Производство газобетона технология: Технология производства автоклавного газобетона — этапы
Технология
Газобетон
Производство автоклавного газобетона по технологии WKB Systems GmbH
Преимущества технологической линии:
- Высокая производительность технологической линии — 300 тыс. м3в год обусловлена полной автоматизацией производственного процесса.
- Литьевая технология фирмы WKB позволяет добиться высокой однородности готовых изделий по плотности и прочности.
- Установленная на линии система контроля дозирования и перемешивания компонентов позволяет отслеживать весь процесс производства газобетона с заданными стабильными параметрами.
- Пневматически натянутые металлические струны, расположенные в смещенном положении, входят и выходят из массива под углом 0-60 градусов, что позволяет получать изделия с максимальными отклонениями не более 1 мм.
- Технология фирмы WKB подразумевает использование на линии резки двух кантователей, что позволяет избежать автоклавирования донного слоя и тем самым избежать не вынужденных отходов в производстве.
- Благодаря способу штабелирования WKB возможно размещение трех автоклавных поддонов на одной автоклавной вагонетке. При этом один автоклавный поддон размещается на двух стоящих рядом поддонах. Этот способ гарантирует оптимальное использование автоклава и значительное снижение расходов на энергоресурсы.
- Регенерация тепла в процессе автоклавирования позволяет обеспечить цех паром на отопление и подогрев воды на производство в холодное время года.
О высоком уровне сервиса нашего предприятия
можно судить по внимательному отношению к мельчайшим деталям.
Компаний доверяют
нашей продукции
Работаем с регионами
Производство:
Краснодарский край, Динской район,
станица Васюринская,
Мы производим большой
ассортимент продукции для гражданского и промышленного строительства.
Стоимость доставки зависит от удаленность строящегося объекта заказчика от нашего производства,
а так же от объема доставляемой продукции.
Технология производства автоклавного газобетона.. Статьи компании «АБАДОМ»
Дозировка и рецептура
В отдельных бункерах подготавливаются все основные компоненты: цемент, кварцевый песок (либо зола уноса), газообразователи, гипс и известь. В качестве специализированных газообразователей используются алюминиевые пасты и пудры. Песок (либо зола уноса) предварительно перемалывается до состояния муки.
Экологически чистые компоненты, точность дозирования компонентов и отработанная рецептура позволяют производить строительные блоки с заданными характеристиками плотности и прочности. Мы предлагаем 4 вида плотности.
В специальном бункере происходит смешивание компонентов в регламентированных дозах.
Тщательное перемешивание позволяет получить однородную массу и обеспечить стабильные характеристики по всему массиву.
Заливка формСырье, смешанное с водой, тщательно перемешивается и заливается в форму.
Заливка крупной формы позволяет оптимизировать процесс перемещения массива газобетона по всей технологической линии и увеличить производительность производства.
Процесс порообразованияОбразование замкнутых пор в массе бетона придает газобетону его уникальные характеристики по энергоэффективности.
Передовые технологии, применяемые в процессе порообразования, а, в частности, встряхивание массива, позволяют распределить газообразователь равномерно по всему объёму массива.
Камера предварительного созревания (горячий тоннель)В камере предварительного созревания происходит реакция гидратации цемента параллельно с реакцией газообразования.
В условиях стабильной температуры 35–40 градусов в течение 3–4-х часов происходит вспучивание массива бетона за счет выделения водорода, и происходит созревание бетонной смеси (набор распалубочной прочности).
Линия резкиМассив газобетона попадает на линию струнной резки, где при помощи кантования массива происходит нарезка в трех плоскостях.
Идеальная геометрия строительных блоков.
Выборка захватов для рук и формирование системы паз-гребеньВысококлассное оборудование позволяет кроме обычной резки выполнять прорезывание системы паз-гребень и устройство захватов для рук.
Преимущества — захваты для рук упрощают работу с блоком, а система паз-гребень обеспечивает непродуваемость кладки из автоклавного газобетона.
Отличительной особенностью производства качественного газобетона является обработка строительных блоков в автоклаве. Автоклавирование проходит при температуре 180 градусов и давлении 12 атмосфер.
Автоклавирование позволяет сократить сроки набора прочности, повысить конечную прочность строительных блоков. В результате автоклавирования в строительных блоках из автоклавного газобетона отсутствует усадка.
Контроль качестваКонтроль качества продукции на выходе с производства осуществляется отделом технического контроля и аккредитованной лабораторией.
Присутствует высокий контроль качества на всех стадиях производства.
Упаковка продукцииПосле проведения технического контроля строительные блоки из автоклавного газобетона поступают на участок упаковки, здесь они укладываются на деревянные поддоны, упаковываются полиэтиленовой пленкой и перетягиваются стреплентами.
Упаковывание строительных блоков на производстве позволяет обеспечить сохранность продукции, а также обеспечивает удобство при складировании и транспортировке.
Склад готовой продукцииНа специально подготовленных площадках продукция хранится до отгрузки клиенту.
Соблюдение требований складирования и хранения позволяет гарантировать сохранность продукции и обеспечить наличие качественного продукта в любое время в любом объеме.
ДоставкаДоставка клиенту возможна автотранспортом. Доступна услуга самовывоза.
Для Вас бесплатное хранение газобетона:
- Вы можете оплатить материалы, для того чтобы зафиксировать цену, и оставить их на хранение до начала строительных работ;
- проекты индивидуальных жилых домов от производителя «Байкальский газобетон».
Наши добрые менеджеры Вас ждут!
Мы находимся: г. Абакан, ул. Буденного, 116 с. Звоните т. 8 (3902) 202-225.
OPK — Статьи о газобетоне
ОСНОВНЫЕ ПРЕИМУЩЕСТВА ПРОИЗВОДСТВА И ПРИМЕНЕНИЯ СТЕНОВЫХ БЛОКОВ ИЗ НЕАВТОКЛАВНОГО ГАЗОБЕТОНА ПО ВИБРОУДАРНОЙ ТЕХНОЛОГИИ НА ЗАВОДАХ НОВОГО ПОКОЛЕНИЯ
В настоящее время массово выпускаются стеновые блоки из ячеистого бетона, изготовленные по автоклавному газобетонному и по неавтоклавному пенобетонному способу производства.
Широко известен тот факт, что показатели физико-технических характеристик пенобетона при одинаковой плотности, особенно в востребованных сейчас марках D500 — D600, намного уступают аналогичным показателям автоклавного газобетона. Много нареканий к пенобетонным блокам по соблюдению геометрических размеров. Однако очевиден факт более низких начальных и производственных капиталовложений в технологию ячеистого бетона по неавтоклавному способу производства. Поэтому, приступая к разработке новой технологии, наше предприятие ставило задачу объединить все лучшие достижения и научные разработки как внедренные, так и перспективные в области технологии ячеистого бетона по автоклавному и неавтоклавному способу производства.
Целью нашей компании стало получение неавтоклавного ячеистого бетона, которой по своим основным эксплуатационным и потребительским свойствам не уступает автоклавному газобетону.
Анализируя результаты, достигнутые на действующих производствах, уже с уверенностью можно сказать, что поставленная цель, достигнута.
Как уже было сказано, нами был выбран путь синтеза лучших достижений из автоклавного и неавтоклавного способов производства. В результате мы постепенно произвели переход от традиционной пенобетонной технологии и выпуска соответствующего оборудования на принципиально новое направление – производство неавтоклавного газобетона по ударной технологии.
Остановимся на этом более подробно.
В настоящее время в технологии автоклавного способа производства одним из наиболее перспективных направлений является так называемый ударный способ формовки. Именно это направление получило развитие и используется в производстве на российских и белорусских газобетонных предприятиях. Разработки российских, белорусских и эстонских ученых (Меркин А.П., Терентьев А.Е., Сажнев Н.П., Домбровский А. В., Куннос Г.Я.) позволили значимо улучшить физико-технические характеристики газобетона. Эти разработки получили мировое признание. В настоящее время несколько западных компаний — производителей оборудования для автоклавного газобетона, среди которых такая известная фирма, как «Masa-Henke», используют при строительстве заводов оборудование для ударной технологии производства газобетона.
Способ формовки массивов из вязких газобетонных смесей с применением ударных динамических воздействий мы с успехом использовали в ходе разработки технологии неавтоклавного газобетона.
Вторым значимым направлением является разработанная в ХХ веке, технология производства ячеистого бетона по автоклавной и неавтоклавной технологии с применением микронаполнителей (золы-уноса, шлаковой пыли, карбонатной муки и т.д.). Использование преимуществ этой технологии в комплексе с добавками-модификаторами (пластифицирующие, ускорители схватывания и твердения и т.д.) позволило наладить выпуск продукции, которая успешно прошла сертификационные испытания на соответствие нормативных требований к блокам из неавтоклавного ячеистого бетона.
Из современных достижений в области производства неавтоклавного пенобетона были учтены положительные результаты использования дисперсного армирования микрофиброй. Микрофибра может быть изготовлена из минерального (базальтовое, стекловолокно) и синтетического (пропилен, лавсан) сырья. Благодаря применению микрофибры получены нерасслаиваемые газобетонные смеси.Плотность газобетона в верхней и нижней части массива практически одинакова, что недостижимо в литьевой технологии автоклавного газобетона. Кроме того микрофибра значительно повышает трещиностойкость изделий.
Способ формования | Высота формуемого массива,м | Плотность бетона,кг/м3 | Коэффицент вариации | Разность плотности между верхним и нижним слоем,кг/м3 |
Литьевой(автоклавный)* |
0,9 1,6 |
700 620 |
0. 0,15…0,18 |
55 75 |
Ударный(автоклавный)* |
0,6 1,5 |
600 600 |
0,11…0,13 0,11…0,15 |
20 45 |
Ударный (фиброгазобетон) | 0,6 | 600 | 0,06…0,09 | 15 |
*Н.П.Сажнев и др.Производство ячеистобетонных изделий:теория и практика.-Минск:Стринко,1999.С.124
В технологии пенобетона в последнее время получил развитие низкоэнергоемкий способ тепловой обработки изделий методом «термосного» самозапаривания. При этом затраты на тепловую обработку снижаются в 2 раза. Все это было учтено в наших разработках.
Энергозатраты на тепловую обработку при производстве ячеистого бетона маркой по плотности D500,Гкал/м3 | |
Автоклавный газобетон | Неавтоклавный фиброгазобетон |
0,6 | 0,3 |
Одним из основных доводов в пользу автоклавной технологии производства газобетона приводится факт соблюдения точности геометрических размеров выпускаемой продукции. Благодаря такой точности возможна кладка стеновых блоков на тонкошовные клеевые растворы, что повышает теплозащитные свойства таких стен. Поэтому нашими специалистами был разработан комплекс оборудования, включающий резательный станок нового поколения. На сегодняшний день это единственная в мире технология программируемой резки газобетонных массивов, в которой возможно получение заданных геометрических размеров блоков с точностью ±1мм. При этом учтено требование нового ГОСТ 31360-2007 об изготовлении стеновых блоков с любыми размерами (кроме длины) под заказ потребителя. На данном станке можно получать блоки по ширине и толщине с шагом типоразмерного ряда в 1 мм, т.е. практически любые размеры. Из одного массива одновременно можно нарезать стеновые и перегородочные блоки. Перепрограммирование занимает считанные минуты. На современных заводах автоклавного газобетона на сегодняшний день это сделать невозможно.
Наименование показателя | Для показателей автоклавного газобетона блоки 1-й категории | Для показателей газобетона на координатном ленточнопильном станке Риф-1 |
Отклонение геометрических размеров, не более,мм: | ||
по длине | ±3 | ±1 |
по ширине | ±2 | ±1 |
по высоте | ±1 | ±1 |
Благодаря такому комплексному подходу в процессе серийного производства стеновых блоков на наших заводах по газобетонной ударной технологии достигнуты показатели, близкие по своим основным эксплуатационным свойствам к автоклавному газобетону. Полученные результаты намного превосходят технико-экономические показатели производства неавтоклавного пенобетона.
Наименование технических показателей | Значения технических показателей для разных видов ячеистого бетона | ||
Неавтоклавный пенобетон | Автоклавный газобетон | Неавтоклавный газобетон | |
Марка по средней плотности | D600 | D600 | D600 |
Предел прочности при сжатии, МПа | 1,2…2,0 | 2,5…4,9 | 2,5…3,5 |
Коээф. теплопроводности в сух.состянии lо, Вт/моС | 0,14 | 0,14 | 0,11…0,14 |
Марка по морозостойкости | F15 | F25 | F25 |
Одним из самых дискуссионых в настоящее время стал вопрос о долговечности автоклавного газобетона. Как известно, основным носителем прочности в автоклавном бетоне является тоберморит. Независимые исследования показали, что автоклавный газобетон, в отличии от неавтоклавного, подвержен процессу старения, связанного с карбонатным разрушением тоберморитовой связки (Сажнев Н.П. и др.Производство ячестобетонных изделий:теория и практика.-Минск:Стринко,2010.-С.67-68). Падение прочности автоклавного газобетона и газосиликата с маркой по плотности D500 может достигать после окончания карбонизации от 20 до 50% (Силаенков Е.С. Долговечность изделий из ячеистых бетонов.-М.:Стройиздат,1986.-с.85-87). В ходе карбонизации плотность газобетона может увеличиться на 20%, что приведет к ухудшению теплозащитных свойств такого бетона. Производители автоклавного газобетона приводят примеры существования зданий из автоклавного газобетона, построенных еще 60-80 лет назад. Но при этом надо сказать, что стеновые блоки производились с гораздо большей плотностью и цемента с известью тогда не жалели. В погоне за низкой себестоимостью и отпускной ценой производители автоклавного газобетона могут идти на уменьшение расхода дорогостоящего цемента и извести, тем самым еще более ухудшая его долговечность.
Вид ячеистого бетона | Плотность,кг/м3 | Расход вяжущего,кг/м3 | Прочности при сжатии,МПа |
|
||
цемент | известь | по карбонизации | после карбонизации | |||
Автоклавный газосиликат, газобетон | 502 | — | 107 | 4,3 | 2 | 51 |
512 | 70 | 47 | 2,7 | 1,7 | 63 | |
484 | 43 | 65 | 2,5 | 1,9 | 76 | |
Неавтоклавный газобетонот начальной | 490 | 200 | — | 2,4 | 2,7 | 112 |
Очень перспективным направлением на сегодняшний день является технология получения ВНВ – вяжущего низкой водопотребности. Применение именно этой технологии в наших исследованиях позволило получить материалы, аналогичные по своим основным эксплутационным свойствам и даже превосходящие по показателям долговечности автоклавный газобетон. Работа в этом направлении успешно ведется и эта технология уже сейчас внедряется нами на вновь проектируемых производствах.
Наименование технических показателей | Значения технических показателей для разных видов ячеистого бетона | ||
Неавтоклавный пенобетон | Автоклавный газобетон | Неавтоклавный газобетон по технологии ВНВ | |
Марка по средней плотности | D500 | D500 | D500 |
Предел прочности при сжатии, МПа | 0,8…1,2 | 2,0…3,5 | 2,0…3,5 |
Марка по морозостойкости | F15 | F25 | F35 |
© 2010 г. «Объединенная промышленная компания» Хабиров Д.М, Загарских С.А. ОПК
Газобетонные блоки своими руками: технология изготовления
Сегодня для строительства все чаще применяются материалы, которые можно сделать своими руками, закупив только необходимые ингредиенты. Все они характеризуются отличными эксплуатационными особенностями, прочностью; стоимость их выходит в итоге не слишком большая. Одним из таких материалов является газобетон. Укладка блоков простая, а сам материал отличается многочисленными достоинствами включая хорошие теплоизоляционные свойства, важные для строительства дома.
Газобетонные блоки имеют хорошие теплоизоляционные свойства.
Газобетон не является новинкой на рынке, впервые он использовался для строительства еще в начале прошлого века. Активное его применение в сооружении зданий началось около 10 лет назад. Хотя сама технология изготовления газобетона была запатентована Эриксоном, архитектором из Швеции, в далеком 1924 году.
Ранее газобетон изготавливался только в заводских условиях, так как для этого требовалось в точности соблюдать технологию и подбор пропорции для замешивания. Само производство несложное, но вес одного блока, который получается после заливки, не самый малый, поэтому работы надо выполнять хотя бы вдвоем.
Для производства газобетона потребуются:
Таблица производства газобетонных блоков.
- портландцемент;
- кварцевый песок;
- алюминиевая пудра;
- вода;
- известь.
Сам процесс изготовления основан на использовании одного из 2-х методов:
- автоклавного;
- неавтоклавного.
Первый метод применяется в заводских условиях, так как для него необходимо наличие спецоборудования. Блоки после заливки спекаются при специально созданных условиях. Самостоятельно создать их не получится, поэтому практичнее использовать 2-й метод. Бетон заливается в формы и высыхает в естественных условиях. Газобетонный блок затем извлекается и при необходимости разрезается на части. Хотя лучше сразу использовать для заливки формы, которые соответствуют требуемым размерам.
Компоненты для изготовления смеси
Чтобы сделать газобетонные блоки своими руками, необходимо приготовить следующие ингредиенты:
Таблица размеров газобетонных блоков.
- На каждый кубометр готового газобетона (по выходу) требуется примерно 250-300 л воды. Это должна быть чистая питьевая воды. Лучше всего ее брать из поверхностных слоев любых чистых источников.
- На кубометр готового газобетона требуется примерно 260-320 кг цемента. Для самостоятельного изготовления используются марки M500D0, M400D0.
- Карьерный песок, речной, очищенный. Количество его на кубометр готовой смеси составляет 250-350 кг. Лучше всего брать мелкий, размер частиц которого составляет до 2 мм.
Ни в коем случае не допускается содержание веток, мусора, глины.
- Специальные добавки для газобетона. Количество 1-3 кг на каждый кубометр готовой смеси.
- Газообразователь, т. е. алюминиевая пудра. Достаточно 0,5-0,7 кг на каждый готовый кубометр бетона. Пудра нужна для того, чтобы в смеси началась реакция, необходимая для газообразования. Во время замешивания начинает выделяться газ, внутри бетона образуются пузырьки, ячейки, которые и придают составу необходимые ему качества.
- Смазка для контейнеров в количестве 0,3-0,5 кг на куб. Перед тем как начать заливку эмульсиями тщательно смазываются формы. Нельзя применять отработанные масла, так как они содержат большое количество сажи.
Сделать газобетон своими руками не так сложно, но важно в точности соблюдать все этапы производства, подобрать ингредиенты для будущей смеси в правильной пропорции.
Список оборудования:
- Формы для заливки будущих газобетонных блоков, которые могут иметь различный размер.
Лучше всего приобретать уже готовые контейнеры.
- Струны, которые необходимы для удаления излишков смеси с поверхности форм.
- Бетономешалка, которая будет использована для перемешивания смеси.
Требования к ингредиентам
Таблица сравнения характеристик газобетона и пенобетона.
Самостоятельно сделать большой объем строительного материала не получится, но для сооружения небольшого дома их вполне хватит. Вес одного блока стандартного размера может составлять примерно 650 кг. Поэтому необходимо присутствие нескольких человек не только для выполнения кладки стен, но и для заливки форм, вытаскивания газобетонных блоков из контейнеров. При выполнении всех условий газобетонные блоки получатся прочными и качественными, стоимость их будет меньше, чем при покупке уже готового материала.
Можно использовать специальные установки, которые замешивают газобетон в автоматическом режиме. Их можно арендовать, но зато оборудование самостоятельно дозирует ингредиенты, выполняет замешивание бетона именно того качества, которое необходимо. Расходы на аренду будут оправданы.
Пропорции газобетона могут быть различными, но лучше всего придерживаться следующей формулы (для газобетона D-600):
- портландцемент ПЦ500 D0 – 65%;
- очищенный песок – 30%;
- доломит – 5%;
- В/Т – до 0,48.
Известковая мука, т. е. доломит, может содержать примерно до 10% газобетона, но важно определиться с тем, какой цвет блоков необходим. При большем количестве извести цвет газобетонных блоков будет более светлым. Большое количество пудры также не требуется, она выступает в качестве катализатора реакции газообразования.
Процесс изготовления газобетона
Схема дома из газобетонных блоков.
Чтобы сделать ячеистый бетон, необходимо выполнить несколько этапов, которые включают:
- дозировку ингредиентов, перемешивание сухой смеси;
- добавление воды, замешивание раствора;
- заполнение получившейся массой форм для заливки;
- выдержку смеси для набора прочности, высыхание газобетонных блоков и их извлечение из форм.
Необходимо тщательно отмерить все сухие ингредиенты, нужные для производства газобетонных блоков. Основными материалами являются цемент, известь, песок. Чтобы запустить процесс газообразования, необходимо использовать алюминиевую пудру. После реакции с водой она провоцирует выделение водорода, смесь начинает вспениваться. Пропорции очень важны, так как именно от них зависит прочность, пористость и другие характеристики будущего газобетона.
Схема производства газобетона.
На втором этапе осуществляется перемешивание компонентов. Масса должна получиться однородной. От качества замеса зависит и то, каким будет газобетон после приготовления. Для замешивания необходимо использовать только специальное оборудование. Подойдут бетономешалки, вручную этот процесс не производится.
Когда будущий бетон перемешан, необходимо начинать его заливку по формам.
Формы применяются специальные, лучше всего приобрести уже готовые, которые полностью соответствуют всем требованиям.
Заливка проводится только до половины форм, ни в коем случае нельзя заливать их полностью. Это объясняется тем, что в процессе газообразования смесь сильно увеличивается в объемах, полностью заполняя все формы. После того как увеличение объема закончено, при помощи металлического прута необходимо сверху все излишки смеси убрать, чтобы верхняя часть получилась ровной и гладкой. Производится это примерно через 6 часов после того, как заливка была выполнена.
Как происходит сушка газобетонных блоков?
Правильная и неправильная отделка домов из газобетона.
Далее будущие блоки выдерживаются в формах примерно 12 часов, при этом держать их надо на закрытой площадке. Затем их можно извлекать из контейнеров, далее их на пару суток оставляют на ровной поверхности для набора прочности. Для полного приобретения всех необходимых показателей газобетонный блок надо выдерживать 28 дней.
Во время заливки можно использовать контейнеры различных форм и размеров. Во время планирования надо учесть и то, что некоторое количество материала может уйти на подбор правильной пропорции, так как универсального рецепта нет. Еще некоторое количество может уйти на брак. В любом случае изготовление газобетонных блоков своими руками будет более дешевым, чем покупка уже готовых или использование других материалов для строительства, например, традиционного кирпича.
После того как весь материал готов, может начинаться его укладка. Для этого применяется специальный клеевой раствор, который обеспечивает не такую большую толщину шва, как при цементном растворе. В итоге теплопотери будут меньшие, а прочность выше. Начинается кадка от угла, обязательно надо для каждого ряда соблюдать перевязку, чтобы стена получилась прочной и надежность. Во время кладки необходимо использовать металлические пруты для армирования. Процесс этот несложный, следует заранее проделать в блоках пазы – в них и будут устанавливаться пруты. После этого сверху укладывается слой раствора, начинается кладка следующего ряда.
Газобетонные блоки представляют собой прочный и качественный строительный материал, который используется для различных целей. Сегодня он стал популярен для малоэтажного частного строительства. Некоторые умельцы предпочитают не покупать такие блоки в уже готовом виде, а делать их своими руками. Для этого необходимо в точности соблюдать разработанную технологию изготовления.
Технология производства пенобетона от А до Я
Ячеистый бетон (газобетон или пенобетон) не нуждается в рекламе — это наиболее известный строительный материал, как тёплый и шумопоглощающий. Равному этому материалу по своим свойствам в настоящее время нет.
Большинство домов за рубежом и в РФ строится с применением автоклавного ячеистого бетона.
Одним из самых перспективных направлений в насыщении рынка лёгким бетоном — является развитие безавтоклавного производства ячеистого бетона. Стоимость такого производства в 100 раз меньше автоклавных линий.
Пористость ячеистого бетона сравнительно легко регулировать в процессе изготовления, в результате получают бетоны разной плотности и назначения.
В силу простоты технологии и малой потребляемой энергоёмкости производства, наличие входных компонентов — делает такие технологии доступным для рядовых граждан, и поэтому могут являться массовым (народным) производством.
Неавтоклавный ячеистый бетон, в отличие от автоклавного, может производиться при обычных климатических условиях с применением обычного не измельченного песка.
По некоторым своим характеристикам превосходит автоклавный ячеистый бетон, является наиболее дешёвым и доступным производством для малого и среднего бизнеса.
Ячеистые бетоны делят на три группы:
- теплоизоляционные, плотностью в высушенном состоянии не более 500 кг/м3;
- конструкционно-теплоизоляционные, плотностью 500-900 кг/м3;
- конструкционные (для железобетона), плотностью 900-1200 кг/м3.
Существует несколько технологий производства пенобетона, которые по своей сути достаточно просты.
В цементно-песчаную смесь добавляется пенообразователь или готовая пена. После перемешивания компонентов получается бетон насыщенный пузырьками воздуха плотностью от 250 до 1400 кг/куб.м.
Получаемая смесь сразу готова для формирования из нее различных строительных изделий: стеновых блоков, перегородок, перемычек, плит перекрытия и т.д.
Такой пенобетон с успехом можно использовать для заливки в формы, пола, кровли, а также для монолитного строительства.
В отличие от ячеистого газобетона, при получении пенобетона используется менее энергоемкая безавтоклавная технология.
Кроме простоты производства, пенобетон обладает и множеством других положительных качеств.
Например, в процессе его приготовления легко удается придать этому материалу требуемую плотность путем изменения подачи количества пенообразователя. В результате возможно получение изделий плотностью от 250 кг/м3 до самых предельных значений легкого бетона 1400.
Пенобетон является экологически чистым материалом.
Характеристики пенобетона
Показатель | Ед.![]() изм. | Кирпич строительный | Строительные блоки | Пенобетон | ||
глин. | силик. | керамзит | газобетон | |||
Плотность | кг/м3 | 1550 — 1750 | 1700 — 1950 | 900 — 1200 | 300 — 1200 | 300 — 1200 |
Масса 1 м2 стены | кг | 1200 — 1800 | 1450 — 2000 | 500 — 900 | 90-900 | 90 — 900 |
Теплопроводность | Вт/мК | 0. | 0.85 — 1.15 | 0.75 — 0.95 | 0.07 — 0.38 | 0.07 — 0.38 |
Морозостойкость | цикл | 25 | 25 | 25 | 35 | 35 |
Водопоглощение | % по массе | 12 | 16 | 18 | 20 | 14 |
Предел прочности при сжатии | МПа | 2.5 — 25 | 5-30 | 3.5 — 7.5 | 0.5 — 25.0 | 0.25 — 12.5 |
Марка бетона по средней плотности в сухом состоянии | 400 | 500 | 600 | 700 | 800 | 900 | 1000 |
Пределы отклонения средней плотности бетона в сухом состоянии,. | 351 — 450 | 451 — 550 | 551 — 650 | 651 — 750 | 751 — 850 | 851 — 950 | 951 — 1050 |
Коэффициент теплопроводности бетона в сухом состоянии не более, Вт/(мК) | 0.1 | 0.12 | 0.14 | 0.18 | 0.21 | 0.24 | 0.29 |
Класс бетона по прочности на сжатие | В0.5 | В0.75 | В1 | В1.5 | В2 | В2.5 | В5 |
Средняя прочность на сжатие (при коэффициенте вариации Vп=17%) не менее, МПа | 0.7 | 1.1 | 1.4 | 2.2 | 2.9 | 3.6 | 7.2 |
Сравнительная таблица конструкций стен из пенобетона и керамического кирпича:
№ | Наименование | Материал | ||
Керамический кирпич | Пенобетон | |||
1 | Объемный вес, кг/м3 | 1800 | 500 | 400 |
2 | Размер,мм высота | 250 | 200 | 200 |
3 | Объем шт в м3 | 0,00195 | 0,048 | 0,048 |
4 | Коэффициент теплопроводности (сух) (L), Вт/м*0oС | 0,80 | 0,12 | 0,10 |
5 | Количество, шт в 1м3 | 513 | 21 | 21 |
6 | Количество, шт в м2 стены в 1 кирпич | 33 | 13 | 13 |
7 | Вес, шт/кг | 3,51 | 24 | 19,2 |
8 | Толщина стены, м для R=2. | 1,45 | 0,24 | 0,20 |
9 | Количество шт, для заданной R | 744 | 5 | 4 |
10 | Масса 1 м2 стены, кг (при заданной толщине) | 2610 | 120 | 80 |
11 | Трудозатраты на 1 м2 стены, чел/час | 7,19 | 1,20 | 1,00 |
В предлагаемой документации подробно рассмотрена технология производства пенобетона. Представлены чертежи, рисунки с описанием различного оборудования, от самого простого до более сложного, предназначенного для изготовления пеноблоков и производства пенобетона своими руками.
Если вы заинтересовались, свяжитесь со мной любым удобным для вас способом, обсудим способ получения документации.
Передовые технологии бетона: Газобетон и пенобетон
Запуская любое производство пенобетона и пенобетона, необходимо учитывать спрос на пенобетон и газобетон, стоимость оборудования и технологическую сложность плюс сырье. Это, по словам Елизаветы из Inntechgroup, современного российского предприятия, которое проектирует и производит оборудование для неавтоклавного газобетона.
Спрос на пенобетон и газобетонОба материала обладают высокой текучестью, малым собственным весом, минимальным расходом заполнителя, контролируемой низкой прочностью, отличными теплоизоляционными свойствами.Так что существенной разницы между газоблоками и пенобетонными блоками для заказчика нет.
Стоимость оборудования Рассмотрим подробнее оборудование, которое используется для производства пено- и газобетонных блоков.
Смеситель, предназначенный для производства пенобетона, технически сложнее. Процесс смешивания происходит под давлением с помощью пеногенераторов или в открытом смесителе с помощью насоса героторного типа. Жизненно важно поддерживать один и тот же уровень давления, но это приводит к чрезмерному износу наполнителей, сальникового уплотнения и т. д.Насос героторного типа более дорогой и технически сложный. Положительным моментом является медленная скорость процесса смешивания и меньшая нагрузка на подшипниковый узел, также вы можете заливать смесь в формы по шлангам на расстоянии. Смесители
, предназначенные для газобетона, имеют более простую конструкцию и более удобны в эксплуатации, так как перемешивают жидкую смесь. Все, что вам нужно, это просто снабдить миксер маленькими лопастями и высокой скоростью для правильного процесса смешивания. Нет напора и специальных сливных устройств – смесь сливается самотеком.Но есть недостаток – необходимо организовать перемещение форм или смесителя, так как нет возможности залить смесь в формы с расстояния
Основные требования к формам – точность размеров, качественные замки, предотвращающие протечки, и гладкая поверхность. Формы изготовлены из тонкостенного листового металла с каркасом из профильных труб. Эти формы легкие, простые в использовании, передвижные и их производство не требует больших вложений.
Кассетные формы пользуются популярностью у производителей пенобетона.Эти формы изготавливаются рабочими перед процессом заливки, что занимает много времени. К материалам, используемым для изготовления этих форм, предъявляются строгие требования, так как они напрямую влияют на геометрию блоков и скорость их изготовления. Поэтому формы изготавливают из толстостенного металла, что делает их тяжелее и дороже. Кроме того, сначала эти формы обеспечивают отличную геометрию блоков, но в дальнейшем деформации становятся неустранимыми.
Существуют различные виды дозирующих систем как для пенобетона, так и для пенобетона.У них схожие характеристики, поэтому существенной разницы нет.
При использовании кассетных форм для пенобетона вам не нужно будет резать массив. Но некоторые производители используют технологию резки как для пенобетона, так и для газобетона.
Пенобетону требуется больше времени для набора достаточной прочности перед расформовкой, это занимает от 8 до 20 часов в зависимости от использования нагревательных приборов. Что касается газобетона – его можно резать уже через 1,5 – 3 часа после заливки. Есть еще одно отличие в технологии резки: газобетон режут струнными пилами вручную или на автоматическом отрезном станке.Для резки пенобетона необходимо использовать циркулярные или ленточные пилы. Разумеется, устройство для резки струны стоит меньше, чем комплект пил, к тому же пилы имеют ускоренный износ.
Читайте также: Использование стеклопластиков для усиления бетона
Технологическая сложность и стоимость сырья Безусловно, основное отличие пенобетона от газобетона заключается в технологии производства. Пенобетон получают путем смешивания песка, цемента, воды и пенообразователя. Пена подается пеногенератором непосредственно в смеситель с заданной частотой и весом.В процессе смешивания частицы цемента и песка обволакивают пузырьки пены. Смесь заливают в собранную и смазанную форму. Масса набирает прочность на отрыв в течение 12-24 часов.
Основные технологические трудности. Поддержание того же качества пены требует вашего постоянного внимания. Нестабильная пена вызывает нестабильную плотность продукта. Но главная трудность заключается в медленном развитии силы. Производство пенобетона требует использования холодной воды, так как горячая вода разрушает пену.Но холодная вода не способствует набору прочности, к тому же сам пенообразователь замедляет схватывание цемента. Так что развитие отрывной прочности займет 24 часа, дальнейшее развитие прочности также происходит очень медленно. Эти факторы напрямую влияют на расход цемента.
Газобетон. Основными компонентами для производства газобетона также являются песок, цемент, вода. Эти компоненты смешиваются и в последний момент добавляется пенообразователь – алюминиевая пудра. Смесь заливается в форму и начинается реакция.Пузырьки воздуха образуются в результате химической реакции и взрывают газобетонную смесь. Через 20-30 минут реакция прекращается и массив начинает набирать отрывную прочность. Для производства используется горячая вода, ее температура составляет около 40-60 С. При реакции также выделяется тепло, так что температура массива составляет около 50-60 С, что обеспечивает быстрое развитие прочности. Через 2-3 часа массив следует разрезать на блоки.
Основные технологические трудности. Основная сложность заключается в разработке соответствующего технологического процесса и состава в зависимости от вашего сырья.Какого-то уникального состава для газобетона не существует. Факторами, влияющими на процесс, являются вода, ее количество, щелочность, количество алюминиевой пудры. Как правило, поставщики оборудования предоставляют полный комплекс услуг по обучению и технологическому регламенту для каждого клиента индивидуально.
Резюме.
Для ваших клиентов нет разницы, пеноблок это или газобетонный блок, они будут сравнивать качество и цену. Поскольку качество такое же, они выберут более дешевый.
Производителям следует иметь в виду, что оборудование для пенобетона технически сложнее, кассетные формы дороже и из-за медленной циркуляции вам потребуются большие количества. Оборудование для производства газобетона обойдется дешевле из-за меньшего расхода металла. К тому же оборудование для газобетона многофункционально — вы можете производить блоки любых размеров! Вам также потребуется меньшее количество цемента (20% экономии), так что себестоимость газобетонных блоков намного меньше, поэтому продукт более конкурентоспособен! А конкурентоспособность продукта – это полдела для любого производителя стройматериалов.
IRJET-Запрошенная вами страница не найдена на нашем сайте Выпуск 1, январь 2022 г. Публикация находится в процессе…
Просмотр статей
IRJET Получен «Импакт-фактор научного журнала: 7,529» за 2020 год. регистрация в системе менеджмента качества.
IRJET приглашает статьи из различных технических и научных дисциплин для тома 9, выпуск 2 (февраль 2022 г. ) Документы
IRJET Получил «Импакт-фактор научного журнала: 7,529» за 2020 год.
Подтвердить здесь
IRJET Получил сертификат о регистрации ISO 9001:2008 для своей системы управления качеством.
IRJET приглашает статьи из различных технических и научных дисциплин для тома 9, выпуск 2 (февраль 2022 г.) Документы
IRJET Получил «Импакт-фактор научного журнала: 7,529» за 2020 год.
Подтвердить здесь
IRJET Получил сертификат о регистрации ISO 9001:2008 для своей системы управления качеством.
IRJET приглашает статьи из различных технических и научных дисциплин для тома 9, выпуск 2 (февраль 2022 г.) Документы
IRJET Получил «Импакт-фактор научного журнала: 7,529» за 2020 год.
Подтвердить здесь
IRJET Получил сертификат о регистрации ISO 9001:2008 для своей системы управления качеством.
IRJET приглашает статьи из различных технических и научных дисциплин для тома 9, выпуск 2 (февраль 2022 г. ) Документы
IRJET Получил «Импакт-фактор научного журнала: 7,529» за 2020 год.
Подтвердить здесь
IRJET Получил сертификат о регистрации ISO 9001:2008 для своей системы управления качеством.
IRJET приглашает статьи из различных технических и научных дисциплин для тома 9, выпуск 2 (февраль 2022 г.) Документы
IRJET Получил «Импакт-фактор научного журнала: 7,529» за 2020 год.
Подтвердить здесь
IRJET Получил сертификат о регистрации ISO 9001:2008 для своей системы управления качеством.
IRJET приглашает статьи из различных технических и научных дисциплин для тома 9, выпуск 2 (февраль 2022 г.) Документы
IRJET Получил «Импакт-фактор научного журнала: 7,529» за 2020 год.
Подтвердить здесь
IRJET Получил сертификат о регистрации ISO 9001:2008 для своей системы управления качеством.
IRJET приглашает статьи из различных технических и научных дисциплин для тома 9, выпуск 2 (февраль 2022 г. ) Документы
IRJET Получил «Импакт-фактор научного журнала: 7,529» за 2020 год.
Подтвердить здесь
IRJET Получил сертификат о регистрации ISO 9001:2008 для своей системы управления качеством.
(PDF) ПРОЦЕСС ПРОИЗВОДСТВА БЛОКА
8 | С т р а й
Цемент – для изготовления газобетонных блоков
требуется обычный портландцемент марки 53 (OPC) от производителя. Цемент, поставляемый заводами, не рекомендуется из-за различий в качестве
разных партий цемента.
Летучая зола или песок – Летучая зола смешивается с водой с образованием золы-уноса. Полученный таким образом шлам смешивают с
другими ингредиентами, такими как известковая мука, цемент, гипс и алюминиевая пудра в пропорциональном количестве, чтобы сформировать
блоков.
Порошок известняка. Порошок извести, необходимый для производства газобетона, получают путем дробления известняка до мелкого порошка
на заводе газобетона или путем его прямой закупки в виде порошка на различных заводах.
Гипс — Гипс легко доступен на рынке.
Этап 2 – Дозирование и смешивание-
После подготовки сырья следующим этапом процесса производства газобетонных блоков является дозирование и смешивание. Процесс
дозирования и смешивания означает качество конечных продуктов.Поддерживающее соотношение всех ингредиентов: —
ЗОЛА ИЛИ ПЕСОК: ИЗВЕСТЬ:ЦЕМЕНТ: ГИПС = 69:20:8:3
Алюминий составляет около 0,08% от общего количества сухих материалов в смеси
Водоотношение = 0,60 -0,65
Цикл перемешивания и заливки 5,5 мин. Блок дозирования и смешивания используется для формирования правильной смеси для
производства газобетонных блоков. Летучая зола перекачивается в контейнер. После заливки нужного веса насос
останавливается. Аналогичным образом известковая мука, цемент и гипс засыпаются в отдельные емкости с помощью конвейеров.
После того, как необходимое количество каждого ингредиента будет помещено в отдельные контейнеры, система управления подает все
ингредиентов в смесительный барабан. Чаша меньшего размера, используемая для подачи алюминиевого порошка, также
присоединена к смесительному блоку. После взбивания смеси в течение заданного времени ее можно разливать в формы
с помощью дозатора. Дозатор выдает эту смесь в заданном количестве в формы. Процесс дозирования и смешивания
выполняется непрерывно, потому что если между загрузкой и выгрузкой ингредиентов есть промежуток,
остаточная смесь может начать затвердевать и засорить всю установку.При производстве газобетонных блоков вся операция дозирования и смешивания
полностью автоматизирована и требует минимального вмешательства человека.
Этап 3 – Литье, подъем и отверждение-
После того, как смесь сырья готова, ее разливают по формам. Формы могут быть различных размеров в зависимости от установленной мощности
, например, размером 4,2 м x 1,2 м x 0,65 м. Перед отливкой формы покрывают тонким слоем масла
, чтобы сырой кек не прилипал к формам.Пока суспензия смешивается и выливается в смазанные формы, алюминий
вступает в реакцию с гидроксидом кальция и водой и выделяет газообразный водород. Это приводит к образованию крошечных
клеток, что приводит к расширению смеси навозной жижи. Такое расширение может быть в три раза больше первоначального объема. Размер пузырьков составляет около 2-
5 мм. Таким образом, это является причиной легкого веса и изоляционных свойств газобетонных блоков. Когда процесс подъема
завершен, зеленому пирогу дают отстояться и затвердеть.
Газобетон, произведенный с использованием местного сырья | Маталка
Нараянан, Н.и К. Рамамурти. «Структура и свойства газобетона: обзор». Цементно-бетонные композиты 22, вып. 5 (2000): 321-329.
Нараянан Н. и К. Рамамурти. «Микроструктурные исследования газобетона». Исследования цемента и бетона 30, вып. 3 (2000): 457-464.
Мицуда, Такеши, Каори Сасаки и Хидэки Исида. «Фазовая эволюция в процессе автоклавирования газобетона». Журнал Американского керамического общества 75, вып. 7 (1992): 1858-1863.
Гоуаль М.С., А. Бали и М. Кенеудек. «Эффективная теплопроводность глинистого газобетона в сухом состоянии: экспериментальные результаты и моделирование». Журнал физики D: Прикладная физика 32, вып. 23 (1999): 3041.
Маталка, Фарис, Парвиз Сорушян, Сакиб Уль Абидин и Амирпаша Пейванди. «Использование золы сжигания недревесной биомассы при разработке щелочеактивированного бетона». Строительство и строительные материалы 121 (2016): 491-500.
Маталка, Фарис, Парвиз Сорушян, Ранкотге Ранджит Вирасири и Амирпаша Пейванди.«Разработка местных вяжущих в качестве строительных материалов». Труды Института инженеров-строителей-Строительные материалы (2017): 1-10.
Маталка, Фарис, Парвиз Сорушян, Анаги Балчандра и Амирпаша Пейванди. «Характеристика активированного щелочью геополимерного бетона на основе золы из недревесной биомассы». Журнал материалов в гражданском строительстве (2016): 04016270.
Маталка, Фарис, Ливэй Сюй, Венда Ву и Парвиз Сорушян. «Механохимический синтез однокомпонентного щелочноалюмосиликатного гидравлического цемента.Материалы и конструкции 50, №1 (2017): 97.
Даксон, Питер и Джон Л. Провис. «Разработка прекурсоров для геополимерных цементов». Журнал Американского керамического общества 91, вып. 12 (2008): 3864-3869.
Рамамурти, К., Э.К. Кунханандан Намбиар и Г. Инду Шива Ранджани. «Классификация исследований свойств пенобетона». Цементно-бетонные композиты 31, вып. 6 (2009): 388-396.
Abdullah, M.M.A.B., et al., Легкий геополимерный бетон на основе летучей золы с использованием пенообразователя.Международный журнал молекулярных наук, 2012. 13(6): с. 7186-7198.
Сингх, М. и М. Гарг, Исследование прочного гипсового вяжущего для строительных материалов. Строительство и строительные материалы, 1992. 6(1): с. 52-56.
Маталка, Ф. и др., Разработка и характеристика вяжущего на основе гипса. Европейский журнал достижений в области техники и технологий, 2017. 4(3): с. 153-157.
Камарини, Г. и Дж.А. De Milito, смеси полугидрата гипса и цемента для повышения долговечности штукатурки.Строительство и строительные материалы, 2011. 25(11): с. 4121-4125.
Элсен, Дж., Микроскопия исторических растворов — обзор. Исследования цемента и бетона, 2006. 36(8): с. 1416-1424 гг.
Маталка, Ф. и др., Разработка сэндвич-композитов для строительства зданий с использованием местных материалов. Строительство и строительные материалы, 2017. 147(С): с. 380-387.
Хамад, Али Дж. «Материалы, производство, свойства и применение легкого ячеистого бетона: обзор.» Международный журнал материаловедения и инженерии 2, № 2 (2014): 152-157.
Обзор использования отходов для производства автоклавного ячеистого бетона†
Обзор использования отходов производства автоклавного ячеистого бетона †
- Р. А. Рахман 1 , А. Фазлизан 1,* , Н. Асим 1 , А. Тонгта 2
2 Кафедра физики, Факультет естественных наук, Университет Наресуан, Пхитсанулок, 65000, Таиланд
* Автор, ответственный за переписку: А.
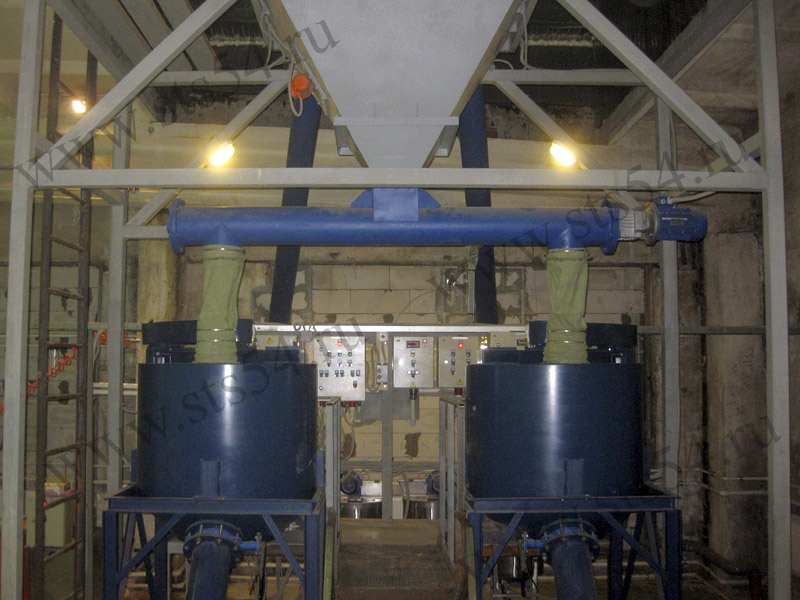
(Эта статья относится к этому специальному выпуску: Возобновляемые материалы для устойчивого развития)
Поступила в редакцию 01 августа 2020 г .; Принято 13 октября 2020 г .; Выпуск опубликован 30 ноября 2020 г.
Аннотация
Автоклавный газобетон (АГБ) стал более привлекательным благодаря
его отличные и экологически чистые свойства в строительстве.ААС
относительно легкий, обладает более низкой теплопроводностью, более высокой термостойкостью, меньшей усадкой и прочной конструкцией, чем обычный бетон. ААС — это
сочетание кварцевого песка, цемента, гипса, извести, воды и расширительного агента.
Чтобы улучшить его физико-механические свойства и снизить себестоимость производства,
были сделаны огромные инновации, в которых отходы использовались в качестве частичной замены материалов AAC. Эта статья предназначена для представления литературы
по утилизации отходов как средства частичной замены газобетона
материалы для улучшения его физико-механических свойств и тепловых характеристик.Физические свойства, такие как микроструктура и механические свойства
такие как плотность, прочность на сжатие, водопоглощение представлены для классификации
исследование, которое было сделано в таких новшествах. Кроме того, было представлено обсуждение инноваций для улучшения его тепловых характеристик.
Согласно обзору, увеличение применения газобетона приводит к образованию большого количества отходов на строительных площадках и переработке порошка бетонных отходов в стеновой бетон; в частности, газобетон не часто применялся в строительстве.
Ключевые слова
Автоклавный газобетон; микроструктура; отходы; прочность на сжатие
Процитировать эту статью
Рахман, Р. А., Фазлизан, А., Асим, Н., Тонгта, А. (2021). Обзор использования отходов производства автоклавного ячеистого бетона † . Журнал возобновляемых материалов, 9(1) , 61–72.
как энергоэффективный и экономичный строительный материал повышает спрос на газобетон: TMR
ОЛБАНИ, Нью-Йорк, 26 июня 2018 г. /PRNewswire/ —
Согласно новому рыночному отчету, опубликованному Transparency Market Research под названием « Рынок автоклавного газобетона – глобальный отраслевой анализ, размер, доля, рост, тенденции и прогноз, 2018–2026 годы», глобальный рынок автоклавного газобетона (AAC) была оценена примерно в 11 млрд долларов США в 2017 году и, по прогнозам, достигнет почти 20 млрд долларов США к 2026 году, увеличившись в среднем на более чем 7% в год в период с 2017 по 2026 год.
(логотип: https://mma.prnewswire.com/media/664869/Transparency_Market_Research_Logo.jpg )
Автоклавный ячеистый бетон (AAC), также известный как автоклавный ячеистый бетон (ACC) или автоклавный легкий бетон (ALC), представляет собой легкий сборный строительный материал, применение которого в последнее время растет.
Запрос Образец Автоклавный газобетон (АГБ) Рынок: https://www.transparencymarketresearch.com/sample/sample.php?flag=S&rep_id=12650
Хотя этот продукт используется с 1923 года, в последнее время он приобрел огромную популярность благодаря своей способности обеспечивать жесткую структуру, изоляцию, огнестойкость и экономичность конструкции. AAC имеет пористую структуру. Он содержит карманы захваченного воздуха, что делает его легче, чем другие строительные материалы. Благодаря высокой теплоизоляции и простоте монтажа материал можно использовать как для внутренней, так и для внешней отделки.AAC используется в качестве экологически чистого зеленого строительного материала в жилом, коммерческом и других типах строительства. Он производится с использованием летучей золы, которая является неизбежным отходом тепловых электростанций и доступна в изобилии. Также газобетон является энергоэффективным строительным материалом, что снижает общую стоимость строительства. Энергозатраты на производство газобетона меньше, чем на другие строительные материалы. Газобетон потребляет примерно на 50% меньше энергии, чем бетон. Крошечные воздушные карманы и тепловая масса газобетона обеспечивают теплоизоляцию, что снижает затраты на строительство, связанные с отоплением и кондиционированием воздуха.Газобетон снижает потребность в отоплении и охлаждении до 30 % благодаря своим теплоизоляционным свойствам, что обеспечивает постоянную финансовую выгоду в течение всего срока службы конструкции.
Посмотреть подробное содержание этого отчета по телефону https://www.transparencymarketresearch.com/report-toc/12650
Увеличение расходов на строительство за счет расширения строительного сектора:
Спрос на традиционные строительные материалы в первую очередь обусловлен расширением строительного сектора во всем мире.Общий рост строительной и инфраструктурной деятельности во всем мире привел к росту спроса на жилое, коммерческое и промышленное строительство, что привело к последовательному расширению производства строительных материалов. Кроме того, ожидается, что макроэкономические факторы, такие как рост ВВП в Европе, постепенное восстановление расходов на строительство в жилых и нежилых секторах, а также ожидаемый рост в секторе недвижимости, поддерживаемый государственными инициативами по обеспечению доступного жилья, будут стимулировать рынок AAC.Строительство стены из газобетонных блоков приводит к экономии средств по сравнению с традиционным кирпичом. Из-за низкой плотности газобетона нагрузка на конструкцию (собственная нагрузка) очень мала, и элементы конструкции могут быть спроектированы соответствующим образом. В свою очередь потребность в бетоне и стали меньше для фундамента и всех конструктивных элементов здания. Количество стыков меньше из-за большего размера блоков AAC. Это снижает потребность в цементном растворе. Трудозатраты, необходимые для укладки газобетонных блоков, также значительно меньше, что приводит к значительной экономии времени.
Запрос на Несколько глав по автоклавному газобетону (AAC)
Высокие инвестиционные затраты, связанные с производством газобетона:
Газобетон уже более 70 лет демонстрирует свои преимущества благодаря таким свойствам, как высокая тепло- и огнезащитная способность. Конструкционные элементы из газобетона с армированием можно комбинировать в комплексном производстве с неармированным блочным материалом и т.д.Комплексное производство армированных изделий и блочных материалов требует наличия квалифицированного завода с передовой технологией армирования. Изделия из газобетона производятся на заводах по производству блоков или на заводах с интегрированной технологией армирования, которая позволяет изготавливать изделия из газобетона, такие как элементы настила и крыши, стеновые панели и перемычки отдельно от блоков. С точки зрения объема, производство усовершенствованных армированных компонентов, таких как панели и перемычки, остается низким по сравнению с производством блоков.Инвестиции, необходимые для строительства комплексного производства панелей и перемычек вместе с блоками, более чем в два раза превышают инвестиции в простой блок.
Завод, предназначенный для производства армированных изделий, также может производить блоки, но с небольшими изменениями. Однако заводы, предназначенные специально для производства блоков, имеют меньшие капитальные затраты, чем заводы, предназначенные для производства армированных изделий. Кроме того, время обработки панелей и перемычек для подъема давления и отверждения в автоклавах почти в два раза больше, чем для блоков.
Получите брошюру в формате PDF, чтобы узнать больше о специалистах и технических специалистах отрасли: https://www.transparencymarketresearch.com/sample/sample.php?flag=B&rep_id=12650
Доступное жилье в развивающихся странах:
Спрос на доступное жилье, вероятно, останется устойчивым, что обусловлено ростом населения, молодым демографическим составом, переходом к нуклеарным семьям и быстрой урбанизацией. Например, ожидается, что к 2022 году рыночный потенциал проектов доступного жилья в Индии достигнет 930 миллиардов долларов США.План индийского правительства, Pradhan Mantri Awas Yojana, направлен на строительство двух крор (20 миллионов) домов в Индии в три этапа до 2022 года. Ожидается, что нехватка жилья увеличится с нынешнего уровня в 19 миллионов единиц до 25 миллионов к 2021 году. основанный на стабильном десятилетнем темпе роста.
Спрос на газобетон в основном обусловлен растущим использованием газобетонных блоков в качестве предпочтительного строительного материала
Рынок автоклавного ячеистого бетона (AAC) был сегментирован в зависимости от продукта и конечного использования.В зависимости от продукта рынок газобетона делится на блоки, стеновые панели, панели для пола, панели для крыши, панели для облицовки и другие. С точки зрения конечного использования рынок подразделяется на жилой, коммерческий и другие. Блоки были доминирующим продуктовым сегментом на рынке газобетона в 2017 году. С точки зрения выручки, на долю сегмента блоков приходилось более 48% мирового рынка газобетона в 2017 году. Сегмент панелей также, вероятно, будет расширяться значительными темпами в течение прогнозируемый период, так как панели сочетают в себе прочность, тепло- и звукоизоляцию. Стеновые панели из газобетона — идеальное решение для крупномасштабного, промышленного и коммерческого строительства
Жилищный сектор из-за быстрой урбанизации, особенно в странах с развивающейся экономикой, является доминирующим сегментом конечного пользователя
С точки зрения конечного использования, сегмент жилищного строительства доминировал на мировом рынке газобетона в 2017 году. По оценкам, рост урбанизации, увеличение покупательной способности, рост населения и потребность в доступном жилье будут стимулировать рынок газобетона в развивающихся странах в течение прогнозируемого периода. .Однако недостаточная осведомленность о газобетонном бетоне среди специалистов в области строительства, строителей, девелоперов и архитекторов, вероятно, будет ограничивать глобальный рынок газобетонных блоков.
Запросите скидку на премиальный исследовательский отчет (5795 долларов США) с полным оглавлением: https://www.transparencymarketresearch.com/sample/sample. php?flag=D&rep_id=12650
Европа является крупнейшим потребителем и производителем газобетона
Спрос на газобетон высок в Европе, за ней следуют Азиатско-Тихоокеанский регион, Ближний Восток и Африка.Изделия из газобетона используются в Европе уже более 70 лет. Европа доминировала на мировом рынке газобетона с точки зрения выручки, на долю которой в 2017 году приходилось более 34% мирового рынка. Это связано с наличием местных производственных мощностей газобетона по всей Европе, в таких странах, как Польша, Россия, Германия и Великобритания доминирует на рынке в регионе. Ожидается, что рынок AAC в Азиатско-Тихоокеанском регионе значительно расширится в течение прогнозируемого периода. Это связано с ростом населения и быстрой урбанизацией, особенно в развивающихся странах, таких как Китай и Индия.Ожидается, что увеличение количества объектов инфраструктуры и коммерческого развития подстегнет спрос на газобетон на Ближнем Востоке и в Африке. Ожидается, что рынок газобетона в Северной Америке будет расти устойчивыми темпами в течение прогнозируемого периода из-за преобладания деревянного строительства в регионе и ограниченного количества производственных мощностей по производству газобетона. Кроме того, правительственные инициативы по содействию экологичному строительству зданий и созданию советов штатов в различных регионах Всемирным советом по экологическому строительству (WGBC), вероятно, будут способствовать развитию рынка газобетонных блоков в Северной Америке и Латинской Америке
Расширение производственных возможностей ключевыми игроками
Ключевые игроки, представленные в отчете о рынке газобетона, включают Xella Group, H+H International, SOLBET, ACICO, AERCON AAC, UltraTech Cement Ltd., Biltech Building Elements Limited, AKG Gazbeton, Bulidmate, Eastland Building Materials Co., Ltd., Brickwell и UAL Industries Ltd. Основные игроки, работающие на рынке, вкладывают значительные средства в расширение производственных мощностей, чтобы удовлетворить растущий спрос . Например, CSR Hebel, ведущий австралийский производитель высококачественного автоклавного ячеистого бетона (AAC), расширила свои производственные мощности, построив вторую производственную линию в Сомерсби, Австралия, в сентябре 2017 года. Этот высокоавтоматизированный завод специально разработан только для производства панелей и, как ожидается, будет иметь мощность 300 000 кубометров в год. Завод оснащен новейшей доступной технологией Aircrete, что делает его одним из самых передовых и высокоавтоматизированных заводов по производству газобетонных блоков в мире.
В отчете мировой рынок автоклавного ячеистого бетона (AAC) сегментирован следующим образом:
Рынок автоклавного газобетона (AAC): анализ продукции
- Блок
- Стеновая панель
- Панель пола
- Панель крыши
- Облицовочная панель
- Другие
Рынок автоклавного газобетона (AAC): анализ конечного использования
- Жилой
- Коммерческий
- Другие
Просмотрите популярные отчеты об исследованиях TMR:
О нас
Transparency Market Research (TMR) — международная компания по изучению рынка, предоставляющая отчеты и услуги в области бизнес-информации. Эксклюзивное сочетание количественного прогнозирования и анализа тенденций, разработанное компанией, позволяет тысячам лиц, принимающих решения, получать прогнозные данные. Опытная команда аналитиков, исследователей и консультантов TMR использует собственные источники данных и различные инструменты и методы для сбора и анализа информации.
TMR постоянно обновляется и пересматривается группой экспертов-исследователей, чтобы всегда отражать последние тенденции и информацию. Обладая обширными возможностями исследования и анализа, Transparency Market Research использует строгие первичные и вторичные методы исследования для разработки отличительных наборов данных и исследовательского материала для бизнес-отчетов.
Контакты
Transparency Market Research
State Tower,
90 State Street,
Suite 700,
Albany NY — 12207
United States
Tel: +1-518-618-1030
USA — Canada6 Бесплатный звонок: 8 -3453
Электронная почта: [электронная почта защищена]
Веб-сайт : http://www. transparencymarketresearch.com
Исследовательский блог : https://cmfenews.com/
ИСТОЧНИК Transparency Market Research
AAC: Автоклавный газобетон | Инженеры-консультанты PSE
Адель является менеджером проектов в PSE, который пришел в отрасль в 1997 году и имеет опыт в разнообразных аспектах структурного инженерного анализа, проектирования и управления.В дополнение к сильной технической базе и естественному структурному любопытству, он имеет большой опыт работы на местах, что дает ему уникальное понимание всего цикла проекта и потребностей. Он начал посещать аспирантуру Университета Северной Флориды в январе 2011 года. Он также посещал аспирантуру Университета Алабамы в Бирмингеме в августе 2012 года. В декабре 2014 года он получил докторскую степень в области проектирования конструкций.
Присоединившись к PSE в 2015 году, г-н Эльфайюми работал над разнообразными проектами, включая коммерческие, жилые, мосты, вантовые конструкции, мембранные конструкции и бамбуковые дома. Его многолетний профессиональный опыт привил ему страсть и способность решать уникальные задачи и сотрудничать с коллегами и клиентами.
В дополнение к сильной технической базе и природной любознательности в области строительства, он обладает большим опытом работы в полевых условиях, что дает ему уникальное понимание всего цикла проекта и потребностей. Адель увлечен структурным проектированием и созданием инновационных решений, которые работают для всех: структурно, архитектурно, конструктивно, экономически и, в конечном счете, для владельца и конечного пользователя.
Его академическое образование и опыт проектирования конструкций подготовили его к тому, чтобы стать эффективным ключевым лицом в PSE.
Проекты:
- Steele Residence, Санта-Роза, Калифорния (июль – сентябрь 2018 г.).
Одноэтажная резиденция площадью 11 246 кв. футов. Он включает в себя строительство стен из изолированных бетонных форм (ICF). Крыша представляет собой легкую бетонную балку перекрытия на расстоянии 24 дюйма друг от друга. Внутренние перегородки — легкие каркасные стены. Патио было покрыто настилом из легкого металла, поддерживаемым секциями из быстрорежущей стали из красного железа.
- Резиденция Адмани, Корнелиус, Северная Каролина (август – октябрь 2019 г.)
Этот проект представляет собой 3-этажное жилое здание площадью 30 685 кв. футов.
Проект в основном состоит из фермы перекрытия LGS с шагом 16 дюймов и балок крыши LGS с расстоянием между ними 24 дюйма. Колонны различаются между колоннами коробчатой формы LGS и секциями из красного железа (горячекатаного проката).
- Garrard Bradley, Meridale, NY (март – апрель 2018 г.)
Одноэтажный жилой дом площадью 1620 кв. футов.
Одноэтажное здание с наружными и внутренними стенами из деревянных каркасов и крышей из сборных деревянных ферм (другие производители).
4- Johnson Controls, City of Charleston, SC (апрель – июнь 2018 г.)
Это павильон для бассейна площадью 17 239 кв. футов. Бассейн (86’x187’) и вход (24’x55’). Проект в основном состоит в том, чтобы покрыть общественный бассейн алюминиевой рамной фермой 86’@6’ и еще одним набором алюминиевой рамы 55’@6’ OC для входа.
5–120-футовый стальной купол, временное мероприятие, Лас-Вегас, штат Невада (2019 г.)
Я разработал FEM с использованием RISA3D для моделирования стальных распорок купола, 2 вестибюлей с одним входом в туннель.
Опыт включает, но не ограничивается следующим:
- Бассейн
- Schmits, бассейн Leslie площадью 1500 кв. ярдов (бесконечный бассейн) – Kailua Kona, HI (2019),
- Legacy Pool (обычный бассейн), Grants Pass, OR, 1200 кв. ярдов
- Стальные конструкции
- Eide Industries, Натяжные конструкции — тканевые конструкции, навесы и вантовые конструкции, по всей стране, площадью от 25 до 2200 кв. ярдов. (2016-2018)
- Американский садовый перлит — 432 кв.ft система поддержки проема крыши – Klamath Falls, OR (2017)
- Более 10 деревянных геодезических куполов площадью более 1300 кв.