Производство вата – Производство ваты и технология изготовления (как делают)
Производство ваты и технология изготовления (как делают)
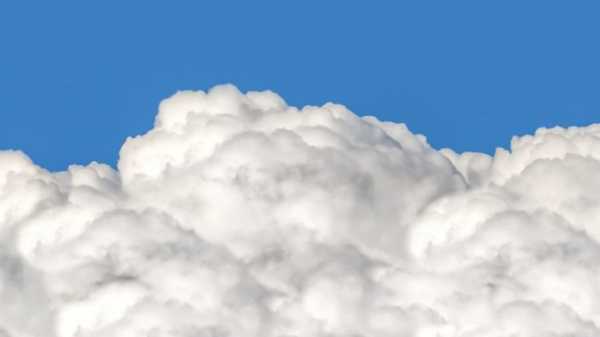
Вата (от нем. Watte) — пушистая масса волокон, слабо переплетённых между собой в различных направлениях.
По способу получения различают ваты: естественную — шерстяную, шёлковую, пуховую, хлопковую, льняную, пеньковую, сосновую, асбестовую, и искусственную — целлюлозную, стеклянную, металлическую, шлаковую, базальтовую.
По назначению вата разделяется на одёжную, мебельную, техническую (термоизоляционная, огнестойкая и др.), прокладочную, листовую клеёную и медицинскую.
Технология производства ваты + видео как делают
Производство ваты осуществляют из сырья, которое получают после обработки мохнатого хлопчатника. После того как плод начинает созревать, коробка растения начинает раскрываться. С внутренней стороны коробки имеется мягкое волокно белого цвета совместно с семенами. Затем такое волокно собирают на специальных пунктах, упаковывают и отправляют на хлопкоочистительный завод. На заводе волокна отделяют от семян и разделяют по длине. Длинные волокна должны составлять по длине не меньше двух с половиной сантиметров. Такие волокна используют для изготовления тканей, а короткие волоски называют линтами, и их используют для изготовления ваты.
Сегодня, производство ваты осуществляют не только из хлопка, но еще изо льна или шерсти. Льняная вата по своим потребительским качествам, к вате, сделанной из хлопка, считаются больше распространенными. Помимо этого можно купить вату, сделанную из смеси вискозы и хлопка. Вискозное волокно считается одним из первых искусственных волокон, так как выделяется высоким уровнем гигроскопичности, но потребители и производители больше всего отдают предпочтение натуральному материалу, и считаются менее аллергенными материалами.
Производство ваты из шерстяного и хлопкового сырья осуществляется по следующей технологической схеме. Для такого производства отбирают хлопок не больше четвертого сорта. Сегодня больше всего отдают предпочтение упругому и низкомерному хлопку, который по своей фактуре напоминает шерсть. А если рассматривать шерстяную вату, то ее делают из чистой натуральной шерсти, а также используют искусственное добавление хлопка.
Вату, которую используют для изготовления одежды, или гигроскопическая медицинская вата отличаются между собой не только по сырью, но еще и по производственной технологии. Для обычного производства ваты стали отбирать засоренные угары, а именно, угары, образующие при переработке текстильные волокнистые материалы. Чаще всего для этого используют короткие волокна.
Производство ваты начинается с того, что сырье очищают от мусора на специальном пыльном волчке. Что касается жестких волокон, то они заранее расщепляются на специальных многобарабанных щипках. Получившаяся волокнистая масса, сделанная из такого сырья, начнет очищаться, и смешиваться, а также формироваться в холсты с помощью специального оборудования. В основании холста имеется волокнистая масса без формы, и с помощью чесальной валичной машины превращается в съем ваты с определенной структурой и толщиной.
После этого, готовая вата проходит осмотр на брак, затем ее прессуют и упаковывают в специальные кипы, вес которых составляет от сорока до пятидесяти килограмм. Только в таком виде вату отправляют на мебельные и швейные производства. Производство ваты имеет свои отличия, в таком случае сырье предварительно разрыхляют и очищают на очистительном и рыхлительном агрегате. После этого его отваривают в щелочи под особым давлением и при температуре не выше 130 градусов, а затем обрабатывают специальным гипосульфитом натрия. При таком обрабатывающем процессе меняется структура физического волокна и природный желтый цвет. Затем удаляют пектиновые и азотистые вещества. В результате волокно получается с белым оттенком и имеет свои характерные свойства. В завершении медицинскую вату стерилизуют при температуре 125 градусов и при давлении трех атм.
Видео как делают:
Некоторую часть ваты упаковывают и отправляют на склады, а остальную часть используют для изготовления гигиенических изделий. К таким изделиям относят ватные палочки, которые используют для очистки труднодоступных мест, для снятия и поправления макияжа и для нанесения мазей. Для косметических целей используют специальные ватные палочки, один конец которых немного заострен. С помощью такого кончика стало намного удобнее снимать остатки лака для ногтей или же стало удобно проводить контур для губ или глаз. Что касается второго кончика палочки, то он имеет плоскую и округлую форму. Такой кончик лучше всего использовать в качестве аппликатора, который необходим для нанесения теней. Помимо этого, стали делать еще и ватные палочки для не косметического назначения, а именно, для чистки техники. Также из ваты стали делать ватные диски, и другие изделия для снятия макияжа, и снятия лака с ногтей. А также с такими дисками предоставляется возможность наносить компрессоры и крема.
Что касается таких ватных дисков, то они имеют высокий уровень плотности, по сравнению с обычной ватой и выпускаются только в чистом виде. Поверхность такого диска имеет вид рельефа. За счет этого предоставляется возможность равномерно наносить средства на кожу или мазь. Помимо этого, ватный диск по сравнению с ватой в момент смачивания не меняет свой формы. Сегодня вы можете купить прямоугольные, круглые диски, а также ватные шарики разных цветов. Причем такие диски используют не только для прямого назначения, но еще и для изготовления разных подделок.
moybiznes.org
Технология производства минеральной ваты, производители в России
Каменная вата — это разновидность утеплителя, изготовленного на основе габбро-базальтовых горных пород, который позволяет выполнять тепло- и звукоизоляцию различных сооружений или же осуществлять противопожарную защиту.
Благодаря своим физико-химическим свойствам данный тип утеплителя служит в качестве основной энергосберегающей технологии при отделке фасадов, кровли, полов и инженерных сетей как промышленных, так и полупромышленных и бытовых объектов.
Технология производства каменной минеральной ваты
Производство минеральной (базальтовой) ваты заключается в плавке горных пород при температуре 1500 С. После чего, жидкая лавоподобная масса с помощью центрифуги, специальных фильтров на основе платины или других тяжело плавких металлов и сильных воздушных потоков вытягивается в каменные волокна.
Далее в полученные волокна добавляются различные водоотталкивающие добавки и пластификаторы, после чего, при температуре порядка 200 С происходит процесс полимеризации в результате чего оборудование для производства минеральной ваты выпускает готовые базальтовые плиты, которые разрезаются в соответствии с необходимыми размерами.
Химический состав каменной ваты
Поскольку производство теплоизоляционных материалов данного класса осуществляется исключительно из горных пород, полученные базальтовые волокна имеют следующий химический состав:
- Диоксид кремния SiO2 в количестве от 45 до 55%.
- Диоксид титана TiO2 с массовой долей от 1.36 до 2%.
- Оксид кальция CaO в количестве от 7 до 11%.
- Окислы железа FeO и Fe2O3 с массовой долей от 5,38 до 13,5%.
- Оксид мангана MnO в диапазоне от 0,25 до 0,5%.
- Оксид алюминия Al2O3 с процентной долей от 14 до 20%.
- Оксид марганца MgO в количестве от 3 до 8%.
- Оксида натрия и калия (Na2O, K2O) в количестве от 2,7 до 7,5%.
- Прочие вещества составляют не более 5%.
Все вышеуказанные оксиды связываются между собой при помощи битумных, синтетических или композиционных связующих, или же при помощи бентонитовой глины.
Основной показатель качества полученного базальтового волокна — это модуль кислотности, который зависит от соотношения между кислотными и основными (лужными) окислами. Его значение регламентируется согласно требованиям ГОСТ 4640-93 «ВАТА МИНЕРАЛЬНАЯ. Технические условия».
Согласно вышеуказанному документу, каменная вата подразделяется на 3 категории:
- Категория «А» с показателем модуля кислотности от 1,6 и выше.
- Категория «Б» с показателем модуля кислотности в диапазоне от 1,4 до 1,6.
- Категория «С» с показателем модуля кислотности ниже 1,4.
Как видно из вышеуказанной категорийности, чем выше показатель модуля кислотности, тем высшего качества получается базальтовая вата, поскольку она является более долговечной и влагостойкой.
Очень часто для регулирования вышеуказанного показателя производители применяют различные добавки на основе карбонатных соединений.
Виды и сфера применения базальтовых волокон
Оборудование для производства минеральной ваты позволяет изготавливать следующие виды каменного (базальтового) волокна:
- Микротонкие волокна для изготовления фильтров тонкой очистки воздушной или жидкостной среды с диаметров волокон менее чем 0.6 мкм.
- Ультратонкие каменные волокна применяются в фильтрах тонкой очистки воздушной, газовой или жидкостной среды, или же при изготовлении сверхлёгких звуко- и теплоизоляционных материалов с диаметров волокна в диапазоне от 0,6 до 1 мкм.
- Супертонкие (микрокристаллические) базальтовые волокна служат для изготовления теплозвукоизоляционных гидрофобизированных изделий (матов или рулонов), различных жгутов и фильтров. Данный тип волокон считается наиболее популярным, поскольку благодаря специальной термической обработке, полученные микрокристаллы способны выдерживать температуру на 200 С выше чем предыдущие типы волокон. Также супертонкое микроволокно (диаметр от 1 до 3 мкм) не усаживается в процессе эксплуатации, что значительно увеличивает спектр применения данного материала.
- Тонкие волокна на минеральной основе представляют собой хаотические структуры с диаметром волокна в диапазоне от 9 до 15 мкм. Длинна отдельных волокон колеблется в диапазоне от 3 до 2000 мм. Данный материал широко применяется в фильтрах грубой очистки, а также при производстве минерального утеплителя для промышленных нужд.
- Утолщенные каменные волокна в большинстве случаев применяются в качестве основных систем фильтрации дренажных систем. Толщина данного типа волокон колеблется в диапазоне от 15 до 25 мкм, а длинна от 5 до 1500 мм.
- Толстые волокнистые структуры представляют собой хаотически расположенные волокна с диаметром от 25 до 150 мкм и длинной одного волокна от 0,05 до 3 м. Благодаря этому полученный материал может выдерживать колоссальные нагрузки на разрыв до 650 МПа.
- Грубые волокна — дисперсионно волокнистая масса из волокнистых структур толщиной от 150 до 500 мкм. Данная разновидность утеплителя может применяются в качестве армированного слоя при помощи специальных вяжущих элементов.
Сфера применения базальтовой (каменной) ваты
В связи с тем, что каменная вата является натуральным негорючим и долговечным материалом (поскольку на 95% состоит из натурального камня) она широко стала применятся в строительстве еще с начала 20-го века.
Благодаря своим отменным свойствам, которые заключаются в снижении потерь тепловой энергии в холодный период времени, и в сокращении попадания тепловой энергии вовнутрь здания летом, каменная вата широко применяются в следующих сферах:
- При утеплении фасадов зданий с последующей штукатуркой или монтаже сайдинга или профильного листа.
- При утеплении помещения изнутри (балконы, лоджии, наружные стены и т.д.).
- При утеплении основания пола с последующей заливкой стяжки.
- Для звукоизоляции «плавающего пола».
- При устройстве кровли или утеплении мансардных этажей.
- Для огнезащиты инженерных конструкций и сетей (данный материал способен выдерживать температуру до 700 С).
Достоинства каменной ваты (базальтового утеплителя)
Высокая химическая стойкость. Благодаря этому свойству материал не реагирует с щелочами и кислотами и имеет повышенную стойкость к продуктам нефтепереработки и растворителям.
Пористая структура. Благодаря данному свойству волокна составляют всего 70% от общего объема материала. Остальная часть — это прослойки воздуха, которые обеспечивают низкую теплопроводность полученного материала.
Огнеупорность. Данное свойство позволяет производить утепление как паропроводов, так и промышленного оборудования с высокими температурами. Поскольку материал изготавливается из натурального камня, он способен выдерживать температуру до 7000С.
Высокая паропроницаемость. Благодаря этому свойству материал не впитывает, а пропускает через себя влагу без образования конденсата.
Основные производители каменной ваты
На современном рынке, существует 3 основных производителя минеральной ваты на базальтовой основе:
- Технониколь.
- Knauf.
- Rockwool.
Минеральная вата Технониколь
Данный материал служит для тепло- и звукоизоляции фасадов, кровли, перегородок и технологических трубопроводов. Плотность данного материала находится в диапазоне от 30 (РОКЛАЙТ и ТКХНОЛАЙТ Экстра) до 145 кг/м3 (ТЕХНОФАС).
На современном рынке России, данный продукт представлен следующими разновидностями:
Наименование | Номинальная плотность, кг/м3 | Тепловая характеристика, Вт/м*0С | Область применения |
РОКЛАЙТ | 30 | 37-41*10-3 | Теплоизоляция стен и перегородок внутри помещения, утепление скатной кровли и полов на лагах |
ТЕХНОЛАЙТ ЭКСТРА | 35 | 36-41*10-3 | Устройство звуко- и теплоизоляции перегородок офисных и бытовых помещений |
ТЕХНОФАС | 145 | 36-42*10-3 | Утепление фасадов перед последующей штукатуркой или отделкой с помощью сайдинга |
ТЕХНОФЛОР | 90-170 | 34-47*10-3 | Утепление плавающих, теплых или наливных полов с последующим устройством цементно-песчаной стяжки |
ТЕХНОРУФ | 140-190 | 36-42*10-3 | Основной теплоизоляционный слой при новом строительстве или проведении реконструкции кровельного покрытия без необходимости в последующей стяжке |
ТЕХНОБЛОК СТАНДАРТ | 45 | 34-39*10-3 | Утепление и звукоизоляция всех типов зданий и сооружений, в которых слой утеплителя не подвержен высоким статическим нагрузкам |
ТЕХНОВЕНТ СТАНДАРТ | 80-90 | 33-40*10-3 | Устройство вентилируемых фасадов |
Базальтовая вата Knauf
Каменная вата Кнауф — это эффективная тепло- и звукоизоляция на основе горных пород, которая обладает высокой паропроницаемостью, химической стойкостью к кислотам, лугам и продуктам нефтепереработки.
На рынке России данный материал выпускается под маркой Knauf Insulation и представлен следующим ассортиментом:
Наименование | Номинальная плотность, кг/м3 | Тепловая характеристика, Вт/м*0С | Область применения |
Insulation DDP | 150-200 | 40*10-3 | Утепление и звукоизоляция плоской кровли, угол наклона которой не превышает 150 |
Insulation DDP-K | 105-110 | 37-41*10-3 | Утепление и звукоизоляция плоской кровли, угол наклона которой не превышает 150, а также для утепления плавающих полов |
Insulation FKD | 140-150 | 39*10-3 | Утепление наружных фасадов здания или устройство вентилируемых фасадов |
Insulation FKD-S | 100-140 | 36*10-3 | Утепление стен снаружи и устройство скрепленных фасадов |
Insulation FKL | 85 | 40*10-3 | Наружное утепление стен перед монтажом сайдинга |
Insulation HTB | 35-150 | 37-39*10-3 | Утепление инженерных сетей, трубопроводов и воздухопроводов с температурой от -180 до 7000С |
Insulation LMF AluR | 35-90 | 40*10-3 | Утепление инженерных сетей, трубопроводов и воздухопроводов с температурой от -180 до 7000С |
Insulation PVT | 175 | 40*10-3 | Утепление перекрытий и плавающих полов |
Insulation WM 640 GG/WM 660 GG | 80-100 | 35*10-3 | Утепление технологического оборудования и трубопроводов |
Insulation цилиндры | 75 | 40*10-3 | Техническая изоляция инженерных сетей и трубопроводов |
Базальтовая вата Rockwool
Продукция концерна Роквул — это высокоэффективные гидрофобизированные минеральные плиты, изготавливаемые из базальтовой породы с добавлением специальных добавок для улучшения технических характеристик.
Компания предлагает на территории России следующий ассортимент:
Наименование | Номинальная плотность, кг/м3 | Тепловая характеристика, Вт/м*0С | Область применения |
EPIROCK | 20 | 45*10-3 | Утепление вентилируемых перекрытий, а также деревянных полов на лагах |
ROCKROLL | 22 | 44*10-3 | Утепление вентилируемых перекрытий, а также деревянных полов на лагах |
ROCKSLAB ACUSTIC | 50 | 36*10-3 | Звукоизоляция перекрытий и перегородок помещений различного назначения |
ROCKSLAB | 26 | 42*10-3 | Утепление стен, потолков и полов без нагрузки на слой каменной ваты |
STEPROCK HD | 140 | 39*10-3 | Утепление строительных конструкций и перекрытий с высокими динамическими нагрузками |
ROCKMIN | 26 | 39*10-3 | Устройство не нагружаемого теплоизоляционного слоя |
STEPROCK HD4F | 140 | 39*10-3 | Устройство динамического модуля упругости для производственных и жилых зданий |
FRONTROCK S | 110 | 39*10-3 | Утепление фасадов зданий и сооружений с последующим нанесением армированного слоя и штукатурки |
MONROCK MAX E | 115-220 | 37*10-3 | Утепление всех типов перекрытий без необходимости в последующем устройстве цементно-песчаной стяжки |
FIREROCK | 80 | 42*10-3 | Теплоизоляция поверхности каминов и технологического оборудования |
Выводы
Оборудование для производства минеральной ваты позволяет изготавливать высокоэффективные утеплители для любых типов помещений, а также обеспечивать надёжную тепло- и звукоизоляцию как кровли, так и полов, и стен.
На современном рынке можно найти большое разнообразие минеральных утеплителей на основе базальтовых пород, которые обладают не только высокими техническими характеристиками, но и обеспечивают огнеупорность технологическим трубопроводам в соответствии с мировыми стандартами.
remontami.ru
Медицинская вата: производство, виды, назначение
Медицинская вата относится к категории самого востребованного расходного материала, который применяют в широкой сфере. Ею пользуются во время проведения хирургических операций для того, чтобы делать стерильные перевязки. Также материал используется для проведения инвазивных лечебных, либо диагностических мероприятий. В зависимости от того, из чего делают этот полезный помощник, будет зависеть его дальнейший спектр применения. Некоторые виды, которые имеют отметку ГОСТ, привлекаются даже для реализации косметических процедур.
Цена представленного расходника напрямую зависит от того, насколько натуральным оказался состав, а также методику обработки сырья. Чем выше класс, тем меньше рисков для пациента столкнуться с аллергическими проявлениями или другими вариантами патологий вроде воспалительного процесса. Хорошая стерильная вата не тормозит процесс выздоравливания, что благотворно сказывается на общем состоянии здоровья.
Сырье для производства
Несмотря на то, что большинство обывателей до сих пор полагают, будто пользуются исключительно хлопковой ватой, это далеко от истины. Сегодня ее производство шагнуло вперед, используя в качестве основания некоторые другие составляющие.
Общий алгоритм переработки при любом раскладе остается идентичным, ведь в большинстве случаев все равно приходится закладывать для «фундамента» хлопковое волокно. Но сейчас часто встречаются вискозные вариации, либо смешанные типы.
Еще несколько десятков лет назад каждый производитель подвергался строгой проверке со стороны соответствующих служб. Ими было запрещено привлекать различные добавки. С тех пор у многих потребителей отложилось в голове, что вата представляет собой просто специально обработанный хлопок. Но теперешние нормы позволяют замещать часть состава синтетическими или другими природными компонентами.
С точки зрения разработчиков подобной стратегии, это позволяет существенно удешевить себестоимость продукции, из-за чего ее цена оптом окажется незначительной. Самым любопытным эксперты предлагают приобрести несколько пакетиков такого материала от разных брендов, а потом в домашних условиях сравнить их структуру. Обычно упаковка с внешней стороны исчерпывающую информацию о составе содержимого не раскрывает. Чтобы узнать подробности, приходится вчитываться в мелкий шрифт на обратной стороне пачки. А некоторые недобросовестные изготовители вовсе предпочитают умалчивать часть важной потребительной информации. Их выдаст только детальное изучение текстуры содержимого пакетика.
Всего по заданному вопросу имеется всего три версии классификации:
- хлопковая;
- вискозная;
- регенерированная.
Первую версию легко отличить по говорящим за себя внешним признакам. Речь идет о длинных волокнах, а также белом цвете с желтоватым оттенком. Текстура включает небольшие горошинки.
Вторая модификация отличается белоснежным цветом, который иногда отдает голубизной. При встряхивании содержимого такого пакетика будет летать пыль. Если при надавливании на рулончик слышится поскрипывание, то это практически всегда свидетельствует не в пользу натуральности.
Обычно производители для достижения идеальной цветовой палитры привлекают оптические отбеливатели, среди которых на первом месте по популярности числится диоксин. Именно он считается одним из наиболее потенциально опасных канцерогенных веществ.
Регенерированный аналог создаются на основе вторсырья. Об этом ярко свидетельствуют наличие ниток, что является отходами текстильного производства. Многих интересует, что будет, если встряхнуть рулончик. От него тоже разлетится пыль, как при тесте вискозной альтернативы. Цвет может быть как чисто белым, так и с легким синеватым отливом. Поставляется она обычно в рулонах или больших тюках, и используется в довольно узком перечне областей эксплуатации.
Отдельно рассматривается так называя кипная вариация. Это специальная хирургическая вата, которую иногда еще можно встретить в кабинетах косметологов. Отличительная характеристика такого предложения предусматривает полное отсутствие различных добавок, синтетических составляющих вроде красителей или химических отбеливателей.
Подобная предосторожность окупается за счет того, что продукт оказывается гипоаллергенным. Но вот приобрести его в аптеке просто так вряд ли получится. Больницы и лечебницы заказывают ее напрямую от производителя в больших объемах.
Требования к качеству
Разобравшись с тем, из чего сделана классическая и современная вата, потребители полагают, будто других классификаций для нее не существует. Но на самом деле вся гигроскопическая продукция такого рода имеет отдельную сортировку согласно конкретному предназначению.
Разделение рассчитано на три лагеря:
- глазной;
- хирургический;
- гигиенический.
Первое решение отличается от других сырьем. Тут задействуют исключительно хлопковое волокно первого сорта. Благодаря этому получается добиваться оптимальной поглощающей способностью и капиллярностью. На практике это означает, что расходник хорошо впитывает влагу любого типа.
Чтобы добиться подобного эффекта, авторы привлекают только длинноволокнистый вид хлопка. Результат порадует отсутствием специфичного «ватного пуха».
Хирургическое предложение имеет наиболее высокую степень прочеса. За счет подобной скрупулезности получается нейтрализовать даже мельчайшие сорные составляющие. Не зря же она потом легко впитывает, удерживает жидкости и хорошо разделяется по слоям после извлечения из коробки.
Гигиеническая вата проходит при проверке соответствующими органами меньше стадий контроля. Тут допускаются некоторые примеси, даже синтетическая составляющая вроде отбеливателя не является редкостью. Обычно именно гигиенические наполнители встречаются в свободной продаже в аптеке. Они могут содержать узелки или короткие волокна, а также иметь неравномерную белизну.
Но даже у самого простого ватного решения имеются рамки, установленные специалистами из службы контроля качества. Для решений высшего сорта, требования более жесткие, и включают в себя:
- Наличие в составе только 100%-ого содержимого натурального хлопка.
- Отсутствие комочков, неравномерно расположенных толстых нитей. Хороший расходник обязан быстро и легко расслаиваться, а также быть отлично прочесанным.
- А вот небольшое наличие узелков является допустимым вариантом развития событий.
- Приятные текстильные ощущения должны объясняться мягкой текстурой изделия.
- Цветовая палитра может колебаться только в рамках допустимых отклонений в кремовые оттенки. Если покупка имеет слишком ярко выраженный белый тон, либо присутствуют голубые тона, то это свидетельствует об оптических отбеливателях. Людям с чувствительным кожным покровом стоит избегать таких экземпляров, чтобы не нарваться потом на крапивницу или другое проявление аллергии.
- Впитывание поступившей на поверхность слоя влаги должно происходить мгновенно. Стекание по ватному шарику свидетельствует об обилии ненатуральных компонентов.
- Разделение по слоям происходит быстро и без значительных усилий. Пыль, а также выпадающие короткие волокна – тоже признак недоброкачественного продукта.
- Распакованная покупка должна быть внутри полностью сухой вне зависимости от того, какое у нее финальное назначение.
Отдельно стоит провести тест на подозрительный запах. Настоящая вата его не имеет, а адаптации с ароматизаторами, либо сопутствующие запахи вроде едких химических или лекарственных ароматов – плохой знак.
Как получают стерильный материал
Если требуется создать своими руками временно компрессионное белье, то для него берут эластичные бинты и нестерильную вату. Такое средство отлично подходит для ситуаций, когда по умолчанию касания материала с открытой раневой поверхностью не предусмотрено.
Самое большое отличие стерильной или нестерильной комбинации заключается в обязательном прохождении процедуры просушки сырья в специальной печи. Так получается за короткое время уничтожить различные болезнетворные микроорганизмы. Потом очищенный и обеззараженный расходник разрешают прикладывать даже на открытые раны без опаски возможного заражения.
Нестерильное решение обходится без вспомогательной стерилизации, а сразу же после первичной обработки отправляется в упаковочный цех. При этом плотность двух представителей практически не отличается.
Нестерильная комбинация подходит для следующих целей:
- медицинских;
- косметологических;
- гигиенических.
На основе представленного вида далее на производствах создают перевязочные детали, а также используют во время выполнения манипуляций, связанных с индустрией красоты в центрах эстетической медицины. Разработанные на их основе диски, шарики, спонжи потом позиционируются в качестве помощников по уходу за лицом и телом в домашних условиях.
Привлекать нестерильный материал допускается только в ситуациях, когда риски инфицирования сведены к нулю. Потребителям она нравится за счет своей относительно небольшой стоимости и возможности в считанные секунды впитывать большое количество жидкости.
Если уделить пару минут изучению инструкции, то можно заодно уточнить, добавлялся ли в состав хлор в качестве отбеливателя. Его отсутствие – пропуск к не возникающему кожному раздражению. Но если человек проглотил кусочек шарика или диска без воздействия хлором, все равно следует обратиться за консультацией к специалисту.
Причем сделать это нужно как можно скорее, чтобы избежать возможного негативного развития событий и сопутствующих осложнений.
Стерильные экземпляры имеют сертификацию, а также должны в обязательном порядке проходить процедуру паровой, либо химической стерилизации. Результат отлично зарекомендовал себя в следующих ситуациях:
- производство повязок, которые потом будут контактировать с открытой раневой поверхностью или следами ожогов;
- изготовление перевязочного материала, накладываемого поверх обработанной антисептиком территории;
- при необходимости не допустить даже малейшей процентной вероятности занести инфекцию.
Эта вата получила однородную структуру, а также мягкий гриф и однотонную цветовую палитру без голубых разводов, ведь здесь не допускается привлечение любых видов примесей. Сорбционные свойства значительно повышены.
Технологический процесс
Основой для создания привычной аптечной ваты является мохнатый хлопчатник, прошедший несколько стадий обработки.
Сначала его приходится собирать, что выпадает на период созревания плодов растения, представляющих необычные коробочки. Со временем они раскрываются, и внутри виднеется мягкое волокно светлых оттенков вместе с семенами. Именно это содержимое считается наиболее ценным, поэтому его собирают, сдают на специальных пунктах сбора, а потом оттуда уже передают на хлопкоочистительные комбинаты.
Уже в заводских условиях собранный первоисточник сначала отделяют от попавших семян, а также делят волокна согласно показателям длины. Стандарты для длинных волокон составляют не менее 2,5 сантиметров. Таких «гигантов» привлекают для изготовления хлопчатобумажной ткани.
Короткие волокна в профессиональной терминологии называют линтами. Как раз именно их привлекают к производству ваты и последующих из нее изделий.
Иногда основой для продукта выступает шерсть или даже лен. Причем последнее сырье числится более распространенным. Но большинство изготовителей предпочитает смешивать несколько типов, чтобы добиваться оптимальных технических и эстетических характеристик. Особенно часто встречаются хлопково-вискозные комбинации, ставшие одними из первых версий сочетаний искусственного и натурального материала.
В последующей обработке используется только хлопок, который был оценен не ниже четвертого сорта. Лучше всего, если это будет упругий и низкомерный хлопок, который по структурному распределению больше напоминает шерсть.
Разница в технологическом процессе базируется на том, требуется ли создать наполнитель для одежды, либо для медицинских целей. Для традиционного производства специалисты отдают предпочтение засоренным угарам. Так называют основу, которая при переработке выдает текстильные волокнистые материалы. Для таких целей вполне годятся короткие волокна.
Сначала сырье очищают от природного мусора, привлекая для этого специальный пыльный волчок. Также на предварительной стадии обрабатываются особо жесткие волокна, которые должны расщепиться во время прохождения многобарабанных щипков.
Получившийся итог очищают, смешивают, формируют в холсты, используя заводские прессы и другое оборудование. В начале пласта устанавливается волокнистая масса без четких контуров. На нее придется воздействовать чесальной и валочной машинами, чтобы преобразовать бесформенное нечто во вполне нормальный ватный съем. На этой же стадии определяется четкая структура согласно заданным параметрам, а также предпочитаемая толщина.
Далее полуфабрикат проходит контроль качества, чтобы исключить риски производственного брака, после чего ее прессуют, упаковывают по кипам. Один такой куб может потянуть на полсотни килограмм. В таком виде материал отправляют далее на фабрики швейного производства, мебельные заводы или на другие профильные предприятия.
Отдельно рассматриваются случаи необходимости создать полностью чистый, готовый к практическому применению продукт. При таком раскладе изначально массу сначала разрыхляют, а потом отправляют на очистительный и рыхлительный станок.
После чего наступает стадия варки в щелочном растворе, чего получается достичь при нагнетании температурного режиме около 130 градусов и правильной отметке внешнего давления. Заключительная ступень очистки предусматривает обработку гипосульфитом натрия.
Последний шаг необходим для преобразования физического волокна и нейтрализации природного желтоватого оттенка. Составной фазой очистки выступает удаление пектинового и азотистого вещества. Итог порадует белоснежностью.
Если требуется дополнительно обеспечить вату возможностью эксплуатации при открытых раневых поверхностях, то ее отправляют стерилизовать. Для этого печь разогревают до 125 градусов, устанавливая планку давления на границе 3 атмосфер.
Часть получившегося товара пакуют и отвозят на склады, а оставшуюся половину сразу же пускают в оборот. Речь идет о производстве ватных палочек для очистки труднодоступных мест. Отдельно существует категория очистительных ватных средств исключительно технического назначения, а не гигиенического, что позволяет снизить их стоимость.
Отдельно рассматривается выпуск ватных исков, плотность которых несколько выше, нежели у пористого стандартного исходника. Потребители высоко оценили такого помощника в нанесении и снятии макияжа за счет того, что при намачивании он значительно не меняет своей формы.
Вне зависимости от конечной цели эксплуатации, эксперты советуют выбирать вату без химических добавок, если планируется прикасаться ею к кожному покрову, даже если это не открытая раневая поверхность.
foodandhealth.ru
Технология производства минеральной ваты
Минеральная вата обретает сегодня всё большую популярность и востребованность, что вызвано не только её прекрасными техническими и эксплуатационными данными, но и вполне приемлемой ценовой политикой. Вместе с тем, многие даже и не подозревают о том, как изготавливается данный материал. Именно о том, как проходит производство минеральной ваты и особенностях технологического процесса и пойдёт речь в рамках этой статьи.
Технология производства минеральной ваты
Сразу же заметим, что вата минеральная в России изготавливается на основе множества материалов – доломита, базальта, диабаза, шлаковый материал получают за счёт шлакового отхода, идущего из доменной металлургии. Несмотря на тот факт, что внешне минеральная вата от разных производителей абсолютно идентична, на самом деле технология производства всё же имеет определённые различия. Формулы рассчитываются в специальных лабораториях, а итоги исследований хранятся в строжайшем секрете.
Рецептура данного материала учитывает его максимально возможные эксплуатационные и технические параметры, отличные теплоизоляционные данные, а также повышенную сопротивляемость нагрузкам динамического характера. На качество материала огромное значение оказывает его химическая формула, а также толщина получаемого волокна – чем оно тоньше, тем лучше теплоизоляционные характеристики у минваты. Да и стоимость такого материала значительно выше.
Этапы изготовления минеральной ваты
Поговорим теперь о том, в какой именно очерёдности изготавливаются минеральные ваты в России и какова особенность каждого из этапов:
- В первую очередь проводится расплавление исходного сырья. Предварительно подготовленная смесь загружается в специальные печи, ванные или вагранки. Рабочая температура достигает 1400-1500 градусов. Степень вязкости расплава определяет длину и толщину волокон, их динамику и теплоизоляционные данные;
- Готовый расплав перемещается внутрь центрифуги, где вращающиеся при скорости 7000 об/мин валки превращают состав во множество отдельных и независимых волокон. Здесь же они покрываются связующими на синтетической основе, для чего чаще всего применяются различные смолы. За счёт мощного потока воздуха волокна перемещаются в камеру охлаждения, формируя нечто, напоминающее ковёр;
- Ламельное или гофрировочное оборудование придаёт волокнам требуемый объём и длину, после чего наступает черёд термокамеры. Под воздействием высокой температуры состав полимеризуется и обретает окончательный объём, размер и форму. Показатели прочности формируются на завершающем этапе, где чрезвычайно важно выдержать верный температурный режим;
- В завершение минвата режется на блоки требуемых габаритов и упаковывается. Для упаковки применяется плёнка с эффектом термоусадки, благодаря чему можно гарантировать сохранность минваты в процессе погрузки, транспортировки и последующего хранения.
osnovam.ru
Бизнес на производстве минеральной ваты
Производство минеральной ваты можно разбить на несколько стадий: подготовка сырья, получение волокна из расплава, полимеризация и нарезка готового материала. Минеральная вата на данный момент является отличным материалом, который имеет широкий спектр применения в различных отраслях.
- Что нужно знать о базальтовой минеральной вате перед началом производства
- Технология производства минеральной ваты
- Какое оборудование выбрать?
- Достоинства и недостатки бизнеса по производству минеральной ваты
Высокую эффективность применения данного материала специалисты отмечают и в строительной индустрии. Среди многообразия минеральной ваты, которая представлена на рынке строительных материалов, потребители выделяют уникальные свойства такого материала, изготовленного из базальтовых пород.
Что нужно знать о базальтовой минеральной вате перед началом производства
Данный материал имеет волокнистую структуру. Если перевести с английского языка «базальтовый утеплитель», то дословно можно получить «горная шерсть».
Именно из-за того, что структура материала имеет волокнистый компонент, в ней идет накопление воздуха в больших объемах. При этом такие объемы воздуха практически не перемещаются по толщине этого материала. Это объясняется наличием ряда препятствий в виде большого количества волокон. Такое свойство в комбинации с малым диаметром волокна дает возможность базальтовой вате иметь высокие теплоизоляционные свойства.
На данный момент специалисты выделяют два типа базальтовых волокон, которые встречаются в утеплителях:
- Штапельное волокно. Для данного типа характерным является его диаметр.
- Непрерывное волокно.
При этом сами базальтовые волокна, которые применяются в изготовлении минеральной ваты, могут иметь различные диаметры, от 0,6 мкм до 500 мкм.
Поэтому принято разделять волокна на следующие виды:
- Микротонкие с толщиной 0,6 мкм.
- Ультратонкие с диаметром порядка 1,0 мкм.
- Супертонкие. Их диаметр составляет 3 мкм.
- Тонкие с толщиной около 15 мкм.
- Утолщенные, в диаметре равные 25 мкм.
- Грубые. Такие волокна могут достигать в диаметре 500 мкм.
Во время процесса изготовления материал формируется в рулоны. Также часто применяется формирование его в плиты или маты. При этом материал подразделяется специалистами на нефольгированный и фольгированный виды.
Технология производства минеральной ваты
Способ, с помощью которого производится минеральная вата, был открыт на Гавайских островах. Это стало возможным, когда были найдены камни в результате извержения вулкана. Тогда нашли тонкие нити вулканической породы. Это были первые представители современных волокон, которые используются при изготовлении минеральной ваты. После этого в 1897 г. в Северной Америке получили и первую минеральную вату.
Для производства материала используется следующая технология:
- Применяется специальная печь, в которой температура достигает 1500°С.
- В печь помещается горная порода. Из нее выходит специальный огненный расплав в жидком виде.
- Далее происходит вытягивание такого расплава в волокна. Для этого применяется несколько способов, среди них центробежное дутье, простое дутье и модифицированные методы.
- Когда волокна уже сформированы, в них вводится специальное связующее вещество. Для этого может применяться технология распыления на волокна. Часто используют и полив на ковер из ваты базальтового типа. Есть еще вариант, связанный с приготовлением гидромассы.
- Чтобы минеральной вате придать дополнительные свойства при ее последующей эксплуатации, добавляется специальная смесь. Она позволяет улучшать показатели плотности, проницаемости, гидрофобности и ряд других характеристик.
- Полученный ковер, на который нанесено связующее вещество, обрабатывают термическим путем при температуре, достигающей 230°С. Это позволяет тепловому носителю провоцировать реакцию поликонденсации связующего элемента.
- Когда проведена термическая обработка базальта и туда добавлены необходимые примеси, то на выходе получаем продукт. Он имеет структуру, которая характеризуется ячеистой сеткой открытой формы. Такой продукт может работать на эффективном уровне при температуре, достигающей 1000°С. Это так называемый верхний предел рабочего диапазона температур минеральной ваты.
- В таком готовом продукте содержание веществ, имеющих органическое происхождение, не превышает обычно показателя в 3%.
- Теперь технология изготовления этого материала выходит на свою завершающую стадию. Производится нарезка в виде плит, которые необходимы для утепления. После этого выполняется упаковка материала и доставка потребителям.
Какое оборудование выбрать?
Оборудование для производства минеральной ваты состоит из шахтной печи, сушильных линий, подпрессовочного оборудования, камеры термообработки.
Достоинства и недостатки бизнеса по производству минеральной ваты
Бизнес на производстве и продаже минеральной ваты — это очень выгодно и не требует крупных вложений.
Данный продукт имеет отличные показатели в плане эксплуатации. Также данный утеплитель может эффективно применяться и при высоких температурах, которые характерны для мест с повышенным коэффициентом пожарной опасности.
Среди недостатков такого продукта специалисты отмечают свойство материала впитывать влагу. Это может значительно ухудшить его свойства тепловой изоляции, а в некоторых случаях привести и к их полной потере. Поэтому, чтобы исключить такие факторы, производители используют покрытия кашированного или алюминиевого типа.
Данный тип минеральной ваты активно используется в строительстве как эффективное средство, при помощи которого осуществляется тепловая изоляция помещений.
Перед тем как применять ее, необходимо обратиться за консультацией к специалистам, которые помогут эффективно организовать утепление дома.
vipidei.com
Хлопковая вата – происхождение, преимущества, особенности
Хлопковая вата – материал знакомый всем с детства. Делают ее из разного сырья, но лучшей в большинстве случаев считается вата из хлопка, представляющая собой волокна хлопковых семян, слабо связанные друг с другом и разделенные на слои.
Преимущества хлопковой ваты
Хлопчатник – растение, чьё волокно используется для производства тканей и ваты, знаком человечеству уже тысячи лет. Специалисты до сих пор спорят, появился ли он в Индии или в Древнем Египте. Очевидно одно – материал, получаемый из этого растения, очень нужен и полезен людям, иначе оно не удержалось бы столько лет рядом с человеком.
Список преимуществ хлопковой ваты не длинный, но выразительный:
- Хлопчатобумажная вата – материал натуральный, проверенный веками, а, следовательно – абсолютно безопасный с экологической точки зрения.
- На хлопковую вату не бывает аллергии. Если неправильно ухаживать за ватными изделиями, в них, как и везде, может скопиться пыль. Реакцию на нее часто путают с аллергией, но хлопковая вата не аллергенна.
- Вата лучше всего остального сохраняет тепло. Несмотря на многочисленные изобретения химиков, ничего лучше ваты для сохранения тепла до сих пор не придумали. Исключение – очищенный птичий пух, без примеси пера, но изделия из него очень дороги.
- Хлопковая вата – материал упругий, хорошо впитывающий влагу.
- Изделия, в которых использован ватный наполнитель, не требуют сложного ухода – их можно стирать, сушить, стерилизовать паром. Главное – после просушки расправить волокна, чтобы вернуть вещи упругость и пышность.
- Стоимость ваты из хлопка – одна из самых низких по сравнению с другими натуральными наполнителями. Отработанный веками процесс производства позволил понизить себестоимость этого материала и повысить его качество, причем новые разработки в этой области и сегодня время от времени появляются на рынке.
Производство хлопковой ваты
Чтобы разобраться, на чем основаны преимущества ваты, и понять, в каких областях ее лучше всего использовать, необходимо разобраться, из чего именно и как ее производят. Собранные семенные коробочки хлопчатника поступают на заводы, где их в первую очередь очищают от всевозможных примесей: песка, мелких камушков, стеблей, недозревших семян и прочего. Затем необходимо отделить волокна хлопка от семян. Выполняется это при помощи специальных машин, которые называют джинами.
Джины-волокноотделители в первую очередь разделяют хлопок на волокна, линт и делинт. Волокна используются для изготовления пряжи и ткани, а вот из линта – волокон короче 2 см и делинта (волокна короче 0,5 см) изготавливают вату. Для того чтобы собрать весь линт полностью, семена с оставшимся на них пухом еще несколько раз пропускают через специальные очистители – линтеры.
Кроме волокон в производстве ваты используются еще и хлопковые угары. Так называют остатки пуха, которые оседают на стенках машин после очистки сырья и при производстве хлопчатобумажных тканей.
Угары делят на три вида:
- волокнистые угары,
- регенерированное волокно
- хлопковый пух.
Волокнистые угары используют для производства высококачественной ваты, остальные же виды чаще добавляют в набивку мебели и матрасов.
Получившуюся смесь расщепляют с помощью механизмов и формуют в листы и кипы. На этом обработка большинства видов ваты заканчивается, исключением являются кипы, предназначенные для изготовления медицинской ваты. Их еще раз очищают, разрыхляют и отваривают в растворах щёлочи при достаточно высокой температуре, чтобы отбелить. Затем удаляют пектиновые и азотистые соединения и стерилизуют под высоким давлением, после чего вата готова к отправке.
Виды хлопковой ваты
Хлопковая вата делится на группы в зависимости от длины волокон и степени очистки. Названия виды получили по области применения разновидностей этого продукта. Современные стандарты выделяют 4 вида:
- одежную, которая легко делится на слои;
- мебельную, нерасчесанную;
- медицинскую, белую, иногда желтоватую, для компрессов, повязок и операций;
- техническую, которая используется для упаковки или в качестве сырья.
Одежная вата
Одежную вату производят из хлопка четвертого, пятого и шестого сортов, не пригодного для производства пряжи. К хлопковым волокнам добавляют пух, хлопкопрядильные угары, иногда вторичное сырье.
По количеству и виду примесей вату делят на несколько сортов, требования к которым регламентирует ГОСТ 5679 — 91 «Вата хлопчатобумажная одежная и мебельная. Технические условия»:
- Вата «Люкс»
- Вата «Прима»
- Вата «Швейная».
Этот стандарт четко регламентирует свойства ваты, и именно его соблюдение гарантирует, что вы получите именно то, что вам требуется.
В вате сортов Люкс и Прима хлопковые угары почти не встречаются, основной их состав – коротковолокнистый хлопок. Вата Люкс – самая чистая: количество необработанных волокон в ней, по ГОСТ 5679 минимально – всего 2,6%, это вата самая упругая – упругость 67%. Ее плотность всего 22 кг/м3, а значит, изделия из ваты Люкс будут легкими, теплыми, пышными и долго не потеряют форму.
Вата Прима сортом чуть ниже, в ней сорных примесей уже 5%, она менее упругая (65%), то есть изделия из нее чуть хуже сохраняют форму. Весит она тоже больше – ее плотность 23 кг/м3, правда в этом случае разница с ватой Люкс не очень заметна.
Швейная вата делается из хлопчатого пуха и угаров, доля длинных хлопковых волокон в ней 35%. Вата Швейная более плотная и тяжелая, чем Люкс и Прима, ее плотность 25 кг/м3. Сорные примеси и необработанные волокна составляют в ней 7%. При этом Швейная остаётся достаточно упругой (60%) и продукция из нее хорошо держит форму. Применяют такую Швейную как утеплитель одежды, включая спецодежду, для производства одеял и высококачественных беспружинных матрасов.
Мебельная вата
Мебельная вата (она же тюфячная) по составу близка к Швейной – она так же делается из низкосортового хлопка, угаров и отходов текстильных фабрик. Ее приходится долго чистить, затем пропускать через рыхлительно-трепательные механизмы, чтобы волокнистая масса приобрела объём и упругость.
Для мебельной ваты характерна загорошенность – так называется наличие в вате узелков и пороков волокна, которые не удалось растрепать. Их легко почувствовать, прикоснувшись к такой вате. Уровень загорошенности тоже строго регулируется ГОСТами. Этой ватой набивают мягкую мебель и тюфяки.
Медицинская вата
Медицинская вата – наиболее чистый продукт. Она делится на несколько групп – глазную, бытовую гигиеническую, хирургическую (стерильную или нет) и прочее. Главный признак, на котором основано использование медицинской ваты — обезжирена она или нет. Обезжиренная вата, вываренная в щелочном растворе, используется при перевязках и операциях, а необезжиренная – более упругая и пышная, чаще используется для подклада под фиксаторы при лечении переломов и для компрессов.
Техническая вата
Этот сорт ваты делают из регенерированного хлопкового волокна, которое получают переработкой отходов от производства ваты более высоких сортов, и вторичного сырья. Техническую вату тоже иногда используют для набивки мебели и матрасов, но основная область ее применения – упаковка бьющихся товаров, а также теплоизоляция и звукоизоляция помещений. Хлопковая техническая вата встречается нечасто, обычно в такой продукции есть синтетические волокна, количество которых может достигать 40%.
Востребованность хлопковой ваты
Натуральная хлопковая вата еще долго будет востребована в швейной и мебельной промышленности, в строительстве и медицине. Даже самые новые материалы никогда не смогут превзойти лучшего мастера – природу по экологичности, безопасности и комфорту, которые дает хлопковый ватный наполнитель.
lurtex.ru
Ведущие производители минеральной ваты в России
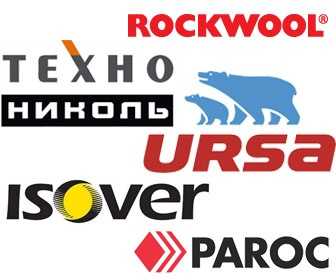
Минеральная вата – современный теплоизоляционный материал, являющийся одним из самых востребованных, представлен на нашем рынке большим количеством известных зарубежных производителей. Кроме продукции мировых лидеров, есть возможность приобрести вполне конкурентоспособные изоляторы от отечественных заводов.
Основные производители минеральной ваты в России
Производители минеральной ваты в России – это отечественные заводы, и филиалы промышленных концернов из других стран, развернувшие цеха на нашей территории. Кроме общепризнанных лидеров, по стране разбросано множество малых предприятий по производству минватных утеплителей, чья продукция менее известна и востребована, хотя может соответствовать принятым в отрасли стандартам. Производители минеральной ваты в России поставляют свой товар в больших объемах, которые если и не способны полностью покрыть спрос, то обеспечивают его значительную долю.
Производители плит минераловатных в России чаще всего используют в качестве сырьевой базы шлаковые отходы или базальтовые горные породы, выпуская шлаковую или каменную разновидность минеральной ваты, из которой в последующем формируются плиты – одна из наиболее популярных форм выпуска. Стекловолоконная минвата (кварцевый песок, отходы стекольных заводов) также изготавливается российскими предприятиями, но ее доля значительно меньше.
Производство минеральной ваты в России ощутимо подкосил финансовый кризис, начавшийся в 2007 и длившийся по 2010 год, в результате которого начавшие успешно развиваться молодые предприятия обанкротились. Заводы продолжали закрываться и в течение 2011 года. В результате такого естественного отбора выжили только сильнейшие игроки рынка стройматериалов, выпускающие качественную продукцию и имеющие продуманную маркетинговую политику.
На фоне провалов более слабых организаций, производители плиты минераловатной Rockwool в России только упрочили свои позиции, приобретя для своего концерна новые заводы. Начав в 1999 году с одного предприятия в городе Железнодорожный, сегодня датчане распространили свою производственную сеть по всей стране. Открывшийся в 2012 году в Елабуге филиал, оснащенный оборудованием последнего поколения, может стать самым крупным в своем сегменте не только у нас, но и на всем Евразийском континенте.
Список производителей минеральной ваты в России
В группу лидеров по производству минераловатных теплоизоляционных материалов в нашей стране, входят несколько ведущих предприятий.
- Концерн Rockwool – имеет обширную сеть предприятий объединенных в ЗАО «Минеральная вата». Выпускают различную минватную продукцию для всех элементов конструкции, бытового и промышленного назначения. Специализируются на использовании сырья базальтовых пород.
- Компания Технониколь – Российский производитель, разместивший свои предприятия не только по всей стране, но и в ближнем зарубежье (бывшие компаньоны по СССР) и странах Европы. Торговая сеть имеет представительства более чем в 30 странах. Продукция рассчитана на частное и промышленное применение.
- Компания Изорок – отечественное производство с зарубежными акционерами (100% иностранного капитала). Выпускает изделия из каменной минваты на заводе в Тамбове, построенном в 80-х годах прошлого века и прошедшем модернизацию.
- Компания Эковер – новичок в сфере производства базальтовых минватных утеплителей, чья продукция, выпускаемая на Урале, завоевывает все большую популярность во всех регионах. Материалы этой компании составляют достойную конкуренцию товарам лидеров.
Производство теплоизоляционных материалов на основе минеральной ваты крупнейшими Российскими предприятиями – возможность обеспечить постоянно растущий в стране спрос и сделать дорогостоящие утеплители на каменном сырье более доступными.
bazaltovaya-vata.ru