Изготовление стекла – Производство Стекла. Как делают стекло в 2019 году
Изготовление автостекла на заказ
Есть много ситуаций, когда изготовление стекла выгоднее, чем покупка: стекло стоит на раритетном или редком автомобиле, оригинальное стекло дорогое, а срок его поставки очень долог, нужно стекло с нестандартными опциями (тонировка, светозащитная полоса, обогрев).
Предлагаем услугу по изготовлению автомобильных стекол (триплекс и закалённые) по Вашим размерам или образцу. Также, мы изготавливаем стекла с полным «невидимым» электрообогревом для любых автомобилей и других видов техники.
Возможно, нужное стекло уже есть в нашем каталоге стекол.
Мы можем изготовить стекло на заказ триплекс со светозащитной полосой сверху, с зеленоватым оттенком (атермальное) либо бесцветное. Обычно триплекс на заказ изготавливается для лобовых стекол, реже для боковых и задних. Закаленное стекло (сталинит) заказывается для боковых окон или при заказе стеклопакета.
Изготовление автостекла становится единственно возможным решением для остекления аварийного кузова. Если оконный проём деформирован и стандартное стекло в него не встаёт, мы изготовим стекло триплекс или закаленное непосредственно по размерам кузова.
К изготовлению автостекла на заказ прибегают и в случае самостоятельного оборудования оконных проёмов в кузове автомобиля. Обращайтесь, и мы проконсультируем Вас по вопросам установки стекла при переоборудовании кузова.
Что нужно, чтобы изготовить автостекло на заказ
Заказать изготовление автостекла можно одним из способов
1. По образцу
Если старое стекло сохранило свою форму контуры, мы сможем изготовить по нему шаблон-лекало для нового стекла. Если стекло имеет своего «двойника» в зеркальном отражении, — это характерно для боковых стекол, мы изготовим шаблон, используя размеры «двойника».
2. По чертежу
Чертёж плоского или выгнутого в одной плоскости несложного стекла под силу выполнить любому человеку с минимальными инженерными навыками. Можете прислать свой чертёж по электронной почте и наши технологи ответят о возможности изготовления стекла по чертежу и его стоимости.
3. По месту установки стекла
Если элемент машины, в котором надо заменить стекло, можно снять, — привозите его. Как правило к таким элементам относятся двери и открывающиеся окна на рамке. Мы сами измерим, изготовим стекло по размерам, и установим его. Вы получите готовую дверь или окно со стеклом.
4. Выездной замер и замена стекла
Если ни один из вышеперечисленных способов Вам не подошёл, можете воспользоваться услугами выездного замера и устанавки стекла. В этом случае все риски, связанные с неточными размерами, мы берём на себя.
www.steklolux.ru
Производство из вторичного стекла — битого или стеклотары: товаров, изделий и другой продукции, а также способы переработки таких отходов и что из них можно сделать
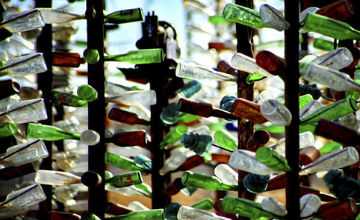
Отходы стекла — это одни из немногих материалов, которые не разлагаются в природной среде.
Поэтому их вторичное использование — это не только способ снижения производственных затрат, но и эффективный вклад в дело защиты экологии родного края.
Повторному использованию подлежат не все виды стекла.
Из-за сложности обработки из общей массы отходов рекомендуется исключить:
- материал с армосеткой;
- зеркальное стекло;
- триплекс.
На начальном этапе стеклопереработки проводится сортировка сырья по цветовой гамме. Смешанная сырьевая масса имеет ограниченную сферу применения, поэтому низко ценится.
Перед отправкой на измельчение стекло очищается от мусора и примесей.
Раздробленная масса промывается, пропускается через магнитные улавливатели и вакуумную камеру и отправляется в стеклоплавильную печь.
Дальнейшая судьба получившегося материала зависит от того, с какой целью планируется его использование.
В данной статье мы расскажем подробнее о том, какие способы вторичной переработки стеклобоя существуют, а также о том, какие товары и изделия можно из него производить.
Что можно сделать из стеклосырья?
В производстве стройматериалов стеклобой все чаще начинает использоваться в качестве дешевого наполнителя.
Стекольные заводы добавляют в шихту при варке стекла определенную долю стеклосырья.
Отходы с низким оптическим индексом используют для производства облицовочных панелей, стеклотары, материала для кровельных работ, пеностекла.
Еще одно направление использования — производство гласасфальта, абразивных материалов.
Производство пеностекла
Первые упоминания о пеностекле датируются 30-ми годами прошлого столетия. Тогда же появились первые технологии его изготовления и наметились пути возможного использования.
Основным источником сырьевого материала для изготовления пеностекла является стеклянный лом, который образуется на предприятиях по производству стеклянных изделий и в избытке присутствует в составе ТБО.
За прошедшие годы технологические процессы «отточились», возросло качество готовой продукции.
Стадии производства
Весь производственный процесс базируется на свойстве газообразователя свободно перемещаться в жидкой стеклянной массе. При выходе наружу газообразной составляющей, создается устойчивая пористая стекольная структура.
Отжиг затвердевшего пеностекла повышает прочность материала, увеличивает срок его полезного использования.
В общих чертах процесс изготовления пеностекла выглядит следующим образом:
- Подготовительные работы. Собранное сырье тщательно очищается от посторонних включений, промывается и просушивается.
- Дробление стекла. Специальные машины измельчают стекломассу до состояния мелкого порошка.
- Вспенивание стекломассы. В полученный на предыдущем этапе обработки порошок добавляется газообразовательная смесь. Полученная масса отправляется в стеклоплавильную печь для нагревания до температуры порядка 800 градусов С.
- Охлаждение продукции с последующим отжигом.
Термическая обработка способствует вспениванию жидкого стекла.
В зависимости от нюансов технологического процесса, получается пеностекло следующих видов:
- Гранулированное. Для изготовления продукции используются вращающиеся печи, в которые помещают заранее окатанные заготовки.
- Плитное. Для производства данного вида продукции используются печи туннельного типа. Отформованная готовая продукция подлежит последующей распиловке для получения изделий строго заданного размера.
Характеристики пеностекла:
- отличная теплоизоляция;
- пожаробезопасность;
- инертность;
- морозостойкость;
- экологическая безопасность.
Сфера использования материала:
- строительные работы различного назначения;
- промышленность, включая атомную.
Изготовление стекловаты и стекловолокна
До 80% компонентного состава стекловаты — сода, известняк, бура, доломит и песок — может быть заменено стеклянным боем.
Производство стекловолокна может быть организовано как в одну, так и две стадии:
- сбор стеклобоя и его очистка;
- закупка вспомогательных материалов – красителей и осветлителей, ускорителей варки и глушителей;
- приготовление шихты;
- размягчение стекла;
- выработка первичных стеклозаготовок;
- плавление стеклянных заготовок с вытягиванием стекловолокна.
Более экономичный, с точки зрения расхода энергии, одностадийный способ производства заключается в вытягивании стекловолокон при первой расплавке сырья.
При недостатке сырьевого материала в рабочую массу можно добавлять обломки керамики или шлак.
Обработка полимерами придает стекловате свойства, за которые она ценится потребителями:
- устойчивость к вибронагрузкам;
- отличная тепло- и шумоизоляция;
- повышенная упругость;
- нетоксичность;
- химическая инертность;
- пожаробезопасность;
- устойчивость к «биологической» угрозе – порче грызунами, росту плесени.
Используется стекловата на производстве и в быту в качестве теплоизоляционного материала и для создания шумоизоляции.
Подробнее о стекловате читайте здесь.
Вяжущие смеси для строительных работ
Мелкозернистый бетон, щелочеземельная вяжущая масса – строительные смеси, для изготовления которых используется мелкофракционный стеклобой.
Инновационные технологии позволяют получить связующие материалы с отличными физико-механическими свойствами.
Рассмотрим подробнее преимущества использования стекла в смеси с бетоном и разновидности стеклобетонов.
Бетон с добавлением стеклоотходов
Желание получить прочный и в то же время упругий строительный материал натолкнуло строителей на мысль добавлять в привычную смесь из цемента, песка и щебня с водой фрагменты стекла.
Полученный материал обладал следующими свойствами:
- высокая прочность с достижением максимальных значений после четырех неделе выстаивания;
- быстрое затвердевание, позволяющее продолжать работы уже на следующие сутки после заливки бетонной смеси;
- сейсмоустойчивость;
- устойчивость к неблагоприятным условиям внешней среды.
Стеклобетон быстро заполняет пространство любой площади, не боится влаги.
Разновидность стеклобетонов:
- стеклоармированный;
- со стеклофиброй;
- с оптиковолокном;
- со стеклобоем;
- с жидким стеклом.
Не все виды стекла можно безопасно подвергать вторичному использованию.
Отходы кинескопов, особенно старых телевизоров, при переработке выделяют вредные соли бора, свинца и бария.
Разработки российских ученых позволили создать технологию изготовления стеклобетона, где неиспользуемый ранее лом телевизионных и компьютерных мониторов служит добавкой, придающей готовому бетону свойство защиты от ионизирующего излучения.
Отделочные материалы
Широкое применения в области производства строительных работ находят отделочные материалы из стекла. Перечислим, что можно производить из битого стекла.
Стеклянная плитка
Стеклоплитка – это эффективная защита зданий от неблагоприятного воздействия внешней среды. Технологически возможен выпуск изделий различного размерного ряда, формы и цветовой гаммы. Итальянские производители плитки выпускают свыше 100 наименований стекломозаичных панелей.
Смальта
Изделия, полученные путем литья стеклянной массы или прессования мелкофактурного стекла, используются для декорирования фасадов, изготовления панно и других элементов декора помещений. Высокий потребительский спрос на изделия объясняется их эксклюзивностью и доступной ценой.
Подробнее о смальте — здесь.
Декоративная крошка
Оформление внутренних и внешних интерьеров декоративной стеклокрошкой позволяет значительно сократить расходы на проведение отделочных работ.
Изделия из гранул размером до 1 см прекрасно смотрятся в помещениях любого назначения.
Стеклокрошка изготавливается как из окрашенного, так и бесцветного стекла.
Пенодекор
Еще один вариант декорирования помещений – создание панно из плиток, покрытых стеклянной пленкой. Покрытие для облицовочного материала изготавливается из стеклобоя широкой цветовой гаммы.
Сигран
Изделия из прессованных стеклоотходов, внешне имитирующие мраморную или гранитную поверхность, называются сиграном.
Сигран имеет стеклокристаллическую структуру, придающую материалу прекрасные светроотражающие свойства.
Создание витражей для внутренних и внешних дизайнов помещений – одно из направлений использования сиграна.
Стеклокристаллит
Плиты из бесцветных или окрашенных стеклянных гранул, полученные путем их сплавления, широко используются для отделки полов, внутренних и внешних стен зданий. Плиточные панели выпускаются квадратной и прямоугольной формы.
Стеклокремнезит
Плиточные изделия, полученные путем нагревания стеклогранул и наполнителей природного происхождения, часто применяются для облицовки и создания декоративных поверхностей.
Стеклянная черепица
Светопрозрачный облицовочный материал для кровли популярен в европейских странах.
Такая черепица используется для создания прозрачных, пропускающих солнечные лучи зон на крышах из бетонных и керамических материалов.
Стеклянные облицовочные материалы – это гигиенически безопасные изделия, устойчивые к низким температурам, эстетически привлекательные, имеющие долгий срок службы.
Микроизделия
Стеклошарики и микросферы, микроптарики и бисерные шары цельные и пустотелые – изделия из стеклобоя от производства окон, нашедшие применение в дорожном хозяйстве и медицине, строительстве и промышленности.
Мелкоразмолотые частицы стекла нагреваются до высоких температур с последующим формированием микросфер. Охлаждение продукции, ее очистка от продуктов сгорания и сортировка по размерам завершают процесс изготовления легкого светопрозрачного, инертного материала.
Стеклянная тара
Производство банок и бутылок из стеклоотходов набирает все большую популярность в нашей стране.
Доступность и низкая стоимость сырья, быстрая окупаемость затрат, элементарность технологического процесса позволяет даже неспециалисту наладить производственную линию в домашних условиях.
Основные этапы изготовления стеклотары:
- приобретение необходимых компонентов;
- подготовка шихты;
- тепловая обработка стеклянной массы;
- формование и отжиг продукции;
- проверка качества и фасовка.
Некоторая толика усилий по поиску покупателей продукции — и бизнес по выпуску тары из стекла можно считать налаженным.
Жидкое стекло
Изготовление жидкого стекла предполагает использование кремноземного сырья.
В качестве него с успехом применяется стеклянный бой.
Технология производства строится на измельчении стеклосырья, его обработке щелочью и добавлении в рабочую массу соды и кварцевого песка.
Плавление полученного состава дает всем известный водный раствор силикатов, широко используемый при производстве стройматериалов.
Гласасфальт
Смесь стекла с асфальтом, иначе называемая гласасфальт, на три четверти состоит из стеклянного боя.
Каменная мука и ингредиенты, используемые для производства асфальто-бетонной смеси – все это остальные составляющие материала, служащего для формирования дорожного покрытия нового поколения.
Преимущества использования гласасфальта:
- возможность использования при низких температурах;
- отличная видимость в ночное время, благодаря эффекту светоотражения;
- высокая степень сцепления с колесами автотранспорта;
- более долгий срок эксплуатации.
Стеклоотходы в интерьере
Декупаж – искусство, дарящее вторую жизнь ставшим ненужными бутылкам и тарелкам, банкам, кружкам, стеклянной мебели и даже утратившим первоначальную привлекательность елочным игрушкам.
Это настоящая находка для людей творческих, не боящихся кропотливого труда.
Немного бумаги, клея и лака – и в руках мастера рождается маленький шедевр. Перечень поделочных материалов, подходящих для изготовления украшений очень широк и ограничивается только вашей фантазией.
Изготовление картин из стеклобоя, мозаичных панно, декора для фоторамок, женских украшений – все это может стать не только способом переработки ненужного стекла, но и процессом создания настоящих предметов искусства.
Идеи использования стеклосырья
Существует еще несколько вариантов того, что можно сделать из стеклянных отходов:
- фильтр сточных вод;
- дренажное покрытие вокруг строения;
- теплоизолятор для потолков и напольных покрытий.
Видео по теме
В данном видео описаны основные этапы вторичной переработки стекла.
Итоги
Стекло – материал удивительный. Пожалуй, это единственное вещество, которое можно без остатка использовать повторно.
Существует множество проверенных, отработанных годами технологий, приносящих стабильный доход. В то же время остается достаточное пространство для рождения и реализации новых творческих идей и задумок.
rcycle.net
Завод по производству листового стекла, изделий в Москве и Московской области, цены от 424 руб
Любое предприятие, которое планирует выпускать качественную продукцию, должно быть укомплектовано современным и высокотехнологичным оборудованием. Но этого мало, также необходим квалифицированный, ответственный и слаженный коллектив. Наше производство стекла обладает всеми необходимыми требованиями – у нас есть команда профессионалов своего дела, а также современное европейское стеклообрабатывающее оборудование.
Основные этапы производства стекла
Данный процесс включает несколько стадий.
- Подготовка сырья и необходимых ингредиентов. Главные составляющие — кварц и песок. Их доля в составе стека — 70–75 %. Помимо этих элементов необходимы марганец, никель, хром, сода, свинец и другие компоненты для придания различных оттенков и уменьшения температуры плавления.
- Плавка. Подготовленный и точно взвешенный состав направляют в печи, где происходит его нагрев до температуры около 1600 ˚C. Задача на этой стадии производства стекла — получить однородную массу без пузырьков газа.
- Охлаждение расплавленного состава. Далее материал в жидком виде погружается в специальную емкость с оловом, в которой температура состава снижается до 950–1000, а после остужения она составляет уже 550–600 ˚C.
- Резка и обработка. Следующий этап производства стекла начинается, когда заготовка достигает температуры 250 градусов. Материал нарезают, шлифуют, фрезеруют различными методами, обрабатывают кромки и т. д.
- Декоративная обработка. Заготовки подвергаются фигурной резке, сверлению отверстий, фрезеровке с помощью лазера или пескоструйной машины. Если требуются выполнить сложные декоративные украшения, то используется лазерная гравировка или УФ-склейка.
Кроме того, в производстве стекол применяются различные способы повышения прочности и безопасности изделий в эксплуатации: закалка, ламинирование и т. д. Наша компания также выпускает материалы для витрин магазинов и выставочных павильонов по технологии оптивайт.
Наше производство стекла
Загрузчик стеклянных листов Hager и автоматический стол резки итальянской компании Intermac позволяют быстро и точно производить резку материала различных толщин.
Высокопроизводительный многофункциональный обрабатывающий центр с ЧПУ фирмы Intermac (Италия) позволяет добиваться высокой точности и качества обрабатываемых изделий.
И еще один итальянский высокоточный обрабатывающий центр с ЧПУ NRG 330/4 POWER-JET фирмы GLASTON-Bavelloni, предназначенный для выполнения сложной высококачественной обработки стекла в процессе производства.
Вторая печь триплексования LAMIFLEX также по технологии EVA изготавливает панели из различных видов стекол, как сырых, так и закаленных с использованием разнообразных вставок: тканей, металлов, цветных пленок и многого другого. Максимальные габариты изготавливаемых деталей 1800 х 3600 мм.
Качественную обработку кромки материала производят кромочные станки итальянской компании Z.Bavelloni.
Итальянский станок с ЧПУ Bottero 810BCS для обработки прямолинейной кромки. Позволяет обрабатывать стекло толщиной от 3 до 55 мм и углом фаски от 0 до 45 градусов.
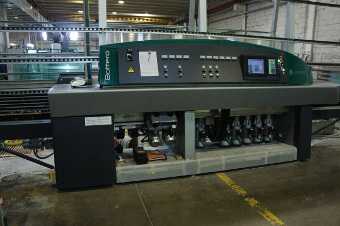
Для производства безопасного закалённого стекла установлена финская печь термической обработки Tamglass.
Изготовление триплекса осуществляется с помощью вакуумной электрической печи.
nayada-glass.ru
Отраслевая энциклопедия. Окна, двери, мебель
В этой статье описывается история возникновения стекла и развития стекловарения в мире от времен Древнего Египта до наших дней. Особое внимание уделено методам производства оконного стекла, использовавшимся в различное время.
Происхождение стекла
Изготовление листового стекла началось около 2000 лет назад. Но до его появления уже существовали основные приемы работы с расплавленным стеклом и разнообразная техника изготовления несложных изделий из стекла в виде бус, сосудов и браслетов.
Возникновение древнего стеклоделия восходит примерно к III тыс. до н. э. К этому периоду древними мастерам создан новый материал – стекло. Создание стекла по масштабам открытия — колоссальное научно-техническое достижение, его появление в истории техники и культуры может быть сопоставлено с открытием металлов, керамики и металлических сплавов.
Как, где, когда и кто начал делать искусственное стекло? На этот вопрос существуют разные версии. Стекло – искусственный материал, который создан человеком, но известны и природные стекла — обсидианы, которые образуются в магматических расплавах при высоких температурах во время извержения вулканов и падение метеоритов. Обсидианы представляют собой полупрозрачные черные стекла, обладающие высокой твердостью, и коррозионной стойкость и использовались в древности в качестве режущего инструмента. Некоторые считают, что именно обсидианы толкнули человека на создание их искусственных аналогов, однако области распространения природных и искусственных стекол не совпадают. Наиболее вероятно, что представления о стекле развивались в тесной связи с изготовление гончарных изделий и металлообработкой. Возможно, на ранних стадиях стеклоделия древние мастера увидели аналогии в свойствах стекла и металлов, которое и определили технологические приемы обработки стекла. Признав стекло аналогичным металлу (пластичность в горячем состоянии, твердость в холодном), древние создали возможность перенести в стеклоделие приемы обработки металлов. Таким путем были заимствованы тигли для варки стеклянной массы, формы для отливки изделий, технологические приемы горячей обработки (литье, сварка). Этот процесс происходил постепенно, особенно на первых этапах, настолько различны по своей природе стекло и металл.
Наиболее ранняя «теория» происхождения стекла – предложена римским ученым Плинием Старшим в «Естественной истории»:
«Однажды, в очень далекие времена, финикийские купцы везли по Средиземному морю груз добытой в Африке природной соды. На ночлег они высадились на песчаном берегу и стали готовить себе пищу. За неимением под рукой камней обложили костер большими кусками соды. Поутру, разгребая золу, купцы обнаружили чудесный слиток, который был тверд как камень, горел огнем на солнце и был чист и прозрачен как вода. Это было стекло».
Рассказ этот мало достоверен, даже сам Плиний начинает его cловами «fama est…..» или «по слухам…», потому что образование стекла при температуре пламени костра на открытом пространстве произойти не может. Всего вероятнее предположение немецкого ученого Вагнера, который связывает появление стекла с получением металлов. В процессе плавления меди и железа образовывались шлаки, которые могли под действием тепла превращались в стекло. Сейчас трудно установить, как именно было изобретено стекло, но без сомнений это открытие было случайным.
Самые древние изделия имели только стекловидный слой на поверхности фаянса, и найдены в гробнице фараона Джосера (III династия Древнего царства в Египте, 2980-2900 г.г. до н.э). Образцы стекла в виде слитков, датируемые XXII-XXI вв. до н. э., обнаружены при раскопках в области Древнего Двуречья.
Стеклоделие в Древнем Египте и Месопотамии
Наиболее ранние археологически известные стекольные мастерские датируются серединой II тыс. до н. э. Необходимо отметить, что сначала был получен сам материал (стекло), а затем осознается его новизна, и раскрываются его свойства. Приемы обработки нового материала подбираются применительно к его свойствам: вытягивание, сгибание, накручивание. Лишь со временем были подобраны и приспособлены и другие приемы: литье, прессование, обкатка.
История стеклоделия начинается с изготовление бус. Новый материал нашел свое применение в непроизводственной сфере, и изделия из него приравнивались к ценностям благородных камней и самоцветов. К древнейшими изделиями из стекла считаются стеклянные бусы царицы Хатшепсут, которая правила Египтом в 1525-1503 гг. до н. э. и стеклянный кубок, имеющий иероглифическую надпись с именем фараона Тутмоса III, относящийся ко времени Нового царства.
К середине II тыс. до н. э. стеклоделие сложилось в основных чертах почти одновременно в разных очагах древнейших цивилизаций Египте и Месопотамии. Единственным источником, на основании которого можно судить о становлении и начальных этапах истории стекла и его происхождении являются готовые изделия: бусы, вставки, сосуды. Как считают ученые, бусы для египтян выполняли функцию амулетов.
Начиная с середины VIII в. до н. э. набор найденных находок расширяется и к бусам и сосудам прибавляются перстни, браслеты, ритуальная и туалетная посуда, которых стали находить не только в районе Средиземноморье, но и на Кавказе и Западной Европе. Значительно повышаются декоративность и сложность найденных изделий. Техника изготовления изделий усложняется, мастера наряду с формовкой, навивкой и литьем, освоили и другие приемы работы с расплавленным стеклом: резание, гравировку, шлифовку, полировку и прессование в формах, различных по конструкции и материалу. Технические приемы обработки стеклянной массы сопровождалось усложнением инструментария и оборудования мастерской.
Изобретение процесса выдувания стекла
К началу римского периода стеклоделием был накоплен весьма большой производственный опыт и знания, чтобы сделать подлинный переворот в области технологии изготовления изделий из стекла.
Первой «революцией» в стекловарении считается изобретение метода выдувания стекла. Процесс выдувания изделий из расплавленной стекломассы начался с важнейшего изобретения – стеклодувной трубки сирийскими мастерами между 27 г. до н. э и 14 г. н. э. С открытием процесса выдувания стеклянных изделий Сирия на целые сотни лет становится крупнейшим центром стеклоделия. Изобретение выдувания привело к рождению нового качества и составило основу не только древнего, но и современного методов изготовления стеклянной посуды, а впоследствии и оконного стекла
Выдувание – ранее вспомогательная операция, в римское время стало использоваться как самостоятельный прием. После набора стекломассы на стеклодувную трубку мастер выдувал исходную заготовку в деревянную форму и получал различные стеклянные полые изделия в виде кувшинов, банок, кубков флаконов. Наряду с простой посудой мастера выполняли и декоративные уникальные предметы, украшенные нитями и накладом из цветного стекла.
Первое оконное стекло
Первое оконное, по настоящему плоское стекло впервые появилось значительно позже, в Древнем Риме. Оно было обнаружено при раскопках Помпеи и датируется годом извержения вулкана Везувий, 79 г. н. э. Оконное стекло получали методом литья на плоскую каменную поверхность. Конечно, качество стекла при этом сильно отличалось от современного. Это стекло было окрашенным в зеленоватые тона и матовым (бесцветное стекло в то время изготавливать еще не умели), содержало большое количество пузырей, что говорило о низкой температуре варки, и было довольно толстым (около 8-10 мм). Но, тем не менее, это был первый случай применения стекла в архитектуре, что дало значительный толчок к дальнейшему развитию стекловарения и распространению стекла по всей Европе.
Краун процесс
2-я революция в стекловарении произошла приблизительно в начале II в., когда сирийские мастера изобрели совершенно новую для тех времен технологию производства плоского стекла – краун (crown) или как его в России называли лунный способ. Это идея возникла, возможно, при выдувании больших плоских тарелок. Стекло изготавливались методом выдуванием больших пузырей, которые на следующей стадии отделялись от стеклодувной трубки, и прикреплялась к другой трубке — понтии. После интенсивного вращения на понтии, исходная заготовка под действием центробежных сил утончалась и превращалась в плоский круглый диск (см. рис.). Диаметр этого диска мог достигать 1,5 м. Из него уже после охлаждения вырезали куски стекла квадратной и прямоугольной формы. Центральная часть диска имела утолщение – след от понтии, который назывался «бычьим глазом». Как правило, эта часть диска не использовалась и шла на переплавку, однако, в некоторых средневековых зданиях эти кругляшки до сих пор сохранились (см. рис.).
Эта технология позволяла получать стекло довольно хорошего для тех времен качества, практически без искажений. Неудивительно, что эта технология просуществовала вплоть до середины XIX века. Так, известный всем и один из старейших в мире производителей стекла — английская компания Пилкингтон (Pilkington) полностью прекратил использовать краун процесс только в 1872 г.
Однако существовала и проблема — ограничение по размерам. С помощью краун процесса невозможно было получить стекло большого размера. Поэтому на протяжении многих лет в разных странах Европы осуществлялись попытки усовершенствования этой технологии, что привело к созданию нового метода производства стекла – метода выдувания цилиндров.
Производства оконного стекла цилиндрическим способом
В целом этот метод был очень похож на краун процесс, но при этом стеклодув набирал стекло из горшка в несколько приемов и раздувал заготовку (пульку) в форму цилиндра при постоянном вращении. Для формования цилиндрической формы мастер раскачивал заготовку в специальной прямоугольной яме. После затвердевания заготовки, суженные концы отделяют специальным нагретым крюком. Затем внутри охлажденного цилиндра делают продольный разрез и выправляют в плоские листы в особых “правильных печах”, где цилиндры постепенно разогреваются до размягчения на плоских основаниях их глины и разглаживаются в лист деревянной чуркой, закрепленной на железный стержень. К концу XIX века для выдувания цилиндров стали использовать воздушные насосы, а вскоре появился и метод механического вытягивания цилиндров (см. рис.).
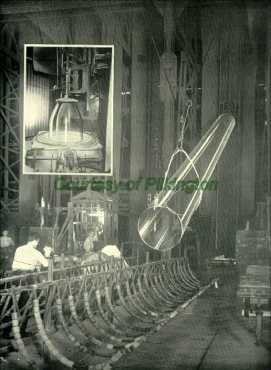
Применение более эффективного метода производства оконного стекла позволил увеличить размер листового стекла и снизить количество отходов стеклянного боя. Так, установленные в 1910 году на одной из английских фабрик Пилкингтон (Pilkington) воздушные машины американского инженера Джона Любберса (John H. Lubbers) позволили получать стеклянные цилиндры длиной до 13 м и диаметром до 1 м.
Производство оконного стекла методом вытягивания из расплава
Уильям Кларк из Питтсбурга первый предложил способ производства листового стекла вытягиванием со свободной поверхности расплав. В 1857 г. он представил английский патент, согласно которому, формование плоского листа осуществляется медленным вертикальным вытягиванием затравки с поверхности расплава. В течение последующих 50 лет старались решить основную проблему – сужение ленты стекла при вытягивании, но все попытки были неудачными.
В 1871 году бельгийский изобретатель Ф.Вэллин (F.Vallin) получил французский патент (№ 91787) на производство оконного стекла механическим вытягиванием стекла. Для непрерывной подачи расплава он предложил систему горшков, которые связаны между собой трубкой, так что стекломасса из одного горшка поступала в другой. В последний большой овальный горшок, который был заключен в трубу, опускалась металлическая пластина (затравка). Формование плоского листа происходило при движении этой пластины вверх. В трубе также располагались по бокам стекла воздушные трубки с отверстиями для охлаждения стекла. Лист стекла поддерживался роликами, покрытыми асбестовой тканью. Вытягивание стекла может происходить в двух направлениях: вертикальном и горизонтальном. В последнем случае предусматривался специальный металлический валок. Вэллин был гениальным изобретателем и предложил практически все основные элементы механического вытягивания, которые в 20 столетии будут применяться во всех способах вытягивания стекла. В то время, когда ванные печи были неизвестны, он представил систему стекловаренных горшков, в которых осветленная стекломасса поступала снизу по трубкам из одного горшка в другой, до основного, из которого происходило вытягивание стекла. Эта система непрерывной подачи расплава стала основой появления ванных стекловаренных печей. В 1890 году Вэллин основал в Гифорсе компанию по производству оконного стекла механическим вытягиванием.
В 1905 году бельгийский инженер Эмиль Фурко (Emile Fourcault) предложил свой способ вертикального вытягивания стекла. При этом старейшем способе (ВВС) используется шамотная лодочка, из щели которой под действием гидростатического давления вытекает постоянный поток стекла. Скорость вытягивание можно регулировать глубиной погружения лодочки. Лента стекла из лодочки поступала в шахтную камеру, где с двух сторон находятся водо-охлаждаемые трубки, и далее по роликам поступала в печь отжига. Для предотвращения сужения ленты по краям ленты были установлены бортоформующие ролики и охлаждаемые трубки. Толщина ленты стекла определялась скоростью вытягивания и температурой в зоне вытяжки («луковицы»). Первые машины Фурко для вытягивания листового стекла были установлены в Бельгии и Чехии в 1913 году. Производительность 11 машин, установленных на одной ванной печи, составляла 250 тонн стекла в день.
Процесс вытягивания стекла позволил производить дешевое оконное стекло с огненно-полированными поверхностями Основной дефект тянутого стекла появляется при формовании (вытягивании) и связан с нарушением плоскостности стекла. Такие нарушения приводят к оптическому эффекту линзы и искажению изображения. Тянутое (машинной выработки) оконное стекло широко применялось в строительстве для остекления окон и теплиц.
Производство оконного стекла методом литья и шлифования
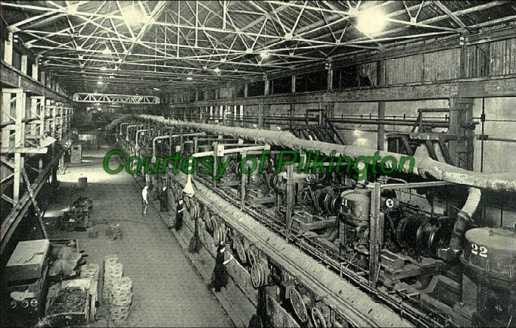
Как уже говорилось выше, и краун процесс и метод выдувания цилиндров, да и метод ВВС имели ряд недостатков, связанных либо с наличием оптических дефектов и искажений, либо с невозможностью получить листы стекла большого размера. Поэтому как альтернатива с начала XIX века в Европе использовался также еще один способ производства методом литья и последующего отжига литого прокатного стекла. В нем горшок с расплавленным стеклом выливался прямо на разливочный стол и прокатывался роликами. Для отжига применялась специальная печь с несколькими рядами полок, позволяющая увеличить загрузочную мощность. Прокатное стекло могло быть изготовлено любого требуемого размера и толщиной 3-6,5 мм. Этим методом изготавливали цветное и бесцветное узорчатое стекло, а также большие листы неполированного оконного стекла. Особой популярностью пользовалось узорчатое цветное стекло для остекления окон в церквях и соборах.
В дальнейшем с появлением потребности в более качественном стекле на финальном этапе стали применять абразивную обработку поверхностей стекла. В то время это был трудоемкий, длительный и многоступенчатый процесс, который включал перемещение горшка с расплавом стекла, отливку и раскатку в лист, отжиг, шлифовку и полировку. Время обработки стекла составляло около 17 часов.
В начале XX века рост автомобильной промышленности стимулировал развитие более эффективных высокопроизводительных методов производства полированного стекла. Одним из пионеров этого метода была также компания Пилкингтон (Pilkington), которая в 1923 году совместно с компанией Форд Моторс разработала и запустила непрерывный процесс производства прокатного стекла. Расплав стекла плавился в ванной печи и через сливное устройство непрерывным потоком проходил через водоохлаждаемые валы и прессовался до заданной толщины. Основная проблема заключалась в получении качественного расплава в ванной печи. В 1925 году этот метод был дополнен машиной для односторонней шлифовки и полировки. Следующим шагом к автоматизации производства была разработка машин для двухсторонней шлифовки и полировки стекла. После долгих экспериментов и трудных сборочных работ первая поточная линия производства полированного стекла была запущена на фабрике Пилкингтон в Донкастере (Великобритания) в 1935 году. Непрерывная лента стекла длиной 300 м двигалась со скоростью 66 м/час и обрабатывалась одновременно с двух сторон огромными плоскими шлифовальными дисками. Введение этой технологии явилось наиболее значительной разработкой в длинной истории производства полированного стекла.
Более дорогое полированное стекло обладало хорошим оптическим качеством, и с успехом использовалось для остекления зданий, витрин, транспорта, изготовления зеркал. Но процесс производства полированного стекла всегда отличался большой энергоемкостью, высокими операционными и капитальными затратами. Отходы стекла при шлифовке и полировке доходили до 20%. Так, например, производственная линия двухстороннего непрерывного шлифования и полировки компании Пилкингтон (Pilkington) в Коули Хилл (Великобритания) в 1944 году, включая стекловаренную печь, лер, станки для шлифовки и полировки растягивалась на более чем 430 м. Современники замечали с гордостью или сожалением, что производственная линия была на 21 м длиннее самого большого в то время океанского лайнера «Queen Mary».
К середине XX века назрела необходимость использования новых более простых и дешевых методов производства высококачественного стекла.
Переход на новые способы производства оконного стекла – флоат-процесс
Заслуга создания революционного способа производства полированного стекла (флоат процесс) принадлежит Сэру Аластару Пилкингтону (Alastair Pilkington).
Лайонел Александр Бетин (Аластар) Пилкингтон родился в 1920 году, после окончания школы в Шерборне поступил в Тринити Колледж в Кембридже, где получил свою первую научную степень в области механики. Во время войны он покинул университет и поступил на службу в Королевскую артиллерию. Участвовал в военных действиях в Греции и на Крите. После освобождения из плена в конце войны, он вернулся в Кембридж для продолжения учебы и решил продолжить карьеру как гражданский инженер. В марте 1947 году он был назначен техническим помощником на фабрике листового стекла Пилкингтон, а через два года выполняет обязанности производственного менеджера на фабрике в Донкастере. В 1952 году Аластар возвращается в Сент-Хеленс, и под его руководством начинаются экспериментальные работы над разработкой флоат процесса. В результате первых экспериментов, он предложил для формования и транспортировки ленты стекла использовать расплав металла. В 1953 году на первой опытной установке был изготовлен образец флоат-стекла (float-glass) шириной 300 мм. В 1955 году на новой экспериментальной установке было получено флоат-стекло шириной 760 мм, и правление Пилкингтон принимает смелое и рискованное решение о строительстве производственной флоат линии (float-line) шириной 2540 мм. Компания надеялась на успех, но в тоже время понимала, что в случае неудачи финансовые потери будут составлять миллионы фунтов. С другой стороны, успешный запуск линии гарантировал значительный и революционный скачок в технологии листового стекла за всю длительную историю производства стекла.
Производственная линия, работающая по флоат-методу, была введена в Коулей Хилле (Великобритания) 6 мая 1957 года. Многие в то время не верили в новый процесс, и говорили, что эта линия не произведет даже 1 m² стекла. Только через 14 месяцев было получено первое качественное флоат-стекло (float-glass) толщиной 6,5 мм, и 20 января 1959 года компания Пилкингтон официально опубликовала пресс-релиз, в котором представила флоат-процесс следующими словами:
«Флоат-процесс является наиболее фундаментальным, революционным и важным достижением в производстве стекла в 20 столетии»
В соответствии с разработанной компанией Пилкингтон (Pilkington) флоат-способом стекломасса из студочного бассейна при температуре 1100°С непрерывной лентой поступает из стекловаренной печи на поверхность расплавленного олова. Лента выдерживается при достаточно высокой температуре для удаления всех дефектов и неровностей на поверхности стекла. Так как поверхность расплавленного металла является идеально ровной поверхностью, то стекло приобретает “огненно-полированную” блестящую поверхность, которая не нуждается в дальнейшей шлифовке и полировке. При проведении экспериментов установлено, что расплавленная стекломасса не растекается бесконечно на поверхности расплавленного олова. Когда силы тяжести и поверхностного натяжения уравновешиваются, лента приобретает равновесную толщину около чуть меньше 7 мм. Для получения ленты стекла различной толщины были созданы методы, основанные на регулировании вязкости стекла в зоне формования и величины растягивающего усилия. Если необходимо получить толщину ленты стекла больше 7 мм, то ее сжимают несмачивающими бортовыми ограничителями.
В начале работе возникла проблема выбора расплавленного металла, который должен находиться в жидком состоянии в пределах температурного интервала от 600 до 1050°С, иметь низкие значения давления паров, а величина плотности должна быть выше, чем стекла. Исследования показали, что всем этим требованиям соответствует олово, которое почти не взаимодействует со стеклом, и является вполне доступным и дешевым продуктом. Но олово при высоких температурах окисляется кислородом с образованием оксидных соединений. Поэтому, чтобы исключить окисление поверхности расплава олова, во флоат-ванне необходимо создавать инертную атмосферу азота с малой добавкой водорода. После формования лента стекла охлаждается до 620°С и транспортируется в печь отжига.
Вклад участников
Толстов Илья
www.wikipro.ru
Описание состава и современного процесса изготовления оконного стекла
Стекло является одним из древнейших и практичных материалов, который и по сей день очень активно используется в самых разнообразных областях, от производства стеклянных электродов и оптоволокна до создания посуды и сувенирной продукции. Человечество более 6000 лет практикует изготовление разнообразных предметов из расплавленных стекломасс различного состава. Развитие цивилизации, появление новых технологий и модернизация оборудования позволили создавать разнообразные виды стёкол:
- Армированное с металлической сеткой внутри.
- Закалённое и термостойкое.
- Посудное, моллированное и тарное.
- С узорчатой, полированной, матовой и неполированной поверхностью.
- Кварцевые разновидности и хрусталь.
- Химико-лабораторное.
- Стеклоэмаль.
- Непрозрачные и прозрачные аналоги.
- Цветное стекло.
- Термохромные, электрохромные, атермальные и фотохромные листы.
- Пористые аналоги и пеностекло.
Отдельной группой изделий стоит выделить оконное стекло. Современная торгово-промышленная компания «Русский дом» профессионального уровня представляет продукцию собственного производства на официальном сайте. Мы работаем с крупными оптовыми покупателями и розничными клиентами. Наши квалифицированные специалисты рады проконсультировать клиентов и принять заказы на оригинальные изделия. Действует система впечатляющих скидок!
Состав стекломассы и создание продукции
Подробное описание процесса создания оконных стёкол может быть переполнено технической терминологией. Такой материал, как правило, сложнее читается посетителями сайта, поэтому мы постарались сделать наиболее понятное, ёмкое и в то же время информативное описание данного производственного процесса.
Сырьём для прозрачных и гладких листов привычного нам материала выступает многокомпонентная смесь, в состав которой входят определённые добавки и стеклообразующие элементы. По сути, основой являются силикаты кальция и натрия, сплавленные с двуокисью кремния. Зачастую битое или бракованное стекло активно используется для повторного производства. Если углубиться в состав, то можно выделить такие элементы, как:
- Доломит или пегматит.
- Кварцевый песок.
- Карбонат калия (поташ).
- Кальцинированная сода или сульфат натрия.
- Известняк или мел.
- Нефелиновый сиенит.
Если требуется придать материалу определённый цвет, в состав добавляют оксиды различных металлов:
- Титан и кобальт.
- Марганец и хром.
- Медь и ванадий.
- Никель и церий.
- Железо.
Кроме того, для глушения и осветления среди примесей могут присутствовать трёхокись мышьяка, окись бария, селитра, селен и сера, а также сернистые соединения свинца, кадмия, меди или железа.
Стоит сказать, что на данный момент используется два основных способа производства оконного стекла:
- Флоат – технология основана на подаче стекломассы в камеру с расплавленным оловом. После термического отжига заготовки подвергаются резке. Такой способ позволяет получить листы с минимальными искажениями и дефектами, обладающие идеально ровной поверхностью, которая не потребует полирования или шлифовки. Так и получается современное оконное стекло, толщину которого можно регулировать от 4 до 25 миллиметров.
- Фурко – метод представляет собой прокатывание стекломассы через специальные валики, после чего заготовки охлаждаются и режутся.
Флоат технология позволяет с лёгкостью изменить химический состав сырья, что повлияет на свойства изделий:
- Прочность и упругость.
- Поглощение и светопропускание УФ лучей.
- Диэлектрические свойства.
- Прозрачность и хрупкость.
- Теплопроводность.
- Плотность.
- Цвет.
Процесс изготовления происходит в несколько этапов:
- Подготовка компонентов – дробление и измельчение сырья.
- Варка (расплав) – сырьё плавится в специальных стеклоплавильных печах периодического или непрерывного типа действия при температуре 1100-1600 градусов Цельсия.
- Получение однородной массы – перемешивание стекломассы в гомогенизаторе.
- Формование в ванной с расплавом олова, футерованной огнеупорным материалом – осуществляется вытягиванием, литьём, прокатом, штампованием, прессованием или выдуванием.
- Отжиг – ступенчатое охлаждение.
- Измерение – лазерный сканер оценивает толщину листа.
- Резка – листы остывшего стекла разрезаются автоматически гидроабразивным или фигурным способом.
- Обрезка – специальный ролик обрезает края листов.
- Дополнительная обработка – полировка, гравировка и шлифование краёв (фаска, карандаш или фацет), декорирование (химическое травление, сверление и тому подобное).
- Контроль качества – осуществляется специалистами.
- Фасовка и хранение – товар фасуется, упаковывается и складируется.
Разумеется, каждый товар имеет определённые характеристики, исходя из которых, определяется его класс и стоимость. Цена формируется в зависимости от габаритов, состава, типа стекла, толщины, фактуры, наличия дополнительной обработки и прочих факторов. ГОСТ определяет несколько 8 марок стекла, подходящее для остекления зданий считаются изделия с маркировкой М4, М5 и М6.
Для получения наиболее подробной информации и заказа товаров рекомендуем связаться с менеджерами «Русский дом».
rusdoms.com
38. Стекло. Понятие, виды, способы производства изделий из стекла.
Стекло – материал аморфно-криталлической структуры, получаемый путём
переохлаждения расплава, состоящего из различных окислов, независимо от
химического состава и температурной области затвердевания, обладающий при
постепенном повышении вязкости механическими свойствами твёрдых тел. По
назначению: бытовые, строительные и технические стёкла.
По типу стёклообразователя: силикатные стёкла (кремнозём), боратные (B2O3),
фосфатные (Р2О5), смешанные (несколько различных стеклообразователей). По
типу стеклообразователя бытовые товары вырабатывают силикатными, реже –
смешанными. По химическому составу делятся на: обычное стекло, хрусталь,
специальные стёкла. Группа обычных стёкол представлена следующими видами:
натрийсиликатным стеклом (натрийизвестковым) и калийсиликатным
(калийизвестковым). Группа хрусталей включает в себя хрустальное стекло,
свинцовый хрусталь, высокосвинцовый хрусталь. Специальные — жаростойкое
стекло и ситаллы.
Способы производства:
Прессование – верхний диаметр больше нижнего, большая толщина стеной, рисунок
от формы, отсутст. Резкие грани и углы, наличие на дне маркировки.
Прессовыдувание – изделие с горлом, средняя толщина стенок, невысокая
гладкость поверхности, заметны боковые швы.
Выдувание ручное – разнообразная форма, очень гладкая поверхность,
разнообразное декорирование.
Выдувание механическое – чаще – стаканы, малая толщина стенок, крученность
стенок и дна, декорирование на готовых изделиях.
Гутенская работа – преимущественно большая толщина стенок, очень гладкая
поверхность, наличие налёпов.
Многостадийная выработка – очень гладкая поверхность, разнообразная форма,
прессованная ножка.
39. Украшения, наносимые на стеклянные бытовые изделия.
Декоративная обработка влияет на эстетические достоинства и цену изделий.
Украшения изделий классифицируют по стадии и методу нанесения, характеру,
сложности. По методу нанесения: украшения, выполненные вручную,
полумеханизированным способом, на механизированных линиях с применением
автоматов.
Украшения, наносимые в горячем состоянии. Сущ. Несколько групп.
1. Украшения, в основе которых – получение оптического эффекта или
рельефа поверхности. Это «валик», рифление, мелкие пузырьки, «мороз».
«Пулька» выдувается в черновой форме с углублениями или выступами. При
выдувании в чистовой форме создаётся оптический эффект волнообразной
поверхности или углублений, заполненных воздухом. «Мороз» — украшение в виде
сетки заплавленных трещин, напоминающих морозные узоры на стекле.
2. Украшения с орнаментами. Их получают при внесении заготовки стекла
донного цвета в полуфабрикат или готовое изделие другого цвета. Цветные нити,
полосы, пятна, налепы, крошка, украшения стеклотканью, акварельное пятно,
цветной наклад. Заготовки размягчённого цветного стекла в виде нитей, шнура,
кусочков или ажурной стеклоткани различными приёмами накладывают на
«Пульку». После формования получают украшения в виде витой или путанной нити,
полос, пятен, кружевного рисунка. Изображение эмблемы получают с помощью
штампа. Для высокохудожественных изделий применяют
3. Нанесение на поверхность изделия радужной плёнки осаждением
ирризирующих веществ. Изделие обрабатывают в специальной камере с парами
хлористого олова, азотнокислого стронция, хлористого бария. В зависимости от
соотношения этих соединений, температуры и времени выдержки создаётся эффект
бесцветной плёнки с синим или красноватым оттенком.
Способы декорирования изделий в холодном состоянии в процессе заключительной
обработки. Украшения, наносимые обработкой поверхности абразивами.
Шлифовка – рисунки в виде плоских сферических шлифов, ямок, тонких линий или
их сочетаний. Матовая лента, матовая шлифовка, пескоструйная обработка. В
сложной шлифовке имеются элементы гранения. Наносят украшения на автоматах.
Сплошная обработка поверхности – пескоструйная матовка.
Гранение – сочетание глубокой резьбы с плоскостными или выпуклыми элементами.
Поверхности граней отполированы до полной прозрачности. Алмазная грань (куст,
ромб, треугольник, медальон, звезда, камень, овал), широкая грань, литерная
грань, встречная грань. Применяют для украшения хрустальных изделий и
высокохудожественных изделий из цветного стекла.
Гравировка – сложные плоскостные рисунки с тонкой проработкой деталей.
Шлифующий материал – наждачный порошок, смешанный с машинным маслом. Для
граверных работ применяют также алмазный инструмент типа АПП, А2П, А5П.
Поверхность шелковистая, матовая.
Химические способы (травление) основаны на разрушении стекла плавиковой
кислотой. Химическая матовка, гильоширное, пантографное, глубокое и
художественное. Всю поверхность изделия обрабатывают в травильном растворе,
которую наносят кисточкой. Декорируют высокохудожественные изделия из
накладного стекла. Снимают слои различной толщины. Живопись, штамп, лента,
диффузное окрашивание, шелкография.
Для украшения прессовыдувной и многостадийной выработки широко применяют
матовую насечку, шелкографию, трафаретную печать.
studfiles.net