Технология производства керамзита – оборудование, состав, из чего делают, дробилка и мини завод своими руками, сертификат, фасовка, видео
Технология производства керамзита — Как производят керамзит
Технология производства керамзита и сущность технологического процесса производства состоит в обжиге глиняных гранул по оптимальному режиму.
Для вспучивания глиняной гранулы нужно, чтобы активное газовыделение совпало по времени с переходом глины в пиропластическое состояние.
Между тем, в обычных условиях газообразование при обжиге глин происходит в основном при более низких температурах, чем их пиропластическое размягчение.
Например, температура диссоциации карбоната магния — до 600°С, карбоната кальция — до 950 °С, дегидратация глинистых минералов происходит в основном при температуре до 800 °С. А выгорание органических примесей еще ранее, реакции восстановления окислов железа развиваются при температуре порядка 900 °С, тогда как в пиропластическое состояние глины переходят при температурах, как правило, выше 1100 °С.
Схема вращающейся печи для производства керамзита:
1—загрузка сырцовых гранул; 2— вращающаяся печь; 3— форсунка; 4— вспученный керамзитовый гравий; 5—поток горячих газов
В связи с этим при обжиге сырцовых гранул в производстве керамзита необходим быстрый подъем температуры. Так как при медленном обжиге значительная часть газов выходит из глины до ее размягчения и в результате получаются сравнительно плотные маловспученные гранулы. Но чтобы быстро нагреть гранулу до температуры вспучивания, ее сначала нужно подготовить, т. е. высушить и подогреть. В данном случае интенсифицировать процесс нельзя. Так как при слишком быстром нагреве в результате усадочных и температурных деформаций, а также быстрого парообразования гранулы могут потрескаться или разрушиться (взорваться).
Оптимальным считается ступенчатый режим термообработки по С. П. Онацкому: с постепенным нагревом сырцовых гранул до 200—600 °С (в зависимости от особенностей сырья) и последующим быстрым нагревом до температуры вспучивания (примерно 1200 °С).
Обжиг осуществляется во вращающихся печах (рис.), представляющих собой цилиндрические металлические барабаны диаметром до 2,5—5 м и длиной до 40— 75 м, футерованные изнутри огнеупорным кирпичом. Печи устанавливаются с уклоном примерно 3% и медленно вращаются вокруг своей оси. Благодаря этому сырцовые гранулы, подаваемые в верхний конец печи, при ее вращении, постепенно передвигаются к другому концу барабана, где установлена форсунка для сжигания газообразного или жидкого топлива. Таким образом, вращающаяся печь работает по принципу противотока: сырцовые гранулы перемещаются навстречу потоку горячих газов,подогреваются. И, наконец, попав в зону непосредственного воздействия огненного факела форсунки,вспучиваются. Среднее время пребывания гранул в печи — примерно 45 мин.
Технология производства керамзита — оптимальный режим термообработки.
Чтобы обеспечить оптимальный режим термообработки, зону вспучивания печи, непосредственно примыкающую к форсунке, иногда отделяют от остальной части (зоны подготовки) кольцевым порогом. Применяют также двухбарабанные печи, в которых зоны подготовки и вспучивания представлены двумя сопряженными барабанами, вращающимися с разными скоростями.
В двухбарабанной печи удается создать оптимальный для каждого вида сырья режим термообработки.
Промышленный опыт показал, что при этом улучшается качество керамзита, значительно увеличивается его выход, а также сокращается удельный расход топлива.
В связи с тем, что хорошо вспучивающегося глинистого сырья для производства керамзита сравнительно мало, при использовании средне- и слабовспучивающегося сырья необходимо стремиться к оптимизации режима термообработки.
Из зарубежного опыта известно, что для получения заполнителей типа керамзита из сырья (промышленных отходов), отличающегося особой чувствительностью к режиму обжига. Используют трехбарабанные вращающиеся печи или три-четыре последовательно располагаемые печи. В которых обеспечиваются не только оптимальные скорость и длительность нагрева на каждом этапе термообработки, но и различная газовая среда.
Значение характера газовой среды в производстве керамзита обусловлено происходящими при обжиге химическими реакциями. В восстановительной среде окись железа Fe2O3 переходит в закись FeO. Это является не только одним из источников газообразования, но и важнейшим фактором перехода глины в пиропластическое состояние.
Внутри гранул восстановительная среда обеспечивается за счет присутствия органических примесей или добавок, но при окислительной среде в печи (при большом избытке воздуха) органические примеси и добавки могут преждевременно выгореть.
Поэтому окислительная газовая среда на стадии термоподготовки, как правило, нежелательна, хотя имеется и другая точка зрения, согласно которой целесообразно получать высокопрочный керамзитовый гравий с невспученной плотной корочкой. Такая корочка толщиной до 3 мм образуется (по предложению Северного филиала ВНИИСТ) при выгорании органических примесей в поверхностном слое гранул, обжигаемых в окислительной среде.
По мнению автора, при производстве керамзита следует стремиться к повышению коэффициента вспучивания сырья, так как невспучивающегося или маловспучивающегося глинистого сырья для получения высокопрочного заполнителя имеется много, а хорошо вспучивающегося не хватает.
С этой точки зрения наличие плотной корочки значительной толщины на керамзитовом гравии свидетельствует о недоиспользовании способности сырья к вспучиванию и уменьшении выхода продукции.
В восстановительной среде зоны вспучивания печи может произойти оплавление поверхности гранул, поэтому газовая среда здесь должна быть слабоокислительной. При этом во вспучивающихся гранулах поддерживается восстановительная среда, обеспечивающая пиропластическое состояние массы и газовыделение, а поверхность гранул не оплавляется.
Характер газовой среды косвенно, через окисное или закисное состояние железистых примесей, отражается на цвете керамзита. Красновато-бурая поверхность гранул говорит об окислительной среде (Fe2O3), темно-серая, почти черная окраска в изломе — о восстановительной (FeO).
Технология производства керамзита: 4 основных схемы
Различают четыре основные технологические схемы подготовки сырцовых гранул, или четыре способа производства керамзита: сухой, пластический, порошково-пластический и мокрый.
Сухой способ используют при наличии камнеподобного глинистого сырья (плотные сухие глинистые породы, глинистые сланцы). Он наиболее прост: сырье дробится и направляется во вращающуюся печь. Предварительно необходимо отсеять мелочь и слишком крупные куски, направив последние на дополнительное дробление.
Этот способ оправдывает себя, если исходная порода однородна, не содержит вредных включений и характеризуется достаточно высоким коэффициентом вспучивания.
Наибольшее распространение получил пластический способ. Рыхлое глинистое сырье по этому способу перерабатывается в увлажненном состоянии в вальцах, глиномешалках и других агрегатах (как в производстве кирпича). Затем из пластичной глиномассы на дырчатых вальцах или ленточных шнековых прессах формуются сырцовые гранулы в виде цилиндриков, которые при дальнейшей транспортировке или при специальной обработке окатываются, округляются.
Качество сырцовых гранул во многом определяет качество готового керамзита.
Поэтому целесообразна тщательная переработка глинистого сырья и формование плотных гранул одинакового размера.
Размер гранул задается исходя из требуемой крупности керамзитового гравия и установленного для данного сырья коэффициента вспучивания.
Гранулы с влажностью примерно 20% могут сразу направляться во вращающуюся печь или, что выгоднее, предварительно подсушиваться в сушильных барабанах. В других теплообменных устройствах с использованием тепла отходящих дымовых газов вращающейся печи. При подаче в печь подсушенных гранул ее производительность может быть повышена.
Таким образом, технология производства керамзита по пластическому способу сложнее, чем по сухому.
Более энергоемко, требует значительных капиталовложений. Но, с другой стороны, переработка глинистого сырья с разрушением его естественной структуры, усреднение, гомогенизация, а также возможность улучшения его добавками позволяют увеличить коэффициент вспучивания.
Порошково-пластический способ отличается от пластического тем, что вначале помолом сухого глинистого сырья получают порошок, а потом из этого порошка при добавлении воды получают пластичную глиномассу, из которой формуют гранулы, как описано выше. Необходимость помола связана с дополнительными затратами. Кроме того, если сырье недостаточно сухое, требуется его сушка перед помолом. Но в ряде случаев этот способ подготовки сырья целесообразен: если сырье неоднородно по составу, то в порошкообразном состоянии его легче перемешать и гомогенизировать; если требуется вводить добавки, то при помоле их легче равномерно распределить.
Если в сырье есть вредные включения зерен известняка, гипса, то в размолотом и распределенном по всему объему состоянии они уже не опасны.
Если такая тщательная переработка сырья приводит к улучшению вспучивания, то повышенный выход керамзита и его более высокое качество оправдывают произведенные затраты.
Мокрый (шликерный) способ заключается в разведении глины в воде в специальных больших емкостях — глиноболтушках. Влажность получаемой пульпы (шликера, шлама) примерно 50%. Пульпа насосами подается в шламбассейны и оттуда — во вращающиеся печи. В этом случае в части вращающейся печи устраивается завеса из подвешенных цепей. Цепи служат теплообменником: они нагреваются уходящими из печи газами и подсушивают пульпу, затем разбивают подсыхающую «кашу» на гранулы, которые окатываются, окончательно высыхают, нагреваются и вспучиваются. Недостаток этого способа — повышенный расход топлива, связанный с большой начальной влажностью шликера. Преимуществами являются достижение однородности сырьевой пульпы, возможность и простота введения и тщательного распределения добавок, простота удаления из сырья каменистых включений и зерен известняка. Этот способ рекомендуется при высокой карьерной влажности глины, когда она выше формовочной (при пластическом формовании гранул). Он может быть применен также в сочетании с гидромеханизированной добычей глины и подачей ее на завод в виде пульпы по трубам вместо применяемой сейчас разработки экскаваторами с перевозкой автотранспортом.
Керамзит, получаемый по любому из описанных выше способов, после обжига необходимо охладить. Технология производства керамзита.
Установлено, что от скорости охлаждения зависят прочностные свойства керамзита. При слишком быстром охлаждении керамзита его зерна могут растрескаться или же в них сохранятся остаточные напряжения, которые могут проявиться в бетоне. С другой стороны, и при слишком медленном охлаждении керамзита сразу после вспучивания возможно снижение его качества из-за смятия размягченных гранул. А также в связи с окислительными процессами, в результате которых FeO переходит в Fe2O3, что сопровождается деструкцией и снижением прочности.
Сразу после вспучивания желательно быстрое охлаждение керамзита до температуры 800—900 °С для закрепления структуры и предотвращения окисления закисного железа. Затем рекомендуется медленное охлаждение до температуры 600—700 °С в течение 20 мин для обеспечений затвердевания стеклофазы без больших термических напряжений, а также формирования в ней кристаллических минералов, повышающих прочность керамзита. Далее возможно сравнительно быстрое охлаждение керамзита в течение нескольких минут.
Технология производства керамзита
Первый этап охлаждения керамзита осуществляется еще в пределах вращающейся печи поступающим в нее воздухом. Затем керамзит охлаждается воздухом в барабанных, слоевых холодильниках, аэрожелобах.
Для фракционирования керамзитового гравия используют грохоты, преимущественно барабанные — цилиндрические или многогранные (бураты).
Внутризаводской транспорт керамзита — конвейерный (ленточные транспортеры), иногда пневматический (потоком воздуха по трубам). При пневмотранспорте возможно повреждение поверхности гранул и их дробление. Поэтому этот удобный и во многих отношениях эффективный вид транспорта керамзита не получил широкого распространения.
Фракционированный керамзит поступает на склад готовой продукции бункерного или силосного типа.
Технология производства керамзита, раскрыта не в полной мере в данной статье. Но, если у Вас появились вопросы, то можете задать их нашим менеджерам в любое удобное время.
keramzitik.ru
Из чего делают керамзит и технология изготовления своими руками
Это легкий материал с гранулированной пористой структурой, представляющий собой продукт ускоренно обожженной глины и глинистых сланцев под высоким температурным режимом. Керамзитовые шарики отличаются плотно спекшейся оболочкой темновато-бурого оттенка, на изломе практически черного. Сегодня постараемся разобраться детально, из чего делают керамзит, рассмотрим его технические показатели.
Состав и характеристики
В составе керамзита содержатся глина и ее сланцы, процесс изготовления проходит методом обжига исходной сырьевой массы в специальных печах
При температуре в 1 000 – 1 300 градусов глина вспучивается и переходит в пиропластическое состояние. С учетом качества исходного материала, создаваемого температурного режима, длительности процесса обжига и иных технологических особенностей изготовления получаются разные технические показатели материала, самыми значимыми из которых считаются размеры зерен, плотность и объемный вес.
Параметры керамзита определены ГОСТом, регламентирующим качественные показатели строительных материалов с пористой структурой. Часть показателей не регулируется, но они все же остаются важными характеристиками. Основные свойства рассмотрим более подробно:
- фракции керамзита. Их всего три, и размеры варьируются в диапазонах 5 – 10, 10 – 20, 20 – 40 мм. В отдельную категорию вынесены фракции, используемые в строительстве. Это гранулы и щебенка, размеры которых составляют от 2.5 до 10 мм, и широкие смесевые фракции от 5 до 20 мм;
- марки по насыпной плотности. Всего их семь. Этот параметр определяет плотность материала без учета промежуточных участков, образуемых гранулами или осколками;
- показатель прочности. Гравийный материал насчитывает тринадцать марок, для щебня их несколько меньше – всего одиннадцать. Показатель прочности щебня и гравия одной марки отличается. Между керамзитовыми марками по значениям плотности и прочности прослеживается взаимосвязь – рост плотности влечет за собой увеличение прочности;
- коэффициент уплотнения. Данная величина согласовывается с потребителем и не превышает показатель 1.15. Ее применяют для учета уплотнения керамзита в процессе транспортировки и хранения. Пользуются таким показателем часто при погрузке материала и его реализации;
- тепловая проводимость. Один из важных показателей, определяющий теплоизоляционные возможности керамзита. Диапазон узкий, что подтверждает высокие теплоизоляционные показатели керамзита, и от роста плотности этот коэффициент увеличивается;
- влагопоглощение. Этот важный параметр показывает изменения качеств керамзита под воздействием воды. Керамзит считается относительно устойчивым материалом, значение влагопоглощения составляет 8 – 20 процентов;
- шумоизоляция. Лучших показателей с помощью керамзита можно достичь, засыпав керамзит под деревянный пол;
- устойчивость к морозам. Из-за низкого влагопоглощения и особенностей основного сырья (глины) керамзит обладает высокими морозоустойчивыми свойствами.
Особенности технологии изготовления
С помощью специальных исследований исходного сырья определяют его пригодность к производству керамзита. Основными требованиями к начальному материалу считаются:
- возможность вспучивания от обжига;
- легкая плавкость;
- определенное время для вспучивания.
В сырье иногда добавляют специальные компоненты, улучшающие вспучивание. Это могут быть мазут или соляровое масло, перлит, анулит и т. п.
Результатом переработки сырья становятся сырцовые гранулы с определенными размерами и составом. Их сначала высушивают, потом обжигают и охлаждают. На очередном этапе производства материал рассортировывается по показателю плотности, при необходимости – дробится, чтобы получились более мелкие фракции. В завершении всего керамзит сортируется, складируется либо отгружается для отправки.
Весь процесс по своей сущности выглядит следующим образом: после подготовки глина подвергается тепловому удару, придающему ей пористость и способствующему процессу вспучивания. Из-за оплавлений оболочки керамзит получает герметизацию и становится прочным.
Добыча исходного сырья
Производственный процесс начинается с добычи исходного материала карьерным способом и его перевозки в глинозапасники. Разработки ведутся открытым способом, для этого используются одно- и многоковшовые экскаваторы. Отдельные пласты не выделяются, добыча идет по всей высоте.
При добыче камнеподобных пород в виде аргиллита и глинистых сланцев, используют буровзрывные работы. Такие породы могут разрабатываться в любое время года, а мягкие – только в подходящий для этого период.
Чтобы производственный процесс шел непрерывно, возводятся специальные морозостойкие хранилища для складирования глины, вмещающие полугодовой запас сырья. Можно под хранение использовать промежуточные конусы, в которых глина под открытым воздухом находится несколько месяцев.
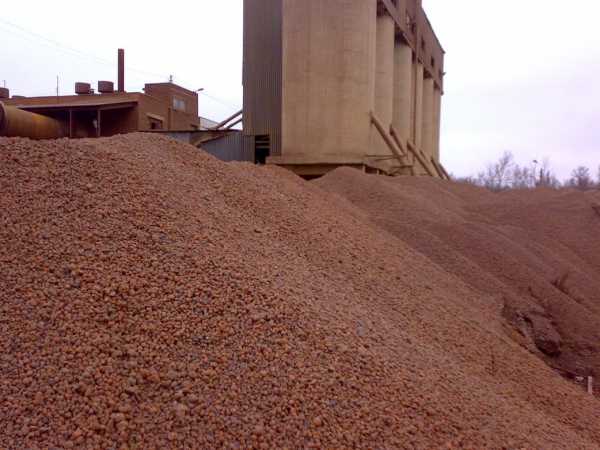
Под воздействием температуры, периодических увлажнений и высыханий, структурное строение сырья частично нарушается, что существенно облегчает процесс его последующей переработки в однородную массу.
Способы получения керамзитовых гранул
Для изготовления керамзита применяют один из четырех способов
Сухой способ
Применяется, если керамзит получают из плотных каменистых глинистых пород и сланцев, используется иная технология изготовления. Исходный материал размельчается на дробильном оборудовании до получения зерен размером 1 – 20 мм. Керамзитовое сырье обжигается в барабанной печи, охлаждается, распределяется по фракциям. В таком варианте производства не предусмотрен этап формовки зерен, и конечный продукт отличается кубическими угловатыми очертаниями.
Мокрый способ
Глина помещается в большие емкости, называющиеся глиноболтушками. После этого заливается вода, чтобы получился шликер с уровнем влажности до пятидесяти процентов. Насосными установками его перекачивают в шламбассейны, откуда он попадает во вращающиеся печи. В печных барабанах происходит разбивка на отдельные гранулы, которые просушиваются газами, выделяемыми печью.
Способ подразумевает большой расход топлива, так как уровень влажности шликера достаточно высок. Но с его помощью сырье очищается от каменистых вкраплений, в него вводятся добавки, чтобы получилась однородная масса. Применяется такой вариант для сырья, отличающегося большим показателем влажности.
Пластический способ
Подготовленную природную глину, влажность которой не превышает тридцати процентов, подвергают двум этапам помола на специальных зубчатых вальцах – грубом и тонком. От такого процесса образуются гранулы, диаметр которых составляет 5 – 10 мм, поступающие в сушильные барабаны. В них полуфабрикат просушивается, подвергается окончательной обкатке, пока не приобретет овальные формы. После этого начинается обжиг, для которого в печах создается температурный режим от 800 до 1 350 градусов. Процесс проходит под постоянным вращением печных барабанов. Спекшиеся керамические гранулы, которые увеличили свой диаметр из-за вспучивания, попадают во вращающиеся холодильные установки. После остывания наступает последний этап – керамзит рассеивается по фракциям.
Порошково-пластический способ
Как производится керамзит таким способом? Исходный материал в сухом состоянии доводится до порошкообразной массы, потом в него добавляется вода. В итоге образуется пластичная масса, пригодная для формирования гранул. Способ считается довольно дорогостоящим, потому что приходится дополнительно измельчать сырье. Второй недостаток – гранулы подвергаются дополнительной сушке.
Так как качество керамзита зависит от качественного состояния сырца, глину следует хорошо переработать и сформировать из нее гранулы одинаковых размеров, параметры которых увеличатся при вспучивании.
Оборудование для производства керамзита
Из чего делают керамзит, мы выяснили. Остается разобраться, как устроена производственная линия по изготовлению этого строительного материала. В нее входят следующие агрегаты и приспособления:
- устройства для рыхления;
- дырчатые вальцы;
- глиносмесители;
- барабаны для сушки;
- печи, в которых выполняется обжиг;
- бункеры;
- пневматические транспортеры, ленточные и другие конвейеры;
- лотки;
- сортировщики для гравия.
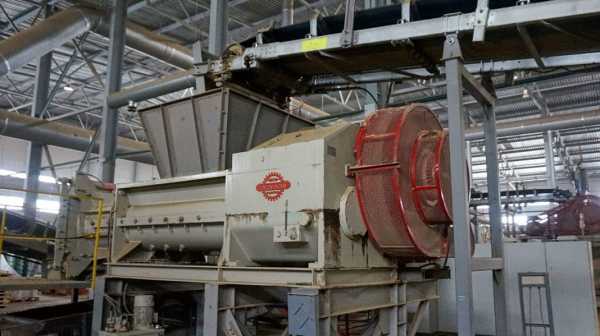
На первичной обработке исходного материала применяется специальная дробильная установка. Состоит она из узла измельчения, в который входят:
- валы лопастного типа, способные совершать вращательные движения по направлению друг к другу;
- жесткая рама;
- зубчатый привод;
- приемочный бункер.
Как только валы начинают свое вращение, сырье измельчается до необходимых размеров. Специальные добавки вводятся через смесительную установку.
Сырье обжигается в печных устройствах с вращающимися барабанами, имеющими цилиндрические корпуса из стального материала. Конструктивно печь состоит из следующих элементов:
- головки для загрузки сырья и выгрузки материала;
- опорной станции;
- приводов;
- уплотнения концов;
- кожуха венцовой пары и т. д.
Печь устанавливается на фундаментной площадке. Опорой служит сварная рама и ролики, регулирующие ее положение.
Изготовление керамзита в домашних условиях
Возможно ли изготовление керамзита своими руками? Для этого потребуется качественное оснащение, с помощью которого можно готовить до 250 тысяч кубометров керамзита за один год. Для приготовления керамзита своими руками пользуются мини-заводами, топливом для которых служат мазут, уголь, газ природный.
При помощи таких заводиков получают керамзитовый песок, размеры гранул которого варьируются от 0.16 до 5 мм. Для этого гранулированное либо подвергнутое измельчению сырье обжигается в печи.
Зачастую для домашнего пользования покупают специальные дробильные установки, существенно упрощающие весь производственный процесс. Отметим, что с помощью чертежей, необходимых материалов и наличия желания, можно изготовить дробилку своими руками.
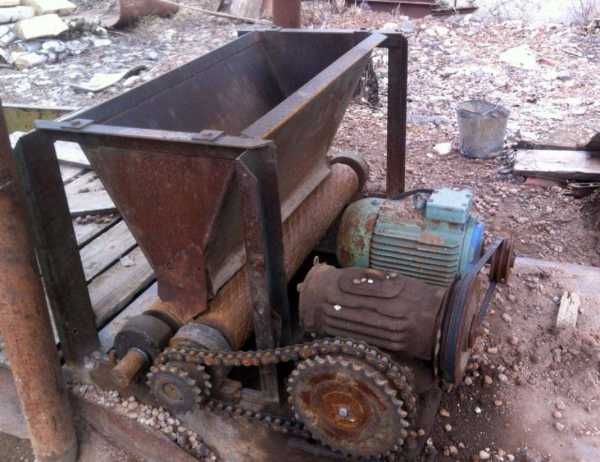
На домашнем мини-заводе производится керамзитовый песок из гравийного некондиционного материала. Для получения глинозольного керамзита используют в виде сырья плавкие породы и золу, полученную при сжигании торфа либо каменного и бурого угля. В результате образуется заполнитель, своими свойствами схожий с простым керамзитом. Зольный керамзитовый материал получается с помощью обжига или безобжиговым методом.
Изготовление керамзита – процесс достаточно энергоемкий. Но высокий уровень производительности и постоянный спрос на этот строительный материал помогают быстро окупить все предварительные затраты.
1nerudnyi.ru
Главная Что такое керамзит Область применения Характеристики керамзита Перевозка керамзита Фасовка керамзита Гост на керамзит ЧаВо(Частые вопросы о керамзите) Технология производства керамзита Перед тем как заказать Цена на керамзит Контакты
каталог ссылок
|
Сущность технологического процесса производства керамзита состоит в обжиге глиняных гранул по оптимальному режиму. Для вспучивания глиняной гранулы нужно, чтобы активное газовыделение совпало по времени с переходом глины в пиропластическое состояние. Между тем в обычных условиях газообразование при обжиге глин происходит в основном при более низких температурах, чем их пиропластическое размягчение. Например, температура диссоциации карбоната магния — до 600°С, карбоната кальция — до 950 °С, дегидратация глинистых минералов происходит в основном при температуре до 800 °С, а выгорание органических примесей еще ранее, реакции восстановления окислов железа развиваются при температуре порядка 900 °С, тогда как в пиропластическое состояние глины переходят при температурах, как правило, выше 1100 °С. Схема вращающейся печи для производства керамзита: 1—загрузка сырцовых гранул; 2— вращающаяся печь; 3— форсунка; 4— вспученный керамзитовый гравий; 5—поток горячих газов
В связи с этим при обжиге сырцовых гранул в производстве керамзита необходим быстрый подъем температуры, так как при медленном обжиге значительная часть газов выходит из глины до ее размягчения и в результате получаются сравнительно плотные маловспученные гранулы. Но чтобы быстро нагреть гранулу до температуры вспучивания, ее сначала нужно подготовить, т. е. высушить и подогреть. В данном случае интенсифицировать процесс нельзя, так как при слишком быстром нагреве в результате усадочных и температурных деформаций, а также быстрого парообразования гранулы могут потрескаться или разрушиться (взорваться). Оптимальным считается ступенчатый режим термообработки по С. П. Онацкому: с постепенным нагревом сырцовых гранул до 200—600 °С (в зависимости от особенностей сырья) и последующим быстрым нагревом до температуры вспучивания (примерно 1200 °С). Обжиг осуществляется во вращающихся печах (рис.), представляющих собой цилиндрические металлические барабаны диаметром до 2,5—5 м и длиной до 40— 75 м, футерованные изнутри огнеупорным кирпичом. Печи устанавливаются с уклоном примерно 3% и медленно вращаются вокруг своей оси. Благодаря этому сырцовые гранулы, подаваемые в верхний конец печи, при ее вращении, постепенно передвигаются к другому концу барабана, где установлена форсунка для сжигания газообразного или жидкого топлива. Таким образом, вращающаяся печь работает по принципу противотока: сырцовые гранулы перемещаются навстречу потоку горячих газов,подогреваются и, наконец, попав в зону непосредственного воздействия огненного факела форсунки,вспучиваются. Среднее время пребывания гранул в печи — примерно 45 мин. Чтобы обеспечить оптимальный режим термообработки, зону вспучивания печи, непосредственно примыкающую к форсунке, иногда отделяют от остальной части (зоны подготовки) кольцевым порогом. Применяют также двухбарабанные печи, в которых зоны подготовки и вспучивания представлены двумя сопряженными барабанами, вращающимися с разными скоростями. В двухбарабанной печи удается создать оптимальный для каждого вида сырья режим термообработки. Промышленный опыт показал, что при этом улучшается качество керамзита, значительно увеличивается его выход, а также сокращается удельный расход топлива. В связи с тем, что хорошо вспучивающегося глинистого сырья для производства керамзита сравнительно мало, при использовании средне- и слабовспучивающегося сырья необходимо стремиться к оптимизации режима термообработки. Из зарубежного опыта известно, что для получения заполнителей типа керамзита из сырья (промышленных отходов), отличающегося особой чувствительностью к режиму обжига, используют трехбарабанные вращающиеся печи или три-четыре последовательно располагаемые печи, в которых обеспечиваются не только оптимальные скорость и длительность нагрева на каждом этапе термообработки, но и различная газовая среда. Значение характера газовой среды в производстве керамзита обусловлено происходящими при обжиге химическими реакциями. В восстановительной среде окись железа Fe2O3 переходит в закись FeO, что является не только одним из источников газообразования, но и важнейшим фактором перехода глины в пиропластическое состояние. Внутри гранул восстановительная среда обеспечивается за счет присутствия органических примесей или добавок, но при окислительной среде в печи (при большом избытке воздуха) органические примеси и добавки могут преждевременно выгореть. Поэтому окислительная газовая среда на стадии термоподготовки, как правило, нежелательна, хотя имеется и другая точка зрения, согласно которой целесообразно получать высокопрочный керамзитовый гравий с невспученной плотной корочкой. Такая корочка толщиной до 3 мм образуется (по предложению Северного филиала ВНИИСТ) при выгорании органических примесей в поверхностном слое гранул, обжигаемых в окислительной среде. По мнению автора, при производстве керамзита следует стремиться к повышению коэффициента вспучивания сырья, так как невспучивающегося или маловспучивающегося глинистого сырья для получения высокопрочного заполнителя имеется много, а хорошо вспучивающегося не хватает. С этой точки зрения наличие плотной корочки значительной толщины на керамзитовом гравии свидетельствует о недоиспользовании способности сырья к вспучиванию и уменьшении выхода продукции. В восстановительной среде зоны вспучивания печи может произойти оплавление поверхности гранул, поэтому газовая среда здесь должна быть слабоокислительной. При этом во вспучивающихся гранулах поддерживается восстановительная среда, обеспечивающая пиропластическое состояние массы и газовыделение, а поверхность гранул не оплавляется. Характер газовой среды косвенно, через окисное или закисное состояние железистых примесей, отражается на цвете керамзита. Красновато-бурая поверхность гранул говорит об окислительной среде (Fe2O3), темно-серая, почти черная окраска в изломе — о восстановительной (FeO). Различают четыре основные технологические схемы подготовки сырцовых гранул, или четыре способа производства керамзита: сухой, пластический, порошково-пластический и мокрый. Сухой способ используют при наличии камнеподобного глинистого сырья (плотные сухие глинистые породы, глинистые сланцы). Он наиболее прост: сырье дробится и направляется во вращающуюся печь. Предварительно необходимо отсеять мелочь и слишком крупные куски, направив последние на дополнительное дробление. Этот способ оправдывает себя, если исходная порода однородна, не содержит вредных включений и характеризуется достаточно высоким коэффициентом вспучивания. Наибольшее распространение получил пластический способ. Рыхлое глинистое сырье по этому способу перерабатывается в увлажненном состоянии в вальцах, глиномешалках и других агрегатах (как в производстве кирпича). Затем из пластичной глиномассы на дырчатых вальцах или ленточных шнековых прессах формуются сырцовые гранулы в виде цилиндриков, которые при дальнейшей транспортировке или при специальной обработке окатываются, округляются. Качество сырцовых гранул во многом определяет качество готового керамзита. Поэтому целесообразна тщательная переработка глинистого сырья и формование плотных гранул одинакового размера. Размер гранул задается исходя из требуемой крупности керамзитового гравия и установленного для данного сырья коэффициента вспучивания. Гранулы с влажностью примерно 20% могут сразу направляться во вращающуюся печь или, что выгоднее, предварительно подсушиваться в сушильных барабанах, в других теплообменных устройствах с использованием тепла отходящих дымовых газов вращающейся печи. При подаче в печь подсушенных гранул ее производительность может быть повышена. Таким образом, производство керамзита по пластическому способу сложнее, чем по сухому, более энергоемко, требует значительных капиталовложений, но, с другой стороны, переработка глинистого сырья с разрушением его естественной структуры, усреднение, гомогенизация, а также возможность улучшения его добавками позволяют увеличить коэффициент вспучивания.Порошково-пластический способ отличается от пластического тем, что вначале помолом сухого глинистого сырья получают порошок, а потом из этого порошка при добавлении воды получают пластичную глиномассу, из которой формуют гранулы, как описано выше. Необходимость помола связана с дополнительными затратами. Кроме того, если сырье недостаточно сухое, требуется его сушка перед помолом. Но в ряде случаев этот способ подготовки сырья целесообразен: если сырье неоднородно по составу, то в порошкообразном состоянии его легче перемешать и гомогенизировать; если требуется вводить добавки, то при помоле их легче равномерно распределить; если в сырье есть вредные включения зерен известняка, гипса, то в размолотом и распределенном по всему объему состоянии они уже не опасны; если такая тщательная переработка сырья приводит к улучшению вспучивания, то повышенный выход керамзита и его более высокое качество оправдывают произведенные затраты. Мокрый (шликерный) способ заключается в разведении глины в воде в специальных больших емкостях — глиноболтушках. Влажность получаемой пульпы (шликера, шлама) примерно 50%. Пульпа насосами подается в шламбассейны и оттуда — во вращающиеся печи. В этом случае в части вращающейся печи устраивается завеса из подвешенных цепей. Цепи служат теплообменником: они нагреваются уходящими из печи газами и подсушивают пульпу, затем разбивают подсыхающую «кашу» на гранулы, которые окатываются, окончательно высыхают, нагреваются и вспучиваются. Недостаток этого способа — повышенный расход топлива, связанный с большой начальной влажностью шликера. Преимуществами являются достижение однородности сырьевой пульпы, возможность и простота введения и тщательного распределения добавок, простота удаления из сырья каменистых включений и зерен известняка. Этот способ рекомендуется при высокой карьерной влажности глины, когда она выше формовочной (при пластическом формовании гранул). Он может быть применен также в сочетании с гидромеханизированной добычей глины и подачей ее на завод в виде пульпы по трубам вместо применяемой сейчас разработки экскаваторами с перевозкой автотранспортом. Керамзит, получаемый по любому из описанных выше способов, после обжига необходимо охладить. Установлено, что от скорости охлаждения зависят прочностные свойства керамзита. При слишком быстром охлаждении керамзита его зерна могут растрескаться или же в них сохранятся остаточные напряжения, которые могут проявиться в бетоне. С другой стороны, и при слишком медленном охлаждении керамзита сразу после вспучивания возможно снижение его качества из-за смятия размягченных гранул, а также в связи с окислительными процессами, в результате которых FeO переходит в Fe2O3, что сопровождается деструкцией и снижением прочности. Сразу после вспучивания желательно быстрое охлаждение керамзита до температуры 800—900 °С для закрепления структуры и предотвращения окисления закисного железа. Затем рекомендуется медленное охлаждение до температуры 600—700 °С в течение 20 мин для обеспечений затвердевания стеклофазы без больших термических напряжений, а также формирования в ней кристаллических минералов, повышающих прочность керамзита. Далее возможно сравнительно быстрое охлаждение керамзита в течение нескольких минут. Первый этап охлаждения керамзита осуществляется еще в пределах вращающейся печи поступающим в нее воздухом. Затем керамзит охлаждается воздухом в барабанных, слоевых холодильниках, аэрожелобах. Для фракционирования керамзитового гравия используют грохоты, преимущественно барабанные — цилиндрические или многогранные (бураты). Внутризаводской транспорт керамзита — конвейерный (ленточные транспортеры), иногда пневматический (потоком воздуха по трубам). При пневмотранспорте возможно повреждение поверхности гранул и их дробление. Поэтому этот удобный и во многих отношениях эффективный вид транспорта керамзита не получил широкого распространения. Фракционированный керамзит поступает на склад готовой продукции бункерного или силосного типа. |
moskeramzit.narod.ru
сырье и технология производства, фракции и цены
ОГреческое слово «Керамос» (глина) прослеживается во многих названиях современных стройматериалов – керамзитовый гравий, щебень или песок. Керамзит – это продукт, получаемый при обжиге глины легкоплавких сортов. Рабочий процесс превращает исходное сырье в легкие, пористые зерна кубической или овальной формы. Характеризуется огнестойкостью, не пропускает воду, имеет низкую теплопроводность. Основные свойства – высокая прочность, малый вес, устойчивость к химическим воздействиям, антисептические качества. Важной особенностью является экологическая безвредность при неограниченном сроке использования.
Оглавление:
- Из чего делают керамзит?
- Технология изготовления
- Цена за мешок и куб
Характеристики обработки глины регулируют получение разного веса и насыпной плотности в отдельно взятом объеме. В зависимости от способа изготовления и режима воздействия можно получить керамзитовый щебень, крупный гравий или песок. Этим обуславливается использование материала в легких бетонах, как засыпка для звуко и теплоизоляции в конструктивах зданий, сооружений, составляющая строительных растворов. Также керамзит широко используется, имея положительные характеристики, в грунтовом растениеводстве. Со стоимостью мешка керамзита вы можете ознакомиться, пройдя по ссылке.
Производственное сырье
Из чего же делают керамзит? Промышленное сырье — это легкоплавкие осадочные глинистые породы, содержание кварца в которых менее 30 %. Реже используется камнеподобный материал. Во время производства для образования воздушных пустот (вспучивания) применяют определенные добавки, имеющие оксиды железа, солярка, мазут.
Основным критерием выбора материала для керамзита является способность к вспучиванию при 1000 – 1250 градусах. Во время процесса продукт приобретает ячеистую структуру с равномерным распределением закрытых пор. Используемое в производстве сырье должно быть тонкодисперсным, низкой запесоченности, с интервалом размягчения в пределах 50 градусов. Наилучшими считаются монтмориллонитовые и гидрослюдистые. Улучшение качества слабо вспучиваемых глин делают введением в состав шихты добавок, таких как:
- молотый каменный уголь;
- мазут;
- соляровое масло;
- сульфитно-спиртовая барда;
- пиритные огарки;
- пылевидные железные руды.
Основной состав шихты включает в себя:
- оксид алюминия 12%;
- оксид и окись железа 10%;
- кремнезем 70%;
- кварц 30%;
- органика 1-2%.
Степень качества, пригодности глиняного сырья определяется и контролируется лабораторными исследованиями на производстве.
Методика изготовления
Технология изготовления керамзита состоит из доставки материала и его предварительной подготовки, термической обработки, охлаждения конечной продукции, сортировки, перевозки на склад хранения. Существует четыре вида методик: сухая, мокрая, пластическая, порошково-пластическая. Качество и характеристики сырья диктуют выбор определенного способа производства.
1. Для использования камнебитной глины более приемлем сухой тип. Масса измельчается на мелкие фракции, а затем подвергается обжигу.
2. Шликерный (мокрый) метод требует разведения глины водой в специальных емкостях до 50% влажности. Из накопительных бассейнов масса отправляется на обжиг. В печи устроена завеса из цепей, на которых шликер просушивается и разрушается на мелкие фрагменты.
3. Чаще всего используется пластический способ. Он основан на увлажнении сырьевой массы и переработке ее в цилиндрические гранулы. Затем полуфабрикат просушивается в сушильной емкости и подается в печь.
4. Последняя технология предусматривает измельчение сухого материала в порошок. После добавления воды из получившейся массы формуют гранулы. Заключительная стадия процесса такая же, как при пластическом способе обработки.
Основное оборудование для производства керамзита включает в себя формовочные аппараты, конвейеры, агрегаты сушки сырья, печи для обжига, холодильные установки. Глиняный материал поступает сверху в наклонный барабан с расположенной внизу форсункой. Гранулы подвергаются тепловому удару. В потоке встречного горячего газа они постепенно опускаются вниз. Под действием жара глина закипает, вспучивается, оплавляется наружный слой. Длительность цикла – примерно 45′.
Следующая операция – охлаждение. Во избежание растрескивания готовых гранул делается медленное понижение температуры. Благодаря поступающему воздуху, действие начинается в печке, продолжается в аэрожелобах и заканчивается барабанными холодильниками. Остывший керамзит отправляют на склад. Процесс изготовления этим завершается.
Стоимость готового продукта
Цена зависит от многих факторов: стоимость сырья, материалов, цена используемых энергоносителей. Кроме того, стоит не забывать про транспортные расходы, критерии оптовых и розничных продаж.
Купить керамзит можно по следующим ценам:
Фракция | Россыпью, цена за м3/руб | В мешках (0,03 м3), цена за мешок/рубли |
0-5 | 2200 | от 70 |
5-10 | 1900 | 60 |
10-20 | 1300 | 42 (при объеме 1000 мешков) |
20-40 | 1300 | 42 (при объеме 1000 мешков) |
Керамзит среднего размера (фракции 10-20 мм) наиболее востребован в производстве строительных работ.
stroitel-list.ru
какое сырье используется, цена за м3 и мешок
Керамзит представляет собой пористый сыпучий материал в виде гранул овальной или округлой формы. В зависимости от режима обработки сырья получаются разные фракции – от песка до гравия. Используют как заполнитель в производстве легких бетонов, а также в виде теплоизолирующей засыпки при строительстве зданий.
Оглавление:
- Из чего производится керамзит?
- Технология изготовления и оборудование
- Виды и характеристики
- Расценки за куб и мешок
Из чего же делают керамзит?
В качестве промышленного сырья используют глинистые легкоплавкие породы (кремнезем) с содержанием кварца не менее 30 %. Их добывают в карьерах открытым способом. Во время разработки не выделяют отдельные пласты, а снимают глину по всей высоте залежи. Для добычи мягкого сырья используют экскаваторы. В случае камнеподобных пород (аргиллиты, глинистые сланцы) проводятся буровзрывные работы. Чтобы непрерывно обеспечивать производство сырьем, делают вместительные морозостойкие хранилища.
Главное требование к глинистым породам – способность к вспучиванию при сверхвысоких температурах. Во время обжига керамзит приобретает пористую структуру с равномерно распределенными воздушными ячейками. Поэтому шихта должна быть тонкодисперсной с низким содержанием песка. Для улучшения качества и усиления вспучиваемости в нее вводят некоторые добавки: угольный порошок, солярку, мазут, железные и алюминиевые руды.
Технология изготовления керамзита
Подготовленное глиняное сырье обжигают в специальных печах при постоянном вращении. В процессе производства температуру резко повышают до 1300 градусов и удерживают в течение получаса. В результате термического удара глина сильно вспучивается и превращается в пористую стекловидную массу. Быстрое оплавление наружной поверхности образует прочную герметичную оболочку.
Методики изготовления:
1. Сухой – простая переработка, применяемая для камнебитной глины с однородной структурой. Перед отправкой в печь делается дробление. Достоинства сухого метода: минимальные затраты и низкая энергоемкость.
2. Шликерный (мокрый) – перед обжигом делают шликер – разводят сырье водой, добиваясь 50% влажности. Во вращающейся печи масса разбивается на гранулы и подсушивается. Мокрый способ помогает хорошо очистить глинистую породу от твердых включений. Шликер имеет однородную консистенцию, в него легко вводить присадки. Недостатком является большой расход топлива.
3. Пластический – методика основана на увлажнении рыхлого сырья с последующим формированием цилиндрических гранул. Им делают округлые формы, просушивают и отправляют в печь на обжиг. Пластический способ считается сложным в исполнении, энергозатратным и дорогостоящим, зато благодаря структурным изменениям массы получается керамзит с высокими качественными характеристиками.
4. Порошково-пластический – сначала из сухого сырья делают порошок, который разводят водой и получают пластичную массу. Затем из нее формируют одинаковые по размеру гранулы. Недостатки: измельчение глины и сушка влекут за собой дополнительные расходы по производству.
Способ изготовления определяют на основе качества и характеристик исходного сырья.
Оборудование для производства керамзита
Технологическая линия включает в себя агрегаты для рыхления, перемешивания, формования и сушки, печи, конвейерные ленты, бункеры, гравийные сортировщики, холодильные установки. Предварительная обработка заключается в измельчении. Это делается при помощи специальной дробилки.
Печь для обжига представляет собой стальной барабан, установленный под небольшим наклоном. Диаметр вращающейся емкости – 2-5 м, длина достигает 70 м. Раздробленное сырье засыпают в печь сверху. Снизу находится топка с форсункой. Полный цикл порообразования занимает 30-45 минут с момента разогрева.
Для изготовления керамзита из низкокачественного сырья используют печи с двумя барабанами. Они разделены между собой и вращаются с разной скоростью.
Характеристики керамзита
Готовые гранулы керамзита имеют пористую структуру и прочную спекшуюся оболочку. Они обладают малым весом, огнестойкостью, газо- и водонепроницаемостью.
Ячеистый материал классифицируют по типоразмеру, форме зерен, прочности и насыпной плотности.
- Гравий – окатыши овальных форм фракцией от 5 до 40 мм и выше. Цвет снаружи – буро-коричневый, на изломе – черный. Керамзитовый гравий широко применяется в строительной отрасли. Наиболее востребована фракция – 10-20.
- Щебень – результат дробления крупных конгломератов керамзита. Форма неправильная с острыми угловатыми краями, фракция – 5-40. Применяется при производстве бетона в качестве добавочного компонента.
- Песок (отсев) – Мелкие частицы фракции 0-5. Представляют собой побочный продукт обжига или дробления керамзита. Используются в качестве наполнителя при изготовлении строительных блоков.
Стоимость керамзита
Фракция, мм | Цена, руб/куб | Цена, руб/мешок* |
0-5 | 1800-2200 | 70-140 |
5-10 | 1700-1900 | 60-120 |
10-20 | 1000-1300 | 40-95 |
20-40 | 1000-1300 | 40-85 |
Тем, кто планирует купить фасованный керамзит, следует помнить, что в одном мешке содержится 0,03-0,005 м3.
stroitel-lab.ru
Производство керамзита
Керамзит — популярный и доступный материал с уникальным сочетанием свойств. Его внедрение в строительство изменило многие технологии и, к тому же, он нашел применение в других областях производства и быта. Это легкий, пористой структуры материал, получаемой по специальной технологии обжига глины.
Глины-сланцы имеют в своем составе до 30% кварца и легко плавятся, причем при обжиге гранул глины, при осуществлении такого процесса, как производство керамзита, они вспучиваются, увеличиваются в объеме, становится прекрасным строительным материалом, по форме напоминающим щебень.
Основные качества керамзита, делающие его незаменимым материалом для строительных работ:
• Он обладает низкой влагопоглощающей способностью, так как при обжиге, на элементах продукта создается защитная пленка. Это очень ценное качество для строительных материалов-наполнителей, применяемых для изоляции.
• Пористая структура снижает коэффициент деформации, поэтому керамзит почти не дает усадки, что ускоряет строительные циклы.
• Имеет отличные теплоизоляционные свойства, которые могут умеренно колебаться в зависимости от технологии производства.
• К другим характеристикам относятся: звуко- и теплоизоляция, огнеупорность, морозоустойчивость, химическая инертность, долговечность, экологическая чистота, доступная цена.
Оборудование для производства керамзита
Производство керамзита отработано достаточно и успешно используются во всем мире. Для создания собственного производства, прежде всего, необходимо специальное оборудование, которое обеспечит все стадии такого процесса как производство керамзита: подсушку сырья, обработку с гранулированием, обжиг, охлаждение керамзита.
Оборудование монтируется на специальной площадке. Производство керамзита начинается с доставки сырья, затем поступающего на приспособления для сушки глины, (глинорыхлитель, камневыделительные вальцы и сушильный барабан). После этого глина подается на линию переработки. Она перемещается на вальцы грубого помола, лопастный смеситель, вальцы тонкого помола и попадает в питатель.
Уже подготовленная смесь, поступает в формовочный агрегат, представляющий собой шнековый пресс, имеющий приставку для грануляции. Порции керамзита уже сформированные, затем доставляются в печь для обжига. Следующий этап – охлаждение в слоевом холодильнике и дальше поступление для транспортировки на ленточный конвейер.
Производительность таких линий от 100000 до 200000 куб. метров в год керамзита. Размер площадки под такой производственный цикл должен быть 7200 – 14000 кв. метров. Собственно производственный цех займет 860 кв. метров, на остальной площади будет расположено вспомогательное оборудование, склады, бытовые строения.
Технология производства керамзита
При выборе оборудования нужно определиться со способом производства керамзита: сухой, пластический, порошково-пластинчатый или мокрый. Сухой возможен тогда, когда есть возможность получать однородную камнебитную глину. Эта глина измельчается и сразу идет на обжиг. Пластический способ требует предварительного увлажнения и перемешивания глины в смесителях.
Затем идет формирование гранул в дырчатых вальцах или шнековых прессах. После чего происходит основной процесс — обжигание в печах. Порошково-пластинчатый вариант предполагает предварительное перемалывание сырья в порошок, увлажнение, гранулирование в дырчатых вальцах, затем обжиг. При мокром методе производства керамзита глина в смесителях превращается в однородную массу, которая поступает в шламбассейн, а оттуда в печь. Чаще всего выбирается пластический способ, как экономически более выгодный.
promplace.ru
Технология производства керамзита | Новости в строительстве
Технология производства керамзита основана на способе термоудара с обжигом гранул в монослое, при этом для его получения используется кольцевая (карусельная) печь с вращающимся подом. Такая печь применяется в металлургической промышленности с некоторыми конструктивными изменениями, для закладки стального литья.
Керамзит является основным видом искусственных пористых заполнителей используемых в строительстве, на долю которого приходится свыше 68% объема производства. Получают керамзит из слабовспучивающихся глин, но с повышенным содержанием карбонатных примесей. Технология производства легкого керамзитового гравия, предложенная ЦНИИЭПсельстроем исходит из следующих предпосылок:
1. Скорость нагрева должна быть максимальной, так как это способствует сохранению большей части паров и газов, обусловливающих поризацию.
2. Оптимальная температура обжига гранул ограничивается верхним пределом интервала вспучивания и температурой размягчения глин.
Технология производства керамзита основана на способе термоудара с обжигом гранул в монослое, при этом для его получения используется кольцевая (карусельная) печь с вращающимся подом. Такая печь применяется в металлургической промышленности с некоторыми конструктивными изменениями, для закладки стального литья.
Читать далее на http://stroivagon.ru азерит
Такая печь считается более удачной в технологическом плане. так как она лишена тех недостатков, которые возникают во вращающихся печах, в пересыпающемся слое во время обжига. При этом удается избегать перетирании гранул керамзита и значительные теплопотери в процессе производства.Технология производства керамзита способом термоудара состоит из следующих основных операций:
Читать далее на http://stroivagon.ru -гравий керамзитовый
1. Изготовление сырцовых гранул, сушку сырцовых гранул и предварительную термоподготовку гранул на оборудовании существующих керамзитовых заводах.
2. Обжиг керамзитовых гранул в кольцевой печи и охлаждение керамзита.
Керамзит имеющий наименьшую среднюю плотность образуется в условиях термоподготовки гранул при температуре 200…250°С в течении 25…35 минут.Термоподготовка гранул керамзита в течении 25 минут и более при температуре 300 °С и выше увеличивает плотность гранул на 60…70 %. Установлены следующие оптимальные режимы предварительной термоподготовки гранул керамзита:
1. Сушка в сушильном барабане при температуре 100…120°С в течении 30 минут до остаточной влажности в пределах 12…17 %.
2. Термообработка в течении 25 минут при температуре 200…250°С до остаточной влажности 0…3 %.
Определение оптимальных параметров вспучивания гранул производилось для способа термического удара. При этом замечено что обжиг гранул керамзита из курского суглинка способом термического удара в температурном интервале вспучивания позволяет получить легкий керамзитовые гранулы со средней плотностью 400 кг/м³. То есть на 32 % ниже средней плотности керамзитовых гранул полученных во вращающихся печах (570…600 кг/м³).
Для наглядности основные физико-механические свойства керамзита, полученного способом термоудара в кольцевой печи, приведены в таблицу № 1.
Таблица № 1. Основные физико-механические свойства керамзита, полученного способом термоудара в кольцевой печи
При обжиге гранул керамзита из глины способом термоудара получен керамзит со средней плотностью 280…425 кг/м³. Такие гранулы имеют величину средней плотности значительно ниже, чем керамзитовые гранулы полученные во вращающихся печах. при этом поверхность гранул керамзита получается частично оплавленной но шероховатой и структура равномерно пористая.
Легкий керамзит полученный из слабовспучивающихся глин способом термоудара в кольцевой печи (смотри рисунок-1) выдерживает более 400 циклов замораживания-оттаивания без признаков разрушения (ГОСТ 9753-81*). При этом керамзит имеет сравнительно низкое водопоглощение которое можно объяснить частичным оплавлением его поверхности в процессе производства.
При этом кислотостойкость керамзитовых гранул составляет примерно 90…98 %, а щелочестойкость в пределах 50…60 %. Керамзитовые гранулы показали высокую водостойкость, а коэффициент размягчения составляет всего 0,95…0,96. С использованием в строительстве этого керамзита был получен конструктивный теплоизоляционный керамзитобетон со средней плотностью 850…950 кг/м³, имеющий прочность при сжатии в пределах 3,5…6 МПа.
Предварительный технико-экономический анализ эффективности производства керамзитового гравия способом термоудара показал что снижение средней плотности керамзита в два раза позволит снизить его заводскую себестоимость примерно на 50 %. Разработан проект технологической линии производства керамзитовых гранул способом термоудара в кольцевой (карусельной) печи производительностью 100 тысяч м³ в год.
Производство керамзита
Предложенный способ производства включает сушку и трехстадийную скоростную термообработку гранул керамзита:
1. Предварительная термоподготовка в течении 20…40 минут до 200…400°С.
2. Скоростной подъем температуры до 800…1100°С и изотермическая выдержка при конечной температуре до 10 минут.
3. Вспучивание-скоростной подъем температуры до 1150…1250 °С и изотермическая выдержка при конечной температуре до 5 минут.
Дополнительная термоподготовка при температуре 800…1100°С обеспечивает образование в гранулах окисленной оболочки различной толщины. Характерной особенностью обжига в неподвижном монослое является то, что окисленная оболочка не подвергается абразивному истиранию как при обжиге в пересыпающемся слое и сохраняется до стадии вспучивания.
Это обеспечивает вспучивание гранул при оптимальной температуре без межзернового агрегирования.
Рисунок-1. Технологическая схема обжигового агрегата. Кольцевая печь для получения керамзита способом термоудара.
1- кладка печи, 2-газовоздухопроводы, 3-выгружатель слоев, 4-вентиляционная система, 5- дутьевые вентиляторы , 6-аэрожелоб, 7 вращающийся под печи, 8-привод пода.
Кольцевая печь с внешним диаметром 15 м состоит из стационарных стен и свода, вращающегося футерованного пода , опорно-упорной системы и ванн гидрозатвора. Толщина стационарных ограждений печи 0,8 м, футеровка пода -0,5 м. Диаметр средней окружности пода и ее длина соответственно- 11,2 и 35,5 м( в том числе 30 метров -зона обжига ), ширина канала печи -2,4 м, высота от поверхности пода до замка свода -0,75 м.
Кольцевой канал заканчивается дымоотборной шахтой, из которой дымовые газы подаются в слоевой подготовитель и далее выбрасываются в атмосферу с помощью концевого дымососа. В обжиговом агрегате технологический процесс осуществляется следующим образом:
Термоподготовительные сырцовые гранулы подаются монослоем барабанным разгружателем на вращающийся под печи и перемещаются в зону горения топлива где происходит их вспучивание. Керамзит с поверхности пода удаляется выгружателем и охлаждается в холодильнике. Полученные в период эксплуатации технологические и теплотехнические показатели опытно-промышленного агрегата приведены в таблицу№ 2, в сравнении с аналогичными характеристиками однобарабанной печи 2,5 х 40 м Кольчугинского ССК.
Таблица №2. Физико-механические показатели печных агрегатов
Эти данные а также результаты испытаний привозных глин свидетельствуют о снижении насыпной плотности керамзита на 25…40 % и удельного расхода топлива на 35…45 % по сравнению с производством в однобарабанных печах. Более высокие показатели обжигового агрегата с кольцевой печью обусловлены его следующими тепло-технологическими особенностями.
Обжиг монослоя гранул в стационарных условиях осуществляется при оптимальных температурах вспучивания с перепадом по ширине канала печи ± 5°С без опасности интенсивной агломерации материала. Небольшие конгломераты, образованные точечными сварами гранул, легко разрушаются при падении в приемную течку.
Стабильность температурного режима в печи позволяет использовать для производства керамзита глины с короткими ( менее 50°С) температурными интервалами вспучивания. Следствием интенсификации процесса теплообмена является повышение скорости нагрева материала до 300…350°С/мин, чем обеспечивается скоростной режим обжига-термический удар.
Данные факторы обеспечивают снижение насыпной плотности керамзита на 25…40 % по сравнению с производством во вращающихся печах. Более совершенная тепловая схема кольцевой печи по сравнению с барабанными обеспечивает снижение расхода топливана обжиг в результате снижения теплопотерь с отходящими печными газами при сжигании топлива при относительно небольших коэффициентах избытка воздуха (а=1,3…1,35).
Это объясняется наличием многочисленных горелочных устройств и хорошей герметизацией печного пространства. А также увеличением толщины теплоизоляции, рекуперацией тепла отходящих печных газов путем подогрева первичного воздуха до 300…350°С.
Эти факторы, а также применение эффективного запечного теплообменника-слоевого подготовителя -обеспечивают снижение удельного расхода топлива на 52…60 кг/м³условного топлива. Конструктивные особенности кольцевой печи обеспечивают более высокие эксплуатационно -технические показатели по сравнению с барабанными печами.
При этом существенным преимуществом является сокращение эксплуатационных расходов на ремонт футеровки печи, что обусловлено долговечностью стационарной кладки печи и футеровка пода.
stroivagon.ru