Производство арболита технология: Изготовление арболита своими руками: технология производства и самостоятельные работы
Изготовление арболита своими руками: технология производства и самостоятельные работы
Поэтапная технология изготовления арболита предвидит подготовку основания, определения компонентов и состава блочного материала. В данной статье рассмотрим особенности производства своими руками с применением необходимого оборудования, расчета массы и заливки.
Оглавление:
- Преимущества и недостатки арболита
- Технология производства арболита
- Подготовка основания для работы
- Компоненты и состав арболита
- Процесс и принципы изготовления
- Оборудование: применение на практике
- Блочные формы для арболита
- Процесс производства своими руками
- Советы экспертов при изготовлении блоков своими руками
Преимущества и недостатки арболита
Для многих строителей арболитные блоки являются ценным и качественным материалом для возведения домов.
1. Прочность материала составляет 600-650 кг/м3, что по компонентной структуре не уступает иному строительному материалу. Главной особенностью является пластичность, что формируется в результате использования древесины, которая качественно армирует блоки. Таким образом, арболит не трескается под тяжестью иных материалов, а может только слегка деформироваться сохраняя общую систему конструкции.
2. Стойкость к низким температурам, что очень важно в процессе возведения дома и его эксплуатации. Дело в том, что если здание нагреется и замерзнет несколько раз, то это не повлияет на качество материала. Фактически дом из арболита может простоять минимум 50 лет в любые погодные условия. Конструкции из пеноблоков не имеют подобных свойств, ведь при постоянном замораживании они быстро потеряют свою функциональность.
3. Арболит не поддается воздействию углекислого газа, так что не стоит беспокоиться о карбонизации блоков, ведь их структура не позволит превратиться материалу в мел.
4. Теплопроводность блоков свидетельствует о популярности материала. Сравнивая показатели, стоит отметить, что стена из арболита в 30 см равняется 1 метру толщины кирпичной кладке. Структура материала позволяет сохранять тепло внутри помещения даже в самые холодные зимы, что весьма экономично при строительстве.
5. Звукоизоляционные свойства свидетельствуют о высоком коэффициенте поглощения арболита, который составляет от 0,7 до 0,6. Для сравнения древесина имеет показатели 0,06 -0,1, а кирпич немного больше около 0,04-0,06.
6. Легкость материала, что позволяет сэкономить средства на заливку фундамента.
7. Арболит является экологически чистым и долговечным строительным материалом, что определяет компонентный состав блоков. После возведения дома он не образует плесень и грибок на стенах.
8. Материал является безопасным, так он не воспламенятся.
9. Арболитные блоки легко применять в строительных работах, поскольку без труда в них можно забить гвозди, просверлить отверстие, использовать шурупы и так далее. Внешняя структура материала позволяет покрывать его штукатуркой без использования специальных сеток и дополнительных утеплителей.
Мы рассмотрели преимущества арболитных блоков, но для полного воссоздания картины о данном строительном материале приведем некоторые недостатки:
1. Стеновая панель может не выделяться точными геометрическими параметрами, от чего для восстановления ровности стены используют вагонку, сайдинг или гипсокартон, а сверху все отделяют штукатуркой.
2. Блоки не являются дешевым строительным материалом, ведь изготовление щепы для арболита требует некоторых затрат. Делая расчеты по сравнению из газобетоном, данный строительный материал обойдется только на 10-15 процентов дороже, что не формирует полное преимущество.
Технология производства арболита
Изготовление арболита требует следованию технологиям производства с расчетом состава и объема для одного блока. Арболитные блоки представляют собой строительный материал простой по компонентному составу, в который входят древесина, вода, опилки, цемент и другие предметы.
Главной основой для производства считается древесная щепа. Составная часть арболитового блока определяет его прочность и устойчивость к повреждениям, что высчитывается высшим уровнем, чем у пено- или газоблоков. Производство в домашних условиях осуществить не сложно, однако необходимо придерживаться распределения массы предмета и следовать инструкции.
Подготовка основания для работы
Основной составляющей для изготовления щепы для арболита является соотношение пропорций стружки и опилок – 1:2 или 1:1. Все предметы хорошо высушивают, для чего их помещают на 3 – 4 месяца на свежий воздух, время от времени обрабатывая известью и переворачивая.
Примерно на 1 кубический метр средства потребуется около 200 литров извести 15-ти процентной. В них помещают все щепы на четыре дня и перемешивают их от 2 до 4 раз на день. Все работы проводятся с целью убрать сахар с древесины, который может спровоцировать гниение блоков. Щепу приобретают в готовом виде, однако, с помощью щепорезов можно сделать самостоятельно.
Компоненты и состав арболита
Компонентный состав арболита является самым важным этапом технологии производства и требует внимательного соотношения всех материалов. При изготовлении блоков важно следить за качеством и разновидностью приобретаемых материалов, которые определяют готовый строительный материал. После процесса изготовления в щепу добавляют следующие материалы, такие как:
- известь гашеную;
- жидкое стекло растворимое;
- портландцемент;
- хлористый калий;
- алюминий и сернокислый кальций.
Производство арболита в пропорциях представлено в таблице 1. Стоит учесть, что для всех компонентов масса рассчитана на четыре процента доли цемента. Данная компоновка помогает сохранить огнеупорность предмета и придает пластичности.
Таблица 1. Состав арболита по объему
Марка арболита | Цемент (М400) | Кол-во извести | Кол-во песка | Кол-во опилок | Получаемая плотность (кг/м3) |
5 | 1 | 1,5 | — | 15 | 300-400 |
10 | 1 | 1 | 1,5 | 12 | 600-700 |
15 | 1 | 0,5 | 2,5 | 9 | 900-1000 |
25 | 1 | — | 3 | 6 | 1200-1300 |
Процесс и принципы изготовления
Оптимальные параметры блоков для технологии производства арболита составляют 25х25х50 сантиметров. Установленные размеры удобны при кладке стен домов, а также в процессе промышленности. Заливка блока состоит из трех рядов смеси и арболита, после каждого этапа необходимо уплотнять раствор молотком, отделанным жестью.
Излишняя масса свертывается при содействии шпателя. Выдерживается блок при температуре 18 градусов тепла на раскрытом воздухе. По истечении суток арболит выстукивается из формы на ровную поверхность, где он скрепляется на протяжении 10 дней.
Оборудование: применение на практике
Для производства необходимо разное снабжение, например, станки для изготовления арболита, которые выбираются в соответствии с объемом продукции и количества сырья. Технология промышленного процесса должна отвечать требованиям и критериям СН 549-82 и ГОСТу 19222-84. В качестве основного материала для выработки выступают хвойные деревья. Раздробление древесины происходит с помощью рубильных машин, таких как РРМ-5, ДУ-2, а более скрупулезное дробление осуществляется на оборудовании ДМ-1.
Арболитовую смесь подготавливают со смесителями и растворителями различного цикличного воздействия на материал. Подвозят большие объемы обработанной смеси к формам с помощью приспособления в качестве бетонораздатчиков или кюбелей. Подъем или опускание машины должно осуществляться при параметрах 15о по верхнему подъему и 10о по нижнему, а скорость оборудования рассчитывается в 1 м/с. Разлив арболитовой смеси по формам делают на высоте до 1 метра.
Уплотнения раствора производят с содействием вибропреса или ручной трамбовки. Для производства небольшого количества блоков нужно применить мини-станок. Изготовление своими руками арболита не представляет особых трудностей, однако на промышленных объектах применяется специальное оборудование по смешиванию, изготовления блоков. На некоторых заводах присутствуют тепловые камеры с ИК-излучением или ТЭНом, что позволяет определить нужную температуру для высыхания блоков.
Блочные формы для арболита
Существуют разные блочные формы для обработки арболита, а примерные величины могут составлять: 20х20х50 см или 30х20х50 см. Выпускаются предметы и прочих размеров, особенно для постройки вентиляционных систем, покрытий и так далее. Формы можно приобрести в строительных магазинах или же подготовить все своими руками. Для этого, используют доски толщиной в 2 сантиметра, которые скрепляют до образования определенной конструкции. Внешне форма отделывается фанерой, или пленкой.
В зависимости от класса арболитовые блоки применяют в малоэтажном строительстве для возведения несущих стен, перегородок, а также для теплоизоляциии и звукоизоляции конструктивных элементов здания.
Процесс производства своими руками
Рассмотрев технологию изготовления состава арболита, можно приступать к выполнению работы самостоятельно. Для начала потребуются некоторые материалы и оборудование:
- специальный лоток для смеси;
- падающий и вибрирующий стол;
- стол с ударно-встряхивающим эффектом;
- разъемные формы и подставки;
- поддон из металла для форм.
Производить арболит своими руками очень сложно без использования необходимых инструментов, станков и оборудования. Как правило, на производстве потребуются некоторые приспособления:
1. Для получения качественного раствора необходимо применить бетономешалку. Разумеется, в процессе можно все сделать своими руками, однако придется, много времени потратить на получение раствора необходимой консистенции.
2. Для формирования структуры блоков важно приобрести формы соответствующих размеров. Как правило, арболит имеет прямоугольную форму, а в производстве используются пластиковые формы.
3. При помощи станка вы профессионально измельчите щепу.
4. Используя пресс можно получить хорошую плотность материала при трамбовке, при этом важно убрать воздух из консистенции. В качестве приспособлений применяется вибростол.
5. Обязательное наличие камеры для сушки арболита, что позволит его превратить в твердую однокомпонентную структуру.
6. В домашних условиях понадобится лопата для загрузки смеси в формы, а для скрепления блоков используют армирующую сетку.
При наличии выше перечисленных приспособлений можно производить в день около 350 – 450 м3 строительного раствора в месяц. Места для монтажа потребуется около 500 квадратных метров, а затрат на электроэнергию пойдет 15-45 кВт/ч. Для самостоятельного процесса органические средства заливаются водой, а также цементом до образования однородной смеси. Все пропорции и расчеты отображены в таблице 1, главное чтобы вышедшая смесь была сыпучей.
Перед заливкой раствора в формы, их обмазывают с внутренней стороны молочком известковым. После этого, средство скрупулезно и аккуратно укладывают и утрамбовывают специальными приспособлениями. Верхняя часть блока выравнивается с помощью шпателя или линейки и заливается раствором штукатурки на слой в 2 сантиметра.
После образованной формы арболита его потребуется тщательно уплотнить с помощью деревянной конструкции, оббитой железом. Прочными и надежными считаются блоки, которые выстоялись и схватились на протяжении десяти дней при температуре 15о. Чтобы арболит не пересох, рекомендуется периодически поливать его водой.
Технология изготовления арболита своими руками не представляет определенной сложности, а поэтому все работы провести легко при наличии необходимых инструментов и приспособлений. При соблюдении правил и критериев производства, правильного расчета компонентов строительный материал получится качественным и прочным для применения.
Советы экспертов при изготовлении блоков своими руками
Рекомендации специалистов по производству арболитных блоков основаны на практике их использования и применения. Чтобы достичь высокого качества продукции необходимо следовать некоторым факторам. В производстве рекомендуется применять не только большую щепу, но и использовать опилки, стружку из дерева. Обработка консистенции и выдавливание из него сахара позволяет избежать дальнейшего вспучивания строительного материала, что не приспускается при сооружении дома.
В процессе изготовления раствор следует тщательно перемешивать, чтобы все части оказались в цементе. Это важно для качественного и прочного скрепления древесины и иных материалов в блоке. В производстве не менее важным остается добавление следующих компонентов, таких как алюминий, гашеная известь и так далее. Весь состав образует дополнительные свойства арболита, например жидкое стекло не позволяет впитывать влагу блокам, а известь служит в качестве антисептика.
Хлористый калий способствует уничтожению микроорганизмов и других веществ, что не благотворно влияют на структуру. При добавлении всех компонентов стоит следить за таблицей пропорциональности, чтобы готовый раствор соответствовал требованиям производства арболитных блоков.
Изготовление арболита своими руками: технология производства и самостоятельные работы
Поэтапная технология изготовления арболита предвидит подготовку основания, определения компонентов и состава блочного материала. В данной статье рассмотрим особенности производства своими руками с применением необходимого оборудования, расчета массы и заливки.
Оглавление:
- Преимущества и недостатки арболита
- Технология производства арболита
- Подготовка основания для работы
- Компоненты и состав арболита
- Процесс и принципы изготовления
- Оборудование: применение на практике
- Блочные формы для арболита
- Процесс производства своими руками
- Советы экспертов при изготовлении блоков своими руками
Преимущества и недостатки арболита
Для многих строителей арболитные блоки являются ценным и качественным материалом для возведения домов. Главная особенность теплоизоляционных свойств позволяет из раствора производить напольные листы. Технология изготовления и принципы выдержки и сушки блоков предоставляют арболиту некоторые преимущества:
1. Прочность материала составляет 600-650 кг/м3, что по компонентной структуре не уступает иному строительному материалу. Главной особенностью является пластичность, что формируется в результате использования древесины, которая качественно армирует блоки. Таким образом, арболит не трескается под тяжестью иных материалов, а может только слегка деформироваться сохраняя общую систему конструкции.
2. Стойкость к низким температурам, что очень важно в процессе возведения дома и его эксплуатации. Дело в том, что если здание нагреется и замерзнет несколько раз, то это не повлияет на качество материала. Фактически дом из арболита может простоять минимум 50 лет в любые погодные условия. Конструкции из пеноблоков не имеют подобных свойств, ведь при постоянном замораживании они быстро потеряют свою функциональность.
3. Арболит не поддается воздействию углекислого газа, так что не стоит беспокоиться о карбонизации блоков, ведь их структура не позволит превратиться материалу в мел.
4. Теплопроводность блоков свидетельствует о популярности материала. Сравнивая показатели, стоит отметить, что стена из арболита в 30 см равняется 1 метру толщины кирпичной кладке. Структура материала позволяет сохранять тепло внутри помещения даже в самые холодные зимы, что весьма экономично при строительстве.
5. Звукоизоляционные свойства свидетельствуют о высоком коэффициенте поглощения арболита, который составляет от 0,7 до 0,6. Для сравнения древесина имеет показатели 0,06 -0,1, а кирпич немного больше около 0,04-0,06.
6. Легкость материала, что позволяет сэкономить средства на заливку фундамента.
7. Арболит является экологически чистым и долговечным строительным материалом, что определяет компонентный состав блоков. После возведения дома он не образует плесень и грибок на стенах.
8. Материал является безопасным, так он не воспламенятся.
9. Арболитные блоки легко применять в строительных работах, поскольку без труда в них можно забить гвозди, просверлить отверстие, использовать шурупы и так далее. Внешняя структура материала позволяет покрывать его штукатуркой без использования специальных сеток и дополнительных утеплителей.
Мы рассмотрели преимущества арболитных блоков, но для полного воссоздания картины о данном строительном материале приведем некоторые недостатки:
1. Стеновая панель может не выделяться точными геометрическими параметрами, от чего для восстановления ровности стены используют вагонку, сайдинг или гипсокартон, а сверху все отделяют штукатуркой.
2. Блоки не являются дешевым строительным материалом, ведь изготовление щепы для арболита требует некоторых затрат. Делая расчеты по сравнению из газобетоном, данный строительный материал обойдется только на 10-15 процентов дороже, что не формирует полное преимущество.
Технология производства арболита
Изготовление арболита требует следованию технологиям производства с расчетом состава и объема для одного блока. Арболитные блоки представляют собой строительный материал простой по компонентному составу, в который входят древесина, вода, опилки, цемент и другие предметы.
Главной основой для производства считается древесная щепа. Составная часть арболитового блока определяет его прочность и устойчивость к повреждениям, что высчитывается высшим уровнем, чем у пено- или газоблоков. Производство в домашних условиях осуществить не сложно, однако необходимо придерживаться распределения массы предмета и следовать инструкции.
Подготовка основания для работы
Основной составляющей для изготовления щепы для арболита является соотношение пропорций стружки и опилок – 1:2 или 1:1. Все предметы хорошо высушивают, для чего их помещают на 3 – 4 месяца на свежий воздух, время от времени обрабатывая известью и переворачивая.
Примерно на 1 кубический метр средства потребуется около 200 литров извести 15-ти процентной. В них помещают все щепы на четыре дня и перемешивают их от 2 до 4 раз на день. Все работы проводятся с целью убрать сахар с древесины, который может спровоцировать гниение блоков. Щепу приобретают в готовом виде, однако, с помощью щепорезов можно сделать самостоятельно.
Компоненты и состав арболита
Компонентный состав арболита является самым важным этапом технологии производства и требует внимательного соотношения всех материалов. При изготовлении блоков важно следить за качеством и разновидностью приобретаемых материалов, которые определяют готовый строительный материал. После процесса изготовления в щепу добавляют следующие материалы, такие как:
- известь гашеную;
- жидкое стекло растворимое;
- портландцемент;
- хлористый калий;
- алюминий и сернокислый кальций.
Производство арболита в пропорциях представлено в таблице 1. Стоит учесть, что для всех компонентов масса рассчитана на четыре процента доли цемента. Данная компоновка помогает сохранить огнеупорность предмета и придает пластичности.
Таблица 1. Состав арболита по объему
Марка арболита | Цемент (М400) | Кол-во извести | Кол-во песка | Кол-во опилок | Получаемая плотность (кг/м3) |
5 | 1 | 1,5 | — | 15 | 300-400 |
10 | 1 | 1 | 1,5 | 12 | 600-700 |
15 | 1 | 0,5 | 2,5 | 9 | 900-1000 |
25 | 1 | — | 3 | 6 | 1200-1300 |
Процесс и принципы изготовления
Оптимальные параметры блоков для технологии производства арболита составляют 25х25х50 сантиметров. Установленные размеры удобны при кладке стен домов, а также в процессе промышленности. Заливка блока состоит из трех рядов смеси и арболита, после каждого этапа необходимо уплотнять раствор молотком, отделанным жестью.
Излишняя масса свертывается при содействии шпателя. Выдерживается блок при температуре 18 градусов тепла на раскрытом воздухе. По истечении суток арболит выстукивается из формы на ровную поверхность, где он скрепляется на протяжении 10 дней.
Оборудование: применение на практике
Для производства необходимо разное снабжение, например, станки для изготовления арболита, которые выбираются в соответствии с объемом продукции и количества сырья. Технология промышленного процесса должна отвечать требованиям и критериям СН 549-82 и ГОСТу 19222-84. В качестве основного материала для выработки выступают хвойные деревья. Раздробление древесины происходит с помощью рубильных машин, таких как РРМ-5, ДУ-2, а более скрупулезное дробление осуществляется на оборудовании ДМ-1.
Арболитовую смесь подготавливают со смесителями и растворителями различного цикличного воздействия на материал. Подвозят большие объемы обработанной смеси к формам с помощью приспособления в качестве бетонораздатчиков или кюбелей. Подъем или опускание машины должно осуществляться при параметрах 15о по верхнему подъему и 10о по нижнему, а скорость оборудования рассчитывается в 1 м/с. Разлив арболитовой смеси по формам делают на высоте до 1 метра.
Уплотнения раствора производят с содействием вибропреса или ручной трамбовки. Для производства небольшого количества блоков нужно применить мини-станок. Изготовление своими руками арболита не представляет особых трудностей, однако на промышленных объектах применяется специальное оборудование по смешиванию, изготовления блоков. На некоторых заводах присутствуют тепловые камеры с ИК-излучением или ТЭНом, что позволяет определить нужную температуру для высыхания блоков.
Блочные формы для арболита
Существуют разные блочные формы для обработки арболита, а примерные величины могут составлять: 20х20х50 см или 30х20х50 см. Выпускаются предметы и прочих размеров, особенно для постройки вентиляционных систем, покрытий и так далее. Формы можно приобрести в строительных магазинах или же подготовить все своими руками. Для этого, используют доски толщиной в 2 сантиметра, которые скрепляют до образования определенной конструкции. Внешне форма отделывается фанерой, или пленкой.
В зависимости от класса арболитовые блоки применяют в малоэтажном строительстве для возведения несущих стен, перегородок, а также для теплоизоляциии и звукоизоляции конструктивных элементов здания.
Процесс производства своими руками
Рассмотрев технологию изготовления состава арболита, можно приступать к выполнению работы самостоятельно. Для начала потребуются некоторые материалы и оборудование:
- специальный лоток для смеси;
- падающий и вибрирующий стол;
- стол с ударно-встряхивающим эффектом;
- разъемные формы и подставки;
- поддон из металла для форм.
Производить арболит своими руками очень сложно без использования необходимых инструментов, станков и оборудования. Как правило, на производстве потребуются некоторые приспособления:
1. Для получения качественного раствора необходимо применить бетономешалку. Разумеется, в процессе можно все сделать своими руками, однако придется, много времени потратить на получение раствора необходимой консистенции.
2. Для формирования структуры блоков важно приобрести формы соответствующих размеров. Как правило, арболит имеет прямоугольную форму, а в производстве используются пластиковые формы.
3. При помощи станка вы профессионально измельчите щепу.
4. Используя пресс можно получить хорошую плотность материала при трамбовке, при этом важно убрать воздух из консистенции. В качестве приспособлений применяется вибростол.
5. Обязательное наличие камеры для сушки арболита, что позволит его превратить в твердую однокомпонентную структуру.
6. В домашних условиях понадобится лопата для загрузки смеси в формы, а для скрепления блоков используют армирующую сетку.
При наличии выше перечисленных приспособлений можно производить в день около 350 – 450 м3 строительного раствора в месяц. Места для монтажа потребуется около 500 квадратных метров, а затрат на электроэнергию пойдет 15-45 кВт/ч. Для самостоятельного процесса органические средства заливаются водой, а также цементом до образования однородной смеси. Все пропорции и расчеты отображены в таблице 1, главное чтобы вышедшая смесь была сыпучей.
Перед заливкой раствора в формы, их обмазывают с внутренней стороны молочком известковым. После этого, средство скрупулезно и аккуратно укладывают и утрамбовывают специальными приспособлениями. Верхняя часть блока выравнивается с помощью шпателя или линейки и заливается раствором штукатурки на слой в 2 сантиметра.
После образованной формы арболита его потребуется тщательно уплотнить с помощью деревянной конструкции, оббитой железом. Прочными и надежными считаются блоки, которые выстоялись и схватились на протяжении десяти дней при температуре 15о. Чтобы арболит не пересох, рекомендуется периодически поливать его водой.
Технология изготовления арболита своими руками не представляет определенной сложности, а поэтому все работы провести легко при наличии необходимых инструментов и приспособлений. При соблюдении правил и критериев производства, правильного расчета компонентов строительный материал получится качественным и прочным для применения.
Советы экспертов при изготовлении блоков своими руками
Рекомендации специалистов по производству арболитных блоков основаны на практике их использования и применения. Чтобы достичь высокого качества продукции необходимо следовать некоторым факторам. В производстве рекомендуется применять не только большую щепу, но и использовать опилки, стружку из дерева. Обработка консистенции и выдавливание из него сахара позволяет избежать дальнейшего вспучивания строительного материала, что не приспускается при сооружении дома.
В процессе изготовления раствор следует тщательно перемешивать, чтобы все части оказались в цементе. Это важно для качественного и прочного скрепления древесины и иных материалов в блоке. В производстве не менее важным остается добавление следующих компонентов, таких как алюминий, гашеная известь и так далее. Весь состав образует дополнительные свойства арболита, например жидкое стекло не позволяет впитывать влагу блокам, а известь служит в качестве антисептика.
Хлористый калий способствует уничтожению микроорганизмов и других веществ, что не благотворно влияют на структуру. При добавлении всех компонентов стоит следить за таблицей пропорциональности, чтобы готовый раствор соответствовал требованиям производства арболитных блоков.
Изготовление арболита своими руками: технология производства и самостоятельные работы
Поэтапная технология изготовления арболита предвидит подготовку основания, определения компонентов и состава блочного материала. В данной статье рассмотрим особенности производства своими руками с применением необходимого оборудования, расчета массы и заливки.
Оглавление:
- Преимущества и недостатки арболита
- Технология производства арболита
- Подготовка основания для работы
- Компоненты и состав арболита
- Процесс и принципы изготовления
- Оборудование: применение на практике
- Блочные формы для арболита
- Процесс производства своими руками
- Советы экспертов при изготовлении блоков своими руками
Преимущества и недостатки арболита
Для многих строителей арболитные блоки являются ценным и качественным материалом для возведения домов. Главная особенность теплоизоляционных свойств позволяет из раствора производить напольные листы. Технология изготовления и принципы выдержки и сушки блоков предоставляют арболиту некоторые преимущества:
1. Прочность материала составляет 600-650 кг/м3, что по компонентной структуре не уступает иному строительному материалу. Главной особенностью является пластичность, что формируется в результате использования древесины, которая качественно армирует блоки. Таким образом, арболит не трескается под тяжестью иных материалов, а может только слегка деформироваться сохраняя общую систему конструкции.
2. Стойкость к низким температурам, что очень важно в процессе возведения дома и его эксплуатации. Дело в том, что если здание нагреется и замерзнет несколько раз, то это не повлияет на качество материала. Фактически дом из арболита может простоять минимум 50 лет в любые погодные условия. Конструкции из пеноблоков не имеют подобных свойств, ведь при постоянном замораживании они быстро потеряют свою функциональность.
3. Арболит не поддается воздействию углекислого газа, так что не стоит беспокоиться о карбонизации блоков, ведь их структура не позволит превратиться материалу в мел.
4. Теплопроводность блоков свидетельствует о популярности материала. Сравнивая показатели, стоит отметить, что стена из арболита в 30 см равняется 1 метру толщины кирпичной кладке. Структура материала позволяет сохранять тепло внутри помещения даже в самые холодные зимы, что весьма экономично при строительстве.
5. Звукоизоляционные свойства свидетельствуют о высоком коэффициенте поглощения арболита, который составляет от 0,7 до 0,6. Для сравнения древесина имеет показатели 0,06 -0,1, а кирпич немного больше около 0,04-0,06.
6. Легкость материала, что позволяет сэкономить средства на заливку фундамента.
7. Арболит является экологически чистым и долговечным строительным материалом, что определяет компонентный состав блоков. После возведения дома он не образует плесень и грибок на стенах.
8. Материал является безопасным, так он не воспламенятся.
9. Арболитные блоки легко применять в строительных работах, поскольку без труда в них можно забить гвозди, просверлить отверстие, использовать шурупы и так далее. Внешняя структура материала позволяет покрывать его штукатуркой без использования специальных сеток и дополнительных утеплителей.
Мы рассмотрели преимущества арболитных блоков, но для полного воссоздания картины о данном строительном материале приведем некоторые недостатки:
1. Стеновая панель может не выделяться точными геометрическими параметрами, от чего для восстановления ровности стены используют вагонку, сайдинг или гипсокартон, а сверху все отделяют штукатуркой.
2. Блоки не являются дешевым строительным материалом, ведь изготовление щепы для арболита требует некоторых затрат. Делая расчеты по сравнению из газобетоном, данный строительный материал обойдется только на 10-15 процентов дороже, что не формирует полное преимущество.
Технология производства арболита
Изготовление арболита требует следованию технологиям производства с расчетом состава и объема для одного блока. Арболитные блоки представляют собой строительный материал простой по компонентному составу, в который входят древесина, вода, опилки, цемент и другие предметы.
Главной основой для производства считается древесная щепа. Составная часть арболитового блока определяет его прочность и устойчивость к повреждениям, что высчитывается высшим уровнем, чем у пено- или газоблоков. Производство в домашних условиях осуществить не сложно, однако необходимо придерживаться распределения массы предмета и следовать инструкции.
Подготовка основания для работы
Основной составляющей для изготовления щепы для арболита является соотношение пропорций стружки и опилок – 1:2 или 1:1. Все предметы хорошо высушивают, для чего их помещают на 3 – 4 месяца на свежий воздух, время от времени обрабатывая известью и переворачивая.
Примерно на 1 кубический метр средства потребуется около 200 литров извести 15-ти процентной. В них помещают все щепы на четыре дня и перемешивают их от 2 до 4 раз на день. Все работы проводятся с целью убрать сахар с древесины, который может спровоцировать гниение блоков. Щепу приобретают в готовом виде, однако, с помощью щепорезов можно сделать самостоятельно.
Компоненты и состав арболита
Компонентный состав арболита является самым важным этапом технологии производства и требует внимательного соотношения всех материалов. При изготовлении блоков важно следить за качеством и разновидностью приобретаемых материалов, которые определяют готовый строительный материал. После процесса изготовления в щепу добавляют следующие материалы, такие как:
- известь гашеную;
- жидкое стекло растворимое;
- портландцемент;
- хлористый калий;
- алюминий и сернокислый кальций.
Производство арболита в пропорциях представлено в таблице 1. Стоит учесть, что для всех компонентов масса рассчитана на четыре процента доли цемента. Данная компоновка помогает сохранить огнеупорность предмета и придает пластичности.
Таблица 1. Состав арболита по объему
Марка арболита | Цемент (М400) | Кол-во извести | Кол-во песка | Кол-во опилок | Получаемая плотность (кг/м3) |
5 | 1 | 1,5 | — | 15 | 300-400 |
10 | 1 | 1 | 1,5 | 12 | 600-700 |
15 | 1 | 0,5 | 2,5 | 9 | 900-1000 |
25 | 1 | — | 3 | 6 | 1200-1300 |
Процесс и принципы изготовления
Оптимальные параметры блоков для технологии производства арболита составляют 25х25х50 сантиметров. Установленные размеры удобны при кладке стен домов, а также в процессе промышленности. Заливка блока состоит из трех рядов смеси и арболита, после каждого этапа необходимо уплотнять раствор молотком, отделанным жестью.
Излишняя масса свертывается при содействии шпателя. Выдерживается блок при температуре 18 градусов тепла на раскрытом воздухе. По истечении суток арболит выстукивается из формы на ровную поверхность, где он скрепляется на протяжении 10 дней.
Оборудование: применение на практике
Для производства необходимо разное снабжение, например, станки для изготовления арболита, которые выбираются в соответствии с объемом продукции и количества сырья. Технология промышленного процесса должна отвечать требованиям и критериям СН 549-82 и ГОСТу 19222-84. В качестве основного материала для выработки выступают хвойные деревья. Раздробление древесины происходит с помощью рубильных машин, таких как РРМ-5, ДУ-2, а более скрупулезное дробление осуществляется на оборудовании ДМ-1.
Арболитовую смесь подготавливают со смесителями и растворителями различного цикличного воздействия на материал. Подвозят большие объемы обработанной смеси к формам с помощью приспособления в качестве бетонораздатчиков или кюбелей. Подъем или опускание машины должно осуществляться при параметрах 15о по верхнему подъему и 10о по нижнему, а скорость оборудования рассчитывается в 1 м/с. Разлив арболитовой смеси по формам делают на высоте до 1 метра.
Уплотнения раствора производят с содействием вибропреса или ручной трамбовки. Для производства небольшого количества блоков нужно применить мини-станок. Изготовление своими руками арболита не представляет особых трудностей, однако на промышленных объектах применяется специальное оборудование по смешиванию, изготовления блоков. На некоторых заводах присутствуют тепловые камеры с ИК-излучением или ТЭНом, что позволяет определить нужную температуру для высыхания блоков.
Блочные формы для арболита
Существуют разные блочные формы для обработки арболита, а примерные величины могут составлять: 20х20х50 см или 30х20х50 см. Выпускаются предметы и прочих размеров, особенно для постройки вентиляционных систем, покрытий и так далее. Формы можно приобрести в строительных магазинах или же подготовить все своими руками. Для этого, используют доски толщиной в 2 сантиметра, которые скрепляют до образования определенной конструкции. Внешне форма отделывается фанерой, или пленкой.
В зависимости от класса арболитовые блоки применяют в малоэтажном строительстве для возведения несущих стен, перегородок, а также для теплоизоляциии и звукоизоляции конструктивных элементов здания.
Процесс производства своими руками
Рассмотрев технологию изготовления состава арболита, можно приступать к выполнению работы самостоятельно. Для начала потребуются некоторые материалы и оборудование:
- специальный лоток для смеси;
- падающий и вибрирующий стол;
- стол с ударно-встряхивающим эффектом;
- разъемные формы и подставки;
- поддон из металла для форм.
Производить арболит своими руками очень сложно без использования необходимых инструментов, станков и оборудования. Как правило, на производстве потребуются некоторые приспособления:
1. Для получения качественного раствора необходимо применить бетономешалку. Разумеется, в процессе можно все сделать своими руками, однако придется, много времени потратить на получение раствора необходимой консистенции.
2. Для формирования структуры блоков важно приобрести формы соответствующих размеров. Как правило, арболит имеет прямоугольную форму, а в производстве используются пластиковые формы.
3. При помощи станка вы профессионально измельчите щепу.
4. Используя пресс можно получить хорошую плотность материала при трамбовке, при этом важно убрать воздух из консистенции. В качестве приспособлений применяется вибростол.
5. Обязательное наличие камеры для сушки арболита, что позволит его превратить в твердую однокомпонентную структуру.
6. В домашних условиях понадобится лопата для загрузки смеси в формы, а для скрепления блоков используют армирующую сетку.
При наличии выше перечисленных приспособлений можно производить в день около 350 – 450 м3 строительного раствора в месяц. Места для монтажа потребуется около 500 квадратных метров, а затрат на электроэнергию пойдет 15-45 кВт/ч. Для самостоятельного процесса органические средства заливаются водой, а также цементом до образования однородной смеси. Все пропорции и расчеты отображены в таблице 1, главное чтобы вышедшая смесь была сыпучей.
Перед заливкой раствора в формы, их обмазывают с внутренней стороны молочком известковым. После этого, средство скрупулезно и аккуратно укладывают и утрамбовывают специальными приспособлениями. Верхняя часть блока выравнивается с помощью шпателя или линейки и заливается раствором штукатурки на слой в 2 сантиметра.
После образованной формы арболита его потребуется тщательно уплотнить с помощью деревянной конструкции, оббитой железом. Прочными и надежными считаются блоки, которые выстоялись и схватились на протяжении десяти дней при температуре 15о. Чтобы арболит не пересох, рекомендуется периодически поливать его водой.
Технология изготовления арболита своими руками не представляет определенной сложности, а поэтому все работы провести легко при наличии необходимых инструментов и приспособлений. При соблюдении правил и критериев производства, правильного расчета компонентов строительный материал получится качественным и прочным для применения.
Советы экспертов при изготовлении блоков своими руками
Рекомендации специалистов по производству арболитных блоков основаны на практике их использования и применения. Чтобы достичь высокого качества продукции необходимо следовать некоторым факторам. В производстве рекомендуется применять не только большую щепу, но и использовать опилки, стружку из дерева. Обработка консистенции и выдавливание из него сахара позволяет избежать дальнейшего вспучивания строительного материала, что не приспускается при сооружении дома.
В процессе изготовления раствор следует тщательно перемешивать, чтобы все части оказались в цементе. Это важно для качественного и прочного скрепления древесины и иных материалов в блоке. В производстве не менее важным остается добавление следующих компонентов, таких как алюминий, гашеная известь и так далее. Весь состав образует дополнительные свойства арболита, например жидкое стекло не позволяет впитывать влагу блокам, а известь служит в качестве антисептика.
Хлористый калий способствует уничтожению микроорганизмов и других веществ, что не благотворно влияют на структуру. При добавлении всех компонентов стоит следить за таблицей пропорциональности, чтобы готовый раствор соответствовал требованиям производства арболитных блоков.
Технология производства Арболит 33
Не секрет, что качество строительного материала напрямую зависит от строгого соблюдения технологии изготовления и от правильного подбора ингредиентов.
В этой статье мы расскажем, как получить качественный арболит, соответствующий современным требованиям экологичности, безопасности и энергоэффективности жилья.
Арболит на 80-90% состоит из древесной щепы, а значит, ей надо уделять особое внимание — ведь именно от качества щепы зависят будущие свойства блока и теплофизические характеристики Вашего дома. Не редко для производства арболита, вместо технологической щепы, используют опилки, стружку от оцилиндровки бревен, в ход идет горелая, гнилая или с большим содержанием коры древесина. В течение 2-х лет мы вели разработку оборудования для создания «идеальной» щепы — без примесей и с соответствующими для арболита размерами. На фотографиях Вы видите, каких результатов удалось добиться. Именно такая щепа составляет основу арболитовых блоков, выпускаемых нашей компанией.
Не менее значим в производстве арболита цемент: он отвечает за прочность блоков, био- и огнестойкость материала, и, как следствие, за надежность и безопасность будущего жилья. Ввиду того, что цемент является основной затратной частью производства, то некоторые производители пытаются сэкономить на нем. Кто-то экономит на количестве, а кто-то на качестве — в любом случае получается, что «скупой платит дважды», только в данном случае получается, что платит из Вашего кармана. Для производства мы используем только проверенный цемент, напрямую с завода изготовителя — «Портландцемент» М-500 Д0, производства Мордовии. Каждая партия поставляемого с завода цемента сопровождается сертификатом соответствия.
Вернёмся к щепе. Как известно, древесина содержит сахар, что приводит к гниению и разрушению. Это может коснуться и арболита, если своевременно не избавить щепу от сахара. Мы решаем проблему путем обработки щепы сульфатом алюминия. Это химическое вещество также применяется для очистки питьевой воды, в качестве пищевой добавки и полностью соответствует экологическим нормам и требованиям.
Сульфат алюминия, используемый на нашем производстве, также как и цемент, имеет сертификаты качества.
С целью понижения гигроскопичности материала в производстве арболита можно использовать «жидкое стекло». Согласно ГОСТ 19222-84. Арболит и изделия из него, «жидкое стекло» является рекомендуемой добавкой. | |
Чтобы сделать качественный блок нужной плотности и правильной геометрии необходимо профессиональное оборудование, разработанное специально для производства арболита. Для приготовления арболитовой смеси мы используем бетоносмеситель принудительного действия, благодаря которому каждая щепочка покрывается защитным слоем цемента. |
|
Центральное место на линии занимает вибропресс, который обеспечивает равномерное распределение щепы и необходимую плотность блока. | |
Особое внимание мы уделяем геометрии металлических форм, в которых арболитовая смесь выдерживается до первичного затвердевания цемента, в противном случае линейные отклонения блоков могли бы исчисляться сантиметрами!!! |
Вот и все «секреты» производства, позволяющие нашей компании выпускать арболитовые блоки точных размеров и качества, соответствующего ГОСТу 19222-84.
Особенности технологии производства арболитовых блоков, панелей и конструкций
Само название арболит раскрывает состав и технологию изготовления этого современного строительного материала. В переводе с греческого языка «арбо» означает дерево, «литое» — камень. Основой для изготовления блоков являются древесный заполнитель и цемент, обеспечивающие в сочетании с химической добавкой и водой особую прочность всей конструкции. Примерный расход компонентов на кубический метр арболита показан в таблице № 1.
Табл. 1. Средний расход компонентов в килограммах на 1 кубический метр арболита
Компоненты | Марка | ||||
5 | 10 | 15 | 25 | 35 | |
Портландцемент марки 400 | 260/290 | 280/310 | 300/330 | 330/360 | 360/390 |
Древесная дробленка (сухая) | 160/180 | 180/200 | 200/220 | 220/240 | 240/250 |
Сульфат алюминия | 6 | 6-7 | 7 | 8 | 8 |
Вода | 280/330 | 300/360 | 330/390 | 360/430 | 400/460 |
Расход составляющих каждой марки при использовании хвойной древесины размещен до косой линии, лиственной и смешанной – после. В качестве химической добавки могут быть использованы и другие компоненты: растворимое стекло, гашеная известь, хлористый кальций. Составляющие и схема производства могут варьироваться в зависимости от назначения и особенностей эксплуатации готового изделия.
Производство арболита своими руками: состав, пропорции, оборудование
Арболит (он же деревобетон) все чаще используется в малоэтажном строительстве. Во многом это связано с простотой производственной технологии и доступностью исходных компонентов. Именно о технологии, оборудовании и способах производства я расскажу в этой статье.
Производственное оборудование
Оборудование для производства арболита не отличается особой сложностью и габаритами. Его можно разместить на приусадебном или дачном участке, в любом боксе, цеху или просто на улице под навесом. Главное условие – наличие электроэнергии и удобство эксплуатации. Полный перечень заводского оборудования, необходимого для промышленного производства арбоблоков выглядит следующим образом:
- Шредер – измельчитель органических наполнителей (щепы, соломы и т.
д.).
- Ёмкость для приготовления и розлива химических компонентов.
- Дозатор цемента.
- Дозатор органических наполнителей.
- Дозатор заполнителей для бетонного раствора.
- Бетоносмеситель для арболита принудительного типа действия.
- Подъёмно-поворотный бункер для приёма и дальнейшего розлива готового арболитового раствора.
- Система лебёдок для погрузочно-разгрузочных работ.
- Самозапечатываемые формы для отливки блоков.
- Вибропресс для арболита.
При кустарном производстве деревобетона, для собственных нужд, могут использоваться самодельные станки.
Состав арболита
Состав арболита регламентируется ГОСТ №19-222-84. Готовая к заливке арболитовая смесь состоит из следующих компонентов:
- Цементный раствор;
- Химические добавки;
- Органические наполнители.
Цемент
В качестве связующего компонента в производстве используется раствор на цементной основе. По ГОСТу, портландцемент для приготовления арболита должен иметь марку не ниже М-400.
Таблица . Технические характеристики цемента М-400
Добавлять песок в состав арболитного раствора не рекомендуется, так как это ухудшает показатели сцепки органических наполнителей с цементным вяжущим веществом. В результате блоки становятся менее прочными и склонными к расслоению и растрескиванию.
Химические добавки
Химические добавки предназначены для улучшения эксплуатационных характеристик арболита. В состав арболита входят следующие химические компоненты:
- Сернокислый алюминий, он же сульфат алюминия – неорганическая соль, хорошо растворимая в воде. При изготовлении арболита он используется в качестве гидроизолятора, увеличивающего стойкость материала к воздействию сырости.
Из-за высокой гигроскопичности, хранение сернокислого алюминия должно производиться в помещениях с низким уровнем влажности и в герметичной упаковке.
- Хлористый кальций – химический элемент, получаемый при промышленном производстве соды. Добавляется в арболитную смесь для связывания сахаров, содержащихся в органических заполнителях, что значительно повышает прочностные характеристики получаемого цементного раствора и позволяет повысить степень его сцепления с древесными компонентами.
- Жидкое стекло – водорастворённые силикаты натрия или калия. При изготовлении смеси для деревобетона, жидкое стекло выполняет роль отвердителя, а также для придания цементному раствору кислотоупорных и гидроупорных свойств.
- Гашёная известь добавляется в раствор для нейтрализации содержащихся в органических добавках природных сахаров и улучшения связующих качеств цемента и древесины.
Органические заполнители
В качестве наполнителя при производстве арболита используются отходы деревообрабатывающего производства. Главное отличие арболита от других видов лёгких бетонов состоит в том, что в его состав входят достаточно крупные компоненты – древесная щепа, костра льна, конопляная солома и т. д. От процентного содержания органического наполнителя зависят основные показатели материала: плотность, гигроскопичность, коэффициент теплопроводности и т.д.
- Древесная щепа – наиболее часто используемый заполнитель. Согласно ГОСТу, её размер не должен превышать 4 х 1 х 0,5 см. В связи с этим, технические характеристики арболитовых конструкций отличаются от характеристик опилкобетона и фибролита (стружкобетона).
Древесная щепа – главная составляющая арболитового блока
Нужный размер органической фракции получают при помощи специального станка-щепореза (шредера). Содержание щепы в общем объёме арболита может быть разным, и составлять от 30% до 90%.
- Льняная костра добавляется в таком же виде, в каком она получается на льноперерабатывающем заводе после предварительной обработки сырья.
- Конопляную солому перед использованием следует перемолоть в шредере.
Согласно техническим нормативам, льняные и конопляные наполнители должны иметь следующие размеры:
- Длина – от 15 до 25 мм.
- Ширина – от 2 до 5 мм.
В разных регионах для производства арболитовых блоков и панелей могут применяться и другие органические заполнители: рисовая и гречневая солома, отходы обработки хлопчатника и т.п.
В таблице даны технические характеристики арболита, изготовленных с применением разных органических наполнителей:
Технология производства
Технология производства арболита имеет ряд отличительных особенностей, которые касаются подготовки сырья, рецепта приготовления, дозировки компонентов. Её соблюдение обязательно как при промышленном выпуске, так и при производстве арболита своими руками в домашних условиях.
Подготовка органических заполнителей
Для деревобетона может использоваться щепа древесины хвойных пород – ели, сосны, пихты, а также лиственных деревьев с твёрдой древесиной – дуба, ясеня, берёзы.
Не рекомендуется применять в производстве щепу лиственницы и бука из-за химического состава – их древесина содержит значительно больше сахаров, что приводит к значительному снижению качества блоков. В крайнем случае, при производстве раствора с лиственничной или буковой щепой, придётся, как минимум, вдвое увеличить количество химдобавок – извести или хлористого кальция.
Щепа березы и ясеня – лучший наполнитель для арболитового блока
Первым шагом древесные отходы измельчаются посредством щепореза до размеров, регламентируемых ГОСТ №19-222-84 – не более 40х10х50 мм. Фактически же оптимальными размерами древесной фракции для формовки блоков являются 25х5х3 мм, так как более крупные компоненты хуже связываются цементным раствором и более склонны к расслаиванию в процессе эксплуатации.
После измельчения щепа просушивается. На крупных производственных линиях для этих целей применяют специальные сушилки барабанного типа, в которые подаётся горячий воздух.
Если арболит производится в домашних условиях, щепу складируют для просушки под навесами на срок не менее месяца, при температуре воздуха +15С.
Непосредственно перед замешиванием щепа замачивается на 6-8 ч в растворе воды с химическими добавками. Вода для этого должна соответствовать ГОСТу №23-732-79, где регламентируется её химический состав, кислотность и т.д. На деле же, при кустарном производстве деревобетона применяется любая доступная вода – из водопровода, реки или колодца. Единственное необходимое условие – она должна быть чистой и иметь температуру не ниже +15…+20С. После замачивания древесный наполнитель должен иметь влажность не более 30%.
Костра льна и солома конопли, для удаления из неё излишков сахаров, выдерживается на открытом воздухе не менее 2 – 3 месяцев при плюсовой температуре, либо замачивается в известковом молоке на 3-4 дня. Известковый раствор приготавливается в следующих пропорциях на 1 куб. м органики.
Органический заполнитель | Гашёная известь | Вода | Дополнительные условия |
1 куб. м костры льна или конопли | 2 – 2,5 кг | 150 – 200 л в зависимости от влажности наполнителя | Смесь перемешивается каждые 2 дня |
Пропорции смеси
Пропорции замеса могут незначительно изменяться, в зависимости от класса прочности деревобетона. Для получения более высокой марки арболита увеличивают долю цемента в общем объёме раствора. Ниже представлены рекомендуемые пропорции замеса раствора для деревобетона различных марок на куб готового раствора:
Марка | Портландцемент М-400 | Органический наполнитель | Химдобавки | Вода |
М-5 | 200 – 220 кг | 280 – 320 кг | 12-14 кг | 350 – 400 л |
М-15 | 250 – 280 кг | 240 – 300 кг | 12 кг | 350 – 400 л |
М-25 | 300 – 330 кг | 240 – 300 кг | 12 кг | 350 – 400 л |
М-50 | 350 – 400 кг | 220 – 240 кг | 10-12 кг | 350 – 400 л |
Химические добавки могут добавляться как по отдельности, так и комплексно. К примеру, строительные нормативы СН №54982 допускают смешивание сернокислого алюминия с известью в пропорции 8 кг и 4 кг на куб раствора.
Очерёдность загрузки
При замесе раствора важно соблюдать не только пропорции, но и очерёдность загрузки компонентов. Для изготовления качественной арболитной смеси обычные бетоносмесители, используемые для замеса бетона, не подойдут – щепа в них не сможет хорошо перемешаться с цементным раствором. Бетономешалка для арболита должна быть принудительного типа, например отечественные модели серии СБ, РН, импортные ZZBO и т.д. В них перемешивание компонентов производится не вращением барабана, а расположенным внутри него шнеком или лопастью.
Таблица 3. Технические характеристики принудительных смесителей серии СБ:
- Первым шагом в барабан смесителя насыпается подготовленная щепа в нужной пропорции.
- Затем бетоносмеситель запускается и в него заливается вода с растворёнными в ней химическими добавками. Органический заполнитель размешивается с химраствором в течение 30-60 секунд, чтобы щепки хорошо пропитались.
- После этого добавляется цемент и продолжается размешивание смеси в течение 3-5 минут, до получения однородной массы.
Формирование блоков
Формовка арбоблоков происходит с помощью специальных матриц, в которые заливается готовый раствор. Они изготавливаются из нержавеющей стали разборной конструкции для более лёгкого извлечения блоков.
Также такие формы можно изготовить самому из дерева или фанеры, обив их изнутри линолеумом или жестью. Размеры ячеек матрицы могут быть различными, в зависимости от потребностей в блоках тех или иных габаритов.
Трамбовка производится вручную, либо для этого используется вибростанок. В первом случае раствор заливается в формы слоями толщиной в 5 см, каждый из которых уплотняется металлической трамбовкой.
Во втором случае уплотнение раствора производится на вибростоле, которым обычно оборудуется промышленный станок для производства арболита.
Также при формовке для уплотнения раствора можно использовать ручной или механический пресс. Чтобы из уплотняемых блоков лучше выходил воздух, они периодически прокалывается металлическим стержнем.
Сушка
Сушка готовой продукции является завершающим этапом производственного процесса. В связи с особенностью конструкции, наилучшим вариантом является мягкий режим просушки.
Пропаривать арбоблоки по примеру железобетонных конструкций, не рекомендуется, так как материал теряет прочность из-за возрастающих внутренних напряжений. По этой же причине не следует пытаться ускорить высыхание блоков при помощи сушильных камер и других приспособлений.
Оптимальный режим просушки для арболита – температура 40-50 градусов, при влажности воздуха порядка 70-80%. В этом случае блоки набирают необходимую для распалубки прочность уже спустя 18-20 ч. что составляет около 1/3 от окончательной марочной. Дальнейшая выдержка материала производится при температуре 15-20 С в течение одной-двух недель – за это время деревобетон набирает окончательную прочность.
Технология изготовления качественного арболита — ЭкоДревПродукт
Состав, требования и этапы изготовления арболита
Технология производства арболита заключается в объединении двух натуральных компонентов: чистого портландцемента и отходов деревообрабатывающей/лесозаготовительной промышленности — древесной щепы. Главным критерием, обеспечивающим соответствие строительных блоков на основе арболита регламентам стандарта, является применение качественных деревоматериалов. Они должны соответствовать следующим параметрам:
- Низкая сучковатость. В идеале сучков не должно быть вовсе.
- Отсутствие коры. Примеси древесной коры способны испортить готовые блоки, поскольку данный биологический материал обладает совершенно иными свойствами, нежели древесина, намного быстрее разлагается.
- Низкая влажность. При использовании древесных компонентов с высоким уровнем влажности добиться качества арболита не представляется возможным, поэтому щепу предварительно просушивают.
- Отсутствие разрушающих структуру древесины биологических процессов. Щепа, на которой обнаружены следы гнили, колоний плесневых грибов, непригодна для производства арболитовых блоков.
Для измельчения деревоматериалов, древесных отходов до состояния щепы используются специализированные щепорубительные агрегаты. Готовый компонент блоков из арболита — щепа — должна быть практически однородной по размерам.
Этапы изготовления арболита
- Изготовление щепы. Преимущественно для этих целей используется древесина большинства видов деревьев хвойных пород, но можно применять и другие, характеризующиеся повышенной стойкостью к биологическому разрушению — осина, береза. Плохое качество готового арболита может быть обусловлено применением деревоматералов из бука, лиственницы.
- Минерализация щепы. Данная процедура необходима для придания этому компоненту повышенного уровня адгезии с портландцементом. Для этих целей применяется хлористый кальций, реже — сернокислый алюминий.
- Смешивание предварительно минерализованной щепы с остальными компонентами — цементной массой и связующим составом. После тщательного перемешивания полученную смесь заливают в предварительно подготовленные формы, затем оставляют для затвердевания. Длительность данного процесса зависит от многих условий, главным из которых является температурный режим. Летом либо в прогретом помещении готовый продукт можно получить гораздо быстрее, чем при низких температурах. Не рекомендуется осуществлять производство арболитовых блоков при температуре, не превышающей пятнадцати градусов.
Цемент на основе дерева с высокой прочностью и многофункциональностью
Формование и трехмерная архитектура древесноподобного цемента. а) Схематические изображения микромеханизмов образования древесного цемента в процессе замораживания, оттаивания и твердения.
Природа часто предлагает многообещающее вдохновение для биомиметических искусственных материалов. В новом отчете, опубликованном в Advanced Science , Фахэн Ван и группа ученых в области передовых материалов, техники и науки в Китае разработали новые цементные материалы на основе однонаправленно-пористой архитектуры, чтобы воспроизвести дизайн натурального дерева.Полученный древесноподобный цементный материал показал более высокую прочность при равной плотности, наряду с многофункциональными свойствами для эффективной теплоизоляции, водопроницаемости и легкой регулировки водоотталкивания. Команда одновременно добилась высокой прочности и многофункциональности, чтобы сделать древесноподобный цемент перспективным новым строительным материалом для конструкций, имитирующих древесину, с высокими эксплуатационными характеристиками. Они представили простую процедуру изготовления для повышения эффективности при массовом производстве с применением, подходящим для других систем материалов.
Разработка древесноподобных материалов с использованием биоинспирации
Пористые материалы на основе цемента обладают низкой теплопроводностью для теплоизоляции, высокой звукопоглощающей эффективностью, отличной воздухо- и водопроницаемостью при сохранении легкого веса и огнестойкости. Тем не менее, по-прежнему остается ключевой задачей одновременное улучшение как механических, так и многофункциональных свойств, включая механическую поддержку, эффективную транспортировку и хорошую теплоизоляцию.Поэтому крайне желательно создавать материалы с повышенными механическими и многофункциональными свойствами, чтобы активно реализовывать принципы дизайна натурального дерева. В ходе экспериментов Wang et al. разработал древесноподобный цемент с однонаправленно-пористой структурой, образованной методом двунаправленной заморозки. Процесс позволил образовать мосты между составляющими конструкции, затем команда оттаивала полностью замороженные тела до тех пор, пока лед постепенно не растаял, а цемент не затвердел.Последующий процесс гидратации привел к образованию новых минералов и гелей в цементе, включая гидроксид кальция в форме шестиугольника, игольчатый эттрингит и гели с гидратом силиката кальция. Фазы в основном образовывались в цементных пластинах и врастали в их промежутки в процессе оттаивания и отверждения для лучшей структурной целостности с усилением взаимосвязей пластин во время формирования пористого цемента. Затем с помощью рентгеновской томографии (XRT) команда обнаружила образование однонаправленных микропор в цементе с ледяным шаблоном.
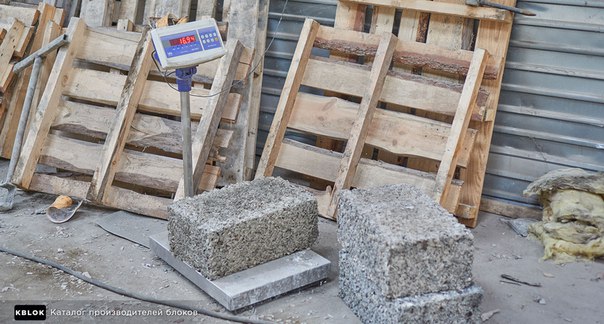
Ван и др.использовали изображения сканирующей электронной микроскопии (СЭМ), чтобы выявить однонаправленные поры между ламелями в ледяном цементе, которые охватывают большое количество взаимосвязей, соединяющих ламели. Команда классифицировала взаимосвязи на три типа: (1) мосты и пересечения, образованные из-за частиц цемента, поглощенных кристаллами льда в процессе замораживания, (2) шестиугольный гидроксид кальция и (3) игольчатый эттрингит. Последние минералы образовались в результате реакций гидратации цемента в процессе оттаивания и твердения.Ламели цемента содержали обильные поры, образовавшиеся в процессе сушки цемента за счет обезвоживания гелей и удаления воды. Ученые классифицировали поры в древесноподобном цементе на три типа, включая (1) межламеллярные открытые поры, (2) внутриламеллярные открытые поры и (3) внутриламеллярные закрытые поры. Межпластинчатая пористость в основном определялась содержанием воды, которая играла роль порообразующего агента.
- The general varying trends are indicated by the dashed curves for clarity. e) Dependence of the compressive strength on the relative density in the wood‐like cement. f) Interpretation of the strength according to the equivalent element approach by taking different types of pores into account. The data in panels (c)–(f) are obtained from at least three measurements for each set of samples and presented in form of mean ± standard deviation. Credit: Advanced Science, doi: 10.1002/advs.202000096″>
Механические свойства древесного цемента.a,b) Репрезентативные кривые напряжения-деформации при сжатии древесноподобного цемента, изготовленного из растворов с различным В/Ц а) без и б) с добавками SF. c, d) Изменения в c) деформации разрушения, d) плотности поглощения энергии, представленные с использованием площади под кривой напряжение-деформация до пикового напряжения и удельной прочности (вставка на панели (d)) как функция общей пористости Pобщ. Общие изменяющиеся тенденции показаны пунктирными кривыми для ясности.
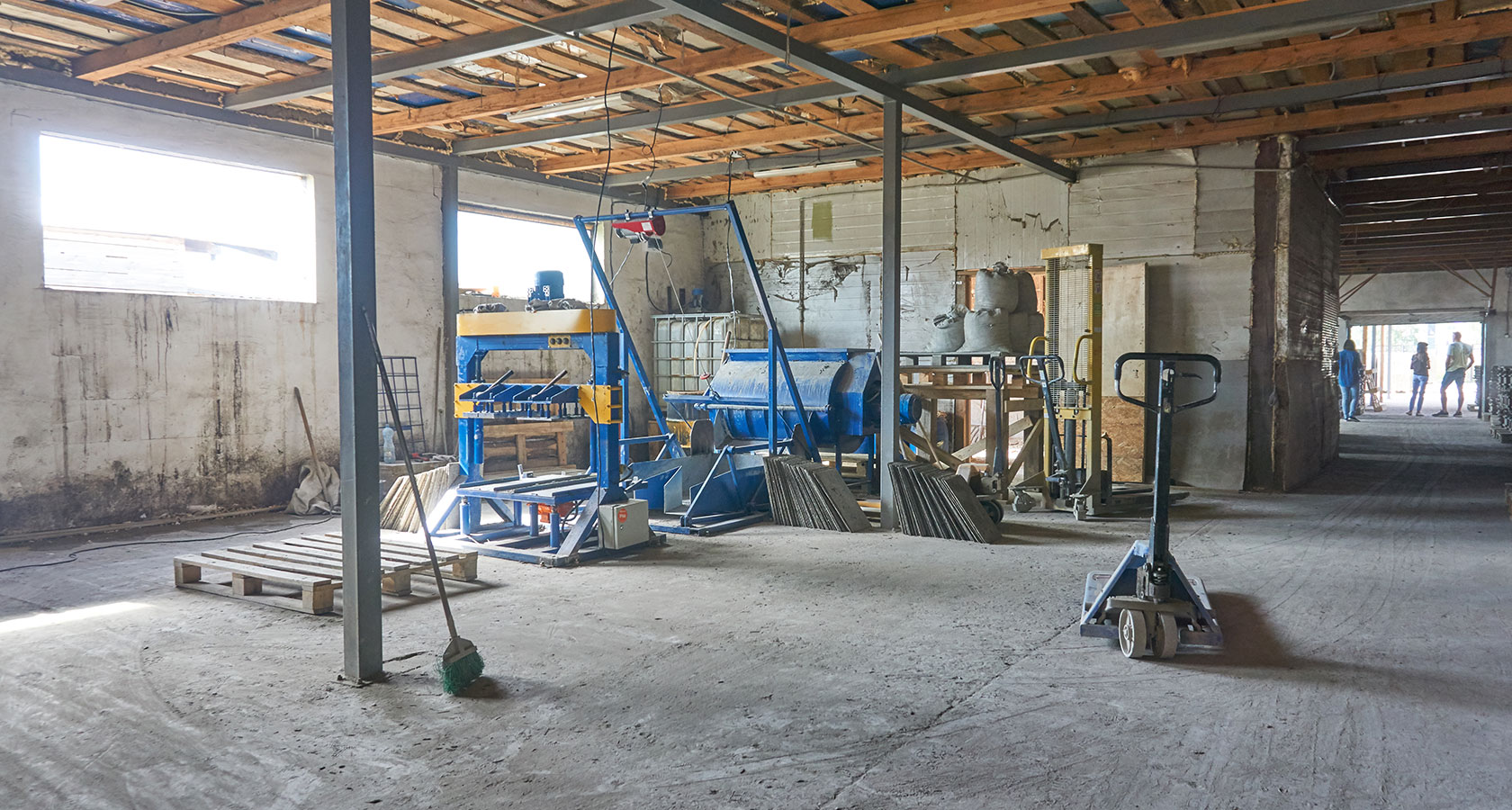
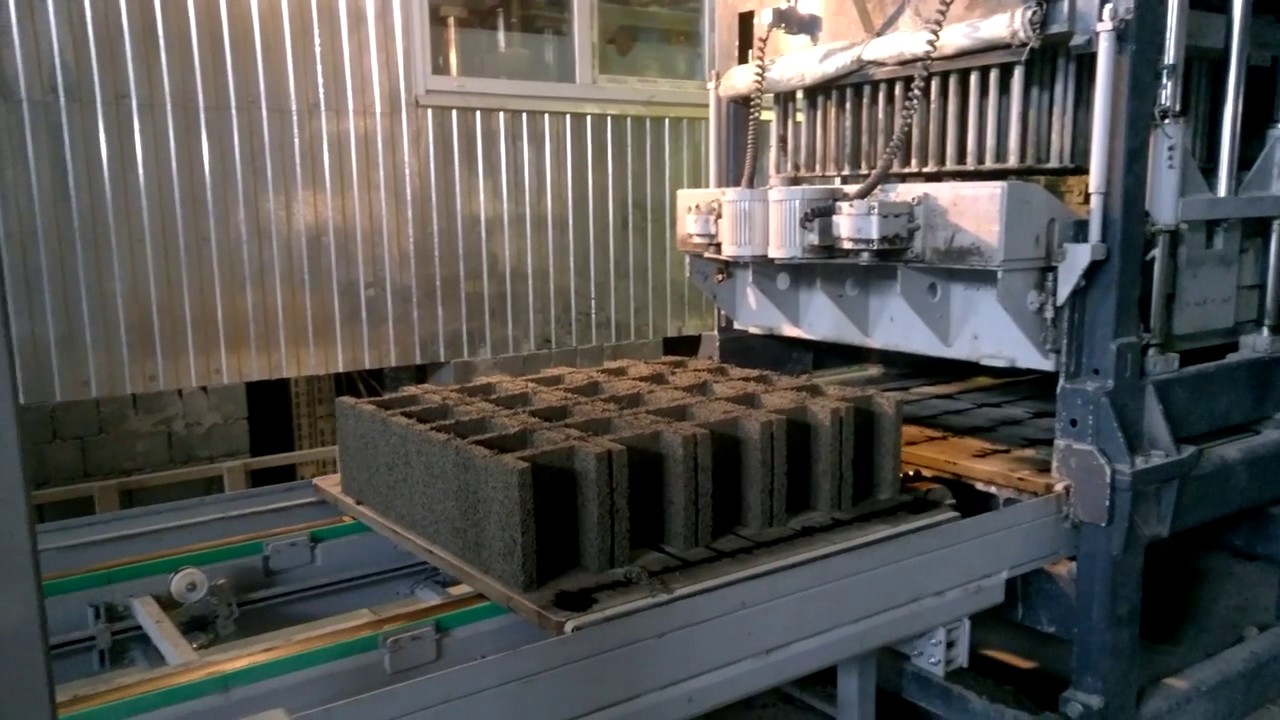
Механические и многофункциональные свойства материала
Команда получила репрезентативные кривые напряжения-деформации при сжатии древесноподобного цемента с добавлением или без добавок кремния в его состав. Прочность на сжатие монотонно снижалась с увеличением соотношения вода/цемент в растворах, используемых для разработки материала, что в конечном итоге привело к увеличению пористости цемента. Поскольку деформация разрушения материала увеличивается с увеличением общей пористости, прочность пористых твердых тел может определяться их пористостью. Затем команда измерила коэффициент теплопроводности древесноподобного цемента с ледяным шаблоном, чтобы показать снижение теплопроводности с увеличением пористости материала.Они также использовали инфракрасные (ИК) изображения, чтобы четко увидеть прочные теплоизоляционные свойства цементного материала с ледяным шаблоном. Для регулирования эффективности теплоизоляции Wang et al. отрегулировать содержание твердых частиц в вяжущих растворах, увеличив содержание воды/цемента. Полученный цементный материал поглощал воду из-за гидрофильного (привлекающего воду) характера его внутренних поверхностей. Напротив, они могли предотвратить проникновение воды в поры, гидроизолируя поверхности кремнийорганическим агентом; такие усилия по гидрофобности могут даже привести к тому, что материал будет плавать на воде.
Таким образом, способ может облегчить переключаемые приложения в качестве водопроницаемых или водонепроницаемых конструкций, подходящих в качестве строительных материалов.
Перспективы древесно-цементных материалов
Таким образом, Faheng Wang и его коллеги представили метод ледяного шаблона как жизнеспособный подход к созданию однонаправленных микропор для применения в керамике, полимерах, металлах и их композитах. Ученые разработали процесс лиофильной сушки, основанный на самозатвердевании цемента при контакте с реакциями гидратации. Получившаяся древесно-цементная архитектура содержала множество пор в открытой или закрытой форме и множество взаимосвязей, соединяющих их ламели. При увеличении пористости прочность цемента снижается. Древесноподобный цемент также отличался меньшей теплопроводностью и хорошей водопроницаемостью. Команда могла изменить цементный материал на водоотталкивающий или водопривлекательный с помощью гидрофобной или гидрофильной обработки соответственно.Простая и практичная стратегия разработки материалов в сочетании с самозатвердевающей природой ее компонентов может значительно повысить экономическую и временную эффективность метода ледяного шаблона для формирования устойчивого бетона с потенциалом для применения этого метода к другим системам материалов.
Наноинженерный цемент перспективен для герметизации протекающих газовых скважин
Дополнительная информация: Ван Ф.
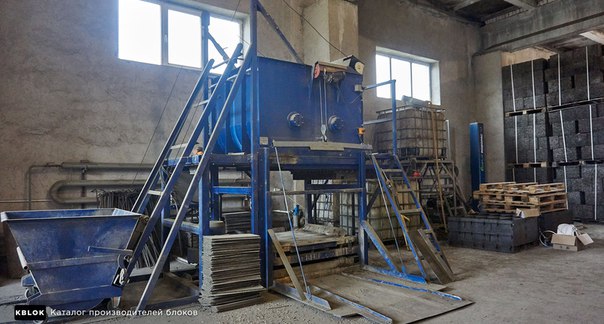
Монтейро П. и др. На пути к устойчивому бетону, Nature Materials , doi.org/10.1038/nmat4930
Рой Д. М. Новые прочные цементные материалы: химически связанная керамика, Science , 10.1126/science.235.4789.651
© 2021 Наука Х Сеть
Цитата :
Цемент под дерево с высокой прочностью и многофункциональностью (2021, 5 января)
получено 26 января 2022 г. с https://физ.org/news/2021-01-wood-inspired-cement-high-strength-multifunctionality.html
Этот документ защищен авторским правом. Помимо любой добросовестной сделки с целью частного изучения или исследования, никакие часть может быть воспроизведена без письменного разрешения. Контент предоставляется только в ознакомительных целях.
Является ли дерево новым бетоном?
В поисках новых способов улавливания углерода девелоперы, архитекторы и компании, стремящиеся к нулевому уровню выбросов, задаются вопросом: «Дерево — это новый бетон?» Новая технология в так называемом «массовом производстве древесины» предлагает альтернативу сокращению выбросов углерода бетону и стали в строительном секторе.
В дополнение к эстетическим преимуществам дерева как строительного материала, сторонники говорят, что использование древесины может существенно сократить выбросы парниковых газов в строительном секторе. Его использование также может сократить отходы, загрязнение окружающей среды, затраты и время по сравнению с более широко используемыми сейчас материалами.
«Массовая древесина не является подходящим материалом навсегда, но это правильный материал на данный момент», — говорит архитектор Майкл Грин, сторонник деревянного строительства из Ванкувера. «Если бы у нас были другие углеродно-нейтральные способы строительства, нам не понадобилась бы массивная древесина.»
Новые методы обрезки, сушки и склеивания деревянных досок, включая древесные отходы, для создания больших «плит», массивная древесина используется для всего: от полов, стен и потолков до целых зданий и небоскребов — даже городов.
Технический гигант Microsoft обновляет свой кампус в Силиконовой долине, используя древесину с учетом ее углеродных и других экологических преимуществ. Кампус площадью 644 000 квадратных футов станет крупнейшим проектом по производству массивной древесины в Северной Америке.
Массивная древесина не является подходящим материалом навсегда, но на данный момент это подходящий материал.
«Использование массивной древесины является частью обязательства Microsoft стать к 2030 году углеродно-отрицательным, включая сокращение выбросов категории 3 на 55 процентов», — сказал Даррен Ломбарди, старший менеджер по недвижимости в Microsoft SVC. Объем 3 Выбросы – это выбросы от клиентов или активов, не принадлежащих компании или не контролируемых ею, но которые косвенно влияют на ее цепочку создания стоимости и выбросы. Microsoft использует данные из инструмента Embodied Carbon Calculator for Construction (EC3), который анализирует строительные материалы, для принятия решений по строительству, включая наиболее эффективные способы сокращения выбросов углерода.
В настоящее время самое высокое в мире массивное деревянное здание находится в Норвегии, его высота составляет 18 этажей и 280 футов. Градостроители в Хельсинки, Финляндия, создают то, что называется Wood City, целый город, построенный из дерева в качестве основного строительного материала.
«Массовая древесина включает в себя набор строительных элементов, которые превращают относительно низкоценное древесное сырье в структурные элементы, которые имеют более высокие характеристики веса и прочности, чем сталь или бетон», — говорит Кит Крюс, профессор австралийского университета Квинсленда.По его словам, поддержка энергоэффективных зданий на протяжении всего их жизненного цикла может стать эффективным способом сокращения долгосрочных выбросов углерода и достижения нулевого уровня выбросов.
Смотрите нашу историю по теме: Calix получает инвестиции в размере 17,7 миллионов долларов от Carbon Direct для улавливания углерода в бетоне.
Как правило, массивная древесина изготавливается из быстрорастущих хвойных пород деревьев, таких как пихта, сосна и ель. Чтобы превратить его в прочный и адаптируемый строительный материал, используются различные методы, в том числе ламинированные дюбелями (DLT), клееные (Glulam или GLT) балки, клееные пиломатериалы из шпона (LVL) и ламинированные гвоздями. древесина (NLT).Наиболее перспективным типом для крупных строительных проектов является кросс-клееная древесина (CLT).
«Это немного похоже на то, что IKEA сделала с мебелью, — говорит Крюс. «Все предварительно изготовлено с очень высокими допусками, поставляется в плоской упаковке и собирается в конечный продукт».
Большое улавливание углеродаСогласно новому отчету U.N. Отчет программы по окружающей среде. Использование древесины вместо стали и бетона может значительно уменьшить углеродный след строительства, предотвращая попадание углерода в атмосферу и улавливая его на протяжении всего срока службы здания. Поскольку древесина улавливает и хранит углерод посредством фотосинтеза, сторонники говорят, что массовая древесина действует как форма удаления углерода.
Выбросы в строительном секторе составляют почти 38% от общего объема выбросов парниковых газов в мире и достигли рекордно высокого уровня в 2019 году.
К 2050 году ООН ожидает, что 70 процентов населения мира будет жить в городах, что означает создание дополнительной инфраструктуры. Это не сулит ничего хорошего для борьбы с изменением климата. Сталь и бетон, которые в настоящее время являются двумя наиболее распространенными строительными материалами, используемыми во всем мире, производят примерно 8 процентов мировых выбросов углерода.
Уже предпринимаются усилия по использованию технологий для уменьшения углеродного следа бетона и стали. Бетон можно использовать в качестве секвестра углерода, когда переработанный углекислый газ постоянно внедряется в цемент в процессе смешивания.Зеленый водород, производимый с использованием возобновляемых источников энергии, выглядит наиболее многообещающим решением для снижения углеродного следа стали, если его можно будет производить в больших количествах и транспортировать.
Не новый, не навсегда
Противники массового использования древесины говорят, что вырубка деревьев для строительства недопустима. Но Боди Кабийо, доктор философии. кандидат Калифорнийского университета в Беркли не согласен. Он говорит, что не видит, что массовый спрос станет проблемой в ближайшее время, но устойчивое управление лесами имеет важное значение.
«Нам действительно нужно помнить, что мы не создадим всплеск спроса на массивную древесину без устойчивых методов ведения лесного хозяйства», — говорит он. «Мы не хотим рубить 1000-летние деревья на массовую древесину».
«Потребители забывают, что мы уже вырубаем деревья для производства бумаги и пиломатериалов, — говорит Кабийо. Древесина используется для всего: от туалетной бумаги и тетрадей до настилов и мебели. Дело в том, говорит он, что деревья сажают и выращивают, чтобы их рубили для бесчисленных ежедневных нужд.
Массовая древесина может сыграть роль в создании экономики замкнутого цикла и обеспечить рабочие места в лесном хозяйстве, проектировании, строительстве и монтаже.
Строительство — это отрасль стоимостью 9 триллионов долларов, а массовое производство древесины — это растущее предприятие, которое недавно стало частью решения проблемы изменения климата. По оценкам, к 2027 году мировой рынок CLT, являющийся лишь одним из множества изделий из древесины массового производства, достигнет 3,5 млрд долларов США.
Грин говорит, что необходимо продолжать стимулировать инвестиции и инновации, чтобы найти способы строить лучше, и массовая древесина — это всего лишь ступенька к тому, что мы в конечном итоге можем сделать.
Некоторые мировые лидеры, использующие массивную древесину, включают Stora Enso в Финляндии, Mayr Melnhof Holz Holding AG в Австрии и Xlam Ltd. в Австралии и Новой Зеландии. Глобальный девелопер Lendlease построил несколько многоэтажных деревянных зданий на своей базе в Австралии. Walmart даже вступает в игру с массовой древесиной и заключает контракт со Structurlam, ведущим поставщиком массивной древесины в Северной Америке, на строительство новых офисов в кампусе.
Массовая древесина может сыграть роль в создании экономики замкнутого цикла и обеспечить рабочие места в лесном хозяйстве, проектировании, строительстве и монтаже, согласно отчету Forest Economic Advisors.В идеальном мире, по словам Боди, мы бы использовали меньше древесины для производства целлюлозы и бумаги — за счет увеличения переработки и других средств — чтобы вместо этого ее можно было использовать для производства массивной древесины.
«Переход от использования древесины с недолговечных продуктов к долговечным продуктам, таким как [здания], имел бы огромные преимущества для климата», — сказал Боди.
сталь против дерева против бетона
ширина: 80%;}
]]>
Сталь против дерева против бетона
Строительная инженерия зависит от знания строительных материалов и их соответствующих свойств, чтобы мы могли лучше прогнозировать поведение различных материалов при их применении к конструкции.Как правило, три (3) наиболее часто используемых материала в строительстве – это сталь, бетон и дерево/древесина. Знание преимуществ и недостатков каждого материала важно для обеспечения безопасного и экономичного подхода к проектированию конструкций. Итак, давайте взглянем на плюсы и минусы стали, дерева и бетона!
Конструкционная сталь
Сталь представляет собой сплав, состоящий в основном из железа и углерода. Другие элементы также примешиваются к сплаву, чтобы получить другие свойства.Одним из примеров является добавление хрома и никеля для создания нержавеющей стали. Увеличение содержания углерода в стали имеет ожидаемый эффект увеличения прочности материала на растяжение. Повышение содержания углерода делает сталь более хрупкой, что нежелательно для конструкционной стали.
Преимущества конструкционной стали
- Сталь имеет высокое соотношение прочности и веса. Таким образом, собственный вес стальных конструкций относительно невелик. Это свойство делает сталь очень привлекательным конструкционным материалом для высотных зданий, большепролетных мостов, сооружений, расположенных на грунтах с низкой несущей способностью и в районах с высокой сейсмической активностью.
- Пластичность. Перед разрушением сталь может подвергаться большой пластической деформации, что обеспечивает большой запас прочности.
- Предсказуемые свойства материала.
Свойства стали можно предсказать с высокой степенью достоверности. На самом деле сталь демонстрирует упругое поведение вплоть до относительно высокого и обычно четко определенного уровня напряжения. В отличие от железобетона свойства стали со временем существенно не изменяются.
- Скорость возведения. Стальные элементы просто устанавливаются на конструкцию, что сокращает время строительства.Обычно это приводит к более быстрой экономической отдаче в таких областях, как стоимость рабочей силы.
- Простота ремонта. Стальные конструкции в целом ремонтируются легко и быстро.
- Адаптация сборных конструкций. Сталь отлично подходит для сборного и массового производства.
- Многократное использование. Сталь можно использовать повторно после разборки конструкции.
- Расширение существующих структур. Стальные здания можно легко расширить, добавив новые отсеки или крылья. Стальные мосты могут быть расширены.
- Усталостная прочность. Стальные конструкции имеют относительно хорошую усталостную прочность.
Недостатки конструкционной стали
- Общая стоимость. Сталь очень энергоемкая и, естественно, более дорогая в производстве. Стальные конструкции могут быть более дорогими в строительстве, чем другие типы конструкций.
- Противопожарная защита. Прочность стали существенно снижается при нагреве при температурах, обычно наблюдаемых при пожарах в зданиях. Сталь также довольно быстро проводит и передает тепло от горящей части здания.Следовательно, стальные каркасы зданий должны иметь достаточную противопожарную защиту.
- Техническое обслуживание. Сталь, подвергающаяся воздействию окружающей среды, может повредить материал и даже загрязнить конструкцию в результате коррозии. Стальные конструкции, подверженные воздействию воздуха и воды, такие как мосты и башни, регулярно окрашиваются. Применение атмосферостойких и коррозионностойких сталей может устранить эту проблему.
- Склонность к короблению.
Из-за высокого отношения прочности к весу стальные сжимаемые элементы, как правило, более тонкие и, следовательно, более подвержены короблению, чем, скажем, железобетонные сжимаемые элементы.В результате требуется больше конструктивных соображений для улучшения сопротивления продольному изгибу тонких стальных сжимаемых элементов.
Программное обеспечение для проектирования стали SkyCiv
Рисунок 1. Обзор металлоконструкций
Железобетон
Бетон представляет собой смесь воды, цемента и заполнителей. Соотношение трех основных компонентов важно для создания бетонной смеси с желаемой прочностью на сжатие. Когда в бетон добавляют арматурные стальные стержни, два материала работают вместе: бетон обеспечивает прочность на сжатие, а сталь обеспечивает прочность на растяжение.
Преимущества железобетона
- Прочность на сжатие. Железобетон обладает высокой прочностью на сжатие по сравнению с другими строительными материалами.
- Прочность на растяжение. Благодаря армированию железобетон также может выдерживать значительные растягивающие напряжения.
- Огнестойкость. Бетон обладает хорошей способностью защищать арматурные стержни от огня в течение длительного времени. Это позволяет выиграть время для арматурных стержней, пока пожар не будет потушен.
- Материалы местного производства. Большинство материалов, необходимых для производства бетона, легко получить на месте, что делает бетон популярным и экономически выгодным выбором.
- Прочность. Железобетонная строительная система более долговечна, чем любая другая строительная система.
- Формуемость. Железобетон, как текучий материал в начале, может быть экономично отформован в почти безграничный диапазон форм.
- Низкие эксплуатационные расходы. Железобетон разработан так, чтобы быть прочным, с использованием недорогих материалов, таких как песок и вода, которые не требуют тщательного обслуживания.Бетон предназначен для того, чтобы полностью покрыть арматуру таким образом, чтобы арматура не была нарушена.
Это делает стоимость обслуживания железобетонных конструкций очень низкой.
- В конструкциях, таких как фундаменты, дамбы, опоры и т. д. железобетон является наиболее экономичным строительным материалом.
- Жесткость. Он действует как жесткий элемент с минимальным прогибом. Минимальный прогиб хорош для удобства эксплуатации зданий.
- Удобство использования. По сравнению с использованием стали в конструкции, при строительстве железобетонных конструкций может использоваться менее квалифицированный труд.
Недостатки железобетона
- Долгосрочное хранение. Бетон нельзя хранить после того, как он замешан, так как цемент вступает в реакцию с водой, и смесь затвердевает. Его основные ингредиенты должны храниться отдельно.
- Время отверждения. Бетон имеет тридцатидневный период отверждения. Этот фактор сильно влияет на график строительства здания. Это делает скорость возведения монолитного бетона медленнее, чем сталь, однако ее можно значительно улучшить с использованием сборного железобетона.
- Стоимость бланков. Стоимость форм, используемых для литья ЖБ, относительно выше.
- Большее сечение. Для многоэтажного здания секция железобетонной колонны (ЖБК) больше, чем стальная, поскольку прочность на сжатие ниже в случае ЖБК.
- Усадка. Усадка вызывает развитие трещин и потерю прочности.
Программное обеспечение SkyCiv RC Design
Рисунок 2. Типичный пример железобетона
Древесина
Древесина – органический, гигроскопичный и анизотропный материал.Его теплотехнические, акустические, электрические, механические, эстетические, рабочие и др. свойства очень удобны, при использовании только деревянных изделий можно построить комфортный дом. С другими материалами это практически невозможно. Очевидно, что древесина является обычным и исторически сложившимся материалом в качестве конструкционного инженерного материала. Однако за последние несколько десятилетий произошел отказ от дерева в пользу инженерных изделий или металлов, таких как алюминий.
Преимущества древесины
- Прочность на растяжение.Будучи относительно легким строительным материалом, древесина превосходит даже сталь по разрывной длине (или длине самонесущей конструкции). Проще говоря, он может лучше выдерживать собственный вес, что позволяет увеличить пространство и уменьшить количество необходимых опор в некоторых конструкциях зданий.
- Электрическая и термостойкость. Он имеет естественное сопротивление электропроводности при сушке до стандартного уровня влажности (MC), обычно от 7% до 12% для большинства пород древесины. Его прочность и размеры также не сильно зависят от тепла, что обеспечивает устойчивость готового здания и даже безопасность при определенных пожарных ситуациях.
- Звукопоглощение. Его акустические свойства делают его идеальным для минимизации эха в жилых или офисных помещениях. Дерево поглощает звук, а не отражает или усиливает его, и может помочь значительно снизить уровень шума для дополнительного комфорта.
- Местный источник. Древесина — это строительный материал, который можно выращивать и повторно выращивать с помощью естественных процессов, а также с помощью программ повторной посадки и управления лесным хозяйством. Выборочный сбор урожая и другие методы позволяют продолжать рост, пока собирают более крупные деревья.
- Экологически чистый. Одна из самых больших проблем со многими строительными материалами, включая бетон, металл и пластик, заключается в том, что после их выбрасывания требуется невероятно много времени для разложения. При воздействии естественных климатических условий древесина разрушается гораздо быстрее и фактически пополняет почву в процессе.
Недостатки древесины
Усадка и набухание древесины – один из основных ее недостатков.
Древесина является гигроскопичным материалом.Это означает, что он будет поглощать окружающие конденсируемые пары и отдавать влагу воздуху ниже точки насыщения волокна. Еще одним недостатком является его износ. Агенты, вызывающие порчу и разрушение древесины, делятся на две категории: биотические (биологические) и абиотические (небиологические). К биотическим агентам относятся гнилостные и плесневые грибы, бактерии и насекомые. К абиотическим агентам относятся солнце, ветер, вода, некоторые химические вещества и огонь.
Программное обеспечение для проектирования дерева SkyCiv
Рис. 3.Деревянный/деревянный каркас
Резюме
Для лучшего описания стали, бетона и дерева. Подытожим их основные характеристики, которые позволили бы выделить каждый материал.
Сталь очень прочна как на растяжение, так и на сжатие и поэтому обладает высокой прочностью на сжатие и растяжение. Сталь имеет предел прочности от 400 до 500 МПа (58-72,5 тысяч фунтов на квадратный дюйм). Это также пластичный материал, который уступает или прогибается перед разрушением. Сталь выделяется своей скоростью и эффективностью в строительстве. Его относительный легкий вес и простота конструкции позволяют использовать рабочую силу примерно на 10–20% меньше, чем при строительстве аналогичной бетонной конструкции. Стальные конструкции также обладают отличной долговечностью.
Бетон чрезвычайно прочен при сжатии и, следовательно, имеет высокую прочность на сжатие примерно от 17 МПа до 28 МПа. С более высокой прочностью до или выше 70 МПа. Бетон позволяет проектировать очень прочные и долговечные здания, а использование его тепловой массы за счет удержания его внутри оболочки здания может помочь регулировать внутреннюю температуру.Также в строительной отрасли все шире используется сборный железобетон, что дает преимущества с точки зрения воздействия на окружающую среду, стоимости и скорости строительства.
Древесина устойчива к воздействию электрического тока, что делает ее оптимальным материалом для электроизоляции. Прочность на растяжение также является одной из основных причин выбора древесины в качестве строительного материала; его исключительно прочные качества делают его идеальным выбором для тяжелых строительных материалов, таких как конструкционные балки. Дерево намного легче по объему, чем бетон и сталь, с ним легко работать, и оно легко адаптируется на месте. Он прочен, приводит к меньшему тепловому мостику, чем его аналоги, и легко включает сборные элементы. Его структурные характеристики очень высоки, а его прочность на сжатие аналогична прочности бетона. Несмотря на все это, древесина более широко используется для жилых и малоэтажных сооружений. Его редко используют в качестве основного материала для высотных конструкций.
Это наиболее распространенные строительные материалы, используемые для строительства.Каждый материал имеет свой уникальный набор преимуществ и недостатков. В конце концов, они могут быть заменены материалами, которые практически не имеют ограничений с технологическими достижениями в будущем. Несмотря на это, наши нынешние строительные материалы останутся актуальными на многие десятилетия вперед.
В центре внимания исследований: древесно-бетонные композитные системы — строительные технологии
Описание
Древесно-бетонные композиты представляют собой системы перекрытия и настила, состоящие из бетонной плиты, неразрывно соединенной с деревянными балками или слоистой деревянной плитой под ней с помощью соединителя, работающего на сдвиг. Использование соединителя на сдвиг может значительно повысить прочность и жесткость настила (примерно в 2 и 4 раза соответственно) по сравнению с несвязанной конструкцией, что приводит к высокоэффективному использованию материалов. Звуковые и вибрационные характеристики, а также огнестойкость также улучшены по сравнению с деревянными полами. Добавленная бетонная плита также часто может придать зданию дополнительную боковую жесткость. Эта система хорошо подходит как для реставрации, так и для нового строительства.
Основным преимуществом цельного соединения бетона с деревом является композиционное действие. Дерево и бетон действуют в унисон и, таким образом, достигают общей жесткости и прочности, которые превосходят любой из компонентов, действующих по отдельности. В результате действия композита бетонная плита испытывает преимущественно напряжения сжатия, а древесина испытывает преимущественно напряжения растяжения, что позволяет наилучшим образом использовать структурные свойства каждого материала. Конечным результатом является исключительная прочность и жесткость, а также меньший вес по сравнению с эквивалентной цельнобетонной секцией.
Современное использование WCC распространено по всей Европе. Несколько компаний предлагают металлические соединители, специально предназначенные для соединения бетонных плит с деревянными балками для достижения комбинированного действия. Среди них вклеенный растянутый металл, диагонально вставленные шурупы, стальные или бетонные ключи, армированные арматурой, и многие другие. Примеры последних проектов в Европе можно найти здесь: TICOMTEC
Экономические преимущества этой системы заключаются в экономии труда за счет использования древесины в качестве несъемной опалубки, использования меньшего количества материала для фундаментов в результате меньшей статической нагрузки на пол (дерево легче, чем бетон или сталь), а также, в случае восстановления. , сочетая конструктивные функции (улучшенная система пола и добавленная жесткая диафрагма), а также более быстрое время выполнения работ по сравнению с заменой пола.
BCT изучил множество различных аспектов древесно-бетонных композитных систем. Мы проверили прочность на сдвиг и жесткость различных крепежных элементов на сдвиг, а также общие характеристики деревянно-бетонной плиты – как для внутренних, так и для наружных работ. Мы также накопили опыт в анализе и проектировании этих систем. Для получения дополнительной информации см. список публикаций ниже.
Эта технология использовалась при строительстве здания Olver Design Building в Университете Массачусетса в Амхерсте, где на площади около 50 000 квадратных футов используется система BCT, протестированная и опубликованная в прошлом.См. верхнее изображение на этой странице для изображения этой установки.
Документы
- КЛОСТОН, П.; ШРЕЙЕР, А. 2012. « Экспериментальная оценка соединительных систем для деревянно-бетонных композитных полов при реконструкции мельничных зданий ». Международный журнал искусственно созданной среды, Vol. 2
- КЛОУСТОН, П.
; SCHREYER, A. 2011. Ферменные пластины для использования в качестве соединителей при сдвиге в ламинированных пиломатериалах – бетонных композитных системах. Proceedations, 2011 Конгресс структур ASCE SEI, Лас-Вегас, Невада, США
- КЛОУСТОН, П.; SCHREYER, A. 2008. Проектирование и использование древесно-бетонных композитов . Практическое издание ASCE по структурному проектированию и строительству, 13(4), стр. 167–175 .
- КЛОУСТОН, П.; SCHREYER, A. 2006. Древесно-бетонные композиты: структурно эффективный вариант материала . Практика гражданского строительства. Секция Бостонского общества инженеров-строителей (BSCE) / Американское общество инженеров-строителей (ASCE). Весна/Лето 2006
- КЛОУСТОН, П.; БАТОН, Л.; SCHREYER, A. 2005. Прочность на сдвиг и изгиб новой древесно-бетонной композитной системы .Журнал строительной инженерии ASCE. 131(9), стр.1404-1412
- КЛОУСТОН, П.; ЦИВЖАН, С.
; BATHON, L. 2004. Экспериментальное поведение непрерывного металлического соединителя для древесно-бетонной композитной системы . Журнал лесных товаров. 54(6) стр. 76-84
- Еще публикации…
Вовлеченный преподавательский состав
загрузок
Умная древесина может стать городским строительным материалом будущего
Архитектура (заново) открыла дерево как строительный материал для городских пространств.За последние месяцы два самых высоких деревянных здания в мире были построены в Вене, Австрия, и Брумунддале, Норвегия. Планируется даже строительство небоскреба в Токио. Об этом строительном материале можно сказать многое, подчеркивает профессор Йоханнес Коннерт из Университета природных ресурсов и наук о жизни (BOKU) в Вене. Использование древесины позволяет строить быстрее и эффективнее, а также более экологично.
В настоящее время наиболее распространенным строительным материалом является цемент, а значит, и бетон. В процессе производства потребляется большое количество ископаемого топлива и выделяется огромное количество CO2. Древесина, с другой стороны, получается из CO2 из атмосферы, солнечного света и дождя. Преобразование ствола в доску и, наконец, в готовый материал требует меньше энергии, чем вырабатывается из ископаемого топлива. Таким образом, древесина стала бы более эффективным строительным материалом и могла бы значительно сократить выбросы CO2, объясняет Коннерт. Тем не менее, исследования все еще должны быть проведены, прежде чем прорыв станет реальностью.Он преподает в Институте технологии обработки древесины и возобновляемых материалов BOKU. Сейчас он вводит там две новые исследовательские специализации. Его внимание сосредоточено на новых технологиях производства и интеллектуальных свойствах древесины. Исследователь Йоханнес Коннерт в интервью Innovation Origins:
При использовании древесины в строительстве многоэтажных зданий в городских районах – что следует учитывать в первую очередь?
Несущими материалами, которые в настоящее время в основном используются в Европе, являются клееный брус (GLT) и кросс-клееный брус (CLT). Оба материала очень безопасны, чрезвычайно универсальны и просты в расчетах. Древесина как строительный материал уже экономически конкурентоспособна, особенно для крупных сооружений, таких как стадионы, залы и бассейны. Преимущество перед бетоном и сталью заключается в более легком весе в сочетании с исключительной прочностью и жесткостью. Статическая нагрузка на балку также должна поддерживаться.
В классическом многоэтажном жилищном строительстве стоимость несущего каркаса в настоящее время примерно на 10% выше, чем в классическом бетонном строительстве.Этот недостаток может быть частично компенсирован значительно более быстрыми сроками строительства. Кроме того, использование древесины также влечет за собой более низкие транспортные расходы из-за ее относительной легкости. Тем не менее, его финансовый недостаток часто является решающим.
Подписывайтесь на IO в Telegram!
Хотите получать вдохновение 365 дней в году? Вот возможность. Предлагаем вам один «источник инноваций» в день в компактном Telegram-сообщении. Семь дней в неделю, доставка около 20:00. CET. Прямо из нашей редакции.Подпишитесь здесь, это бесплатно!
В производстве конструктивных пород древесины, упомянутых выше, еще есть возможности для улучшения, что потенциально может оказать огромное влияние на их общую себестоимость. Основная проблема — низкий выход с каждого бревна. Конические и гнутые стволы необходимо распилить на квадратные блоки по принципу «круг к квадрату». Обрезки составляют около 50% и отправляются в другие цепочки создания стоимости, такие как бумага, мебельный щит или гранулы. Затем доски сушат и строгают, что также приводит к увеличению потерь.
В конечном счете, только от 25% до 45% бревен остается в качестве высококачественного строительного материала. Альтернативные производственные процессы предлагают огромный потенциал, но также создают проблемы. С одной стороны, они должны иметь свойства GLT и CLT. С другой стороны, они должны быть в состоянии значительно сократить потери. Это позволит производить из древесины ресурсосберегающие материалы с выгодной структурой затрат.
В последние месяцы появилось несколько проектов маяков – какие из них?
Существует бесчисленное множество примеров деревянных коммерческих зданий.Среди многоэтажных зданий к ним относятся Hoho в Вене высотой 84 метра и Mjøstårnet в Брумунддале в Норвегии, которое высотой 85,4 метра в настоящее время является самым высоким деревянным зданием в мире. Одним из первых многоэтажных зданий является Stadthaus в Лондоне, построенный в 2009 году.
Японский консорциум планирует построить 350-метровую деревянную башню в центре Токио – сейсмоопасной зоне. За ним стоят старейшее японское архитектурное бюро Nikken Sekkei и японская деревообрабатывающая компания Sumitomo Forestry Co., ООО . Но она не обязательно может быть такой высокой. Подавляющее большинство людей живут в домах от трех до десяти этажей.
«Если нам удастся предложить разумные и доступные альтернативы для домов от трех до десяти этажей, то деревянное строительство также испытает прорыв в городских условиях».
Профессор Йоханнес Коннерт.
Как повысить рентабельность древесины как строительного материала?
Как описано выше, посредством новых производственных процессов и избегая чрезмерных потерь потенциальной ценности, создаваемой в этих процессах.Чтобы производить изделия из дерева в больших масштабах, не обязательно делать квадратные блоки. В настоящее время промышленность вполне способна продавать эти побочные продукты в секторе биоэнергетики.
Тем не менее, есть еще одна проблема. В настоящее время в основе большинства этих изделий лежит хвойная древесина и чаще всего ель. Однако хвойные леса подвергаются давлению в результате изменения климата и увеличения периодов засухи. В Центральной Европе уже идет массовое переустройство лесов.Следовательно, это означает, что в будущих производственных процессах должны использоваться и другие породы древесины. В настоящее время это возможно только в ограниченной степени. Нужны новые производственные процессы, они также должны быть более универсальными в отношении доступных ресурсов.
Чем так привлекательна ель? И какие альтернативы существуют?
Ель имеет много преимуществ. Среди прочего, он есть или был очень легко доступен и растет прямо. Это актуально с точки зрения урожайности.Спрайс также легко обрабатывается и легко склеивается, а также обладает очень хорошим набором природных свойств.
Альтернативы должны соответствовать как минимум двум условиям. Во-первых, они должны быть способны выдерживать изменяющиеся климатические условия. Кроме того, их ствол должен был достигать определенного диаметра, чтобы быть полезным. В то же время должны быть технологии их более эффективной переработки, чтобы мы могли производить конечные продукты с высокими эксплуатационными характеристиками. В этом отношении Спрюс всегда была чрезвычайно гибкой.Последующие альтернативные сорта древесины, вероятно, будут использоваться гораздо более конкретно.
Ожидается, что интеллектуальное дерево появится в результате одного из новых направлений исследований.
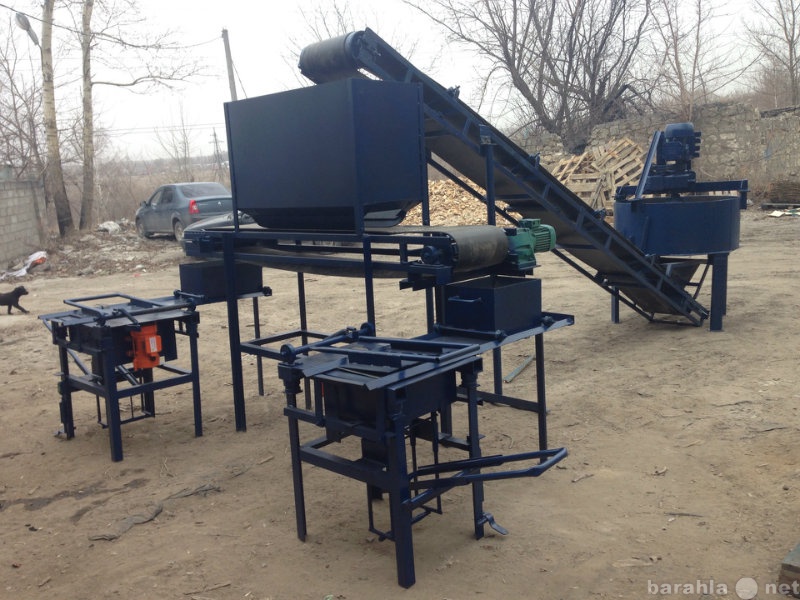
Мы проведем фундаментальные исследования нанотехнологических концепций материалов на основе лигноцеллюлозных материалов. Целлюлоза является ключевым компонентом древесины ( lignum ). По сути, это означает, что это материалы, полученные из древесины.Для производства таких материалов используются как механические, так и химические процессы. Основными химическими компонентами древесины являются целлюлоза, лигнин и гемицеллюлоза. Они могут присутствовать в различных пропорциях в конечных продуктах и могут не обязательно соответствовать натуральному составу. В некоторых случаях свойства можно изменить, просто изменив состав. Другие модификации также могут быть сделаны, чтобы создать определенные свойства.
Что касается новых функций древесины – какие параметры свойств необходимо разработать?
Мы должны показать, что древесина является или может быть высокотехнологичным материалом и во многих случаях слишком ценна, чтобы ее сжигать. Умная древесина, например, может взять на себя функцию датчика и регулировать климат в жилых помещениях. В прошлом группа по науке о древесных материалах профессора Инго Бургерта в ETH Zurich в Швейцарии представила примеры этого. Я также сотрудничаю с ними в этой области.
Спасибо за это интервью.
Также интересно:
Стартап дня: Работа с природой, а не против нее
Бесплатно посадить лес в Испании в помощь климату
И статьи IO об устойчивой древесине в целом.
Дерево против бетона: лучший выбор для строителей и GC
Дерево и бетон использовались в строительстве тысячи лет и не зря. Оба материала обладают свойствами, которые делают их привлекательными строительными материалами.
В этом блоге мы поднимем извечный спор между деревом и бетоном. Но прежде чем мы с головой погрузимся в эту жаркую дискуссию, необходимо учесть несколько соображений.
Как профессионалы в области строительства, мы знаем, что вы можете смотреть на этот вопрос с разных точек зрения, что в конечном итоге влияет на вашу интерпретацию преимуществ и недостатков, перечисленных ниже. Мы также признаем различие между непосредственными преимуществами и долгосрочными выгодами. Другими словами, преимущества, которые материал обеспечивает в долгосрочной перспективе, могут перевесить недостатки, с которыми вы сталкиваетесь сегодня. Поэтому, читая этот пост, вы должны помнить о своих собственных приоритетах.
Подробный обзор бетонных конструкций
Согласно этому исследованию, бетон является вторым наиболее используемым материалом после воды, и есть много причин, почему он так популярен. Тем не менее, у использования бетона в качестве строительного материала есть свои преимущества и недостатки:
Преимущества бетона
- Очень прочный
- Низкие эксплуатационные расходы
- Не ржавеет, не гниет и не горит
- Поглощает и сохраняет тепло (повышает эффективность зданий и сокращает счета за отопление/охлаждение)
- Ветро- и водостойкий
- Негорючий (пожаробезопасный)
- Эффективный звукоизоляционный материал
Недостатки бетона
- Дороже
- Тяжелый и трудно транспортируемый (хотя легкий бетон существует)
- Ограниченная универсальность
- Медленнее строить с
- Склонен к выцветанию
Подробный обзор деревянных конструкций
Точно так же, как бетон, дерево или древесина имеют свои преимущества и недостатки в качестве строительного материала:
Преимущества дерева
- Легкий и удобный в работе
- Недорогой
- Природный ресурс (легкодоступный, открывающий многообещающие возможности)
Недостатки древесины
Как и бетон, деревянное строительство имеет свои преимущества и недостатки.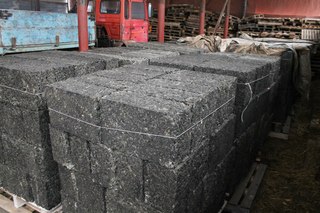
Устойчивое развитие и окружающая среда
Когда мы думаем о дереве, мы часто представляем себе натуральный, устойчивый и экологически чистый строительный материал. И во многом так оно и есть. Древесина удерживает углекислый газ, что приводит к сокращению выбросов углекислого газа на 2432 метрических тонны (что эквивалентно снятию с дорог 500 автомобилей в год).
Бетончасто критикуют за то, что он неустойчив, поскольку для его производства требуется много ресурсов. Цемент, основной компонент бетона, является одним из крупнейших в мире источников выбросов парниковых газов.Многие люди предполагают, что поскольку производство цемента вредно для окружающей среды, то и производство бетона вредно. Но правда гораздо сложнее, чем это.
Давайте посмотрим поближе…
- Бетон долговечен — его срок службы фактически в два или три раза больше, чем у других обычных строительных материалов.
- Бетон отлично поглощает и удерживает тепло, а это означает, что он повысит энергоэффективность здания и сократит расходы на ОВКВ.
- Его отражающие свойства уменьшат затраты на кондиционирование воздуха в жаркие летние месяцы. Бетон
- производит мало отходов , поскольку его можно производить партиями, специфичными для нужд проекта.
Что безопаснее: бетон или дерево?
И последнее, но не менее важное: безопасность. В целом деревянные конструкции не так безопасны, как бетонные. Древесина уязвима для внешних угроз, таких как огонь, ветер, насекомые, влага и плесень, — все это может привести к структурным повреждениям и рискам для безопасности.
Несмотря на то, что бетон является долговечным и прочным материалом, он также представляет определенные риски для безопасности. Например, в случае обрушения бетонной конструкции либо на стройплощадке, либо после того, как здание занято, падающий бетон может серьезно травмировать любого, кто находится поблизости.
Кроме того, если вы строитель, работающий с сухим или влажным бетоном, у вас может возникнуть раздражение глаз, носа, горла или кожи. Кроме того, воздействие кремнезема, основного ингредиента сухого бетона, может вызвать гораздо более серьезные проблемы со здоровьем, включая рак легких.
Теперь, когда вы знаете все о строительстве из бетона и дерева, что бы вы выбрали? Дайте нам знать, комментируя ниже!
Источники
Цемент и бетон как конструкционные материалы: историческая оценка и анализ конкретных случаев
Средства защиты от плесени
Страхование наследия
**Примечание редактора: этот пост был первоначально опубликован 25 апреля 2018 г. и был обновлен для обеспечения точности и полноты.
3 способа сделать ваш бетонный бизнес более прибыльным
Производство бетона — отличный бизнес, но не без проблем.
Растущие материалы и рабочая сила расходы сокращают размер прибыли; усиление конкуренции со стороны других строительных материалов сокращает долю рынка ; а социальное и политическое давление вынуждает производителей бетона инвестировать в более методов устойчивого производства .
Несмотря на эти серьезные проблемы, производители бетона сохраняют устойчивость, предпринимая действия, чтобы их предприятия оставались прибыльными и продуктивными. В этом сообщении в блоге описаны три места для начала:
.- Снижение затрат на производство бетона за счет уменьшения количества цемента;
- Повышение эффективности процессов за счет инвестиций в технологии и удержания талантов;
- Применяйте устойчивые методы производства, чтобы конкурировать за долю рынка.
Для более глубокого изучения загрузите нашу электронную книгу «Секреты повышения рентабельности вашего бетона» .
1. Снижение затрат на производство бетона за счет уменьшения количества цемента
Снижение производственных затрат — один из самых быстрых способов повысить рентабельность. Для производителей бетона это означает сокращение использования их самого дорогого ингредиента — цемента. Заменяя или уменьшая количество цемента, необходимого для производства качественного бетона, производители могут значительно повысить прибыльность.
Репутация производителя бетона зависит от качества и долговечности его продукции, поэтому изменение методов производства сопряжено с определенным риском. К счастью, есть способы снизить этот риск, используя проверенные технологии материалов и дизайны смесей.
Одним из способов является оптимизация составов смесей с использованием дополнительных вяжущих материалов (SCM), таких как летучая зола, побочный продукт угольной промышленности, который стоит значительно дешевле , чем цемент, но сохраняет такое же качество. Исследования доказали, что SCM действительно увеличивают прочность бетона с течением времени до уровней, превышающих прочность традиционных бетонных смесей.
Еще одним способом снижения производственных затрат является внедрение инновационных технологий утилизации углерода, таких как CarbonCure, при котором переработанный CO₂ впрыскивается в свежий бетон во время смешивания. После введения CO₂ вступает в химическую реакцию, в ходе которой он превращается в минерал, повышая прочность бетона на сжатие. Это приводит к корректировке состава смеси с учетом добавления CO₂ и увеличения прочности; содержание цемента может быть уменьшено при сохранении прочности и эксплуатационных характеристик бетона.
Производители бетона могут повысить прибыльность своего бизнеса, используя технологии для улучшения процессов доставки и контроля качества, а также применяя стратегии для привлечения и удержания талантов.
Многие производители уже используют программное обеспечение для отправки и контроля качества, такое как Command Alkon или Jonel , для объединения данных, полученных на этапе коммерческого предложения, для планирования работ, ввода заказов, планирования ресурсов, планирования материалов, программного обеспечения для смешивания, отправки и доставки. Интеллектуальные данные, полученные с помощью этих инструментов, позволяют улучшить процессы доставки и контроля качества, что может значительно повлиять на итоговую прибыль производителя и помочь сократить количество отходов.
Некоторые производители отмечают, что внедрение инновационных технологий и процессов оказывает положительное влияние на прием на работу . Эти инновации помогают оживить взгляды людей на строительную отрасль в целом и могут привлечь молодых работников на рынок, который сталкивается с острой нехваткой рабочей силы.Кроме того, внедрив устойчивых инноваций , производители бетона могут привлечь экологически сознательных кандидатов из миллениалов и представителей поколения Z.
Скачать электронную книгу
Столкнувшись с проблемами роста затрат, общественным давлением в отношении экологичных строительных материалов и изменениями в нормативных актах в пользу экологически чистых методов строительства, бетонная промышленность переживает трансформацию.
Умные производители бетона стратегически планируют будущее, обращая внимание на новых инноваций , чтобы они могли эффективно вернуть себе долю рынка и позиционировать устойчивость как конкурентное преимущество.
И это очень скоро. За последние несколько лет индустрия массового деревянного строительства (MTC) уже завоевала популярность на многих ключевых строительных рынках, отняв долю рынка у производителей бетона. На рынке существует мнение, что присущая древесине способность накапливать углерод делает ее более экологичным выбором для строительства. Однако недавние исследования доказывают, что лишь небольшое количество (около 15 процентов ) углерода, первоначально хранившегося в живом, стоящем дереве, улавливается в конечном продукте из древесины.И в то время как древесина в зданиях удерживает небольшое количество углерода, древесина на свалках фактически выделяет метан, который имеет потенциал глобального потепления в 28-36 раз больше, чем CO₂ .
Обучив продавцов справляться с возражениями по поводу устойчивого развития, производители могут вернуть долю рынка, утраченную в последнее время из-за дерева, и рассказать о преимуществах бетона — он более устойчив к стихийным бедствиям, служит дольше, локален (большинство видов бетона используется в небольшом радиусе места его производства), и он может непрерывно улавливать углерод в течение всего срока службы конструкции.
Производители также могут получить новую долю рынка, внедрив такие технологии, как технология CarbonCure, чтобы предлагать устойчивые бетонные изделия на рынке, который жаждет решений. Когда производители бетона вводят CO₂ в бетон с помощью CarbonCure, выбросы CO₂, которые когда-то были в атмосфере, используются для производства более экологичного бетона. Повышение прочности за счет добавления CO₂ позволяет производителям снизить процентное содержание вяжущего вещества в некоторых смесях, сохраняя при этом требования к прочности .
Кроме того, из-за химической реакции, которая происходит между CO₂ и бетонной смесью, CO₂ становится минералом и, следовательно, постоянно внедряется в бетон и никогда не выбрасывается в атмосферу. Такое использование CO₂ в бетоне не только устойчиво, но и выгодно для бизнеса. Аналитики говорят, что к 2030 году она может превратиться в глобальную индустрию с оборотом 400 миллиардов долларов .
Производители, которые не думают о разработке устойчивых бетонных смесей, упустят эту возможность для бизнеса. и уступят значительную долю рынка конкурентам, поскольку все больше отраслевых ассоциаций и государственных органов устанавливают стандарты для методов строительства, снижающих выбросы углерода.
Бетонная промышленность является одной из старейших отраслей промышленности в мире, потому что на протяжении столетий она продолжала адаптироваться и внедрять инновации для удовлетворения потребностей общества.