точность). Затем всю эту массу загружают в смеситель и тщательно перемешивают. Иногда специалисты для этих целей предлагают использовать бетономешалку. Затем вводят газообразователь — это происходит через 10-15 минут перемешивания исходных ингредиентов. Алюминиевый порошок в любом случае вступает в реакцию с раствором, для этого ему не нужно автоклавирование.
Полуфабрикат разливают по формам, выдерживают положенные 4-6 часов, после чего производится нарезка газоблоков. До набора прочности они должны полежать еще 10-18 часов.
Но самое важное — знать, как делают автоклавирование после всех описанных выше процедур. Сформированные блоки перегружают в специальную печь, в герметичную камеру, где при высокой температуре каждый блок обрабатывают насыщенным водяным паром. Давление при этом также должно быть высоким — до 12 кг/см².
Неавтоклавный бетон сушат в естественных условиях, но для автоклавных изделий этого не нужно. Тем не менее и их нужно держать около 28-30 суток на складе, где они будут набирать марочную прочность.
Мало знать, как делать газобетон, нужно еще суметь доставить его потребителю. Для этого газоблоки пакуют в специальную термоусадочную пленку и транспортируют на деревянных поддонах.
Похожие статьи
kamedom.ru
Автоклавный и неавтоклавный газобетон — отличия
Изначально технология создания газобетона предусматривала его производство только на технологичном производстве. Но со временем спрос на этот материал так возрос, что газобетон автоклавный стал использоваться в равной мере с подобным видом ячеистого материала, произведенного без дополнительной тепловлажностной обработки. И если нырнуть в пучину огромного выбора газобетона неподготовленному новичку, то он может запросто потонуть в потоке предоставляемой информации о нем. Так чем отличается автоклавный газобетон от неавтоклавного и какой лучше всего приобрести? На эти злободневные вопросы найдете ответы в нашей публикации.
Технология производства газобетона
Прежде чем говорить о существенных различиях в свойствах и качестве автоклавного газобетона и блоков естественной выдержки рассмотрим их компонентный состав, который абсолютно идентичен:
- бездобавочный портландцемент марок М300, М400, иногда используют М500;
- чистый песок мелких фракций – от 2,0 до 2,5 мм.
- вода средней жесткости без химических примесей;
- газообразователь — пудра или паста алюминиевая;
- вещество запускающее химические реакции вспучивания – известь, вид, состояние и дисперсность которой зависит от способа производства;
- модификаторы, улучшающие качество конечного продукта – добавляются по желанию и не являются обязательными составляющими.
Еще одно сходство, объединяющее автоклавный и неавтоклавный газобетон – принцип производства раствора.
На первом этапе в соответствии с технологией готовится обычный цементно-песчаный раствор необходимой консистенции. Полученную смесь распределяют по опалубкам. После чего в нее вводится алюминиевый порошок и известь. Именно реакция этих компонентов обеспечивает образования газа, раствор вспучивается, образуя поры.
Дальше технологии расходятся на этапе выдержки и обработки газобетона. При естественном твердении готовый раствор заливается в опалубку, формирующую блоки нужного размера. После набора прочности изделия распалубливают и отправляют на склад готовой продукции.
При использовании автоклава для газобетона, этот этап происходит немного сложнее. А именно, смесь заливают в монолитную опалубку. После ее вспучивания и набора минимальной прочности газобетонную глыбу разрезают на изделия необходимых размеров и отправляют их для дополнительного обжига в автоклав, где поддерживается температура в пределах 200 0С и давление в 10 Бар. Такие условия по максимуму активируют процессы гидратации цемента и позволяют удалить из бетона лишнюю влагу.
В итоге получается, что изделия естественной сушки – это всего лишь затвердевшая вспученная цементно-песчаная смесь, когда автоклавные газоблоки в процессе обжига образуют новый синтетический компонент – тоберморит, качественно улучшающий характеристики конечного продукта.
Свойства неавтоклавного и автоклавного газобетона
Полученные блоки, изготовленные по двум разным технологиям настолько разные как по виду, так и по своим характеристикам, что даже неопытный обыватель сможет различить их между собой.
Внешние показатели
Первое с чем сталкивается покупатель при выборе, так это с внешним видом материалов. Казалось бы, какая разница как выглядят стеновые блоки, которые впоследствии все равно нужно штукатурить. Однако внешний вид – наиболее точная визуальная характеристика, которая поможет отсеять некачественные изделия.
Геометрические размеры
Если сравнивать газоблоки по критерию геометрии, то изделия автоклавного твердения отличаются большей точностью. Это отчасти заслуга автоклавирования и, конечно же, резанной технологии. Даже ГОСТы регламентируют отклонения линейных размеров от номинальных по-разному, в зависимости от применяемого способа производства.
Допустимые отклонения по параметрам | Автоклавный газобетон | Неавтоклавный газобетон |
---|---|---|
Длина, мм/м | 3 | 5 |
Ширина, мм/м | 2 | 4 |
Высота, мм/м | 1 | 2 |
Эти данные только подчеркивают тот факт, что автоклавный газобетон отличается точной геометрией готовых изделий, которая предотвращает:
- промерзание стен за счет утолщения кладочного шва, которым компенсируются недостатки в форме блоков;
- перерасход кладочного клея, ведущий к увеличению затрат на него.
Цвет
При покупке блоков обращайте внимание на их цвет. Конечно, он будет серым в случае изделий естественного твердения и практически белый у автоклавного газобетона. Различие в оттенках блоков и неоднородности цвета говорит об изменениях в производственном процессе, которые зачастую приводят к снижению эксплуатационных характеристик.
Автоматизированное оборудование для производства автоклавного газобетона сводит любые ошибки к нулю, что изначально считается гарантом качества и долговечности. К тому же такие масштабные цеха дополнены собственной строительной лабораторией, своевременное проведение испытаний в которой вычленяют несоответствия в технологии или рецептуре.
Физико-механические свойства
Газобетонные блоки отличаются не только по внешним показателям и цвету, но и по физико-механическим свойствам.
Прочность
Газобетон представлен богатой номенклатурой марок по прочности – от В1 до В7,5. Их широко применяют не только в качестве создания несущих конструкций, но и для утепления стен. Если сравнивать газобетоны, произведенные по различным технологиям, то автоклавные отличаются большей прочностью при одинаковой плотности с неавтоклавными.
Например, блоки плотностью D600 должны иметь класс по прочности В3,5. Если для автоклавных изделий показатель соблюдается, то с естественно выдержанными изделиями класс прочности едва ли дотягивает до половины нормы. Еще хуже дела обстоят с прочностными показателями у газобетона, произведённого своими руками. Если хотите лично убедиться в этом, купите по блоку и протестируйте в независимой строительной лаборатории. Результаты будут на лицо.
Теплопроводность
Теплопроводность газобетона напрямую зависит от показателей плотности этого материала. Чем ниже марка по плотности блока, тем качественнее его теплоемкостные качества. Разумнее приобрести изделия меньшей плотности, но с более высокими прочностными характеристиками, уменьшая этим показатель теплопроводности стен.
Усадка
Слабейшая сторона любого ячеистого бетона – это его усадка после возведения стен. При применении неверной строительной методики могут появиться трещины, и произойдет отслоение штукатурного слоя. Процессы усадки газобетона естественной выдержки могут длиться до нескольких лет, когда автоклавированные блоки практически лишены такого недостатка, так как при тепловлажностной обработке они уже достигли марочной прочности и полного высыхания.
К тому же, выдержанные газобетонные блоки в естественных условиях далеки от идеальных показателей, что негативно проявляется в виде усадки. Это не только ведет к нарушению линейных размеров, но и к разрушению структуры.
Подводя итоги, можно с легкостью сделать вывод, что блоки из газобетона автоклавного твердения обладают неоспоримыми преимуществами над изделиями естественной выдержки. Но в любом случае при покупке такого стенового материала всегда спрашивайте документы, удостоверяющие его качество.
zamesbetona.ru